China ABS Injection Molding Factory Direct Services
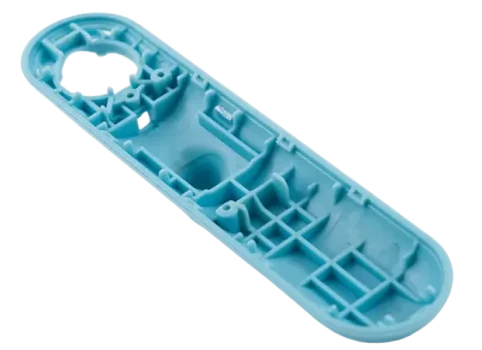
LOW MOQ 100 PCS
50% Cost Savings vs US/EU
Fast Turnaround & Global Shipping
Machines Ranging From 30 Tons to 1,600 Tons






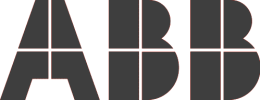

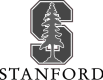
What Our Clients Say
Our clients are located worldwide, and their feedback speaks for itself. If you’d like to verify our reputation with customers in your area, don’t hesitate to contact us—we’d be happy to connect you with them and share relevant case studies.
Top 8 Industries Using ABS Injection Molding
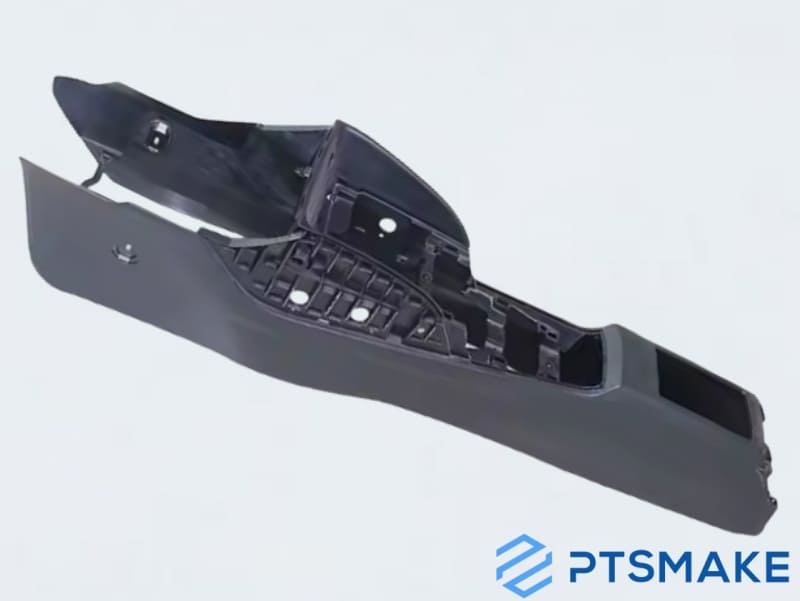
Automotive
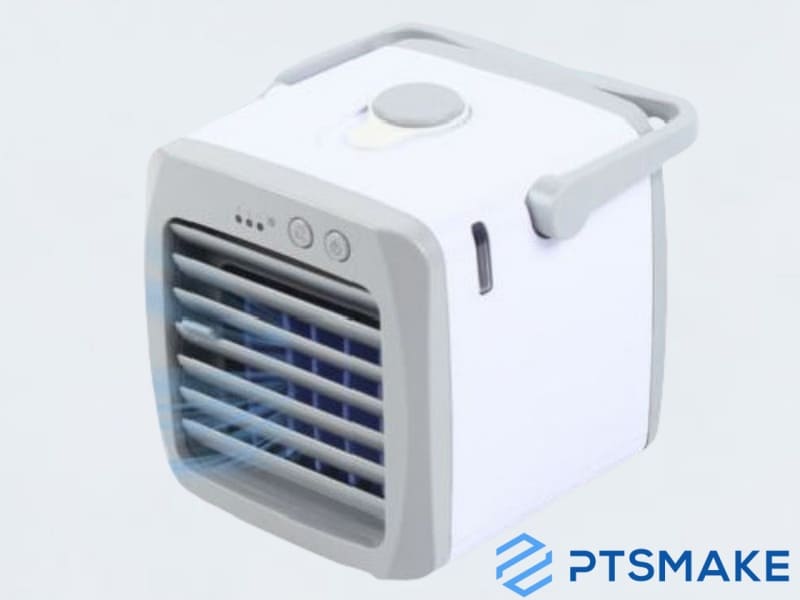
Consumer
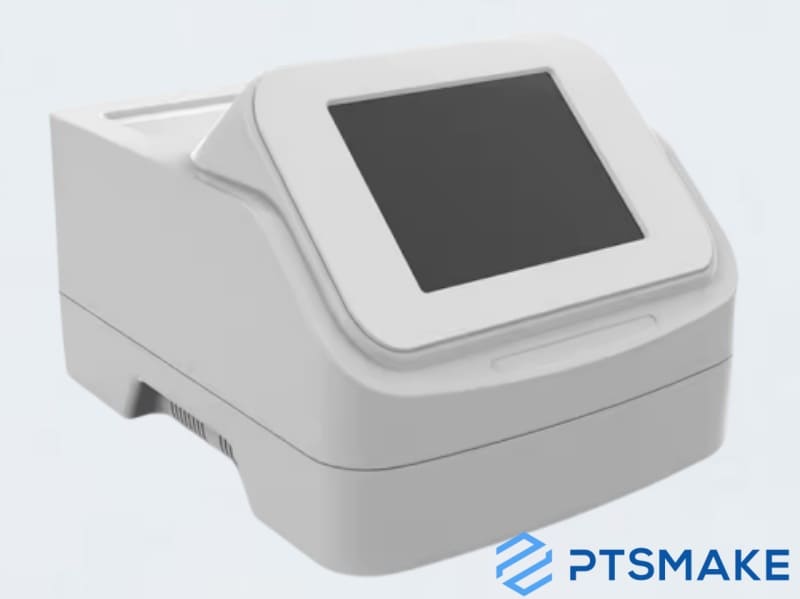
Medical
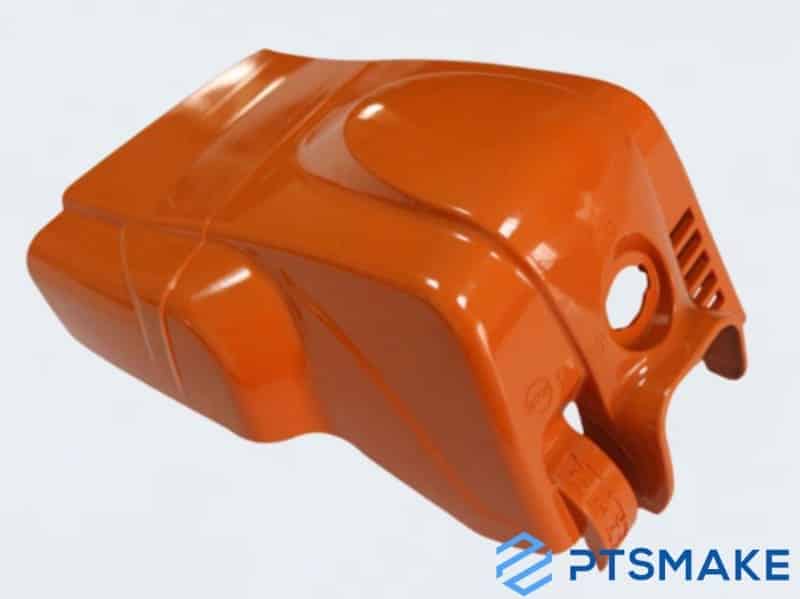
Home Appliances
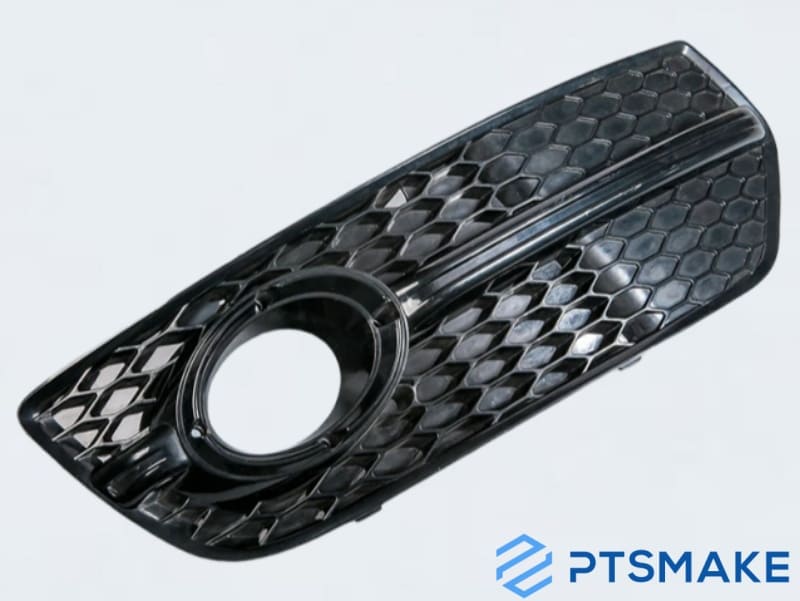
Industrial Tools
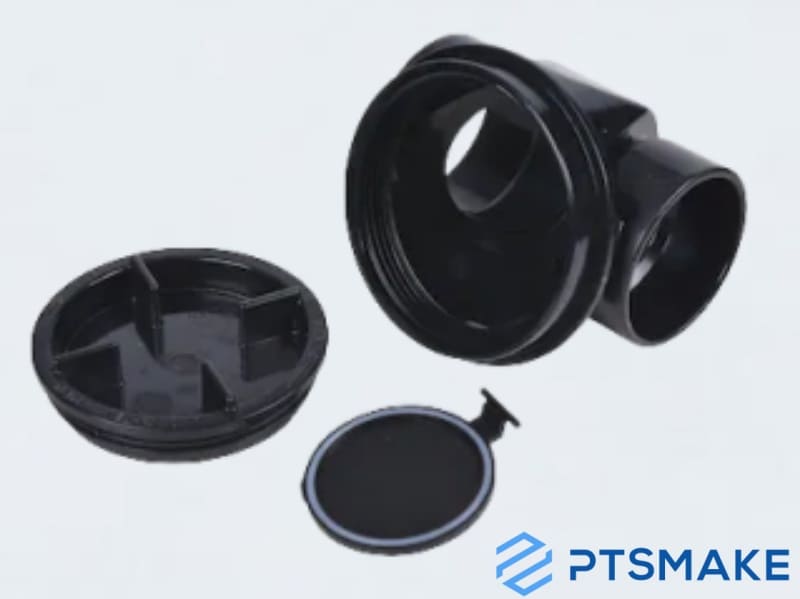
Plumbing Systems
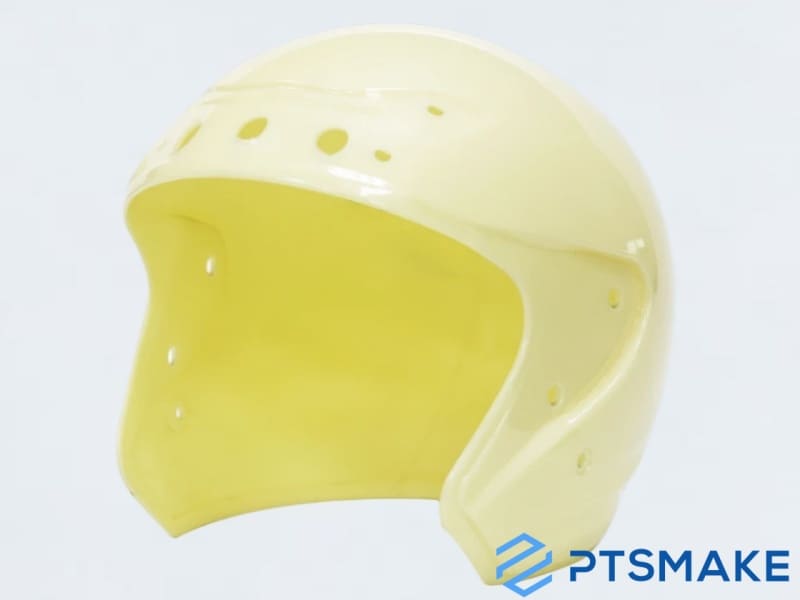
Safety Gear
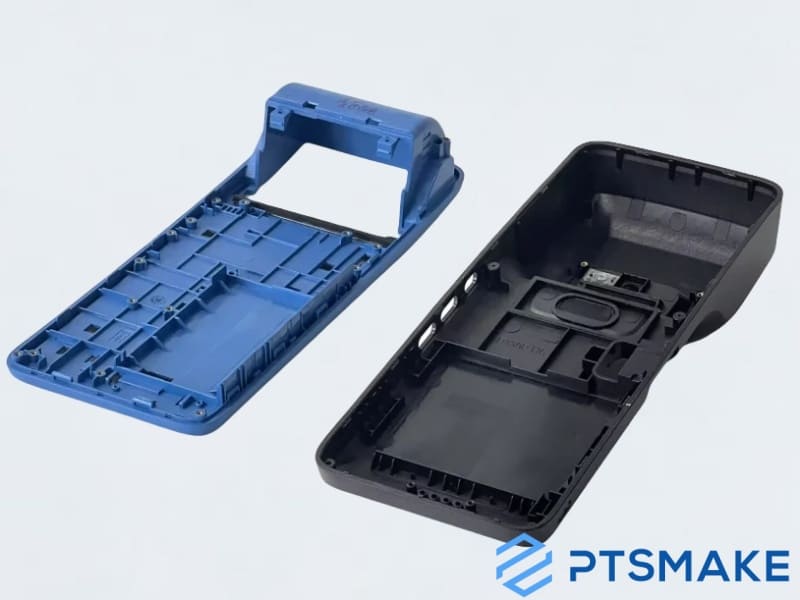
Telecommunications
Why Choose PTSMAKE for ABS Injection Molding?
ISO 9001 certified with <0.01mm precision and 99.8% pass rate on first inspection across all manufacturing processes.
Utilizing advancedmachines, we ensure dimensional accuracy and optimize designs, reducing production costs by up to 30%.
22+ years specialized experience with engineering team of 30+ professionals handling complex projects across 8 major industries.
Strategic China location reduces costs by 30-40% while maintaining global quality standards and offering volume-based discounts .
How We Ensure Quality Control in ABS Injection Molding
- At PTSMAKE, we implement a 5-step quality control system for ABS injection molding. Let us explain how each stage prevents defects and ensures consistent results.
- Step 1: Raw Material Certification
We only use UL-proven ABS resins from suppliers like Covestro and LG Chem. Every batch undergoes FTIR testing to verify chemical composition.
- Step 2: Precision Mold Maintenance
Our 50+ injection molding machines work with molds that receive weekly PM checks. Temperature sensors in mold cavities maintain ±0.5°C accuracy.
- Step 3: Real-Time Process Monitoring
IoT-enabled machines track 14 parameters including melt temp (230-260°C), injection pressure (60-100 bar), and cooling rate. Alerts trigger if values deviate by 2%.
- Step 4: First Article Inspection
We produce 10 sample parts for CMM measurement before mass production. All critical dimensions are checked against your CAD files.
- Step 5: Batch Testing Protocol
3% of finished parts undergo mechanical testing – we guarantee tensile strength ≥40MPa and impact resistance ≥200J/m per ASTM D638 standards.
- With 20+ years of experience and ISO 9001-certified workflows, PTSMAKE delivers high quality overmolding and insert molding solutions you can trust. Our 24/7 engineering support team resolves issues 3x faster than industry averages.
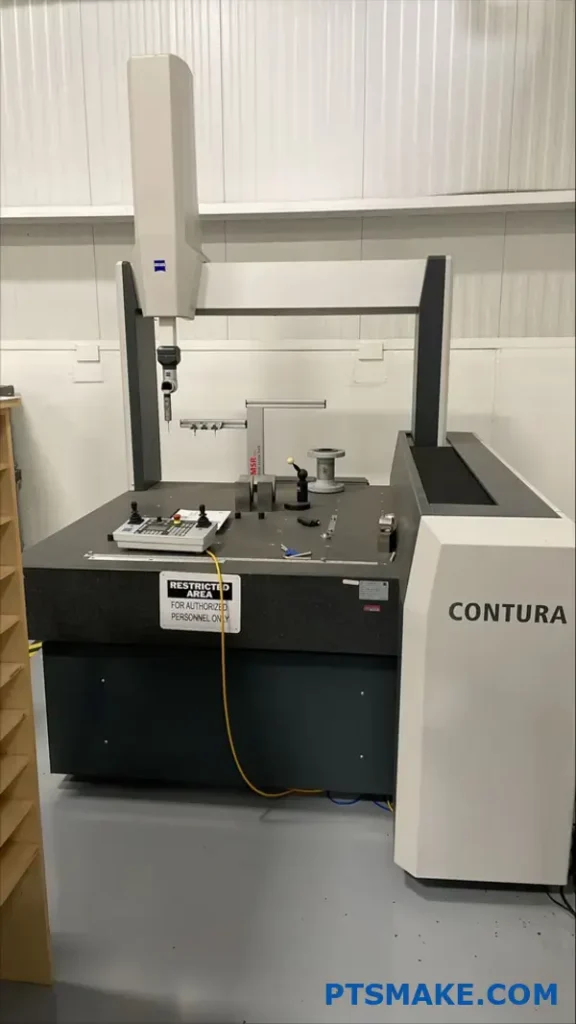
"The durability and finish on the casings for our new consumer gadget are fantastic. PTSMAKE understood our design needs and delivered exactly what we envisioned. We highly recommend their service.
Antoine, Product Designer, France"
Most Common Materials for ABS Injection Molding
General ABS
High-Impact ABS
Flame-Retardant ABS
Heat-Resistant ABS
Medical-Grade ABS
Glass-Filled ABS
Electroplating-Grade ABS
UV-Stabilized ABS
Understanding Typical Lead Times for ABS Injection Molding
- For most ABS injection molding projects, you can expect typical lead times ranging from 4-8 weeks. This timeline covers everything from mold design to final part production. However, several factors can either shorten or extend this timeframe.
- The complexity of your part design significantly impacts lead time. Simple parts with basic shapes might be completed in just 4 weeks, while complex parts with intricate features, tight tolerances, or textured surfaces could extend lead times to 10 weeks or more.
- Order volume also plays a crucial role. Small production runs (under 1,000 parts) generally fit within standard lead times. For high-volume orders (over 10,000 pieces), additional production time may be necessary, adding 1-2 weeks to your timeline.
- Many clients overlook the importance of design readiness. Having production-ready CAD files with proper tolerances and draft angles can save significant time. Design changes mid-production can add weeks to your timeline and increase costs.
- Material availability can cause unexpected delays. Standard ABS variants are usually readily available, but specialty grades with fire-retardant properties or custom colors may require additional procurement time.
- Quality testing requirements also affect delivery schedules. If your project needs extensive testing, dimensional verification, or material certifications, allocate an additional 3-5 days in your timeline.
- At PTSMAKE, we provide detailed lead time estimates during the quoting process. Our transparent approach helps you plan your supply chain effectively without unwelcome surprises down the line.
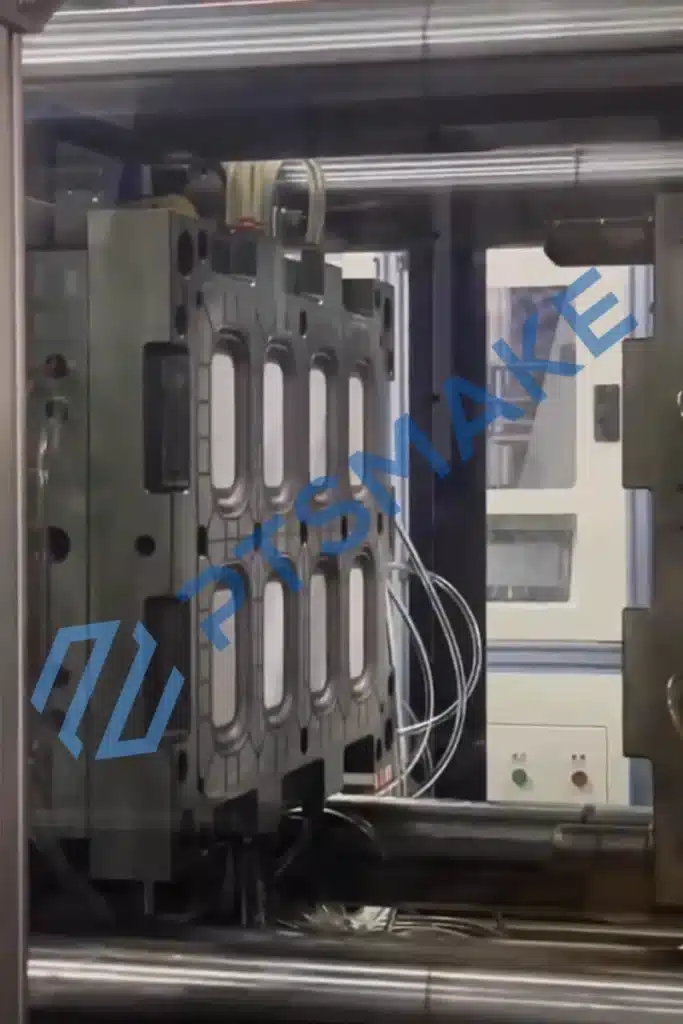
8 Essential Steps for ABS Injection Molding
1. Material Selection
2. Mold Design
3. Material Preparation
4. Machine Setup
5. Injection Process
6. Cooling Phase
7. Part Ejection
8. Quality Inspection
Request a Custom Quote Today
Get an accurate estimate for your project today. Let us help you meet your exact specifications.
Cost-Effective Solutions for ABS Injection Molding
1. Design Optimization
2. Material Selection
3. Family Molds
4. Automation Integration
5. Hot Runner Systems
6. Surface Finishing Considerations
7. Bulk Material Purchasing
8. Multi-Cavity Molds
9. Supplier Partnership
Customization Options for ABS Injection Molding
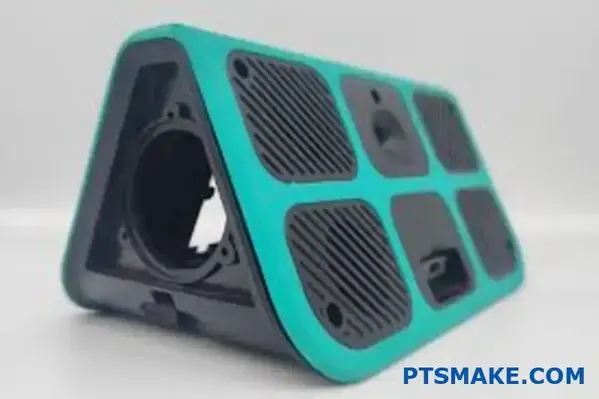
Material Customization
Color Customization
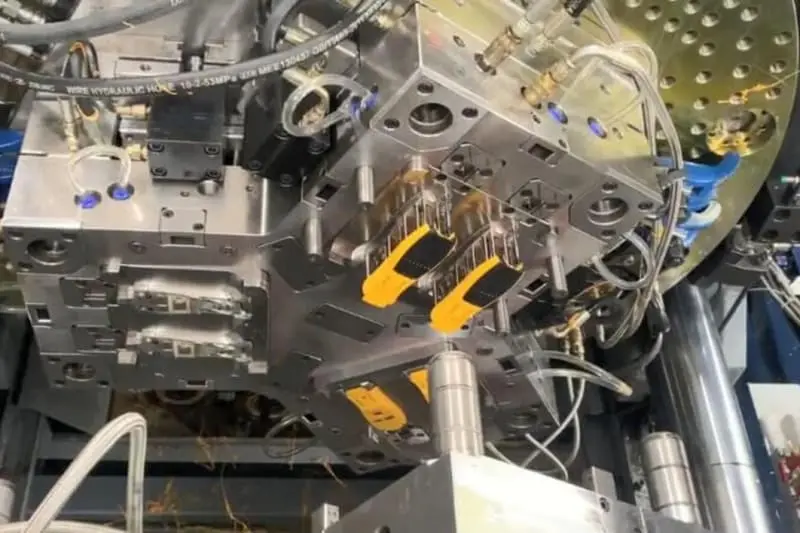
Surface Finish Customization
No Geometry Limits
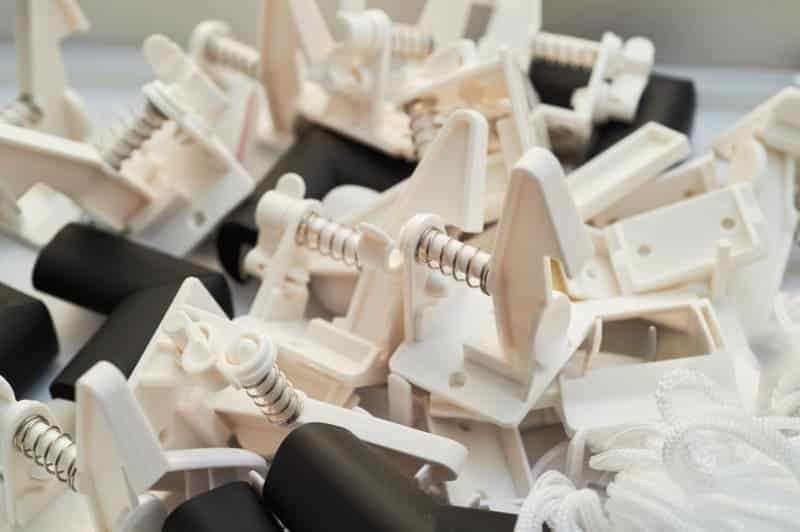
Secondary Operations
Insert Integration
ABS Injection Molding Success Stories
Consumer Electronics Company in Canada
Client Type: Consumer Electronics Company
Client Country: Canada
Client’s Problem: The client was preparing to launch a new high-end wireless speaker. A key aesthetic feature was its sleek ABS casing, requiring a flawless, high-gloss finish with very tight parting lines. Their challenge was finding a supplier who could consistently achieve this finish without defects like flow lines or sink marks, especially around complex features like speaker grilles and button openings. Previous suppliers had struggled, leading to high scrap rates and delaying their product launch timeline.
Our Solution: PTSMAKE leveraged its deep experience in high-quality ABS injection molding. We selected a premium ABS grade specifically designed for high-gloss cosmetic applications. Our tooling engineers paid meticulous attention to the mold surface polishing, achieving a mirror-like finish. We carefully designed the injection gates and venting to optimize melt flow and prevent surface imperfections. During molding, we precisely controlled injection speed, temperature, and holding pressure. We also implemented a multi-stage cooling process to minimize residual stress and prevent sink marks. Each part underwent careful inspection under specialized lighting to ensure finish consistency.
The Result: The ABS speaker casings produced by PTSMAKE exhibited a consistently flawless high-gloss finish, exceeding the client’s demanding aesthetic standards. Parting lines were virtually invisible. The scrap rate due to cosmetic defects dropped dramatically compared to their previous experiences. This allowed the client to meet their launch date with confidence. The premium look and feel of the product contributed significantly to positive customer reviews and strong initial sales, solidifying the product’s position in the competitive market.
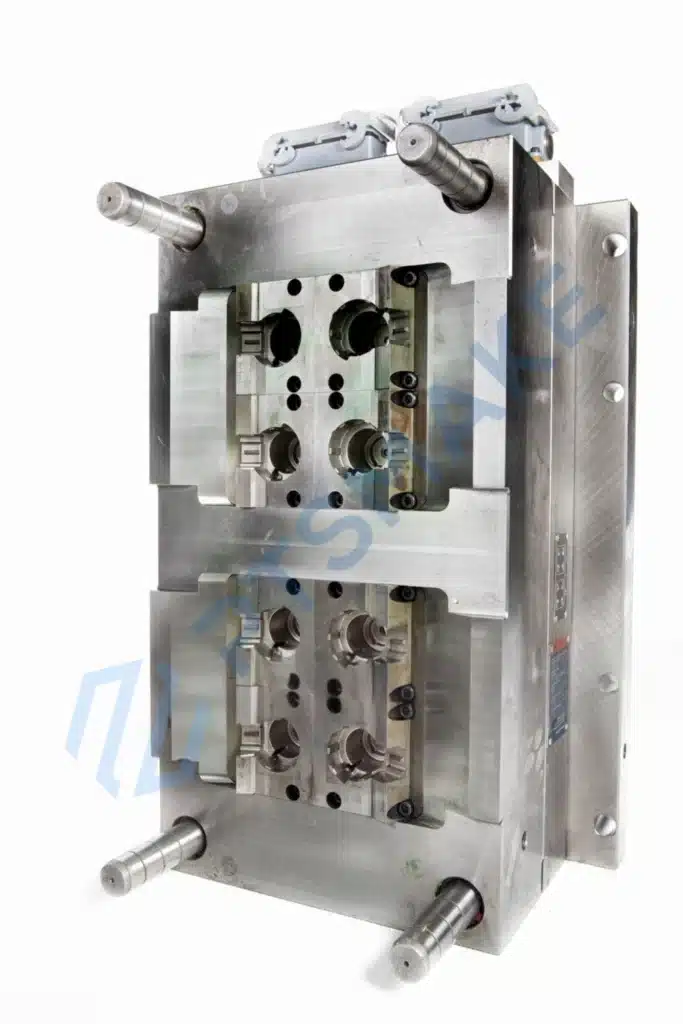
Contact Custom ABS Injection Molding Expert Today!
We look forward to the opportunity to work with you and contribute to your project’s success.