Custom Plastic Injection
Molding Service
We are committed to being your trusted partner for plastic injection molding, from prototype to production.
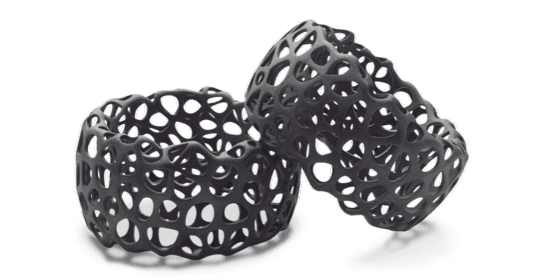
No geometric limitations, Good at complex project, 2k molding.
Machines Ranging From
30 Tons to 1,600 Tons
MOQ 50 PCS
100+ Plastic Materials






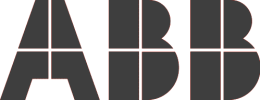

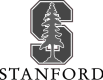
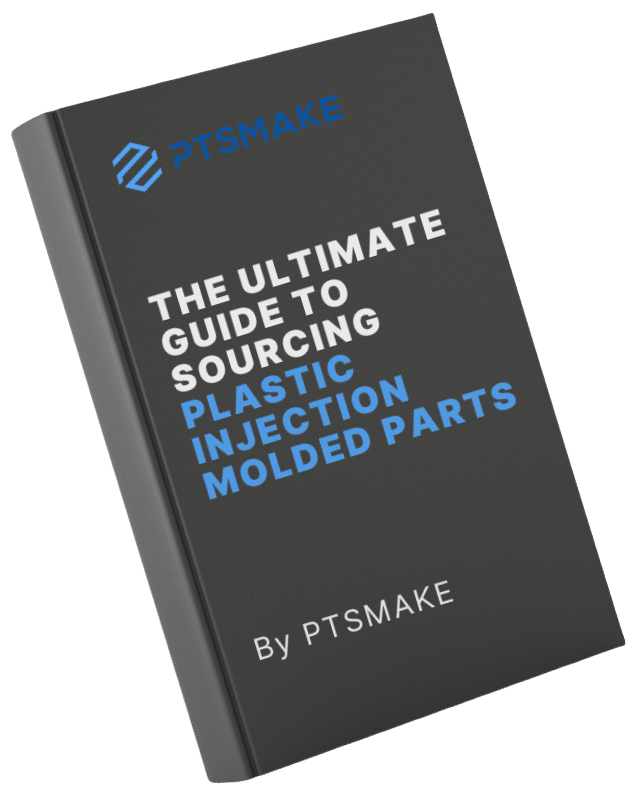
To save you time, we have also prepared a PDF version containing all the contents of this page, only leave your email and you will get the download link immediately.
Quality Control and Inspection
We are dedicated to delivering high-quality injection molded products. Our quality control process ensures that each product meets your expectations.
Quality Control Process
At our injection molding factory, we ensure that every product meets high standards. Here is how we manage quality:
- Raw Material Inspection: We carefully check all raw materials before production. This ensures that only materials of the required quality are used.
- Production Monitoring: During production, we use advanced equipment to monitor each step. This helps us maintain precision and accuracy throughout the process.
- In-Process Inspections: We conduct inspections at various stages of production. This allows us to identify and fix any issues quickly.
- Final Product Inspection: After production, we thoroughly examine each product. We ensure that there are no defects and that each item meets our quality standards.
- Packaging and Shipment Checks: Before packaging and shipping, we perform another inspection. We make sure that the products are safely packaged and ready for delivery.
- Trained Quality Team: Our quality team is professionally trained. They focus on every detail to maintain our high-quality standards.
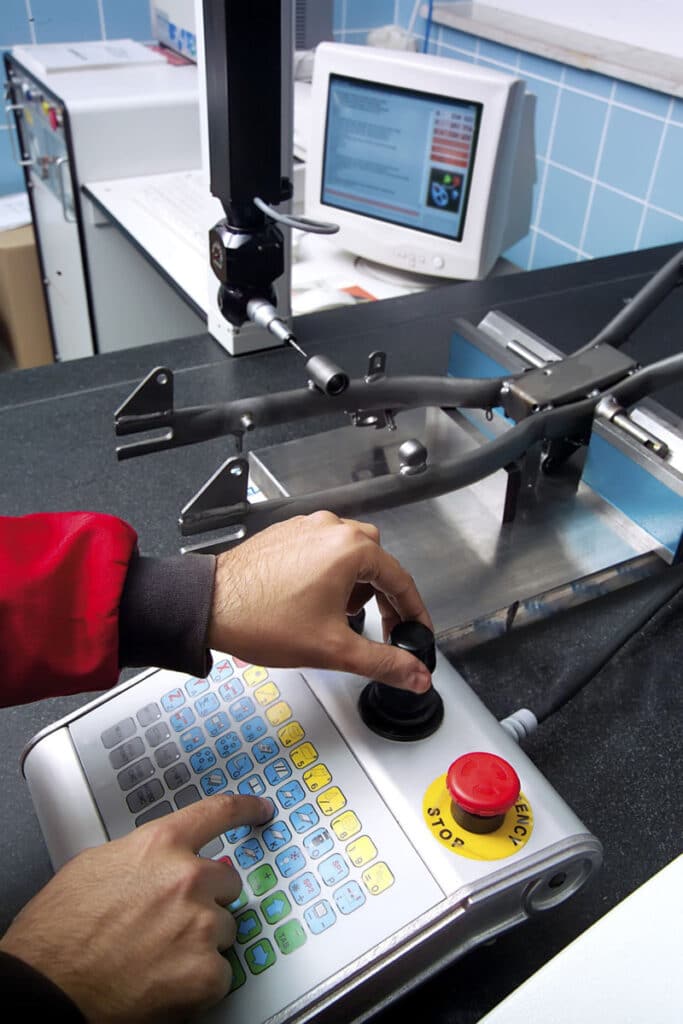
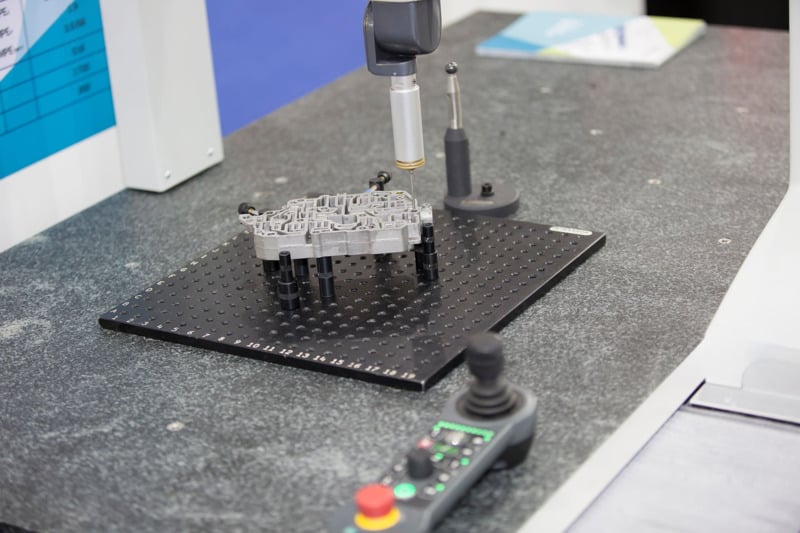
CMM
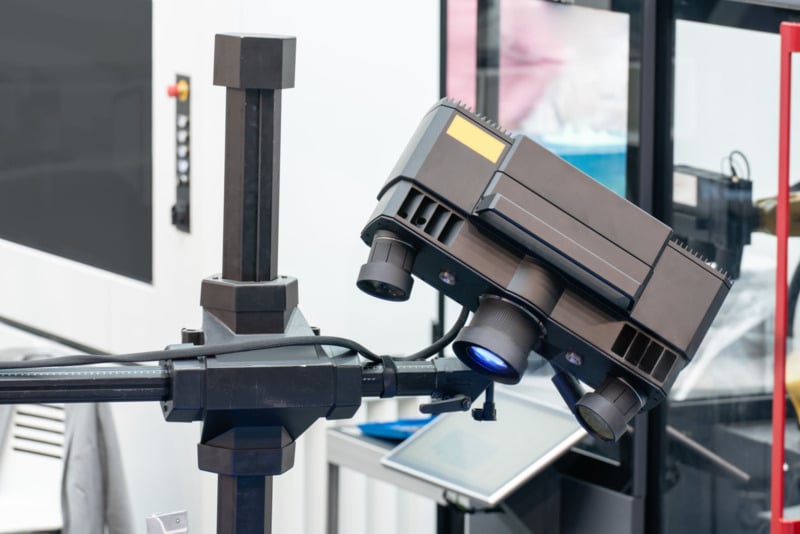
GOM 3D-Scanner
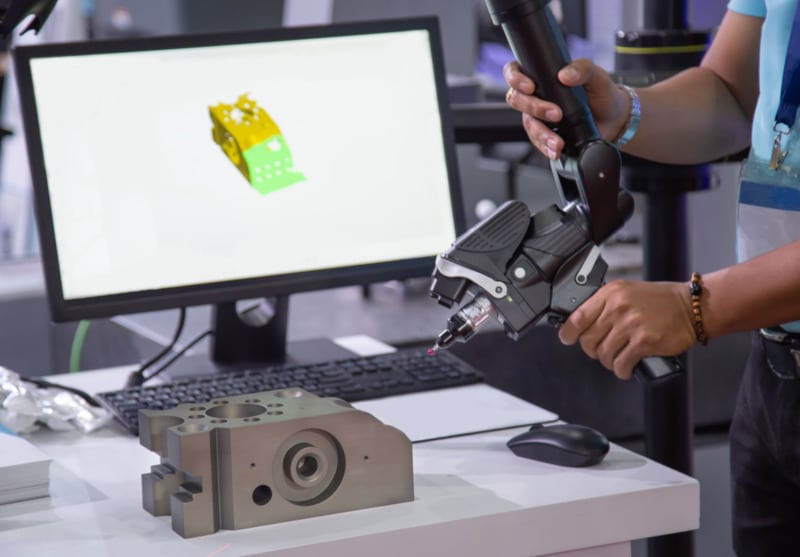
Portable CMM
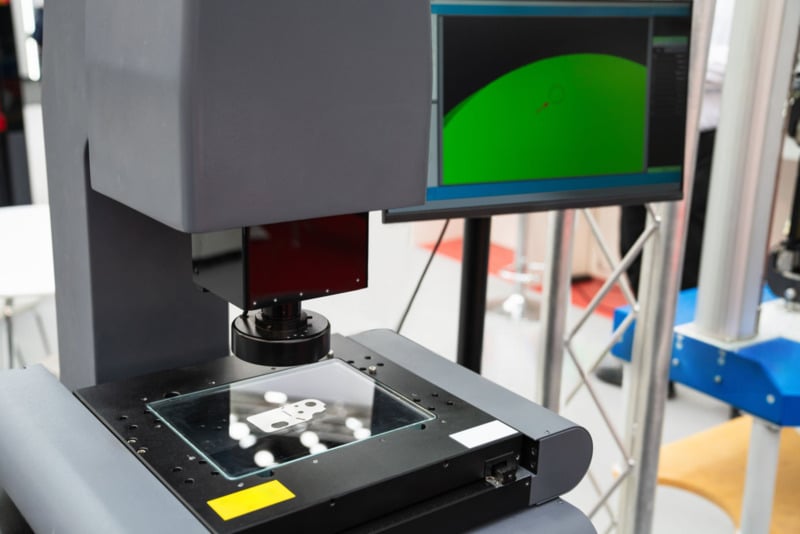
Projector
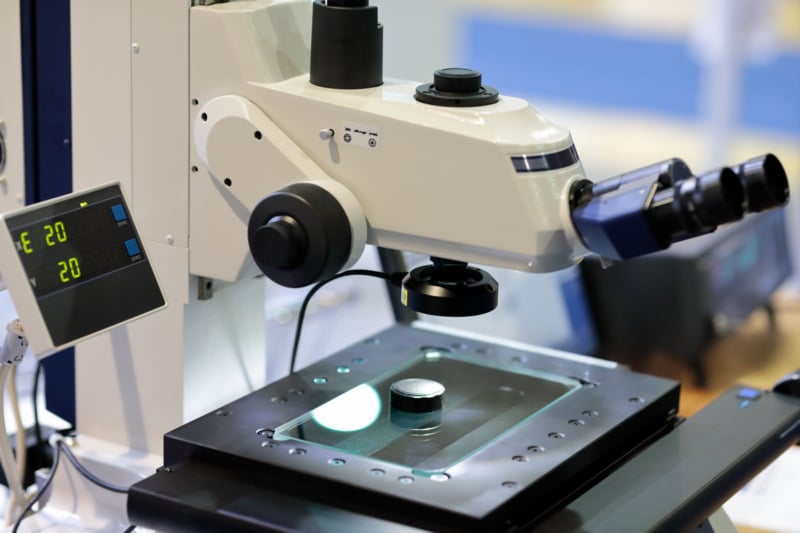
Optical microscope
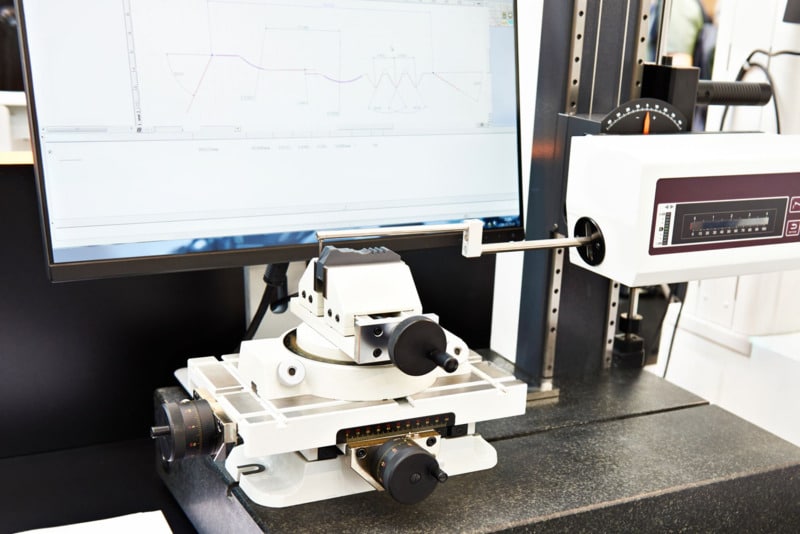
Roughness Tester
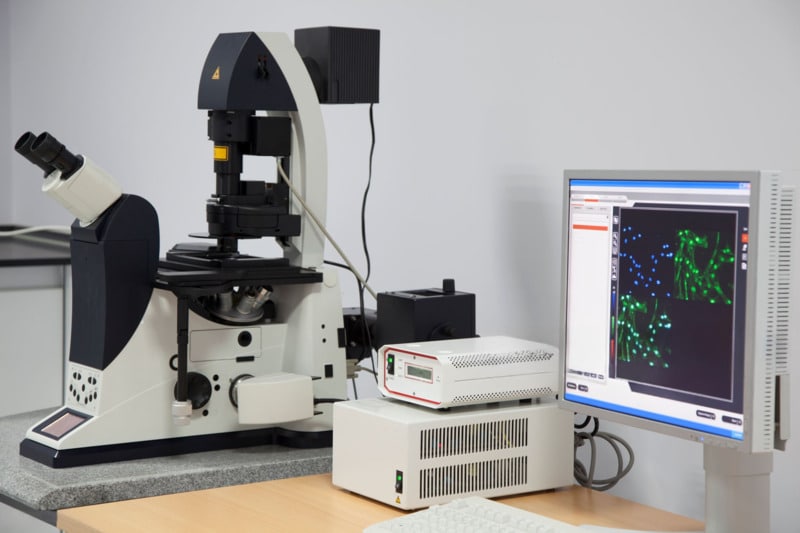
Raw material analyzer
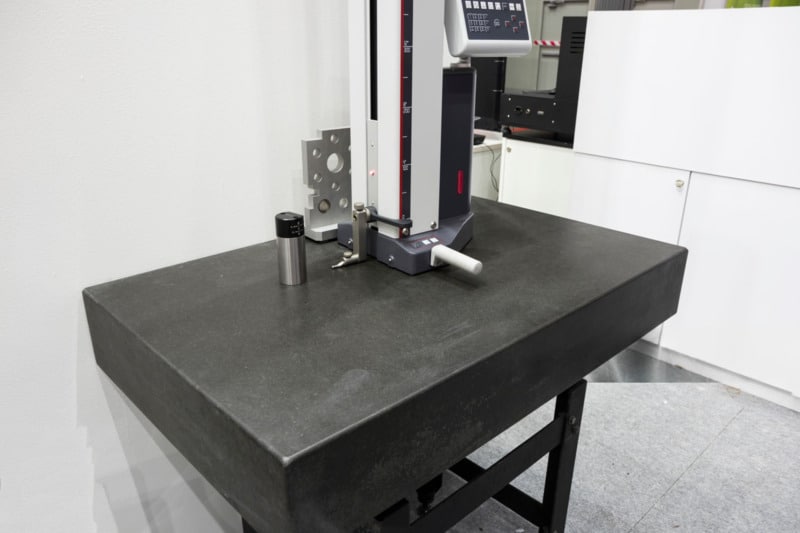
Altimeter
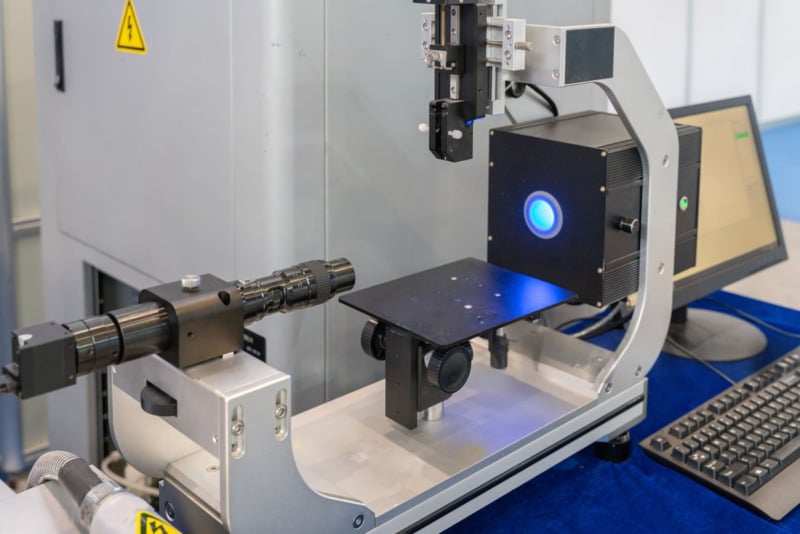
Laser Inspection
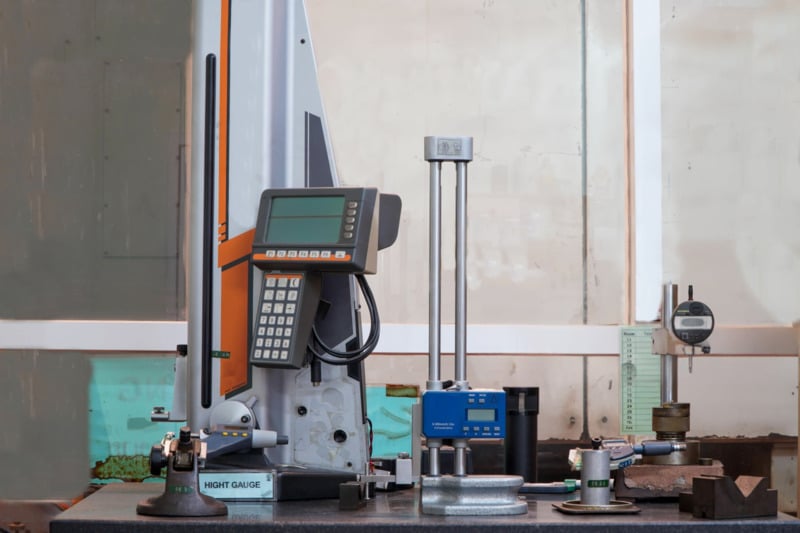
Others
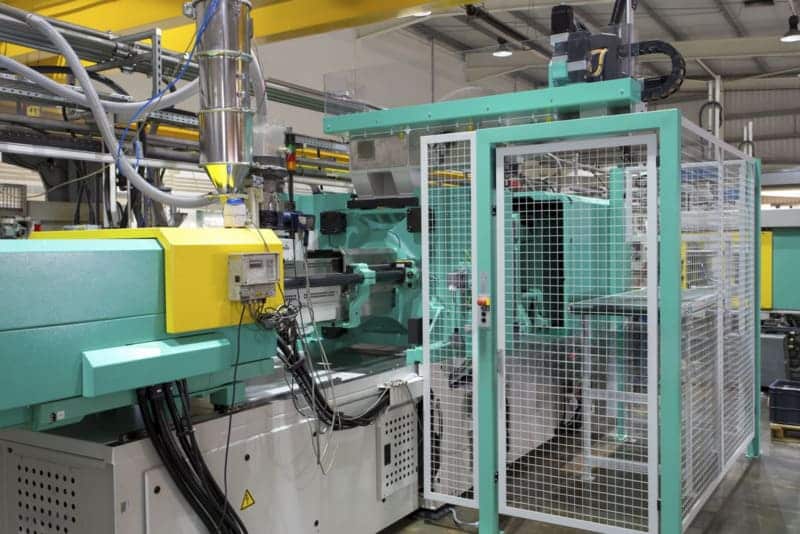
Injection Machine
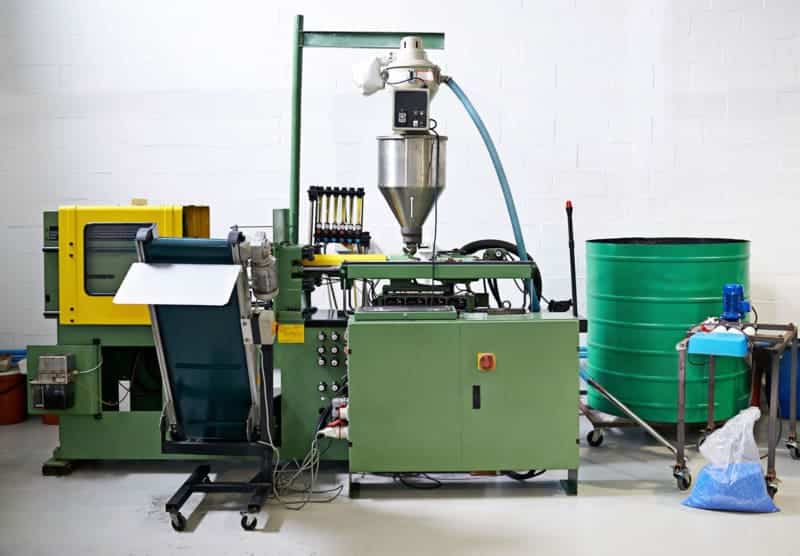
Vertical Injection Machine
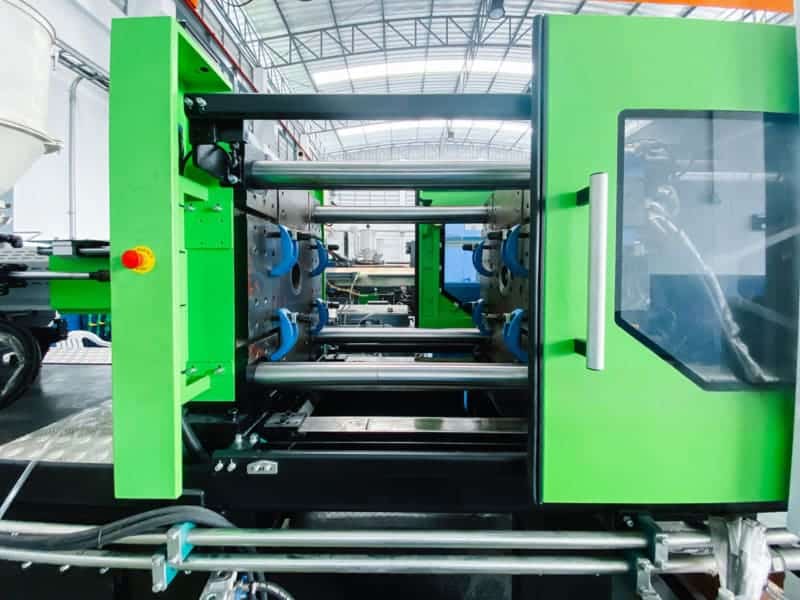
Double-shot Injection Machine
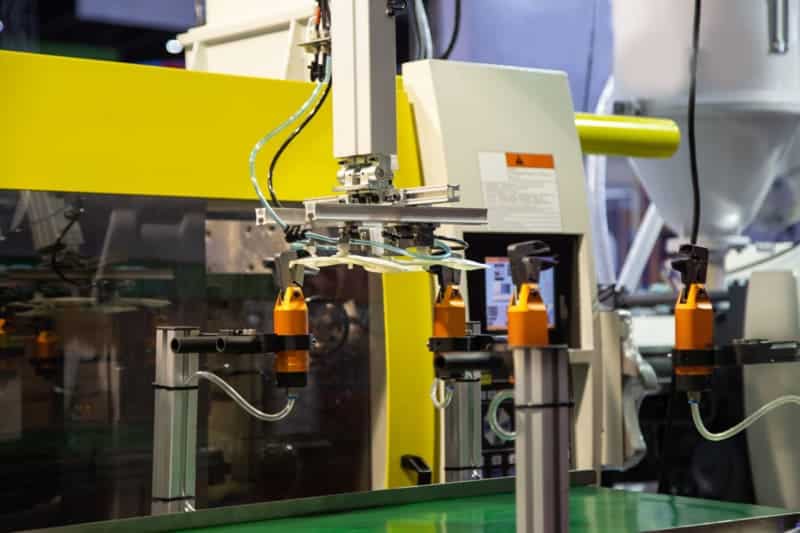
Robotic Arms for Automated Molding
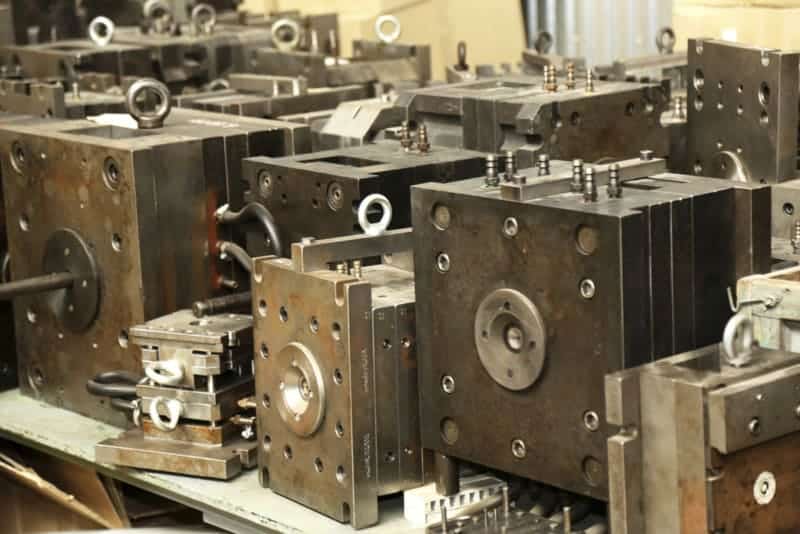
Various Plastic Injection Molds
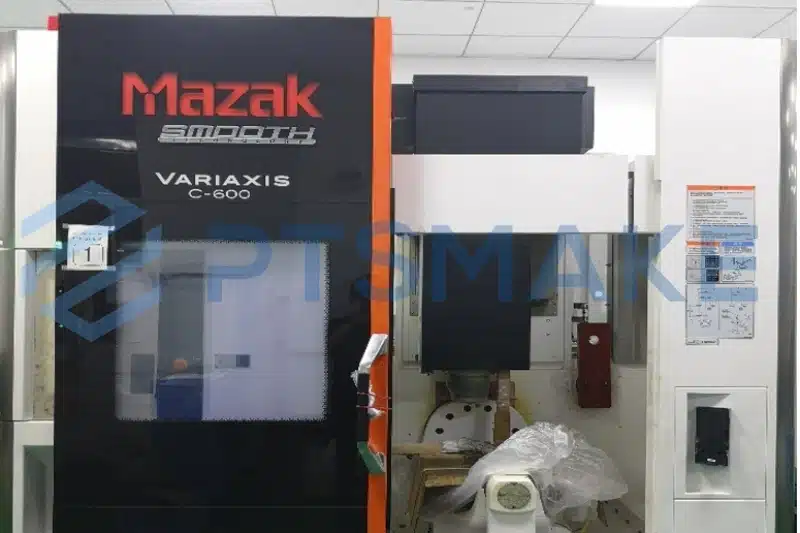
CNC Milling Machine (Japan)
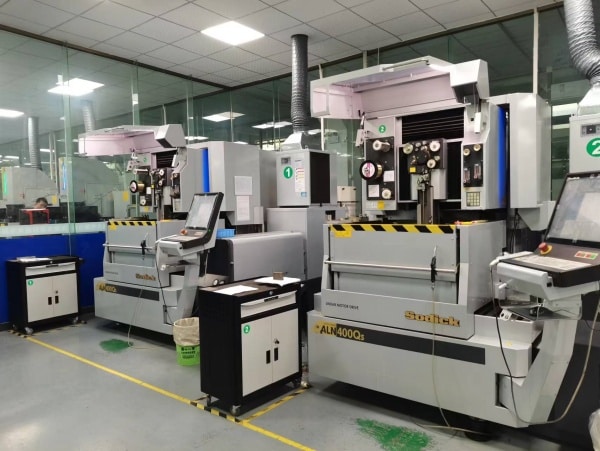
Slow Wire Cut (Japan)
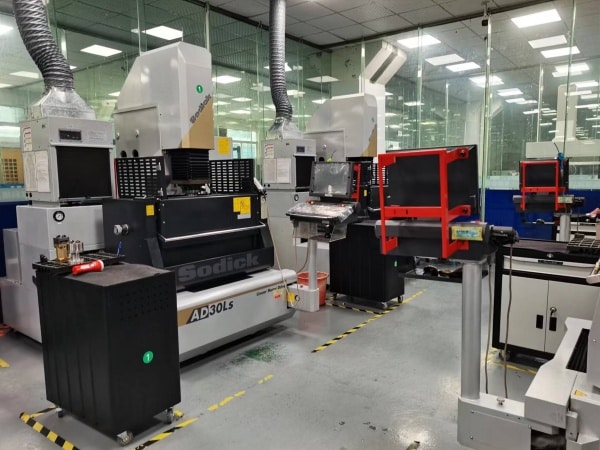
Electric Discharge Machining (Japan)
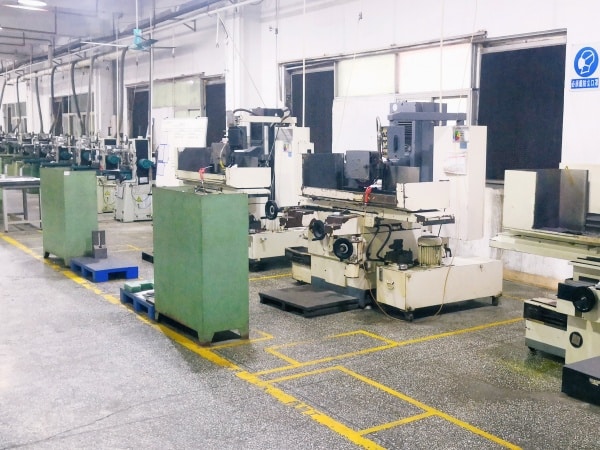
Precision Grinding Machine (Japan)
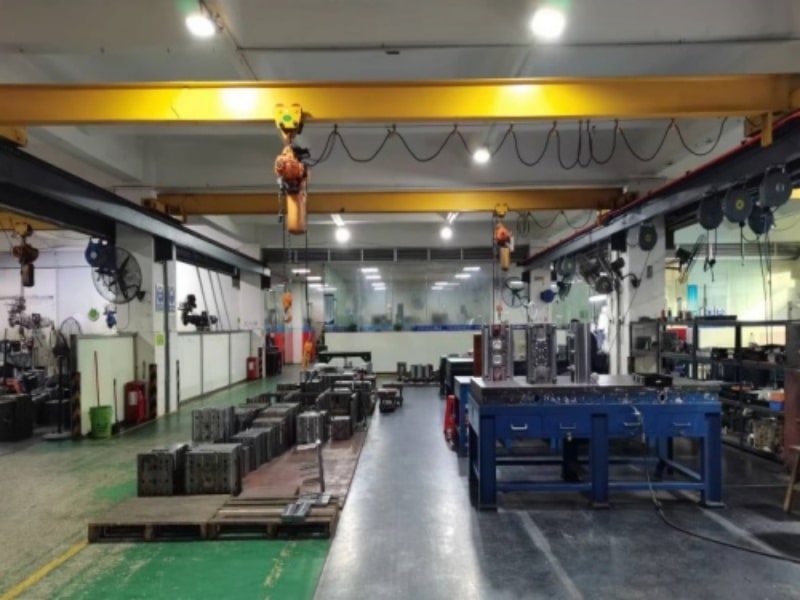
Mold Assembly
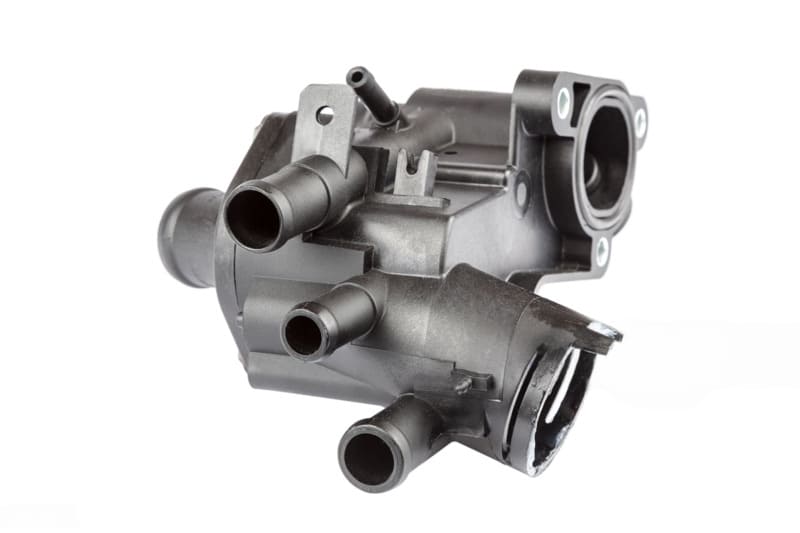
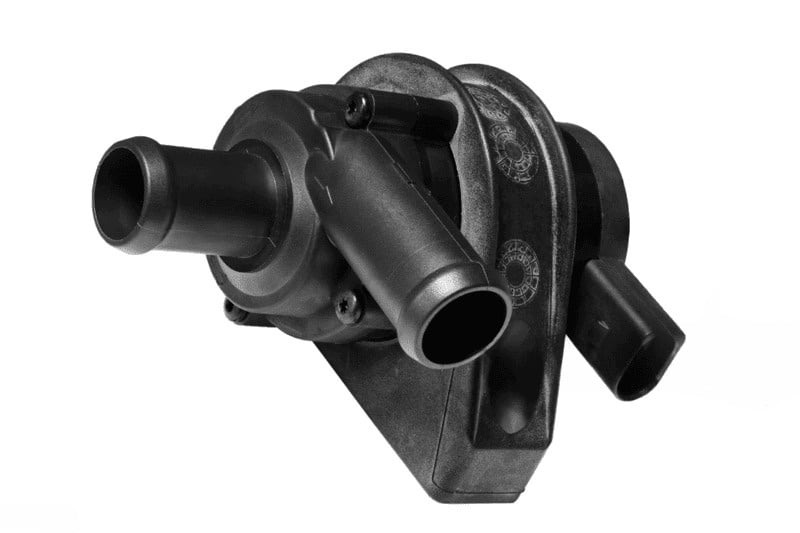

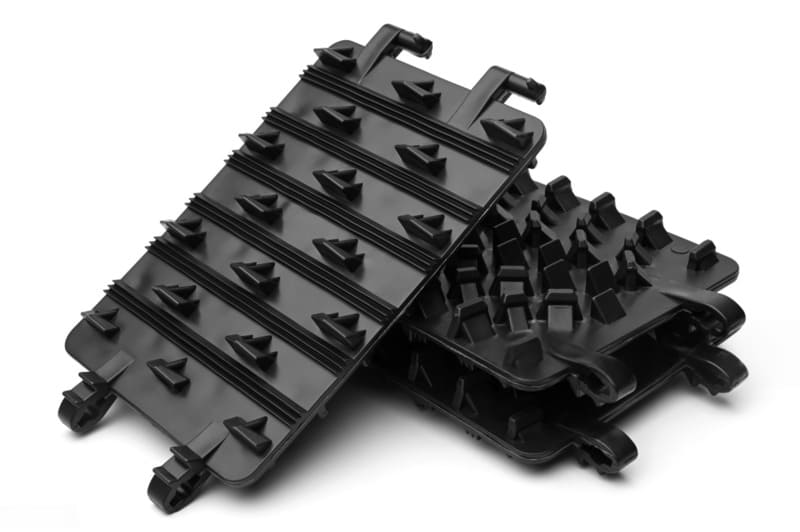
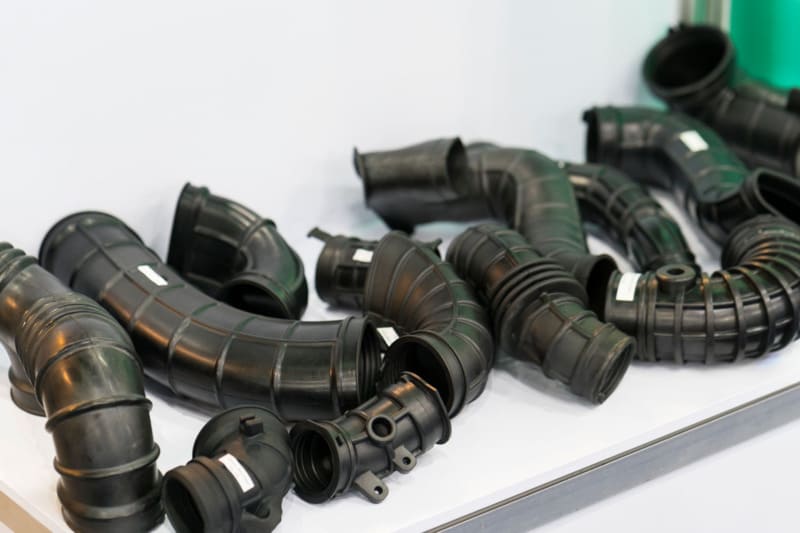
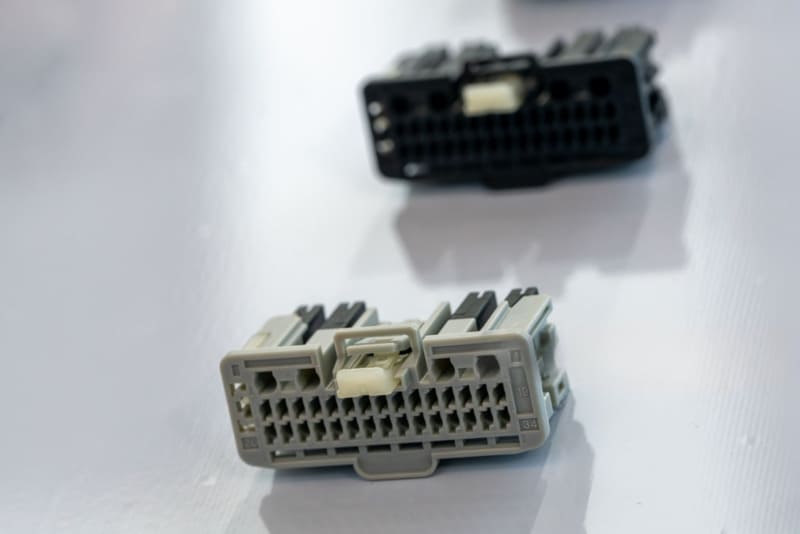

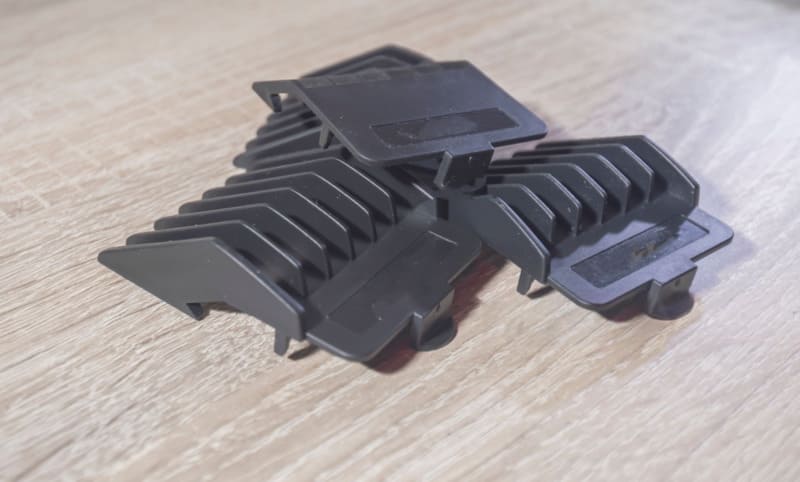
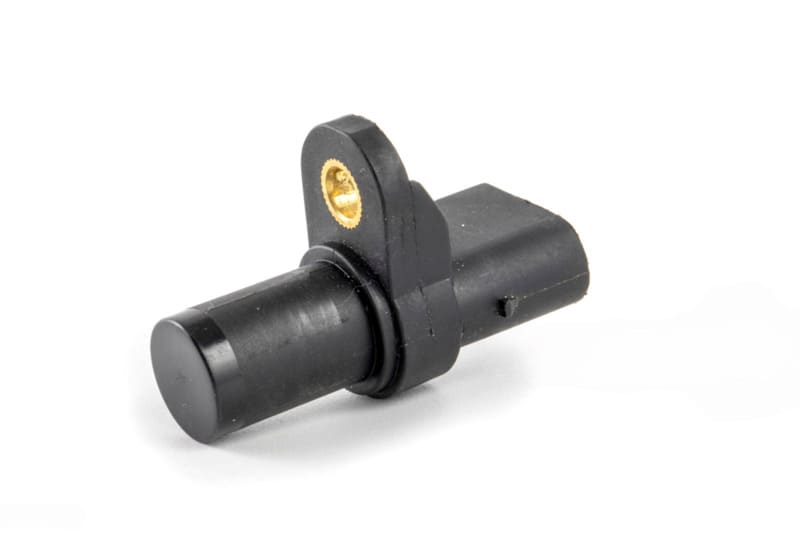
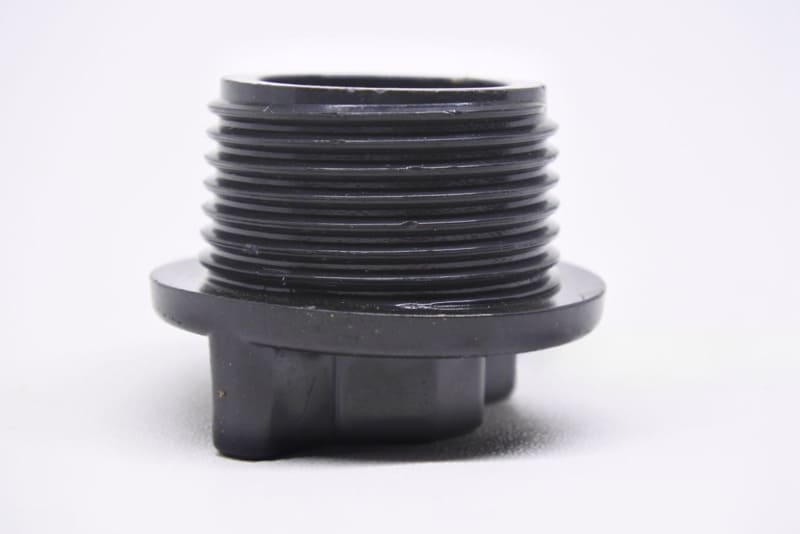
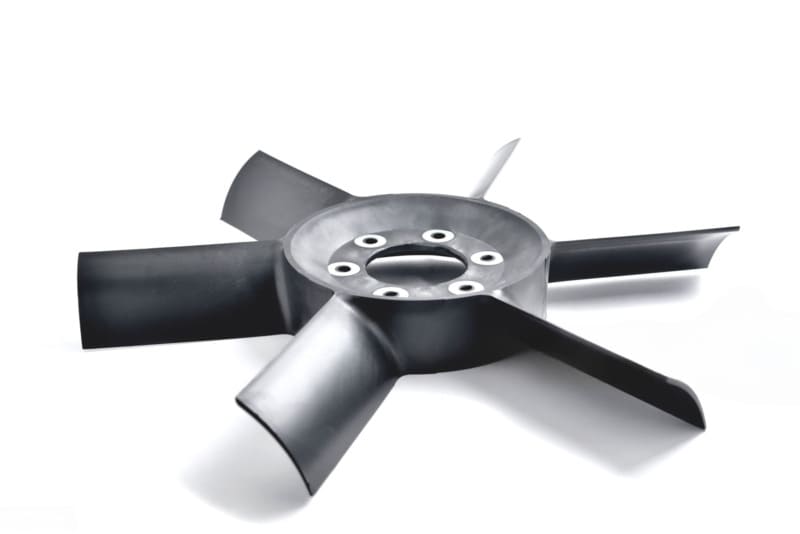
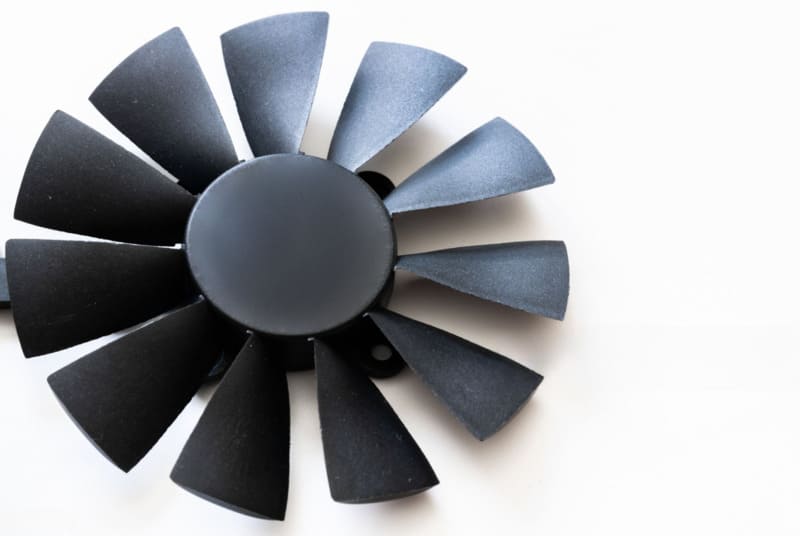
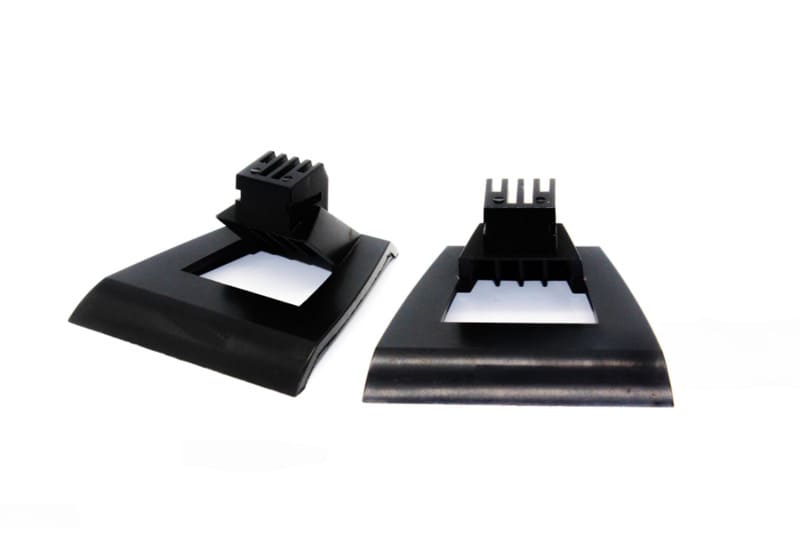
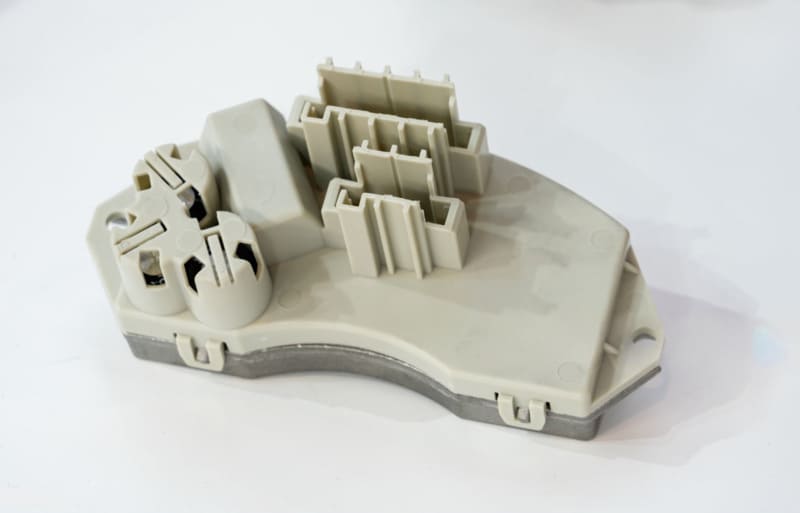
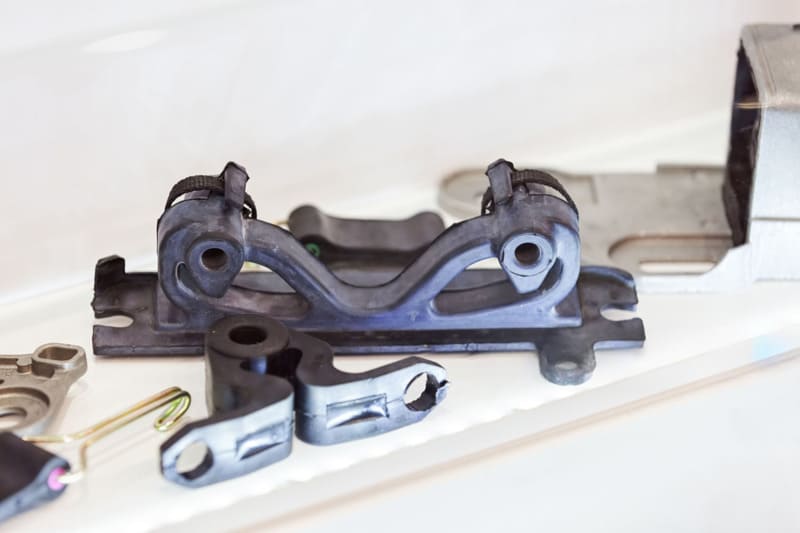
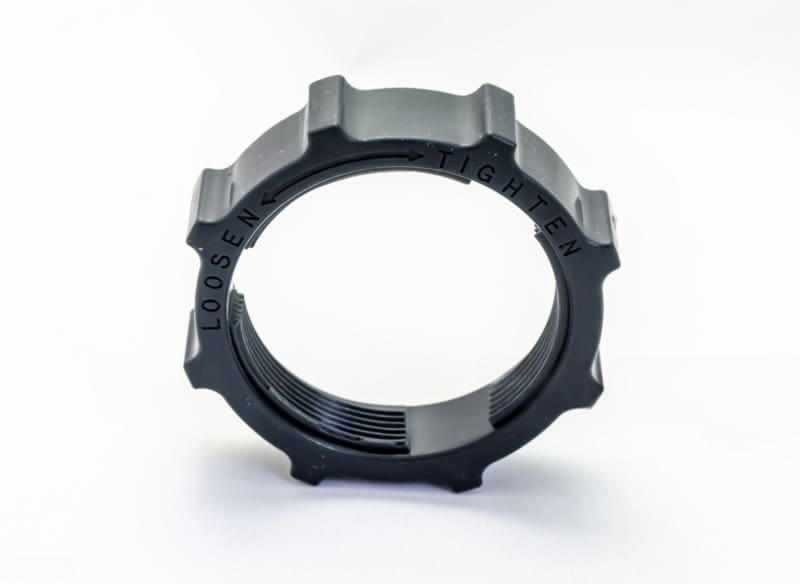
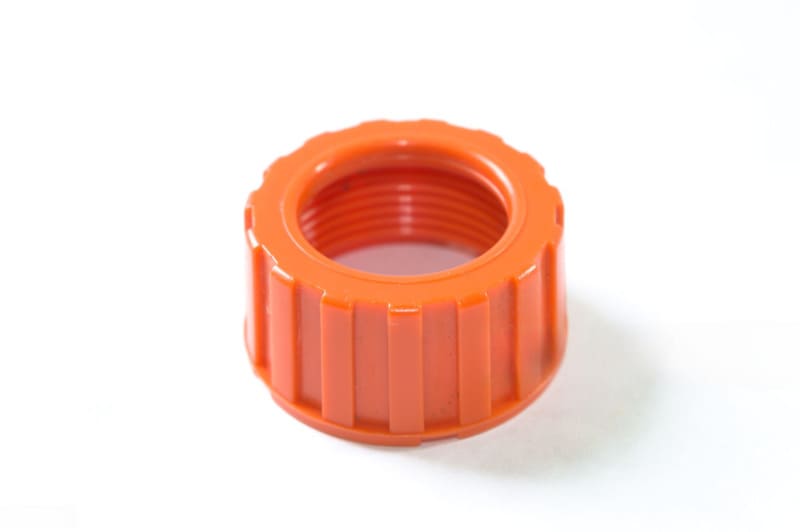
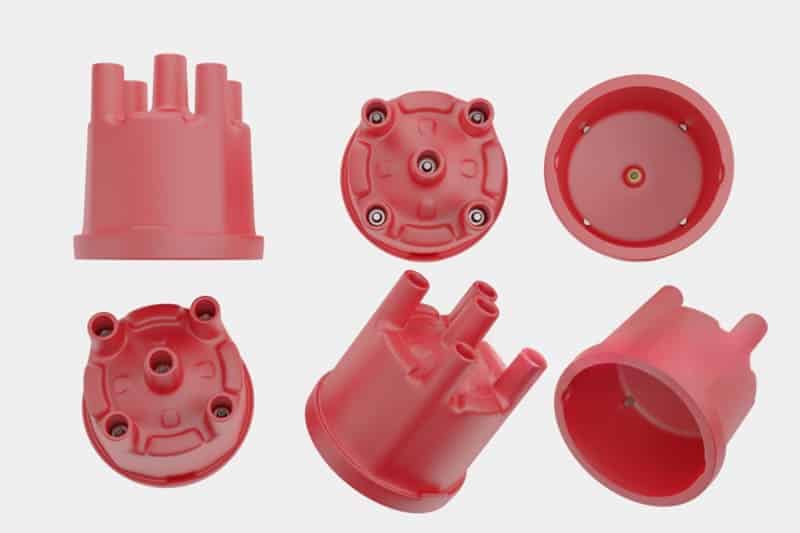
How to Choose a Reliable Plastic Injection Molding Supplier
- Extensive Experience: Choose suppliers with a proven track record in precision manufacturing, particularly in injection molding relevant to your industry or product type.
- Technical Expertise: Ensure the supplier offers technical support and guidance throughout the production process, aiding in design and manufacturing challenges.
- Quality Control Processes: Ensure the supplier has robust quality control systems and adherence to industry standards.
- Defect Rates & Continuous Improvement: Inquire about historical defect rates and the supplier’s commitment to ongoing quality enhancements.
- Consider Product Variety and Customization Capabilities: Ensure the supplier can provide tailored solutions and custom parts that meet your specific project requirements.
- Customer References: Request references from similar projects or industries to gauge the supplier’s reliability and performance.
- Case Studies: Review examples of successful projects the supplier has completed to understand their capabilities and expertise.
- Evaluate Supplier Network and Supply Chain Reliability: A well-connected supplier network ensures consistent access to quality materials and reliable production capabilities, minimizing supply chain disruptions.
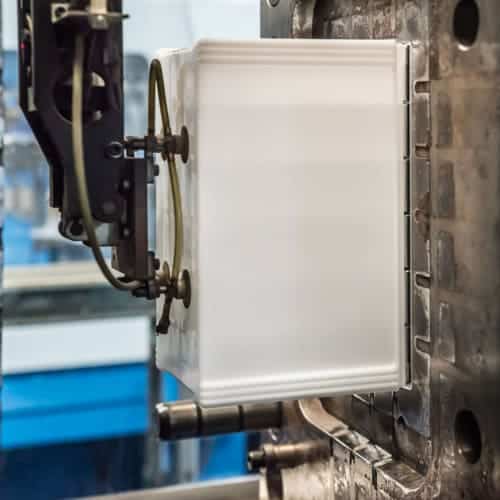

- Analyze Cost Considerations: While price is important, prioritize suppliers who offer quality, precision, and reliability over those with the lowest costs. Ensure that all potential costs, including tooling, materials, production, labor, and shipping, are clearly outlined.
- Transparency: Choose suppliers who are responsive, clear, and transparent in their communications regarding pricing, lead times, and terms of service.
- Sample Assessment: Before committing to large orders, request samples to evaluate the quality and accuracy of the supplier’s parts, ensuring they meet your standards.
- Timely Delivery: Confirm that the supplier has a strong track record of meeting deadlines to prevent delays in your project schedule.
- Communication: Effective communication is vital; choose a supplier that communicates clearly and responsively, In particular, sales have their own technical and design capabilities.
- Customer Service: Good customer support indicates the supplier’s dedication to addressing your concerns and providing timely solutions.
- Growth Capacity: Choose suppliers capable of scaling their production as your business grows.
- Upfront Information: The supplier should provide clear and transparent information about pricing, lead times, and service terms without hidden fees.
Why Use PTS Plastic Injection molding Services
We have specialized in plastic injection molding since 2002, We understand what our customers need.
We carefully check every part to make sure it meets high standards, with almost zero defects
We provide quick prototyping services, You can get your samples as fast as 10 days.
We have modern machines and technology. This helps us make precise parts.
I have worked with PTSMAKE for a long time, They make plastic parts for us, They always deliver on time. Their parts fit well with our machines, Once, we had a problem with a design, I called them, and they helped us fix it quickly. Their team is friendly and smart, Their machines are new and fast, They always check to ensure the quality is good. Working with PTSMAKE saves us time and money, I trust them with our important projects. They are more than just a supplier, They feel like a partner.
— John, Product Manager
Injection Molding Capabilities
We are prepared to tackle the challenges of any injection molding parts, including precise tolerances, thin walls, small draft angles, undercuts, intricate geometries, and flawless surface finishes.
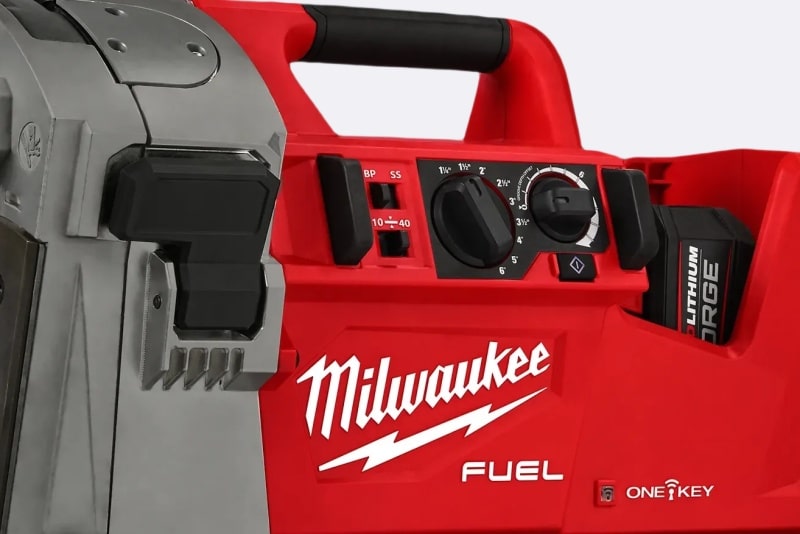
Two-shot & 3-shot Injection molding
Multi-material molding for complex, durable parts with enhanced functionality.
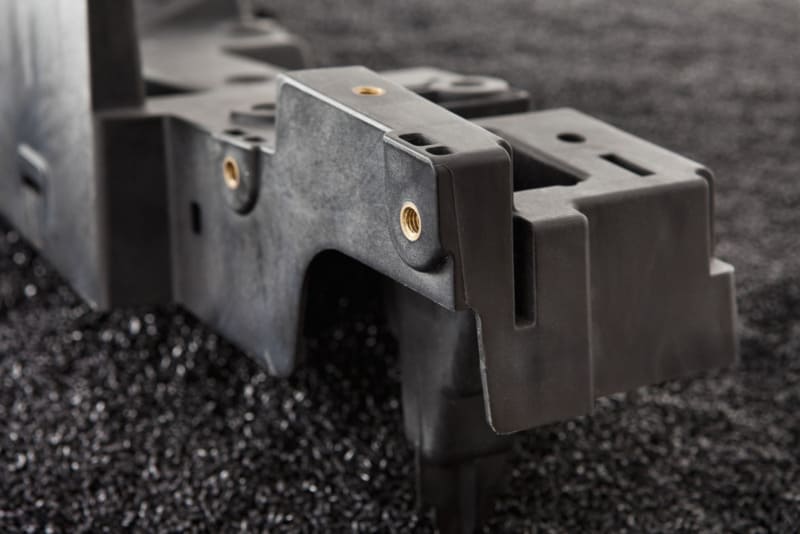
Overmolding and Insert Molding
Combining different materials to create robust, multi-functional parts with inserts.
- Read More
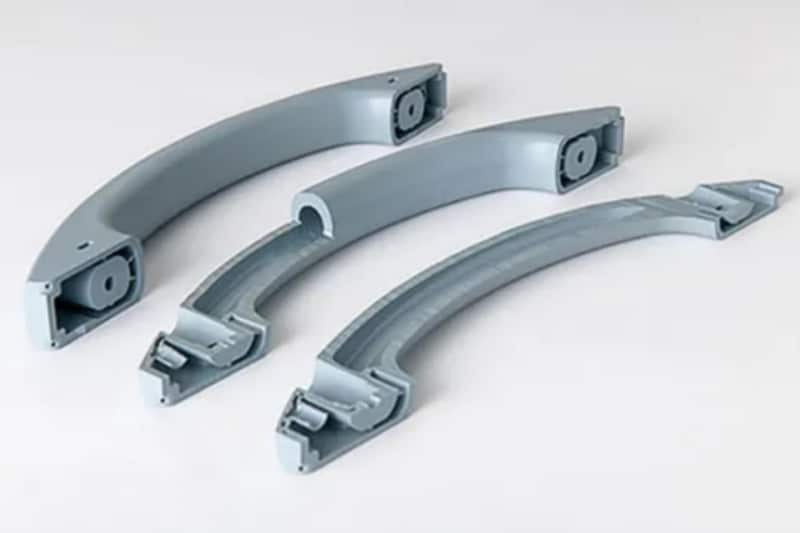
Gas-Assisted Injection Molding
Uses gas to reduce part weight and improve design flexibility while maintaining strength.
- Read More
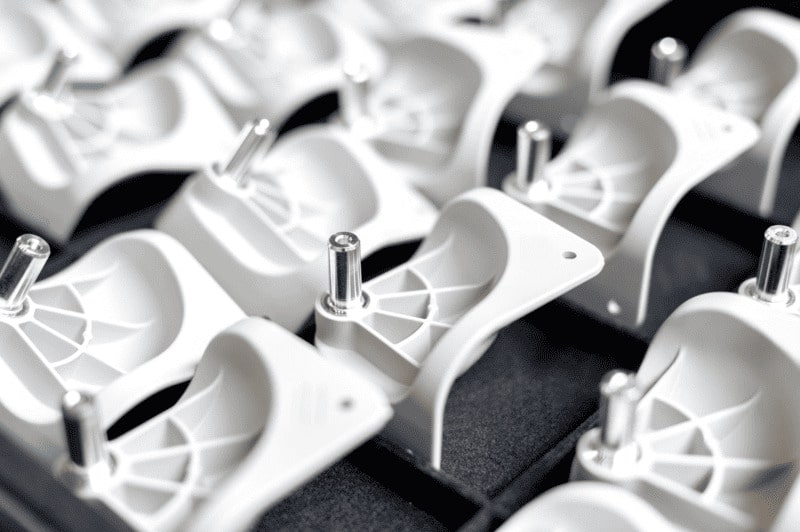
Other Custom Injection Molding
Tailored molding solutions for specialized parts, materials, and design requirements.
- Read More
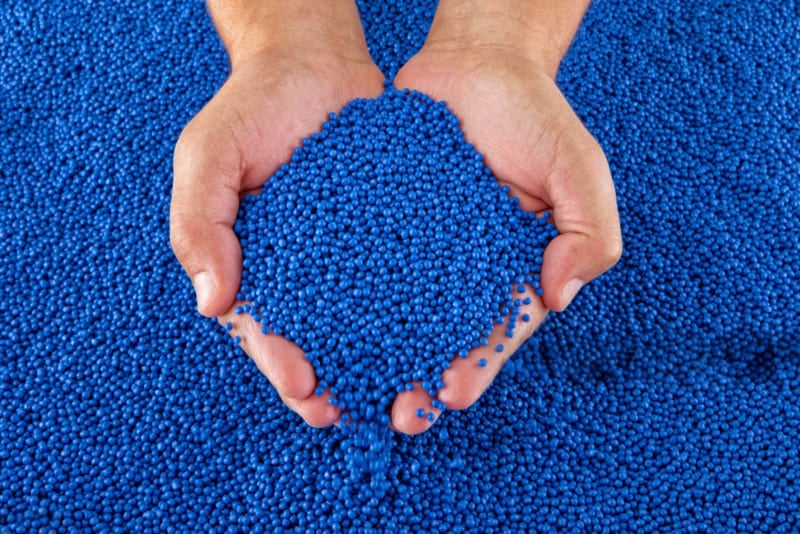
Wide Variety of Plastic Materials
We offer a comprehensive selection (100+) of plastic materials to suit diverse applications.
• Acrylic (PMMA)
• ABS
• Nylon (PA6, PA66, PA12)
• Polycarbonate (PC)
• Polyethylene (PE)
• Polyoxymethylene (POM)
• Polypropylene (PP)
• Polystyrene (PS)
• TPE
• TPU
• Polyurethane (PU)
• LDPE
• HDPE
• PPS
• PC/ABS
• Polysulfone (PSU)
• Polyetherimide (PEI)
• TPV
• PET
• PBT Glass-Filled
• PA+30GF/50GF
• Polyphenylene oxide (PPO)
• PEEK
• PBT
• Polyvinyl chloride(PVC)
• PASA
• liquid crystal polymers(LCP)
• polysulfone(PSU)
• Polyphthalamide (PPA)
Expert Material Recommendations
Selecting the right material is critical for product success.
Our team considers factors such as:
- Mechanical Requirements: Strength, flexibility, durability
- Thermal Properties: Operating temperature ranges, heat resistance
- Chemical Compatibility: Resistance to solvents, acids, and other chemicals
- Aesthetic Considerations: Color, finish, transparency
- Regulatory Compliance: Meeting industry-specific standards
We work closely with you to recommend materials that balance performance and cost-effective.
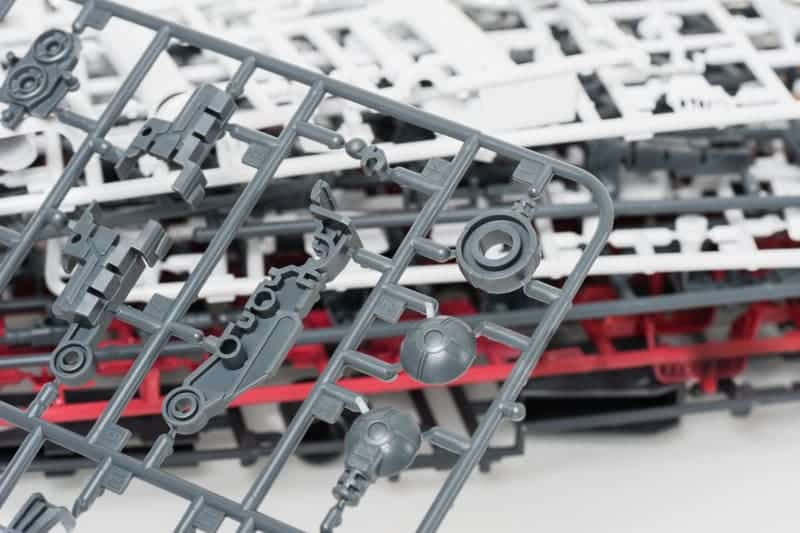
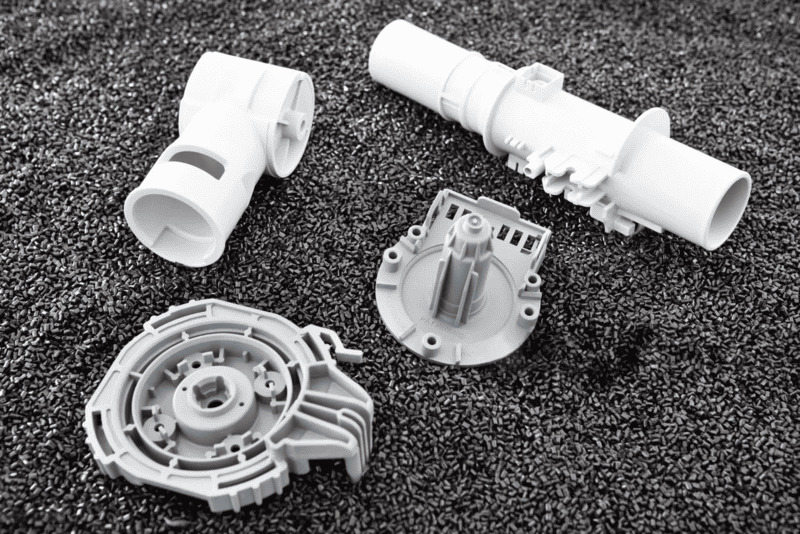
All materials we use comply with international safety and environmental standards, including:
All materials we use comply with international safety and environmental standards, including:
- RoHS: Restriction of Hazardous Substances Directive
- REACH: Registration, Evaluation, Authorisation, and Restriction of Chemicals
- FDA: For materials intended for food contact or medical devices
- UL: Underwriters Laboratories certifications for flammability standards
We can provide material certifications upon request to ensure your products meet the necessary regulations.
Not sure which material is best for your project? Our engineers are here to help you choose the right material that meets your performance, durability, and cost requirements.
Injection Molding Part Surface Finishes
PTSMAKE offers a wide range of high-quality surface finishes for injection molded parts. Below are some of the most common options, but we also provide additional custom finishes tailored to your specific needs.
MoldTech Finishes (Mold Texturing): We offer a variety of textured finishes, such as matte, swirl, line, and pattern effects. Common MoldTech options include MT11010, MT11020, and MT11030. Additional textures can be requested.
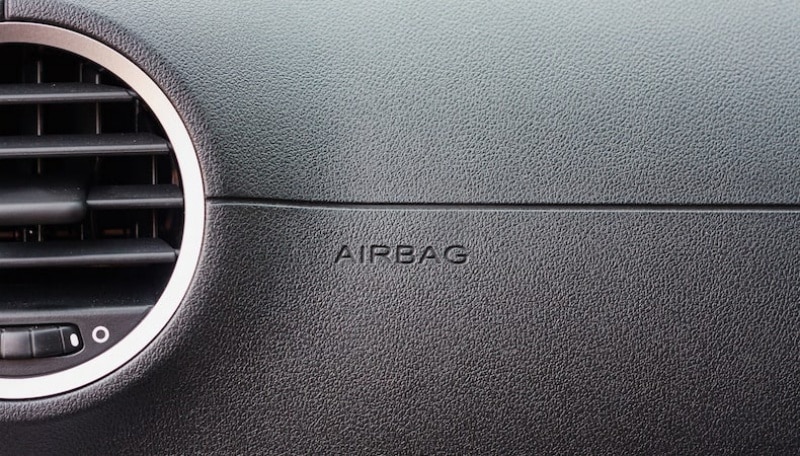
Standard Finish: This is the moldmaker’s default choice, typically following SPI B-2 standards. The finish is determined by the mold’s geometry and draft angles, with interior, non-visible areas often left with as-machined finishes.
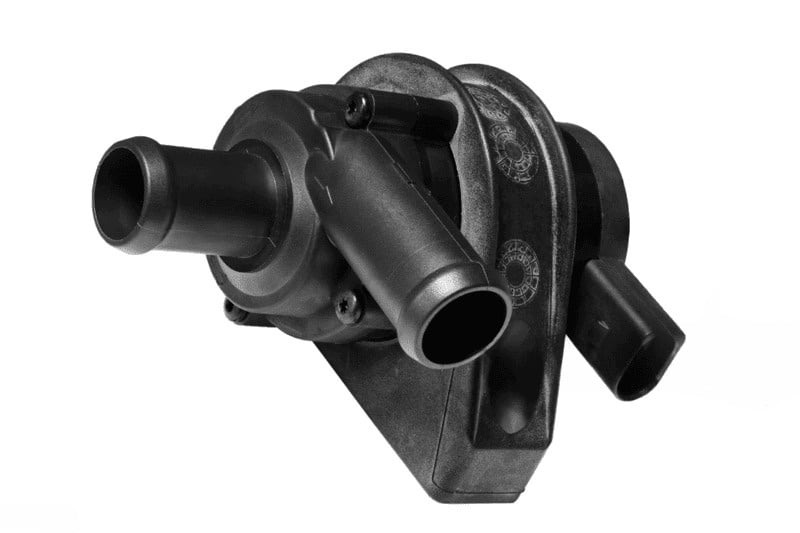
SPI Finishes: A range of Society of Plastics Industry (SPI) finishes is available, from Grade 3 diamond polish to a 320 stone low polish. Options include SPI A-1, A-2, A-3, B-1, B-2, B-3, C-1, C-2, C-3, D-1, D-2, and D-3.
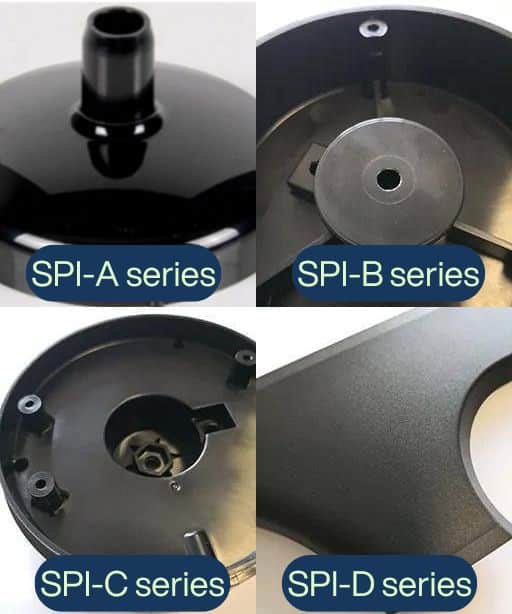
Other Textures – VDI: The VDI 3400 surface finish is based on a German engineering standard (VDI) and is typically achieved through EDM machining. It offers a range from fine to coarse matte finishes.

As Molded: This finish involves no additional polishing or grinding. The part will display tooling marks from the molding process.
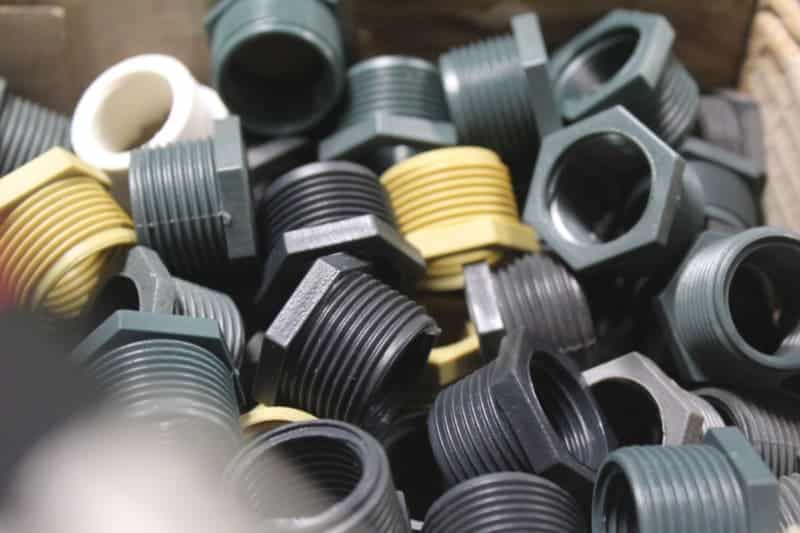
Threaded Inserts: We install a wide variety of standard threaded inserts in both UNF and metric sizes, accommodating your project’s needs.
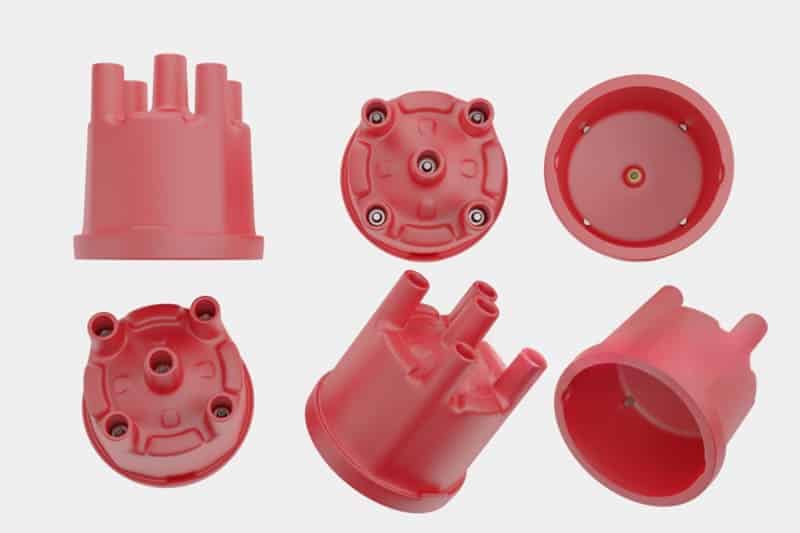
Pad Printing: We provide pad printing services to transfer 2D images onto 3D parts. All images are reviewed before transfer.
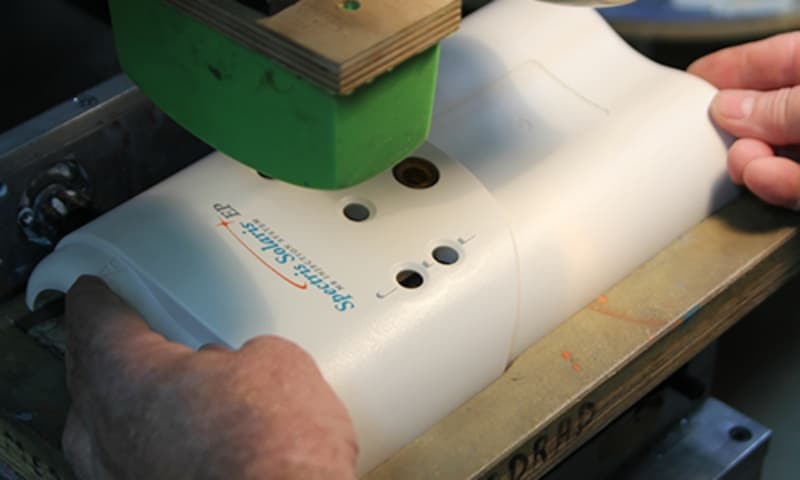
Laser Engraving: Laser engraving allows for precise etching of part numbers, logos, or custom designs directly onto parts.
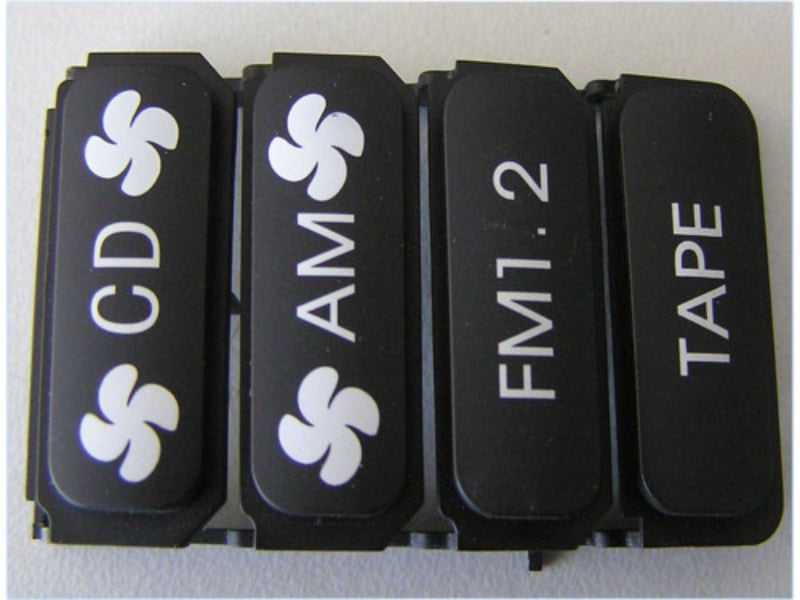
Assembly: PTSMAKE can handle part assembly and labeling services for injection molded components. Please consult with oour sales representative for details.
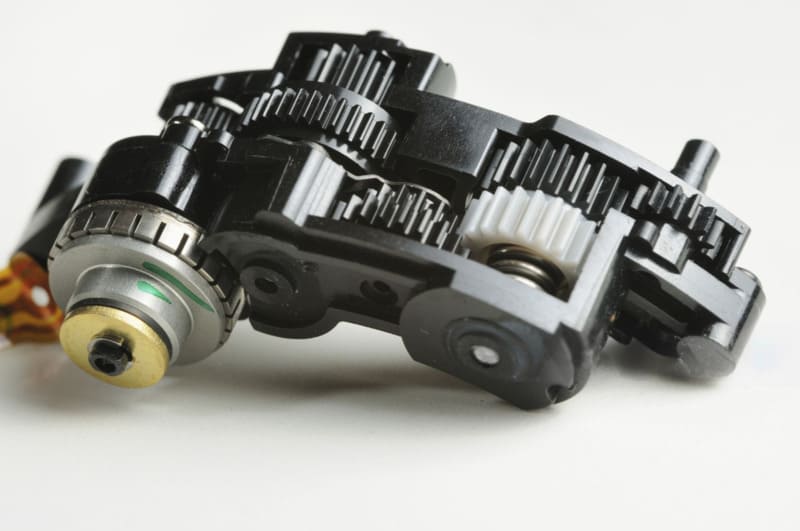
Request a Custom Quote Today
Get an accurate estimate for your injection molding project. Let us help you meet your exact specifications.
Cost and Quotation
We believe in transparency and clear communication with our clients. Our cost structure is carefully designed to balance quality and affordability, while our delivery lead times are optimized to ensure we meet your business requirements. Below, we provide a detailed breakdown of how we manage costs and delivery for our injection molding products.
Raw Material Costs
Raw materials are a major part of the manufacturing cost for injection-molded products. We source a wide range of high-quality materials, including various types of plastic resins like ABS, PC, PP, PE, and PVC, as well as additives and pigments. The choice of material depends on your product’s functional needs and appearance, such as strength, flexibility, heat resistance, or look.
- Material Sourcing: We work with trusted suppliers to ensure consistent quality and competitive pricing.
- Material Type & Grade: Different material grades affect the performance and cost of your product. High-performance engineering plastics may cost more than standard materials.
- Material Waste: We strive to minimize waste during production to reduce costs and environmental impact. This helps us pass savings on to you.
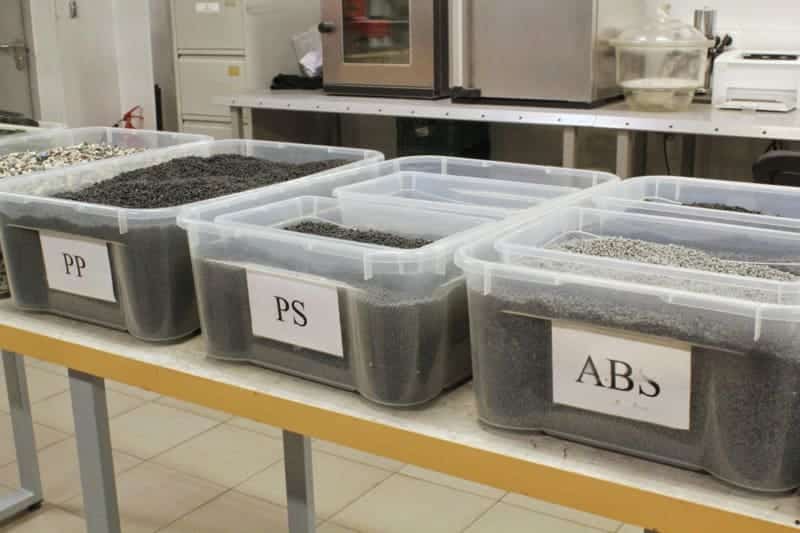
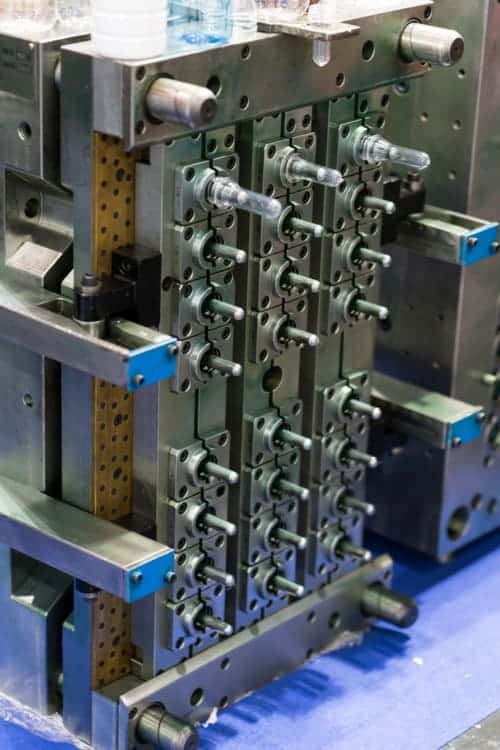
Mold Costs
Manufacturing custom injection molds is essential for injection molding. Mold costs are one-time fees that vary based on the product’s complexity and the number of cavities in the mold.
- Mold Design & Prototyping: The design and prototyping stage is crucial in ensuring that your mold will produce the desired part quality and quantity. We work with you to refine the design and reduce costly changes later in production.
- Mold Material: The material used for making the mold (such as steel, aluminum, or alloy) directly impacts the mold cost. Steel molds are more durable and suited for high-volume production, while aluminum molds are typically less expensive but suitable for lower-volume runs.
- Mold Life & Maintenance: Molds can run last for hundreds of thousands of cycles, but regular maintenance may be required to maintain their performance, especially for high-precision molds. We ensure that molds are built to last and are properly maintained to avoid unplanned downtime during production.
Production and Processing Costs
Production costs are determined by the complexity of the injection molding process, the efficiency of the equipment, and the required post-processing steps (such as assembly or finishing).
- Cycle Time: The cycle time for each injection cycle depends on the material, part size, and complexity of the design. More intricate parts may take longer to molding, which affects the overall cost of production.
- Tooling & Setup: Setting up machines, adjusting molds, and running test batches all take time and are factored into the production cost. For high-volume orders, we can optimize production schedules to minimize setup time and reduce costs.
- Post-Processing: Many injection molded products require secondary processes such as trimming, polishing, painting, or assembling. These additional steps are factored into the overall cost.
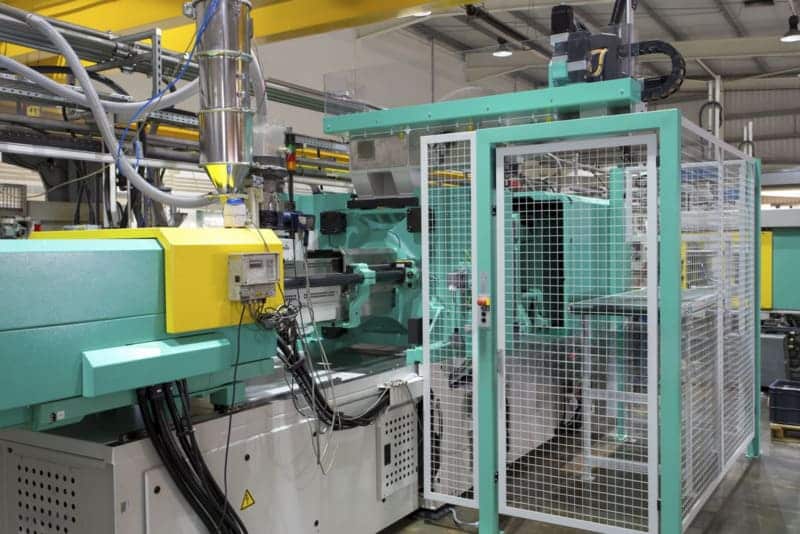
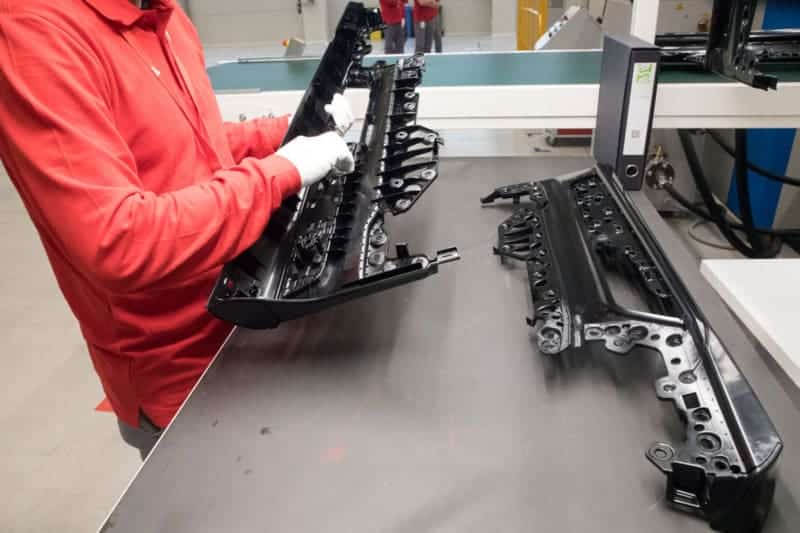
Labor Costs
Skilled labor is essential in injection molding. This includes machine operators, mold setup technicians, quality inspectors, and assembly staff. Labor costs can vary depending on production volume and the skill levels required.
- Skilled Workforce: Our team is highly trained in operating advanced injection molding machines and ensuring quality control throughout the process.
- Quality Assurance: Labor costs are also affected by the number of quality checks required to meet strict customer specifications.
Shipping and Logistics Costs
Shipping costs depend on the order’s destination, volume, weight, and the chosen shipping method. We offer a variety of shipping options to help you manage costs and ensure timely delivery.
- International Freight: We coordinate sea freight, air freight, and express courier services depending on the urgency of your order. Sea freight is typically more cost-effective for larger shipments, while air freight is faster but more expensive.
- Customs Duties & Taxes: Import duties, taxes, and customs clearance fees vary by country and region. We can provide assistance in calculating these costs to ensure there are no surprises.
- Packaging: We ensure that all products are securely packaged to prevent damage during transit. The cost of packaging is included in the shipping costs.
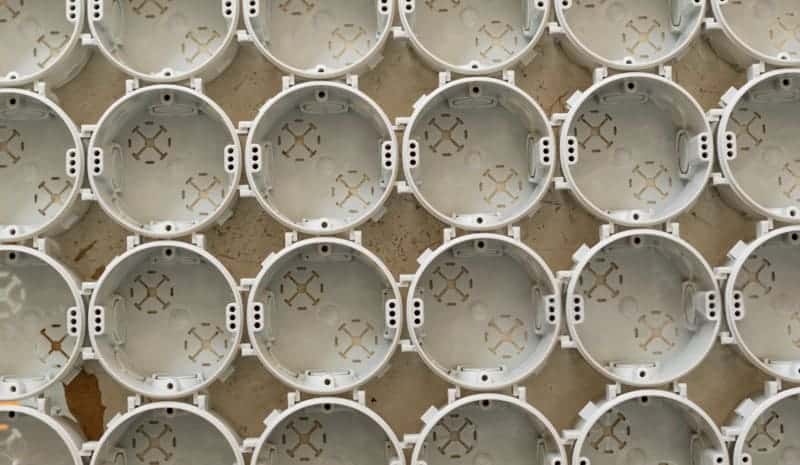
Custom Plastic Injection Molding Project Lead Time
We understand the importance of on-time delivery and work hard to ensure that our production schedules align with your business needs. Our delivery lead times vary depending on order specifics, product complexity, and shipping method.
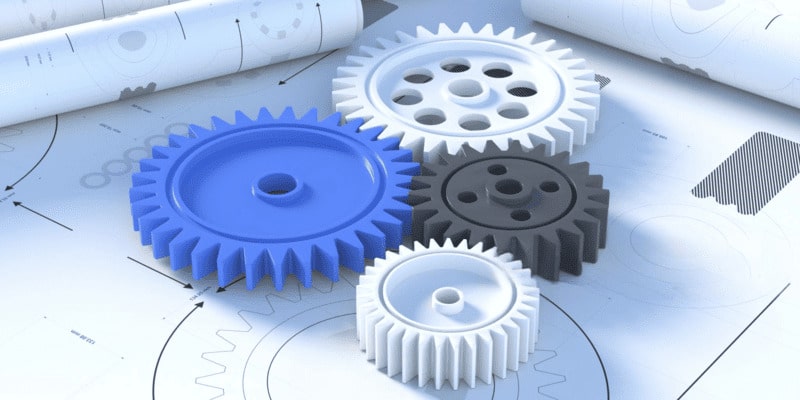
Analysis Your Design
Our technical manager will review your design, helping you develop and assess new products faster, more cost-effectively, and with reduced risk, ultimately lowering your overall costs.
This process typically takes 1 to 5 days.
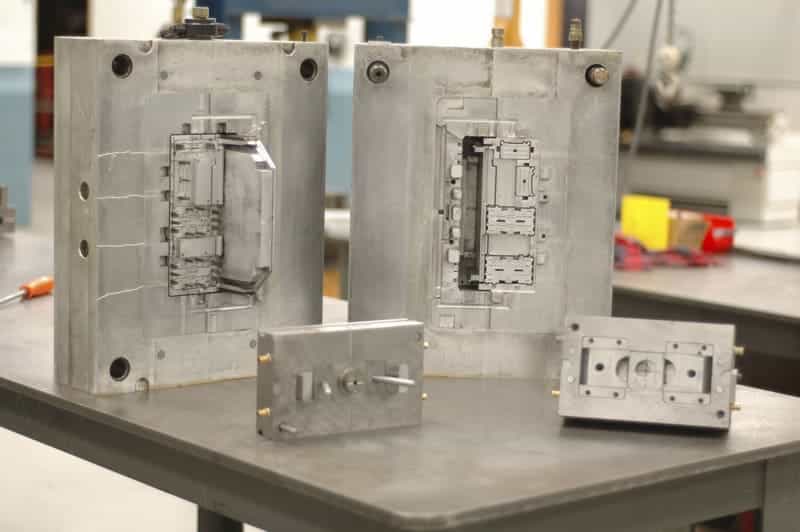
Mold Manufacturing
Once the mold design is approved, we create the mold and conduct trial runs to ensure that the product meets your specifications. This phase can take additional time depending on the complexity of the design and required adjustments.
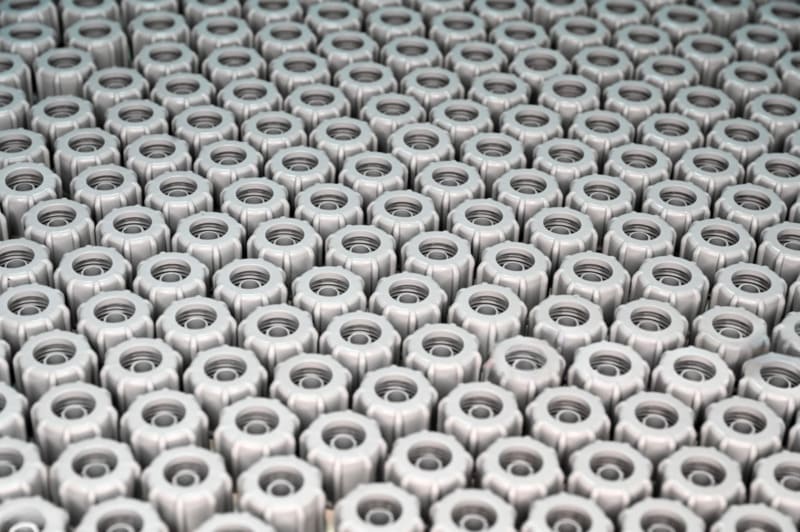
Production Runs
Once the mold is created, we will produce a sample for your approval. Production will only begin once the sample meets your expectations. 1-15 days after sample and mold approval, depending on order size.
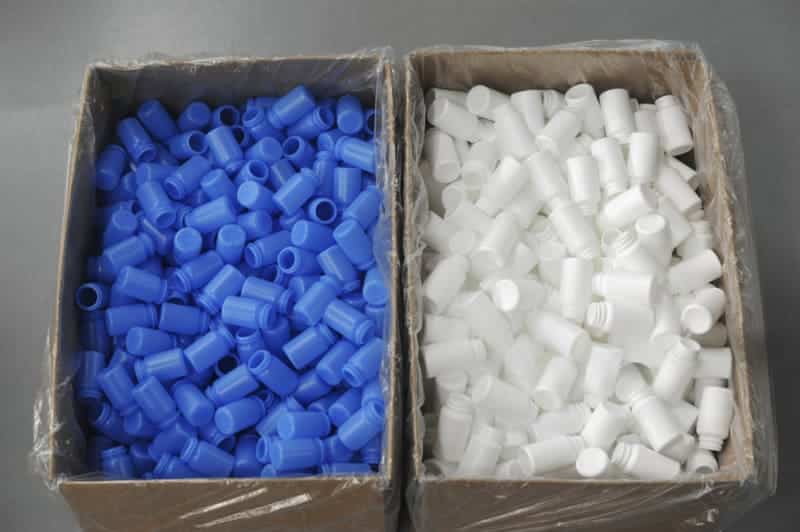
Shipping Time
The shipping time depends on the chosen shipping method and destination: Sea Freight: Typically takes 4-6 weeks, depending on the destination port and customs processing time. Air Freight: Generally takes 5-7 days, but this option is more expensive.
Our Production Capacity
Our facilities are equipped to handle large-scale production demands, This ensures we can accommodate your production needs, regardless of scale.
- Monthly Capacity: Over 1,000,000 units, depending on part complexity.
- Multiple Shifts: Operating 24/7 when needed to meet deadlines.
- Scalable Operations: Ability to expand capacity quickly for large orders.
Meeting Urgent Deadlines
We are experienced in handling expedited orders:
- Prioritized Scheduling: Adjusting production plans to accommodate urgent needs.
- Express Services: Accelerated mold fabrication and production.
- Dedicated Resources: Allocating additional personnel and equipment.
Please communicate your deadlines early so we can plan effectively.
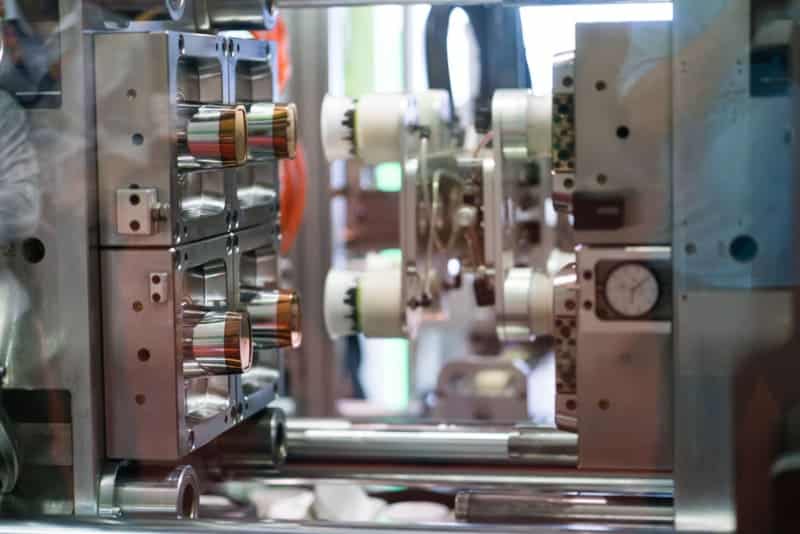
Contact Molding Expert Today!
We look forward to the opportunity to work with you and contribute to your project’s success.
How Does Plastic Injection Molding Work?
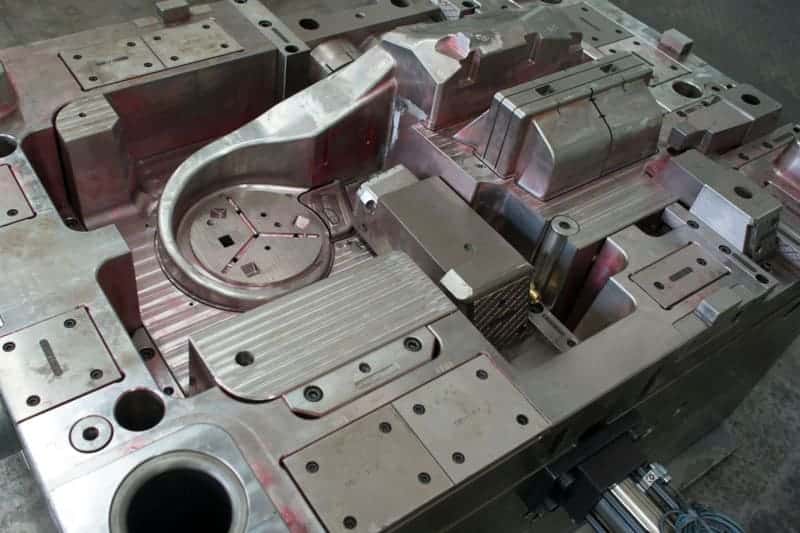
1. Mold Desig & Manufacturing
We design and manufacture precise molds to ensure the shape and details of the products.
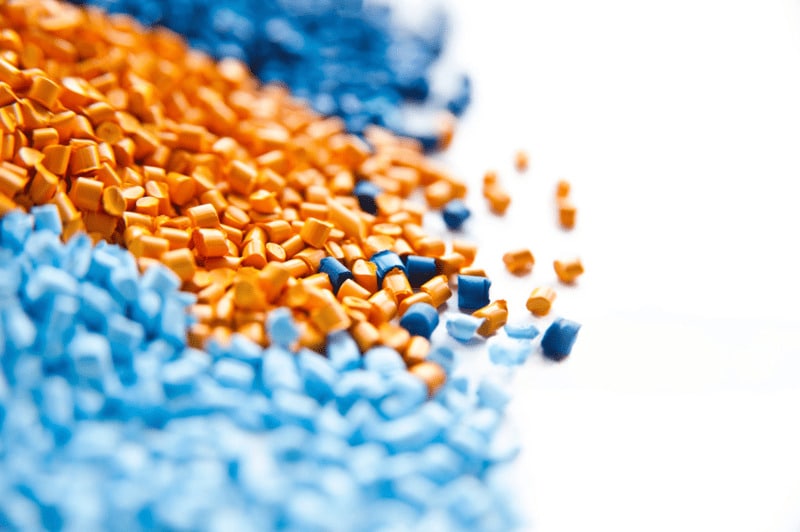
2. Plastic Material Preparation
Select high-quality plastic pellets and dry them to ensure molding quality.
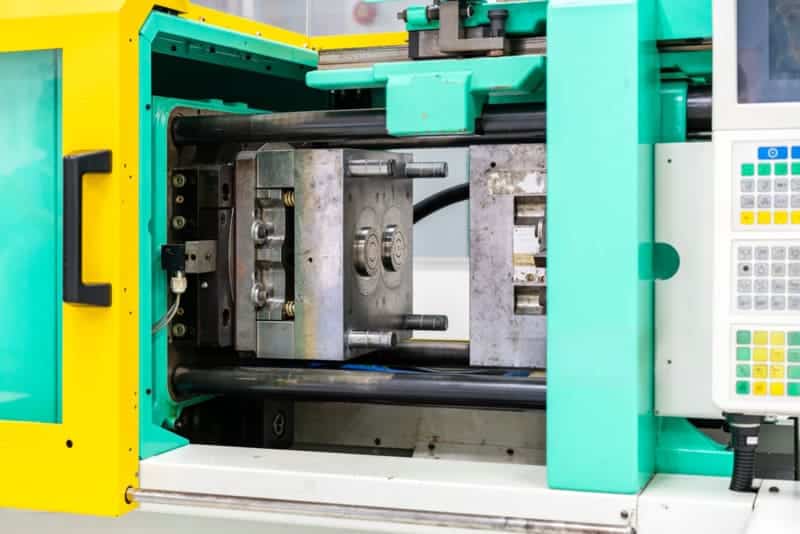
3. Injection Parameter Debug
Adjust machine parameters, such as temperature and pressure, to suit different product requirements.
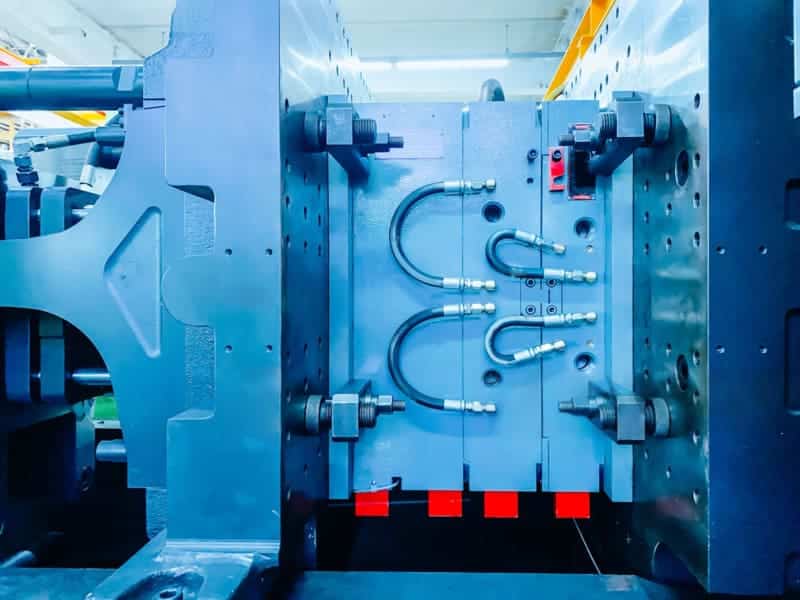
4. Injection
High pressure injects molten plastic into the mold, forming the basic shape of the product.
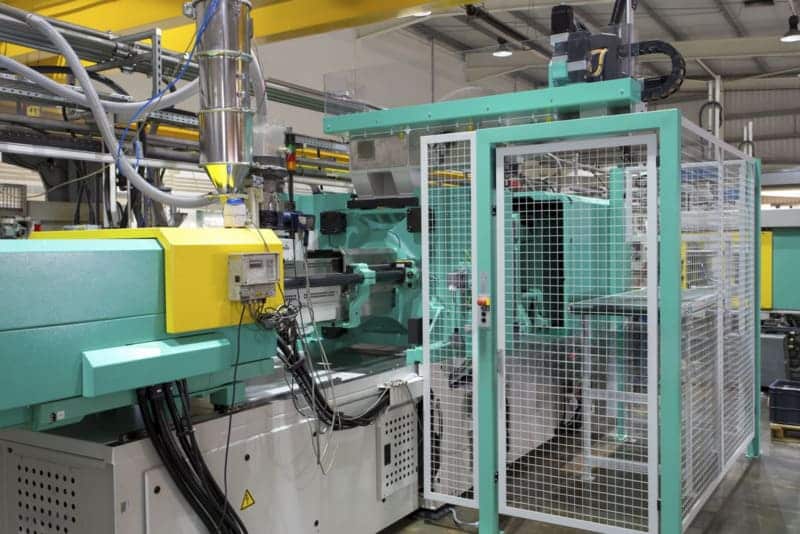
5. Cooling and Solidification
Plastic cools and solidifies in the mold, forming the final shape and ensuring dimensional stability.
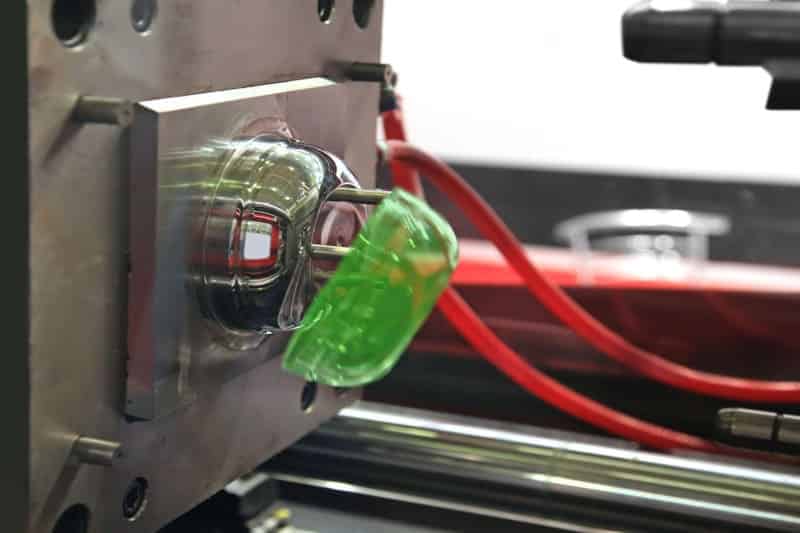
6. Ejection and Take Out
After cooling, the mold opens, and mechanical devices eject and remove the finished product.
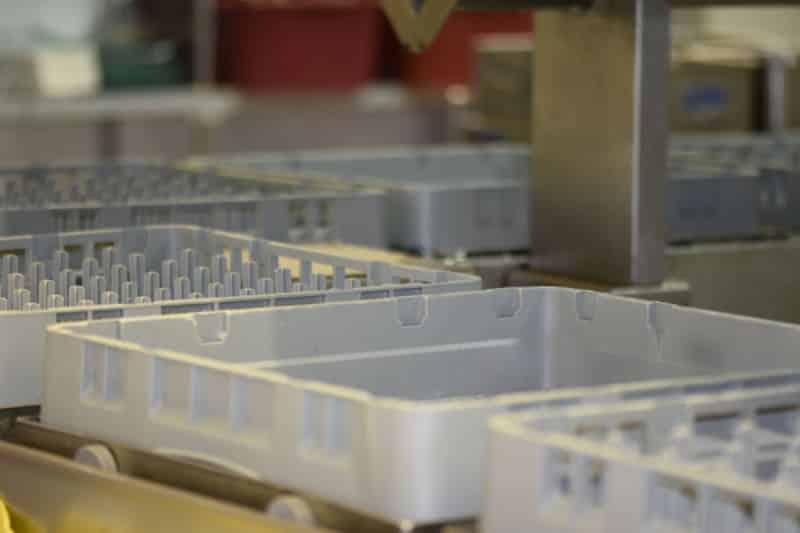
7. Post-Processing
Perform surface treatments to ensure the product is smooth and aesthetically pleasing.
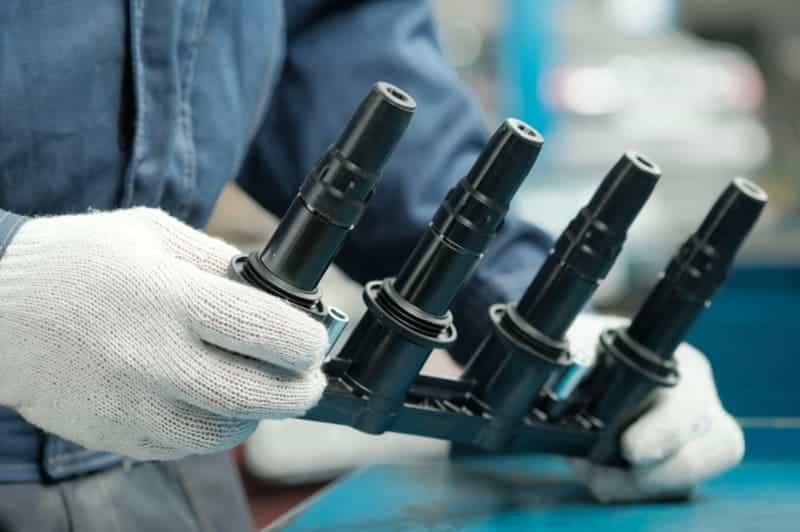
8. Inspection and Packaging
Strictly inspect product quality, ensure no defects, then package and prepare for shipment.
Injection Mold Design and Development
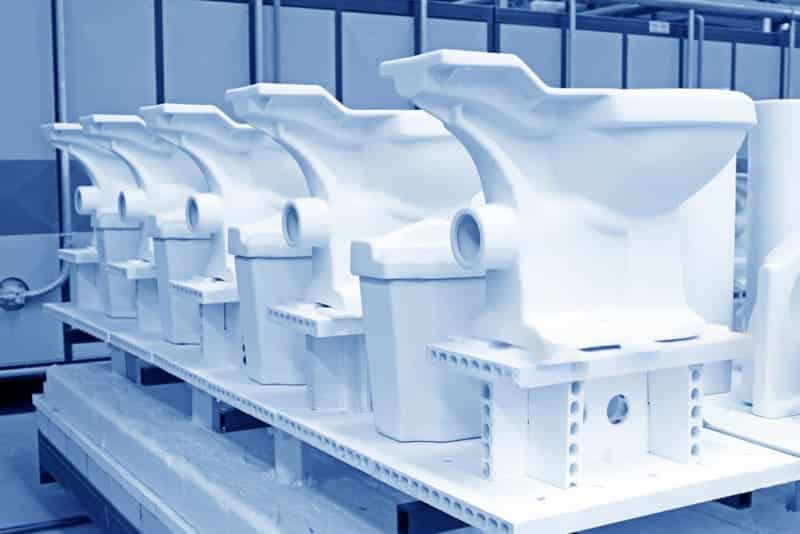
Prototype Development and Sampling Services
View Details
Recognizing the importance of functional validation, we offer prototype development and sampling services. By producing prototypes, we allow you to assess the design’s viability, test functionality, and make informed decisions before committing to mass production. This step is crucial for minimizing risks and ensuring product succe
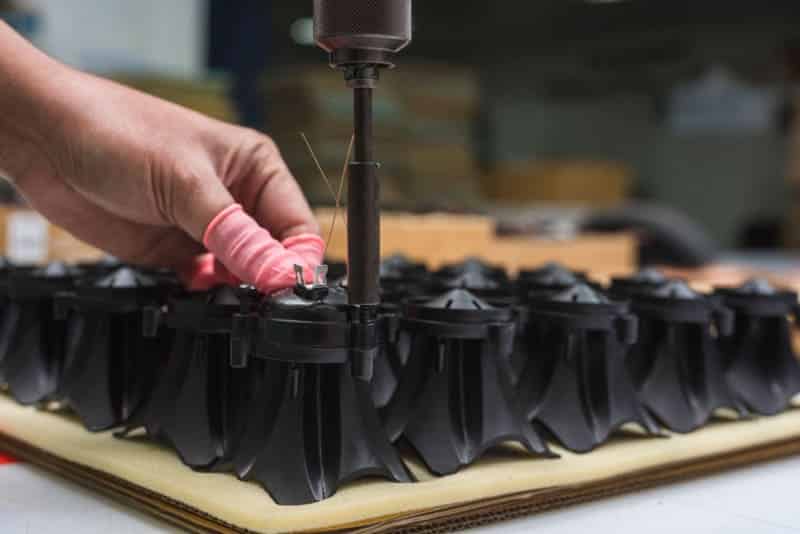
Design File Requirements
View Accepted Files
To facilitate accurate translation from design to production, we accept a variety of CAD file formats, including:
●SolidWorks (.sldprt)
●ProE (.prt)
●IGES (.igs)
●STEP (.step)
●ACIS (.sat)
●Parasolid (.x_t or .x_b)
●STL (.stl)
●DWG
●DXF
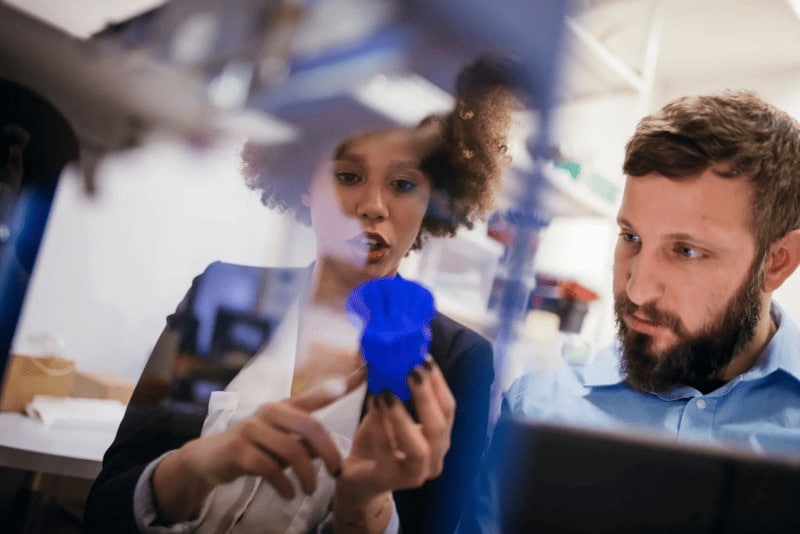
Guidelines for Essential Information
View Guidelines
●Detailed Geometry and Dimensions
●Tolerances and Critical Features
●Material Specifications
●Surface Finish Requirements
●Assembly Considerations
Providing comprehensive design documentation allows us to fully understand your requirements and produce parts that align with your vision.
Technical Support for Design Optimization
Our engineering team is committed to supporting your design efforts. We apply Design for Manufacturing (DFM) principles to evaluate your designs and suggest improvements. Areas we focus on include:
- Wall thickness uniformity to prevent warping or sinking
- Draft angles to facilitate part ejection
- Rib and boss design for structural integrity
- Gate placement for optimal material flow
- Minimizing undercuts to reduce complexity and costs
By optimizing these aspects, we enhance the manufacturability and performance of your product while controlling costs.
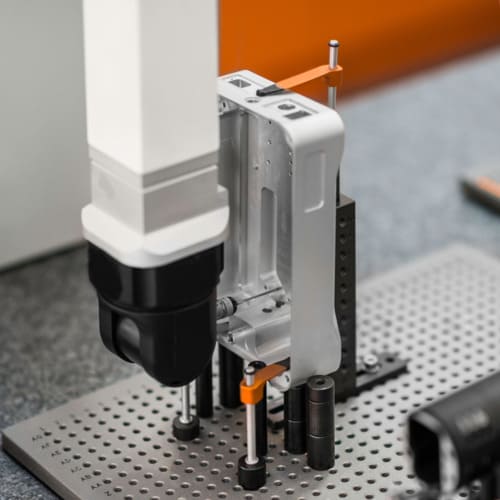
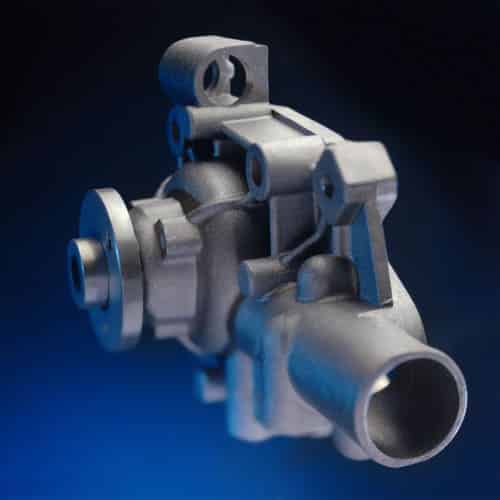
Structured Design Review Process
Our design review process involves:
- Initial Assessment: We review your design files to understand the project’s scope and complexity.
- DFM Analysis: Our engineers perform a DFM analysis to identify potential issues.
- Feedback and Consultation: We provide a detailed report with recommendations and collaborate with you to implement changes.
- Finalization: We finalize the design based on agreed-upon adjustments, ensuring readiness for production.
By optimizing these aspects, we enhance the manufacturability and performance of your product while controlling costs.
Plastic Injection Molding Applications
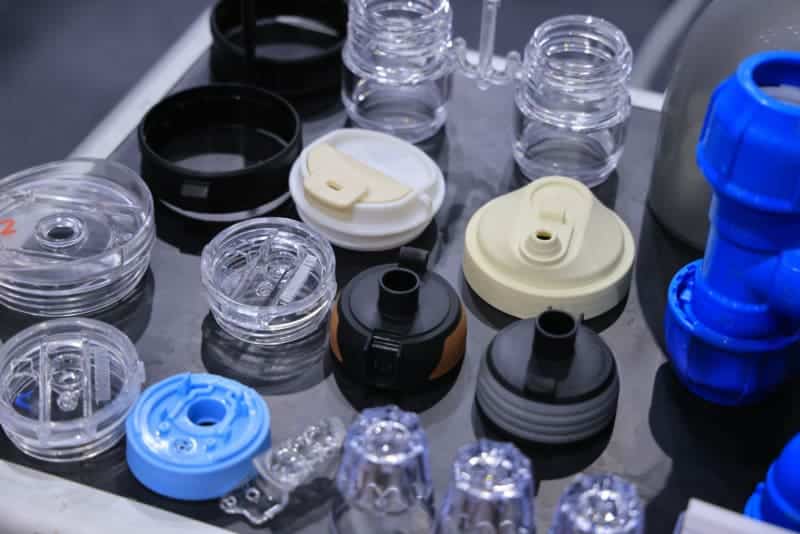
Medical
- Read More
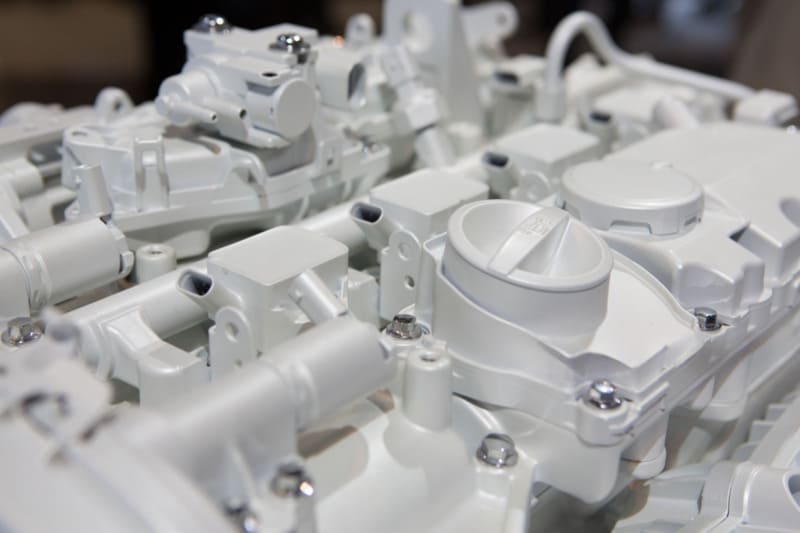
Automotive
- Read More
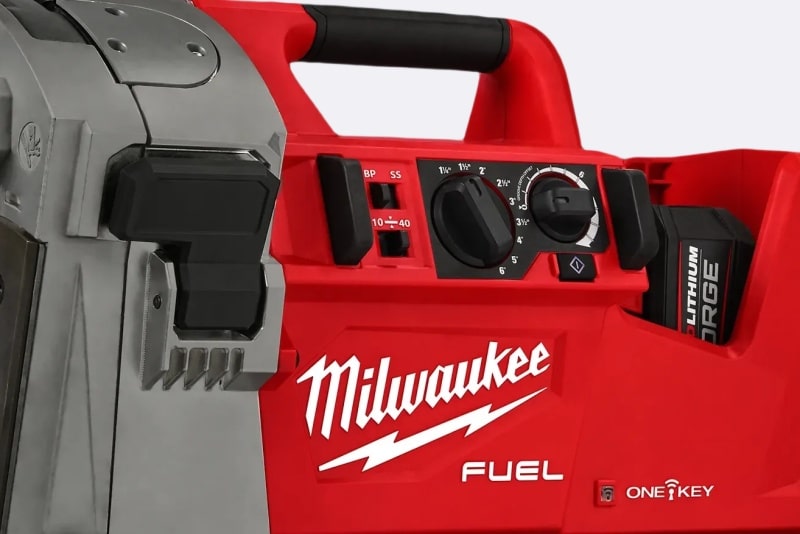
Consumer Products
- Read More
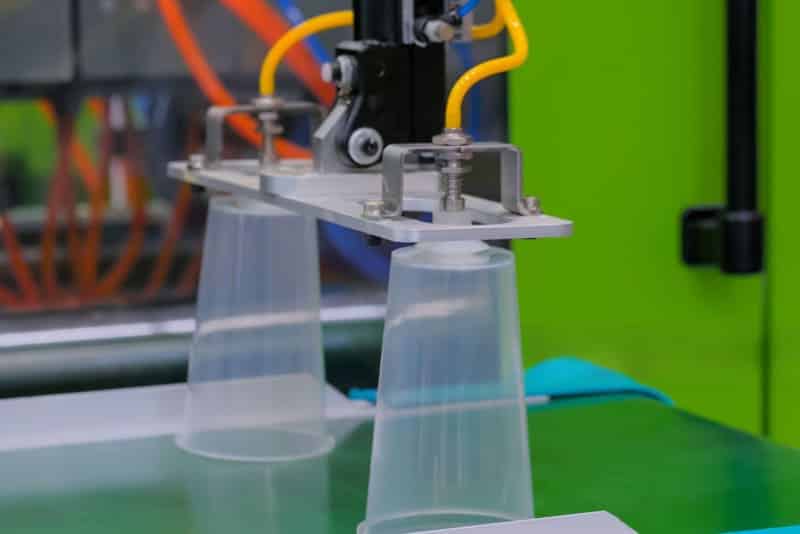
Packaging
- Read More
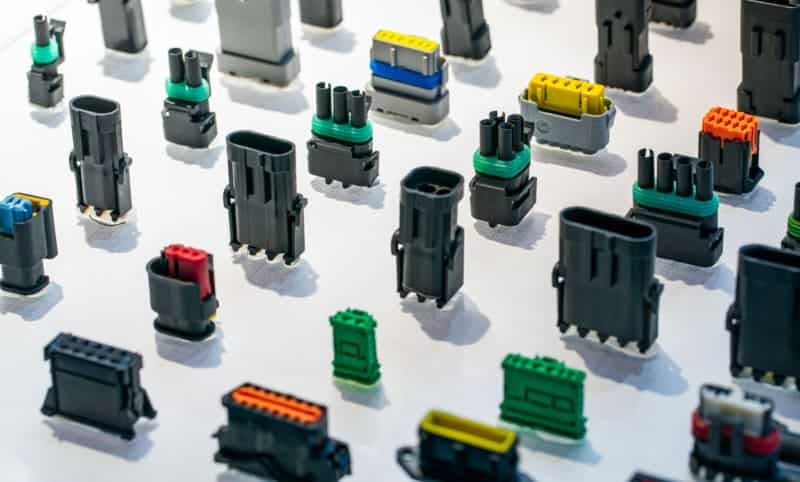
Electronics
- Read More
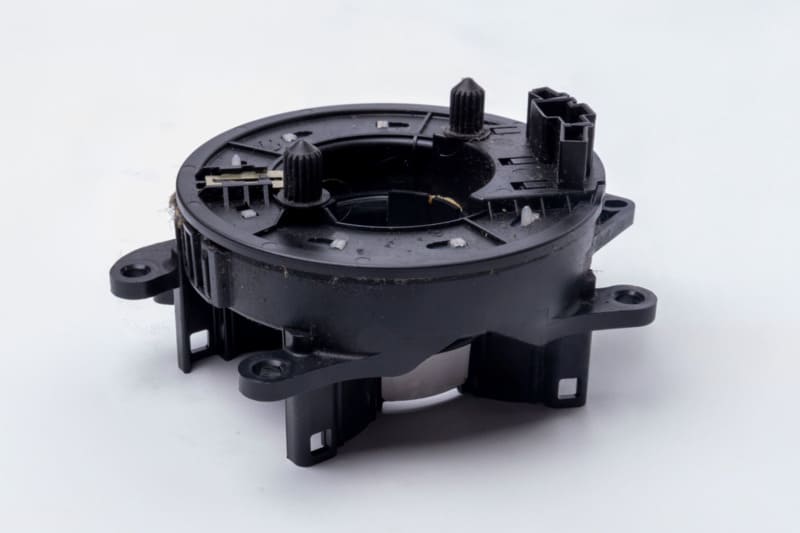
Energy
- Read More
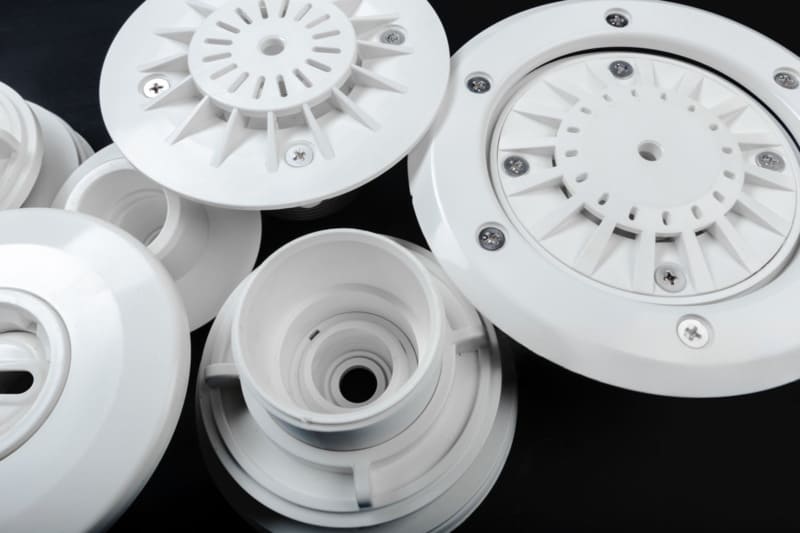
Industrial Machinery
- Read More
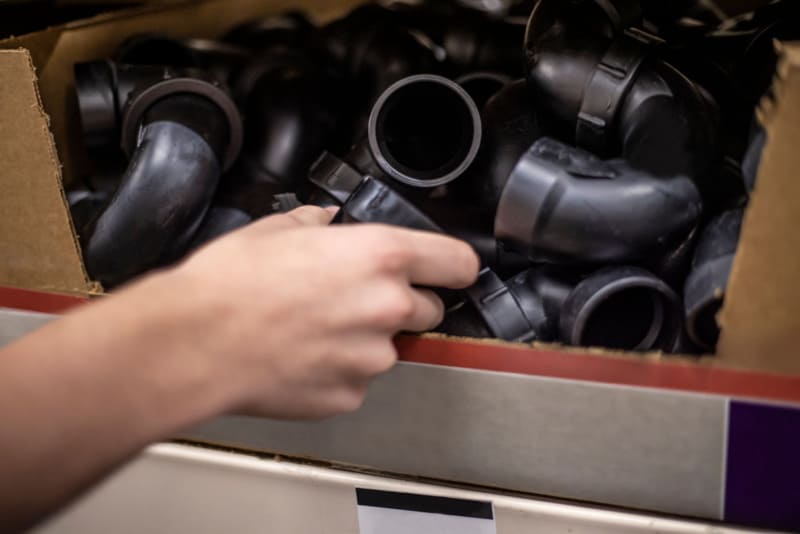
Marine
- Read More
Injection Molding FAQs
What is your minimum order quantity requirement?
Our standard MOQ for injection molding projects is typically 500 units. However, we understand that some projects require smaller quantities, especially during prototyping or initial market testing phases.
Is there a different pricing strategy for small batch orders?
Yes, for smaller orders, the unit cost may be higher due to the proportionate impact of setup and production costs. We strive to provide competitive pricing regardless of order size and are open to discussing your specific needs to find a suitable arrangement.
Is there a price discount for large-volume production?
Yes, we offer tiered pricing that provides cost savings for larger production volumes. As quantities increase, we can optimize production efficiencies and pass those savings on to you.
Do you have ISO 9001 or other relevant quality certifications?
Yes, we are proud to be ISO 9001 certified. This certification reflects our commitment to maintaining the highest quality standards throughout our manufacturing processes. We continually strive to exceed industry standards to ensure our customers receive products that meet and often surpass their expectations.
Can you provide references or case studies from previous clients?
Certainly. Over the years, we have had the privilege of serving renowned companies such as Huawei, BMW, and Epson. For instance, we collaborated with Huawei on developing precision components for their telecommunications equipment, ensuring each part met strict industry specifications. While we respect our clients’ confidentiality agreements, we’re more than willing to discuss general aspects of these projects to showcase our capabilities.
Do you have the capability to design and manufacture molds?
Yes, we offer comprehensive mold design and manufacturing services in-house. Our mold-making division utilizes advanced CAD/CAM software and CNC machining to create high-precision molds. By controlling the entire process under one roof, we ensure seamless integration between mold fabrication and part production, resulting in optimal efficiency and quality.
Can you provide assistance during the design phase?
Yes, we offer engineering support during the design phase. Our team can provide design feedback, material recommendations, and manufacturability assessments to optimize your product.
Can you accommodate urgent orders?
Yes, we offer expedited services for urgent orders. If you have tight deadlines, please let us know, and we will work diligently to meet your timeline, potentially adjusting production schedules and resources to prioritize your project.
Do you have a dedicated customer service team or project manager?
Yes, our customer service team includes experienced project managers who specialize in international projects. They coordinate internally to make sure your requirements are understood and met.
Can you provide free sample production?
We offer sample production services. While there may be a nominal fee to cover material and processing costs, we aim to make this process as economical as possible to help you validate the design before full-scale production.
Are samples rigorously tested to verify their function and quality?
Yes, all samples undergo the same rigorous testing and quality checks as full production runs. Our goal is to ensure the samples meet all functional and quality expectations before proceeding.
How do you handle order changes or cancellations?
We understand that project requirements can change. Any modifications or cancellations are handled on a case-by-case basis. We’ll work with you to adjust schedules and costs accordingly, aiming to minimize any inconvenience.
How are shipping costs calculated?
Shipping costs are calculated based on the shipment’s weight, volume, destination, and the chosen shipping method. We have partnerships with reliable logistics providers to ensure competitive rates and efficient service.
Can you assist with customs clearance procedures?
Yes, we can assist with documentation and coordination necessary for customs clearance. Our logistics team is experienced in international shipping regulations and will help ensure a smooth import process.
How does your company handle quality issues if they arise?
Customer satisfaction is our top priority. If any quality issues are identified, we will promptly investigate and provide solutions, which may include product replacement, rework, or refunds as appropriate. Our after-sales team is dedicated to resolving issues efficiently and effectively.
Do you provide technical support and solutions?
Yes, we offer ongoing technical support for our products. Whether you need assistance with product integration, performance optimization, or troubleshooting, our experts are available to help.
What is the warranty period?
We provide a standard warranty period of one year for our products. This warranty covers defects in materials and workmanship under normal use conditions.
How does your company protect customers' designs and intellectual property?
We take intellectual property (IP) protection very seriously. We have strict internal policies to safeguard your designs and proprietary information. All data is handled securely, and access is limited to authorized personnel involved in your project.
Is it possible to sign a Non-Disclosure Agreement (NDA)?
Yes, we are more than willing to sign an NDA to formalize our commitment to confidentiality. This agreement ensures that your sensitive information remains protected throughout our collaboration.
Do your products comply with U.S. environmental regulations?
Yes, our products comply with international environmental regulations, including those in the United States. We adhere to standards such as RoHS (Restriction of Hazardous Substances) and can produce FDA-compliant parts when required.
Who owns the molds?
Typically, once the mold fabrication cost is fully paid, the ownership of the mold transfers to you. We will store and maintain the mold for production purposes unless you request otherwise.
Who is responsible for the mold's lifespan and maintenance?
We take responsibility for the mold’s maintenance and proper storage while it’s in our facility. Regular maintenance ensures optimal performance and extends the mold’s lifespan. We will inform you when the mold approaches the end of its useful life.
Can mold designs be modified as needed?
Yes, mold designs can be modified to accommodate design changes or improvements. Our engineering team will assess the modifications and advise on the feasibility and associated costs.