Vous est-il déjà arrivé d'acheter des pièces métalliques galvanisées et de constater que des taches de rouille apparaissaient quelques mois plus tard ? Il est frustrant d'investir dans ce que l'on pensait être un matériau inoxydable, mais d'être confronté à des problèmes de corrosion. Cela peut entraîner des remplacements coûteux et des retards potentiels du projet.
Bien que le métal galvanisé soit très résistant à la rouille, il n'est pas complètement à l'épreuve de la rouille. La couche de zinc constitue une barrière protectrice qui ralentit considérablement la corrosion, mais des facteurs tels que les rayures, l'exposition à l'environnement et le contact avec des produits chimiques peuvent finir par entraîner la formation de rouille.
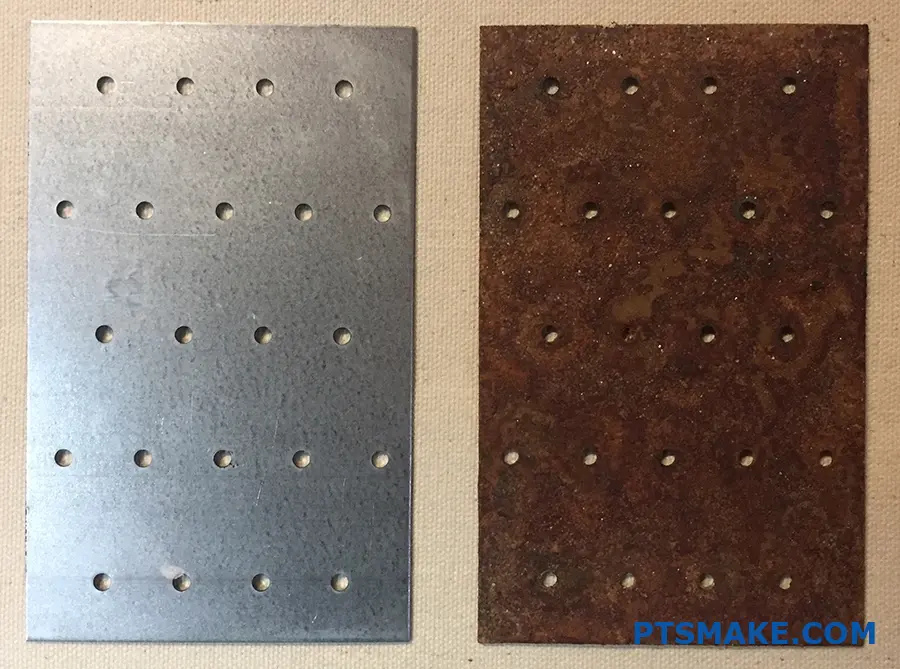
En tant que professionnel de la fabrication, j'ai vu comment la galvanisation affecte les pièces métalliques dans diverses applications. L'efficacité du revêtement galvanisé dépend de plusieurs facteurs clés. Laissez-moi vous expliquer comment fonctionne la galvanisation, quelles sont ses limites et ce que vous pouvez attendre en termes de résistance à la rouille pour vos projets.
Que signifie le fait qu'un objet soit galvanisé ?
Vous êtes-vous déjà demandé pourquoi certains produits métalliques semblent immunisés contre la rouille alors que d'autres se détériorent rapidement ? La différence réside souvent dans un processus de protection crucial que beaucoup négligent, laissant leurs composants métalliques vulnérables à la corrosion et à une défaillance prématurée.
La galvanisation est un procédé de revêtement protecteur dans lequel le métal, généralement de l'acier ou du fer, est recouvert d'une couche de zinc pour prévenir la rouille et la corrosion. Ce traitement crée une barrière sacrificielle qui protège le métal de base, prolongeant ainsi considérablement sa durée de vie et sa durabilité.
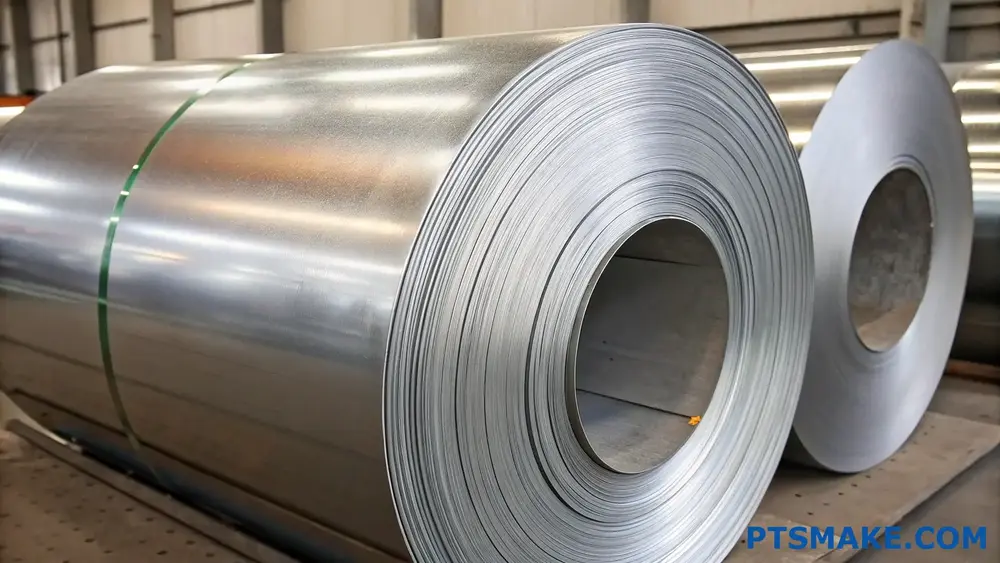
Comprendre le processus de galvanisation
Le processus de galvanisation comprend plusieurs étapes critiques qui transforment un métal ordinaire en un matériau résistant à la corrosion. Chez PTSMAKE, nous travaillons régulièrement avec des matériaux galvanisés pour nos projets de fabrication de précision. La méthode la plus courante est la galvanisation à chaud, où le métal propre est immergé dans du zinc en fusion à une température d'environ 450°C (842°F).
La science derrière la galvanisation
Au cours du processus, une série de réactions métallurgiques1 se produisent entre l'acier et le zinc, formant plusieurs couches distinctes :
- Couche gamma : La couche la plus interne
- Couche Delta : La couche intermédiaire
- Couche zêta : La couche cristalline externe
- Couche Eta : La couche superficielle de zinc pur
Avantages de la galvanisation
Durabilité et longévité
Les produits galvanisés offrent une durabilité exceptionnelle, qui dure souvent plus de 50 ans sans entretien. Cette longévité les rend particulièrement précieux dans :
Application | Durée de vie prévue | Entretien nécessaire |
---|---|---|
Zones rurales | 70 ans et plus | Minime |
Zones urbaines | 50 ans et plus | Inspection régulière |
Régions côtières | 25 ans et plus | Inspection annuelle |
Rapport coût-efficacité
Si les coûts initiaux peuvent être plus élevés que ceux des métaux non traités, les matériaux galvanisés permettent de réaliser d'importantes économies à long terme :
- Réduction des coûts de maintenance
- Durée de vie prolongée
- Réduction de la fréquence de remplacement
- Exigences minimales en matière d'inspection
Applications dans tous les secteurs d'activité
Construction et infrastructure
Dans la construction, l'acier galvanisé est essentiel pour.. :
- Poutres de soutien structurel
- Matériaux de couverture
- Composants du pont
- Garde-corps
- Systèmes de canalisations souterraines
Fabrication et production
Chez PTSMAKE, nous avons mis en œuvre des composants galvanisés dans divers projets de fabrication de précision, en particulier lorsque la résistance à la corrosion est cruciale. Les applications les plus courantes sont les suivantes :
- Pièces pour machines industrielles
- Composants automobiles
- Équipements marins
- Machines agricoles
- Armoires électriques pour l'extérieur
Impact environnemental et durabilité
La galvanisation contribue à la durabilité environnementale de plusieurs façons :
- Le zinc est 100% recyclable sans perte de qualité
- La réduction du besoin de pièces de rechange entraîne une diminution des déchets
- Des besoins d'entretien moindres réduisent l'utilisation de produits chimiques
- L'allongement de la durée de vie des produits réduit la consommation de ressources
Contrôle de la qualité de la galvanisation
Méthodes d'essai
Pour garantir une protection optimale, les revêtements galvanisés sont soumis à des tests rigoureux :
Type de test | Objectif | Fréquence |
---|---|---|
Essai d'épaisseur | Mesure de la profondeur du revêtement | Chaque lot |
Test d'adhérence | Vérifier l'adhérence du revêtement | Base de l'échantillon |
Inspection visuelle | Vérifier la qualité de la surface | Inspection 100% |
Essais au brouillard salin | Résistance à la corrosion | Validation périodique |
Problèmes courants et solutions
Les défis de la galvanisation sont les suivants :
- Déformation pendant le processus d'immersion à chaud
- Epaisseur inégale du revêtement
- Imperfections de surface
- Fragilisation par l'hydrogène
Meilleures pratiques pour l'entretien des produits galvanisés
Pour maximiser la durée de vie des matériaux galvanisés :
Inspection régulière
- Vérifier que la surface n'est pas endommagée
- Contrôler les signes d'usure
- Documenter tout changement
Stockage adéquat
- Tenir à l'écart des substances acides
- Assurer une ventilation adéquate
- Éviter l'exposition prolongée à l'humidité
Lignes directrices pour la manipulation
- Utiliser les outils appropriés
- Éviter de rayer la surface
- Nettoyer régulièrement avec des solutions douces
Tendances futures de la technologie de galvanisation
Le secteur continue d'évoluer avec :
Technologies avancées de revêtement
- Revêtements de zinc nano-améliorés
- Des couches de protection intelligentes
- Procédés respectueux de l'environnement
Contrôle de qualité automatisé
- Systèmes d'inspection alimentés par l'IA
- Contrôle en temps réel
- Maintenance prédictive
Galvanisé signifie-t-il imperméable ?
Avez-vous déjà investi dans des matériaux galvanisés pour votre projet, en pensant qu'ils étaient parfaitement étanches, pour découvrir par la suite la formation de rouille ? Cette idée reçue a conduit de nombreuses personnes à faire face à des problèmes de corrosion inattendus et à des remplacements coûteux.
Non, galvanisé n'est pas synonyme d'imperméable. Bien que la galvanisation offre une résistance significative à l'eau grâce à sa couche de zinc protectrice, elle n'est pas complètement étanche. La couche de zinc constitue une barrière sacrificielle qui ralentit la corrosion, mais qui peut finir par s'user dans certaines conditions.
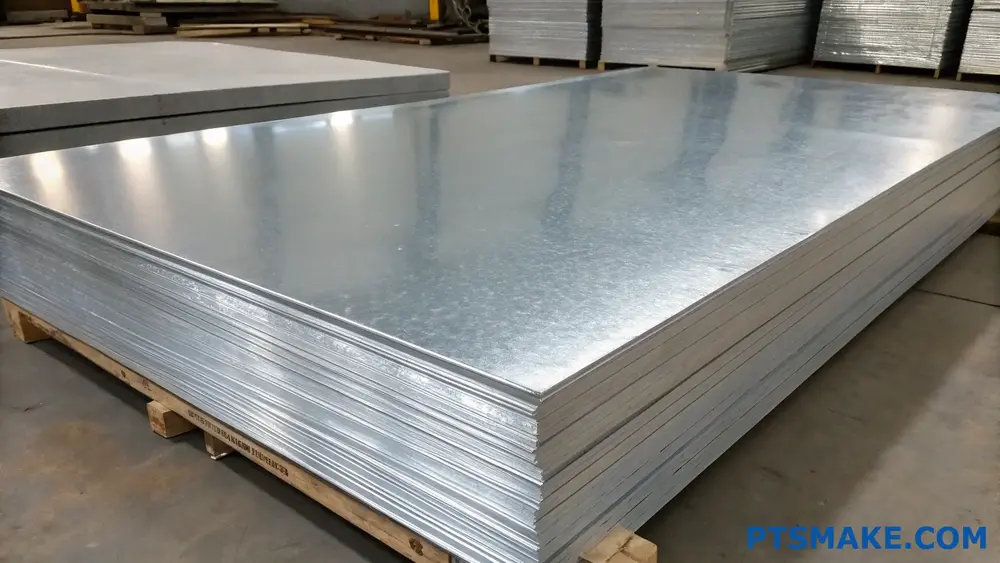
Comprendre le processus de galvanisation
Le processus de galvanisation consiste à recouvrir l'acier ou le fer d'une couche protectrice de zinc. Lors de la fabrication, le métal de base subit galvanisation à chaud2Ce processus forme plusieurs couches d'alliage de zinc et de fer qui offrent une protection supérieure contre l'eau et les autres éléments corrosifs. Ce processus forme plusieurs couches d'alliage zinc-fer qui offrent une protection supérieure contre l'eau et les autres éléments corrosifs.
Types de méthodes de galvanisation
Galvanisation à chaud
- Méthode la plus courante
- Fournit le revêtement le plus épais
- Offre la protection la plus longue
- Convient le mieux aux applications extérieures
Electrogalvanisation
- Revêtement plus fin
- Un contrôle plus précis
- Idéal pour les petites pièces
- Mieux pour l'intérieur
Facteurs affectant la protection galvanisée
Plusieurs facteurs influencent la résistance à l'eau des matériaux galvanisés :
Conditions environnementales
Condition | Niveau d'impact | Durée de la protection |
---|---|---|
Marine | Haut | 10-15 ans |
Industriel | Moyenne-élevée | 15-20 ans |
Rural | Faible | 20-25 ans |
Intérieur | Très faible | 25 ans et plus |
Épaisseur du revêtement
L'efficacité de la résistance à l'eau est directement liée à l'épaisseur du revêtement. Chez PTSMAKE, nous avons constaté que les spécifications relatives à l'épaisseur du revêtement sont cruciales pour garantir des performances optimales dans différentes applications.
Idées reçues sur les matériaux galvanisés
Mythe 1 : Imperméabilisation complète
Nombreux sont ceux qui pensent que les matériaux galvanisés sont entièrement imperméables. En réalité, ils sont résistants à l'eau. Le revêtement de zinc se sacrifie lentement pour protéger le métal de base, mais cette protection n'est pas permanente.
Mythe 2 : Sans entretien
Si les matériaux galvanisés nécessitent moins d'entretien que l'acier brut, ils doivent néanmoins faire l'objet d'une inspection et d'un entretien périodiques, en particulier dans les environnements difficiles.
Meilleures pratiques pour la protection de l'eau
Pour maximiser la résistance à l'eau des matériaux galvanisés :
Considérations relatives à la conception
- Éviter les pièges à eau
- Assurer un drainage adéquat
- Maintenir une ventilation adéquate
- Tenir compte de l'exposition à l'environnement
Lignes directrices pour l'installation
- Utiliser des matériaux compatibles
- Éviter le contact avec des métaux dissemblables
- Protection contre les dommages mécaniques
- Mettre en place des systèmes de drainage adéquats
Applications et solutions industrielles
Les différents secteurs d'activité requièrent des niveaux de protection de l'eau variables :
Industrie de la construction
- Composants en acier de construction
- Matériaux de couverture
- Quincaillerie et fixations
- Renforcement des fondations
Secteur manufacturier
Chez PTSMAKE, nous sommes spécialisés dans la fabrication de précision de composants galvanisés. Notre expérience montre qu'une sélection et un traitement appropriés des matériaux sont cruciaux pour obtenir une résistance à l'eau optimale.
Applications marines
Les environnements marins exigent le plus haut niveau de protection :
- Augmentation de l'épaisseur du revêtement
- Mesures de protection supplémentaires
- Calendrier d'entretien régulier
- Systèmes de revêtement spécialisés
Essais et assurance qualité
Pour garantir une étanchéité fiable :
Type de test | Objectif | Fréquence |
---|---|---|
Vaporisateur de sel | Résistance à la corrosion | Chaque lot |
Épaisseur du revêtement | Contrôle de la qualité | Inspection 100% |
Test d'adhérence | Force d'adhérence | Base de l'échantillon |
Tests d'impact | Contrôle de durabilité | Base de l'échantillon |
Entretien et protection à long terme
Pour maintenir la résistance à l'eau :
Inspections régulières
- Vérifier que le revêtement n'est pas endommagé
- Contrôler la formation de rouille
- Évaluer l'exposition environnementale
- Documenter les changements au fil du temps
Mesures préventives
- Nettoyer régulièrement les surfaces
- Réparer rapidement les zones endommagées
- Appliquer des couches de protection supplémentaires
- Contrôler les conditions environnementales
Développements futurs
Le secteur continue d'évoluer avec :
- Technologies de revêtement avancées
- Méthodes d'application améliorées
- Procédures de test améliorées
- Solutions durables
L'équipe de PTSMAKE se tient au courant de ces développements afin de fournir des solutions de pointe aux besoins de nos clients en matière de protection de l'eau.
Quels sont les inconvénients de l'acier galvanisé ?
Avez-vous déjà installé des éléments en acier galvanisé pour découvrir au bout de quelques mois la formation d'une rouille blanche inesthétique ? Ou avez-vous vu votre projet soigneusement planifié se détériorer plus rapidement que prévu, en vous demandant si vous aviez fait le bon choix de matériau ?
L'acier galvanisé présente plusieurs inconvénients, notamment un coût initial plus élevé, des irrégularités dans la finition de la surface et une fragilisation potentielle par l'hydrogène. Le revêtement peut également être endommagé lors de la manipulation, et le soudage de l'acier galvanisé dégage des fumées toxiques qui nécessitent des mesures de sécurité particulières.
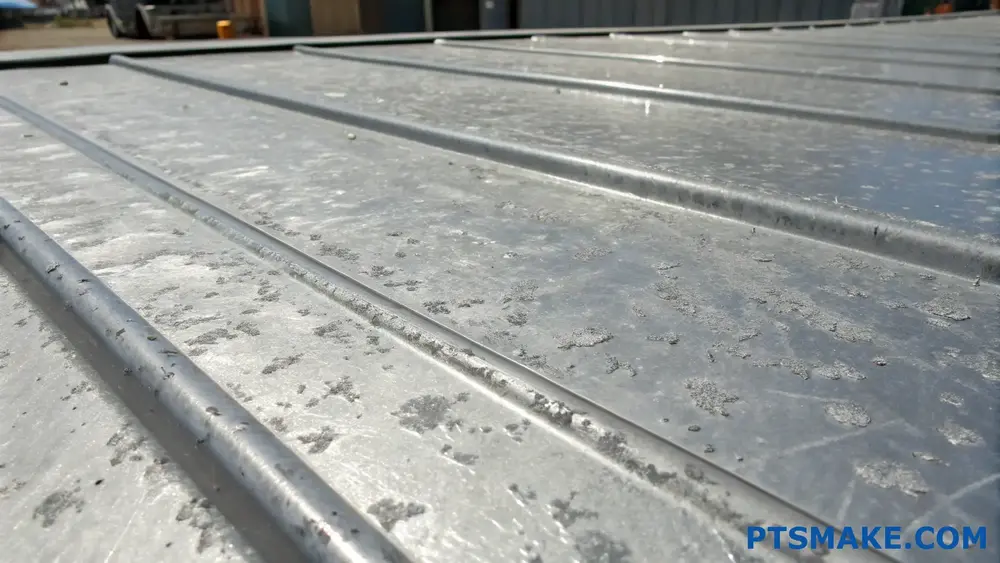
Comprendre l'impact des coûts
Le coût de l'acier galvanisé surprend souvent de nombreux chefs de projet. Si les avantages à long terme peuvent justifier l'investissement, les coûts initiaux sont importants.
Investissement initial par rapport à l'acier traditionnel
Facteur de coût | Acier galvanisé | Acier traditionnel |
---|---|---|
Coût des matériaux | 1,5 à 2 fois plus élevé | Prix de base |
Frais de dossier | Supplémentaire 20-30% | Standard |
Coût de l'installation | Plus élevé en raison du poids | Plus bas |
Défis en matière de qualité de surface
Le processus de galvanisation peut entraîner plusieurs imperfections de surface. Au cours de la fabrication, la couche de zinc fondu peut ne pas se répartir uniformément, ce qui crée ce que l'on appelle des paillettes de galvanisation3. Cela affecte non seulement l'esthétique, mais aussi les performances du matériau.
Problèmes de surface courants :
- Ruptures de stock
- Epaisseur inégale du revêtement
- Marques de gouttes
- Variations de couleur
Préoccupations environnementales et sanitaires
Travailler avec de l'acier galvanisé présente plusieurs défis environnementaux et sanitaires qu'il convient d'examiner attentivement.
Génération de fumées toxiques
Lors du soudage ou du découpage de l'acier galvanisé, des fumées d'oxyde de zinc se dégagent. Chez PTSMAKE, nous avons mis en place des protocoles de sécurité stricts pour la manipulation de ces matériaux :
- Systèmes de ventilation obligatoires
- Équipements de protection individuelle
- Surveillance régulière de la qualité de l'air
Défis liés à l'élimination des déchets
La couche de zinc complique le processus de recyclage. Bien qu'elle soit recyclable, elle nécessite des méthodes de manipulation et de traitement spécialisées.
Limites mécaniques
Le processus de galvanisation peut affecter les propriétés mécaniques de l'acier de plusieurs manières :
Réduction de la force
La galvanisation à chaud peut potentiellement réduire la résistance des aciers à haute résistance jusqu'à 15%. Cette réduction est particulièrement importante dans les applications porteuses.
Fragilisation par l'hydrogène
Le processus de galvanisation peut introduire de l'hydrogène dans la structure de l'acier, ce qui peut entraîner des dommages :
- Réduction de la ductilité
- Augmentation de la fragilité
- Formation potentielle de fissures
Restrictions d'application
Tous les environnements ne conviennent pas à l'utilisation de l'acier galvanisé :
Incompatibilité chimique
Environnement | Impact sur l'acier galvanisé |
---|---|
Solutions acides | Détérioration rapide du revêtement |
Conditions alcalines | Corrosion accélérée |
Eau salée | Réduction de la durée de vie de la protection |
Limites de température
Les revêtements galvanisés sont peu performants dans :
- Environnements à haute température (plus de 200°C)
- Conditions du cycle de congélation-décongélation
- Zones soumises à des fluctuations de température extrêmes
Considérations esthétiques
L'aspect de l'acier galvanisé peut ne pas répondre à toutes les exigences de conception :
Défis visuels
- Aspect gris terne
- Texture de surface irrégulière
- Options de couleurs limitées
- Imperfections visibles du revêtement
Exigences en matière de maintenance
Bien que l'acier galvanisé soit souvent présenté comme ne nécessitant pas d'entretien, certaines conditions requièrent une attention régulière :
Points d'inspection
- Contrôle de l'épaisseur du revêtement
- Évaluation des dommages
- Réparations de retouches
- Contrôles de l'intégrité des joints
Difficultés de traitement
La fabrication d'acier galvanisé présente des défis uniques :
Complications liées au soudage
- Techniques spéciales requises
- Réduction de la résistance des soudures
- Production de fumées toxiques
- Mesures de sécurité supplémentaires
Limites de la formation
Le revêtement peut :
- S'effrite lors du pliage
- Fissure sous contrainte
- Créer des surfaces irrégulières
- Affectent la précision dimensionnelle
Chez PTSMAKE, nous avons développé des techniques spécialisées pour surmonter ces défis, garantissant ainsi à nos clients des composants en acier galvanisé de haute qualité qui répondent à leurs spécifications tout en minimisant ces inconvénients inhérents.
Grâce à une sélection minutieuse des matériaux, à des procédures de manipulation adéquates et à des techniques de traitement avancées, bon nombre de ces inconvénients peuvent être gérés efficacement. Toutefois, il est essentiel de tenir compte de ces facteurs au cours de la phase initiale de planification du projet afin de garantir le choix du matériau le plus approprié pour votre application spécifique.
Comment prolonger la durée de vie de l'acier galvanisé dans l'eau salée ?
Avez-vous déjà investi dans des composants en acier galvanisé pour un projet maritime, pour ensuite les voir se détériorer plus rapidement que prévu ? La lutte constante entre l'eau salée et la protection du métal peut être frustrante, en particulier lorsque les délais et les budgets du projet sont en jeu.
En eau salée, l'acier galvanisé dure généralement de 10 à 15 ans s'il est correctement entretenu. Toutefois, la durée de vie varie considérablement en fonction de facteurs tels que la salinité de l'eau, la température, l'épaisseur du revêtement et les conditions environnementales. Des inspections et un entretien réguliers peuvent prolonger cette durée.
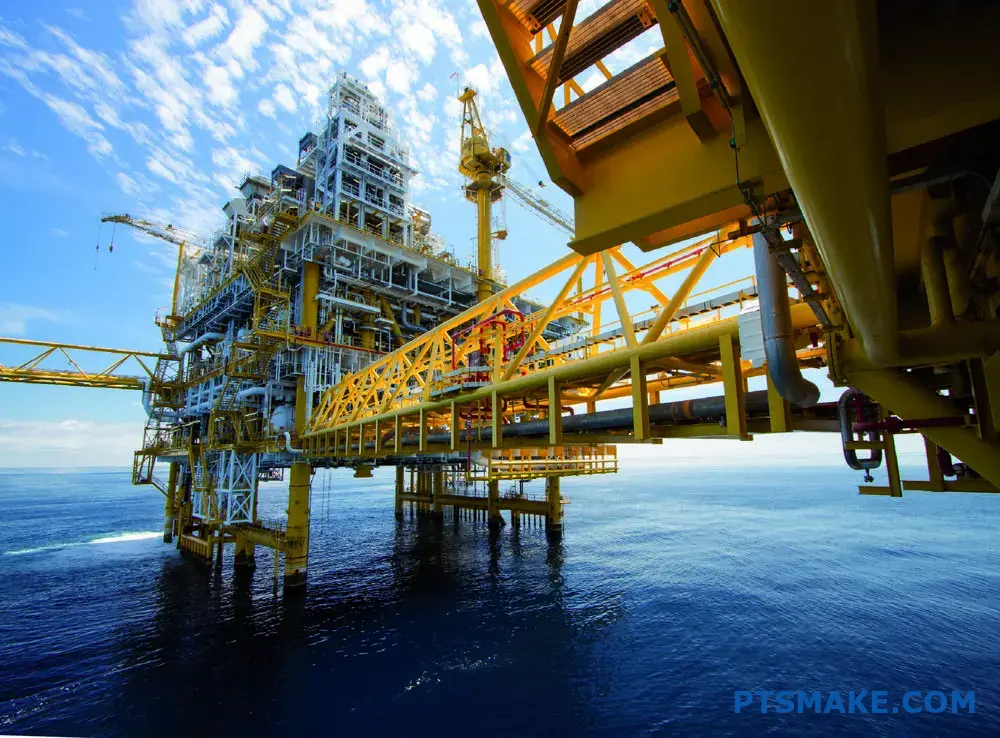
Comprendre les exigences en matière de maintenance
La clé pour maximiser la durée de vie de l'acier galvanisé dans les environnements d'eau salée réside dans la mise en œuvre de procédures d'entretien appropriées. Chez PTSMAKE, nous avons mis au point des protocoles d'entretien complets qui aident nos clients à protéger leurs investissements. Voici les points sur lesquels vous devez vous concentrer :
Calendrier des inspections régulières
Il est essentiel de maintenir un calendrier d'inspection cohérent. Je recommande :
- Contrôles visuels hebdomadaires pour détecter les signes de corrosion
- Inspections mensuelles détaillées des zones à haut risque
- Évaluations trimestrielles complètes de l'intégrité du revêtement
- Évaluations professionnelles annuelles
Protocoles de nettoyage
Un bon nettoyage permet d'éviter dissolution cathodique4 et prolonge la durée de vie des composants galvanisés :
- Enlever chaque semaine les dépôts de sel à l'eau douce
- Nettoyer les surfaces tous les mois avec des nettoyants au pH neutre
- Éviter les outils de nettoyage abrasifs qui pourraient endommager le revêtement.
- Documenter les procédures de nettoyage pour en assurer la cohérence
Facteurs d'impact sur l'environnement
Différentes conditions environnementales affectent la durabilité de l'acier galvanisé :
Facteur environnemental | Niveau d'impact | Stratégie d'atténuation |
---|---|---|
Température de l'eau | Haut | Surveiller les fluctuations de température |
Niveaux de salinité | Critique | Rinçage régulier à l'eau douce |
Exposition aux UV | Modéré | Revêtement supplémentaire résistant aux UV |
Débit d'eau | Important | Positionnement stratégique |
Méthodes de renforcement de la protection
Pour prolonger la durée de vie de l'acier galvanisé dans l'eau salée, envisagez les méthodes de protection suivantes :
Autres systèmes de revêtement
- Produits d'étanchéité à base d'époxy
- Couches de finition en polyuréthane
- Traitements antisalissures
- Anodes sacrificielles
Considérations relatives à la conception
La phase de conception est cruciale pour la longévité :
- Éviter les arêtes et les coins tranchants
- Inclure des systèmes de drainage appropriés
- Intégrer l'isolation des métaux dissemblables
- Conception facilitant l'accès à la maintenance
Suivi des performances
La mise en œuvre d'un système de surveillance solide permet de suivre la dégradation :
Indicateurs clés de performance
- Mesures de l'épaisseur du revêtement
- Niveaux de pH en surface
- Surveillance du taux de corrosion
- Suivi de la détérioration visuelle
Exigences en matière de documentation
Tenir des registres détaillés :
- Conditions initiales d'installation
- Résultats des inspections régulières
- Activités de maintenance
- Données sur l'exposition environnementale
Des solutions rentables
Chez PTSMAKE, nous aidons les clients à trouver un équilibre entre protection et budget :
Optimisation des investissements
- Choisir l'épaisseur de revêtement appropriée
- Choisir les intervalles d'entretien optimaux
- Planifier des remplacements stratégiques
- Tenir compte des coûts du cycle de vie
Allocation des ressources
Concentrer les ressources sur :
- Zones à haut risque
- Composants critiques
- Maintenance préventive
- Formation du personnel
Intégration de la technologie
Les technologies modernes améliorent les stratégies de protection :
Systèmes de surveillance
- Capteurs IoT pour des données en temps réel
- Programmes d'inspection automatisés
- Documentation numérique
- Algorithmes de maintenance prédictive
Outils d'analyse
- Calculateurs de taux de corrosion
- Évaluations de l'impact sur l'environnement
- Modèles de prévision du cycle de vie
- Logiciel d'analyse coût-bénéfice
Conformité aux normes industrielles
Le respect des normes industrielles garantit des performances optimales :
Exigences réglementaires
- Normes internationales ASTM
- Certifications ISO
- Réglementation maritime locale
- Respect de l'environnement
Contrôle de la qualité
- Protocoles d'essai des matériaux
- Vérification de l'installation
- Validation des procédures d'entretien
- Normes de suivi des performances
Cette approche globale de l'entretien de l'acier galvanisé en milieu salin permet de garantir une durée de vie maximale et des performances optimales. En suivant ces directives et en travaillant avec des fabricants expérimentés comme PTSMAKE, vous pouvez prolonger de manière significative la durée de vie de vos composants en acier galvanisé tout en préservant leur intégrité structurelle et leur fonctionnalité.
L'acier galvanisé peut-il être peint ou revêtu d'une peinture en poudre pour une protection supplémentaire ?
Avez-vous déjà remarqué que votre acier galvanisé commençait à perdre sa couche protectrice de zinc au fil du temps ? Il est frustrant de constater que cette barrière cruciale contre la corrosion commence à s'effriter, en particulier dans les environnements extérieurs ou difficiles où une protection maximale est essentielle.
Oui, l'acier galvanisé peut être peint et recouvert d'un revêtement en poudre pour une meilleure protection. Alors que la galvanisation offre une excellente résistance à la corrosion, l'ajout d'une couche de peinture ou de revêtement en poudre crée un système de protection double qui prolonge considérablement la durée de vie du matériau et en améliore l'aspect.
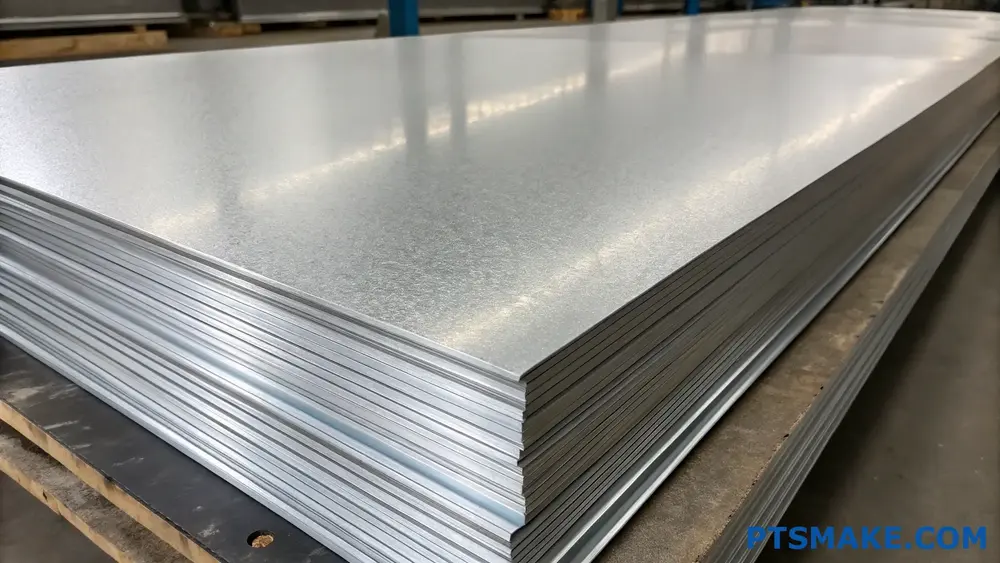
Comprendre les exigences en matière de préparation des surfaces
Le succès de toute application de revêtement sur de l'acier galvanisé dépend en grande partie d'une bonne préparation de la surface. Chez PTSMAKE, nous suivons une approche systématique pour garantir une adhérence optimale :
Méthodes de nettoyage des surfaces
- Nettoyage au solvant : Elimine les huiles et les contaminants organiques
- Nettoyage alcalin : Élimine les salissures et les graisses tenaces.
- Lavage à l'eau : élimine les contaminants solubles dans l'eau
- Gravure chimique5: Crée des micro-rugosités pour une meilleure adhérence du revêtement
Processus de création d'un profil
Le profil de la surface doit faire l'objet d'une attention particulière afin d'obtenir une bonne adhérence du revêtement. Voici l'approche que nous recommandons :
- Sablage abrasif léger
- Revêtement de conversion chimique
- Météorologie (lorsque le temps le permet)
- Rugosité mécanique
Options de revêtement de peinture pour l'acier galvanisé
Lorsqu'il s'agit de peindre de l'acier galvanisé, le choix du bon système de revêtement est crucial. Sur la base de mon expérience dans diverses applications industrielles, voici les options les plus efficaces :
Systèmes de peinture recommandés
Type de peinture | Avantages | Meilleures applications |
---|---|---|
Epoxy | Excellente adhérence, résistance chimique | Équipements industriels |
Polyuréthane | Résistance aux UV, conservation des couleurs | Structures extérieures |
Acrylique | Rentabilité et facilité d'application | Utilisation légère à l'intérieur |
Vinyle | Flexibilité, résistance aux chocs | Milieux marins |
Méthodes d'application
La technique d'application influence considérablement les performances du revêtement :
Application par pulvérisation
- HVLP (haut volume basse pression)
- Pulvérisation sans air
- Pulvérisation d'air conventionnelle
Application au pinceau et au rouleau
- Convient aux petites surfaces
- Travaux de retouche
- Revêtement d'entretien
Processus de revêtement par poudre pour l'acier galvanisé
Le revêtement en poudre offre des avantages indéniables par rapport aux peintures liquides traditionnelles. Chez PTSMAKE, nous avons affiné notre processus de revêtement en poudre pour garantir une durabilité maximale :
Étapes du prétraitement
- Dégraissage
- Phosphatation
- Conversion du chromate
- Rincer et sécher
Techniques d'application des poudres
Le processus d'application de la poudre nécessite un contrôle précis :
Paramètres | Fourchette recommandée | Facteurs critiques |
---|---|---|
Température | 350-400°F | Epaisseur du matériau |
Temps de séchage | 10-15 minutes | Epaisseur du revêtement |
Épaisseur du film | 2-3 mils | Couverture des bords |
Tension | 40-90 kV | Géométrie des pièces |
Considérations sur les performances
Lorsque vous choisissez entre la peinture et le revêtement en poudre pour l'acier galvanisé, tenez compte des facteurs suivants :
Facteurs environnementaux
- Exposition aux UV
- Fluctuations de température
- Exposition aux produits chimiques
- Niveaux d'humidité
Analyse des coûts
Facteur | Revêtement de peinture | Revêtement par poudre |
---|---|---|
Coût initial | Plus bas | Plus élevé |
Vitesse d'application | Plus rapide | Modéré |
Durabilité | Bon | Excellent |
Maintenance | Régulière | Minime |
Mesures de contrôle de la qualité
Pour garantir la réussite de l'enrobage, il convient de mettre en œuvre les mesures de contrôle de la qualité suivantes :
- Mesure du profil de la surface
- Surveillance de l'état de l'environnement
- Vérification de l'épaisseur du revêtement
- Test d'adhérence
- Inspection visuelle
Exigences en matière de maintenance
Pour une performance optimale de l'acier galvanisé revêtu :
Calendrier des inspections régulières
- Inspections visuelles mensuelles
- Examens trimestriels détaillés
- Test de performance annuel
Procédures d'entretien
- Nettoyer régulièrement les surfaces
- Réparer rapidement les zones endommagées
- Documenter toutes les activités de maintenance
- Contrôler la performance du revêtement
En suivant ces directives détaillées, vous pouvez appliquer avec succès des revêtements de protection supplémentaires sur l'acier galvanisé, en prolongeant de manière significative sa durée de vie et en améliorant son apparence. Chez PTSMAKE, nous avons mis en œuvre ces pratiques dans de nombreux projets, obtenant systématiquement d'excellents résultats en termes d'esthétique et de protection à long terme.
Quelles sont les alternatives à l'acier galvanisé pour la résistance à la corrosion ?
Avez-vous déjà été confronté à la défaillance prématurée de pièces en acier galvanisé en raison de la corrosion ? La frustration de voir la rouille apparaître malgré la galvanisation, combinée à l'augmentation du coût des matériaux, pousse de nombreux ingénieurs à chercher de meilleures alternatives.
Il existe plusieurs alternatives efficaces à l'acier galvanisé, notamment l'acier inoxydable, les alliages d'aluminium, les métaux revêtus par poudrage, les alliages zinc-nickel et les plastiques techniques. Chaque option offre des avantages uniques en matière de résistance à la corrosion, tout en offrant potentiellement un meilleur rapport coût-efficacité et de meilleures performances dans des applications spécifiques.
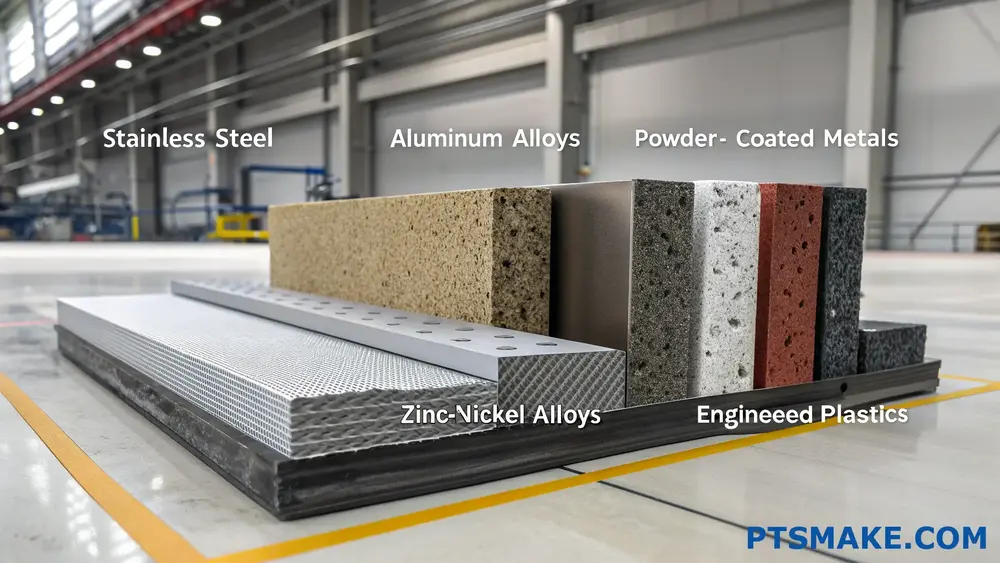
Comprendre les matériaux modernes résistants à la corrosion
Solutions en acier inoxydable
L'acier inoxydable est une alternative de choix à l'acier galvanisé. Chez PTSMAKE, nous recommandons fréquemment les qualités 304 et 316 pour leur résistance exceptionnelle à la corrosion. La clé réside dans leur teneur en chrome, qui forme une couche auto-cicatrisante. couche de passivation6 en surface.
Voici une analyse comparative des qualités d'acier inoxydable les plus courantes :
Grade | Teneur en chrome | Résistance à la corrosion | Meilleures applications |
---|---|---|---|
304 | 18-20% | Bon | Équipement intérieur, transformation des aliments |
316 | 16-18% | Excellent | Milieux marins, traitement chimique |
430 | 16-18% | Modéré | Pièces automobiles, articles de décoration |
Les alliages d'aluminium comme alternatives légères
Les alliages d'aluminium offrent des avantages indéniables par rapport à l'acier galvanisé, en particulier dans les applications sensibles au poids. Les alliages des séries 5000 et 6000 offrent une excellente résistance à la corrosion grâce à la formation naturelle d'une couche d'oxyde.
Les principaux avantages sont les suivants :
- Résistance naturelle à la corrosion sans revêtement supplémentaire
- Poids nettement plus léger (environ 1/3 de l'acier)
- Excellente conductivité thermique
- Rentable pour la production à grande échelle
Traitements de surface avancés
Technologie du revêtement par poudre
Les technologies modernes de revêtement par poudre ont révolutionné la protection des métaux. Le processus comprend :
- Préparation de la surface par sablage
- Application de poudre électrostatique
- Durcissement à la chaleur pour créer une finition durable
Revêtements d'alliages zinc-nickel
Ces revêtements avancés offrent une protection supérieure à la galvanisation traditionnelle :
- 5 à 8 fois plus résistant à la corrosion
- Meilleures propriétés d'adhésion
- Epaisseur uniforme du revêtement
- Amélioration de l'aspect esthétique
La révolution des plastiques techniques
Polymères haute performance
Les progrès réalisés dans le domaine des plastiques techniques ont permis de créer des alternatives viables à l'acier galvanisé. Des matériaux tels que :
- PEEK (polyéther éther cétone)
- PPS (sulfure de polyphénylène)
- PVDF (Fluorure de polyvinylidène)
Ces matériaux offrent une résistance inhérente à la corrosion sans nécessiter de traitements supplémentaires.
Analyse coûts-avantages
Lorsque vous comparez les alternatives à l'acier galvanisé, tenez compte des facteurs suivants :
Matériau | Coût initial | Coût de la maintenance | Durée de vie | Impact sur l'environnement |
---|---|---|---|---|
Acier inoxydable | Haut | Faible | 25 ans et plus | Moyen |
Aluminium | Moyen | Faible | 20 ans et plus | Faible |
Plastiques techniques | Moyenne-élevée | Minime | 15-20 ans | Variable |
Acier revêtu de poudre | Moyen | Moyen | 15-20 ans | Faible |
Solutions spécifiques à l'industrie
Applications marines
Dans les environnements marins, où la résistance à la corrosion est cruciale, j'ai constaté que les aciers inoxydables duplex et certains alliages d'aluminium donnent d'excellents résultats. Chez PTSMAKE, nous usinons régulièrement ces matériaux pour les fabricants d'équipements marins.
Industrie chimique
Pour les applications de traitement chimique, le choix se situe souvent entre les deux :
- Acier inoxydable super duplex
- Alliages de titane
- Polymères à haute performance
Chaque matériau offre des avantages spécifiques en fonction de l'environnement chimique.
Applications architecturales
Dans les projets architecturaux, l'esthétique et la durabilité doivent s'équilibrer. Les options les plus courantes sont les suivantes :
- Aluminium anodisé
- Acier peint par poudrage
- Acier inoxydable de qualité architecturale
Tendances futures et innovations
Technologies émergentes
De nouvelles technologies de traitement de surface apparaissent constamment :
- Revêtements nanocéramiques
- Couches protectrices à base de graphène
- Matériaux auto-cicatrisants intelligents
Considérations sur le développement durable
Les alternatives modernes à l'acier galvanisé offrent souvent de meilleurs profils environnementaux :
- Réduction des émissions toxiques lors de la fabrication
- Meilleure recyclabilité
- Réduction de la consommation d'énergie dans la production
- Durée de vie prolongée réduisant la fréquence de remplacement
En sélectionnant soigneusement les matériaux et en comprenant les exigences spécifiques de l'application, nous pouvons souvent trouver des alternatives supérieures à l'acier galvanisé. La clé consiste à équilibrer les exigences de performance, les contraintes de coût et les considérations environnementales afin d'obtenir des résultats optimaux.
Quel est l'entretien nécessaire pour les composants métalliques galvanisés ?
Avez-vous déjà remarqué la formation de rouille blanche sur vos pièces galvanisées ou observé avec frustration la perte progressive de leur revêtement protecteur ? Ces problèmes peuvent avoir un impact significatif sur les performances et la longévité des pièces, ce qui peut entraîner des remplacements coûteux et des retards de production.
Les composants métalliques galvanisés nécessitent un entretien minimal mais spécifique, notamment un nettoyage régulier avec de l'eau et du savon doux, des inspections annuelles pour vérifier que le revêtement n'est pas endommagé, des retouches sur les petites zones endommagées et un stockage approprié dans des conditions sèches pour prévenir la corrosion prématurée et prolonger la durée de vie du produit.
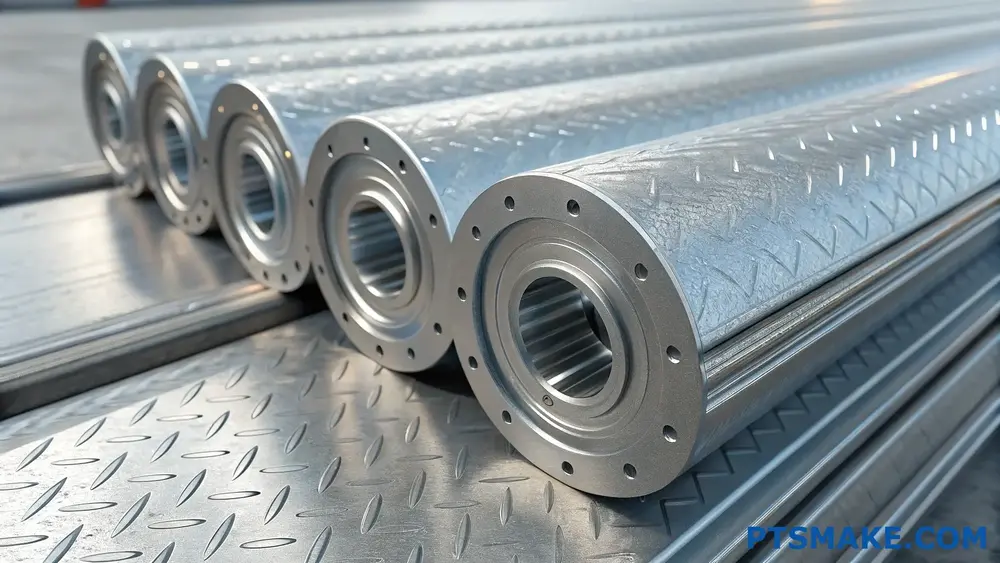
Comprendre le comportement du revêtement galvanisé
L'efficacité des revêtements galvanisés dépend largement de la façon dont ils interagissent avec leur environnement. Lorsqu'ils sont exposés à l'atmosphère, les revêtements galvanisés forment une couche protectrice. patine7 qui protège le métal de base. Chez PTSMAKE, nous avons observé qu'un entretien adéquat prolonge considérablement cette protection.
Facteurs affectant la performance du revêtement
Plusieurs facteurs environnementaux peuvent avoir un impact sur la durabilité des revêtements galvanisés :
- Conditions atmosphériques (humidité, température)
- Exposition chimique
- Dommages physiques
- Rayonnement UV
- Polluants industriels
Procédures d'entretien essentielles
Protocole de nettoyage régulier
Un nettoyage régulier est indispensable à l'entretien des pièces galvanisées. Je recommande de suivre les étapes suivantes :
- Utiliser du savon doux et de l'eau tiède
- Éviter les outils de nettoyage abrasifs
- Rincer abondamment à l'eau claire
- Laisser les composants sécher complètement
- Consigner les dates de nettoyage dans les registres d'entretien
Lignes directrices en matière d'inspection
Les inspections périodiques permettent d'identifier les problèmes potentiels avant qu'ils ne deviennent graves :
Zone d'inspection | Fréquence | Principaux points de contrôle |
---|---|---|
Revêtement de surface | Trimestrielle | Rayures, éclats |
Zones communes | Mensuel | Formation de rouille |
Points à forte tension | Bimensuel | Usure du revêtement |
Profilés soudés | Trimestrielle | Intégrité du revêtement |
Stratégies de maintenance préventive
Recommandations en matière de stockage
Un stockage adéquat joue un rôle essentiel dans l'entretien des composants galvanisés :
- Stocker dans des endroits secs et bien ventilés
- Éviter le contact direct avec le sol
- Maintenir une circulation d'air adéquate
- Protection contre l'exposition aux produits chimiques
- Utiliser des méthodes d'empilage appropriées
Procédures de retouche
En cas de dommages mineurs, il est essentiel d'intervenir rapidement :
- Nettoyer soigneusement la zone endommagée
- Appliquer une peinture riche en zinc ou un composé de galvanisation à froid
- Prévoir un temps de durcissement adéquat
- Documenter les réparations pour référence ultérieure
Considérations environnementales
Gestion de l'impact sur le climat
Des environnements différents requièrent des approches de maintenance différentes :
Zones côtières
- Des inspections plus fréquentes
- Revêtements de protection supplémentaires
- Calendrier de nettoyage amélioré
Zones industrielles
- Contrôle de la résistance chimique
- Évaluation de l'impact de la pollution
- Produits de nettoyage spécialisés
Sites ruraux
- Entretien standard suffisant
- Dépoussiérage régulier
- Protection de base adéquate
Techniques de maintenance avancées
Lignes directrices pour l'évaluation professionnelle
Pour un entretien optimal, tenez compte de ces critères d'évaluation professionnelle :
Type d'évaluation | Objectif | Fréquence |
---|---|---|
Essai d'épaisseur | Mesure de l'usure du revêtement | Annuel |
Test d'adhérence | Force d'adhérence du revêtement | Deux fois par an |
Analyse chimique | Contrôle de la contamination | Selon les besoins |
Inspection visuelle | État de surface | Mensuel |
Méthodes de restauration
Lorsqu'une dégradation importante se produit :
- Préparation de la surface
- Renouvellement du revêtement
- Renforcement de la protection
- Tests de performance
Maintenance spécifique à l'industrie
Les différents secteurs d'activité nécessitent des approches de maintenance spécialisées :
Industrie automobile
- Nettoyage régulier des bas de caisse
- Procédures de réparation des collisions
- Protection saisonnière
Secteur de la construction
- Gestion de l'exposition aux intempéries
- Entretien des éléments porteurs
- Protection des articulations
Équipement de fabrication
- Contrôle de l'environnement opérationnel
- Surveillance des points d'usure
- Application d'un revêtement préventif
Planification rentable de la maintenance
La mise en œuvre d'un plan de maintenance structuré permet d'optimiser les coûts :
Calendrier des inspections régulières
- Réduit les défaillances inattendues
- Prévient les réparations importantes
- Prolonge la durée de vie
Système de documentation
- Suivi de l'historique de la maintenance
- Identifie les schémas de problèmes
- Orienter les améliorations futures
Allocation des ressources
- Formation du personnel
- Besoins en équipement
- Exigences matérielles
Chez PTSMAKE, nous avons mis en œuvre ces protocoles de maintenance dans nos processus de production, afin de garantir que nos composants galvanisés conservent leurs propriétés protectrices tout au long de leur durée de vie. Notre expérience montre que la maintenance proactive réduit considérablement les coûts à long terme et améliore la fiabilité des composants.
En quoi la galvanisation à chaud diffère-t-elle des procédés d'électro-galvanisation ?
Avez-vous déjà eu du mal à choisir entre la galvanisation à chaud et l'électro-galvanisation pour vos pièces métalliques ? La confusion qui règne autour de ces deux procédés peut conduire à des erreurs coûteuses, susceptibles de compromettre la durabilité et les performances de votre produit.
La galvanisation à chaud et l'électro-galvanisation sont deux procédés de revêtement distincts. La galvanisation à chaud consiste à immerger le métal dans du zinc en fusion à 850°F, tandis que l'électro-galvanisation utilise un courant électrique pour déposer du zinc sur des surfaces métalliques à température ambiante, ce qui se traduit par des épaisseurs de revêtement et des applications différentes.
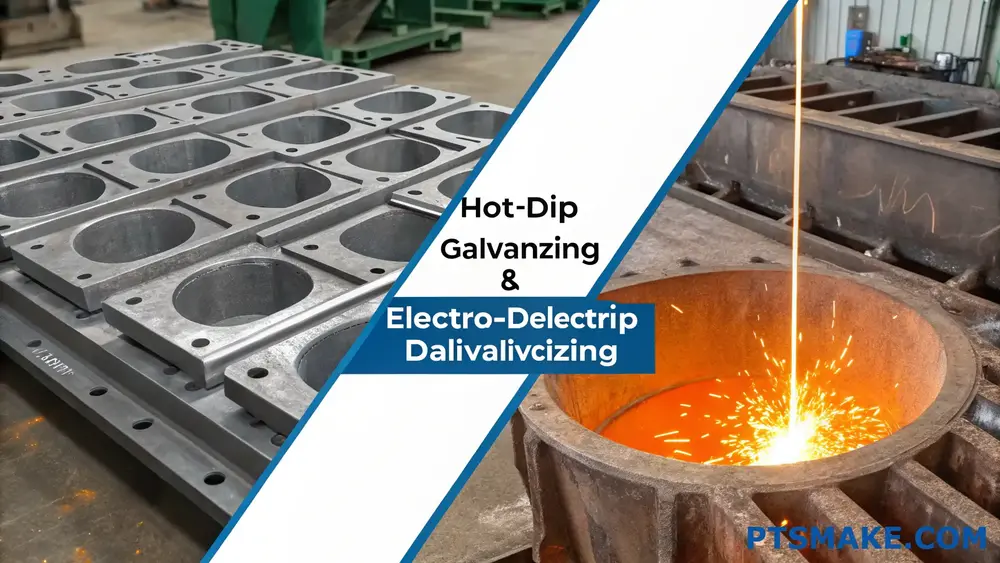
Comprendre les différences fondamentales
Température du processus et méthodes
La galvanisation à chaud consiste à chauffer le zinc à environ 450°C (850°F) dans de grandes cuves. Les pièces métalliques sont immergées dans ce bain de zinc en fusion après un nettoyage approfondi et une préparation de la surface. En revanche, l'électro-galvanisation s'effectue à température ambiante, les ions de zinc étant déposés électriquement sur la surface du métal dans un environnement contrôlé.
Épaisseur et répartition du revêtement
L'épaisseur du revêtement varie considérablement entre ces deux méthodes. La galvanisation à chaud produit généralement des revêtements plus épais, allant de 3,0 à 5,0 mils (75-125 micromètres). Chez PTSMAKE, nous avons observé que les revêtements électro-galvanisés sont généralement plus fins, de l'ordre de 0,2 à 1,0 mil (5-25 micromètres).
Analyse comparative des deux processus
Caractéristique | Galvanisation à chaud | Electro-galvanisation |
---|---|---|
Température du processus | 850°F (450°C) | Température ambiante |
Épaisseur du revêtement | 3,0-5,0 mils | 0,2-1,0 mils |
Finition de la surface | Légèrement plus rugueux | Lisse et uniforme |
Coût par unité | Coût initial plus élevé | Coût initial moins élevé |
Vitesse de production | Plus lent | Plus rapide |
Applications et utilisations industrielles
Galvanisation à chaud Meilleures utilisations
Ce procédé excelle dans les applications en extérieur et dans les environnements difficiles. Le revêtement épais offre une protection supérieure contre la corrosion, ce qui le rend idéal pour :
- Composants en acier de construction
- Glissières de sécurité
- Poteaux d'éclairage
- Matériel agricole
- Milieux marins
Avantages de l'électro-galvanisation
Le liaison métallurgique8 créé lors de l'électro-galvanisation le rend parfait pour :
- Pièces de carrosserie automobile
- Fixations
- Produits en tôle
- Boîtiers électroniques
- Applications intérieures
Considérations sur les coûts et l'impact économique
Investissement initial
La galvanisation à chaud nécessite des installations plus grandes et plus d'énergie, ce qui se traduit par des coûts initiaux plus élevés. L'équipement nécessaire comprend
- Grandes bouilloires en zinc
- Des systèmes de chauffage performants
- Ventilation extensive
- Équipement de manutention
Les installations d'électrozingage sont nécessaires :
- Cuves de placage
- Redresseurs électriques
- Systèmes de filtration
- Contrôles chimiques
Analyse de la valeur à long terme
Malgré des coûts initiaux plus élevés, la galvanisation à chaud offre souvent une meilleure valeur à long terme en raison de ses avantages :
- Durée de vie prolongée
- Besoins d'entretien moindres
- Meilleure durabilité dans des conditions difficiles
- Réduction de la fréquence de remplacement
Considérations environnementales et de sécurité
Impact sur l'environnement
Les deux processus sont liés à des considérations environnementales :
Galvanisation à chaud :
- Consommation d'énergie plus élevée
- Production de cendres de zinc
- Matériaux recyclables
- Réduction des déchets chimiques
Electro-galvanisation :
- Réduction de la consommation d'énergie
- Gestion des déchets chimiques
- Exigences en matière de traitement de l'eau
- Besoins en matière de surveillance continue
Protocoles de sécurité
Chez PTSMAKE, nous appliquons des mesures de sécurité strictes pour les deux processus :
Exigences en matière de sécurité pour l'immersion à chaud :
- Équipement de protection contre la chaleur
- Systèmes de ventilation
- Protection contre les éclaboussures
- Procédures d'urgence
Besoins en matière de sécurité pour l'électro-galvanisation :
- Protocoles de manipulation des produits chimiques
- Mesures de sécurité électrique
- Ventilation adéquate
- Équipements de protection individuelle
Contrôle de la qualité et essais
Méthodes d'inspection
Le contrôle de la qualité diffère d'un processus à l'autre :
Inspection par immersion à chaud :
- Mesure de l'épaisseur du revêtement
- Inspection visuelle
- Test d'adhérence
- Contrôle de l'uniformité de la surface
Inspection de l'électrozingage :
- Homogénéité de l'épaisseur
- Aspect de la surface
- Test d'adhérence
- Essais de résistance à la corrosion
Normes de performance
Les deux processus doivent répondre à des normes industrielles spécifiques :
- ASTM A123 pour la galvanisation à chaud
- ASTM B633 pour l'électro-galvanisation
- ISO 1461 pour les exigences en matière de revêtement par immersion à chaud
- ISO 2081 pour les revêtements électro-galvanisés
Entretien et longévité
Exigences en matière de maintenance
Les revêtements galvanisés à chaud nécessitent généralement un minimum d'entretien en raison de leurs propriétés :
- Couche protectrice plus épaisse
- Collage métallurgique
- Propriétés d'autocicatrisation
- Formation d'une patine naturelle
Les surfaces électro-galvanisées peuvent nécessiter :
- Inspection régulière
- Revêtement de retouche
- Peinture de protection
- Nettoyage périodique
Espérance de vie
La durée de vie varie considérablement :
- Trempage à chaud : 50+ ans dans de nombreux environnements
- Electro-galvanisé : 10-20 ans selon les conditions
Cliquez ici pour en savoir plus sur le processus de liaison chimique dans la protection des métaux. ↩
Cliquez pour en savoir plus sur le processus de galvanisation à chaud et les normes industrielles. ↩
Cliquez pour en savoir plus sur les caractéristiques de l'état de surface et sur la façon dont elles affectent les performances du produit. ↩
Cliquez pour en savoir plus sur ce processus électrochimique et sur la manière de le prévenir efficacement. ↩
Cliquez pour en savoir plus sur les techniques de gravure chimique qui maximisent l'adhérence du revêtement. ↩
Cliquez pour en savoir plus sur la science qui sous-tend la formation de la couche passive et ses avantages. ↩
Cliquez pour en savoir plus sur la façon dont la patine protège les surfaces galvanisées et prolonge la durée de vie des composants. ↩
Cliquez pour découvrir comment le collage métallurgique améliore la durabilité du revêtement et la protection contre la corrosion. ↩