Custom Hydraulic Cylinder Parts Manufacturer
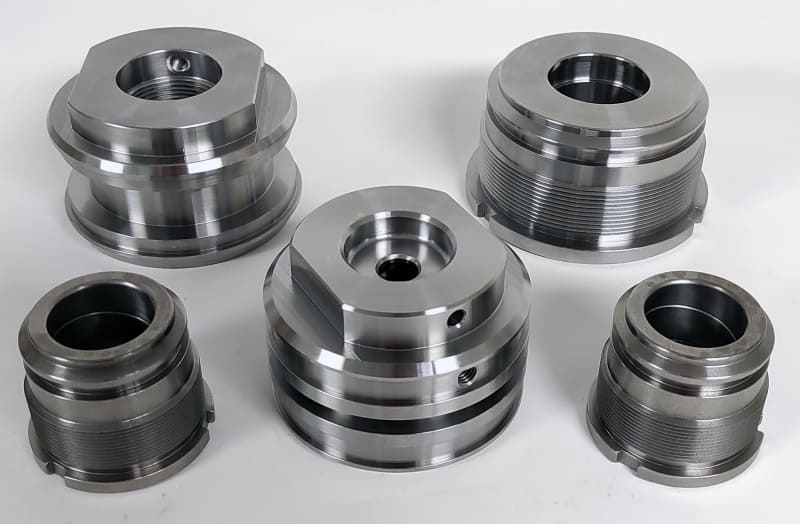
±0.001mm Tolerance Guarantee
Precision Custom Designs
72-Hour Sample Delivery
Global Logistics Network






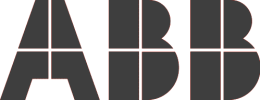

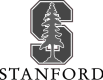
What Our Clients Say
Our clients are located worldwide, and their feedback speaks for itself. If you’d like to verify our reputation with customers in your area, don’t hesitate to contact us—we’d be happy to connect you with them and share relevant case studies.
Key Hydraulic Cylinder Component Parts
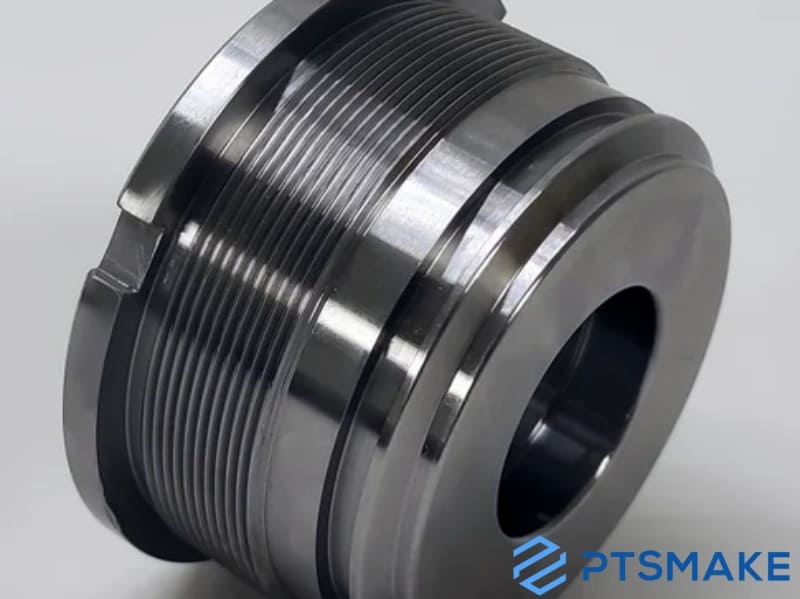
Hydraulic Cylinder Heads
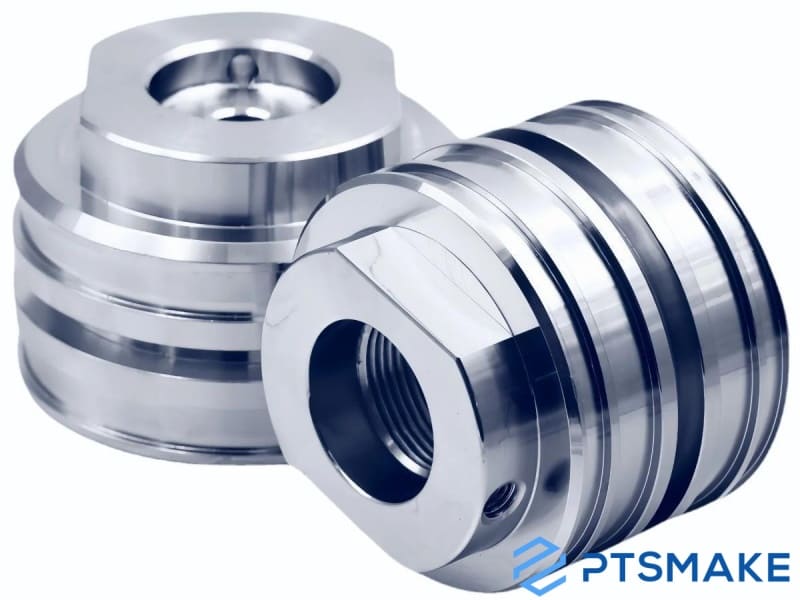
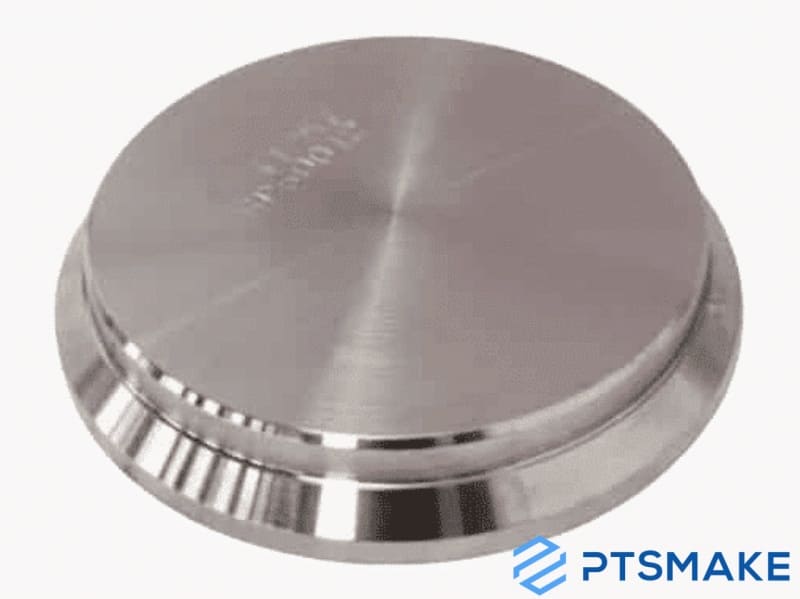
Hydraulic Cylinder End Caps
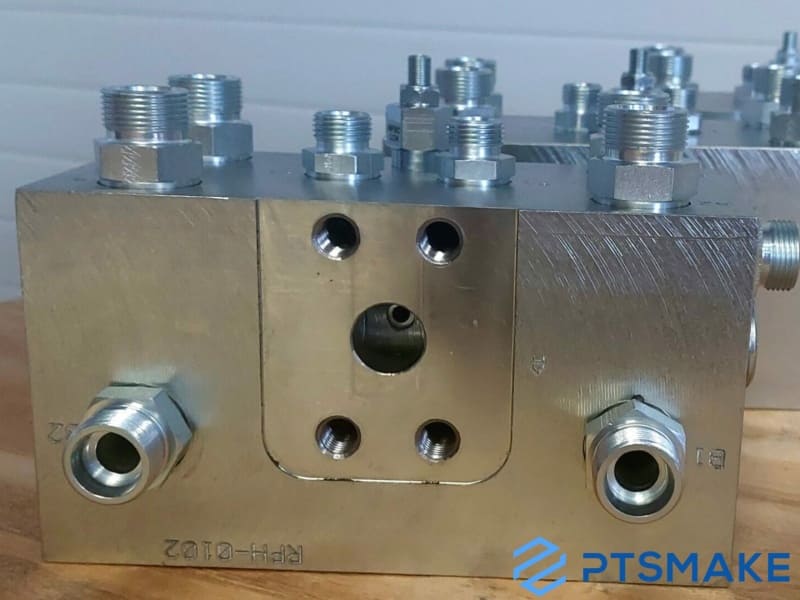
Hydraulic Cylinder Valve Blocks
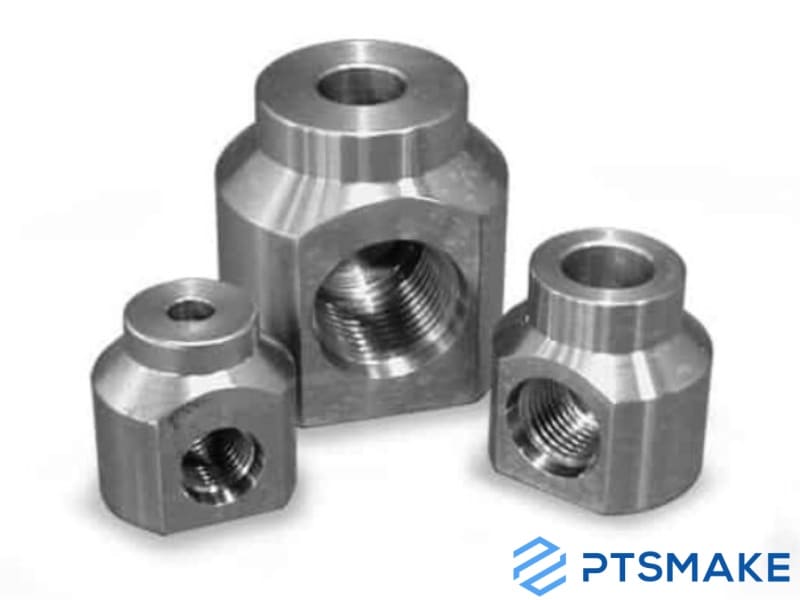
Hydraulic Cylinder Ports
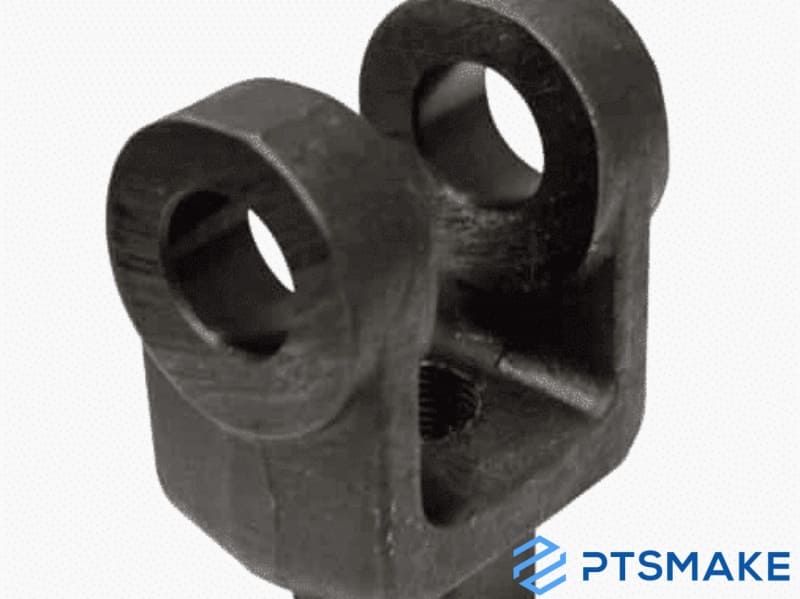
Hydraulic Cylinder Mounts
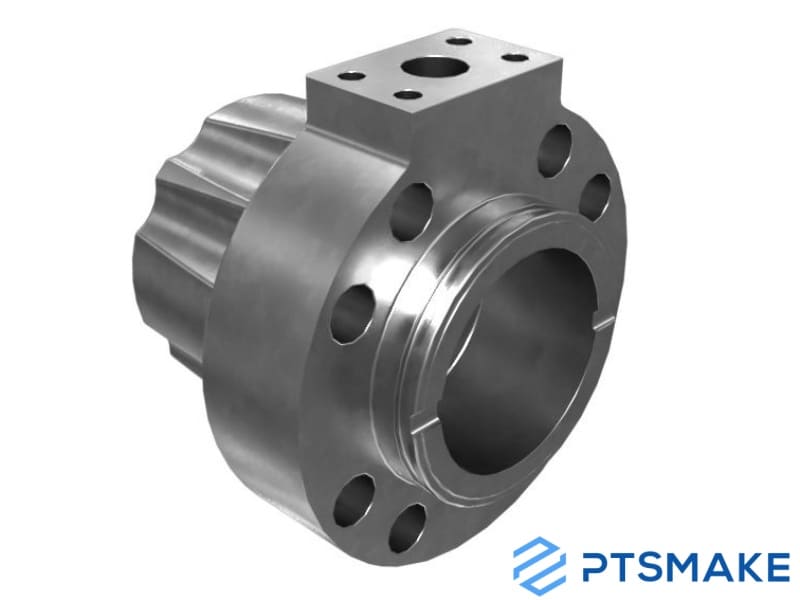
Hydraulic Cylinder Glands
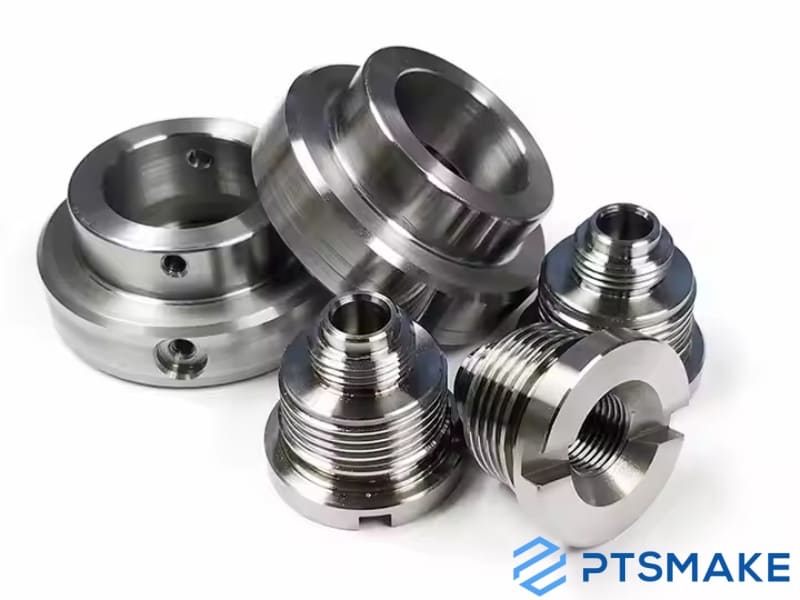
Other Hydraulic Accessories
Why Choose PTSMAKE for Hydraulic Cylinder Parts
We deliver ±0.001mm tolerances using 20+ years of CNC expertise.
20+ years of ISO-certified production. Every hydraulic component undergoes 3-stage precision inspection.
35% shorter lead times through optimized production workflows.
Optimized material usage reduces expenses. Free DFM analysis prevents redesign costs upfront.
How We Ensure Premium Quality in Hydraulic Cylinder Parts Manufacturing
- At PTSMAKE, quality control starts with material verification. We use certified raw materials from trusted suppliers for all hydraulic cylinder components. Every batch undergoes hardness testing and chemical composition analysis to meet ISO standards.
- Our CNC machining and injection molding processes are monitored in real-time. Advanced sensors track tolerances (±0.005mm) during production of rods, barrels, and seals. First-article inspections and random sampling prevent defects before mass production.
- We combine CMM measurements with hydraulic pressure testing. Critical parts like piston heads undergo 48-hour endurance simulations. Our lab technicians document test results that clients can access through our secure portal.
- Our commitment to quality extends beyond the technical to include exceptional client communication and support. Our 24/7 engineering support system is designed to prevent delays and facilitate immediate resolution of any issues that may arise. Moreover, our modular production system is adept at handling both prototype adjustments and bulk orders without compromising on quality, ensuring timely delivery and utmost client satisfaction.
- Through these comprehensive measures, PTSMAKE stands as a beacon of quality in the hydraulic cylinder parts industry, marrying cutting-edge technology with stringent quality control protocols. Our relentless pursuit of excellence guarantees that our clients receive nothing short of the best, every time.
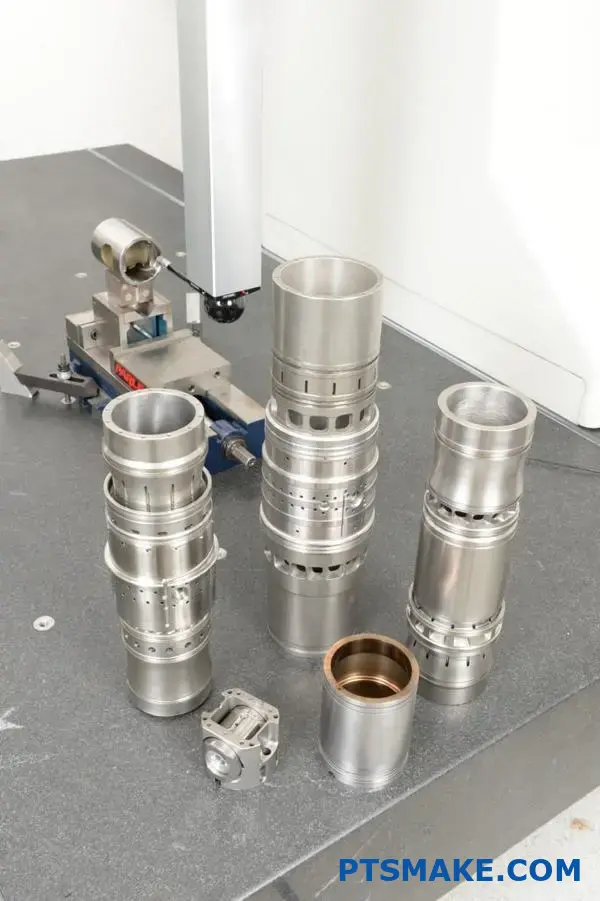
"We ordered 5,000 hydraulic gland nuts, Zero defects in two years of use. PTSMAKE’s CNC Machining expertise ensured consistent wall thickness, even on high-volume batches. Pricing beat local suppliers by 18%.
Emma Lee, Quality Assurance Lead, France"
Top Materials Used in Hydraulic Cylinder Parts Manufacturing
Carbon Steel
Stainless Steel
Aluminum Alloy
Brass (C36000)
Bronze (C93200)
Hardened Steel
Engineering Plastics
PTFE
Typical Lead Times for Hydraulic Cylinder Parts Manufacturing?
Understanding production timelines for hydraulic cylinder components
- Manufacturing lead times for hydraulic cylinder parts depend on part complexity, material availability, and order volume. Simple components like rods or seals may take 1-2 weeks, while complex assemblies often require 2-3 weeks. At PTSMAKE, we optimize CNC machining and injection molding processes to reduce wait times without compromising precision
- Our 20+ years of experience in hydraulic systems manufacturing helps predict and prevent delays. We maintain raw material stocks for common alloys like Stainless Steel and carbon steel. For urgent orders, our Shenzhen facility offers expedited 7-15 day turnaround for prototype quantities.
- Our CNC machining and injection molding teams work concurrently. This reduces wait times between manufacturing stages. For urgent orders, we offer expedited services with 30% faster turnaround without quality compromises.
- Lead times shrink through our integrated manufacturing approach. Unlike suppliers who outsource machining or molding, PTSMAKE handles all processes in-house. This eliminates coordination delays between multiple vendors, ensuring faster delivery of your hydraulic cylinder components.
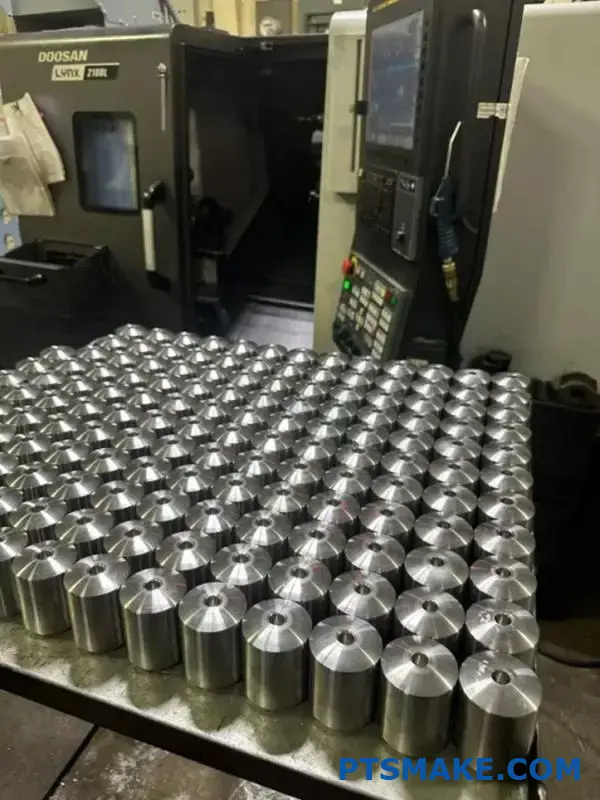
8 Steps to Manufacture High-Quality Hydraulic Cylinder Parts
1. Material Selection
2. CNC Programming
3. CNC Machining
4. Surface Treatment
5. Quality Testing
6. Assembly Prep
7. Prototype Testing
8. Bulk Production
Request a Custom Quote Today
Get an accurate estimate for your project today. Let us help you meet your exact specifications.
Cost-Effective Solutions for Hydraulic Cylinder Parts
1. Material Optimization
2. Precision Manufacturing
3. Bulk Production Savings
4. Rapid Prototyping
5. Streamlined Supply Chains
6. Preventive Maintenance
Customization Options for Hydraulic Cylinder Parts
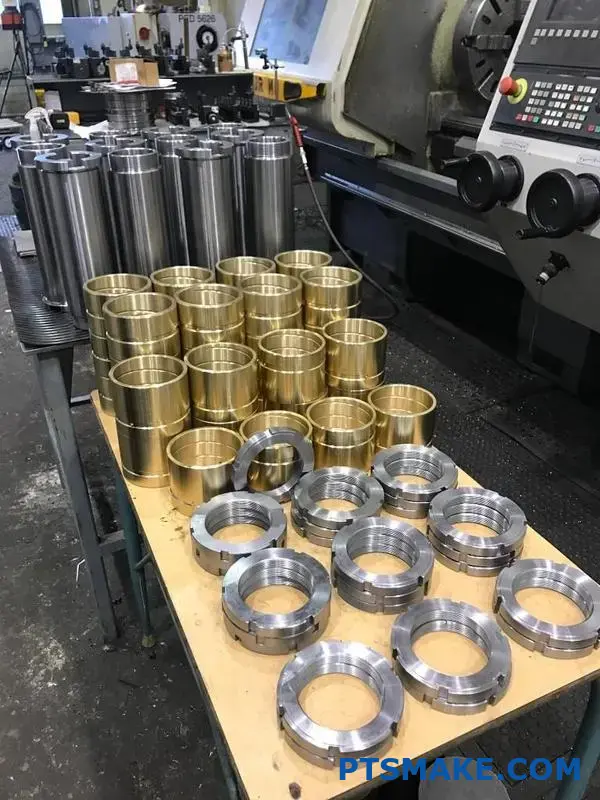
Tailored Solutions for Precision and Performance
Hydraulic Cylinder Parts Success Stories
Client: Emergency Replacement for Mining Equipment
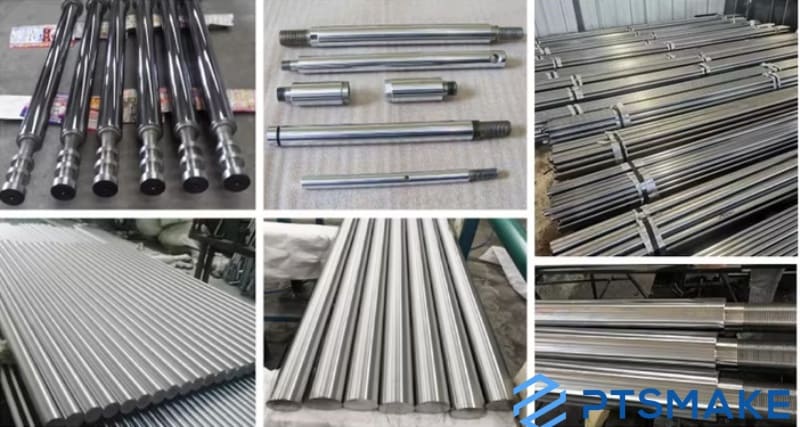
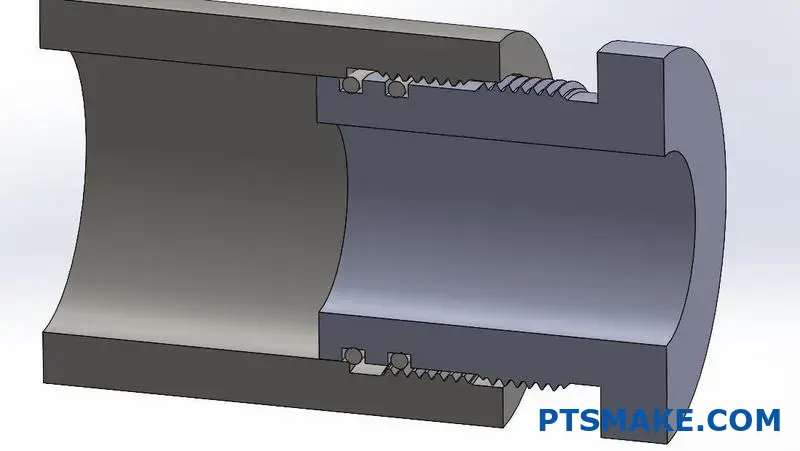
Client: High-Precision Seal Groove Machining
Client: Complex Port Block Manufacturing
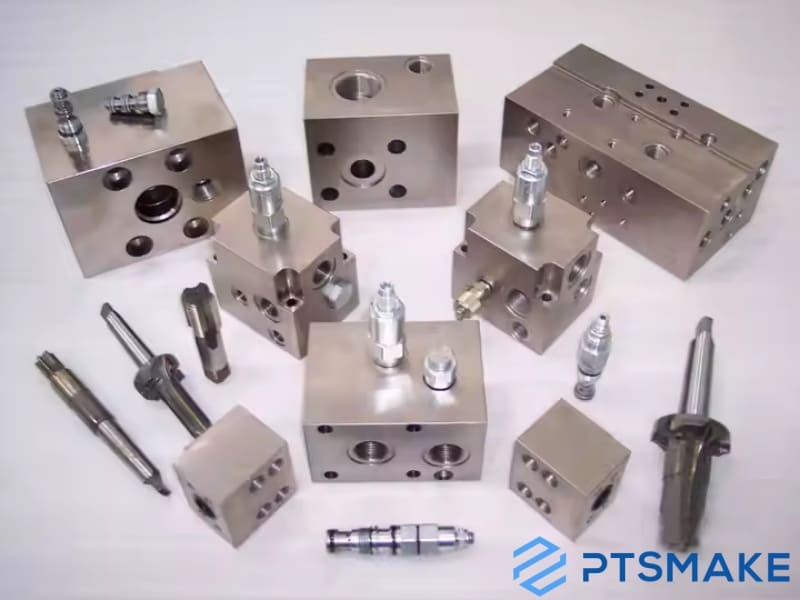
Contact Custom Hydraulic Cylinder Parts Expert Today!
We look forward to the opportunity to work with you and contribute to your project’s success.