On-demand Custom CNC Machining Services
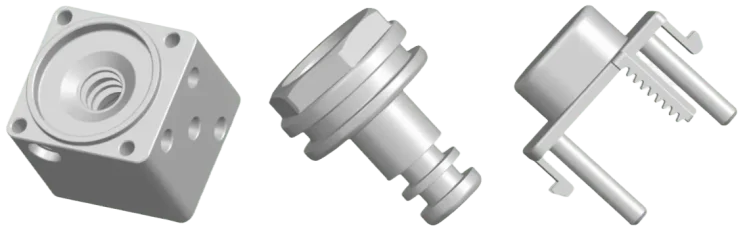
STEP STP SLDPRT IPT PRT SAT IGES IGS CATPART X_T OBJ STL files
- All uploads are secure and confidential.
Western companies Trusted CNC Machining Partner
Ranging from 3-Axis to 5-Axis Machining
Leading CNC Machining Manufacturer in China
Strict quality control meets EU and US standards








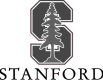
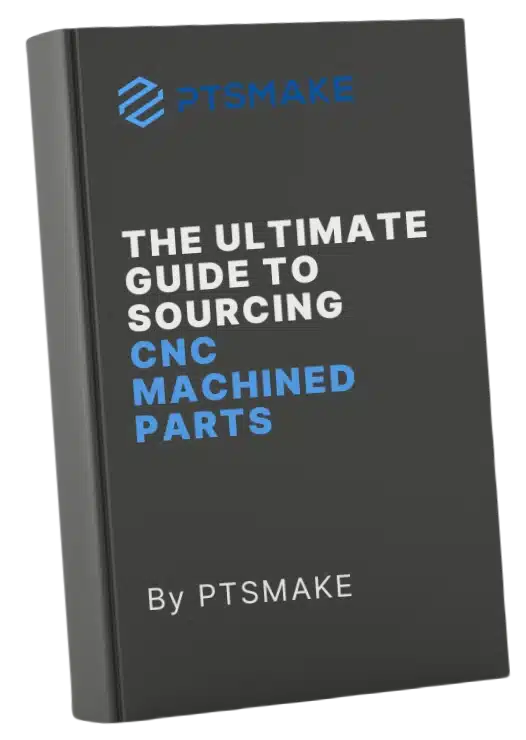
To save you time, we have also prepared a PDF version containing all the contents of this page, only leave your email and you will get the download link immediately.
Our Quality Control Process for Precision CNC Machining
At PTSMAKE, we understand that precision and reliability are critical to your business. Our commitment to quality control in CNC machining ensures that every part we produce meets your exact standards and supports your operational success.
Quality Control Process
The precision required in CNC machining demands careful attention at every stage. Here’s how we ensure top-quality results throughout our production process:
- Raw Material Inspection: Before we begin machining, we thoroughly inspect all raw materials. We verify that each material meets your specific requirements and is suitable for high-precision CNC milling or turning. This step is essential to ensure the final parts perform as expected.
- Real-Time Production Monitoring: We use advanced equipment to monitor the machining process in real-time. This allows us to maintain tight tolerances and ensure that every cut and movement is executed with accuracy and consistency.
- In-Process Multi-stage Inspections: Our team conducts inspections during multiple stages of production. By checking parts throughout the machining process, we can identify and address any issues immediately. This proactive approach ensures both the functionality and quality of the final product.
- Comprehensive Final Inspection: After machining is complete, we perform a detailed inspection of each part. We verify dimensions, tolerances, and surface finishes to make sure everything matches your exact specifications. This final check ensures you receive parts that are ready to use.
- Secure Packaging and Shipping: We know that precision parts require careful handling. Before shipping, we inspect the packaging to ensure that each item is protected during transit. This attention to detail helps your parts arrive safely and ready for immediate use.
- Experienced Quality Control Team: Our dedicated quality control professionals are highly trained in CNC machining processes. They focus on every detail, ensuring that the parts we produce help improve your products and support your business objectives.
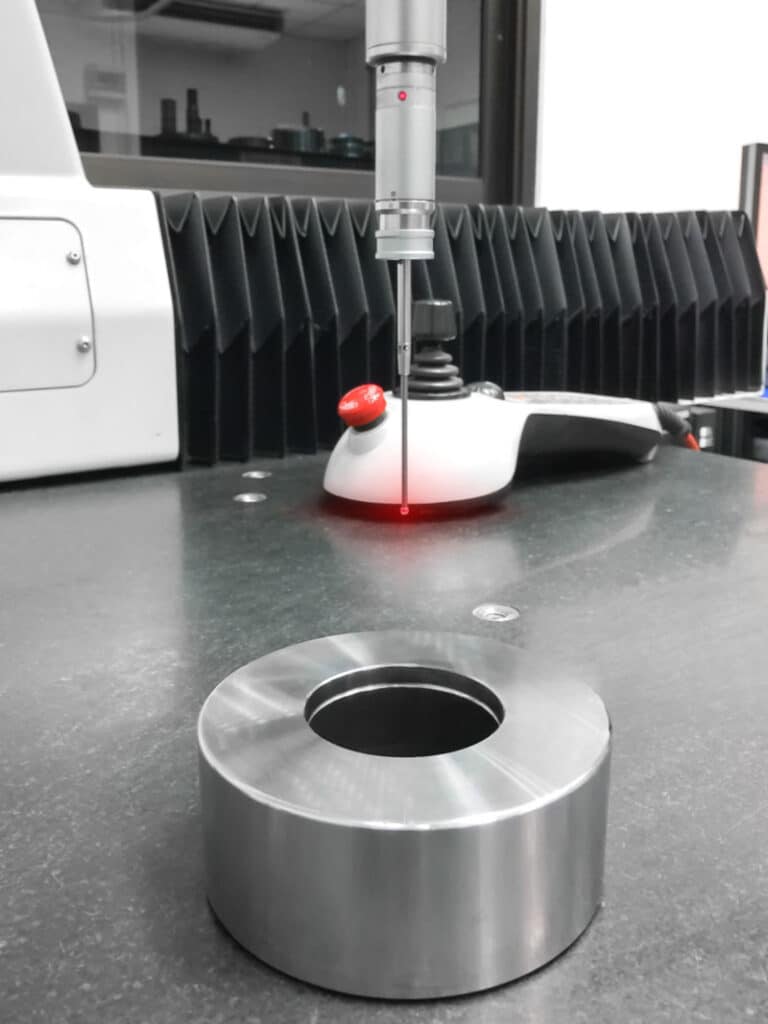
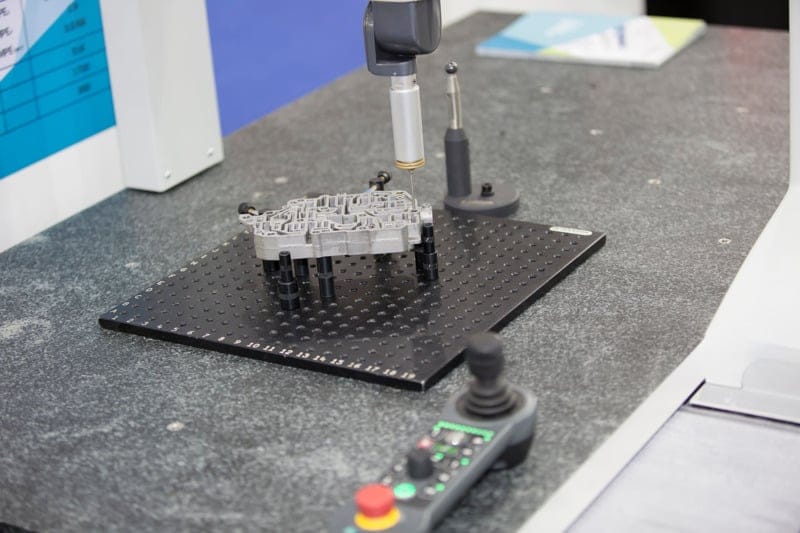
CMM
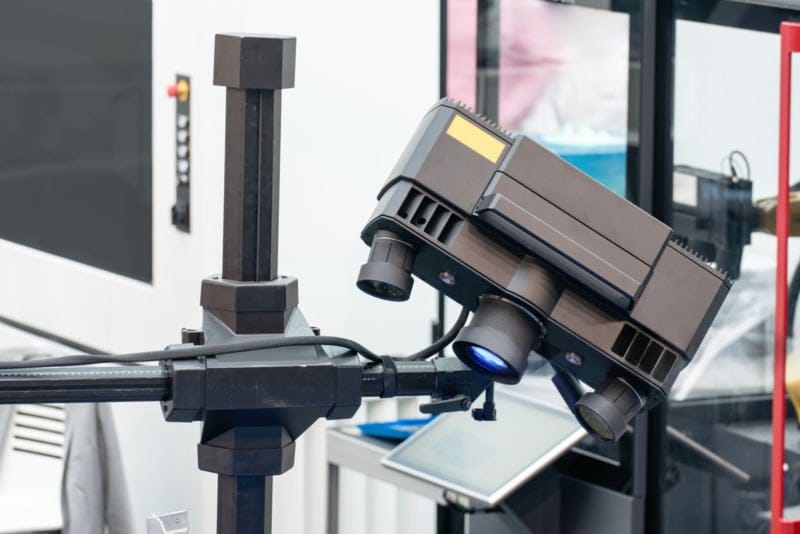
GOM 3D-Scanner
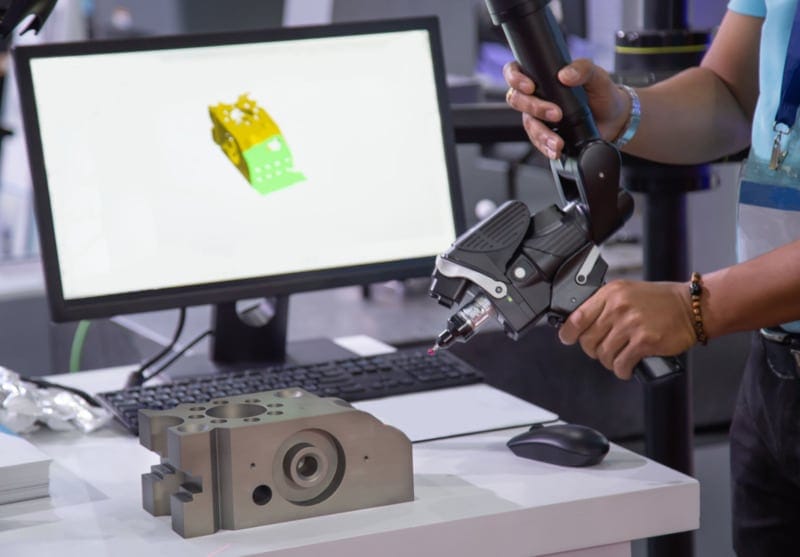
Portable CMM
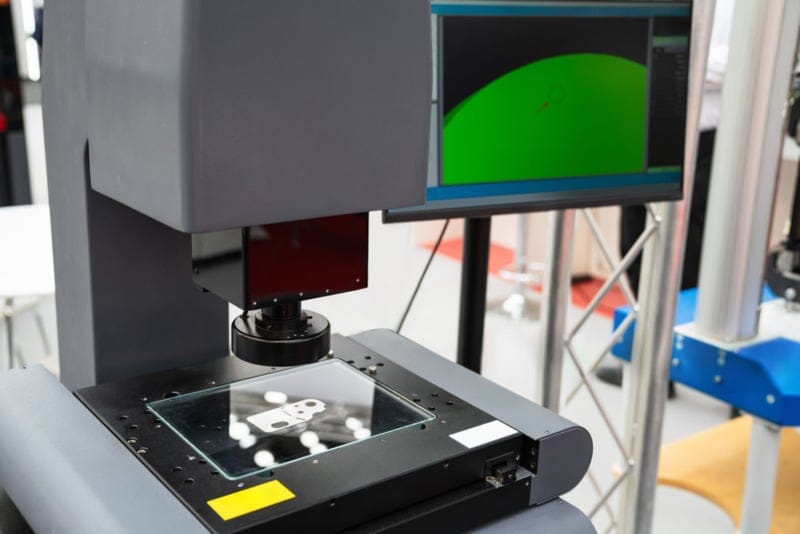
Projector
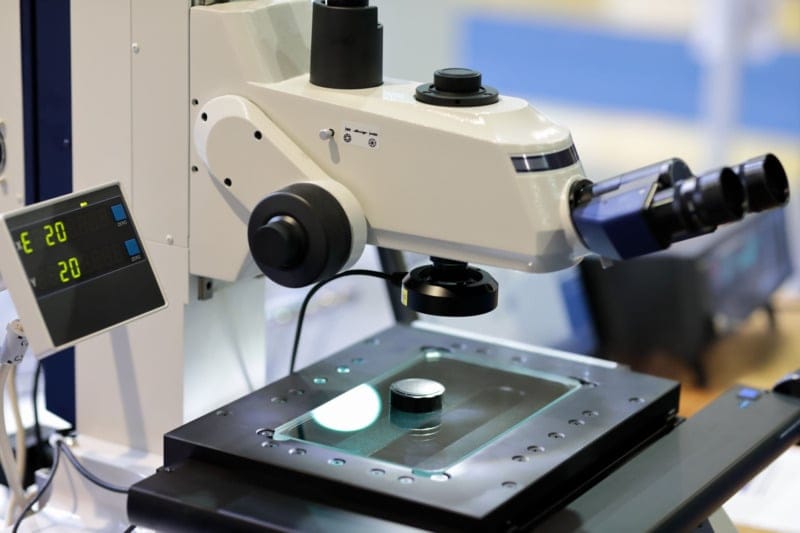
Optical microscope
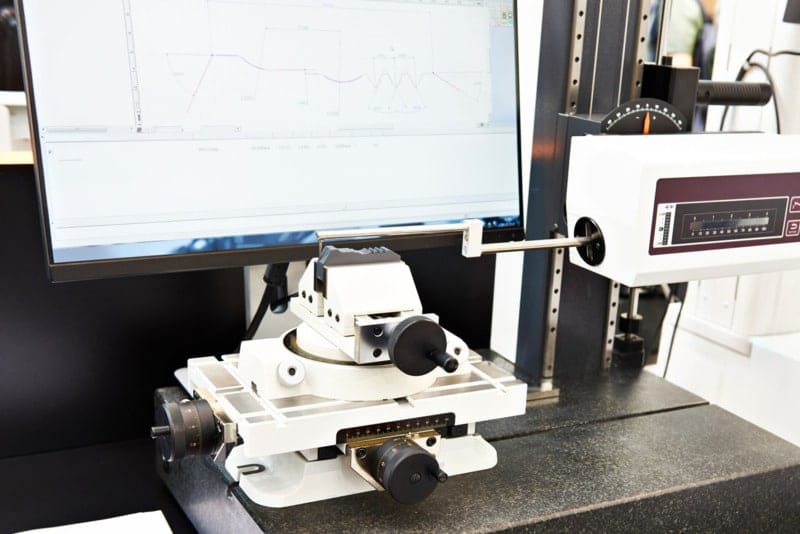
Roughness Tester
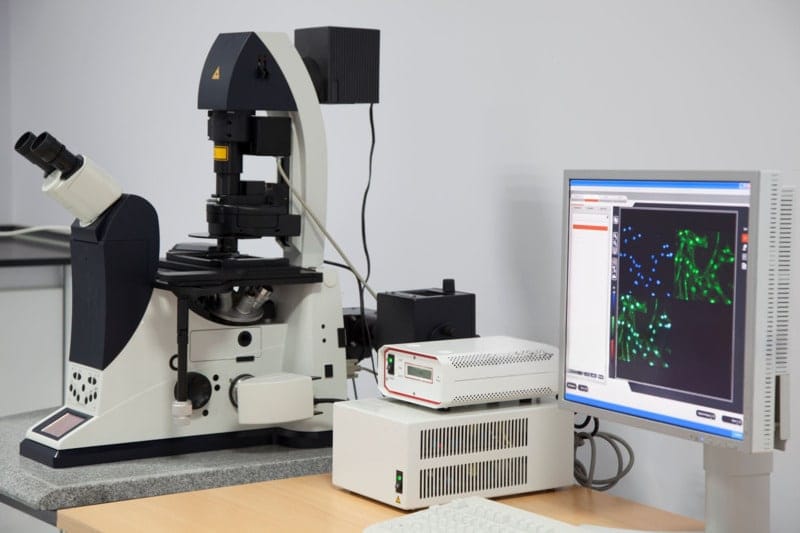
Raw material analyzer
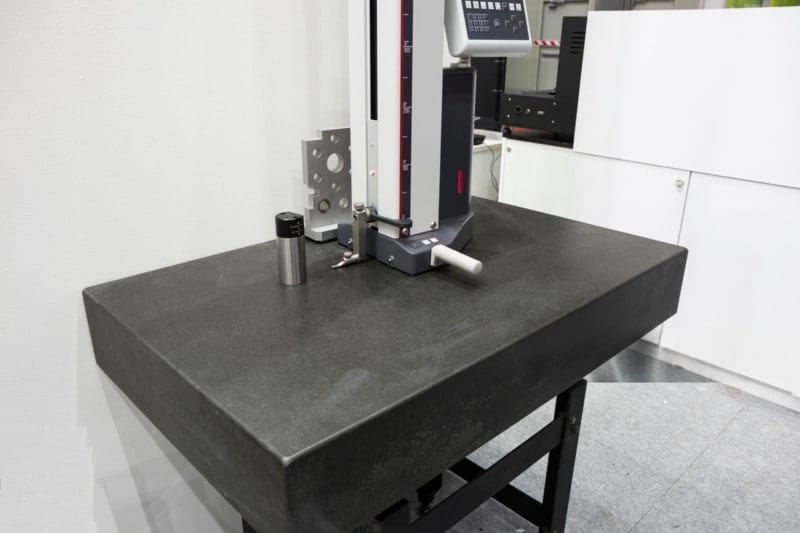
Altimeter
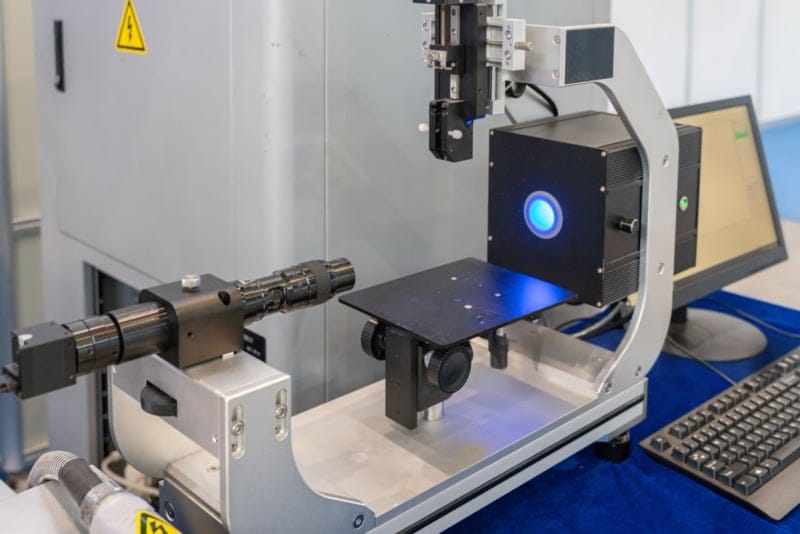
Laser Inspection
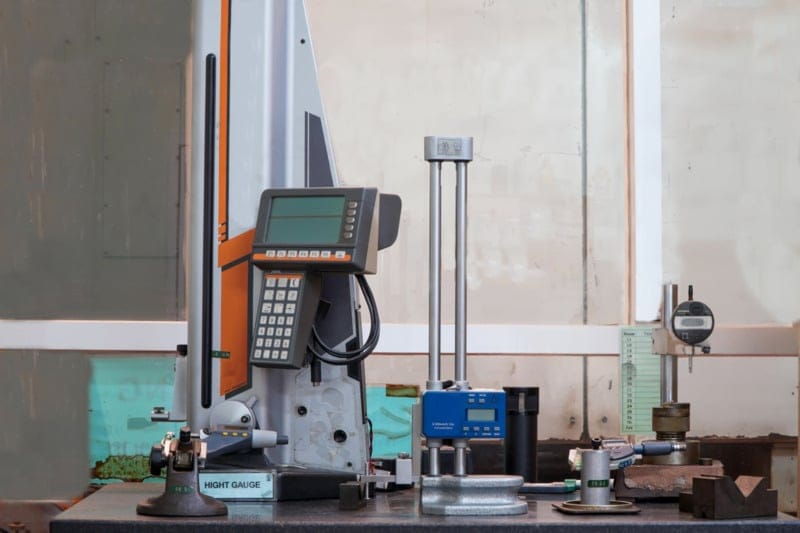
Others
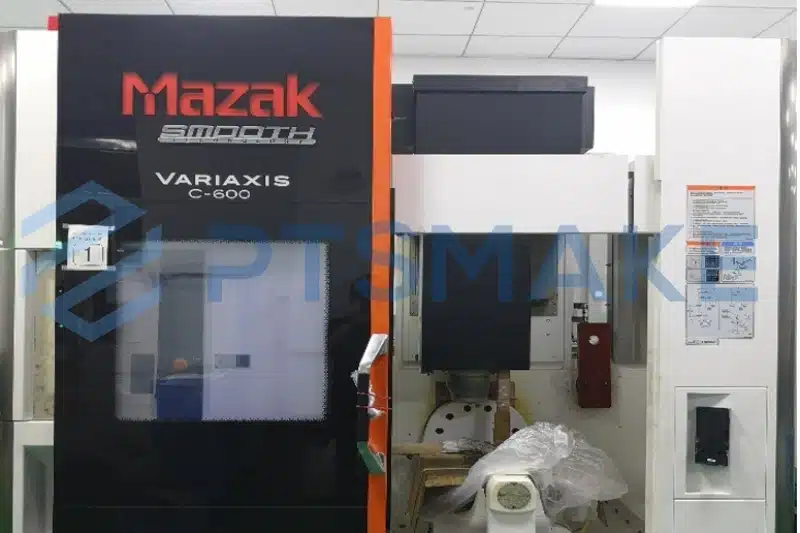
CNC Milling Machine (Japan)
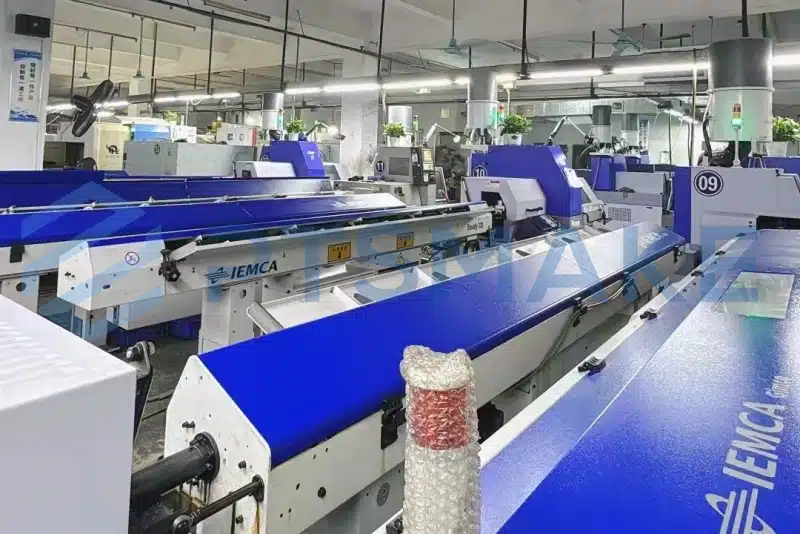
Swiss Turning Machine (Japan)

CNC Turning Machine (TaiWan)
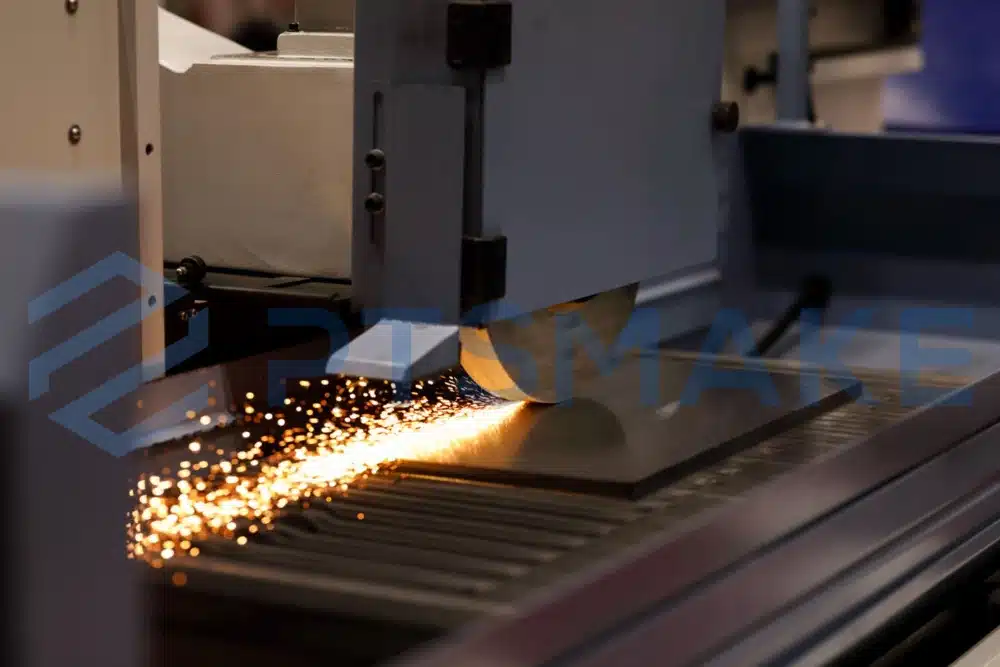
Precision Grinding Machine (Japan)
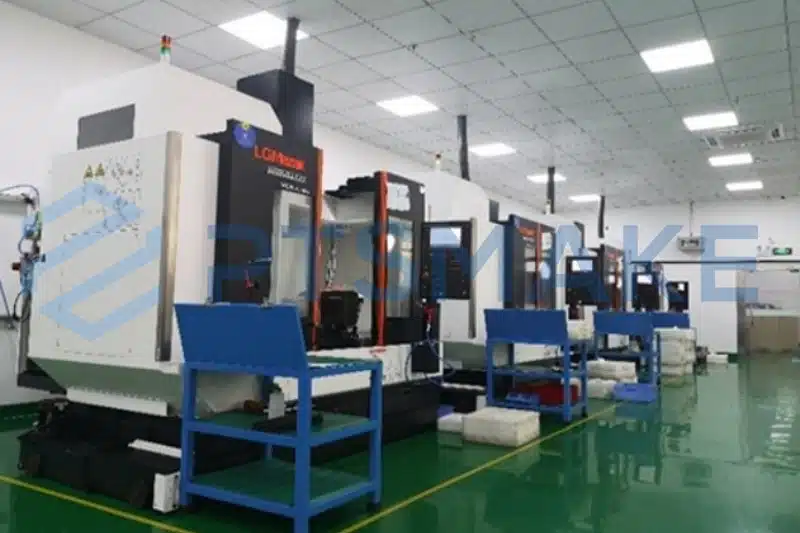
5 Axis Machine (Japan)
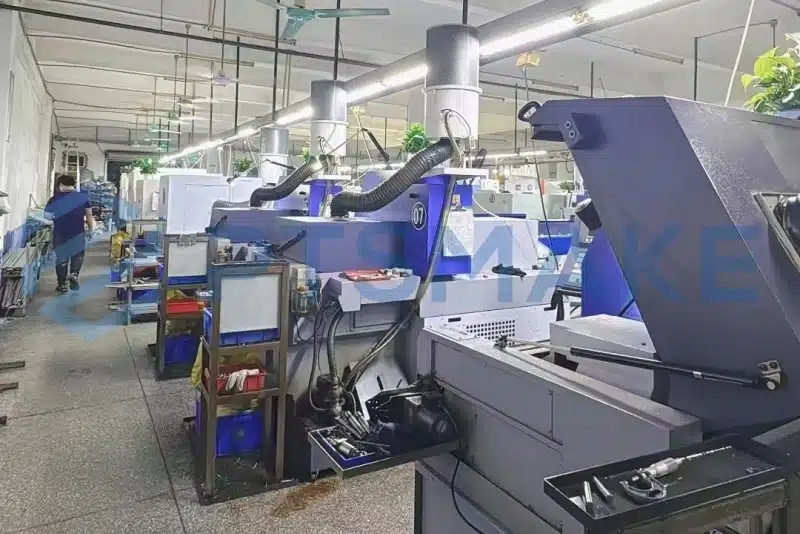
Swiss Turning Machine (Japan)
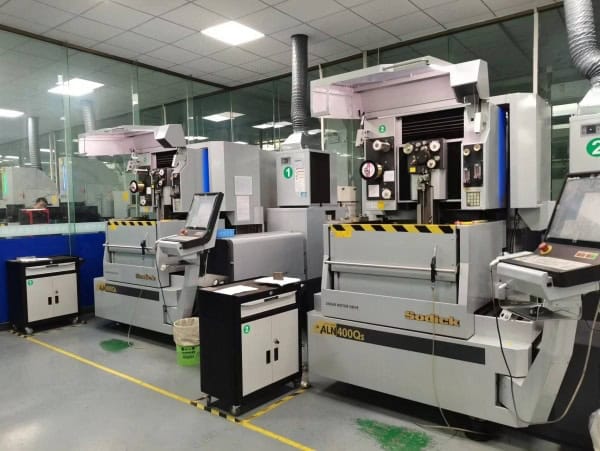
Slow Wire Cut (Japan)
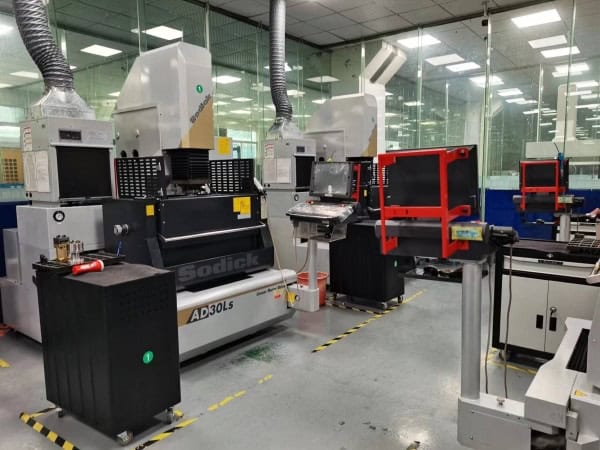
Electric Discharge Machining (Japan)
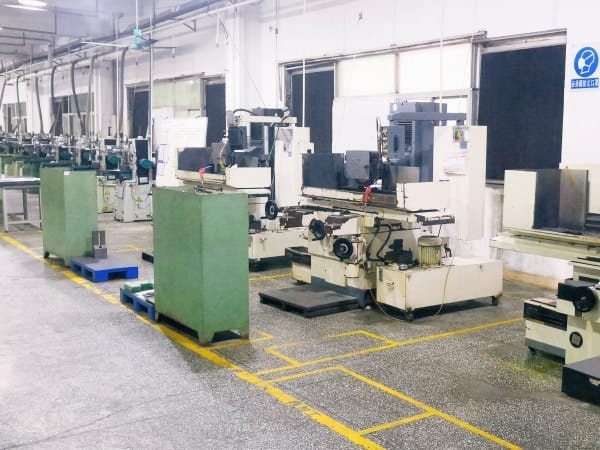
Precision Grinding Machine (Japan)

CNC Turning Machine (TaiWan)
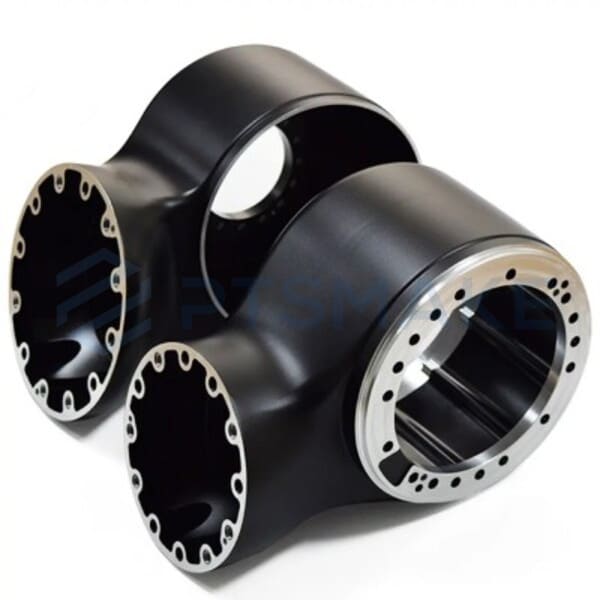
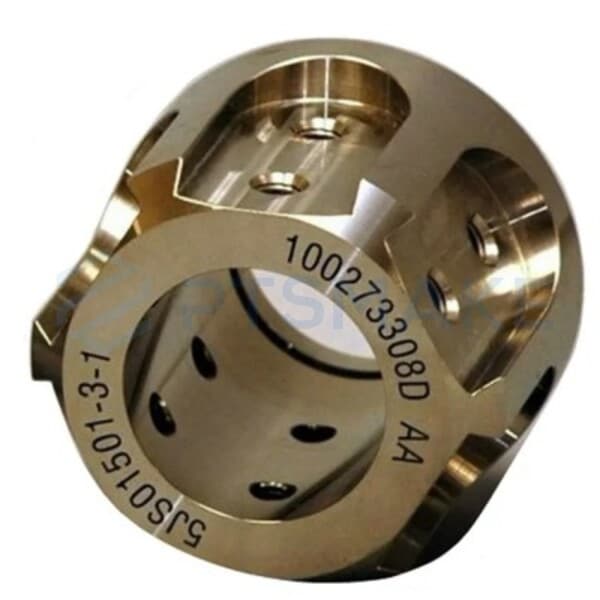
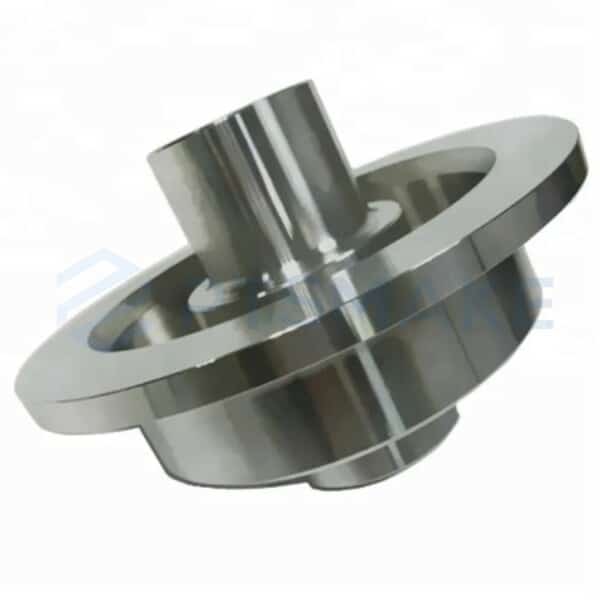
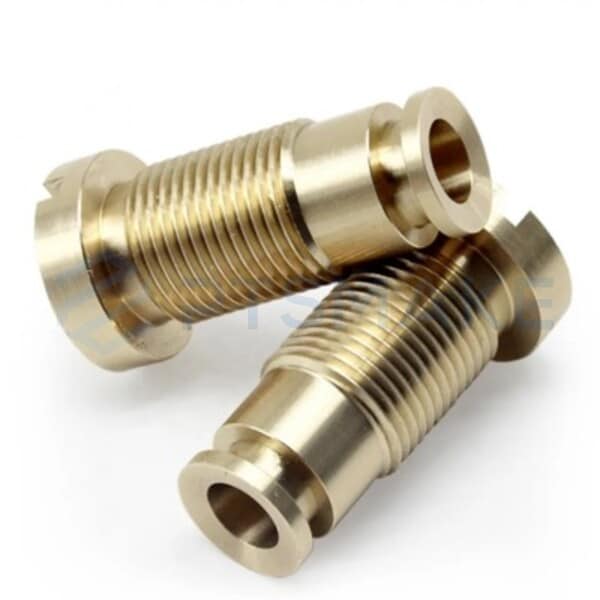
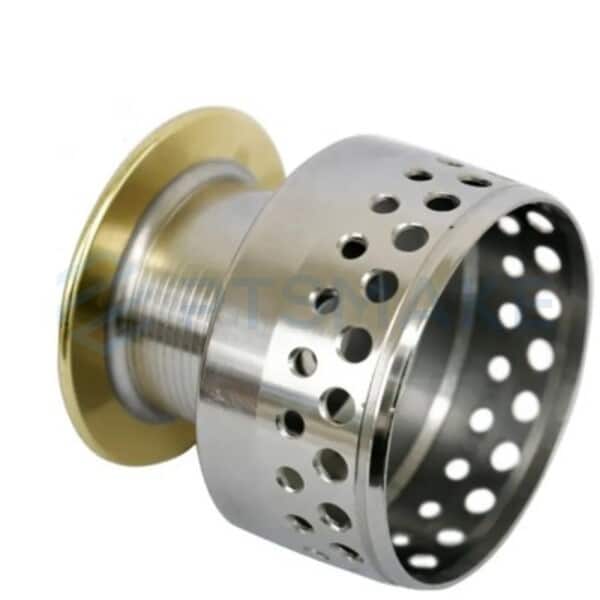

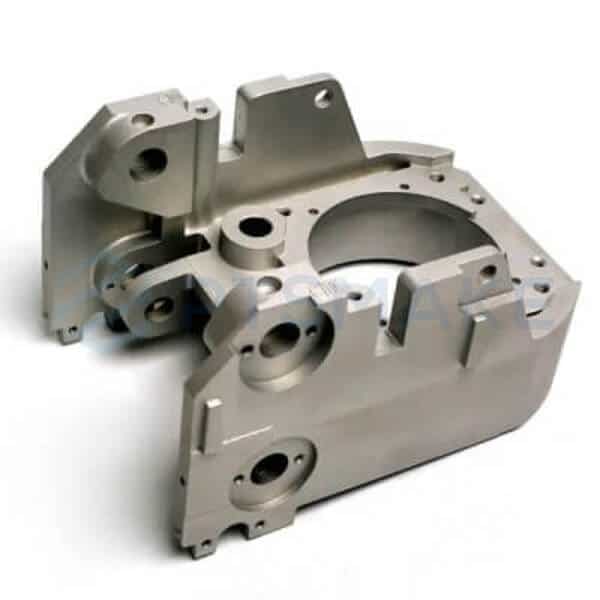
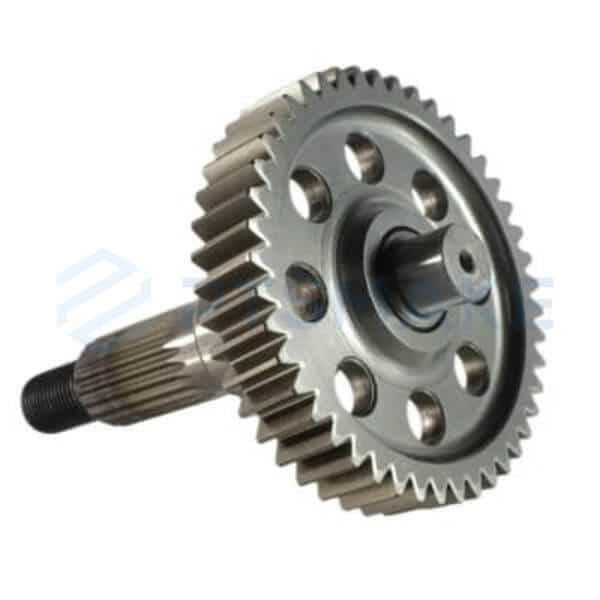

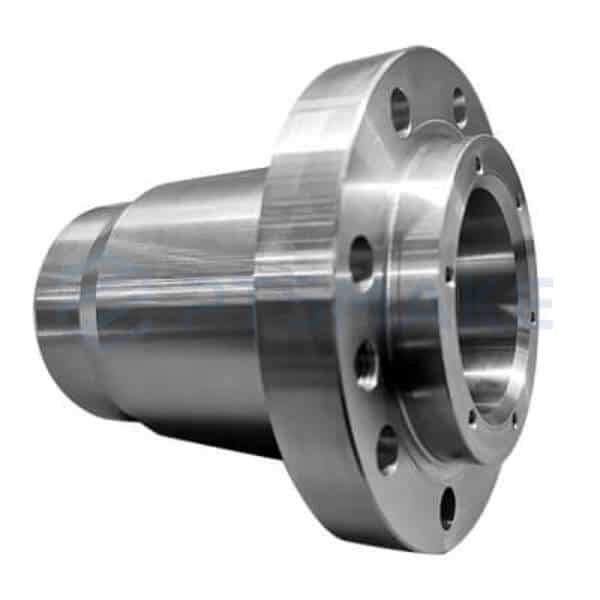
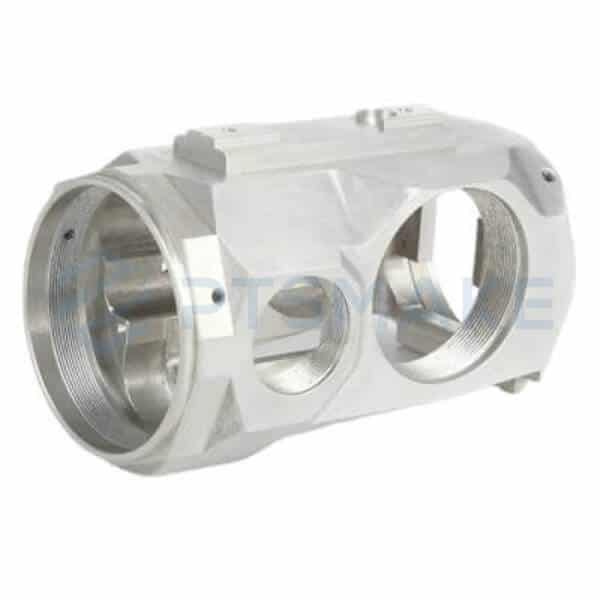
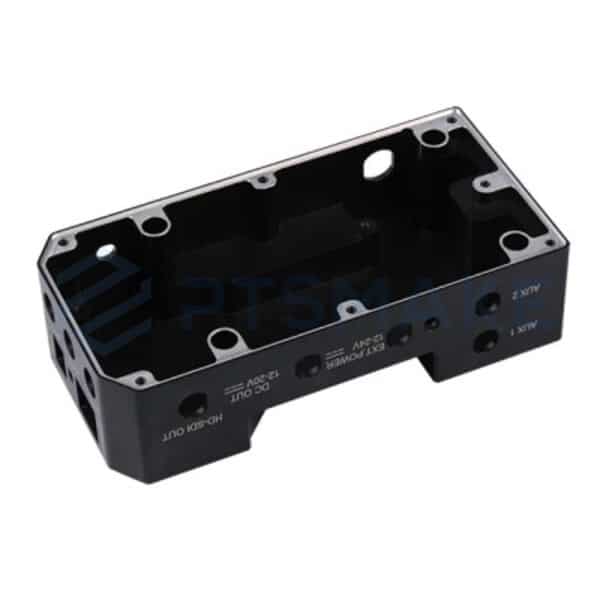
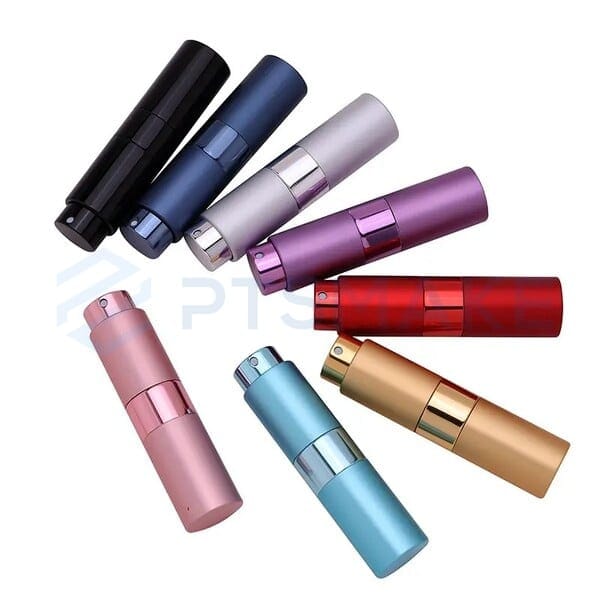
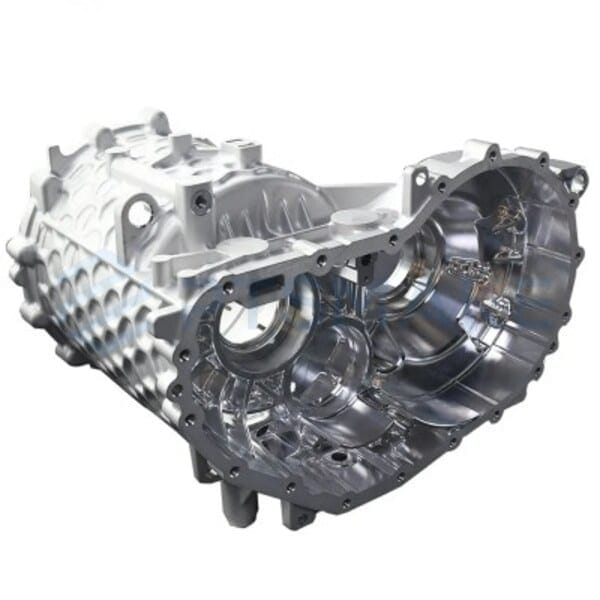
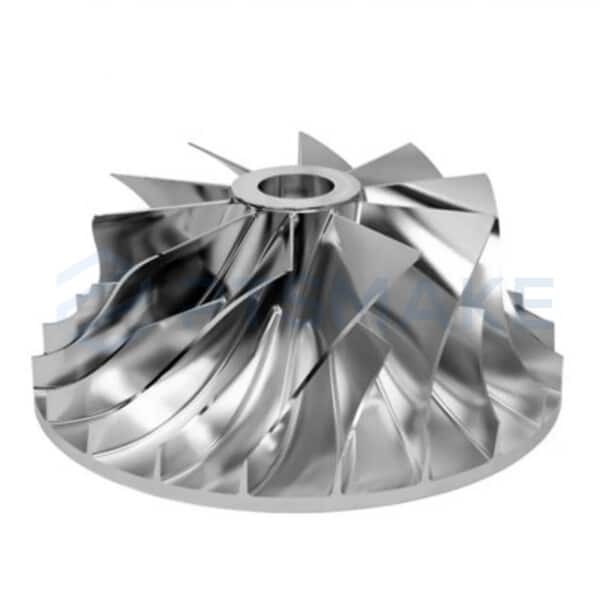
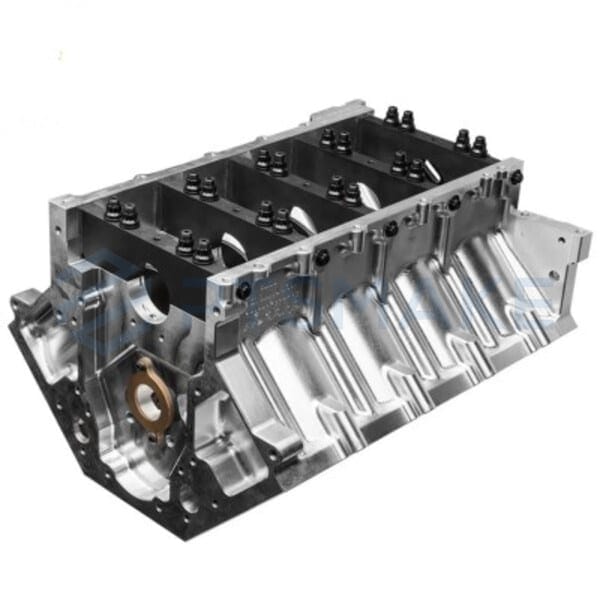
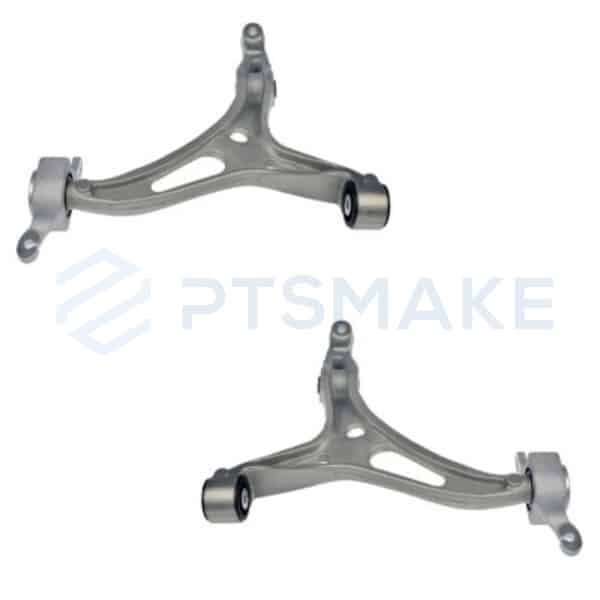
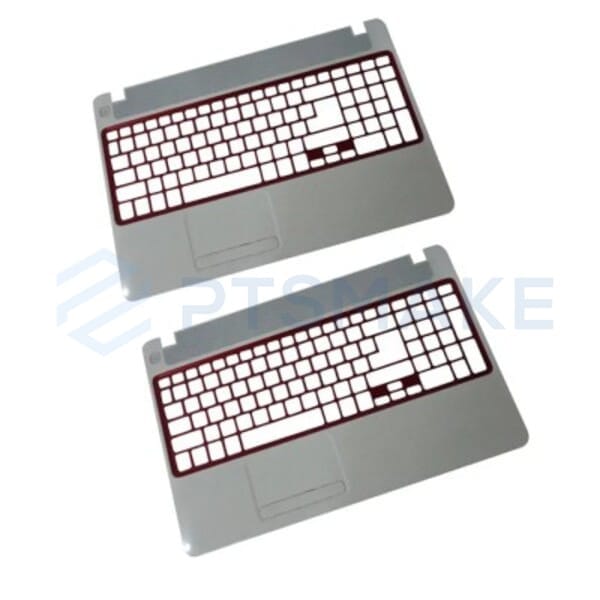
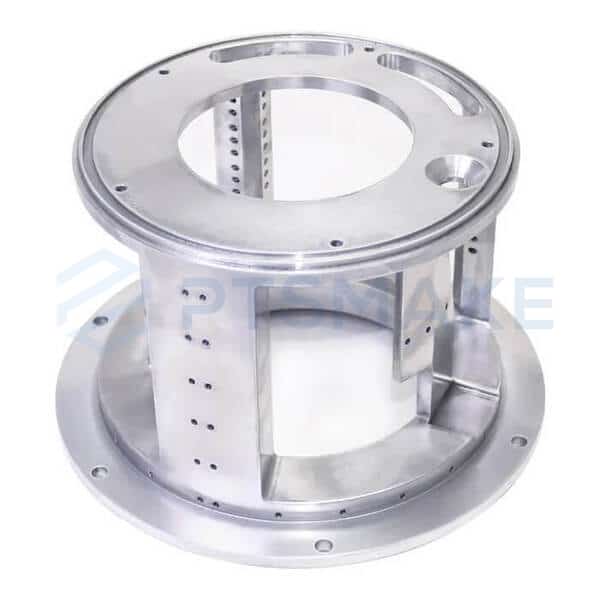

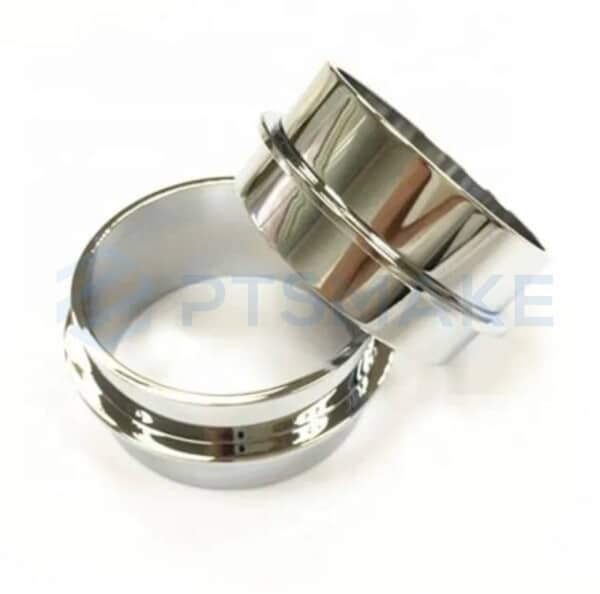
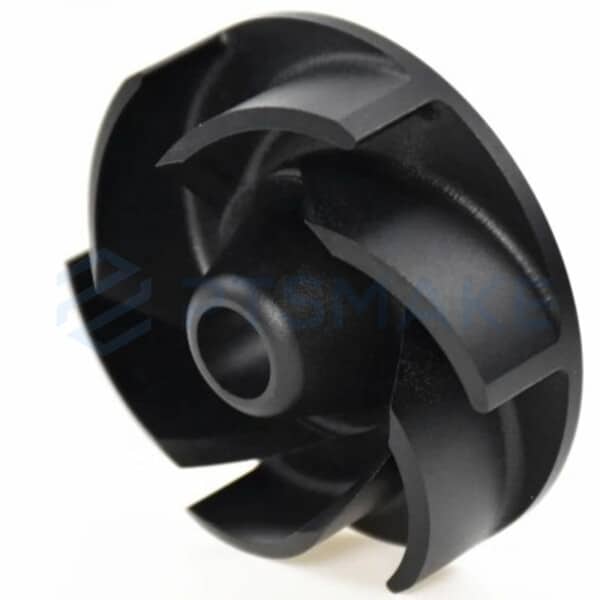
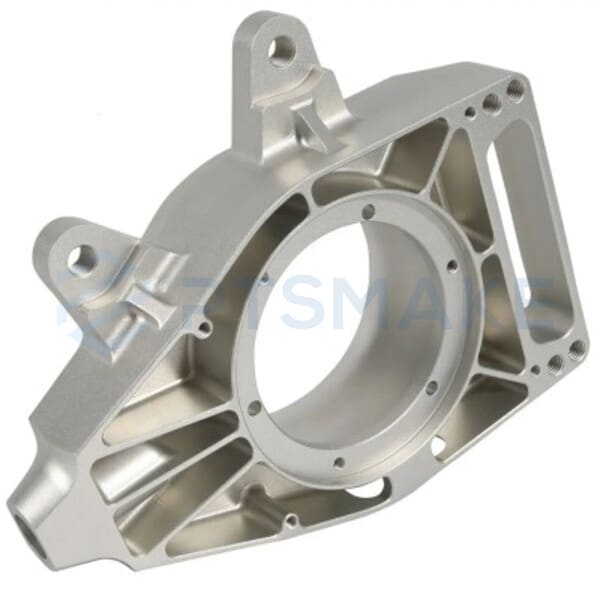
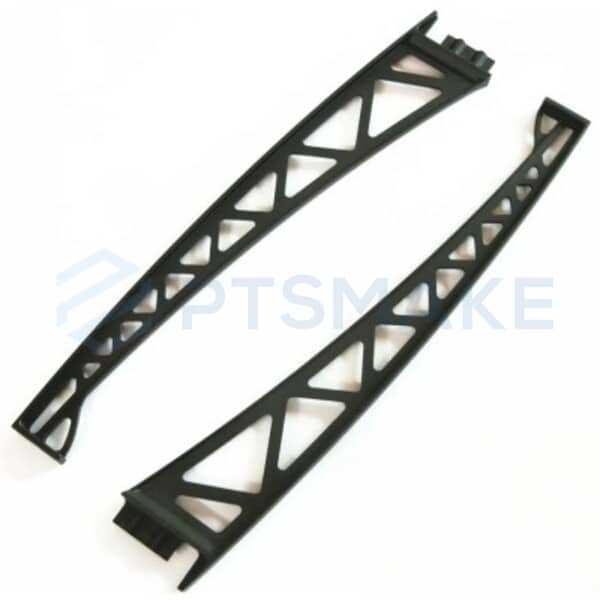
How to Choose the Right CNC Machining Supplier
Choosing the right precision CNC machining partner is vital for the success of your projects. A reliable partner ensures high-quality parts, timely delivery, and supports your business objectives. Here are key factors to consider when selecting a CNC machining supplier:
- Technical Expertise: Look for a supplier with a strong technical background in CNC milling and turning. Their expertise will help you achieve complex designs and meet tight tolerances required for your components.
- Modern Equipment: Ensure the supplier uses advanced CNC machines equipped with the latest technology. Modern machinery enhances precision, efficiency, and can handle both low and high-volume production runs.
- Quality Assurance: A robust quality control system is essential. Verify that the supplier has certifications and follows strict quality standards throughout the production process, from raw material inspection to final product evaluation.
- Material Proficiency: The supplier should have extensive knowledge of various materials, such as metals and plastics. Their understanding of material properties ensures the right selection for your specific applications.
- Customization Capabilities: Choose a partner who can provide custom solutions tailored to your needs. This includes the ability to produce prototypes, handle complex geometries, and adapt to changing project requirements.
- Reliable Delivery Times: Timely delivery is crucial to keep your projects on schedule. Assess the supplier’s track record for meeting deadlines and their capacity to scale production as needed.
- Transparent Communication: Effective communication is key to a successful partnership. The supplier should be responsive, provide clear updates, and be open about any challenges that may arise during production.
- Competitive Pricing: While cost should not compromise quality, finding a supplier offering fair and transparent pricing is important. Ensure all costs are outlined clearly, including materials, machining, finishing, and shipping.
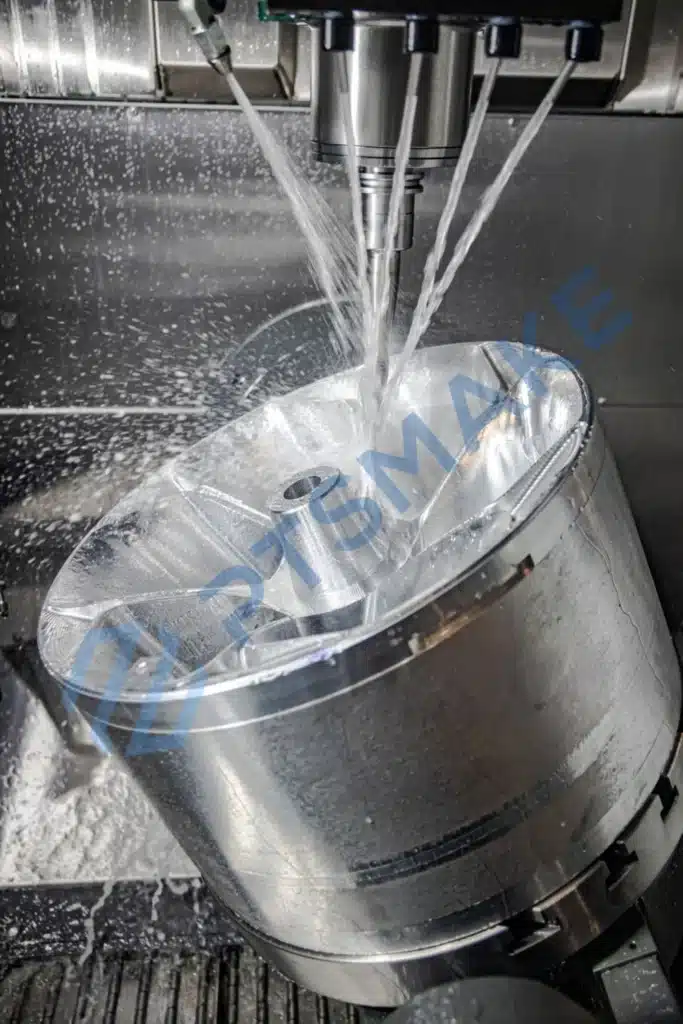
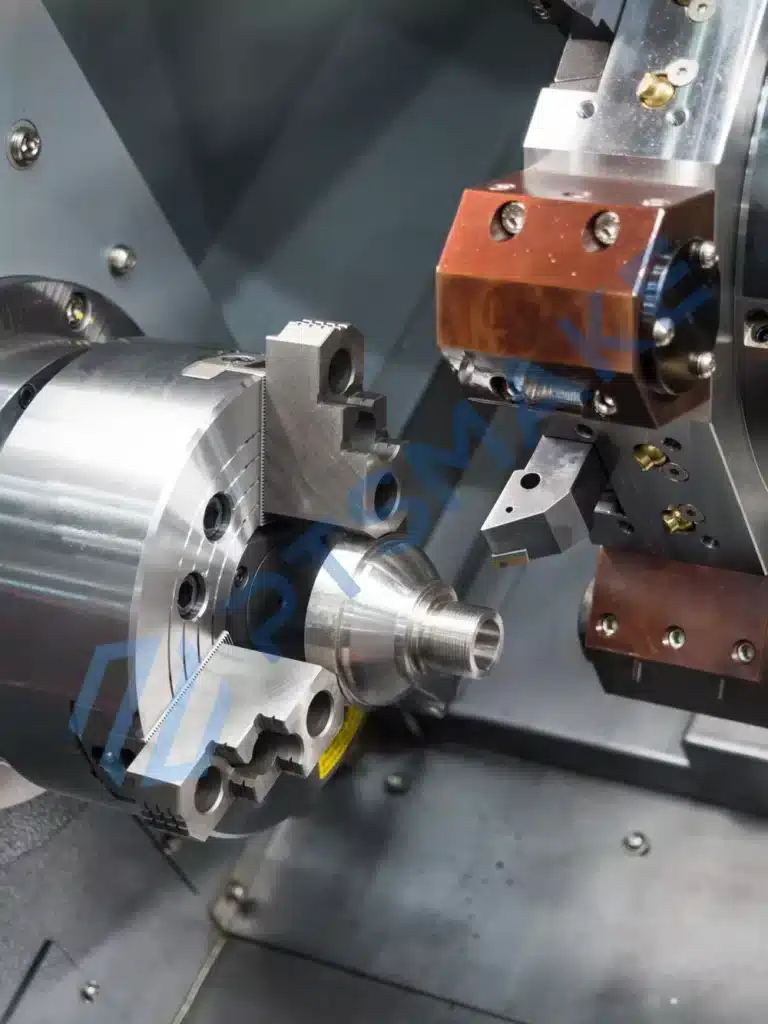
- Client References: Ask for references or case studies from previous clients in your industry. This provides insight into the supplier’s reliability and the quality of their work.
- After-Sales Support: A good supplier offers excellent customer service even after the parts are delivered. This includes addressing any issues promptly and providing ongoing technical support.
- Production Capacity: Make sure they can handle your required production volume, whether it’s a small run or large-scale manufacturing.
- Long-Term Partnership Potential: Choose a supplier who can grow with your business and support future needs, fostering a strong, long-term relationship.
- Intellectual Property Protection: Ensure the supplier has strict policies to protect your designs and proprietary information. A trustworthy partner will have confidentiality agreements and secure data handling practices in place.
- Technological Adaptability: A supplier willing to adopt new technologies and processes can offer innovative solutions and improvements over time.
- Customization of Services: Beyond producing parts, some suppliers offer additional services like design assistance, material selection guidance, or finishing options tailored to your needs.
- Sustainability Practices: Consider suppliers who adopt environmentally friendly practices. Sustainable operations not only benefit the environment but can also reflect positively on your business.
What Sets Us Apart
Using advanced CNC technology, we deliver complex, precise components that meet your exact specifications.
Our engineers collaborate with you to optimize designs for manufacturability, saving time and reducing costs without compromising quality.
We provide prompt and clear communication, addressing your concerns quickly to facilitate smooth collaboration throughout your project.
From prototypes to large-scale production, we adapt to your needs, streamlining your supply chain.
"PTSMAKE has been an outstanding partner for our company. We needed precise CNC machined parts for our latest product line, and their team delivered exceptional quality. Their commitment to our project timelines and attention to detail helped us bring our products to market faster. We highly value their professionalism and look forward to continued collaboration.
Michael, Production Manager, United States"
CNC Machining Capabilities
We offer a comprehensive range of CNC machining services tailored to your needs. Here are our common machining scope:
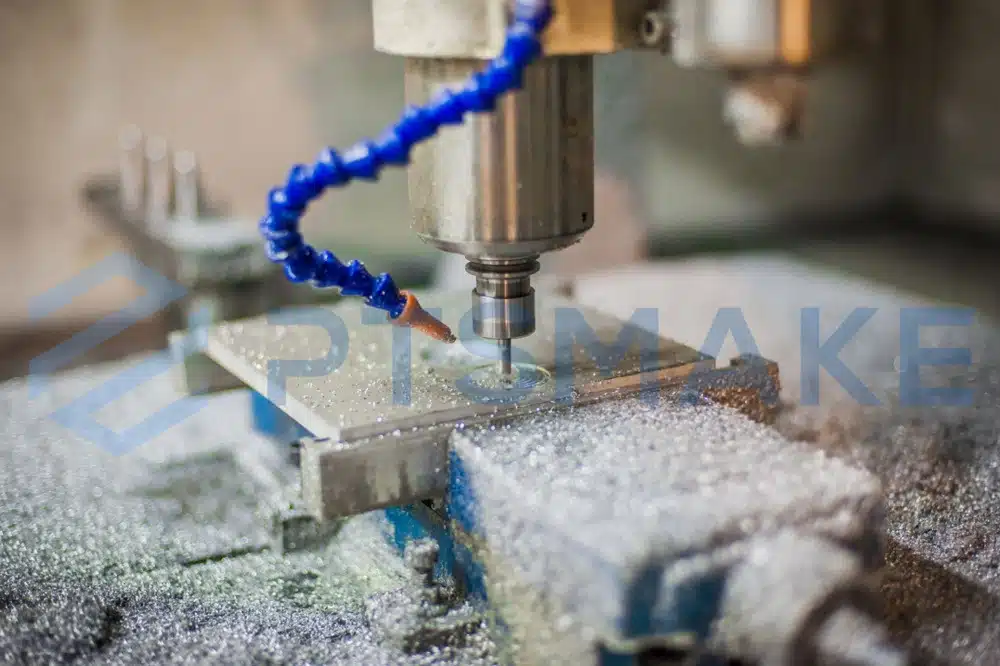
CNC Milling
High-precision milling for complex parts, ensuring accuracy and consistency in every component.
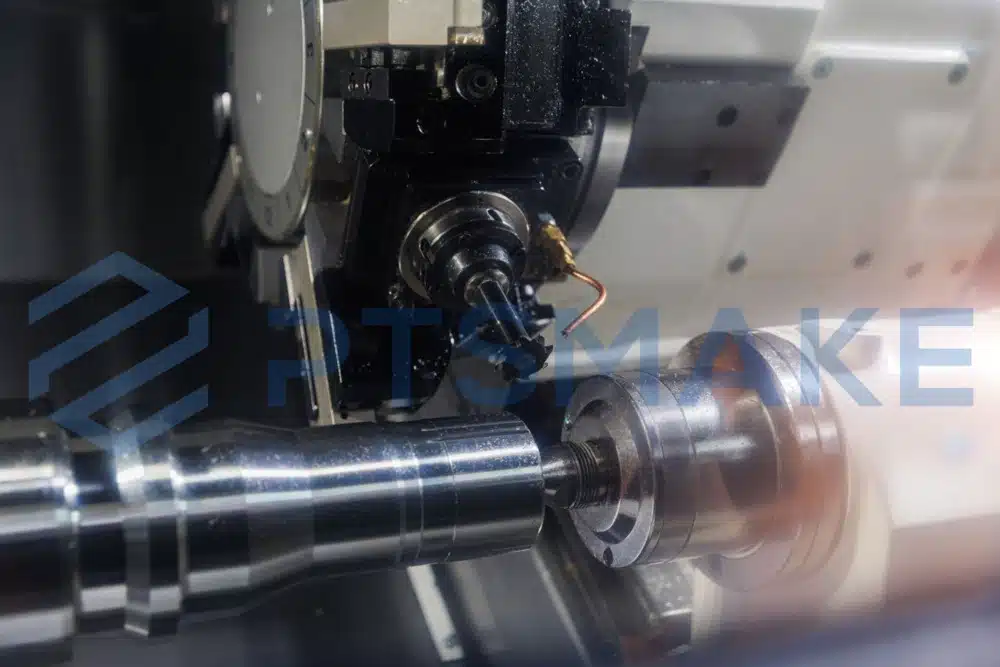
CNC Turning
Expert turning services for producing precise cylindrical parts with tight tolerances.
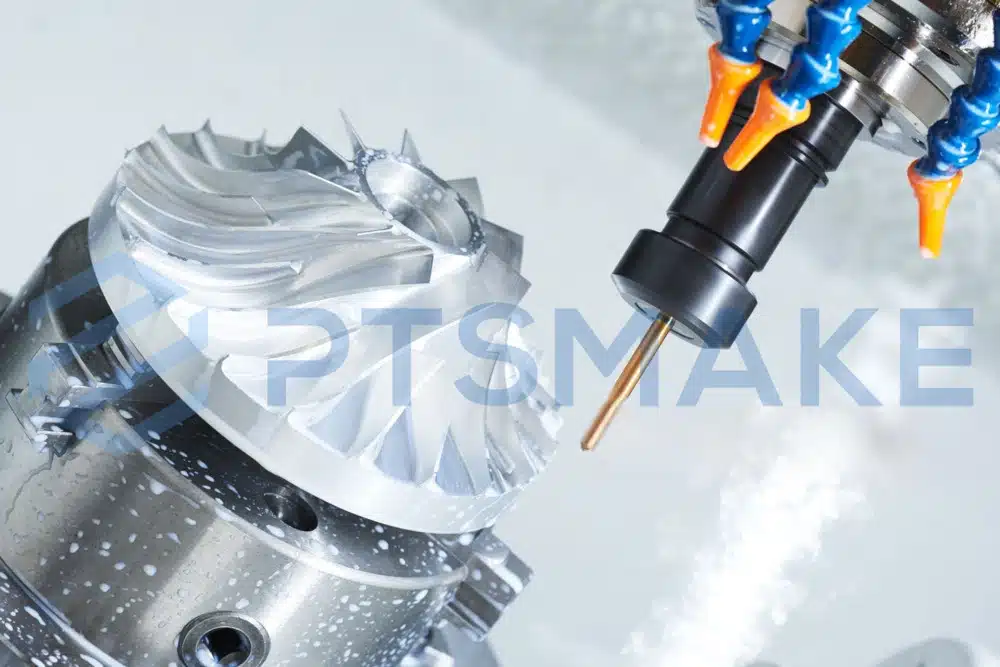
5 Axis Machining
Advanced 5-axis machining for intricate parts, enabling complex geometries in a single setup.
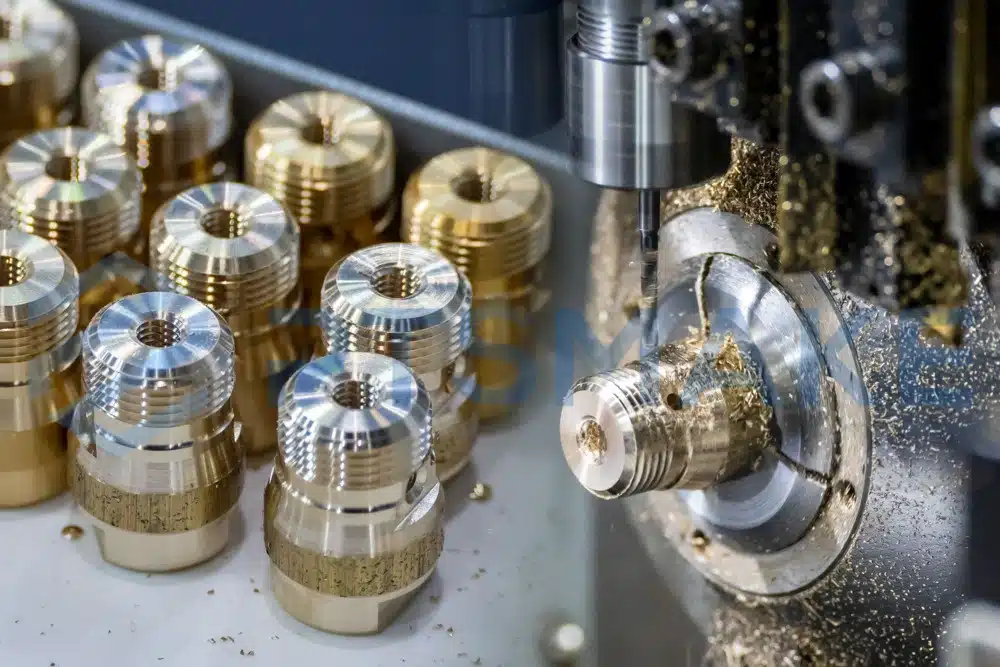
Swiss CNC Turning
Precision turning for small, complex components, ideal for high-volume production with exceptional accuracy.
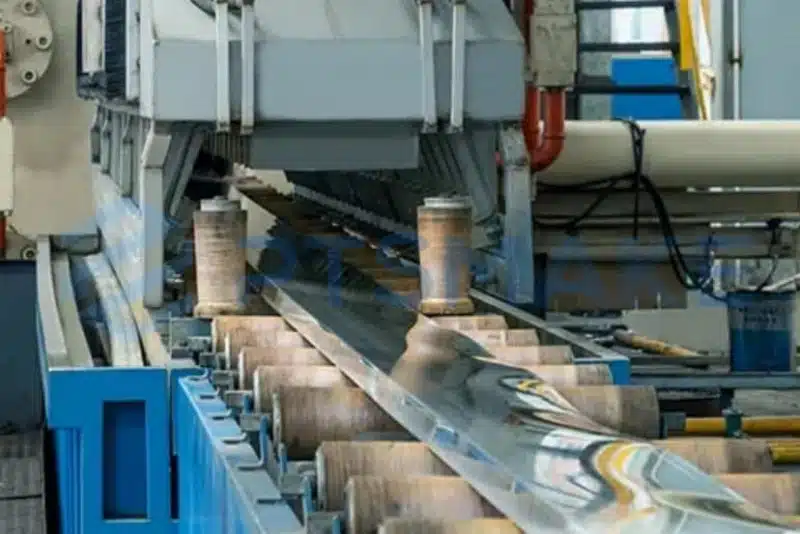
Aluminium Extrusion
Custom aluminium extrusion services for creating lightweight and durable parts specific to your designs.
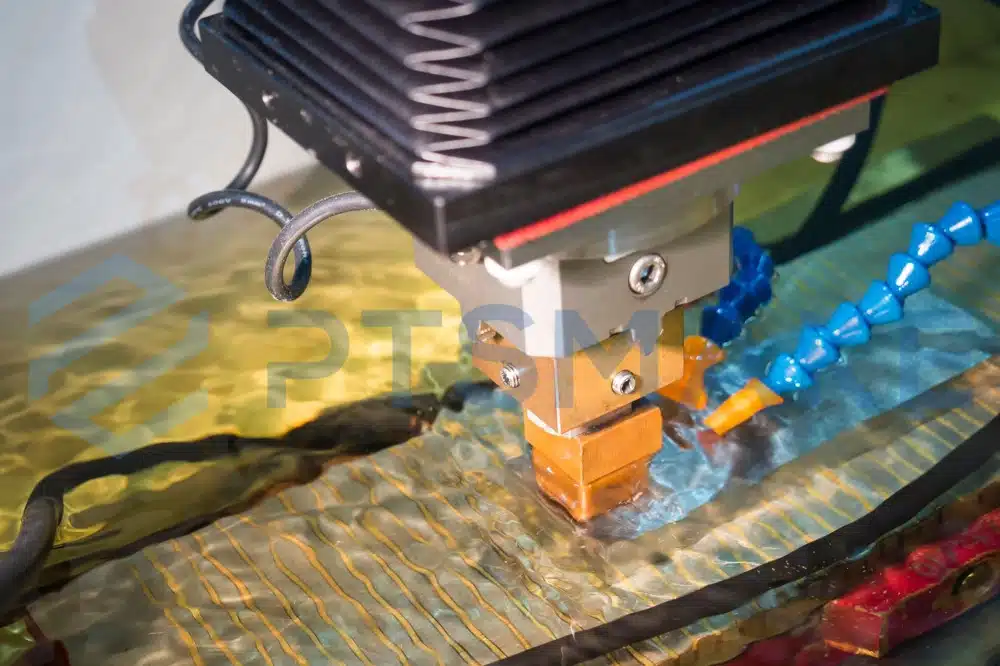
EDM Machining
Electrical Discharge Machining for producing intricate shapes in hard materials with high precision.
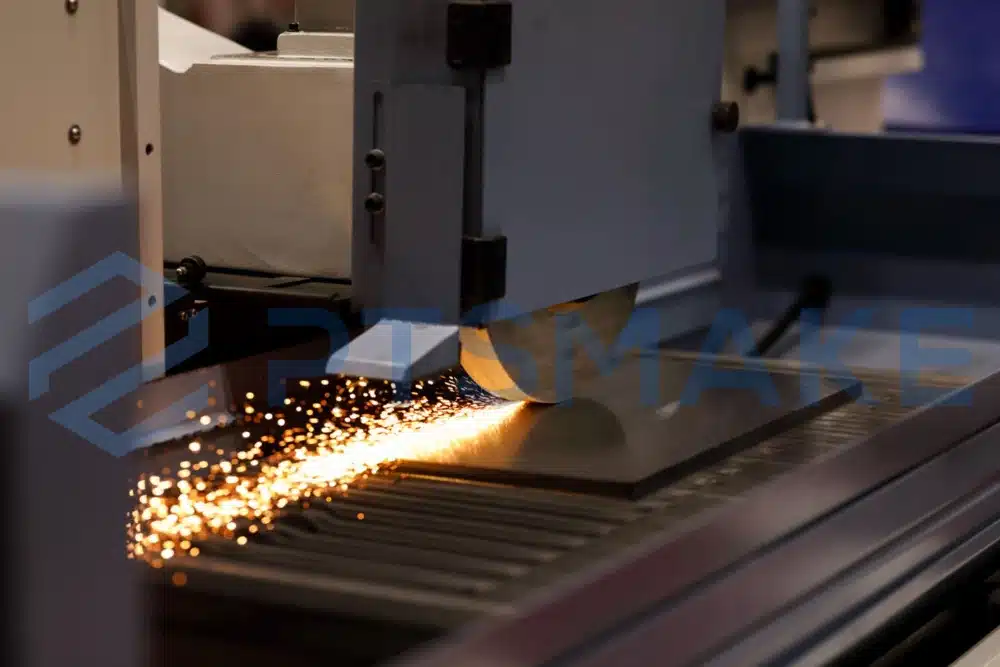
Precision Grinding
High-quality grinding services to achieve exact dimensions and superior surface finishes on critical components.
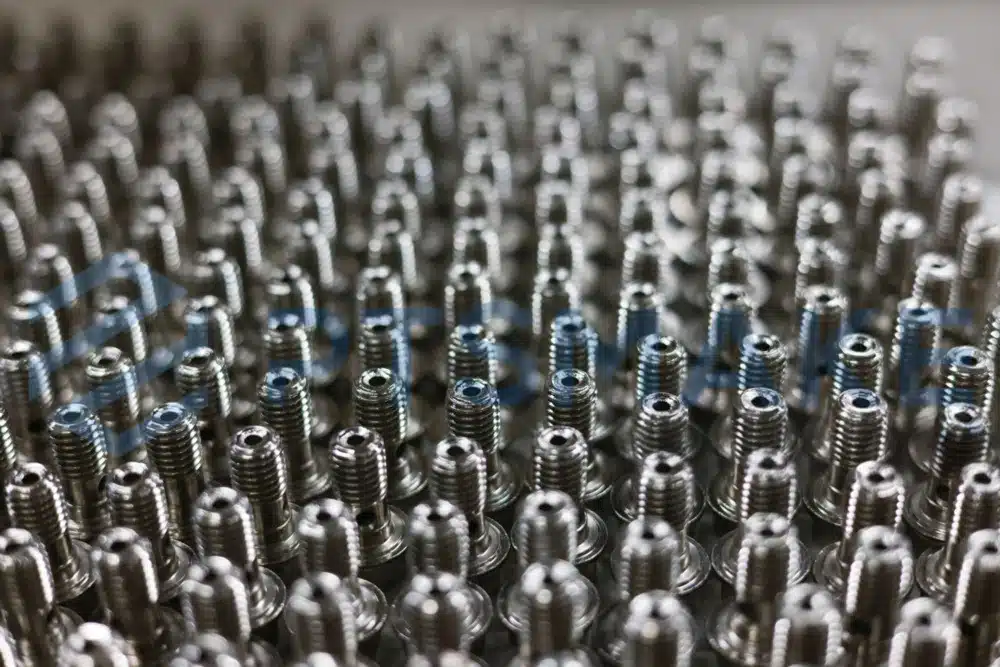
High Volume CNC Machining
Efficient machining solutions for large production runs, ensuring consistency and timely delivery.
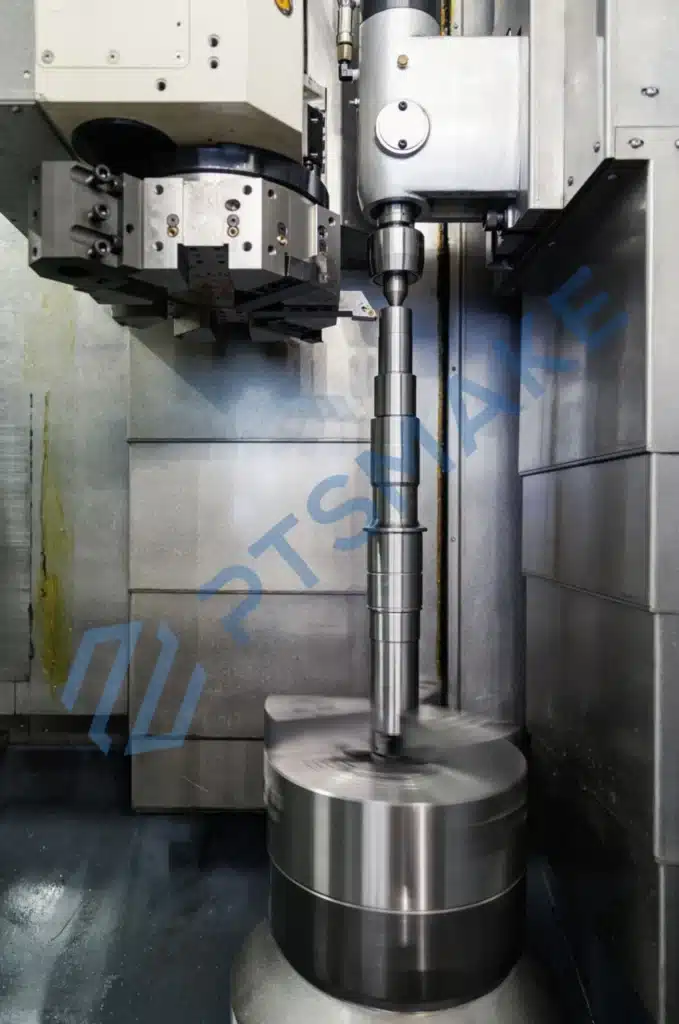
Diverse Material Options
We machine a wide range of metals & plastic to create strong and precise components. Materials like aluminum, stainless steel, brass, plastic, inconel, carbon steel, steel alloy, titanium and copper are commonly used in our processes. These material offer durability and excellent mechanical properties. We select the appropriate material based on your requirements to ensure optimal performance.
- Aluminum: Lightweight and corrosion-resistant, ideal for aerospace and automotive components.
- Stainless Steel: Durable and resistant to wear and corrosion, suitable for medical devices and food processing equipment.
- Carbon Steel: Offers high strength and versatility for construction and industrial machinery.
- Brass: Excellent machinability and electrical conductivity, used in fittings and electrical components.
- Copper: Superior thermal and electrical conductivity, perfect for heat exchangers and wiring systems.
- Titanium: High strength-to-weight ratio and corrosion resistance, ideal for aerospace and medical implants.
- Magnesium: The lightest structural metal, used where weight reduction is critical.
- Bronze: Good wear resistance, suitable for bushings and bearings.
- Nickel Alloys: Exceptional corrosion and heat resistance, used in chemical processing and power generation.
- Tool Steel: High hardness and abrasion resistance, perfect for cutting and drilling tools.
- Inconel: Maintains strength at high temperatures, ideal for jet engines and gas turbines.
We also machine plastics such as ABS, polycarbonate, nylon, POM (Delrin), and PTFE (Teflon). This variety ensures we can meet your performance requirements and budget constraints.
- ABS: Strong and impact-resistant, suitable for prototypes and consumer products.
- Polycarbonate: High toughness and transparency, used in safety equipment and optical applications.
- Nylon (PA) : Excellent mechanical properties and wear resistance, ideal for gears and bearings.
- POM (Delrin) : Low friction and high stiffness, used in precision parts like valves and pumps.
- PTFE (Teflon) : Exceptional chemical resistance and low friction, perfect for seals and gaskets.
- Polyethylene (PE) : Good chemical resistance and impact strength, used in containers and liners.
- Polypropylene (PP) : Resistant to fatigue, suitable for hinges and automotive components.
- PVC: Durable and corrosion-resistant, used in piping and electrical insulation.
- PEEK: High-temperature resistance and strength, ideal for aerospace and medical applications.
- Acrylic (PMMA) : Clarity and weather resistance, used in lenses and display cases.
- Ultem (PEI) : High strength and flame resistance, suitable for electrical and electronics industries.
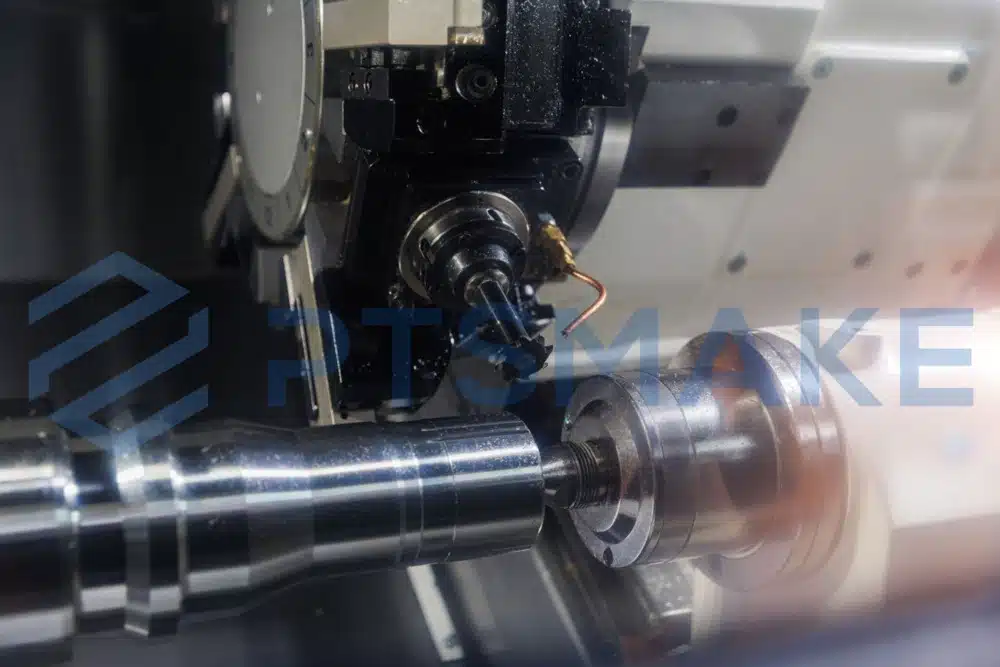
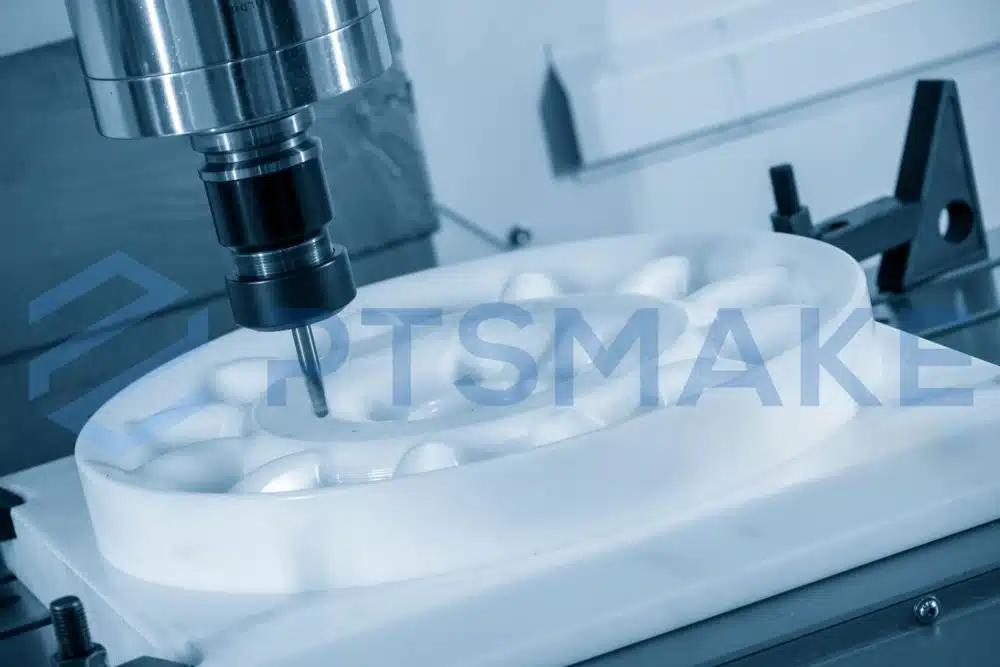
At PTSMAKE, our extensive material capabilities enable us to serve a broad spectrum of industries, including aerospace, automotive, medical, electronics, and more. We are dedicated to delivering precise and reliable CNC machined parts, regardless of complexity or material.
We understand that the choice of material is critical to the success of your product. That’s why we offer consultation services to help you select the most suitable material for your application. Our experts consider factors such as mechanical properties, environmental conditions, and regulatory requirements to guide you in making informed decisions.
We invite you to reach out to us to discuss your CNC machining needs. Together, we can explore the wide range of materials we offer and determine the best fit for your project. Our commitment is to exceed your expectations by providing exceptional quality and service.
Not sure which material is best for your project? Our engineers are here to help you choose the right material that meets your performance, durability, and cost requirements.
CNC Machining Parts Surface Finishes
At PTSMAKE, we offer a wide range of surface finishes for CNC machined parts to meet your specific requirements. Below are some of the most common options available, and we also provide custom finishes tailored to your needs. Selecting the right finish enhances the appearance, functionality, and durability of your parts.
- Surface Roughness: Ra 3.2μm / Ra 126μin
- Description: Our standard finish where parts are precisely machined and deburred. Sharp edges are slightly chamfered to remove burrs. Tool marks from the machining process are visible.
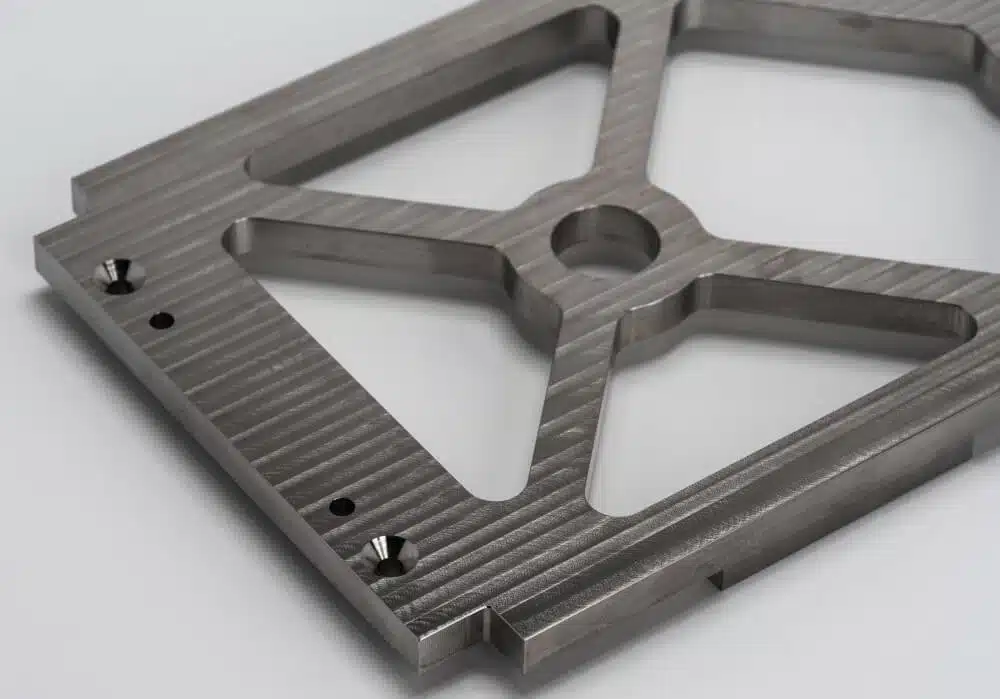
- Surface Roughness: Ra 1.6μm / Ra 63μin
- Description: Similar to the “As Machined” finish but with less noticeable machine marks. Achieved by machining with lower feed rates. No additional hand polishing is applied.
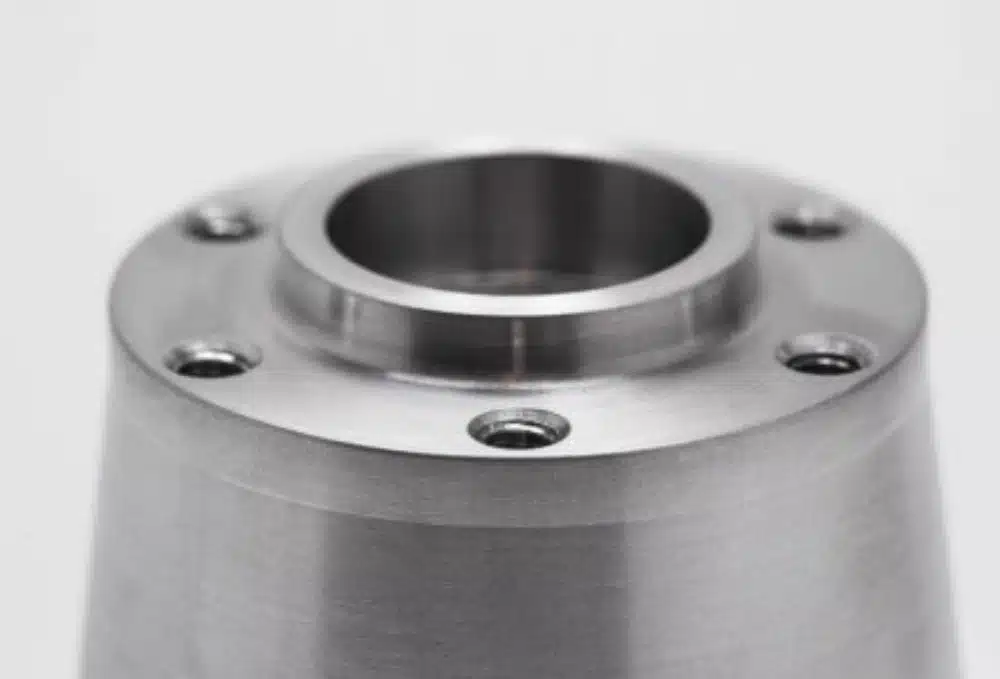
- Surface Roughness: N/A
- Description: A strong, wear-resistant finish applicable to all metal materials. Powder coating applies a durable layer of paint, offering various color options and textures. Enhances corrosion resistance and appearance.
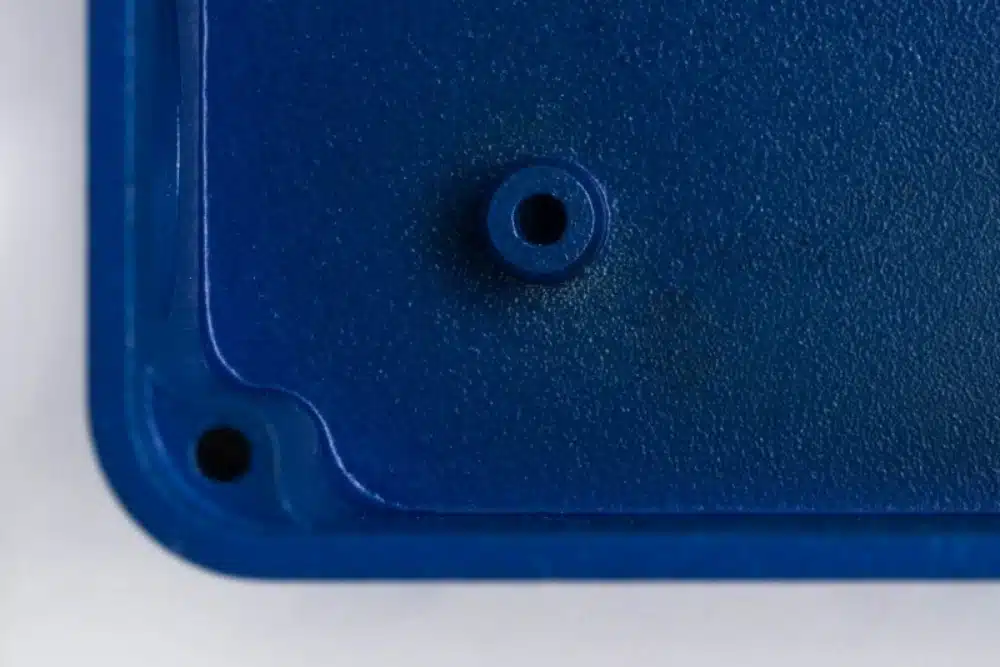
- Surface Roughness: Ra 0.1μm / Ra 3.94μin
- Description: Provides a highly reflective, mirror-like surface. Ideal for applications where a premium appearance is desired. Achieved through meticulous polishing processes.
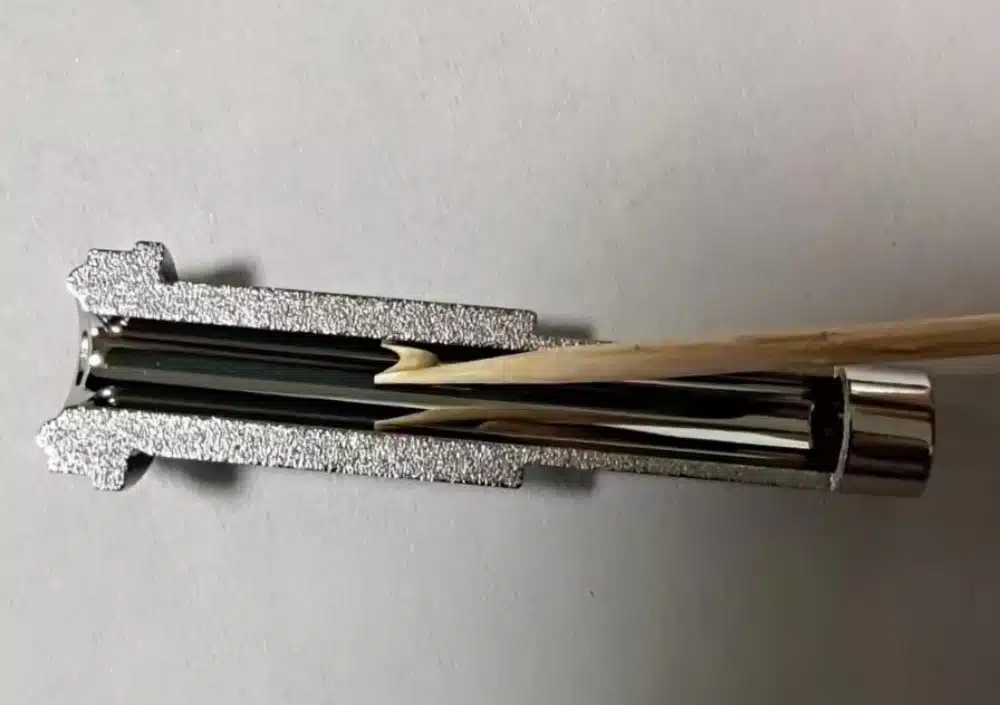
- Surface Roughness: N/A
- Description: Creates a uniform matte or satin surface by blasting the part with fine glass beads. This results in a smooth, grainy texture that reduces surface imperfections.
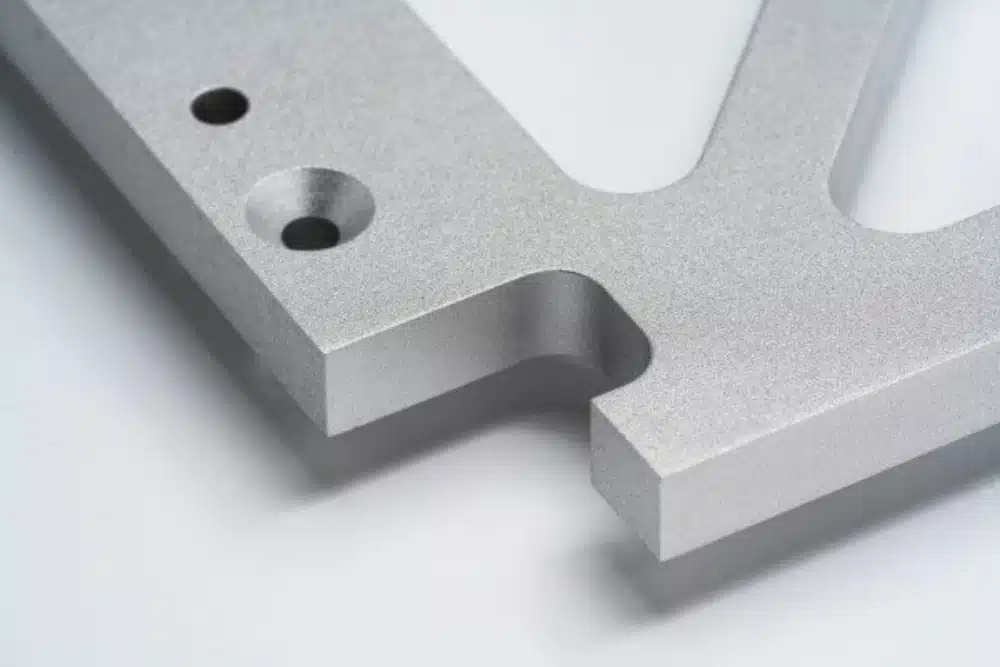
- Surface Roughness: Ra 1.2μm / Ra 47μin
- Description: Parts are brushed using fine abrasive belts to produce a satin finish. This process reduces surface roughness and provides a linear texture.
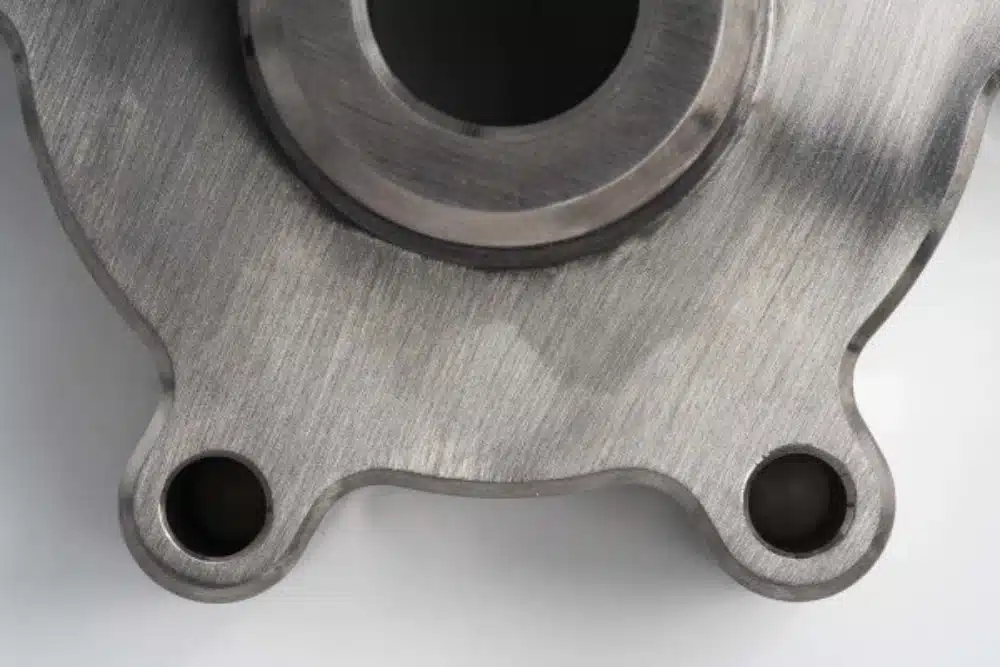
- Surface Roughness: N/A
- Description: Parts are first brushed to create a linear finish and then anodized to Type II standards. This results in a glossy, corrosion-resistant surface. Anodizing adds a thin, protective oxide layer, allowing for color customization.
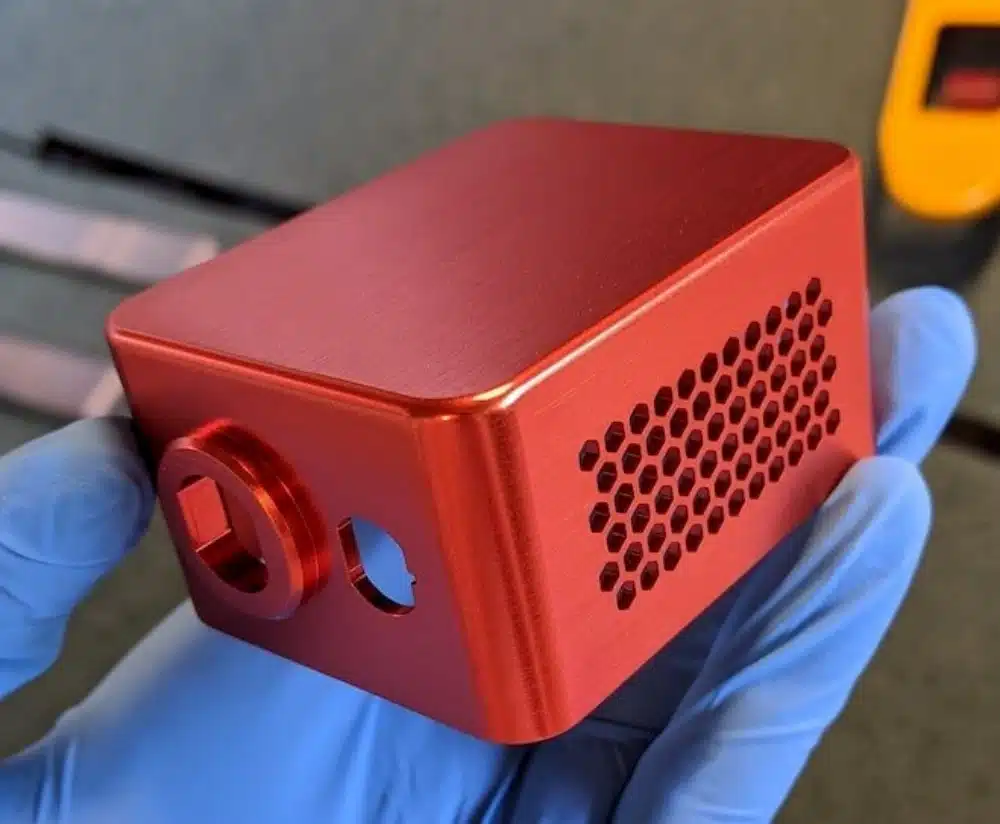
- Surface Roughness: N/A
- Description: Parts undergo bead blasting to achieve a matte texture and are then anodized Type II. This combination provides a durable, corrosion-resistant finish with a naturally matte appearance.
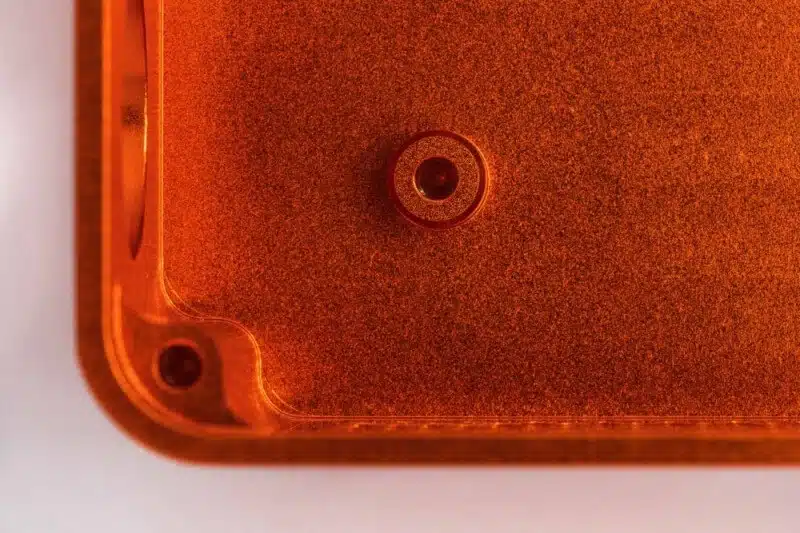
- Surface Roughness: N/A
- Description: Anodizing Type III creates a thicker oxide layer on aluminum parts, enhancing wear and corrosion resistance. Ideal for parts exposed to harsh environments or requiring increased durability.
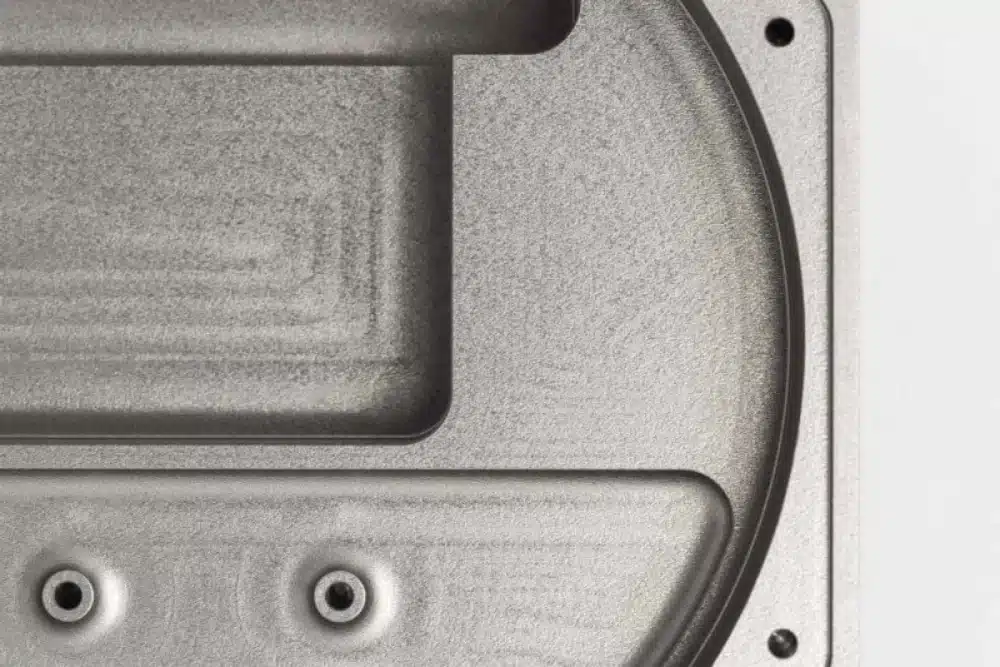
- Surface Roughness: N/A
- Description: A conversion coating applied to steel parts to improve corrosion resistance and minimize light reflection. Produces a smooth, black surface without significant dimensional changes.
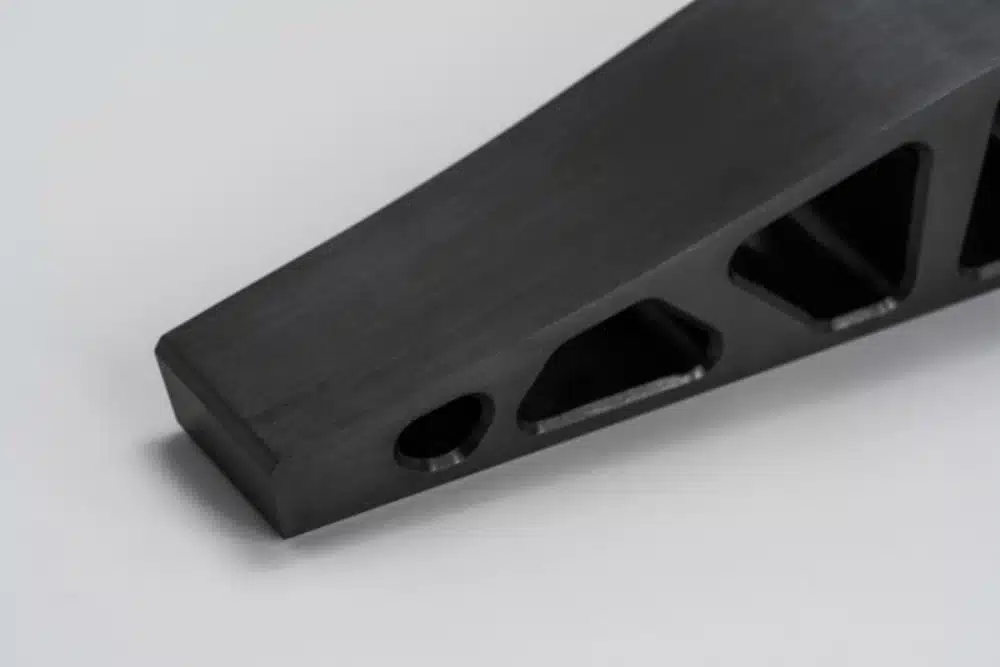
- Surface Roughness: N/A
- Description: Deposits a uniform nickel-phosphorus layer onto metal or plastic parts. Enhances hardness, wear resistance, and corrosion protection. Finish can range from matte to bright, depending on requirements.
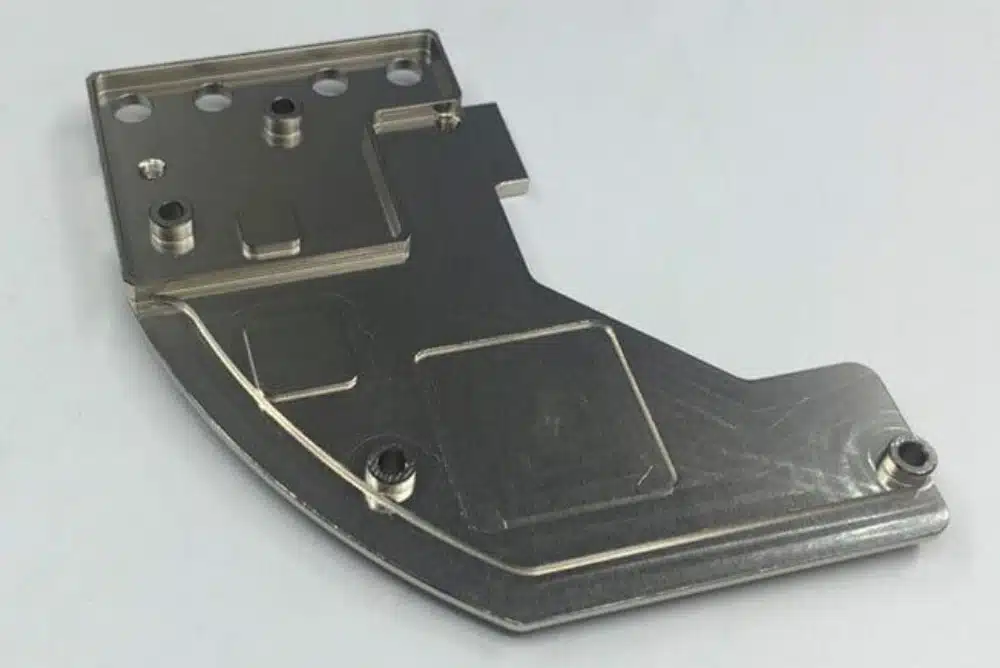
- Surface Roughness: N/A
- Description: Applied to aluminum parts to increase corrosion resistance while maintaining electrical conductivity. This finish is RoHS compliant and provides a good base for paints.
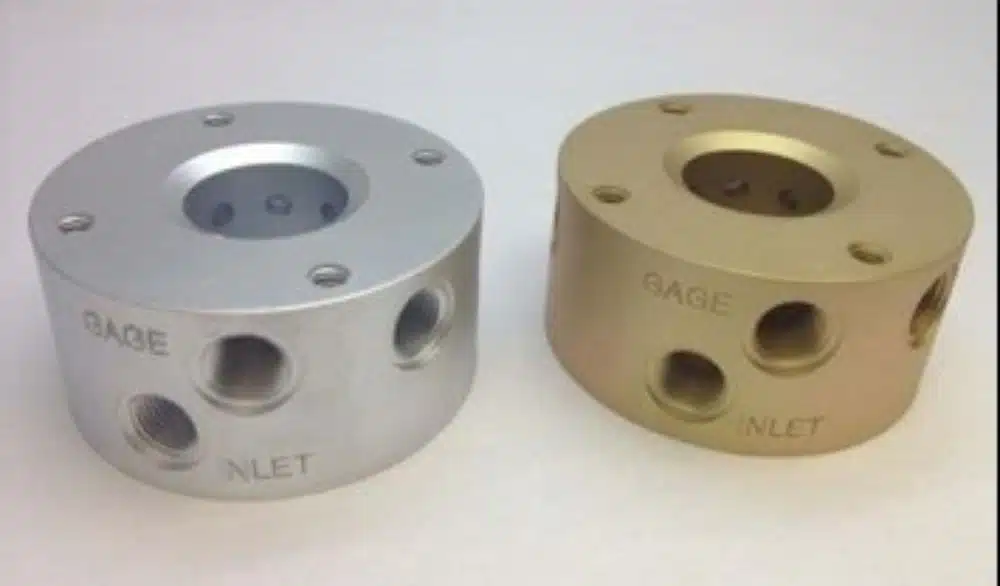
- Surface Roughness: Ra 0.8μm / Ra 32μin
- Description: Manual polishing in multiple directions to achieve a smooth and slightly reflective surface. Reduces micro-roughness and is suitable for parts requiring enhanced aesthetics.
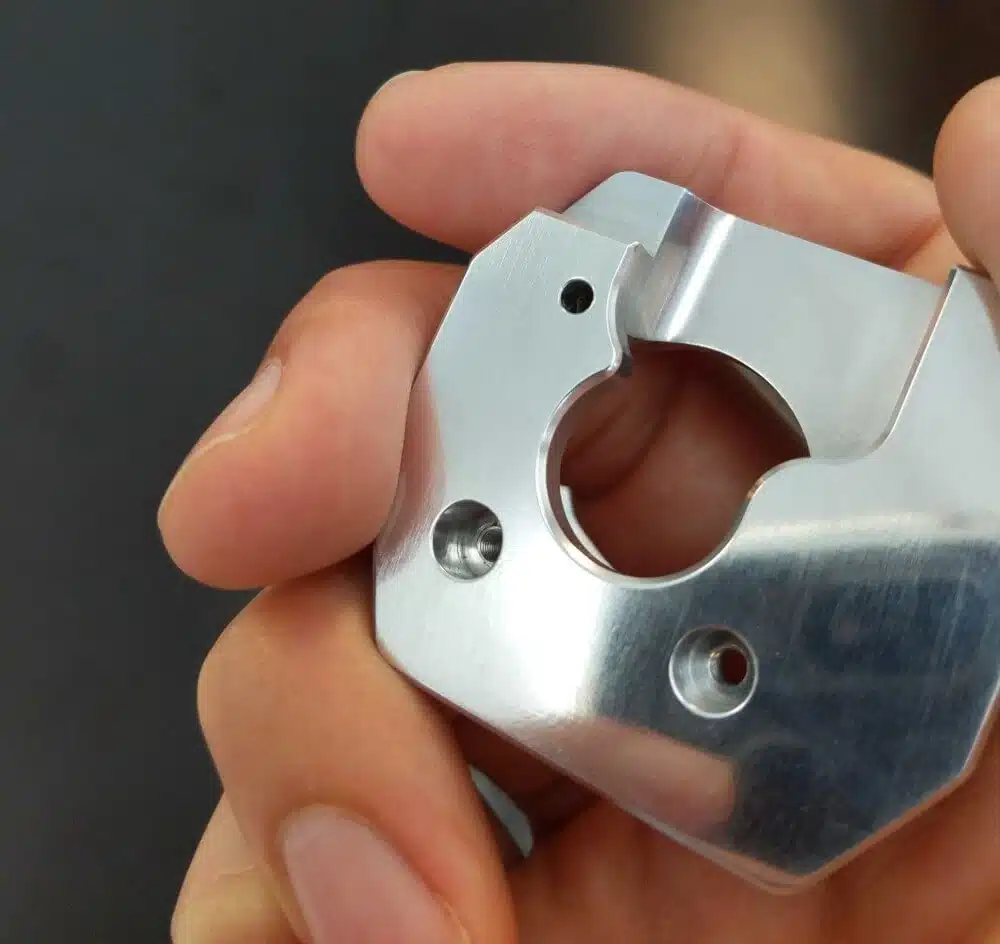
Request a Custom Quote Today
Get an accurate estimate for your cnc machining project. Let us help you meet your exact specifications.
Cost of CNC Machining Parts
At PTSMAKE, we understand that cost is a crucial factor when it comes to CNC machining services. We strive to provide high-quality components at competitive prices. Here is an overview of how we manage costs without compromising on quality.
Factors Influencing CNC Machining Costs
Several factors affect the cost of CNC machining. Understanding these can help in optimizing designs and reducing expenses.
- Material Selection: Different materials have varying costs and machining characteristics. Metals like aluminum are generally more cost-effective to machine compared to harder materials like titanium.
- Complexity of Design: Complex parts with intricate features require more machining time and specialized tools, increasing the cost.
- Tolerance and Precision Requirements: Parts that require tight tolerances and high precision may need additional machining processes, impacting the cost.
- Surface Finish and Post-Processing: Additional finishes like polishing, anodizing, or painting add to the overall expense.
- Quantity of Production: Higher production volumes can reduce the cost per unit due to economies of scale.
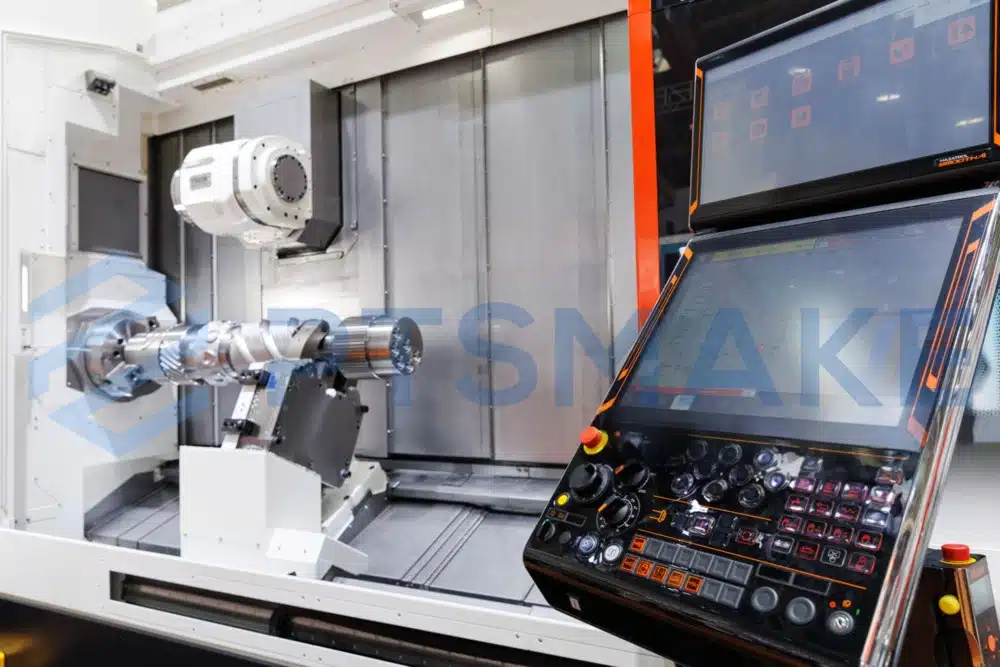
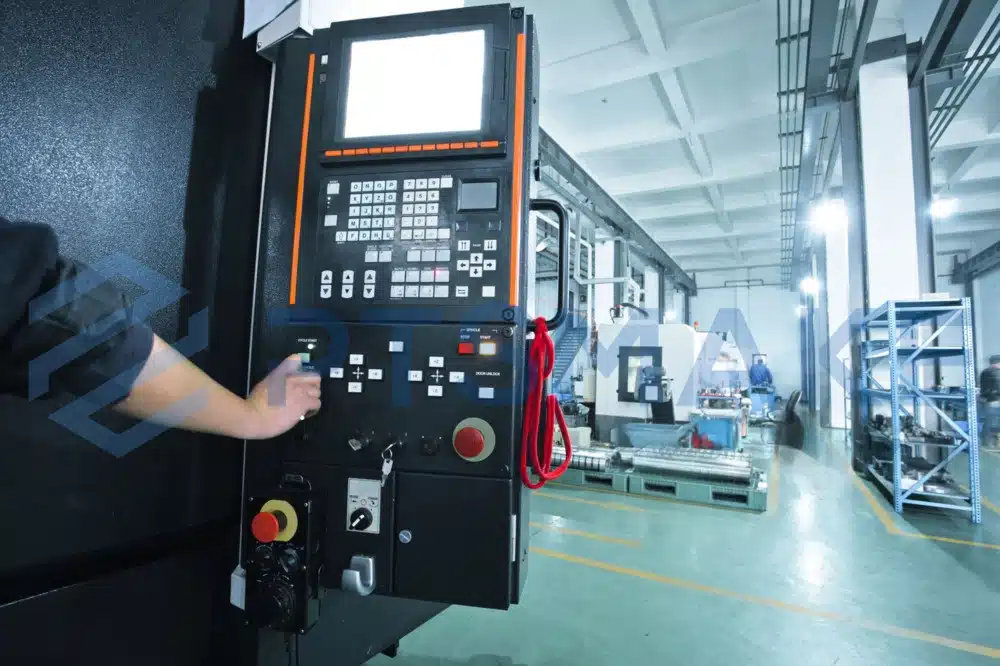
Our Cost-Effective Solutions
We are committed to offering cost-effective CNC machining services without sacrificing quality.
- Efficient Production Processes: We utilize advanced CNC machinery and optimized production techniques to reduce machining time and material waste.
- Material Optimization: Our experts help in selecting materials that meet performance requirements while being cost-effective.
- Design for Manufacturability: We provide guidance on designing parts that are easier and less expensive to machine.
- Bulk Production Benefits: We offer competitive pricing for larger orders, passing on the savings from bulk purchasing and production efficiencies.
Commitment to Quality and Value
Our focus is on delivering value to our customers through quality and affordability.
- Quality Assurance: We maintain strict quality control processes to ensure every part meets your specifications.
- Transparent Pricing: We provide clear and detailed quotations, so you understand the cost breakdown.
- Customer Collaboration: We work closely with you to find the best solutions that fit your budget and requirements.
- Continuous Improvement: We regularly review and improve our processes to find new ways to save costs and enhance quality.
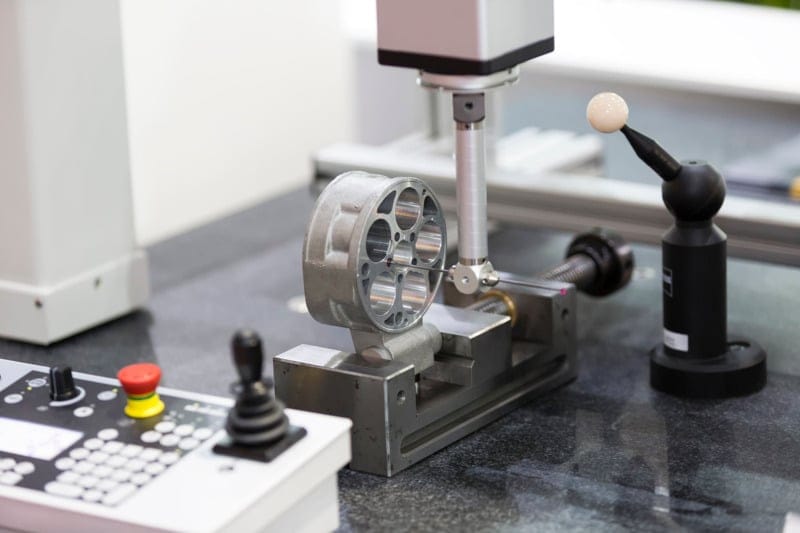
By choosing PTSMAKE for your CNC machining needs, you benefit from our dedication to providing high-quality parts at competitive prices. We are here to support your projects with cost-effective solutions and exceptional service.
Feel free to contact us to discuss your requirements and get a detailed quote. Let’s work together to bring your ideas to life while keeping costs under control.
Balancing Quality and Cost in CNC Machining
Finding the right balance between quality and cost in CNC machining is important for your business. High-quality parts ensure reliability, but managing expenses matters too. Here are strategies to help you achieve this balance:
1. Define Your Quality Requirements
Knowing exactly what quality you need helps in making cost-effective decisions.
- Identify Critical Features Focus on the aspects of your part that are essential for performance. This prevents unnecessary spending on non-critical areas.
- Set Appropriate Tolerances Specify tolerances that meet your needs without being too tight. Overly strict tolerances increase machining time and cost.
2. Choose Suitable Materials
Materials affect both quality and cost.
- Select Materials That Meet Your Needs Pick materials that offer the required strength and durability. Avoid using high-end materials if a standard option suffices.
- Consider Material Alternatives Explore different materials that provide similar properties at a lower cost.
3. Optimize Your Design
Designing with manufacturing in mind can reduce costs without sacrificing quality.
- Simplify Complex Features Simple designs are easier and cheaper to machine. Remove unnecessary complexities that do not add value.
- Use Standard Dimensions Standard sizes and features reduce machining time. This leads to cost savings.
4. Collaborate with Reliable Partners
Working with experienced CNC machining providers ensures quality.
- Assess Their Capabilities Choose a provider with the right expertise and equipment. This ensures they can meet your quality standards.
- Discuss Quality Control Measures Make sure they have strong quality assurance processes. Consistent quality reduces the risk of defects.
5. Communicate Clearly
Effective communication prevents misunderstandings that can affect quality and cost.
- Provide Detailed Specifications Share complete drawings and requirements. Clear information helps the provider understand your needs.
- Maintain Open Dialogue Stay in regular contact with your provider. This allows you to address issues promptly.
6. Plan Your Production Quantities
Order quantity influences the cost per part.
- Consider Larger Batches Bigger orders often reduce the unit price. Evaluate your needs to find the most cost-effective quantity.
- Schedule Production Wisely Allowing sufficient lead time can lower costs. Rushed orders may increase expenses.
7. Balance Lead Time and Quality
Time affects both cost and quality.
- Set Realistic Deadlines Giving your provider enough time helps maintain quality. Tight deadlines can lead to mistakes.
- Prioritize Based on Need Decide which parts need faster turnaround and which can wait. This helps in managing costs.
8. Evaluate Total Value
Look beyond the initial price to understand the overall value.
- Consider Longevity and Performance Investing in quality may save money in the long run. Durable parts reduce replacement costs.
- Weigh Cost Against Benefits Analyze how spending more or less affects your product. Aim for the best return on investment.
By considering these benefits, you can see how CNC machining addresses your needs. It offers precision, efficiency, and flexibility. These advantages help you deliver quality products to your customers, strengthening your position in the market.
Lead Time of CNC Machining Parts
Manufacturing time is critical for your projects. Delays can impact schedules and increase costs. Understanding the factors that affect manufacturing time in CNC machining can help you plan better and meet your deadlines.
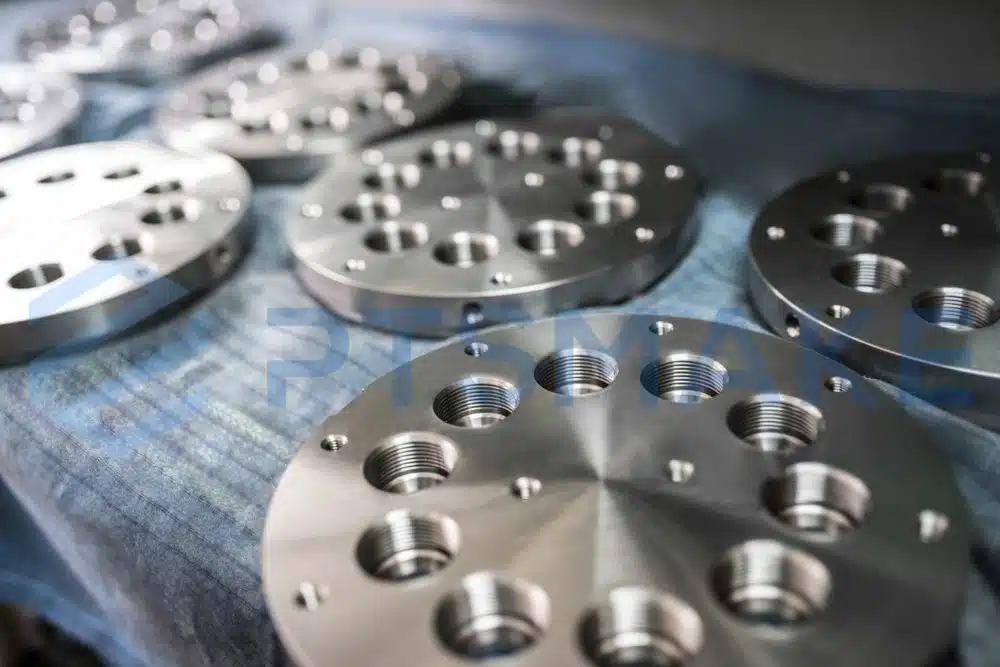
Factors That Influence Manufacturing Time
Several elements can affect how long it takes to produce your CNC machined parts:
- Design Complexity: Simple designs are quicker to produce. Complex parts with intricate details or tight tolerances require more time.
- Material Choice: Some materials are easier to machine than others. Hard or exotic materials may slow down the process.
- Order Quantity: Larger orders may benefit from economies of scale, but they also require more production time. Small batches or prototypes usually take less time per part.
- Additional Finishes: Processes like polishing, painting, or coating add extra steps and time to the production schedule.
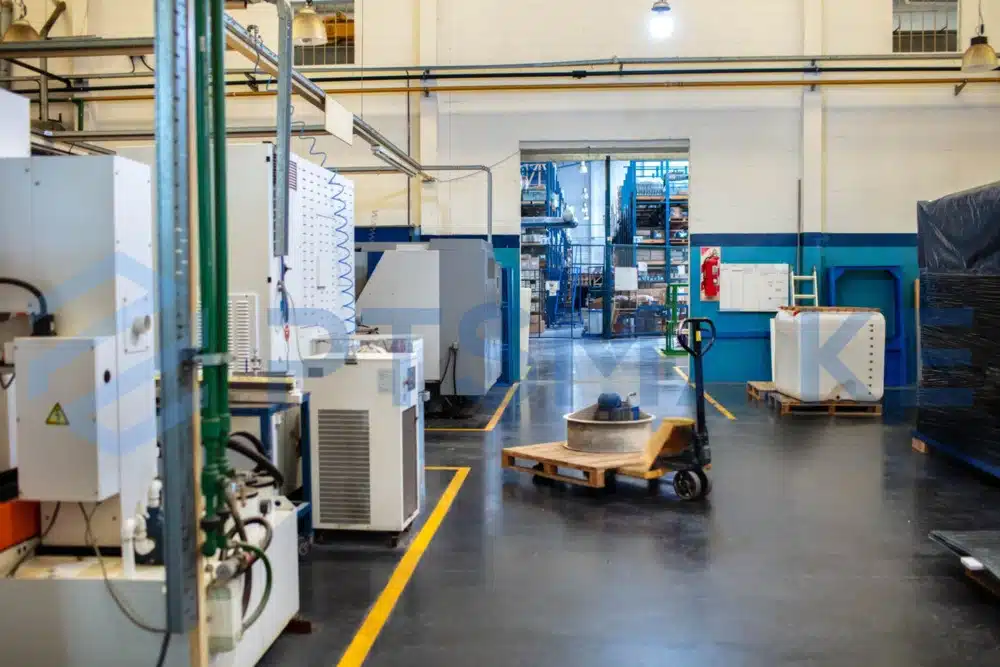
Tips to Reduce Manufacturing Time
You can take steps to shorten the manufacturing time:
- Optimize Your Design: Simplify your design where possible. Reducing unnecessary complexity can speed up machining.
- Select Machinable Materials: Choosing materials that are readily available and easy to machine can save time.
- Provide Clear Specifications: Detailed drawings and clear requirements help prevent delays caused by misunderstandings.
- Plan Ahead: Early communication about your deadlines allows for better scheduling and on-time delivery.
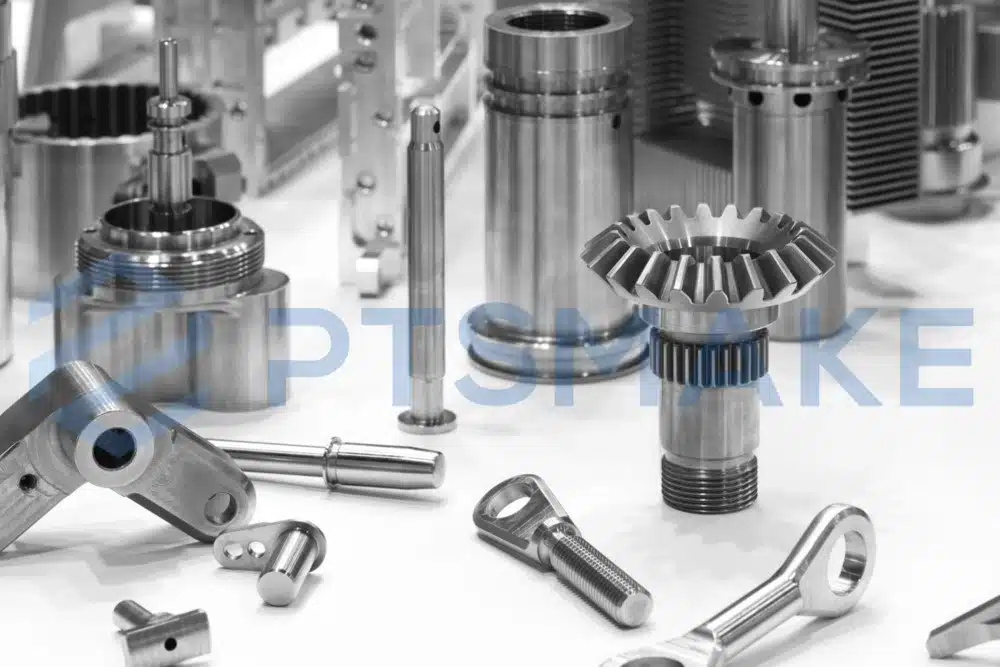
Our Commitment to Your Deadlines
Meeting your timelines is important. Here’s how we support you:
- Efficient Processes: We use advanced CNC machines that work fast without sacrificing quality.
- Experienced Team: Our skilled professionals manage projects effectively to avoid unnecessary delays.
- Flexible Scheduling: We can adjust our production schedule to prioritize urgent orders when needed.
- Transparent Communication: We keep you informed about the progress of your order so there are no surprises.
Our Production Capacity of CNC Machining
Understanding the exact capabilities of your CNC machining partner is crucial for your business. You need assurance that your projects will be handled efficiently and delivered on time. Here is detailed information about our production capacity, including specific numbers to highlight our capabilities.
Our Equipment and Facilities
- Extensive Machine Fleet: We operate 50+ advanced CNC machines, including multi-axis machining centers, turning centers, and high-speed milling machines. This variety allows us to handle complex designs and large production runs with precision.
- Large-Scale Production Space: Our facility spans over 10,000 square meters, providing ample space for efficient production workflows. Dedicated areas for machining, quality control, and finishing processes ensure streamlined operations.
- High Production Capacity: With the ability to operate 24/7, we can produce up to 300,000+ machined parts per week, depending on the complexity and size of the components. This means we can meet tight deadlines and accommodate large orders.
Our Workforce Capacity
- Experienced Technicians: We have a team of 25 skilled CNC machinists and technicians. Their expertise ensures that your parts are manufactured accurately and efficiently, adhering to your exact specifications.
- Dedicated Engineering Team: Our engineering department comprises 15 engineers who specialize in design optimization and process planning. They work closely with you to reduce production time and costs while maintaining quality.
- Quality Assurance Staff: A team of 12 quality inspectors conducts rigorous inspections at every production stage. This guarantees that each part we produce meets your standards for quality and performance.
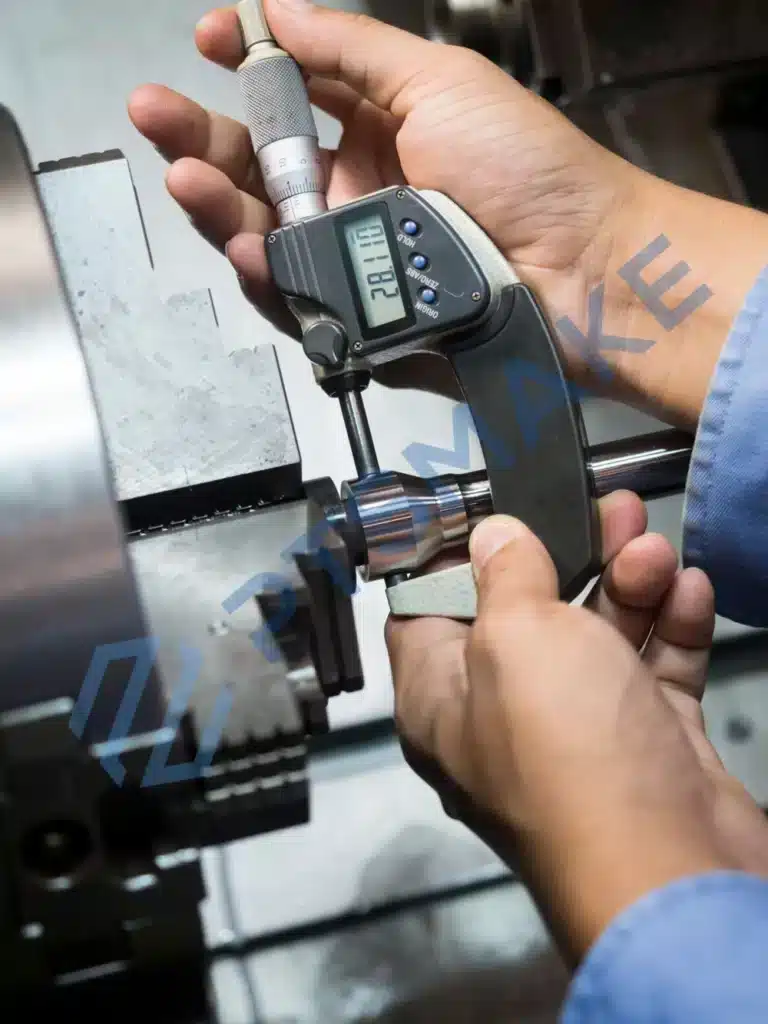
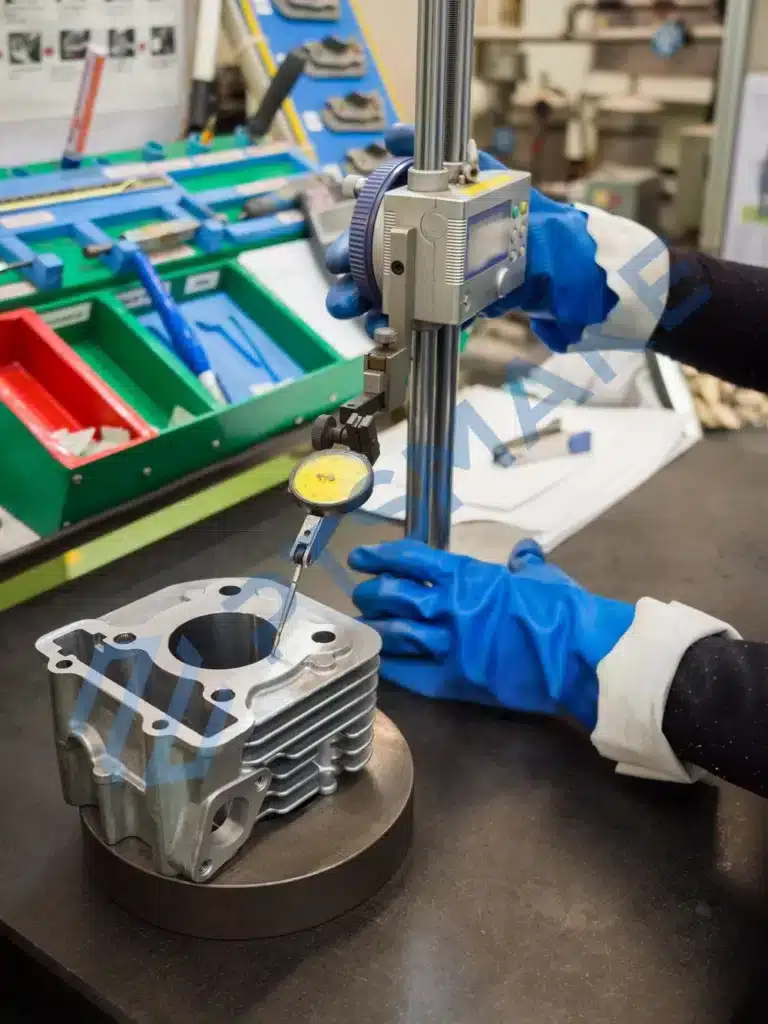
Ability to Handle Large Orders
- Scalable Production: Our substantial equipment and workforce allow us to scale production to meet your needs. Whether you require 50 or 500,000 units, we have the capacity to fulfill your order promptly.
- Efficient Manufacturing Processes: We utilize lean manufacturing principles and the latest scheduling software to optimize our production schedules. This minimizes lead times and ensures on-time delivery.
- High Production Capacity: With the ability to operate 24/7, we can produce up to 300,000+ machined parts per week, depending on the complexity and size of the components. This means we can meet tight deadlines and accommodate large orders.
Consistent Quality at Any Scale
- Certified Quality Management: We hold ISO 9001 certifications, reflecting our commitment to stringent quality control standards.
- Advanced Inspection Equipment: Our quality control utilizes precision instruments like CMMs (Coordinate Measuring Machines) and optical comparators to verify that each part meets your specifications.
Flexibility to Meet Your Needs
- Versatile Material Handling: We can machine a wide range of materials, including aluminum, steel, brass, and various plastics, allowing you to choose the best material for your application.
- Customized Solutions: Our flexible manufacturing systems enable us to accommodate special requests, be it for prototyping or adjustments in design.
Reliable Supply Chain
- Consistent Material Supply: Partnerships with reputable suppliers ensure we have uninterrupted access to high-quality materials, preventing delays in production.
- Effective Logistics: Our dedicated logistics team coordinates shipping and delivery, ensuring your parts arrive on time, wherever you are located.

By choosing us for your CNC machining projects, you gain a partner with substantial production capacity and a commitment to quality. Our advanced equipment, skilled workforce, and efficient processes enable us to complete your projects according to your timeline and specifications. This reliability allows you to focus on your core business objectives with confidence.
Please note: To provide exact figures and certifications, kindly supply the specific numbers and details you wish to include. This will help us ensure the information is accurate and tailored to your needs.
Contact CNC Machining Expert Today!
We look forward to the opportunity to work with you and contribute to your project’s success.
How Does CNC Machining Work?
Navigating the CNC machining process can seem complex. By understanding each step, you can make better decisions for your business. This knowledge helps ensure your parts are made to your exact needs. Here are eight key steps:
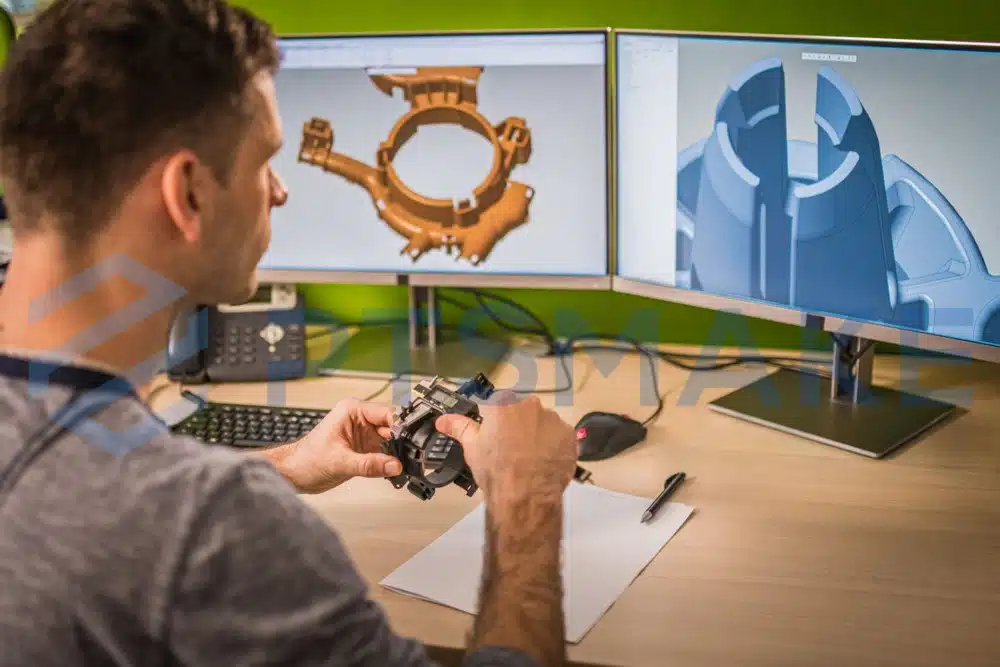
1. Reviewing and Optimizing Your Design
We examine your design carefully. We suggest improvements to enhance manufacturability and reduce costs.
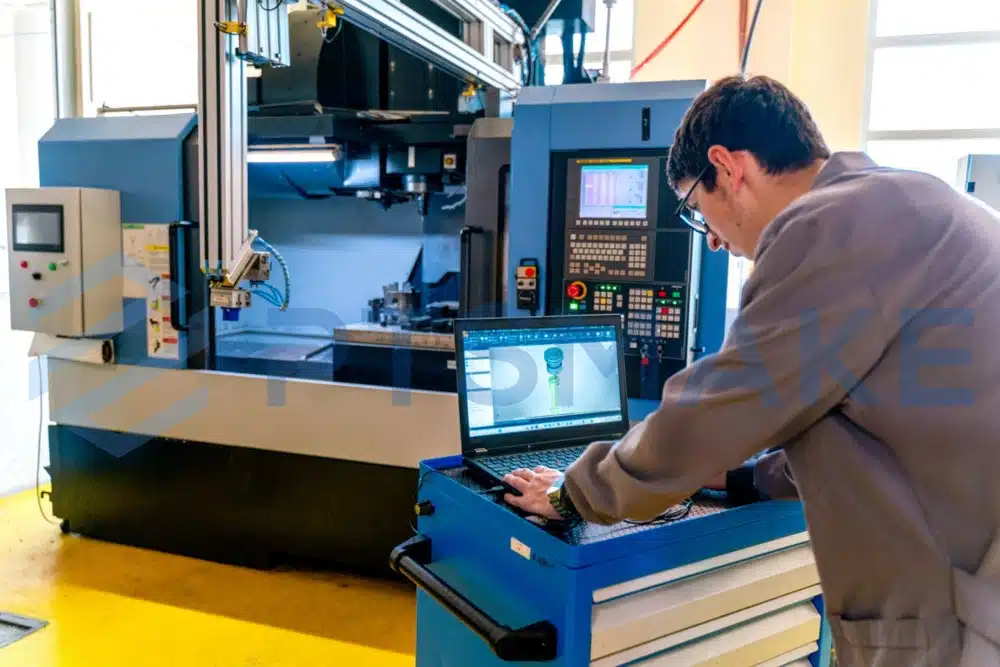
2. Converting the Design to CNC Code
The CAD model is translated into CNC code with CAM software. This code controls the machine’s movements.

3. Preparing the CNC Machine
The machine is set up with the correct tools and fixtures. Proper setup ensures accurate machining.
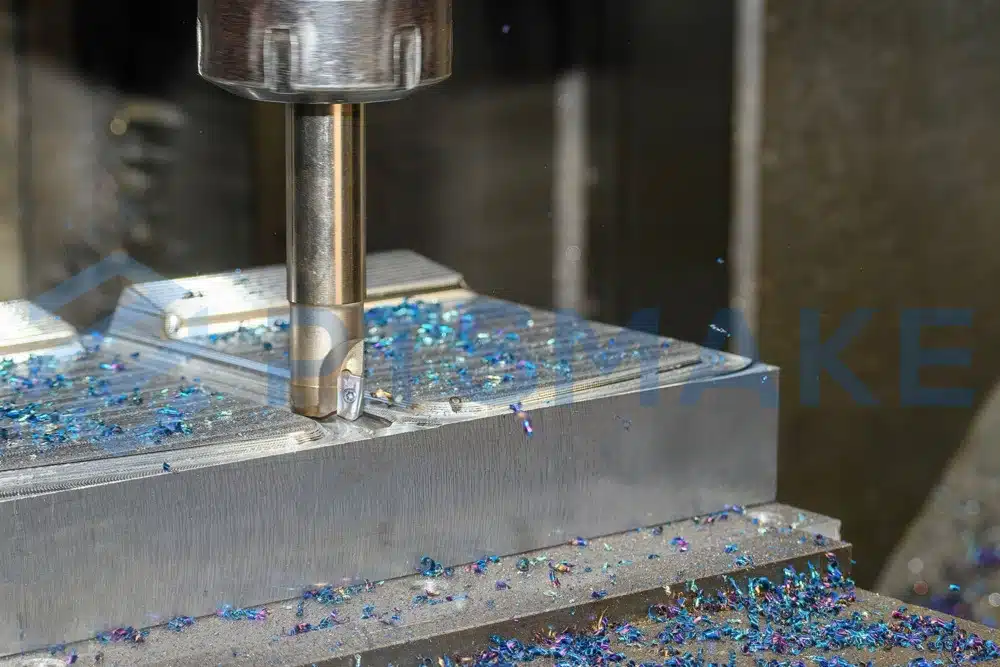
4. Securing the Material
The raw material, called the workpiece, is firmly fixed in the machine. This prevents movement during machining.
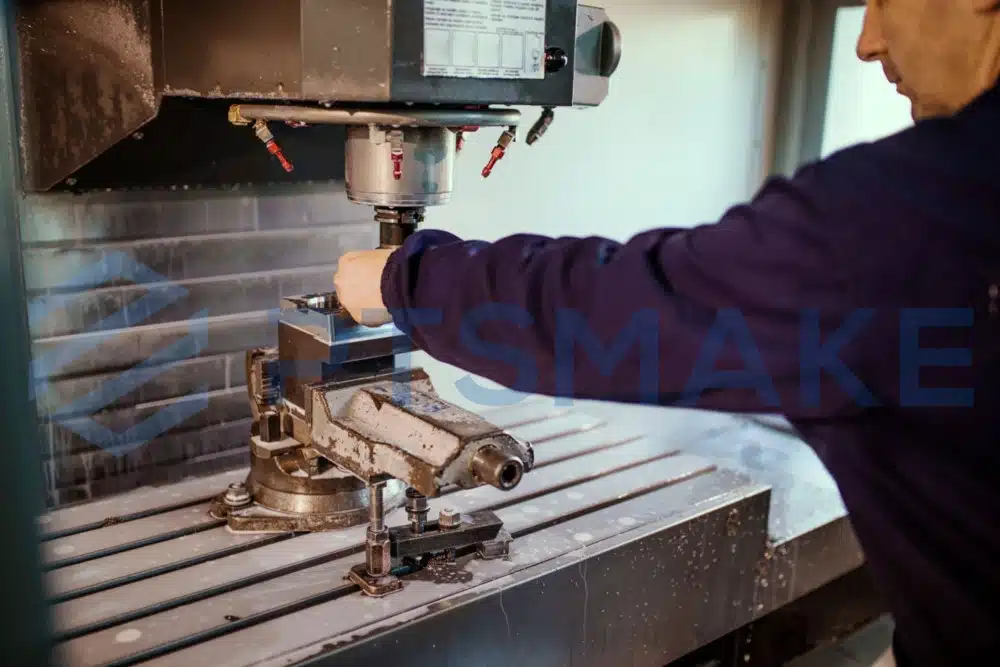
5. Running the CNC Program
The machine runs the CNC code to cut the material. It follows the path defined by the program.
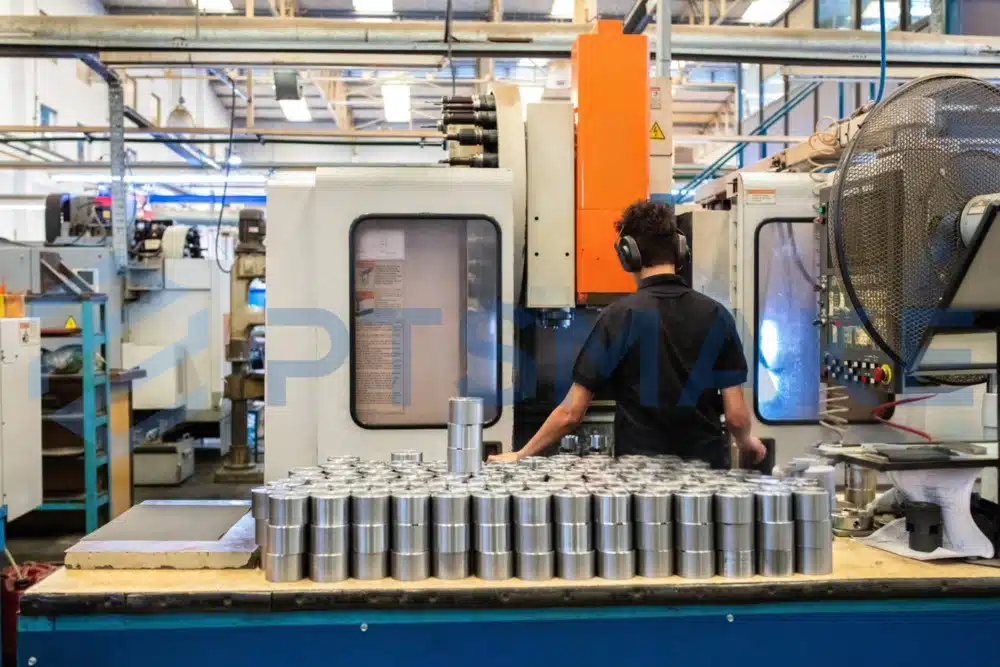
6. Monitoring the Process
The machining process is watched closely. Adjustments are made if needed to ensure quality.
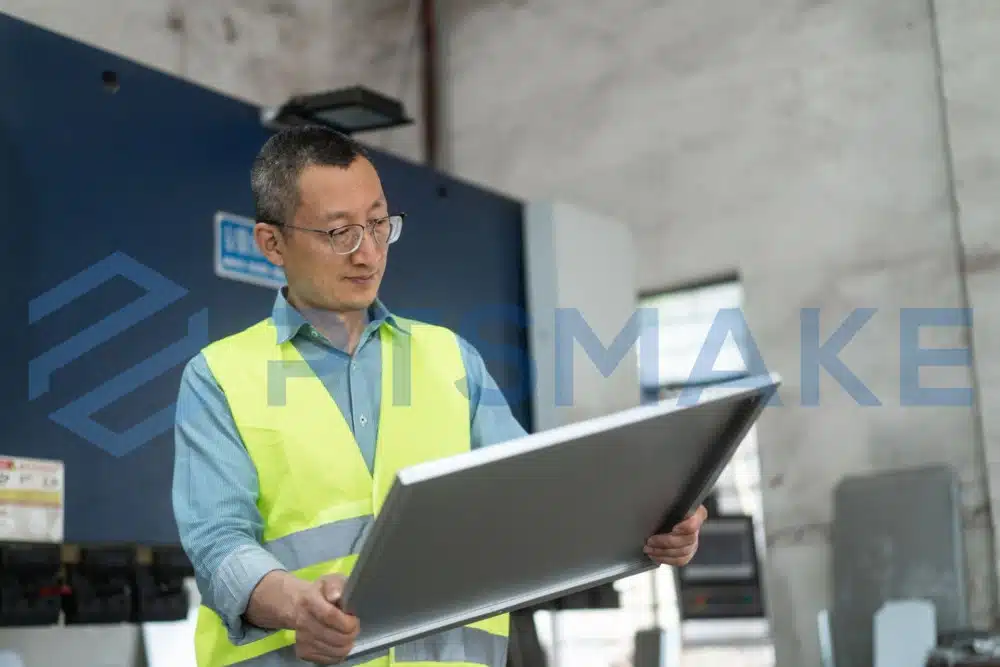
7. Removing and Inspecting the Part
The finished part is removed from the machine. It is checked for accuracy and any defects.
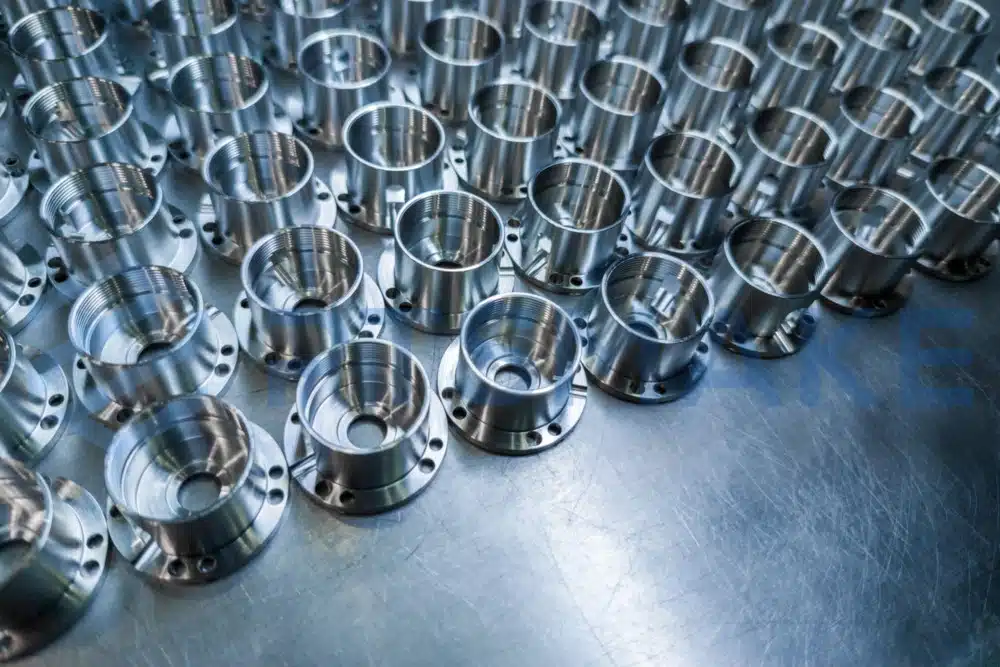
8. Finishing and Quality Control
Additional finishing processes may be applied. Final inspections ensure the part meets all requirements.
Effective Communication with CNC Machining Factories
1. Clearly Define Your Requirements
View Details
- Provide Detailed Specifications Share all measurements, tolerances, and material types. Precise information prevents mistakes.
- Share CAD Drawings and Models Offer complete drawings or 3D models. Visual aids make your requirements clear.
2. Establish Open Lines of Communication
View Details
- Choose Preferred Communication Methods Decide if you will use email, phone calls, or messaging apps. Select what works best for both parties.
- Set Regular Updates Schedule check-ins to discuss progress. Regular contact helps resolve issues quickly.
3. Understand Cultural and Language Differences
View Details
- Use Simple Language Avoid slang and complex terms. Clear language reduces misunderstandings.
- Be Mindful of Time Zones Consider time differences when scheduling meetings. This shows respect and improves cooperation.
4. Provide Prompt Feedback
View Details
- Review Samples Quickly Examine prototypes as soon as you receive them. Timely feedback helps make necessary adjustments.
- Communicate Changes Clearly If you need changes, explain them in detail. Clear instructions ensure the factory makes the right modifications.
5. Ask Questions When Uncertain
View Details
- Confirm Understanding If unsure about any aspect, ask the factory for explanation. It’s better to ask than to assume.
- Encourage Questions Invite the factory to ask you questions. This promotes mutual understanding.
6. Agree on Terms and Expectations
View Details
- Discuss Timelines and Deadlines Agree on schedules for production and delivery. Clear timelines keep the project on track.
- Clarify Quality Standards Explain your quality requirements. Ensure the factory knows what standards you expect.
7. Maintain Professional Relationships
View Details
- Respect Their Expertise Acknowledge the factory’s skills and knowledge. Mutual respect fosters better cooperation.
- Build Long-Term Partnerships A stable relationship can improve future projects. Consistency benefits both you and the factory.
8. Use Visual Aids When Possible
View Details
- Share Photos and Videos Images can highlight specific details. They help explain complex ideas simply.
- Utilize Collaboration Tools Use online platforms for sharing documents and updates. This keeps information organized and accessible.
Benefits of CNC Machining
In the manufacturing world, meeting high standards is a constant challenge. You need parts that are precise, consistent, and delivered on time. Errors and delays can harm your reputation and cost you money. You might wonder how to overcome these obstacles.
CNC machining offers a solution. It helps you produce quality parts efficiently. Here are the benefits that matter to you:
1. High Precision and Accuracy
You require parts that meet exact specifications. CNC machining provides exceptional precision.
- Consistent Results Machines follow precise instructions every time. Each part matches your design perfectly.
2. Consistency and Repeatability
Uniformity is crucial for your products. CNC machining ensures consistent quality in every part.
- Identical Production Every piece produced is the same as the last. This consistency helps in seamless assembly.
3. Efficiency and Speed
Meeting tight schedules is important. CNC machining increases production speed.
- Fast Production Machines work quickly and continuously. This reduces production time and helps you meet deadlines.
4. Ability to Handle Complex Designs
Your projects may involve intricate designs. CNC machining can create complex shapes with ease.
- Complex Geometries Machines can produce detailed and intricate parts. This allows you to innovate without design limitations.
5. Scalability and Flexibility
Your production needs can change. CNC machining adapts to different volumes.
- From Prototypes to Large Batches You can produce one item or thousands. This flexibility helps you manage varying demands.
6. Reduced Human Error
Mistakes can be costly. CNC machining minimizes errors.
- Automated Precision Machines follow programmed instructions. This reduces the risk of mistakes compared to manual processes.
7. Cost-Effectiveness Over Time
Managing costs is important for your business. CNC machining can save money in the long run.
- Lower Labor Costs Automation reduces the need for manual labor. This decreases production expenses over time.
8. Wide Range of Materials
Different projects require different materials. CNC machining works with many types.
- Various Metals and Plastics You can choose from metals like aluminum and steel or plastics. This versatility meets your specific needs.
9. Improved Safety
Safety is a priority in your operations. CNC machining reduces risks.
- Less Manual Handling Machines handle the work, reducing the chance of accidents. This makes the production environment safer.
10. Better Quality Control and Documentation
Maintaining high standards is crucial. CNC machining helps with detailed records.
- Traceability Machines keep precise data. This helps you track production and ensure quality.
By considering these benefits, you can see how CNC machining addresses your needs. It offers precision, efficiency, and flexibility. These advantages help you deliver quality products to your customers, strengthening your position in the market.
CNC Machining Applications
Aerospace
- Read More
Automotive
- Read More
Medical
- Read More
Consumer Products
- Read More
Industrial Machinery
- Read More
Electronics
- Read More
Hot Runner
- Read More
Telecommunications
- Read More
CNC Machining FAQs
What materials can be machined?
A wide range of materials can be machined, including metals like aluminum, steel, brass, and plastics like ABS, nylon, and acrylic.
What tolerances can be achieved?
Tight tolerances up to ±0.002 mm can be achieved, ensuring parts meet exact specifications.
How much does CNC machining cost?
Costs depend on factors like material, complexity, and quantity. Detailed quotes are provided based on specific requirements.
What is the typical lead time for CNC machined parts?
Lead times vary based on the project. Prototypes often take 1-2 weeks, and production runs may take 3-4 weeks.
Is there a minimum order quantity?
There is no minimum order quantity. Single prototypes or large production runs can be accommodated.
Can large volume orders be handled?
Yes, production can scale to meet demands from small batches to large volumes.
Are prototypes or small batch production offered?
Yes, prototyping services and small batch production are available to test designs before large-scale manufacturing.
Can complex shapes and designs be machined?
Yes, CNC machines can create complex geometries and intricate parts based on precise designs.
Are finishing services like painting or anodizing available?
Yes, various finishing services are offered, including painting, anodizing, plating, and polishing.
What certifications are held?
Certifications such as ISO 9001 are maintained, demonstrating a commitment to quality management.
How is intellectual property and confidentiality handled?
Intellectual property is respected. Non-disclosure agreements can be signed to protect designs.
Is design assistance or engineering support offered?
Yes, engineers can assist with design optimization to improve manufacturability and reduce costs.
How can designs or drawings be submitted for quotation?
Designs can be sent in formats like DWG, DXF, XT, or STEP. They will be reviewed, and a quote will be provided.
How are shipping and logistics handled?
Shipping and logistics are managed, with worldwide shipping available through reliable carriers.
Is international shipping offered?
Yes, shipping to countries worldwide is available, ensuring parts arrive safely and on time.
How are customs and import/export regulations handled?
Customs and regulations are managed, providing necessary documentation for smooth shipping.
What are the benefits of using CNC machining over other methods?
CNC machining offers high precision and repeatability. It is suitable for complex parts and various materials.
Are emergency or rush services available?
Yes, orders can be expedited if needed. Requirements can be discussed to accommodate urgent needs.
How do I get a quote for my CNC machining project?
You can send us your design files and specifications. We will review them and provide a detailed quote based on material, complexity, and quantity.
What if I need to make changes after production has started?
If changes are needed, please inform us as soon as possible. We will assess the impact on cost and schedule and work with you to adjust the order.
Can you machine parts with tight tolerances and high precision?
Yes, we specialize in producing high-precision parts with tight tolerances, ensuring your parts meet exact requirements.
Can you work with specialized or uncommon materials?
Yes, we can work with a variety of materials, including specialized metals and plastics. Let us know your requirements, and we will advise accordingly.
What happens if the parts do not meet my specifications?
If parts do not meet agreed specifications, we will investigate the issue. We will provide solutions such as reworking the parts or producing new ones.