Custom Plastic Injection Molds Manufacturer
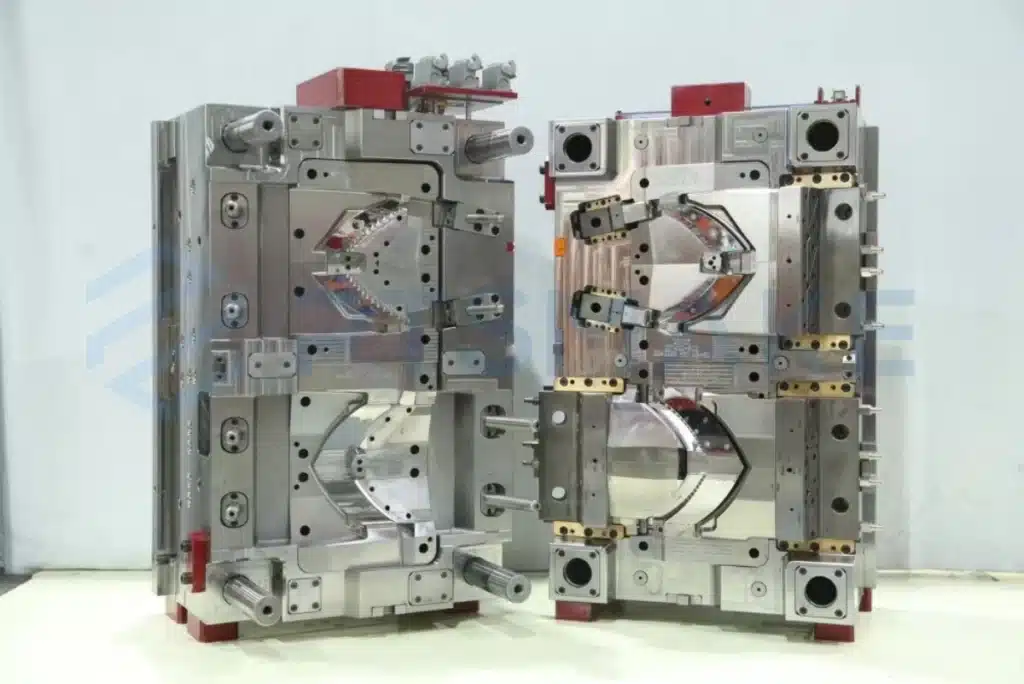
Our molds life last 50% longer than other molds.
40 + Countries We Exported To
We Excel in Complex And Two-Shot Molds
4,000 + Successfully Molds Finished.






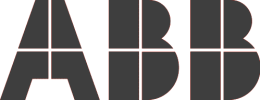

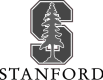
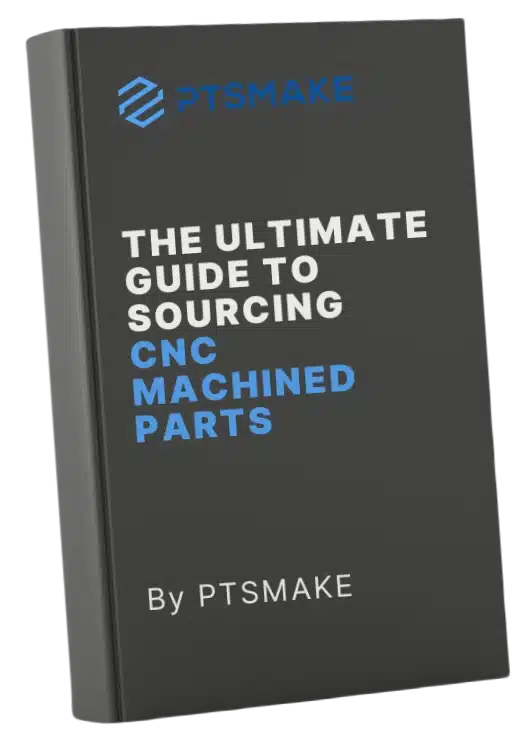
To save you time, we have also prepared a PDF version containing all the contents of this page, only leave your email and you will get the download link immediately.
Our Quality Control Process for Plastic Injection Molds
We understand that quality is your top concern when it comes to plastic injection molds. Ensuring that every mold meets your standards is our priority. Here is how we control quality at each step.
Design Review: We start by reviewing your design specifications thoroughly. Our team checks for any issues that might affect the mold’s performance. By addressing potential problems early, we aim to meet your requirements from the very beginning.
Material Inspection: Choosing the right material is crucial for a durable mold. We select high-quality steels suitable for injection molding. Before production, we inspect all materials to ensure they meet our standards. This step helps us prevent defects and extend the mold’s lifespan.
- Precision Manufacturing: During manufacturing, we use advanced machines for precise results. Our technicians monitor the process closely. We focus on achieving exact dimensions and smooth surfaces. Precision at this stage means better performance in your production line.
- In-Process Checks: Quality checks continue throughout production. We measure critical dimensions regularly. If we find any deviations, we correct them immediately. These checks help us maintain consistency and prevent delays.
- Sample Testing: After the mold is made, we conduct test runs. We produce sample parts using the mold. Our team inspects these samples for accuracy and finish. If the samples meet your specifications, we proceed. If not, we make the necessary adjustments.
- Final Inspection: Before shipping, we perform a final inspection. We verify all aspects of the mold, including its functionality. We ensure that everything works smoothly. This step gives you confidence that the mold is ready for production.
- Documentation: We provide detailed reports of our quality control process. You receive records of inspections and test results. This transparency allows you to understand how we achieved the quality you expect.
- Continuous Improvement: We value your feedback. After you receive the mold, we stay in touch to ensure it meets your needs. Your input helps us improve our processes. Together, we strive for excellence in every project.
- Commitment to Quality: Our goal is to provide molds that enhance your production efficiency. By focusing on quality control, we aim to build long-term partnerships with you. We are dedicated to delivering products that you can trust.
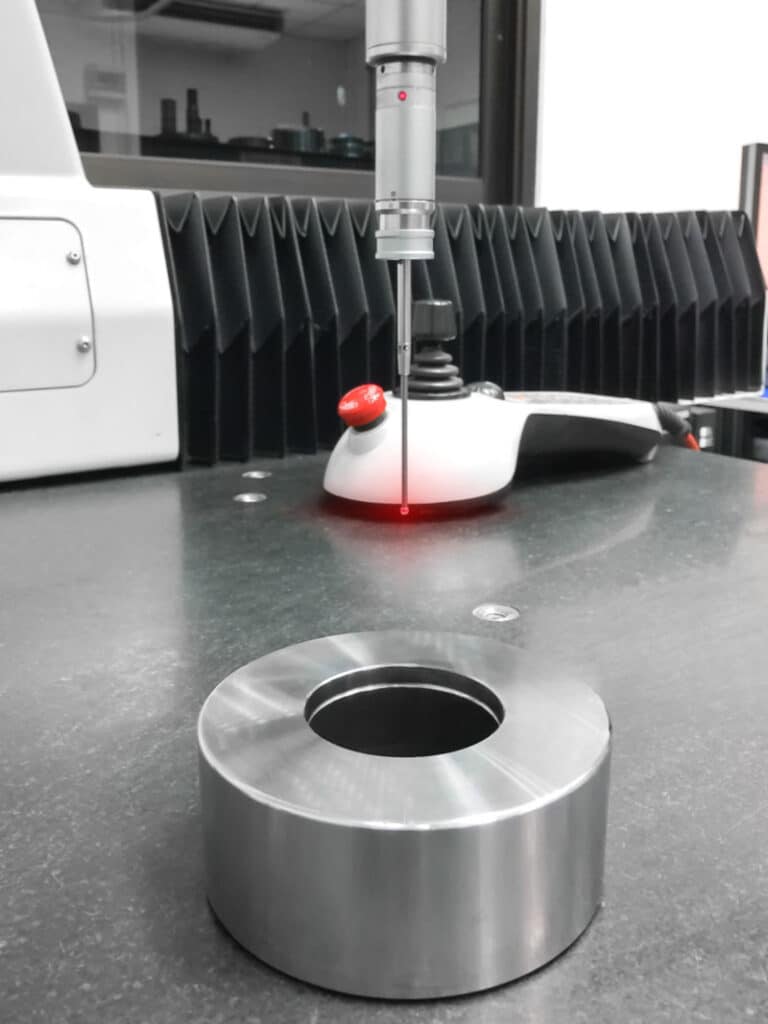
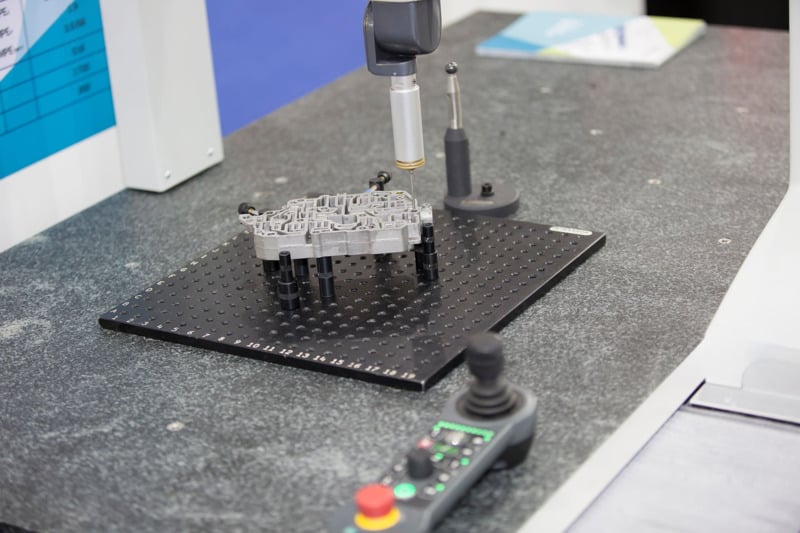
CMM
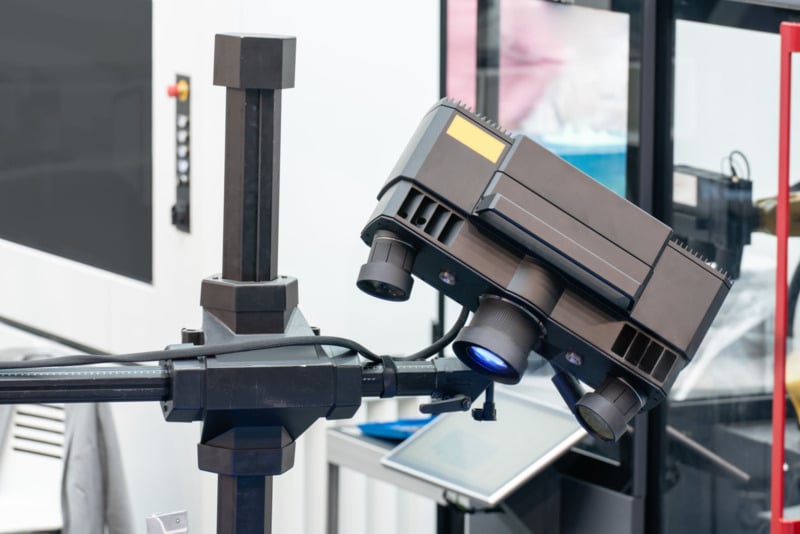
GOM 3D-Scanner
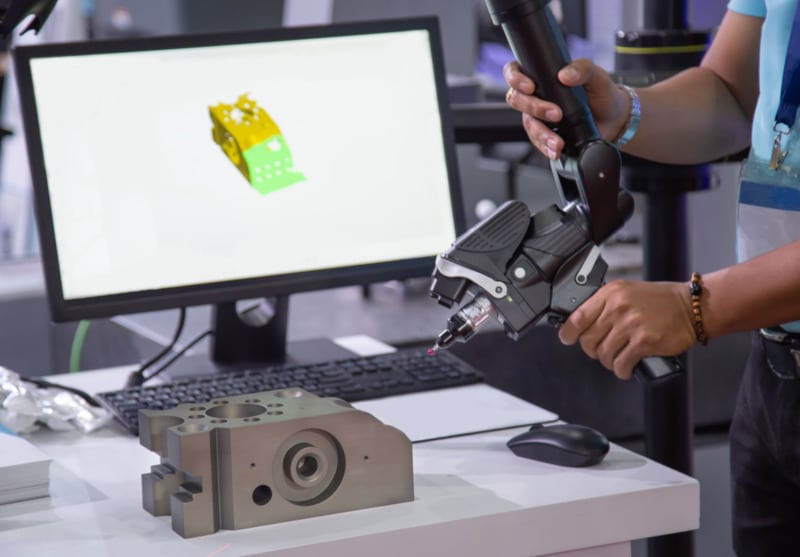
Portable CMM
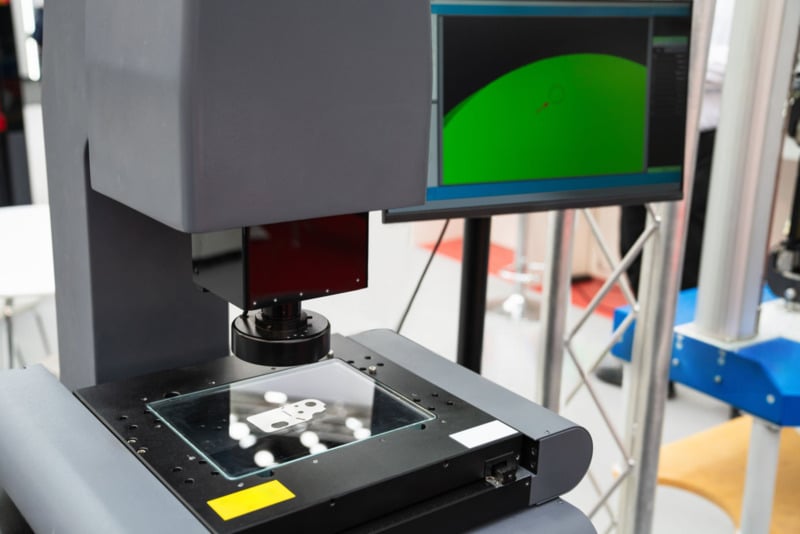
Projector
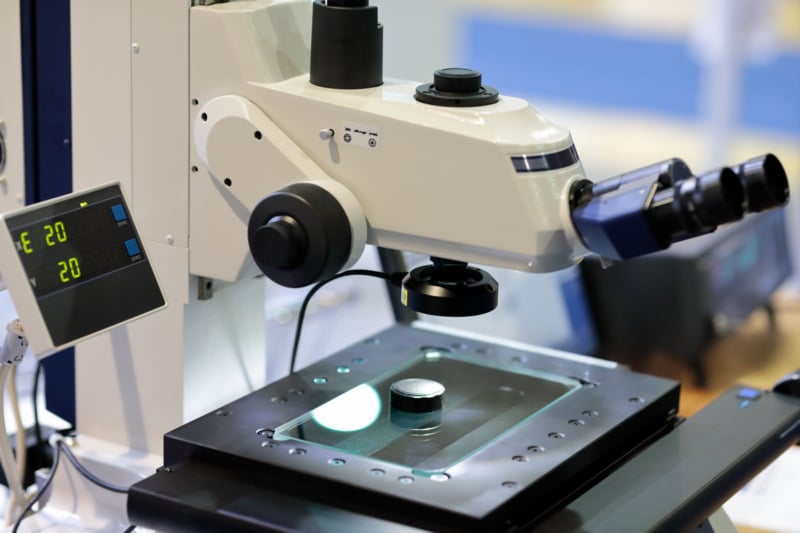
Optical microscope
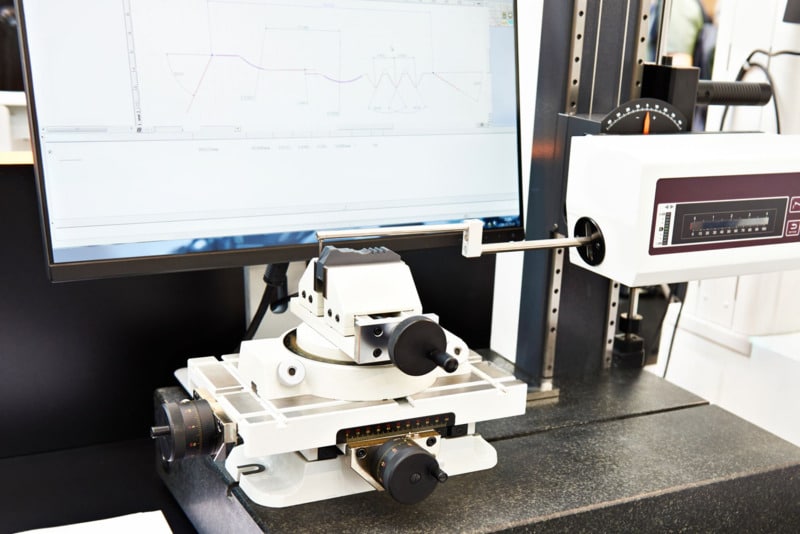
Roughness Tester
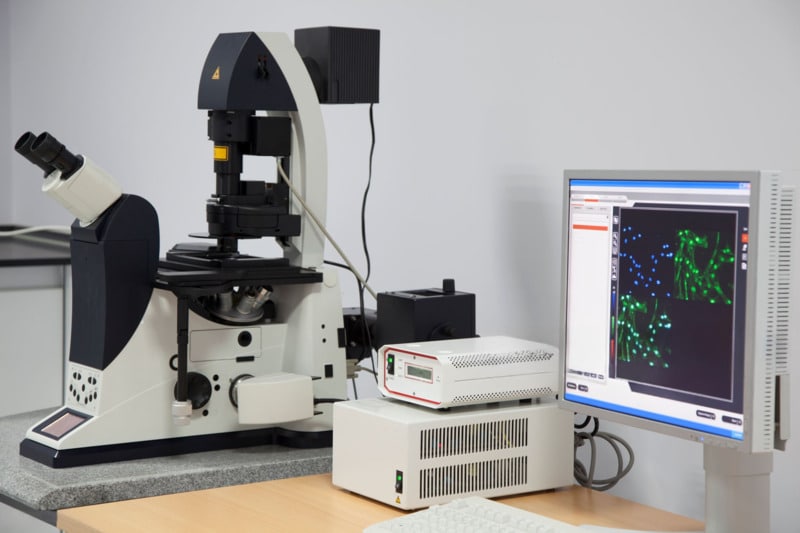
Raw material analyzer
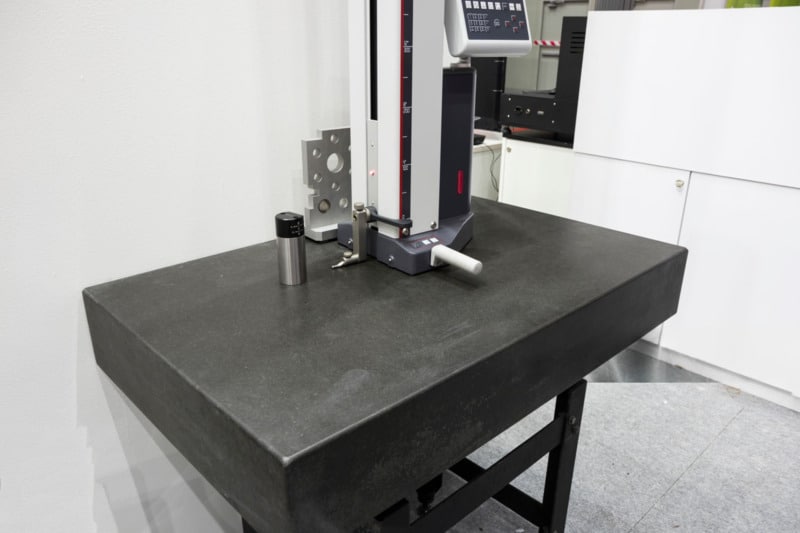
Altimeter
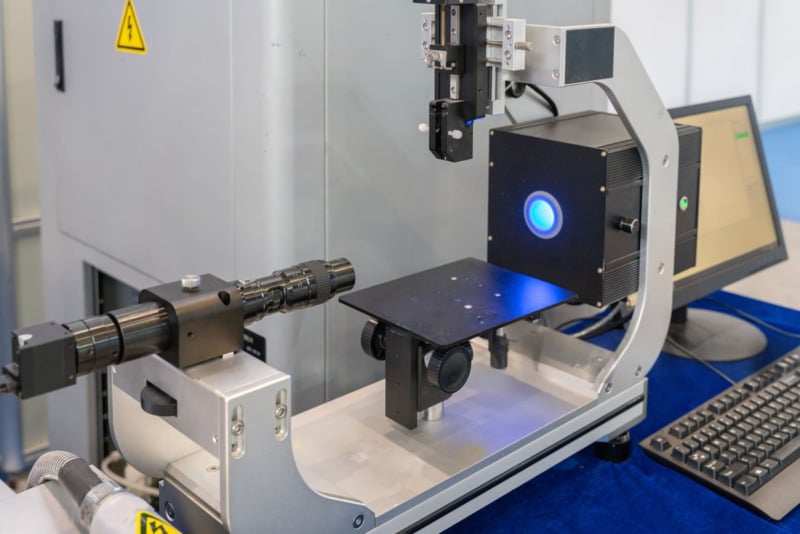
Laser Inspection
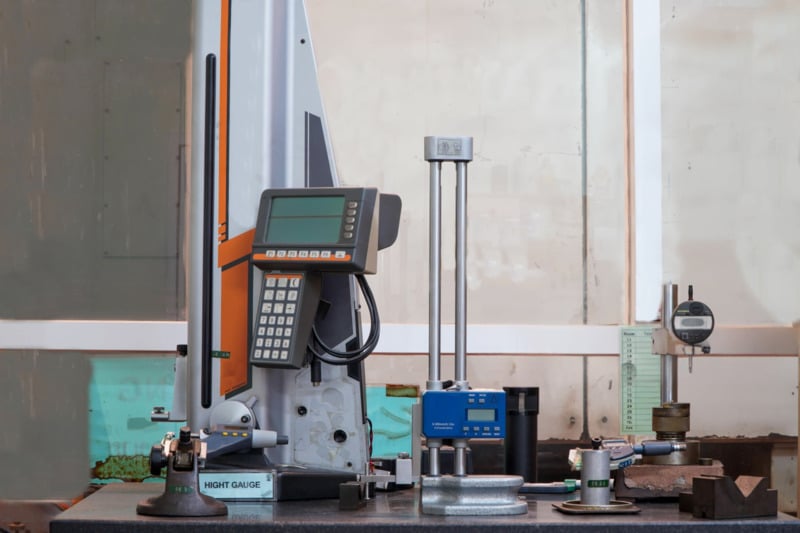
Others
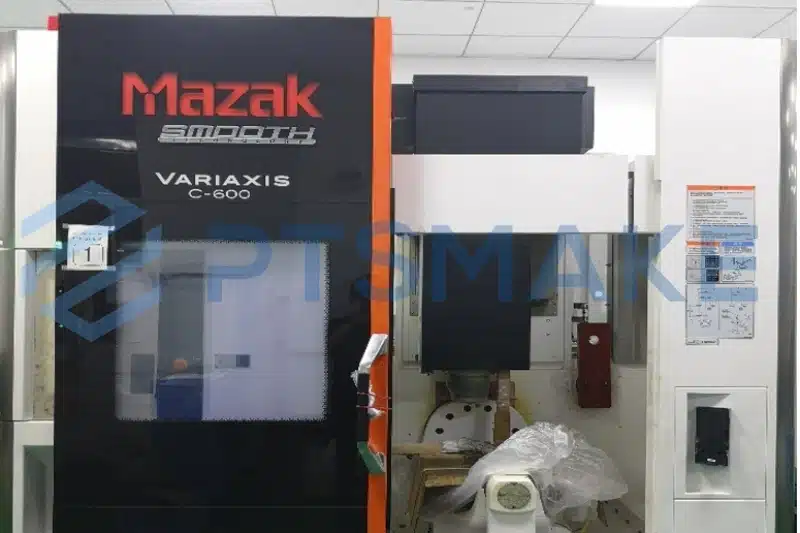
CNC Milling Machine (Japan)
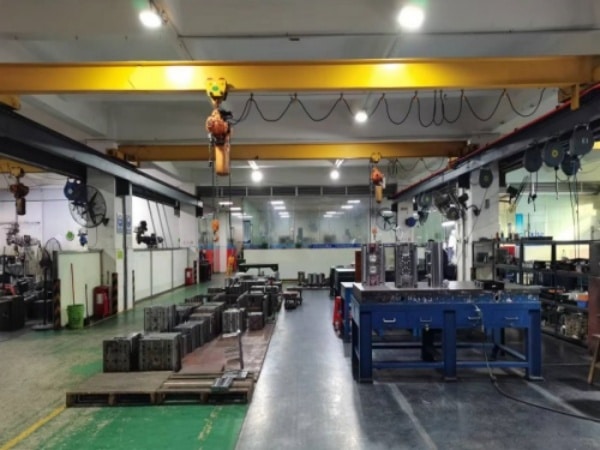
Mold Assembly Shop
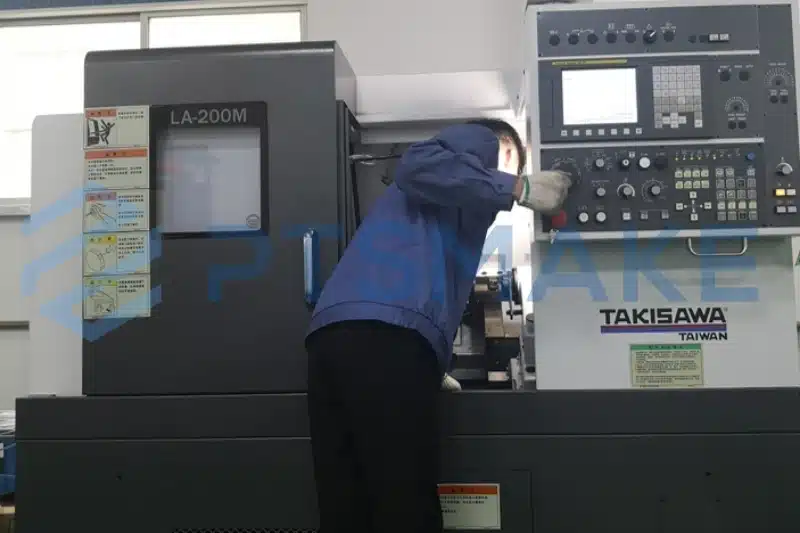
CNC Turning Machine (TaiWan)
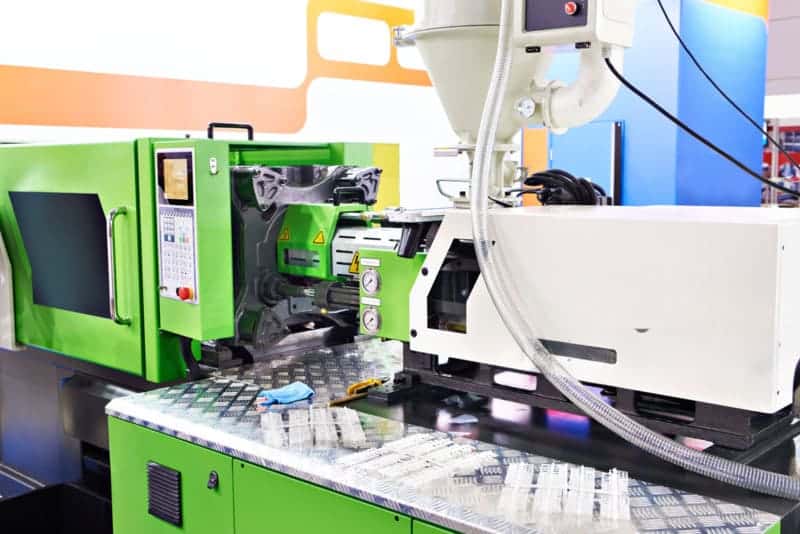
Injection Machine
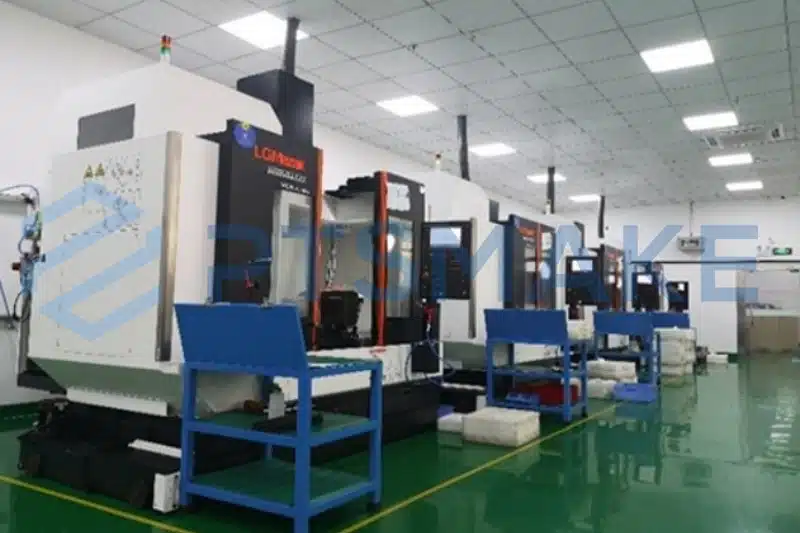
5 Axis Machine (Japan)
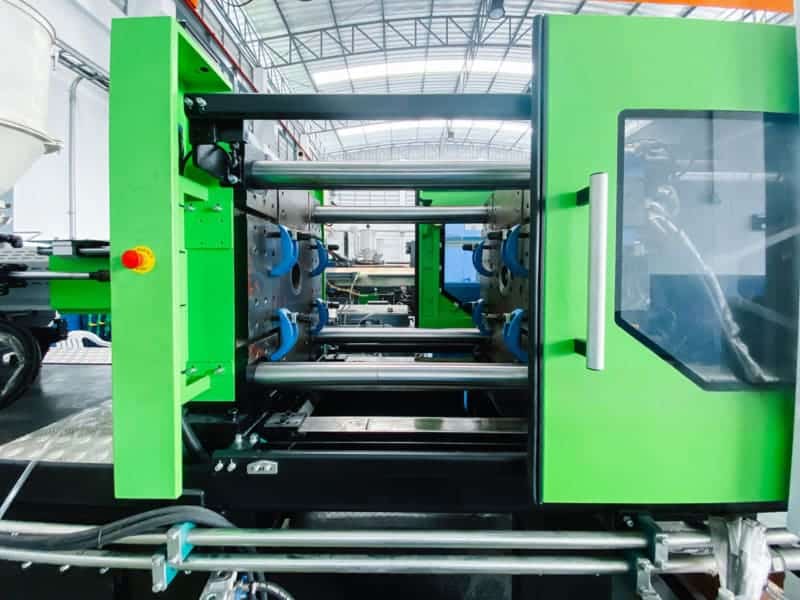
Double-Shot Injection Machine
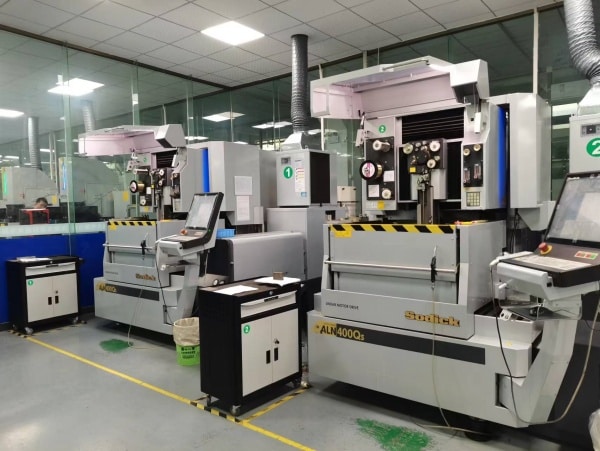
Slow Wire Cut (Japan)
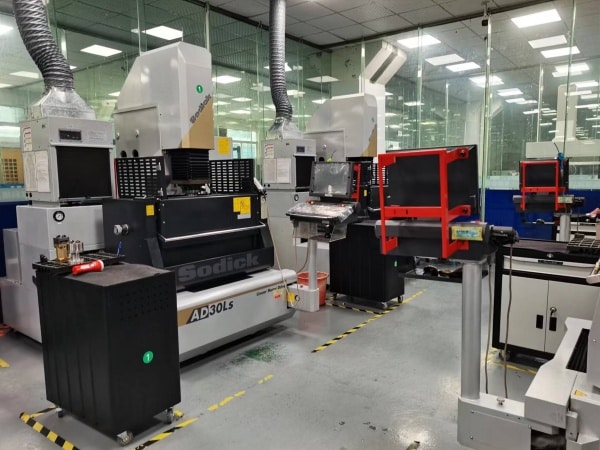
Electric Discharge Machining (Japan)
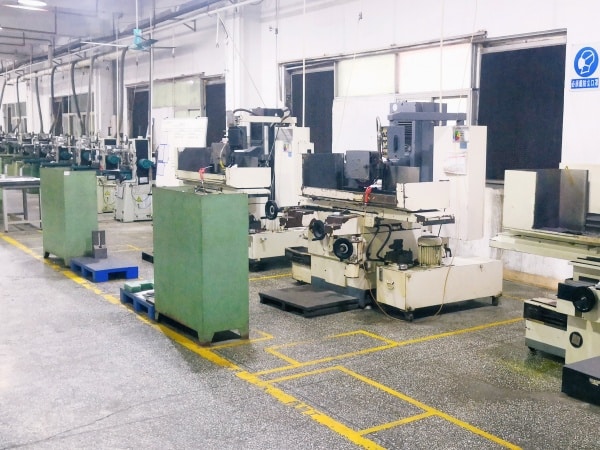
Precision Grinding Machine (Japan)
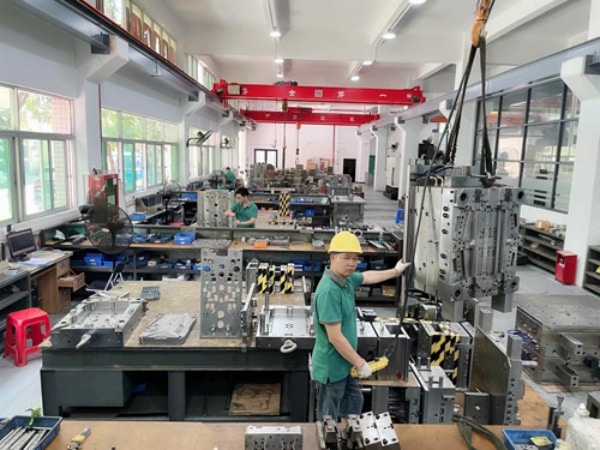
Second Mold Assembly Shop
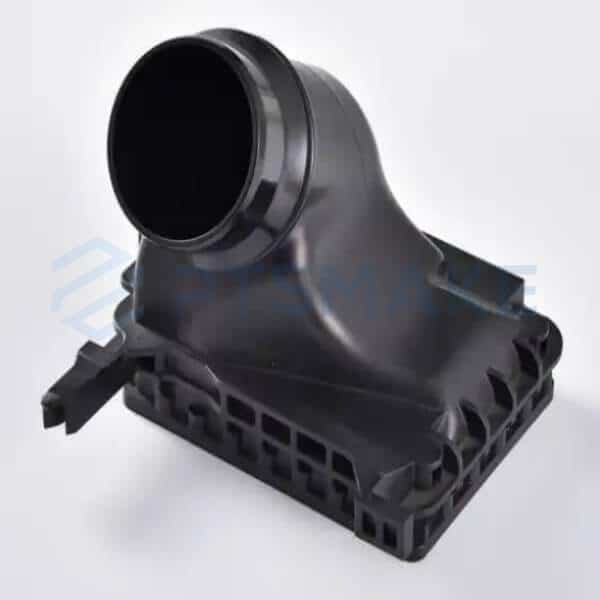
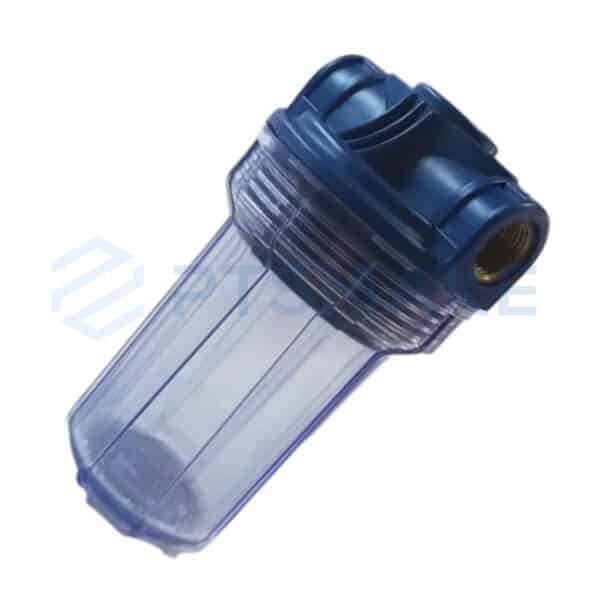
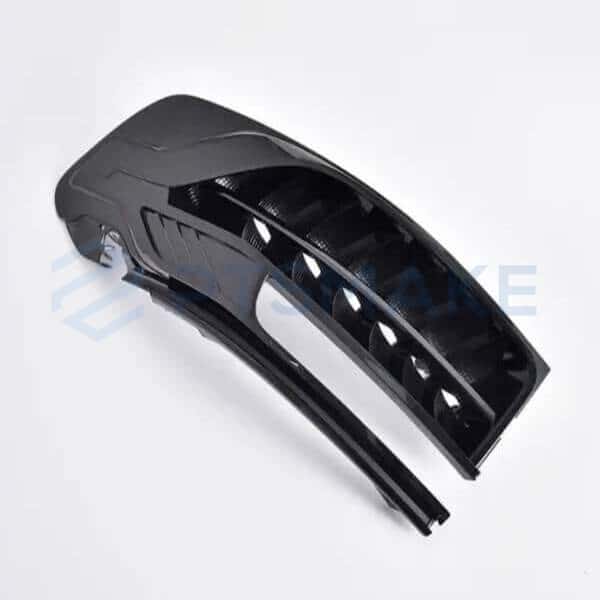
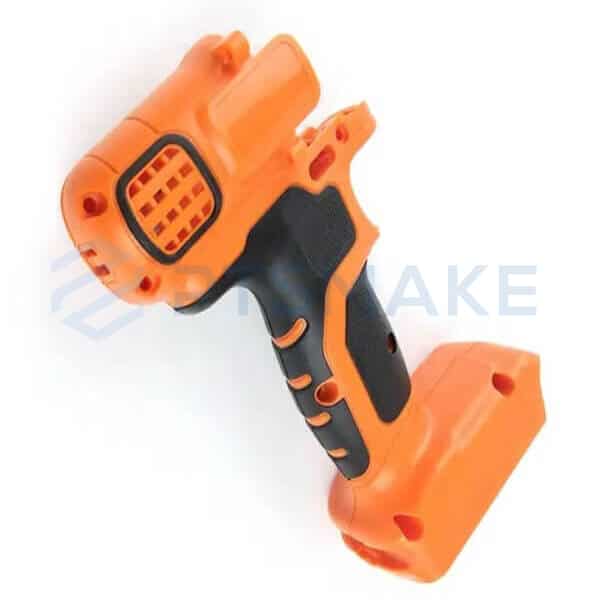
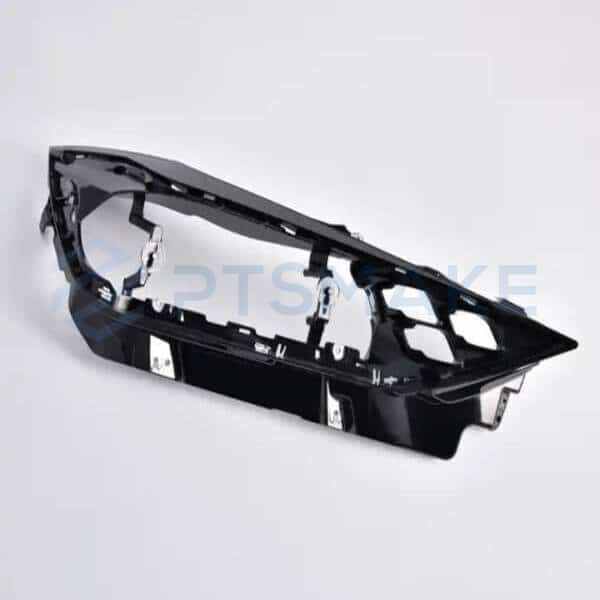
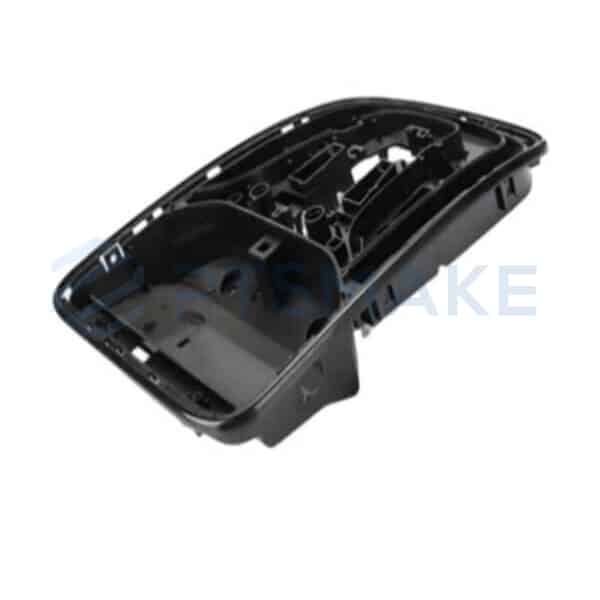
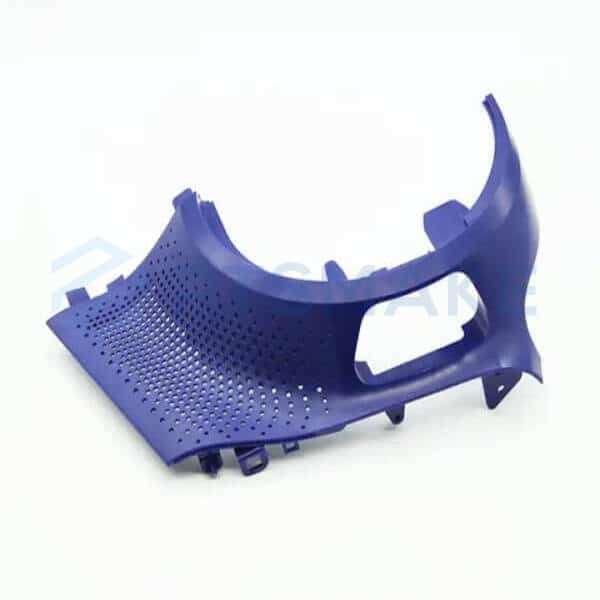
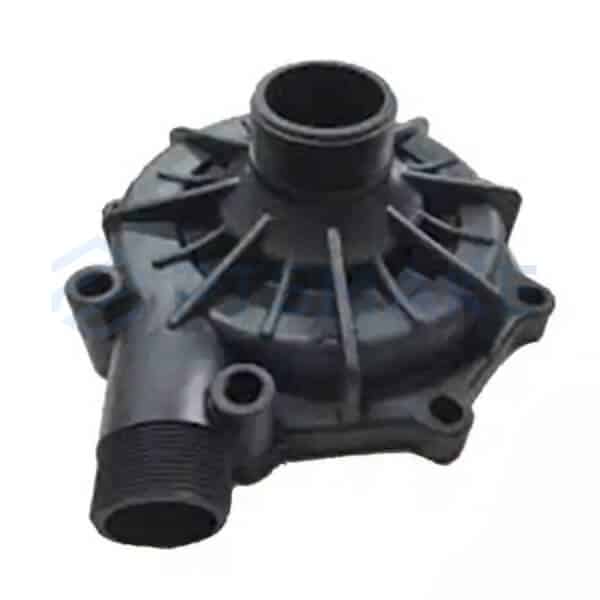
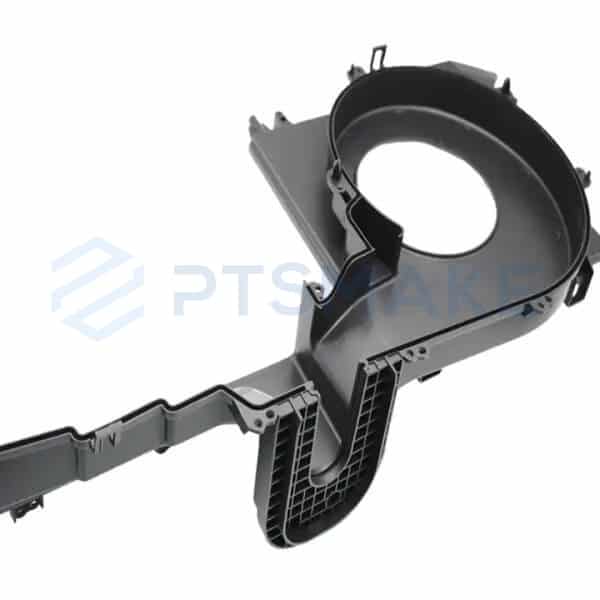
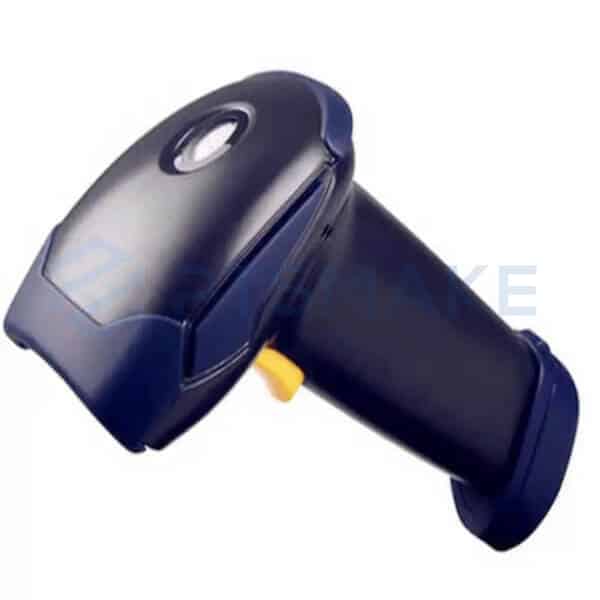
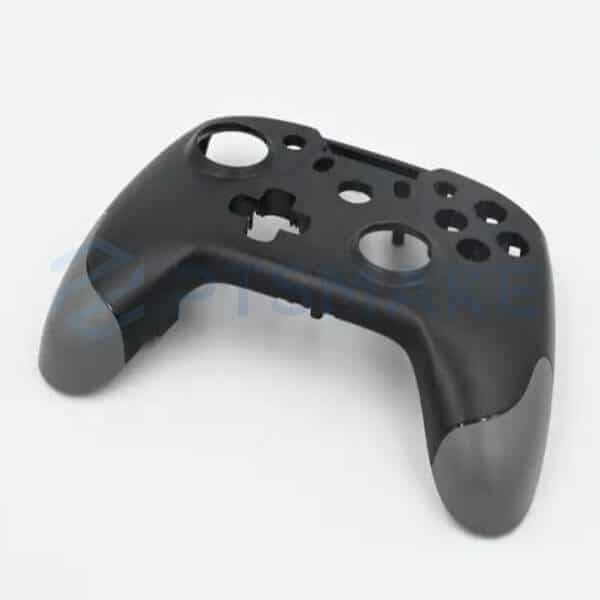
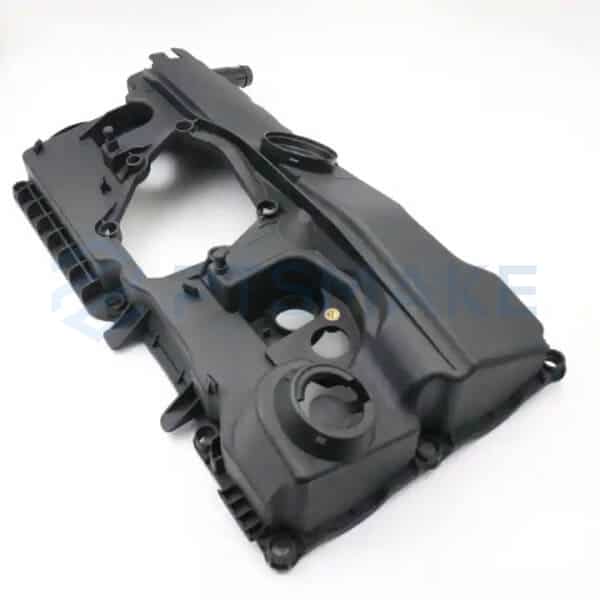
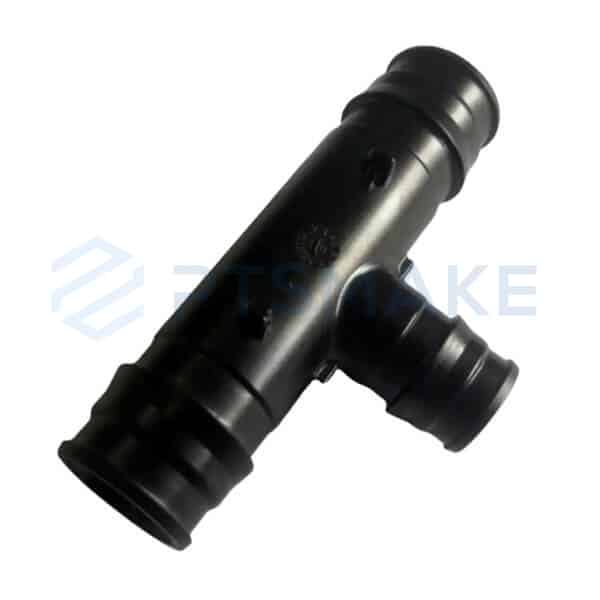
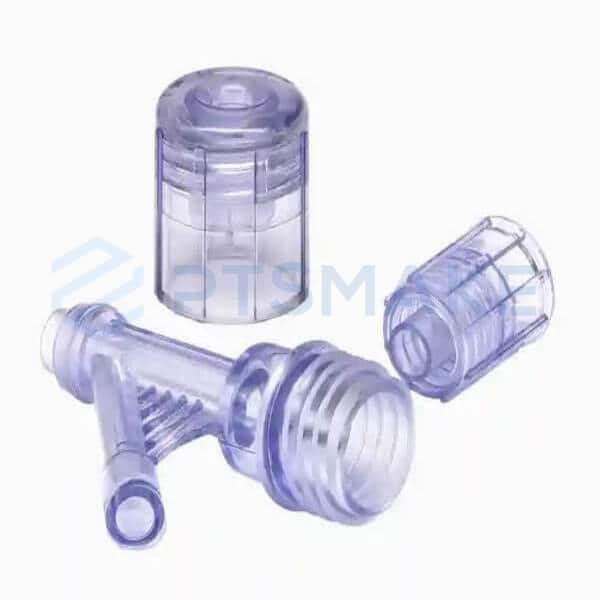
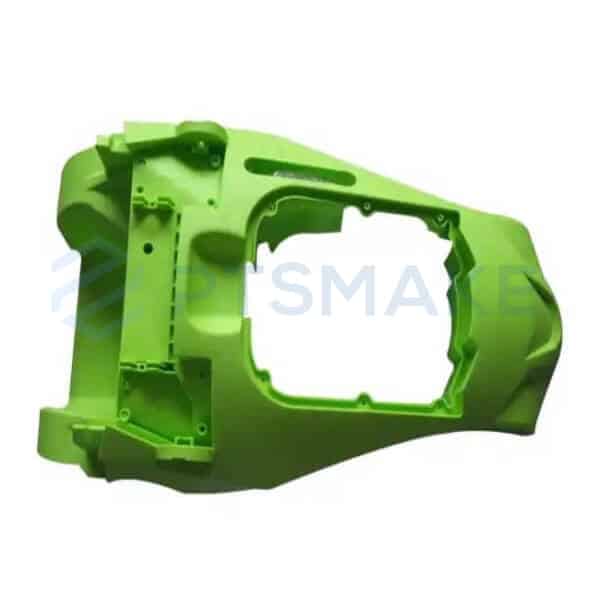
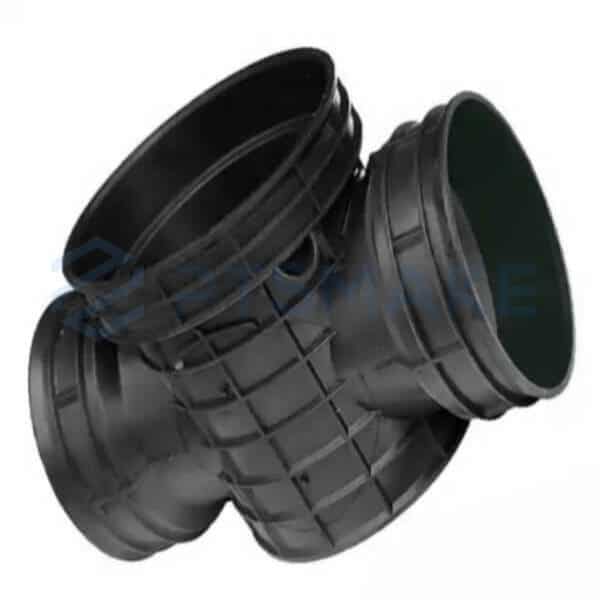
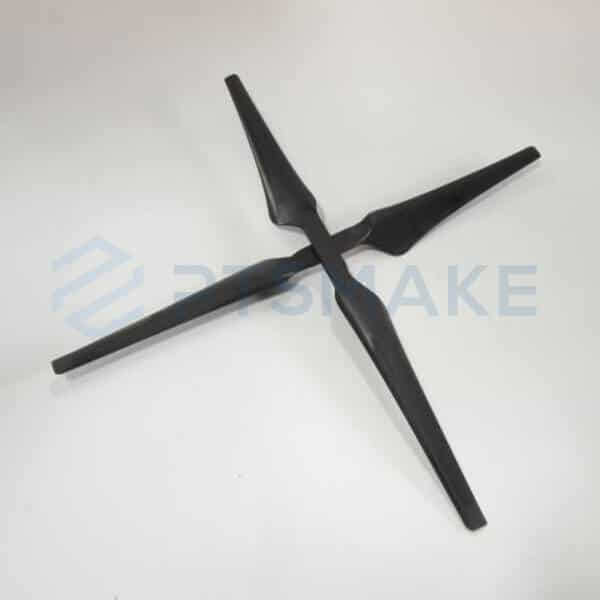
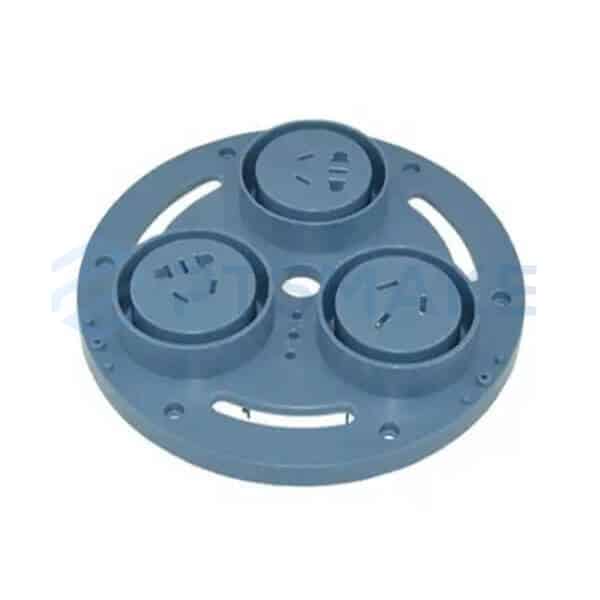
How to Choose the Right Plastic Injection Molds Manufacturer
Choosing the right plastic injection molds manufacturer is crucial for your business. The quality of your molds affects the quality of your final products. Here are some key factors to consider when making this important decision.
- Understand Your Product Requirements: Ensure your supplier knowing your specific needs. Define the type of mold you require, the materials to be used, and the expected production volume. Supplier understanding these details is the most important place to start your project.
- Assess Technical Expertise: Technical skills are crucial for high-quality molds. Ensure the manufacturer has expertise in design, engineering, and production. Skilled technicians contribute to better precision and durability.
- Evaluate Quality Control Measures: Quality assurance is essential. Ask about the manufacturer’s quality control processes. Check if they have certifications like ISO 9001. Strong quality control ensures your molds meet your standards.
- Review Material Selection: The materials used affect mold performance. Confirm that the manufacturer uses high-quality steels and plastics suitable for your application. Proper material selection enhances mold lifespan.
- Check Design Capabilities: Design is the foundation of a good mold. Ensure the manufacturer uses advanced design software. They should be able to provide detailed drawings and simulations before production.
- Understand Production Capacity: Make sure the manufacturer can handle your production needs. Whether you need a single mold or large-scale production, they should have the capacity to deliver on time.
- Evaluate Communication Skills: Effective communication is key to a successful partnership. The manufacturer should be responsive and able to understand your requirements. Good communication reduces errors and delays.
- Ask About Lead Times: Time is critical in production. Inquire about the manufacturer’s lead times for design, production, and delivery. Ensure their timelines align with your project schedule.
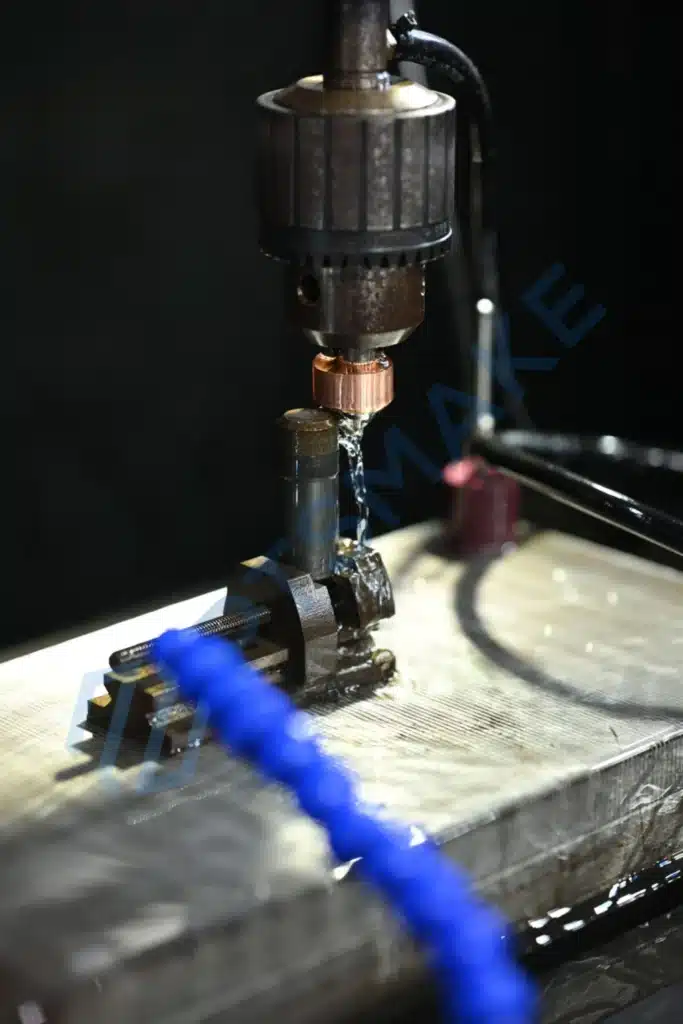
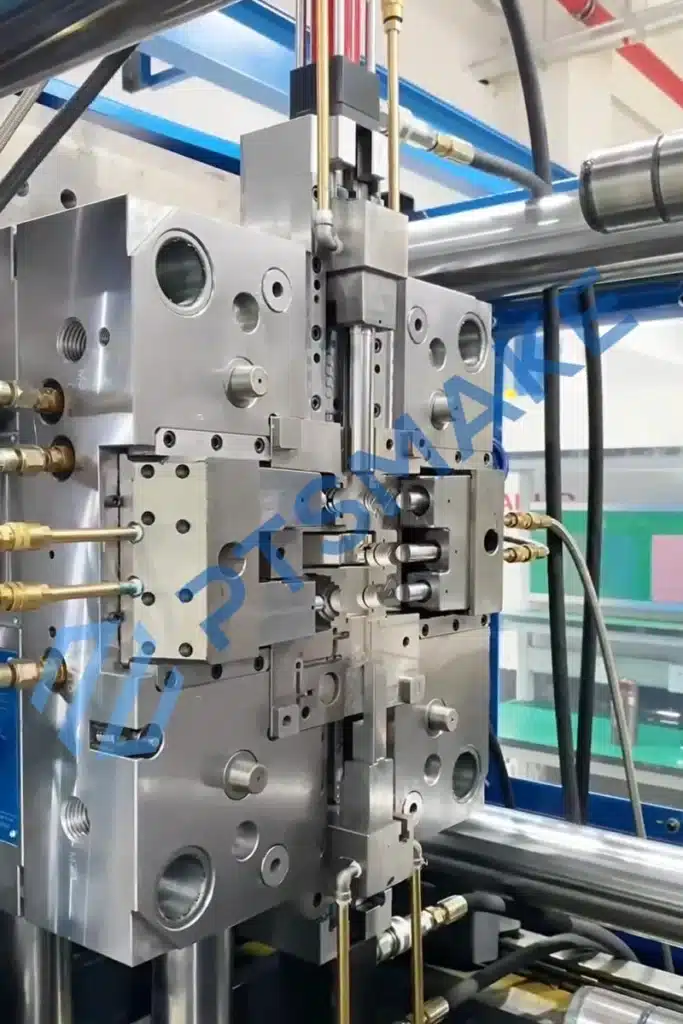
- Review Pricing Structure: Price is an important factor. Request detailed quotes and understand what is included. Look for transparent pricing without hidden costs. Remember that the cheapest option may not offer the best value.
- Consider After-Sales Support: Support after delivery is valuable. The manufacturer should offer assistance with installation, maintenance, and any issues that arise. Good after-sales support contributes to long-term success.
- Look for Flexibility: Your needs may change over time. A flexible manufacturer can adapt to new requirements, whether it’s design modifications or scaling production up or down.
- Check References and Reviews: Ask for references from past clients. Reviews and testimonials provide insights into the manufacturer’s reliability and quality. Positive feedback is a good sign of trustworthy service.
- Evaluate Intellectual Property Protection: Protecting your designs is important. Ensure the manufacturer has policies to safeguard your intellectual property. This prevents unauthorized use or sharing of your proprietary information.
- Test Their Problem-Solving Skills: Manufacturing can involve unexpected challenges. A good manufacturer should demonstrate problem-solving abilities. They should be proactive in finding solutions when issues arise.
- Consider Long-Term Partnership Potential: Think about the future. A manufacturer interested in a long-term relationship is more likely to invest in your success. Long-term partnerships can lead to better pricing and priority service.
- Review Technology Adoption: Manufacturing technology evolves quickly. A manufacturer that keeps up with the latest advancements can offer better quality and efficiency. Ask about their investment in new technologies.
What Sets Us Apart
You need molds that meet your exact specifications. This ensures your products are consistent, reliable, and of the highest quality.
Timely delivery is crucial for your production schedule. Receiving molds on time helps you avoid delays and extra costs.
You value prompt and transparent communication. Quick responses to your questions keep you informed at every step.
Fair and honest pricing matters to you. Getting good value without hidden fees helps you manage your budget effectively.
"Working with PTSMAKE has transformed our manufacturing process. Their plastic injection molds are of exceptional quality and precision. The molds integrated seamlessly with our equipment, improving our product consistency significantly. The team at PTSMAKE listened to our needs and delivered everything ahead of schedule. Their dedication to excellence is clear in every interaction we've had.
Liam O'Connor, Manufacturing Director, Ireland"
Plastic Injection Molds Making Capabilities
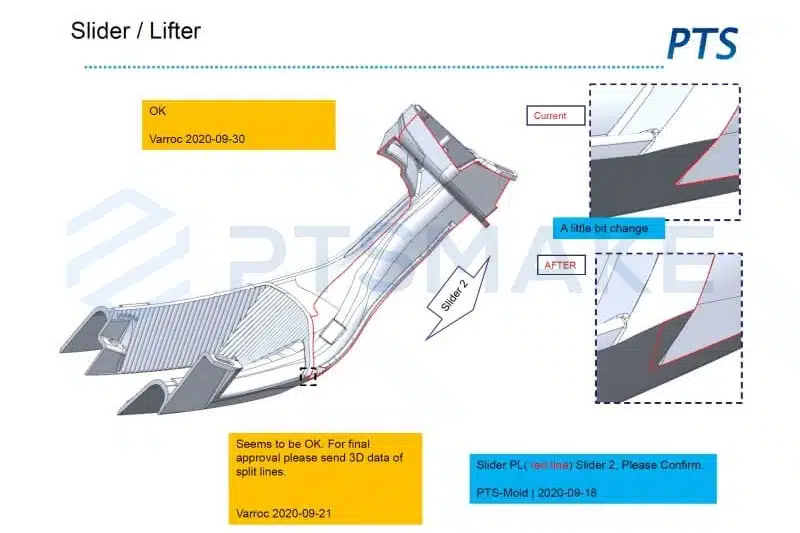
DFM
We examine your product design to make manufacturing simple, helping you save time and money.
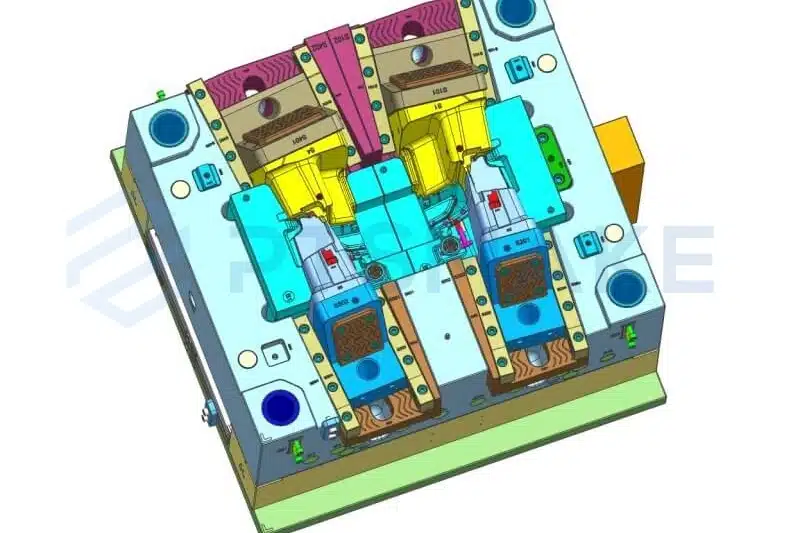
Mold Design
Our design team ensures every detail aligns with your production needs for high-quality results.
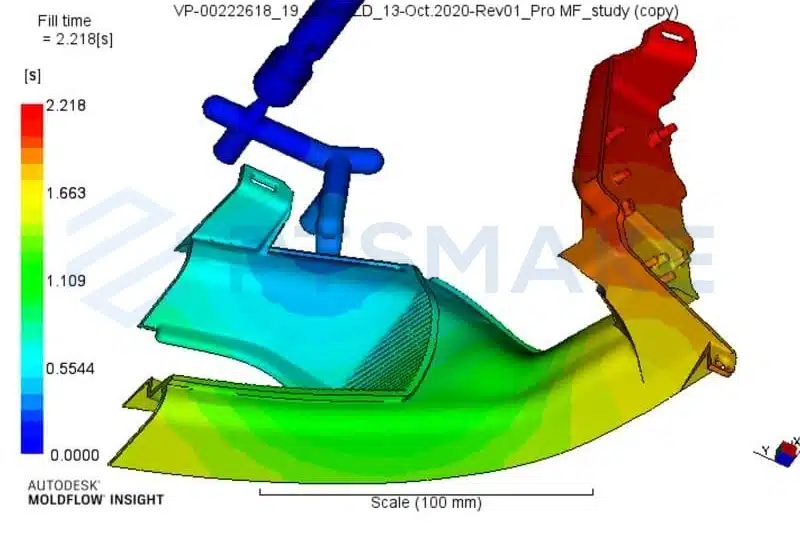
Mold Flow Analysis
We study how plastic flows in the mold to prevent defects, giving you better quality parts.
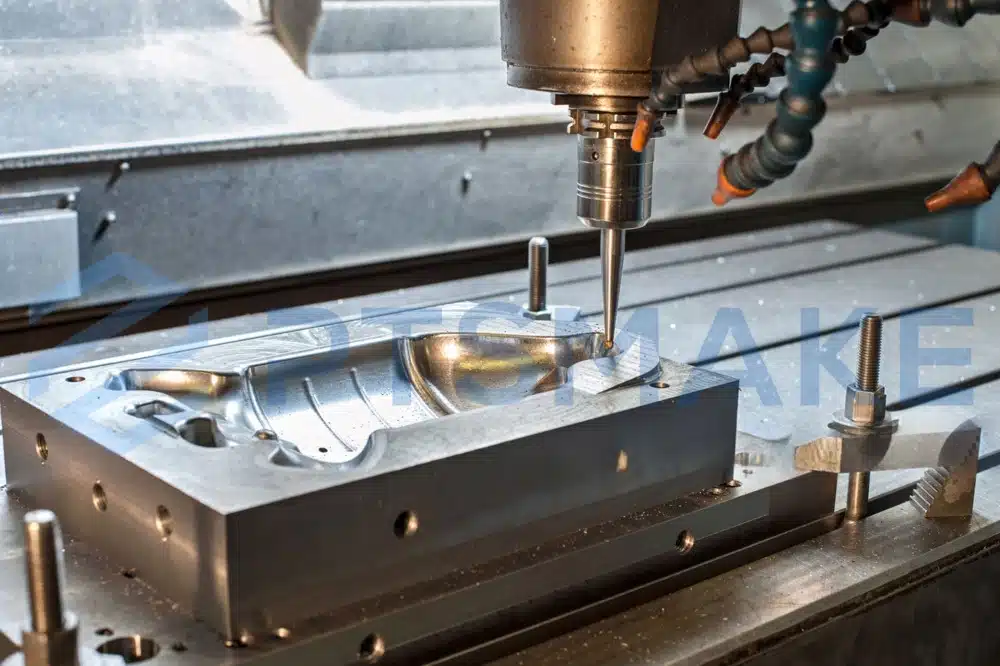
Mold Making
We build precise molds with advanced equipment, providing tools that produce accurate parts every time.
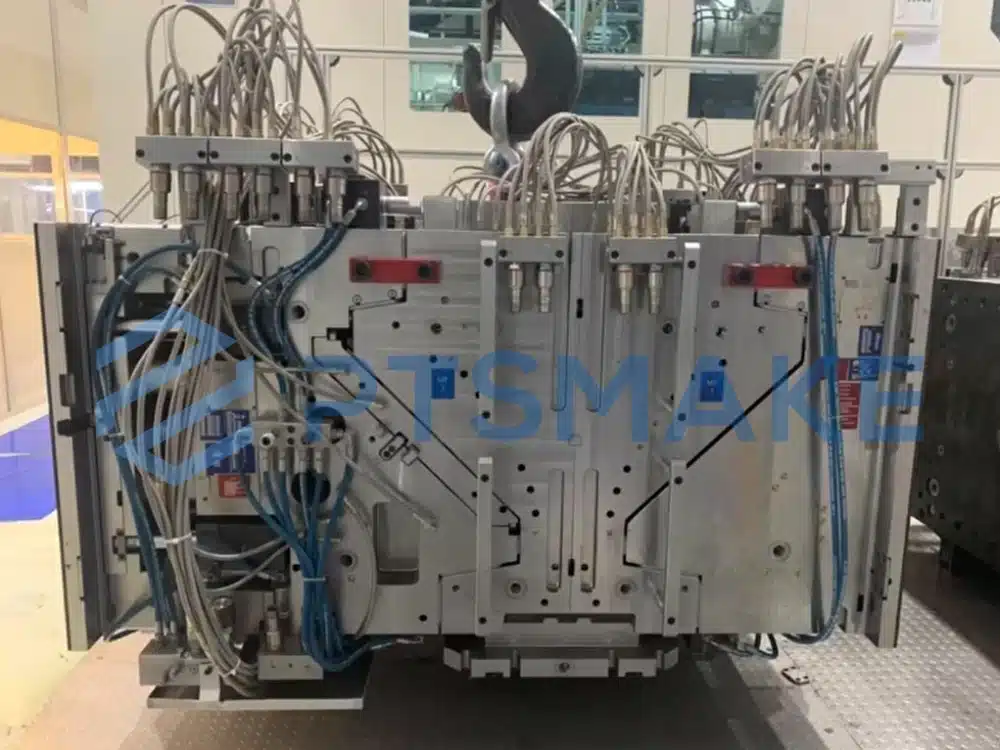
Complex Mold Making
We specialize in creating complex molds for intricate parts, meeting your challenging production needs.
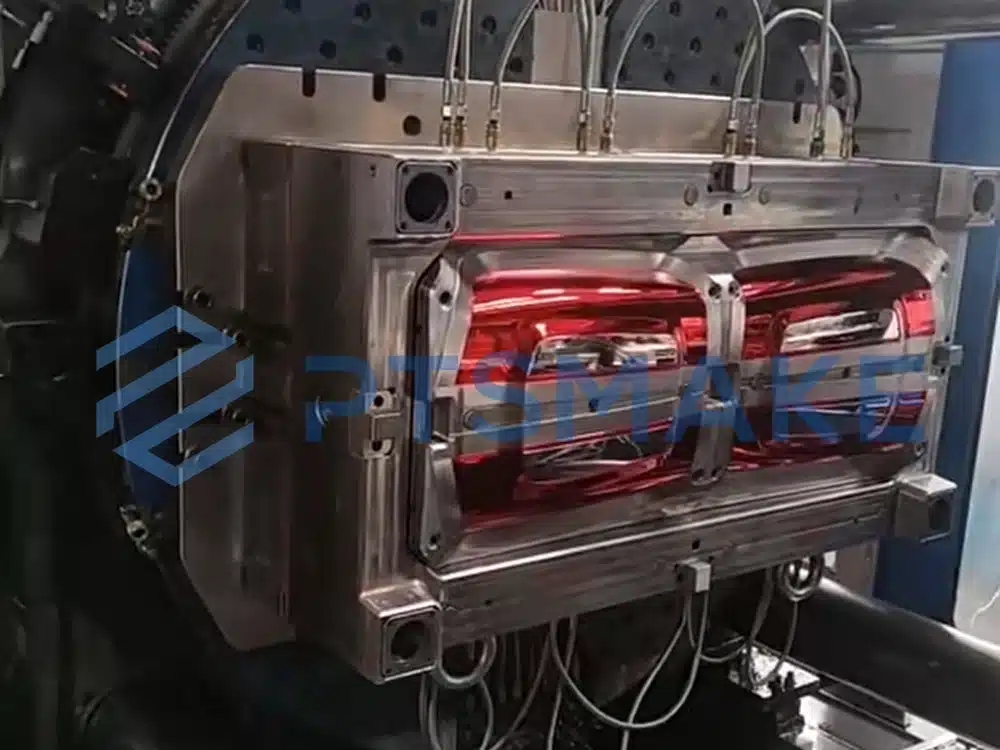
Two-Shot Mold Making
We make molds for two-shot molding, allowing you to produce parts with two materials in a single process.
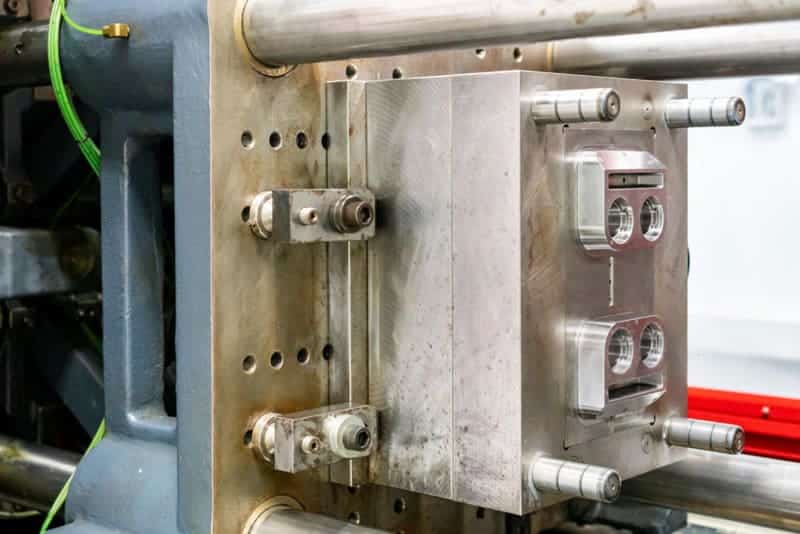
Mold Trial and Debug
We thoroughly test and adjust molds to fix issues, ensuring smooth and problem-free production for you.
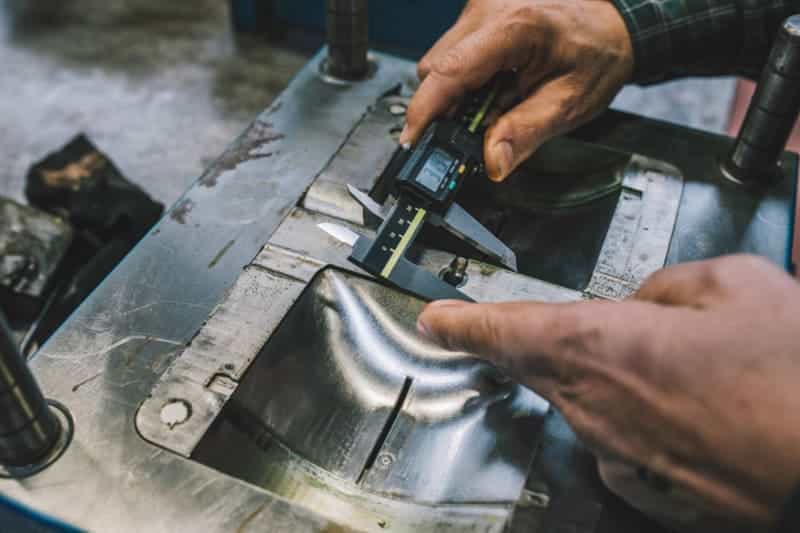
Mold Repair and Maintenance
We offer services to fix and maintain your molds, keeping them in top condition and extending their life.
Mold Steel and Mold Accessories
When selecting injection molds suppliers, the quality of the steel and accessories is crucial. High-quality materials lead to durable molds and consistent products. Understanding the importance of material sources and standards can help you make the best choice for your manufacturing needs.
High-Quality Mold Steel
Using imported steel from reputable suppliers ensures the mold’s durability and stability. Brands like ASSAB, BÖHLER, LKM, Finkl and DAIDO are known for their superior steel quality. These steels offer:
- Exceptional Durability: They resist wear and deformation, extending the mold’s lifespan.
- Consistent Performance: High-quality steel maintains its properties under production stresses.
- Precision Machinability: Superior steels allow for precise mold making, resulting in accurate parts.
Benefits of Imported Steel
- Strict Quality Control: Ensuring the steel meets international standards.
- Material Certifications: Providing assurance of the steel’s composition and properties.
- Proven Track Record: These steels are widely used and trusted in the industry.
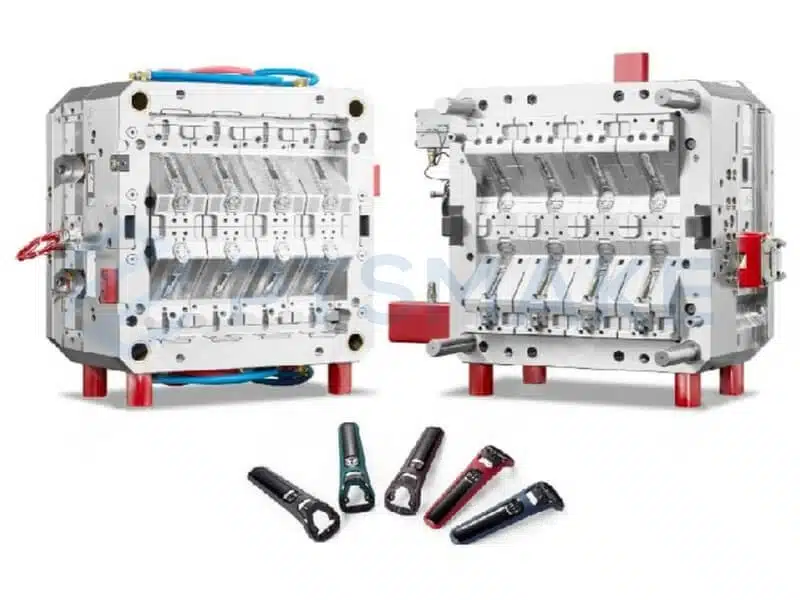
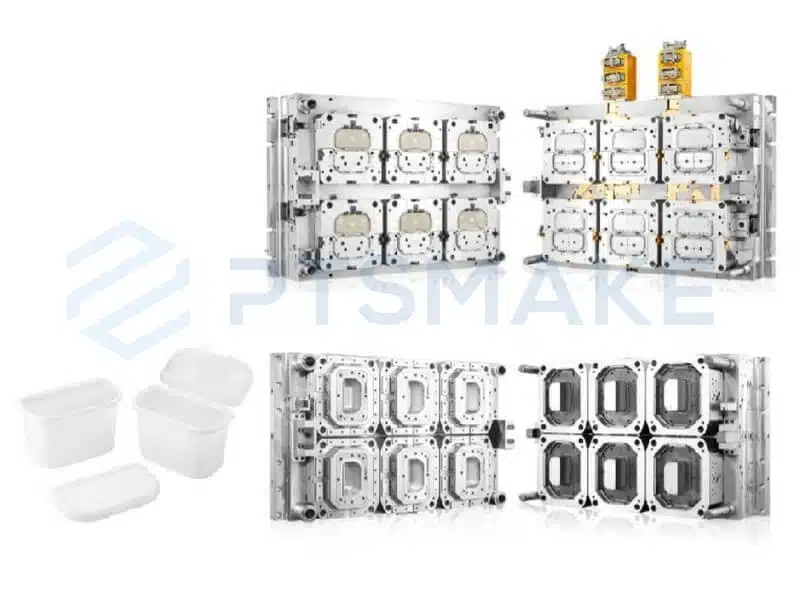
Standards-Compliant Mold Accessories
Mold accessories play a vital role in the mold’s operation and longevity. Using accessories that comply with US and international standards ensures compatibility and reliability. Brands such as HASCO and DME offer:
- High-Quality Components: Made with precision to fit and function perfectly.
- Global Standards Compliance: Ensuring that parts meet industry norms for interchangeability.
- Reliable Performance: Reducing downtime caused by component failures.
Why Choose Standardized Accessories
- Ease of Replacement: Standard parts are readily available and easy to source.
- Consistent Quality: Well-known brands maintain high production standards.
- Compatibility: Standardized components fit seamlessly into existing systems.
Cost of Plastic Injection Molds
Understanding the cost of plastic injection molds is important for businesses planning production. Knowing what affects the price helps you make informed decisions and manage expenses effectively.
Factors That Influence Mold Cost
- Size of the Mold: Larger molds need more material and time to build, which increases cost.
- Complexity of the Design: Complex designs require more work and precision, leading to higher prices.
- Number of Cavities: Molds with more cavities produce more parts per cycle but are more expensive to manufacture.
- Type of Mold Material: Materials like hardened steel last longer but cost more than softer metals.
- Surface Finish Requirements: Special surface textures or high-gloss finishes add to the cost due to extra processing steps.
- Brand of Mold Accessories: Using accessories from reputable brands can improve quality but may increase the initial cost.
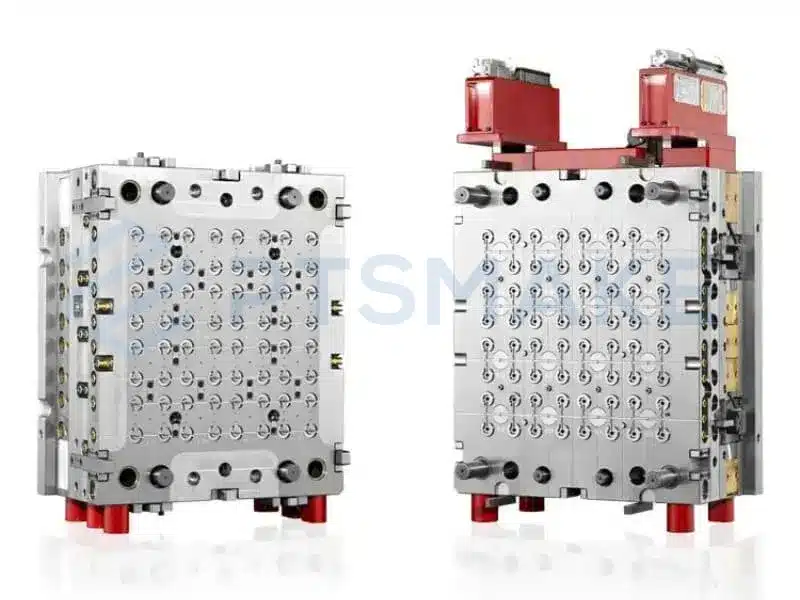
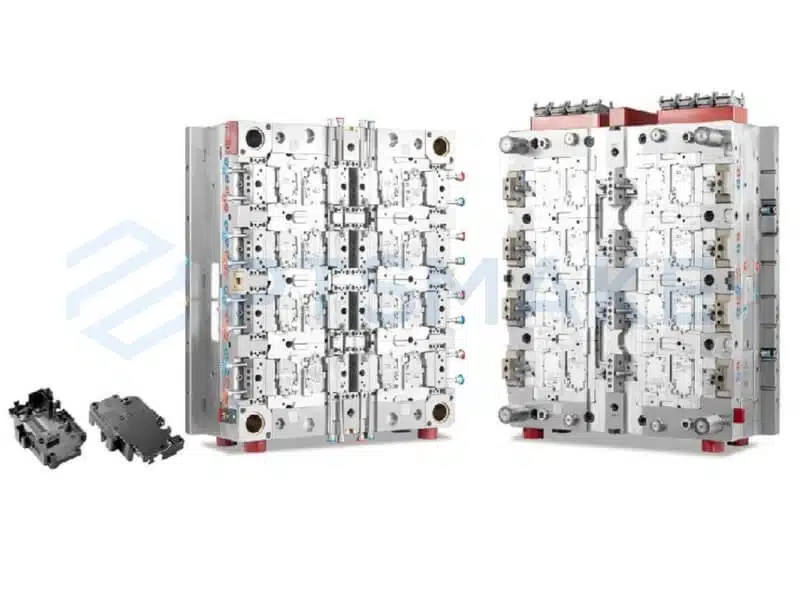
Material Selection and Cost Impact
- Hardened Steel: Offers long life and is suitable for high-volume production but has a higher upfront cost.
- Pre-Hardened Steel: Less costly than hardened steel and good for medium-volume production.
- Aluminum: Ideal for prototypes or low-volume production due to lower cost but wears out faster.
Design Complexity and Cost
- Intricate Features: Small details or complex shapes need precise machining, increasing cost.
- Undercuts and Side Actions: Features that prevent the part from releasing easily require special mechanisms in the mold.
- Tight Tolerances: Demanding high precision raises manufacturing time and costs.
Mold Accessories Brands and Cost
- Reputable Brands: Accessories from well-known brands like HASCO or DME meet international standards and offer high reliability. They may cost more but provide consistent performance.
- Generic Brands: Cheaper options might save money upfront but could lead to issues like poor fit or shorter lifespan.
- Quality vs. Cost: Investing in quality accessories can reduce downtime and maintenance costs over time.
Mold Lifespan Considerations
- High-Volume Production: Requires durable molds made from high-quality materials to withstand wear.
- Low-Volume Production: May allow for cheaper materials since the mold will be used less frequently.
- Maintenance Needs: Regular maintenance can extend mold life but adds to overall costs.
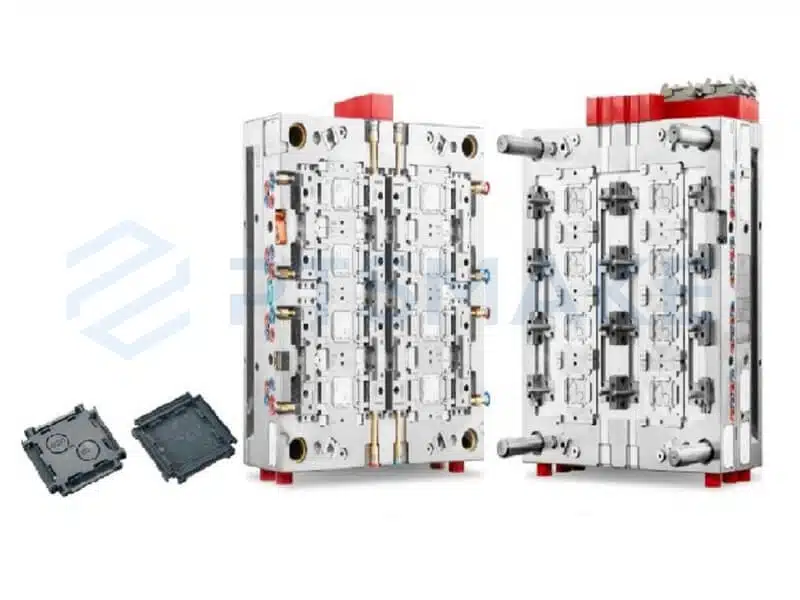
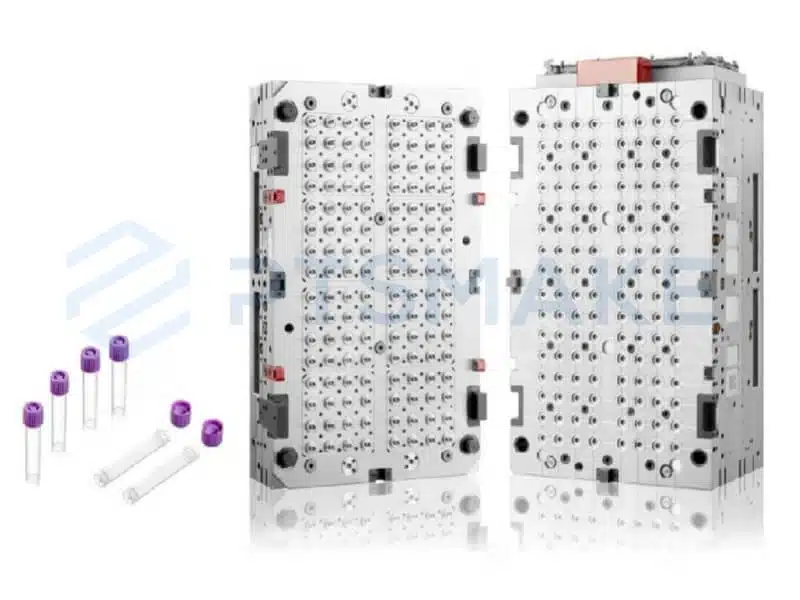
Ways to Manage and Reduce Costs
- Collaborate on Design: Work with mold makers to optimize the design for cost-effectiveness.
- Select Suitable Materials: Choose mold materials that fit your production volume and budget.
- Consider Multi-Cavity Molds: If high production is needed, more cavities can reduce the cost per part over time.
- Evaluate Accessory Brands: Balance the cost and quality of mold accessories to find the best value.
- Get Detailed Quotes: Ask for breakdowns in quotes to understand where costs are coming from.
- Plan Ahead: Allowing adequate time for mold making can avoid rush fees and allow for cost-saving options.
The cost of plastic injection molds depends on many factors including size, design, material, and the brands of accessories used. By understanding these factors, you can make decisions that balance quality and cost. Investing in reputable mold accessories like HASCO or DME ensures reliability but may increase initial expenses. Careful planning and collaboration with experienced mold makers can lead to significant savings and successful production outcomes.
Request a Custom Quote Today
Get an accurate estimate for your injection molds project. Let us help you meet your exact specifications.
Balancing Quality and Cost in Plastic Injection Molds
Creating plastic injection molds requires careful planning. As a buyer, you want high-quality molds that fit your budget. Balancing quality and cost is crucial for successful production.
1. Understanding Your Production Needs
Before making decisions, consider:
- Production Volume: How many parts do you need? Large quantities may justify higher initial costs for durable molds.
- Product Complexity: Does your design have intricate details? Complex molds can cost more due to precision requirements.
- Material Compatibility: What plastic materials are you using? Some plastics may need specialized molds, affecting cost.
By understanding your needs, you can make choices that balance cost and quality.
2. Choosing the Right Mold Steel
The mold material impacts both quality and price:
- Hardened Steel Molds: Best for high-volume production. They offer longevity but have higher upfront costs.
- Pre-Hardened Steel Molds: Suitable for medium-volume runs. They are less expensive but may wear out sooner.
- Aluminum Molds: Ideal for prototypes or low-volume production. They cost less but have a shorter lifespan.
Selecting the appropriate material helps control costs while meeting quality standards.
3. Optimizing Mold Design
Design affects both the functionality and cost of the mold:
- Simplify the Design: Remove unnecessary features to reduce complexity and cost.
- Use Standard Components: Standardized parts are cheaper and readily available.
- Collaborate with Experts: Working with mold designers can optimize the design for efficiency and cost savings.
An optimized design can maintain quality while reducing expenses.
4. Considering Mold Base Options
The mold base is the foundation of the mold:
- Standard Mold Bases: Using standard sizes can reduce costs and lead times.
- Custom Mold Bases: Necessary for unique designs but increase cost.
- Material Choice: The material of the mold base affects durability and price.
Choosing the right mold base aligns your needs with your budget.
5. Selecting Mold Accessories Wisely
Accessories play a vital role in mold performance:
- Consider Reputable Brands: High-quality accessories may cost more but offer reliability and longevity.
- Balance Cost and Quality: Evaluate if premium accessories provide benefits that justify the additional cost.
- Ensure Compatibility: Compatible accessories prevent issues during production, saving time and money.
Choosing the right accessories contributes to overall efficiency and cost management.
6. Evaluating Suppliers
Your choice of supplier can impact quality and cost:
- Experience Matters: Suppliers with a proven track record can deliver quality molds but may charge more.
- Technical Support: Suppliers offering support can help troubleshoot issues, saving costs in the long run.
- Quality Assurance: Ensure the supplier follows quality standards to avoid defects and rework.
Selecting a reliable supplier balances initial costs with long-term benefits.
7. Long-Term Cost Considerations
Look beyond the initial price tag:
- Durability and Lifespan: Investing in quality molds may reduce costs over time due to fewer replacements.
- Maintenance Needs: High-quality molds often require less maintenance, saving money.
- Production Efficiency: Quality molds can improve cycle times and reduce waste.
Considering long-term factors helps in making cost-effective decisions.
Balancing quality and cost in plastic injection molds is a strategic process. By understanding your needs, optimizing design, choosing suitable materials and accessories, and selecting the right supplier, you can achieve the desired balance. Making informed decisions ensures that you get quality molds without exceeding your budget.
Lead Time of Plastic Injection Molds
The lead time for plastic injection molds is a crucial aspect of any manufacturing project. It refers to the period from the initial design phase to the completion of the mold ready for production. By understanding this timeline, we can plan our projects more effectively and meet market demands on schedule.
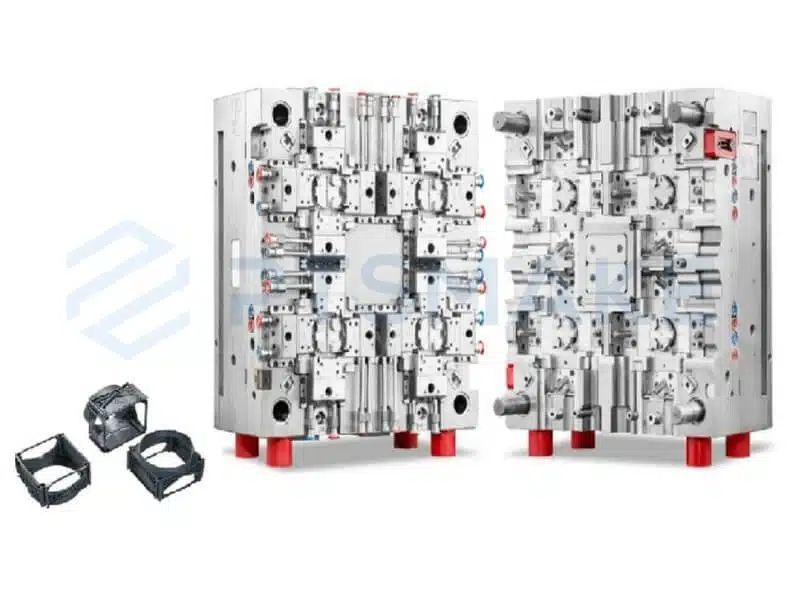
Factors Influencing Lead Time
Several factors can affect the lead time of plastic injection molds:
- Design Complexity: Complex designs with intricate details require more time to produce. Simplifying the design where possible can help reduce the lead time.
- Mold Size and Type: Larger molds or those with multiple cavities take longer to manufacture. The type of mold, whether it’s a prototype or production mold, also impacts the timeline.
- Material Selection: The choice of materials for the mold and the final product influences the production process. Using readily available materials can shorten procurement times.
- Manufacturing Techniques: Advanced techniques like CNC machining and EDM offer precision but may add to the production time.
- Supply Chain Factors: Delays in obtaining necessary components or materials can extend the lead time. Efficient supply chain management is essential.
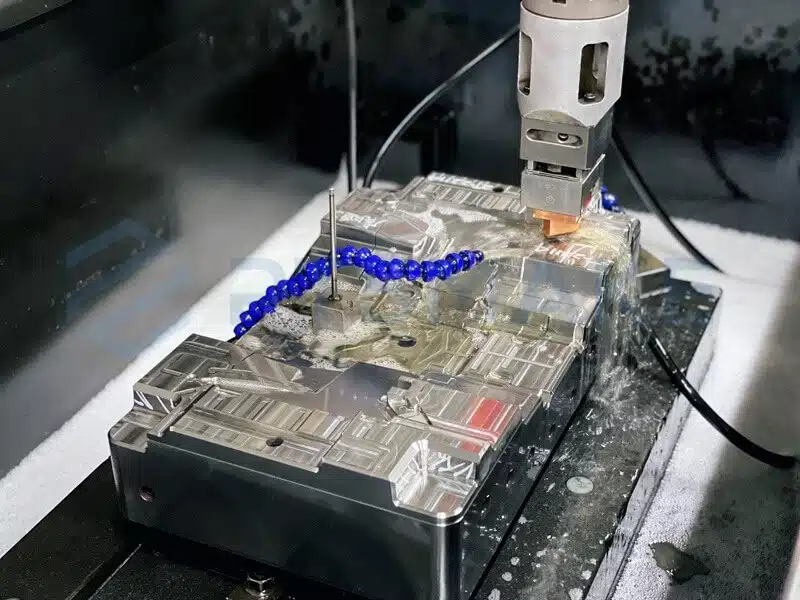
Reducing Lead Time
We can implement strategies to minimize lead time:
- Early Design Finalization: Finalizing the design before production begins prevents delays caused by changes during the manufacturing process.
- Collaborative Planning: Working closely with the manufacturing team ensures that all requirements are clear, reducing misunderstandings and rework.
- Efficient Communication: Maintaining open and regular communication helps us address issues promptly and keep the project on track.
- Material Availability: Selecting materials that are in stock or have short lead times can expedite the production process.
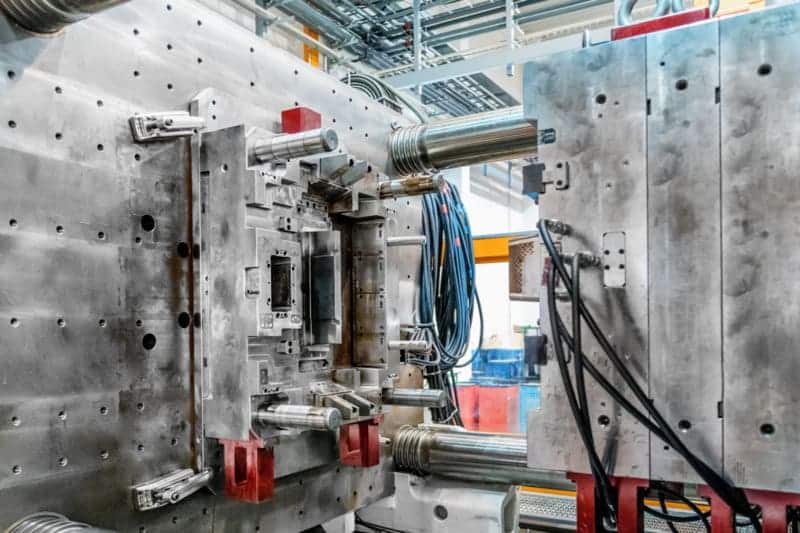
Planning for Success
Proactive planning is key to managing lead times effectively. By considering all factors that influence the timeline, we can make informed decisions that keep our projects moving forward. Collaboration with all stakeholders ensures that everyone is aligned and working towards the same goals.
Our Production Capacity of Plastic Injection Molds
When you have a large order to fulfill, you need a supplier who can keep up. Understanding the production capacity of plastic injection molds is important. It helps you know if deadlines can be met and if quality will stay high.
Advanced Manufacturing Facilities
Our state-of-the-art facilities are equipped with over 100+ advanced machines. This extensive setup allows us to produce up to 60 molds per month. By operating multiple machines simultaneously, we ensure a high output rate without compromising on precision or quality.
Skilled Workforce
We have a dedicated team of over 100 skilled professionals. Their expertise and attention to detail are crucial in maintaining a smooth production process. Our team works in shifts to keep the production line running 24/7. This round-the-clock operation maximizes our efficiency and output.
Efficient Production Processes
- Rapid Tooling Techniques: We utilize rapid tooling to reduce the time it takes to produce molds. This means we can start production faster.
- Automated Systems: Automation in key areas speeds up production and reduces the potential for errors.
- Lean Manufacturing Principles: By minimizing waste and streamlining workflows, we can deliver products faster.
Quality Assurance at Scale
- In-Line Inspection: Continuous monitoring during production catches issues immediately.
- Final Quality Control: Detailed inspections after production ensure each mold meets your specifications.
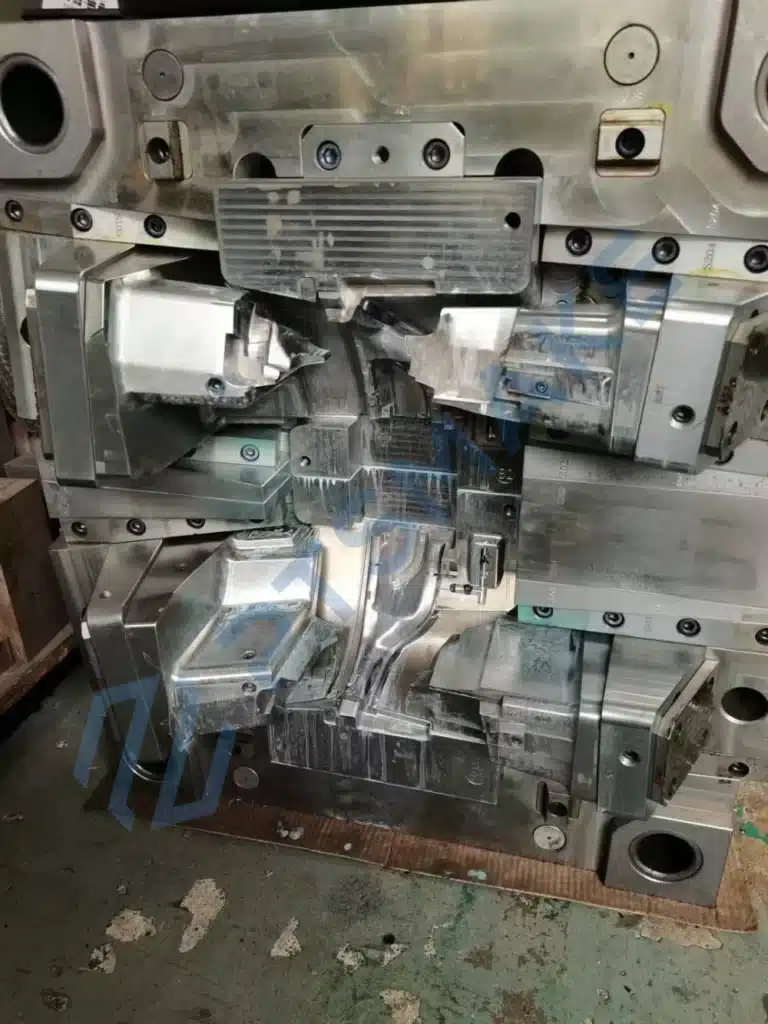
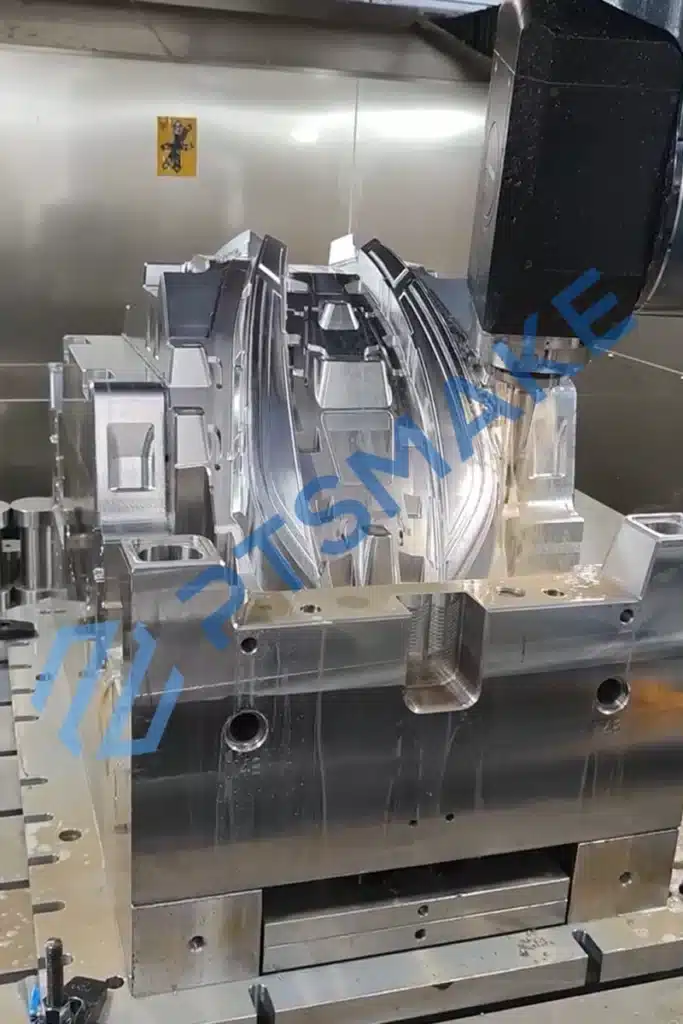
Flexible Scaling for Your Needs
We understand that business needs can change rapidly. Our production capacity is flexible:
- Scalable Output: We can increase our output to 100 molds per month during peak demand periods.
- Customization Capability: Even with high volumes, we offer customization options to meet your specific requirements.
Global Supply Capability
- Efficient Logistics: We have established logistics processes to handle international shipments promptly.
- Experience with Export Regulations: Familiarity with export procedures ensures smooth delivery to countries like the US, Germany, and more.
Supporting Your Business Growth
- On-Time Delivery: Our capacity ensures that we meet your schedules.
- Consistent Quality: High-quality molds contribute to the reliability of your products.
- Competitive Advantage: With our support, you can respond quickly to market demands.
Choosing a supplier with significant production capacity is crucial for your business success. Our ability to produce large volumes of plastic injection molds quickly and efficiently makes us the ideal partner for your needs. We’re committed to supporting your projects and helping your business thrive.
Contact Plastic Injection Molds Expert Today!
We look forward to the opportunity to work with you and contribute to your project’s success.
The Plastic Injection Molds Manufacturing Process?
Understanding how molds are made helps you make informed decisions. Here are eight key steps in the mold manufacturing process.
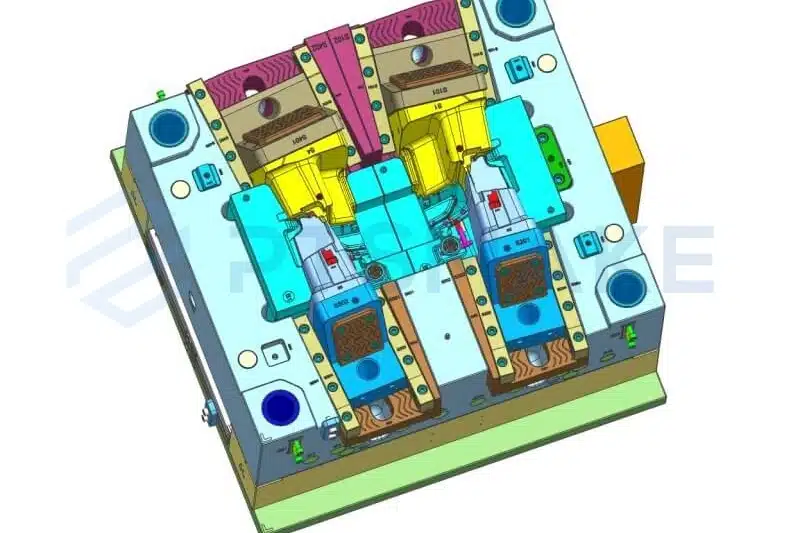
1. Designing the Mold
We design molds that match your specifications, ensuring accurate dimensions and optimal functionality.
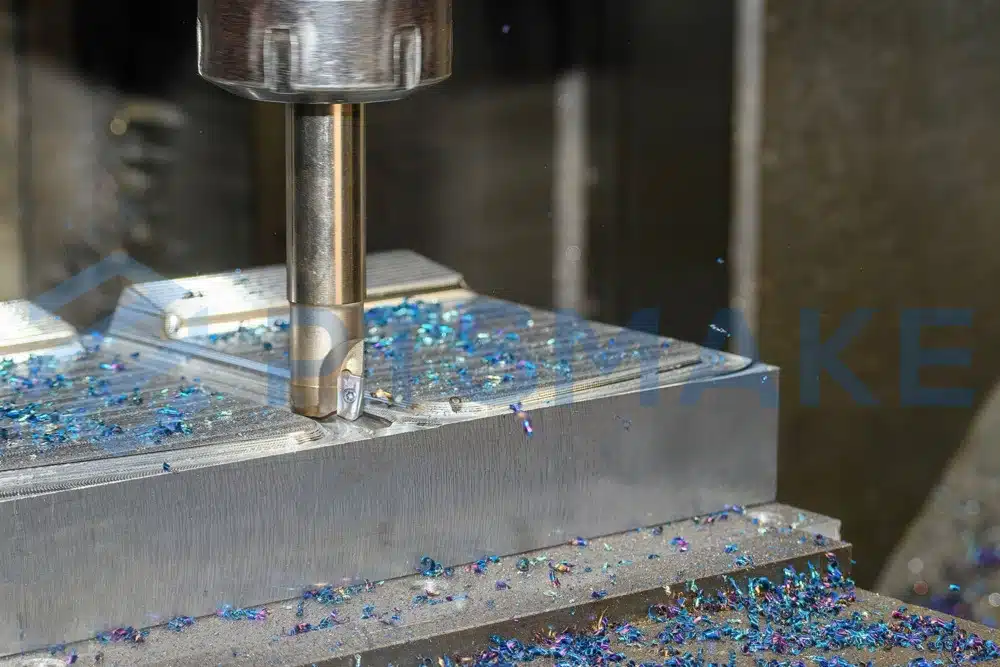
2. CNC Machining
We use CNC machining to precisely cut and shape mold components according to the design.
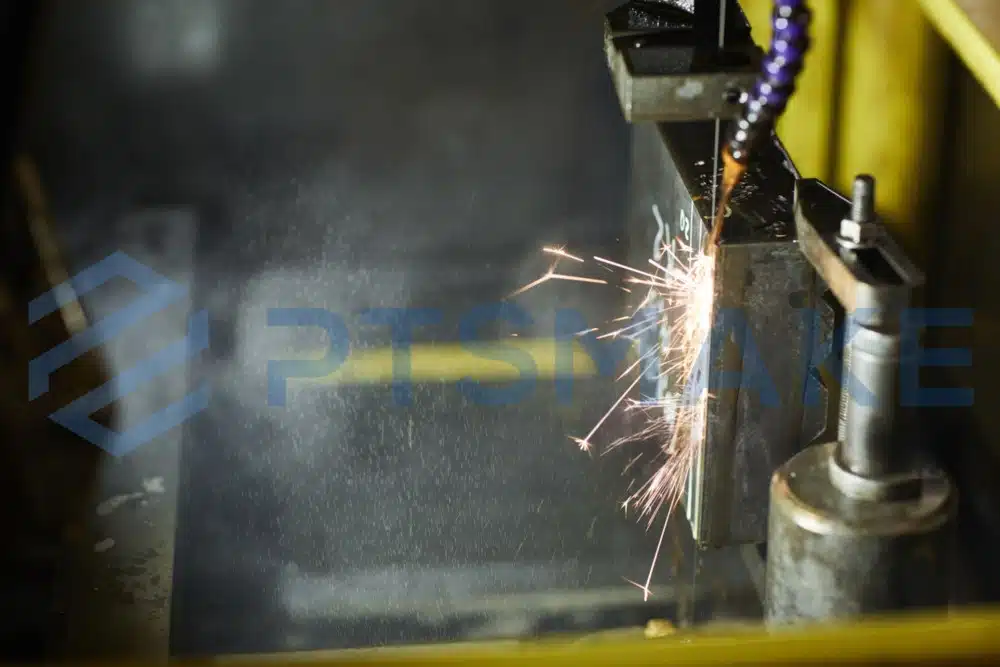
3. Wire-Cut Process
We utilize wire-cutting for precise cuts, achieving tight tolerances for complex geometries.
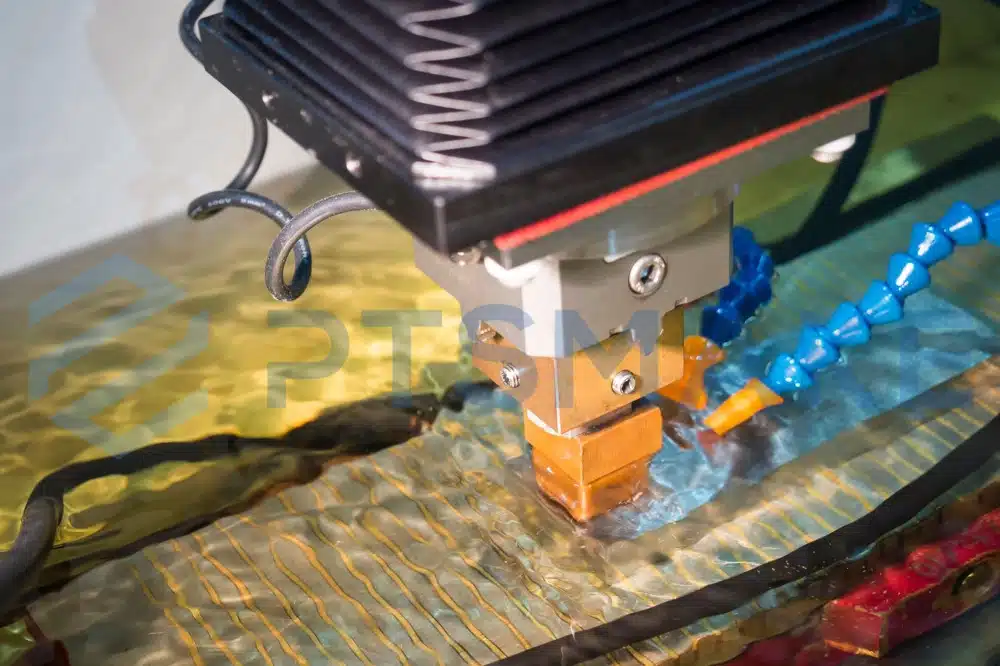
4. EDM Process
We apply EDM to create intricate details and complex shapes that standard machining can’t achieve.
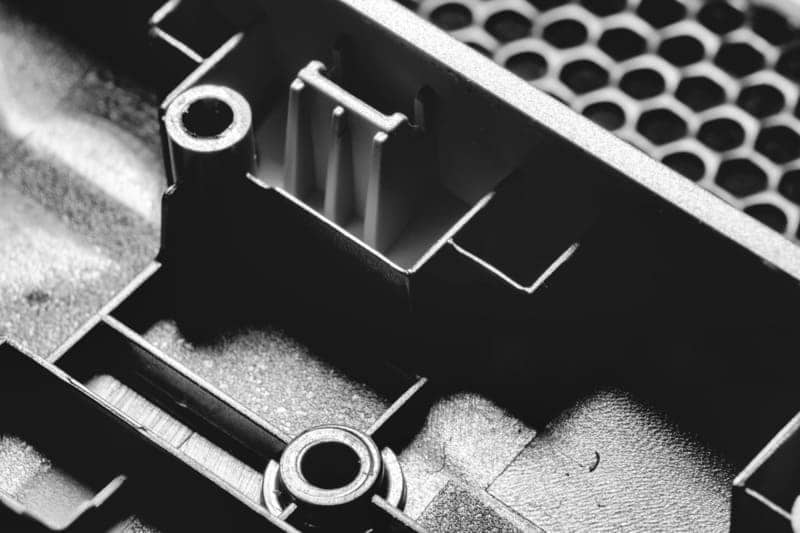
5. Polishing and Texturing
We polish surfaces for smooth finishes and add textures to meet your design requirements.
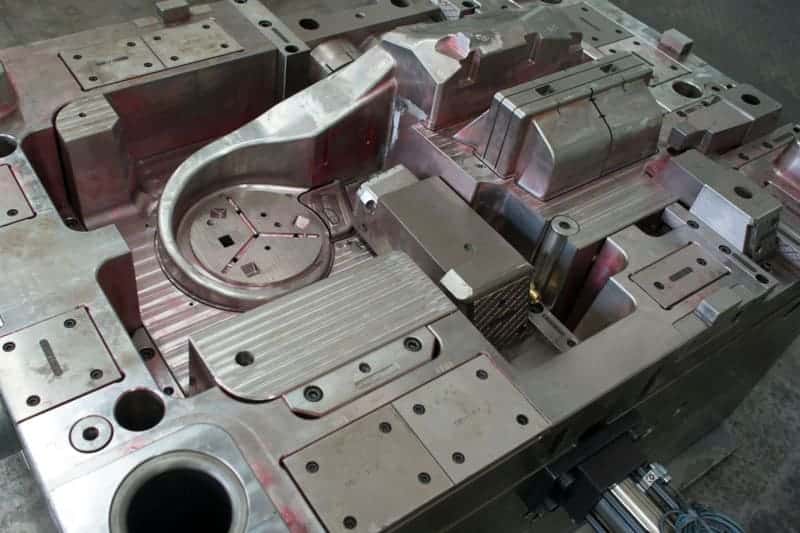
6. Mold Assembly
We carefully assemble all mold components to ensure proper function during production.
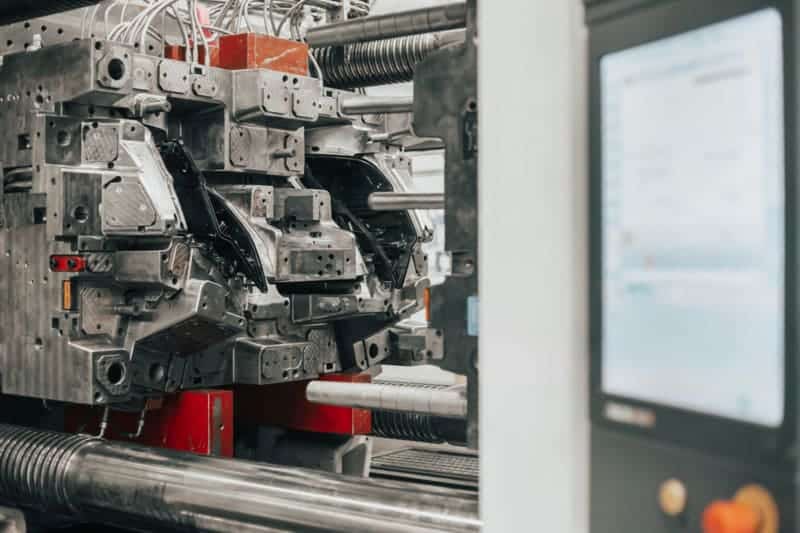
7. Mold Testing
We test the assembled mold by producing samples, verifying quality before ship mold.
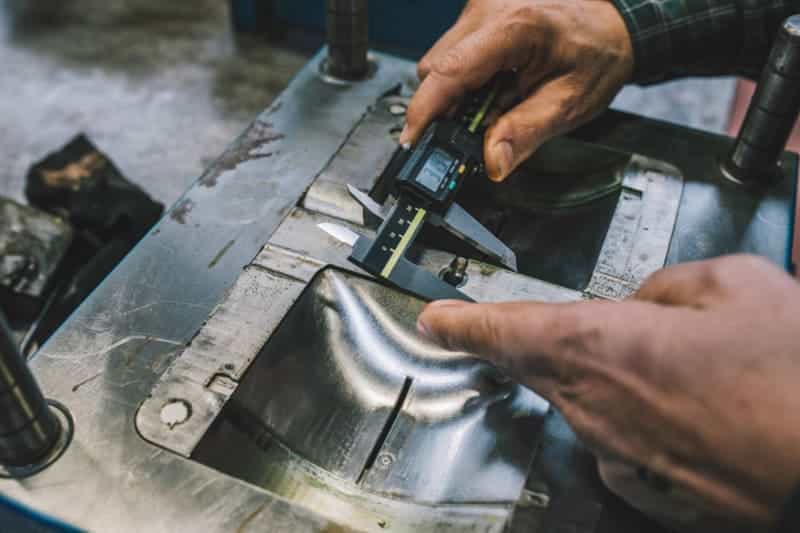
8. Mold Repair
After testing the injection mold, we carefully modify it to precisely meet your requirements.
Effective Communication with Plastic Injection Molds Factory
Communicating well with two-shot injection molding factories is crucial to ensure your design requirements are fully understood and implemented. Here are some strategies to help you achieve successful collaboration.
1. Provide Clear Specifications
View Details
- We need precise product details, including dimensions and materials, to meet your exact requirements.
2. Share Accurate Design Files
View Details
- We require your CAD files to understand your design thoroughly and avoid misunderstandings.
3. Set Realistic Timelines
View Details
- We agree on achievable schedules to deliver your project on time without compromising quality.
4. Discuss Material Requirements
View Details
- We confirm material types and grades to ensure your product meets performance standards.
5. Define Quality Expectations
View Details
- We align on quality standards to produce parts that consistently meet your specifications.
6. Specify Quantity Needs
View Details
- We need to know production volumes to plan manufacturing processes efficiently.
7. Establish Communication Channels
View Details
- We determine preferred contact methods to provide timely updates and address concerns.
8. Review and Approve Samples
View Details
- We provide prototypes for your evaluation and approval before full-scale production.
Benefits of Plastic Injection Molding
Understanding the advantages of plastic injection molding can help your business make better choices. Here, we focus on the benefits that matter to you.
1. High Efficiency
Plastic injection molding allows for fast production of parts. We can produce large quantities in a short time. This efficiency saves you time and money.
2. Consistent Quality
The process ensures each part is made with precision. Your products will have consistent quality. This reliability strengthens your brand.
3. Cost-Effective Production
Once the mold is created, the cost per unit is low. This method is ideal for large production runs. It helps you reduce manufacturing costs.
4. Design Flexibility
Plastic injection molding supports complex designs. You can create intricate shapes and detailed features. This flexibility meets your specific needs.
5. Material Variety
You can choose from many plastic materials. Each material offers different properties. This range allows you to select the best fit for your product.
6. Reduced Waste
The process generates minimal waste. Excess material can be recycled and reused. This approach supports your sustainability goals.
7. Strong and Durable Parts
The molded parts are strong and durable. They can withstand various conditions. You receive products that last longer.
8. Automated Production
The process is highly automated. Automation reduces errors and labor costs. This efficiency benefits your bottom line.
By considering these benefits, you can see how plastic injection molding supports your business. It offers efficiency, quality, and flexibility that help you succeed.
Plastic Injection Molds Applications
Aerospace
- Read More
Automotive
- Read More
Medical
- Read More
Consumer Products
- Read More
Industrial Machinery
- Read More
Electronics
- Read More
Packaging
- Read More
Telecommunications
- Read More
Plastic Injection Molds FAQs
How long does it take to make a mold?
Making a mold can take several weeks, The time depends on the mold’s complexity and size.
What is the cost of a plastic injection mold?
The cost varies based on design, size, and materials. We can provide a quote after reviewing your specifications.
What is the lifespan of a mold?
A mold can produce thousands to millions of parts. Its lifespan depends on the material and how it is maintained.
How do I choose the right material for my product?
Consider factors like strength, flexibility, and temperature resistance. We can help you select the best material.
Can you assist with product design?
Yes, we offer design assistance. We can help optimize your design for better manufacturing results.
What are the tolerances achievable with injection molds?
We can achieve tight tolerances 0.005mm. The exact tolerance depends on the part’s design and material.
What surface finishes are available?
We offer various finishes like matte, glossy, or textured surfaces. Tell us your preference.
Can you work with tight deadlines?
We strive to meet your timelines. Please discuss your schedule with us, and we will do our best to accommodate.
Do you offer prototyping services?
Yes, we can create prototypes. This step helps you test and refine your design before full production.
How do I maintain the molds?
Proper maintenance includes regular cleaning and storage in a dry place. We can provide maintenance guidelines.
What if I need changes after the mold is made?
Changes can be made but may incur additional costs. It is best to finalize the design before mold production.
How are molds shipped to me?
We can arrange shipping to your location. We handle packaging to ensure the mold arrives safely.
How do you protect my intellectual property?
We respect your intellectual property rights. We can sign a non-disclosure agreement to ensure confidentiality.
Can I visit your facility?
Yes, you are welcome to visit. Please contact us to schedule a tour.
Do you provide after-sales support?
es, we offer support after the sale. We can assist with any issues that arise.