PEEK Injection Molding Factory
As a leading PEEK injection molding manufacturer in China, we deliver high-performance polymer solutions for aerospace, medical, and industrial applications. 20+ years expertise, ISO 9001 certified.
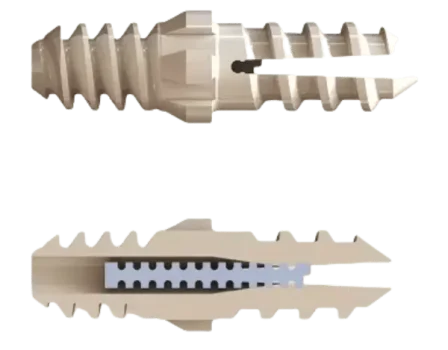
High-Performance PEEK Materials
Complex Part Precision Molding
Fast Turnaround & Global Shipping
Machines Ranging From 30 Tons to 1,600 Tons






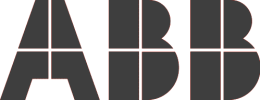

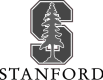
What Our Clients Say
Our clients are located worldwide, and their feedback speaks for itself. If you’d like to verify our reputation with customers in your area, don’t hesitate to contact us—we’d be happy to connect you with them and share relevant case studies.
8 Key Industrial Applications of PEEK Injection Molding Solutions
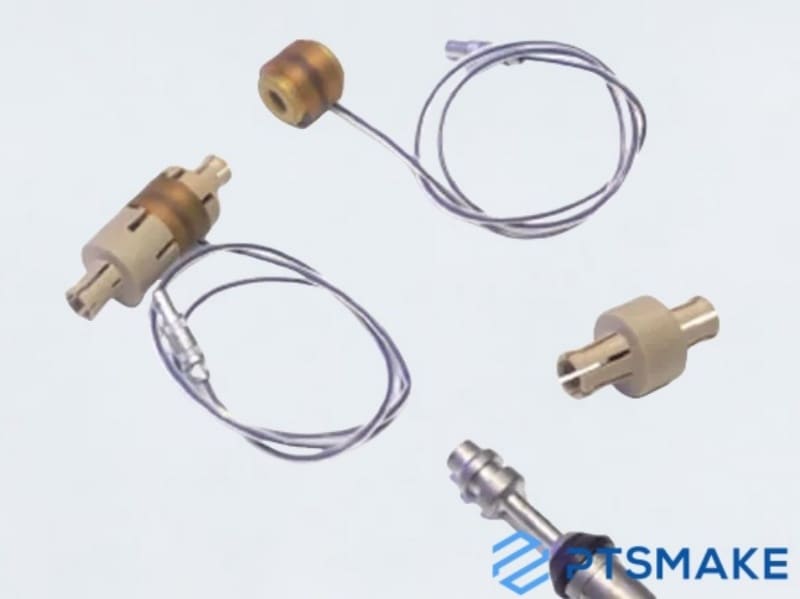
Aerospace Components
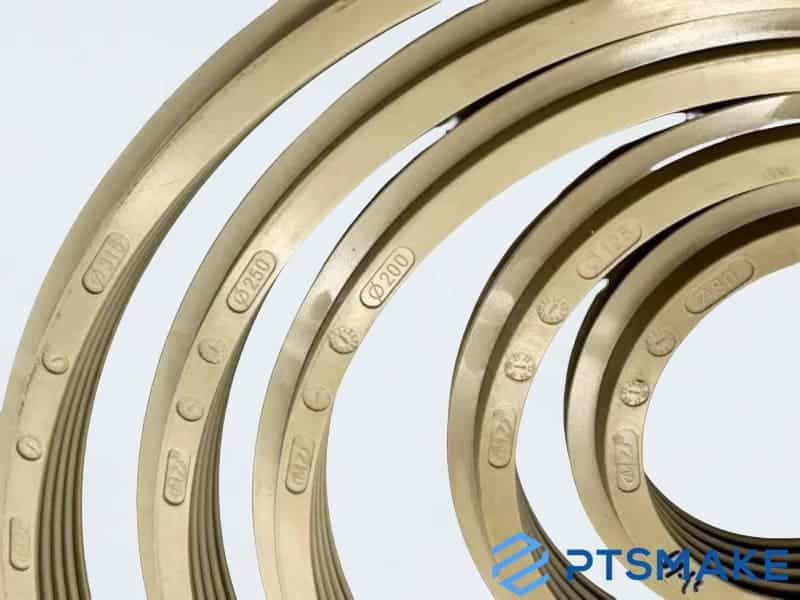
Automotive Seals
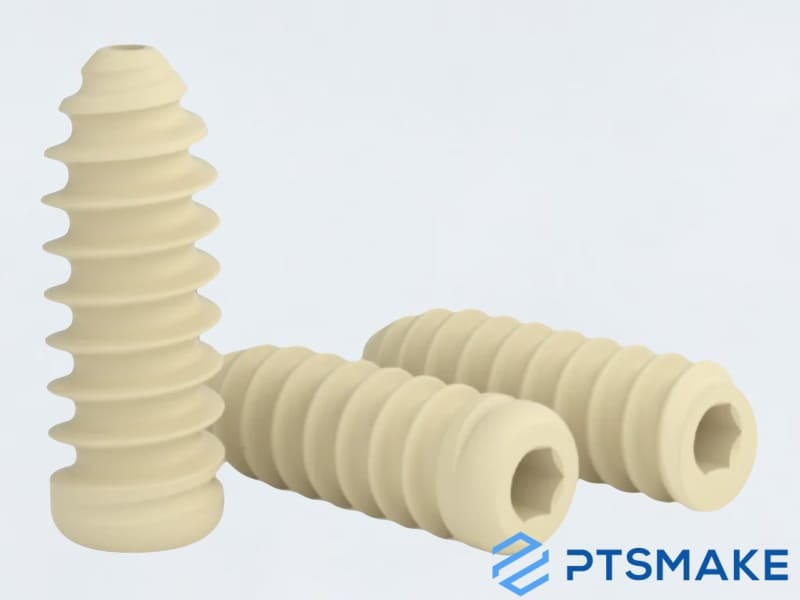
Medical Screws
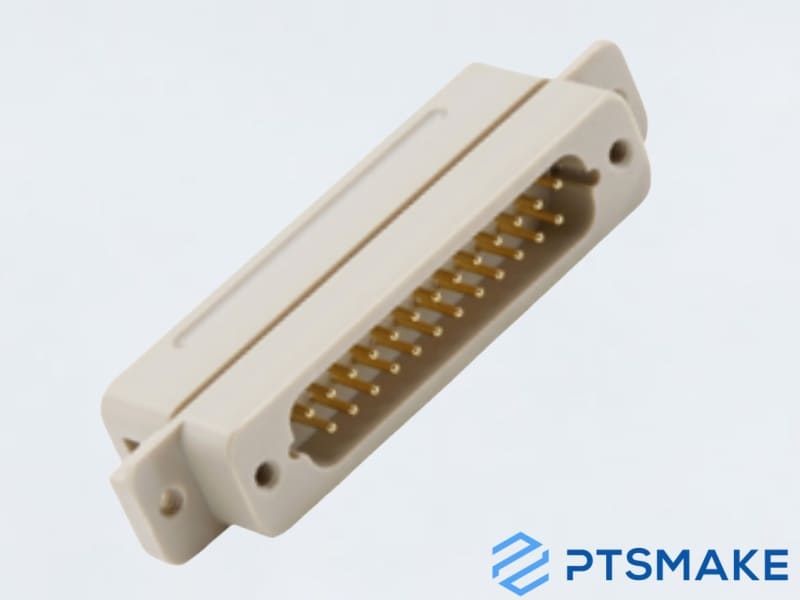
Electronics Connectors
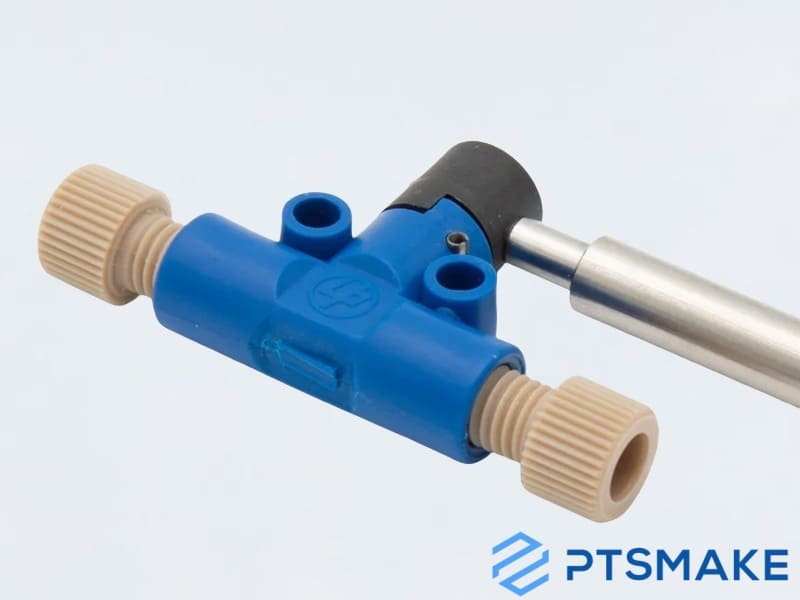
Oil & Gas Valves
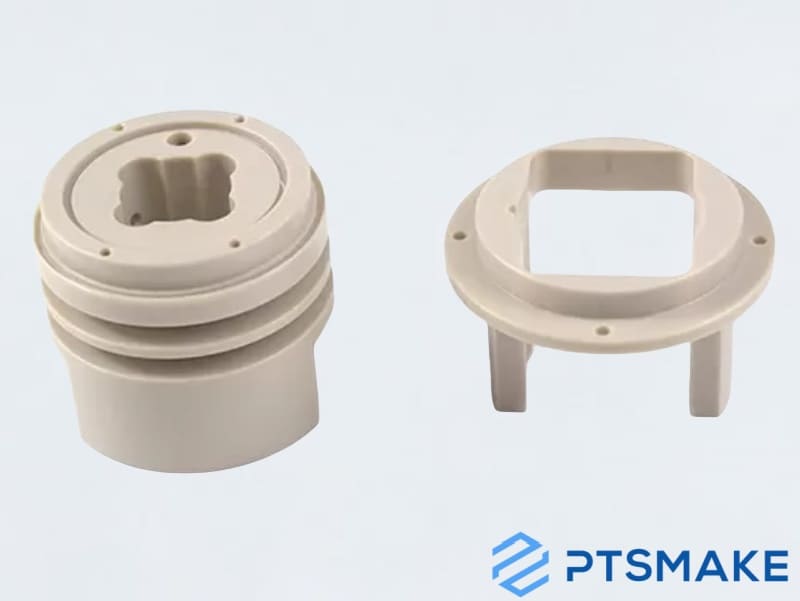
Robotics Parts
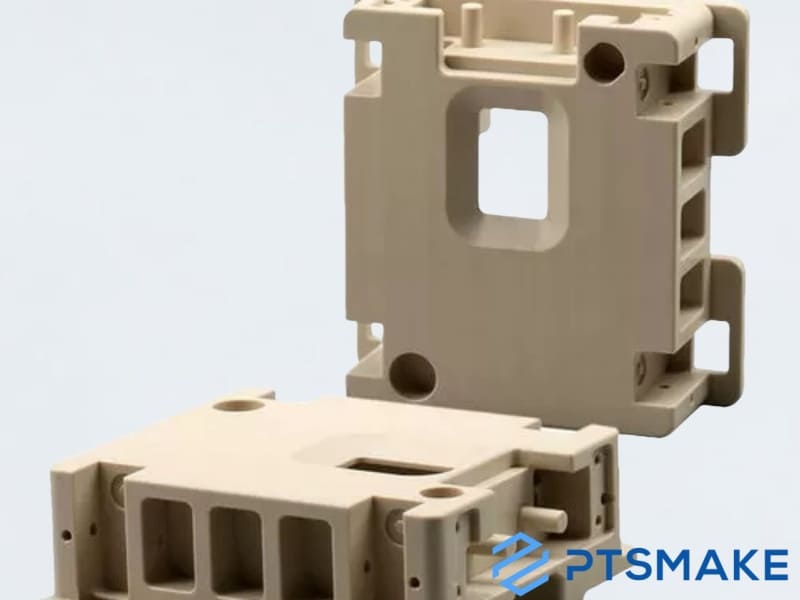
Industrial Housings
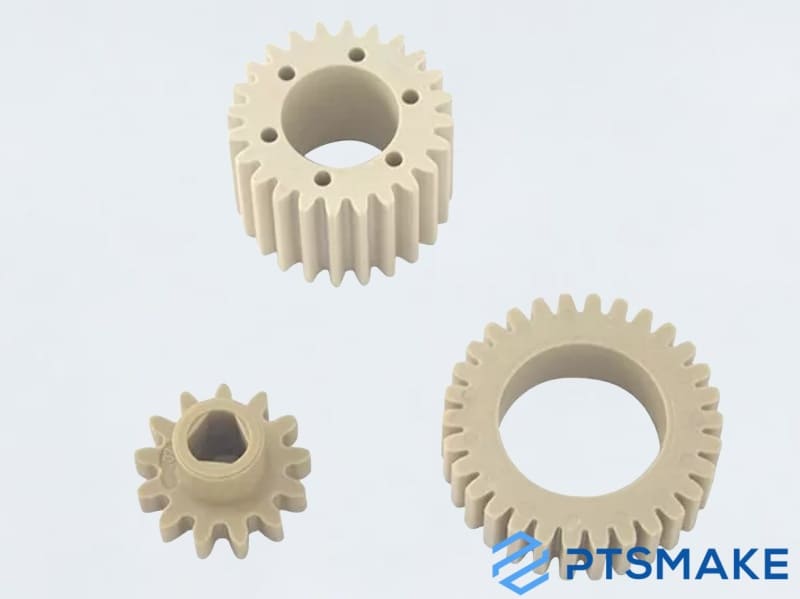
Industrial Gears
Why Choose PTSMAKE for PEEK Injection Molding?
PTSMAKE has over 20 years of injection molding experience, providing solutions trusted by global brands like BMW and Huawei.
Utilizing advancedmachines, we ensure dimensional accuracy and optimize designs, reducing production costs by up to 30%.
Our 50+ advanced molding machines enable 15-day prototype cycles and 30% faster production timelines.
Our 3-stage quality checks maintain a defect rate below 0.2% with full traceability for every molded parts.
Quality Control in PEEK Injection Molding: How We Ensure Precision and Reliability
- At PTSMAKE, quality control is the backbone of our PEEK injection molding services. Since 2002, we’ve built our reputation by exceeding strict industry standards for aerospace, medical, and automotive clients. For high-performance materials like PEEK, even minor flaws can lead to part failure. That’s why we enforce a 6-step quality control process to eliminate risks at every stage.
- Step 1: Material Certification & Pre-Processing Checks
We source PEEK pellets only from ISO-certified suppliers. Every batch undergoes FTIR testing to verify chemical composition and moisture content. Before molding, we pre-dry materials to prevent bubbles or warping—critical for maintaining PEEK’s mechanical stability.
- Step 2: Precision Mold Design & Validation
Our engineers use Moldflow simulation to predict flow behavior and cooling stresses. All molds are CNC-machined in-house, with tolerances held to ±0.005mm. We run 50+ test shots per mold, measuring dimensions and surface finish against your CAD specs before mass production.
- Step 3: Real-Time Process Monitoring
During molding, sensors track temperature (±5°C), pressure (0.7MPa resolution), and cycle times. If parameters drift, our system auto-pauses production and alerts technicians. This prevents defects like sink marks or incomplete filling—common pain points in PEEK projects.
- Step 4: Post-Molding Inspections
First-article inspections include CMM measurements and tensile tests. We check 100% of parts for visual defects under 10x magnification. For medical-grade orders, we conduct biocompatibility tests per ISO 10993 protocols.
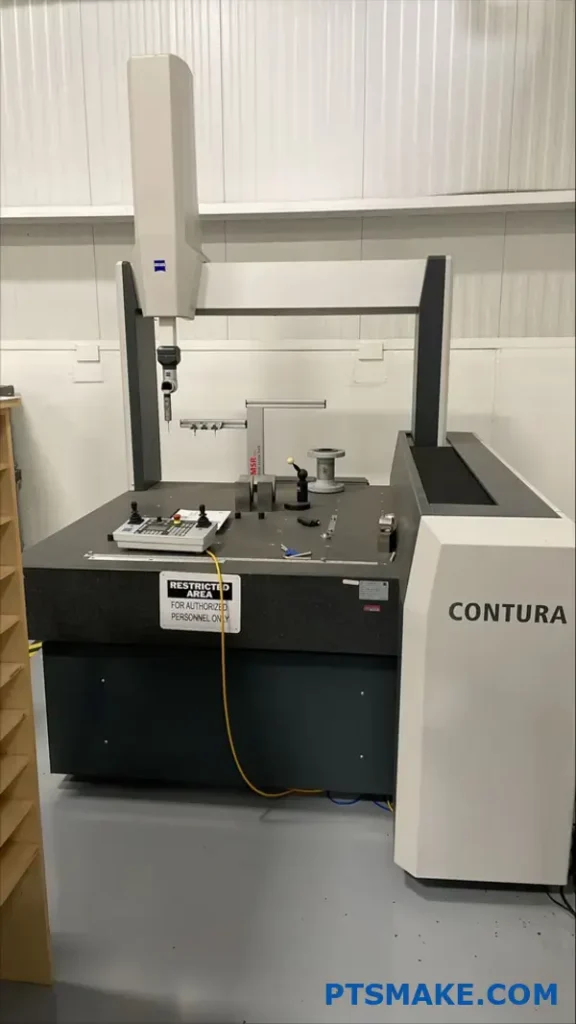
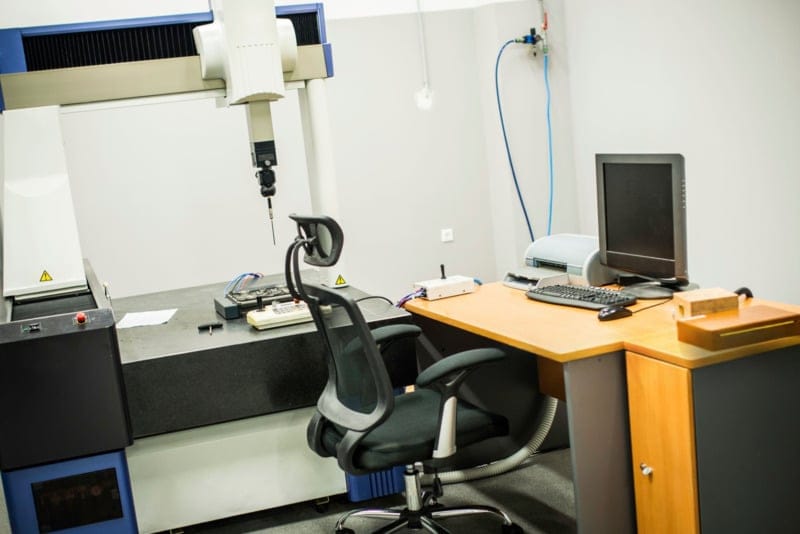
- Step 5: Traceability & Documentation
Every batch ships with a quality dossier: material certs, inspection reports, and process logs. Our cloud platform lets you track production status 24/7, addressing concerns like delivery delays upfront.
- Step 6: Continuous Improvement
After delivery, we analyze your feedback to refine processes. Over 80% of clients report 30% fewer revisions after switching to PTSMAKE—proof of our commitment to long-term partnerships.
- With 4 subsidiaries and clients like Huawei and BMW, we simplify complex supply chains. Our US-based project managers respond within 2 hours, ensuring alignment across design, production, and logistics
We needed PEEK parts with ultra-thin walls for a medical device. PTSMAKE not only nailed the 0.2mm tolerances but also delivered in 12 days. Their engineers even suggested a better cooling design, saving us 20% cycle time. Zero defects after 10k+ shots!
Mark Sullivan, Medical Device Engineer, USA"
Top Materials Used in PEEK Injection Molding
Virgin PEEK
Glass-Fiber Reinforced PEEK
Wear-Resistant PEEK
Carbon-Fiber Reinforced PEEK
ESD PEEK (Electrostatic Discharge PEEK)
Mineral-Filled PEEK
Typical Lead Times for PEEK Injection Molding
What to Expect for PEEK Injection Molding Lead Times
- Lead times for PEEK injection molding vary based on project complexity, order volume, and design requirements. Simple geometries with standard tooling may take 4-6 weeks. Complex parts requiring custom molds or tight tolerances often need 6-8 weeks. At PTSMAKE, we optimize processes to meet deadlines without compromising precision.
- Factors like material availability, mold design revisions, and quality checks impact timelines. Our 20+ years of experience in precision manufacturing help us anticipate delays. We maintain a stocked inventory of PEEK resins and use advanced CNC machining for faster mold creation. This reduces lead times by 15-20% compared to industry averages.
- We prioritize transparency. Clients receive weekly updates and real-time access to project dashboards. For urgent needs, our rapid prototyping service delivers samples in 7-10 days. This flexibility supports industries like aerospace and medical devices, where speed and accuracy are critical.
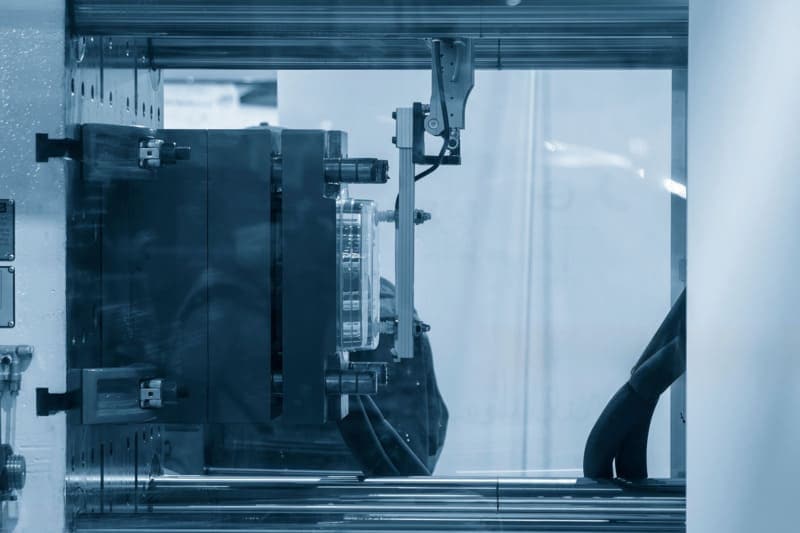
8 Key Steps in PEEK Injection Molding Manufacturing
Discover the precise process behind high-quality PEEK injection molding parts for aerospace, medical, and robotics industries.
1. Material Preparation
2. Pre-Drying
3. Mold Setup
4. Machine Parameters
5. Injection Process
6. Cooling Phase
7. Post-Processing
8. Quality Inspection
Request a Custom Quote Today
Get an accurate estimate for your project today. Let us help you meet your exact specifications.
Cost-Effective Solutions for PEEK Injection Molding: 7 Proven Strategies to Reduce Costs
1. Material Optimization
2. Mold Design Efficiency
3. Process Automation
4. Bulk Material Purchasing
5. Secondary Operations
6. Design Simplification
7. Scalable Production
Customization Options for PEEK Injection Molding
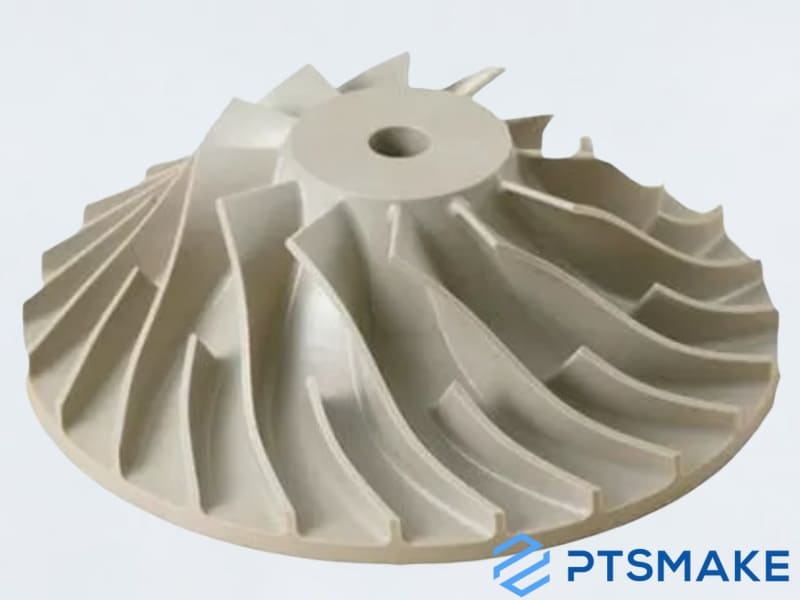
PEEK Injection Molding Success Stories in B2B Manufacturing
High-Performance Medical Device Components
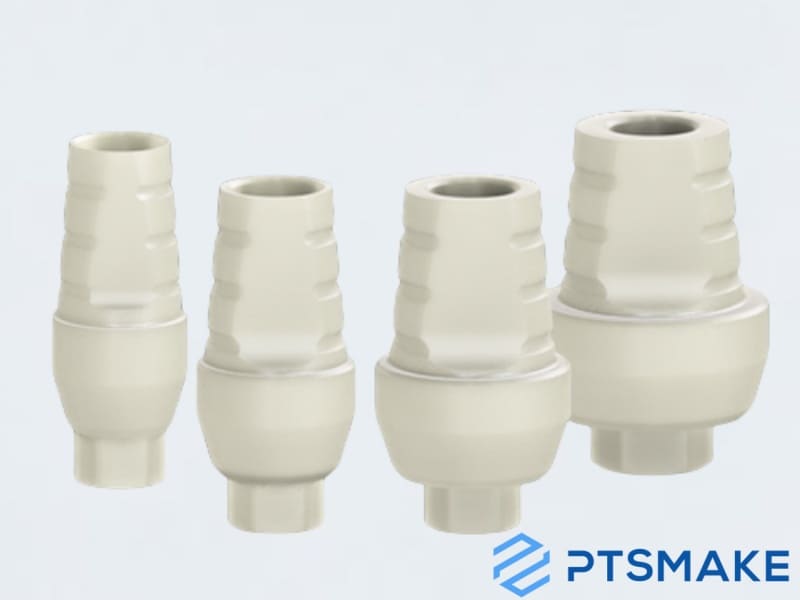
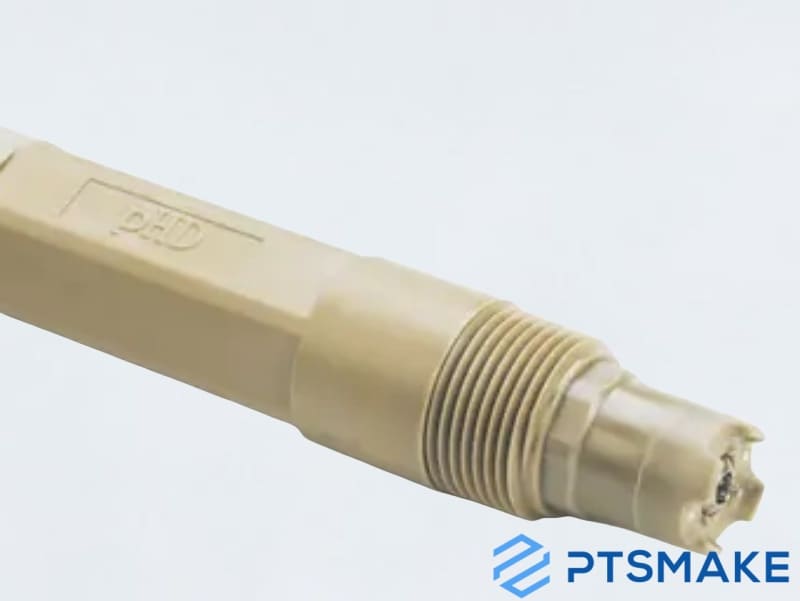
Automotive Sensor Housing for Extreme Conditions
Aerospace Connector Insulation
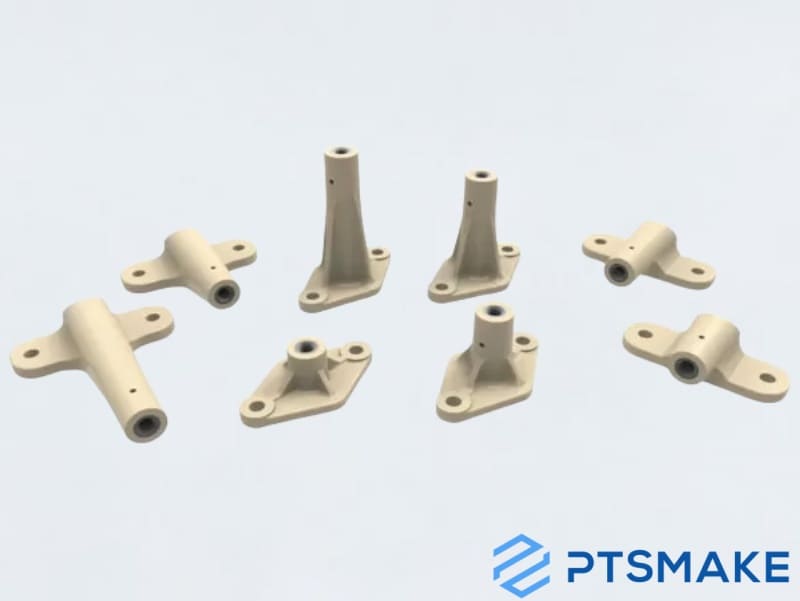
Contact Custom Peek Injection Molding Expert Today!
We look forward to the opportunity to work with you and contribute to your project’s success.