Have you ever purchased galvanized metal parts only to find rust spots appearing months later? It’s frustrating when you invest in what you thought was rust-proof material, yet still face corrosion issues. This can lead to costly replacements and potential project delays.
While galvanized metal is highly resistant to rust, it’s not completely rust-proof. The zinc coating provides a protective barrier that significantly slows down corrosion, but factors like scratches, environmental exposure, and chemical contact can eventually lead to rust formation.
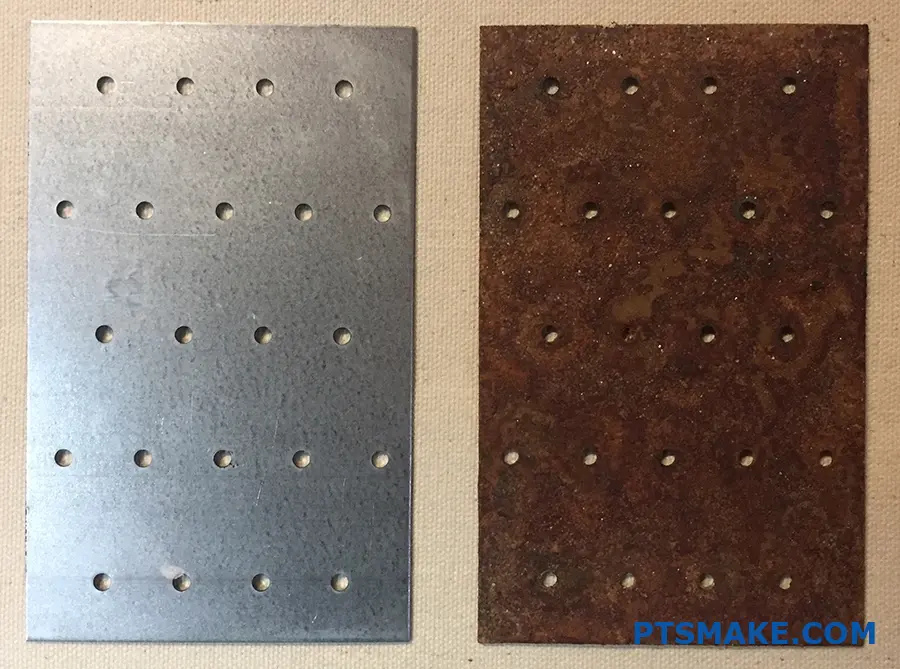
As a manufacturing professional, I’ve seen how galvanization affects metal parts in various applications. The effectiveness of galvanized coating depends on several key factors. Let me share some insights about how galvanization works, its limitations, and what you can expect in terms of rust resistance for your projects.
What Does It Mean If Something Is Galvanised?
Have you ever wondered why some metal products seem immune to rust while others quickly deteriorate? The difference often lies in a crucial protective process that many overlook, leaving their metal components vulnerable to corrosion and premature failure.
Galvanization is a protective coating process where metal, typically steel or iron, is coated with a layer of zinc to prevent rust and corrosion. This treatment creates a sacrificial barrier that protects the base metal, significantly extending its lifespan and durability.
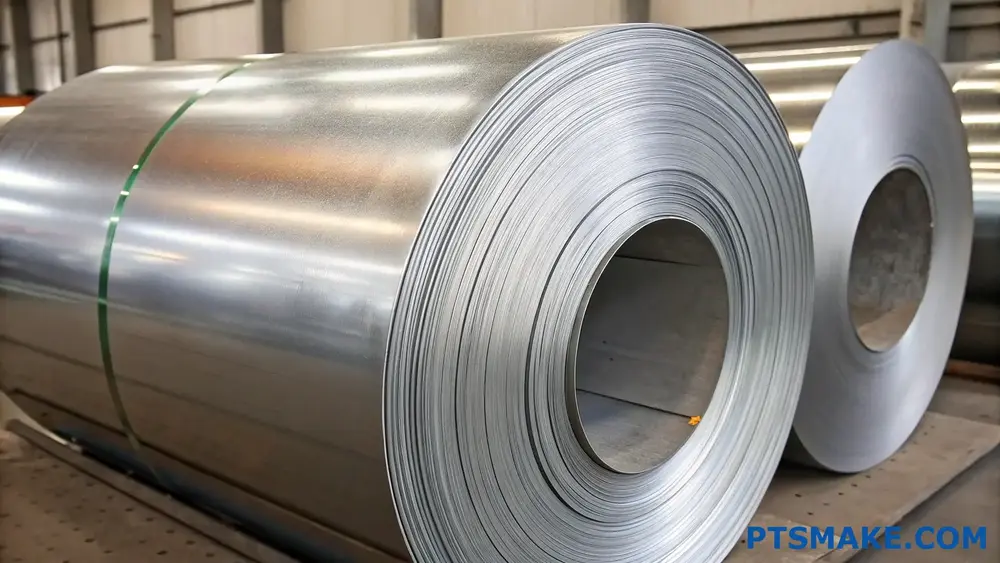
Understanding the Galvanization Process
The galvanization process involves several critical steps that transform ordinary metal into a corrosion-resistant material. At PTSMAKE, we regularly work with galvanized materials for our precision manufacturing projects. The most common method is hot-dip galvanization, where clean metal is immersed in molten zinc at approximately 450°C (842°F).
The Science Behind Galvanization
During the process, a series of metallurgical reactions1 occur between the steel and zinc, forming several distinct layers:
- Gamma Layer: The innermost layer
- Delta Layer: The intermediate layer
- Zeta Layer: The outer crystalline layer
- Eta Layer: The pure zinc surface layer
Benefits of Galvanization
Durability and Longevity
Galvanized products offer exceptional durability, often lasting 50+ years without maintenance. This longevity makes it particularly valuable in:
Application | Expected Lifespan | Maintenance Required |
---|---|---|
Rural Areas | 70+ years | Minimal |
Urban Areas | 50+ years | Regular inspection |
Coastal Regions | 25+ years | Annual inspection |
Cost-Effectiveness
While initial costs might be higher than untreated metals, galvanized materials offer significant long-term savings:
- Reduced maintenance costs
- Extended service life
- Lower replacement frequency
- Minimal inspection requirements
Applications Across Industries
Construction and Infrastructure
In construction, galvanized steel is essential for:
- Structural support beams
- Roofing materials
- Bridge components
- Guard rails
- Underground piping systems
Manufacturing and Production
At PTSMAKE, we’ve implemented galvanized components in various precision manufacturing projects, particularly where corrosion resistance is crucial. Common applications include:
- Industrial machinery parts
- Automotive components
- Marine equipment
- Agricultural machinery
- Outdoor electrical enclosures
Environmental Impact and Sustainability
Galvanization contributes to environmental sustainability in several ways:
- Zinc is 100% recyclable without quality loss
- Reduced need for replacement parts means less waste
- Lower maintenance requirements reduce chemical usage
- Extended product life decreases resource consumption
Quality Control in Galvanization
Testing Methods
To ensure optimal protection, galvanized coatings undergo rigorous testing:
Test Type | Purpose | Frequency |
---|---|---|
Thickness Testing | Measure coating depth | Every batch |
Adhesion Testing | Verify coating bond | Sample basis |
Visual Inspection | Check surface quality | 100% inspection |
Salt Spray Testing | Corrosion resistance | Periodic validation |
Common Issues and Solutions
Some challenges in galvanization include:
- Warping during hot-dip process
- Uneven coating thickness
- Surface imperfections
- Hydrogen embrittlement
Best Practices for Maintaining Galvanized Products
To maximize the lifespan of galvanized materials:
Regular Inspection
- Check for surface damage
- Monitor for signs of wear
- Document any changes
Proper Storage
- Keep away from acidic substances
- Ensure adequate ventilation
- Avoid prolonged moisture exposure
Handling Guidelines
- Use appropriate tools
- Avoid scratching the surface
- Clean regularly with mild solutions
Future Trends in Galvanization Technology
The industry continues to evolve with:
Advanced Coating Technologies
- Nano-enhanced zinc coatings
- Smart protective layers
- Environmental-friendly processes
Automated Quality Control
- AI-powered inspection systems
- Real-time monitoring
- Predictive maintenance
Does Galvanized Mean Waterproof?
Have you ever invested in galvanized materials for your project, assuming they were completely waterproof, only to discover rust forming later? This common misconception has led many to face unexpected corrosion issues and costly replacements.
No, galvanized does not mean waterproof. While galvanization provides significant water resistance through its protective zinc coating, it’s not completely waterproof. The zinc layer offers a sacrificial barrier that slows down corrosion but can eventually wear away under certain conditions.
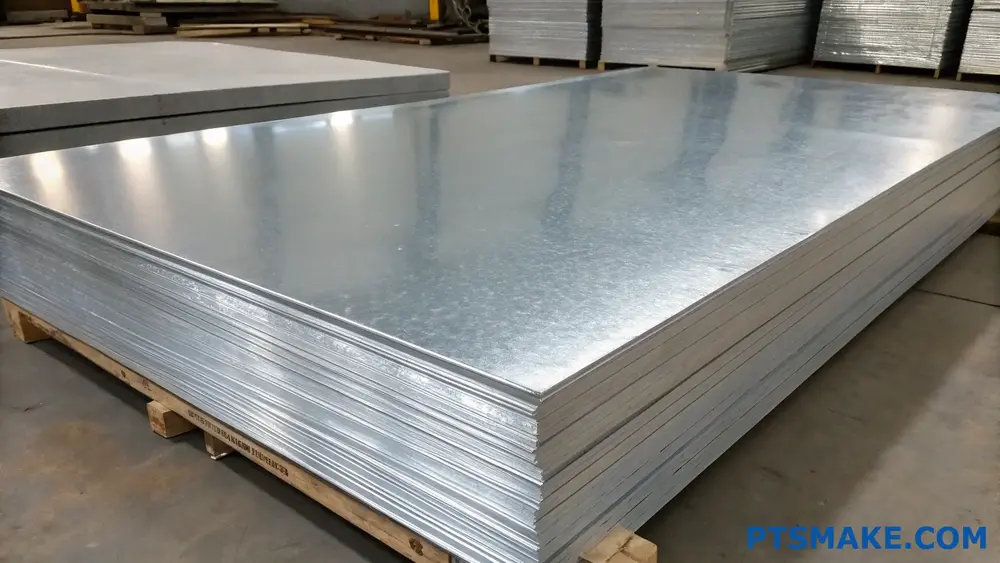
Understanding the Galvanization Process
The galvanization process involves coating steel or iron with a protective layer of zinc. During manufacturing, the base metal undergoes hot-dip galvanization2, creating a metallurgical bond between the zinc and steel. This process forms several zinc-iron alloy layers that provide superior protection against water and other corrosive elements.
Types of Galvanization Methods
Hot-Dip Galvanizing
- Most common method
- Provides thickest coating
- Offers longest protection
- Best suited for outdoor applications
Electrogalvanizing
- Thinner coating
- More precise control
- Ideal for small parts
- Better for indoor use
Factors Affecting Galvanized Protection
Several factors influence how well galvanized materials resist water:
Environmental Conditions
Condition | Impact Level | Protection Duration |
---|---|---|
Marine | High | 10-15 years |
Industrial | Medium-High | 15-20 years |
Rural | Low | 20-25 years |
Indoor | Very Low | 25+ years |
Coating Thickness
The effectiveness of water resistance directly correlates with coating thickness. At PTSMAKE, we’ve found that proper coating thickness specifications are crucial for ensuring optimal performance in different applications.
Common Misconceptions about Galvanized Materials
Myth 1: Complete Waterproofing
Many believe galvanized materials are entirely waterproof. However, they’re actually water-resistant. The zinc coating sacrifices itself slowly to protect the base metal, but this protection isn’t permanent.
Myth 2: Maintenance-Free
While galvanized materials require less maintenance than raw steel, they still need periodic inspection and care, especially in harsh environments.
Best Practices for Water Protection
To maximize water resistance of galvanized materials:
Proper Design Considerations
- Avoid water traps
- Ensure adequate drainage
- Maintain proper ventilation
- Consider environmental exposure
Installation Guidelines
- Use compatible materials
- Avoid contact with dissimilar metals
- Protect against mechanical damage
- Implement proper drainage systems
Industry Applications and Solutions
Different industries require varying levels of water protection:
Construction Industry
- Structural steel components
- Roofing materials
- Hardware and fasteners
- Foundation reinforcement
Manufacturing Sector
At PTSMAKE, we specialize in precision manufacturing of galvanized components. Our experience shows that proper material selection and processing are crucial for achieving optimal water resistance.
Marine Applications
Marine environments demand the highest level of protection:
- Enhanced coating thickness
- Additional protective measures
- Regular maintenance schedules
- Specialized coating systems
Testing and Quality Assurance
To ensure reliable water resistance:
Test Type | Purpose | Frequency |
---|---|---|
Salt Spray | Corrosion resistance | Every batch |
Coating Thickness | Quality control | 100% inspection |
Adhesion Testing | Bonding strength | Sample basis |
Impact Testing | Durability check | Sample basis |
Maintenance and Long-term Protection
To maintain water resistance:
Regular Inspections
- Check for coating damage
- Monitor for rust formation
- Assess environmental exposure
- Document changes over time
Preventive Measures
- Clean surfaces regularly
- Repair damaged areas promptly
- Apply additional protective coatings
- Monitor environmental conditions
Future Developments
The industry continues to evolve with:
- Advanced coating technologies
- Improved application methods
- Enhanced testing procedures
- Sustainable solutions
Our team at PTSMAKE stays current with these developments to provide cutting-edge solutions for our clients’ water protection needs.
What Is The Downside Of Galvanized Steel?
Have you ever installed galvanized steel components only to discover unsightly white rust forming within months? Or watched your carefully planned project deteriorate faster than expected, leaving you wondering if you made the right material choice?
Galvanized steel has several disadvantages, including initial higher costs, surface finish irregularities, and potential hydrogen embrittlement. The coating can also be damaged during handling, and welding galvanized steel releases toxic fumes that require special safety measures.
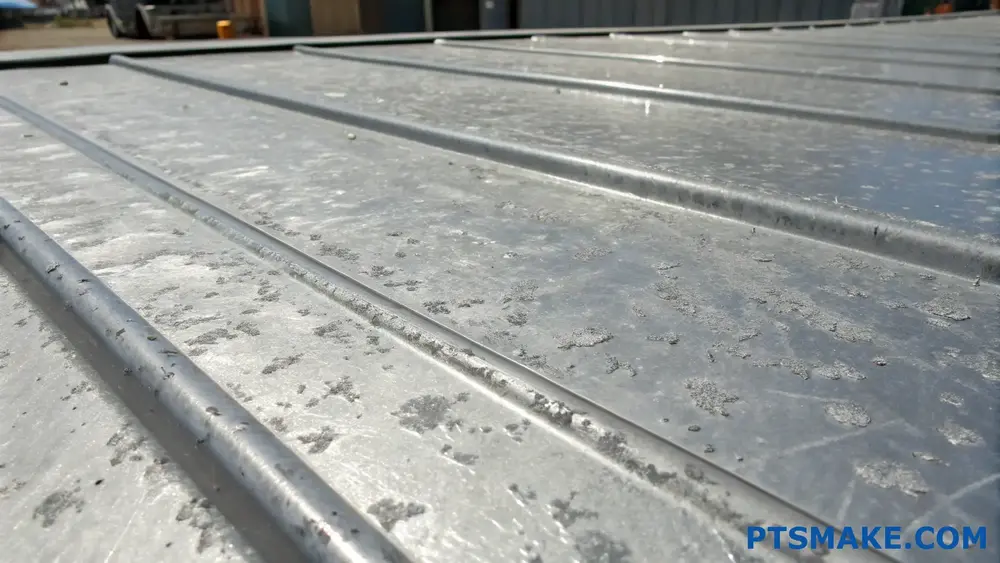
Understanding the Cost Impact
The cost factor of galvanized steel often surprises many project managers. While the long-term benefits can justify the investment, the upfront costs are significant.
Initial Investment vs. Traditional Steel
Cost Factor | Galvanized Steel | Traditional Steel |
---|---|---|
Material Cost | 1.5-2x higher | Base price |
Processing Fee | Additional 20-30% | Standard |
Installation Cost | Higher due to weight | Lower |
Surface Quality Challenges
The galvanization process can lead to several surface imperfections. During manufacturing, the molten zinc coating may not distribute evenly, creating what we call galvanization spangle3. This affects not only aesthetics but also the material’s performance.
Common Surface Issues:
- Rough patches
- Uneven coating thickness
- Drip marks
- Color variations
Environmental and Health Concerns
Working with galvanized steel presents several environmental and health challenges that need careful consideration.
Toxic Fume Generation
When welding or cutting galvanized steel, zinc oxide fumes are released. At PTSMAKE, we’ve implemented strict safety protocols for handling such materials, including:
- Mandatory ventilation systems
- Personal protective equipment
- Regular air quality monitoring
Disposal Challenges
The zinc coating complicates the recycling process. While still recyclable, it requires specialized handling and processing methods.
Mechanical Limitations
The galvanization process can affect the mechanical properties of steel in several ways:
Strength Reduction
Hot-dip galvanizing can potentially reduce the strength of high-strength steels by up to 15%. This is particularly crucial in load-bearing applications.
Hydrogen Embrittlement
The galvanizing process may introduce hydrogen into the steel structure, leading to:
- Reduced ductility
- Increased brittleness
- Potential crack formation
Application Restrictions
Not all environments are suitable for galvanized steel use:
Chemical Incompatibility
Environment | Impact on Galvanized Steel |
---|---|
Acidic Solutions | Rapid coating deterioration |
Alkaline Conditions | Accelerated corrosion |
Salt Water | Reduced protection life |
Temperature Limitations
Galvanized coatings perform poorly in:
- High-temperature environments (above 200°C)
- Freeze-thaw cycle conditions
- Areas with extreme temperature fluctuations
Aesthetic Considerations
The appearance of galvanized steel may not meet all design requirements:
Visual Challenges
- Dull gray appearance
- Inconsistent surface texture
- Limited color options
- Visible coating imperfections
Maintenance Requirements
While galvanized steel is often marketed as maintenance-free, certain conditions require regular attention:
Inspection Points
- Coating thickness monitoring
- Damage assessment
- Touch-up repairs
- Joint integrity checks
Processing Difficulties
Manufacturing with galvanized steel presents unique challenges:
Welding Complications
- Required special techniques
- Reduced weld strength
- Toxic fume generation
- Additional safety measures
Forming Limitations
The coating can:
- Flake during bending
- Crack under stress
- Create uneven surfaces
- Affect dimensional accuracy
At PTSMAKE, we’ve developed specialized techniques to overcome these challenges, ensuring our clients receive high-quality galvanized steel components that meet their specifications while minimizing these inherent drawbacks.
Through careful material selection, proper handling procedures, and advanced processing techniques, many of these disadvantages can be managed effectively. However, it’s crucial to consider these factors during the initial project planning phase to ensure the most appropriate material choice for your specific application.
How Can I Extend Galvanized Steel’s Lifespan in Saltwater?
Have you ever invested in galvanized steel components for a marine project, only to watch them deteriorate faster than expected? The constant battle between saltwater and metal protection can be frustrating, especially when project timelines and budgets are at stake.
Galvanized steel in saltwater typically lasts 10-15 years with proper maintenance. However, lifespan varies significantly based on factors like water salinity, temperature, coating thickness, and environmental conditions. Regular inspections and maintenance can extend this duration.
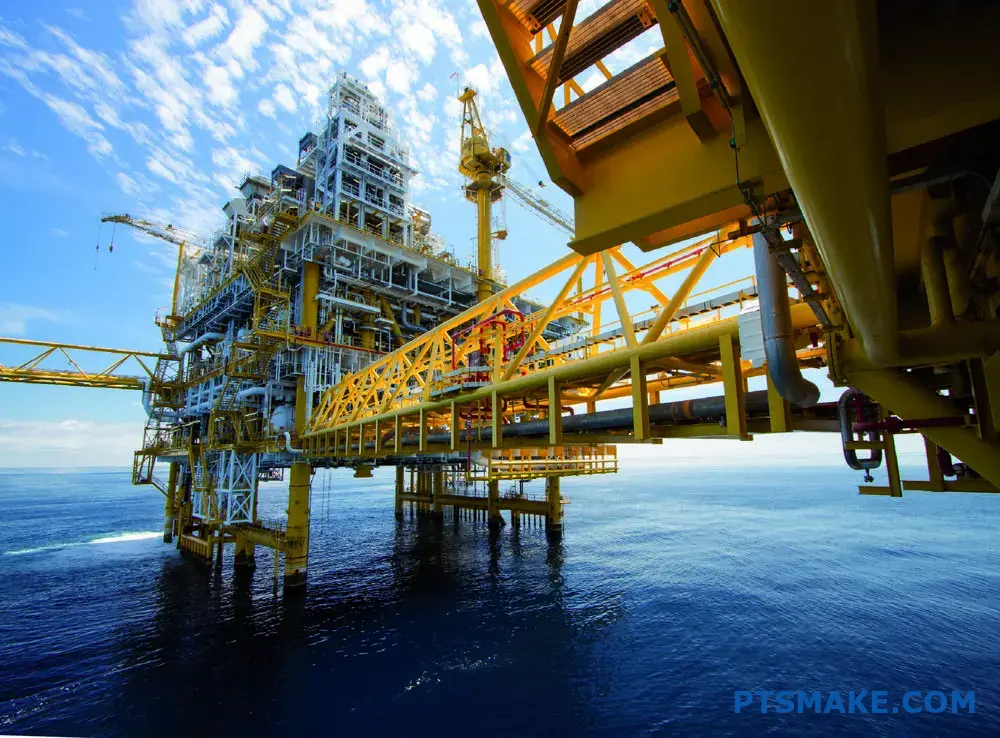
Understanding Maintenance Requirements
The key to maximizing galvanized steel’s lifespan in saltwater environments lies in implementing proper maintenance procedures. At PTSMAKE, we’ve developed comprehensive maintenance protocols that help our clients protect their investments. Here’s what you need to focus on:
Regular Inspection Schedule
Maintaining a consistent inspection schedule is crucial. I recommend:
- Weekly visual checks for signs of corrosion
- Monthly detailed inspections of high-stress areas
- Quarterly comprehensive evaluations of coating integrity
- Annual professional assessments
Cleaning Protocols
Proper cleaning helps prevent cathodic dissolution4 and extends the life of galvanized components:
- Remove salt deposits weekly using fresh water
- Clean surfaces monthly with pH-neutral cleaners
- Avoid abrasive cleaning tools that might damage the coating
- Document cleaning procedures for consistency
Environmental Impact Factors
Different environmental conditions affect galvanized steel’s durability:
Environmental Factor | Impact Level | Mitigation Strategy |
---|---|---|
Water Temperature | High | Monitor temperature fluctuations |
Salinity Levels | Critical | Regular freshwater rinsing |
UV Exposure | Moderate | Additional UV-resistant coating |
Water Flow Rate | Significant | Strategic positioning |
Protection Enhancement Methods
To extend the lifespan of galvanized steel in saltwater, consider these protection methods:
Additional Coating Systems
- Epoxy-based sealants
- Polyurethane top coats
- Anti-fouling treatments
- Sacrificial anodes
Design Considerations
The design phase is crucial for longevity:
- Avoid sharp edges and corners
- Include proper drainage systems
- Incorporate isolation from dissimilar metals
- Design for easy maintenance access
Performance Monitoring
Implementing a robust monitoring system helps track degradation:
Key Performance Indicators
- Coating thickness measurements
- Surface pH levels
- Corrosion rate monitoring
- Visual deterioration tracking
Documentation Requirements
Maintain detailed records of:
- Initial installation conditions
- Regular inspection results
- Maintenance activities
- Environmental exposure data
Cost-Effective Solutions
At PTSMAKE, we help clients balance protection and budget:
Investment Optimization
- Choose appropriate coating thickness
- Select optimal maintenance intervals
- Plan for strategic replacements
- Consider lifecycle costs
Resource Allocation
Focus resources on:
- High-risk areas
- Critical components
- Preventive maintenance
- Staff training
Technology Integration
Modern technology enhances protection strategies:
Monitoring Systems
- IoT sensors for real-time data
- Automated inspection schedules
- Digital documentation
- Predictive maintenance algorithms
Analysis Tools
- Corrosion rate calculators
- Environmental impact assessments
- Lifecycle prediction models
- Cost-benefit analysis software
Industry Standards Compliance
Meeting industry standards ensures optimal performance:
Regulatory Requirements
- ASTM International standards
- ISO certifications
- Local maritime regulations
- Environmental compliance
Quality Control
- Material testing protocols
- Installation verification
- Maintenance procedure validation
- Performance monitoring standards
This comprehensive approach to galvanized steel maintenance in saltwater environments helps ensure maximum lifespan and optimal performance. By following these guidelines and working with experienced manufacturers like PTSMAKE, you can significantly extend the service life of your galvanized steel components while maintaining their structural integrity and functionality.
Can Galvanized Steel Be Painted Or Powder-Coated For Additional Protection?
Have you ever noticed your galvanized steel starting to lose its protective zinc coating over time? It’s frustrating when this crucial barrier against corrosion begins to fail, especially in outdoor or harsh environments where maximum protection is essential.
Yes, galvanized steel can be both painted and powder-coated for enhanced protection. While galvanization provides excellent corrosion resistance, adding a paint or powder coating layer creates a dual protection system that significantly extends the material’s lifespan and enhances its appearance.
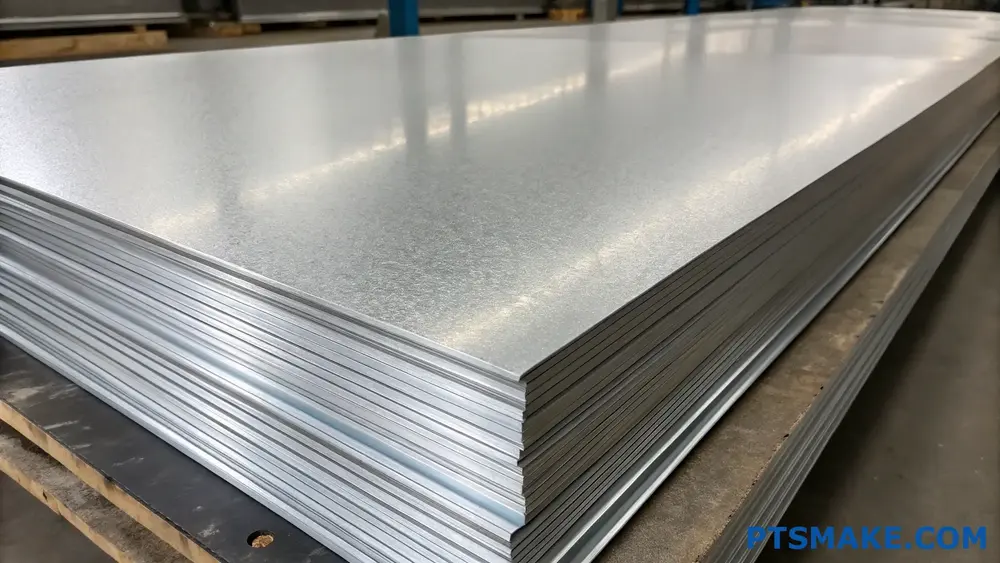
Understanding Surface Preparation Requirements
The success of any coating application on galvanized steel largely depends on proper surface preparation. At PTSMAKE, we follow a systematic approach to ensure optimal adhesion:
Surface Cleaning Methods
- Solvent Cleaning: Removes oils and organic contaminants
- Alkaline Cleaning: Eliminates stubborn dirt and grease
- Water Washing: Removes water-soluble contaminants
- Chemical Etching5: Creates micro-roughness for better coating adhesion
Profile Creation Process
The surface profile needs careful attention to achieve proper coating adhesion. Here’s our recommended approach:
- Light Abrasive Blasting
- Chemical Conversion Coating
- Weathering (when time permits)
- Mechanical Roughening
Paint Coating Options for Galvanized Steel
When it comes to painting galvanized steel, selecting the right coating system is crucial. Based on my experience working with various industrial applications, here are the most effective options:
Recommended Paint Systems
Paint Type | Advantages | Best Applications |
---|---|---|
Epoxy | Excellent adhesion, chemical resistance | Industrial equipment |
Polyurethane | UV resistance, color retention | Outdoor structures |
Acrylic | Cost-effective, easy application | Light-duty indoor use |
Vinyl | Flexibility, impact resistance | Marine environments |
Application Methods
The application technique significantly influences the coating’s performance:
Spray Application
- HVLP (High Volume Low Pressure)
- Airless Spray
- Conventional Air Spray
Brush and Roller Application
- Suitable for small areas
- Touch-up work
- Maintenance coating
Powder Coating Process for Galvanized Steel
Powder coating offers distinct advantages over traditional liquid paints. At PTSMAKE, we’ve refined our powder coating process to ensure maximum durability:
Pre-Treatment Steps
- Degreasing
- Phosphating
- Chromate Conversion
- Rinse and Dry
Powder Application Techniques
The powder application process requires precise control:
Parameter | Recommended Range | Critical Factors |
---|---|---|
Temperature | 350-400°F | Material thickness |
Cure Time | 10-15 minutes | Coating thickness |
Film Thickness | 2-3 mils | Edge coverage |
Voltage | 40-90 kV | Part geometry |
Performance Considerations
When selecting between paint and powder coating for galvanized steel, consider these factors:
Environmental Factors
- UV Exposure
- Temperature Fluctuations
- Chemical Exposure
- Humidity Levels
Cost Analysis
Factor | Paint Coating | Powder Coating |
---|---|---|
Initial Cost | Lower | Higher |
Application Speed | Faster | Moderate |
Durability | Good | Excellent |
Maintenance | Regular | Minimal |
Quality Control Measures
To ensure coating success, implement these quality control steps:
- Surface Profile Measurement
- Environmental Condition Monitoring
- Coating Thickness Verification
- Adhesion Testing
- Visual Inspection
Maintenance Requirements
For optimal performance of coated galvanized steel:
Regular Inspection Schedule
- Monthly visual inspections
- Quarterly detailed examinations
- Annual performance testing
Maintenance Procedures
- Clean surfaces regularly
- Repair damaged areas promptly
- Document all maintenance activities
- Monitor coating performance
By following these comprehensive guidelines, you can successfully apply additional protective coatings to galvanized steel, significantly extending its service life and enhancing its appearance. At PTSMAKE, we’ve implemented these practices in numerous projects, consistently achieving excellent results in both aesthetic appeal and long-term protection.
What Are The Alternatives To Galvanized Steel For Corrosion Resistance?
Have you ever struggled with galvanized steel parts failing prematurely due to corrosion? The frustration of seeing rust appear despite galvanization, combined with rising material costs, leaves many engineers searching for better alternatives.
Several effective alternatives to galvanized steel exist, including stainless steel, aluminum alloys, powder-coated metals, zinc-nickel alloys, and engineered plastics. Each option offers unique advantages in corrosion resistance while potentially providing better cost-effectiveness and performance in specific applications.
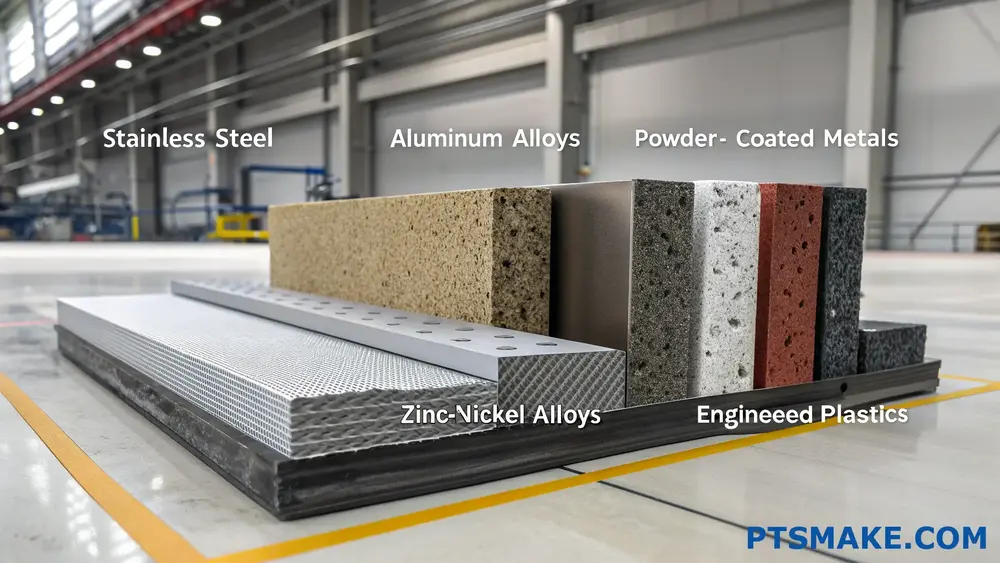
Understanding Modern Corrosion-Resistant Materials
Stainless Steel Solutions
Stainless steel stands as a premium alternative to galvanized steel. At PTSMAKE, we frequently recommend 304 and 316 grades for their exceptional corrosion resistance. The key lies in their chromium content, which forms a self-healing passivation layer6 on the surface.
Here’s a comparative analysis of common stainless steel grades:
Grade | Chromium Content | Corrosion Resistance | Best Applications |
---|---|---|---|
304 | 18-20% | Good | Indoor equipment, food processing |
316 | 16-18% | Excellent | Marine environments, chemical processing |
430 | 16-18% | Moderate | Automotive parts, decorative items |
Aluminum Alloys as Lightweight Alternatives
Aluminum alloys offer compelling advantages over galvanized steel, particularly in weight-sensitive applications. The 5000 and 6000 series alloys provide excellent corrosion resistance through their natural oxide layer formation.
Key benefits include:
- Natural corrosion resistance without additional coating
- Significantly lighter weight (approximately 1/3 of steel)
- Excellent thermal conductivity
- Cost-effective for large-scale production
Advanced Surface Treatments
Powder Coating Technology
Modern powder coating technologies have revolutionized metal protection. The process involves:
- Surface preparation through sandblasting
- Electrostatic powder application
- Heat curing to create a durable finish
Zinc-Nickel Alloy Coatings
These advanced coatings offer superior protection compared to traditional galvanization:
- 5-8 times more corrosion resistant
- Better adhesion properties
- Uniform coating thickness
- Enhanced aesthetic appearance
Engineered Plastics Revolution
High-Performance Polymers
The advancement in engineered plastics has created viable alternatives to galvanized steel. Materials like:
- PEEK (Polyether Ether Ketone)
- PPS (Polyphenylene Sulfide)
- PVDF (Polyvinylidene Fluoride)
These materials offer inherent corrosion resistance without requiring additional treatments.
Cost-Benefit Analysis
When comparing alternatives to galvanized steel, consider these factors:
Material | Initial Cost | Maintenance Cost | Lifespan | Environmental Impact |
---|---|---|---|---|
Stainless Steel | High | Low | 25+ years | Medium |
Aluminum | Medium | Low | 20+ years | Low |
Engineered Plastics | Medium-High | Minimal | 15-20 years | Variable |
Powder Coated Steel | Medium | Medium | 15-20 years | Low |
Industry-Specific Solutions
Marine Applications
In marine environments, where corrosion resistance is crucial, I’ve found that duplex stainless steels and specific aluminum alloys perform exceptionally well. At PTSMAKE, we regularly machine these materials for marine equipment manufacturers.
Chemical Processing Industry
For chemical processing applications, the choice often falls between:
- Super duplex stainless steel
- Titanium alloys
- High-performance polymers
Each material offers specific advantages depending on the chemical environment.
Architectural Applications
In architectural projects, aesthetics and durability must balance. Popular options include:
- Anodized aluminum
- Powder-coated steel
- Architectural grade stainless steel
Future Trends and Innovations
Emerging Technologies
New surface treatment technologies are constantly emerging:
- Nano-ceramic coatings
- Graphene-based protective layers
- Smart self-healing materials
Sustainability Considerations
Modern alternatives to galvanized steel often offer better environmental profiles:
- Reduced toxic emissions during manufacturing
- Better recyclability
- Lower energy consumption in production
- Extended service life reducing replacement frequency
Through careful material selection and understanding specific application requirements, we can often find superior alternatives to galvanized steel. The key is balancing performance requirements, cost constraints, and environmental considerations to achieve optimal results.
What Maintenance Is Required For Galvanized Metal Components?
Have you ever noticed white rust forming on your galvanized parts, or watched in frustration as your galvanized components gradually lost their protective coating? These issues can significantly impact part performance and longevity, potentially leading to costly replacements and production delays.
Galvanized metal components require minimal but specific maintenance, including regular cleaning with mild soap and water, annual inspections for coating damage, touch-up of small damaged areas, and proper storage in dry conditions to prevent premature corrosion and extend service life.
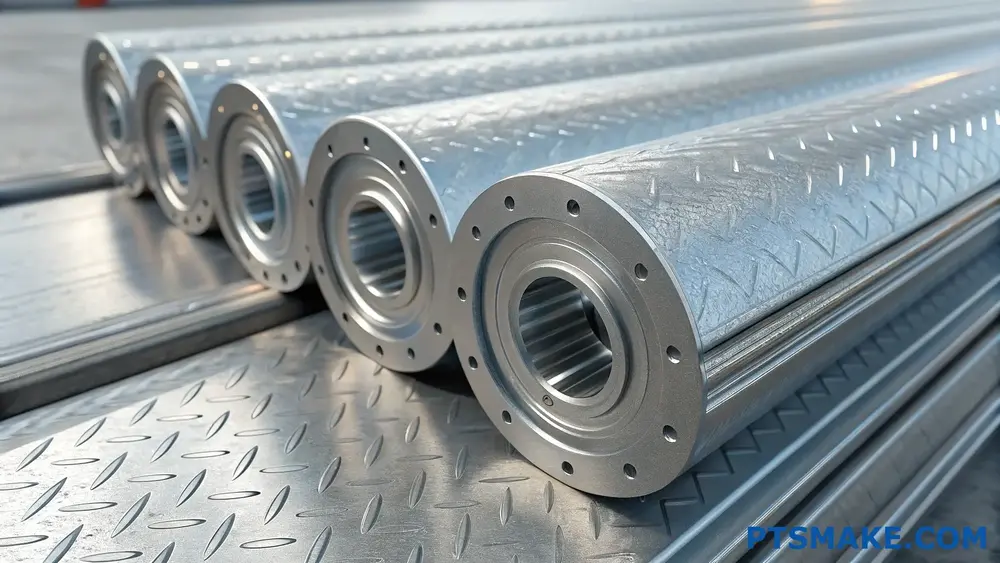
Understanding Galvanized Coating Behavior
The effectiveness of galvanized coatings largely depends on how they interact with their environment. When exposed to the atmosphere, galvanized coatings form a protective patina7 layer that shields the base metal. At PTSMAKE, we’ve observed that proper maintenance significantly extends this protection.
Factors Affecting Coating Performance
Several environmental factors can impact the durability of galvanized coatings:
- Atmospheric conditions (humidity, temperature)
- Chemical exposure
- Physical damage
- UV radiation
- Industrial pollutants
Essential Maintenance Procedures
Regular Cleaning Protocol
Regular cleaning is crucial for maintaining galvanized components. I recommend following these steps:
- Use mild soap and warm water
- Avoid abrasive cleaning tools
- Rinse thoroughly with clean water
- Allow components to dry completely
- Document cleaning dates for maintenance records
Inspection Guidelines
Periodic inspections help identify potential issues before they become serious problems:
Inspection Area | Frequency | Key Check Points |
---|---|---|
Surface Coating | Quarterly | Scratches, chips |
Joint Areas | Monthly | Rust formation |
High-stress Points | Bi-monthly | Coating wear |
Welded Sections | Quarterly | Coating integrity |
Preventive Maintenance Strategies
Storage Recommendations
Proper storage plays a vital role in maintaining galvanized components:
- Store in dry, well-ventilated areas
- Avoid direct ground contact
- Maintain adequate air circulation
- Protect from chemical exposure
- Use appropriate stacking methods
Touch-up Procedures
When minor damage occurs, prompt attention is essential:
- Clean the damaged area thoroughly
- Apply zinc-rich paint or cold galvanizing compound
- Allow proper curing time
- Document repairs for future reference
Environmental Considerations
Climate Impact Management
Different environments require different maintenance approaches:
Coastal Areas
- More frequent inspections
- Additional protective coatings
- Enhanced cleaning schedule
Industrial Zones
- Chemical resistance monitoring
- Pollution impact assessment
- Specialized cleaning products
Rural Locations
- Standard maintenance sufficient
- Regular dust removal
- Basic protection adequate
Advanced Maintenance Techniques
Professional Assessment Guidelines
For optimal maintenance, consider these professional assessment criteria:
Assessment Type | Purpose | Frequency |
---|---|---|
Thickness Testing | Coating wear measurement | Annual |
Adhesion Testing | Coating bond strength | Bi-annual |
Chemical Analysis | Contamination check | As needed |
Visual Inspection | Surface condition | Monthly |
Restoration Methods
When significant degradation occurs:
- Surface preparation
- Coating renewal
- Protection enhancement
- Performance testing
Industry-Specific Maintenance
Different industries require specialized maintenance approaches:
Automotive Industry
- Regular underbody cleaning
- Collision repair procedures
- Seasonal protection
Construction Sector
- Weather exposure management
- Load-bearing component care
- Joint protection
Manufacturing Equipment
- Operating environment control
- Wear point monitoring
- Preventive coating application
Cost-Effective Maintenance Planning
Implementing a structured maintenance plan helps optimize costs:
Regular Inspection Schedule
- Reduces unexpected failures
- Prevents major repairs
- Extends service life
Documentation System
- Tracks maintenance history
- Identifies problem patterns
- Guides future improvements
Resource Allocation
- Staff training
- Equipment needs
- Material requirements
At PTSMAKE, we’ve implemented these maintenance protocols in our production processes, ensuring our galvanized components maintain their protective properties throughout their service life. Our experience shows that proactive maintenance significantly reduces long-term costs and improves component reliability.
How Does Hot-Dip Galvanizing Differ From Electro-Galvanizing Processes?
Have you ever struggled with choosing between hot-dip and electro-galvanizing for your metal parts? The confusion around these two processes can lead to costly mistakes, potentially compromising your product’s durability and performance.
Hot-dip galvanizing and electro-galvanizing are two distinct coating processes. Hot-dip involves immersing metal in molten zinc at 850°F, while electro-galvanizing uses electrical current to deposit zinc onto metal surfaces at room temperature, resulting in different coating thicknesses and applications.
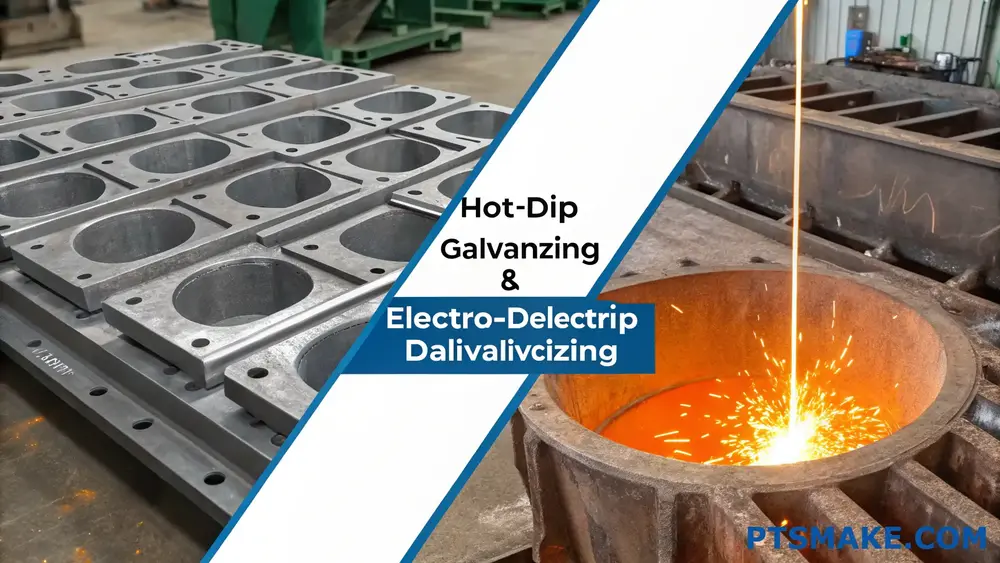
Understanding the Fundamental Differences
Process Temperature and Methods
Hot-dip galvanizing requires heating zinc to approximately 850°F (450°C) in large kettles. The metal parts are immersed in this molten zinc bath after thorough cleaning and surface preparation. In contrast, electro-galvanizing operates at room temperature, where zinc ions are electrically deposited onto the metal surface in a controlled environment.
Coating Thickness and Distribution
The coating thickness varies significantly between these two methods. Hot-dip galvanizing typically produces thicker coatings, ranging from 3.0 to 5.0 mils (75-125 micrometers). At PTSMAKE, we’ve observed that electro-galvanized coatings are usually thinner, typically 0.2 to 1.0 mils (5-25 micrometers).
Comparative Analysis of Both Processes
Characteristic | Hot-Dip Galvanizing | Electro-Galvanizing |
---|---|---|
Process Temperature | 850°F (450°C) | Room temperature |
Coating Thickness | 3.0-5.0 mils | 0.2-1.0 mils |
Surface Finish | Slightly rougher | Smooth and uniform |
Cost per Unit | Higher initial cost | Lower initial cost |
Production Speed | Slower | Faster |
Applications and Industry Uses
Hot-Dip Galvanizing Best Uses
This process excels in outdoor and harsh environment applications. The thick coating provides superior protection against corrosion, making it ideal for:
- Structural steel components
- Highway guardrails
- Light poles
- Agricultural equipment
- Marine environments
Electro-Galvanizing Advantages
The metallurgical bond8 created during electro-galvanizing makes it perfect for:
- Automotive body parts
- Fasteners
- Sheet metal products
- Electronics housings
- Indoor applications
Cost Considerations and Economic Impact
Initial Investment
Hot-dip galvanizing requires larger facilities and more energy, resulting in higher initial costs. The equipment needed includes:
- Large zinc kettles
- Powerful heating systems
- Extensive ventilation
- Material handling equipment
Electro-galvanizing facilities need:
- Plating tanks
- Electrical rectifiers
- Filtration systems
- Chemical controls
Long-term Value Analysis
Despite higher initial costs, hot-dip galvanizing often provides better long-term value due to:
- Extended service life
- Lower maintenance requirements
- Better durability in harsh conditions
- Reduced replacement frequency
Environmental and Safety Considerations
Environmental Impact
Both processes have environmental considerations:
Hot-dip galvanizing:
- Higher energy consumption
- Zinc ash production
- Recyclable materials
- Lower chemical waste
Electro-galvanizing:
- Lower energy usage
- Chemical waste management
- Water treatment requirements
- Continuous monitoring needs
Safety Protocols
At PTSMAKE, we implement strict safety measures for both processes:
Hot-dip safety requirements:
- Heat protection equipment
- Ventilation systems
- Splash protection
- Emergency procedures
Electro-galvanizing safety needs:
- Chemical handling protocols
- Electrical safety measures
- Proper ventilation
- Personal protective equipment
Quality Control and Testing
Inspection Methods
Quality control differs between processes:
Hot-dip inspection:
- Coating thickness measurement
- Visual inspection
- Adhesion testing
- Surface uniformity checks
Electro-galvanizing inspection:
- Thickness uniformity
- Surface appearance
- Adhesion testing
- Corrosion resistance testing
Performance Standards
Both processes must meet specific industry standards:
- ASTM A123 for hot-dip galvanizing
- ASTM B633 for electro-galvanizing
- ISO 1461 for hot-dip coating requirements
- ISO 2081 for electro-galvanized coatings
Maintenance and Longevity
Maintenance Requirements
Hot-dip galvanized coatings typically require minimal maintenance due to:
- Thicker protective layer
- Metallurgical bonding
- Self-healing properties
- Natural patina formation
Electro-galvanized surfaces may need:
- Regular inspection
- Touch-up coating
- Protective paint
- Periodic cleaning
Life Expectancy
The service life varies significantly:
- Hot-dip: 50+ years in many environments
- Electro-galvanized: 10-20 years depending on conditions
Click here to learn more about the chemical bonding process in metal protection. ↩
Click to learn more about hot-dip galvanization process and industry standards. ↩
Click to learn more about surface finish characteristics and how they affect product performance. ↩
Click to learn about this electrochemical process and how to prevent it effectively. ↩
Click to learn about chemical etching techniques that maximize coating adhesion. ↩
Click to learn more about the science behind passive layer formation and its benefits. ↩
Click to learn more about how patina formation protects galvanized surfaces and extends component life. ↩
Click to learn how metallurgical bonding enhances coating durability and protection against corrosion. ↩