Is Extrusion An Expensive Process?
Many manufacturers struggle when deciding whether extrusion is right for their project because of cost concerns. I’ve seen clients hesitate to choose extrusion, worried about high tooling investments and uncertain if the process will be economically viable for their production needs.
Extrusion is generally not expensive compared to other manufacturing processes. While initial tooling costs range from $2,000-$10,000, the per-part costs become very economical at higher volumes, often dropping to cents per part, making it cost-effective for medium to high-volume production.
Let me break down exactly why extrusion can be surprisingly economical for the right projects. I’ve helped dozens of clients at PTSMAKE save significantly by choosing extrusion for appropriate applications. The key is understanding when this process makes financial sense and how to optimize your designs to take advantage of its cost efficiency. Keep reading to discover if extrusion could be your most cost-effective manufacturing solution.
How Much Does Custom Aluminum Extrusion Cost?
Ever tried to budget for a custom aluminum extrusion and found the pricing surprisingly variable? Getting a straightforward cost seems challenging when your design is unique, right?
Custom aluminum extrusion costs depend heavily on factors like the complexity of the extrusion die (tooling), the specific aluminum alloy chosen, the intricacy of the profile design, the total order quantity, and any required finishing touches. While there’s an initial investment for the die, the cost per part often drops significantly with higher production volumes.
Let’s dig a bit deeper into what drives these costs. Pinpointing the exact price requires understanding how different elements interact. Based on project experience at PTSMAKE, we know that several key factors consistently influence the final quote you receive from an Aluminum Extrusion Manufacturer.
Understanding the Core Cost Drivers
Breaking down the costs helps clarify where your budget is going and where potential savings might lie.
Tooling (Die) Investment
The extrusion die is the custom tool that shapes the aluminum. Its cost is a primary factor, especially for new profiles. More complex shapes, tighter tolerances, or larger profiles generally mean a more expensive die. However, this is usually a one-time cost, and understanding die amortization1 shows how this investment spreads across the total parts produced, significantly lowering the per-part cost over larger runs.
Materialeomkostninger
Aluminum isn’t just aluminum. The specific alloy (like 6061 or 6063) impacts the price based on its properties and market availability. Naturally, the weight of the aluminum profile itself is also a major component – heavier or larger profiles use more raw material. Market fluctuations in aluminum prices can also play a role.
Profile Complexity and Tolerances
An intricate design with many cavities, thin walls, or exceptionally tight dimensional tolerances requires more precise tooling and slower extrusion speeds. This increases manufacturing difficulty and can influence the cost. Simpler profiles are generally less expensive to produce.
Bestillingsmængde
Like most manufacturing processes, volume matters. Initial setup costs and the die investment are spread over the number of units produced. Higher quantities typically result in a lower cost per extruded foot or part. Small runs will inevitably have a higher unit cost.
Finishing and Secondary Operations
Does your part need anodizing, powder coating, special cutting, drilling, or CNC machining after extrusion? Each additional step adds value but also contributes to the final cost. Define these needs early on for an accurate quote.
Here’s a quick summary table:
Cost Driver | Primary Influence | Potential Impact on Unit Cost |
---|---|---|
Tooling (Die) | Profile Complexity, Size | High (Initial), Low (Amortized) |
Aluminiumslegering | Market Price, Specific Alloy Selected | Medium |
Profilens kompleksitet | Design Intricacy, Tolerances | Middel til høj |
Bestillingsmængde | Volume of Parts | High (Lower volume), Low (Higher volume) |
Finishing/Secondary | Anodizing, Coating, Machining etc. | Low to High (Depends on needs) |
Working with an experienced partner like PTSMAKE can help navigate these factors, potentially optimizing your design for better cost-efficiency without compromising function.
What Is The Demand For Aluminum Extrusion?
Ever wonder just how widespread the use of aluminum extrusions really is? Are you trying to understand if this versatile material has a solid future in various industries?
The demand for aluminum extrusion is robust and steadily growing across multiple sectors globally. Key drivers include the construction, automotive (particularly electric vehicles), industrial machinery, and consumer electronics industries, valuing its lightweight, strength, corrosion resistance, and recyclability.
Let’s explore where this demand is coming from. Understanding the specific applications and trends helps paint a clearer picture of why aluminum extrusions are so sought after. In my experience working with various clients at PTSMAKE, the versatility of aluminum extrusion is its core strength, driving adoption in unexpected places.
Key Industries Driving Demand
Several major industries rely heavily on aluminum extrusions, each leveraging its unique properties.
Building and Construction
This sector is arguably the largest consumer. Think window frames, door frames, curtain walls, and structural components. Aluminum’s resistance to weather, low maintenance, and ability to be formed into complex shapes make it ideal. The push towards energy-efficient buildings also boosts demand for thermally broken aluminum profiles. Many projects we’ve consulted on at PTSMAKE specifically require custom profiles for unique architectural designs, showcasing the need for a capable Aluminum Extrusion Manufacturer.
Biler og transport
Weight reduction is critical here, especially with the rise of electric vehicles (EVs) seeking longer range. Aluminum extrusions are used in battery enclosures, body structures, chassis components, and trim. Its high strength-to-weight ratio helps improve fuel efficiency and performance. We’ve observed a significant uptick in inquiries for complex profiles like 6061-T62 for automotive applications.
Industrielle anvendelser
From factory automation equipment frames and conveyor systems to heat sinks for machinery and electronics, aluminum extrusions provide structural integrity and design flexibility. The ease of assembly using T-slot profiles, for example, is a major advantage.
Consumer Goods and Electronics
You’ll find extrusions in appliances, furniture, lighting fixtures, and electronic casings (like laptop bodies or smartphone frames). The aesthetic appeal and durable finish options (like anodizing or powder coating) are key factors here.
Here’s a quick look at the main drivers:
Industri | Key Demand Drivers | Trend Outlook |
---|---|---|
Konstruktion | Architectural Design, Energy Efficiency, Durability | Strong Growth |
Biler | Lightweighting (EVs), Safety, Performance | High Growth |
Industriel | Modularity, Strength, Heat Dissipation | Steady Growth |
Forbrugsgoder | Aesthetics, Durability, Miniaturization | Moderate Growth |
The overall trend points towards continued strong demand, fueled by innovation and the inherent advantages of aluminum as a material. Partnering with a knowledgeable Aluminum Extrusion Manufacturer ensures you can leverage these benefits effectively for your specific needs.
Why Is It Called 80/20 Aluminum?
Ever found yourself wondering about the name "80/20 Aluminum"? It sounds quite specific, almost like a formula, but its origin often seems unclear, right?
The term "80/20 Aluminum" primarily refers to a modular T-slot aluminum extrusion framing system, popularized by the company 80/20 Inc. The name itself is inspired by the Pareto principle, or the 80/20 rule, reflecting the system’s efficiency and versatility rather than a specific aluminum composition.
Let’s break down this naming convention a bit more. It’s a common point of confusion, as many initially assume it relates to the material properties or dimensions. However, the reality is more about a philosophy and a product system. Understanding this distinction is key, especially when you’re considering different structural aluminum options for your projects.
The Pareto Principle Connection
The core idea comes from the Pareto principle, often called the 80/20 rule. This principle suggests that roughly 80% of effects come from 20% of causes.
How 80/20 Inc. Applied It
The founders of 80/20 Inc. adopted this name to embody the idea that their modular framing system provided a highly efficient solution – perhaps implying that 80% of framing solutions could be achieved with 20% of the traditional effort or components, thanks to the system’s flexibility. It speaks to the versatility and problem-solving power of their T-slot aluminum extrusion system.
It’s About the System, Not the Alloy
It’s crucial to understand that "80/20" doesn’t define the type of aluminum alloy used.
Almindelige misforståelser
Many engineers initially think "80/20" might refer to:
- An 80% aluminum, 20% other metals mix (Incorrect).
- A specific profile dimension (Incorrect – profiles come in many sizes).
- A specific series of aluminum (Incorrect – typically uses alloys like 6105-T5 or 6063-T6, common in structural extrusions).
The system revolves around extruded aluminum profiles with a distinctive T-slot profile3, allowing components to be easily connected using specialized fasteners. This modularity is the defining characteristic.
%[Silver aluminum T-slot profiles used by a structural extrusion manufacturer](
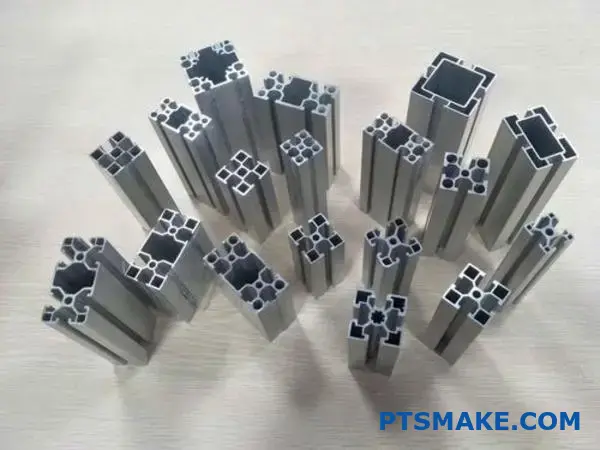
"T-Slot Aluminum Extrusion Profiles")
What Defines the System?
Funktion | Beskrivelse | Implication |
---|---|---|
Modularitet | Components easily connect and disconnect using T-slots and fasteners. | High flexibility, reconfigurable structures. |
Ekstrudering | Profiles created via aluminum extrusion, ensuring strength and consistency. | Lightweight yet strong, complex shapes possible. |
Alsidighed | Used for machine guarding, frames, workstations, automation structures, etc. | Broad application range across industries. |
Effektivitet | Faster assembly compared to welded steel structures. | Potential reduction in labor time and cost. |
While 80/20 Inc. popularized the system and the name, the concept of T-slot aluminum extrusions is now widely adopted. Many companies, including reliable Aluminum Extrusion Manufacturer partners like us at PTSMAKE, produce similar compatible profiles. When discussing "80/20 type" aluminum, people usually refer to this modular T-slot system in general, regardless of the specific manufacturer. Understanding the origin helps clarify that you’re looking for a type of system, not a specific material blend.
What Are The Defects Of Aluminum Extrusion?
Have you ever received extruded parts only to find unexpected flaws that compromise their function or appearance? Dealing with imperfections after production can be frustrating and costly, right?
Common defects in aluminum extrusion include surface issues like scratches, die lines, and blisters; dimensional problems such as twisting, warping, and incorrect angles; and internal structural flaws like voids, cracks, or poor metallurgical bonds4.
While aluminum extrusion is a highly effective process, like any manufacturing method, it’s not immune to potential defects. Understanding these common issues is the first step toward preventing them. Based on project experience at PTSMAKE, identifying the root cause is crucial for implementing corrective actions and ensuring consistent quality from your Aluminum Extrusion Manufacturer.
Common Surface Imperfections
These defects are visible on the exterior of the extrusion and often affect aesthetics and potentially surface treatments.
Scratches and Handling Marks
These can occur during extrusion, cooling, stretching, or transportation if profiles aren’t handled carefully. Proper equipment maintenance and handling protocols are essential.
Die Lines
Fine, parallel lines running along the extrusion length. They are usually caused by imperfections or wear on the die bearing surface. Minor lines are often acceptable, but heavy lines indicate die issues.
Blisters or Bubbles
Raised areas on the surface, often caused by trapped gases (like hydrogen) in the aluminum billet or moisture introduced during the process.
Dimensional and Shape Deviations
These relate to the profile not matching the specified geometric tolerances.
Twisting and Warping
The extrusion doesn’t remain straight along its length. This often results from uneven cooling after exiting the die or improper stretching.
Incorrect Dimensions or Angles
Sections of the profile are thicker, thinner, or angled incorrectly compared to the design specifications. This usually points back to die design or wear issues.
Internal Structural Problems
These defects are within the material itself and can impact the part’s strength and integrity.
Voids and Porosity
Small internal cavities caused by gas entrapment or shrinkage during solidification. Billet quality and process control are key prevention factors.
Sprækker
Internal or surface cracks can arise from excessive stress during extrusion or cooling, or from issues with the alloy itself.
Here’s a quick summary table:
Defect Category | Specific Examples | Potential Causes |
---|---|---|
Overflade | Scratches, Die Lines, Blisters | Handling, Die Wear, Trapped Gas/Moisture |
Dimensional/Shape | Twisting, Warping, Off-Spec | Uneven Cooling, Stretching Issues, Die Design/Wear |
Intern struktur | Voids, Cracks, Poor Bonds | Gas Entrapment, Shrinkage, Stress, Alloy Quality |
Partnering with a meticulous Aluminum Extrusion Manufacturer involves clear communication about acceptable quality standards and thorough inspection processes to catch these potential defects early.
What Certifications Should A Quality Aluminum Extrusion Manufacturer Have?
Ever feel overwhelmed trying to decipher which certifications actually guarantee a manufacturer’s quality? Does seeing a logo make you wonder if it truly reflects consistent, reliable production?
A quality Aluminum Extrusion Manufacturer should, at minimum, hold ISO 9001 certification, demonstrating a robust quality management system. Depending on the industry served, certifications like IATF 16949 (Automotive) or AS9100 (Aerospace) indicate specialized capabilities and adherence to stricter standards.
Certifications aren’t just badges; they represent a commitment to standardized processes and continuous improvement. They provide objective evidence that a manufacturer has implemented systems to control quality consistently. At PTSMAKE, we view certifications as essential frameworks that support our mission of delivering trusted, high-precision parts. Let’s look at the key ones.
Core Certifications Indicating Quality
Understanding what each certification signifies helps you gauge a manufacturer’s operational maturity and dedication to quality control.
ISO 9001: Grundlaget for kvalitetsstyring
This is the most widely recognized international standard for quality management. Holding ISO 9001 certification means an Aluminum Extrusion Manufacturer has established and follows effective processes for:
- Fokus på kunderne
- Leadership involvement
- Procestilgang
- Forbedring
- Evidensbaseret beslutningstagning
- Relationship management
It signifies a structured approach to managing quality across the organization, from initial inquiry to final delivery. Think of it as the baseline for a reliable manufacturing partner. It ensures procedures are documented, followed, and regularly audited.
Branchespecifikke certificeringer
For industries with particularly stringent requirements, look for additional certifications.
Automotive: IATF 16949
If you’re in the automotive sector, this standard is crucial. It builds upon ISO 9001 but adds specific requirements for automotive production, focusing heavily on defect prevention, reduction of variation, and waste reduction in the supply chain.
Aerospace: AS9100
Suppliers to the aerospace industry often require AS9100. This standard incorporates all of ISO 9001 but includes additional requirements related to safety, airworthiness, product conformity, and reliability critical to aerospace applications.
Material and Process Certifications
Beyond system-level certifications, inquire about how the manufacturer ensures the quality of the raw aluminum itself. This often involves requesting material certifications (mill test reports) that verify the alloy composition and properties, ensuring traceability back to the source. A good manufacturer will have processes for verifying incoming materials against specifications. A robust Quality Management System (QMS)5 integrates all these aspects.
Here’s a summary table:
Certificering | Primary Focus | Relevance |
---|---|---|
ISO 9001 | General Quality Management System | Foundational for any reliable manufacturer |
IATF 16949 | Automotive Quality Management + Defect Prevention | Essential for automotive suppliers |
AS9100 | Aerospace Quality Management + Safety & Reliability | Critical for aerospace suppliers |
Material Certs | Raw Material Composition & Properties Verification | Ensures input material meets specifications |
Verifying certifications is a key step in assessing whether an Aluminum Extrusion Manufacturer has the documented systems and commitment needed to meet your quality expectations consistently.
What Certifications Should A Reliable Aluminum Extrusion Manufacturer Have?
Feeling lost navigating the alphabet soup of manufacturing certifications? How do you know which ones genuinely signal a partner you can count on for consistent, long-term performance?
A reliable Aluminum Extrusion Manufacturer typically showcases ISO 9001 for core processes. For enhanced reliability, look for IATF 16949 (Automotive), AS9100 (Aerospace), and potentially ISO 14001 (Environmental) or ISO 45001 (Safety), indicating robust, responsible, and stable operating systems.
It’s easy to get impressed by logos, but what do they really mean for the reliability of your supply chain? Based on my 15+ years at PTSMAKE, focusing on specific certifications helps filter out suppliers who merely meet minimum specs from those truly committed to dependable, long-term partnerships. Reliability isn’t just about a single good batch; it’s about consistent results, predictable lead times, and proactive problem-solving, all supported by robust management systems.
Key Certifications Signaling Reliability
Think of these certifications as evidence of a manufacturer’s commitment to structured operations and risk management – crucial factors for reliability.
ISO 9001: The Foundation for Consistent Processes
This is the bedrock. ISO 9001 certification confirms an Aluminum Extrusion Manufacturer has documented processes for everything from quoting to shipping. It mandates regular internal audits, corrective actions for non-conformities, and a focus on continuous improvement. For reliability, this means they have systems to catch potential issues before they affect your order and a structured way to manage changes. It emphasizes a Process Approach6, ensuring activities are managed as interrelated processes, which leads to more predictable outcomes.
Industry-Specific Standards: Proving Specialized Capability
If your parts are for demanding sectors, look beyond ISO 9001:
- IATF 16949 (Automotive): This standard requires rigorous defect prevention planning (like FMEAs), stricter process controls, and robust supply chain management. Achieving this signals a manufacturer capable of meeting the high-volume, zero-defect expectations crucial for automotive reliability.
- AS9100 (Aerospace): This adds critical layers for risk management, product safety, configuration management, and prevention of counterfeit parts. An AS9100 certified Aluminum Extrusion Manufacturer demonstrates the discipline needed for components where failure is not an option.
Broader Responsibility Certifications: Indicators of Stability
Certifications like ISO 14001 (Environmental Management) and ISO 45001 (Occupational Health & Safety) might seem secondary, but they indicate a well-managed, responsible company less prone to disruptions from environmental incidents or safety issues. This operational stability contributes significantly to overall supplier reliability. At PTSMAKE, integrating these principles reinforces the dependable foundation our clients rely on.
Here’s a table summarizing the reliability aspect:
Certificering | Key Focus for Reliability | Hvorfor det er vigtigt |
---|---|---|
ISO 9001 | Consistent Processes, Continuous Improvement, Audit Trails | Predictable quality, systematic problem-solving |
IATF 16949 | Defect Prevention, Supply Chain Stability, Risk Reduction | Reduced variability, reliable high-volume supply |
AS9100 | Rigorous Risk Management, Safety Focus, Traceability | High assurance for critical applications |
ISO 14001 | Environmental Risk Management, Compliance | Operational stability, reduced disruption risk |
ISO 45001 | Worker Safety, Hazard Prevention | Stable workforce, fewer operational interruptions |
Ultimately, certifications are tools. A truly reliable Aluminum Extrusion Manufacturer doesn’t just collect certificates; they live the principles behind them, embedding quality and dependability into their culture.
How To Reduce Lead Time With Aluminum Extrusion Manufacturers?
Struggling with project delays because aluminum extrusion orders take too long? Are tight deadlines constantly threatened by supplier turnaround times, impacting your entire production schedule?
Reducing lead time involves optimizing designs for extrudability, choosing standard profiles or alloys when possible, maintaining clear communication with your manufacturer, efficient die design approval, and partnering with responsive suppliers who manage capacity well.
Getting your aluminum extrusions faster often comes down to proactive planning and smart collaboration with your chosen Aluminum Extrusion Manufacturer. From my experience at PTSMAKE, bottlenecks can occur at various stages, from design finalization to the actual extrusion process. Let’s look at practical ways to shorten that crucial timeline.
Strategies for Faster Extrusion Turnaround
Implementing a few key strategies can significantly cut down the waiting time for your custom extrusions.
Design Optimization for Speed
The complexity of your part directly impacts how quickly it can be extruded. Overly intricate profiles with very thin walls or extremely tight tolerances require more complex tooling and slower extrusion speeds. Simplifying the design, where possible without compromising function, can yield faster results. Engaging in Design for Manufacturability (DFM) discussions early with your supplier helps identify potential time-saving modifications.
Material and Profile Selection
Opting for standard aluminum alloys like 6063 or 6061, which are readily available, can save time compared to ordering custom or less common alloys. Similarly, if a standard, off-the-shelf profile shape meets your needs, it eliminates the die creation lead time entirely. We often guide clients at PTSMAKE toward suitable standard options when project requirements allow.
Streamlining the Die Process
Creating the extrusion die is often the longest part of the initial lead time for custom profiles. The complexity of the die design plays a big role here. Equally important is how quickly you review and approve the die drawings provided by the manufacturer. Prompt feedback prevents delays. The subsequent Die Trials7 phase, where the first extrusions are tested against specifications, also needs efficient management.
Communication and Collaboration
Clear, concise, and complete information exchange is vital. Ensure your Request for Quote (RFQ) includes all necessary drawings, specifications, quantities, and desired delivery dates. Quick responses to supplier questions and prompt approvals keep the process moving smoothly. A proactive Aluminum Extrusion Manufacturer will also keep you informed about progress and potential issues.
Supplier Capacity and Planning
Understand your supplier’s typical lead times and current workload. Manufacturers with good capacity planning can often provide more reliable timelines. Discussing potential expedited options early might be possible, though often at a higher cost. Building a strong relationship with a reliable partner helps in navigating urgent needs.
Here’s a summary of factors influencing lead time:
Faktor | Impact on Lead Time | Afbødningsstrategi |
---|---|---|
Designets kompleksitet | High Complexity = Longer Time | Simplify design, DFM review |
Die Creation | Significant for Custom Profiles | Fast drawing approval, clear specs |
Valg af materiale | Custom Alloys = Longer Time | Use standard alloys (6063/6061) if possible |
Bestillingsmængde | Very small/large orders may affect timing | Discuss volume impact with supplier |
Kommunikation | Slow Feedback = Delays | Provide clear RFQs, respond promptly |
Supplier Capacity | Overloaded Supplier = Longer Time | Choose responsive partner, discuss scheduling |
Efterbehandling | Additional Steps = Added Time | Factor finishing time into overall schedule |
By addressing these areas proactively, you can work effectively with your Aluminum Extrusion Manufacturer to significantly reduce lead times and keep your projects on track.
How To Reduce Lead Time With Aluminum Extrusion Manufacturers?
Feeling the pressure as project deadlines loom, constantly hampered by unpredictable extrusion lead times? Does this bottleneck frequently throw your entire production schedule off track?
Shortening lead times hinges on proactive collaboration: optimizing designs early, selecting standard materials where feasible, ensuring swift communication and approvals, and partnering with a manufacturer skilled in efficient production planning.
Getting aluminum extrusions delivered faster isn’t just about asking the supplier to hurry; it requires a strategic approach involving both your team and the manufacturer. Reducing delays means looking at the entire process, from initial design to final shipment. In past projects at PTSMAKE, we’ve found that addressing potential bottlenecks early is the most effective way to meet tight schedules. Let’s explore some key areas where time can often be saved.
Proactive Design and Planning Phase
The choices made before production even begins significantly impact the overall timeline.
Engaging Early for Design for Manufacturability (DFM)
Bringing your Aluminum Extrusion Manufacturer into the loop early allows for valuable feedback. Discussing the profile design with experienced engineers can identify features that might slow down extrusion or complicate tooling. Simplifying complex geometries or adjusting tolerance requirements, where possible, can drastically cut production time. This collaborative Design for fremstillbarhed (DFM)8 review helps optimize the part for both function and efficient production.
Smart Material and Profile Choices
While custom alloys offer specific properties, they often come with longer lead times due to sourcing requirements. Standard alloys like 6061 or 6063 are typically stocked by manufacturers and are quicker to procure. Similarly, leveraging existing standard profiles, if they meet the functional needs, bypasses the entire die creation process, saving weeks.
Streamlining the Tooling and Approval Process
For custom profiles, the die creation and approval stage is often the most time-consuming.
Efficient Die Design Review
Once the manufacturer provides die drawings, a swift and thorough review is crucial. Delays in approving these drawings directly push back the start of die manufacturing. Ensure your engineering team prioritizes this review and provides clear, consolidated feedback if changes are needed.
Expediting Die Trials
After the die is made, initial samples (die trials) are run to verify dimensions and quality. Streamlining the evaluation of these first articles and providing quick approval or clear feedback for adjustments keeps the momentum going.
Optimizing Production and Communication Flow
Effective communication and understanding the supplier’s operations are key during production.
Clear Information Exchange
Ensure all purchase orders, drawings, and specifications are complete and unambiguous from the start. Respond quickly to any queries from the manufacturer. Regular, proactive communication, asking for status updates rather than waiting for delays to be announced, can help manage expectations and address potential issues early.
Understanding Supplier Capacity and Scheduling
Discuss lead times upfront and understand the factors influencing them, such as current workload or planned maintenance. A reliable Aluminum Extrusion Manufacturer, like PTSMAKE, maintains transparent communication about their capacity and scheduling, helping you plan more accurately. Sometimes, discussing potential batching of orders or slightly flexible delivery windows can help fit your order into their schedule more efficiently.
Here’s a summary of areas where time savings can be achieved:
Area of Impact | Handling påkrævet | Potential Time Saving Indicator |
---|---|---|
Designfasen | Early DFM collaboration, simplify complex features | Middel til høj |
Valg af materiale | Choose standard alloys/profiles when possible | Medium |
Die Drawing Approval | Prompt internal review and feedback | Høj |
Die Trial Approval | Quick evaluation of first articles | Medium |
Information Clarity | Provide complete, clear specs upfront | Lav til middel |
Kommunikation | Respond quickly to queries, proactive check-ins | Medium |
Supplier Partnership | Choose partner with good capacity mgmt & comms | Medium |
Working closely with your Aluminum Extrusion Manufacturer and addressing these points proactively can significantly shorten lead times, helping keep your projects on schedule and reducing overall stress.
Learn how tooling costs are spread over production runs to reduce per-part expenses. ↩
Click to understand the properties and common uses of this specific aluminum alloy temper. ↩
Explore the technical details and design advantages of T-slot profiles for modular construction. ↩
Understand how internal material structure impacts extrusion quality and strength. ↩
Learn more about the framework used to ensure consistent quality and customer satisfaction. ↩
Discover how focusing on processes ensures consistent and reliable manufacturing outcomes. ↩
Learn about the die testing phase and how it impacts overall extrusion project timelines. ↩
Learn how optimizing designs for manufacturing efficiency can significantly reduce production time. ↩