High Temperature Injection Molding Factory
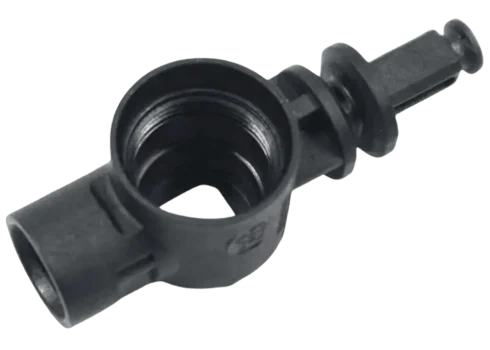
LOW MOQ 100 PCS
Complex Part Precision Molding
Fast Turnaround & Global Shipping
Machines Ranging From 30 Tons to 1,600 Tons






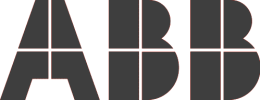

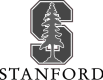
What Our Clients Say
Our clients are located worldwide, and their feedback speaks for itself. If you’d like to verify our reputation with customers in your area, don’t hesitate to contact us—we’d be happy to connect you with them and share relevant case studies.
8 Key Industries Relying on High Temperature Injection Molding Solutions
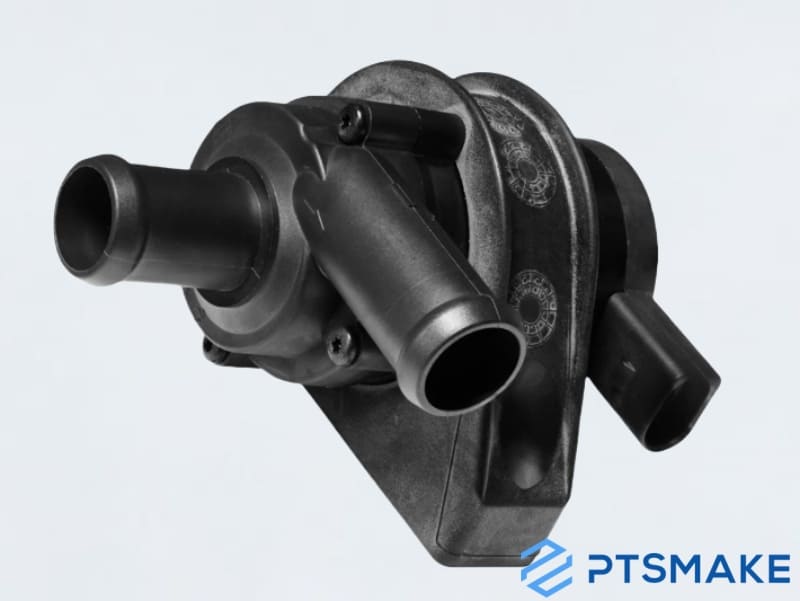
Automotive

Electronics
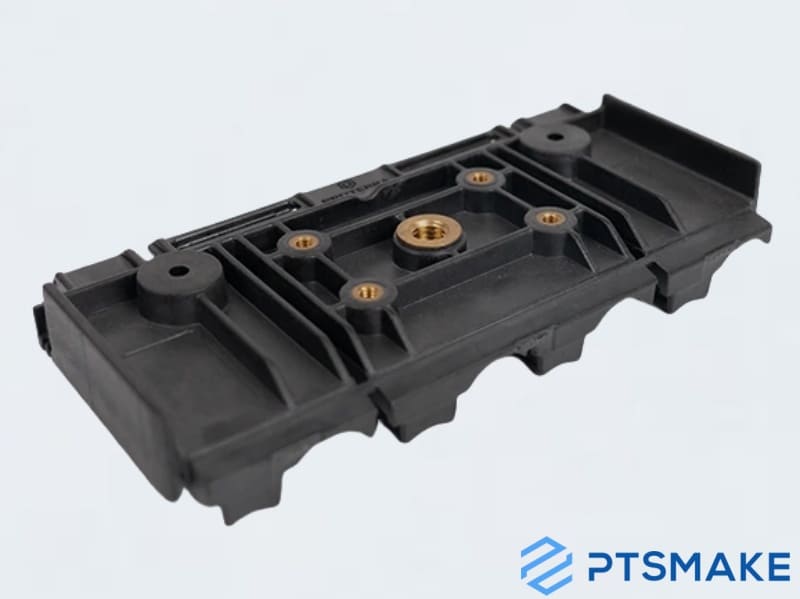
Home Appliance
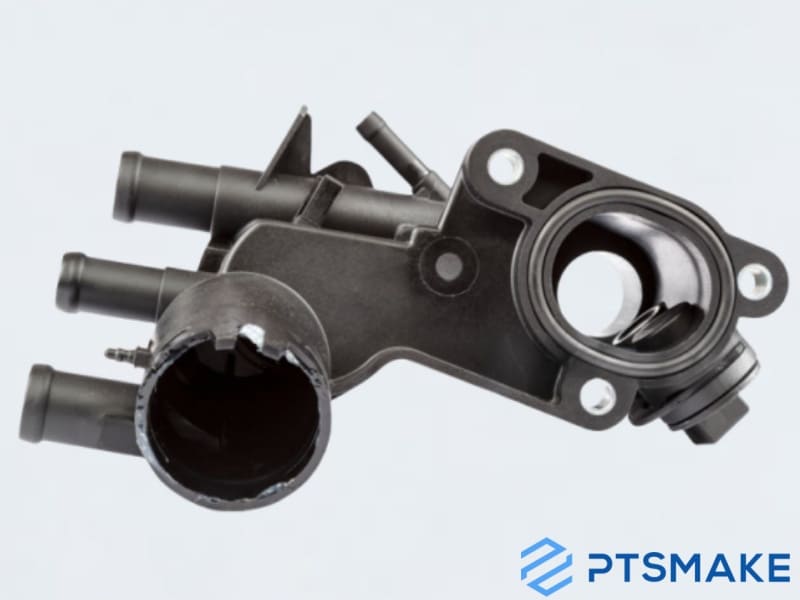
Aerospace
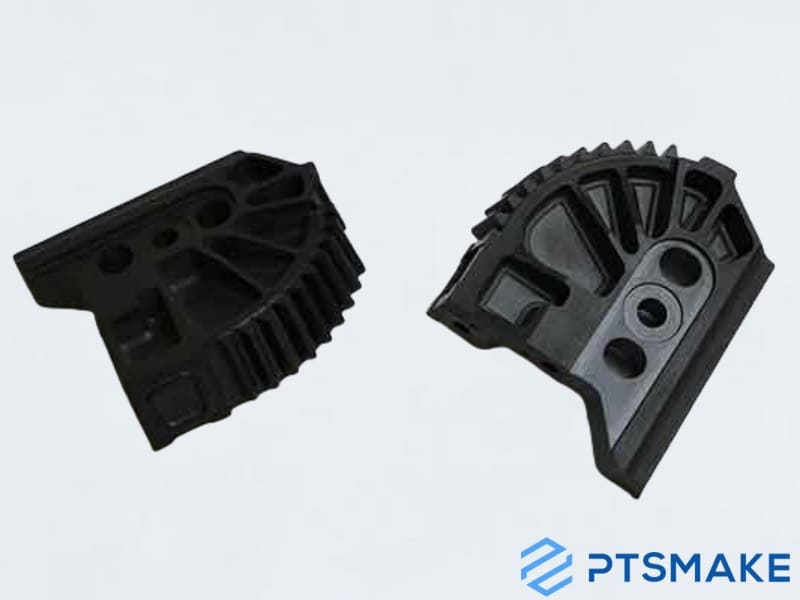
Industrial Machinery
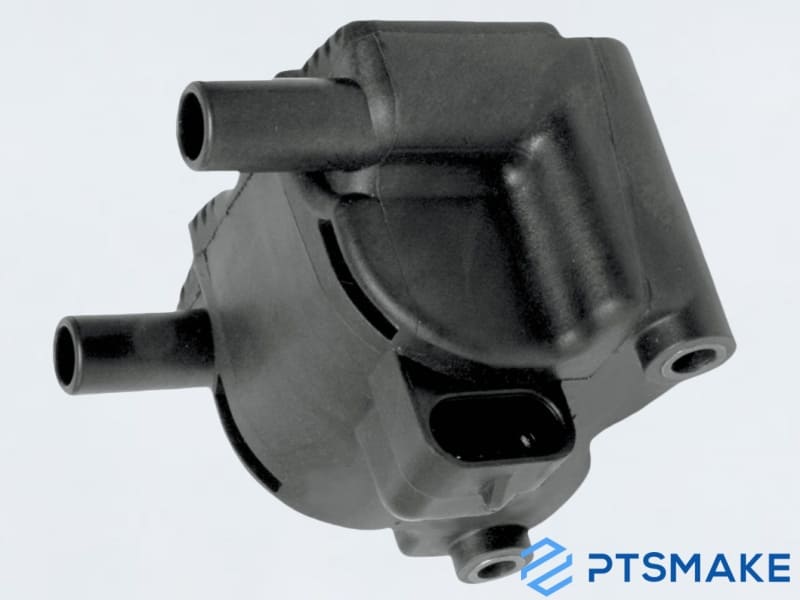
Medical Devices
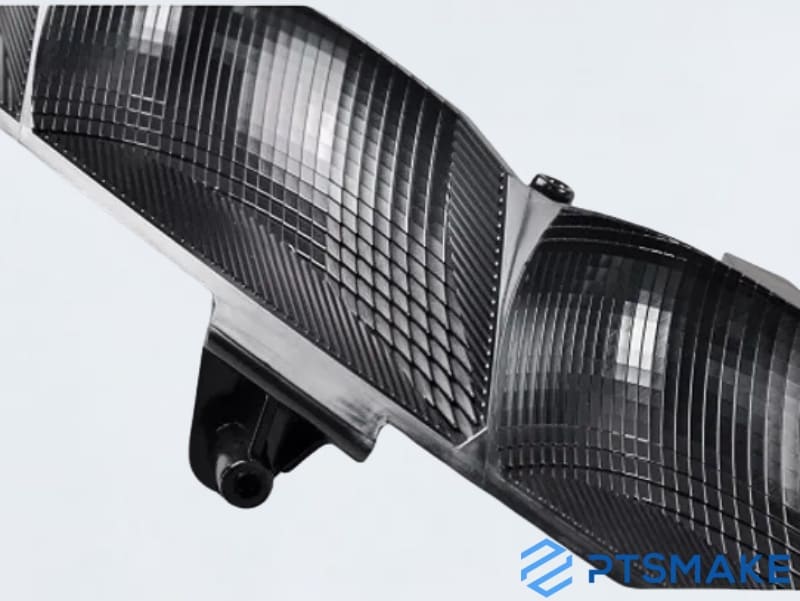
Lighting Industry
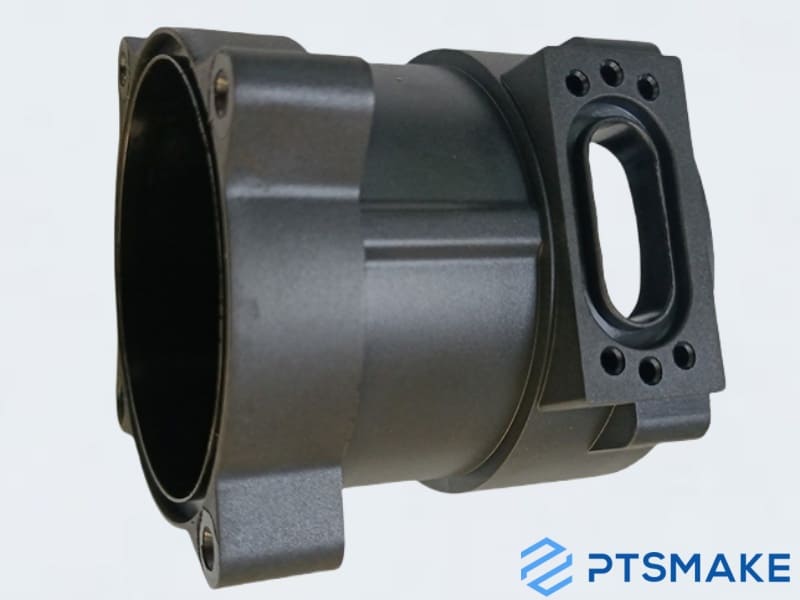
Energy & Power
Why Choose PTSMAKE for High Temperature Injection Molding?
We process 50+ high-temperature materials (PTFE, PEEK, PPS, PPSU, PPO, PI, PVDF, PEI, PAI, PBI, LCP) with ±0.01mm precision
Utilizing advancedmachines, we ensure dimensional accuracy and optimize designs, reducing production costs by up to 30%.
Our 50+ advanced molding machines enable 15-day prototype cycles and 30% faster production timelines.
Our 3-stage quality checks maintain a defect rate below 0.2% with full traceability for every molded parts.
How We Ensure Top Quality in High Temperature Injection Molding at PTSMAKE
- High temperature injection molding requires strict quality control to meet demanding industry standards. At PTSMAKE, we use a 5-stage quality management system to guarantee precision and reliability in every part. Let’s break down how we do it.
- Stage 1: Material Selection & Pre-Testing
We start by testing polymer materials at 300°F–500°F using ASTM D638 standards. Our engineers verify heat resistance, shrinkage rates, and chemical stability before approving materials. This prevents warping and degradation during high-temperature molding.
- Stage 2: Precision Mold Design
Our team designs molds with ±0.005mm accuracy using Siemens NX software. We simulate heat distribution patterns to identify hot spots and optimize cooling channels. 98% of our molds pass first-article inspection (FAI) thanks to this digital validation process.
- Stage 3: Real-Time Production Monitoring
During molding, sensors track barrel temperatures (up to 450°F), injection pressure (1,500–2,500 psi), and cycle times. Any deviation triggers automatic alerts. Our operators perform hourly checks using calibrated tools, ensuring consistent output across batches.
- Stage 4: Post-Process Verification
We test 100% of parts for:
• Dimensional accuracy (CMM measurements)
• Surface defects (3D optical scanners)
• Mechanical strength (ISO 527 tensile tests)
Critical components undergo additional heat aging tests at 250°F for 48+ hours.
- Stage 5: Continuous Improvement
Every project is documented in our cloud-based QMS. We analyze data like defect rates (consistently <0.3%) and customer feedback to refine processes. This system helped clients like Huawei reduce part failures by 67% in high-heat robotics applications.
- With 20+ years of experience and ISO 9001-certified workflows, PTSMAKE delivers high temperature injection molding solutions you can trust. Our 24/7 engineering support team resolves issues 3x faster than industry averages.
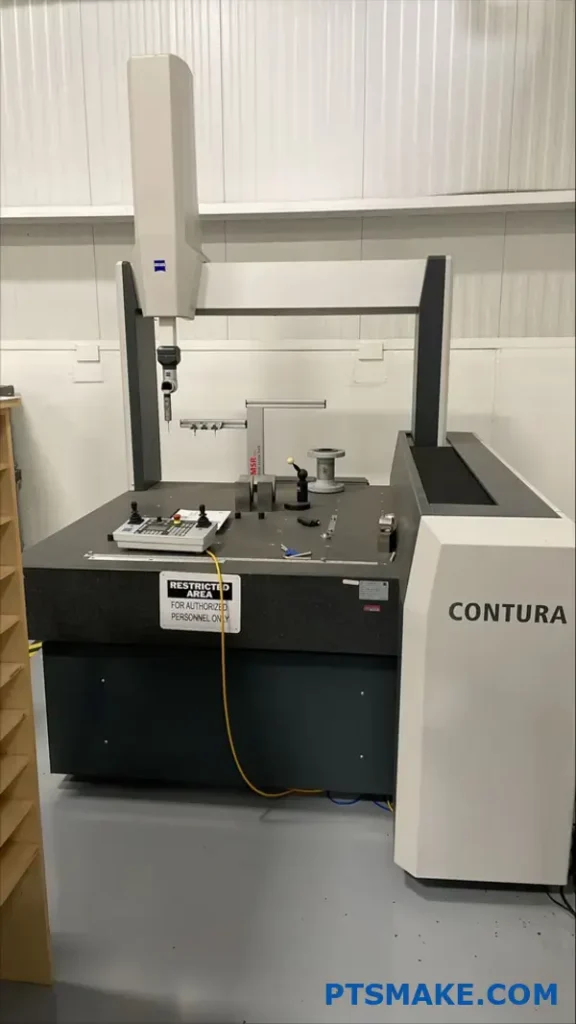
"PTSMAKE delivered heat-resistant nylon gears for our aerospace project. Their molding process met MIL-spec requirements. Zero warping issues even at 130°C continuous use. Saved us 3 weeks vs. previous suppliers
Ryan Carter, Manufacturing Director, USA"
Top Materials for High Temperature Injection Molding
PTFE
PEEK
PPS
PPO
PI
PEI
PBI
LCP
Typical Lead Times for High Temperature Injection Molding
Balancing speed and precision in manufacturing timelines
- High temperature injection molding projects often face longer lead times due to material-specific challenges. At PTSMAKE, we’ve reduced average lead times to 2-3 weeks for custom molds and 7-10 days for production batches. Our 20+ years of expertise in precision manufacturing helps streamline processes without compromising quality.
- Key factors affecting lead times include material curing requirements (e.g., PEEK, PEI), part complexity, and order volume. For urgent needs, our team offers expedited services that cut timelines by 30-40%. Over 85% of projects meet or beat initial deadlines through our dedicated project management system.
- We maintain 48-72 hour response times for quotes and design feedback. Clients like HUA WEI and BMW rely on our ISO-certified facilities in Shenzhen and Dongguan, where 90% of tooling is completed in-house. Real-time updates via our client portal ensure transparency at every stage.
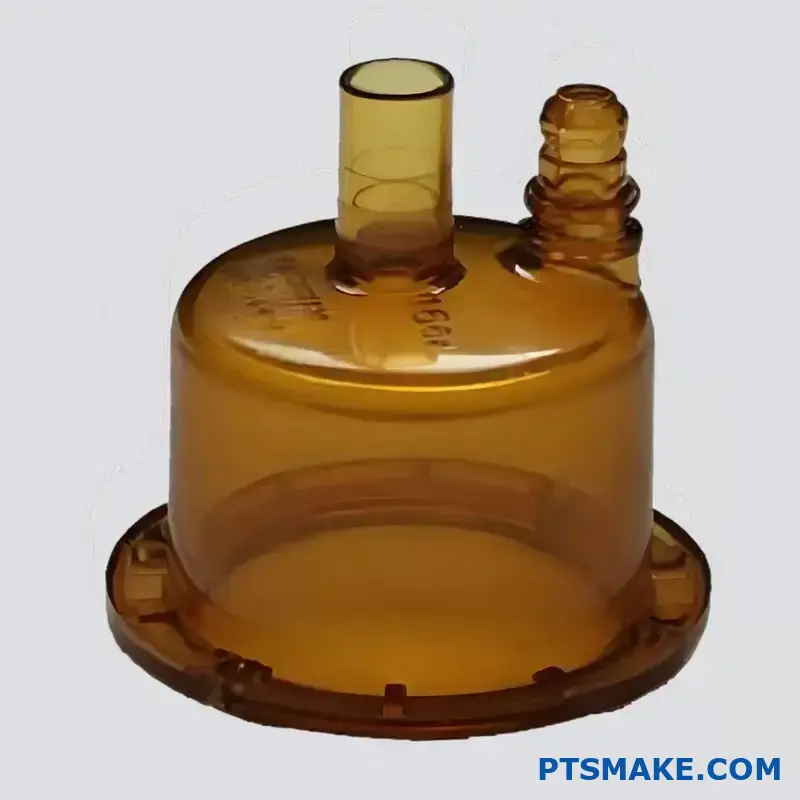
High-Temperature Injection Molding: 8-Step Manufacturing Process
1. Material Selection
2. Mold Design
3. Machine Setup
4. Material Drying
5. Injection Molding
6. Cooling Process
7. Part Ejection
8. Quality Inspection
Request a Custom Quote Today
Get an accurate estimate for your project today. Let us help you meet your exact specifications.
Cost-Effective Solutions for High Temperature Injection Molding
1. Material Optimization
2. Mold Design Efficiency
3. Cycle Time Reduction
4. Automation
5. Bulk Purchasing
6. Design Simplification
7. Secondary Process Elimination
Customization Options for High Temperature Injection Molding
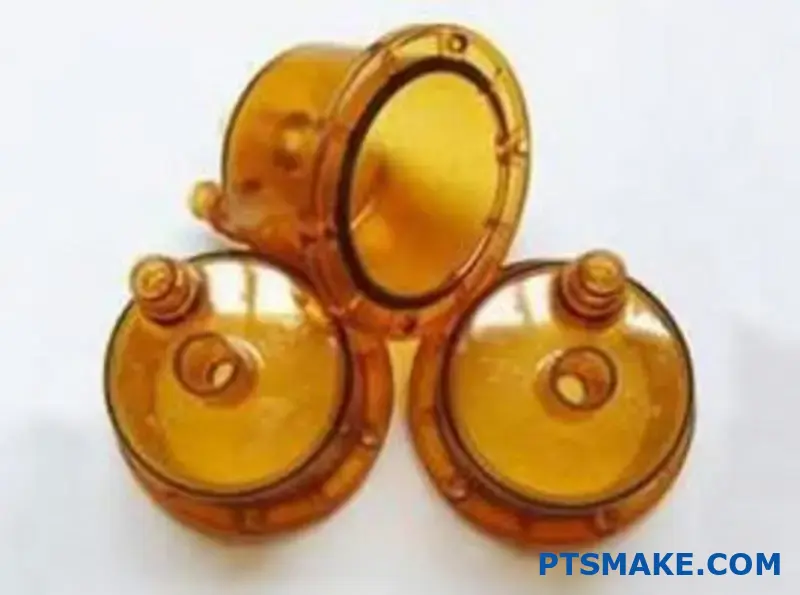
Material Customization for High-Temperature Resistance
Tooling and Mold Design Flexibility
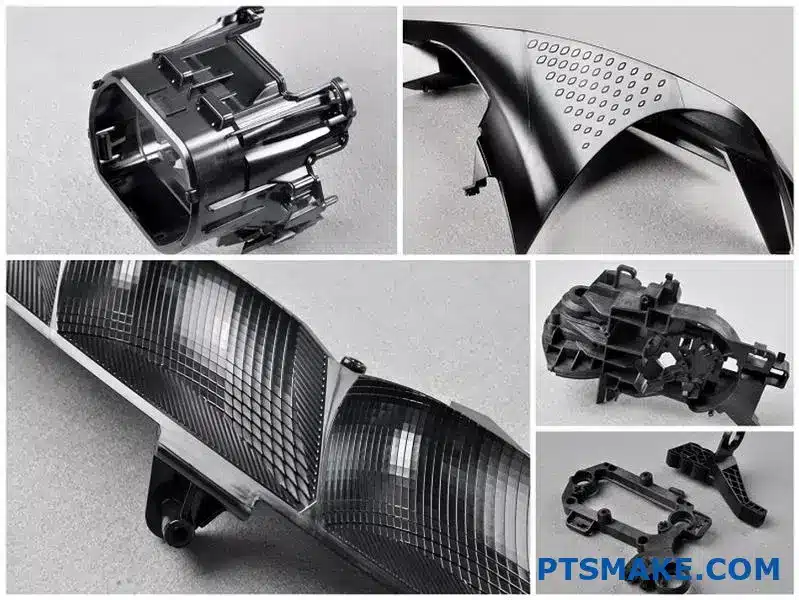
Surface Finish and Post-Processing Options
Rapid Prototyping to Full Production Scaling
Success Stories: High Temperature Injection Molding Solutions
Medical Device Manufacturer in Germany
PTSMAKE redesigned the mold with conformal cooling channels and switched to a heat-stabilized PEEK material. This reduced cycle time by 18% and achieved ±0.05mm dimensional stability across 500+ sterilization cycles.
The solution helped the client secure a critical WHO certification and expand into emerging markets.
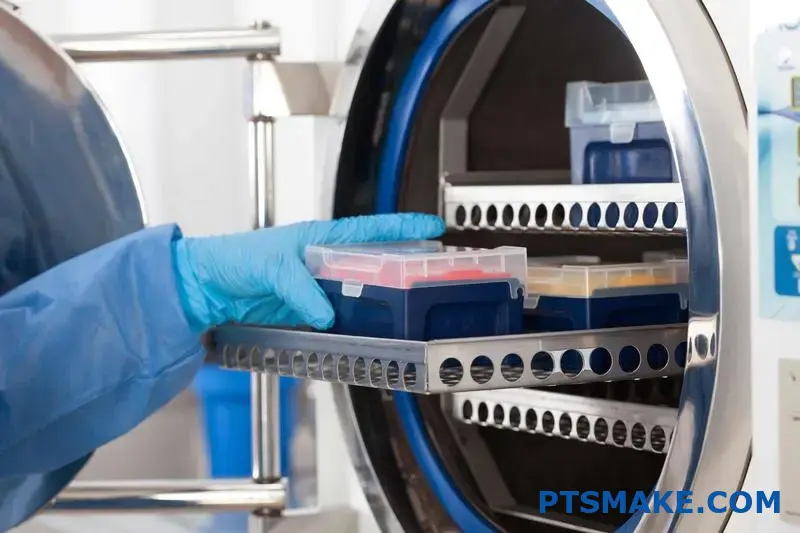
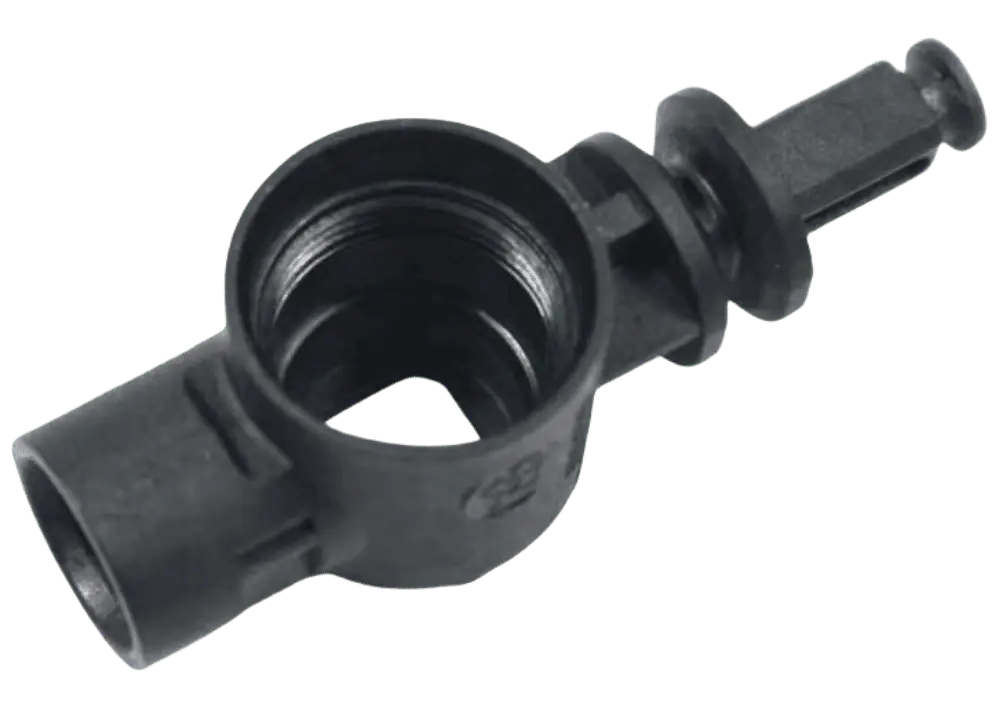
European Industrial Robotics Company
PTSMAKE implemented a hybrid approach combining CNC-machined mold inserts with high-precision temperature control during injection molding. The resulting gears showed 98% less wear than industry benchmarks, allowing the client to extend maintenance intervals and win a flagship factory automation project.
Contact Custom High Temperature Injection Molding Expert Today!
We look forward to the opportunity to work with you and contribute to your project’s success.