China’s Leading Custom Hydraulic Fittings Manufacturer & Supplier
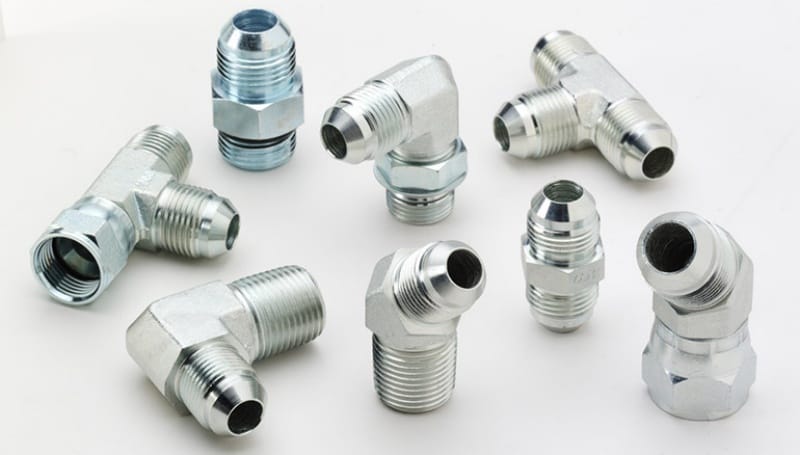
±0.001mm Tolerance Guarantee
Precision Custom Designs
72-Hour Sample Delivery
Global Logistics Network






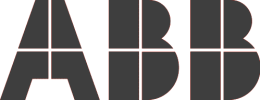

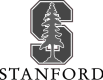
What Our Clients Say
Our clients are located worldwide, and their feedback speaks for itself. If you’d like to verify our reputation with customers in your area, don’t hesitate to contact us—we’d be happy to connect you with them and share relevant case studies.
Custom Hydraulic Fittings for Industrial Excellence
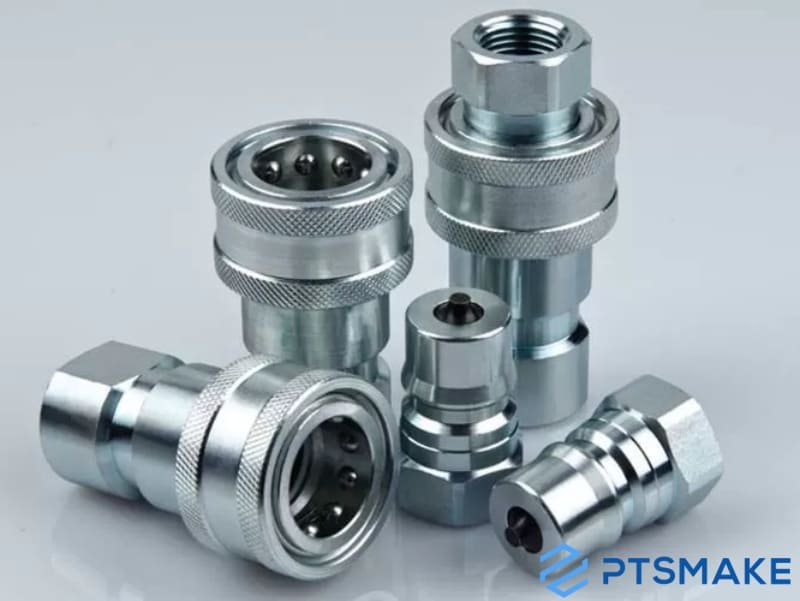
Agricultural Machinery
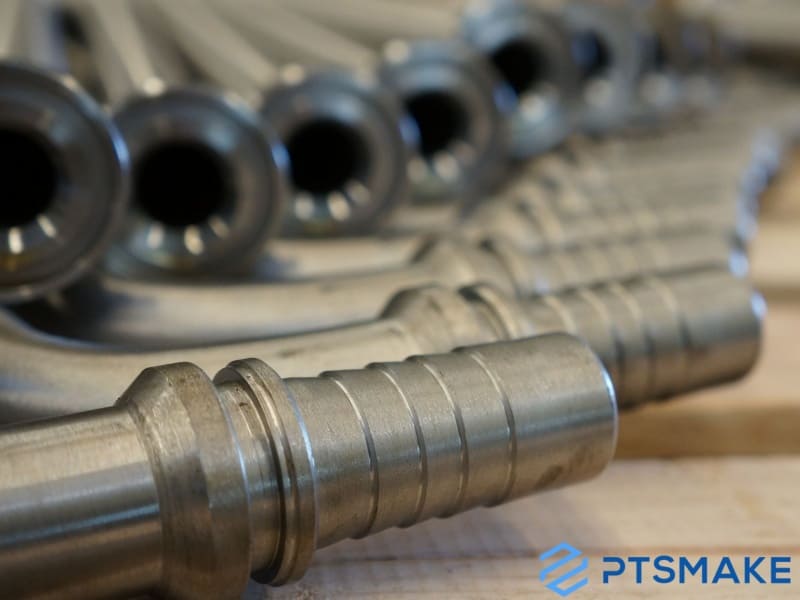
Aerospace Hydraulics
Why Choose PTSMAKE for Custom Hydraulic Fittings
We deliver ±0.001mm tolerances using 20+ years of CNC expertise.
24/7 engineering team responds in 2 hours max.
35% shorter lead times through optimized production workflows.
Single-source production from molds to final CNC parts.
How We Ensure Quality in Custom Hydraulic Fittings Manufacturing
- At PTSMAKE, quality control starts with material selection. We use ISO 9001-certified suppliers for raw materials like stainless steel and high-performance alloys. Every batch undergoes hardness tests and chemical composition checks before production begins. This ensures your custom hydraulic fittings meet strict pressure and corrosion resistance requirements.
- Our CNC machining process uses Mitutoyo-measured tools and Zeiss CMM systems. Tight tolerances (±0.005mm) are maintained through real-time monitoring. For injection-molded hydraulic fittings, we perform mold flow analysis to prevent warping. Each production run includes first-article inspections and random sampling at 3 stages: machining, surface treatment, and assembly
- We solve your pain points proactively. Our traceability system logs every custom hydraulic fitting’s production data – from machine operator IDs to calibration dates. If any defect occurs, we pinpoint the issue within 2 hours. Quality reports are shared openly through our client portal, eliminating communication delays.
- Since 2002, we’ve delivered hydraulic fittings for BMW Factory and Huawei’s industrial equipment. Our 24/7 engineering support ensures design specs are met exactly. No compromises. No surprises.
- Real-time Feedback and Corrective Action System: Deploy a real-time feedback mechanism that immediately alerts operators of deviations, facilitating immediate corrective actions to reduce waste and rework.
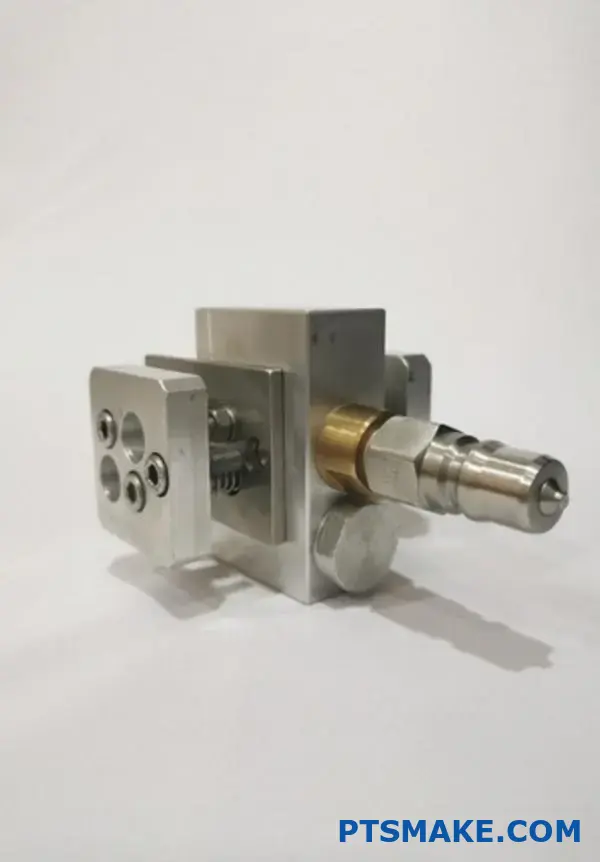
"We ordered 500pcs hydraulic adapters for agricultural machinery. The surface finish exceeded expectations, and PTSMAKE caught a potential sealing issue in our design pre-production. Trustworthy partner!
Emma Vogel, Procurement Director, , Germany"
Top Materials Used in Manufacturing Custom Hydraulic Fittings
Stainless Steel
Brass
Titanium
PTFE (Teflon)
Nylon
Alloy Steel
Carbon Steel
Aluminum
Lead Times for Custom Hydraulic Fittings Manufacturing
Why lead times matter for B2B buyers of hydraulic fittings
- Businesses need reliable timelines to plan production and avoid delays. Custom hydraulic fittings often require specialized machining, which impacts lead times. At PTSMAKE, we prioritize transparency to ensure clients know exactly when parts will arrive.
- Lead times depend on material availability, design complexity, and order volume. Simple designs with common materials take 1-2 weeks. Complex geometries or rare alloys may require 2-3 weeks. We maintain a 1,000m² facility with raw material stocks to minimize delays.
How PTSMAKE Optimizes Hydraulic Fitting Production
- Our CNC machining and injection molding teams work concurrently. This reduces wait times between manufacturing stages. For urgent orders, we offer expedited services with 30% faster turnaround without quality compromises.
- We serve clients globally, including automotive and robotics industries. Our ISO-certified processes ensure consistent quality across all orders. Real-time tracking updates keep clients informed at every production phase.
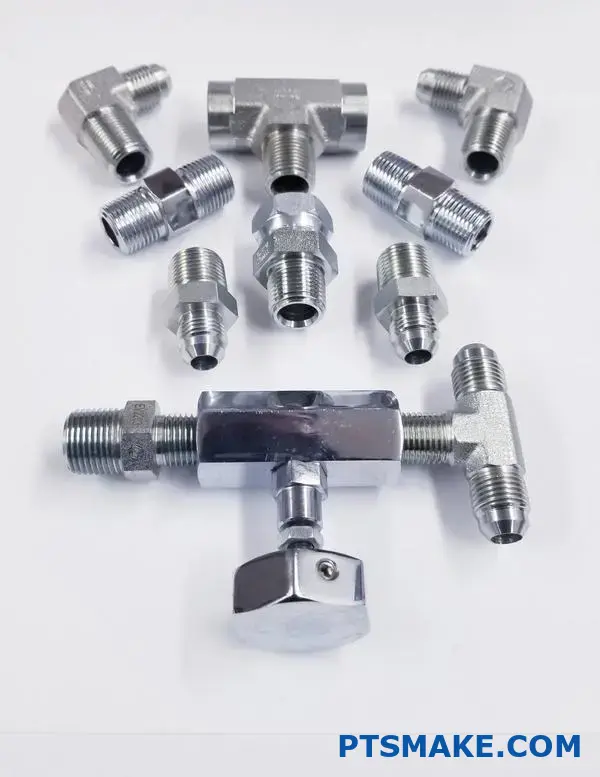
Manufacturing Process of Custom Hydraulic Fittings
1. Design Review
2. Material Selection
3. CNC Machining
4. Thread Forming
5. Surface Treatment
6. Quality Inspection
7. Pressure Testing
8. Packaging & Delivery
Request a Custom Quote Today
Get an accurate estimate for your project today. Let us help you meet your exact specifications.
Cost-Effective Solutions for Custom Hydraulic Fittings
1. Optimize Design for Manufacturability
2. Material Selection Guidance
3. Bulk Order Discounts
4. Reusable Prototyping
5. Standardized Component Sizes
6. Advanced CNC Machining
7. Supplier Consolidation
Customization Options for Hydraulic Fittings
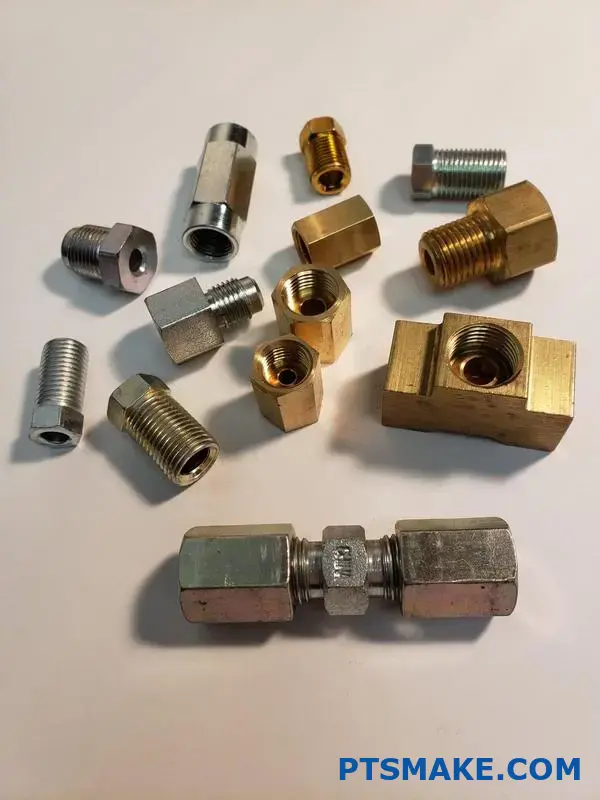
Meeting Specific Requirements with Precision Engineering
Custom Hydraulic Fittings: Real-World Success Stories
Client: US-based agricultural machinery manufacturer
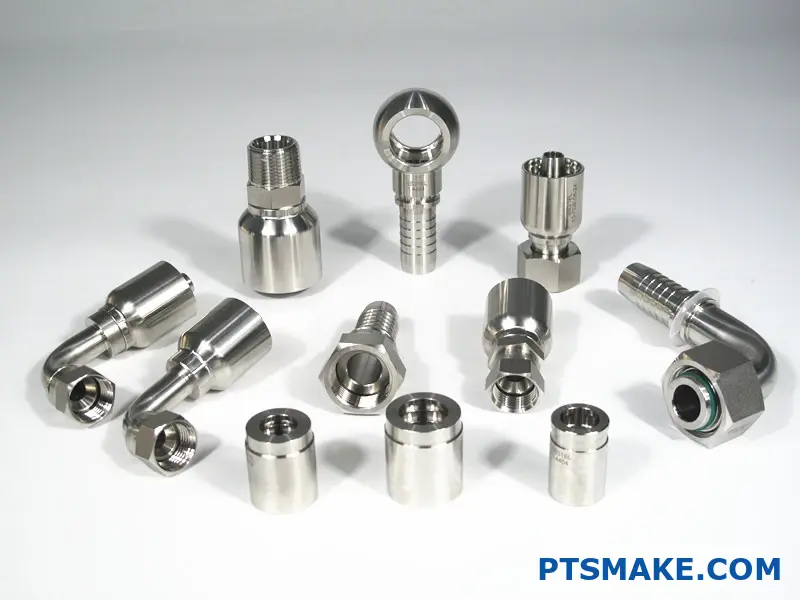
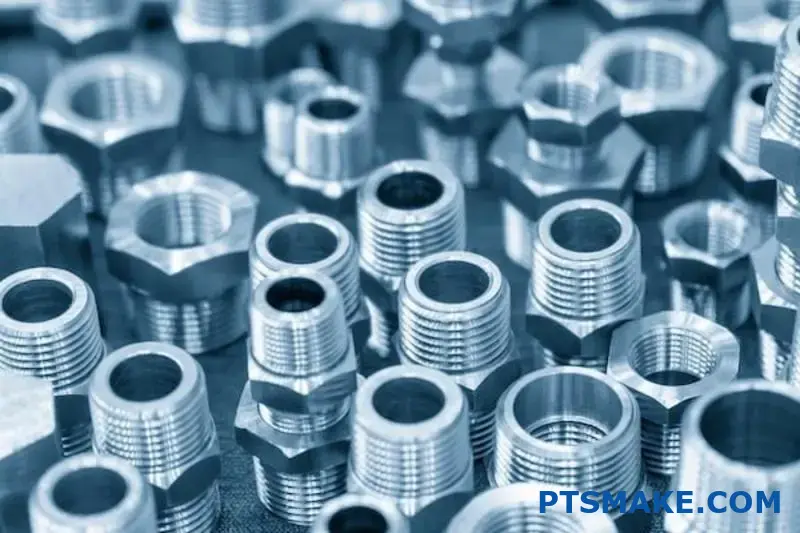
Client: German underwater ROV manufacturer
Client: Canadian construction equipment OEM
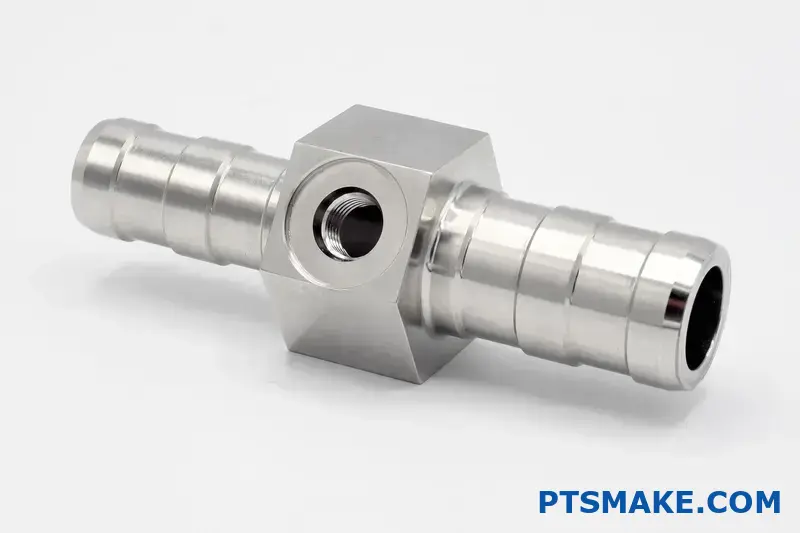
Contact Custom Hydraulic Fittings Expert Today!
We look forward to the opportunity to work with you and contribute to your project’s success.