Kæmper du med at finde det rigtige materiale til krævende anvendelser, hvor standardplast ikke slår til? Mange ingeniører står over for udfordringer, når komponenter skal kunne modstå ekstreme temperaturer, kemikalier eller mekanisk stress. Traditionel plast kan simpelthen ikke holde til det, hvilket fører til hyppige delfejl og dyre udskiftninger.
PEEK-bearbejdning er processen med at skære, bore og forme polyetheretherketon (PEEK)-materiale ved hjælp af CNC-maskiner. Denne højtydende termoplast har en enestående varmebestandighed på op til 480°F, en fremragende kemisk resistens og en styrke, der kan sammenlignes med visse metaller.
Jeg har arbejdet med utallige kunder, som er gået over til PEEK-bearbejdning af deres kritiske komponenter. Resultaterne taler for sig selv - dele med længere holdbarhed, bedre ydeevne i barske miljøer og reducerede vedligeholdelsescyklusser. Hvis du spekulerer på, om PEEK kan være løsningen til din applikation, så læs videre for at opdage de unikke egenskaber og bearbejdningsteknikker, der gør dette materiale så værdifuldt inden for præcisionsfremstilling.
Er PEEK bedre end Delrin til bearbejdning?
Har du nogensinde stået midt i et materialevalgsdilemma og været splittet mellem PEEK og Delrin til dit kritiske ingeniørprojekt? Når ydeevne er vigtig, og fejl ikke er en mulighed, kan valg af forkert plast føre til for tidlig slitage, nedetid for udstyr og dyre redesigns.
Mens PEEK giver overlegen temperaturbestandighed (op til 480°F), enestående kemisk stabilitet og højere styrke, giver Delrin (POM) bedre bearbejdelighed, dimensionsstabilitet og lavere omkostninger. Det "bedre" valg afhænger helt af dine specifikke anvendelseskrav og budgetbegrænsninger.
Forståelse af PEEK og Delrin: Grundlæggende forskelle
Når man sammenligner disse to højtydende tekniske plastmaterialer, er det vigtigt at forstå deres grundlæggende sammensætning og egenskaber. PEEK (polyetheretherketon) er en semikrystallinsk termoplast med enestående modstandsdygtighed over for termisk nedbrydning, mens Delrin (polyoxymethylen eller POM) er en acetalhomopolymer, der er kendt for sin fremragende dimensionsstabilitet.
Sammenligning af materialeegenskaber
Disse materialers fysiske og mekaniske egenskaber har stor betydning for deres bearbejdningsegenskaber og ydeevne ved slutbrug.
Ejendom | PEEK | Delrin (POM) |
---|---|---|
Varmeafbøjningstemperatur | 157 °C (315 °F) | 125 °C (257 °F) |
Trækstyrke | 14.500 psi | 10.000 psi |
Kemisk modstandsdygtighed | Fremragende (modstår de fleste syrer og baser) | God (sårbar over for stærke syrer) |
Modstandsdygtighed over for slid | Overlegen | Meget god |
Omkostningsfaktor | 4-5× højere end Delrin | Moderat |
Tæthed | 1,32 g/cm³ | 1,41 g/cm³ |
Bearbejdningsegenskaber: Hvordan de opfører sig under værktøjet
Min erfaring hos PTSMAKE er, at bearbejdeligheden ofte er den afgørende faktor, når man skal vælge mellem disse materialer. Delrin kan generelt bearbejdes mere forudsigeligt end PEEK og giver en glattere overfladefinish med mindre indsats.
Værktøjsslid og skæreparametre
PEEK slider mere på skæreværktøjer og kræver hyppigere værktøjsskift. Ved bearbejdning af PEEK reducerer vi typisk skærehastigheden med ca. 15-20% sammenlignet med Delrin for at minimere varmeudviklingen. Dette er afgørende, fordi PEEK's lave varmeledningsevne forårsager varmekoncentration i skærezonen, hvilket potentielt kan forårsage termisk deformation1 hvis den ikke håndteres korrekt.
Delrin giver på den anden side fremragende dimensionsstabilitet under bearbejdning og kan skæres ved højere hastigheder. Det giver mindre værktøjsslitage og kræver generelt færre specialiserede bearbejdningsteknikker.
Overvejelser om overfladefinish
En fordel ved Delrin er dens evne til at opnå fremragende overfladefinish med standard bearbejdningsparametre. PEEK kræver ofte yderligere poleringstrin for at opnå en sammenlignelig overfladekvalitet.
Cost-benefit-analyse til tekniske anvendelser
Omkostningsforskellen mellem disse materialer kan være betydelig. PEEK koster typisk 4-5 gange mere end Delrin, så det er vigtigt at vurdere, om de gode egenskaber retfærdiggør investeringen.
Når PEEK retfærdiggør sin høje pris
Jeg anbefaler PEEK til applikationer, der involverer:
- Ekstreme driftstemperaturer (over 250°F)
- Aggressive kemiske miljøer
- Høj mekanisk belastning ved høje temperaturer
- Medicinske eller rumfartsapplikationer, der kræver biokompatibilitet eller flammebestandighed
Når Delrin er det bedste valg
Delrin giver mere økonomisk mening, når:
- Driftstemperaturer forbliver under 180°F
- Kemisk eksponering er begrænset til moderate opløsningsmidler
- Omkostningsfølsomhed er en vigtig faktor
- Dele kræver fremragende dimensionsstabilitet og bearbejdet præcision
- Store produktionsmængder gør materialeomkostninger til en væsentlig faktor
Branchespecifikke overvejelser
Forskellige industrier prioriterer forskellige materialeegenskaber. I luftfartssektoren, hvor vi har leveret mange komponenter, retfærdiggør PEEK's flammebestandighed og enestående styrke/vægt-forhold ofte den højere pris. Til bilindustrien vinder Delrins kombination af rimelige omkostninger og gode mekaniske egenskaber ofte.
Anvendelser inden for medicin og fødevareforarbejdning
Til medicinsk udstyr gør PEEK's biokompatibilitet og steriliseringsmodstand det uvurderligt på trods af merprisen. I udstyr til fødevareforarbejdning gør Delrins FDA-overholdelse og lavere omkostninger det ofte til det foretrukne valg, medmindre der er tale om høje temperaturer.
Komponenter til industrimaskiner
I industrielle applikationer har jeg set, at beslutningen ofte handler om driftsforhold. Tandhjul, lejer og sliddele, der arbejder under moderate forhold, fungerer fremragende i Delrin, mens de, der udsættes for ekstreme forhold, nyder godt af PEEK's overlegne egenskaber.
Træf det rigtige valg til din applikation
Beslutningen mellem PEEK og Delrin skal træffes på baggrund af en grundig analyse af dine specifikke driftsforhold. Hos PTSMAKE overvejer vi:
- Maksimal driftstemperatur
- Kemisk eksponeringsprofil
- Krav til mekanisk belastning
- Begrænsninger i budgettet
- Forventninger til levetid
Ved omhyggeligt at evaluere disse faktorer i forhold til hvert materiales egenskaber kan du træffe en informeret beslutning, der afbalancerer ydeevne og omkostningseffektivitet for din specifikke anvendelse.
Hvad er forskellen på Acetal og PEEK?
Har du nogensinde kæmpet med at vælge mellem acetal og PEEK til dine kritiske tekniske komponenter? Når projektets succes afhænger af materialevalget, kan det forkerte valg føre til for tidlige fejl, uventet nedetid og budgetnedbrydende redesigns, som kunne have været undgået med korrekt materialekendskab.
Acetal (POM) og PEEK adskiller sig primært ved deres egenskaber og pris. PEEK giver overlegen varmebestandighed (480°F vs. 180°F), bedre kemisk modstandsdygtighed og højere styrke, mens acetal giver fremragende bearbejdelighed, dimensionsstabilitet og koster betydeligt mindre, hvilket gør det ideelt til mindre krævende anvendelser.
De vigtigste forskelle mellem Acetal og PEEK
Det er afgørende at forstå de grundlæggende forskelle mellem disse to tekniske plastmaterialer for at kunne træffe informerede beslutninger om dine projekter. Begge materialer har etableret sig som foretrukne inden for præcisionsfremstilling, men de tjener vidt forskellige formål baseret på deres iboende egenskaber.
Materialets sammensætning og struktur
Acetal, almindeligvis kendt under varemærket Delrin (når det er i homopolymerform) eller under det kemiske navn polyoxymethylen (POM), har en meget krystallinsk struktur med gentagne -CH₂O-grupper. Denne struktur giver det fremragende dimensionsstabilitet og bearbejdelighed.
PEEK (polyetheretherketon) tilhører derimod polyaryletherketon-familien og indeholder aromatiske ringe, der er forbundet med ether- og ketonbindinger. Denne molekylære struktur skaber enestående termisk stabilitet og kemisk resistens.
Sammenligning af præstationsegenskaber
Forskellene i ydeevne mellem disse materialer gør dem velegnede til forskellige anvendelser:
Ejendom | Acetal (POM) | PEEK | Bedst til |
---|---|---|---|
Varmebestandighed | 82°C (180°F) kontinuerligt | 250 °C (480 °F) kontinuerligt | PEEK |
Kemisk modstandsdygtighed | God (undtagen stærke syrer) | Fremragende (modstandsdygtig over for de fleste kemikalier) | PEEK |
Trækstyrke | 8.800-10.000 psi | 14.500-16.000 psi | PEEK |
Modstandsdygtighed over for slid | Meget god | Fremragende | PEEK |
Bearbejdelighed | Fremragende | God (kræver specialiserede teknikker) | Acetal |
Omkostningsfaktor | Basisreference (1×) | 4-7× højere end Acetal | Acetal |
Absorption af fugt | 0.2-0.25% | 0.1-0.15% | PEEK |
Cost-benefit-analyse
I de år, jeg har arbejdet med kunder hos PTSMAKE, har jeg bemærket, at omkostningsovervejelser ofte styrer den indledende materialevalgsproces. Acetal er betydeligt mere økonomisk end PEEK, hvilket gør det til standardvalget, når der ikke er tale om ekstreme forhold.
PEEK's høje pris afspejler dens overlegne ydeevne. Når du vurderer, om den ekstra investering er berettiget, skal du overveje følgende faktorer:
- Krav til driftstemperatur
- Kemisk eksponeringsprofil
- Mekaniske stressniveauer
- Forventet levetid
- Omkostninger til nedetid i forbindelse med komponentfejl
Overvejelser om bearbejdning
Værktøjslevetid og skæreparametre
Acetal er kendt for sin enestående bearbejdelighed. Det skærer rent, holder snævre tolerancer og giver fremragende overfladefinish med minimal indsats. Standard karbidværktøjer fungerer godt, og materialet forårsager ikke overdreven værktøjsslitage.
PEEK giver flere udfordringer under bearbejdningen. Dets høje temperaturbestandighed betyder, at varmeafledningen under bearbejdningen er dårlig, hvilket kræver:
- Nedsatte skærehastigheder (typisk 20-30% langsommere end acetal)
- Hyppigere værktøjsskift
- Vær opmærksom på varmeudvikling
- Specialiserede køleteknikker
Hos PTSMAKE har vi udviklet specifikke Protokoller til varmestyring2 til PEEK-bearbejdning for at sikre dimensionsnøjagtighed og forhindre materialenedbrydning under skæreprocessen.
Dimensionel stabilitet
Acetal giver fremragende dimensionsstabilitet efter bearbejdning med minimal krumning eller spændingsaflastning. Det gør det særligt værdifuldt til præcisionskomponenter med snævre tolerancer.
PEEK udviser også god dimensionsstabilitet, men kræver mere omhyggelige udglødningsprocesser for at aflaste indre spændinger efter bearbejdning. Uden korrekt termisk konditionering kan PEEK-dele opleve små dimensionsændringer over tid, især i applikationer med høj præcision.
Applikationsspecifikke anbefalinger
Biler og transport
I bilindustrien, hvor temperaturen forbliver moderat (under 180°F), giver acetal ofte den bedste værdi. Almindelige anvendelser omfatter:
- Brændstofsystemets komponenter
- Låsemekanismer til døre
- Clips og skruer til indvendig beklædning
- Lejeoverflader i ikke-kritiske områder
I zoner med højere temperaturer, som f.eks. komponenter under motorhjelmen eller dele i nærheden af udstødningssystemer, gør PEEK's termiske stabilitet det til et bedre valg på trods af de højere omkostninger.
Medicinsk og farmaceutisk
Medicinalindustrien har taget PEEK til sig på grund af dets biokompatibilitet og modstandsdygtighed over for steriliseringsmetoder. Det bruges ofte i:
- Implanterbare enheder
- Kirurgiske instrumenter
- Komponenter til medicinsk billeddannelse
- Laboratorieudstyr
Acetal finder stadig anvendelse i mindre krævende medicinske miljøer, som f.eks:
- Engangskomponenter til instrumenter
- Testudstyr til laboratorier
- Kabinetter til diagnoseudstyr
Industrielt udstyr
For industrimaskiner afhænger valget ofte af driftsbetingelserne:
- Standard driftsmiljøer: Acetal giver fremragende værdi for tandhjul, lejer og slidflader under normale forhold.
- Hårde miljøer: PEEK retfærdiggør sin høje pris, når det udsættes for høje temperaturer, kemikalier eller ekstrem mekanisk belastning.
Træf det optimale valg
Når jeg hjælper kunder med at vælge mellem acetal og PEEK ved PTSMAKE, anbefaler jeg en systematisk tilgang:
- Identificer de mest krævende forhold, som delen vil blive udsat for (temperatur, kemikalier, belastninger)
- Find ud af, om acetals egenskaber er tilstrækkelige til at håndtere disse forhold
- Beregn omkostningsforskellen mellem mulighederne for dine specifikke volumenkrav
- Overvej konsekvenserne af en fejl og de tilhørende omkostninger til nedetid
- Vurder, om PEEK's førsteklasses ydeevne retfærdiggør den højere pris
Husk, at materialevalg sjældent er noget, der passer til alle. Nogle gange fungerer en hybridtilgang bedst, hvor man kun bruger PEEK til de mest kritiske komponenter, mens man bruger acetal til mindre krævende dele i den samme samling.
Hvad er forskellen på PTFE og PEEK?
Har du nogensinde været fortabt i et hav af højtydende plastmaterialer og været i tvivl om, hvorvidt du skulle vælge PTFE eller PEEK til din kritiske applikation? Når projektdeadlines truer, og materialevalget kan være afgørende for dit design, kan presset for at træffe det rigtige valg være overvældende, især når begge materialer har imponerende tekniske specifikationer.
PTFE og PEEK er begge højtydende termoplaster med tydelige forskelle. PTFE har uovertruffen kemisk resistens, ekstremt lav friktion (0,05-0,10 koefficient) og fungerer fra -328°F til 500°F, men har ringe mekanisk styrke. PEEK har overlegne mekaniske egenskaber, fremragende slidstyrke og opretholder strukturel integritet op til 480°F, samtidig med at det er mere bearbejdeligt.
Molekylær struktur og grundlæggende egenskaber
De grundlæggende forskelle mellem PTFE og PEEK begynder på det molekylære niveau, hvilket forklarer deres forskellige egenskaber i forskellige anvendelser.
Kemisk sammensætning
PTFE (polytetrafluorethylen) har en kulstofryggrad, der er fuldstændig omgivet af fluoratomer. Denne unikke struktur giver PTFE sin enestående kemiske inerti og lave friktionsegenskaber. Kulstof-fluorbindingerne er blandt de stærkeste i organisk kemi, hvilket gør PTFE utroligt modstandsdygtigt over for kemiske angreb.
PEEK (polyetheretherketon) har derimod en mere kompleks molekylær struktur med aromatiske ringe, der er forbundet med ether- og ketonbindinger. Denne aromatiske rygrad giver PEEK sin fremragende mekaniske styrke og termiske stabilitet.
Sammenlignende ejendomsanalyse
Ejendom | PTFE | PEEK | Fordel |
---|---|---|---|
Maksimal temperatur ved kontinuerlig brug | 260 °C (500 °F) | 250 °C (480 °F) | PTFE (lidt) |
Minimum driftstemperatur | -328°F (-200°C) | -65°F (-54°C) | PTFE |
Friktionskoefficient | 0,05-0,10 (laveste af alle faste stoffer) | 0.35-0.40 | PTFE |
Trækstyrke | 3.000-5.000 psi | 14.000-16.000 psi | PEEK |
Kemisk modstandsdygtighed | Overlegen (universel) | Fremragende (begrænset af stærke syrer) | PTFE |
Bearbejdelighed | Udfordrende (blød, deformeres let) | God | PEEK |
Modstandsdygtighed over for slid | Dårlig til moderat | Fremragende | PEEK |
Elektriske egenskaber | Fremragende isolator | God isolator | PTFE |
Omkostningsfaktor | Moderat | Høj (3-4× mere end PTFE) | PTFE |
Forskelle i termisk ydeevne
Temperaturegenskaber er ofte en afgørende faktor, når man skal vælge mellem disse materialer.
Varmebestandighed og stabilitet
Selv om begge materialer har en enestående varmebestandighed, opfører de sig forskelligt ved høje temperaturer. PTFE bevarer sin kemiske inerti og lave friktion op til den maksimale temperatur, men begynder at miste sin mekaniske integritet ved meget lavere temperaturer (omkring 260°F/127°C).
I mellemtiden bevarer PEEK sin mekaniske styrke meget tættere på den maksimale temperatur. Det gør PEEK betydeligt mere værdifuld i applikationer, der kræver både varmebestandighed og mekanisk belastning.
Jeg har set mange anvendelser, hvor kunder oprindeligt valgte PTFE udelukkende baseret på temperaturangivelser, men hvor de opdagede, at materialet ikke kunne klare de mekaniske belastninger ved disse temperaturer. PEEK's evne til at opretholde strukturel integritet ved høje temperaturer gør, at det ofte er den højere pris værd.
Ydeevne ved kolde temperaturer
Til kryogene anvendelser har PTFE en klar fordel. Det forbliver fleksibelt og funktionelt ned til -200 °C, mens PEEK bliver mere og mere skørt under -54 °C. Det gør PTFE til det klare valg til rumfart, laboratorier og andre miljøer med meget lave temperaturer.
Sammenligning af mekanisk styrke
De mekaniske egenskaber ved disse materialer er meget forskellige, hvilket gør dem anvendelsesspecifikke.
Strukturel integritet under belastning
PEEK har en langt bedre mekanisk ydeevne med en gennemsnitlig trækstyrke på 14.000-16.000 psi sammenlignet med PTFE's beskedne 3.000-5.000 psi. Det gør PEEK velegnet til bærende opgaver, hvor PTFE hurtigt ville blive deformeret eller svigte.
Hos PTSMAKE anbefaler vi ofte PEEK til strukturelle komponenter, der udsættes for vedvarende mekaniske belastninger, især ved høje temperaturer. Materialets exceptionelle kryberesistens gør det muligt at opretholde dimensionsstabilitet under kontinuerlig belastning.
Slidstyrke og friktion
PTFE's bemærkelsesværdigt lave friktionskoefficient (0,05-0,10) gør det til det foretrukne materiale til anvendelser, der kræver minimal friktion. Men den samme egenskab bidrager til dets dårlige slidstyrke, da materialet let kan skrabes væk i situationer med meget slid.
PEEK udviser fremragende slidstyrke og har samtidig en rimelig friktionskoefficient (0,35-0,40). Til anvendelser, der involverer kontinuerlig bevægelse mod andre overflader, overlever PEEK typisk PTFE med en betydelig margin.
Mange af vores kunder opnår det bedste fra begge verdener ved at bruge PEEK som strukturelt materiale med en tynd PTFE-belægning eller liner, hvor der er behov for friktionsreduktion.
Profiler for kemisk modstandsdygtighed
Begge materialer har en enestående kemisk resistens, men med vigtige forskelle.
Modstandsdygtighed over for aggressive miljøer
PTFE repræsenterer guldstandarden for kemisk resistens, idet det er stort set inert over for næsten alle kemikalier (med sjældne undtagelser som smeltede alkalimetaller og elementært fluor). Denne universelle kemikaliebestandighed gør PTFE uvurderlig i kemisk forarbejdning, halvlederproduktion og laboratoriemiljøer.
PEEK har fremragende kemisk resistens over for de fleste stoffer, men kan angribes af koncentreret svovlsyre og visse andre stærke syrer. I de fleste industrielle miljøer er PEEK's kemiske modstandsdygtighed dog mere end tilstrækkelig.
Hydrolyse og fugtabsorption
PTFE er fuldstændig hydrofobisk og absorberer stort set ingen fugt, selv efter længere tids eksponering. PEEK er meget modstandsdygtig over for hydrolyse, men absorberer en lille mængde fugt (0,1-0,3%), når det udsættes for fugtige miljøer i længere tid.
Til applikationer med ultrarent vand eller systemer, hvor selv den mindste forurening er uacceptabel, er PTFE ofte det foretrukne valg på trods af dets mekaniske begrænsninger.
%[PEEK- og PTFE-bearbejdede komponenter til strukturel sammenligning](
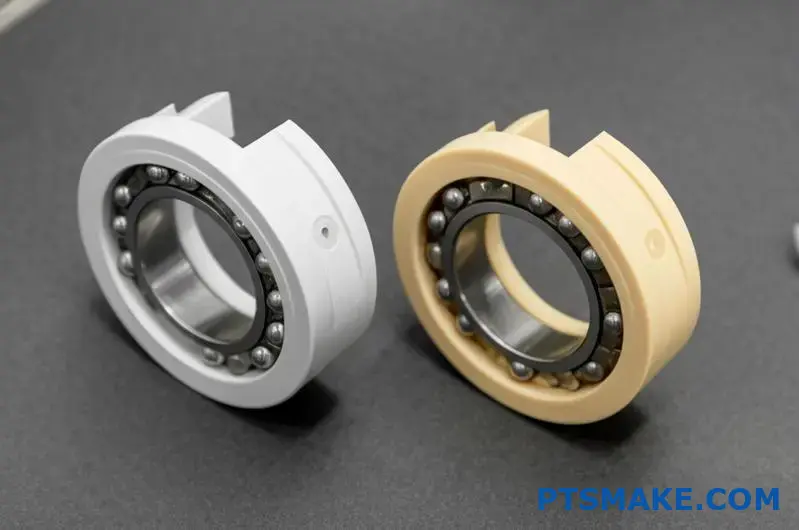
"PEEK- og PTFE-lejekomponenter")
Overvejelser om bearbejdning og fremstilling
Den Bearbejdelighed3 Forskellene mellem disse materialer har stor betydning for produktionsomkostningerne og -mulighederne.
Bearbejdningsudfordringer og løsninger
PTFE giver unikke bearbejdningsudfordringer på grund af sin blødhed og tendens til koldflydning. Det kræver specialværktøj, lavere skærehastigheder og omhyggelig fastgørelse for at forhindre deformation under bearbejdningen. Skarpt værktøj er afgørende for at forhindre, at materialet rives over eller deformeres.
PEEK bearbejdes mere som traditionel teknisk plast, selvom dets slibende natur forårsager hurtigere værktøjsslitage end mange andre materialer. Når vi bearbejder PEEK, bruger vi typisk hårdmetalværktøj og passende køleteknikker til at styre varmeudviklingen.
Kompatibilitet med fremstillingsprocesser
PTFE's høje smelteviskositet gør konventionel sprøjtestøbning umulig. I stedet skal det forarbejdes ved hjælp af teknikker som kompressionsstøbning, rammeekstrudering eller skæring af emner. Det begrænser designkompleksiteten og øger produktionsomkostningerne for komplekse former.
PEEK kan bearbejdes ved hjælp af konventionelle metoder som sprøjtestøbning og ekstrudering, hvilket giver mulighed for mere komplekse geometrier og potentielt lavere produktionsomkostninger ved større mængder. Denne alsidighed i forarbejdningen giver PEEK en fordel til komplicerede komponenter eller ved overgang fra prototyper til masseproduktion.
Cost-benefit-analyse for forskellige applikationer
Den betydelige prisforskel mellem disse materialer gør det nødvendigt at overveje deres brugsspecifikke værdi nøje.
Sammenligning af værditilbud
Selv om PEEK typisk koster 3-4 gange mere end PTFE, giver dets overlegne mekaniske egenskaber og slidstyrke ofte en bedre langsigtet værdi i applikationer, hvor mekaniske fejl ville være dyre eller farlige.
Til anvendelser, der primært kræver kemisk resistens, lav friktion eller elektriske isoleringsegenskaber uden betydelig mekanisk belastning, giver PTFE normalt bedre værdi på trods af sine begrænsninger.
Branchespecifikke udvælgelseskriterier
Forskellige brancher prioriterer forskellige materialeegenskaber:
- Kemisk behandling: PTFE's universelle kemiske modstandsdygtighed opvejer typisk dens mekaniske begrænsninger.
- Luft- og rumfart: Begge materialer finder anvendelse, hvor PEEK bruges til strukturelle komponenter og PTFE til tætninger og elektrisk isolering.
- Medicinske formål: PEEK's biokompatibilitet og strukturelle styrke gør det populært til implantater, mens PTFE foretrækkes til kateterforinger og andre anvendelser med lav friktion.
- Halvledere: PTFE dominerer på grund af sin enestående renhed og modstandsdygtighed over for aggressive kemikalier.
- Bilindustrien: PEEK's slidstyrke og mekaniske egenskaber gør det værdifuldt til komponenter under motorhjelmen, der udsættes for mekanisk belastning.
Hvad er forskellen mellem PVDF og PEEK?
Har du nogensinde stået i det dilemma at skulle vælge mellem PVDF og PEEK til et kritisk projekt, hvor materialevalget kan være afgørende for dit design? Når standardplast ikke er nok, og du har brug for exceptionel kemisk resistens eller termisk stabilitet, kan forvirringen mellem disse to højtydende materialer føre til dyre fejltagelser eller forringet ydeevne.
PVDF (polyvinylidenfluorid) og PEEK (polyetheretherketon) adskiller sig primært ved deres egenskaber og anvendelsesområder. PEEK giver overlegen varmebestandighed (480°F vs. 300°F), bedre mekanisk styrke og enestående slidstyrke, mens PVDF giver fremragende kemisk resistens, UV-stabilitet og kommer til en betydeligt lavere pris.
De vigtigste forskelle mellem PVDF og PEEK
Når man sammenligner disse to tekniske termoplastmaterialer, hjælper en forståelse af deres grundlæggende egenskaber med at afgøre, hvilket materiale der er bedst egnet til specifikke anvendelser. Begge materialer anses for at være højtydende, men de udmærker sig i forskellige miljøer og anvendelser.
Materialets sammensætning og struktur
PVDF er en semikrystallinsk fluorpolymer, der består af gentagne enheder af vinylidendifluorid. Dens molekylære struktur omfatter kulstof-fluorbindinger, der giver fremragende kemisk modstandsdygtighed, men ikke så omfattende som fuldt fluorerede polymerer som PTFE.
PEEK tilhører polyaryletherketon-familien og har en kompleks molekylær struktur med aromatiske ringe, der er forbundet med ether- og ketonbindinger. Denne unikke struktur giver PEEK sin enestående termiske stabilitet og mekaniske styrke.
Sammenligning af præstationsegenskaber
Følgende tabel giver en detaljeret sammenligning af de vigtigste egenskaber mellem PVDF og PEEK:
Ejendom | PVDF | PEEK | Overlegent materiale |
---|---|---|---|
Maksimal temperatur ved kontinuerlig brug | 300°F (149°C) | 250 °C (480 °F) | PEEK |
Mekanisk styrke (trækstyrke) | 5.800-7.800 psi | 14.500-16.000 psi | PEEK |
Kemisk modstandsdygtighed | Fremragende (de fleste syrer og baser) | Meget god (begrænset af stærke syrer) | PVDF |
UV-bestandighed | Fremragende | Rimelig til god | PVDF |
Modstandsdygtighed over for slid | God | Fremragende | PEEK |
Friktionskoefficient | 0.25-0.35 | 0.35-0.40 | PVDF |
Omkostningsfaktor | Moderat | 2-3× højere end PVDF | PVDF |
Absorption af fugt | 0.03-0.04% | 0.1-0.15% | PVDF |
Tæthed | 1,75-1,78 g/cm³ | 1,30-1,32 g/cm³ | Applikationsafhængig |
Termisk ydeevne og stabilitet
Temperaturegenskaber er ofte afgørende for beslutninger om materialevalg i mange tekniske anvendelser.
Sammenligning af varmebestandighed
PEEK udviser enestående termisk stabilitet og bevarer sine mekaniske egenskaber ved temperaturer på op til 250 °C (480 °F) ved kontinuerlig brug. Det gør det ideelt til anvendelser i højtemperaturmiljøer, hvor traditionel plast ville svigte.
PVDF anses stadig for at være højtemperaturplast, men har en lavere maksimal kontinuerlig brugstemperatur på ca. 149 °C (300 °F). Dette temperaturområde er tilstrækkeligt til mange industrielle anvendelser, men kommer til kort i ekstreme termiske miljøer.
Min erfaring med at arbejde med kunder hos PTSMAKE er, at denne temperaturforskel ofte bliver den afgørende faktor, når man skal vælge mellem disse materialer til applikationer som halvlederudstyr, hvor procestemperaturerne kan overstige PVDF's kapacitet.
Opførsel ved termisk cykling
Begge materialer håndterer termisk cykling forskelligt:
- PVDF udviser god dimensionsstabilitet under termisk cykling, selv om det kan opleve en større termisk udvidelse end PEEK.
- PEEK bevarer en enestående dimensionsstabilitet selv gennem gentagne termiske cyklusser, hvilket gør det foretrukket til præcisionskomponenter, der skal opretholde snævre tolerancer over varierende temperaturer.
Profiler for kemisk modstandsdygtighed
Kemikalieresistens er en anden afgørende faktor, der adskiller disse materialer.
Modstandsdygtighed over for aggressive miljøer
PVDF giver fremragende modstandsdygtighed over for en lang række kemikalier, herunder:
- De fleste syrer (herunder koncentreret saltsyre og svovlsyre)
- Alifatiske og aromatiske kulbrinter
- Alkoholer og klorerede opløsningsmidler
- Oxiderende midler
PEEK udviser god kemisk modstandsdygtighed over for mange stoffer, men kan angribes af koncentreret svovlsyre og andre stærke syrer. Det er særligt modstandsdygtigt over for hydrolyse og dampsterilisering, hvilket gør det værdifuldt i medicinske anvendelser.
Branchespecifikke overvejelser om kemikalier
Forskellige industrier prioriterer specifikke kemiske resistensegenskaber:
- Kemisk behandling: PVDF foretrækkes ofte på grund af sin omfattende modstandsdygtighed over for syrer og klorerede forbindelser.
- Halvleder: Begge materialer bruges, og valget afhænger af specifikke proceskemikalier.
- Olie og gas: PEEK's kombination af mekaniske egenskaber og kemisk resistens gør det værdifuldt til anvendelse i borehuller.
- Farmaceutisk: PVDF's fremragende modstandsdygtighed over for rengøringsmidler og steriliseringsmetoder gør det populært til procesudstyr.
Mekaniske egenskaber og strukturelle anvendelser
Den mekanisk styrke4 Forskellene mellem disse materialer har stor betydning for deres egnethed til bærende opgaver.
Kapacitet til at bære belastning
PEEK har en væsentlig højere mekanisk styrke med trækværdier på typisk 14.500-16.000 psi sammenlignet med PVDF's mere beskedne 5.800-7.800 psi. Det gør PEEK overlegen til strukturelle komponenter, der skal kunne modstå betydelige mekaniske belastninger.
Til applikationer, der kræver både kemisk resistens og strukturel integritet, giver PEEK ofte den bedste balance mellem egenskaber på trods af den højere pris. Jeg har anbefalet PEEK til mange anvendelser hos PTSMAKE, hvor komponenterne skal kunne modstå både aggressive kemikalier og mekanisk belastning.
Slidstyrke og friktionsegenskaber
PEEK har en fremragende slidstyrke, hvilket gør det ideelt til lejer, bøsninger og andre komponenter, der er udsat for kontinuerlig friktion. Dets selvsmørende egenskaber er med til at forlænge levetiden for bevægelige dele i krævende miljøer.
PVDF har god slidstyrke, men ikke på samme niveau som PEEK. Dens lavere friktionskoefficient (0,25-0,35 sammenlignet med PEEK's 0,35-0,40) kan være en fordel i visse glideanvendelser med lav belastning, hvor reduceret friktion er vigtigere end maksimal slidstyrke.
Elektriske og termiske isoleringsegenskaber
Begge materialer har forskellige elektriske egenskaber, som gør dem velegnede til forskellige anvendelser.
Dielektriske egenskaber
PVDF er kendt for sine piezoelektriske egenskaber, som gør det muligt at generere en elektrisk ladning som reaktion på påført mekanisk stress. Denne unikke egenskab gør PVDF værdifuld i sensorapplikationer.
PEEK har fremragende elektriske isoleringsegenskaber over et bredt temperaturområde og bevarer sin dielektriske styrke selv ved høje temperaturer. Det gør det særligt værdifuldt i elektriske applikationer ved høje temperaturer, hvor standardplast ville svigte.
Termisk ledningsevne
PVDF og PEEK har begge en relativt lav varmeledningsevne sammenlignet med metaller, hvilket gør dem til gode varmeisolatorer:
- PVDF: 0,17-0,19 W/m-K
- PEEK: 0,25-0,29 W/m-K
Denne lave varmeledningsevne kan enten være en fordel eller en ulempe afhængigt af anvendelsen. Til komponenter, der kræver termisk isolering, fungerer begge materialer godt, selvom PVDF giver lidt bedre isolering.
Omkostningsovervejelser og værdianalyse
Den betydelige prisforskel mellem disse materialer gør en cost-benefit-analyse afgørende.
Indledende materialeomkostninger
PEEK koster typisk 2-3 gange mere end PVDF, hvilket er en betydelig merpris, der skal retfærdiggøres af kravene til ydeevne. Denne prisforskel skyldes PEEK's mere komplekse fremstillingsproces og de højere omkostninger til råmaterialer.
Vurdering af livstidsværdi
Når man vurderer de samlede ejeromkostninger, skal man tage højde for flere faktorer end de oprindelige materialeomkostninger:
- Forventet levetid i målmiljøet
- Udskiftningsfrekvens og tilhørende omkostninger til nedetid
- Krav til installation og vedligeholdelse
- Problemer med sikkerhed og pålidelighed
I mange applikationer med høj temperatur eller høj belastning retfærdiggør PEEK's overlegne ydeevne den højere startpris gennem forlænget levetid og forbedret pålidelighed. Til anvendelser inden for PVDF's muligheder giver det billigere materiale ofte en bedre samlet værdi.
Overvejelser om forarbejdning og fremstilling
Produktionsmuligheder og -begrænsninger påvirker også materialevalget.
Forskelle i bearbejdning
Ved bearbejdning af disse materialer ved PTSMAKE har vi observeret betydelige forskelle:
- PVDF kan bearbejdes relativt godt, men kræver skarpt værktøj og passende hastigheder for at forhindre smeltning eller fastbrænding.
- PEEK er mere udfordrende at bearbejde på grund af dets slidstyrke og dårlige varmeledningsevne, som kan føre til varmeopbygning under skæreoperationer.
Til præcisionskomponenter holder PEEK generelt snævrere tolerancer under bearbejdningen, men kræver mere specialiserede teknikker og værktøjer, hvilket potentielt kan øge produktionsomkostningerne.
Kompatibilitet med fremstillingsmetoder
Begge materialer kan bearbejdes ved hjælp af flere forskellige fremstillingsmetoder:
- PVDF: Sprøjtestøbning, ekstrudering, kompressionsstøbning, bearbejdning
- PEEK: Sprøjtestøbning, ekstrudering, kompressionsstøbning, bearbejdning, 3D-printning (specialudstyr)
PVDF giver lidt mere behandlingsfleksibilitet ved lavere temperaturer, mens PEEK kræver højere behandlingstemperaturer, men giver flere muligheder for komplekse geometrier ved hjælp af avancerede fremstillingsteknikker.
Ansøgningsspecifikke retningslinjer for udvælgelse
Forskellige brancher prioriterer forskellige materialeegenskaber, hvilket fører til forskellige materialepræferencer.
Halvlederindustrien
I halvlederproduktion finder begge materialer anvendelse, men inden for forskellige områder:
- PVDF: Bruges ofte til ultrarene vandsystemer, komponenter til kemisk levering og filtreringsudstyr.
- PEEK: Foretrukket til komponenter, der udsættes for høje temperaturer, såsom waferhåndteringsudstyr og proceskammerkomponenter.
Udstyr til kemisk forarbejdning
Til kemisk forarbejdning:
- PVDF: Fremragende til pumper, ventiler, fittings og tanke, der håndterer ætsende kemikalier ved moderate temperaturer.
- PEEK: Bedre egnet til komponenter, der kræver både kemisk resistens og evne til at klare høje temperaturer eller mekanisk styrke.
Medicinske og farmaceutiske anvendelser
I medicinske anvendelser:
- PVDF: Bruges ofte i filtreringsmembraner, suturer og visse implanterbare enheder.
- PEEK: Foretrukket til implanterbare enheder, især ortopædiske applikationer, på grund af dets biokompatibilitet, radiolucens og mekaniske egenskaber, der ligner knogle.
Når jeg hjælper kunder med at vælge mellem PVDF og PEEK hos PTSMAKE, anbefaler jeg en systematisk tilgang, der først evaluerer de mest kritiske miljøfaktorer (temperatur, kemikalier, mekaniske belastninger) og derefter tager højde for sekundære faktorer som omkostninger, forarbejdningskrav og tilgængelighed.
<
Er PEEK en polyethylen?
Har du nogensinde været forvirret over udvalget af tekniske plastmaterialer med enslydende navne? Når du vælger materialer til kritiske anvendelser, kan denne forvirring føre til dyre fejl, manglende ydeevne og spildte ressourcer, hvis du fejlagtigt udskifter en højtydende plast med en anden.
Nej, PEEK (polyetheretherketon) er ikke en polyethylen. PEEK er en aromatisk polyether med ketongrupper i rygraden, hvilket skaber en semikrystallinsk termoplast med enestående varmebestandighed (op til 480°F), fremragende kemisk resistens og overlegne mekaniske egenskaber, der langt overgår polyethylenmaterialernes.
Kemisk struktur og klassificeringsforskelle
Når man undersøger PEEK i forhold til polyethylen, starter de grundlæggende forskelle på molekylært niveau. Disse strukturelle variationer forklarer, hvorfor disse materialer opfører sig så forskelligt i praktiske anvendelser.
Sammenligning af molekylær rygrad
PEEK har en kompleks aromatisk rygradstruktur med ether- og ketonbindinger mellem benzenringe. Denne molekylære arkitektur giver PEEK sin enestående termiske stabilitet og mekaniske styrke. De aromatiske ringe skaber stivhed, mens etherbindingerne giver en vis fleksibilitet.
Polyethylen har derimod en af de simpleste polymerstrukturer, der findes - blot en lineær kæde af kulstofatomer med tilknyttede brintatomer. Denne enkle struktur findes i forskellige former (HDPE, LDPE, UHMWPE), men alle mangler de aromatiske komponenter og funktionelle grupper, der giver PEEK dets enestående egenskaber.
Denne grundlæggende strukturelle forskel betyder, at PEEK tilhører en helt anden polymerfamilie end polyethylen. Mens polyethylen er klassificeret som en polyolefin, tilhører PEEK polyaryletherketon-familien (PAEK) af højtydende termoplast.
Vigtige ejendomsforskelle
De molekylære strukturforskelle giver sig udslag i dramatiske variationer i ydeevne:
Ejendom | PEEK | Polyethylen (HDPE) | Forskelsfaktor |
---|---|---|---|
Maksimal temperatur ved kontinuerlig brug | 250 °C (480 °F) | 82°C (180°F) | PEEK er 2,7× højere |
Trækstyrke | 14.500 psi | 4.500 psi | PEEK er 3,2× stærkere |
Kemisk modstandsdygtighed | Fremragende (modstår de fleste kemikalier) | God (sårbar over for aromatiske opløsningsmidler) | PEEK giver bredere modstandsdygtighed |
Omkostninger | Høj | Lav | PEEK koster 15-20× mere |
Tæthed | 1,32 g/cm³ | 0,95 g/cm³ | PEEK er 39% tættere |
Hårdhed (Shore D) | 85-90 | 60-70 | PEEK er betydeligt hårdere |
Forskelle i fremstillingsprocessen
Produktionsmetoderne for PEEK og polyethylen afspejler deres forskellige molekylære strukturer og egenskaber.
Produktionsproces for PEEK
PEEK fremstilles gennem en kompleks proces, der involverer nukleofil aromatisk substitutionspolymerisation. Det kræver præcis temperaturkontrol og specialiserede katalysatorer. Monomermaterialerne er betydeligt dyrere end ethylen, hvilket bidrager til PEEK's højere pris.
Når vi hos PTSMAKE bearbejder PEEK-komponenter, skal vi tage højde for dette materiales unikke egenskaber - dets lavere varmeledningsevne betyder, at varmestyring under bearbejdning er afgørende for at forhindre lokal termisk nedbrydning.
Fremstilling af polyethylen
Polyethylen fremstilles ved additionspolymerisation af ethylen ved hjælp af forskellige katalysatorer afhængigt af den ønskede tæthed og forgrening. Denne relativt enkle proces kan udføres ved lavere temperaturer og tryk end PEEK-produktion, især for varianter med lav densitet.
Ydeevne i ekstreme miljøer
Ydeevne ved høje temperaturer
En af de største forskelle mellem disse materialer er deres termiske stabilitet:
- PEEK bevarer sine mekaniske egenskaber op til 250 °C (480 °F) ved kontinuerlig brug og kan modstå korte eksponeringer for endnu højere temperaturer.
- Polyethylen begynder at blive blødt omkring 82 °C (180 °F) og mister det meste af sin mekaniske styrke langt under denne temperatur.
Jeg har set adskillige applikationer, hvor kunderne oprindeligt valgte polyethylen på grund af prisen, men hvor de oplevede hurtige fejl, når driftstemperaturerne oversteg forventningerne. I en rumfartsapplikation skiftede en kunde fra polyethylen til PEEK til en komponent i nærheden af en varmekilde, hvilket forlængede levetiden fra måneder til år på trods af de højere materialeomkostninger.
Sammenligning af kemisk modstandsdygtighed
Begge materialer har en god kemisk resistens, men PEEK giver en bredere beskyttelse mod barske kemikalier:
- PEEK er modstandsdygtig over for de fleste syrer, baser, kulbrinter og organiske opløsningsmidler
- Polyethylen har god modstandsdygtighed over for syrer og baser, men kan angribes af aromatiske kulbrinter og visse oxidationsmidler.
Denne forskel bliver kritisk i kemisk procesudstyr, halvlederproduktion og medicinske applikationer, hvor eksponering for flere kemikalier er almindelig.
Egnethed til anvendelse
Anvendelser inden for rumfart og forsvar
Inden for rumfart gør PEEK's kombination af lav vægt, flammebestandighed og termisk stabilitet det uvurderligt til komponenter som f.eks:
- Indvendige komponenter, der kræver flammebestandighed
- Elektriske stik og isolatorer
- Strukturelle komponenter i højtemperaturzoner
- Brændstofsystemkomponenter, der kræver kemisk resistens
Polyethylen opfylder sjældent de krævende krav til rumfartsapplikationer på grund af dets begrænsede termiske stabilitet og mekaniske egenskaber.
Medicinske og sundhedsmæssige anvendelser
Disse materialers biokompatibilitetsprofiler er også meget forskellige:
- PEEK er biokompatibelt og bruges til implantater, kirurgiske instrumenter og medicinsk udstyr, der skal steriliseres.
- Polyethylen af medicinsk kvalitet (primært UHMWPE) bruges i nogle implantater som kunstige led, men mangler PEEK's temperaturbestandighed til gentagen dampsterilisering.
Komponenter til industrielt udstyr
For industrimaskiner afhænger valget mellem disse materialer typisk af driftsbetingelserne:
- PEEK udmærker sig i miljøer med høje temperaturer, applikationer, der kræver fremragende slidstyrke, eller eksponering for barske kemikalier.
- Polyethylen giver tilstrækkelig ydeevne i applikationer ved omgivelsestemperatur med moderate mekaniske krav og vælges ofte på grund af de lavere omkostninger og den nemme forarbejdning.
Overvejelser om cost-benefit
Prisforskellen mellem disse materialer er betydelig - PEEK koster typisk 15-20 gange mere end polyethylen med høj densitet. Denne betydelige prisforskel betyder, at materialevalget skal baseres på en grundig analyse af:
- Påkrævet driftstemperaturområde
- Kemisk eksponeringsprofil
- Krav til mekanisk belastning
- Forventet levetid
- Konsekvenser af fiasko
Til anvendelser inden for polyethylens kapacitetsområde gør de lavere omkostninger det til det økonomiske valg. Men når kravene til ydeevne overstiger polyethylens begrænsninger, kan PEEK's overlegne egenskaber nemt retfærdiggøre den højere pris gennem forlænget levetid, forbedret pålidelighed og reducerede vedligeholdelsesomkostninger.
Forskelle i bearbejdning og forarbejdning
Hos PTSMAKE har vi fundet betydelige forskelle i bearbejdningen af disse materialer:
- PEEK kræver særlige skæreparametre på grund af dets termisk opførsel5 under bearbejdningen, men holder snævre tolerancer og giver fremragende overfladefinish
- Polyethylen er lettere at bearbejde, men har en tendens til at deformere sig under skærekræfter, hvilket gør det sværere at opretholde stramme tolerancer.
Det er vigtigt at forstå disse behandlingsforskelle, når man designer komponenter, der skal kunne fremstilles og være præcise.
Hvad er ulemperne og fordelene ved PEEK?
Har du nogensinde kæmpet med at beslutte, om PEEK er sin høje pris værd til din kritiske applikation? Når projektets succes afhænger af materialevalget, kan det være en svær balancegang at vælge mellem dyre højtydende plastmaterialer og mere økonomiske alternativer med reelle konsekvenser for pålideligheden og levetiden.
PEEK tilbyder enestående fordele, herunder bemærkelsesværdig varmebestandighed (op til 480 °F), fremragende kemisk resistens, fremragende mekanisk styrke og overlegne slidegenskaber. Disse fordele kommer dog med betydelige ulemper, herunder høje omkostninger (5-10 gange mere end standard teknisk plast), udfordrende bearbejdelighed, begrænsede farvemuligheder og dårlig UV-bestandighed.
Forstå PEEK's enestående egenskaber
PEEK (Polyetheretherketon) skiller sig ud blandt tekniske plastmaterialer på grund af sin unikke kombination af egenskaber, der gør det velegnet til de mest krævende anvendelser. Som en person, der har specificeret materialer til utallige præcisionskomponenter, har jeg på første hånd set, hvordan PEEK's egenskaber giver fordele i den virkelige verden.
Fordele ved termisk ydeevne
En af PEEK's mest imponerende egenskaber er den termiske stabilitet. Materialet bevarer sine mekaniske egenskaber ved temperaturer, der ville få de fleste plastmaterialer til at bryde katastrofalt sammen.
Temperaturkarakteristik | PEEK ydeevne | Sammenligning med standardplast |
---|---|---|
Kontinuerlig driftstemperatur | Op til 250 °C (480 °F) | 2-3× højere end de fleste tekniske plasttyper |
Glasovergangstemperatur | 143°C (289°F) | Bevarer stivheden ved højere temperaturer |
Smeltepunkt | 649°F (343°C) | Giver mulighed for dampsterilisering |
Termisk ledningsevne | 0,25 W/m-K | Bedre varmeafledning end mange plastmaterialer |
Denne enestående termiske modstand gør det muligt at bruge PEEK i applikationer nær varmekilder, hvor standardplast hurtigt ville blive deformeret eller nedbrudt. Jeg har hjulpet mange kunder med at udskifte defekte komponenter lavet af mindre gode materialer med PEEK-dele, der fortsætter med at fungere fejlfrit trods udfordrende termiske miljøer.
Fordele ved kemisk resistens
PEEK's kemiske resistensprofil er næsten lige så imponerende som dets termiske egenskaber. Materialet udviser fremragende modstandsdygtighed over for:
- Kulbrinter og organiske opløsningsmidler
- De fleste syrer og baser (undtagen koncentreret svovlsyre)
- Damp og varmt vand
- Væsker og brændstoffer til biler
- Medicinske steriliseringsprocesser
Denne brede kemikaliebestandighed gør PEEK særligt værdifuld i miljøer, hvor man forventer at blive udsat for flere aggressive stoffer. I halvlederindustrien kan PEEK-komponenter f.eks. modstå de barske kemikalier, der bruges i wafer-behandling, samtidig med at de bevarer dimensionsstabiliteten.
Fordele ved mekaniske egenskaber
PEEK's mekaniske styrke adskiller det fra de fleste andre termoplastmaterialer:
- Trækstyrke på 14.500 psi (kan sammenlignes med visse metaller)
- Fremragende modstandsdygtighed over for træthed
- Enestående slagfasthed og sejhed
- Overlegen slidstyrke
- Lav friktionskoefficient
Disse egenskaber gør PEEK velegnet til strukturelle anvendelser, hvor de fleste plasttyper ville bryde sammen. Jeg har specificeret PEEK til tandhjul, lejer og andre komponenter med høj slitage, der arbejder under betydelig mekanisk belastning, og ofte erstattet metaldele med lettere PEEK-alternativer, der giver yderligere fordele som korrosionsbestandighed og støjreduktion.
De væsentlige ulemper ved PEEK
På trods af de imponerende egenskaber har PEEK flere væsentlige ulemper, som man skal være opmærksom på, når man vælger materiale.
Omkostningsbegrænsninger
Den mest åbenlyse ulempe ved PEEK er prisen. Hos PTSMAKE er vi ofte nødt til at hjælpe kunderne med at forstå, at PEEK er dyrere end andre tekniske plastmaterialer:
- PEEK koster typisk 5-10 gange mere end teknisk plast som nylon eller acetal.
- Materialeomkostningerne for PEEK-dele kan være 20-30% højere end for tilsvarende metalkomponenter
- Den høje råvarepris påvirker økonomien for små dele betydeligt
Denne omkostningsfaktor tvinger ofte ingeniører til kun at reservere PEEK til de mest kritiske anvendelser, hvor dets unikke egenskaber er absolut nødvendige. I mange tilfælde anbefaler vi mere omkostningseffektive alternativer til ikke-kritiske komponenter i en samling.
Udfordringer i produktionen
PEEK giver flere produktionsudfordringer, som kan øge produktionskompleksiteten og -omkostningerne:
Bearbejdningsvanskeligheder: PEEK's høje termiske modstand betyder dårlig varmeledningsevne, hvilket medfører varmeudvikling under bearbejdning. Det kræver lavere skærehastigheder, hyppige værktøjsskift og omhyggelige kølestrategier.
Krav til forarbejdningstemperatur: Med et smeltepunkt på 343 °C (649 °F) kræver PEEK specialiseret højtemperaturudstyr til sprøjtestøbning og ekstrudering.
Begrænset behandlingsvindue: Forskellen mellem PEEK's smeltetemperatur og den begyndende nedbrydning er relativt lille, hvilket skaber udfordringer under behandlingen.
Krympning af formen: PEEK udviser betydelig krympning (omkring 1-1,3%) under afkøling, hvilket kræver præcist formdesign for at opnå snævre tolerancer.
Hos PTSMAKE har vi udviklet specialiserede bearbejdningsprotokoller til PEEK for at løse disse udfordringer, men de øger uundgåeligt de samlede omkostninger og kompleksiteten ved fremstilling af PEEK-komponenter.
Begrænsninger i anvendelsen
På trods af sine imponerende egenskaber har PEEK begrænsninger, der gør det uegnet til visse anvendelser:
- Dårlig UV-bestandighed: Uden tilsætningsstoffer nedbrydes PEEK, når det udsættes for langvarigt UV-lys, hvilket begrænser brugen af det i udendørs applikationer.
- Begrænsede farvemuligheder: På grund af sin naturlige gule/brune farve og høje forarbejdningstemperaturer er PEEK vanskelig at farve konsekvent.
- Elektriske begrænsninger: Selv om PEEK er en god isolator, er det ikke ideelt til højfrekvente elektriske anvendelser sammenlignet med specialiserede elektriske polymerer.
- Problemer med at knytte bånd: PEEK's kemiske modstandsdygtighed gør limning til en udfordring og kræver ofte særlige overfladebehandlinger.
Cost-benefit-analyse: Hvornår er PEEK det værd?
På grund af PEEK's betydelige merpris er det vigtigt med en grundig cost-benefit-analyse, før man specificerer dette materiale. Min erfaring er, at PEEK giver den bedste værdi i følgende scenarier:
Scenarier, hvor PEEK udmærker sig
Omgivelser med høj temperatur: Når driftstemperaturen overstiger 149 °C (300 °F), er PEEK ofte den eneste brugbare plastmulighed, hvilket gør den høje pris berettiget.
Kemisk aggressive miljøer: I applikationer, der udsættes for mange kemikalier eller særligt barske stoffer, forhindrer PEEK's brede kemiske resistens de hyppige udskiftninger, der kræves med mindre materialer.
Anvendelser med kritisk slid: For komponenter, der er udsat for konstant friktion og slid i kritiske systemer, kan PEEK's enestående slidstyrke og lave friktion forlænge serviceintervallerne dramatisk.
Krav til vægtreduktion: Når PEEK erstatter metalkomponenter i rumfart eller højtydende applikationer, kan forholdet mellem styrke og vægt give præstationsfordele, der retfærdiggør prisen.
Anvendelser af medicinske implantater: PEEK's biokompatibilitet og kemiske stabilitet gør det ideelt til langtidsimplanterbare enheder, hvor materialesvigt ikke er en mulighed.
Sammenligning af alternative materialer
Til anvendelser, der ikke specifikt kræver PEEK's ekstreme egenskaber, er der flere alternativer, der kan give tilstrækkelig ydeevne til en lavere pris:
Materiale | Komparativ fordel | Omkostninger vs. PEEK | Nøglebegrænsning |
---|---|---|---|
PPS (polyphenylensulfid) | God varmebestandighed (400°F) | 40-60% lavere | Mindre modstandsdygtig over for kemikalier |
PTFE (polytetrafluorethylen) | Overlegen kemisk modstandsdygtighed | 30-50% lavere | Dårlig mekanisk styrke |
PEI (polyetherimid) | God varmebestandighed, gennemsigtighed | 30-40% lavere | Mindre slidstærk |
PAI (polyamid-imid) | Høj styrke, god slidstyrke | 10-20% lavere | Sværere at behandle |
Acetal (POM) | Fremragende bearbejdelighed, lave omkostninger | 80-90% lavere | Begrænset temperaturbestandighed |
Branchespecifikke overvejelser
Forskellige industrier prioriterer forskellige aspekter af PEEK's egenskabsprofil:
Luft- og rumfart og forsvar
Inden for rumfart retfærdiggør PEEK's kombination af lav vægt, flammebestandighed (med tilsætningsstoffer) og termisk stabilitet den høje pris for komponenter som f.eks:
- Bøsninger og lejer i styresystemer
- Elektriske stik og isolatorer
- Strukturelle komponenter i højtemperaturzoner
- Brændstofsystemkomponenter, der kræver kemisk resistens
Medicin og sundhedspleje
Medicinalindustrien værdsætter PEEK for dets:
- Biokompatibilitet (implantatkvalitet)
- Modstandsdygtighed over for gentagen sterilisering
- Radiolucens (forstyrrer ikke røntgenbilleder)
- Mekaniske egenskaber svarende til knogler (når de er forstærkede)
Disse egenskaber gør PEEK ideelt til implanterbare enheder og kirurgiske instrumenter på trods af dets høje pris.
Industrielt udstyr
Til industrielle anvendelser afhænger beslutningen om at bruge PEEK typisk af driftsbetingelsernes sværhedsgrad:
- Ekstreme miljøer (høj temperatur, kemisk eksponering) retfærdiggør ofte PEEK
- Anvendelser, hvor nedetid er ekstremt dyrt, nyder godt af PEEK's pålidelighed
- Komponenter med høj præcision nyder godt af PEEK's dimensionsstabilitet
Hos PTSMAKE hjælper vi kunderne med at navigere i disse overvejelser for at afgøre, om PEEK's førsteklasses ydeevne retfærdiggør den høje pris i forhold til deres specifikke anvendelsesbehov.
Jeg genererer indholdet til kapitel 7 i artiklen "Hvorfor er PEEK så dyrt?" i henhold til dine krav.
Hvorfor er PEEK så dyrt?
Har du nogensinde oplevet et prischok, når du har bedt om et tilbud på PEEK-komponenter? Når ingeniører først møder prisen på denne højtydende plast, spørger mange, om noget materiale overhovedet kan retfærdiggøre en så høj pris, især når det sammenlignes med mere almindelige tekniske plastmaterialer, der ser ud til at have en god ydeevne til en brøkdel af prisen.
PEEK's høje pris skyldes den komplekse fremstillingsproces, dyre råmaterialer, krav til specialudstyr og relativt lave produktionsmængder. Den indviklede polymeriseringsproces kræver præcise betingelser, mens produktionsteknologiens proprietære karakter og PEEK's status som specialmateriale hæver markedsprisen yderligere.
Den komplekse fremstillingsproces bag PEEK
For at forstå, hvorfor PEEK har så høj en pris, skal man først undersøge fremstillingsprocessen. I modsætning til enklere polymerer involverer PEEK-produktion sofistikeret kemi og præcise forarbejdningsbetingelser, som har stor indflydelse på de endelige omkostninger.
Råvareomkostninger og knaphed
De monomerer, der bruges til at producere PEEK, er i sig selv dyre specialkemikalier. De primære ingredienser omfatter:
- Difenylether
- 4,4′-difluorbenzofenon
- Kaliumkarbonat
- Difenylsulfon (som opløsningsmiddel)
Disse forstadier kræver flere raffineringstrin for at opnå den renhed, der er nødvendig for PEEK-syntese, hvilket øger omkostningerne, før polymerisationen overhovedet begynder. Derudover har nogle af disse kemikalier begrænset produktionskapacitet på verdensplan, hvilket skaber forsyningsbegrænsninger, der driver priserne op.
Når vi hos PTSMAKE køber PEEK til bearbejdningsprojekter, betaler vi ikke kun for selve polymeren, men for hele værdikæden af specialkemikalier, der er indgået i fremstillingen af den.
Polymeriseringsprocessens kompleksitet
Syntesen af PEEK involverer en sofistikeret nukleofil aromatisk substitutionspolymerisationsproces. Denne reaktion skal foregå under præcist kontrollerede forhold:
- Temperaturer mellem 300-400 °C (572-752 °F)
- Inert atmosfære for at forhindre oxidering
- Specialiserede trykbeholdere
- Forlænget reaktionstid (ofte 3-5 timer)
- Omhyggelig håndtering af katalysatorer
Hvert af disse krav øger kompleksiteten og omkostningerne ved fremstillingen. Reaktionen skal overvåges nøje under hele forløbet for at sikre korrekt molekylvægtfordeling og krystallinitet, som direkte påvirker materialets egenskaber.
Begrænset produktionsskala og markedsdynamik
PEEK's status som specialmateriale har stor betydning for produktionsøkonomien og markedspriserne.
Proprietær teknologi og patentbeskyttelse
Den oprindelige PEEK-produktionsteknologi blev udviklet og patenteret af Victrex (tidligere ICI) i 1970'erne. Selv i dag er produktionsteknologien i vid udstrækning proprietær og beskyttet af forskellige patenter. Denne begrænsede konkurrence inden for fremstillingsmetoder har fastholdt en højere pris sammenlignet med almindelig plast.
Selv om der nu er flere producenter på verdensplan (herunder Victrex, Solvay og Evonik), bruger de hver især proprietære processer, som det har krævet enorme investeringer i forskning og udvikling at udvikle. Disse udviklingsomkostninger skal tjenes ind via materialepriserne.
Økonomi i produktionsvolumen
I modsætning til almindelig plast, der produceres i millioner af tons om året, fremstilles PEEK i relativt små mængder:
Plasttype | Global årlig produktion | Relativ omkostningsfaktor |
---|---|---|
Polyethylen (PE) | ~100 millioner tons | 1× (baseline) |
Nylon (PA) | ~8 millioner tons | 2-3× |
Polykarbonat (PC) | ~4,5 millioner tons | 3-4× |
PEEK | <10.000 tons | 30-50× |
Den begrænsede produktionsmængde betyder, at producenterne ikke kan opnå de stordriftsfordele, der får omkostningerne til almindelig plast til at falde. Faste omkostninger som vedligeholdelse af anlæg, kvalitetskontrol og forskning og udvikling fordeles på færre kilo produkt, hvilket øger omkostningerne pr. enhed.
Krav til udstyr og forarbejdning
Produktionsanlæggene til PEEK kræver specialudstyr, der kan håndtere de ekstreme temperaturer og tryk, der er nødvendige for polymerisering, blanding og forarbejdning:
- Højtemperaturreaktorer med præcise kontrolsystemer
- Specialiseret ekstruderings- og pelleteringsudstyr
- Avancerede filtrerings- og rensningssystemer
- Omfattende kvalitetskontrol og testfaciliteter
Disse kapitalinvesteringer er betydelige og bidrager væsentligt til de endelige materialeomkostninger. Når vi bearbejder PEEK-dele hos PTSMAKE, indregner vi disse produktionsomkostninger i råmaterialeprisen.
Udfordringer i forbindelse med forarbejdning og bearbejdning
Når PEEK er produceret, giver det ekstra udfordringer i forbindelse med forarbejdning og bearbejdning, som yderligere bidrager til de høje omkostninger ved færdige komponenter.
Høje forarbejdningstemperaturer
Med et smeltepunkt på ca. 343 °C (649 °F) kræver PEEK specialiseret forarbejdningsudstyr:
- Sprøjtestøbemaskiner med kapacitet til høje temperaturer
- Støbeforme med særlige varmestyringssystemer
- Dyrere varmeelementer og regulatorer
- Forbedrede sikkerhedssystemer til håndtering af materialer med høj temperatur
Disse krav betyder, at færre producenter er udstyret til at bearbejde PEEK, hvilket begrænser konkurrencen og fastholder højere bearbejdningsomkostninger.
Bearbejdningsovervejelser og værktøjsslitage
Når vi bearbejder PEEK ved PTSMAKE, støder vi på flere faktorer, der bidrager til højere produktionsomkostninger:
Slid på værktøjet: PEEK forårsager betydeligt mere værktøjsslitage end standardplast, hvilket kræver hyppigere udskiftning af værktøj eller brug af førsteklasses værktøj.
Håndtering af varme: PEEK's lave varmeledningsevne betyder, at der opbygges varme under bearbejdningen, hvilket kræver langsommere skærehastigheder og særlige køleteknikker.
Specialiseret ekspertise: Korrekt bearbejdning af PEEK kræver erfaring og viden for at forhindre materialenedbrydning og opnå snævre tolerancer.
Krav til efterbehandling: Mange PEEK-anvendelser kræver yderligere forarbejdningstrin som f.eks. udglødning for at afhjælpe indre spændinger og sikre dimensionsstabilitet.
Hver af disse faktorer øger de samlede omkostninger ved at producere færdige PEEK-komponenter ud over blot råvareprisen.
Omkostninger til kvalitetskontrol og certificering
Som et højtydende materiale, der ofte bruges i kritiske applikationer, kræver PEEK streng kvalitetskontrol under hele produktionen og forarbejdningen.
Strenge krav til testning
Hvert parti PEEK gennemgår typisk omfattende test for at verificere:
- Fordeling af molekylvægt
- Krystallinitet i procent
- Termiske egenskaber (glasovergang og smeltepunkter)
- Mekaniske egenskaber (trækstyrke, modulus, forlængelse)
- Renhed og niveauer af forurenende stoffer
Disse tests kræver specialiseret udstyr og uddannet personale, hvilket øger omkostningerne til kvalitetssikring betydeligt i forhold til den endelige produktpris.
Branchecertificeringer og sporbarhed
Mange PEEK-anvendelser i rumfarts-, medicinal- og halvlederindustrien kræver fuld materialesporbarhed og overholdelse af branchespecifikke standarder:
- Luft- og rumfartscertificeringer (AS9100, NORSOK)
- Standarder for medicinsk udstyr (ISO 13485, USP klasse VI)
- Certificeringer inden for den nukleare industri (NQSA-1)
- Krav til halvlederindustrien (høj renhed)
Opretholdelse af disse certificeringer kræver omfattende dokumentation, regelmæssige revisioner og nogle gange separate produktionsfaciliteter eller udstyr, hvilket alt sammen bidrager til højere omkostninger.
Sammenligning af PEEK med alternative materialer
For at forstå PEEK's pris i sammenhæng er det nyttigt at sammenligne det med alternative materialer med hensyn til både omkostninger og ydeevne.
Analyse af omkostninger og ydeevne
PEEK koster typisk 5-10 gange mere end almindelig teknisk plast og kan endda være dyrere end nogle specialmetaller på volumenbasis. Men dets ydeevne i ekstreme miljøer retfærdiggør ofte denne merpris:
Ejendom | PEEK | Standard Engineering Plastics | Førsteklasses metaller |
---|---|---|---|
Temperatur ved kontinuerlig brug | Op til 250 °C (480 °F) | 80-170°C (176-338°F) | Typisk ubegrænset |
Kemisk modstandsdygtighed | Fremragende | Variabel (ofte begrænset) | Ofte dårlig (korrosion) |
Specifik styrke | Meget høj | Moderat | Høj |
Omkostninger til råmaterialer | Meget høj | Lav til moderat | Moderat til høj |
Procesomkostninger | Høj | Lav til moderat | Høj |
Livstidsværdi | Fremragende | Begrænset under barske forhold | God, men med korrosionsproblemer |
Hos PTSMAKE hjælper vi ofte kunder med at evaluere disse afvejninger for at afgøre, om PEEK's højere pris er berettiget i forhold til dens fordele i deres specifikke applikation.
Er PEEK den høje pris værd?
Spørgsmålet om, hvorvidt PEEK's høje pris er berettiget, afhænger helt af kravene til anvendelsen.
Anvendelser, hvor PEEK giver værdi på trods af omkostninger
PEEK giver fremragende værdi på trods af sin høje pris i applikationer med:
- Ekstreme driftsmiljøer hvor andre materialer hurtigt ville svigte
- Vægtkritiske systemer hvor PEEK's styrke-til-vægt-forhold giver fordele
- Vedligeholdelsesfølsomt udstyr hvor omkostningerne ved nedetid langt overstiger materialeomkostningerne
- Ætsende miljøer hvor metaller ville blive nedbrudt hurtigt
- Medicinske implantater hvor biokompatibilitet og langtidsstabilitet er afgørende
I disse scenarier omsættes PEEK's ydelsesfordele direkte til lavere levetidsomkostninger på trods af den højere startinvestering.
Strategier til omkostningsreduktion for PEEK-komponenter
For projekter, der kræver PEEK's ydeevne, men er begrænset af budgettet, kan du overveje disse tilgange:
- Hybride designs Brug kun PEEK til kritiske komponenter
- Optimerede bearbejdningsteknikker at reducere materialespild
- Behandling af næsten-netform at minimere materialeforbruget
- Optimering af design for at reducere den samlede materialevolumen
- Uopfyldte karakterer når forstærkninger ikke er nødvendige for at præstere
Hos PTSMAKE har vi hjulpet mange kunder med at implementere disse strategier for at få PEEK's fordele og samtidig styre omkostningerne effektivt.
Hvordan optimerer man PEEK-bearbejdning til omkostningseffektiv produktion?
Har du nogensinde tænkt på, om der er en måde at udnytte PEEK's enestående egenskaber på uden at sprænge dit projektbudget? Når man arbejder med en af de dyreste tekniske plasttyper på markedet, handler optimering af bearbejdningen ikke kun om effektivitet - det kan betyde forskellen mellem et rentabelt projekt og et, der mister penge på grund af for meget materialespild og unødvendig bearbejdningstid.
Optimering af PEEK-bearbejdning til omkostningseffektiv produktion kræver brug af de rigtige skæreværktøjer (hårdmetal eller diamantbelagt), opretholdelse af passende hastigheder og tilspændinger (typisk langsommere end standardplast), implementering af effektive kølestrategier, minimering af materialespild ved hjælp af næsten-net-form-design og omhyggelig planlægning af værktøjsbaner for at reducere cyklustiderne.
Valg af det optimale værktøj til PEEK-bearbejdning
Når du bearbejder PEEK, har dit valg af værktøj stor indflydelse på både emnets kvalitet og de samlede bearbejdningsomkostninger. Jeg har lært gennem mange års erfaring, at hvis man investerer i de rigtige værktøjer på forhånd, sparer man betydeligt mere i det lange løb.
Skæreværktøjsmaterialer og -geometrier
Den slibende karakter af PEEK, især fyldte kvaliteter, der indeholder kulfiber eller glas, kræver omhyggeligt valg af værktøj:
Værktøjsmateriale | Bedst til | Værktøjets levetid | Omkostningsfaktor |
---|---|---|---|
Hårdmetal (ubelagt) | Ufyldt PEEK | God | Moderat |
Diamantbelagt hårdmetal | Fyldt PEEK | Fremragende | Høj |
PCD (polykrystallinsk diamant) | Produktion i store mængder | Overlegen | Meget høj |
Højhastighedsstål (HSS) | Enkle operationer på ufyldt PEEK | Begrænset | Lav |
Til de fleste opgaver hos PTSMAKE bruger vi hårdmetalværktøjer med specifikke geometrier, der er designet til højtydende plast. De vigtigste egenskaber, vi kigger efter, omfatter:
- Skarpe skærekanter (reducerer varmeudvikling)
- Høje positive hældningsvinkler (10-15°)
- Polerede riller (forbedrer spånevakuering)
- Tilstrækkelige frigangsvinkler (forhindrer gnidning)
Selv om premium-værktøjer koster mere i starten, bevarer de kantskarpheden længere og giver bedre overfladefinish, hvilket reducerer behovet for sekundære bearbejdninger.
Overvejelser om værktøjsslitage
Værktøjsslitage sker meget hurtigere ved bearbejdning af PEEK sammenlignet med almindelig teknisk plast. Vi har fundet ud af, at overvågning og styring af værktøjsslitage er afgørende for at opretholde både emnekvalitet og omkostningskontrol.
Jeg anbefaler, at man laver en tidsplan for værktøjsskift baseret på den bearbejdede mængde i stedet for at vente på visuelle tegn på slitage. I vores værksted skiftes værktøjer til bearbejdning af fyldt PEEK typisk efter ca. 60-70% af den værktøjslevetid, vi ville forvente ved bearbejdning af aluminium. Denne proaktive tilgang forhindrer de kvalitetsproblemer og potentielt kasserede dele, der opstår ved bearbejdning med slidte værktøjer.
Optimering af skæreparametre
At finde den rette balance mellem hastighed, tilspænding og skæredybde er afgørende for effektiv PEEK-bearbejdning. Målet er at maksimere materialefjernelseshastigheden uden at generere for meget varme eller gå på kompromis med overfladekvaliteten.
Anbefalinger om hastighed og foder
Gennem omfattende test hos PTSMAKE har vi udviklet disse generelle retningslinjer for PEEK-bearbejdningsparametre:
PEEK Type | Skærehastighed (SFM) | Tilførselshastighed | Skæredybde | Kølevæske |
---|---|---|---|---|
Ufyldt PEEK | 300-500 | Moderat | 0.005"-0.020" | Luft eller tåge |
30% Fyldt med kulstof | 200-400 | Reduceret (75%) | 0.005"-0.015" | Tåge/oversvømmelse |
30% Glasfyldt | 250-450 | Reduceret (85%) | 0.005"-0.015" | Tåge/oversvømmelse |
Disse parametre skal justeres ud fra dit specifikke værktøj, maskinens stivhed og emnets krav. Jeg anbefaler generelt at starte i den konservative ende af disse intervaller og gradvist øge parametrene, mens man overvåger resultaterne.
Strategier til håndtering af varme
PEEK's dårlige varmeledningsevne kan føre til varmeopbygning under bearbejdning, hvilket potentielt kan forårsage..:
- Dimensionel ustabilitet
- Forringet overfladefinish
- Accelereret slid på værktøjet
- Nedbrydning af materiale i ekstreme tilfælde
For at bekæmpe disse problemer implementerer vi flere teknikker til varmestyring:
Korrekt valg af kølevæske: Til ufyldt PEEK fungerer trykluftkøling ofte godt. Til fyldte kvaliteter giver tåge- eller oversvømmelseskøling bedre varmeafledning.
Intermitterende skæring: Når man holder pause med jævne mellemrum under dybe lommeoperationer, kan varmen spredes.
Klatrefræsning: Brug af klatrefræsning i stedet for konventionel fræsning reducerer friktion og varmeudvikling.
Flere lyspassager: Flere lette efterbehandlinger i stedet for en tung skæring forbedrer dimensionsnøjagtigheden og overfladefinishen.
Strategier for udnyttelse af materialer
På grund af PEEK's høje pris (ofte $75-200 per pund afhængigt af kvalitet og form) bliver materialeudnyttelsen en kritisk omkostningsfaktor. Hver eneste smule spild har direkte indflydelse på din bundlinje.
Udgangsmateriale med næsten netform
At starte med materiale, der er tættere på dine endelige dimensioner, kan reducere spild betydeligt. Overvej disse tilgange:
Tilpassede ekstruderinger: For dele med ensartede tværsnit kan det at starte med specialekstruderede profiler eliminere betydeligt materialespild. De højere opsætningsomkostninger opvejes af materialebesparelser ved større produktionskørsler.
Forudskårne emner: Hvis din materialeleverandør leverer forudskårne emner, der er dimensioneret specifikt til dine dele, reduceres både spild og den indledende bearbejdningstid.
Software til indlejring: For flade dele, der bearbejdes fra plade, kan brug af avanceret nesting-software optimere materialeforbruget med 15-30% sammenlignet med manuel layoutplanlægning.
Hos PTSMAKE har vi hjulpet kunder med at reducere PEEK-materialeomkostningerne med over 40% ved at implementere disse tilgange til deres højvolumenkomponenter.
Overvejelser om genbrug af chips
I modsætning til andre termoplaster kan PEEK ikke nemt genbruges internt på grund af den høje forarbejdningstemperatur. Der findes dog specialiserede genbrugstjenester:
- Rene, sorterede PEEK-chips kan sælges til genbrugsvirksomheder
- Nogle genbrugsvirksomheder krediterer materialeværdien mod fremtidige køb
- Fyldte kvaliteter har typisk lavere genbrugsværdi på grund af forureningsproblemer
Selv om genbrug ikke helt opvejer dine materialeomkostninger, kan det give en vis omkostningsdækning for større bearbejdningsoperationer.
Optimering af bearbejdningsstrategi
Ud over værktøj og parametre har din overordnede bearbejdningsmetode stor indflydelse på både emnets kvalitet og produktionsomkostningerne.
Fixturdesign til flere dele
Veldesignede fiksturer, der gør det muligt at bearbejde flere dele i en enkelt opsætning, giver flere fordele:
- Reduceret opsætningstid pr. del
- Forbedret konsistens på tværs af dele
- Mere effektiv udnyttelse af maskinerne
- Bedre materialeudbytte fra plademateriale
For en rumfartskunde designede vi en opspænding, der gjorde det muligt at bearbejde 16 små PEEK-komponenter samtidigt, hvilket reducerede omkostningerne pr. del med 62% sammenlignet med individuelle opsætninger.
Forbedring af CAM-strategi
Optimerede værktøjsbaner kan reducere bearbejdningstiden dramatisk og forbedre emnets kvalitet:
Høj effektiv fræsning: Brug af avancerede CAM-strategier, der opretholder ensartet værktøjsindgreb, reducerer cyklustiderne og forlænger værktøjets levetid.
Bearbejdning i hvile: Korrekt tilrettelagte arbejdsgange, hvor man bruger større værktøjer til at fjerne store mængder materiale og kun mindre værktøjer, hvor det er nødvendigt, optimerer både materialefjernelsen og værktøjets levetid.
Optimerede indflyvningsbevægelser: Minimering af luftskæring gennem effektive til- og frakørselsbevægelser kan reducere cyklustiderne med 5-15% uden at påvirke emnets kvalitet.
Kvalitetskontrol for at minimere skrot
På grund af PEEK's høje materialeomkostninger bliver reduktion af skrot en primær omkostningsbesparende strategi. Effektive kvalitetskontrolprocesser, der fanger problemer tidligt, forhindrer spild af dyrt materiale på dele, der ikke opfylder specifikationerne.
Måling undervejs i processen
Vi har implementeret flere verifikationstrin i processen:
Inspektion af første artikel: Grundig måling af den første del af hver serie, før man går videre med produktionen.
Trinvise inspektioner: Måling af kritiske funktioner, før man går videre til efterfølgende operationer, især når man vender eller fastgør dele igen.
Termisk stabilisering: Lad delene nå omgivelsestemperatur før de endelige målinger, da PEEK's varmeudvidelse kan påvirke dimensionerne.
Denne praksis har hjulpet os med at holde en skrotprocent på under 2% for PEEK-komponenter, hvilket er betydeligt lavere end branchens gennemsnit.
Overvejelser om efterbearbejdning
Processen slutter ikke, når emnet kommer ud af maskinen. Efterbearbejdningen kan have stor indflydelse på både kvalitet og omkostninger.
Stressaflastning og dimensionsstabilitet
PEEK-emner med komplekse geometrier eller ujævn materialefjernelse kan have gavn af spændingsaflastning for at sikre langsigtet dimensionsstabilitet:
Termisk glødning: Kontrolleret opvarmning under glasovergangstemperaturen efterfulgt af langsom afkøling kan afhjælpe indre spændinger.
Strategi fra grov til færdig: Ved at fjerne det meste materiale i en første arbejdsgang og derefter lade emnet stabilisere sig før den endelige bearbejdning forbedres målnøjagtigheden.
For kritiske komponenter med snævre tolerancer er disse ekstra skridt investeringen værd for at forhindre dyre fejl i marken eller dimensionsafvigelser over tid.
Ved at implementere disse optimeringsstrategier har vi hjulpet adskillige kunder hos PTSMAKE med at opnå omkostningseffektiv PEEK-bearbejdning uden at gå på kompromis med de enestående egenskaber, der gør dette materiale så værdifuldt. Nøglen er en holistisk tilgang, der tager højde for alle aspekter af fremstillingsprocessen, fra materialevalg til slutinspektion.
Lær om varmestyringsteknikker til højtydende plastbearbejdning. ↩
Lær avancerede teknikker til præcisionsbearbejdning af højtydende termoplast. ↩
Klik her for at udforske specialiserede teknikker til præcisionsbearbejdning af højtydende termoplast. ↩
Opdag, hvordan mekaniske egenskaber påvirker materialevalg til højtydende komponenter. ↩
Lær specialiserede bearbejdningsteknikker til at forhindre varmerelateret deformation i højtydende termoplast. ↩