Overmolding & Insert Molding Factory Solutions
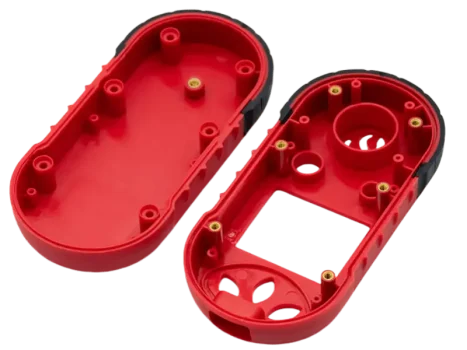
LOW MOQ 100 PCS
50% Cost Savings vs US/EU
Fast Turnaround & Global Shipping
Machines Ranging From 30 Tons to 1,600 Tons






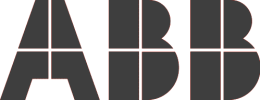

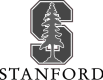
What Our Clients Say
Our clients are located worldwide, and their feedback speaks for itself. If you’d like to verify our reputation with customers in your area, don’t hesitate to contact us—we’d be happy to connect you with them and share relevant case studies.
Top 8 Industries Using Overmolding and Insert Molding
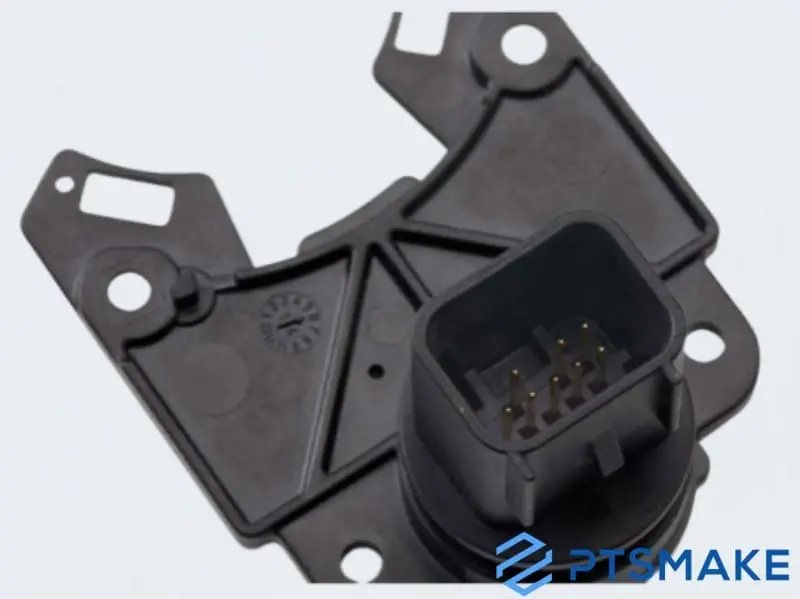
Automotive
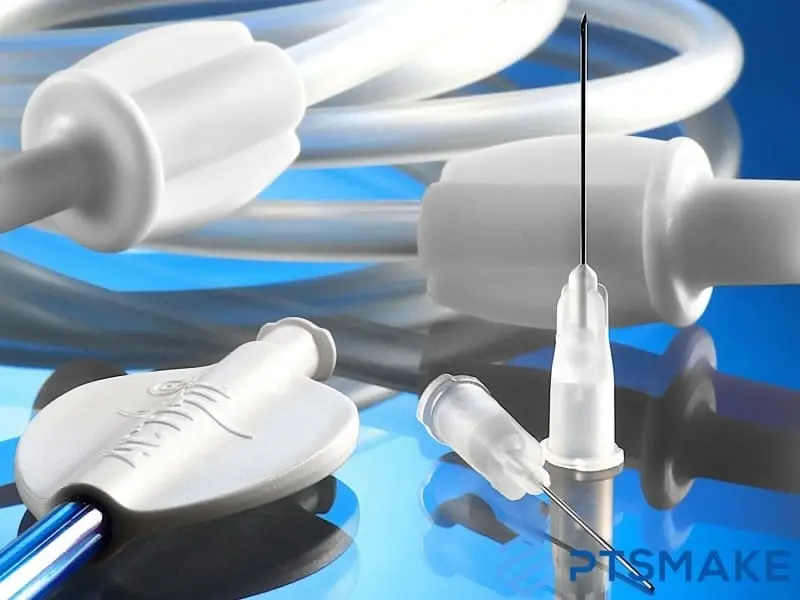
Medical Devices
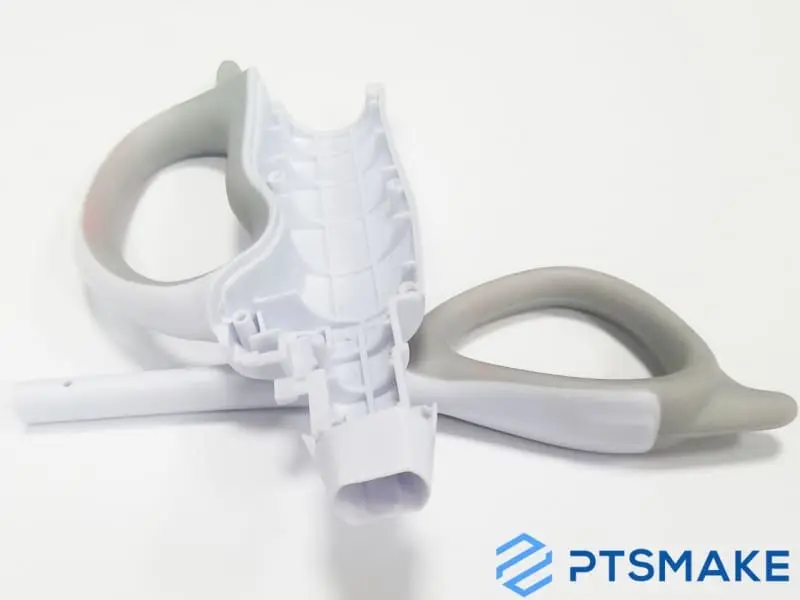
Consumer Electronics
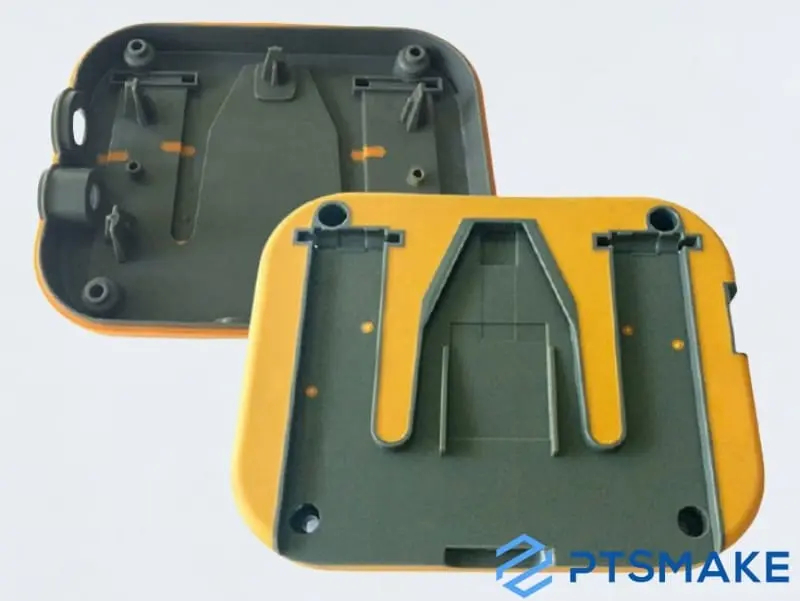
Industrial Machinery
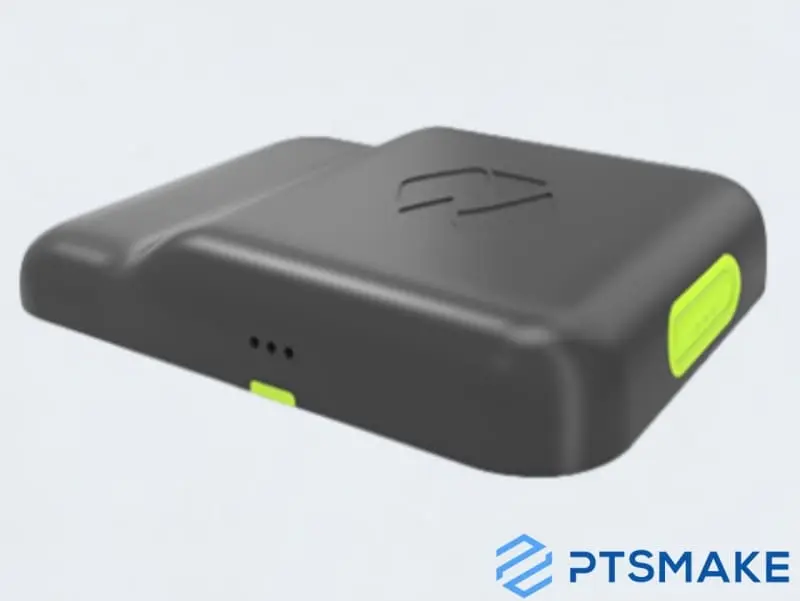
Aerospace Parts
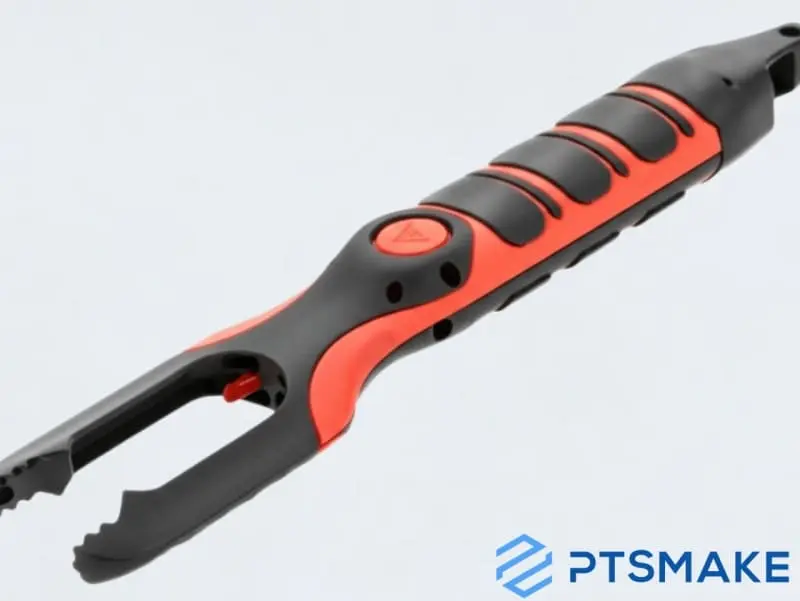
Electrical Systems
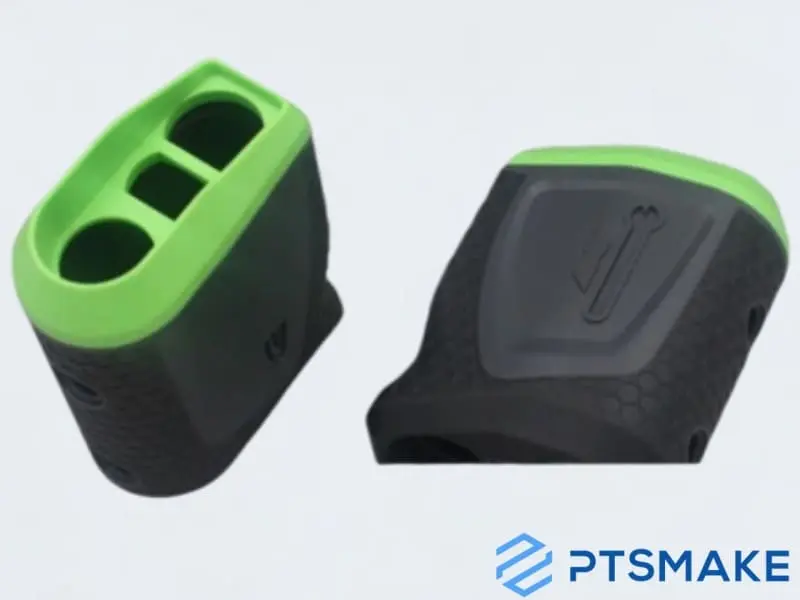
Packaging Industry
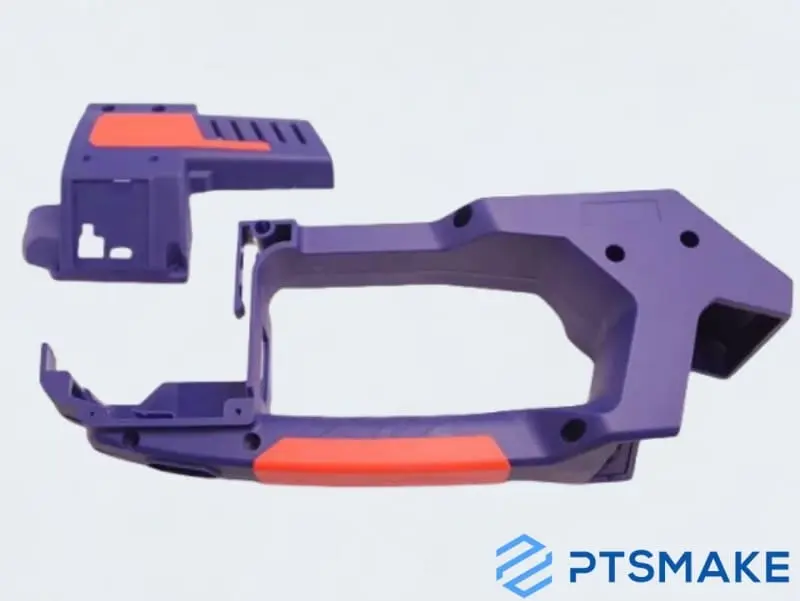
Robotics
Why Choose PTSMAKE for Overmolding & Insert Molding?
Combines CNC machining, mold making, and injection molding under one roof. Eliminate multi-supplier coordination.
Utilizing advancedmachines, we ensure dimensional accuracy and optimize designs, reducing production costs by up to 30%.
Our 50+ advanced molding machines enable 15-day prototype cycles and 30% faster production timelines.
Our 3-stage quality checks maintain a defect rate below 0.2% with full traceability for every molded parts.
How We Ensure Quality Control in Overmolding and Insert Molding Processes at PTSMAKE
- At PTSMAKE, we know quality control is your top concern. Overmolding and insert molding require extreme precision to bond materials like silicone, rubber, and metal seamlessly. Here’s how we guarantee defect-free results across 15+ industries, including medical devices and automotive.
- Step 1: Material Testing
We start by testing every batch of raw materials. Our ISO 9001-certified labs use FTIR spectroscopy to verify polymer composition. For insert molding, we check metal inserts for surface roughness (Ra ≤ 0.8μm) and dimensional accuracy (±0.01mm).
- Step 2: Process Automation
Our 50+ injection molding machines have IoT sensors that track pressure (800-1,200 bar) and temperature (180-320°C) in real time. If any parameter deviates by 2%, the system auto-pauses production. This prevents 99.7% of material waste issues.
- Step 3: Dual Inspection System
Every 30 minutes, our team performs manual checks using coordinate measuring machines (CMM). We also use automated vision systems to scan 100% of parts for:
– Bond line thickness (0.1-0.3mm tolerance)
– Flash (<0.05mm)
– Voids (0% acceptance)
- Step 4: Real-Time Reporting
You get daily updates via our client portal, including:
– High-speed camera footage of mold cycles
– 3D scan comparisons against CAD files
– Statistical process control (SPC) charts tracking CpK ≥ 1.67
- With 20+ years of experience and ISO 9001-certified workflows, PTSMAKE delivers high quality overmolding and insert molding solutions you can trust. Our 24/7 engineering support team resolves issues 3x faster than industry averages.
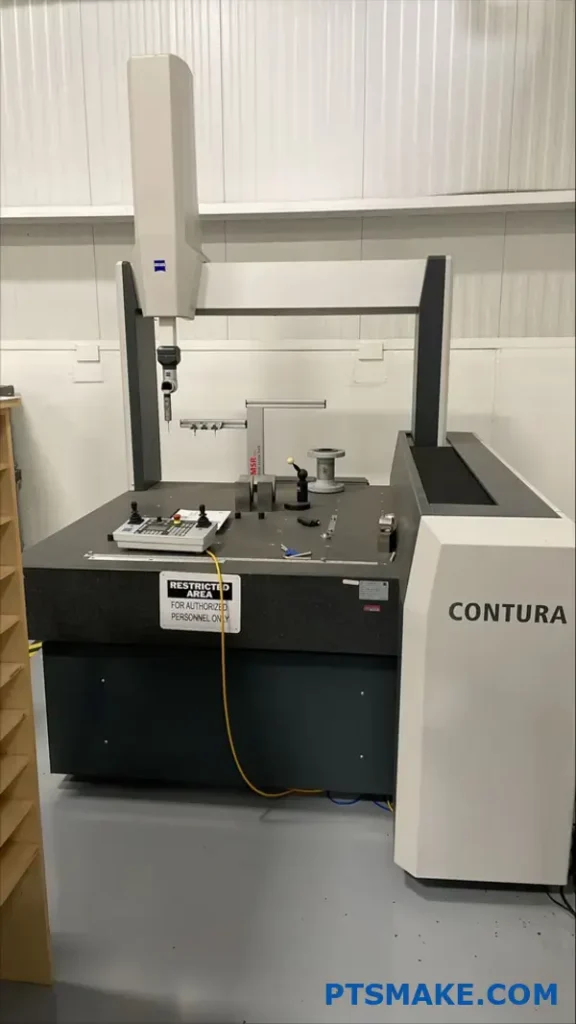
"Perfectly overmolded ergonomic handles for power tools – tight tolerances, no delamination. Their DFM report highlighted 3 critical adjustments we’d overlooked. Trustworthy partner.
Emily Chen, COO, Taiwan"
Top Materials for Overmolding and Insert Molding
TPE
PP
ABS
PA
PC
Silicone
TPU
PE
What Are Typical Lead Times for Overmolding and Insert Molding?
Factors that impact production timelines for overmolding and insert molding projects.
- Lead times for overmolding and insert molding depend on design complexity, material selection, and production volume. Simple projects may take 2-3 weeks, while intricate designs with tight tolerances often require 4-6 weeks. At PTSMAKE, we use automated mold flow analysis to reduce trial phases by 30%, accelerating project timelines without compromising precision.
- Material curing times significantly affect schedules. Silicone overmolding typically adds 1-2 days compared to rigid thermoplastics. For insert molding, pre-production steps like CNC machining metal inserts add 3-5 days. Our vertically integrated facility handles both processes under one roof, eliminating 72-hour delays from third-party coordination.
Why Supplier Choice Impacts Lead Times
- Suppliers with in-house tooling shops reduce lead times by 25% compared to those outsourcing molds. PTSMAKE’s 55 CNC machines operate 24/7, completing mold bases 30% faster than industry averages. Our real-time production tracking portal lets clients monitor progress hourly, reducing communication delays by 80%.
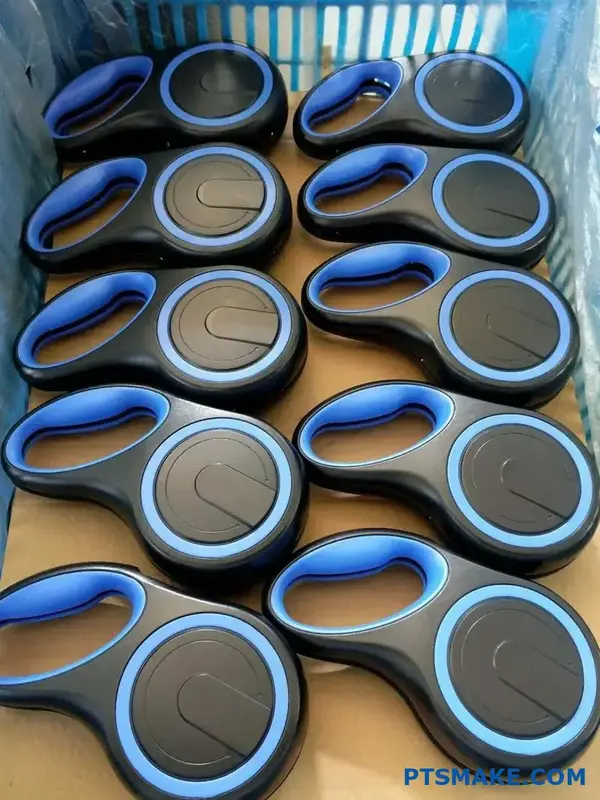
Overmolding and Insert Molding: 8 Key Manufacturing Steps
1. Material Selection
2. Mold Design
3. Insert Preparation
4. First Molding
5. Cooling & Solidification
6. Insert Placement
7. Second Molding
8. Quality Inspection
Request a Custom Quote Today
Get an accurate estimate for your project today. Let us help you meet your exact specifications.
Cost-Effective Solutions for Overmolding and Insert Molding
1. Material Selection
2. Design Optimization
3. Prototype Testing
4. Pick-n-Place Method
5. Process Consolidation
6. Standardized Inserts
7. Volume Planning
8. Overseas Partnership
Customization Options for Overmolding and Insert Molding
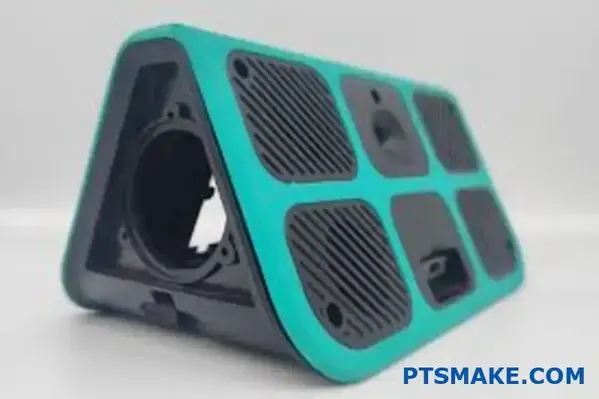
Material Customization
Material Selection: Choose from over 50+ engineering-grade plastics, silicones, or rubber materials. We support combinations like TPE over PC or nylon inserts with soft-touch coatings. Our team helps select materials for chemical resistance, durability, or specific industry certifications.
No Geometry Limits
Geometry & Tooling: Create complex shapes with multi-cavity molds or micro-sized components. Our CNC machining capabilities enable tight tolerances (±0.01mm) for insert placement accuracy. We handle undercuts, thin walls, and textured surfaces.
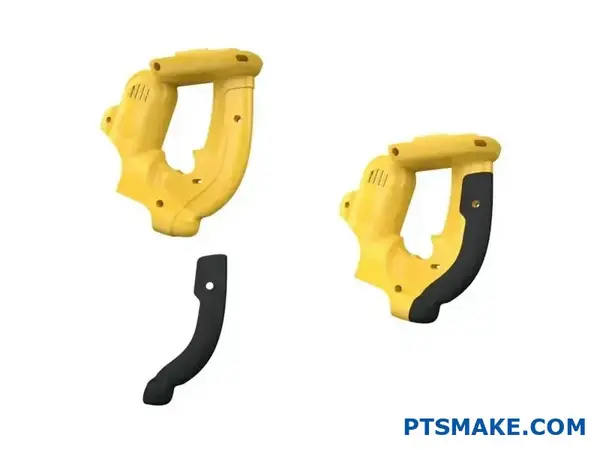
Surface Finish and Post-Processing Options
Surface Finishes: Customize appearance and performance with options like matte, glossy, or UV-resistant coatings. We offer EMI shielding layers, anti-slip textures, or medical-grade smooth finishes for specialized applications.
Insert Components
Insert Integration: Combine metal, ceramics, or pre-molded plastic inserts with overmolding. Our vertical integration allows seamless coordination between CNC machining and molding teams, reducing production delays.
Overmolding and Insert Molding Success Stories
Consumer electronics Manufacturer in Germany
Client Type: Consumer electronics company developing waterproof smart home devices
Country: Germany
Problem: Failed IP68 certification due to micro-gaps in insert-molded sensor housings. The existing process couldn’t maintain consistent bonding between PBT plastic and copper contacts.
Solution: Our engineers developed a multi-stage insert molding approach with pre-heated inserts. We created custom tooling with 112 micro-cooling channels to control thermal expansion differences. The revised process achieved 100% adhesion strength requirements.
Result: The client launched products 3 weeks ahead of schedule, capturing 23% market share in Q1. Warranty claims dropped by 62% post-implementation.
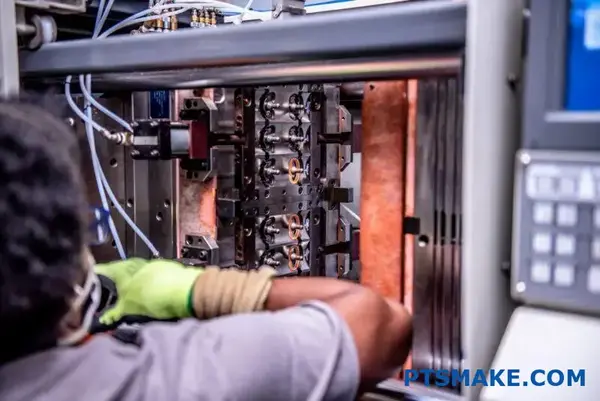
Contact Custom Overmolding And Insert Molding Expert Today!
We look forward to the opportunity to work with you and contribute to your project’s success.