هل تكافح من أجل العثور على عملية تصنيع يمكنها التعامل مع درجات الحرارة القصوى؟ تذوب المواد البلاستيكية القياسية أو تتحلل تحت ظروف الحرارة المرتفعة، مما يتسبب في فشل المنتج في أسوأ اللحظات الممكنة. تحتاج مكوناتك إلى تحمّل البيئات القاسية، ولكن المواد التقليدية لا تفي بالغرض.
القولبة بالحقن في درجة حرارة عالية هي عملية متخصصة تستخدم اللدائن الحرارية الهندسية القادرة على تحمل درجات حرارة أعلى من 300 درجة فهرنهايت (150 درجة مئوية) مع الحفاظ على السلامة الهيكلية والأداء. توفر هذه المواد مقاومة استثنائية للحرارة والثبات الكيميائي والقوة الميكانيكية للتطبيقات الصعبة.
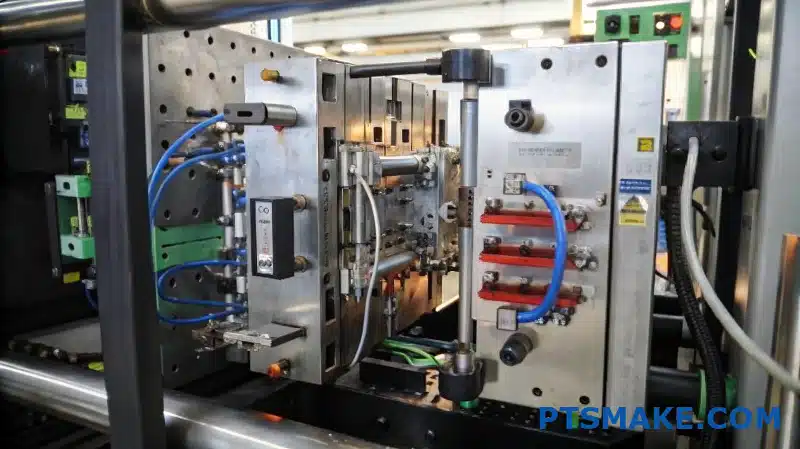
دعني أطلعك على ما يجعل هذه العملية ذات قيمة كبيرة للتطبيقات الصعبة. خلال السنوات التي قضيتها في PTSMAKE، عملت مع عملاء واجهوا تحديات خطيرة عندما لم تستطع المواد البلاستيكية القياسية التعامل مع متطلباتهم الحرارية. فتحت المواد عالية الحرارة إمكانيات جديدة لهم - وقد تفعل الشيء نفسه لمشروعك. دعنا نستكشف ما يمكن أن تفعله هذه المواد الخاصة وسبب أهميتها.
العلم وراء درجة الحرارة ومتانة البلاستيك الحراري
هل سبق لك أن سحبت قطعة بلاستيكية من سيارة ساخنة لتجدها مشوهة أو هشة؟ أو لاحظت أن بعض المنتجات البلاستيكية يبدو أنها تتعطل بشكل غير متوقع عند تعرضها لبيئات معينة؟ غالبًا ما تكون إدارة درجة الحرارة هي الحلقة المفقودة بين الأداء المتوسط والاستثنائي للقطع البلاستيكية.
تعمل عملية التشكيل بالحقن بدرجة حرارة عالية على تحسين متانة القِطع من خلال تعزيز التوجه الجزيئي، وتقليل الإجهاد الداخلي، وإنشاء هياكل بلورية أكثر اتساقًا، والسماح بترابط أفضل مع مواد التعزيز. تنتج هذه العملية أجزاءً ذات خواص ميكانيكية فائقة ومقاومة حرارية واستقرار كيميائي.
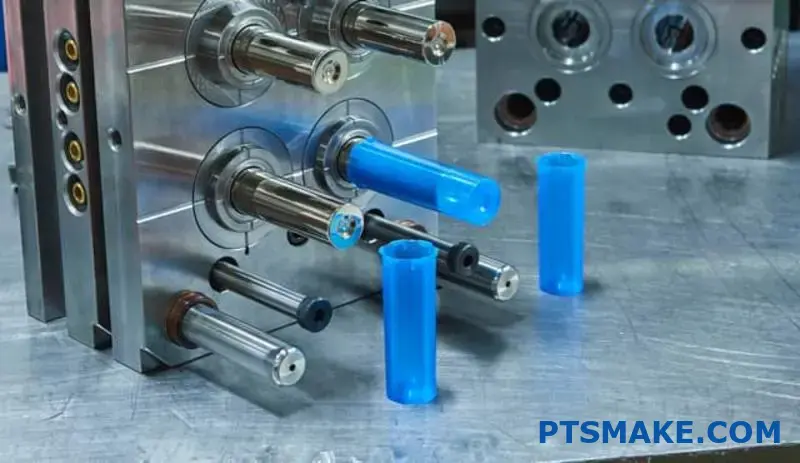
كيفية تأثير درجة الحرارة على بنية البوليمر
عندما نتحدث عن المتانة في الأجزاء المصبوبة بالحقن، نحتاج إلى فهم ما يحدث على المستوى الجزيئي أثناء المعالجة. تعد درجة الحرارة أحد أهم المتغيرات التي تؤثر على الخصائص النهائية للأجزاء البلاستيكية الحرارية.
محاذاة السلسلة الجزيئية
أثناء قولبة الحقن بدرجة حرارة عالية، تصبح سلاسل البوليمر أكثر حركة ومرونة. تسمح هذه الحركة المتزايدة للسلاسل بتوجيه نفسها بشكل أكثر فعالية في اتجاه التدفق أثناء الحقن. عندما يتم التحكم فيها بشكل صحيح، ينتج عن ذلك:
- قوة شد معززة على طول اتجاه التدفق
- مقاومة الصدمات المحسّنة
- خواص ميكانيكية أفضل بشكل عام
لقد لاحظت أن الأجزاء المصبوبة في درجات حرارة أعلى تُظهر عادةً تحسنًا في قوة الشد بمقدار 15-30% مقارنةً بتلك المنتجة في درجات الحرارة التقليدية. ويتضح ذلك بشكل خاص في المواد ذات الدرجة الهندسية مثل البوليمرات المعقدة الانسيابية1 مثل PEEK وPPS والبوليمرات البلورية السائلة.
تطوير التبلور
بالنسبة للبوليمرات شبه البلورية، تؤثر درجة حرارة المعالجة بشكل كبير على تطور البنية البلورية. توفر درجات حرارة المعالجة الأعلى:
- مزيد من الوقت لتكوين البلورات
- مناطق بلورية أكبر حجماً وأكثر اكتمالاً في الشكل البلوري
- توزيع بلوري أكثر اتساقًا في جميع أنحاء الجزء
يُترجم هذا التبلور المحسّن مباشرةً إلى مقاييس متانة أفضل. من خلال تجربتي مع التطبيقات عالية الأداء، تُظهر الأجزاء ذات الهياكل البلورية المثلى مقاومة أفضل بكثير للزحف والتعب والتشقق الإجهادي البيئي.
الحد من الضغوط الداخلية من خلال المعالجة في درجات حرارة عالية
تتمثل إحدى أهم مزايا القولبة بالحقن بدرجة حرارة عالية في تقليل الضغوط المتبقية في الجزء النهائي.
لماذا تعتبر الضغوطات المتبقية مهمة
الإجهادات المتبقية هي القوى الداخلية التي تبقى في الجزء بعد التشكيل والتبريد. هذه الضغوط:
- العمل كمركزات إجهاد يمكن أن تؤدي إلى حدوث تشققات
- تقليل الأداء الميكانيكي الكلي
- يمكن أن يسبب عدم استقرار الأبعاد بمرور الوقت
- جعل الأجزاء أكثر عرضة للهجوم الكيميائي
دور درجة الحرارة في الحد من التوتر
عند المعالجة في درجات حرارة أعلى:
- يتدفق ذوبان البوليمر بسهولة أكبر، مما يتطلب ضغط حقن أقل
- يمكن التحكم في معدل التبريد بشكل أفضل، مما يسمح بتصلب أكثر اتساقًا
- تتمتع الجزيئات بوقت أطول للاسترخاء قبل أن تتجمد في موضعها
لقد اختبرت القِطع المنتجة في درجات الحرارة القياسية مقابل درجات الحرارة المرتفعة، وكان الفرق في الأعطال المرتبطة بالإجهاد ملحوظًا. في أحد تطبيقات السيارات، أظهرت القِطع المصبوبة في درجات حرارة عالية عمر إجهاد أطول بحوالي 40% تحت التحميل الدوري.
توافق المواد المحسّنة وتعزيزها
تتيح المعالجة بدرجة حرارة عالية أيضًا تفاعلًا أفضل بين البوليمر الأساسي والمواد المضافة أو المعززة المختلفة.
فوائد تقوية الألياف
بالنسبة للمركبات المقواة بالألياف، توفر درجات حرارة المعالجة الأعلى:
المزايا | الآلية | تأثير المتانة |
---|---|---|
تحسين التصاق الألياف بالمصفوفة الليفية | ترطيب أفضل للألياف بواسطة البوليمر المنصهر | تحسين نقل الحمولة وتقليل سحب الألياف |
تقليل تكسر الألياف | لزوجة منخفضة تتطلب قوة قص أقل | الحفاظ على طول الألياف لتقوية مثالية |
توزيع أكثر اتساقاً للألياف | خصائص تدفق أفضل | التخلص من نقاط الضعف في الجزء |
التوافق مع المواد المضافة عالية الأداء
تتطلب العديد من الإضافات المعززة لقوة التحمل درجات حرارة معالجة أعلى لتعمل بشكل صحيح. وتشمل هذه الإضافات:
- مضادات الأكسدة التي تحمي من التدهور الحراري
- مثبتات الأشعة فوق البنفسجية للاستخدامات الخارجية
- معدِّلات التأثير التي تحسن الصلابة
- مثبطات اللهب للتطبيقات الحرجة للسلامة
أمثلة للتطبيق العملي
من خلال عملي مع العملاء في مختلف الصناعات، رأيت عن كثب كيف أن القولبة بالحقن في درجة حرارة عالية تغير أداء القِطع:
مكونات أسفل غطاء محرك السيارة
بالنسبة للأجزاء التي يجب أن تتحمل درجات الحرارة المرتفعة والسوائل العنيفة، مثل خزانات سائل التبريد أو فتحات سحب الهواء، فقد أثبتت القوالب ذات درجة الحرارة العالية أنها ضرورية. هذه الأجزاء عادةً ما ترى:
- إطالة عمر الخدمة (3-5 أضعاف التحسين)
- ثبات أبعاد أفضل في ظل التدوير الحراري
- مقاومة محسّنة لمواد التبريد ومواد التشحيم القائمة على الجليكول
تطبيقات الأجهزة الطبية
بالنسبة للمكونات الطبية القابلة للتعقيم، يوفر القولبة بالحقن بدرجة حرارة عالية:
- قدرة معززة على تحمل ظروف الأوتوكلاف (بخار 121 درجة مئوية)
- مقاومة كيميائية أفضل للمطهرات
- دقة أبعاد محسّنة للميزات الوظيفية الحرجة
في شركة PTSMAKE، تخصصنا في تصنيع هذه المكونات الصعبة لأكثر من 15 عامًا، حيث نحقق باستمرار مقاييس متانة استثنائية من خلال التحكم الدقيق في درجة الحرارة أثناء عملية القولبة بالحقن.
الموازنة بين المتانة وقابلية التصنيع
وعلى الرغم من أن درجات الحرارة المرتفعة تحسن المتانة بشكل عام، إلا أنه يجب موازنتها بعناية مع اعتبارات المعالجة:
- مخاوف التدهور المادي
- أوقات الدورات الممتدة
- زيادة استهلاك الطاقة
- تآكل أكبر للأدوات
- متطلبات تبريد أكثر تعقيداً
يتطلب هذا التوازن خبرة واسعة وقدرات متطورة للتحكم في العمليات. وهذا هو السبب في أن الشركاء ذوي الخبرة الراسخة في التشكيل في درجات الحرارة العالية، مثل فريقنا في PTSMAKE، يمكنهم إحداث فرق كبير في نتائج أداء الأجزاء.
كيف نضمن الدقة في الأجزاء المصبوبة بالحقن في درجة حرارة عالية؟
هل عانيت من قبل من عدم اتساق الأبعاد أو التواء في مكوناتك المصبوبة بالحقن ذات درجة الحرارة العالية؟ هل تجد نفسك ترفض مرارًا وتكرارًا الأجزاء التي لا تفي بمواصفاتك على الرغم من استخدام مواد "عالية الجودة"؟ قد تكون تحديات تحقيق الدقة في درجات الحرارة المرتفعة محبطة بشكل خاص.
يتطلب ضمان الدقة في القِطع المصبوبة بالحقن في درجة حرارة عالية اختيار المواد بعناية، وتصميم القالب الأمثل، والإعداد المناسب للماكينة، وتقنيات المعالجة المتخصصة. من خلال التحكم في ملامح درجة الحرارة، وإدارة معدلات التبريد، وتنفيذ تدابير مراقبة الجودة المناسبة، يمكن للمصنعين إنتاج مكونات دقيقة تتحمل الظروف الحرارية القاسية باستمرار.
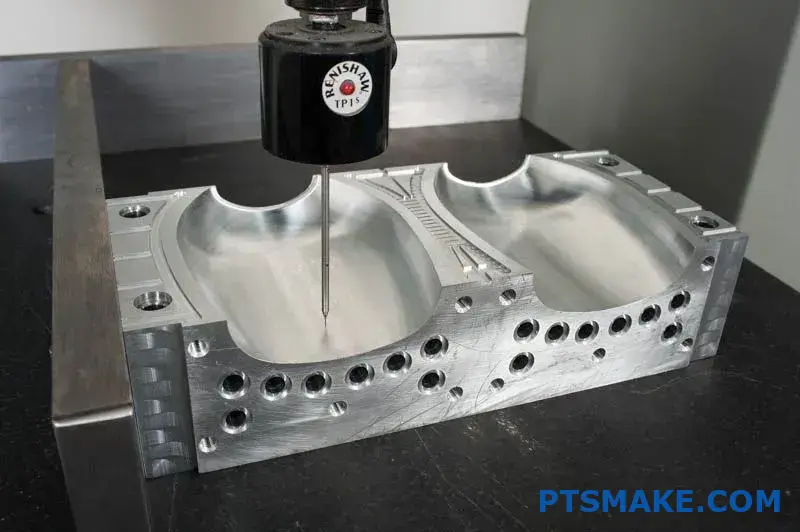
فهم سلوك المواد في درجات الحرارة المرتفعة
يمثل العمل مع البوليمرات ذات درجة الحرارة العالية تحديات فريدة من نوعها بالنسبة للقولبة الدقيقة. فعلى عكس المواد البلاستيكية القياسية، تُظهر المواد عالية الحرارة مثل PEEK وPPS وPEI (Ultem) وLCP خصائص تدفق واستجابات أبعاد مميزة أثناء المعالجة.
عند اختيار المواد للتطبيقات ذات درجات الحرارة المرتفعة، يجب ألا نأخذ في الاعتبار مقاومة الحرارة فحسب، بل أيضًا كيفية تصرف المادة أثناء دورة التشكيل بأكملها. إن درجة حرارة الانتقال الزجاجي2 يؤثر البوليمر بشكل كبير على كيفية تدفقه وتعبئته وتصلبه في القالب في النهاية.
في شركة PTSMAKE، لاحظت أن مطابقة خصائص المواد بشكل صحيح مع متطلبات التطبيق هي أساس التشكيل الدقيق. على سبيل المثال، توفر البوليمرات شبه البلورية مثل PEEK ثباتًا ممتازًا في الأبعاد ولكنها تتطلب تحكمًا دقيقًا في التبريد لإدارة معدلات التبلور، بينما توفر المواد غير المتبلورة مثل PEI إعادة إنتاج تفاصيل أفضل ولكن أنماط انكماش مختلفة.
إرشادات اختيار المواد للأجزاء الدقيقة ذات درجة الحرارة العالية
ينطوي اختيار المادة المثلى على الموازنة بين عدة عوامل حاسمة:
الخاصية المادية | التأثير على الدقة | الاعتبارات |
---|---|---|
التمدد الحراري | يؤثر على ثبات الأبعاد | توفر المعاملات المنخفضة تحكمًا أفضل في الأبعاد |
خصائص التدفق | يحدد القدرة على ملء المقاطع الرقيقة | مواد ذات تدفق ذائب أعلى قد تحسن الدقة في الأشكال الهندسية المعقدة |
معدل الانكماش | تؤثر بشكل مباشر على الأبعاد النهائية | انكماش أكثر اتساقًا وقابلية للتنبؤ يحسن الدقة |
حساسية الرطوبة | يمكن أن يسبب مشاكل في الأبعاد | بروتوكولات التجفيف المناسبة ضرورية للمواد المسترطبة |
محتوى الحشو | يقلل من الانكماش والالتواء | تعمل الحشوات الزجاجية أو الكربونية على تحسين ثبات الأبعاد |
تحسين تصميم القوالب من أجل دقة درجات الحرارة العالية
يلعب تصميم القالب دورًا حاسمًا في تحقيق الدقة في درجات الحرارة المرتفعة. يجب تكييف مبادئ تصميم القوالب التقليدية مع التحديات الفريدة التي تمثلها البوليمرات عالية الحرارة.
عناصر تصميم القالب الحرجة
موقع البوابة وحجم البوابة: بالنسبة للمواد عالية الحرارة، يجب وضع البوابات بعناية لضمان أنماط تعبئة متوازنة. يمكن للبوابات الصغيرة الحجم أن تؤدي إلى تسخين مفرط للقص مما يؤدي إلى تدهور خصائص المواد، بينما قد تؤدي البوابات كبيرة الحجم إلى مشاكل في الأبعاد أثناء التبريد.
أنظمة العداء: تعد أنظمة العداء المتوازن ضرورية للقوالب متعددة التجاويف لضمان التعبئة والتعبئة المنتظمة. بالنسبة للمواد ذات درجات الحرارة العالية، يمكن لأنظمة العداء الساخن المعزولة بشكل صحيح الحفاظ على درجات حرارة ذوبان ثابتة.
تصميم قناة التبريد: تمكّن قنوات التبريد المطابقة التي تتبع هندسة القِطع من استخراج الحرارة بشكل موحد، مما يمنع الالتواء الناتج عن التبريد غير المتساوي. في PTSMAKE، نستخدم أدوات محاكاة متقدمة لتحسين تخطيط التبريد قبل تصنيع القالب.
التنفيس: تعتبر التهوية الكافية مهمة بشكل خاص للبوليمرات ذات درجة الحرارة العالية، حيث أن الغازات المحتبسة يمكن أن تسبب عيوبًا تجميلية وأبعادًا. تسمح الفتحات الأرضية الدقيقة (عادةً بعمق 0.025-0.038 مم) بخروج الغازات دون حدوث وميض للمادة.
معلمات المعالجة للتحكم الدقيق
حتى مع الاختيار المثالي للمواد والتصميم المثالي للقالب، فإن معلمات المعالجة تحدد في النهاية دقة الجزء. يتطلب التشكيل في درجات الحرارة العالية أساليب متخصصة للمراحل الأربع الحرجة للقولبة بالحقن.
إدارة درجة الحرارة
ربما يكون التحكم في درجة الحرارة هو العامل الأكثر أهمية في التشكيل في درجات الحرارة العالية. وهذا يشمل:
- تحديد ملامح درجة حرارة البرميل: إنشاء التدرج الأمثل لدرجة الحرارة المثلى من منطقة التغذية إلى الفوهة
- التحكم في درجة حرارة القالب: الحفاظ على درجات حرارة ثابتة لسطح القالب، وغالبًا ما يتم ذلك باستخدام وحدات التحكم في درجة الحرارة المعتمدة على الزيت
- تجفيف المواد: ضمان إزالة الرطوبة بشكل كامل قبل المعالجة (غالبًا في درجات حرارة أعلى من 120 درجة مئوية لأكثر من 4 ساعات)
استراتيجيات التحكم في الضغط
تؤثر إدارة الضغط بشكل مباشر على أبعاد القِطع والضغط الداخلي:
- ضغط الحقن: يتم التحكم فيها بعناية لملء التجويف دون خلق ضغوط داخلية مفرطة
- الضغط القابضة: مُحسّنة لتعويض انكماش المواد دون الإفراط في التعبئة
- الضغط الخلفي: تمت إدارتها لضمان التجانس السليم للذوبان دون إطالة أزمنة الدورات
مراقبة الجودة للأجزاء عالية الدقة في درجات الحرارة العالية
يتطلب تحقيق الدقة تنفيذ بروتوكولات قوية لمراقبة الجودة مصممة خصيصًا للمكونات ذات درجات الحرارة العالية:
- المراقبة أثناء العملية: استخدام مستشعرات ضغط التجويف وأجهزة مراقبة درجة حرارة القالب للكشف عن التغيرات في الوقت الحقيقي
- مراقبة العمليات الإحصائية: تتبع الأبعاد الحرجة ومعلمات العملية لتحديد الاتجاهات قبل تجاوز حدود المواصفات
- الاختبارات البيئية: إخضاع الأجزاء لظروف استخدام محاكاة للتحقق من ثبات الأبعاد في ظل التدوير الحراري
- تقنيات القياس المتقدمة: استخدام أنظمة قياس عدم التلامس للأجزاء وهي لا تزال ساخنة لفهم التغيرات في الأبعاد أثناء التبريد
ومن خلال هذه الأساليب الشاملة لاختيار المواد وتصميم القوالب والمعالجة ومراقبة الجودة، يصبح تحقيق الدقة في المكونات المصبوبة بالحقن في درجات حرارة عالية أمرًا ممكنًا باستمرار. لقد قمنا في شركة PTSMAKE بتحسين هذه التقنيات من خلال سنوات من الخبرة، مما يساعد عملائنا على التغلب على التحديات الفريدة من نوعها في التشكيل الدقيق في درجات الحرارة العالية.
ما هي الصناعات الأكثر استفادة من القولبة بالحقن بدرجة حرارة عالية؟
هل تساءلت يومًا عن سبب قدرة بعض المنتجات على تحمل الحرارة الشديدة بينما تذوب منتجات أخرى؟ أو ربما واجهت صعوبة في إيجاد حلول تصنيع للمكونات التي تحتاج إلى الأداء في ظل ظروف قاسية؟ يؤثر التحدي المتمثل في إنشاء أجزاء تظل مستقرة في درجات الحرارة العالية على عدد لا يحصى من المشاريع الهندسية في مختلف القطاعات.
يفيد القولبة بالحقن في درجات الحرارة العالية الصناعات التي تتطلب مكونات مقاومة للحرارة، بما في ذلك صناعة السيارات والفضاء والطب والإلكترونيات والمعدات الصناعية. تعتمد هذه القطاعات على هذه العملية المتخصصة لإنشاء أجزاء تحافظ على السلامة الهيكلية والأداء في ظل الظروف الحرارية القاسية.
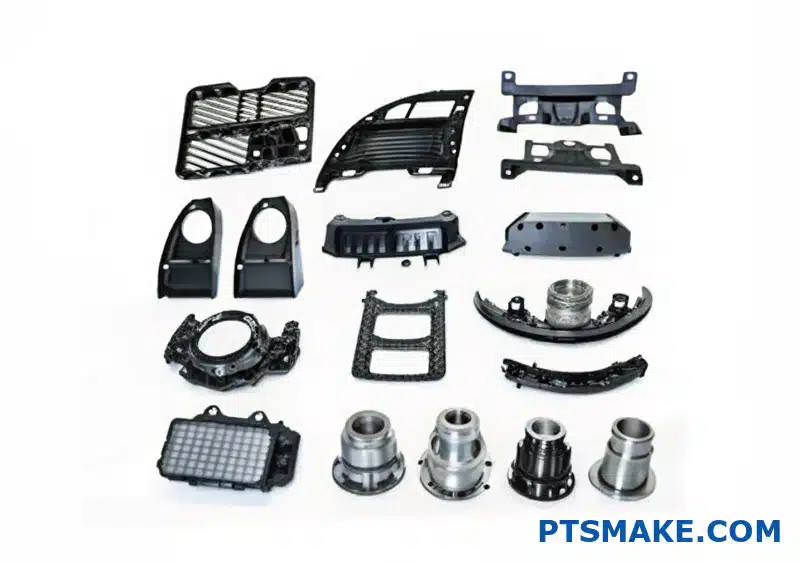
تطبيقات صناعة السيارات
تُعد صناعة السيارات أحد المستفيدين الرئيسيين من تقنية القولبة بالحقن في درجة حرارة عالية. حيث تعمل السيارات الحديثة بمحركات وأنظمة تولد حرارة عالية، مما يتطلب مكونات يمكنها تحمل هذه الظروف الصعبة دون تدهور.
تمثل المكونات الموجودة تحت غطاء المحرك مجال استخدام بالغ الأهمية. يجب أن تحافظ الأجزاء مثل مشعبات سحب الهواء وأغطية المحرك وخزانات سائل التبريد ومكونات نظام الوقود على ثبات الأبعاد والخصائص الميكانيكية في درجات حرارة قد تتجاوز 200 درجة مئوية. إن اعتماد اللدائن الحرارية الهندسية3 مثل PEEK وPPS وPEI من خلال القولبة في درجات حرارة عالية سمحت لمصنعي السيارات باستبدال المكونات المعدنية وتقليل الوزن مع الحفاظ على المقاومة الحرارية اللازمة.
تمثل السيارات الكهربائية تحديات وفرصًا جديدة للأجزاء المصبوبة في درجات حرارة عالية. تتطلب جميع أغطية البطاريات ومكونات العزل وعناصر نظام الشحن مواد يمكنها تحمل درجات الحرارة المرتفعة مع توفير خصائص العزل الكهربائي. في شركة PTSMAKE، شهدنا طلبًا متزايدًا على هذه المكونات المتخصصة مع توسع سوق السيارات الكهربائية.
فوائد الأداء في تطبيقات السيارات
نوع المكون | مقاومة درجات الحرارة | المزايا الرئيسية |
---|---|---|
مكونات المحرك | حتى 280 درجة مئوية | تقليل الوزن، ومقاومة التآكل، والأشكال الهندسية المعقدة |
الموصلات الكهربائية | 150-200°C | العزل الكهربائي ومثبطات اللهب وثبات الأبعاد |
قطع غيار ناقل الحركة | 180-240°C | مقاومة المواد الكيميائية وتقليل الضوضاء والاهتزاز والخشونة (الضوضاء والاهتزاز والخشونة) |
مكونات بطارية السيارة الكهربائية | 120-180°C | الإدارة الحرارية، والعزل الكهربائي، والسلامة الهيكلية |
صناعة الطيران والفضاء والدفاع
يتطلب قطاع الطيران مكونات يمكن أن تعمل بشكل موثوق في ظل الظروف القاسية. يتيح القولبة بالحقن بدرجة حرارة عالية إنتاج أجزاء خفيفة الوزن ومتينة في نفس الوقت يمكنها تحمل المتطلبات الصارمة لتطبيقات الطائرات والمركبات الفضائية.
تستفيد المكونات الداخلية مثل مشابك المقاعد وطاولات الصواني وأجزاء نظام التهوية من عمليات التشكيل في درجات الحرارة العالية. لا يجب أن تتحمل هذه الأجزاء درجات الحرارة التشغيلية العادية فحسب، بل يجب أن تفي أيضًا بمتطلبات القابلية الصارمة للاشتعال. توفر مواد مثل PEEK وPEI مثبطات لهب ممتازة مع الحفاظ على خصائصها الهيكلية في درجات الحرارة المرتفعة.
وتمثل مكونات المحركات والهياكل الخارجية للمحركات مجالاً آخر من مجالات الاستخدام الهامة. إن القدرة على إنشاء أشكال هندسية معقدة ذات تفاوتات دقيقة تجعل من القولبة بالحقن بدرجة حرارة عالية مثالية لإنتاج المكونات التي يجب أن تتحمل القرب من المحركات النفاثة، حيث يمكن أن تكون درجات الحرارة مرتفعة للغاية.
تطبيقات الفضاء الحرجة
تمثل التطبيقات العسكرية والدفاعية بعضًا من أكثر المتطلبات المطلوبة لمقاومة درجات الحرارة العالية. من علب الرادار إلى مكونات الصواريخ، غالبًا ما تعمل هذه التطبيقات في بيئات لا يكون فيها الفشل خيارًا. إن الدقة والاتساق اللذين يوفرهما القولبة بالحقن في درجة حرارة عالية تجعلها طريقة التصنيع المفضلة للعديد من المكونات الدفاعية المهمة.
تصنيع الأجهزة الطبية
تعتمد الصناعة الطبية بشكل متزايد على قولبة الحقن بدرجة حرارة عالية للأجهزة التي يجب أن تتحمل عمليات التعقيم. عادةً ما يحدث التعقيم بالأوتوكلاف في درجات حرارة تتراوح بين 121-134 درجة مئوية تحت الضغط، وهي ظروف من شأنها أن تشوه أو تتلف العديد من المواد البلاستيكية القياسية.
تستفيد الأدوات الجراحية، من المقابض إلى الأدوات المتخصصة، من مواد مثل PPSU وPSU وPEEK المعالجة من خلال صبها في درجة حرارة عالية. تحافظ هذه المواد على خصائصها من خلال مئات دورات التعقيم، مما يضمن الموثوقية والأداء على المدى الطويل.
ربما تمثل الأجهزة الطبية القابلة للزرع أكثر التطبيقات تطلبًا. يجب أن تكون المواد متوافقة حيويًا مع تحمل درجة حرارة الجسم والبيئات البيولوجية التي يحتمل أن تكون معادية لسنوات أو حتى عقود. توفر اللدائن الحرارية الهندسية ذات درجة الحرارة العالية المزيج الضروري من التوافق الحيوي والقوة والثبات على المدى الطويل.
صناعة الإلكترونيات وأشباه الموصلات
تواجه صناعة الإلكترونيات تحديات فريدة من نوعها مع المكونات التي تولد حرارة كبيرة أثناء التشغيل. يجب أن تحافظ الموصلات والأغلفة والمكونات العازلة على خواصها الكهربائية والميكانيكية على الرغم من تعرضها لدرجات حرارة عالية.
تخضع مكونات تقنية التركيب السطحي (SMT) لعملية إعادة لحام الإنحسار عند درجات حرارة تتجاوز عادةً 220 درجة مئوية. وتظل الأجزاء المصبوبة بالحقن ذات درجة الحرارة العالية ثابتة الأبعاد خلال هذه العملية، مما يضمن توصيلات كهربائية موثوقة.
جدول تطبيقات الإلكترونيات
التطبيق | متطلبات درجة الحرارة | خصائص المواد الرئيسية |
---|---|---|
مقابس IC | 260-280 درجة مئوية (لحام) | ثبات الأبعاد، والعزل الكهربائي |
علب الصمام الثنائي الباعث للضوء (LED) | 120-180 درجة مئوية (تشغيل) | الوضوح البصري، والإدارة الحرارية |
إلكترونيات الطاقة | 150-200°C | العزل الكهربائي، وتبديد الحرارة |
معالجة أشباه الموصلات | حتى 300 درجة مئوية | مقاومة للمواد الكيميائية، نقاوة عالية للغاية |
تصنيع المعدات الصناعية
غالبًا ما تعمل المعدات الصناعية في بيئات تتضافر فيها الحرارة والمواد الكيميائية والإجهاد الميكانيكي لخلق ظروف صعبة للغاية. تستفيد مكونات المضخات والصمامات ومعدات المعالجة بشكل كبير من القولبة بالحقن في درجات حرارة عالية.
تتطلب معدات صناعة المعالجة التي تتعامل مع السوائل أو الغازات الساخنة مكونات تحافظ على خصائص الإغلاق وثبات الأبعاد في درجات الحرارة المرتفعة. المواد مثل PEEK وPPS والبوليمرات الفلورية المعالجة من خلال صب درجات الحرارة العالية تخلق قطعًا يمكن أن تعمل بشكل موثوق في هذه التطبيقات الصعبة.
من خلال خبرتي في العمل مع العملاء الصناعيين في شركة PTSMAKE، وجدت أن القدرة على دمج مكونات متعددة في جزء واحد مصبوب غالبًا ما توفر مزايا كبيرة تتجاوز مجرد مقاومة درجات الحرارة، بما في ذلك تحسين الموثوقية وخفض تكاليف التجميع.
معالجة النفط والغاز والكيماويات
ربما لا يوجد قطاع صناعي يتطلب من المواد أكثر مما يتطلبه قطاع النفط والغاز والمعالجة الكيميائية. يجب أن تتحمل المكونات ليس فقط درجات الحرارة المرتفعة ولكن أيضًا التعرض للمواد الكيميائية العدوانية والضغوط العالية.
تعمل مكونات قاع البئر لاستخراج النفط والغاز في بيئات يمكن أن تتجاوز فيها درجات الحرارة 200 درجة مئوية أثناء تعرضها للنفط الخام والغاز الطبيعي وسوائل الحفر المختلفة. ينتج القولبة بالحقن في درجة حرارة عالية الأجزاء مع المزيج الضروري من مقاومة درجات الحرارة والتوافق الكيميائي والقوة الميكانيكية.
ما هي الحلول الفعالة من حيث التكلفة لمشاريع صب القوالب في درجات الحرارة العالية؟
هل سبق لك أن واجهت قيودًا على الميزانية أثناء محاولتك الحفاظ على الجودة في مشاريع التشكيل في درجات الحرارة العالية؟ هل تجد نفسك توازن باستمرار بين أداء المواد والتكلفة دون التضحية بالخصائص المهمة؟ يمكن أن تصبح هذه الموازنة صداعًا كبيرًا عندما تلوح المواعيد النهائية في الأفق وتضيق الميزانيات.
تشمل الحلول الفعالة من حيث التكلفة لمشاريع القوالب ذات درجات الحرارة العالية تحسين تصميم القوالب، واختيار بدائل المواد المناسبة، وتنفيذ أنظمة تبريد فعالة، والنظر في القوالب متعددة التجاويف، والشراكة مع الشركات المصنعة ذات الخبرة. تقلل هذه الاستراتيجيات من زمن الدورة، وتقلل من هدر المواد، وتقلل من تكاليف الإنتاج الإجمالية مع الحفاظ على الجودة.
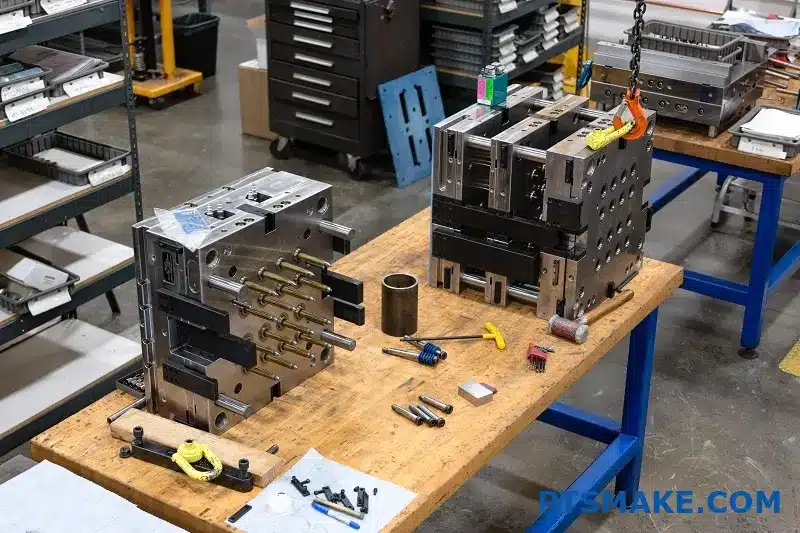
الاختيار الاستراتيجي للمواد من أجل تحسين التكلفة
عند إدارة مشروعات التشكيل في درجات الحرارة العالية، يمثل اختيار المواد أحد أهم عوامل التكلفة. وغالبًا ما تأتي البوليمرات الممتازة المقاومة لدرجات الحرارة العالية بعلامات سعرية ممتازة، ولكن هناك طرق استراتيجية لتحسين هذه النفقات.
البدائل المادية المستندة إلى القيمة
لا تتطلب كل استخدامات درجات الحرارة العالية مواد ذات أداء عالٍ للغاية. من خلال خبرتي في العمل مع العملاء في مختلف الصناعات، وجدت أن العديد من المهندسين يحددون في البداية مواد ذات مقاومة درجات حرارة مفرطة في حين أن البدائل الأقل تكلفة ستكون كافية. على سبيل المثال، على الرغم من أن نظرة خاطفة PEEK توفر مقاومة استثنائية لدرجات الحرارة حتى 480 درجة فهرنهايت (250 درجة مئوية)، إلا أن PPS المعدلة أو بعض النايلون عالي الحرارة يمكن أن تتعامل مع العديد من التطبيقات بتكلفة مواد أقل 30-40%.
المفتاح هو إجراء تحليل مناسب للتطبيق. فمن خلال التحديد الدقيق لدرجات الحرارة الفعلية والمدة والمتطلبات الميكانيكية للتعرض للحرارة الفعلية، يمكنك في كثير من الأحيان اختيار مواد أكثر اقتصادًا تلبي جميع معايير الأداء دون دفع تكاليف الخصائص غير الضرورية.
خيارات مزج المواد وتقويتها
وهناك نهج آخر فعال من حيث التكلفة ينطوي على استخدام البوليمرات الأساسية مع تعزيزات أو إضافات مستهدفة. على سبيل المثال، بدلًا من التحول إلى بوليمر مختلف تمامًا عالي التكلفة، يمكن أن تؤدي إضافة الألياف الزجاجية إلى بلاستيك هندسي قياسي إلى زيادة مقاومة الحرارة بشكل كبير بأقل تكلفة إضافية.
إن درجة حرارة الانحراف الحراري4 يمكن زيادتها بشكل كبير من خلال إجراء تعديلات استراتيجية على المواد، مما يوفر وفورات كبيرة في التكلفة مقارنةً بالانتقال إلى البوليمرات عالية الحرارة الممتازة.
تحسين تصميم القوالب للإنتاج الاقتصادي
ويمثل القالب نفسه فرصة رئيسية أخرى لتحسين التكلفة في صب القوالب ذات درجة الحرارة العالية.
تصميم للإدارة الحرارية
تؤثر الإدارة الحرارية الفعالة داخل القالب بشكل مباشر على أزمنة الدورات والجودة والتكلفة. يمكن أن يؤدي الوضع الاستراتيجي لقنوات التبريد، واستخدام تصميمات التبريد المطابق، والبوابات والعدّادات ذات الحجم المناسب إلى تقليل أزمنة الدورات بشكل كبير بالنسبة للمواد ذات درجات الحرارة العالية التي تتطلب عادةً فترات تبريد أطول.
في PTSMAKE، ننفذ ميزات إدارة حرارية متخصصة في قوالبنا ذات درجة الحرارة العالية، والتي قللت من أزمنة الدورات بما يصل إلى 25% في العديد من المشاريع مقارنةً بأساليب التبريد التقليدية.
اعتبارات العفن متعدد التجاويف والعفن العائلي
بالنسبة لأحجام الإنتاج المناسبة، توفر القوالب متعددة التجاويف مزايا كبيرة من حيث التكلفة لكل جزء:
نوع القالب | الاستثمار المبدئي | تخفيض التكلفة لكل جزء من الأجزاء | الأفضل لـ |
---|---|---|---|
تجويف واحد | $ | خط الأساس | نماذج أولية، بأحجام منخفضة |
2-4 تجويف 2-4 | $$ | 30-40% | أحجام متوسطة |
8+ تجويف 8+ | $$$ | 50-70% | أحجام كبيرة |
العفن العائلي | $$ | 25-35% | الأجزاء ذات الصلة، الأحجام المتوازنة |
على الرغم من أن القوالب متعددة التجاويف تتطلب استثمارًا أوليًا أعلى، إلا أن تكلفة الأدوات المطفأة لكل جزء تنخفض بشكل كبير، مما يجعلها ذات قيمة خاصة للمواد ذات درجة الحرارة العالية حيث تكون تكاليف المواد مرتفعة بالفعل.
تحسين العمليات من أجل كفاءة التكلفة
توفر عملية التشكيل نفسها العديد من الفرص لخفض التكلفة دون المساس بالجودة.
استراتيجيات تقليل وقت الدورة الزمنية
تتطلب المواد ذات درجات الحرارة العالية عادةً أوقات معالجة أطول، ولكن يمكن للعديد من الاستراتيجيات التخفيف من حدة ذلك:
- مراحل محسّنة للتسخين المسبق لتقليل وقت الدورة الإجمالي
- تنفيس فعال لتقليل الهواء المحبوس وتقليل زمن الدورة
- ملامح حقن مصممة خصيصًا للمواد ذات درجة الحرارة العالية
- أنظمة الإزالة الآلية للأجزاء لتقليل تكاليف العمالة وأوقات الدورات
في مشروع حديث للسيارات في PTSMAKE، أدى تنفيذ هذه الاستراتيجيات إلى تقليل وقت الدورة بمقدار 18% مع الحفاظ على جميع معايير الجودة الحرجة لمكون PPS عالي الحرارة.
تقنيات الحد من الخردة
البوليمرات ذات درجة الحرارة العالية باهظة الثمن، مما يجعل تقليل الخردة ذات قيمة خاصة. يمكن للمراقبة المتقدمة للعملية باستخدام أجهزة استشعار داخل القالب اكتشاف انحرافات العملية وتصحيحها قبل أن تتسبب في حدوث خردة. يساعد تنفيذ التحكم في العمليات الإحصائية في الحفاظ على معايير المعالجة المثلى باستمرار.
استراتيجيات شراكة الموردين
يمكن للعمل مع شريك التصنيع المناسب أن يؤثر بشكل كبير على تكاليف المشروع.
قيمة الخبرة المتخصصة
يقدم المصنعون ذوو الخبرة المحددة في التشكيل في درجات الحرارة العالية قيمة تتجاوز قدرات الإنتاج الأساسية. فعادةً ما تُترجم خبرتهم إلى أوقات إعداد أسرع، ومشاكل إنتاج أقل، ومعدلات إنتاجية أعلى في المرحلة الأولى - وكل ذلك يؤثر مباشرةً على تكاليف المشروع.
مراعاة التكلفة الإجمالية مقابل سعر الوحدة
عند تقييم شركاء التصنيع، ضع في اعتبارك صورة التكلفة الإجمالية بدلاً من التركيز فقط على عروض أسعار الوحدات. غالبًا ما يؤدي السعر الأعلى قليلاً لكل قطعة من أخصائي قولبة ذات خبرة في التشكيل في درجات الحرارة العالية إلى انخفاض التكاليف الإجمالية للمشروع بسبب:
- تقليل عدد مرات تكرار التطوير
- وقت أسرع للتسويق
- انخفاض معدلات الخردة
- عدد أقل من مشكلات الجودة التي تتطلب إعادة العمل
- جودة القطع الأكثر اتساقًا
بعد أكثر من 15 عامًا من العمل في مجال التصنيع الدقيق، رأيت مرارًا وتكرارًا مشاريع ذات أقل سعر مبدئي تكلف في نهاية المطاف أكثر بسبب هذه النفقات الخفية.
نُهج تحسين التكلفة على المدى الطويل
بالإضافة إلى الاحتياجات الفورية للمشروع، يمكن للعديد من الاستراتيجيات أن تخفض التكاليف على مدار دورة حياة المنتج.
تصميم أدوات معيارية وقابلة للتكيف
يتيح الاستثمار في تصميمات القوالب المعيارية مع إدخالات قابلة للاستبدال إجراء تعديلات على التصميم دون الحاجة إلى قوالب جديدة تمامًا. يوفر هذا النهج المرونة لتكرار المنتج مع احتواء تكاليف الأدوات على المدى الطويل.
فوائد التوحيد القياسي للمواد
عندما يكون ذلك ممكنًا، يمكن أن يوفر توحيد المواد عبر تطبيقات متعددة لدرجات الحرارة المرتفعة ميزة الشراء وتقليل تكاليف المخزون. حتى عندما يكون للمنتجات المختلفة متطلبات درجات حرارة مختلفة، فإن إيجاد فرص لتوحيد اختيارات المواد يمكن أن يحقق وفورات كبيرة من خلال الشراء بكميات كبيرة.
ما هي اعتبارات تصميم القوالب الضرورية للتطبيقات ذات درجات الحرارة العالية؟
هل سبق لك أن شاهدت مكوِّنًا بلاستيكيًا يتشوه أو يتشقق أو يفشل تمامًا عند استخدامه في إعدادات الحرارة العالية؟ أو هل عانيت مع القوالب التي تتشوه بعد بضع دورات إنتاج فقط مع مواد ذات درجة حرارة عالية؟ يمكن لهذه السيناريوهات المحبطة أن تعرقل المشاريع وتضر بعلاقاتك مع العملاء.
عند تصميم القوالب للتطبيقات ذات درجات الحرارة المرتفعة، تشمل الاعتبارات الحاسمة اختيار المواد (فولاذ الأدوات والبلاستيك على حد سواء)، وتصميم نظام التبريد المناسب، والتهوية المتقدمة، واختيار البوابات الدقيقة، والمعالجات السطحية المناسبة. تضمن هذه العناصر طول عمر القالب وجودة القِطع الثابتة.
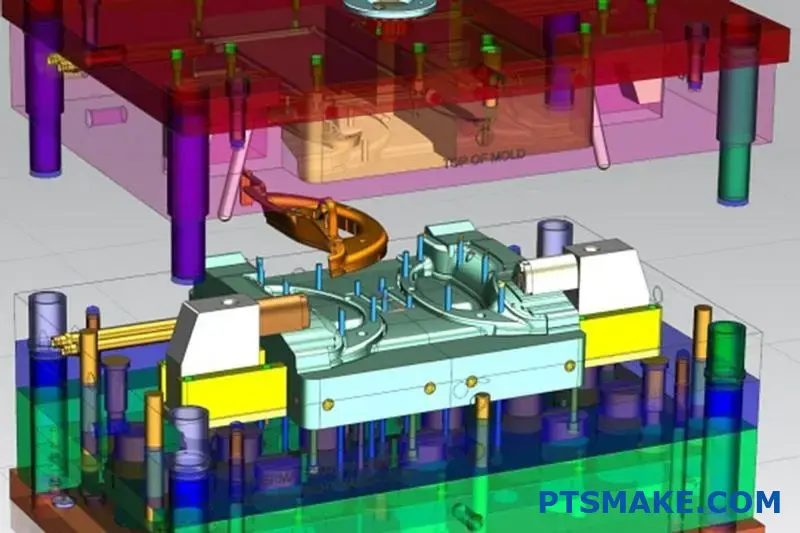
اختيار المواد للقوالب ذات درجة الحرارة العالية
ربما يكون اختيار المواد المناسبة لتطبيقات القوالب ذات درجة الحرارة العالية هو القرار الأساسي الذي ستتخذه. من خلال تجربتي في توجيه العديد من العملاء خلال هذه العملية في PTSMAKE، وجدت أن كلاً من الفولاذ القالب والمواد البلاستيكية تتطلب دراسة متأنية.
اختيار الأدوات الفولاذية
بالنسبة للتطبيقات ذات درجات الحرارة العالية، لا يتساوى أداء جميع أنواع الفولاذ المستخدم في درجات الحرارة العالية. توفر الدرجات الممتازة مثل H13 وP20 وS7 مقاومة ممتازة للإجهاد الحراري، وهي مشكلة شائعة عندما تتعرض القوالب بشكل متكرر لتقلبات شديدة في درجات الحرارة.
لا يزال فولاذ الأدوات H13 هو الفولاذ الذي أوصي به لمعظم الاستخدامات ذات درجات الحرارة العالية نظرًا لامتيازه مقاومة الإجهاد الحراري5 وخصائص الصلابة الساخنة. عند العمل مع المواد التي تتطلب درجات حرارة معالجة أعلى من 300 درجة مئوية (572 درجة فهرنهايت)، نستخدم عادةً H13 المقوى إلى 48-52 HRC لمنع التآكل والتشوه المبكر.
بالنسبة للتطبيقات شديدة الصعوبة، يمكن للفولاذ المتخصص الذي يحتوي على نسب أعلى من التنجستن والموليبدينوم والفاناديوم أن يوفر أداءً محسنًا، على الرغم من أنه يأتي مع تكاليف تصنيع أعلى.
اعتبارات المواد البلاستيكية
تؤثر المادة البلاستيكية نفسها بشكل كبير على قرارات تصميم القالب. تتطلب المواد البلاستيكية الحرارية الهندسية عالية الحرارة مثل PEEK وPPS وPEI (Ultem) وLCP (بوليمر البلورات السائلة) أساليب تصميم قوالب محددة. عادةً ما يكون لهذه المواد:
- درجات حرارة معالجة أعلى (غالبًا 320-420 درجة مئوية)
- معدلات انكماش أكبر
- زيادة الحساسية لتغيرات التبريد
- خصائص تدفق أكثر عدوانية
يتطلب العمل مع هذه المواد بوابات دقيقة، وأنظمة عداءة، وتصميم قناة تبريد لتجنب العيوب مثل الاعوجاج، وعلامات الحوض، والوميض.
تصميم نظام تبريد متقدم
تصبح فعالية نظام التبريد أكثر أهمية بشكل كبير في التطبيقات ذات درجات الحرارة العالية. يساعد التبريد المنتظم في الحفاظ على ثبات الأبعاد وتقليل أزمنة الدورات.
قنوات التبريد المطابقة
غالبًا ما تكون قنوات التبريد التقليدية المحفورة بشكل مستقيم غير كافية للأجزاء المعقدة ذات درجة الحرارة العالية. في شركة PTSMAKE، قمنا بشكل متزايد بتطبيق تقنيات التبريد المطابق التي تتبع هندسة القِطع بشكل أوثق. يمكن لهذه التصميمات المتقدمة أن:
- تقليل أزمنة الدورات بمقدار 20-40%
- تحسين جودة القِطع من خلال تقليل الالتواء إلى الحد الأدنى
- إطالة عمر القالب عن طريق تقليل الإجهاد الحراري
على الرغم من أن التبريد المطابق أكثر تكلفة في البداية، إلا أنه غالبًا ما يوفر عائدًا كبيرًا على الاستثمار من خلال تحسين الإنتاجية والجودة، خاصةً للإنتاج بكميات كبيرة.
وسائط التبريد بدرجة حرارة عالية
قد يكون التبريد بالماء القياسي غير كافٍ للتطبيقات ذات درجات الحرارة العالية جدًا. وتشمل وسائط التبريد البديلة التي يجب أخذها في الاعتبار ما يلي:
وسيط التبريد | نطاق درجة الحرارة | المزايا | القيود |
---|---|---|---|
المياه المضغوطة | حتى 180 درجة مئوية | فعالة من حيث التكلفة وممتازة في نقل الحرارة | تتطلب أنظمة التحكم في الضغط |
المبردات ذات الأساس الزيتي | حتى 350 درجة مئوية | ثبات في درجات الحرارة العالية | كفاءة أقل في نقل الحرارة، تكلفة أعلى |
الملح المنصهر | 150-550°C | أداء استثنائي في درجات الحرارة العالية | المعدات المتخصصة المطلوبة، ومخاوف التآكل |
بالنسبة للتطبيقات القصوى، يمكن أن توفر أنظمة التبريد المتتالية التي تجمع بين مناطق تبريد مختلفة إدارة حرارية مثالية.
اعتبارات التنفيس
تعتبر التنفيس الكافي أمرًا بالغ الأهمية في التطبيقات ذات درجات الحرارة العالية لأن الغازات تتمدد أكثر في درجات الحرارة المرتفعة ويمكن أن تسبب احتراقًا أو تعبئة غير كاملة أو حتى تراكم ضغط خطير.
أوصي عادةً بأعماق تنفيس تتراوح بين 0.025-0.038 مم للبلاستيك الهندسي عالي الحرارة، مع قنوات تنفيس أوسع من تلك المستخدمة في البلاستيك التقليدي. يساعد وضع الفتحات الاستراتيجية في آخر نقاط التعبئة، خاصةً في المقاطع رقيقة الجدران، على منع احتباس الغاز.
بالنسبة لمواد مثل PPS أو PEEK التي تطلق غازات أكالة أثناء المعالجة، قد تكون مواد التنفيس أو الطلاءات المتخصصة ضرورية لمنع التآكل المبكر.
أنظمة البوابات والعداءات
يصبح تصميم نظام البوابة والعداء أكثر أهمية مع المواد ذات درجات الحرارة العالية التي لها نوافذ معالجة ضيقة.
اختيار نوع البوابة
بالنسبة للتطبيقات ذات درجات الحرارة العالية، أوصي عادةً بما يلي:
- بوابات الأنفاق للأجزاء الصغيرة إلى المتوسطة التي تتطلب إزالة القوالب الأوتوماتيكية
- بوابات الحواف للأجزاء الكبيرة التي تتطلب أقصى قدر من الثبات في الأبعاد
- أنظمة التشغيل على الساخن للإنتاج بكميات كبيرة للقضاء على مخاوف إعادة الطحن
يجب معايرة حجم البوابة بعناية - صغيرة جدًا وقد تتجمد المادة قبل الأوان؛ كبيرة جدًا وقد ينتج عن ذلك بقايا بوابة مفرطة أو تشذيب صعب.
اعتبارات تصميم العداء
تستفيد المواد ذات درجات الحرارة العالية من:
- عدائين دائريين كاملين بأسطح مصقولة
- آبار باردة ذات أحجام مناسبة لالتقاط أول مادة تدخل القالب
- أنظمة عداء متوازنة لضمان أنماط تعبئة موحدة
تساعد عناصر التصميم هذه في الحفاظ على ثبات درجة حرارة المواد طوال عملية التعبئة.
المعالجات السطحية والطلاءات
غالبًا ما تستفيد التطبيقات ذات درجات الحرارة العالية من المعالجات السطحية المتخصصة التي تطيل عمر القالب وتحسن جودة القِطع.
يمكن أن تزيد المعالجات مثل الطلاء بالنترة من صلابة السطح مع الحفاظ على صلابة القلب، مما يساعد القالب على تحمل التدوير الحراري. يمكن لطلاءات PVD (الترسيب الفيزيائي للبخار) المتقدمة مثل نيتريد التيتانيوم (TiN) أو نيتريد الكروم (CrN):
- تحسين مقاومة التآكل
- تقليل التصاق المواد
- تعزيز خصائص تحرير العفن
- تحسين مقاومة التآكل
في PTSMAKE، شهدنا إطالة عمر القالب 30-50% من خلال التطبيق الاستراتيجي لهذه المعالجات السطحية في التطبيقات ذات درجات الحرارة العالية.
6. الأساليب المتقدمة والاتجاهات المستقبلية في منع الالتواء؟
هل سبق لك أن قضيت أسابيع في ضبط معلمات القولبة بالحقن في درجة حرارة عالية، فقط لتظل تعاني من مشاكل الاعوجاج المستمرة؟ أو استثمرت في مواد ممتازة ومعدات متطورة ولكنك لا تزال غير قادر على تحقيق ثبات الأبعاد الذي يطلبه عملاؤك؟
لإتقان الوقاية من الاعوجاج في قولبة الحقن بدرجة حرارة عالية، تحتاج إلى النظر إلى ما هو أبعد من الاستراتيجيات الأساسية نحو التقنيات المتقدمة والتقنيات الناشئة. تشمل هذه الأساليب المبتكرة التحسين القائم على المحاكاة والتبريد المطابق المتقدم وحلول الأدوات المركبة والتحكم في العملية بمساعدة الذكاء الاصطناعي - تعمل جميعها معًا لتقليل الضغوط الحرارية والحفاظ على ثبات الأبعاد.
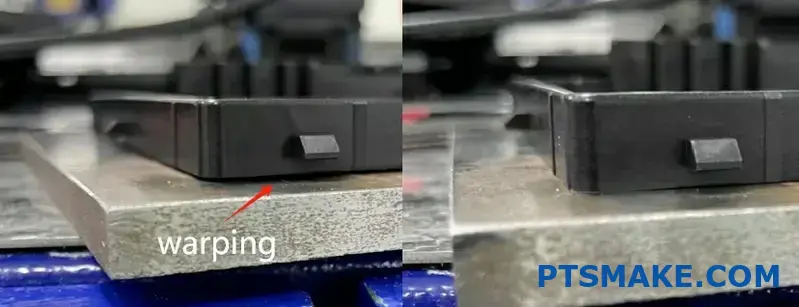
6.1 مناهج التحسين القائم على المحاكاة
6.1.1 تحليل CAE المتقدم للتنبؤ بالالتواء
لقد أحدثت الهندسة بمساعدة الحاسوب ثورة في كيفية التعامل مع الاعوجاج في قولبة الحقن بدرجة حرارة عالية. يمكن لبرامج المحاكاة الحديثة الآن التنبؤ بالاعوجاج بدقة ملحوظة من خلال دمج نماذج واقعية لسلوك المواد وظروف العملية والديناميكيات الحرارية.
عندما أقوم بتنفيذ مناهج تعتمد على المحاكاة في PTSMAKE، فإننا عادةً ما نتبع سير عمل منهجي:
- إنشاء نماذج ثلاثية الأبعاد مفصلة لكل من الجزء والقالب
- تحديد خصائص المواد الدقيقة (بما في ذلك حركية التبلور)
- إعداد شروط وقيود عملية واقعية
- إجراء محاكاة شاملة للالتواء
- تحليل أنماط التبريد والإجهادات المتبقية
- تحسين التصميم بناءً على نتائج المحاكاة
الميزة الرئيسية هنا هي اكتشاف مشاكل الاعوجاج المحتملة قبل قطع أي فولاذ. بالنسبة للتطبيقات ذات درجات الحرارة العالية، نولي اهتمامًا خاصًا لما يلي انكماش متباين الخواص6 الأنماط التي غالبًا ما يتم تجاهلها في عمليات المحاكاة الأساسية ولكن يمكن أن تؤثر بشكل كبير على هندسة الجزء النهائي.
6.1.2 التصميم الافتراضي للتجارب (DOE)
يمثل الاختبار التشغيلي الافتراضي نهجًا قويًا يسمح باختبار متغيرات متعددة في وقت واحد دون استهلاك موارد مادية. وباستخدام هذه التقنية، يمكننا تقييم كيفية تفاعل العوامل المختلفة للتأثير على الالتواء.
في مشروع فضاء جوي حديث يتضمن مكونات PEEK، استخدمنا نظام التشغيل الافتراضي DOE لتحسينه:
- مواقع البوابات وأبعادها
- تصميم نظام العداء
- تكوينات تخطيط التبريد
- تركيبات معلمات المعالجة
سمح لنا هذا النهج بتحديد تركيبات المعلمات غير البديهية التي تقلل من الاعوجاج بكفاءة أكبر بكثير من طرق التجربة والخطأ التقليدية. تنبأت المحاكاة بتخفيض الاعوجاج بمقدار 37%، وعند التنفيذ، حققنا تحسنًا فعليًا بمقدار 32% - مما يدل على قوة هذه التقنية.
6.2 حلول التبريد المتقدمة
6.2.1 ابتكارات التبريد المطابق
يمثّل التبريد المطابق أحد أهم التطورات في معالجة الالتواء في القوالب عالية الحرارة. على عكس قنوات التبريد التقليدية التي تتبع مسارات الحفر المستقيمة، تعكس قنوات التبريد المطابقة هندسة الجزء، مما يوفر تبريدًا موحدًا.
وتظهر فوائد التطبيقات ذات درجات الحرارة العالية بشكل خاص:
- تقليل أزمنة الدورات بما يصل إلى 40%
- أنماط تبريد أكثر اتساقًا
- الحد من البقع الساخنة التي تساهم في الالتواء
- جودة تشطيب أفضل للأسطح
في شركة PTSMAKE، قمنا بتنفيذ حلول التبريد المطابق باستخدام كل من إدخالات القوالب المفرغة من الهواء والتلبيد المباشر بالليزر المعدني (DMLS) للأشكال الهندسية المعقدة. في حين أن الاستثمار الأولي أعلى، إلا أن الفوائد طويلة الأجل في جودة الأجزاء وتقليل زمن الدورة توفر عائد استثمار استثنائي للمكونات عالية القيمة.
6.2.2.2 تقنيات التبريد الناشئة
بالإضافة إلى التبريد المطابق التقليدي، هناك العديد من التقنيات الناشئة الواعدة:
أنظمة تبريد القنوات الدقيقة: تسمح هذه القنوات فائقة الصغر (غالباً ما يكون قطرها أقل من 1 مم) بالتبريد في المناطق التي كان يتعذر الوصول إليها سابقاً، مما يوفر تحكماً دقيقاً للغاية في درجة الحرارة في الميزات الحرجة.
إدخالات توصيل متغيرة: وضع استراتيجي لمواد عالية التوصيل الحراري في مناطق محددة من القوالب للتحكم في معدلات استخلاص الحرارة.
تبريد بالتبديل المرحلي: الاستفادة من المواد التي تمتص الحرارة من خلال التحول الطوري، مما يوفر قدرة تبريد معززة أثناء مراحل التصلب الحرجة.
تُعد هذه التقنيات ذات قيمة خاصة عند قولبة البوليمرات الهندسية عالية الحرارة مثل PEEK أو PEI أو PPS، حيث تكون الإدارة الحرارية أمرًا بالغ الأهمية لمنع الالتواء.
6.3 أنظمة التحكم الذكي في العمليات
6.3.1 المعالجة التكيفية مع التعلم الآلي
يمثل دمج الذكاء الاصطناعي في التحكم في عملية القولبة بالحقن قفزة كبيرة إلى الأمام في منع الاعوجاج. يمكن للأنظمة الحديثة الآن:
- مراقبة معلمات عملية متعددة في الوقت الفعلي
- الكشف عن الانحرافات التي قد تؤدي إلى الاعوجاج
- إجراء تعديلات تلقائية للحفاظ على الظروف المثلى
- التعلّم من كل دورة إنتاج للتحسين المستمر
لقد قمنا في مصنعنا بتطبيق أنظمة معالجة تكيفية تقوم بضبط ضغط التعبئة ووقت التبريد ودرجة حرارة الذوبان بناءً على البيانات في الوقت الفعلي. لقد كان هذا النهج فعالاً بشكل خاص في عمليات الإنتاج الطويلة للأجزاء المعقدة ذات درجة الحرارة العالية حيث يتسبب انحراف العملية عادةً في حدوث اختلافات في الجودة.
6.3.2 تقنيات الاستشعار داخل القالب
توفر المستشعرات المتقدمة المدمجة داخل القالب رؤية غير مسبوقة لما يحدث أثناء دورة التشكيل:
نوع المستشعر | ما الذي يقيسه | فائدة منع التشوه |
---|---|---|
مستشعرات الضغط | ملامح ضغط التجويف | يضمن التعبئة المتسقة عبر الدورات |
مستشعرات درجة الحرارة | درجة حرارة القالب والصهر | تحديد حالات التبريد الشاذة التي تؤدي إلى انكماش غير متساوٍ |
مقاييس الإجهاد | انحراف القالب | يكتشف المشكلات المحتملة في توزيع الضغط غير المنتظم |
أجهزة الاستشعار بالموجات فوق الصوتية | معدل تصلب المواد | يحسن وقت التبريد بناءً على التصلب الفعلي |
من خلال دمج هذه الحساسات مع أنظمة التحكم في العمليات، يمكننا تطوير أساليب تحكم ذات حلقة مغلقة تقلل بشكل كبير من تباين الاعوجاج، حتى في التطبيقات الصعبة ذات درجات الحرارة العالية.
6.4 ابتكارات المواد للحد من الاعوجاج
يستمر مشهد البوليمرات ذات درجات الحرارة العالية في التطور، مع تركيبات جديدة مصممة خصيصًا لمواجهة تحديات الاعوجاج:
6.4.1 التحكم في توجيه الألياف
تركز التطورات الجديدة في البوليمرات المقواة بالألياف على التحكم في اتجاه الألياف أثناء التدفق لتقليل الانكماش التفاضلي. ويشمل ذلك:
- أنظمة الألياف الهجينة التي تجمع بين أنواع مختلفة من الألياف
- التوزيعات المثلى لأطوال الألياف
- المعالجات السطحية التي تحسن من الترابط بين الألياف والمصفوفة
- المواد المضافة المتخصصة التي تؤثر على اتجاه الألياف أثناء التعبئة
لقد لاحظت تحسنًا ملحوظًا عند استخدام هذه المواد في التطبيقات الهيكلية ذات الجدران الرقيقة حيث كان الاعوجاج يبدو حتميًا في السابق.
6.4.2 البوليمرات المعدلة التبلور
بالنسبة للبوليمرات شبه البلورية ذات درجة الحرارة العالية، يعد التحكم في حركية التبلور أمرًا بالغ الأهمية لإدارة الاعوجاج. تشمل الابتكارات الحديثة ما يلي:
- عوامل التنوي التي تعزز التبلور المنتظم
- مُعدِّلات نمو البلورات التي تتحكم في حجم الكرية
- خلطات البوليمر ذات خصائص التبلور التكميلية
- إضافات تغيير الطور التي تمتص الحرارة أثناء التبلور
يمكن لهذه التركيبات المتخصصة أن تقلل بشكل كبير من حساسية المعالجة وتحسن من ثبات الأبعاد، حتى عندما لا يتم التحكم في ظروف المعالجة بشكل مثالي.
6.5 الاتجاهات المستقبلية في منع الاعوجاج
واستشرافًا للمستقبل، هناك العديد من الاتجاهات الناشئة التي تعد بإحداث ثورة في كيفية منع الاعوجاج في التشكيل في درجات الحرارة العالية:
تقنية التوأم الرقمي: إنشاء تمثيلات افتراضية لكل من العملية والقالب يتم تحديثها في الوقت الفعلي، مما يسمح بالصيانة التنبؤية وتحسين العملية.
خوارزميات التصميم التوليدي: أنظمة تصميم مدعومة بالذكاء الاصطناعي يمكنها توليد تصميمات محسنة للقطع والقوالب تلقائيًا مع مقاومة متأصلة للالتواء.
مناهج التصنيع الهجين: الجمع بين القولبة بالحقن والتصنيع الإضافي أو غيرها من العمليات لتحقيق الخصائص الهندسية وخصائص الأداء التي كان من المستحيل تحقيقها في السابق.
تصاميم تبريد مستوحاة من البيئة الحيوية: تصميمات هندسية لقنوات التبريد مبنية على الهياكل الطبيعية مثل عروق الأوراق أو الأوعية الدموية التي توفر كفاءة نقل الحرارة المحسنة.
في شركة PTSMAKE، نبحث بنشاط في هذه التقنيات للبقاء في طليعة قدرات التشكيل الدقيق في درجات الحرارة العالية للتطبيقات الأكثر تطلبًا.
كيف يمكن تقليل زمن الدورة في صب القوالب بالحقن بدرجة حرارة عالية؟
هل سبق لك أن عانيت من دورات الإنتاج البطيئة في عمليات التشكيل في درجات الحرارة العالية؟ تلك الاختناقات المحبطة التي تستنزف مواردك، وتؤخر عمليات التسليم، وتؤثر في النهاية على أرباحك النهائية؟ إنه تحدٍ يمكن أن يجعل جدول الإنتاج بطيئًا أو ينهيه.
يتطلب تقليل أزمنة الدورات في صب القوالب بالحقن في درجة حرارة عالية تحسين استراتيجيات التبريد، واختيار المواد، ومعلمات العملية، وصيانة المعدات. من خلال تطبيق تقنيات مثل قنوات التبريد المطابقة ومواقع البوابات المحسّنة والتحكم المتقدم في درجة حرارة القالب، يمكن للمصنعين تقليل زمن الدورة بشكل كبير مع الحفاظ على جودة القِطع.

فهم استراتيجيات تحسين التبريد
عادةً ما يمثل وقت التبريد أكثر من 60% من إجمالي وقت الدورة في قولبة الحقن بدرجة حرارة عالية. عند العمل مع مواد ذات درجة حرارة عالية مثل PEEK أو PPS أو LCP، يصبح التبريد أكثر أهمية. لقد وجدت أن تنفيذ تحسين التبريد الاستراتيجي يمكن أن يقلل بشكل كبير من أزمنة الدورات.
قنوات التبريد المطابقة
غالبًا ما تخلق قنوات التبريد التقليدية المثقوبة بشكل مستقيم ظروف تبريد غير متساوية. توفر قنوات التبريد المطابقة، التي تتبع محيط الجزء، استخلاصًا أكثر اتساقًا للحرارة. من خلال تجربتي في PTSMAKE، أدى التحول إلى التبريد المطابق للقطع المعقدة ذات درجة الحرارة العالية إلى تقليل زمن التبريد بمقدار 20-30%.
الميزة الرئيسية هي توحيد درجة الحرارة عبر سطح الجزء. وهذا لا يسرّع التبريد فحسب، بل يحسّن أيضًا من جودة القِطع من خلال تقليل الالتواء والإجهاد الداخلي. في حين أن التكلفة الأولية للقالب أعلى، فإن تقليل وقت الدورة على المدى الطويل يبرر الاستثمار في الإنتاج بكميات كبيرة.
مواقع البوابات الاستراتيجية
يؤثر موقع البوابة بشكل كبير على كل من أنماط التعبئة وكفاءة التبريد. بالنسبة للمواد ذات درجات الحرارة المرتفعة، أوصي بوضع البوابات في أقسام أكثر سمكًا حيث يكون احتباس الحرارة أعلى. يسمح هذا النهج بتبريد أكثر كفاءة ويساعد على تجنب معدلات التبريد التفاضلي7 التي يمكن أن تسبب الاعوجاج.
قد تكون البوابات المتعددة ضرورية في الأشكال الهندسية المعقدة، ولكن يلزم إجراء تحليل دقيق لتجنب خطوط اللحام في المناطق الحرجة. في شركة PTSMAKE، نستخدم عادةً برنامج محاكاة التدفق لتحسين مواقع البوابات قبل قطع أي فولاذ، مما يوفر الوقت والموارد أثناء الإنتاج.
اختيار المواد وإعدادها
يؤثر اختيار المواد بشكل كبير على أزمنة الدورات في تطبيقات درجات الحرارة العالية. وتشمل بعض الاعتبارات الرئيسية ما يلي:
متغيرات التدفق العالي
توفر العديد من البوليمرات عالية الحرارة أنواعًا مختلفة عالية التدفق تحافظ على الخصائص الحرارية الضرورية مع الحاجة إلى درجات حرارة وضغوط حقن أقل. يمكن أن تقلل هذه التركيبات من أزمنة الدورات من خلال السماح بحقن أسرع وفترات تبريد أقصر.
التجفيف المناسب للمواد
يؤدي التجفيف غير الكافي للبوليمرات المسترطبة ذات درجة الحرارة العالية إلى زيادة اللزوجة، مما يتطلب درجات حرارة معالجة أعلى وأزمنة دورة أطول. أضمن دائمًا تجفيف مواد مثل PEEK وPEI وفقًا لمواصفات الشركة المصنعة - عادةً 3-4 ساعات عند درجة حرارة 150 درجة مئوية أو أعلى.
مقارنة بين البوليمرات عالية الحرارة الشائعة وتأثيرها على أزمنة الدورات:
المواد | درجة حرارة المعالجة | زمن الدورة النسبية | خصائص التدفق |
---|---|---|---|
معيار PEEK | 360-400°C | أطول | تدفق معتدل |
نظرة خاطفة عالية التدفق | 340-380°C | 15-20% أقصر 15-20% | التدفق المعزز |
PPS | 310-330°C | معتدل | تدفق جيد |
نظام الملوثات العضوية الثابتة عالي التدفق | 290-320°C | 10-15% أقصر 10-15% | تدفق ممتاز |
LCP | 330-350°C | أقصر | تدفق عالٍ جداً |
تحسين معلمة العملية المتقدمة
يعد ضبط معلمات المعالجة بدقة أمرًا بالغ الأهمية لتقليل أزمنة الدورات دون المساس بجودة القِطع.
ملفات تعريف التعبئة الديناميكية
لقد وجدت أن تنفيذ ملفات تعريف التعبئة متعددة المراحل يمكن أن يقلل بشكل كبير من وقت الدورة الكلي. من خلال البدء بضغط تعبئة أعلى ثم خفضه تدريجيًا مع تجمد البوابة، يمكننا تحسين مرحلة التعبئة دون تمديد الدورة الكلية.
في شركة PTSMAKE، نقوم بشكل روتيني بإجراء دراسات ختم البوابة لتحديد اللحظة الدقيقة التي يتوقف فيها الضغط على الجزء، مما يسمح لنا بتقليل مرحلة التعبئة إلى الحد الأدنى الضروري فقط.
التحكم في درجة حرارة القالب
بالنسبة للمواد ذات درجات الحرارة العالية، فإن الحفاظ على درجة حرارة القالب المناسبة أمر بالغ الأهمية. يساعد استخدام أنظمة المياه المضغوطة التي تعمل عند درجة حرارة 120-140 درجة مئوية أو الأنظمة القائمة على الزيت لدرجات حرارة أعلى على تحقيق دورات أسرع من خلال:
- تقليل اللزوجة أثناء التعبئة
- السماح بتعبئة أكثر اتساقًا
- تمكين التبريد السريع والمضبوط
إن الاستثمار في وحدات التحكم في درجة الحرارة المتقدمة يؤتي ثماره من خلال تقليل زمن الدورة وتحسين اتساق القِطع.
اعتبارات المعدات والصيانة
حتى مع وجود معلمات المعالجة المثلى، يمكن أن تؤدي المعدات القديمة أو سيئة الصيانة إلى إفساد جهود تقليل زمن الدورة.
وحدات الحقن عالية الأداء
تسمح الماكينات الحديثة ذات معدلات الحقن الأعلى والتحكم الدقيق بتعبئة أسرع مع الحفاظ على الجودة. بالنسبة للتطبيقات ذات درجات الحرارة العالية، أوصي بالماكينات المزودة بما يلي:
- براميل وبراغي متخصصة في درجات الحرارة العالية
- قدرة تدفئة معززة
- أنظمة دقيقة للتحكم في درجة الحرارة
- سرعات وضغوط حقن أعلى
جدول الصيانة الوقائية
تمنع الصيانة الدورية التعطل غير المتوقع وتضمن الأداء الأمثل للماكينة. في PTSMAKE، ننفذ في شركة PTSMAKE جداول صيانة شاملة بما في ذلك:
- فحص أسبوعي لعناصر التسخين
- المعايرة الشهرية لمستشعرات درجة الحرارة
- الفحص ربع السنوي للأنظمة الهيدروليكية
- التفكيك والتنظيف نصف السنوي للبراغي والبراميل
وقد أثبت هذا النهج الاستباقي أنه يحافظ على ثبات أوقات الدورات مع منع الأعطال الكارثية التي يمكن أن تعرقل جداول الإنتاج.
تكامل الأتمتة والروبوتات
يمكن أن يؤدي استخدام الروبوتات لإزالة القِطع وعمليات ما بعد التشكيل إلى تقليل أزمنة الدورات الإجمالية بشكل كبير. يمكن للروبوتات الحديثة سداسية المحاور إزالة القِطع وإجراء عمليات ثانوية بينما يستعد القالب للدورة التالية.
يضمن تكامل أدوات نهاية الذراع المصممة خصيصًا للقطع ذات درجة الحرارة العالية مناولة آمنة دون تلف أو تشوه، مما يقلل من معدلات الخردة ويحسن الكفاءة الكلية.
ما معايير مراقبة الجودة المطبقة على المكونات المصبوبة في درجات حرارة عالية؟
هل سبق لك أن استلمت أجزاء مصبوبة بدرجة حرارة عالية تشوهت أو تدهورت أو تعطلت أثناء الاستخدام؟ أو قضيت ساعات لا حصر لها في استكشاف مشكلات الجودة وإصلاحها والتي كان من الممكن منعها باستخدام المعايير المناسبة؟ عندما تكون الدقة والموثوقية غير قابلة للتفاوض، تصبح مراقبة الجودة شريان الحياة بالنسبة لك.
تشمل معايير مراقبة الجودة للمكونات المقولبة في درجات الحرارة العالية في المقام الأول ASTM D3641 للاستقرار الحراري، وISO 9001 لأنظمة إدارة الجودة، والمتطلبات الخاصة بالصناعة مثل UL 746A للتطبيقات الكهربائية. تضمن هذه المعايير الحفاظ على ثبات أبعاد المكونات وسلامة المواد والأداء الوظيفي في درجات الحرارة المرتفعة.
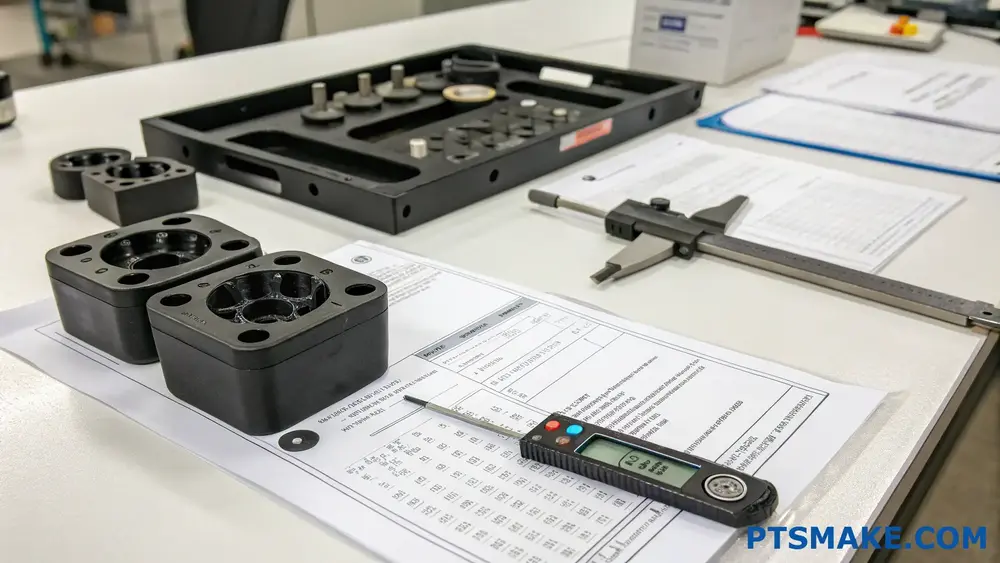
الطبيعة الحرجة لمراقبة الجودة للمكونات ذات درجة الحرارة العالية
تواجه المكونات المصبوبة في درجات حرارة عالية تحديات استثنائية مقارنةً بالأجزاء البلاستيكية القياسية. فمع بيئات التشغيل التي غالبًا ما تتجاوز 150 درجة مئوية (302 درجة فهرنهايت)، يجب أن تحافظ هذه المكونات المتخصصة على سلامتها الهيكلية وثبات أبعادها وخصائص أدائها في ظل الظروف القاسية. بعد العمل مع العديد من العملاء في مجال الطيران والسيارات، وجدتُ أن مراقبة الجودة المناسبة لا تتعلق فقط بتلبية المواصفات - بل تتعلق بضمان السلامة والموثوقية وطول العمر في التطبيقات الصعبة.
تكون المخاطر ببساطة أعلى مع المكونات ذات درجة الحرارة العالية. يمكن أن تؤدي مشكلة جودة بسيطة قد تكون مقبولة في منتج استهلاكي إلى فشل كارثي في مكون محرك سيارات عالي الحرارة أو في تطبيق فضائي. هذا هو السبب في أن معايير مراقبة الجودة القوية ليست اختيارية، بل هي ضرورية.
معايير الصناعة والشهادات
معايير ASTM
توفر الجمعية الأمريكية للاختبار والمواد (ASTM) العديد من المعايير الهامة التي تنطبق تحديدًا على المكونات المصبوبة في درجة حرارة عالية:
- ASTM D3641: الممارسة القياسية لعينات اختبار حقن القوالب بالحقن لمواد التشكيل بالحرارة والبثق
- ASTM D648: طريقة الاختبار القياسية لدرجة حرارة انحراف اللدائن تحت الحمل المرن
- ASTM D1525: طريقة الاختبار القياسية لدرجة حرارة تليين البلاستيك فيكات
وتوفر هذه المعايير منهجيات اختبار محددة للتحقق من خصائص المواد تحت الإجهاد الحراري. في شركة PTSMAKE، ننفذ هذه البروتوكولات بانتظام للتحقق من صحة درجة حرارة الانحراف الحراري8 والاستقرار الحراري للمكونات التي ننتجها.
معايير الأيزو
وتوفر المنظمة الدولية للتوحيد القياسي (ISO) أطر عمل ذات صلة بالموضوع بشكل خاص:
معيار الأيزو | التطبيق على المكونات ذات درجة الحرارة العالية |
---|---|
آيزو 9001 | متطلبات نظام إدارة الجودة |
آيزو 17025 | كفاءة مختبر الاختبار والمعايرة |
الأيزو 1043-1 ISO 1043-1 | الرموز البلاستيكية والمصطلحات المختصرة |
تضمن شهادة ISO 9001 أن الشركة المصنعة تتبع إجراءات جودة متسقة. وهذا مهم بشكل خاص للمكونات ذات درجات الحرارة العالية حيث يكون التحكم في العملية أمرًا بالغ الأهمية لأداء المواد.
المعايير الخاصة بالصناعة
الصناعات المختلفة لها متطلبات متخصصة للمكونات ذات درجة الحرارة العالية:
- السيارات: IATF 16949، الذي يعتمد على المعيار ISO 9001 مع متطلبات خاصة بالسيارات
- الفضاء الجوي: AS9100 لأنظمة إدارة الجودة AS9100 لأنظمة إدارة الجودة
- كهربائي/إلكتروني: UL 746A للمواد البوليمرية المستخدمة في المعدات الكهربائية
اختبار التحقق من صحة المواد
طرق التحليل الحراري
تبدأ مراقبة الجودة بالتحقق المناسب من صحة المواد. تتطلب تطبيقات درجات الحرارة العالية طرق اختبار محددة:
- المسح الحراري التفاضلي (DSC): يقيس خصائص التدفق الحراري ودرجات حرارة الانتقال الزجاجي
- تحليل الثيرموغرافيات الحرارية (TGA): تقييم ثبات المواد ودرجات حرارة التحلل والتحلل
- التحليل الميكانيكي الديناميكي (DMA): تقييم الخواص الميكانيكية عبر نطاقات درجات الحرارة
التحقق من الخصائص الميكانيكية
بعد الاختبار الحراري، يجب أن تخضع المواد للاختبار الميكانيكي للتأكد من أنها تحافظ على سلامتها الهيكلية:
- قوة الشد في درجات الحرارة المرتفعة
- مقاومة الصدمات بعد التقادم الحراري
- مقاومة الزحف تحت التحميل المستمر
- أداء التعب في دورات درجة الحرارة
لقد رأيت حالات اجتازت فيها المواد التأهيل الأولي ولكنها فشلت بعد التقادم الحراري الممتد. وهذا يسلط الضوء على أهمية الاختبار الشامل الذي يحاكي ظروف العالم الحقيقي.
معلمات التحكم في العملية
متغيرات حقن القوالب بالحقن الحرجة
بالنسبة للمواد ذات درجات الحرارة العالية مثل PEEK أو PPS أو PEI، يصبح التحكم في العملية أكثر أهمية:
- التحكم في درجة حرارة الذوبان (عادةً ما تكون أعلى من البلاستيك القياسي بمقدار 30-50 درجة مئوية)
- تنظيم درجة حرارة العفن (غالبًا ما يتطلب أنظمة تسخين الزيت)
- تحسين سرعة الحقن والضغط
- تعديلات ضغط الانتظار ووقت التبريد
التحكم في العمليات الإحصائية (SPC)
يتضمن تطبيق نظام مراقبة الأداء الفردي لصب القوالب ذات درجة الحرارة العالية ما يلي:
معلمة العملية | طريقة المراقبة النموذجية | تحديد حد التحكم |
---|---|---|
درجة حرارة الذوبان | مستشعرات الأشعة تحت الحمراء، المزدوجات الحرارية | ± 5 درجات مئوية من الدرجة المثلى المحددة |
وقت الدورة | التسجيل الآلي | ±2% من خط الأساس |
وزن الجزء | أخذ العينات المنتظمة | ± 0.5% من الوزن المستهدف |
ثبات الأبعاد | أنظمة الرؤية، CMM | حسب التفاوتات المسموح بها في المخطط |
طرق الفحص أثناء العملية والفحص النهائي
الاختبارات غير المدمرة
غالباً ما تكون تقنيات الفحص المتقدمة مطلوبة:
- التصوير الحراري لتحديد تركيزات الإجهاد المحتملة
- الاختبار بالموجات فوق الصوتية للكشف عن الفراغات الداخلية
- الفحص بأشعة X-ray للمكونات المعقدة عالية الدقة
أخذ عينات الاختبارات المدمرة
في حين أنه لا أحد يرغب في تدمير المنتجات النهائية، فإن خطط أخذ العينات التي تشمل الاختبارات التدميرية توفر ضمان جودة بالغ الأهمية:
- تحليل المقاطع العرضية للتحقق من تدفق المواد وجودة خط اللحام
- تقادم حراري متبوع باختبار ميكانيكي
- اختبار الإجهاد البيئي مع تدوير درجة الحرارة
أتذكر أحد المشاريع حيث كان أحد العملاء يعاني من أعطال غامضة في مكونات ذات درجة حرارة عالية. من خلال التحليل المقطعي المستعرض، اكتشفنا عدم كفاية تدفق المواد في المناطق الحرجة - وهي مشكلة غير مرئية للفحص السطحي ولكن تم الكشف عنها من خلال الاختبارات التدميرية.
متطلبات التوثيق والتتبع
التوثيق الكامل ضروري للمكونات ذات درجة الحرارة العالية، بما في ذلك:
- اعتماد المواد وإمكانية تتبع المواد وتتبع الدفعات
- سجلات معلمات المعالجة لكل عملية تشغيل إنتاج
- نتائج الفحص بمعايير نجاح/رسوب واضحة
- تقارير عدم المطابقة والإجراءات التصحيحية
نحتفظ في شركة PTSMAKE بأنظمة توثيق رقمية تسمح لنا بتتبع أي مكوّن إلى مجموعة المواد الدقيقة ومعلمات المعالجة المستخدمة، وهو أمر بالغ الأهمية لاستكشاف الأخطاء وإصلاحها والامتثال التنظيمي.
انقر لمعرفة المزيد عن التحسين الريولوجي لتحسين متانة القِطع. ↩
تعرّف على خاصية البوليمر المهمة هذه لتحسين تصميمات الأجزاء الخاصة بك. ↩
تعرّف على هذه المواد المتقدمة وكيف يمكنها حل تحديات الحرارة العالية التي تواجهها. ↩
تعرف على خصائص المواد الحرجة لاختيار المواد المثلى. ↩
تعرف على كيفية الوقاية من الإجهاد الحراري في القوالب ذات درجات الحرارة العالية لإطالة عمر الأداة. ↩
تعرّف على كيفية تأثير هذا العامل الرئيسي على أنماط الانكماش وجودة القِطع في التشكيل في درجات الحرارة العالية. ↩
انقر لمعرفة المزيد عن تقنيات توحيد التبريد للبوليمرات عالية الحرارة. ↩
انقر للتعرف على طرق اختبار درجة حرارة الانحراف الحراري للبوليمرات عالية الأداء. ↩