Avez-vous du mal à trouver le matériau adéquat pour des applications exigeantes où les plastiques standard échouent ? De nombreux ingénieurs sont confrontés à des défis lorsque les composants doivent résister à des températures extrêmes, à des produits chimiques ou à des contraintes mécaniques. Les plastiques traditionnels ne tiennent tout simplement pas le coup, ce qui entraîne des défaillances fréquentes des pièces et des remplacements coûteux.
L'usinage du PEEK est le processus de découpe, de perçage et de mise en forme du matériau polyétheréthercétone (PEEK) à l'aide de machines à commande numérique. Ce thermoplastique haute performance offre une résistance exceptionnelle à la chaleur jusqu'à 480°F, une résistance chimique remarquable et une solidité comparable à celle de certains métaux.
J'ai travaillé avec d'innombrables clients qui ont opté pour l'usinage du PEEK pour leurs composants critiques. Les résultats parlent d'eux-mêmes : des pièces plus durables, de meilleures performances dans les environnements difficiles et des cycles de maintenance réduits. Si vous vous demandez si le PEEK pourrait être la solution pour votre application, continuez à lire pour découvrir les propriétés uniques et les techniques d'usinage qui rendent ce matériau si précieux dans la fabrication de précision.
Le PEEK est-il meilleur que le Delrin pour l'usinage ?
Avez-vous déjà été pris au milieu d'un dilemme de sélection de matériaux, déchiré entre le PEEK et le Delrin pour votre projet d'ingénierie critique ? Lorsque les performances sont importantes et que l'échec n'est pas envisageable, le choix du mauvais plastique peut entraîner une usure prématurée, des temps d'arrêt de l'équipement et des reconceptions coûteuses.
Alors que le PEEK offre une résistance supérieure à la température (jusqu'à 480°F), une stabilité chimique exceptionnelle et une plus grande solidité, le Delrin (POM) offre une meilleure usinabilité, une meilleure stabilité dimensionnelle et un coût inférieur. Le "meilleur" choix dépend entièrement des exigences spécifiques de votre application et de vos contraintes budgétaires.
Comprendre le PEEK et le Delrin : Différences fondamentales
Lorsque l'on compare ces deux plastiques techniques de haute performance, il est important de comprendre leur composition et leurs caractéristiques de base. Le PEEK (polyétheréthercétone) est un thermoplastique semi-cristallin doté d'une résistance exceptionnelle à la dégradation thermique, tandis que le Delrin (polyoxyméthylène ou POM) est un homopolymère d'acétal connu pour son excellente stabilité dimensionnelle.
Comparaison des propriétés des matériaux
Les propriétés physiques et mécaniques de ces matériaux ont un impact significatif sur leurs caractéristiques d'usinage et sur les performances de l'utilisation finale.
Propriété | PEEK | Delrin (POM) |
---|---|---|
Température de déviation de la chaleur | 315°F (157°C) | 257°F (125°C) |
Résistance à la traction | 14 500 psi | 10 000 psi |
Résistance chimique | Excellent (résiste à la plupart des acides et des bases) | Bon (vulnérable aux acides forts) |
Résistance à l'usure | Supérieure | Très bon |
Facteur de coût | 4-5× plus élevé que le Delrin | Modéré |
Densité | 1,32 g/cm³ | 1,41 g/cm³ |
Caractéristiques d'usinage : Comment elles se comportent sous l'outil
Mon expérience chez PTSMAKE m'a permis de constater que l'usinabilité est souvent le facteur décisif dans le choix de ces matériaux. Le Delrin s'usine généralement de manière plus prévisible que le PEEK, produisant des finitions de surface plus lisses avec moins d'efforts.
Usure de l'outil et paramètres de coupe
Le PEEK est plus abrasif pour les outils de coupe, ce qui nécessite des changements d'outils plus fréquents. Lors de l'usinage du PEEK, nous réduisons généralement les vitesses de coupe d'environ 15-20% par rapport au Delrin afin de minimiser l'accumulation de chaleur. Ce point est crucial car la faible conductivité thermique du PEEK entraîne une concentration de chaleur dans la zone de coupe, ce qui risque de provoquer déformation thermique1 s'il n'est pas géré correctement.
Le delrin, quant à lui, offre une excellente stabilité dimensionnelle pendant l'usinage et peut être coupé à des vitesses plus élevées. Il produit moins d'usure d'outil et nécessite généralement moins de techniques d'usinage spécialisées.
Considérations relatives à l'état de surface
L'un des avantages du Delrin est qu'il permet d'obtenir d'excellents états de surface avec des paramètres d'usinage standard. Le PEEK nécessite souvent des étapes de polissage supplémentaires pour obtenir une qualité de surface comparable.
Analyse coûts-avantages pour les applications d'ingénierie
La différence de coût entre ces matériaux peut être substantielle. Le PEEK coûte généralement 4 à 5 fois plus cher que le Delrin, d'où l'importance d'évaluer si ses propriétés supérieures justifient l'investissement.
Quand le PEEK justifie son prix élevé
Je recommande le PEEK pour les applications impliquant :
- Températures de fonctionnement extrêmes (supérieures à 250°F)
- Environnements chimiques agressifs
- Charge mécanique élevée à des températures élevées
- Applications médicales ou aérospatiales nécessitant une biocompatibilité ou une résistance aux flammes
Quand le Delrin est le meilleur choix
Le Delrin est plus rentable lorsque :
- Les températures de fonctionnement restent inférieures à 180°F
- L'exposition chimique est limitée aux solvants modérés
- La sensibilité aux coûts est un facteur important
- Les pièces nécessitent une excellente stabilité dimensionnelle et une grande précision d'usinage.
- Les volumes de production élevés font du coût des matériaux un facteur important
Considérations spécifiques à l'industrie
Les propriétés des matériaux ne sont pas les mêmes selon les secteurs d'activité. Dans le secteur aérospatial, où nous avons fourni de nombreux composants, la résistance à la flamme du PEEK et son rapport poids/résistance exceptionnel justifient souvent son coût plus élevé. Pour les applications automobiles, la combinaison d'un coût raisonnable et de bonnes propriétés mécaniques du Delrin l'emporte souvent.
Applications médicales et agroalimentaires
Pour les dispositifs médicaux, la biocompatibilité et la résistance à la stérilisation du PEEK le rendent inestimable malgré son coût élevé. Dans les équipements de traitement des aliments, la conformité du Delrin à la FDA et son coût inférieur en font souvent le choix préféré, à moins que des températures élevées ne soient impliquées.
Composants de machines industrielles
Dans les applications industrielles, j'ai constaté que la décision dépendait souvent des conditions d'utilisation. Les engrenages, les roulements et les pièces d'usure qui fonctionnent dans des conditions modérées donnent d'excellents résultats avec le Delrin, tandis que ceux qui sont exposés à des conditions extrêmes bénéficient des propriétés supérieures du PEEK.
Faire le bon choix pour votre application
Le choix entre le PEEK et le Delrin doit être guidé par une analyse approfondie de vos conditions de fonctionnement spécifiques. Chez PTSMAKE, nous prenons en compte :
- Température maximale de fonctionnement
- Profil d'exposition chimique
- Exigences en matière de charge mécanique
- Contraintes budgétaires
- Attentes en matière de durée de vie
En évaluant soigneusement ces facteurs par rapport aux propriétés de chaque matériau, vous pouvez prendre une décision éclairée qui concilie performance et rentabilité pour votre application spécifique.
Quelle est la différence entre l'acétal et le PEEK ?
Avez-vous déjà eu du mal à choisir entre l'acétal et le PEEK pour vos composants d'ingénierie critiques ? Lorsque la réussite d'un projet dépend de la sélection des matériaux, un mauvais choix peut entraîner des défaillances prématurées, des temps d'arrêt inattendus et des remaniements budgétaires qui auraient pu être évités grâce à une bonne connaissance des matériaux.
L'acétal (POM) et le PEEK se distinguent principalement par leurs caractéristiques de performance et leur coût. Le PEEK offre une meilleure résistance à la chaleur (480°F contre 180°F), une meilleure résistance chimique et une plus grande solidité, tandis que l'acétal offre une excellente usinabilité, une stabilité dimensionnelle et un coût nettement inférieur, ce qui le rend idéal pour les applications moins exigeantes.
Principales différences entre l'acétal et le PEEK
Il est essentiel de comprendre les différences fondamentales entre ces deux plastiques techniques pour prendre des décisions éclairées dans le cadre de vos projets. Les deux matériaux se sont imposés comme des options incontournables dans la fabrication de précision, mais ils remplissent des fonctions très différentes en raison de leurs propriétés intrinsèques.
Composition et structure des matériaux
L'acétal, communément connu sous le nom de marque Delrin (lorsqu'il est sous forme d'homopolymère) ou sous son nom chimique polyoxyméthylène (POM), présente une structure hautement cristalline avec des groupes -CH₂O- répétitifs. Cette structure lui confère une excellente stabilité dimensionnelle et une excellente usinabilité.
Le PEEK (polyétheréthercétone), quant à lui, appartient à la famille des polyaryléthercétones et contient des anneaux aromatiques reliés par des liaisons éther et cétone. Cette structure moléculaire lui confère une stabilité thermique et une résistance chimique exceptionnelles.
Comparaison des caractéristiques de performance
Les différences de performances entre ces matériaux les destinent à des applications distinctes :
Propriété | Acétal (POM) | PEEK | Meilleur pour |
---|---|---|---|
Résistance à la chaleur | 180°F (82°C) en continu | 480°F (250°C) en continu | PEEK |
Résistance chimique | Bon (sauf acides forts) | Excellent (résistant à la plupart des produits chimiques) | PEEK |
Résistance à la traction | 8 800-10 000 psi | 14 500-16 000 psi | PEEK |
Résistance à l'usure | Très bon | Excellent | PEEK |
Usinabilité | Excellent | Bonne (nécessite des techniques spécialisées) | Acétal |
Facteur de coût | Référence de base (1×) | 4-7× plus élevé que l'acétal | Acétal |
Absorption de l'humidité | 0.2-0.25% | 0.1-0.15% | PEEK |
Analyse coûts-avantages
Au cours de mes années de collaboration avec les clients de PTSMAKE, j'ai remarqué que les considérations de coût déterminent souvent le processus initial de sélection des matériaux. L'acétal est nettement plus économique que le PEEK, ce qui en fait le choix par défaut en l'absence de conditions extrêmes.
Le prix élevé du PEEK reflète ses performances supérieures. Pour déterminer si l'investissement supplémentaire est justifié, il convient de tenir compte des facteurs suivants :
- Exigences en matière de température de fonctionnement
- Profil d'exposition chimique
- Niveaux de contrainte mécanique
- Durée de vie prévue
- Coûts d'immobilisation liés à la défaillance d'un composant
Considérations relatives à l'usinage
Durée de vie de l'outil et paramètres de coupe
L'acétal est réputé pour son exceptionnelle usinabilité. Il se coupe proprement, maintient des tolérances serrées et produit d'excellents états de surface avec un minimum d'effort. Les outils en carbure standard fonctionnent bien et le matériau ne provoque pas d'usure excessive de l'outil.
Le PEEK présente davantage de difficultés lors de l'usinage. Sa résistance aux températures élevées signifie que la dissipation de la chaleur pendant l'usinage est médiocre, ce qui nécessite.. :
- Vitesses de coupe réduites (typiquement 20-30% plus lente que l'acétal)
- Changements d'outils plus fréquents
- Attention à l'accumulation de chaleur
- Techniques de refroidissement spécialisées
Chez PTSMAKE, nous avons mis au point des protocoles de gestion thermique2 pour l'usinage du PEEK afin de garantir la précision des dimensions et d'éviter la dégradation du matériau pendant le processus de coupe.
Stabilité dimensionnelle
L'acétal offre une excellente stabilité dimensionnelle après usinage, avec un gauchissement ou un relâchement des contraintes minimes. Cela le rend particulièrement utile pour les composants de précision avec des tolérances serrées.
Le PEEK présente également une bonne stabilité dimensionnelle, mais nécessite des processus de recuit plus minutieux pour soulager les contraintes internes après l'usinage. Sans un conditionnement thermique approprié, les pièces en PEEK peuvent subir de légères modifications dimensionnelles au fil du temps, en particulier dans les applications de haute précision.
Recommandations spécifiques à l'application
Automobile et transports
Dans les applications automobiles où les températures restent modérées (inférieures à 180°F), l'acétal offre souvent la meilleure valeur. Les applications les plus courantes sont les suivantes
- Composants du système d'alimentation en carburant
- Mécanismes de verrouillage des portes
- Clips et fixations pour les garnitures intérieures
- Surfaces d'appui dans les zones non critiques
Pour les zones à température élevée, telles que les composants sous le capot ou les pièces proches des systèmes d'échappement, la stabilité thermique du PEEK en fait le meilleur choix, malgré un coût plus élevé.
Médical et pharmaceutique
L'industrie médicale a adopté le PEEK pour sa biocompatibilité et sa résistance aux méthodes de stérilisation. Il est couramment utilisé dans :
- Dispositifs implantables
- Instruments chirurgicaux
- Composants d'imagerie médicale
- Matériel de laboratoire
L'acétal trouve encore des applications dans des environnements médicaux moins exigeants, tels que :
- Composants d'instruments à usage unique
- Dispositifs d'essai en laboratoire
- Boîtiers d'appareils de diagnostic
Équipement industriel
Pour les machines industrielles, le choix dépend souvent des conditions de fonctionnement :
- Environnements d'exploitation standard : L'acétal offre une excellente valeur pour les engrenages, les roulements et les surfaces d'usure dans des conditions normales.
- Environnements difficiles : Le PEEK justifie son prix élevé lorsqu'il est exposé à des températures élevées, à des produits chimiques ou à des contraintes mécaniques extrêmes.
Faire une sélection optimale
Lorsque j'aide mes clients à choisir entre l'acétal et le PEEK à PTSMAKE, je recommande une approche systématique :
- Identifier les conditions les plus exigeantes auxquelles la pièce sera confrontée (température, produits chimiques, charges).
- Déterminer si les propriétés de l'acétal sont suffisantes pour faire face à ces conditions.
- Calculer la différence de coût entre les options pour vos besoins spécifiques en volume
- Tenir compte des conséquences d'une défaillance et des coûts associés aux temps d'arrêt.
- Évaluer si les performances supérieures du PEEK justifient son prix plus élevé
N'oubliez pas que le choix des matériaux est rarement unique. Parfois, une approche hybride fonctionne mieux, en utilisant le PEEK uniquement pour les composants les plus critiques et l'acétal pour les pièces moins exigeantes au sein du même assemblage.
Quelle est la différence entre le PTFE et le PEEK ?
Vous êtes-vous déjà retrouvé perdu dans l'océan des plastiques hautes performances, ne sachant pas s'il fallait choisir le PTFE ou le PEEK pour votre application critique ? Lorsque les échéances du projet approchent et que le choix du matériau peut faire ou défaire votre conception, la pression pour faire le bon choix peut être écrasante, en particulier lorsque les deux matériaux sont accompagnés de spécifications techniques impressionnantes.
Le PTFE et le PEEK sont tous deux des thermoplastiques de haute performance présentant des différences marquées. Le PTFE offre une résistance chimique inégalée, une friction extrêmement faible (coefficient de 0,05-0,10) et fonctionne de -328°F à 500°F, mais sa résistance mécanique est médiocre. Le PEEK offre des propriétés mécaniques supérieures, une excellente résistance à l'usure et conserve son intégrité structurelle jusqu'à 480°F tout en étant plus facile à usiner.
Structure moléculaire et propriétés de base
Les différences fondamentales entre le PTFE et le PEEK commencent au niveau moléculaire, ce qui explique leurs caractéristiques de performance distinctes dans diverses applications.
Composition chimique
Le PTFE (polytétrafluoroéthylène) se caractérise par un squelette de carbone entièrement entouré d'atomes de fluor. Cette structure unique confère au PTFE une inertie chimique exceptionnelle et de faibles propriétés de frottement. Les liaisons carbone-fluor sont parmi les plus fortes de la chimie organique, ce qui rend le PTFE incroyablement résistant aux attaques chimiques.
Le PEEK (polyétheréthercétone), quant à lui, a une structure moléculaire plus complexe avec des anneaux aromatiques reliés par des liaisons éther et cétone. Ce squelette aromatique confère au PEEK son excellente résistance mécanique et sa stabilité thermique.
Analyse comparative des biens
Propriété | PTFE | PEEK | Avantage |
---|---|---|---|
Température maximale d'utilisation continue | 500°F (260°C) | 480°F (250°C) | PTFE (légèrement) |
Température minimale de fonctionnement | -328°F (-200°C) | -65°F (-54°C) | PTFE |
Coefficient de frottement | 0,05-0,10 (le plus faible de tous les solides) | 0.35-0.40 | PTFE |
Résistance à la traction | 3 000-5 000 psi | 14 000-16 000 psi | PEEK |
Résistance chimique | Supérieur (universel) | Excellent (limité par les acides forts) | PTFE |
Usinabilité | Difficile (mou, se déforme facilement) | Bon | PEEK |
Résistance à l'usure | Médiocre à modéré | Excellent | PEEK |
Propriétés électriques | Excellent isolant | Bon isolant | PTFE |
Facteur de coût | Modéré | Élevé (3 à 4 fois plus que le PTFE) | PTFE |
Différences de performances thermiques
La performance en température est souvent un facteur de décision critique dans le choix de ces matériaux.
Résistance à la chaleur et stabilité
Si les deux matériaux offrent une résistance exceptionnelle à la chaleur, ils se comportent différemment à des températures élevées. Le PTFE conserve son inertie chimique et sa faible friction jusqu'à sa température maximale, mais commence à perdre son intégrité mécanique à des températures beaucoup plus basses (environ 260°F/127°C).
Le PEEK, quant à lui, conserve sa résistance mécanique bien plus près de sa température maximale. Le PEEK est donc beaucoup plus utile dans les applications nécessitant à la fois une résistance à la chaleur et une charge mécanique.
J'ai vu de nombreuses applications pour lesquelles les clients avaient initialement choisi le PTFE sur la seule base des températures nominales, avant de découvrir que le matériau ne pouvait pas supporter les contraintes mécaniques à ces températures. La capacité du PEEK à maintenir l'intégrité structurelle à des températures élevées justifie souvent son prix plus élevé.
Performances à froid
Pour les applications cryogéniques, le PTFE présente un avantage certain. Il reste souple et fonctionnel jusqu'à -200°C (-328°F), alors que le PEEK devient de plus en plus fragile en dessous de -54°C (-65°F). Le PTFE est donc le choix évident pour l'aérospatiale, les laboratoires et d'autres environnements à très basse température.
Comparaison de la résistance mécanique
Les propriétés mécaniques de ces matériaux diffèrent considérablement, ce qui rend leur utilisation spécifique.
Intégrité structurelle sous charge
Le PEEK offre des performances mécaniques nettement supérieures, avec une résistance à la traction de 14 000 à 16 000 psi en moyenne, contre 3 000 à 5 000 psi pour le PTFE. Le PEEK convient donc aux applications porteuses où le PTFE se déformerait rapidement ou tomberait en panne.
Chez PTSMAKE, nous recommandons fréquemment le PEEK pour les composants structurels soumis à des charges mécaniques constantes, en particulier à des températures élevées. L'exceptionnelle résistance au fluage du matériau lui permet de conserver sa stabilité dimensionnelle sous une contrainte continue.
Résistance à l'usure et au frottement
Le coefficient de frottement remarquablement bas du PTFE (0,05-0,10) en fait le matériau de choix pour les applications nécessitant un frottement minimal. Toutefois, cette même propriété contribue à sa faible résistance à l'usure, car le matériau peut facilement être raclé dans les scénarios de forte usure.
Le PEEK présente une excellente résistance à l'usure tout en conservant un coefficient de frottement raisonnable (0,35-0,40). Pour les applications impliquant un mouvement continu contre d'autres surfaces, le PEEK surpasse généralement le PTFE par une marge considérable.
Nombre de nos clients obtiennent le meilleur des deux mondes en utilisant le PEEK comme matériau structurel avec un revêtement ou une doublure en PTFE mince là où une réduction de la friction est nécessaire.
Profils de résistance chimique
Les deux matériaux offrent une résistance chimique exceptionnelle, mais avec des différences importantes.
Résistance aux environnements agressifs
Le PTFE représente l'étalon-or en matière de résistance chimique, car il est pratiquement inerte face à presque tous les produits chimiques (à de rares exceptions près, comme les métaux alcalins fondus et le fluor élémentaire). Cette résistance chimique universelle rend le PTFE inestimable dans le traitement chimique, la fabrication de semi-conducteurs et les environnements de laboratoire.
Le PEEK offre une excellente résistance chimique à la plupart des substances, mais peut être attaqué par l'acide sulfurique concentré et certains autres acides forts. Pour la plupart des environnements industriels, cependant, la résistance chimique du PEEK est plus qu'adéquate.
Hydrolyse et absorption d'humidité
Le PTFE est totalement hydrophobe et n'absorbe pratiquement pas d'humidité, même après une exposition prolongée. Le PEEK, bien que très résistant à l'hydrolyse, absorbe une petite quantité d'humidité (0,1-0,3%) lorsqu'il est exposé à des environnements humides pendant de longues périodes.
Pour les applications d'eau ultra-pure ou les systèmes où la moindre contamination est inacceptable, le PTFE reste souvent le choix privilégié malgré ses limitations mécaniques.
% [Composants usinés en PEEK et PTFE pour comparaison structurelle](
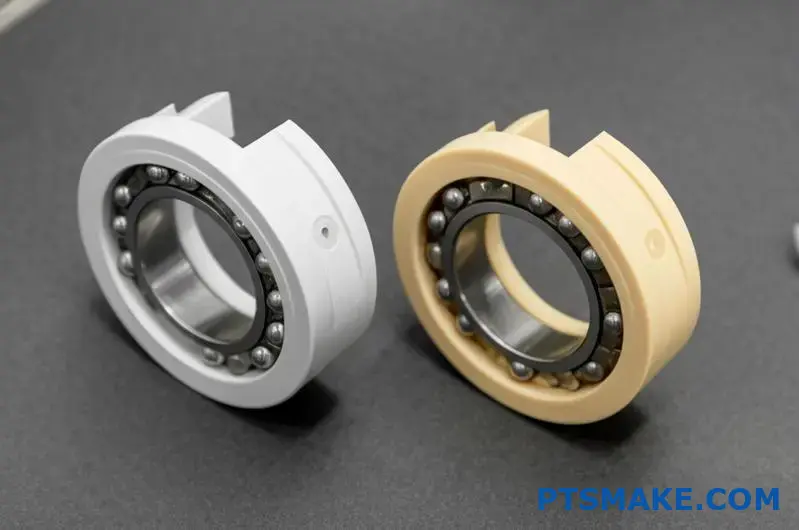
"Composants de roulements en PEEK et PTFE")
Considérations relatives à l'usinage et à la fabrication
Le usinabilité3 Les différences entre ces matériaux ont un impact significatif sur les coûts et les capacités de fabrication.
Défis et solutions en matière d'usinage
Le PTFE présente des difficultés d'usinage uniques en raison de sa souplesse et de sa tendance à s'écouler à froid. Il nécessite un outillage spécialisé, des vitesses de coupe plus lentes et une fixation minutieuse pour éviter les déformations pendant l'usinage. Un outillage tranchant est essentiel pour éviter de déchirer ou de déformer le matériau.
Le PEEK s'usine davantage comme les plastiques techniques traditionnels, bien que sa nature abrasive entraîne une usure plus rapide des outils que de nombreux autres matériaux. Lors de l'usinage du PEEK, nous utilisons généralement des outils en carbure et des techniques de refroidissement appropriées pour gérer l'accumulation de chaleur.
Compatibilité du processus de fabrication
La viscosité élevée du PTFE à l'état fondu rend impossible le moulage par injection conventionnel. Il doit donc être traité à l'aide de techniques telles que le moulage par compression, l'extrusion par bélier ou le découpage en billettes. Cela limite la complexité de la conception et augmente les coûts de fabrication pour les formes complexes.
Le PEEK peut être traité par des méthodes conventionnelles telles que le moulage par injection et l'extrusion, ce qui permet d'obtenir des géométries plus complexes et des coûts de production potentiellement plus faibles pour des volumes plus importants. Cette polyvalence de traitement donne au PEEK un avantage pour les composants complexes ou lors du passage du prototypage à la production de masse.
Analyse coûts-avantages pour différentes applications
La différence de prix significative entre ces matériaux nécessite un examen attentif de leur valeur spécifique à l'application.
Comparaison des propositions de valeur
Bien que le PEEK coûte généralement 3 à 4 fois plus cher que le PTFE, ses propriétés mécaniques supérieures et sa résistance à l'usure offrent souvent une meilleure valeur à long terme dans les applications où une défaillance mécanique serait coûteuse ou dangereuse.
Pour les applications nécessitant principalement une résistance chimique, un faible frottement ou des propriétés d'isolation électrique sans contrainte mécanique importante, le PTFE offre généralement un meilleur rapport qualité-prix malgré ses limites.
Critères de sélection spécifiques à l'industrie
Les propriétés des matériaux varient selon les secteurs d'activité :
- Traitement chimique : La résistance chimique universelle du PTFE l'emporte généralement sur ses limites mécaniques.
- Aérospatiale : Les deux matériaux trouvent des applications, le PEEK étant utilisé pour les composants structurels et le PTFE pour les joints et l'isolation électrique.
- Le médical : La biocompatibilité et la résistance structurelle du PEEK le rendent populaire pour les implants, tandis que le PTFE est préféré pour les revêtements de cathéters et d'autres applications à faible frottement.
- Semi-conducteurs : Le PTFE domine en raison de sa pureté exceptionnelle et de sa résistance aux produits chimiques agressifs.
- Automobile : La résistance à l'usure et les propriétés mécaniques du PEEK en font un matériau précieux pour les composants situés sous le capot et soumis à des contraintes mécaniques.
Quelle est la différence entre le PVDF et le PEEK ?
Avez-vous déjà été confronté au dilemme de choisir entre le PVDF et le PEEK dans le cadre d'un projet critique où le choix du matériau peut faire ou défaire votre conception ? Lorsque les plastiques standard ne suffisent pas et que vous avez besoin d'une résistance chimique ou d'une stabilité thermique exceptionnelles, la confusion entre ces deux matériaux à hautes performances peut conduire à des erreurs coûteuses ou à des performances compromises.
Le PVDF (polyfluorure de vinylidène) et le PEEK (polyétheréthercétone) diffèrent principalement par leurs caractéristiques de performance et leurs applications. Le PEEK offre une résistance thermique supérieure (480°F contre 300°F), une meilleure résistance mécanique et une résistance exceptionnelle à l'usure, tandis que le PVDF offre une excellente résistance chimique, une stabilité aux UV et un coût nettement inférieur.
Principales différences entre le PVDF et le PEEK
Lorsque l'on compare ces deux thermoplastiques techniques, la compréhension de leurs propriétés fondamentales permet de déterminer quel matériau est le mieux adapté à des applications spécifiques. Les deux matériaux sont considérés comme des options de haute performance, mais ils excellent dans des environnements et des applications différents.
Composition et structure des matériaux
Le PVDF est un fluoropolymère semi-cristallin constitué d'unités répétitives de difluorure de vinylidène. Sa structure moléculaire comprend des liaisons carbone-fluor qui lui confèrent une excellente résistance chimique, bien qu'elle ne soit pas aussi complète que celle des polymères entièrement fluorés tels que le PTFE.
Le PEEK appartient à la famille des polyaryléthercétones et présente une structure moléculaire complexe avec des anneaux aromatiques reliés par des liaisons éther et cétone. Cette structure unique confère au PEEK une stabilité thermique et une résistance mécanique exceptionnelles.
Comparaison des caractéristiques de performance
Le tableau suivant présente une comparaison détaillée des principales propriétés du PVDF et du PEEK :
Propriété | PVDF | PEEK | Matériau supérieur |
---|---|---|---|
Température maximale d'utilisation continue | 300°F (149°C) | 480°F (250°C) | PEEK |
Résistance mécanique (traction) | 5 800-7 800 psi | 14 500-16 000 psi | PEEK |
Résistance chimique | Excellent (la plupart des acides et des bases) | Très bon (limité par les acides forts) | PVDF |
Résistance aux UV | Excellent | Moyen à bon | PVDF |
Résistance à l'usure | Bon | Excellent | PEEK |
Coefficient de frottement | 0.25-0.35 | 0.35-0.40 | PVDF |
Facteur de coût | Modéré | 2 à 3 fois plus élevé que le PVDF | PVDF |
Absorption de l'humidité | 0.03-0.04% | 0.1-0.15% | PVDF |
Densité | 1,75-1,78 g/cm³ | 1,30-1,32 g/cm³ | En fonction de l'application |
Performance thermique et stabilité
Les capacités de température déterminent souvent les décisions de sélection des matériaux dans de nombreuses applications techniques.
Comparaison de la résistance thermique
Le PEEK fait preuve d'une stabilité thermique exceptionnelle, conservant ses propriétés mécaniques à des températures allant jusqu'à 250°C (480°F) pour une utilisation continue. Il est donc idéal pour les applications dans des environnements à haute température où les plastiques traditionnels ne résisteraient pas.
Le PVDF, bien qu'il soit toujours considéré comme un plastique haute température, a une température maximale d'utilisation continue plus basse d'environ 149°C (300°F). Cette plage de température est suffisante pour de nombreuses applications industrielles, mais ne suffit pas dans les environnements thermiques extrêmes.
D'après mon expérience avec les clients de PTSMAKE, ce différentiel de température devient souvent le facteur décisif lors du choix entre ces matériaux pour des applications telles que les équipements de traitement des semi-conducteurs, où les températures de traitement peuvent dépasser les capacités du PVDF.
Comportement au cyclage thermique
Les deux matériaux réagissent différemment aux cycles thermiques :
- Le PVDF présente une bonne stabilité dimensionnelle pendant les cycles thermiques, bien qu'il puisse subir une dilatation thermique plus importante que le PEEK.
- Le PEEK conserve une stabilité dimensionnelle exceptionnelle, même en cas de cycles thermiques répétés, ce qui le rend préférable pour les composants de précision qui doivent conserver des tolérances étroites à des températures variables.
Profils de résistance chimique
La résistance chimique est un autre facteur crucial qui distingue ces matériaux.
Résistance aux environnements agressifs
Le PVDF offre une excellente résistance à une large gamme de produits chimiques, notamment :
- La plupart des acides (y compris les acides chlorhydrique et sulfurique concentrés)
- Hydrocarbures aliphatiques et aromatiques
- Alcools et solvants chlorés
- Agents oxydants
Le PEEK présente une bonne résistance chimique à de nombreuses substances, mais peut être attaqué par l'acide sulfurique concentré et certains autres acides forts. Il est particulièrement résistant à l'hydrolyse et à la stérilisation à la vapeur, ce qui le rend précieux dans les applications médicales.
Considérations chimiques spécifiques à l'industrie
Différentes industries privilégient des propriétés de résistance chimique spécifiques :
- Traitement chimique : Le PVDF est souvent préféré pour sa grande résistance aux acides et aux composés chlorés.
- Semi-conducteurs : Les deux matériaux sont utilisés, le choix dépendant des produits chimiques spécifiques du processus.
- Pétrole et gaz : La combinaison des propriétés mécaniques et de la résistance chimique du PEEK en fait un matériau précieux pour les applications en fond de puits.
- Pharmaceutique : L'excellente résistance du PVDF aux agents de nettoyage et aux méthodes de stérilisation le rend populaire pour les équipements de traitement.
Propriétés mécaniques et applications structurelles
Le résistance mécanique4 Les différences entre ces matériaux ont un impact significatif sur leur aptitude à supporter des charges.
Capacités de charge
Le PEEK offre une résistance mécanique nettement plus élevée, avec des valeurs de traction allant généralement de 14 500 à 16 000 psi, contre 5 800 à 7 800 psi pour le PVDF. Le PEEK est donc supérieur pour les composants structurels qui doivent résister à des charges mécaniques importantes.
Pour les applications nécessitant à la fois une résistance chimique et une intégrité structurelle, le PEEK offre souvent le meilleur équilibre de propriétés, malgré son coût plus élevé. J'ai recommandé le PEEK pour de nombreuses applications à PTSMAKE où les composants doivent résister à la fois aux produits chimiques agressifs et aux contraintes mécaniques.
Résistance à l'usure et propriétés de frottement
Le PEEK présente une excellente résistance à l'usure, ce qui le rend idéal pour les roulements, les bagues et d'autres composants soumis à un frottement continu. Ses propriétés autolubrifiantes permettent de prolonger la durée de vie des pièces mobiles dans les environnements exigeants.
Le PVDF offre une bonne résistance à l'usure, mais pas au niveau du PEEK. Son coefficient de frottement plus faible (0,25-0,35 contre 0,35-0,40 pour le PEEK) peut être avantageux dans certaines applications de glissement à faible charge où la réduction du frottement est plus importante que la résistance maximale à l'usure.
Propriétés d'isolation électrique et thermique
Les deux matériaux présentent des caractéristiques électriques distinctes qui les rendent adaptés à différentes applications.
Propriétés diélectriques
Le PVDF est connu pour ses propriétés piézoélectriques, qui lui permettent de générer une charge électrique en réponse à une contrainte mécanique appliquée. Cette caractéristique unique rend le PVDF précieux dans les applications de capteurs.
Le PEEK offre d'excellentes propriétés d'isolation électrique sur une large plage de températures, conservant sa rigidité diélectrique même à des températures élevées. Il est donc particulièrement utile dans les applications électriques à haute température, où les plastiques standard seraient défaillants.
Conductivité thermique
Le PVDF et le PEEK ont tous deux une conductivité thermique relativement faible par rapport aux métaux, ce qui en fait de bons isolants thermiques :
- PVDF : 0,17-0,19 W/m-K
- PEEK : 0,25-0,29 W/m-K
Cette faible conductivité thermique peut être un avantage ou un inconvénient selon l'application. Pour les composants nécessitant une isolation thermique, les deux matériaux donnent de bons résultats, bien que le PVDF offre une isolation légèrement supérieure.
Considérations sur les coûts et analyse de la valeur
La différence de prix significative entre ces matériaux rend l'analyse coût-bénéfice essentielle.
Coût initial des matériaux
Le PEEK coûte généralement 2 à 3 fois plus cher que le PVDF, ce qui représente un surcoût substantiel qui doit être justifié par les exigences de performance. Cette différence de prix s'explique par le processus de fabrication plus complexe du PEEK et le coût plus élevé des matières premières.
Évaluation de la valeur du cycle de vie
Lors de l'évaluation du coût total de possession, il convient de prendre en compte plusieurs facteurs au-delà du coût initial des matériaux :
- Durée de vie prévue dans l'environnement cible
- Fréquence de remplacement et coûts d'immobilisation associés
- Exigences en matière d'installation et d'entretien
- Préoccupations en matière de sécurité et de fiabilité
Dans de nombreuses applications à haute température ou à forte charge, les performances supérieures du PEEK justifient son coût initial plus élevé par une durée de vie prolongée et une fiabilité accrue. Pour les applications relevant des capacités du PVDF, le matériau moins coûteux offre souvent une meilleure valeur globale.
Considérations relatives au traitement et à la fabrication
Les capacités et les limites de fabrication influencent également le choix des matériaux.
Différences d'usinage
Lors de l'usinage de ces matériaux à PTSMAKE, nous avons observé des différences significatives :
- Le PVDF s'usine relativement bien mais nécessite un outillage pointu et des vitesses appropriées pour éviter la fonte ou le grippage.
- Le PEEK est plus difficile à usiner en raison de son caractère abrasif et de sa mauvaise conductivité thermique, qui peut entraîner une accumulation de chaleur pendant les opérations de coupe.
Pour les composants de précision, le PEEK respecte généralement des tolérances plus strictes lors de l'usinage, mais nécessite des techniques et un outillage plus spécialisés, ce qui peut entraîner une augmentation des coûts de fabrication.
Compatibilité des méthodes de fabrication
Les deux matériaux peuvent être traités par de multiples méthodes de fabrication :
- PVDF : Moulage par injection, extrusion, moulage par compression, usinage
- PEEK : moulage par injection, extrusion, moulage par compression, usinage, impression 3D (équipement spécialisé)
Le PVDF offre un peu plus de souplesse de traitement à des températures plus basses, tandis que le PEEK nécessite des températures de traitement plus élevées, mais offre plus d'options pour des géométries complexes grâce à des techniques de fabrication avancées.
Lignes directrices de sélection spécifiques à la demande
Des industries différentes privilégient des propriétés de matériaux différentes, ce qui conduit à des préférences de matériaux variées.
Industrie des semi-conducteurs
Dans la fabrication des semi-conducteurs, les deux matériaux trouvent des applications, mais dans des domaines différents :
- PVDF : Couramment utilisé pour les systèmes d'eau ultra-pure, les composants de distribution de produits chimiques et les équipements de filtration.
- PEEK : Préféré pour les composants exposés à des températures élevées, tels que les équipements de manutention des plaquettes et les composants des chambres de traitement.
Équipement de traitement chimique
Pour les applications de traitement chimique :
- PVDF : Excellent pour les pompes, les vannes, les raccords et les réservoirs manipulant des produits chimiques corrosifs à des températures modérées.
- PEEK : mieux adapté aux composants nécessitant à la fois une résistance chimique et une capacité à supporter des températures élevées ou une résistance mécanique.
Applications médicales et pharmaceutiques
Dans les applications médicales :
- PVDF : couramment utilisé dans les membranes de filtration, les sutures et certains dispositifs implantables.
- PEEK : Préféré pour les dispositifs implantables, en particulier les applications orthopédiques, en raison de sa biocompatibilité, de sa radiotransparence et de ses propriétés mécaniques similaires à celles de l'os.
Lorsque j'aide mes clients à choisir entre le PVDF et le PEEK chez PTSMAKE, je recommande une approche systématique qui évalue d'abord les facteurs environnementaux les plus critiques (température, produits chimiques, charges mécaniques), puis prend en compte des facteurs secondaires tels que le coût, les exigences de traitement et la disponibilité.
<
Le PEEK est-il un polyéthylène ?
Vous est-il déjà arrivé d'être dérouté par l'éventail de plastiques techniques portant des noms à consonance similaire ? Lors de la sélection de matériaux pour des applications critiques, cette confusion peut conduire à des erreurs coûteuses, à des échecs de performance et à un gaspillage de ressources si vous remplacez par erreur un plastique haute performance par un autre.
Non, le PEEK (polyétheréthercétone) n'est pas un polyéthylène. Le PEEK est un polyéther aromatique dont l'ossature comporte des groupes cétoniques, ce qui donne un thermoplastique semi-cristallin présentant une résistance exceptionnelle à la chaleur (jusqu'à 480°F), une excellente résistance chimique et des propriétés mécaniques supérieures qui dépassent de loin celles des matériaux en polyéthylène.
Structure chimique et différences de classification
Lorsqu'on compare le PEEK au polyéthylène, les différences fondamentales commencent au niveau moléculaire. Ces variations structurelles expliquent pourquoi ces matériaux se comportent si différemment dans les applications pratiques.
Comparaison des squelettes moléculaires
Le PEEK présente une structure aromatique complexe avec des liaisons éther et cétone entre les anneaux de benzène. Cette architecture moléculaire confère au PEEK une stabilité thermique et une résistance mécanique exceptionnelles. Les anneaux aromatiques créent la rigidité, tandis que les liaisons éther apportent une certaine flexibilité.
Le polyéthylène, en revanche, possède l'une des structures polymères les plus simples qui soient : une simple chaîne linéaire d'atomes de carbone à laquelle sont attachés des atomes d'hydrogène. Cette structure simple existe sous différentes formes (PEHD, PEBD, UHMWPE), mais toutes sont dépourvues des composants aromatiques et des groupes fonctionnels qui confèrent au PEEK ses propriétés exceptionnelles.
Cette différence structurelle fondamentale signifie que le PEEK appartient à une famille de polymères entièrement différente de celle du polyéthylène. Alors que le polyéthylène est classé parmi les polyoléfines, le PEEK appartient à la famille des polyaryléthercétones (PAEK), des thermoplastiques de haute performance.
Principales différences entre les propriétés
Les différences de structure moléculaire se traduisent par des variations spectaculaires des performances :
Propriété | PEEK | Polyéthylène (PEHD) | Facteur de différence |
---|---|---|---|
Température maximale d'utilisation continue | 480°F (250°C) | 180°F (82°C) | Le PEEK est 2,7 fois plus élevé |
Résistance à la traction | 14 500 psi | 4 500 psi | Le PEEK est 3,2 fois plus résistant |
Résistance chimique | Excellent (résiste à la plupart des produits chimiques) | Bon (vulnérable aux solvants aromatiques) | Le PEEK offre une plus grande résistance |
Coût | Haut | Faible | Le PEEK coûte 15 à 20 fois plus cher |
Densité | 1,32 g/cm³ | 0,95 g/cm³ | Le PEEK est plus dense de 39% |
Dureté (Shore D) | 85-90 | 60-70 | Le PEEK est nettement plus dur |
Différences dans le processus de fabrication
Les méthodes de production du PEEK et du polyéthylène reflètent leurs différentes structures moléculaires et caractéristiques de performance.
Processus de production du PEEK
Le PEEK est fabriqué par un processus complexe de polymérisation par substitution aromatique nucléophile. Ce processus nécessite un contrôle précis de la température et des catalyseurs spécialisés. Les monomères sont nettement plus chers que l'éthylène, ce qui explique le coût plus élevé du PEEK.
Chez PTSMAKE, lorsque nous usinons des composants en PEEK, nous devons tenir compte des propriétés uniques de ce matériau - sa faible conductivité thermique signifie que la gestion de la chaleur pendant l'usinage est essentielle pour éviter une dégradation thermique localisée.
Fabrication de polyéthylène
Le polyéthylène est produit par polymérisation par addition de l'éthylène à l'aide de divers catalyseurs en fonction de la densité et de la ramification souhaitées. Ce processus relativement simple peut être réalisé à des températures et des pressions plus basses que la production de PEEK, en particulier pour les variétés à faible densité.
Performances dans les environnements extrêmes
Performance à haute température
L'une des différences les plus importantes entre ces matériaux est leur stabilité thermique :
- Le PEEK conserve ses propriétés mécaniques jusqu'à 250°C (480°F) en utilisation continue et peut supporter de courtes expositions à des températures encore plus élevées.
- Le polyéthylène commence à se ramollir vers 82°C (180°F) et perd la majeure partie de sa résistance mécanique bien en dessous de cette température.
J'ai vu de nombreuses applications pour lesquelles les clients avaient initialement choisi le polyéthylène pour des raisons de coût, mais qui se sont soldées par une défaillance rapide lorsque les températures de fonctionnement ont dépassé les prévisions. Dans une application aérospatiale, un client a remplacé le polyéthylène par le PEEK pour un composant situé à proximité d'une source de chaleur, ce qui a permis de prolonger sa durée de vie de plusieurs mois à plusieurs années, malgré le coût initial plus élevé du matériau.
Comparaison de la résistance chimique
Bien que les deux matériaux offrent une bonne résistance chimique, le PEEK offre une protection plus large contre les produits chimiques agressifs :
- Le PEEK résiste à la plupart des acides, des bases, des hydrocarbures et des solvants organiques.
- Le polyéthylène présente une bonne résistance aux acides et aux bases, mais peut être attaqué par les hydrocarbures aromatiques et certains agents oxydants.
Cette différence devient critique dans les équipements de traitement chimique, la fabrication de semi-conducteurs et les applications médicales où l'exposition à de multiples produits chimiques est fréquente.
Adéquation de l'application
Applications aérospatiales et de défense
Dans les applications aérospatiales, la combinaison de la légèreté, de la résistance à la flamme et de la stabilité thermique du PEEK en fait un matériau précieux pour des composants tels que.. :
- Composants intérieurs nécessitant une résistance aux flammes
- Connecteurs et isolateurs électriques
- Composants structurels dans les zones à haute température
- Composants du système d'alimentation en carburant nécessitant une résistance chimique
Le polyéthylène répond rarement aux exigences des applications aérospatiales en raison de sa stabilité thermique et de ses propriétés mécaniques limitées.
Utilisations médicales et de soins de santé
Les profils de biocompatibilité de ces matériaux diffèrent également de manière significative :
- Le PEEK est biocompatible et utilisé dans les dispositifs implantables, les instruments chirurgicaux et les équipements médicaux nécessitant une stérilisation.
- Le polyéthylène de qualité médicale (principalement l'UHMWPE) est utilisé dans certains implants tels que les articulations artificielles, mais il n'offre pas la résistance à la température du PEEK pour la stérilisation répétée à la vapeur.
Composants d'équipements industriels
Pour les machines industrielles, le choix entre ces matériaux dépend généralement des conditions de fonctionnement :
- Le PEEK excelle dans les environnements à haute température, les applications nécessitant une excellente résistance à l'usure ou l'exposition à des produits chimiques agressifs.
- Le polyéthylène offre des performances adéquates dans les applications à température ambiante avec des exigences mécaniques modérées et est souvent choisi pour son faible coût et sa facilité de traitement.
Considérations sur les coûts et les avantages
La différence de prix entre ces matériaux est substantielle - le PEEK coûte généralement 15 à 20 fois plus cher que le polyéthylène haute densité. Cette différence de coût significative signifie que le choix du matériau doit être basé sur une analyse approfondie :
- Plage de température de fonctionnement requise
- Profil d'exposition chimique
- Exigences en matière de charge mécanique
- Durée de vie prévue
- Conséquences d'un échec
Pour les applications qui se situent dans la gamme des capacités du polyéthylène, son coût inférieur en fait un choix économique. Cependant, lorsque les exigences de performance dépassent les limites du polyéthylène, les propriétés supérieures du PEEK justifient aisément son prix supérieur par une durée de vie prolongée, une fiabilité améliorée et des coûts de maintenance réduits.
Différences d'usinage et de traitement
Chez PTSMAKE, nous avons constaté des différences significatives dans l'usinage de ces matériaux :
- Le PEEK nécessite des paramètres de coupe spécifiques en raison de son comportement thermique5 pendant l'usinage, mais il maintient des tolérances serrées et produit d'excellents états de surface.
- Le polyéthylène est plus facile à usiner, mais il a tendance à se déformer sous l'effet des forces de coupe, ce qui rend les tolérances serrées plus difficiles à respecter.
Il est essentiel de comprendre ces différences de traitement lors de la conception de composants en vue de leur fabrication et de leur précision.
Quels sont les inconvénients et les avantages du PEEK ?
Avez-vous déjà eu du mal à décider si le PEEK valait son prix élevé pour votre application critique ? Lorsque la réussite d'un projet dépend de la sélection des matériaux, le choix entre des plastiques hautes performances coûteux et des alternatives plus économiques peut s'avérer difficile et avoir des conséquences réelles sur la fiabilité et la longévité.
Le PEEK offre des avantages exceptionnels, notamment une remarquable résistance à la chaleur (jusqu'à 480°F), une résistance chimique exceptionnelle, une excellente résistance mécanique et des propriétés d'usure supérieures. Toutefois, ces avantages s'accompagnent d'inconvénients importants, notamment un coût élevé (5 à 10 fois supérieur à celui des plastiques techniques standard), une usinabilité difficile, des options de couleur limitées et une faible résistance aux UV.
Comprendre les propriétés exceptionnelles du PEEK
Le PEEK (polyétheréthercétone) se distingue des plastiques techniques par sa combinaison unique de propriétés qui le rendent adapté aux applications les plus exigeantes. Ayant spécifié des matériaux pour d'innombrables composants de précision, j'ai vu de mes propres yeux comment les propriétés du PEEK se traduisent par des avantages en termes de performances dans le monde réel.
Avantages de la performance thermique
L'une des caractéristiques les plus impressionnantes du PEEK est sa stabilité thermique. Ce matériau conserve ses propriétés mécaniques à des températures qui provoqueraient une défaillance catastrophique de la plupart des plastiques.
Caractéristiques de température | PEEK Performance | Comparaison avec les plastiques standard |
---|---|---|
Température de service continu | Jusqu'à 250°C (480°F) | 2 à 3 fois plus élevé que la plupart des plastiques techniques |
Température de transition du verre | 289°F (143°C) | Maintien de la rigidité à des températures plus élevées |
Point de fusion | 649°F (343°C) | Permet la stérilisation à la vapeur |
Conductivité thermique | 0,25 W/m-K | Meilleure dissipation de la chaleur que de nombreux plastiques |
Cette résistance thermique exceptionnelle permet d'utiliser le PEEK dans des applications proches de sources de chaleur où les plastiques standard se déformeraient ou se dégraderaient rapidement. J'ai aidé de nombreux clients à remplacer des composants défectueux fabriqués à partir de matériaux de moindre qualité par des pièces en PEEK qui continuent à fonctionner parfaitement malgré des environnements thermiques difficiles.
Résistance aux produits chimiques Avantages
Le profil de résistance chimique du PEEK est presque aussi impressionnant que ses propriétés thermiques. Le matériau présente une excellente résistance aux :
- Hydrocarbures et solvants organiques
- La plupart des acides et des bases (à l'exception de l'acide sulfurique concentré)
- Vapeur et eau chaude
- Fluides et carburants automobiles
- Procédés de stérilisation médicale
Cette large résistance chimique rend le PEEK particulièrement précieux dans les environnements où l'on s'attend à une exposition à de multiples substances agressives. Dans l'industrie des semi-conducteurs, par exemple, les composants en PEEK peuvent résister aux produits chimiques agressifs utilisés dans le traitement des plaquettes tout en conservant leur stabilité dimensionnelle.
Avantages des propriétés mécaniques
La résistance mécanique du PEEK le distingue de la plupart des autres thermoplastiques :
- Résistance à la traction de 14 500 psi (comparable à certains métaux)
- Excellente résistance à la fatigue
- Résistance aux chocs et ténacité exceptionnelles
- Résistance supérieure à l'usure
- Faible coefficient de frottement
Ces propriétés font que le PEEK convient à des applications structurelles où la plupart des plastiques échoueraient. J'ai spécifié le PEEK pour des engrenages, des roulements et d'autres composants à forte usure qui fonctionnent sous une contrainte mécanique importante, remplaçant souvent des pièces métalliques par des alternatives PEEK plus légères qui offrent des avantages supplémentaires tels que la résistance à la corrosion et la réduction du bruit.
Les principaux inconvénients du PEEK
Malgré ses performances impressionnantes, le PEEK présente plusieurs inconvénients importants qui doivent être soigneusement pris en compte lors de la sélection du matériau.
Contraintes de coût
L'inconvénient le plus évident du PEEK est son coût. Chez PTSMAKE, nous devons souvent aider les clients à comprendre le surcoût du PEEK par rapport à d'autres plastiques techniques :
- Le PEEK coûte généralement 5 à 10 fois plus cher que les plastiques techniques tels que le nylon ou l'acétal.
- Les coûts des matériaux pour les pièces en PEEK peuvent être 20-30% plus élevés que ceux des composants métalliques équivalents.
- Le prix élevé des matières premières a un impact significatif sur l'économie des petites pièces.
Ce facteur de coût oblige souvent les ingénieurs à réserver le PEEK aux applications les plus critiques où ses propriétés uniques sont absolument nécessaires. Dans de nombreux cas, nous recommandons des alternatives plus économiques pour les composants non critiques d'un assemblage.
Défis en matière de fabrication
Le PEEK présente plusieurs difficultés de fabrication qui peuvent accroître la complexité et le coût de la production :
Difficultés d'usinage: La résistance thermique élevée du PEEK se traduit par une mauvaise conductivité thermique, ce qui entraîne une accumulation de chaleur pendant les opérations d'usinage. Cela nécessite des vitesses de coupe plus lentes, des changements d'outils fréquents et des stratégies de refroidissement minutieuses.
Exigences en matière de température de traitement: Avec un point de fusion de 343°C (649°F), le PEEK nécessite un équipement spécialisé à haute température pour le moulage par injection et l'extrusion.
Fenêtre de traitement limitée: La différence entre la température de fusion du PEEK et le début de la dégradation est relativement étroite, ce qui pose des problèmes lors du traitement.
Rétrécissement du moule: Le PEEK présente un retrait important (environ 1-1,3%) pendant le refroidissement, ce qui nécessite une conception précise du moule pour obtenir des tolérances serrées.
Chez PTSMAKE, nous avons développé des protocoles d'usinage spécialisés pour le PEEK afin de relever ces défis, mais ils augmentent inévitablement le coût global et la complexité de la fabrication des composants en PEEK.
Limites de l'application
Malgré ses propriétés impressionnantes, le PEEK présente des limites qui le rendent inadapté à certaines applications :
- Faible résistance aux UV: Sans additifs, le PEEK se dégrade lorsqu'il est exposé à une lumière UV prolongée, ce qui limite son utilisation dans les applications extérieures.
- Options de couleurs limitées: En raison de sa couleur naturelle ambre/brun et des températures de traitement élevées, le PEEK est difficile à colorer de manière cohérente.
- Limites électriques: Bien qu'il soit un bon isolant, le PEEK n'est pas idéal pour les applications électriques à haute fréquence par rapport aux polymères électriques spécialisés.
- Difficultés de liaison: La résistance chimique du PEEK rend le collage difficile et nécessite souvent des traitements de surface spéciaux.
Analyse coûts-avantages : Quand le PEEK en vaut-il la peine ?
Compte tenu de l'important surcoût du PEEK, il est essentiel de procéder à une analyse coûts-avantages approfondie avant de spécifier ce matériau. D'après mon expérience, le PEEK offre la meilleure valeur dans les scénarios suivants :
Scénarios dans lesquels PEEK excelle
Environnements à haute température: Lorsque les températures de fonctionnement dépassent 149°C (300°F), le PEEK est souvent la seule option plastique viable, ce qui justifie son coût élevé.
Milieux chimiquement agressifs: Dans les applications exposées à de multiples produits chimiques ou à des substances particulièrement agressives, la grande résistance chimique du PEEK permet d'éviter les remplacements fréquents requis par des matériaux de moindre qualité.
Applications d'usure critique: Pour les composants soumis à un frottement et à une usure constants dans les systèmes critiques, la résistance exceptionnelle à l'usure et le faible frottement du PEEK permettent d'allonger considérablement les intervalles de service.
Exigences en matière de réduction du poids: Lorsqu'il s'agit de remplacer des composants métalliques dans des applications aérospatiales ou de haute performance, le rapport résistance/poids du PEEK peut offrir des avantages en termes de performances qui justifient son coût.
Applications d'implants médicaux: La biocompatibilité et la stabilité chimique du PEEK en font un matériau idéal pour les dispositifs implantables à long terme pour lesquels une défaillance du matériau n'est pas envisageable.
Comparaison des matériaux alternatifs
Pour les applications qui ne requièrent pas spécifiquement les propriétés extrêmes du PEEK, plusieurs alternatives peuvent offrir des performances suffisantes à moindre coût :
Matériau | L'avantage comparatif | Coût par rapport au PEEK | Limitation de la clé |
---|---|---|---|
PPS (sulfure de polyphénylène) | Bonne résistance à la chaleur (400°F) | 40-60% inférieur | Moins résistant aux produits chimiques |
PTFE (Polytétrafluoroéthylène) | Résistance chimique supérieure | 30-50% inférieur | Faible résistance mécanique |
PEI (polyétherimide) | Bonne résistance à la chaleur, transparence | 30-40% inférieur | Moins résistant à l'usure |
PAI (polyamide-imide) | Haute résistance, bonne résistance à l'usure | 10-20% inférieur | Plus difficile à traiter |
Acétal (POM) | Excellente usinabilité, faible coût | 80-90% inférieur | Résistance limitée à la température |
Considérations spécifiques à l'industrie
Différentes industries donnent la priorité à différents aspects du profil de propriété du PEEK :
Aérospatiale et défense
Dans les applications aérospatiales, la combinaison du PEEK avec la légèreté, la résistance à la flamme (avec des additifs) et la stabilité thermique justifie son prix élevé pour des composants tels que :
- Bagues et roulements dans les systèmes de contrôle
- Connecteurs et isolateurs électriques
- Composants structurels dans les zones à haute température
- Composants du système d'alimentation en carburant nécessitant une résistance chimique
Médecine et soins de santé
L'industrie médicale apprécie le PEEK pour ses qualités :
- Biocompatibilité (qualité de l'implant)
- Résistance à la stérilisation répétée
- Radiolucidité (n'interfère pas avec les rayons X)
- Propriétés mécaniques similaires à celles de l'os (lorsqu'elles sont renforcées)
Ces propriétés font du PEEK un matériau idéal pour les dispositifs implantables et les instruments chirurgicaux, malgré son coût élevé.
Équipement industriel
Pour les applications industrielles, la décision d'utiliser le PEEK dépend généralement de la sévérité des conditions de fonctionnement :
- Les environnements extrêmes (températures élevées, exposition aux produits chimiques) justifient souvent l'utilisation du PEEK
- Les applications où les temps d'arrêt sont extrêmement coûteux bénéficient de la fiabilité du PEEK.
- Les composants de haute précision bénéficient de la stabilité dimensionnelle du PEEK
Chez PTSMAKE, nous aidons nos clients à tenir compte de ces considérations pour déterminer si les performances supérieures du PEEK justifient son prix élevé pour les besoins de leurs applications spécifiques.
Je produirai le contenu du chapitre 7 de l'article "Pourquoi le PEEK est-il si cher ?" conformément à vos exigences.
Pourquoi le PEEK est-il si cher ?
Avez-vous déjà fait l'expérience du choc des étiquettes lorsque vous avez demandé un devis pour des composants en PEEK ? Lorsque les ingénieurs découvrent pour la première fois le prix de ce plastique haute performance, ils sont nombreux à se demander si un matériau peut justifier un tel surcoût, surtout si on le compare à des plastiques techniques plus courants qui semblent offrir des performances décentes pour une fraction du prix.
Le coût élevé du PEEK s'explique par la complexité de son processus de fabrication, le coût élevé des matières premières, les exigences en matière d'équipement spécialisé et les volumes de production relativement faibles. Le processus de polymérisation complexe exige des conditions précises, tandis que la nature exclusive de la technologie de production et le statut du PEEK en tant que matériau de spécialité augmentent encore son prix sur le marché.
Le processus de fabrication complexe du PEEK
Pour comprendre pourquoi le PEEK atteint un tel prix, il faut d'abord examiner son processus de fabrication. Contrairement aux polymères plus simples, la production du PEEK implique une chimie sophistiquée et des conditions de traitement précises qui ont un impact significatif sur le coût final.
Coût et rareté des matières premières
Les monomères utilisés pour produire le PEEK sont eux-mêmes des produits chimiques spécialisés coûteux. Les principaux ingrédients sont les suivants :
- Éther diphénylique
- 4,4′-difluorobenzophénone
- Carbonate de potassium
- Diphényl sulfone (comme solvant)
Ces précurseurs nécessitent de multiples étapes de raffinage pour atteindre la pureté nécessaire à la synthèse du PEEK, ce qui ajoute des couches de coûts avant même que la polymérisation ne commence. En outre, certains de ces produits chimiques ont une capacité de production limitée au niveau mondial, ce qui crée des contraintes d'approvisionnement qui font grimper les prix.
Chez PTSMAKE, lorsque nous achetons du PEEK pour des projets d'usinage, nous ne payons pas seulement pour le polymère lui-même, mais aussi pour toute la chaîne de valeur des produits chimiques spécialisés qui ont servi à sa création.
Complexité du processus de polymérisation
La synthèse du PEEK implique un processus sophistiqué de polymérisation par substitution aromatique nucléophile. Cette réaction doit se dérouler dans des conditions précisément contrôlées :
- Températures comprises entre 300 et 400°C (572-752°F)
- Atmosphère inerte pour éviter l'oxydation
- Récipients sous pression spécialisés
- Temps de réaction prolongé (souvent de 3 à 5 heures)
- Une gestion attentive des catalyseurs
Chacune de ces exigences augmente la complexité et le coût de fabrication. La réaction doit être soigneusement contrôlée tout au long du processus afin de garantir une distribution correcte du poids moléculaire et de la cristallinité, ce qui affecte directement les propriétés de performance du matériau.
Échelle de production limitée et dynamique du marché
Le statut du PEEK en tant que matériau de spécialité a un impact significatif sur les coûts de production et les prix du marché.
Technologie exclusive et protection des brevets
La technologie originale de fabrication du PEEK a été développée et brevetée par Victrex (anciennement ICI) dans les années 1970. Aujourd'hui encore, la technologie de production reste largement propriétaire et protégée par divers brevets. Cette concurrence limitée dans les méthodes de fabrication a permis de maintenir des prix plus élevés que ceux des plastiques de base.
Bien qu'il existe aujourd'hui plusieurs fabricants au niveau mondial (notamment Victrex, Solvay et Evonik), chacun d'entre eux utilise des procédés propriétaires dont la mise au point a nécessité d'énormes investissements en R&D. Ces coûts de développement doivent être récupérés par le biais du prix des matériaux. Ces coûts de développement doivent être récupérés par le biais du prix des matériaux.
Économie des volumes de production
Contrairement aux matières plastiques de base produites en millions de tonnes par an, le PEEK est fabriqué en volumes relativement faibles :
Type de plastique | Production annuelle mondiale | Facteur de coût relatif |
---|---|---|
Polyéthylène (PE) | ~100 millions de tonnes | 1× (ligne de base) |
Nylon (PA) | ~8 millions de tonnes | 2-3× |
Polycarbonate (PC) | ~4,5 millions de tonnes | 3-4× |
PEEK | <10 000 tonnes | 30-50× |
Ce volume de production limité signifie que les fabricants ne peuvent pas réaliser les économies d'échelle qui font baisser les coûts des plastiques courants. Les coûts fixes tels que l'entretien des installations, le contrôle de la qualité et la recherche et le développement sont répartis sur un nombre réduit de kilogrammes de produit, ce qui augmente le coût unitaire.
Exigences en matière d'équipement et de traitement
Les installations de production du PEEK nécessitent des équipements spécialisés capables de supporter les températures et les pressions extrêmes nécessaires à la polymérisation, au compoundage et au traitement :
- Réacteurs à haute température avec systèmes de contrôle précis
- Équipements spécialisés d'extrusion et de granulation
- Systèmes de filtration et de purification avancés
- Des installations complètes de contrôle de la qualité et d'essai
Ces investissements sont considérables et contribuent de manière significative au coût final du matériau. Lorsque nous usinons des pièces en PEEK chez PTSMAKE, nous héritons de ces coûts de fabrication en amont dans le prix de la matière première.
Défis en matière de traitement et d'usinage
Une fois produit, le PEEK présente des défis supplémentaires en matière de traitement et d'usinage qui contribuent à son coût élevé dans les composants finis.
Températures de traitement élevées
Avec un point de fusion d'environ 343°C (649°F), le PEEK nécessite un équipement de traitement spécialisé :
- Machines de moulage par injection à haute température
- Moules avec systèmes spéciaux de gestion de la chaleur
- Éléments chauffants et régulateurs plus coûteux
- Systèmes de sécurité renforcés pour la manipulation de matériaux à haute température
Ces exigences signifient que moins de fabricants sont équipés pour traiter le PEEK, ce qui limite la concurrence et maintient les coûts de traitement à un niveau plus élevé.
Considérations relatives à l'usinage et à l'usure des outils
Lors de l'usinage du PEEK à PTSMAKE, nous rencontrons plusieurs facteurs qui contribuent à augmenter les coûts de production :
Usure de l'outil : Le PEEK provoque une usure des outils nettement plus importante que les plastiques standard, ce qui nécessite un remplacement plus fréquent des outils ou l'utilisation d'un outillage de qualité supérieure.
Gestion de la chaleur : La faible conductivité thermique du PEEK signifie que la chaleur s'accumule pendant l'usinage, ce qui nécessite des vitesses de coupe plus lentes et des techniques de refroidissement spéciales.
Expertise spécialisée : L'usinage correct du PEEK nécessite de l'expérience et des connaissances afin d'éviter la dégradation du matériau et d'obtenir des tolérances serrées.
Exigences en matière de post-traitement : De nombreuses applications du PEEK nécessitent des étapes de traitement supplémentaires, comme le recuit, afin de réduire les contraintes internes et de garantir la stabilité dimensionnelle.
Chacun de ces facteurs augmente le coût total de production des composants finis en PEEK au-delà du prix de la matière première.
Coûts du contrôle de la qualité et de la certification
En tant que matériau haute performance souvent utilisé dans des applications critiques, le PEEK nécessite un contrôle de qualité rigoureux tout au long de sa production et de son traitement.
Exigences strictes en matière de tests
Chaque lot de PEEK est généralement soumis à des tests approfondis pour vérifier :
- Distribution du poids moléculaire
- Pourcentage de cristallinité
- Propriétés thermiques (transition vitreuse et points de fusion)
- Propriétés mécaniques (résistance à la traction, module, élongation)
- Pureté et niveaux de contamination
Ces tests nécessitent un équipement spécialisé et un personnel qualifié, ce qui ajoute des coûts d'assurance qualité importants au prix du produit final.
Certifications industrielles et traçabilité
De nombreuses applications du PEEK dans les secteurs de l'aérospatiale, de la médecine et des semi-conducteurs exigent une traçabilité complète des matériaux et le respect de normes spécifiques à l'industrie :
- Certifications aérospatiales (AS9100, NORSOK)
- Normes relatives aux dispositifs médicaux (ISO 13485, USP Class VI)
- Certifications de l'industrie nucléaire (NQSA-1)
- Exigences de l'industrie des semi-conducteurs (haute pureté)
Le maintien de ces certifications nécessite une documentation détaillée, des audits réguliers et parfois des installations de production ou des équipements distincts, ce qui contribue à augmenter les coûts.
Comparaison du PEEK avec d'autres matériaux
Pour comprendre le prix du PEEK dans son contexte, il est utile de le comparer à d'autres matériaux en termes de coût et de performance.
Analyse coût-performance
Le PEEK coûte généralement 5 à 10 fois plus cher que les plastiques techniques standard et peut même être plus cher que certains métaux spéciaux en termes de volume. Toutefois, ses performances dans les environnements extrêmes justifient souvent ce surcoût :
Propriété | PEEK | Standard Engineering Plastics | Métaux de première qualité |
---|---|---|---|
Température d'utilisation continue | Jusqu'à 250°C (480°F) | 80-170°C (176-338°F) | Généralement illimité |
Résistance chimique | Excellent | Variable (souvent limité) | Souvent médiocre (corrosion) |
Force spécifique | Très élevé | Modéré | Haut |
Coût des matières premières | Très élevé | Faible à modéré | Modéré à élevé |
Coût de la transformation | Haut | Faible à modéré | Haut |
Valeur à vie | Excellent | Limité dans des conditions difficiles | Bon mais avec des problèmes de corrosion |
Chez PTSMAKE, nous aidons souvent nos clients à évaluer ces compromis afin de déterminer si le prix élevé du PEEK est justifié par ses avantages en termes de performances dans leur application spécifique.
Le PEEK vaut-il le prix fort ?
La question de savoir si le coût élevé du PEEK est justifié dépend entièrement des exigences de l'application.
Applications où le PEEK apporte une valeur ajoutée malgré le coût
Malgré son prix élevé, le PEEK offre un excellent rapport qualité-prix dans les applications où il est utilisé :
- Environnements d'exploitation extrêmes là où d'autres matériaux s'abîmeraient rapidement
- Systèmes à poids critique où le rapport poids/résistance du PEEK offre des avantages
- Équipements sensibles à la maintenance lorsque le coût des temps d'arrêt dépasse de loin les coûts des matériaux
- Environnements corrosifs où les métaux se dégraderaient rapidement
- Implants médicaux lorsque la biocompatibilité et la stabilité à long terme sont essentielles
Dans ces scénarios, les avantages du PEEK en termes de performances se traduisent directement par des coûts inférieurs pendant toute la durée de vie du produit, malgré un investissement initial plus élevé.
Stratégies de réduction des coûts pour les composants en PEEK
Pour les projets nécessitant les performances de PEEK mais limités par le budget, il convient d'envisager les approches suivantes :
- Modèles hybrides utiliser le PEEK uniquement pour les composants critiques
- Techniques d'usinage optimisées réduire les déchets de matériaux
- Traitement de la forme des filets minimiser la consommation de matériaux
- Optimisation de la conception réduire le volume global des matériaux
- Grades non pourvus lorsque les renforts ne sont pas nécessaires à la performance
Chez PTSMAKE, nous avons aidé de nombreux clients à mettre en œuvre ces stratégies pour bénéficier des avantages du PEEK tout en gérant efficacement les coûts.
Comment optimiser l'usinage du PEEK pour une production rentable ?
Vous êtes-vous déjà demandé s'il existait un moyen d'exploiter les propriétés exceptionnelles du PEEK sans grever le budget de votre projet ? Lorsque vous travaillez avec l'un des plastiques techniques les plus chers du marché, l'optimisation de votre approche de l'usinage n'est pas seulement une question d'efficacité - elle peut faire la différence entre un projet rentable et un projet qui perd de l'argent en raison d'un gaspillage excessif de matériaux et d'un temps d'usinage inutile.
L'optimisation de l'usinage du PEEK pour une production rentable nécessite l'utilisation d'outils de coupe appropriés (en carbure ou revêtus de diamant), le maintien de vitesses et d'avances appropriées (généralement plus lentes que les plastiques standard), la mise en œuvre de stratégies de refroidissement efficaces, la minimisation du gaspillage de matériau grâce à une conception proche de la forme nette et la planification minutieuse des trajectoires d'outils afin de réduire les temps de cycle.
Sélection de l'outillage optimal pour l'usinage du PEEK
Lors de l'usinage du PEEK, le choix de l'outillage a un impact considérable sur la qualité des pièces et les coûts globaux d'usinage. Des années d'expérience m'ont appris qu'investir dans les bons outils dès le départ permet d'économiser beaucoup plus à long terme.
Matériaux et géométries des outils de coupe
La nature abrasive du PEEK, en particulier les grades chargés contenant de la fibre de carbone ou du verre, exige une sélection minutieuse des outils :
Matériau de l'outil | Meilleur pour | Durée de vie de l'outil | Facteur de coût |
---|---|---|---|
Carbure (non revêtu) | PEEK non rempli | Bon | Modéré |
Carbure revêtu de diamant | PEEK chargé | Excellent | Haut |
PCD (diamant polycristallin) | Production en grande quantité | Supérieure | Très élevé |
Acier rapide (HSS) | Opérations simples sur du PEEK non chargé | Limitée | Faible |
Pour la plupart des applications chez PTSMAKE, nous utilisons des outils en carbure avec des géométries spécifiques conçues pour les plastiques à haute performance. Les principales caractéristiques que nous recherchons sont les suivantes
- Arêtes de coupe tranchantes (réduisent la production de chaleur)
- Angles de coupe positifs élevés (10-15°)
- Cannelures polies (améliorent l'évacuation des copeaux)
- Angles de dégagement suffisants (évite les frottements)
Si les outils de qualité supérieure coûtent plus cher au départ, ils conservent leur tranchant plus longtemps et produisent de meilleurs états de surface, ce qui réduit la nécessité de recourir à des opérations secondaires.
Considérations relatives à l'usure des outils
L'usure des outils se produit beaucoup plus rapidement lors de l'usinage du PEEK par rapport aux plastiques techniques standard. Nous avons constaté que la surveillance et la gestion de l'usure des outils sont essentielles pour maintenir à la fois la qualité des pièces et la maîtrise des coûts.
Je recommande d'établir un calendrier de changement d'outils basé sur le volume usiné plutôt que d'attendre les signes visuels d'usure. Dans notre atelier, les outils qui usinent le PEEK chargé sont généralement remplacés après environ 60-70% de la durée de vie de l'outil que nous attendons pour l'usinage de l'aluminium. Cette approche proactive permet d'éviter les problèmes de qualité et les pièces potentiellement mises au rebut qui résultent de l'usinage avec des outils usés.
Optimisation des paramètres de coupe
Trouver le bon équilibre entre la vitesse, l'avance et la profondeur de coupe est crucial pour un usinage efficace du PEEK. L'objectif est de maximiser les taux d'enlèvement de matière sans générer de chaleur excessive ni compromettre la qualité de la surface.
Recommandations en matière de vitesse et d'alimentation
Grâce à des essais approfondis chez PTSMAKE, nous avons élaboré ces lignes directrices générales pour les paramètres d'usinage du PEEK :
PEEK Type | Vitesse de coupe (SFM) | Vitesse d'alimentation | Profondeur de coupe | Liquide de refroidissement |
---|---|---|---|---|
PEEK non rempli | 300-500 | Modéré | 0.005"-0.020" | Air ou brouillard |
30% Rempli de carbone | 200-400 | Réduit (75%) | 0.005"-0.015" | Brume/inondation |
30% Rempli de verre | 250-450 | Réduit (85%) | 0.005"-0.015" | Brume/inondation |
Ces paramètres doivent être ajustés en fonction de l'outillage, de la rigidité de la machine et des exigences de la pièce. Je recommande généralement de commencer par l'extrémité conservatrice de ces fourchettes et d'augmenter progressivement les paramètres tout en surveillant les résultats.
Stratégies de gestion de la chaleur
La mauvaise conductivité thermique du PEEK peut entraîner une accumulation de chaleur pendant l'usinage, ce qui risque de provoquer des dommages :
- Instabilité dimensionnelle
- Finition de surface dégradée
- Usure accélérée de l'outil
- Décomposition des matériaux dans les cas extrêmes
Pour résoudre ces problèmes, nous mettons en œuvre plusieurs techniques de gestion thermique :
Sélection correcte du liquide de refroidissement: Pour le PEEK non chargé, le refroidissement par air comprimé donne souvent de bons résultats. Pour les qualités chargées, le refroidissement par brouillard ou par inondation assure une meilleure dissipation de la chaleur.
Coupe intermittente: Une pause périodique pendant les opérations de mise en poche profonde permet à la chaleur de se dissiper.
Fraisage de l'escalade: L'utilisation du fraisage en avalant plutôt que du fraisage conventionnel réduit les frottements et la production de chaleur.
Passages multiples de la lumière: Le fait d'effectuer plusieurs passes de finition légères plutôt qu'une seule coupe lourde améliore la précision dimensionnelle et l'état de surface.
Stratégies d'utilisation des matériaux
Compte tenu du coût élevé du PEEK (souvent $75-200 par livre en fonction du grade et de la forme), l'utilisation du matériau devient un facteur de coût critique. Chaque déchet a un impact direct sur vos résultats.
Matériau de départ en forme de filet
Commencer par un matériau plus proche de vos dimensions finales peut réduire considérablement les déchets. Envisagez les approches suivantes :
Extrusions sur mesure: Pour les pièces de section constante, l'utilisation de profilés extrudés sur mesure permet d'éviter un gaspillage important de matériau. Le coût d'installation plus élevé est compensé par les économies de matériau réalisées pour les grandes séries.
Ébauches prédécoupées: En demandant à votre fournisseur de matériaux de vous fournir des ébauches prédécoupées et dimensionnées spécifiquement pour vos pièces, vous réduisez à la fois les déchets et le temps d'usinage initial.
Logiciel d'imbrication: Pour les pièces plates usinées à partir de plaques, l'utilisation d'un logiciel d'imbrication avancé peut optimiser l'utilisation des matériaux de 15-30% par rapport à la planification manuelle de l'agencement.
Chez PTSMAKE, nous avons aidé des clients à réduire les coûts des matériaux PEEK de plus de 40% en mettant en œuvre ces approches pour leurs composants à haut volume.
Considérations sur le recyclage des puces
Contrairement à certains thermoplastiques, le PEEK ne peut pas être facilement recyclé en interne en raison de sa température de traitement élevée. Il existe cependant des services de recyclage spécialisés :
- Les copeaux de PEEK propres et triés peuvent être vendus aux recycleurs
- Certains recycleurs créditent la valeur des matériaux en vue d'achats futurs.
- Les qualités remplies ont généralement une valeur de recyclage plus faible en raison des problèmes de contamination.
Bien que le recyclage ne permette pas de compenser complètement les coûts des matériaux, il peut permettre de récupérer une partie des coûts pour les opérations d'usinage plus importantes.
Optimisation de la stratégie d'usinage
Au-delà de l'outillage et des paramètres, votre approche globale de l'usinage a un impact significatif sur la qualité des pièces et les coûts de production.
Conception d'un montage pour des pièces multiples
Les montages bien conçus qui permettent d'usiner plusieurs pièces en une seule fois offrent plusieurs avantages :
- Réduction du temps de préparation par pièce
- Amélioration de la cohérence entre les pièces
- Une utilisation plus efficace des machines
- Meilleur rendement des tôles
Pour un client de l'aérospatiale, nous avons conçu un dispositif permettant d'usiner simultanément 16 petits composants en PEEK, ce qui a permis de réduire le coût par pièce de 62% par rapport à des installations individuelles.
Affinement de la stratégie de la FAO
L'optimisation des parcours d'outils permet de réduire considérablement le temps d'usinage et d'améliorer la qualité des pièces :
Broyage à haut rendement: L'utilisation de stratégies FAO avancées qui maintiennent un engagement constant de l'outil réduit les temps de cycle et prolonge la durée de vie de l'outil.
Usinage de repos: Les opérations correctement séquencées qui utilisent des outils plus grands pour l'enlèvement de la plus grande partie de la matière et des outils plus petits uniquement lorsque cela est nécessaire optimisent à la fois les taux d'enlèvement de matière et la durée de vie de l'outil.
Mouvements d'approche optimisés: La minimisation de la coupe d'air par des mouvements d'approche et de rétraction efficaces peut réduire les temps de cycle de 5-15% sans impact sur la qualité des pièces.
Contrôle de la qualité pour minimiser les rebuts
Compte tenu du coût élevé du PEEK, la réduction des rebuts devient une stratégie primordiale de réduction des coûts. Des processus de contrôle de la qualité efficaces qui détectent les problèmes à un stade précoce permettent d'éviter de gaspiller des matériaux coûteux sur des pièces qui ne répondront pas aux spécifications.
Mesures en cours de réalisation
Nous avons mis en place plusieurs étapes de vérification en cours de processus :
Inspection du premier article: Mesurer minutieusement la première partie de chaque série avant de procéder à la production.
Inspections par étapes: Mesure des caractéristiques critiques avant de procéder aux opérations suivantes, en particulier lors du retournement ou de la refixation de pièces.
Stabilisation thermique: Laisser les pièces atteindre la température ambiante avant de procéder aux mesures finales, car la dilatation thermique du PEEK peut affecter les dimensions.
Ces pratiques nous ont permis de maintenir un taux de rebut inférieur à 2% pour les composants en PEEK, ce qui est nettement inférieur aux moyennes de l'industrie.
Considérations post-usinage
Le processus ne se termine pas lorsque la pièce sort de la machine. Les opérations de post-usinage peuvent avoir un impact significatif sur la qualité et le coût.
Soulagement des contraintes et stabilité dimensionnelle
Les pièces en PEEK présentant des géométries complexes ou un enlèvement de matière irrégulier peuvent bénéficier d'un allègement des contraintes afin de garantir une stabilité dimensionnelle à long terme :
Recuit thermique: Un chauffage contrôlé en dessous de la température de transition vitreuse suivi d'un refroidissement lent peut soulager les contraintes internes.
Stratégie de la première à la dernière étape: L'enlèvement de la plus grande partie de la matière lors d'une première opération, puis la stabilisation de la pièce avant l'usinage final améliorent la précision dimensionnelle.
Pour les composants critiques présentant des tolérances serrées, ces étapes supplémentaires valent bien l'investissement pour éviter des défaillances coûteuses sur le terrain ou des dérives dimensionnelles au fil du temps.
En mettant en œuvre ces stratégies d'optimisation, nous avons aidé de nombreux clients de PTSMAKE à réaliser un usinage rentable du PEEK sans compromettre les propriétés de performance exceptionnelles qui rendent ce matériau si précieux. La clé réside dans une approche holistique qui prend en compte tous les aspects du processus de fabrication, de la sélection des matériaux à l'inspection finale.
Découvrez les techniques de gestion thermique pour l'usinage des plastiques à haute performance. ↩
Apprenez les techniques avancées d'usinage de précision des thermoplastiques haute performance. ↩
Cliquez ici pour découvrir les techniques spécialisées permettant d'usiner avec précision les thermoplastiques à hautes performances. ↩
Découvrez comment les propriétés mécaniques influencent la sélection des matériaux pour les composants de haute performance. ↩
Apprenez les techniques d'usinage spécialisées pour prévenir les déformations dues à la chaleur dans les thermoplastiques à haute performance. ↩