Kämpfen Sie damit, das richtige Material für anspruchsvolle Anwendungen zu finden, bei denen Standardkunststoffe versagen? Viele Ingenieure stehen vor Herausforderungen, wenn Bauteile extremen Temperaturen, Chemikalien oder mechanischen Belastungen standhalten müssen. Herkömmliche Kunststoffe halten dem einfach nicht stand, was zu häufigen Teileausfällen und kostspieligen Ersatzteilen führt.
Unter PEEK-Bearbeitung versteht man das Schneiden, Bohren und Formen von Polyetheretherketon (PEEK) mit CNC-Maschinen. Dieser Hochleistungsthermoplast bietet eine außergewöhnliche Hitzebeständigkeit bis zu 480°F, eine hervorragende chemische Beständigkeit und eine mit einigen Metallen vergleichbare Festigkeit.
Ich habe mit zahllosen Kunden zusammengearbeitet, die für ihre kritischen Komponenten auf PEEK-Bearbeitung umgestiegen sind. Die Ergebnisse sprechen für sich - länger haltbare Teile, bessere Leistung in rauen Umgebungen und reduzierte Wartungszyklen. Wenn Sie sich fragen, ob PEEK die Lösung für Ihre Anwendung sein könnte, lesen Sie weiter und erfahren Sie mehr über die einzigartigen Eigenschaften und Bearbeitungstechniken, die dieses Material für die Präzisionsfertigung so wertvoll machen.
Ist PEEK besser für die Bearbeitung geeignet als Delrin?
Standen Sie schon einmal vor einem Dilemma bei der Materialauswahl und mussten sich zwischen PEEK und Delrin für Ihr wichtiges technisches Projekt entscheiden? Wenn es auf Leistung ankommt und Versagen keine Option ist, kann die Wahl des falschen Kunststoffs zu vorzeitigem Verschleiß, Anlagenstillstand und kostspieligen Umgestaltungen führen.
Während PEEK eine überlegene Temperaturbeständigkeit (bis zu 480°F), außergewöhnliche chemische Stabilität und höhere Festigkeit bietet, ist Delrin (POM) besser zerspanbar, formstabiler und kostengünstiger. Welche Wahl die "bessere" ist, hängt ganz von Ihren spezifischen Anwendungsanforderungen und Budgetbeschränkungen ab.
PEEK und Delrin verstehen: Grundlegende Unterschiede
Beim Vergleich dieser beiden technischen Hochleistungskunststoffe ist es wichtig, ihre grundlegende Zusammensetzung und ihre Eigenschaften zu kennen. PEEK (Polyetheretherketon) ist ein teilkristalliner Thermoplast mit außergewöhnlicher Beständigkeit gegen thermischen Abbau, während Delrin (Polyoxymethylen oder POM) ein Acetal-Homopolymer ist, das für seine hervorragende Dimensionsstabilität bekannt ist.
Vergleich der Materialeigenschaften
Die physikalischen und mechanischen Eigenschaften dieser Werkstoffe haben einen erheblichen Einfluss auf ihre Bearbeitungseigenschaften und ihre Leistung bei der Endanwendung.
Eigentum | PEEK | Delrin (POM) |
---|---|---|
Wärmeumlenkung Temperatur | 315°F (157°C) | 257°F (125°C) |
Zugfestigkeit | 14.500 psi | 10.000 psi |
Chemische Beständigkeit | Ausgezeichnet (widersteht den meisten Säuren und Basen) | Gut (empfindlich gegenüber starken Säuren) |
Abnutzungswiderstand | Überlegene | Sehr gut |
Kostenfaktor | 4-5x höher als Delrin | Mäßig |
Dichte | 1,32 g/cm³ | 1,41 g/cm³ |
Bearbeitungseigenschaften: Wie sie sich unter dem Werkzeug verhalten
Nach meiner Erfahrung bei PTSMAKE ist die Bearbeitbarkeit oft der entscheidende Faktor bei der Wahl zwischen diesen Materialien. Delrin lässt sich im Allgemeinen vorhersehbarer bearbeiten als PEEK und liefert mit weniger Aufwand glattere Oberflächen.
Werkzeugverschleiß und Schnittparameter
PEEK ist abrasiver gegenüber Schneidwerkzeugen und erfordert einen häufigeren Werkzeugwechsel. Bei der Bearbeitung von PEEK reduzieren wir die Schnittgeschwindigkeiten in der Regel um etwa 15-20% im Vergleich zu Delrin, um die Wärmeentwicklung zu minimieren. Dies ist von entscheidender Bedeutung, da die geringe Wärmeleitfähigkeit von PEEK zu einer Wärmekonzentration in der Schneidzone führt, die möglicherweise thermische Verformung1 wenn sie nicht richtig verwaltet werden.
Delrin hingegen bietet eine hervorragende Dimensionsstabilität bei der Bearbeitung und kann mit höheren Geschwindigkeiten geschnitten werden. Es verursacht weniger Werkzeugverschleiß und erfordert im Allgemeinen weniger spezielle Bearbeitungstechniken.
Überlegungen zur Oberflächenbeschaffenheit
Ein Vorteil von Delrin ist, dass sich mit Standardbearbeitungsparametern hervorragende Oberflächengüten erzielen lassen. PEEK erfordert oft zusätzliche Polierschritte, um eine vergleichbare Oberflächenqualität zu erreichen.
Kosten-Nutzen-Analyse für technische Anwendungen
Der Kostenunterschied zwischen diesen Materialien kann erheblich sein. PEEK kostet in der Regel 4-5 Mal so viel wie Delrin, so dass es wichtig ist, zu prüfen, ob seine erstklassigen Eigenschaften die Investition rechtfertigen.
Wenn PEEK seinen Premium-Preis rechtfertigt
Ich empfehle PEEK für Anwendungen mit:
- Extreme Betriebstemperaturen (über 250°F)
- Aggressive chemische Umgebungen
- Hohe mechanische Belastung bei erhöhten Temperaturen
- Medizinische oder Luft- und Raumfahrtanwendungen, die Biokompatibilität oder Flammbeständigkeit erfordern
Wenn Delrin die bessere Wahl ist
Delrin ist wirtschaftlich sinnvoller, wenn:
- Betriebstemperaturen bleiben unter 180°F
- Die chemische Belastung beschränkt sich auf moderate Lösungsmittel
- Kostensensibilität ist ein wichtiger Faktor
- Die Teile erfordern eine hervorragende Maßhaltigkeit und Präzision bei der Bearbeitung
- Hohe Produktionsmengen machen die Materialkosten zu einem wichtigen Faktor
Branchenspezifische Überlegungen
Verschiedene Branchen legen Wert auf unterschiedliche Materialeigenschaften. In der Luft- und Raumfahrt, wo wir zahlreiche Komponenten geliefert haben, rechtfertigen die Flammbeständigkeit und das außergewöhnliche Verhältnis zwischen Festigkeit und Gewicht von PEEK oft die höheren Kosten. Bei Anwendungen in der Automobilindustrie setzt sich Delrin mit seiner Kombination aus günstigen Kosten und guten mechanischen Eigenschaften durch.
Medizinische und lebensmittelverarbeitende Anwendungen
Für medizinische Geräte ist PEEK aufgrund seiner Biokompatibilität und Sterilisationsbeständigkeit von unschätzbarem Wert, auch wenn es einen Aufpreis kostet. Bei Geräten für die Lebensmittelverarbeitung ist Delrin aufgrund seiner FDA-Konformität und niedrigeren Kosten oft die erste Wahl, es sei denn, es geht um hohe Temperaturen.
Komponenten für Industriemaschinen
Bei industriellen Anwendungen hängt die Entscheidung häufig von den Betriebsbedingungen ab. Zahnräder, Lager und Verschleißteile, die unter moderaten Bedingungen eingesetzt werden, funktionieren hervorragend in Delrin, während diejenigen, die extremen Bedingungen ausgesetzt sind, von den überlegenen Eigenschaften von PEEK profitieren.
Die richtige Wahl für Ihre Anwendung
Die Entscheidung zwischen PEEK und Delrin sollte auf der Grundlage einer gründlichen Analyse Ihrer spezifischen Betriebsbedingungen getroffen werden. Bei PTSMAKE berücksichtigen wir:
- Maximale Betriebstemperatur
- Profil der chemischen Belastung
- Anforderungen an die mechanische Belastung
- Budgetzwänge
- Erwartungen an die Nutzungsdauer
Wenn Sie diese Faktoren sorgfältig mit den Eigenschaften der einzelnen Materialien abwägen, können Sie eine fundierte Entscheidung treffen, die ein ausgewogenes Verhältnis zwischen Leistung und Kosteneffizienz für Ihre spezielle Anwendung bietet.
Was ist der Unterschied zwischen Acetal und PEEK?
Hatten Sie schon einmal die Qual der Wahl zwischen Acetal und PEEK für Ihre kritischen technischen Komponenten? Wenn der Projekterfolg von der Materialauswahl abhängt, kann die falsche Wahl zu vorzeitigen Ausfällen, unerwarteten Ausfallzeiten und budgetbelastenden Umgestaltungen führen, die mit der richtigen Materialkenntnis hätten vermieden werden können.
Acetal (POM) und PEEK unterscheiden sich in erster Linie durch ihre Leistungsmerkmale und Kosten. PEEK bietet eine bessere Hitzebeständigkeit (480°F gegenüber 180°F), eine bessere chemische Beständigkeit und eine höhere Festigkeit, während Acetal eine ausgezeichnete Bearbeitbarkeit und Dimensionsstabilität bietet und deutlich weniger kostet, was es ideal für weniger anspruchsvolle Anwendungen macht.
Hauptunterschiede zwischen Acetal und PEEK
Das Verständnis der grundlegenden Unterschiede zwischen diesen beiden technischen Kunststoffen ist entscheidend, um fundierte Entscheidungen für Ihre Projekte zu treffen. Beide Materialien haben sich als erste Wahl in der Präzisionsfertigung etabliert, erfüllen aber aufgrund ihrer inhärenten Eigenschaften ganz unterschiedliche Zwecke.
Materialzusammensetzung und Struktur
Acetal, allgemein bekannt unter dem Markennamen Delrin (wenn es als Homopolymer vorliegt) oder unter seiner chemischen Bezeichnung Polyoxymethylen (POM), weist eine hochkristalline Struktur mit sich wiederholenden -CH₂O-Gruppen auf. Diese Struktur verleiht ihm eine ausgezeichnete Formbeständigkeit und Bearbeitbarkeit.
PEEK (Polyetheretherketon) hingegen gehört zur Familie der Polyaryletherketone und enthält aromatische Ringe, die durch Ether- und Ketonbindungen verbunden sind. Diese Molekularstruktur sorgt für außergewöhnliche thermische Stabilität und chemische Beständigkeit.
Vergleich der Leistungsmerkmale
Die Leistungsunterschiede zwischen diesen Materialien machen sie für unterschiedliche Anwendungen geeignet:
Eigentum | Acetal (POM) | PEEK | Am besten für |
---|---|---|---|
Hitzebeständigkeit | 180°F (82°C) kontinuierlich | 480°F (250°C) kontinuierlich | PEEK |
Chemische Beständigkeit | Gut (außer starke Säuren) | Ausgezeichnet (beständig gegen die meisten Chemikalien) | PEEK |
Zugfestigkeit | 8.800-10.000 psi | 14.500-16.000 psi | PEEK |
Abnutzungswiderstand | Sehr gut | Ausgezeichnet | PEEK |
Bearbeitbarkeit | Ausgezeichnet | Gut (erfordert spezielle Techniken) | Acetal |
Kostenfaktor | Basisreferenz (1×) | 4-7x höher als Acetal | Acetal |
Feuchtigkeitsabsorption | 0.2-0.25% | 0.1-0.15% | PEEK |
Kosten-Nutzen-Analyse
In den Jahren, in denen ich bei PTSMAKE mit Kunden zusammenarbeite, habe ich festgestellt, dass Kostenerwägungen häufig den anfänglichen Materialauswahlprozess bestimmen. Acetal ist wesentlich wirtschaftlicher als PEEK und daher die erste Wahl, wenn keine extremen Bedingungen herrschen.
Der hohe Preis von PEEK spiegelt seine überlegenen Leistungsmerkmale wider. Bei der Beurteilung, ob die zusätzliche Investition gerechtfertigt ist, sollten Sie die folgenden Faktoren berücksichtigen:
- Anforderungen an die Betriebstemperatur
- Profil der chemischen Belastung
- Mechanische Belastungen
- Erwartete Nutzungsdauer
- Kosten für Ausfallzeiten aufgrund von Komponentenausfällen
Überlegungen zur Bearbeitung
Werkzeugstandzeit und Schnittparameter
Acetal ist bekannt für seine außergewöhnliche Bearbeitbarkeit. Es schneidet sauber, hält enge Toleranzen ein und erzeugt mit minimalem Aufwand eine hervorragende Oberflächengüte. Standard-Hartmetallwerkzeuge funktionieren gut, und das Material verursacht keinen übermäßigen Werkzeugverschleiß.
PEEK stellt bei der Bearbeitung eine größere Herausforderung dar. Seine hohe Temperaturbeständigkeit bedeutet, dass die Wärmeableitung während der Bearbeitung schlecht ist, was sie erfordert:
- Geringere Schnittgeschwindigkeiten (normalerweise 20-30% langsamer als Acetal)
- Häufigere Werkzeugwechsel
- Sorgfältige Beachtung von Wärmestauungen
- Spezialisierte Kühltechniken
Bei PTSMAKE haben wir spezielle Wärmemanagement-Protokolle2 für die PEEK-Bearbeitung, um die Maßhaltigkeit zu gewährleisten und eine Materialverschlechterung während des Schneidprozesses zu verhindern.
Dimensionsstabilität
Acetal bietet eine ausgezeichnete Dimensionsstabilität nach der Bearbeitung, mit minimalem Verzug oder Spannungsrelaxation. Dies macht es besonders wertvoll für Präzisionskomponenten mit engen Toleranzen.
PEEK weist ebenfalls eine gute Dimensionsstabilität auf, erfordert jedoch sorgfältigere Glühverfahren, um die inneren Spannungen nach der Bearbeitung abzubauen. Ohne eine angemessene thermische Konditionierung können sich die Abmessungen von PEEK-Teilen im Laufe der Zeit leicht verändern, insbesondere bei Hochpräzisionsanwendungen.
Anwendungsspezifische Empfehlungen
Automobil und Transport
Bei Automobilanwendungen, bei denen die Temperaturen moderat bleiben (unter 180°F), bietet Acetal oft den besten Wert. Zu den üblichen Anwendungen gehören:
- Komponenten des Kraftstoffsystems
- Türverriegelungsmechanismen
- Clips und Befestigungselemente für die Innenverkleidung
- Lagerflächen in unkritischen Bereichen
Für Bereiche mit höheren Temperaturen, wie Komponenten unter der Motorhaube oder Teile in der Nähe von Auspuffanlagen, ist PEEK aufgrund seiner thermischen Stabilität trotz der höheren Kosten die bessere Wahl.
Medizin und Pharmazie
Die medizinische Industrie hat PEEK aufgrund seiner Biokompatibilität und Beständigkeit gegen Sterilisationsverfahren für sich entdeckt. Es wird häufig verwendet in:
- Implantierbare Geräte
- Chirurgische Instrumente
- Komponenten für die medizinische Bildgebung
- Laborausstattung
Acetal findet nach wie vor Anwendung in weniger anspruchsvollen medizinischen Bereichen, wie z. B.:
- Komponenten für Einweginstrumente
- Prüfvorrichtungen für das Labor
- Gehäuse für Diagnostikgeräte
Industrielle Ausrüstung
Bei Industriemaschinen hängt die Wahl oft von den Betriebsbedingungen ab:
- Standard-Betriebsumgebungen: Acetal bietet einen hervorragenden Wert für Zahnräder, Lager und Verschleißflächen unter normalen Bedingungen.
- Raue Umgebungen: PEEK rechtfertigt seinen hohen Preis, wenn es hohen Temperaturen, Chemikalien oder extremen mechanischen Belastungen ausgesetzt ist.
Die optimale Auswahl treffen
Wenn ich Kunden bei der Wahl zwischen Acetal und PEEK bei PTSMAKE helfe, empfehle ich einen systematischen Ansatz:
- Identifizierung der anspruchsvollsten Bedingungen, denen das Teil ausgesetzt ist (Temperatur, Chemikalien, Belastungen)
- Bestimmen Sie, ob die Eigenschaften von Acetal ausreichen, um diese Bedingungen zu bewältigen.
- Berechnen Sie den Kostenunterschied zwischen den Optionen für Ihren spezifischen Volumenbedarf
- Berücksichtigen Sie die Folgen eines Ausfalls und die damit verbundenen Kosten für Ausfallzeiten
- Bewerten Sie, ob die erstklassige Leistung von PEEK seinen höheren Preis rechtfertigt
Denken Sie daran, dass die Materialauswahl selten eine Einheitsgröße ist. Manchmal funktioniert ein hybrider Ansatz am besten, bei dem PEEK nur für die kritischsten Komponenten verwendet wird, während Acetal für weniger anspruchsvolle Teile innerhalb derselben Baugruppe eingesetzt wird.
Was ist der Unterschied zwischen PTFE und PEEK?
Haben Sie sich schon einmal im Meer der Hochleistungskunststoffe verirrt und wussten nicht, ob Sie PTFE oder PEEK für Ihre kritische Anwendung wählen sollten? Wenn die Projektfristen immer kürzer werden und die Materialauswahl über Erfolg oder Misserfolg Ihres Entwurfs entscheiden kann, kann der Druck, die richtige Wahl zu treffen, überwältigend sein, insbesondere wenn beide Materialien beeindruckende technische Spezifikationen aufweisen.
PTFE und PEEK sind beides Hochleistungsthermoplaste mit deutlichen Unterschieden. PTFE bietet eine unübertroffene chemische Beständigkeit, eine extrem niedrige Reibung (Koeffizient 0,05-0,10) und einen Einsatzbereich von -328°F bis 500°F, hat aber eine geringe mechanische Festigkeit. PEEK bietet überlegene mechanische Eigenschaften, eine ausgezeichnete Verschleißfestigkeit und behält seine strukturelle Integrität bis zu 480°F bei, ist aber besser bearbeitbar.
Molekulare Struktur und grundlegende Eigenschaften
Die grundlegenden Unterschiede zwischen PTFE und PEEK beginnen auf molekularer Ebene, was ihre unterschiedlichen Leistungsmerkmale in verschiedenen Anwendungen erklärt.
Chemische Zusammensetzung
PTFE (Polytetrafluorethylen) besteht aus einem Kohlenstoffgerüst, das vollständig von Fluoratomen umgeben ist. Diese einzigartige Struktur verleiht PTFE seine außergewöhnliche chemische Inertheit und seine geringen Reibungseigenschaften. Die Kohlenstoff-Fluor-Bindungen gehören zu den stärksten in der organischen Chemie und machen PTFE unglaublich widerstandsfähig gegen chemische Angriffe.
PEEK (Polyetheretherketon) hingegen hat eine komplexere Molekularstruktur mit aromatischen Ringen, die durch Ether- und Ketonbindungen verbunden sind. Dieses aromatische Grundgerüst verleiht PEEK seine ausgezeichnete mechanische Festigkeit und thermische Stabilität.
Vergleichende Immobilienanalyse
Eigentum | PTFE | PEEK | Vorteil |
---|---|---|---|
Maximale Dauergebrauchstemperatur | 500°F (260°C) | 480°F (250°C) | PTFE (leicht) |
Minimale Betriebstemperatur | -328°F (-200°C) | -65°F (-54°C) | PTFE |
Reibungskoeffizient | 0,05-0,10 (niedrigster Wert aller Feststoffe) | 0.35-0.40 | PTFE |
Zugfestigkeit | 3.000-5.000 psi | 14.000-16.000 psi | PEEK |
Chemische Beständigkeit | Übergeordnet (universal) | Ausgezeichnet (eingeschränkt durch starke Säuren) | PTFE |
Bearbeitbarkeit | Anspruchsvoll (weich, verformt sich leicht) | Gut | PEEK |
Abnutzungswiderstand | Schlecht bis mäßig | Ausgezeichnet | PEEK |
Elektrische Eigenschaften | Ausgezeichneter Isolator | Guter Isolator | PTFE |
Kostenfaktor | Mäßig | Hoch (3-4x mehr als PTFE) | PTFE |
Thermische Leistungsunterschiede
Das Temperaturverhalten ist oft ein entscheidender Faktor bei der Wahl zwischen diesen Materialien.
Hitzebeständigkeit und -stabilität
Beide Materialien bieten zwar eine außergewöhnliche Hitzebeständigkeit, verhalten sich aber bei höheren Temperaturen unterschiedlich. PTFE behält seine chemische Inertheit und geringe Reibung bis zu seiner Höchsttemperatur bei, beginnt aber bei viel niedrigeren Temperaturen (ca. 260°F/127°C) seine mechanische Integrität zu verlieren.
PEEK hingegen behält seine mechanische Festigkeit viel näher an seiner Höchsttemperatur bei. Dadurch wird PEEK bei Anwendungen, die sowohl Hitzebeständigkeit als auch mechanische Belastbarkeit erfordern, wesentlich wertvoller.
Ich habe zahlreiche Anwendungen gesehen, bei denen Kunden PTFE ursprünglich nur aufgrund der Temperaturwerte ausgewählt haben, um dann festzustellen, dass das Material den mechanischen Belastungen bei diesen Temperaturen nicht gewachsen war. Die Fähigkeit von PEEK, die strukturelle Integrität bei hohen Temperaturen aufrechtzuerhalten, macht es oft den höheren Preis wert.
Leistung bei kalten Temperaturen
Bei kryogenen Anwendungen ist PTFE deutlich im Vorteil. Es bleibt bis zu -200°C (-328°F) flexibel und funktionsfähig, während PEEK unter -54°C (-65°F) zunehmend spröde wird. Dies macht PTFE zur klaren Wahl für die Luft- und Raumfahrt, für Labore und andere Tiefsttemperaturbereiche.
Vergleich der mechanischen Festigkeit
Die mechanischen Eigenschaften dieser Materialien sind sehr unterschiedlich, so dass ihre Eignung anwendungsspezifisch ist.
Strukturelle Integrität unter Belastung
PEEK bietet eine weitaus bessere mechanische Leistung mit einer Zugfestigkeit von durchschnittlich 14.000-16.000 psi im Vergleich zu den bescheidenen 3.000-5.000 psi von PTFE. Dadurch eignet sich PEEK für tragende Anwendungen, bei denen sich PTFE schnell verformen oder versagen würde.
Wir bei PTSMAKE empfehlen PEEK häufig für Strukturkomponenten, die konstanten mechanischen Belastungen ausgesetzt sind, insbesondere bei hohen Temperaturen. Die außergewöhnliche Kriechfestigkeit des Materials ermöglicht es, die Dimensionsstabilität unter Dauerbelastung aufrechtzuerhalten.
Verschleißwiderstand und Reibung
Der bemerkenswert niedrige Reibungskoeffizient von PTFE (0,05-0,10) macht es zum Material der Wahl für Anwendungen, die eine minimale Reibung erfordern. Dieselbe Eigenschaft trägt jedoch auch zu seiner geringen Verschleißfestigkeit bei, da das Material in Situationen mit hohem Verschleiß leicht abgeschabt werden kann.
PEEK weist eine ausgezeichnete Verschleißfestigkeit auf und hat einen angemessenen Reibungskoeffizienten (0,35-0,40). Bei Anwendungen, die eine kontinuierliche Bewegung gegen andere Oberflächen erfordern, überlebt PEEK in der Regel deutlich länger als PTFE.
Viele unserer Kunden erreichen das Beste aus beiden Welten, indem sie PEEK als Strukturmaterial mit einer dünnen PTFE-Beschichtung oder -Auskleidung verwenden, wenn eine Reibungsreduzierung erforderlich ist.
Profile der chemischen Beständigkeit
Beide Materialien bieten eine außergewöhnliche chemische Beständigkeit, jedoch mit wichtigen Unterschieden.
Widerstandsfähigkeit gegen aggressive Umgebungen
PTFE ist der Goldstandard für chemische Beständigkeit, denn es ist praktisch inert gegenüber fast allen Chemikalien (mit seltenen Ausnahmen wie geschmolzenen Alkalimetallen und elementarem Fluor). Diese universelle chemische Beständigkeit macht PTFE in der chemischen Verarbeitung, der Halbleiterherstellung und in Laborumgebungen von unschätzbarem Wert.
PEEK bietet eine ausgezeichnete chemische Beständigkeit gegenüber den meisten Substanzen, kann jedoch von konzentrierter Schwefelsäure und einigen anderen starken Säuren angegriffen werden. Für die meisten industriellen Umgebungen ist die chemische Beständigkeit von PEEK jedoch mehr als ausreichend.
Hydrolyse und Feuchtigkeitsabsorption
PTFE ist vollständig hydrophob und nimmt auch nach längerer Einwirkung praktisch keine Feuchtigkeit auf. PEEK ist zwar sehr hydrolysebeständig, nimmt aber eine geringe Menge an Feuchtigkeit auf (0,1-0,3%), wenn es längere Zeit feuchten Umgebungen ausgesetzt ist.
Für Reinstwasseranwendungen oder Systeme, bei denen selbst kleinste Verunreinigungen nicht akzeptabel sind, bleibt PTFE trotz seiner mechanischen Einschränkungen oft die bevorzugte Wahl.
%[Bearbeitete Komponenten aus PEEK und PTFE für den strukturellen Vergleich](
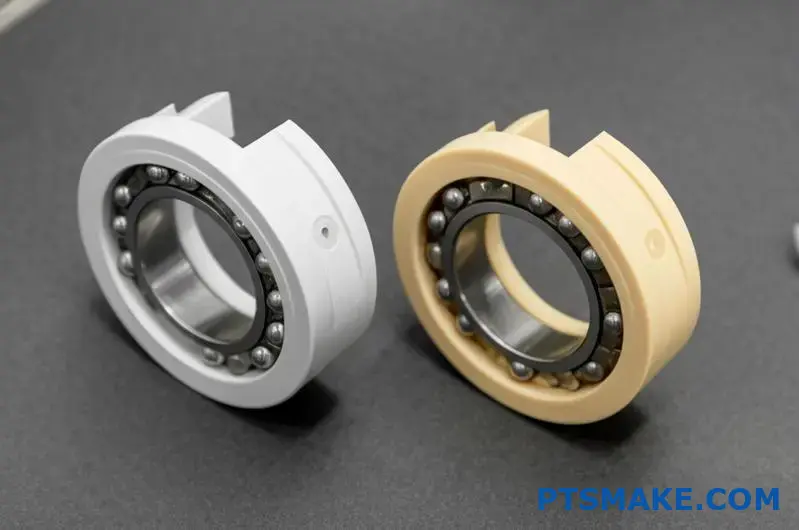
"PEEK- und PTFE-Lagerkomponenten")
Überlegungen zur Bearbeitung und Herstellung
Die Bearbeitbarkeit3 Die Unterschiede zwischen diesen Materialien haben erhebliche Auswirkungen auf die Herstellungskosten und -möglichkeiten.
Herausforderungen und Lösungen bei der Bearbeitung
PTFE stellt aufgrund seiner Weichheit und seiner Neigung zum Kaltfließen besondere Anforderungen an die Bearbeitung. Es erfordert spezielle Werkzeuge, langsamere Schnittgeschwindigkeiten und eine sorgfältige Befestigung, um Verformungen während der Bearbeitung zu vermeiden. Scharfe Werkzeuge sind unerlässlich, um ein Reißen oder Verformen des Materials zu verhindern.
PEEK lässt sich eher wie herkömmliche technische Kunststoffe bearbeiten, obwohl seine abrasive Beschaffenheit einen schnelleren Werkzeugverschleiß verursacht als viele andere Materialien. Bei der Bearbeitung von PEEK verwenden wir in der Regel Hartmetallwerkzeuge und geeignete Kühltechniken, um die Wärmeentwicklung zu kontrollieren.
Kompatibilität der Herstellungsprozesse
Die hohe Schmelzviskosität von PTFE macht herkömmliches Spritzgießen unmöglich. Stattdessen muss es mit Techniken wie Formpressen, Ramextrusion oder Schälen von Knüppeln verarbeitet werden. Dies schränkt die Designkomplexität ein und erhöht die Herstellungskosten für komplexe Formen.
PEEK kann mit herkömmlichen Verfahren wie Spritzguss und Extrusion verarbeitet werden, was komplexere Geometrien und potenziell niedrigere Produktionskosten bei höheren Stückzahlen ermöglicht. Diese Vielseitigkeit in der Verarbeitung verschafft PEEK einen Vorteil bei komplizierten Bauteilen oder beim Übergang von der Prototypen- zur Massenproduktion.
Kosten-Nutzen-Analyse für verschiedene Anwendungen
Der erhebliche Preisunterschied zwischen diesen Materialien erfordert eine sorgfältige Prüfung ihres anwendungsspezifischen Wertes.
Vergleich des Wertangebots
PEEK ist zwar in der Regel 3-4 Mal teurer als PTFE, aber seine überlegenen mechanischen Eigenschaften und seine Verschleißfestigkeit bieten oft einen besseren Langzeitnutzen bei Anwendungen, bei denen ein mechanisches Versagen kostspielig oder gefährlich wäre.
Für Anwendungen, die in erster Linie chemische Beständigkeit, geringe Reibung oder elektrische Isolationseigenschaften ohne nennenswerte mechanische Beanspruchung erfordern, bietet PTFE trotz seiner Einschränkungen in der Regel den besseren Wert.
Branchenspezifische Auswahlkriterien
Verschiedene Branchen legen Wert auf unterschiedliche Materialeigenschaften:
- Chemische Verarbeitung: Die universelle chemische Beständigkeit von PTFE überwiegt in der Regel seine mechanischen Einschränkungen.
- Luft- und Raumfahrt: Beide Materialien finden Anwendung, wobei PEEK für Strukturbauteile und PTFE für Dichtungen und elektrische Isolierungen verwendet wird.
- Medizinisch: Die Biokompatibilität und strukturelle Festigkeit von PEEK machen es zu einem beliebten Material für Implantate, während PTFE für Katheterauskleidungen und andere Anwendungen mit geringer Reibung bevorzugt wird.
- Halbleiter: PTFE dominiert aufgrund seiner außergewöhnlichen Reinheit und Beständigkeit gegen aggressive Chemikalien.
- Automobilindustrie: Die Verschleißfestigkeit und die mechanischen Eigenschaften von PEEK machen es zu einem wertvollen Material für mechanisch beanspruchte Komponenten im Motorraum.
Was ist der Unterschied zwischen PVDF und PEEK?
Standen Sie schon einmal vor dem Dilemma, sich zwischen PVDF und PEEK für ein kritisches Projekt entscheiden zu müssen, bei dem die Materialauswahl über Erfolg oder Misserfolg Ihrer Konstruktion entscheiden kann? Wenn Standardkunststoffe nicht ausreichen und Sie eine außergewöhnliche chemische Beständigkeit oder thermische Stabilität benötigen, kann die Verwirrung zwischen diesen beiden Hochleistungsmaterialien zu kostspieligen Fehlern oder Leistungseinbußen führen.
PVDF (Polyvinylidenfluorid) und PEEK (Polyetheretherketon) unterscheiden sich in erster Linie durch ihre Leistungsmerkmale und Anwendungen. PEEK bietet eine höhere Hitzebeständigkeit (480°F gegenüber 300°F), eine bessere mechanische Festigkeit und eine außergewöhnliche Verschleißfestigkeit, während PVDF eine ausgezeichnete chemische Beständigkeit und UV-Stabilität bietet und deutlich kostengünstiger ist.
Hauptunterschiede zwischen PVDF und PEEK
Beim Vergleich dieser beiden technischen Thermoplaste hilft das Verständnis ihrer grundlegenden Eigenschaften bei der Entscheidung, welches Material für bestimmte Anwendungen am besten geeignet ist. Beide Werkstoffe gelten als leistungsstarke Optionen, aber sie zeichnen sich in unterschiedlichen Umgebungen und Anwendungen aus.
Materialzusammensetzung und Struktur
PVDF ist ein halbkristallines Fluorpolymer, das aus sich wiederholenden Einheiten von Vinylidendifluorid besteht. Seine Molekularstruktur enthält Kohlenstoff-Fluor-Bindungen, die für eine ausgezeichnete chemische Beständigkeit sorgen, wenn auch nicht so umfassend wie bei vollfluorierten Polymeren wie PTFE.
PEEK gehört zur Familie der Polyaryletherketone und weist eine komplexe Molekularstruktur mit aromatischen Ringen auf, die durch Ether- und Ketonbindungen verbunden sind. Diese einzigartige Struktur verleiht PEEK seine außergewöhnliche thermische Stabilität und mechanische Festigkeit.
Vergleich der Leistungsmerkmale
Die folgende Tabelle enthält einen detaillierten Vergleich der wichtigsten Eigenschaften von PVDF und PEEK:
Eigentum | PVDF | PEEK | Überlegenes Material |
---|---|---|---|
Maximale Dauergebrauchstemperatur | 300°F (149°C) | 480°F (250°C) | PEEK |
Mechanische Festigkeit (Zugfestigkeit) | 5.800-7.800 psi | 14.500-16.000 psi | PEEK |
Chemische Beständigkeit | Ausgezeichnet (die meisten Säuren, Basen) | Sehr gut (eingeschränkt durch starke Säuren) | PVDF |
UV-Beständigkeit | Ausgezeichnet | Angemessen bis gut | PVDF |
Abnutzungswiderstand | Gut | Ausgezeichnet | PEEK |
Reibungskoeffizient | 0.25-0.35 | 0.35-0.40 | PVDF |
Kostenfaktor | Mäßig | 2-3x höher als PVDF | PVDF |
Feuchtigkeitsabsorption | 0.03-0.04% | 0.1-0.15% | PVDF |
Dichte | 1,75-1,78 g/cm³ | 1,30-1,32 g/cm³ | Anwendungsabhängig |
Thermische Leistung und Stabilität
Bei vielen technischen Anwendungen sind die Temperaturbedingungen ausschlaggebend für die Materialauswahl.
Vergleich der Hitzebeständigkeit
PEEK weist eine außergewöhnliche thermische Stabilität auf und behält seine mechanischen Eigenschaften bei Temperaturen von bis zu 250 °C (480 °F) im Dauereinsatz bei. Dies macht es ideal für Anwendungen in Hochtemperaturumgebungen, in denen herkömmliche Kunststoffe versagen würden.
PVDF gilt zwar immer noch als Hochtemperaturkunststoff, hat aber eine niedrigere maximale Dauergebrauchstemperatur von etwa 149°C (300°F). Dieser Temperaturbereich ist für viele industrielle Anwendungen ausreichend, reicht aber in extremen thermischen Umgebungen nicht aus.
Nach meiner Erfahrung in der Zusammenarbeit mit Kunden bei PTSMAKE wird dieser Temperaturunterschied oft zum entscheidenden Faktor bei der Auswahl zwischen diesen Materialien für Anwendungen wie Halbleiterverarbeitungsanlagen, wo die Prozesstemperaturen die Möglichkeiten von PVDF übersteigen können.
Thermisches Zyklusverhalten
Beide Materialien gehen unterschiedlich mit Temperaturschwankungen um:
- PVDF weist eine gute Dimensionsstabilität während der thermischen Wechselbeanspruchung auf, obwohl es eine stärkere thermische Ausdehnung als PEEK erfahren kann.
- PEEK behält seine außergewöhnliche Dimensionsstabilität auch bei wiederholten thermischen Zyklen bei, was es zu einem bevorzugten Material für Präzisionskomponenten macht, die enge Toleranzen bei unterschiedlichen Temperaturen einhalten müssen.
Profile der chemischen Beständigkeit
Die chemische Beständigkeit ist ein weiterer entscheidender Faktor, der diese Materialien auszeichnet.
Widerstandsfähigkeit gegen aggressive Umgebungen
PVDF bietet eine ausgezeichnete Beständigkeit gegen eine Vielzahl von Chemikalien, einschließlich:
- Die meisten Säuren (einschließlich konzentrierter Salzsäure und Schwefelsäure)
- Aliphatische und aromatische Kohlenwasserstoffe
- Alkohole und chlorierte Lösungsmittel
- Oxidationsmittel
PEEK weist eine gute chemische Beständigkeit gegenüber vielen Substanzen auf, kann jedoch von konzentrierter Schwefelsäure und einigen anderen starken Säuren angegriffen werden. Es ist besonders widerstandsfähig gegen Hydrolyse und Dampfsterilisation, was es für medizinische Anwendungen wertvoll macht.
Branchenspezifische chemische Erwägungen
Verschiedene Industriezweige legen Wert auf bestimmte Eigenschaften der Chemikalienbeständigkeit:
- Chemische Verarbeitung: PVDF wird häufig wegen seiner umfassenden Beständigkeit gegen Säuren und chlorierte Verbindungen bevorzugt.
- Halbleiter: Beide Materialien werden verwendet, wobei die Auswahl von den spezifischen Prozesschemikalien abhängt.
- Öl und Gas: Die Kombination aus mechanischen Eigenschaften und chemischer Beständigkeit macht PEEK zu einem wertvollen Material für Bohrlochanwendungen.
- Pharmazeutisch: Die ausgezeichnete Beständigkeit von PVDF gegenüber Reinigungsmitteln und Sterilisationsverfahren macht es zu einem beliebten Material für Verarbeitungsgeräte.
Mechanische Eigenschaften und strukturelle Anwendungen
Die mechanische Festigkeit4 Die Unterschiede zwischen diesen Materialien haben erhebliche Auswirkungen auf ihre Eignung für tragende Anwendungen.
Tragfähigkeiten
PEEK bietet eine wesentlich höhere mechanische Festigkeit mit Zugwerten von typischerweise 14.500-16.000 psi, verglichen mit den bescheideneren 5.800-7.800 psi von PVDF. Dadurch eignet sich PEEK hervorragend für Strukturkomponenten, die hohen mechanischen Belastungen standhalten müssen.
Für Anwendungen, die sowohl chemische Beständigkeit als auch strukturelle Integrität erfordern, bietet PEEK trotz seiner höheren Kosten oft das beste Gleichgewicht der Eigenschaften. Ich habe PEEK für zahlreiche Anwendungen bei PTSMAKE empfohlen, bei denen die Komponenten sowohl aggressiven Chemikalien als auch mechanischer Belastung standhalten müssen.
Verschleißwiderstand und Reibungseigenschaften
PEEK weist eine ausgezeichnete Verschleißfestigkeit auf und ist daher ideal für Lager, Buchsen und andere Komponenten, die ständiger Reibung ausgesetzt sind. Seine selbstschmierenden Eigenschaften tragen dazu bei, die Lebensdauer von beweglichen Teilen in anspruchsvollen Umgebungen zu verlängern.
PVDF bietet eine gute Verschleißfestigkeit, wenn auch nicht auf dem Niveau von PEEK. Sein niedrigerer Reibungskoeffizient (0,25-0,35 im Vergleich zu 0,35-0,40 bei PEEK) kann bei bestimmten Gleitanwendungen mit geringer Belastung von Vorteil sein, bei denen eine geringere Reibung wichtiger ist als maximale Verschleißfestigkeit.
Elektrische und thermische Isolationseigenschaften
Beide Materialien haben unterschiedliche elektrische Eigenschaften, die sie für verschiedene Anwendungen geeignet machen.
Dielektrische Eigenschaften
PVDF ist für seine piezoelektrischen Eigenschaften bekannt, die es ihm ermöglichen, als Reaktion auf eine mechanische Belastung eine elektrische Ladung zu erzeugen. Diese einzigartige Eigenschaft macht PVDF zu einem wertvollen Werkstoff für Sensoranwendungen.
PEEK bietet hervorragende elektrische Isolationseigenschaften über einen breiten Temperaturbereich und behält seine Durchschlagsfestigkeit auch bei höheren Temperaturen bei. Dies macht es besonders wertvoll für elektrische Hochtemperaturanwendungen, bei denen Standardkunststoffe versagen würden.
Wärmeleitfähigkeit
PVDF und PEEK haben beide eine relativ niedrige Wärmeleitfähigkeit im Vergleich zu Metallen, was sie zu guten Wärmeisolatoren macht:
- PVDF: 0,17-0,19 W/m-K
- PEEK: 0,25-0,29 W/m-K
Diese niedrige Wärmeleitfähigkeit kann je nach Anwendung entweder ein Vorteil oder ein Nachteil sein. Für Bauteile, die thermisch isoliert werden müssen, sind beide Materialien gut geeignet, wobei PVDF eine etwas bessere Isolierung bietet.
Kostenbetrachtungen und Wertanalyse
Der erhebliche Preisunterschied zwischen diesen Materialien macht eine Kosten-Nutzen-Analyse unerlässlich.
Ursprüngliche Materialkosten
PEEK ist in der Regel 2-3 Mal teurer als PVDF, was einen erheblichen Kostenaufschlag bedeutet, der durch die Leistungsanforderungen gerechtfertigt sein muss. Dieser Preisunterschied ergibt sich aus dem komplexeren Herstellungsverfahren von PEEK und den höheren Kosten für Rohstoffe.
Bewertung des Lebenszeitwerts
Bei der Bewertung der Gesamtbetriebskosten sollten neben den anfänglichen Materialkosten auch andere Faktoren berücksichtigt werden:
- Erwartete Nutzungsdauer in der Zielumgebung
- Häufigkeit des Austauschs und damit verbundene Kosten für Ausfallzeiten
- Installations- und Wartungsanforderungen
- Bedenken hinsichtlich Sicherheit und Zuverlässigkeit
In vielen Hochtemperatur- oder Hochlastanwendungen rechtfertigt die überlegene Leistung von PEEK die höheren Anschaffungskosten durch eine längere Lebensdauer und eine höhere Zuverlässigkeit. Bei Anwendungen, die den Möglichkeiten von PVDF entsprechen, bietet das kostengünstigere Material oft einen besseren Gesamtwert.
Überlegungen zur Verarbeitung und Herstellung
Auch die Fertigungsmöglichkeiten und -beschränkungen beeinflussen die Materialauswahl.
Unterschiede in der Bearbeitung
Bei der Bearbeitung dieser Materialien mit PTSMAKE haben wir erhebliche Unterschiede festgestellt:
- PVDF lässt sich relativ gut bearbeiten, erfordert aber scharfe Werkzeuge und angemessene Geschwindigkeiten, um Schmelzen oder Abrieb zu vermeiden.
- PEEK ist aufgrund seiner Abrasivität und schlechten Wärmeleitfähigkeit schwieriger zu bearbeiten, was zu einem Hitzestau während des Schneidens führen kann.
Bei Präzisionsbauteilen hält PEEK im Allgemeinen engere Toleranzen bei der Bearbeitung ein, erfordert aber auch speziellere Techniken und Werkzeuge, was die Herstellungskosten erhöhen kann.
Kompatibilität der Herstellungsmethoden
Beide Materialien können durch verschiedene Herstellungsmethoden verarbeitet werden:
- PVDF: Spritzgießen, Extrusion, Formpressen, Bearbeitung
- PEEK: Spritzgießen, Extrusion, Formpressen, maschinelle Bearbeitung, 3D-Druck (Spezialausrüstung)
PVDF bietet etwas mehr Verarbeitungsflexibilität bei niedrigeren Temperaturen, während PEEK höhere Verarbeitungstemperaturen erfordert, aber durch fortschrittliche Fertigungstechniken mehr Möglichkeiten für komplexe Geometrien bietet.
Anwendungsspezifische Auswahlrichtlinien
Verschiedene Branchen legen Wert auf unterschiedliche Materialeigenschaften, was zu unterschiedlichen Materialpräferenzen führt.
Halbleiterindustrie
In der Halbleiterfertigung finden beide Materialien Anwendung, allerdings in unterschiedlichen Bereichen:
- PVDF: Wird häufig für Reinstwassersysteme, Komponenten für die Chemikalienzufuhr und Filtrationsanlagen verwendet.
- PEEK: Bevorzugt für Komponenten, die hohen Temperaturen ausgesetzt sind, wie z. B. Wafer-Handling-Geräte und Prozesskammerkomponenten.
Ausrüstung für die chemische Verarbeitung
Für Anwendungen in der chemischen Verarbeitung:
- PVDF: Hervorragend geeignet für Pumpen, Ventile, Armaturen und Tanks, die mit korrosiven Chemikalien bei moderaten Temperaturen umgehen.
- PEEK: Besser geeignet für Bauteile, die sowohl chemische Beständigkeit als auch hohe Temperaturbeständigkeit oder mechanische Festigkeit erfordern.
Medizinische und pharmazeutische Anwendungen
In medizinischen Anwendungen:
- PVDF: Wird häufig für Filtermembranen, Nahtmaterial und einige implantierbare Geräte verwendet.
- PEEK: Bevorzugt für implantierbare Produkte, insbesondere für orthopädische Anwendungen, aufgrund seiner Biokompatibilität, Röntgendurchlässigkeit und knochenähnlichen mechanischen Eigenschaften.
Wenn ich Kunden bei der Auswahl zwischen PVDF und PEEK bei PTSMAKE helfe, empfehle ich einen systematischen Ansatz, bei dem zunächst die kritischsten Umgebungsfaktoren (Temperatur, Chemikalien, mechanische Belastung) bewertet werden und dann sekundäre Faktoren wie Kosten, Verarbeitungsanforderungen und Verfügbarkeit berücksichtigt werden.
<
Ist PEEK ein Polyethylen?
Haben Sie sich schon einmal von der Vielzahl der technischen Kunststoffe mit ähnlich klingenden Namen verwirren lassen? Bei der Auswahl von Materialien für kritische Anwendungen kann diese Verwirrung zu kostspieligen Fehlern, Leistungsausfällen und verschwendeten Ressourcen führen, wenn Sie irrtümlich einen Hochleistungskunststoff durch einen anderen ersetzen.
Nein, PEEK (Polyetheretherketon) ist kein Polyethylen. PEEK ist ein aromatischer Polyether mit Ketongruppen im Grundgerüst, der einen teilkristallinen Thermoplast mit außergewöhnlicher Hitzebeständigkeit (bis zu 480°F), hervorragender chemischer Beständigkeit und hervorragenden mechanischen Eigenschaften bildet, die weit über denen von Polyethylenmaterialien liegen.
Chemische Struktur und Klassifizierungsunterschiede
Bei der Untersuchung von PEEK und Polyethylen beginnen die grundlegenden Unterschiede auf molekularer Ebene. Diese strukturellen Unterschiede erklären, warum sich diese Materialien in praktischen Anwendungen so unterschiedlich verhalten.
Vergleich der molekularen Rückgrate
PEEK weist eine komplexe aromatische Grundstruktur mit Ether- und Ketonbindungen zwischen Benzolringen auf. Diese molekulare Architektur verleiht PEEK seine hervorragende thermische Stabilität und mechanische Festigkeit. Die aromatischen Ringe sorgen für Steifigkeit, während die Etherbindungen für eine gewisse Flexibilität sorgen.
Polyethylen hingegen hat eine der einfachsten Polymerstrukturen überhaupt - nur eine lineare Kette von Kohlenstoffatomen mit Wasserstoffatomen. Diese einfache Struktur gibt es in verschiedenen Formen (HDPE, LDPE, UHMWPE), aber allen fehlen die aromatischen Komponenten und funktionellen Gruppen, die PEEK seine außergewöhnlichen Eigenschaften verleihen.
Dieser grundlegende strukturelle Unterschied bedeutet, dass PEEK zu einer völlig anderen Polymerfamilie gehört als Polyethylen. Während Polyethylen als Polyolefin eingestuft wird, gehört PEEK zur Familie der Polyaryletherketone (PAEK), die zu den Hochleistungsthermoplasten gehören.
Wesentliche Eigenschaftsunterschiede
Die Unterschiede in der Molekularstruktur führen zu dramatischen Leistungsunterschieden:
Eigentum | PEEK | Polyethylen (HDPE) | Unterschiedsfaktor |
---|---|---|---|
Maximale Dauergebrauchstemperatur | 480°F (250°C) | 180°F (82°C) | PEEK ist 2,7x höher |
Zugfestigkeit | 14.500 psi | 4.500 psi | PEEK ist 3,2× stärker |
Chemische Beständigkeit | Ausgezeichnet (widersteht den meisten Chemikalien) | Gut (anfällig für aromatische Lösungsmittel) | PEEK bietet breitere Widerstandsfähigkeit |
Kosten | Hoch | Niedrig | PEEK kostet 15-20x mehr |
Dichte | 1,32 g/cm³ | 0,95 g/cm³ | PEEK ist 39% dichter |
Härte (Shore D) | 85-90 | 60-70 | PEEK ist wesentlich härter |
Unterschiede im Herstellungsprozess
Die Produktionsmethoden für PEEK und Polyethylen spiegeln ihre unterschiedlichen Molekularstrukturen und Leistungsmerkmale wider.
PEEK-Produktionsprozess
PEEK wird in einem komplexen Verfahren durch nukleophile aromatische Substitutionspolymerisation hergestellt. Dies erfordert eine präzise Temperaturkontrolle und spezielle Katalysatoren. Die Monomermaterialien sind wesentlich teurer als Ethylen, was zu den höheren Kosten von PEEK beiträgt.
Bei PTSMAKE müssen wir bei der Bearbeitung von PEEK-Bauteilen die einzigartigen Eigenschaften dieses Materials berücksichtigen. Aufgrund seiner geringeren Wärmeleitfähigkeit ist das Wärmemanagement während der Bearbeitung von entscheidender Bedeutung, um eine örtlich begrenzte thermische Schädigung zu verhindern.
Polyethylen-Herstellung
Polyethylen wird durch Additionspolymerisation von Ethylen unter Verwendung verschiedener Katalysatoren hergestellt, je nach gewünschter Dichte und Verzweigung. Dieses relativ einfache Verfahren kann bei niedrigeren Temperaturen und Drücken durchgeführt werden als die PEEK-Herstellung, insbesondere bei Sorten mit niedriger Dichte.
Leistung in extremen Umgebungen
Leistung bei hohen Temperaturen
Einer der wichtigsten Unterschiede zwischen diesen Materialien ist ihre thermische Stabilität:
- PEEK behält seine mechanischen Eigenschaften bis zu 250 °C (480 °F) im Dauereinsatz bei und kann kurzzeitig sogar noch höheren Temperaturen ausgesetzt werden.
- Polyethylen beginnt bei etwa 82°C (180°F) weich zu werden und verliert den größten Teil seiner mechanischen Festigkeit weit unter dieser Temperatur.
Ich habe zahlreiche Anwendungen gesehen, bei denen sich Kunden zunächst aufgrund der Kosten für Polyethylen entschieden haben, um dann festzustellen, dass es schnell versagt, wenn die Betriebstemperaturen die Erwartungen übersteigen. In einer Luft- und Raumfahrtanwendung wechselte ein Kunde für ein Bauteil in der Nähe einer Wärmequelle von Polyethylen zu PEEK und verlängerte so die Lebensdauer trotz der höheren anfänglichen Materialkosten von Monaten auf Jahre.
Chemische Beständigkeit im Vergleich
Beide Materialien bieten zwar eine gute chemische Beständigkeit, aber PEEK bietet einen umfassenderen Schutz vor aggressiven Chemikalien:
- PEEK widersteht den meisten Säuren, Basen, Kohlenwasserstoffen und organischen Lösungsmitteln
- Polyethylen hat eine gute Beständigkeit gegen Säuren und Basen, kann aber von aromatischen Kohlenwasserstoffen und einigen Oxidationsmitteln angegriffen werden.
Dieser Unterschied ist bei chemischen Verarbeitungsanlagen, in der Halbleiterfertigung und bei medizinischen Anwendungen, bei denen eine Exposition gegenüber mehreren Chemikalien üblich ist, von entscheidender Bedeutung.
Eignung der Anwendung
Luft- und Raumfahrt- und Verteidigungsanwendungen
In der Luft- und Raumfahrt ist PEEK dank seiner Kombination aus geringem Gewicht, Flammfestigkeit und thermischer Stabilität von unschätzbarem Wert für Komponenten wie:
- Innenraumkomponenten, die schwer entflammbar sein müssen
- Elektrische Steckverbinder und Isolatoren
- Strukturelle Komponenten in Hochtemperaturzonen
- Komponenten des Kraftstoffsystems, die chemische Beständigkeit erfordern
Polyethylen erfüllt aufgrund seiner begrenzten thermischen Stabilität und mechanischen Eigenschaften nur selten die hohen Anforderungen der Luft- und Raumfahrt.
Medizinische und gesundheitliche Verwendungszwecke
Auch die Biokompatibilitätsprofile dieser Materialien unterscheiden sich erheblich:
- PEEK ist biokompatibel und wird für implantierbare Geräte, chirurgische Instrumente und medizinische Geräte verwendet, die sterilisiert werden müssen.
- Polyethylen in medizinischer Qualität (hauptsächlich UHMWPE) wird in einigen Implantaten wie künstlichen Gelenken verwendet, verfügt jedoch nicht über die Temperaturbeständigkeit von PEEK für die wiederholte Dampfsterilisation.
Komponenten der Industrieausrüstung
Bei Industriemaschinen hängt die Wahl zwischen diesen Werkstoffen in der Regel von den Betriebsbedingungen ab:
- PEEK eignet sich hervorragend für Umgebungen mit hohen Temperaturen, Anwendungen, die eine hervorragende Verschleißfestigkeit erfordern, oder für den Kontakt mit aggressiven Chemikalien
- Polyethylen bietet eine angemessene Leistung für Anwendungen bei Umgebungstemperaturen mit mäßigen mechanischen Anforderungen und wird oft wegen seiner niedrigeren Kosten und einfachen Verarbeitung gewählt.
Kosten-Nutzen-Erwägungen
Der Preisunterschied zwischen diesen Materialien ist beträchtlich - PEEK kostet in der Regel 15-20 Mal mehr als Polyethylen hoher Dichte. Dieser erhebliche Kostenunterschied bedeutet, dass die Materialauswahl auf einer gründlichen Analyse basieren sollte:
- Erforderlicher Betriebstemperaturbereich
- Profil der chemischen Belastung
- Anforderungen an die mechanische Belastung
- Erwartete Nutzungsdauer
- Folgen des Scheiterns
Für Anwendungen, die innerhalb des Leistungsbereichs von Polyethylen liegen, ist PEEK aufgrund seiner niedrigeren Kosten die wirtschaftliche Wahl. Wenn die Leistungsanforderungen jedoch die Grenzen von Polyethylen überschreiten, rechtfertigen die überlegenen Eigenschaften von PEEK den höheren Preis durch längere Lebensdauer, höhere Zuverlässigkeit und geringere Wartungskosten.
Bearbeitungs- und Verarbeitungsunterschiede
Bei PTSMAKE haben wir erhebliche Unterschiede bei der Bearbeitung dieser Materialien festgestellt:
- PEEK erfordert aufgrund seiner Eigenschaften spezielle Schneidparameter Wärmeverhalten5 während der Bearbeitung, hält aber enge Toleranzen ein und erzeugt hervorragende Oberflächengüten
- Polyethylen ist leichter zu bearbeiten, neigt aber dazu, sich unter den Schnittkräften zu verformen, was die Einhaltung enger Toleranzen erschwert.
Das Verständnis dieser Verarbeitungsunterschiede ist für die Konstruktion von Bauteilen im Hinblick auf Herstellbarkeit und Präzision unerlässlich.
Was sind die Nachteile und Vorteile von PEEK?
Haben Sie schon einmal mit der Entscheidung gerungen, ob PEEK seinen hohen Preis für Ihre kritische Anwendung wert ist? Wenn der Projekterfolg von der Materialauswahl abhängt, kann die Entscheidung zwischen teuren Hochleistungskunststoffen und wirtschaftlicheren Alternativen eine schwierige Gratwanderung mit realen Auswirkungen auf Zuverlässigkeit und Langlebigkeit sein.
PEEK bietet außergewöhnliche Vorteile wie bemerkenswerte Hitzebeständigkeit (bis zu 480°F), hervorragende chemische Beständigkeit, ausgezeichnete mechanische Festigkeit und hervorragende Verschleißeigenschaften. Diese Vorteile sind jedoch mit erheblichen Nachteilen verbunden, wie z. B. hohen Kosten (5-10 Mal teurer als herkömmliche technische Kunststoffe), schwieriger Bearbeitbarkeit, begrenzten Farboptionen und geringer UV-Beständigkeit.
Die außergewöhnlichen Eigenschaften von PEEK verstehen
PEEK (Polyetheretherketon) zeichnet sich unter den technischen Kunststoffen durch seine einzigartige Kombination von Eigenschaften aus, die es für die anspruchsvollsten Anwendungen geeignet machen. Als jemand, der Materialien für zahllose Präzisionskomponenten spezifiziert hat, konnte ich aus erster Hand erfahren, wie sich die Eigenschaften von PEEK in der Praxis auswirken.
Thermische Leistung Vorteile
Eine der beeindruckendsten Eigenschaften von PEEK ist seine thermische Stabilität. Dieses Material behält seine mechanischen Eigenschaften bei Temperaturen, die bei den meisten Kunststoffen zu katastrophalem Versagen führen würden.
Temperatur-Charakteristik | PEEK Leistung | Vergleich mit Standardkunststoffen |
---|---|---|
Kontinuierliche Betriebstemperatur | Bis zu 480°F (250°C) | 2-3x höher als die meisten technischen Kunststoffe |
Glasübergangstemperatur | 289°F (143°C) | Behält die Steifigkeit bei höheren Temperaturen bei |
Schmelzpunkt | 649°F (343°C) | Ermöglicht die Dampfsterilisation |
Wärmeleitfähigkeit | 0,25 W/m-K | Bessere Wärmeableitung als viele Kunststoffe |
Dank dieser außergewöhnlichen Wärmebeständigkeit kann PEEK in Anwendungen in der Nähe von Wärmequellen eingesetzt werden, in denen sich Standardkunststoffe schnell verformen oder abbauen würden. Ich habe vielen Kunden geholfen, ausgefallene Komponenten aus minderwertigen Materialien durch PEEK-Teile zu ersetzen, die trotz schwieriger thermischer Umgebungen weiterhin einwandfrei funktionieren.
Chemische Beständigkeit Vorteile
Das chemische Beständigkeitsprofil von PEEK ist fast so beeindruckend wie seine thermischen Eigenschaften. Das Material zeigt eine ausgezeichnete Beständigkeit gegen:
- Kohlenwasserstoffe und organische Lösungsmittel
- Die meisten Säuren und Basen (außer konzentrierter Schwefelsäure)
- Dampf und Heißwasser
- Kfz-Flüssigkeiten und Kraftstoffe
- Medizinische Sterilisationsverfahren
Diese breite chemische Beständigkeit macht PEEK besonders wertvoll in Umgebungen, in denen mit einer Vielzahl aggressiver Substanzen zu rechnen ist. In der Halbleiterindustrie beispielsweise halten PEEK-Komponenten den aggressiven Chemikalien stand, die bei der Verarbeitung von Wafern verwendet werden, und bleiben dabei formstabil.
Mechanische Eigenschaften Vorteile
Die mechanische Festigkeit von PEEK hebt es von den meisten anderen Thermoplasten ab:
- Zugfestigkeit von 14.500 psi (vergleichbar mit einigen Metallen)
- Ausgezeichnete Ermüdungsfestigkeit
- Hervorragende Schlagfestigkeit und Zähigkeit
- Hervorragende Verschleißfestigkeit
- Niedriger Reibungskoeffizient
Dank dieser Eigenschaften eignet sich PEEK für strukturelle Anwendungen, bei denen die meisten Kunststoffe versagen würden. Ich habe PEEK für Zahnräder, Lager und andere verschleißintensive Komponenten spezifiziert, die unter erheblicher mechanischer Belastung arbeiten. Dabei habe ich oft Metallteile durch leichtere PEEK-Alternativen ersetzt, die zusätzliche Vorteile wie Korrosionsbeständigkeit und Geräuschreduzierung bieten.
Die signifikanten Nachteile von PEEK
Trotz seiner beeindruckenden Leistungsmerkmale weist PEEK einige erhebliche Nachteile auf, die bei der Materialauswahl sorgfältig berücksichtigt werden müssen.
Kostenzwänge
Der offensichtlichste Nachteil von PEEK sind seine Kosten. Bei PTSMAKE müssen wir unseren Kunden oft helfen, den Preisaufschlag von PEEK im Vergleich zu anderen technischen Kunststoffen zu verstehen:
- PEEK kostet in der Regel 5-10 Mal mehr als technische Kunststoffe wie Nylon oder Acetal
- Die Materialkosten für PEEK-Teile können 20-30% höher sein als für entsprechende Metallteile
- Der hohe Rohstoffpreis hat erhebliche Auswirkungen auf die Wirtschaftlichkeit von Kleinteilen
Dieser Kostenfaktor zwingt Ingenieure oft dazu, PEEK nur für die kritischsten Anwendungen zu verwenden, bei denen seine einzigartigen Eigenschaften unbedingt erforderlich sind. In vielen Fällen empfehlen wir kostengünstigere Alternativen für nicht kritische Komponenten in einer Baugruppe.
Herausforderungen bei der Herstellung
Die Herstellung von PEEK ist mit einigen Herausforderungen verbunden, die die Komplexität und die Kosten der Produktion erhöhen können:
Schwierigkeiten bei der Bearbeitung: Der hohe Wärmewiderstand von PEEK führt zu einer schlechten Wärmeleitfähigkeit und damit zu einem Wärmestau während der Bearbeitung. Dies erfordert langsamere Schnittgeschwindigkeiten, häufige Werkzeugwechsel und sorgfältige Kühlstrategien.
Anforderungen an die Verarbeitungstemperatur: Mit einem Schmelzpunkt von 343°C (649°F) erfordert PEEK spezielle Hochtemperaturanlagen für das Spritzgießen und die Extrusion.
Begrenztes Bearbeitungsfenster: Der Unterschied zwischen der Schmelztemperatur von PEEK und dem Beginn der Zersetzung ist relativ gering, was bei der Verarbeitung zu Problemen führt.
Schrumpfung: PEEK schrumpft beim Abkühlen erheblich (ca. 1-1,3%), was eine präzise Formgestaltung erfordert, um enge Toleranzen zu erreichen.
Bei PTSMAKE haben wir spezielle Bearbeitungsprotokolle für PEEK entwickelt, um diese Herausforderungen zu meistern, aber sie erhöhen zwangsläufig die Gesamtkosten und die Komplexität der Herstellung von PEEK-Komponenten.
Anwendungsbeschränkungen
Trotz seiner beeindruckenden Eigenschaften hat PEEK Einschränkungen, die es für bestimmte Anwendungen ungeeignet machen:
- Schlechte UV-Beständigkeit: Ohne Zusatzstoffe baut PEEK ab, wenn es längerem UV-Licht ausgesetzt wird, was seine Verwendung in Außenanwendungen einschränkt.
- Begrenzte Farboptionen: Aufgrund seiner natürlichen bernsteinfarbenen/braunen Farbe und der hohen Verarbeitungstemperaturen ist es schwierig, PEEK gleichmäßig einzufärben.
- Elektrische Beschränkungen: Obwohl PEEK ein guter Isolator ist, ist es im Vergleich zu speziellen elektrischen Polymeren nicht ideal für Hochfrequenzanwendungen.
- Schwierigkeiten bei der Bindung: Die chemische Beständigkeit von PEEK macht das Verkleben zu einer Herausforderung und erfordert häufig eine spezielle Oberflächenbehandlung.
Kosten-Nutzen-Analyse: Wann ist PEEK lohnenswert?
Angesichts des erheblichen Kostenaufschlags von PEEK ist eine gründliche Kosten-Nutzen-Analyse unerlässlich, bevor man sich für dieses Material entscheidet. Nach meiner Erfahrung bietet PEEK in den folgenden Szenarien den besten Nutzen:
Szenarien, in denen sich PEEK auszeichnet
Umgebungen mit hohen Temperaturen: Bei Betriebstemperaturen von über 149°C (300°F) ist PEEK oft die einzige brauchbare Kunststoffoption, so dass die hohen Kosten gerechtfertigt sind.
Chemisch-aggressive Einstellungen: Bei Anwendungen, die einer Vielzahl von Chemikalien oder besonders aggressiven Substanzen ausgesetzt sind, verhindert die breite chemische Beständigkeit von PEEK den häufigen Austausch, der bei weniger hochwertigen Materialien erforderlich ist.
Kritische Verschleißanwendungen: Bei Komponenten, die in kritischen Systemen ständiger Reibung und Abnutzung ausgesetzt sind, können die außergewöhnliche Verschleißfestigkeit und die geringe Reibung von PEEK die Wartungsintervalle drastisch verlängern.
Anforderungen zur Gewichtsreduzierung: Beim Ersatz von Metallkomponenten in der Luft- und Raumfahrt oder bei Hochleistungsanwendungen kann das Verhältnis von Festigkeit zu Gewicht von PEEK Leistungsvorteile bieten, die seine Kosten rechtfertigen.
Medizinische Implantatanwendungen: Die Biokompatibilität und chemische Stabilität von PEEK machen es ideal für langfristig implantierbare Produkte, bei denen ein Materialversagen nicht in Frage kommt.
Vergleich alternativer Materialien
Für Anwendungen, die nicht speziell die extremen Eigenschaften von PEEK erfordern, können mehrere Alternativen ausreichende Leistung zu geringeren Kosten bieten:
Material | Komparativer Vorteil | Kosten vs. PEEK | Taste Einschränkung |
---|---|---|---|
PPS (Polyphenylensulfid) | Gute Hitzebeständigkeit (400°F) | 40-60% unten | Weniger chemikalienbeständig |
PTFE (Polytetrafluorethylen) | Hervorragende chemische Beständigkeit | 30-50% unten | Schlechte mechanische Festigkeit |
PEI (Polyetherimid) | Gute Hitzebeständigkeit, Transparenz | 30-40% unten | Weniger verschleißfest |
PAI (Polyamid-Imid) | Hohe Festigkeit, gute Verschleißfestigkeit | 10-20% unten | Schwieriger zu verarbeiten |
Acetal (POM) | Hervorragende Bearbeitbarkeit, niedrige Kosten | 80-90% unten | Begrenzte Temperaturbeständigkeit |
Branchenspezifische Überlegungen
Verschiedene Industriezweige legen Wert auf unterschiedliche Aspekte des Eigenschaftsprofils von PEEK:
Luft- und Raumfahrt und Verteidigung
In der Luft- und Raumfahrt rechtfertigt die Kombination aus geringem Gewicht, Flammbeständigkeit (mit Additiven) und thermischer Stabilität den hohen Preis von PEEK für Komponenten wie:
- Buchsen und Lager in Steuerungssystemen
- Elektrische Steckverbinder und Isolatoren
- Strukturelle Komponenten in Hochtemperaturzonen
- Komponenten des Kraftstoffsystems, die chemische Beständigkeit erfordern
Medizin und Gesundheitswesen
Die medizinische Industrie schätzt PEEK wegen seiner:
- Biokompatibilität (Implantatqualität)
- Resistenz gegen wiederholte Sterilisation
- Röntgendurchlässigkeit (stört die Röntgenstrahlen nicht)
- Mechanische Eigenschaften ähnlich wie Knochen (wenn verstärkt)
Diese Eigenschaften machen PEEK trotz seiner hohen Kosten zu einem idealen Material für implantierbare Geräte und chirurgische Instrumente.
Industrielle Ausrüstung
Bei industriellen Anwendungen hängt die Entscheidung für die Verwendung von PEEK in der Regel von der Schwere der Betriebsbedingungen ab:
- Extreme Umgebungen (hohe Temperaturen, chemische Belastung) rechtfertigen oft die Verwendung von PEEK
- Anwendungen, bei denen Ausfallzeiten extrem kostspielig sind, profitieren von der Zuverlässigkeit von PEEK
- Hochpräzise Bauteile profitieren von der Dimensionsstabilität von PEEK
Wir von PTSMAKE helfen unseren Kunden, diese Überlegungen zu berücksichtigen, um festzustellen, ob die erstklassige Leistung von PEEK den hohen Preis für ihre spezifischen Anwendungsanforderungen rechtfertigt.
Ich erstelle den Inhalt für Kapitel 7 des Artikels "Why Is PEEK So Expensive?" nach Ihren Vorgaben.
Warum ist PEEK so teuer?
Haben Sie schon einmal einen Preisschock erlebt, als Sie ein Angebot für PEEK-Komponenten einholten? Wenn Ingenieure zum ersten Mal mit dem Preis dieses Hochleistungskunststoffs konfrontiert werden, fragen sich viele, ob ein Material überhaupt einen solchen Preisaufschlag rechtfertigen kann, vor allem im Vergleich zu gebräuchlicheren technischen Kunststoffen, die anscheinend eine angemessene Leistung zu einem Bruchteil des Preises bieten.
Die hohen Kosten von PEEK ergeben sich aus dem komplexen Herstellungsprozess, den teuren Rohstoffen, den speziellen Anforderungen an die Ausrüstung und den relativ geringen Produktionsmengen. Der komplizierte Polymerisationsprozess erfordert präzise Bedingungen, während die geschützte Natur der Produktionstechnologie und der Status von PEEK als Spezialmaterial den Marktpreis weiter erhöhen.
Der komplexe Herstellungsprozess von PEEK
Um zu verstehen, warum PEEK einen so hohen Preis hat, muss man sich zunächst den Herstellungsprozess ansehen. Im Gegensatz zu einfacheren Polymeren sind bei der Herstellung von PEEK eine ausgefeilte Chemie und präzise Verarbeitungsbedingungen erforderlich, die sich erheblich auf die Endkosten auswirken.
Rohstoffkosten und Knappheit
Die zur Herstellung von PEEK verwendeten Monomere sind selbst teure Spezialchemikalien. Zu den Hauptbestandteilen gehören:
- Diphenylether
- 4,4′-Difluorbenzophenon
- Kaliumkarbonat
- Diphenylsulfon (als Lösungsmittel)
Diese Ausgangsstoffe erfordern mehrere Raffinationsschritte, um die für die PEEK-Synthese erforderliche Reinheit zu erreichen, was die Kosten in die Höhe treibt, bevor die Polymerisation überhaupt beginnt. Außerdem sind die Produktionskapazitäten für einige dieser Chemikalien weltweit begrenzt, was zu Lieferengpässen führt, die die Preise in die Höhe treiben.
Wenn wir bei PTSMAKE PEEK für Bearbeitungsprojekte beziehen, zahlen wir nicht nur für das Polymer selbst, sondern auch für die gesamte Wertschöpfungskette von Spezialchemikalien, die in seine Herstellung eingeflossen sind.
Komplexität des Polymerisationsprozesses
Die Synthese von PEEK umfasst einen anspruchsvollen Prozess der nukleophilen aromatischen Substitutionspolymerisation. Diese Reaktion muss unter genau kontrollierten Bedingungen ablaufen:
- Temperaturen zwischen 300-400°C (572-752°F)
- Inerte Atmosphäre zur Vermeidung von Oxidation
- Spezialisierte Druckbehälter
- Längere Reaktionszeiten (oft 3-5 Stunden)
- Sorgfältiges Katalysatormanagement
Jede dieser Anforderungen erhöht die Komplexität und die Kosten der Herstellung. Die Reaktion muss während des gesamten Prozesses sorgfältig überwacht werden, um die richtige Molekulargewichtsverteilung und Kristallinität sicherzustellen, die sich direkt auf die Leistungseigenschaften des Materials auswirken.
Begrenzter Produktionsumfang und Marktdynamik
Der Status von PEEK als Spezialmaterial hat erhebliche Auswirkungen auf die Wirtschaftlichkeit der Produktion und die Marktpreise.
Proprietäre Technologie und Patentschutz
Die ursprüngliche PEEK-Herstellungstechnologie wurde in den 1970er Jahren von Victrex (früher ICI) entwickelt und patentiert. Auch heute noch ist die Produktionstechnologie weitgehend proprietär und durch verschiedene Patente geschützt. Dieser begrenzte Wettbewerb bei den Herstellungsverfahren hat dazu geführt, dass die Preise im Vergleich zu Standardkunststoffen höher sind.
Zwar gibt es inzwischen weltweit mehrere Hersteller (u. a. Victrex, Solvay und Evonik), aber alle verwenden proprietäre Verfahren, deren Entwicklung enorme F&E-Investitionen erfordert. Diese Entwicklungskosten müssen über die Materialpreise wieder hereingeholt werden.
Produktionsvolumen Wirtschaft
Im Gegensatz zu Massenkunststoffen, die jährlich in Millionen von Tonnen produziert werden, wird PEEK in relativ kleinen Mengen hergestellt:
Plastik Typ | Weltweite Jahresproduktion | Relativer Kostenfaktor |
---|---|---|
Polyethylen (PE) | ~100 Millionen Tonnen | 1× (Grundlinie) |
Nylon (PA) | ~8 Millionen Tonnen | 2-3× |
Polycarbonat (PC) | ~4,5 Millionen Tonnen | 3-4× |
PEEK | <10.000 Tonnen | 30-50× |
Dieses begrenzte Produktionsvolumen bedeutet, dass die Hersteller nicht die Größenvorteile erzielen können, die die Kosten für gängige Kunststoffe senken. Fixkosten wie Anlagenwartung, Qualitätskontrolle und F&E verteilen sich auf weniger Kilogramm des Produkts, was die Kosten pro Einheit erhöht.
Anforderungen an Ausrüstung und Verarbeitung
Die Produktionsanlagen für PEEK erfordern eine spezielle Ausrüstung, die den extremen Temperaturen und Drücken standhält, die für die Polymerisation, das Compoundieren und die Verarbeitung erforderlich sind:
- Hochtemperaturreaktoren mit präzisen Kontrollsystemen
- Spezialisierte Extrusions- und Granulieranlagen
- Fortschrittliche Filtrations- und Reinigungssysteme
- Umfassende Qualitätskontrolle und Prüfeinrichtungen
Diese Kapitalinvestitionen sind beträchtlich und tragen erheblich zu den endgültigen Materialkosten bei. Wenn wir PEEK-Teile bei PTSMAKE bearbeiten, werden diese vorgelagerten Herstellungskosten in den Rohstoffpreis eingerechnet.
Herausforderungen bei der Verarbeitung und Bearbeitung
Nach der Herstellung stellt PEEK zusätzliche Anforderungen an die Verarbeitung und Bearbeitung, die zu den hohen Kosten der fertigen Bauteile beitragen.
Hohe Verarbeitungstemperaturen
Mit einem Schmelzpunkt von ca. 343°C (649°F) erfordert PEEK spezielle Verarbeitungsanlagen:
- Spritzgießmaschinen mit Hochtemperaturfähigkeit
- Formen mit speziellen Wärmemanagementsystemen
- Teurere Heizelemente und Steuerungen
- Verbesserte Sicherheitssysteme für den Umgang mit Hochtemperaturmaterialien
Diese Anforderungen bedeuten, dass weniger Hersteller in der Lage sind, PEEK zu verarbeiten, was den Wettbewerb einschränkt und zu höheren Verarbeitungskosten führt.
Überlegungen zur Bearbeitung und zum Werkzeugverschleiß
Bei der Bearbeitung von PEEK bei PTSMAKE treffen wir auf mehrere Faktoren, die zu höheren Produktionskosten beitragen:
Werkzeugverschleiß: PEEK verursacht einen deutlich höheren Werkzeugverschleiß als Standardkunststoffe, was einen häufigeren Austausch der Werkzeuge oder die Verwendung hochwertiger Werkzeuge erfordert.
Wärmemanagement: Aufgrund der geringen Wärmeleitfähigkeit von PEEK entsteht bei der Bearbeitung ein Hitzestau, der langsamere Schnittgeschwindigkeiten und spezielle Kühltechniken erfordert.
Spezialisiertes Fachwissen: Die ordnungsgemäße Bearbeitung von PEEK erfordert Erfahrung und Wissen, um eine Materialverschlechterung zu verhindern und enge Toleranzen zu erreichen.
Nachbearbeitungsanforderungen: Viele PEEK-Anwendungen erfordern zusätzliche Verarbeitungsschritte wie das Glühen, um innere Spannungen abzubauen und die Dimensionsstabilität zu gewährleisten.
Jeder dieser Faktoren trägt über den reinen Rohstoffpreis hinaus zu den Gesamtkosten für die Herstellung fertiger PEEK-Komponenten bei.
Kosten für Qualitätskontrolle und Zertifizierung
Als Hochleistungsmaterial, das häufig in kritischen Anwendungen eingesetzt wird, erfordert PEEK eine strenge Qualitätskontrolle während der gesamten Produktion und Verarbeitung.
Strenge Prüfanforderungen
Jede PEEK-Charge wird in der Regel umfangreichen Tests unterzogen, um sie zu überprüfen:
- Molekulargewichtsverteilung
- Prozentsatz der Kristallinität
- Thermische Eigenschaften (Glasübergangs- und Schmelzpunkte)
- Mechanische Eigenschaften (Zugfestigkeit, Elastizitätsmodul, Dehnung)
- Reinheit und Schadstoffgehalt
Für diese Tests sind spezielle Geräte und geschultes Personal erforderlich, wodurch sich die Kosten für die Qualitätssicherung erheblich auf den Endpreis des Produkts auswirken.
Industriezertifizierungen und Rückverfolgbarkeit
Viele PEEK-Anwendungen in der Luft- und Raumfahrt, der Medizin und der Halbleiterindustrie erfordern eine vollständige Rückverfolgbarkeit des Materials und die Einhaltung branchenspezifischer Normen:
- Zertifizierungen für die Luft- und Raumfahrt (AS9100, NORSOK)
- Normen für Medizinprodukte (ISO 13485, USP Klasse VI)
- Zertifizierungen in der Nuklearindustrie (NQSA-1)
- Anforderungen der Halbleiterindustrie (hohe Reinheit)
Die Aufrechterhaltung dieser Zertifizierungen erfordert eine umfangreiche Dokumentation, regelmäßige Audits und manchmal separate Produktionsanlagen oder Ausrüstungen, was alles zu höheren Kosten führt.
Vergleich von PEEK mit alternativen Materialien
Um die Preisgestaltung von PEEK im Kontext zu verstehen, ist es hilfreich, es mit alternativen Materialien in Bezug auf Kosten und Leistung zu vergleichen.
Kosten-Leistungs-Analyse
PEEK kostet in der Regel 5-10 Mal mehr als herkömmliche technische Kunststoffe und kann sogar teurer sein als einige Spezialmetalle auf Volumenbasis. Seine Leistung in extremen Umgebungen rechtfertigt jedoch häufig diesen Aufpreis:
Eigentum | PEEK | Technische Standardkunststoffe | Hochwertige Metalle |
---|---|---|---|
Dauerbetrieb Temperatur | Bis zu 250°C (480°F) | 80-170°C (176-338°F) | In der Regel unbegrenzt |
Chemische Beständigkeit | Ausgezeichnet | Variabel (oft begrenzt) | Häufig schlecht (Korrosion) |
Spezifische Stärke | Sehr hoch | Mäßig | Hoch |
Kosten für Rohmaterial | Sehr hoch | Gering bis mäßig | Mäßig bis hoch |
Verarbeitungskosten | Hoch | Gering bis mäßig | Hoch |
Lebenszeit-Wert | Ausgezeichnet | Begrenzt unter rauen Bedingungen | Gut, aber mit Korrosionsproblemen |
Wir von PTSMAKE helfen unseren Kunden oft dabei, diese Kompromisse zu bewerten, um festzustellen, ob der hohe Preis von PEEK durch seine Leistungsvorteile in ihrer spezifischen Anwendung gerechtfertigt ist.
Ist PEEK den Premiumpreis wert?
Die Frage, ob die hohen Kosten von PEEK gerechtfertigt sind, hängt ganz von den Anforderungen der Anwendung ab.
Anwendungen, bei denen PEEK trotz der Kosten einen Mehrwert bietet
PEEK bietet trotz seines hohen Preises ein ausgezeichnetes Preis-Leistungs-Verhältnis in Anwendungen mit:
- Extreme Betriebsumgebungen wo andere Materialien schnell versagen würden
- Gewichtskritische Systeme wo das Verhältnis von Festigkeit zu Gewicht von PEEK Vorteile bietet
- Wartungsempfindliche Geräte wo die Kosten für Ausfallzeiten die Materialkosten weit übersteigen
- Korrosive Umgebungen wo sich Metalle schnell zersetzen würden
- Medizinische Implantate wo Biokompatibilität und Langzeitstabilität entscheidend sind
In diesen Szenarien schlagen sich die Leistungsvorteile von PEEK trotz der höheren Anfangsinvestition direkt in niedrigeren Lebenszykluskosten nieder.
Strategien zur Kostensenkung für PEEK-Komponenten
Für Projekte, die die Leistung von PEEK erfordern, aber nur ein begrenztes Budget zur Verfügung haben, bieten sich diese Ansätze an:
- Hybride Entwürfe Verwendung von PEEK nur für kritische Komponenten
- Optimierte Bearbeitungstechniken Verringerung des Materialabfalls
- Near-Net-Shape-Verarbeitung den Materialverbrauch zu minimieren
- Optimierung des Designs das gesamte Materialvolumen zu reduzieren
- Unbesetzte Stellen wenn Verstärkungen für die Leistung nicht notwendig sind
Bei PTSMAKE haben wir vielen Kunden geholfen, diese Strategien umzusetzen, um die Vorteile von PEEK zu nutzen und gleichzeitig die Kosten effektiv zu verwalten.
Wie lässt sich die PEEK-Bearbeitung für eine kosteneffiziente Produktion optimieren?
Haben Sie sich jemals gefragt, ob es einen Weg gibt, die außergewöhnlichen Eigenschaften von PEEK zu nutzen, ohne Ihr Projektbudget zu sprengen? Bei der Arbeit mit einem der teuersten technischen Kunststoffe auf dem Markt geht es bei der Optimierung Ihres Bearbeitungsansatzes nicht nur um Effizienz - es könnte den Unterschied zwischen einem rentablen Projekt und einem Projekt bedeuten, das durch übermäßigen Materialabfall und unnötige Bearbeitungszeit Geld verschlingt.
Die Optimierung der PEEK-Bearbeitung für eine kosteneffiziente Produktion erfordert die Verwendung geeigneter Schneidwerkzeuge (Hartmetall oder diamantbeschichtet), die Beibehaltung geeigneter Drehzahlen und Vorschübe (in der Regel langsamer als bei Standardkunststoffen), die Umsetzung wirksamer Kühlstrategien, die Minimierung des Materialabfalls durch eine endkonturnahe Konstruktion und eine sorgfältige Planung der Werkzeugwege zur Reduzierung der Zykluszeiten.
Auswahl des optimalen Werkzeugs für die PEEK-Bearbeitung
Bei der Bearbeitung von PEEK hat die Auswahl der Werkzeuge einen großen Einfluss auf die Qualität der Teile und die Gesamtbearbeitungskosten. Ich habe in jahrelanger Erfahrung gelernt, dass die Investition in die richtigen Werkzeuge im Vorfeld auf lange Sicht deutlich mehr spart.
Werkstoffe und Geometrien von Schneidwerkzeugen
Die abrasive Beschaffenheit von PEEK, insbesondere von gefüllten Typen mit Kohlenstofffasern oder Glas, erfordert eine sorgfältige Auswahl der Werkzeuge:
Werkzeug Material | Am besten für | Lebensdauer der Werkzeuge | Kostenfaktor |
---|---|---|---|
Hartmetall (unbeschichtet) | Ungefülltes PEEK | Gut | Mäßig |
Diamantbeschichtetes Hartmetall | Gefülltes PEEK | Ausgezeichnet | Hoch |
PCD (Polykristalliner Diamant) | Hochvolumige Produktion | Überlegene | Sehr hoch |
Hochgeschwindigkeitsstahl (HSS) | Einfache Operationen an ungefülltem PEEK | Begrenzt | Niedrig |
Für die meisten Anwendungen bei PTSMAKE verwenden wir Hartmetallwerkzeuge mit spezifischen Geometrien, die für Hochleistungskunststoffe ausgelegt sind. Zu den wichtigsten Merkmalen, auf die wir achten, gehören:
- Scharfe Schnittkanten (reduziert die Wärmeentwicklung)
- Hohe positive Spanwinkel (10-15°)
- Polierte Spannuten (verbessert die Spanabfuhr)
- Ausreichende Freiwinkel (verhindert Reibung)
Premium-Werkzeuge sind zwar zunächst teurer, behalten aber länger ihre Schärfe und erzeugen eine bessere Oberflächengüte, so dass weniger Nacharbeiten erforderlich sind.
Überlegungen zum Werkzeugverschleiß
Der Werkzeugverschleiß tritt bei der Bearbeitung von PEEK im Vergleich zu technischen Standardkunststoffen viel schneller auf. Wir haben festgestellt, dass die Überwachung und Steuerung des Werkzeugverschleißes sowohl für die Qualität der Teile als auch für die Kostenkontrolle entscheidend ist.
Ich empfehle, einen Zeitplan für den Werkzeugwechsel auf der Grundlage des bearbeiteten Volumens aufzustellen, anstatt auf visuelle Anzeichen von Verschleiß zu warten. In unserem Betrieb werden die Werkzeuge für die Bearbeitung von gefülltem PEEK in der Regel nach etwa 60-70% der Standzeit gewechselt, die wir bei der Bearbeitung von Aluminium erwarten würden. Dieser proaktive Ansatz verhindert Qualitätsprobleme und potenzielle Ausschussware, die aus der Bearbeitung mit abgenutzten Werkzeugen resultieren.
Optimierung der Schnittparameter
Für eine effiziente PEEK-Bearbeitung ist es entscheidend, die richtige Balance zwischen Geschwindigkeit, Vorschub und Schnitttiefe zu finden. Ziel ist es, den Materialabtrag zu maximieren, ohne übermäßige Hitze zu erzeugen oder die Oberflächenqualität zu beeinträchtigen.
Empfehlungen für Geschwindigkeit und Vorschub
Durch umfangreiche Tests bei PTSMAKE haben wir diese allgemeinen Richtlinien für PEEK-Bearbeitungsparameter entwickelt:
PEEK-Typ | Schnittgeschwindigkeit (SFM) | Vorschubgeschwindigkeit | Schnitttiefe | Kühlmittel |
---|---|---|---|---|
Ungefülltes PEEK | 300-500 | Mäßig | 0.005"-0.020" | Luft oder Nebel |
30% Kohlenstoffgefüllt | 200-400 | Ermäßigt (75%) | 0.005"-0.015" | Nebel/Hochwasser |
30% Glasgefüllt | 250-450 | Ermäßigt (85%) | 0.005"-0.015" | Nebel/Hochwasser |
Diese Parameter sollten auf der Grundlage Ihrer spezifischen Werkzeuge, Maschinensteifigkeit und Teileanforderungen angepasst werden. Im Allgemeinen empfehle ich, am konservativen Ende dieser Bereiche zu beginnen und die Parameter schrittweise zu erhöhen, während die Ergebnisse überwacht werden.
Strategien zum Wärmemanagement
Die schlechte Wärmeleitfähigkeit von PEEK kann während der Bearbeitung zu einem Hitzestau führen, der möglicherweise die Ursache ist:
- Instabilität der Dimensionen
- Verschlechterte Oberflächenqualität
- Beschleunigter Werkzeugverschleiß
- Materialzersetzung im Extremfall
Um diese Probleme zu bekämpfen, setzen wir verschiedene Wärmemanagementtechniken ein:
Richtige Auswahl des Kühlmittels: Bei ungefülltem PEEK funktioniert die Kühlung mit Druckluft oft gut. Bei gefüllten Qualitäten sorgen Nebel- oder Flutkühlmittel für eine bessere Wärmeableitung.
Intermittierendes Schneiden: Regelmäßige Pausen während des Tiefbohrens sorgen dafür, dass die Wärme abgeleitet werden kann.
Steigfräsen: Gleichlauffräsen anstelle von konventionellem Fräsen reduziert Reibung und Wärmeentwicklung.
Mehrere Lichtdurchgänge: Mehrere leichte Schlichtdurchgänge anstelle eines schweren Schnitts verbessern die Maßgenauigkeit und die Oberflächengüte.
Strategien für die Materialverwendung
Angesichts der hohen Kosten von PEEK (oft $75-200 pro Pfund, je nach Qualität und Form) wird die Materialausnutzung zu einem entscheidenden Kostenfaktor. Jedes bisschen Abfall wirkt sich direkt auf Ihr Endergebnis aus.
Beinahe-Net-Shape-Ausgangsmaterial
Wenn Sie mit Material beginnen, das näher an Ihren endgültigen Abmessungen liegt, können Sie den Abfall erheblich reduzieren. Ziehen Sie diese Ansätze in Betracht:
Kundenspezifische Extrusionen: Bei Teilen mit gleichmäßigem Querschnitt kann durch die Verwendung von kundenspezifischen Strangpressprofilen erheblicher Materialabfall vermieden werden. Die höheren Einrichtungskosten werden durch Materialeinsparungen bei größeren Produktionsserien ausgeglichen.
Vorgeschnittene Rohlinge: Wenn Ihr Materiallieferant speziell für Ihre Teile zugeschnittene Rohlinge liefert, verringert sich sowohl der Ausschuss als auch die anfängliche Bearbeitungszeit.
Nesting-Software: Bei flachen Teilen, die aus Blechen gefertigt werden, kann die Verwendung einer fortschrittlichen Verschachtelungssoftware den Materialverbrauch um 15-30% im Vergleich zur manuellen Layoutplanung optimieren.
Bei PTSMAKE haben wir Kunden geholfen, die PEEK-Materialkosten um mehr als 40% zu senken, indem wir diese Ansätze für ihre hochvolumigen Komponenten umgesetzt haben.
Überlegungen zum Chip-Recycling
Im Gegensatz zu anderen Thermoplasten kann PEEK aufgrund seiner hohen Verarbeitungstemperatur nicht ohne weiteres selbst recycelt werden. Es gibt jedoch spezialisierte Recyclingdienste:
- Saubere, sortierte PEEK-Chips können an Recycler verkauft werden
- Einige Recycler schreiben den Materialwert für künftige Käufe gut.
- Gefüllte Sorten haben in der Regel einen geringeren Recyclingwert aufgrund von Verunreinigungsproblemen.
Auch wenn das Recycling Ihre Materialkosten nicht vollständig ausgleichen kann, kann es bei größeren Bearbeitungsvorgängen eine gewisse Kostendeckung ermöglichen.
Optimierung der Bearbeitungsstrategie
Abgesehen von den Werkzeugen und Parametern wirkt sich Ihr gesamter Bearbeitungsansatz erheblich auf die Qualität der Teile und die Produktionskosten aus.
Vorrichtungsdesign für mehrere Teile
Gut konzipierte Spannvorrichtungen, die die Bearbeitung mehrerer Teile in einer einzigen Aufspannung ermöglichen, bieten mehrere Vorteile:
- Reduzierte Rüstzeit pro Teil
- Verbesserte Konsistenz zwischen den Teilen
- Effizientere Maschinennutzung
- Bessere Materialausbeute aus Plattenmaterial
Für einen Kunden aus der Luft- und Raumfahrtindustrie haben wir eine Vorrichtung entwickelt, mit der 16 kleine PEEK-Komponenten gleichzeitig bearbeitet werden können, was die Kosten pro Teil um 62% im Vergleich zu Einzelanfertigungen reduziert.
Verfeinerung der CAM-Strategie
Optimierte Werkzeugwege können die Bearbeitungszeit drastisch reduzieren und die Teilequalität verbessern:
Hocheffizientes Fräsen: Der Einsatz fortschrittlicher CAM-Strategien, die einen konstanten Werkzeugeingriff gewährleisten, reduziert die Zykluszeiten und verlängert die Lebensdauer der Werkzeuge.
Restbearbeitung: Richtig aufeinanderfolgende Arbeitsgänge, bei denen größere Werkzeuge für den Großteil des Materials und kleinere Werkzeuge nur bei Bedarf eingesetzt werden, optimieren sowohl die Abtragsleistung als auch die Werkzeugstandzeit.
Optimierte Annäherungsbewegungen: Die Minimierung des Luftschneidens durch effiziente An- und Abfahrbewegungen kann die Zykluszeiten um 5-15% reduzieren, ohne die Qualität der Teile zu beeinträchtigen.
Qualitätskontrolle zur Minimierung von Ausschuss
Angesichts der hohen Materialkosten von PEEK wird die Reduzierung von Ausschuss zu einer primären Kosteneinsparungsstrategie. Effektive Qualitätskontrollprozesse, die Probleme frühzeitig erkennen, verhindern die Verschwendung von teurem Material für Teile, die nicht den Spezifikationen entsprechen.
In-Process-Messung
Wir haben mehrere Schritte zur prozessbegleitenden Überprüfung eingeführt:
Erste Artikelüberprüfung: Der erste Teil jedes Durchlaufs wird gründlich vermessen, bevor mit der Produktion begonnen wird.
Abgestufte Inspektionen: Messen Sie kritische Merkmale, bevor Sie mit den nachfolgenden Bearbeitungen fortfahren, insbesondere beim Wenden oder erneuten Einspannen von Teilen.
Thermische Stabilisierung: Die Teile müssen vor den endgültigen Messungen die Umgebungstemperatur erreichen, da die Wärmeausdehnung von PEEK die Abmessungen beeinflussen kann.
Diese Praktiken haben dazu beigetragen, dass wir eine Ausschussrate von unter 2% für PEEK-Komponenten beibehalten konnten, was deutlich unter dem Branchendurchschnitt liegt.
Überlegungen zur Nachbearbeitung
Der Prozess ist nicht zu Ende, wenn das Teil aus der Maschine kommt. Nachbearbeitungsschritte können sowohl die Qualität als auch die Kosten erheblich beeinflussen.
Spannungsabbau und Formstabilität
PEEK-Teile mit komplexen Geometrien oder ungleichmäßigem Materialabtrag können von einer Spannungsentlastung profitieren, um eine langfristige Dimensionsstabilität zu gewährleisten:
Thermisches Glühen: Durch kontrolliertes Erhitzen unter die Glasübergangstemperatur und anschließendes langsames Abkühlen können innere Spannungen abgebaut werden.
Grob-zu-Fertig-Strategie: Das Entfernen des meisten Materials in einem ersten Arbeitsgang und die anschließende Stabilisierung des Teils vor der endgültigen Bearbeitung verbessert die Maßgenauigkeit.
Bei kritischen Komponenten mit engen Toleranzen sind diese zusätzlichen Schritte die Investition wert, um kostspielige Ausfälle vor Ort oder Maßabweichungen im Laufe der Zeit zu vermeiden.
Durch die Umsetzung dieser Optimierungsstrategien haben wir zahlreichen Kunden von PTSMAKE geholfen, PEEK kostengünstig zu bearbeiten, ohne die außergewöhnlichen Leistungseigenschaften zu beeinträchtigen, die dieses Material so wertvoll machen. Der Schlüssel ist ein ganzheitlicher Ansatz, der jeden Aspekt des Fertigungsprozesses berücksichtigt, von der Materialauswahl bis zur Endkontrolle.
Erfahren Sie mehr über Wärmemanagementtechniken für die Hochleistungs-Kunststoffbearbeitung. ↩
Lernen Sie fortschrittliche Techniken für die Präzisionsbearbeitung von Hochleistungsthermoplasten kennen. ↩
Klicken Sie hier, um spezielle Techniken für die präzise Bearbeitung von Hochleistungsthermoplasten zu entdecken. ↩
Entdecken Sie, wie mechanische Eigenschaften die Materialauswahl für Hochleistungskomponenten beeinflussen. ↩
Erlernen Sie spezielle Bearbeitungstechniken zur Vermeidung von wärmebedingten Verformungen bei Hochleistungsthermoplasten. ↩