Two Shot (2K) Injection Molding Manufacturer
Our advanced two-color injection molding technology allows us to produce high-quality, aesthetically pleasing, and functionally superior plastic components tailored to your specific needs, helping your brand stand out in the market.
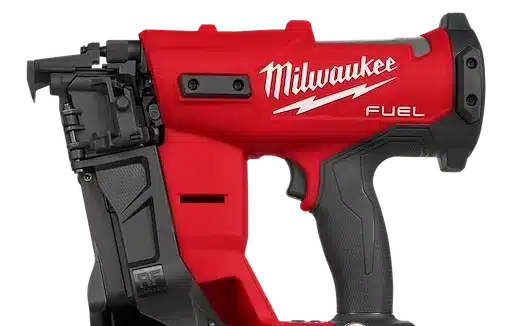
Milwaukee Multi-Material Injection Molding Partner
2K Machines Ranging from 110 Tons to 1,200 Tons
Leading in Two-Color Injection Molding in China
Strict Quality Control Meets EU and US Standards






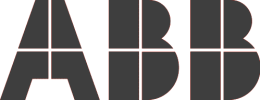

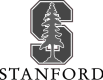
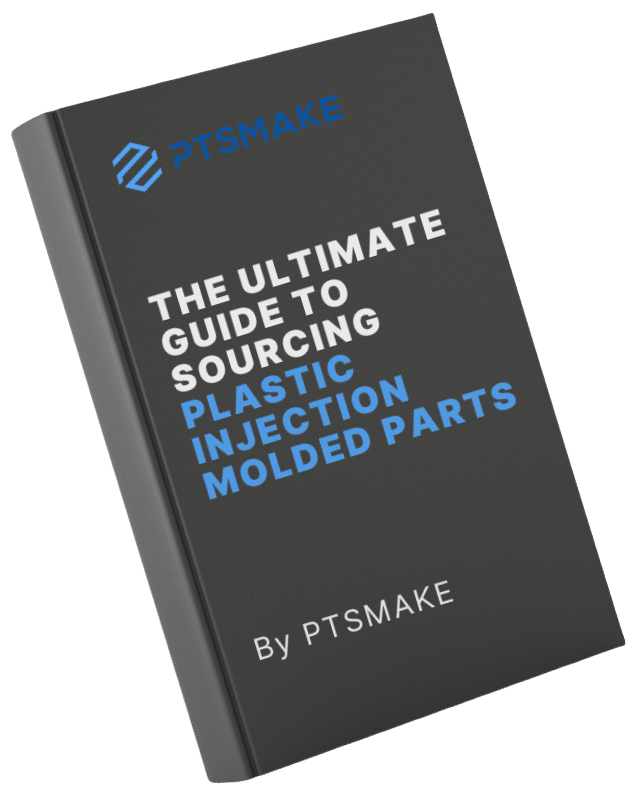
To save you time, we have also prepared a PDF version containing all the contents of this page, only leave your email and you will get the download link immediately.
Two-Shot Injection Molding Quality Control Process
At PTSMAKE, we understand the unique demands of Two-shot (2K) injection molding, where precision, material compatibility, and flawless execution are paramount. Our commitment to quality control ensures that every product we produce meets the highest standards and supports your business growth.
Quality Control Process
The complexity of the Two-shot molding process requires meticulous attention to every detail. Here’s how we ensure top-tier quality in every step of production:
- Raw Material Inspection: Two-shot injection molding involves the use of two different materials, each requiring its own precise set of standards, We inspect all materials before production to make sure they meet your specific requirements and are suitable for the Two-shot process.
- Continuous Production Monitoring: Every phase of Two-shot molding demands a high level of precision. We utilize advanced equipment to monitor the process in real-time, ensuring that each step — from initial injection to the second material being molded — is completed with accuracy and consistency.
- In-Process Multi-stage Inspections: Due to the complexity of the Two-shot molding process, we implement inspections at multiple stages of production. This allows us to identify and resolve any issues early, ensuring both the functional and aesthetic quality of the final product.
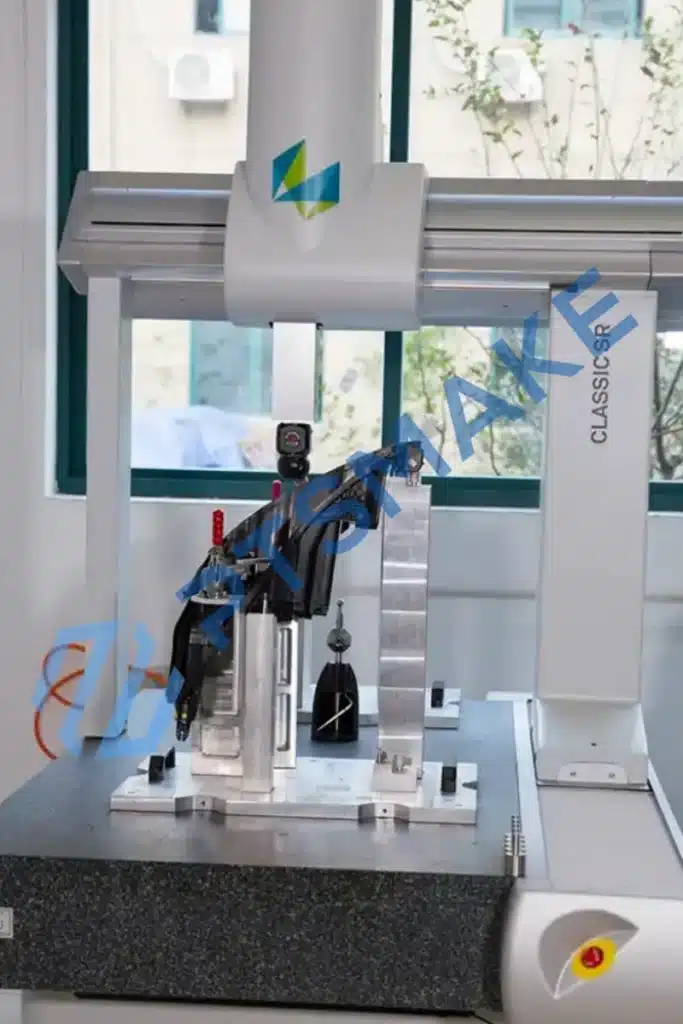
- Comprehensive Final Product Inspection: After production, we conduct a thorough inspection of each Two-shot molded product. This includes verifying that there are no defects, checking the integrity of the material bonds, and confirming that all dimensions and tolerances meet your exact specifications.
- Packaging and Shipping Inspections: With the delicate nature of Two-shot molded products, proper packaging is crucial to ensure safe delivery. Before shipping, we perform a final inspection to ensure that each product is securely packaged and ready for transit without any risk of damage.
- Expert Quality Control Team: Our dedicated quality control team is highly trained and understands the intricacies of the Two-shot molding process. They focus on the smallest details, ensuring that every product adheres to the highest quality standards and your specific requirements.
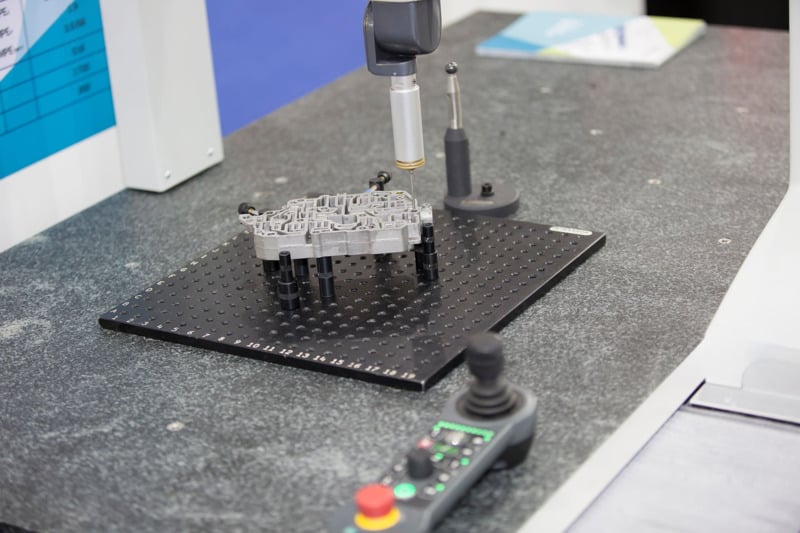
CMM
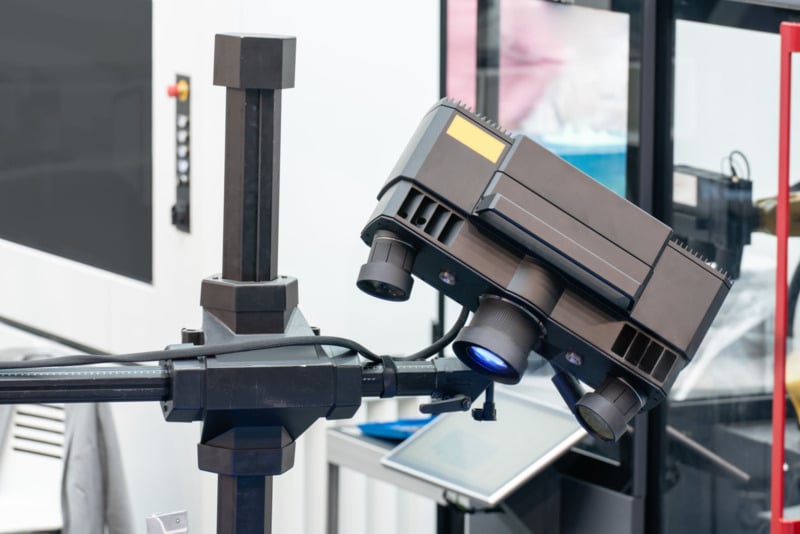
GOM 3D-Scanner
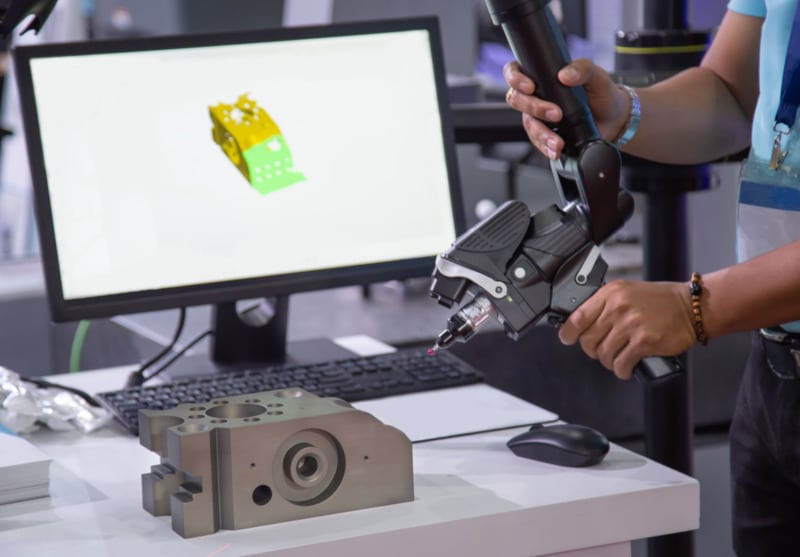
Portable CMM
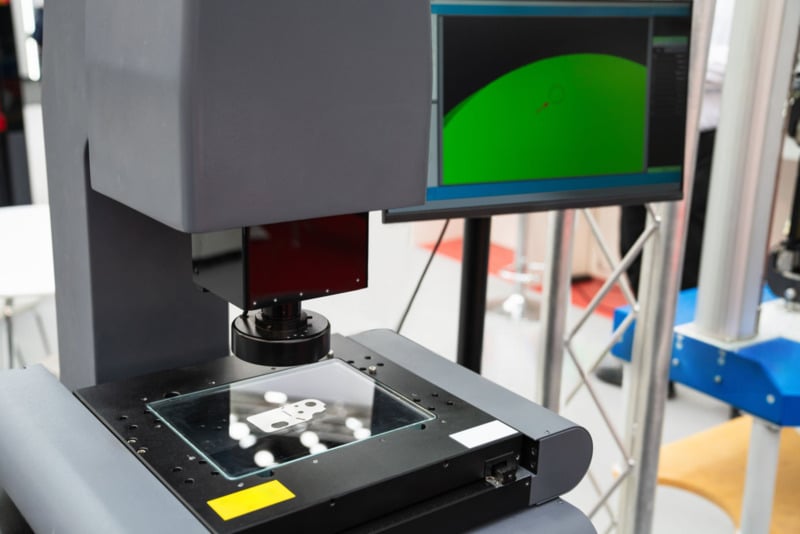
Projector
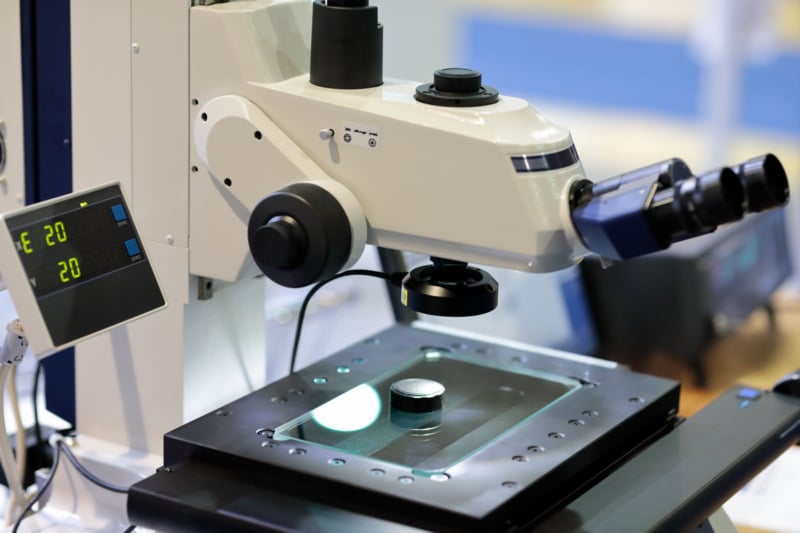
Optical microscope
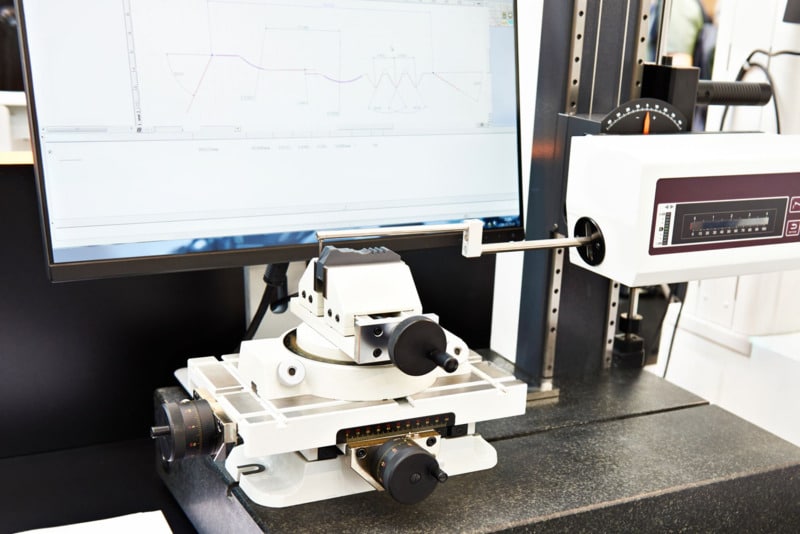
Roughness Tester
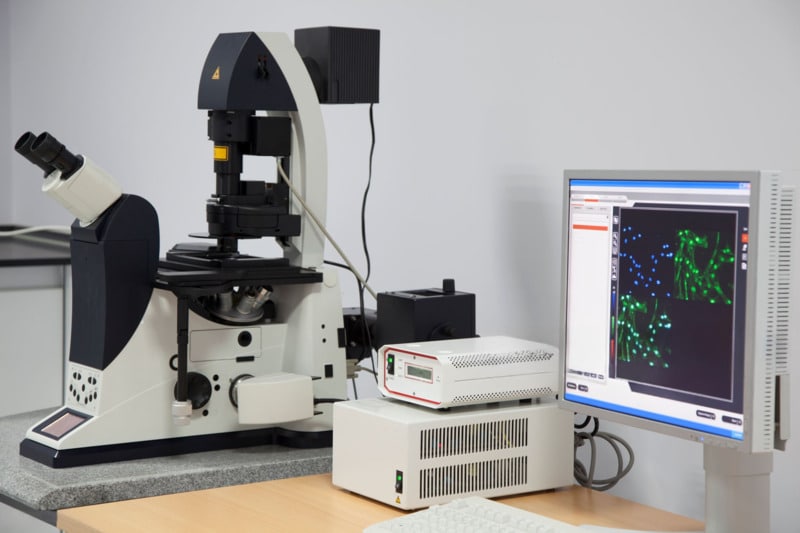
Raw material analyzer
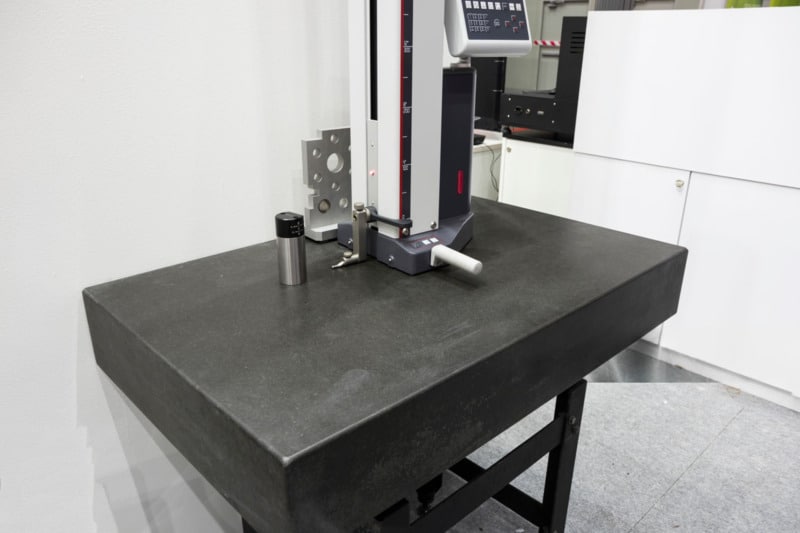
Altimeter
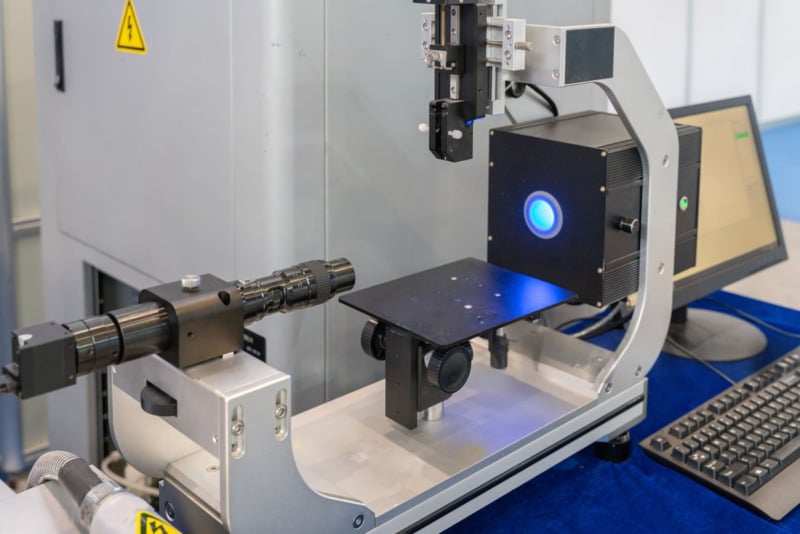
Laser Inspection
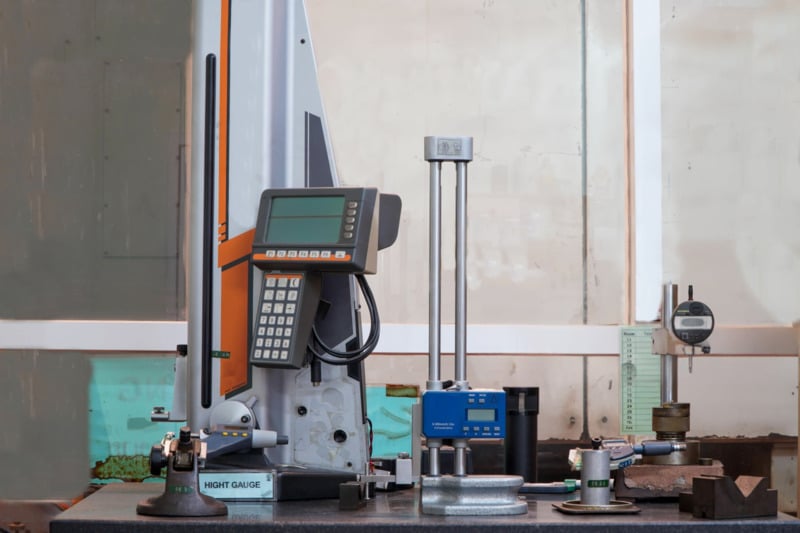
Others
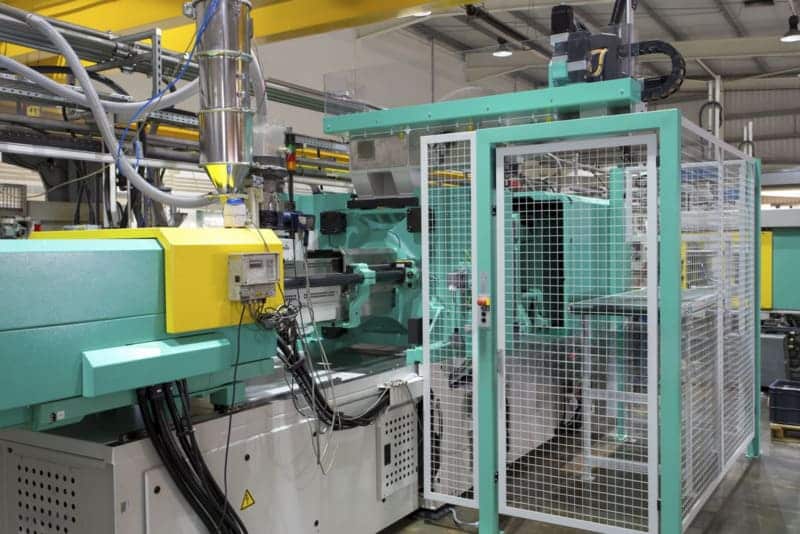
Injection Machine
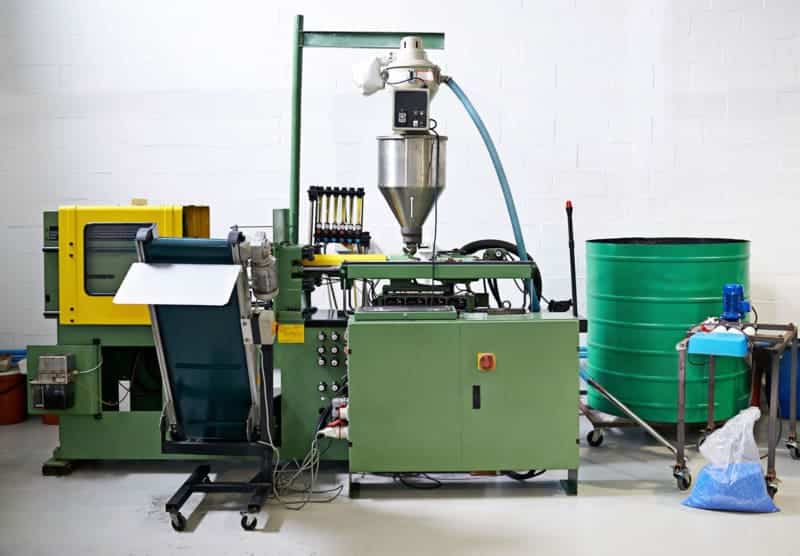
Vertical Injection Machine
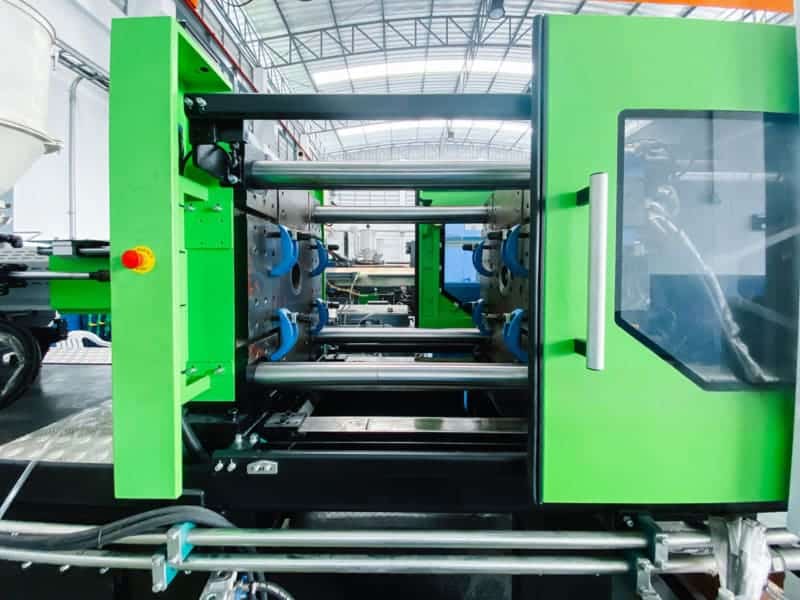
Double-shot Injection Machine
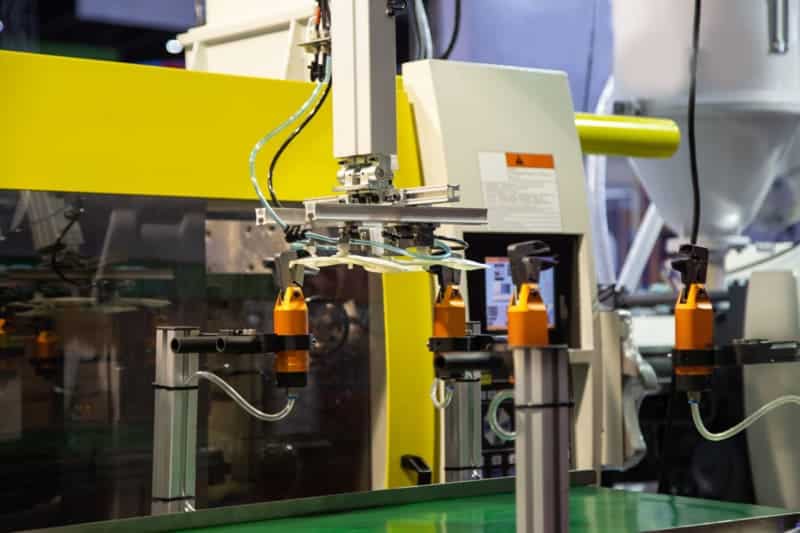
Robotic Arms for Automated Molding
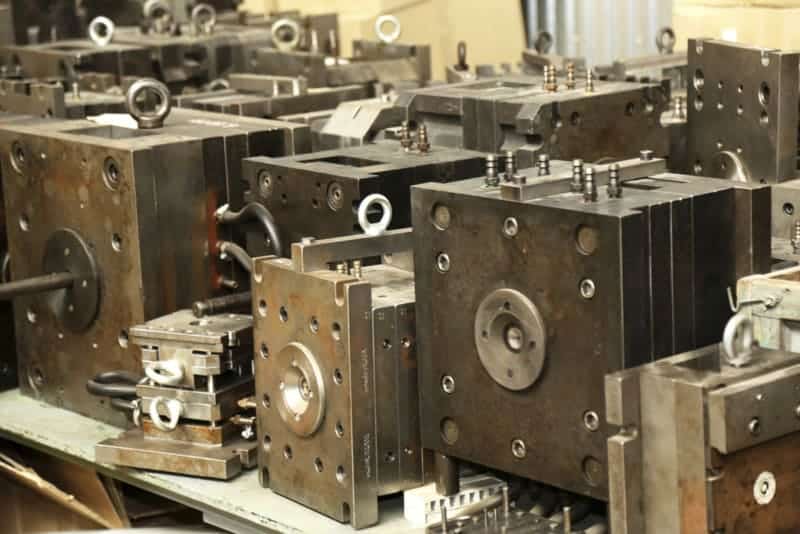
Various Plastic Injection Molds
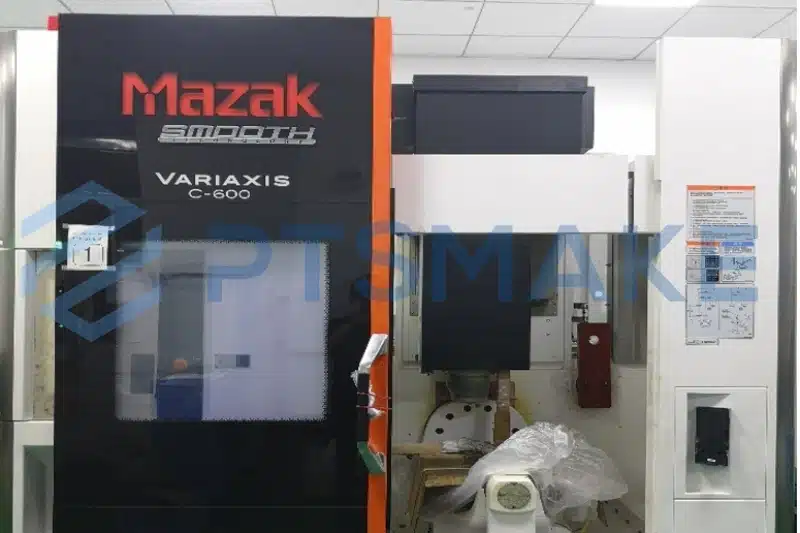
CNC Milling Machine(Japan)
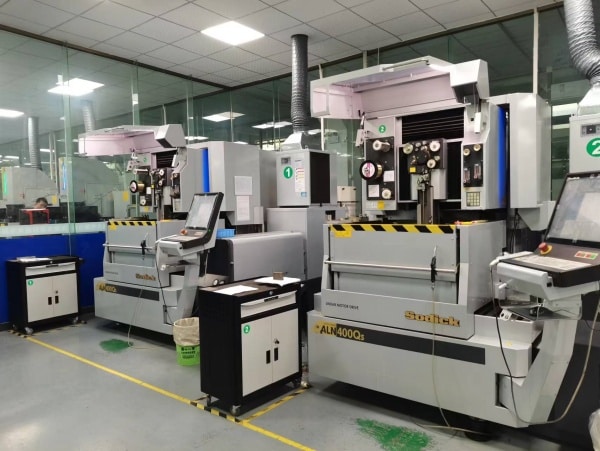
Slow Wire Cut (Japan)
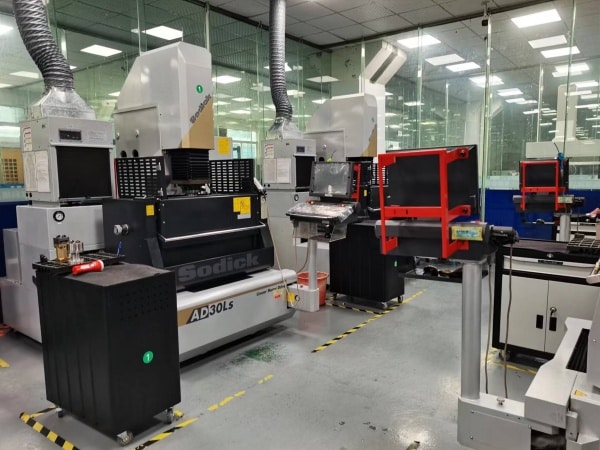
Electric Discharge Machining (Japan)
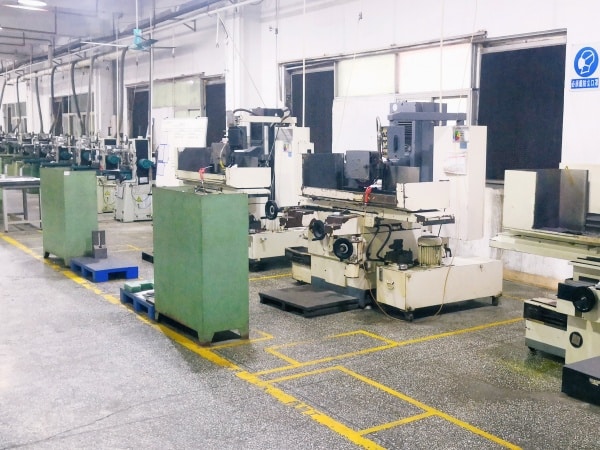
Precision Grinding Machine (Japan)
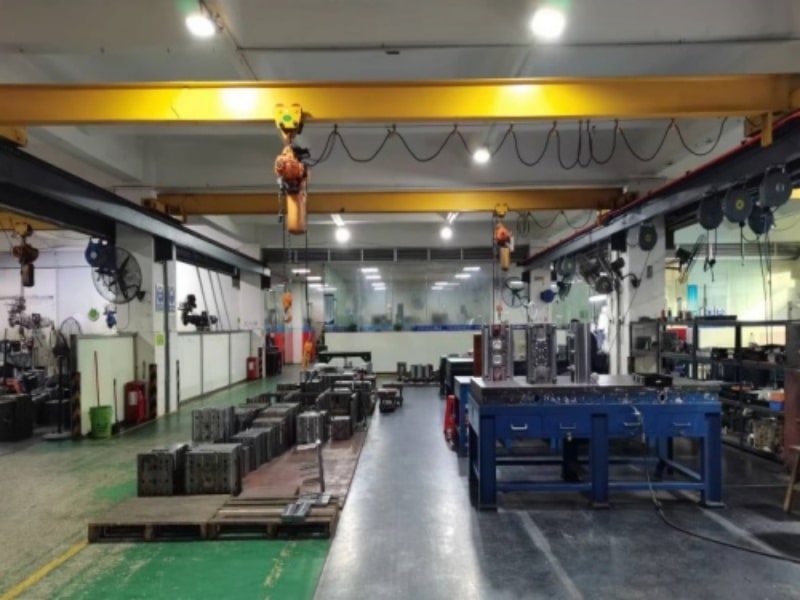
Mold Assembly
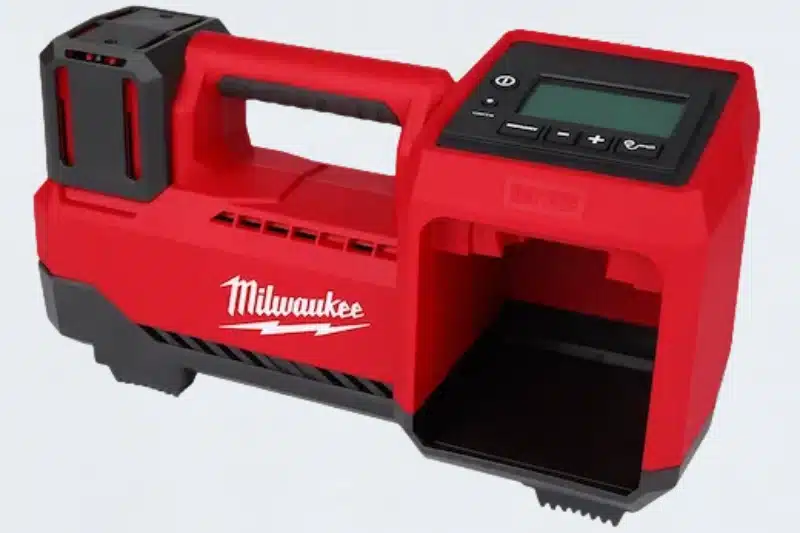
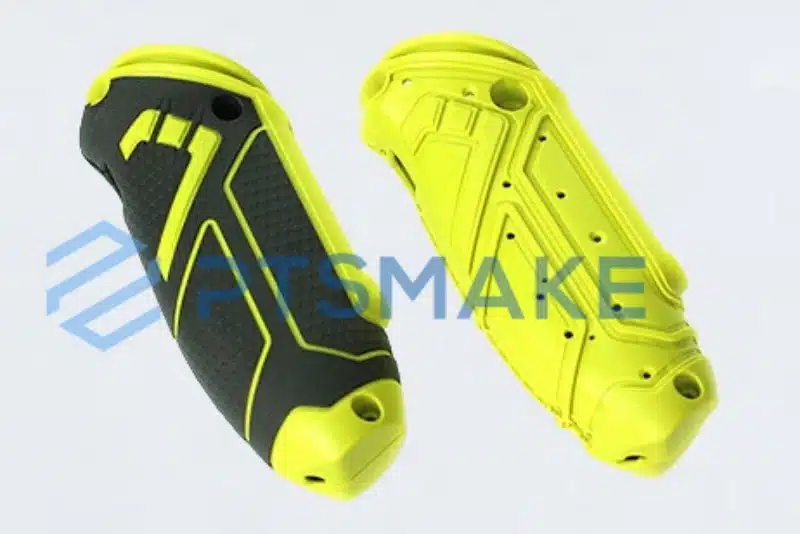
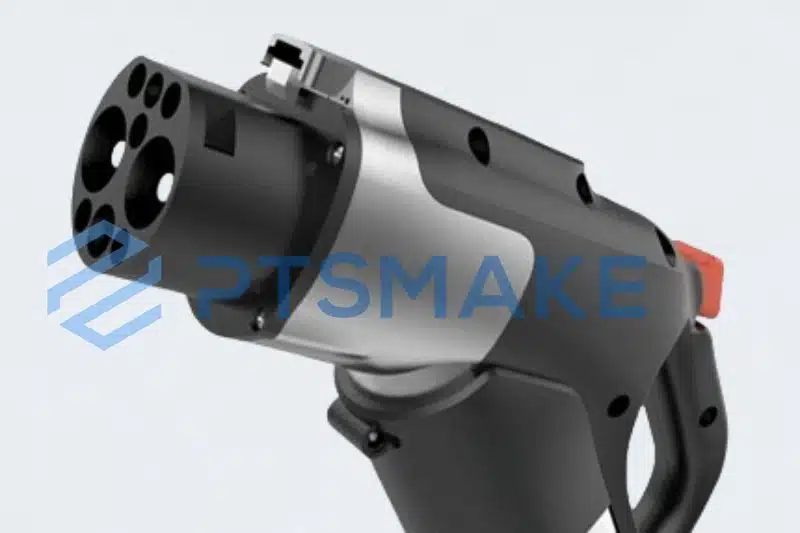
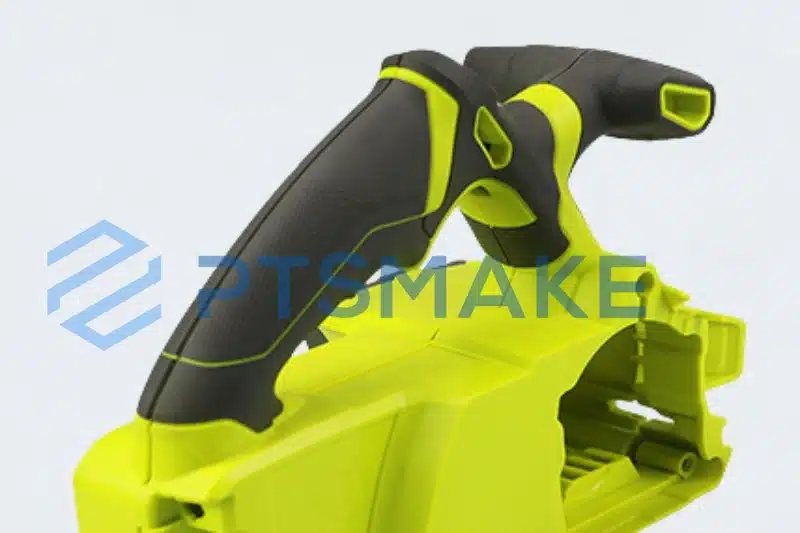
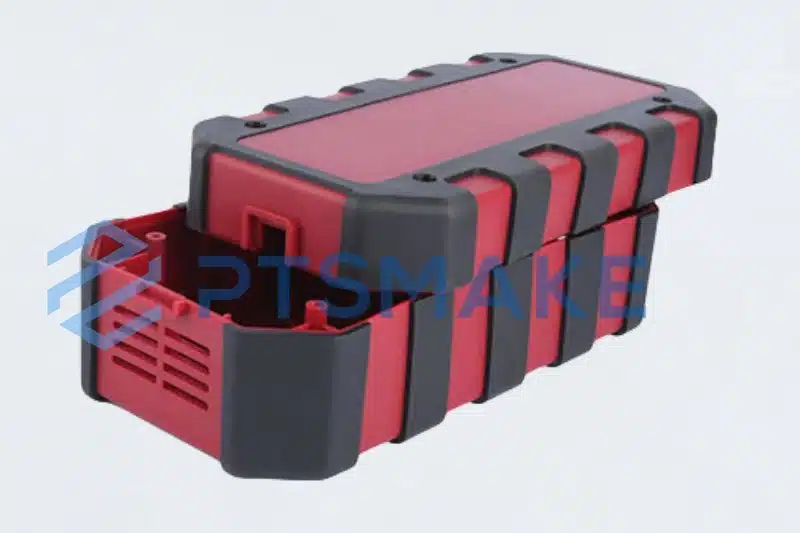
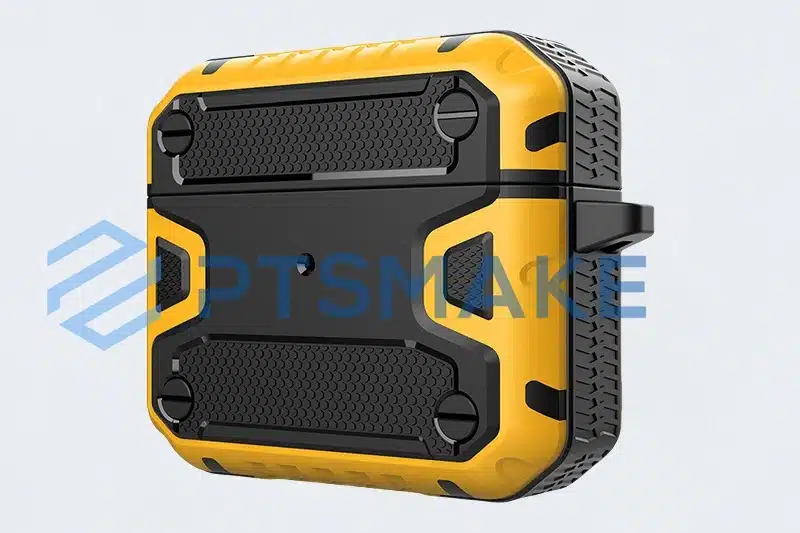
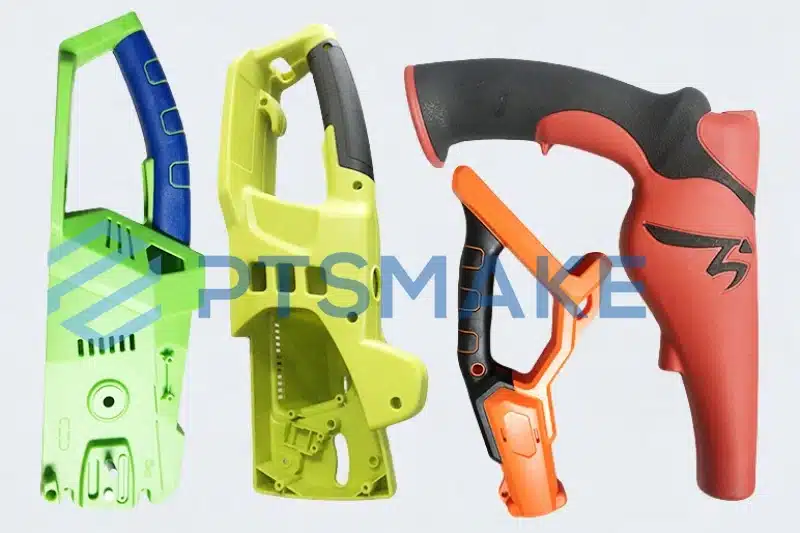
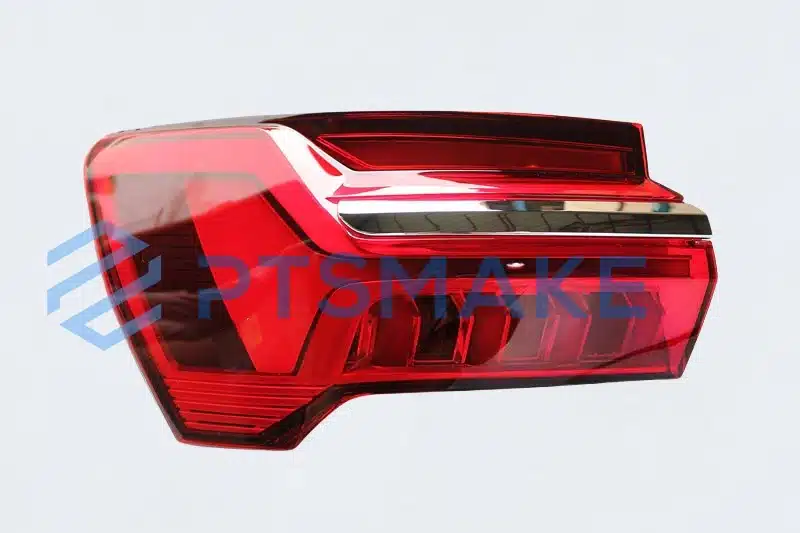
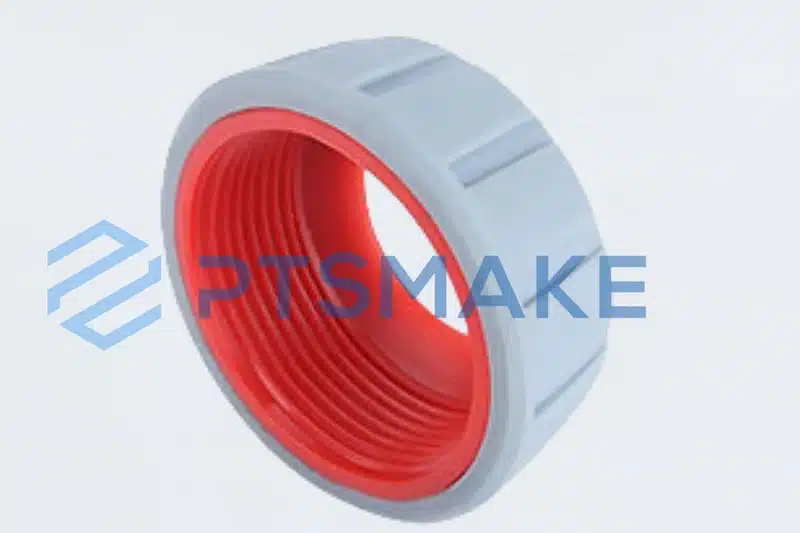
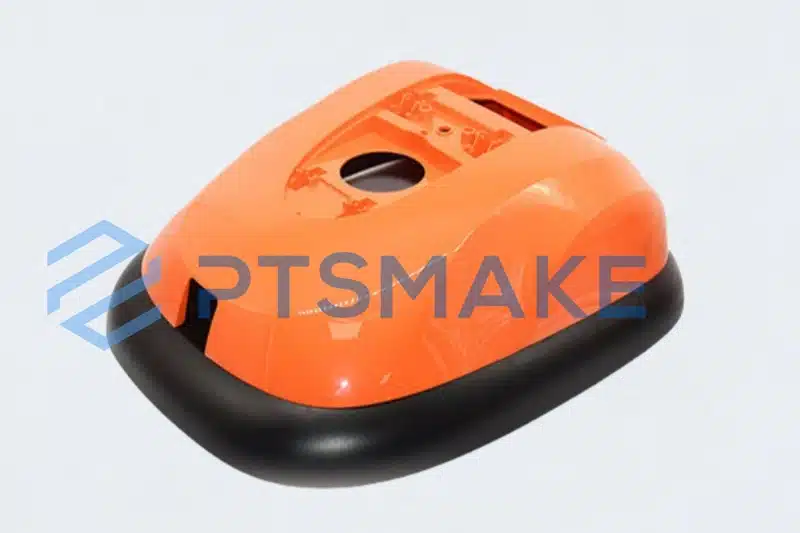
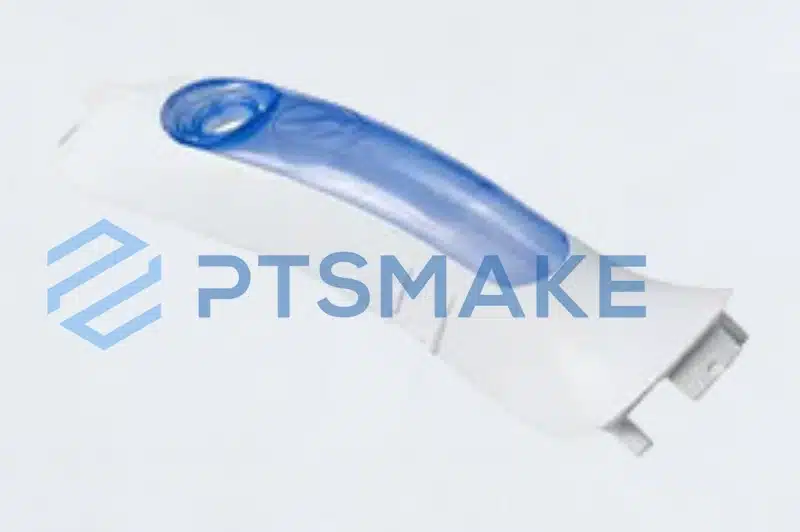
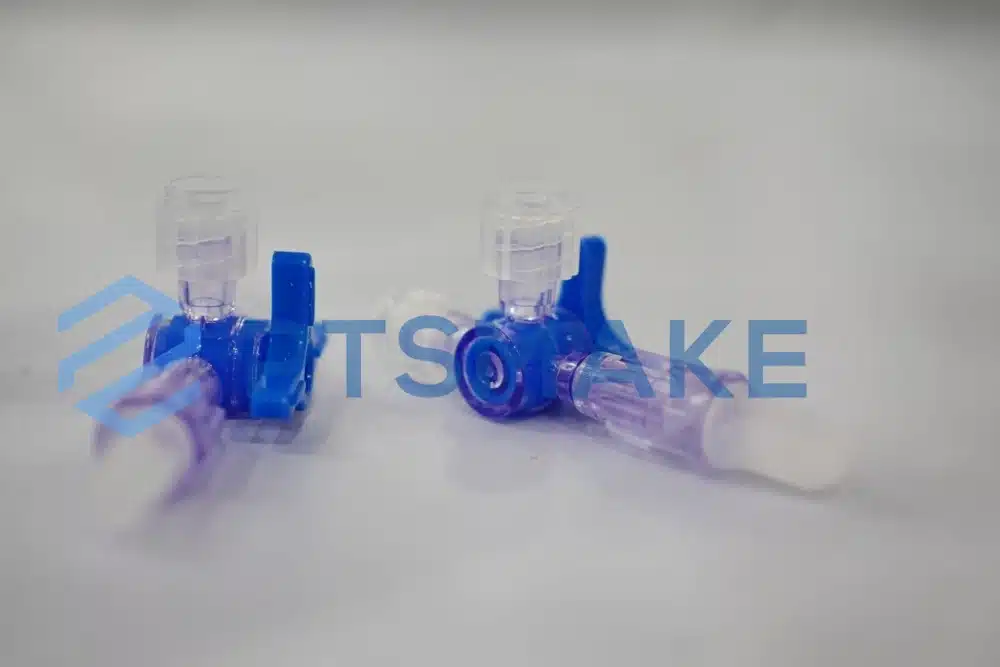
How to Choose the Right Two-Shot Injection Molding Supplier
Selecting a suitable two-shot (2K) injection molding supplier is crucial for the success of your projects. The supplier’s technical capabilities and experience directly affect the quality of your final products. We want to share insights on how to evaluate and select suppliers to ensure they meet high standards.
- Advanced Machinery: Check if the supplier uses modern two-shot injection molding machines. State-of-the-art equipment can handle complex designs and produce high-quality parts consistently.
- Skilled Personnel: Ensure the supplier has a team of experienced engineers and technicians. Their expertise is vital for optimizing the molding process and solving any issues that may arise.
- Material Knowledge: The supplier should have in-depth knowledge of materials. It’s important that they understand the compatibility of different materials used in the first and second shots.
- Mold Design and Manufacturing: Fully verify whether they have the ability to design and develop molds themselves, instead of outsourcing molds to other companies and only completing the injection molding process themselves.
- Internal Quality Control Processes: Examine their comprehensive quality control measures from raw material inspection to finished product delivery.
- Customer References: Request references from similar projects or industries to gauge the supplier’s reliability and performance.
- Case Studies: Review case studies of their past projects similar to yours. This helps you understand how they approach challenges and their ability to deliver quality results.
- Evaluate Supplier Network and Supply Chain Reliability: A well-connected supplier network ensures consistent access to quality materials and reliable production capabilities, minimizing supply chain disruptions.
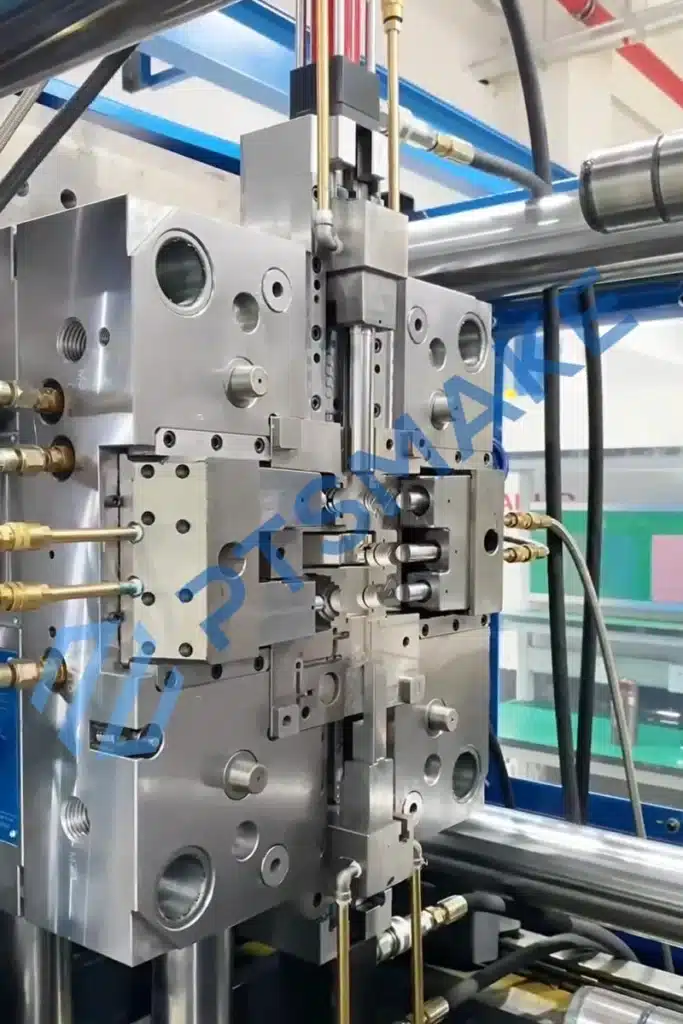
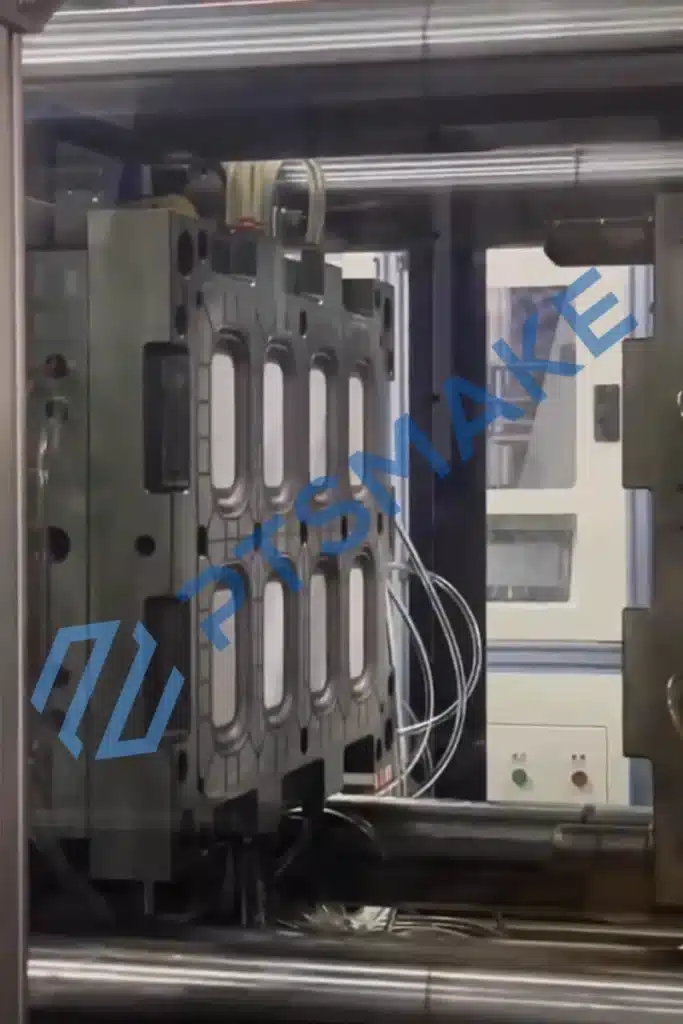
- Analyze Cost Considerations: While price is important, prioritize suppliers who offer quality, precision, and reliability over those with the lowest costs. Ensure that all potential costs, including tooling, materials, production, labor, and shipping, are clearly outlined.
- Transparency: Choose suppliers who are responsive, clear, and transparent in their communications regarding pricing, lead times, and terms of service.
- Sample Assessment: Before committing to large orders, request samples to evaluate the quality and accuracy of the supplier’s parts, ensuring they meet your standards.
- Timely Delivery: Confirm that the supplier has a strong track record of meeting deadlines to prevent delays in your project schedule.
- Communication: Effective communication is vital; choose a supplier that communicates clearly and responsively, In particular, sales have their own technical and design capabilities.
- Customer Service: Good customer support indicates the supplier’s dedication to addressing your concerns and providing timely solutions.
- Growth Capacity: Choose suppliers capable of scaling their production as your business grows.
- Upfront Information: The supplier should provide clear and transparent information about pricing, lead times, and service terms without hidden fees.
What Sets Us Apart
With over two decades in the industry, we bring a wealth of knowledge to every project.
We invest in the latest technology to provide superior services.
We offer high-quality services at competitive rates.
Although based in China, we serve clients around the world.
We once faced a challenge when a client requested a complex two-shot plastic part with high precision and durability. We chose PTSMAKE as our supplier, and they not only understood our requirements but also quickly adjusted the molds and carried out precise two-shot injection molding. The delivery was on time, and every part fit perfectly into our production line with excellent quality. Since then, PTSMAKE has become our long-term partner for two-shot injection molding. Their professionalism and reliability allow us to focus on improving our products, saving us significant hassle.
— Sarah, Engineering Manager
2k Injection Molding Capabilities
We specialize in advanced 2k injection molding solutions, including Two-Color, Two-Material, Two-Component, and Two-Shot Injection Molding. Our expertise allows us to create complex, high-quality products with multiple materials or colors, improving functionality, design flexibility, and durability. Trust us to deliver precise, cost-effective, and innovative solutions for your needs.
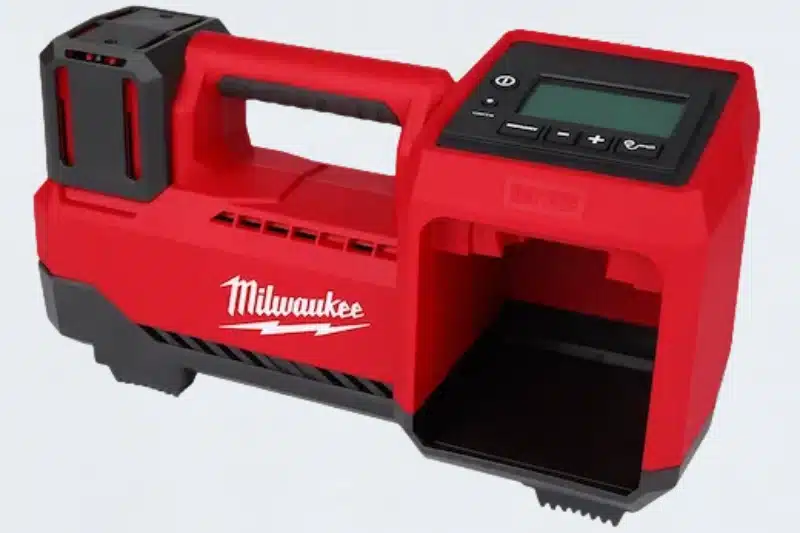
Two-Color Injection Molding
Injecting two different colored plastics to create a two-tone effect.
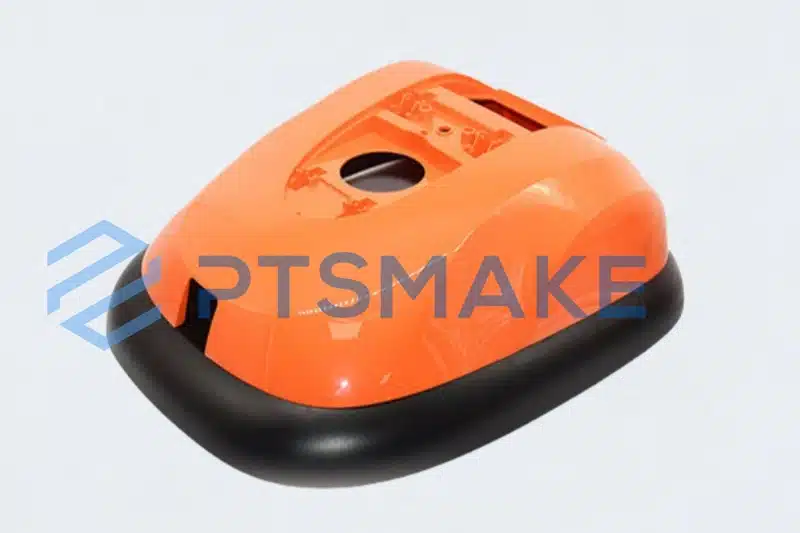
Two-Material Injection Molding
Injecting two different materials (e.g., hard and soft plastics) for functional or aesthetic combinations.
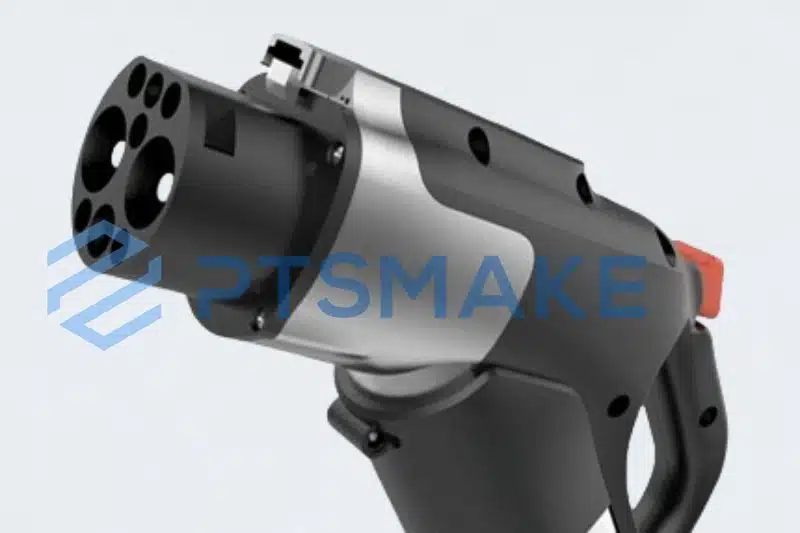
Two-Component Injection Molding
Using two different types of materials (e.g., plastic and metal) in one injection molding process.
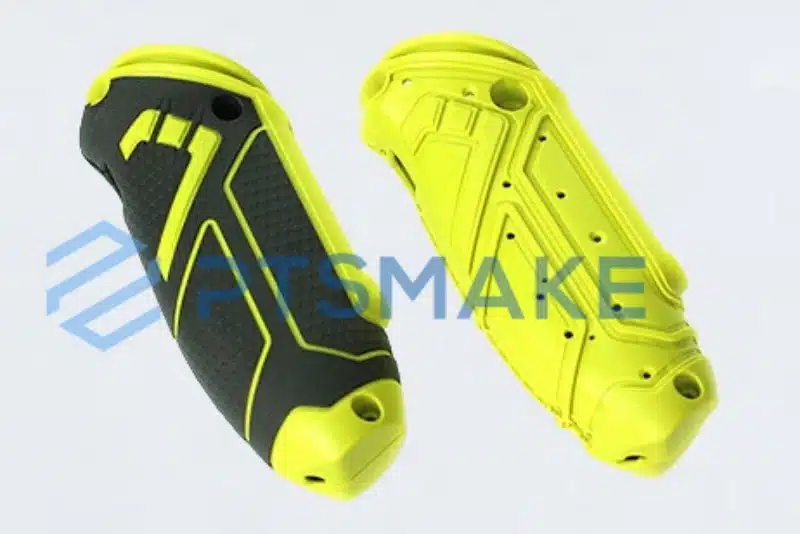
Two-Shot Injection Molding
Two injection cycles with different materials or colors, typically for enhanced functionality or appearance.
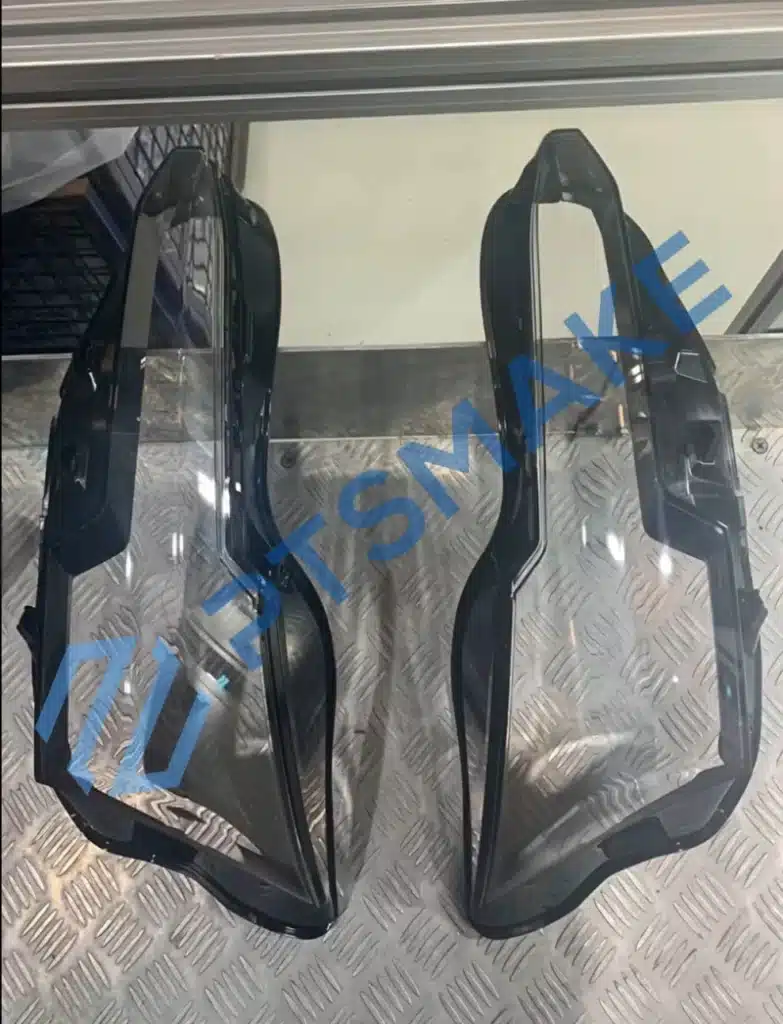
Common Materials in Two-Shot (2K) Injection Molding
First Shot Materials: The first shot typically forms the structural base of the part.
- Polycarbonate (PC): Offers high impact resistance and clarity. Used in applications requiring durability and transparency.
- Acrylonitrile Butadiene Styrene (ABS): Provides toughness and good dimensional stability. Suitable for parts needing rigidity and strength.
- Polypropylene (PP): Known for flexibility and chemical resistance. Ideal for components exposed to chemicals.
- Polyamide (Nylon): Has excellent mechanical properties and wear resistance. Used in high-stress applications.
Requirements:
- Structural Integrity: Must provide strength and support.
- Thermal Stability: Should withstand the processing temperature of the second shot without deforming.
- Bonding Compatibility: Must adhere well to the second shot material.
Second Shot Materials: The second shot often adds functionality or aesthetics.
- Thermoplastic Elastomers (TPE): Provide a soft-touch feel and improved grip. Used in handles and grips.
- Thermoplastic Polyurethane (TPU): Offers flexibility and abrasion resistance. Ideal for protective covers.
- Silicone Rubber: Provides high elasticity and temperature resistance. Used in seals and gaskets.
- Acrylics (PMMA): Offers clarity and UV resistance. Suitable for decorative elements.
Requirements:
- Adhesion: Must bond effectively with the first shot material.
- Desired Properties: Should impart the required flexibility, texture, or aesthetic appeal.
- Processing Compatibility: Must process at a temperature that doesn’t damage the first shot.
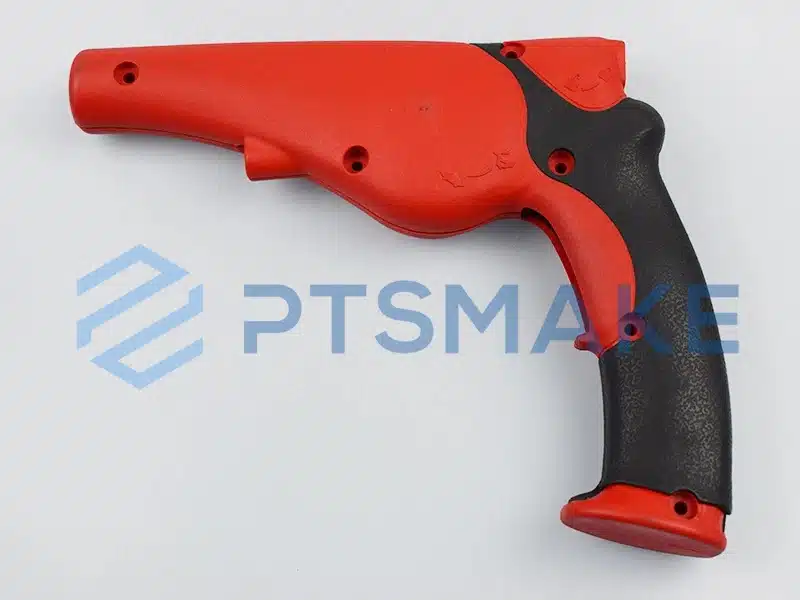
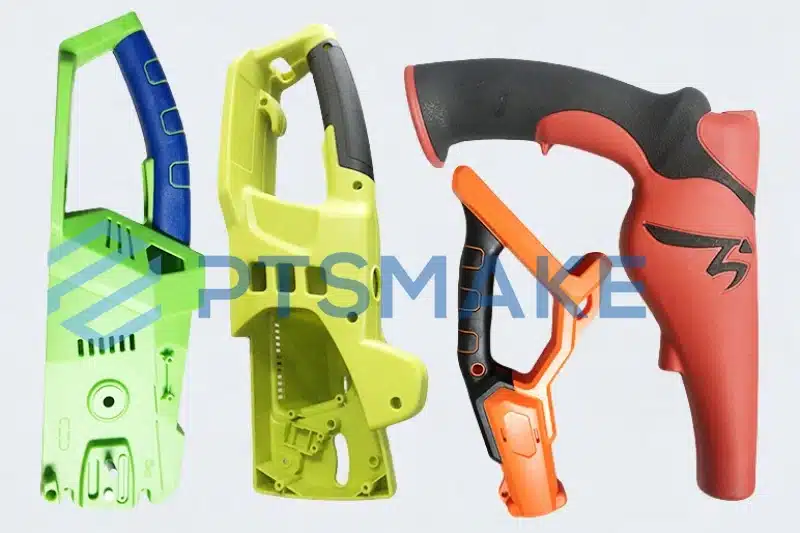
Ensuring Material Compatibility: We take several steps to ensure materials work well together.
- Chemical Compatibility Testing: We conduct tests to assess the bonding between materials.
- Matching Thermal Properties: We select materials with similar thermal characteristics to prevent stress and deformation.
- Shrinkage Rates: We consider materials with compatible shrinkage rates to maintain dimensional accuracy.
- Material Selection: Choose materials with similar properties (e.g., melt temperature, flowability, shrinkage rate) for good bonding. Common pairs include PP and PE, PC and PET, or TPU and ABS.
By carefully selecting materials, optimizing processing parameters, and testing for adhesion, material compatibility in two-shot injection molding can be ensured.
Not sure which material is best for your project? Our engineers are here to help you choose the right material that meets your performance, durability, and cost requirements.
Common Challenges in Two-Shot Injection Molding
Two-shot injection molding combines two different materials into a single, cohesive part. While this process offers many advantages, it also presents unique challenges. Understanding these challenges helps us anticipate issues and implement effective solutions. Here are nine common challenges in two-shot injection molding and how we address them.
- Challenge: Incompatible materials can lead to poor bonding between the two shots. This can result in weak joints, delamination, or part failure.
- Solution: We carefully select materials with compatible chemical and thermal properties. We conduct thorough material testing and bonding trials to ensure strong adhesion between the two materials. By working closely with material suppliers, we identify optimal material pairs that bond well and meet the product’s performance requirements.
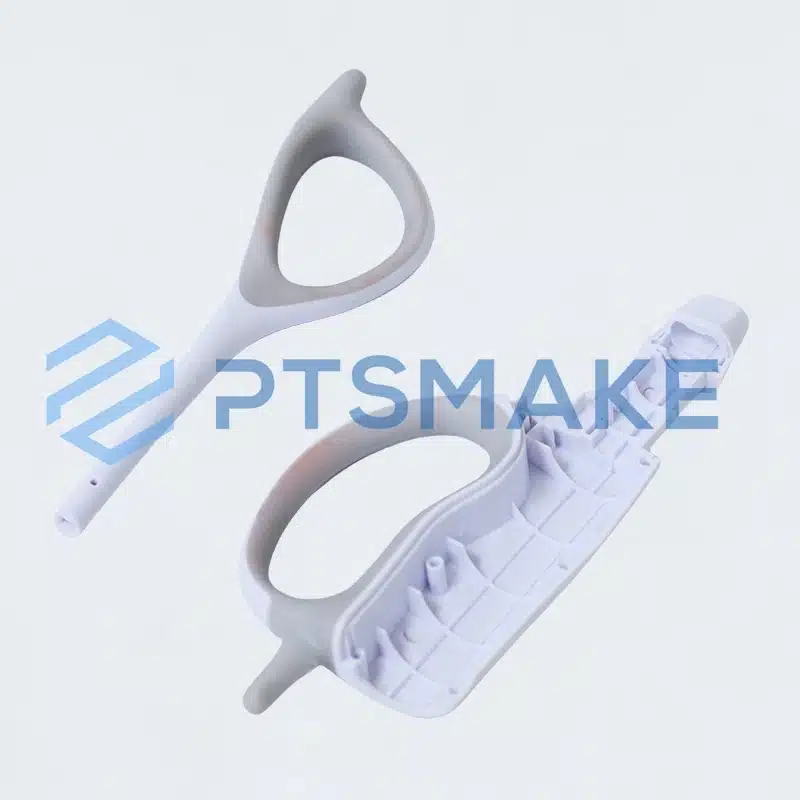
- Challenge: Designing molds for two-shot molding is more intricate than for single-shot processes. The mold must accommodate two different materials and ensure precise alignment and injection sequences.
- Solution: Our experienced engineers use advanced computer-aided design (CAD) software to create precise mold designs. We employ mold flow simulations to predict and optimize the filling process, identify potential defects, and adjust the design accordingly. This proactive approach helps us produce high-quality molds that perform reliably during production.
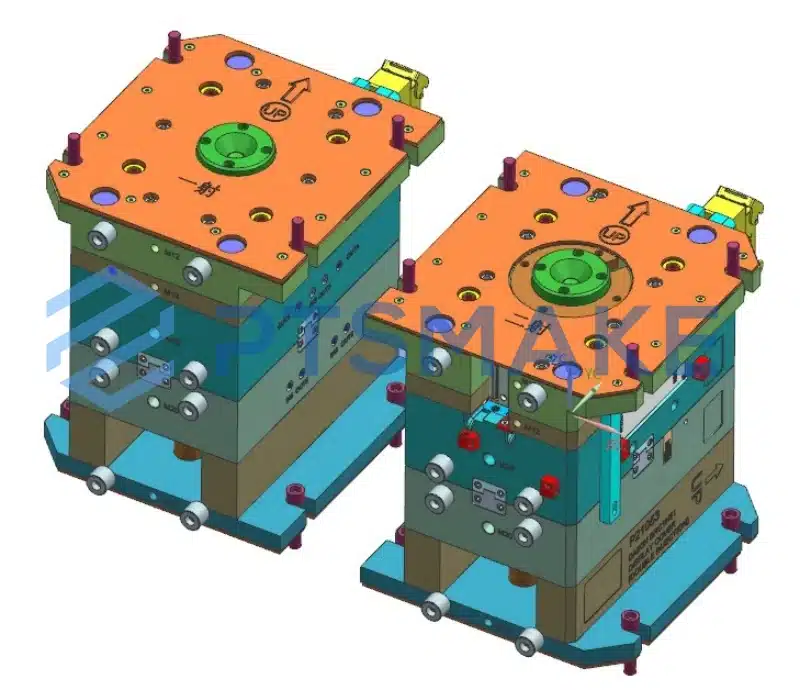
- Challenge: Misalignment between the first and second shots can lead to defective parts. Misaligned components may not fit together properly, affecting the part’s functionality and appearance.
- Solution: We utilize high-precision molding machines equipped with advanced positioning systems. Our machines ensure exact alignment between the two shots. Additionally, we incorporate alignment features into the mold design, such as guide pins and interlocks, to maintain proper positioning throughout the molding process.
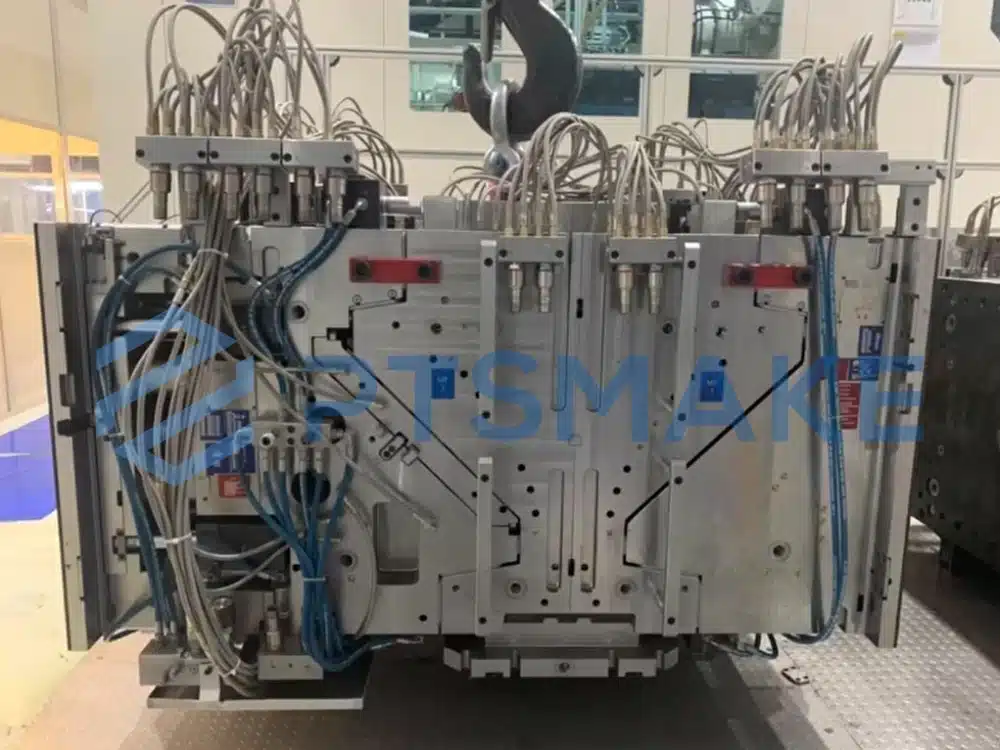
- Challenge: The two materials used may have different melting temperatures and thermal properties. Incorrect thermal settings can cause material degradation or poor bonding.
- Solution: We develop detailed thermal profiles for each material. By carefully controlling the temperature of the molds and the injection units, we ensure that each material is processed at its optimal temperature. We also design the cooling systems within the molds to manage heat transfer effectively, preventing overheating or uneven cooling.
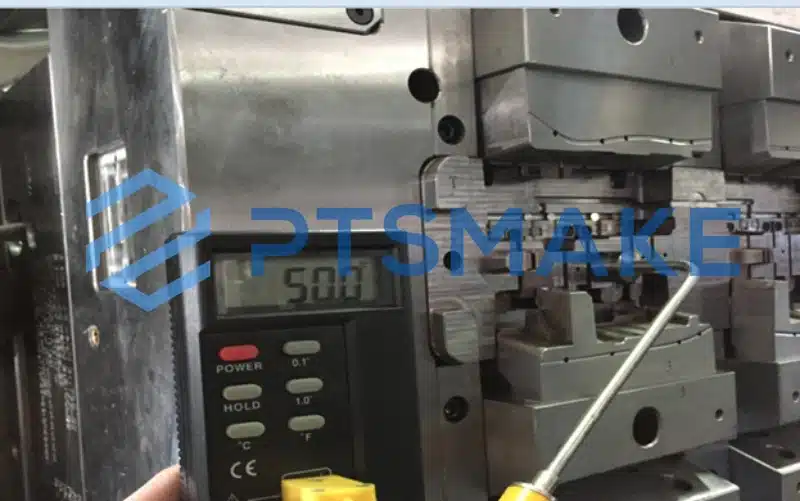
- Challenge: Two-shot molding can have longer cycle times due to the additional injection step and complexity of the process. Extended cycle times increase production costs and affect efficiency.
- Solution: We optimize process parameters to minimize cycle times without compromising quality. This includes fine-tuning injection speeds, pressures, and cooling times. We also use efficient cooling systems and consider mold materials with high thermal conductivity to reduce cooling durations.
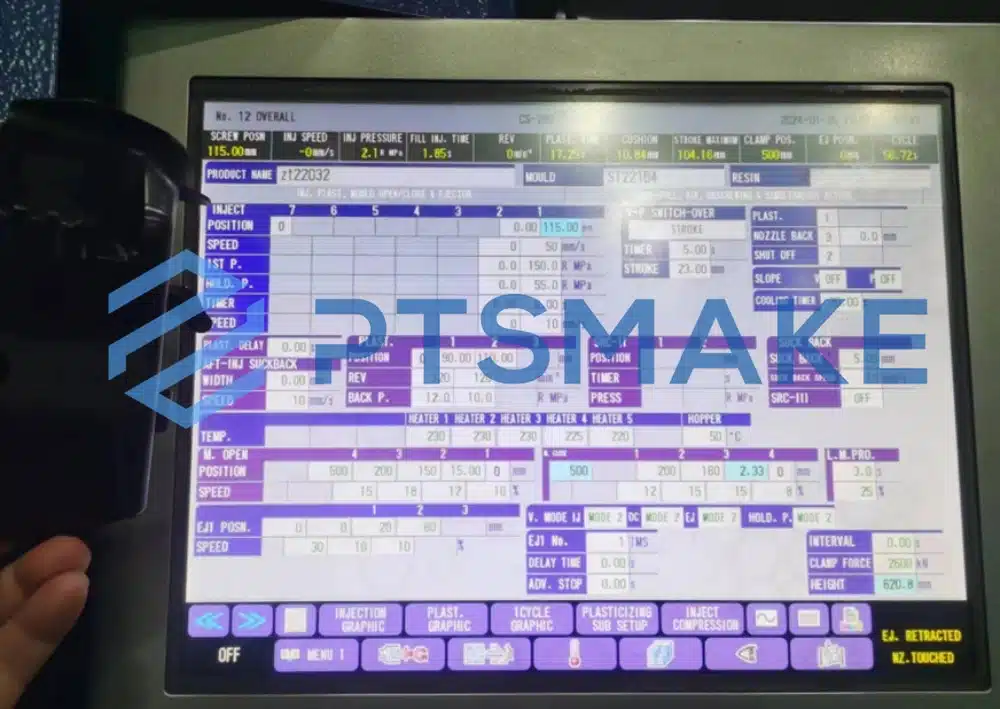
- Challenge: Different materials may have varying shrinkage rates during cooling. This can cause warping, dimensional inaccuracies, or internal stresses in the final part.
- Solution: We select materials with similar shrinkage rates when possible. If different shrinkage rates are unavoidable, we adjust the mold design to compensate for these differences. This may involve strategically placing gates and runners or modifying the cavity dimensions. We also conduct shrinkage analysis during the design phase to predict and mitigate potential issues.
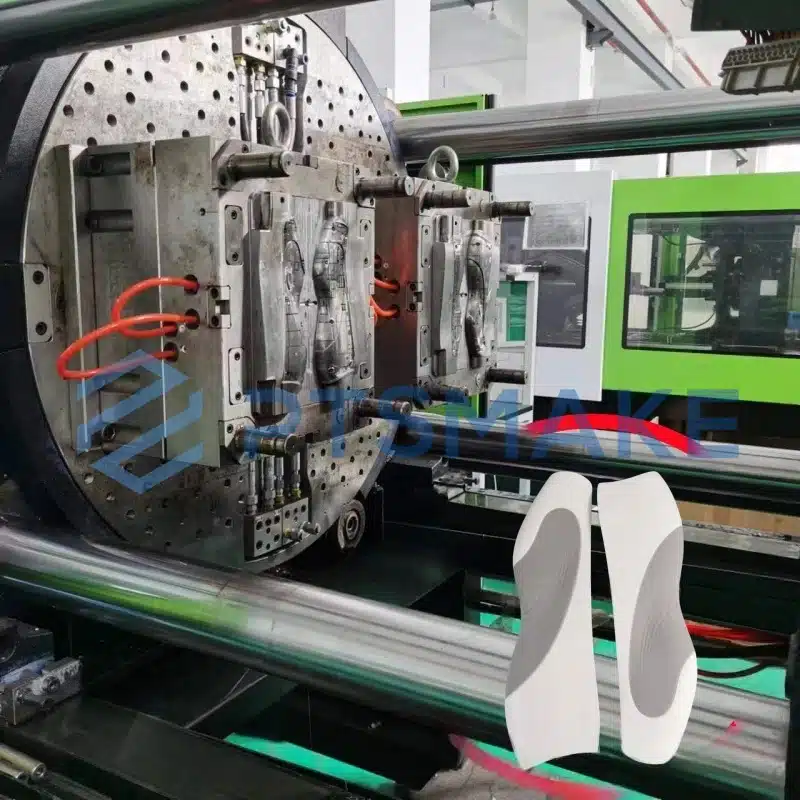
- Challenge: Excess material, or flash, can form at the parting lines of the mold during injection. Flash can affect the part’s appearance and require additional post-processing.
- Solution: We maintain precise control over mold clamping forces and injection pressures to prevent flash. Our molds are designed with tight tolerances and effective sealing at the parting lines. Regular maintenance and inspection of molds ensure that all surfaces fit together properly, minimizing the risk of flash formation.
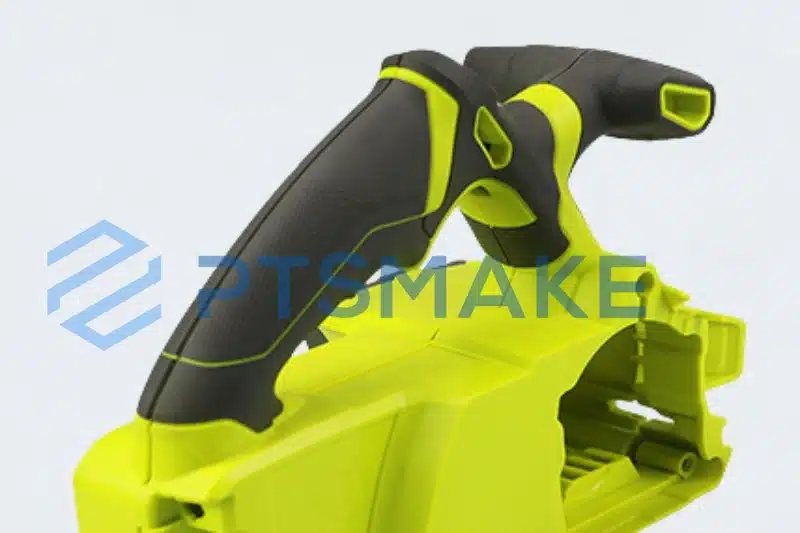
- Challenge: The complexity of two-shot molding equipment can lead to increased wear and maintenance requirements. Equipment downtime can disrupt production schedules.
- Solution: We implement a rigorous preventive maintenance program for all our molding machines and molds. Regular inspections and servicing help us identify and address wear before it leads to equipment failure. We keep critical spare parts in stock to minimize downtime in case of unexpected issues.
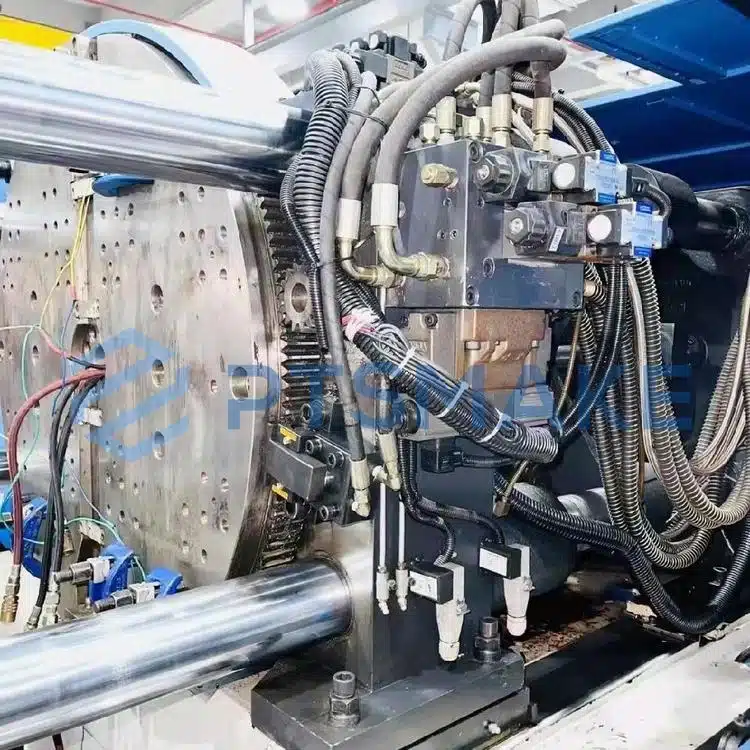
- Challenge: The initial investment for two-shot molding is higher due to complex molds and specialized equipment. Managing costs while maintaining quality can be challenging.
- Solution: We conduct thorough cost analyses during the project planning phase. By optimizing the mold design and production process, we aim to reduce material usage and cycle times, leading to lower unit costs. We also consider the total cost of ownership, factoring in the benefits of improved part quality, reduced assembly times, and enhanced product performance that two-shot molding provides.
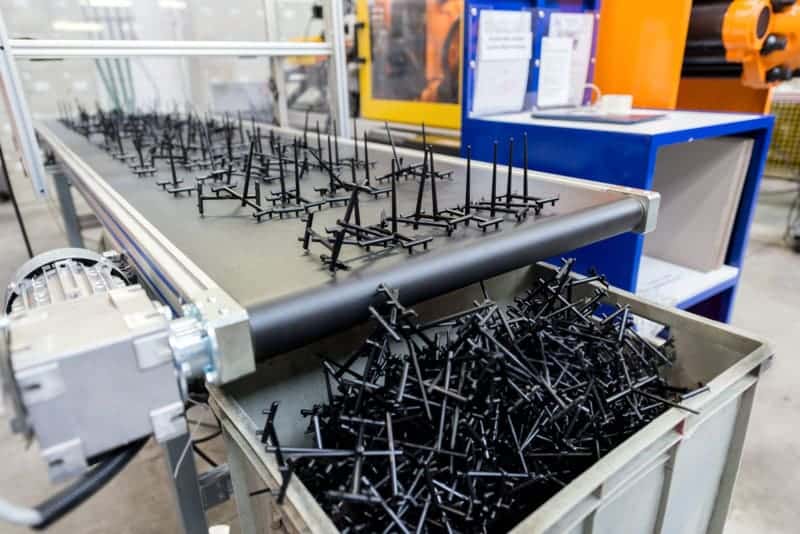
Request a Custom Quote Today
Get an accurate estimate for your injection molding project. Let us help you meet your exact specifications.
Cost of Two-Shot (2K) Injection Molding
Understanding the cost factors involved in two-shot (2K) injection molding is essential for effective budgeting and cost management. We recognize that two-shot molding offers many advantages, but it can also introduce complexities that impact the overall cost. In this section, we delve into the various cost components and provide insights on how to manage and reduce expenses without compromising quality.
Raw Material Costs
Material costs are a variable expense that depends on the type and amount of materials used.
- Material Selection: Engineering-grade plastics with specialized properties (e.g., heat resistance, strength) are more expensive.
- Volume Purchasing: Buying in larger quantities can reduce the cost per unit but may require higher upfront investment.
- Functional Additives: UV stabilizers, flame retardants, and impact modifiers enhance performance but add to costs.
- Colorants: Custom colors or effects require pigments or dyes. Multi-colored parts in two-shot molding may need specific colorants for each material.
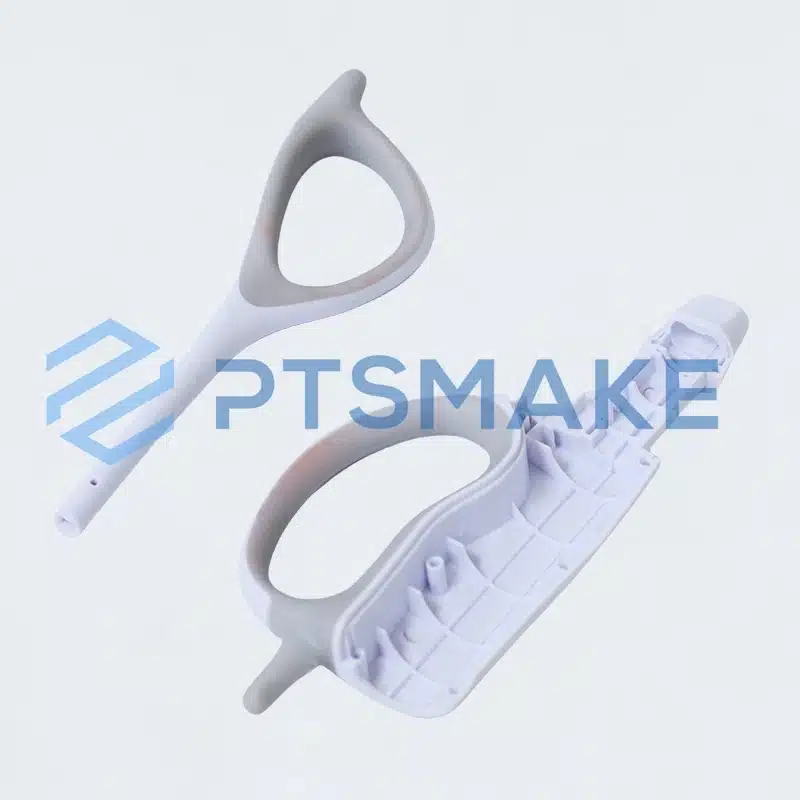
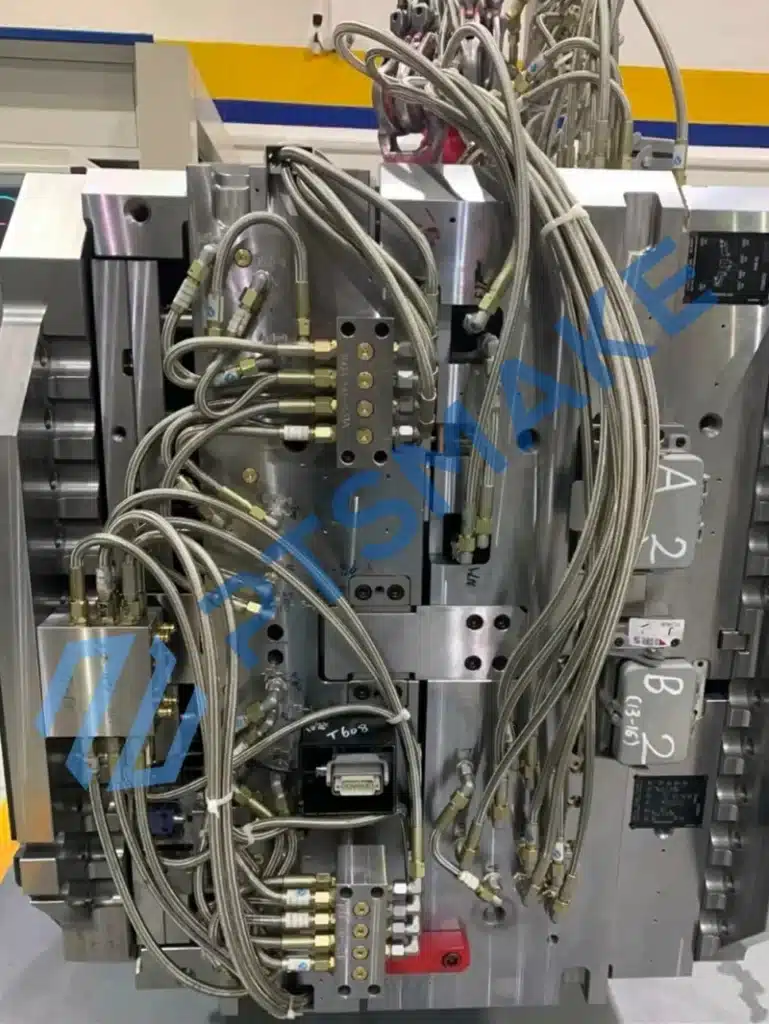
Mold Costs
Mold costs are a significant portion of the initial investment in two-shot injection molding. They encompass the design, manufacturing, and maintenance of molds, which are more intricate in two-shot processes.
- Complex Engineering: Two-shot molds require precise engineering to accommodate two different materials injected sequentially or simultaneously. This involves multiple cavities, intricate runner systems, and gating mechanisms for each material.
- Precision and Accuracy: The molds must align perfectly to ensure proper bonding and prevent defects such as flashing or misalignment. Any errors in design can lead to costly rework or defective products.
- Mold Materials: High-quality materials increase mold life but add to initial costs.
- Surface Treatments: Applying treatments such as nitriding or hard-coating can enhance mold hardness and extend its life but add to the initial cost.
- Precision Machining: CNC machines, EDM (Electrical Discharge Machining), and high-speed milling are used to achieve the required precision. These processes are time-consuming and costly.
- Skilled Labor: Experienced mold makers are essential. Their expertise ensures the mold meets exact specifications but comes at a higher labor cost.
Production and Processing Costs
Production costs include expenses incurred during the manufacturing process, such as cycle times, labor, and energy consumption.
- Longer Cycles in Two-Shot Molding: Coordinating two materials and additional injection steps extend the cycle time. Longer cycle times mean fewer parts are produced per hour, increasing the cost per part.
- Tooling & Setup: Setting up machines, adjusting molds, and running test batches all take time and are factored into the production cost. Setting up two-shot molds is more complex, requiring experienced technicians. For high-volume orders, we can optimize production schedules to minimize setup time and reduce costs.
- Post-Processing: Processes like painting, coating, or plating improve aesthetics or performance but increase costs. If the molded part is part of a larger assembly, additional assembly labor may be needed.
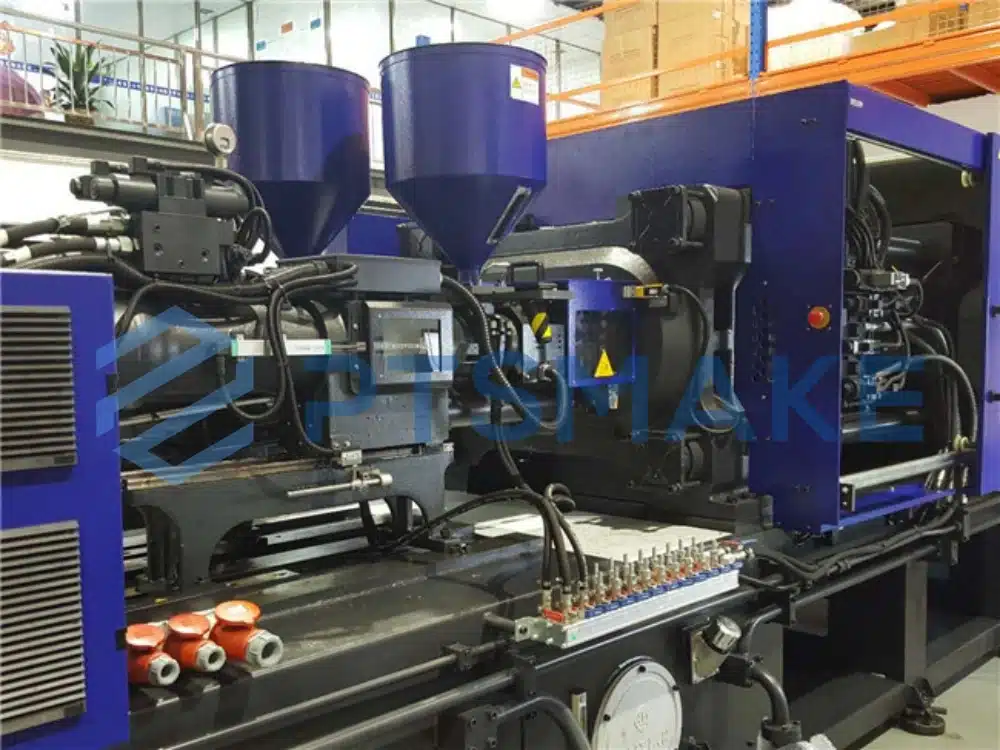
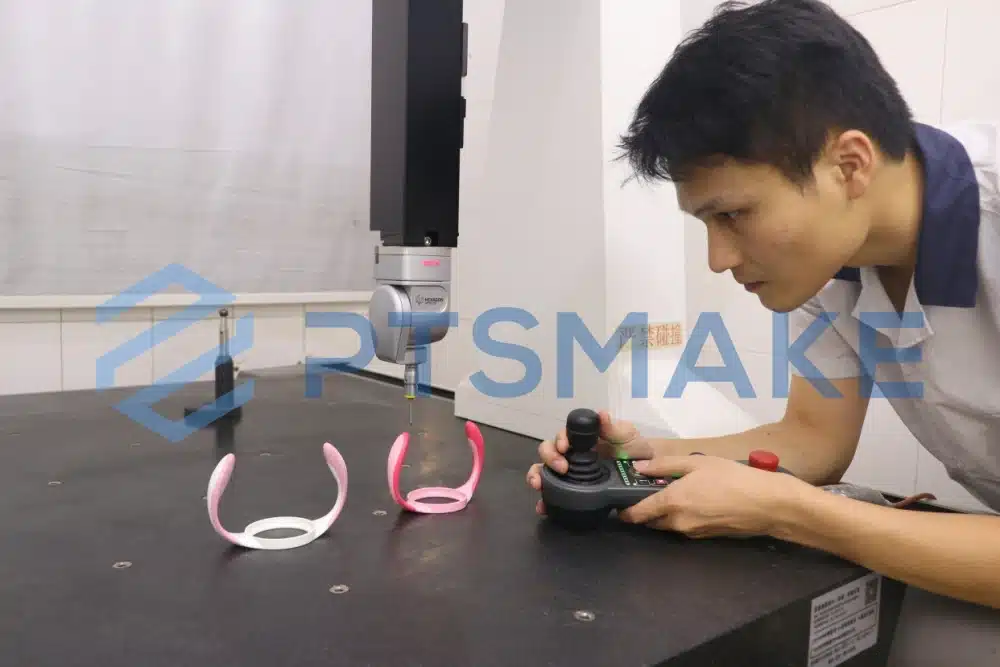
Labor Costs
Skilled labor is crucial for operating two-shot molding machines and ensuring quality.
- Monitoring and Maintenance: Continuous monitoring ensures processes run smoothly. Regular maintenance prevents downtime but adds labor costs.
- Quality Assurance: Labor costs are also affected by the number of quality checks required to meet strict customer specifications.
- Training: Investing in employee training improves efficiency but has associated costs.
Shipping and Logistics Costs
Shipping costs depend on the order’s destination, volume, weight, and the chosen shipping method. We offer a variety of shipping options to help you manage costs and ensure timely delivery.
- International Freight: We coordinate sea freight, air freight, and express courier services depending on the urgency of your order. Sea freight is typically more cost-effective for larger shipments, while air freight is faster but more expensive.
- Customs Duties & Taxes: Import duties, taxes, and customs clearance fees vary by country and region. We can provide assistance in calculating these costs to ensure there are no surprises.
- Packaging: We ensure that all products are securely packaged to prevent damage during transit. The cost of packaging is included in the shipping costs.
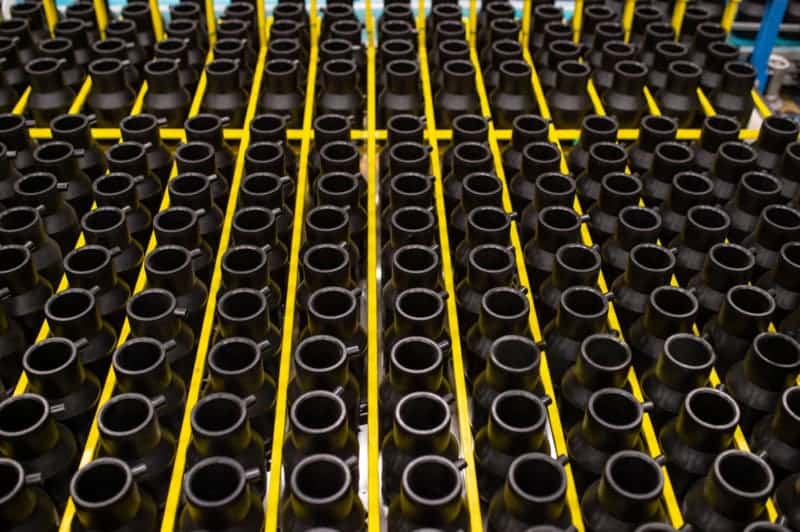
Strategies for Cost Reduction of Two-Shot (2K) Injection Molding
We employ several strategies to manage and reduce the costs associated with two-shot injection molding.
Design Optimization
By refining the design, we can reduce complexity and material usage.
- Simplifying Geometry: Reducing intricate features lowers tooling complexity and machining time.
- Wall Thickness Control: Optimizing wall thickness can decrease material use and shorten cooling times.
- Concurrent Engineering: Collaborating early in the design phase allows us to identify cost-saving opportunities.
Material Selection
Choosing the right materials is key to balancing performance and cost.
- Cost-Effective Alternatives: Identifying materials that meet requirements at a lower cost.
- Standardization: Using common materials across multiple products can reduce costs through bulk purchasing.
- Material Blending: Combining resins may achieve desired properties more economically.
Volume Production
Increasing production volumes can lower the cost per unit.
- Economies of Scale: Higher volumes spread fixed costs, like tooling, over more units.
- Long-Term Planning: Planning for future production needs can justify higher initial investments.
- Flexible Manufacturing: Our facilities can adjust to different production volumes without significant retooling.
Process Efficiency
Improving the efficiency of the manufacturing process reduces time and resources.
- Cycle Time Reduction: We analyze and optimize each phase of the cycle to minimize time without sacrificing quality.
- Automation: Incorporating automation reduces labor costs and increases consistency.
- Preventive Maintenance: Regular maintenance of equipment prevents costly downtime and repairs.
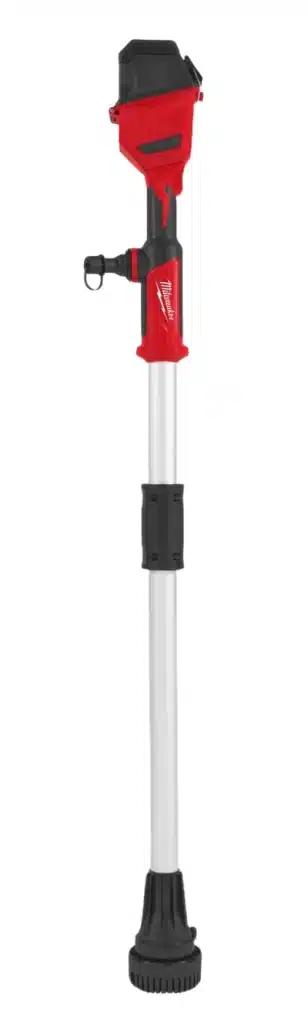
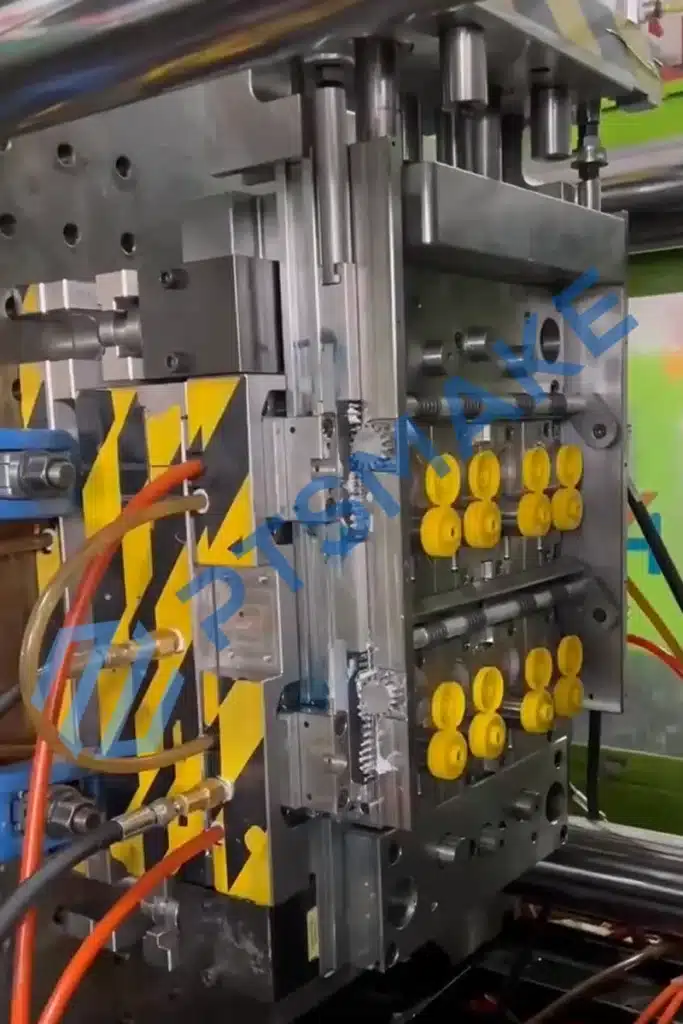
Real-World Example
A scenario where a client requires a high-volume production of a two-shot molded part for a consumer product.
Challenges
- High Tooling Costs: The initial cost for the complex mold is substantial.
- Material Expenses: Specified materials are premium resins with high costs.
Solutions
- Design Collaboration: We work with the client to simplify the part design, reducing tooling complexity.
- Alternative Materials: Proposing equivalent materials that meet performance needs at lower costs.
- Volume Commitment: Planning for larger production volumes to spread tooling costs.
- Process Improvements: Implementing process efficiencies to reduce cycle time and labor costs.
Outcome
- Cost Savings: Achieved a significant reduction in per-unit cost.
- Quality Assurance: Maintained high-quality standards, meeting all client specifications.
- Timely Delivery: Met production schedules, enabling the client to meet market demands.
Long-Term Benefits
- Competitive Pricing: Lower production costs allow us to offer competitive pricing to clients.
- Customer Satisfaction: Delivering quality products at a reasonable cost enhances customer relationships.
- Market Advantage: Clients can price their products more competitively, gaining an edge in the marketplace.
Managing the costs of two-shot injection molding requires a comprehensive understanding of all the factors involved. By focusing on design optimization, smart material selection, efficient production processes, and strategic volume planning, we can control expenses without compromising on quality. Our expertise enables us to guide clients through cost considerations, ensuring that projects are financially viable and successful.
We are committed to working collaboratively with you to find the most cost-effective solutions for your two-shot injection molding needs. By leveraging our experience and resources, we help you achieve your goals while maintaining the highest standards of quality and performance.
Lead Time of Two-Shot (2K) Injection Molding
Timely delivery is crucial in today’s competitive marketplace. We understand that delays can lead to lost opportunities, increased costs, and diminished customer trust. Two-shot (2K) injection molding, while offering significant advantages in product design and functionality, presents unique challenges that can affect lead times. In this comprehensive analysis, we explore the factors influencing the time required for two-shot injection molding projects and our strategies to minimize delays.
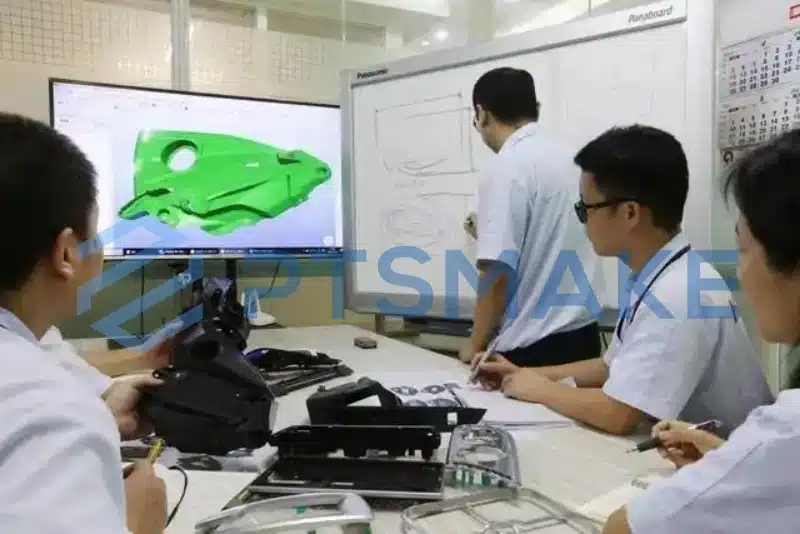
Design Phase
- Complexity of Two-Shot Molds: Designing molds for two-shot molding is inherently more complex than for single-shot molding. The mold must precisely coordinate two different materials, often with varying properties, injected sequentially or simultaneously. This requires meticulous planning and advanced engineering to ensure proper alignment, material flow, and bonding between materials.
- Collaborative Design Process: We engage in close collaboration with clients during the design phase. This involves iterative reviews, modifications, and approvals, which, while essential for a successful outcome, can extend the design timeline if not managed efficiently.
- Use of Advanced Software: Employing sophisticated CAD/CAM software and mold flow simulation tools helps us predict and resolve potential issues before manufacturing begins. These simulations can be time-consuming but are invaluable for optimizing the design and preventing costly mistakes later on.
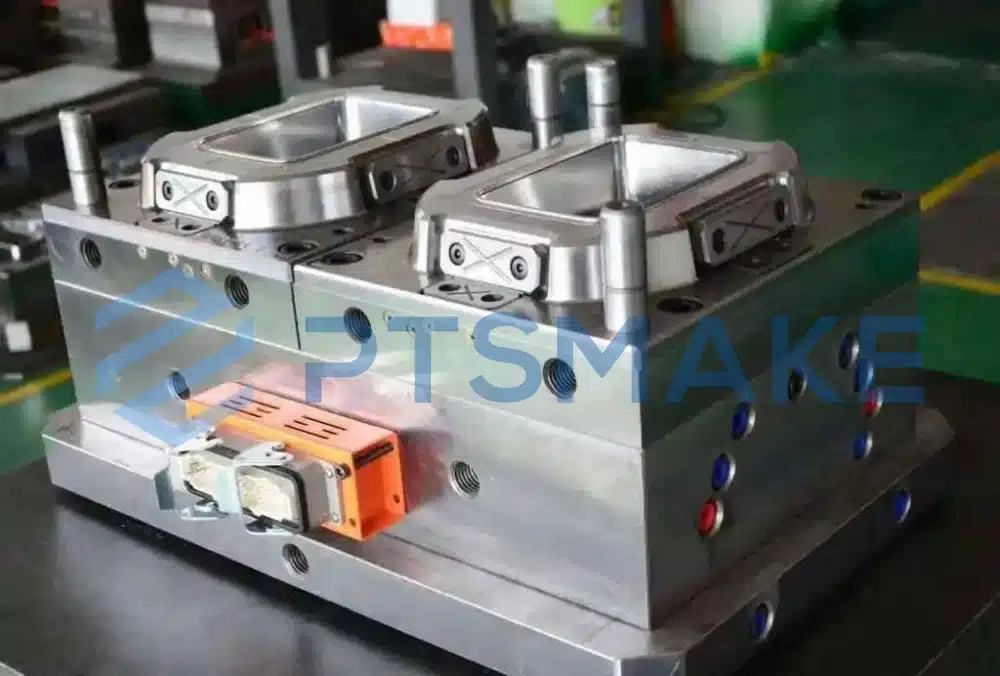
Mold Manufacturing
- Precision Machining: The fabrication of two-shot molds requires high-precision machining techniques, such as CNC milling, EDM (Electrical Discharge Machining), and high-speed machining. Achieving the tight tolerances necessary for two-shot molding is time-intensive.
- Mold Assembly and Testing: After machining, molds must be carefully assembled and tested. This includes trial runs to check for correct material flow, proper bonding, and part quality. Adjustments are often needed, which adds time to the tooling phase.
- Quality Assurance: Rigorous inspection of mold components ensures that every aspect meets design specifications. Any defects or discrepancies identified at this stage necessitate reworking, which can impact the timeline.
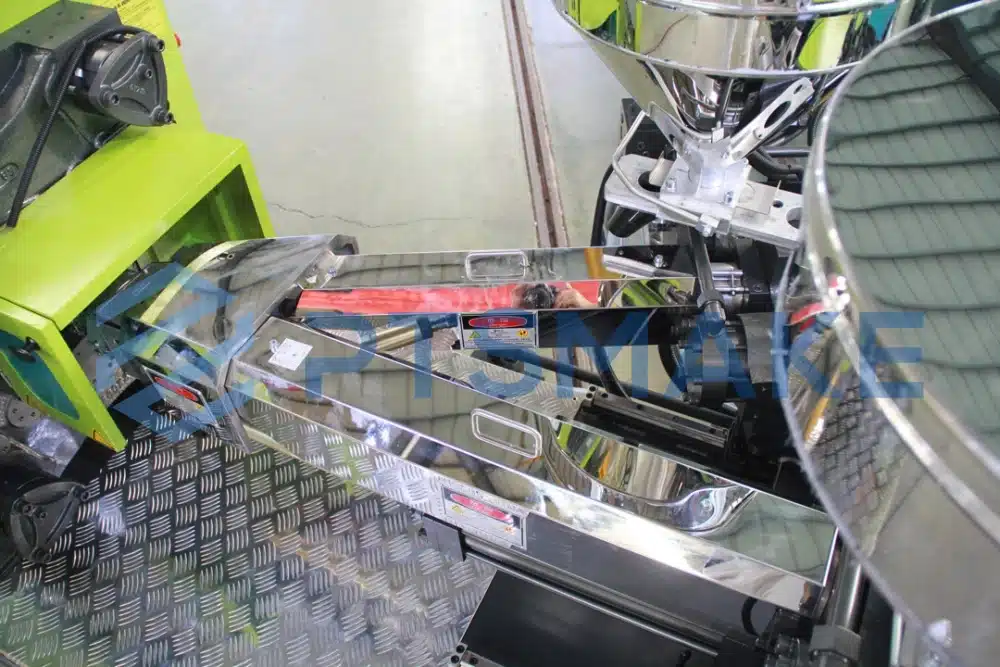
Production Runs
- First Article Inspection (FAI): Before full-scale production, we produce initial samples to validate the process settings and part quality. This involves molding a set number of parts and inspecting them for dimensional accuracy, surface finish, material bonding, and other critical attributes.
- Cycle Time Per Part: Two-shot injection molding often has a longer cycle time per part due to the sequential injection of two materials and the need for precise cooling rates to prevent defects. Optimizing cycle time without compromising quality is a delicate balance.
- Production Volume: The total time required is a function of both cycle time and the number of parts needed. Large orders naturally take longer, but efficiencies can be found through process optimization.
- Machine Downtime: Unexpected machine breakdowns or maintenance needs can cause delays. We mitigate this through preventive maintenance and having contingency plans in place.
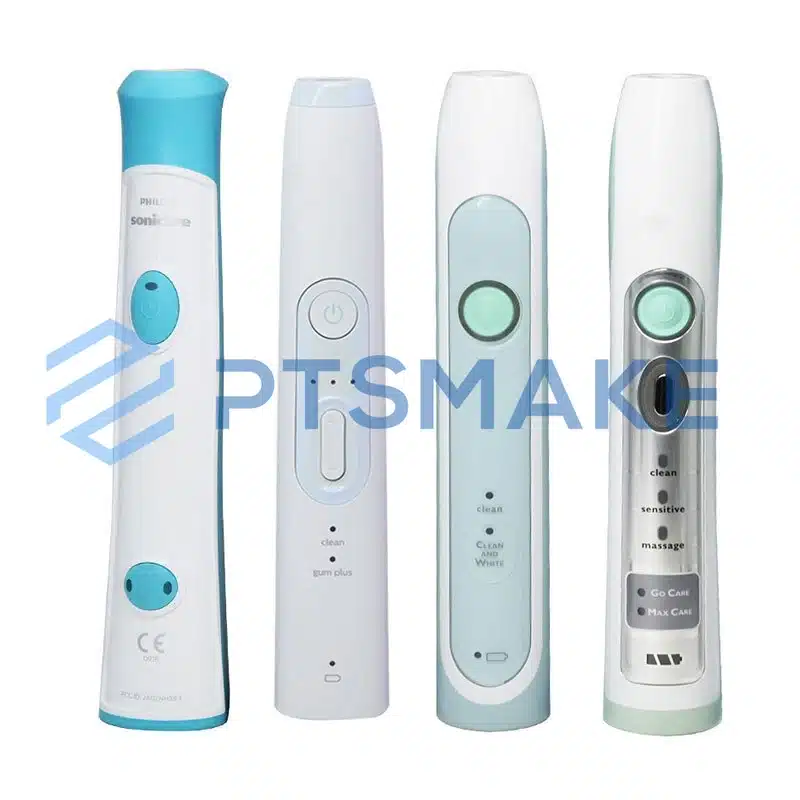
Shipping Time
- Transportation Mode: The choice between air, sea, or land transportation affects delivery times and costs. Air freight is fastest but more expensive, while sea freight is economical but slower.
- Scheduling and Consolidation: Coordinating shipment schedules with carriers and consolidating orders to optimize logistics can influence delivery times.
- Customs Clearance: International shipments require accurate and comprehensive documentation, including commercial invoices, packing lists, bills of lading, and certificates of origin.
- Reputable Carriers: Partnering with reliable carriers known for on-time delivery reduces the risk of delays.
- Engaging Professionals: We utilize experienced customs brokers to navigate complex import/export regulations efficiently.
Strategies to Reduce Lead Time of Two-Shot (2K) Injection Molding
We employ several proactive measures to minimize lead times while maintaining the highest quality standards.
Concurrent Engineering
- Integrated Design and Manufacturing Teams: By involving manufacturing experts during the design phase, we identify potential production issues early on. This integration reduces the need for design revisions later in the process.
- Parallel Processing: We execute certain stages concurrently, such as starting material procurement while the mold is being manufactured. This overlapping of tasks shortens the overall timeline.
Efficient Communication
- Clear Communication Channels: Establishing direct lines of communication between all stakeholders ensures swift resolution of queries and issues. We provide regular updates to keep everyone informed.
- Utilization of Technology: Employing project management software and collaborative platforms enhances transparency and allows real-time tracking of progress.
Technology Investment
- Advanced Machinery: Investing in the latest two-shot injection molding machines increases efficiency. Modern equipment often has faster cycle times and more precise controls.
- Automation: Incorporating automation in material handling, part removal, and secondary processes reduces manual intervention, speeds up production, and minimizes errors.
- Simulation Tools: Using mold flow analysis and other simulation software helps optimize mold designs and process parameters before physical trials, saving time during the tooling phase.
Process Optimization
- Lean Manufacturing Principles: We apply lean methodologies to eliminate waste, streamline processes, and focus on value-added activities. This approach reduces delays caused by inefficiencies.
- Continuous Improvement: Regularly reviewing processes and seeking feedback allows us to identify bottlenecks and implement improvements promptly.
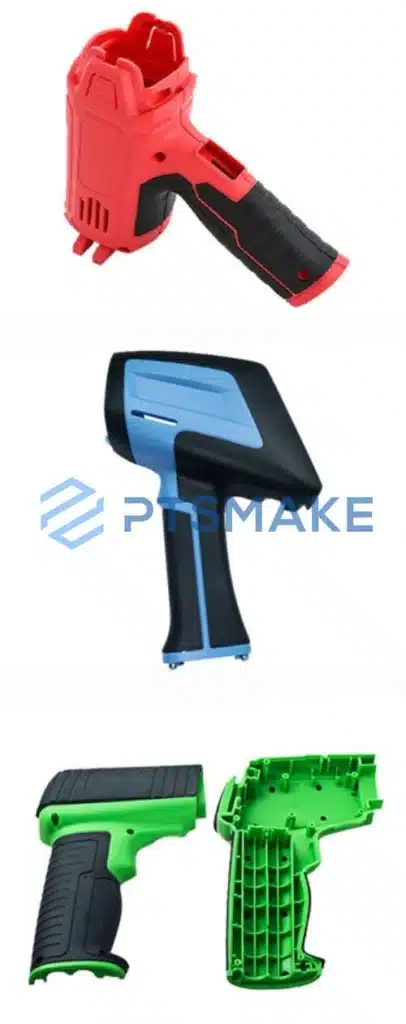
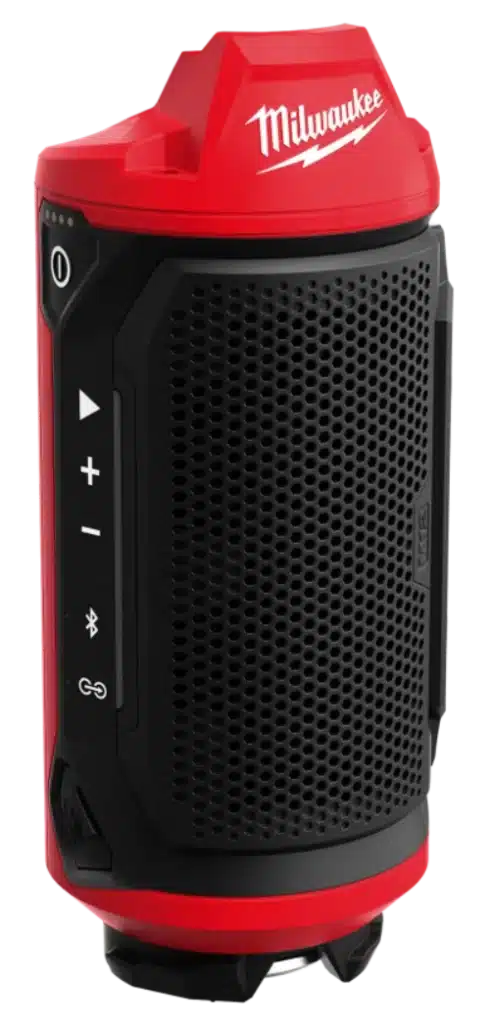
Accelerated Lead Time for a High-Profile Project
A client approached us with an urgent request to produce a complex two-shot molded component for a product launch with a non-negotiable deadline. The stakes were high, as any delay would result in substantial financial losses and damage to their brand reputation.
Approach
- Dedicated Project Team: We assembled a specialized team comprising experienced engineers, project managers, and technical experts focused solely on this project.
- Concurrent Engineering: Design engineers worked alongside tooling engineers to streamline the mold design phase. We initiated material procurement and preliminary process planning concurrently.
- Advanced Simulation: Employed mold flow simulation early to predict and resolve potential issues, reducing the need for time-consuming physical trials.
- Extended Working Hours: Our team operated on an accelerated schedule, including extended shifts and weekend work, to meet the tight timeline.
- Priority Scheduling: Allocated our most advanced machines and prioritized the project in our production schedule.
Outcome
- Successful On-Time Delivery: Despite the tight schedule, we delivered the components on time without compromising quality.
- Quality Assurance Maintained: Rigorous inspections were upheld, ensuring the parts met all specifications.
- Client Satisfaction: The client successfully launched their product, and the project’s success led to a long-term partnership.
Effective time management in two-shot (2K) injection molding is a multifaceted challenge that requires careful coordination across all stages of the production process. By leveraging advanced technologies, fostering a skilled and dedicated workforce, and maintaining open communication both internally and with clients, we are able to deliver high-quality products within tight deadlines.
Our Production Capacity of Two-Shot (2K) Injection Molding
We ensure that our production capacity meets your demands and delivers on time. Our production facility is equipped with advanced machinery and a skilled workforce to handle orders efficiently.
Our Equipment and Facilities
- Machine Availability: We operate 2k injection molding machines with clamping forces ranging from 110 tons to 1,200 tons. This range allows us to produce parts of various sizes and complexities.
- Production Capacity: Our machines can produce up to 100,000 parts per day, depending on the product specifications.
- Facility Size: Our manufacturing plant covers 10,000 square meters, providing ample space for production, quality control, and storage.
Our Workforce Capacity
- Skilled Operators: We have a team of 120 trained operators who ensure consistent and precise production.
- Support Staff: Our team includes 25 engineers, 15 quality inspectors, and dedicated maintenance personnel to support all aspects of operations.
- Flexible Scheduling: We operate 24/7 with multiple shifts, allowing us to adjust production schedules for urgent orders.
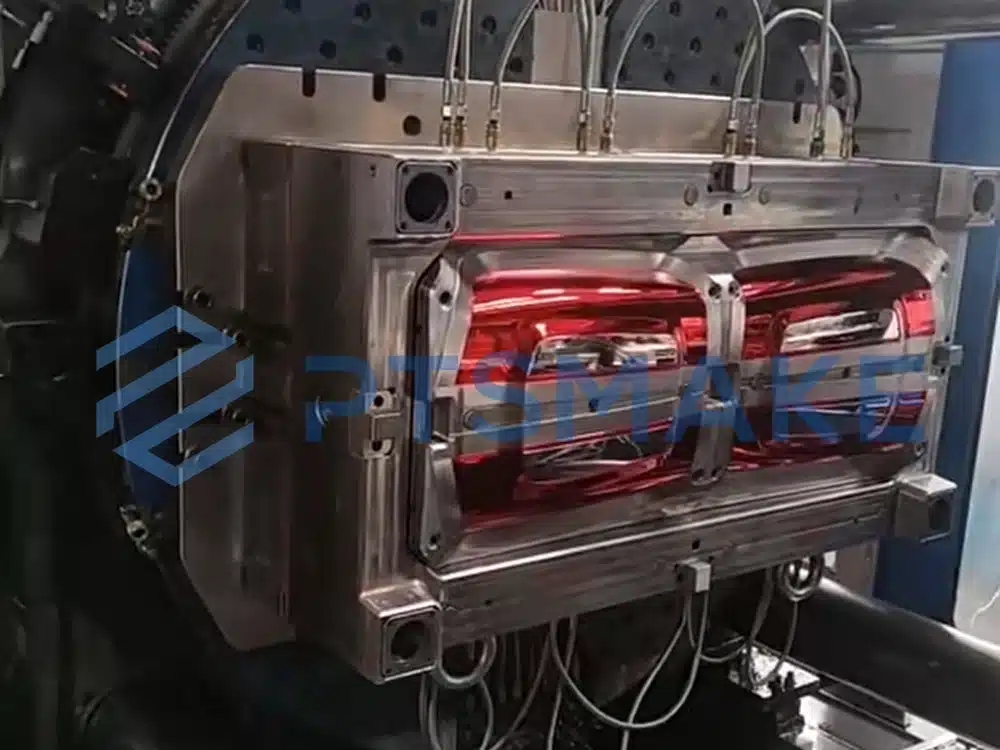
Contact Molding Expert Today!
We look forward to the opportunity to work with you and contribute to your project’s success.
How Does Two-Shot (2K) Injection Molding Work?
We utilize two-shot (2K) injection molding to create complex parts with multiple materials or colors in a single manufacturing process. This technique enhances product functionality and aesthetics efficiently. Here are the eight steps we follow:
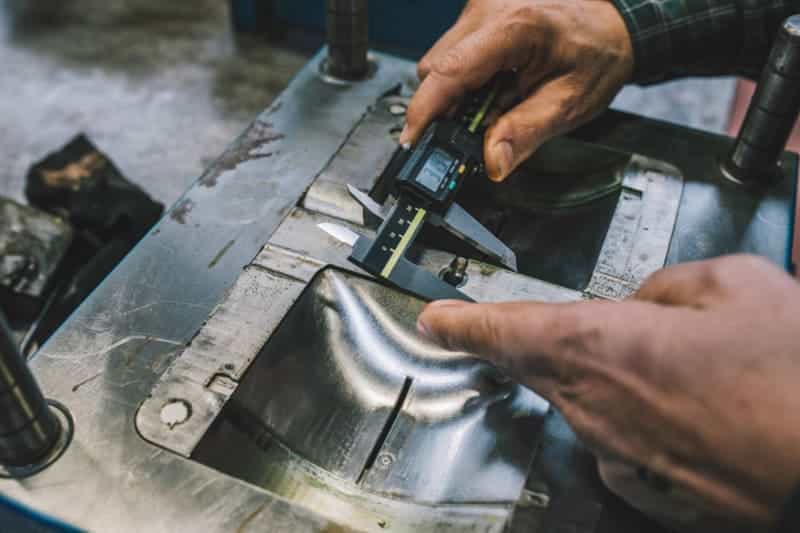
1. Mold Desig & Manufacturing
We design a specialized mold that accommodates two materials, ensuring precise alignment and proper material flow.
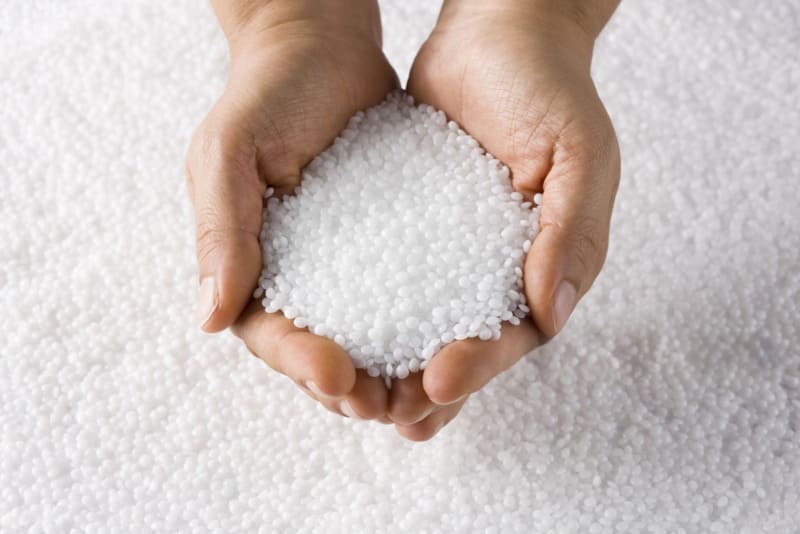
2. Plastic Material Preparation
We select and prepare two compatible materials, readying them for the injection process.
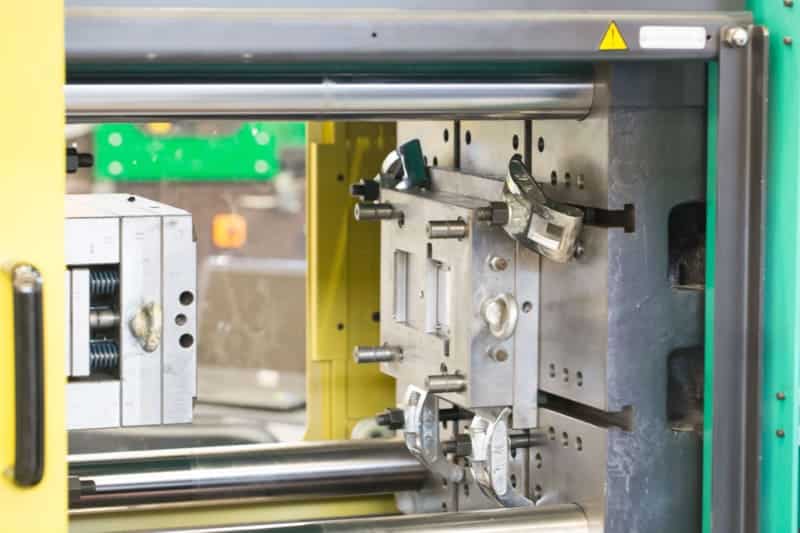
3. Injection Parameter Debug
We set and optimize injection parameters for both materials through testing and adjustments.
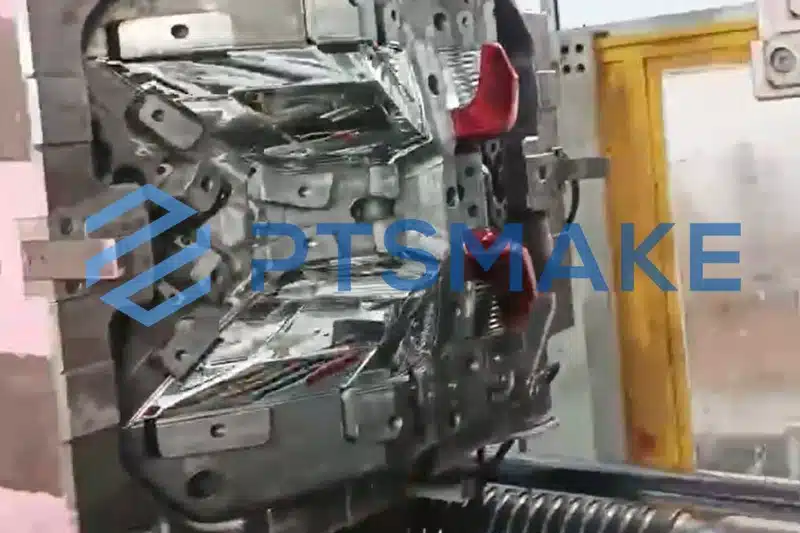
4. First Injection
We inject the first material into the mold, forming the base component with precise features.
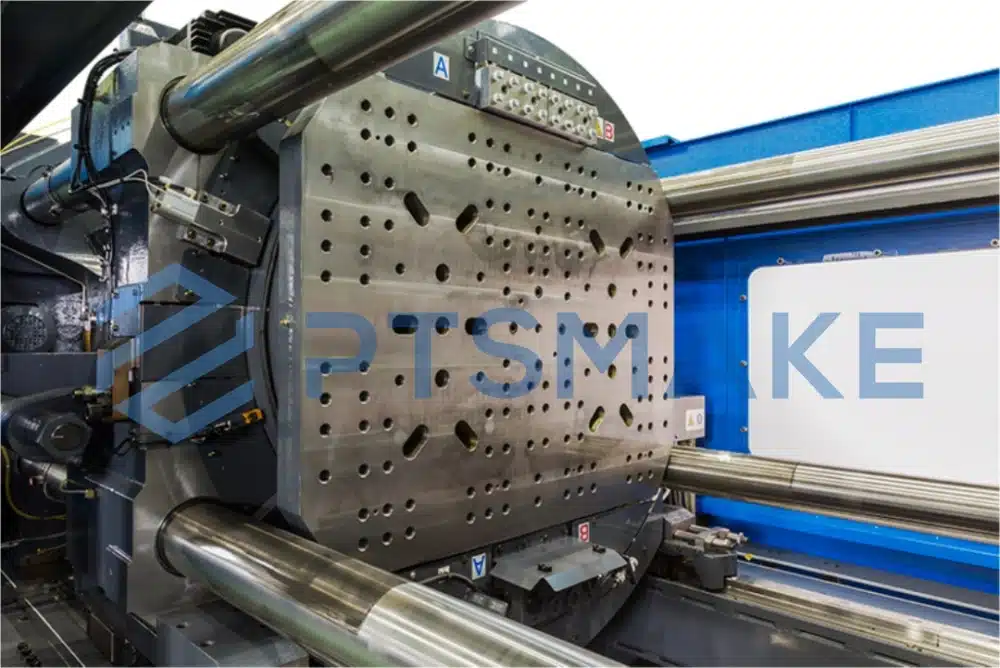
5. Mold Rotation
We rotate or transfer the mold cavity, positioning the first component for the second injection.
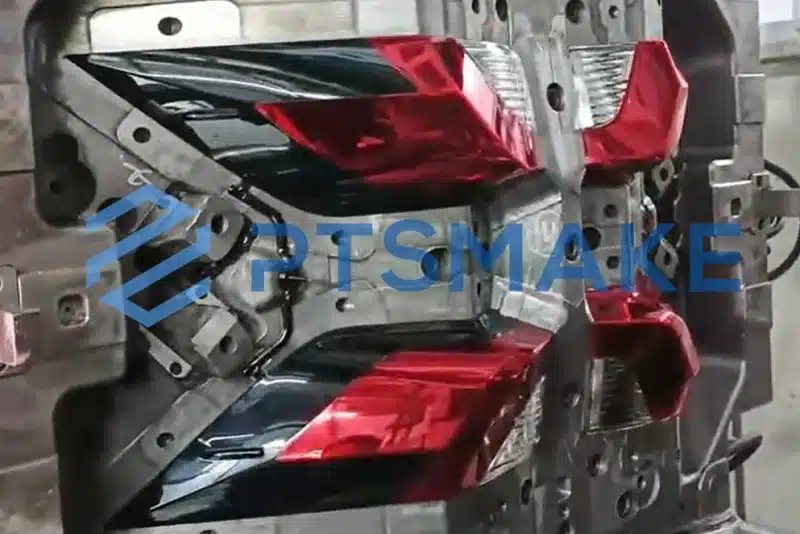
6. Second Injection
We inject the second material, bonding it to the first, creating a unified, integrated part.
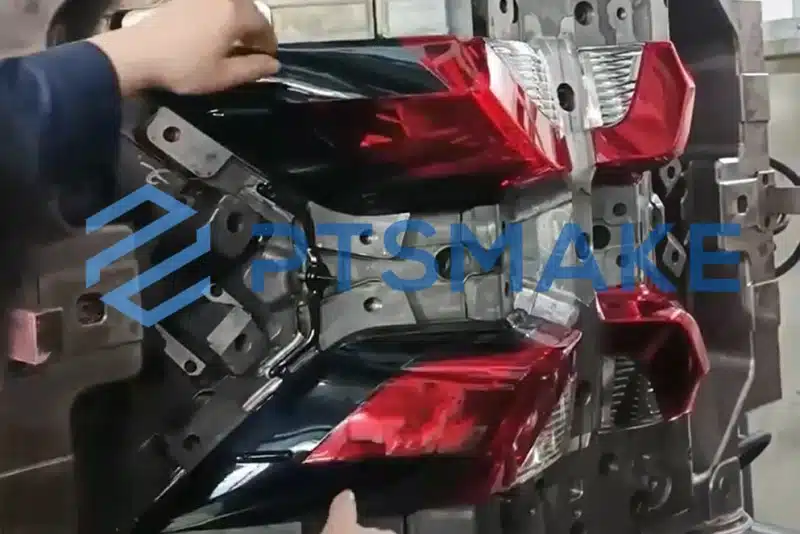
7. Cooling, Eject, Take Out
We allow the combined materials to cool, and then eject the finished part and take out by Robot
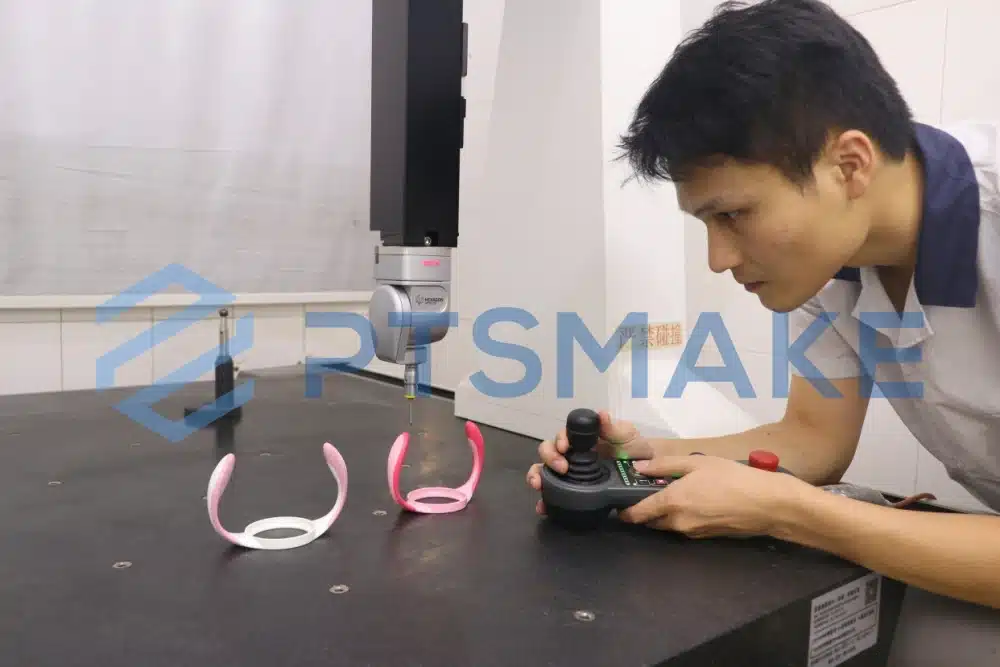
8. Inspection and Packaging
We inspect the finished part for quality, then package it securely for delivery.
Effective Communication with 2K Injection Molding Factories
Communicating well with two-shot injection molding factories is crucial to ensure your design requirements are fully understood and implemented. Here are some strategies to help you achieve successful collaboration.
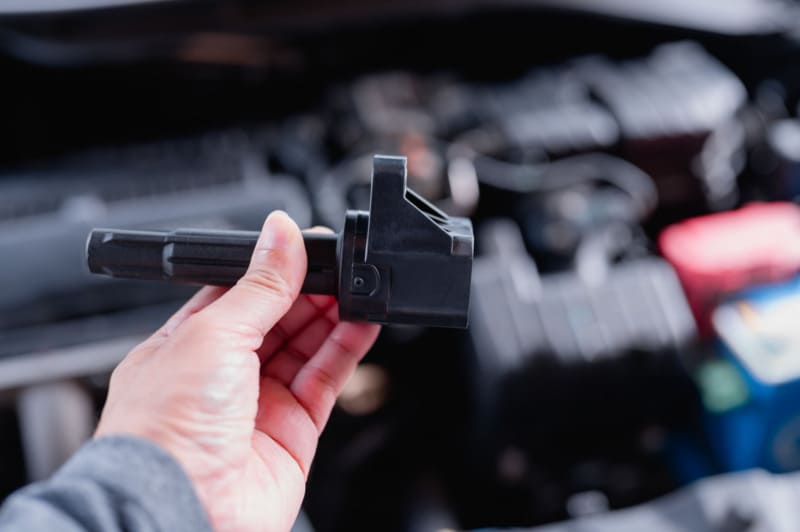
Provide Clear Documentation
View Details
- Detailed Specifications: Provide comprehensive specifications, including dimensions, tolerances, and materials.
- Technical Drawings: Supply accurate drawings and 3D models to help the supplier visualize the final product.
- Process Requirements: Outline any specific processing conditions or constraints.
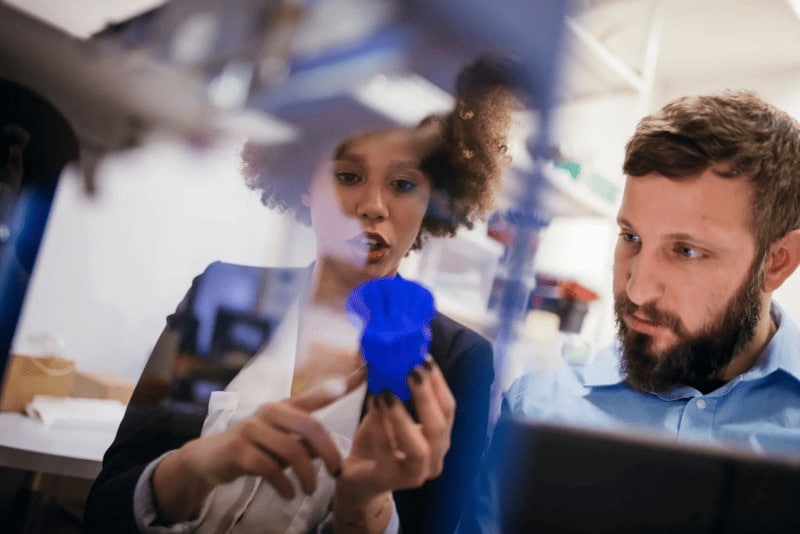
Establish Open Communication Channels
View Details
- Regular Meetings: Schedule regular updates to discuss progress and address concerns.
- Dedicated Contacts: Have specific points of contact to enhance accountability and responsiveness.
- Clear Language: Ensure that all communication is clear and free from jargon.
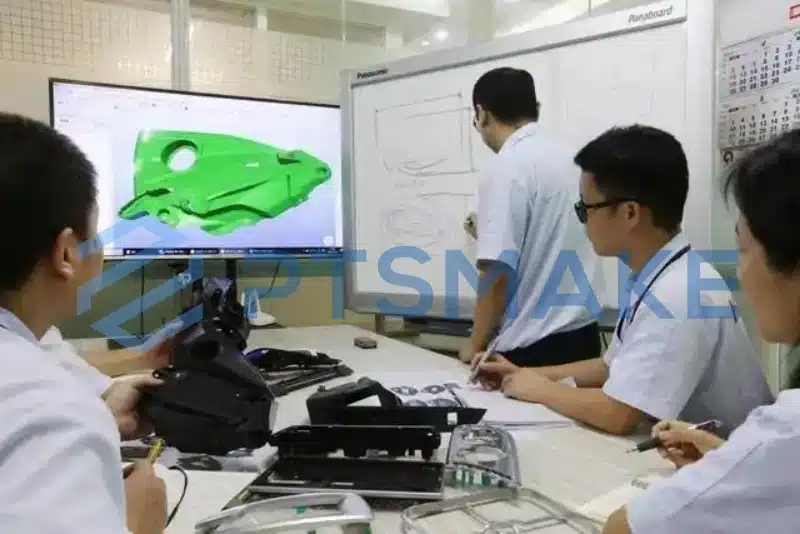
Encourage Feedback
View Details
- Supplier Input: Invite suppliers to share their expertise and suggestions. This can improve the design and process.
- Prototyping and Testing: Collaborate on prototype development to validate designs before full-scale production.
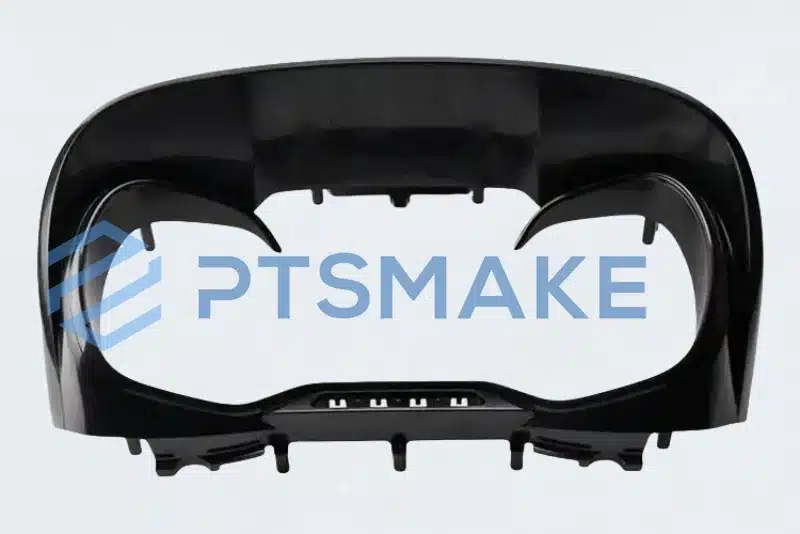
Be Aware of Cultural Differences
View Details
- Understand Cultural Norms: Respect and adapt to cultural practices to improve relationships and communication.
- Local Representation: Consider having local team members or partners to bridge communication gaps.
Balancing Quality and Cost in 2K Injection Molding
Choosing the right two-shot injection molding supplier is crucial for your project’s success. We understand the importance of balancing quality and cost without compromising either. Here’s how we help you achieve this balance.
Understanding Total Costs
Looking beyond the initial price is essential. We consider the total cost over the product’s entire lifecycle.
- Quality vs. Rework Costs: Low-quality products can lead to higher costs due to rework, scrap, or returns. Defects not only increase expenses but also harm your reputation and delay your projects.
- Efficiency and Waste Reduction: Efficient manufacturing processes reduce material waste and labor costs. We invest in advanced machinery and adopt lean practices to produce parts more cost-effectively.
- Supplier Reliability: Dependable suppliers prevent costly delays. Late deliveries can disrupt your schedule and increase holding costs. We ensure on-time delivery and handle challenges effectively.
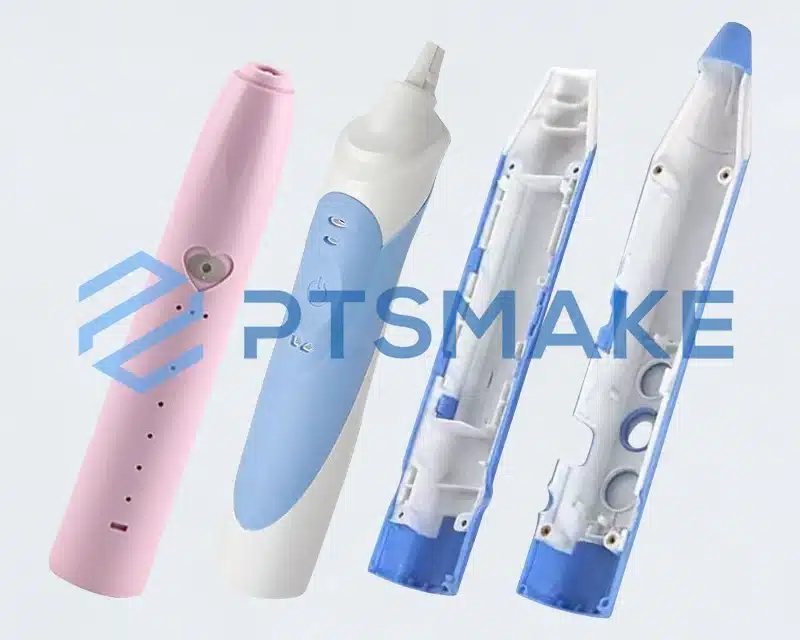
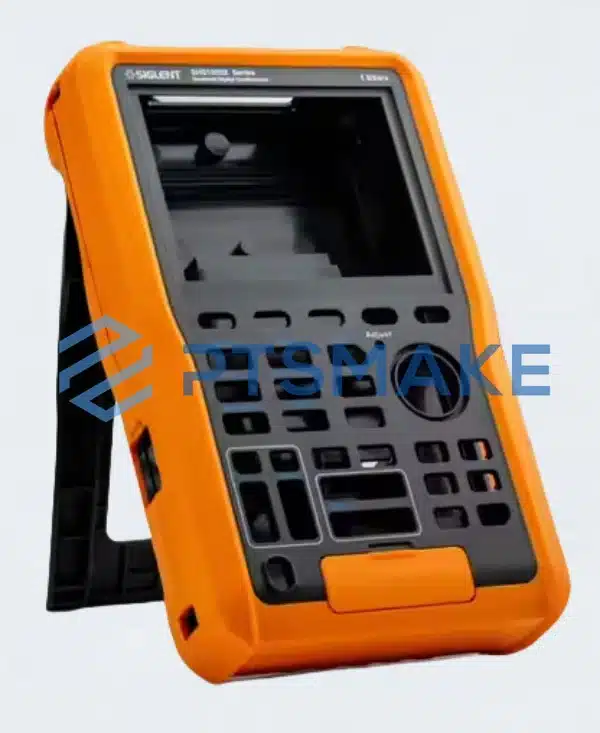
Cost Optimization Strategies
We focus on methods to reduce costs while maintaining high quality.
Design for Manufacturability: By optimizing product designs, we simplify manufacturing and reduce costs.
-Simplify Geometry: Eliminating unnecessary complexity reduces tooling costs and production time.
-Standardize Components: Using standard sizes lowers material costs and simplifies assembly.
Material Selection: Choosing the right materials balances cost and performance.
-Alternative Materials: We explore cost-effective materials with similar properties, like high-performance polymers instead of metal.
-Supplier Partnerships: We collaborate with material suppliers to negotiate better pricing and secure reliable supply chains.
Volume Negotiations: Ordering larger quantities reduces unit costs.
-Economies of Scale: Larger orders spread fixed costs over more units, lowering the cost per part.
-Negotiated Discounts: We leverage volume commitments to secure discounts and favorable terms.
Process Efficiency: Streamlining production saves time and reduces labor costs.
-Lean Manufacturing: We adopt lean principles to eliminate waste and improve efficiency.
-Automation: Implementing automated processes enhances consistency and reduces errors, leading to cost savings.
Balancing quality and cost in two-shot injection molding is essential. By considering total costs, optimizing processes, and ensuring high standards, we deliver quality products at competitive prices. Our commitment to excellence ensures your projects succeed without unnecessary expenses.
We are dedicated to helping you navigate the complexities of supplier selection. With our expertise in two-shot injection molding, we provide solutions that meet your quality expectations while respecting your budget. If you need assistance with your project, we’re here to support you every step of the way.
Benefits of Two-Shot (2k) Injection Molding
Two-shot injection molding offers significant advantages that directly benefit our customers. By combining two different materials in a single molding process, we enhance product functionality, reduce costs, and enable innovative designs.
Innovation and Differentiation
- Unique Product Designs:
Two-shot molding allows us to create products with complex designs that are difficult to achieve with traditional molding methods. We can combine materials with different colors, textures, or properties into one seamless part. This capability lets us produce innovative products that stand out in the market.
- Strengthening Brand Identity:
We can incorporate brand elements directly into the product during molding. By embedding logos, brand colors, or unique design features, we enhance brand recognition without additional manufacturing steps. This direct integration saves time and reinforces your brand in the minds of consumers.
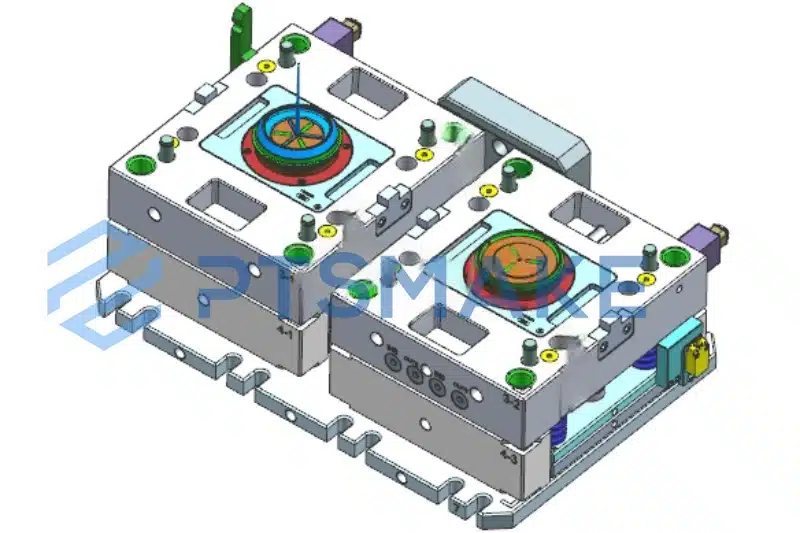
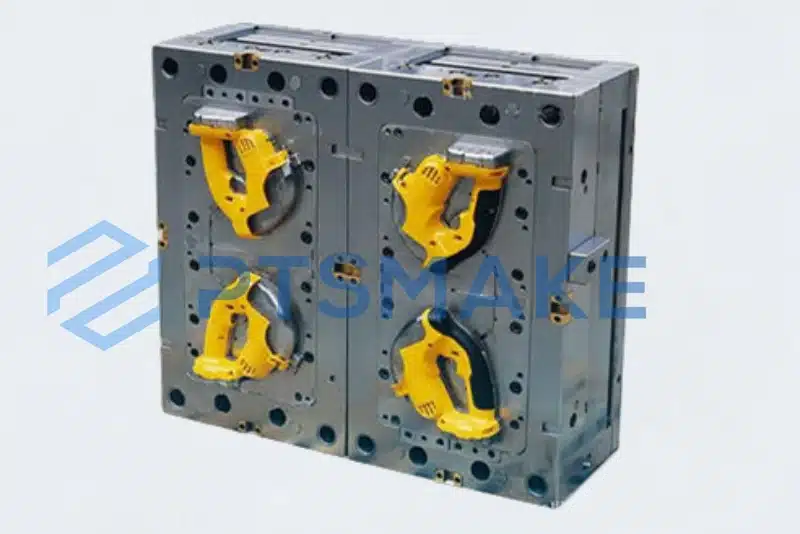
Cost Savings
Eliminating Assembly Costs:
By molding multiple materials into a single part, we remove the need for separate assembly processes. This integration reduces labor costs and minimizes the risk of assembly errors. The streamlined production process leads to lower overall manufacturing costs and faster turnaround times.
Reducing Defect Rates:
Two-shot molding creates strong bonds between materials, resulting in durable, high-quality parts. The risk of weak joints or parts failing due to poor assembly is significantly reduced. Fewer defects mean less waste and lower costs associated with rework or returns.
Increased Market Competitiveness
- Accelerated Time to Market:
Our efficient two-shot molding process speeds up production. By combining steps and reducing assembly time, we help you bring products to market faster. This advantage allows you to respond quickly to market demands and stay ahead of competitors.
- Adapting to Market Trends:
The flexibility of two-shot molding enables us to adjust designs easily. We can quickly modify colors, materials, or features to keep up with changing market trends. This adaptability helps you meet customer needs promptly and maintain a competitive edge.
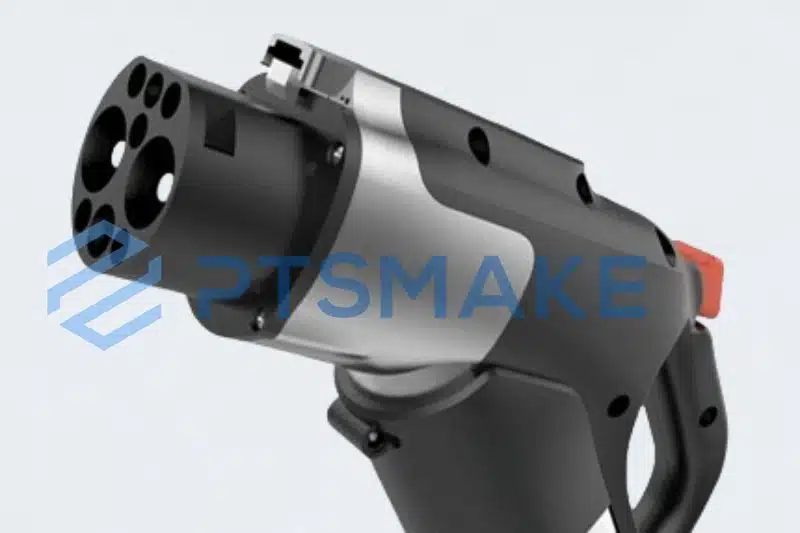
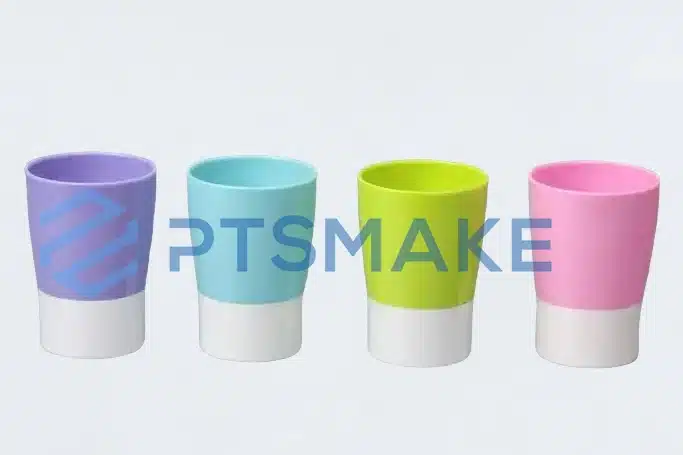
Enhanced User Experience
Improved Functionality:
Combining materials with different properties can enhance product performance. For example, we can mold hard and soft materials together to create ergonomic grips or seals that improve usability. Better functionality leads to higher customer satisfaction and loyalty.
Attractive Aesthetics:
Two-shot molding allows for visually appealing designs with multiple colors or finishes. The seamless integration of materials results in a high-quality appearance that attracts customers. An appealing product can differentiate your brand and boost sales.
Environmental Benefits
- Minimizing Material Waste
By molding parts in one process, we reduce material waste associated with multiple production steps. Efficient use of materials means less scrap and a smaller environmental footprint. This efficiency not only benefits the planet but can also lower material costs.
- Energy Efficiency
Consolidating manufacturing steps into a single process uses less energy. Reduced energy consumption decreases production costs and supports sustainable practices. Embracing energy efficiency helps you meet environmental goals and appeal to eco-conscious consumers.
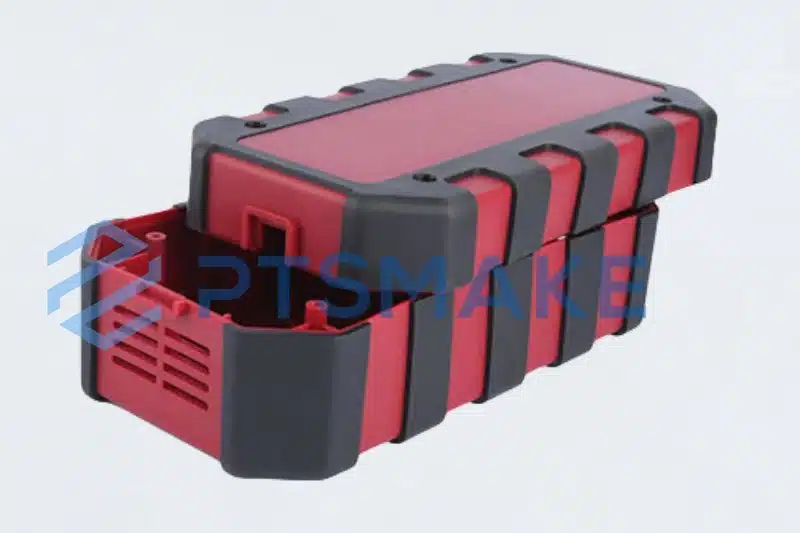
Consolidating manufacturing steps into a single process uses less energy. Reduced energy consumption decreases production costs and supports sustainable practices. Embracing energy efficiency helps you meet environmental goals and appeal to eco-conscious consumers.
By leveraging the advantages of two-shot injection molding, we deliver products that offer both quality and value. Our expertise in this advanced molding technique helps you innovate, save costs, and satisfy your customers’ evolving needs. Partner with us to take full advantage of what two-shot injection molding has to offer.
2k Injection Molding Applications
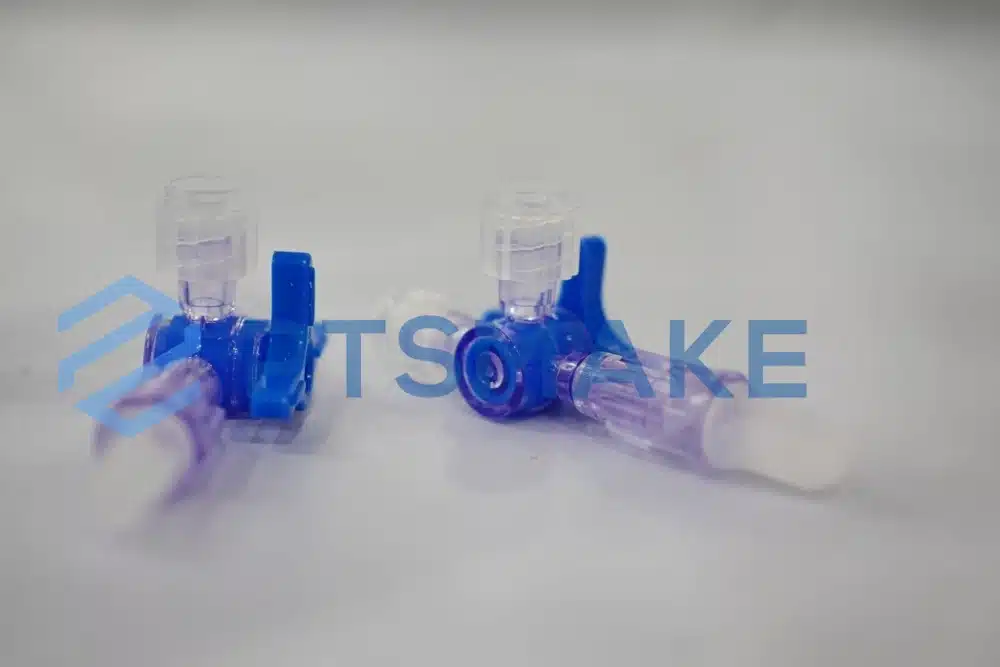
Medical
- Read More
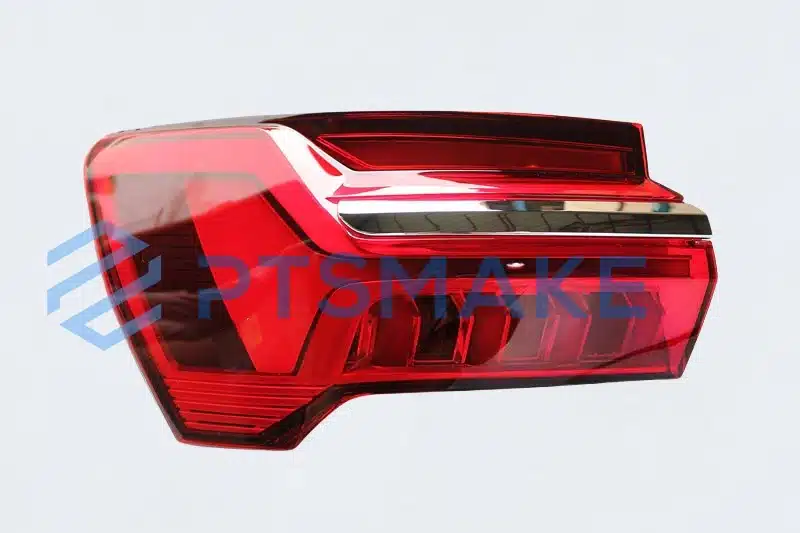
Automotive
- Read More
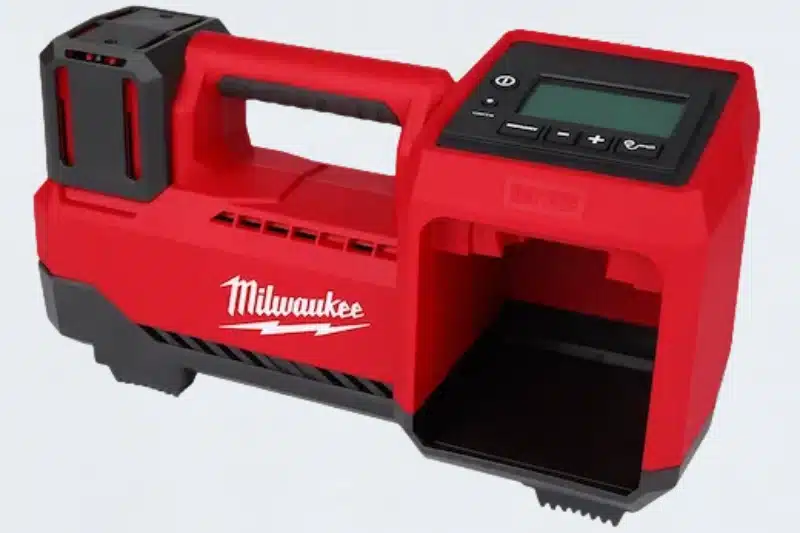
Consumer Products
- Read More
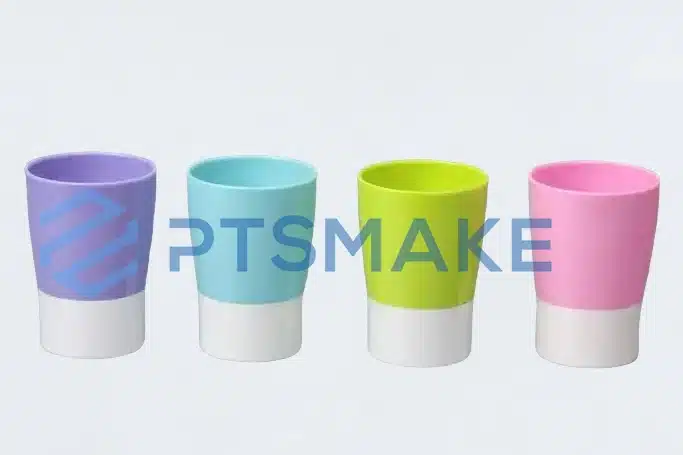
Packaging
- Read More
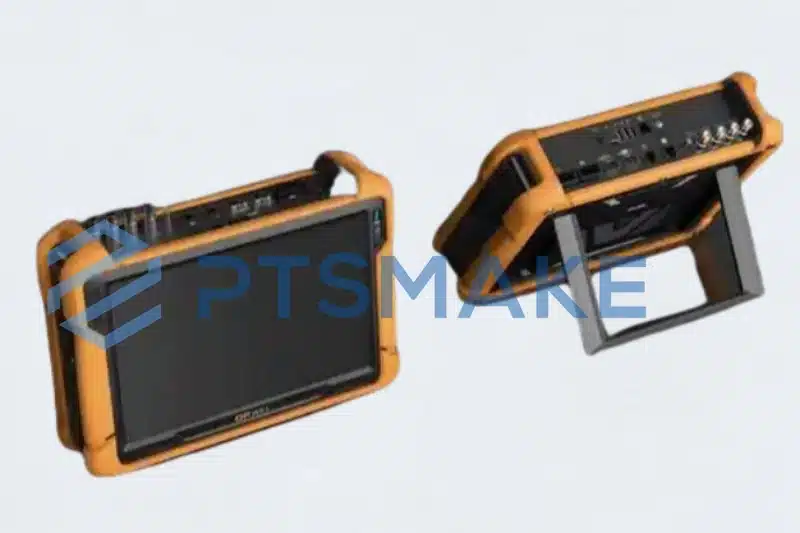
Electronics
- Read More
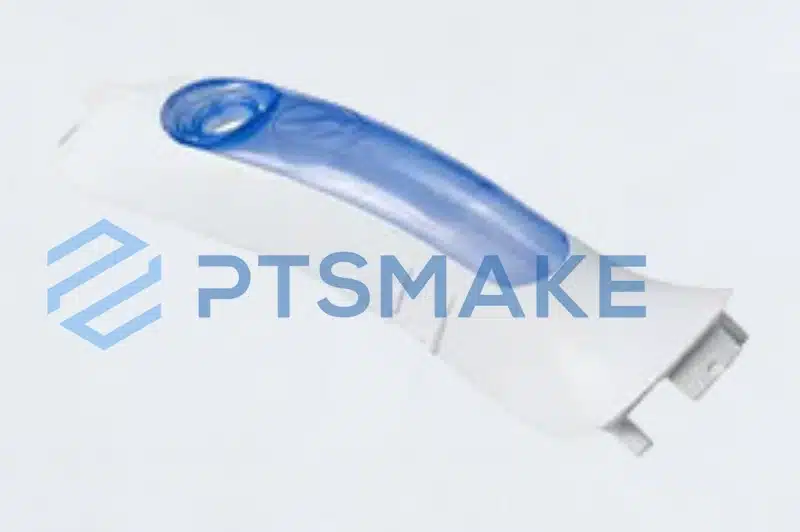
Home Appliances
- Read More
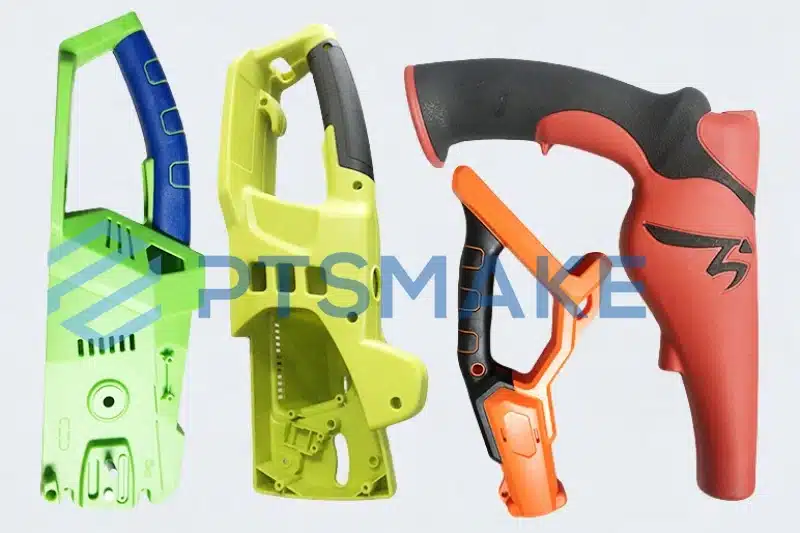
Industrial Machinery
- Read More
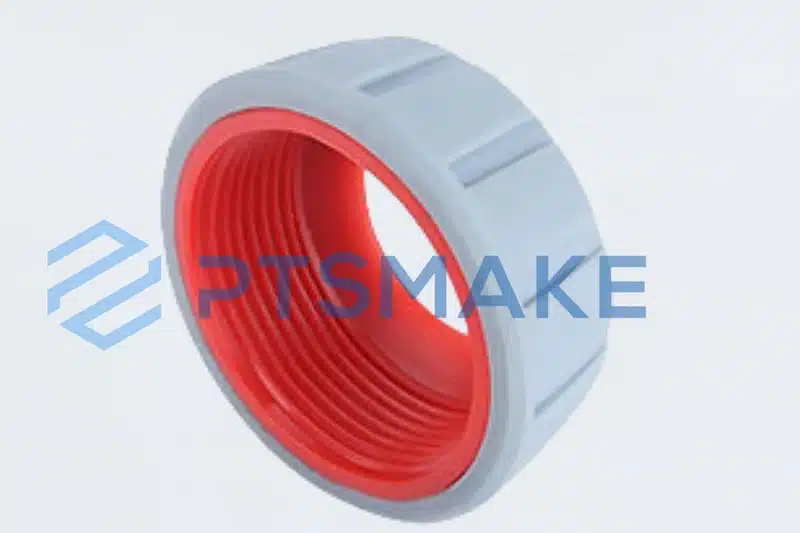
Marine
- Read More
Two Shot (2k) Injection Molding FAQs
Can Any Materials Be Used Together For 2k molding?
Materials must be compatible in terms of bonding and processing temperatures. We help select suitable material combinations.
Is Two-Shot Molding More Expensive?
While the initial tooling cost is higher, the overall cost can be lower due to reduced assembly and increased efficiency.
Can Existing Molds Be Modified for Two-Shot Molding?
Typically, new molds are required due to the unique design of two-shot molds.
Do you have ISO 9001 or other relevant quality certifications?
Yes, we are proud to be ISO 9001 certified. This certification reflects our commitment to maintaining the highest quality standards throughout our manufacturing processes. We continually strive to exceed industry standards to ensure our customers receive products that meet and often surpass their expectations.
What Industries Benefit Most from Two-Shot Molding?
Industries like automotive, medical devices, consumer electronics, gardening tool, electric tool and packaging greatly benefit from this process.
How Does Two-Shot Molding Benefit My Product?
This process allows us to combine materials for enhanced functionality, improved aesthetics, and cost savings by eliminating secondary assembly.
Is Two-Shot Molding Suitable for Complex Designs?
Absolutely. We can create intricate parts with multiple materials or colors, improving design flexibility and product functionality.
Can We Use Two Different Colors in One Part?
Yes, two-shot molding allows us to combine different colors in a single part without painting or secondary operations.
How Does Two-Shot Molding Improve Product Quality?
By molding two materials together, we create stronger bonds and eliminate defects from secondary assembly.
What Are the Limitations of Two-Shot Molding?
Material compatibility is crucial. Not all materials bond well, and tooling costs are higher due to mold complexity.
How Do We Ensure Material Compatibility?
We work with you to select materials that bond effectively and meet your product’s requirements.
Can Two-Shot Molding Be Used for Prototyping?
It is less common due to tooling costs, but we can discuss options for low-volume production.
How are shipping costs calculated?
Shipping costs are calculated based on the shipment’s weight, volume, destination, and the chosen shipping method. We have partnerships with reliable logistics providers to ensure competitive rates and efficient service.
How Does Two-Shot Molding Affect Product Design?
Designs must consider material flow, bonding areas, and mold mechanics. We assist in optimizing your design.
What Is the Difference Between Two-Shot and Overmolding?
In two-shot molding, both materials are injected in one machine during one cycle. Overmolding involves molding over a pre-existing part, often in separate processes.
How Do You Handle Quality Control?
We implement rigorous quality checks to ensure each part meets specifications and industry standards.
Can Two-Shot Molding Combine Hard and Soft Materials?
Yes, we can bond rigid plastics with softer materials like elastomers to enhance grip or sealing functions.
What Is the Cost of Tooling for Two-Shot Molding?
Tooling costs are higher due to complexity, but savings come from reduced production time and assembly costs.
Is it possible to sign a Non-Disclosure Agreement (NDA)?
Yes, we are more than willing to sign an NDA to formalize our commitment to confidentiality. This agreement ensures that your sensitive information remains protected throughout our collaboration.
How Do We Begin a Two-Shot Molding Project?
Contact us with your project details. We guide you through material selection, design optimization, and production planning.
Who owns the molds?
Typically, once the mold fabrication cost is fully paid, the ownership of the mold transfers to you. We will store and maintain the mold for production purposes unless you request otherwise.
How Does Two-Shot Molding Improve Product Safety?
By integrating materials in a single process, we eliminate the need for adhesives or mechanical fasteners, reducing potential points of failure and improving overall product safety.
Can Two-Shot Molding Be Used for High-Volume Production?
Yes, we can use two-shot molding for high-volume production. The process is efficient for large quantities because it reduces assembly steps and accelerates production cycles.