Depuis plus de 15 ans que je travaille chez PTSMAKE, j'ai vu de nombreux clients s'interroger sur le surmoulage et le moulage par injection 2K. C'est comme choisir entre un sandwich et un hamburger - ils peuvent se ressembler, mais chacun répond à des besoins différents.
Le surmoulage consiste à injecter un matériau sur une pièce existante en deux processus distincts, tandis que le moulage par injection 2K (deux tirs) permet de créer des produits multi-matériaux en un seul cycle de machine. Ils diffèrent par les étapes du processus, le coût et les applications finales.
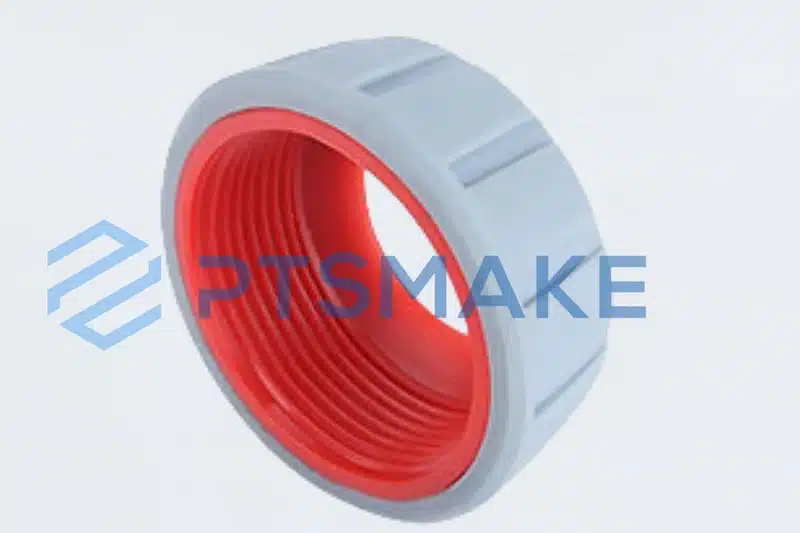
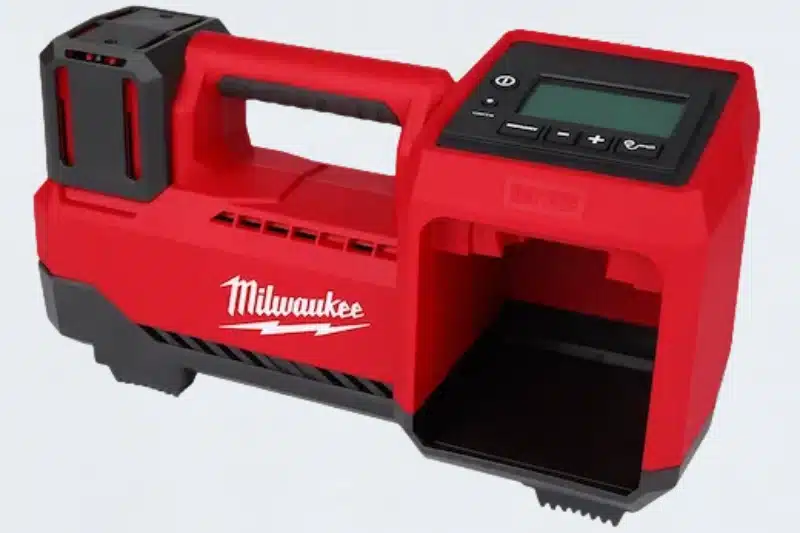
Permettez-moi de vous faire part de ce que j'ai appris en travaillant avec des centaines de clients chez PTSMAKE. Ces deux procédés permettent de créer des produits multimatériaux étonnants, mais le choix du bon procédé peut vous faire gagner du temps et de l'argent. Je vous expliquerai les principales différences, je vous montrerai des exemples réels et je vous aiderai à choisir le procédé qui convient le mieux à votre projet.
Qu'est-ce que le surmoulage ?
Vous êtes-vous déjà demandé comment votre étui de téléphone combine le plastique dur avec des surfaces douces et adhérentes ? Ou pourquoi les dispositifs médicaux modernes sont à la fois robustes et confortables ? Le secret réside dans la technologie du surmoulage.
Le surmoulage est un procédé de fabrication qui consiste à injecter un second matériau sur un premier matériau existant afin de créer un composant unique et multi-matériaux. Cette technique combine les propriétés de différents matériaux afin d'améliorer la fonctionnalité, la durabilité et l'expérience de l'utilisateur du produit.
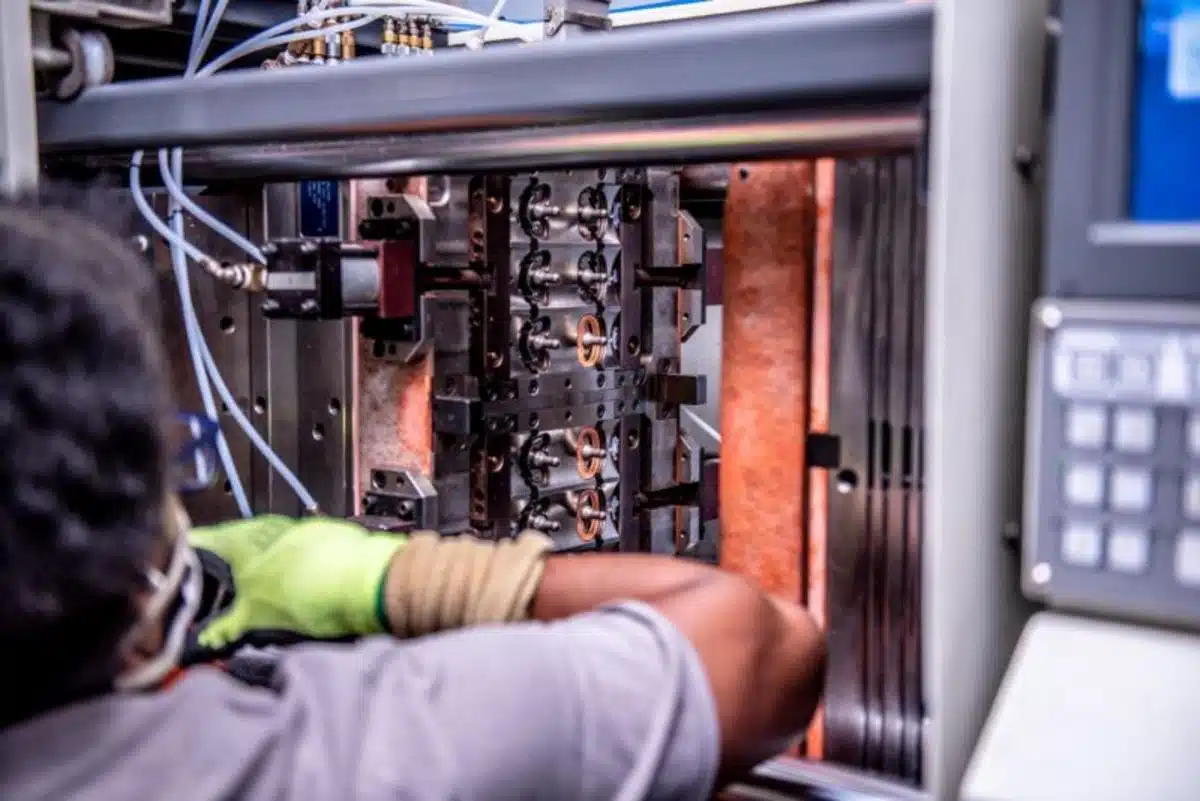
Comprendre les bases du surmoulage
Depuis plus de 15 ans que je travaille chez PTSMAKE, j'ai vu le surmoulage révolutionner la conception de produits dans diverses industries. Ce processus implique généralement deux composants principaux : un substrat rigide (généralement un thermoplastique) et un matériau surmoulé (souvent un matériau plus mou et plus flexible comme le TPE ou le caoutchouc).
Le processus se déroule en deux étapes :
- Tout d'abord, nous créons le composant de base par moulage par injection traditionnel
- Ensuite, nous injectons le second matériau sur des zones spécifiques du composant de base
Principaux avantages du surmoulage
Sur la base de notre vaste expérience de travail avec des clients de différents secteurs, j'ai identifié plusieurs avantages cruciaux :
Bénéfice | Description | Exemple concret |
---|---|---|
Ergonomie améliorée | Les surfaces douces au toucher améliorent la prise en main et le confort de l'utilisateur | Poignées d'outils électriques |
Durabilité améliorée | Absorption des chocs et amortissement des vibrations | Étuis pour appareils électroniques |
Flexibilité de la conception | Multiples combinaisons de couleurs et de matériaux | Boîtiers de produits de consommation |
Rapport coût-efficacité | Élimine les étapes d'assemblage et réduit le nombre de pièces | Composants de dispositifs médicaux |
Scellement environnemental | Crée des barrières étanches à l'eau et à la poussière | Matériel de plein air |
Combinaisons de matériaux et compatibilité
L'un des aspects les plus importants que j'ai appris à connaître dans le domaine du surmoulage est la sélection des matériaux. Voici les combinaisons les plus courantes que nous utilisons chez PTSMAKE :
Matériaux de substrats durs :
- ABS (Acrylonitrile Butadiène Styrène)
- PC (Polycarbonate)
- Nylon
- PP (Polypropylène)
Matériaux de surmoulage :
- TPE (élastomère thermoplastique)
- TPU (Polyuréthane thermoplastique)
- Silicone
- PVC souple
Applications industrielles
Au cours de ma carrière, j'ai vu le surmoulage transformer diverses industries :
Dispositifs médicaux
- Instruments chirurgicaux avec une meilleure prise
- Dispositifs portables combinant des boîtiers rigides et des surfaces confortables en contact avec la peau
- Poignées d'équipement médical aux propriétés antimicrobiennes
Électronique grand public
- Étuis pour smartphones et tablettes
- Poignées pour manettes de jeu
- Boîtiers électroniques étanches
Composants automobiles
- Contrôles du tableau de bord
- Pièces d'habillage intérieur
- Boutons de changement de vitesse
Considérations relatives à la conception
Lors de la conception d'un surmoulage, je conseille toujours à nos clients de tenir compte de ce qui suit :
Compatibilité des matériaux
- Propriétés de liaison chimique
- Taux de dilatation thermique
- Exigences en matière de température de traitement
Caractéristiques géométriques
- Variations de l'épaisseur des parois
- Contre-dépouilles et angles de dépouille
- Emplacement des portes
Exigences de production
- Attentes en matière de volume
- Contraintes de coût
- Normes de qualité
Défis communs et solutions
Au fil de mon expérience, j'ai rencontré plusieurs difficultés dans le surmoulage :
Défi | Solution | Impact |
---|---|---|
Mauvaise adhérence | Essais de compatibilité des matériaux | Amélioration de la durabilité du produit |
Formation éclair | Conception optimisée de l'outil | Meilleure qualité esthétique |
Stabilité dimensionnelle | Calcul correct du temps de refroidissement | Précision accrue |
Gestion des coûts | Sélection stratégique des matériaux | Amélioration de la rentabilité |
Contrôle de la qualité du surmoulage
Chez PTSMAKE, nous mettons en œuvre des mesures rigoureuses de contrôle de la qualité :
Essais de pré-production
- Vérification de la compatibilité des matériaux
- Analyse de l'écoulement des moules
- Évaluation du prototype
Contrôles en cours de fabrication
- Contrôle de la température
- Vérification de la pression
- Optimisation du temps de cycle
Inspection post-production
- Inspection visuelle
- Test d'adhérence
- Vérification dimensionnelle
Au cours de mes années d'expérience dans l'industrie, j'ai vu le surmoulage évoluer d'un processus de niche à une solution de fabrication courante. Sa capacité à combiner différents matériaux en un seul composant tout en réduisant les coûts d'assemblage et en améliorant les performances du produit en fait un outil inestimable dans la fabrication moderne.
Qu'est-ce que le moulage par injection 2K ?
Vous êtes-vous déjà demandé comment ces étuis élégants pour smartphones, dotés de sections à prise souple, sont fabriqués en une seule pièce ? Ou comment le tableau de bord de votre voiture combine harmonieusement le plastique dur et les matériaux doux au toucher ?
Le moulage par injection 2K est un processus de fabrication avancé qui injecte deux matériaux ou couleurs différents dans un seul moule de manière séquentielle, créant ainsi des pièces complexes aux propriétés multiples en un seul cycle de production, éliminant ainsi le besoin d'assemblage.
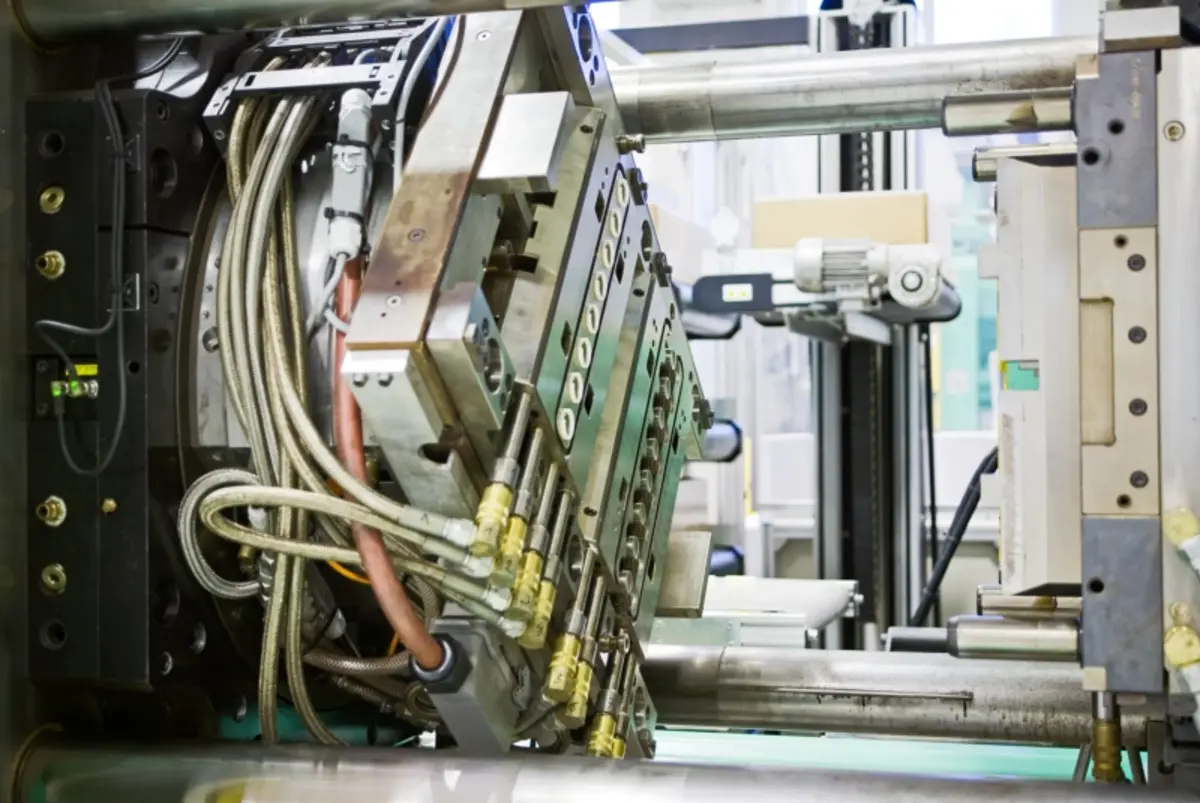
Le mécanisme de base du moulage 2K
Depuis plus de 15 ans que je travaille chez PTSMAKE, j'ai supervisé d'innombrables projets de moulage par injection en 2K. Le processus commence par l'injection du premier matériau (généralement un plastique rigide) dans la cavité du moule. Ensuite, en faisant tourner le moule ou en utilisant un robot, nous injectons le second matériau dans une autre cavité. Les deux matériaux se lient chimiquement ou mécaniquement pendant le processus de refroidissement.
Composants clés du moulage par injection 2K
Composant | Fonction | Importance |
---|---|---|
Unité d'injection primaire | Traitement du premier matériau | Structure de base des formulaires |
Unité d'injection secondaire | Traitement du deuxième matériau | Ajoute des caractéristiques fonctionnelles/esthétiques |
Système de moule rotatif | Permet le transfert de matériel | Assure un alignement précis |
Système de contrôle | Gestion du calendrier et de la séquence | Maintien de la cohérence de la qualité |
Compatibilité et sélection des matériaux
Un aspect crucial sur lequel j'insiste toujours auprès de nos clients est la compatibilité des matériaux. Tous les matériaux ne s'associent pas bien entre eux. Grâce à notre expérience, nous avons élaboré un guide complet sur la compatibilité des matériaux :
Matière première | Matériaux secondaires compatibles | Applications courantes |
---|---|---|
PC | TPE, TPU, Silicone | Boîtiers électroniques |
ABS | TPE, TPU, SEBS | Composants automobiles |
PA | TPE, TPU | Poignées d'outils |
PP | TPE, TPU, SEBS | Biens de consommation |
Avantages par rapport au moulage traditionnel
D'après l'expérience que j'ai acquise en travaillant avec des fabricants internationaux, le moulage par injection 2K offre plusieurs avantages distincts :
Efficacité de la production
- Élimine les étapes d'assemblage
- Réduction des coûts de main-d'œuvre
- Raccourcit les cycles de production de 25-40%
Amélioration de la qualité
- Meilleure liaison des matériaux
- Réduction des taux de défectuosité
- Qualité constante des pièces
Flexibilité de la conception
- Géométries complexes possibles
- Combinaisons de couleurs multiples
- Variations des propriétés des matériaux dans une même pièce
Applications industrielles
Sur la base de notre travail à PTSMAKE, j'ai vu le moulage par injection 2K exceller dans divers secteurs :
Industrie automobile
- Composants du tableau de bord
- Changeurs de vitesse
- Pièces d'habillage intérieur
- Boîtiers d'éclairage
Électronique grand public
- Étuis pour smartphones
- Télécommandes
- Contrôleurs de jeu
- Dispositifs portables
Dispositifs médicaux
- Instruments chirurgicaux
- Dispositifs d'administration de médicaments
- Matériel de diagnostic
- Boîtiers pour dispositifs médicaux
Considérations techniques
Lors de la mise en œuvre du moulage par injection 2K, plusieurs facteurs doivent faire l'objet d'une attention particulière :
Paramètres du processus
- Contrôle de la pression d'injection
- Gestion de la température des matériaux
- Optimisation du temps de cycle
- Coordination du temps de refroidissement
Lignes directrices pour la conception
- Ratios d'épaisseur de paroi
- Emplacement des portes
- Chemins d'écoulement des matériaux
- Surface de liaison
Mesures de contrôle de la qualité
- Protocoles d'inspection visuelle
- Essais de résistance à l'adhérence
- Contrôles de la précision dimensionnelle
- Évaluation de l'état de surface
Implications en termes de coûts
Au fil de nos années d'expérience, j'ai constaté que si les coûts initiaux d'outillage pour le moulage en 2K sont plus élevés, les avantages à long terme justifient souvent l'investissement :
Facteur de coût | Impact | Calendrier du retour sur investissement |
---|---|---|
Outillage | 30-50% plus élevé que le traditionnel | 6-12 mois |
Travail | 40-60% inférieur | Immédiate |
Déchets matériels | Réduction 20-30% | 3-6 mois |
Contrôle de la qualité | 25-35% taux de rejet plus faibles | 3-6 mois |
Limites du processus et solutions
Malgré ses avantages, le moulage par injection 2K présente certaines limites auxquelles nous avons appris à remédier :
Contraintes matérielles
- Combinaisons limitées de matériaux
- Problèmes de compatibilité thermique
- Variations de la force d'adhérence
Restrictions de conception
- Exigences en matière d'épaisseur minimale des parois
- Limites de l'emplacement de la porte
- Contraintes liées à la taille des pièces
Considérations sur les coûts
- Investissement initial plus élevé
- Conception de moules complexes
- Besoins en équipements spécialisés
Grâce à une planification minutieuse et à la sélection des matériaux, ces limitations peuvent être gérées efficacement pour obtenir des résultats optimaux.
En quoi le surmoulage diffère-t-il du moulage par injection 2K ?
Après plus de 15 ans dans le domaine du moulage par injection de plastique, j'ai vu d'innombrables clients confondre le surmoulage et le moulage par injection 2K, ce qui entraîne souvent des retards et des reprises de projets coûteux.
Le surmoulage et le moulage par injection 2K sont des procédés de fabrication distincts. Le surmoulage utilise deux étapes de moulage distinctes en séquence, tandis que le moulage par injection 2K combine les deux étapes en un seul cycle à l'aide d'un équipement spécialisé.
Différences dans le déroulement du processus
Dans mes activités quotidiennes à PTSMAKE, j'ai constaté qu'il est essentiel de comprendre le flux de travail. Permettez-moi de vous présenter les principales différences :
Processus de surmoulage
- Première étape : Créer le composant de base (substrat)
- Deuxième étape : Transfert vers un autre moule ou une autre machine
- Dernière étape : Mouler le second matériau sur le substrat
- Durée totale : Généralement 20 à 45 minutes pour le cycle complet
Processus de moulage par injection 2K
- Fonctionnement d'une seule machine
- Rotation automatisée entre les prises de vue
- Cycle de moulage continu
- Durée totale : Typiquement 30-60 secondes par pièce
Exigences en matière d'équipement
Sur la base de mon expérience de la gestion des deux processus, voici une comparaison détaillée :
Fonctionnalité | Surmoulage | Moulage par injection 2K |
---|---|---|
Type de machine | Machine de moulage par injection standard | Machine spécialisée multi-composants |
Complexité de l'outil | Moules simples et séparés | Système de moule complexe et intégré |
Temps de préparation | Plus long, plusieurs installations | Plus court, un seul réglage |
Coût de l'investissement | Investissement initial moins élevé | Coûts plus élevés des machines et de l'outillage |
Considérations sur la compatibilité des matériaux
J'ai aidé de nombreux clients à choisir les bons matériaux pour leurs projets. Voici ce qu'il faut savoir :
Options de matériaux de surmoulage
- Des combinaisons de matériaux plus souples
- Meilleur pour les matériaux incompatibles
- Permet de prendre le temps d'établir une bonne liaison
- Peut utiliser des promoteurs d'adhésion
Exigences relatives aux matériaux de moulage 2K
- Les matériaux doivent être chimiquement compatibles
- Des températures de traitement similaires sont nécessaires
- Possibilités limitées de combinaison de matériaux
- Des exigences de collage plus rapides
Considérations relatives à la conception
Au cours de mes années de gestion de projets, j'ai identifié ces facteurs critiques de conception :
Avantages de la conception du surmoulage
- Possibilité de géométries plus complexes
- Meilleur contrôle de l'épaisseur de l'interface
- Plus facile de modifier les dessins et modèles
- Des exigences de tolérance plus souples
Limites de la conception des moules 2K
- Limité par le mouvement de l'outil
- Nécessité d'une localisation précise des portes
- Possibilité de contre-dépouilles limitées
- Exigences plus strictes en matière de tolérance
Implications en termes de coûts
Permettez-moi de vous faire part de quelques réflexions issues de nos discussions sur la tarification :
Coûts de surmoulage
- Investissement réduit dans l'outillage
- Coûts de main-d'œuvre plus élevés
- Augmentation des coûts de manutention
- Meilleur pour les faibles volumes
Coûts du moulage 2K
- Investissement initial plus élevé
- Réduction des coûts de main-d'œuvre
- Réduction des coûts de manutention
- Plus économique pour les gros volumes
Considérations sur la qualité
D'après mon expérience en matière de contrôle de la qualité :
Aspects de la qualité du surmoulage
- Un meilleur contrôle de chaque couche
- Inspection plus facile entre les étapes
- Un collage plus cohérent
- Réduction des taux de rejet dans les pièces complexes
Facteurs de qualité du moulage 2K
- Des temps de cycle plus courts peuvent affecter le collage
- Interfaces plus difficiles à contrôler
- Une plus grande cohérence dans les pièces simples
- Meilleur pour la cohérence des grands volumes
Guide de sélection des applications
Sur la base des milliers de projets que j'ai supervisés :
Meilleur pour le surmoulage
- Dispositifs médicaux nécessitant des matériaux certifiés
- Boîtiers électroniques complexes
- Poignées douces au toucher
- Volumes de production faibles à moyens
Meilleur pour le moulage 2K
- Composants automobiles
- Produits de consommation à grand volume
- Applications bicolores simples
- Pièces nécessitant des cycles de production rapides
Grâce à ma vaste expérience chez PTSMAKE, j'ai appris que le choix entre le surmoulage et le moulage par injection 2K n'est pas seulement une question de capacités techniques - il s'agit de comprendre les besoins spécifiques de votre projet, vos volumes de production et vos exigences en matière de qualité. Chaque processus présente des avantages uniques, et le succès réside dans un choix éclairé basé sur votre application particulière.
Quels sont les avantages et les limites du surmoulage ?
En tant qu'expert en fabrication avec plus de 15 ans d'expérience chez PTSMAKE, j'ai vu d'innombrables projets où le surmoulage semblait parfait sur le papier, mais où des défis inattendus sont apparus dans la réalité.
Le surmoulage est un processus de fabrication qui combine plusieurs matériaux en une seule pièce, offrant des avantages tels qu'une meilleure adhérence et des besoins d'assemblage réduits, mais il s'accompagne également de défis tels que des cycles de production plus longs et des problèmes de collage des matériaux.
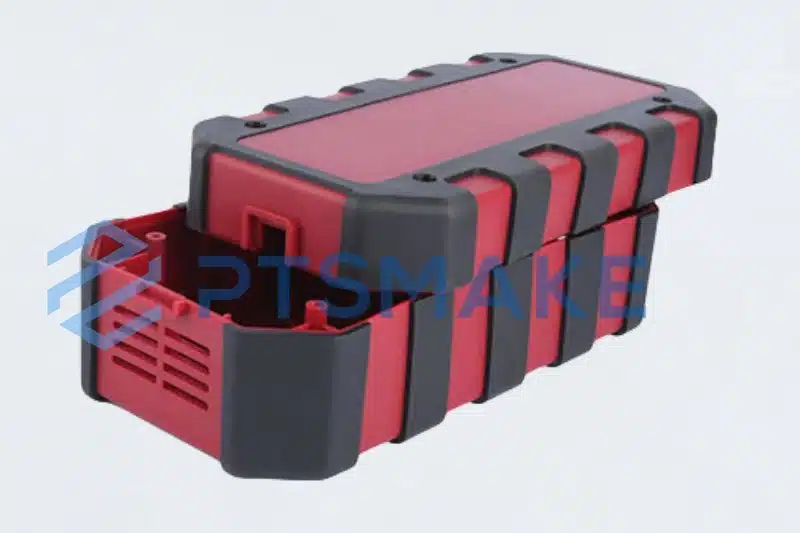
Principaux avantages du surmoulage
Fonctionnalité améliorée du produit
Dans le cadre de ma collaboration avec de grands fabricants d'électronique, le surmoulage s'est avéré inestimable pour améliorer l'adhérence et la sensation du produit. Voici ce que j'ai observé :
- Poignées souples sur les outils électriques
- Surfaces antidérapantes sur les dispositifs médicaux
- Poignées ergonomiques sur les produits de consommation
Exigences réduites en matière d'assemblage
L'un des avantages les plus significatifs que j'ai constatés est l'élimination des multiples étapes d'assemblage :
- Pas besoin d'attaches mécaniques
- Moins de composants individuels
- Réduction des coûts de main-d'œuvre
- Diminution du risque d'erreurs d'assemblage
Amélioration de la protection des produits
Les capacités d'étanchéité du surmoulage sont remarquables :
- Barrières résistantes à l'eau
- Protection contre la poussière et les débris
- Amortissement des vibrations
- Durabilité accrue dans les environnements difficiles
Type de protection | Bénéfice | Applications courantes |
---|---|---|
Joint d'étanchéité | Empêche les infiltrations d'eau | Electronique d'extérieur |
Protection contre les chocs | Absorbe les chocs | Appareils mobiles |
Résistance chimique | Protège contre la corrosion | Équipements industriels |
Isolation thermique | Gestion de la température | Outils à main |
Limites et défis
Cycles de production prolongés
D'après mon expérience dans l'atelier de fabrication :
- Les temps d'installation sont plus longs
- Des contrôles de qualité supplémentaires sont nécessaires
- Exigences multiples en matière de manutention
- Temps de refroidissement entre les prises de vue
Considérations sur les coûts
L'impact financier comprend
- Investissement initial en outillage plus élevé
- Coûts d'exploitation secondaires
- Essais de compatibilité des matériaux
- Renforcement des mesures de contrôle de la qualité
Défis techniques
Questions relatives à l'adhérence des matériaux
J'ai rencontré ces problèmes courants :
- Mauvaise adhérence entre les matériaux
- Inadéquation de la dilatation thermique
- Problèmes de compatibilité chimique
- Exigences en matière de préparation de la surface
Limites de la conception
Les principales restrictions sont les suivantes :
- Contraintes d'épaisseur des matériaux
- Limites de l'emplacement de la porte
- Défis géométriques complexes
- Considérations relatives à la conception des outils
Défi | Impact | Stratégie d'atténuation |
---|---|---|
Compatibilité des matériaux | Risque de délamination | Essais approfondis des matériaux |
Conception d'outils | Plus grande complexité | Simulation CAO avancée |
Contrôle de la qualité | Besoins accrus en matière d'inspection | Systèmes de vision automatisés |
Vitesse de production | Des temps de cycle plus longs | Optimisation des processus |
Applications concrètes et études de cas
Électronique grand public
Dans le cadre de notre travail avec les principaux fabricants d'électronique :
- Touches tactiles sur les télécommandes
- Joints d'étanchéité pour les appareils d'extérieur
- Boîtiers résistants aux chocs pour téléphones portables
Dispositifs médicaux
Nos projets de dispositifs médicaux démontrent :
- Poignées ergonomiques pour outils chirurgicaux
- Boîtiers d'équipement résistant aux produits chimiques
- Composants compatibles avec la stérilisation
Applications automobiles
Les utilisations courantes dans l'industrie automobile sont les suivantes
- Composants de la garniture intérieure
- Connecteurs électriques étanches
- Supports amortisseurs de vibrations
Meilleures pratiques pour un surmoulage réussi
Sur la base de mon expérience de la gestion de milliers de projets :
Sélection des matériaux
- Tests de compatibilité approfondis
- Vérification de la résistance à la température
- Évaluation de la résistance chimique
Optimisation de la conception
- Planification adéquate de l'emplacement des portes d'embarquement
- Prise en compte de l'épaisseur de la paroi
- Mise en œuvre de l'angle d'attaque
Contrôle des processus
- Contrôle de la température
- Optimisation de la pression
- Gestion du temps de cycle
Assurance qualité
- Protocoles d'inspection visuelle
- Essais de résistance à l'adhérence
- Vérification dimensionnelle
Au fil des années passées chez PTSMAKE, j'ai appris qu'un surmoulage réussi exigeait un équilibre minutieux entre ces avantages et ces limites. Bien que les avantages puissent être considérables, une planification et une expertise minutieuses sont essentielles pour obtenir des résultats optimaux. Je conseille toujours à nos clients d'évaluer soigneusement leurs besoins spécifiques en fonction de ces facteurs avant de s'engager dans une solution de surmoulage.
Quels sont les avantages et les limites du moulage par injection 2K ?
Vous avez du mal à décider si le moulage par injection 2K est adapté à votre projet ? Après plus de 15 ans dans l'industrie, j'ai vu à la fois les avantages incroyables et les limites difficiles de cette technologie.
Le moulage par injection 2K offre des cycles de production rapides et une forte adhérence des matériaux, mais il s'accompagne de coûts d'équipement initiaux élevés et convient mieux à la production de gros volumes. Il est essentiel de comprendre ces compromis pour prendre des décisions éclairées en matière de fabrication.
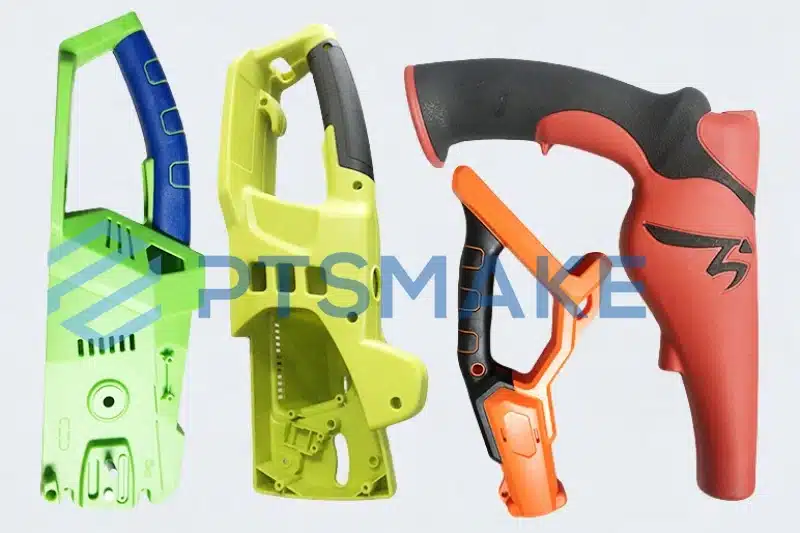
Principaux avantages du moulage par injection 2K
Sur la base de mon expérience chez PTSMAKE, j'ai identifié plusieurs avantages significatifs qui distinguent le moulage par injection 2K :
Cycles de production efficaces
L'intégration de deux matériaux dans un seul cycle de moulage réduit considérablement le temps de production. Dans nos installations, nous avons réalisé :
Processus traditionnel | Processus de moulage 2K | Gain de temps |
---|---|---|
45-60 secondes/partie | 25-35 secondes/partie | Jusqu'à 40% |
Adhésion supérieure des matériaux
Contrairement aux méthodes d'assemblage traditionnelles, le moulage 2K crée une liaison moléculaire entre les matériaux. Il en résulte :
- Une plus grande intégrité structurelle
- Meilleure résistance aux facteurs environnementaux
- Réduction du risque de séparation des composants
- Amélioration de la longévité des produits
Flexibilité accrue de la conception
La possibilité de combiner différents matériaux ouvre de nouvelles possibilités de conception :
- Combinaisons multicolores
- Recouvrement soft-touch
- Joints et garnitures intégrés
- Géométries complexes
Limites et défis
Investissement initial élevé
D'après mon expérience de la gestion de lignes de production, les coûts initiaux peuvent être considérables :
Catégorie d'investissement | Fourchette de coûts approximative |
---|---|
Machine de moulage 2K | $150,000 - $500,000 |
Outillage sur mesure | $25,000 - $100,000 |
Mise en place et formation | $10,000 - $30,000 |
Exigences en matière de volume
Le moulage 2K devient rentable principalement dans le cadre d'une production en grande quantité :
- Volume annuel minimum recommandé : 100 000+ unités
- Fourchette de production optimale : 250 000+ unités
- Le seuil de rentabilité nécessite généralement d'importantes séries de production
Complexités techniques
Depuis plus de 15 ans que je travaille à PTSMAKE, j'ai observé plusieurs défis techniques :
- Exigences en matière de compatibilité des matériaux
- Besoins complexes en matière de conception d'outils
- Exigences en matière de contrôle précis des processus
- Exigences en matière de formation spécialisée des opérateurs
Applications dans le monde réel
Industrie automobile
Nous avons mis en œuvre avec succès le moulage 2K pour :
- Éléments du tableau de bord avec surfaces douces au toucher
- Voyants lumineux multicolores
- Joints intégrés dans les connecteurs électriques
- Garnitures extérieures résistantes aux intempéries
Électronique grand public
Notre expérience comprend
- Étuis pour smartphones avec poignées en caoutchouc
- Composants des contrôleurs de jeu
- Boîtiers d'appareils étanches
- Voyants lumineux multicolores
Dispositifs médicaux
Les applications essentielles sont les suivantes
- Instruments chirurgicaux avec poignées ergonomiques
- Boîtiers de dispositifs médicaux avec joints intégrés
- Dispositifs d'administration de médicaments à matériaux multiples
- Composants d'équipements de laboratoire
Stratégies d'optimisation des processus
Sur la base de notre expérience en matière de fabrication, je recommande :
Sélection des matériaux
- Procéder à des essais approfondis de compatibilité des matériaux
- Tenir compte des taux de rétrécissement des deux matériaux
- Évaluer la rentabilité des combinaisons de matériaux
Conception d'outils
- Mettre en place des canaux d'aération et de refroidissement appropriés
- Concevoir des emplacements optimaux pour les portes
- Tenir compte des schémas de flux de matières
Contrôle de la qualité
- Mettre en place des systèmes d'inspection automatisés
- Établir des paramètres de qualité clairs
- Maintenir une documentation stricte sur les processus
Gestion des coûts
- Optimiser les temps de cycle
- Minimiser les déchets de matériaux
- Mettre en œuvre la maintenance prédictive
- Former efficacement les opérateurs
Au fil des années de collaboration avec divers clients de PTSMAKE, j'ai appris que le succès du moulage par injection en 2K exigeait une prise en compte minutieuse de ces facteurs. Bien que la technologie offre des avantages remarquables en termes d'efficacité de la production et de qualité des produits, il est essentiel d'évaluer soigneusement si les avantages justifient l'investissement initial et les exigences opérationnelles permanentes pour votre application spécifique.
L'essentiel est d'analyser en profondeur vos exigences de production, les spécifications des matériaux et votre stratégie de fabrication à long terme avant de vous engager dans le moulage par injection 2K. Dans de nombreux cas, les avantages de cette technologie peuvent constituer un avantage concurrentiel significatif, mais uniquement s'ils sont correctement adaptés à vos objectifs de fabrication et à vos volumes de production.
Quelles sont les industries qui bénéficient le plus du surmoulage ?
Vous vous demandez quelles industries peuvent vraiment maximiser le potentiel du surmoulage ? Après plus de 15 ans dans l'industrie manufacturière, j'ai été témoin de transformations remarquables dans divers secteurs.
La technologie du surmoulage profite principalement à quatre secteurs clés : les appareils médicaux, l'électronique grand public, l'automobile et les outils portatifs. Ces secteurs utilisent le surmoulage pour améliorer la fonctionnalité des produits, l'expérience des utilisateurs et la durabilité tout en maintenant la rentabilité.
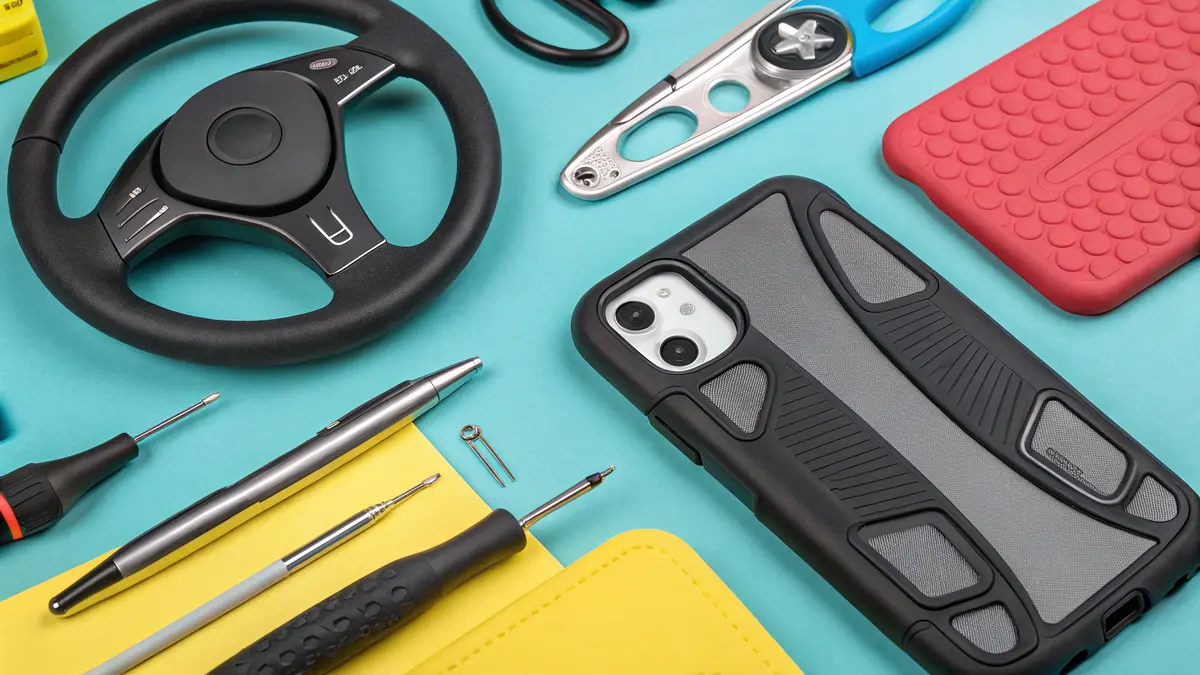
Applications dans l'industrie médicale
D'après mon expérience avec les fabricants de dispositifs médicaux, le surmoulage a révolutionné la conception des équipements médicaux. Les dispositifs médicaux nécessitent une prise en main précise, du confort et des capacités de stérilisation. Voici quelques applications clés :
- Instruments chirurgicaux avec poignées ergonomiques
- Seringues médicales avec poignée renforcée
- Outils dentaires avec poignées confortables
- Enveloppes de dispositifs médicaux avec propriétés d'étanchéité
L'industrie médicale apprécie particulièrement le surmoulage car il permet de créer des surfaces sans couture, résistantes aux bactéries, faciles à nettoyer et à stériliser.
Impact de l'électronique grand public
Le secteur de l'électronique grand public a adopté le surmoulage à des fins de protection et d'esthétique. J'ai vu d'innombrables exemples où cette technologie a amélioré la durabilité du produit et l'expérience de l'utilisateur :
Catégorie de produits | Avantages du surmoulage |
---|---|
Étuis pour smartphones | Résistance aux chocs, amélioration de l'adhérence |
Ecouteurs | Confort, résistance à l'eau |
Télécommandes | Durabilité, absorption des chocs |
Contrôleurs de jeu | Poignée ergonomique, résistance à la transpiration |
Intégration de l'industrie automobile
Le secteur automobile représente l'un des plus grands marchés pour le surmoulage. Ma collaboration avec les principaux constructeurs automobiles m'a permis d'observer ces applications critiques :
Composants intérieurs
- Contrôles du tableau de bord
- Poignées de porte
- Éléments de la console centrale
- Poignées de volant
Pièces externes
- Joints d'étanchéité
- Joints
- Connecteurs de câbles
- Éléments de garniture
La révolution des outils portatifs
Travailler avec des fabricants d'outils m'a montré comment le surmoulage a transformé l'industrie de l'outillage électrique et manuel :
Outils électriques
- Poignées de forage avec amortissement des vibrations
- Poignées de scie avec caractéristiques de sécurité renforcées
- Boîtiers de visseuses à percussion plus durables
- Poignées de tournevis électriques pour un meilleur contrôle
Outils à main
- Poignées de tournevis ergonomiques
- Poignées de pinces avec caractéristiques de confort
- Poignées de clés antidérapantes
- Poignées à marteau avec absorption des chocs
Avantages intersectoriels
Au cours de mes années chez PTSMAKE, j'ai identifié plusieurs avantages universels que le surmoulage apporte à ces industries :
Fonctionnalité améliorée
- Meilleure adhérence et meilleur contrôle
- Amélioration des propriétés d'étanchéité
- Amortissement des vibrations
- Résistance aux chocs
Améliorations esthétiques
- Options de couleurs personnalisées
- Variations de texture
- Différenciation des marques
- Un aspect et une sensation de qualité supérieure
Rapport coût-efficacité
- Réduction des étapes d'assemblage
- Réduction des coûts de main-d'œuvre
- Diminution du temps de production
- Un minimum de déchets
Expérience de l'utilisateur
- Amélioration de l'ergonomie
- Meilleur retour d'information tactile
- Des dispositifs de sécurité renforcés
- Plus de confort
Considérations relatives à la fabrication
Sur la base de notre vaste expérience avec divers clients, j'ai constaté que ces facteurs clés sont essentiels pour une mise en œuvre réussie du surmoulage :
Considération | Impact |
---|---|
Sélection des matériaux | Détermine la force et la performance de l'adhérence |
Optimisation de la conception | Affecte l'efficacité de la fabrication |
Contrôle de la qualité | Garantit des résultats cohérents |
Gestion des coûts | Influence sur la compétitivité du marché |
En travaillant avec diverses industries, j'ai appris que les applications de surmoulage réussies nécessitent un examen attentif des éléments suivants :
- Compatibilité des matériaux
- Exigences en matière de conception
- Volume de production
- Conditions environnementales
- Conformité réglementaire
Le succès du surmoulage dans ces industries démontre sa polyvalence et son efficacité. Ayant supervisé d'innombrables projets, je peux affirmer en toute confiance que, lorsqu'il est correctement mis en œuvre, le surmoulage offre des avantages concurrentiels significatifs en termes de qualité des produits, de satisfaction des utilisateurs et d'efficacité de la fabrication.
Quelles sont les industries qui bénéficient le plus du moulage par injection 2K ?
Vous vous demandez quelles sont les industries qui mènent la révolution du moulage par injection 2K ? Après plus de 15 ans passés dans l'industrie manufacturière, j'ai assisté à des transformations remarquables dans divers secteurs.
Le moulage par injection 2K a changé la donne dans les secteurs de l'automobile, de l'électronique grand public et de la médecine. Ces secteurs bénéficient d'une réduction des coûts d'assemblage, d'une amélioration de la fonctionnalité des produits et d'une plus grande efficacité de la production grâce à ce processus de fabrication avancé.
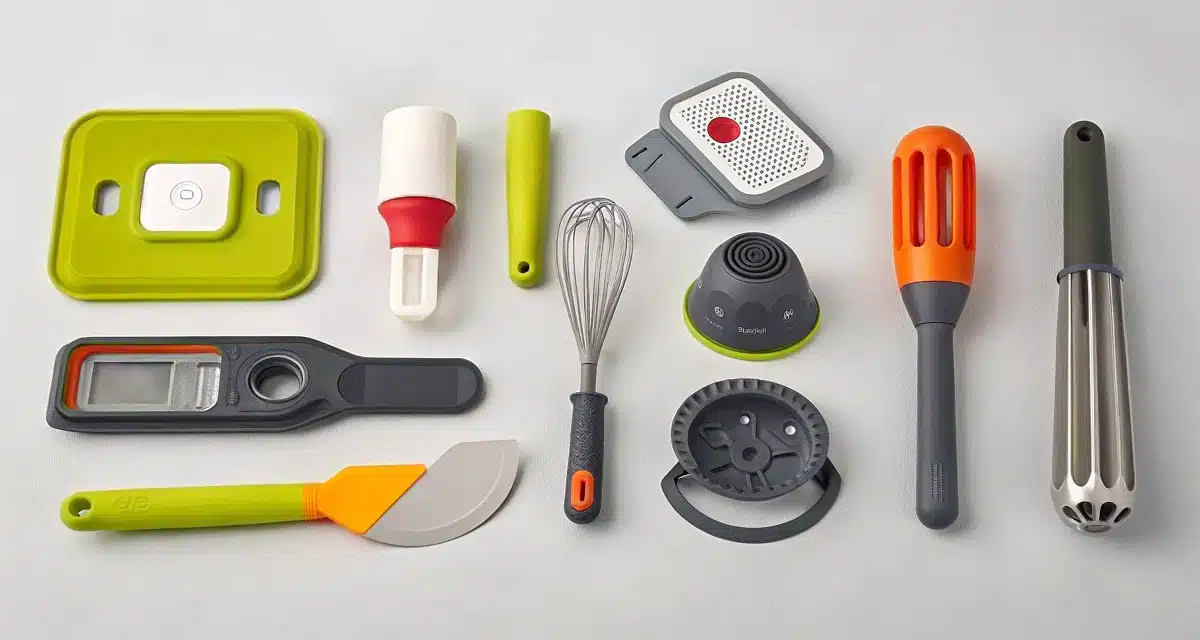
Applications dans l'industrie automobile
D'après mon expérience auprès de grands constructeurs automobiles, le moulage par injection 2K a révolutionné la production de composants intérieurs. Le secteur automobile bénéficie de :
- Composants multimatériaux du tableau de bord
- Commandes au volant au toucher doux
- Assemblages de boutons lumineux
- Garnitures extérieures résistantes aux intempéries
L'intégration de matériaux durs et souples dans un processus unique a permis de réduire considérablement le temps d'assemblage et d'améliorer la qualité des pièces. Par exemple, la production d'une poignée de porte intégrant un matériau à prise souple prend 40% moins de temps que les méthodes traditionnelles.
Évolution de l'électronique grand public
L'industrie électronique a adopté le moulage 2K pour.. :
Type de composant | Avantages | Applications courantes |
---|---|---|
Assemblage de boutons | Options multicolores, sensation tactile améliorée | Téléphones portables, télécommandes |
Boîtiers d'appareils | Etanchéité, esthétique | Appareils intelligents et portables |
Panneaux de contrôle | Durabilité accrue, écrans intégrés | Appareils ménagers, consoles de jeux |
Fabrication de dispositifs médicaux
Le secteur médical bénéficie particulièrement de la capacité du moulage 2K à créer :
- Instruments chirurgicaux ergonomiques avec poignées souples
- Dispositifs de diagnostic à composants multiples
- Boîtiers médicaux étanches avec joints intégrés
J'ai vu des matériaux compatibles avec la stérilisation combinés à des surfaces de préhension confortables, réduisant les étapes de fabrication tout en améliorant la sécurité des produits.
Innovations en matière d'appareils ménagers
Les appareils modernes utilisent des moulures 2K :
- Interfaces du panneau de contrôle
- Composants étanches et résistants à l'eau
- Poignées ergonomiques
- Éléments décoratifs dotés de propriétés fonctionnelles
Produits de soins personnels
L'industrie des soins personnels utilise le moulage 2K pour :
- Poignées de brosse à dents avec zones de préhension
- Poignées en lame de rasoir combinant structure rigide et toucher doux
- Emballage cosmétique avec des propriétés de matériaux multiples
Avantages en termes de coûts pour tous les secteurs d'activité
Mon expérience dans le secteur de la fabrication m'a permis de constater les avantages suivants :
Réduction des coûts d'assemblage
- Élimination des opérations secondaires
- Besoins en main-d'œuvre réduits
- Diminution des besoins en matière de gestion des stocks
Efficacité de la production
- Des cycles plus rapides
- Réduction des taux de rebut
- Amélioration de la cohérence de la qualité
Liberté de conception
- Intégration de fonctions multiples
- Options esthétiques améliorées
- De meilleures solutions ergonomiques
Amélioration de la qualité et des performances
La mise en œuvre du moulage 2K a conduit à :
Aspect | Moulage traditionnel | 2K Molding |
---|---|---|
Étapes d'assemblage | 3-4 étapes | 1 étape |
Durée du cycle | 45-60 secondes | 25-35 secondes |
Taux de défectuosité | 2-3% | <1% |
Résistance de l'adhérence des matériaux | Modéré | Haut |
Impact sur l'environnement
Le moulage par injection 2K offre des avantages environnementaux :
- Réduction des déchets grâce à l'élimination des étapes d'assemblage
- Réduction de la consommation d'énergie dans la production
- Diminution des besoins en transport pour les composants
- Amélioration de la longévité des produits
Lorsque je travaille avec des clients de ces secteurs, je constate systématiquement des économies de 15-20% par rapport aux méthodes de fabrication traditionnelles. La possibilité de combiner des matériaux dans un processus unique améliore non seulement l'efficacité, mais permet également de trouver des solutions de conception innovantes qui n'étaient pas possibles auparavant.
Au cours de mes années passées chez PTSMAKE, j'ai été témoin de la transformation des processus de fabrication dans tous ces secteurs. L'adoption du moulage par injection 2K continue de croître à mesure que de plus en plus d'industries reconnaissent ses avantages en termes de réduction des coûts, d'amélioration de la qualité et de solutions de conception innovantes.
Pour les entreprises qui envisagent le moulage par injection 2K, il est essentiel de comprendre que le succès dépend de la sélection correcte des matériaux, de la conception de l'outillage et du contrôle du processus. L'investissement initial dans la technologie 2K est souvent compensé par des économies à long terme sur les coûts de production et l'amélioration de la qualité des produits.
Quelles sont les combinaisons de matériaux possibles dans le surmoulage ?
Vous êtes-vous déjà demandé pourquoi le manche de votre brosse à dents est souple alors que la tête reste rigide ? Ou pourquoi votre outil électrique présente une surface parfaitement adhérente ? C'est la magie du surmoulage qui opère.
Le surmoulage permet diverses combinaisons de matériaux, notamment des paires thermoplastique-élastomère, des combinaisons métal-plastique et des assemblages multithermoplastiques. La réussite dépend de la compatibilité des matériaux, de la préparation de la surface et des techniques de collage appropriées.
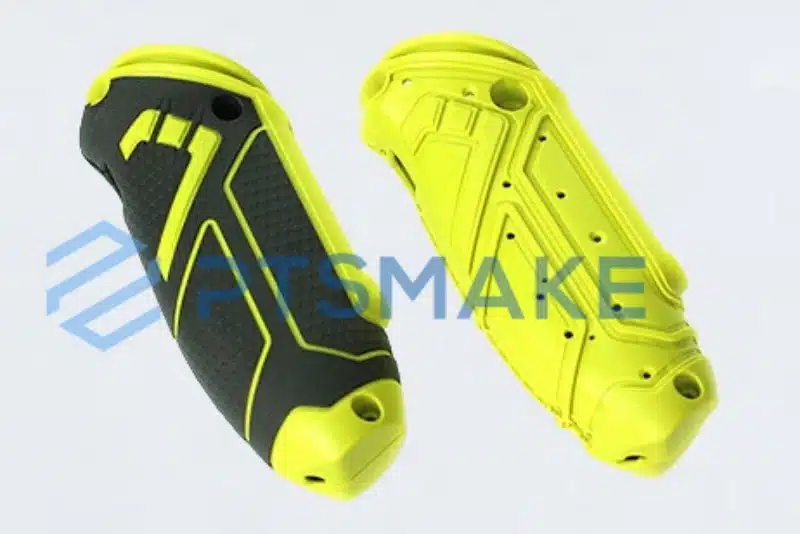
Combinaisons de matériaux courantes
Au cours de mes 15 années d'expérience chez PTSMAKE, j'ai travaillé avec de nombreuses combinaisons de matériaux. Voici les plus courantes :
Combinaisons thermoplastiques-élastomères
La combinaison la plus populaire que nous utilisons est celle des substrats thermoplastiques et des élastomères thermoplastiques (TPE). Ces paires offrent d'excellentes propriétés de collage et une grande polyvalence. Voici un tableau de compatibilité typique que nous utilisons :
Matériau du substrat | TPE compatible | Applications courantes |
---|---|---|
PP | TPE-S, TPV | Produits de consommation, pièces automobiles |
ABS | TPE-S, TPU | Boîtiers électroniques, poignées |
PC | TPE-U, TPE-E | Dispositifs médicaux, outils |
PA | TPE-E, TPU | Composants industriels |
PBT | TPE-E, TPU | Connecteurs électriques |
Combinaisons métal-plastique
Lorsque l'on combine des métaux avec des plastiques, le traitement de surface devient crucial. J'ai vu de nombreux projets échouer en raison d'une mauvaise préparation de la surface. Les principaux matériaux que nous utilisons couramment sont les suivants
- Aluminium et thermoplastiques techniques
- Acier inoxydable avec polymères haute performance
- Laiton avec des qualités spéciales de nylon
Systèmes multithermoplastiques
C'est là que les choses deviennent intéressantes. Nous pouvons combiner différents thermoplastiques pour obtenir des propriétés spécifiques :
- Combinaisons PC/ABS pour une meilleure résistance aux chocs
- Mélanges PBT/PET pour une meilleure résistance chimique
- Systèmes PA/PP pour une résistance rentable
Facteurs critiques pour un collage réussi
Compatibilité des matériaux
D'après mon expérience, la compatibilité chimique est la base d'un surmoulage réussi. Voici ce que nous prenons en compte :
- Similitude de structure chimique
- Plages de température de fusion
- Potentiel d'interaction de la chaîne moléculaire
- Caractéristiques de l'énergie de surface
Techniques de préparation des surfaces
J'ai appris qu'une bonne préparation de la surface peut faire ou défaire un projet de surmoulage :
Méthode de préparation | Meilleur pour | Efficacité |
---|---|---|
Traitement au plasma | Métaux, plastiques à haute performance | Excellent |
Traitement Corona | La plupart des thermoplastiques | Très bon |
Gravure chimique | Métaux, plastiques difficiles à coller | Bon |
Abrasion mécanique | Substrats métalliques | Modéré |
Solutions avancées de collage
Dans le cadre de mon travail à PTSMAKE, nous avons développé plusieurs approches pour améliorer la liaison :
Applications de l'apprêt
- Utilisation d'apprêts spécialisés pour les matériaux incompatibles
- Développement de formulations d'apprêts sur mesure
- Application de traitements spécifiques à la surface
Verrouillage mécanique
- Conception des contre-dépouilles et des caniveaux
- Création de motifs de micro-texture
- Mise en œuvre des caractéristiques de la queue d'aronde
Paramètres du processus
Sur la base de nos données de fabrication :- Contrôle de la température du moule à ±5°C
- Optimisation de la pression d'injection
- Ajustement du temps de cycle pour différentes combinaisons de matériaux
Dépannage des problèmes courants
Au fil des années passées dans le secteur, j'ai été confronté à différents défis :
Prévention du décollement
Pour éviter la séparation entre les couches :
Considérations relatives à la sélection des matériaux
- Vérifier les tableaux de compatibilité
- Vérifier la résistance à la température
- Test de résistance chimique
Contrôle des processus
- Contrôle des vitesses d'injection
- Contrôler les taux de refroidissement
- Maintenir une pression constante
Mesures de contrôle de la qualité
Nous mettons en œuvre des contrôles de qualité stricts :
Méthode d'essai | Paramètre mesuré | Fréquence |
---|---|---|
Test de traction | Résistance de l'adhérence | Chaque lot |
Analyse transversale | Qualité de l'interface | Hebdomadaire |
Essais environnementaux | Durabilité à long terme | Mensuel |
Résistance chimique | Intégrité des matériaux | Par projet |
Mon expérience m'a permis de constater qu'un surmoulage réussi exige une connaissance approfondie des propriétés des matériaux et des paramètres de traitement. Chez PTSMAKE, nous mettons continuellement à jour notre base de données de combinaisons de matériaux et de paramètres de traitement afin de garantir des résultats optimaux à nos clients.
Cette approche globale de la sélection et du traitement des matériaux nous a permis d'atteindre un taux de réussite de 98% dans nos projets de surmoulage, avec un nombre minimal de cas de rupture d'adhérence ou de problèmes de qualité. N'oubliez pas que la clé n'est pas seulement de sélectionner des matériaux compatibles, mais aussi de comprendre comment les traiter correctement.
Quelles sont les combinaisons de matériaux possibles dans le moulage par injection 2K ?
Après plus de 15 ans dans le domaine du moulage par injection, j'ai vu d'innombrables clients se débattre avec le choix des bonnes combinaisons de matériaux pour leurs projets 2K. Permettez-moi de vous faire part de ce qui fonctionne réellement.
Le moulage par injection à deux composants (2K) permet des combinaisons de matériaux spécifiques, comme les plastiques rigides et souples ou les matériaux durs multicolores. Les combinaisons les plus courantes sont l'ABS avec le TPE, le PC avec l'ABS et divers autres thermoplastiques compatibles qui créent de fortes liaisons chimiques.
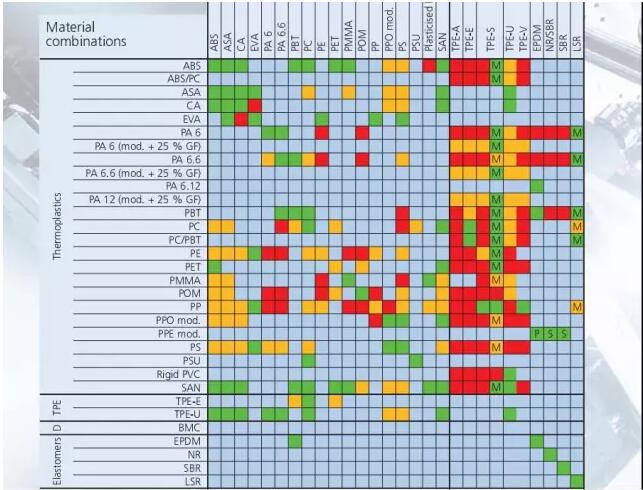
Combinaisons courantes de matériaux compatibles
Dans mon travail quotidien à PTSMAKE, je recommande fréquemment ces combinaisons de matériaux éprouvées à nos clients :
Matériau de base | Matériau de surmoulage compatible | Applications courantes |
---|---|---|
ABS | TPE/TPU | Poignées d'outils électriques, électronique grand public |
PC | ABS | Pièces automobiles, boîtiers électroniques |
PA | TPE/TPU | Composants mécaniques, équipements sportifs |
PP | TPE/TPU | Produits de consommation, dispositifs médicaux |
PBT | TPE/TPU | Connecteurs électriques, pièces automobiles |
Combinaisons de matériaux durs
Lorsque je travaille avec des combinaisons difficiles, j'ai trouvé ces combinaisons particulièrement efficaces :
Combinaison PC/ABS
- Excellentes propriétés mécaniques
- Haute résistance aux chocs
- Bonne résistance chimique
- Courant dans les secteurs de l'automobile et de l'électronique
Combinaison PA/PBT
- Caractéristiques de résistance supérieures
- Bonne stabilité dimensionnelle
- Résistance thermique accrue
- Largement utilisé dans les composants mécaniques
Combinaisons de matériaux souples et durs
Sur la base de mon expérience avec des centaines de projets, ces combinaisons offrent les meilleurs résultats :
Configuration ABS/TPE
- Force d'adhérence élevée
- Excellente finition de surface
- Bonne flexibilité de l'élément souple
- Parfait pour les applications ergonomiques
Configuration PC/TPU
- Grande durabilité
- Résistance supérieure aux chocs
- Excellentes propriétés d'usure
- Idéal pour les applications extérieures
Considérations sur la liaison chimique
Au fil de mes années d'expérience, j'ai appris que la réussite du moulage 2K repose en grande partie sur une bonne liaison chimique :
Compatibilité des matériaux
- Alignement de la structure moléculaire
- Températures de fusion similaires
- Propriétés chimiques compatibles
Paramètres de traitement
- Contrôle de la température de fusion
- Optimisation de la pression d'injection
- Gestion du temps de refroidissement
Stratégies d'optimisation de la conception
Voici les principales stratégies que j'ai développées au cours de ma carrière :
Conception de l'interface
- Maximiser la surface de contact
- Créer des verrouillages mécaniques
- Assurer un flux de matériel adéquat
Géométrie des pièces
- Tenir compte des taux de rétrécissement
- Prévoir la dilatation thermique différentielle
- Concevoir des transitions d'épaisseur de paroi appropriées
Mesures de contrôle de la qualité
Chez PTSMAKE, nous mettons en œuvre ces contrôles de qualité essentiels :
Tests physiques
- Évaluation de la force d'adhérence
- Essais de résistance aux chocs
- Tests de résistance à l'environnement
Inspection visuelle
- Qualité de la finition de la surface
- Cohérence des couleurs
- Vérification des dimensions des pièces
Applications spécifiques à l'industrie
Les différents secteurs exigent des combinaisons de matériaux spécifiques :
Industrie automobile
- PC/ABS pour les composants intérieurs
- PA/TPE pour les garnitures extérieures
- PBT/TPU pour les pièces fonctionnelles
Électronique grand public
- ABS/TPE pour les appareils portables
- PC/ABS pour les boîtiers
- PA/TPE pour les composants de protection
Dispositifs médicaux
- PP/TPE pour les poignées ergonomiques
- PC/TPU pour les boîtiers d'équipement
- PBT/TPE pour les composants d'appareils
Grâce à ma grande expérience du moulage par injection 2K, j'ai appris qu'une sélection réussie de combinaisons de matériaux nécessite une prise en compte attentive des éléments suivants :
- Exigences en matière d'utilisation finale
- Conditions environnementales
- Contraintes de fabrication
- Considérations sur les coûts
- Conformité réglementaire
La clé d'un moulage par injection 2K réussi réside dans la compréhension non seulement des propriétés des matériaux, mais aussi de la manière dont ces matériaux interagissent au cours du processus de moulage. Chez PTSMAKE, nous avons développé une grande expertise dans l'optimisation de ces combinaisons de matériaux afin d'obtenir les meilleurs résultats possibles pour les applications spécifiques de nos clients.
Quelles sont les principales considérations en matière de conception pour le surmoulage ?
Depuis plus de 15 ans que je travaille chez PTSMAKE, j'ai vu d'innombrables projets de surmoulage échouer en raison de mauvaises considérations de conception. Un projet récent m'a appris que le succès réside dans les détails de la planification initiale de la conception.
La conception d'un surmoulage réussi exige une attention particulière aux angles de dépouille, à la cohérence de l'épaisseur du matériau et aux taux de rétraction. La clé est de créer des verrouillages mécaniques appropriés tout en assurant la compatibilité des matériaux entre le substrat et les composants du surmoulage.
Angles de dépouille et épaisseur de paroi essentiels
Après avoir travaillé sur des milliers de projets de surmoulage, j'ai appris que des angles de dépouille appropriés sont cruciaux. Je recommande un angle de dépouille minimum de 1 à 2° pour la plupart des applications, mais les géométries complexes peuvent nécessiter jusqu'à 5°. Le bon angle de dépouille garantit :
- Ejection facile des pièces du moule
- Réduction de l'usure de l'outillage
- Qualité constante des pièces
- Réduction des coûts de production
L'uniformité de l'épaisseur de la paroi est tout aussi importante. Je conseille toujours à mes clients de maintenir un rapport d'épaisseur de paroi cohérent entre le substrat et le matériau de surmoulage, généralement entre 1:1 et 1:3.
Sélection des matériaux et gestion des retraits
Voici un aperçu des combinaisons de matériaux les plus courantes et de leur taux de rétrécissement :
Matériau du substrat | Matériau de surmoulage | Taux de rétrécissement typique | Taux de compatibilité |
---|---|---|---|
ABS | TPE | 0.004-0.006 in/in | Excellent |
PC | TPU | 0.005-0.007 in/in | Très bon |
PP | TPE | 0.015-0.025 in/in | Bon |
Nylon | VPT | 0.008-0.012 in/in | Modéré |
PBT | LSR | 0,002-0,004 in/in | Excellent |
Stratégies de verrouillage mécanique
D'après mon expérience, un verrouillage mécanique réussi nécessite trois éléments clés :
- Contre-dépouilles - je les conçois généralement à une profondeur de 0,5 à 1,0 mm.
- Texturation de la surface - Utilisation de motifs d'une profondeur de 0,1 à 0,3 mm
- Caractéristiques de la queue d'aronde - Avec des angles de 15 à 30° pour une prise en main optimale
Optimisation de la liaison chimique
L'adhérence des matériaux est essentielle pour la durabilité. J'ai mis au point ce procédé pour obtenir une adhérence optimale :
Préparation de la surface
- Traitement au plasma
- Primaires chimiques si nécessaire
- Surfaces propres et exemptes de contamination
Paramètres de traitement
- Contrôle de la température à ±5°C
- Réglages corrects de la pression
- Des temps de cycle optimaux
Contraintes de conception géométrique
Lorsque je conçois des pièces surmoulées, je tiens toujours compte de ces limites géométriques :
- Rayons d'angle - Minimum 0,5 mm pour les angles internes
- Emplacement de la porte - Au moins 1,5 fois l'épaisseur du matériau par rapport aux caractéristiques critiques
- Placement du plan de joint - loin des surfaces cosmétiques
- Exigences en matière d'aération - profondeur de 0,02-0,03 mm pour une bonne évacuation de l'air
Considérations relatives à la fenêtre de traitement
Mes années d'expérience m'ont permis de constater que ces paramètres de traitement sont cruciaux :
Contrôle de la température
- Température du matériau du substrat
- Température du matériau de surmoulage
- Température du moule
Réglages de la pression
- Pression d'injection
- Pression de maintien
- Contre-pression
Mesures de contrôle de la qualité
Pour garantir une qualité constante, j'effectue les contrôles suivants :
Inspection visuelle
- Couverture complète
- Pas de vide ou d'interstice
- Qualité de la finition de la surface
Tests physiques
- Résistance à l'adhésion
- Résistance aux chocs
- Tests de résistance à l'environnement
Conseils pour l'optimisation de la conception
Voici mes stratégies éprouvées pour une conception optimale :
Analyse des flux de matières
- Utiliser un logiciel de simulation
- Identifier les problèmes potentiels
- Optimiser l'emplacement des portes
Essais de prototypes
- Valider les concepts de conception
- Propriétés mécaniques de l'essai
- Vérifier l'ajustement de l'assemblage
Considérations relatives à la production
- Accès à l'entretien des outils
- Optimisation du temps de cycle
- Fabrication rentable
Le succès de la conception du surmoulage dépend de la compréhension et de la mise en œuvre de ces considérations clés. Mon expérience chez PTSMAKE m'a appris que le fait de prêter attention à ces détails dès le début de la phase de conception permet d'éviter des problèmes coûteux au cours de la production et de garantir des pièces durables et de haute qualité qui répondent aux attentes des clients, voire les dépassent.
N'oubliez pas qu'un surmoulage réussi ne consiste pas seulement à suivre des règles de conception - il s'agit de comprendre comment ces éléments fonctionnent ensemble pour créer un produit de qualité supérieure. En examinant attentivement chaque aspect que j'ai décrit, vous serez bien équipé pour concevoir des composants surmoulés réussis qui offrent à la fois fonctionnalité et valeur.
Quelles sont les principales considérations en matière de conception pour le moulage par injection 2K ?
Vous êtes-vous déjà demandé pourquoi certains produits moulés en 2K échouent alors que d'autres réussissent ? Après plus de 15 ans d'expérience dans le domaine du moulage par injection, j'ai pu constater qu'une bonne conception peut faire ou défaire un projet.
Le moulage par injection à deux composants (2K) nécessite un examen minutieux de la compatibilité des matériaux, de la géométrie des pièces, de l'emplacement de l'injection et de la conception du moule. Le succès dépend de la compréhension de ces facteurs critiques et de la mise en œuvre de stratégies de conception appropriées dès le départ.
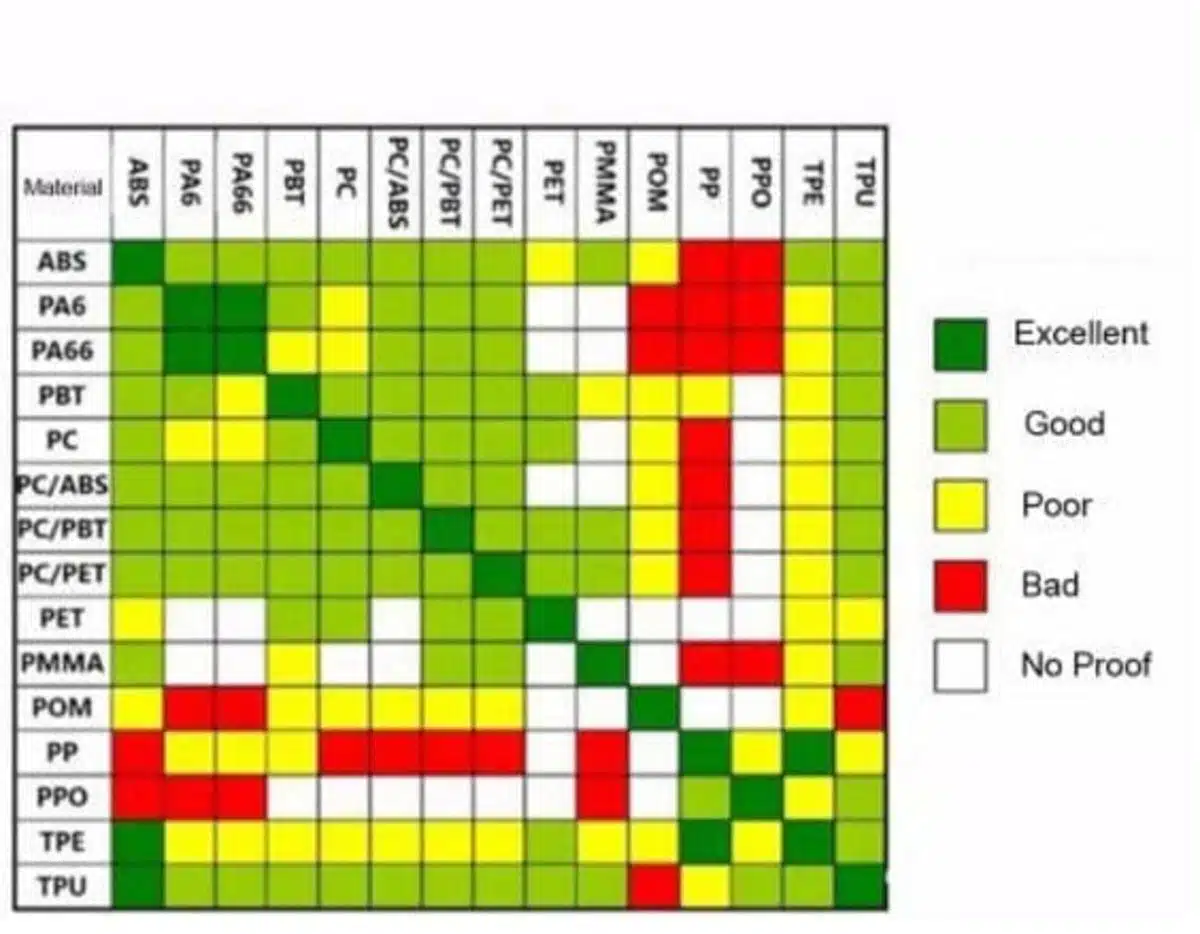
Considérations sur la compatibilité des matériaux
D'après l'expérience que j'ai acquise en travaillant sur d'innombrables projets 2K chez PTSMAKE, la sélection des matériaux est la base d'un moulage 2K réussi. Les deux matériaux doivent avoir :
- Températures de fusion compatibles
- Taux de rétrécissement similaires
- Bonnes propriétés d'adhésion
- Compatibilité chimique
Voici un tableau de compatibilité détaillé que j'ai mis au point après des années de tests :
Matériau 1 | Matériau 2 | Niveau de compatibilité | Applications courantes |
---|---|---|---|
PC | TPE | Excellent | Electronique grand public |
ABS | TPE | Très bon | Pièces détachées automobiles |
PA | TPE | Bon | Poignées d'outils |
PP | TPE | Juste | Biens de consommation |
POM | TPE | Pauvre | Non recommandé |
Lignes directrices pour la conception des dispositifs d'emboîtement
Lors de la conception d'éléments imbriqués, j'insiste toujours sur ces points clés auprès de nos clients :
- Le rapport minimum d'épaisseur de paroi entre les matériaux doit être de 1:1,5.
- Éviter les angles vifs dans les zones d'interface
- Concevoir des verrouillages mécaniques appropriés
- Prévoir un chevauchement suffisant entre les matériaux
Localisation des vannes et analyse des flux
D'après ma vaste expérience, l'emplacement correct de la porte est crucial pour la réussite du moulage 2K. Je recommande :
Emplacement de la porte du matériau primaire :
- Placer les portes en sections épaisses
- Maintenir des voies d'écoulement équilibrées
- Tenir compte de l'emplacement des lignes de soudure
Considérations matérielles secondaires :
- Assurer le remplissage complet des cavités
- Minimiser les pertes de charge
- Tenir compte des différences de viscosité des matériaux
Stratégie d'éjection des pièces
Chez PTSMAKE, nous avons élaboré des directives spécifiques pour une éjection réussie des pièces :
Les angles d'attaque :
- Matériau primaire : minimum 1,5°.
- Matériau secondaire : minimum 2°.
Considérations relatives à la texture de la surface :
- Surfaces lisses : augmenter les angles de dépouille de 1°.
- Surfaces texturées : augmentation des angles de dépouille de 2°.
Optimisation du temps de cycle
Pour obtenir des temps de cycle efficaces, je me concentre toujours sur les points suivants :
Contrôle de la température :
- Optimiser la disposition des canaux de refroidissement
- Équilibrer le refroidissement entre les matériaux
- Contrôle de la température de l'interface
Paramètres du processus :
- Ajuster les vitesses d'injection
- Contrôle des pressions de maintien
- Optimiser les temps de refroidissement
Stratégies de réduction des coûts
Sur la base de mon expérience de la gestion de centaines de projets 2K, voici des moyens efficaces de réduire les coûts :
Optimisation de la conception :
- Minimiser l'utilisation des matériaux
- Simplifier la géométrie des pièces
- Réduire le temps de cycle
Sélection des matériaux :
- Choisir des matériaux rentables
- Envisager l'utilisation du rebroyage
- Optimiser les propriétés des matériaux
Considérations relatives à la fabrication
Lorsque je conçois des produits pour le moulage par injection 2K, je tiens toujours compte de ces aspects de fabrication :
Conception du moule :
- Ventilation adéquate
- Des systèmes d'écoulement efficaces
- Remplissage équilibré
Contrôle des processus :
- Contrôle de la température
- Optimisation de la pression
- Mesures de contrôle de la qualité
Depuis plus de 15 ans que je travaille pour PTSMAKE, j'ai constaté que la réussite du moulage par injection 2K exigeait une approche globale. Chaque aspect - de la sélection des matériaux aux considérations de fabrication - joue un rôle crucial dans l'obtention de pièces de haute qualité. L'essentiel est d'aborder ces considérations de conception dès le début du processus de développement.
La validation de la conception par la simulation et le prototypage est essentielle. Nous recommandons toujours d'effectuer des analyses de flux et de tester différentes combinaisons de matériaux avant la production complète. Cette approche nous a permis d'obtenir une qualité constante tout en minimisant les coûts pour nos clients.
N'oubliez pas que le moulage par injection 2K est un processus complexe qui requiert de l'expertise et une attention particulière aux détails. En suivant ces considérations de conception et en travaillant avec des fabricants expérimentés, vous pouvez maximiser les chances de réussite du projet et obtenir des résultats optimaux.
Quel est le meilleur processus pour votre projet ?
Vous avez du mal à choisir entre le surmoulage et le moulage par injection 2K pour votre prochain projet ? Après plus de 15 ans dans la fabrication, j'ai aidé d'innombrables clients à prendre cette décision cruciale.
Le surmoulage et le moulage par injection 2K offrent tous deux des avantages uniques, mais votre choix doit dépendre de facteurs spécifiques tels que le volume de production, la complexité des pièces, la compatibilité des matériaux et le budget. Laissez-moi vous aider à prendre la bonne décision.
Considérations relatives au volume de production
D'après mon expérience avec différents clients de PTSMAKE, le volume de production est souvent le premier facteur à prendre en considération. Voici comment les deux processus se comparent :
Volume de production | Surmoulage | Moulage par injection 2K |
---|---|---|
Faible volume (<10 000 unités) | Plus rentable | Coûts initiaux plus élevés |
Volume moyen (10 000-100 000) | Efficacité modérée | Bonne efficacité |
Volume élevé (>100 000) | à forte intensité de main-d'œuvre | Le plus rentable |
Analyse de la complexité des pièces
En ce qui concerne la complexité des pièces, j'ai observé des distinctions claires entre ces processus :
Facteur de complexité | Surmoulage | Moulage par injection 2K |
---|---|---|
Complexité géométrique | Limité par la manutention manuelle | Possibilité d'une grande complexité |
Combinaisons de matériaux | Large gamme possible | Limité aux matériaux compatibles |
Détails de la surface | Excellent | Très bon |
Caractéristiques internes | Limitée | Capacités avancées |
Exigences en matière de matériaux et compatibilité
D'après mon expérience de plus de 15 ans dans le domaine de la fabrication, la sélection des matériaux joue un rôle crucial :
Aspect matériel | Surmoulage | Moulage par injection 2K |
---|---|---|
Gamme de matériaux | Une sélection plus large | Limité aux paires compatibles |
Force d'adhérence | Variable | Excellent |
Résistance chimique | Dépend des matériaux | Généralement meilleur |
Résistance à la température | Bon | Excellent |
Ventilation de la structure des coûts
Permettez-moi de vous faire part de ce que j'ai appris sur les aspects financiers de ces deux processus :
Facteur de coût | Surmoulage | Moulage par injection 2K |
---|---|---|
Outillage initial | Plus bas | Plus élevé |
Coût par pièce | Plus élevé | Plus bas |
Coûts de main-d'œuvre | Plus élevé | Plus bas |
Déchets matériels | Modéré | Minime |
Temps de production et efficacité
Depuis que je travaille pour PTSMAKE, j'ai remarqué des différences significatives dans l'efficacité de la production :
Facteur temps | Surmoulage | Moulage par injection 2K |
---|---|---|
Durée du cycle | Plus long | Plus court |
Temps de préparation | Plus court | Plus long |
Temps de changement | Modéré | Plus long |
Efficacité globale | Modéré | Haut |
Qualité et cohérence
Le contrôle de la qualité est crucial, et voici ce que j'ai observé :
Facteur de qualité | Surmoulage | Moulage par injection 2K |
---|---|---|
Cohérence des pièces | Bon | Excellent |
Taux de défectuosité | Plus élevé | Plus bas |
Force d'adhérence | Variable | Cohérent |
Finition de la surface | Excellent | Très bon |
Flexibilité de la conception
D'après l'expérience que j'ai acquise en travaillant sur différents projets :
Facteur de conception | Surmoulage | Moulage par injection 2K |
---|---|---|
Modifications de la conception | Plus flexible | Moins flexible |
Combinaisons de matériaux | Plus d'options | Options limitées |
Liberté géométrique | Modéré | Haut |
Options du prototype | Mieux | Limitée |
Impact sur l'environnement
La durabilité est de plus en plus importante :
Facteur environnemental | Surmoulage | Moulage par injection 2K |
---|---|---|
Déchets matériels | Plus d'informations | Moins |
Consommation d'énergie | Plus élevé | Plus bas |
Recyclabilité | Variable | Mieux |
Émissions des procédés | Plus élevé | Plus bas |
Prendre sa décision
Sur la base de ma vaste expérience, voici un cadre de décision simplifié :
Choisissez le surmoulage quand :
- Vous avez besoin d'une flexibilité maximale en matière de combinaison de matériaux
- Votre volume de production est plus faible
- Vous avez besoin de modifications fréquentes de la conception
- Le budget pour l'outillage initial est limité
Choisissez 2K Injection Molding quand :
- Vous avez des volumes de production élevés
- La cohérence des pièces est cruciale
- Vous avez besoin de temps de cycle plus courts
- La rentabilité à long terme est une priorité
J'ai récemment aidé un client à choisir entre ces deux procédés pour un composant d'appareil médical. Il a d'abord penché pour le surmoulage en raison des coûts initiaux moins élevés. Cependant, après avoir analysé leur volume de production annuel de 500 000 unités, nous avons déterminé que le moulage par injection 2K réduirait leur coût par pièce de 40% et améliorerait la cohérence, ce qui en fait le meilleur choix malgré des coûts d'outillage initiaux plus élevés.
N'oubliez pas qu'il n'existe pas de solution unique. Chez PTSMAKE, nous évaluons chaque projet individuellement, en tenant compte de tous ces facteurs afin de recommander le processus le mieux adapté aux besoins spécifiques de nos clients.
Tendances futures du surmoulage et du moulage par injection 2K ?
En tant qu'expert en fabrication, avec plus de 15 ans d'expérience dans le moulage par injection, j'ai vu des changements spectaculaires. Mais ce qui s'annonce va révolutionner notre façon de concevoir les processus de surmoulage et de moulage 2K.
L'avenir du surmoulage et du moulage par injection 2K s'oriente vers la fabrication intelligente, avec des capteurs intégrés, des matériaux durables et une optimisation des processus pilotée par l'IA. Ces avancées permettront des temps de production plus rapides et des conceptions plus complexes tout en réduisant l'impact sur l'environnement.
Innovation durable en matière de matériaux
D'après mon expérience à PTSMAKE, l'innovation en matière de matériaux évolue rapidement. Nous assistons à de nouveaux développements qui étaient inimaginables il y a seulement quelques années :
- Polymères biosourcés à partir de sources renouvelables
- Matériaux recyclés aux propriétés améliorées
- Polymères auto-cicatrisants pour une plus longue durée de vie des produits
- Des matériaux intelligents qui réagissent aux changements environnementaux
Notre équipe a testé avec succès plusieurs nouveaux matériaux durables, montrant des résultats prometteurs en termes de performances et d'impact sur l'environnement.
Intégration de la fabrication intelligente
L'intégration de technologies intelligentes transforme les processus de moulage traditionnels :
Technologie | Application actuelle | Potentiel futur |
---|---|---|
Capteurs IoT | Surveillance des processus | Maintenance prédictive |
Systèmes d'IA | Contrôle de la qualité | Fonctionnement autonome |
Jumeaux numériques | Optimisation de la conception | Ajustements en temps réel |
Informatique en nuage | Collecte de données | Automatisation complète des processus |
Evolution de la conception des moules
La conception des moules modernes est de plus en plus sophistiquée :
- Canaux de refroidissement conformes
- Structures à topologie optimisée
- Inserts de moules imprimés en 3D
- Systèmes de ventilation dynamique
J'ai personnellement supervisé des projets dans lesquels ces avancées ont permis de réduire les temps de cycle de 35% tout en améliorant la qualité des pièces.
Mise en œuvre de l'industrie 4.0
L'intégration des principes de l'industrie 4.0 remodèle notre approche :
- Surveillance des processus en temps réel
- Systèmes automatisés de contrôle de la qualité
- Gestion du flux de travail numérique
- Programmes de maintenance prédictive
Solutions de fabrication hybride
Chez PTSMAKE, nous explorons des combinaisons de technologies traditionnelles et nouvelles :
- Additif + moulage par injection
- Solutions d'assemblage dans le moule
- Combinaisons multi-matériaux
- Post-traitement automatisé
Capacités de conception améliorées
De nouvelles possibilités de conception apparaissent :
- Géométries complexes
- Électronique intégrée
- Propriétés variables des matériaux
- Moulage de microcaractéristiques
Innovations en matière de procédés respectueux de l'environnement
La durabilité devient un élément central des opérations de moulage :
- Systèmes à haut rendement énergétique
- Recyclage des matériaux en boucle fermée
- Méthodes de conservation de l'eau
- Stratégies de réduction des déchets
L'année dernière, notre établissement a réduit sa consommation d'énergie de 25% grâce à ces innovations.
Optimisation de la vitesse de production
Plusieurs facteurs sont à l'origine de l'accélération de la production :
Facteur | Impact | Calendrier de mise en œuvre |
---|---|---|
Optimisation du cycle grâce à l'IA | 30% plus rapide | 1 à 2 ans |
Systèmes de refroidissement avancés | Réduction 40% | 6-12 mois |
Manipulation automatisée des pièces | 50% gain d'efficacité | 3-6 mois |
Contrôle intelligent des flux de matériaux | 20% amélioration | 1 an |
Avancement du contrôle de la qualité
Le contrôle de qualité moderne évolue avec :
- Capteurs dans le moule
- Systèmes de vision par ordinateur
- Détection des défauts par l'IA
- Ajustement du processus en temps réel
Amélioration du rapport coût-efficacité
Les nouvelles technologies rendent la production plus rentable :
- Réduction des déchets de matériaux
- Réduction de la consommation d'énergie
- Diminution des coûts de main-d'œuvre
- Problèmes de qualité minimes
Nous avons vu les périodes de retour sur investissement passer de 24 mois à seulement 12 mois grâce à ces améliorations.
Adaptations spécifiques à l'industrie
Différents secteurs sont à l'origine d'innovations uniques :
- Médical : Intégration des salles blanches
- Automobile : Solutions légères
- Électronique : Blindage EMI
- Aérospatiale : Matériaux haute performance
Après avoir travaillé avec différentes industries, j'ai remarqué que chaque secteur pousse la technologie dans des directions différentes, créant ainsi un riche écosystème d'innovations.
Ces tendances sont le fruit de mes observations après plus de 15 ans dans l'industrie et de nos travaux en cours à PTSMAKE. L'avenir du surmoulage et du moulage par injection 2K est prometteur, avec des améliorations continues en termes d'efficacité, de durabilité et de capacité. La clé du succès sera de rester adaptable et d'adopter ces nouvelles technologies tout en restant concentré sur la qualité et les besoins des clients.
Je pense que la prochaine décennie apportera des changements encore plus spectaculaires, et les entreprises qui se préparent dès maintenant seront les mieux placées pour bénéficier de ces avancées. Chez PTSMAKE, nous mettons déjà en œuvre un grand nombre de ces innovations, ce qui nous permet de rester à la pointe de la technologie de fabrication.