Comprendre les capacités de moulage par injection à grande échelle
Vous êtes-vous déjà demandé comment ces énormes composants en plastique de votre voiture, de votre machine à laver ou de vos meubles de jardin étaient fabriqués avec une telle précision ? La technologie qui se cache derrière ces merveilles d'ingénierie est plus fascinante que la plupart des gens ne le pensent.
Les services de moulage par injection de plastique de grande taille représentent une capacité de fabrication spécialisée qui transforme les possibilités de production industrielle, permettant la création de composants surdimensionnés avec une précision remarquable tout en maintenant la rentabilité pour les applications à grand volume.
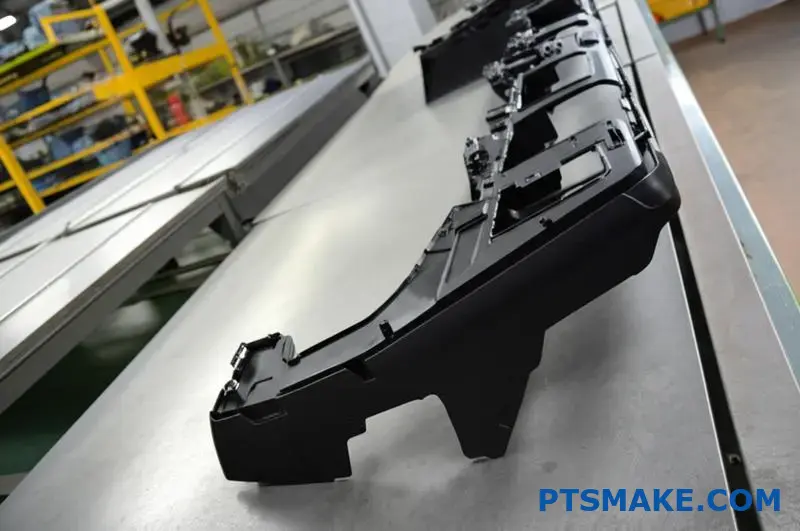
L'évolution du moulage par injection à grande échelle
Le moulage par injection à grande échelle s'est transformé de façon spectaculaire au cours des années que j'ai passées dans l'industrie. Ce qui nécessitait autrefois l'assemblage de plusieurs composants peut aujourd'hui être produit sous la forme d'unités uniques et cohérentes. Cette évolution n'est pas seulement une question de taille, mais aussi de précision, d'efficacité et d'élargissement des possibilités de fabrication des matières plastiques.
Le passage du moulage conventionnel aux capacités à grande échelle a nécessité d'importantes innovations techniques. Les grandes machines modernes de moulage par injection de plastique fonctionnent avec des forces de serrage allant de 1 000 à 4 400 tonnes, soit une force exponentielle par rapport à l'équipement standard. Cette force remarquable est nécessaire pour maintenir la fermeture du moule contre l'immense pression créée lors de l'injection du matériau dans de grandes cavités.
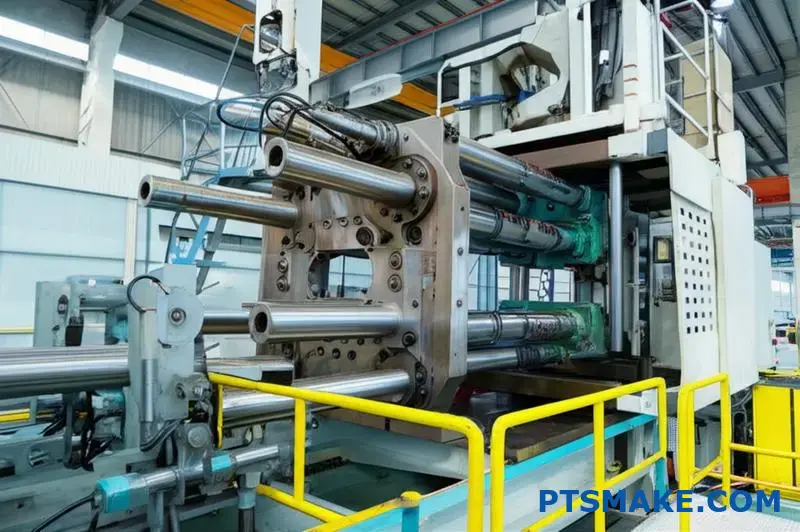
Spécifications techniques du moulage à grande échelle
Taille Capacités
Les dimensions réalisables grâce au moulage par injection à grande échelle sont vraiment impressionnantes. Chez PTSMAKE, notre équipement peut produire des composants jusqu'à 60" x 60" x 25" en pièces détachées. Cette capacité élimine la nécessité d'opérations d'assemblage complexes et réduit les points de défaillance potentiels des produits finis.
Contrôle de la précision et de la tolérance
Ce qui est peut-être le plus remarquable, c'est que ces composants massifs conservent une précision exceptionnelle. Malgré leur taille, nos processus de moulage à grande échelle peuvent atteindre des tolérances aussi étroites que +/-0,003 pouce. Ce niveau de précision nécessite des procédés de moulage sophistiqués. systèmes de surveillance des processus1 qui ajustent continuellement les paramètres pendant la production.
Options de matériaux pour les grands composants
Le moulage à grande échelle ne se limite pas aux matériaux de base. Nous traitons régulièrement :
- Thermoplastiques de qualité technique (PC, ABS, Nylon)
- Composites chargés de verre pour applications structurelles
- Formulations modifiées en fonction de l'impact pour une meilleure durabilité
- Matériaux colorés sur mesure pour une cohérence esthétique
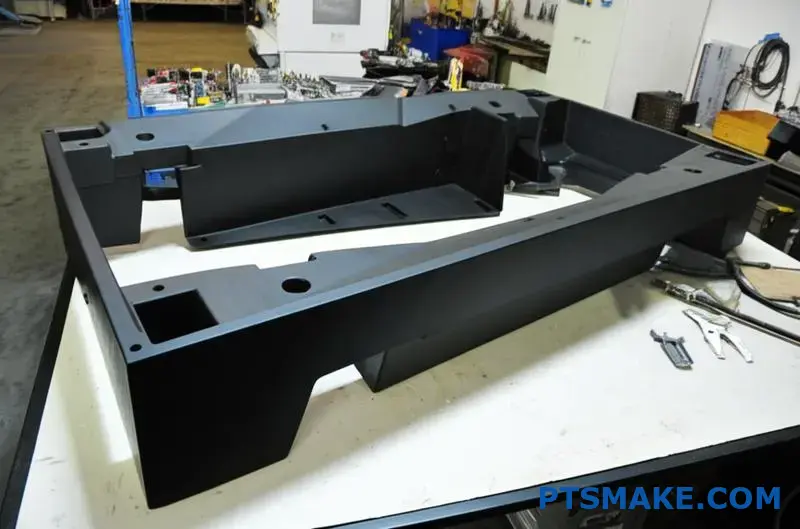
Applications industrielles
Secteur automobile
L'industrie automobile représente l'un des principaux marchés pour les services de moulage par injection de plastique de grande taille. Des composants tels que :
- Tableaux de bord
- Systèmes de pare-chocs
- Panneaux de porte intérieurs
- Composants sous le capot
Toutes bénéficient de capacités de moulage à grande échelle. Ces pièces nécessitent souvent des géométries complexes avec des caractéristiques intégrées telles que des supports de montage, des nervures de renforcement et des raccords de précision, le tout produit en un seul cycle de moulage.
Biens de consommation et appareils ménagers
Les grands fabricants d'appareils électroménagers ont recours au moulage à grande échelle :
- Cuves de machines à laver
- Doublures pour réfrigérateurs
- Boîtiers de gros appareils électroménagers
- Meubles d'extérieur durables
Ces applications bénéficient de la stabilité dimensionnelle et de l'intégrité structurelle que procurent des pièces moulées à grande échelle correctement conçues.
Solutions de manutention
Les conteneurs industriels, les palettes et les systèmes de stockage utilisent de plus en plus de composants moulés à grande échelle :
Bénéfice | Assemblée traditionnelle | Moulage à grande échelle |
---|---|---|
Réduction du poids | Limité par la résistance des joints | Optimisation par la conception |
Durabilité | Points de défaillance multiples | Structure unifiée |
Rapport coût-efficacité | Assemblage à forte intensité de main-d'œuvre | Production automatisée |
Cohérence | Qualité variable | Processus reproductibles |
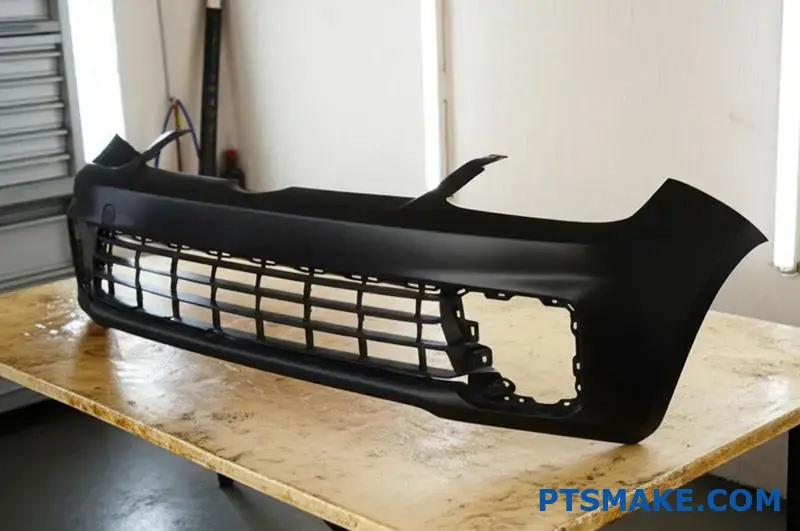
Considérations techniques pour le moulage à grande échelle
La conception pour le moulage par injection à grande échelle nécessite une expertise spécialisée. Les facteurs critiques sont les suivants :
Gestion de l'épaisseur des parois
Le maintien d'une épaisseur de paroi constante devient de plus en plus difficile à mesure que la taille des pièces augmente. Notre équipe d'ingénieurs analyse soigneusement les conceptions afin d'éviter des problèmes tels que :
- Marques d'enfoncement dans les sections plus épaisses
- Déformation due à un refroidissement inégal
- Faiblesses structurelles des zones minces
- L'hésitation du front d'écoulement est à l'origine de défauts esthétiques
Systèmes de portes et de glissières
Le système d'alimentation des grands moules doit être conçu avec soin. Plusieurs vannes sont généralement nécessaires pour assurer un remplissage complet, mais leur emplacement doit être déterminé de manière stratégique afin d'éviter.. :
- Lignes de soudure visibles dans les zones cosmétiques
- Piégeage de l'air provoquant des vides
- Pertes de charge excessives affectant la qualité des pièces
- Emballage inégal et problèmes dimensionnels
Conception du système de refroidissement
Un refroidissement efficace représente peut-être l'aspect le plus critique de la conception des moules à grande échelle. Le système de gestion thermique doit extraire uniformément la chaleur de ces pièces massives afin d'éviter le gauchissement et de garantir l'efficacité du cycle. Chez PTSMAKE, nous mettons en œuvre des canaux de refroidissement conformes avancés qui suivent la géométrie de la pièce afin d'optimiser cet élément critique du processus.
Grâce à des processus de moulage par injection à grande échelle correctement conçus, les fabricants peuvent obtenir des résultats remarquables qui seraient impossibles avec des méthodes conventionnelles, transformant ainsi ce qui est possible en matière de conception et de production de composants en plastique.
Options d'outillage avancées pour les grandes pièces complexes
Vous êtes-vous déjà demandé pourquoi certains fabricants peuvent créer des pièces en plastique massives avec une précision incroyable alors que d'autres peinent à le faire ? Le secret ne réside pas dans les machines, mais dans les systèmes d'outillage sophistiqués qui rendent possible la production à grande échelle.
L'outillage de moulage à haute performance représente la base essentielle de la réussite des services de moulage par injection de plastique de grande taille, avec des options allant des outils de prototypage rapide aux moules multi-empreintes de qualité production conçus spécifiquement pour les composants surdimensionnés.
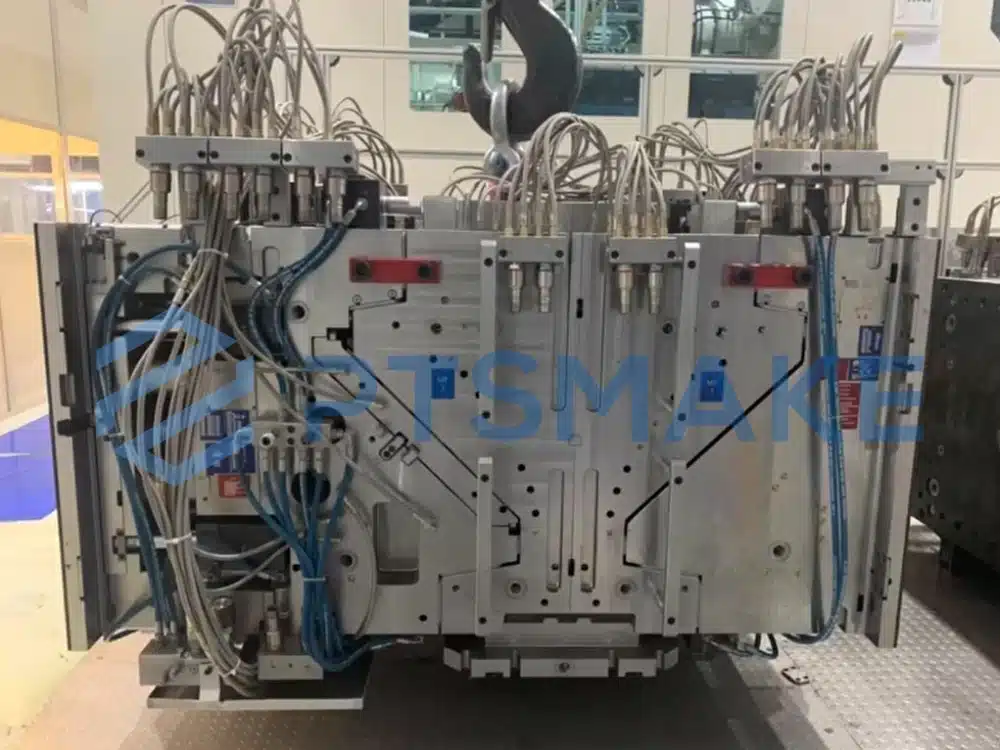
Comprendre les systèmes de classification des moisissures
Lorsqu'il s'agit de grands composants en plastique, le choix de l'outillage devient encore plus critique que pour les pièces de taille standard. L'industrie classe les moules en plusieurs catégories en fonction de leur construction, de leur longévité et de leurs capacités de précision.
Classe 105 : Outillage de prototype
L'outillage prototype offre le chemin le plus rapide vers la validation initiale des pièces pour les composants de grande taille. Ces moules à base d'aluminium présentent plusieurs avantages :
- Délai d'exécution réduit (généralement 2 à 3 semaines contre 8 à 10 pour l'acier)
- Investissement initial moins élevé
- Capacité à valider les concepts de conception avant de s'engager dans l'outillage de production
- Possibilité de produire des quantités limitées pour tester le marché
Cependant, ces outils ont des limites lorsqu'il s'agit de pièces de grande taille. La construction en aluminium signifie qu'ils peuvent supporter moins de cycles avant de montrer de l'usure, en particulier avec les pressions substantielles requises pour les grandes pièces.
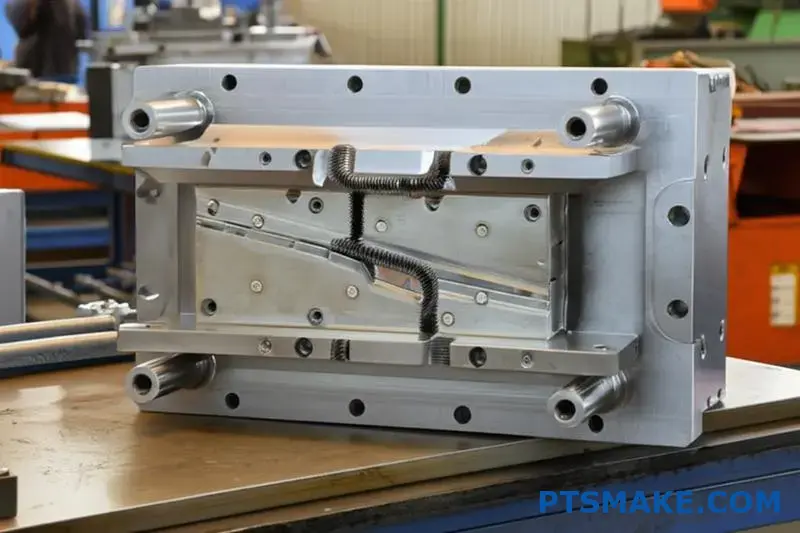
Classes 103 et 104 : Outillage de pont
L'outillage pont représente une solution intermédiaire entre les moules prototypes et les moules de production. Ces outils utilisent des inserts en acier dans les zones d'usure critiques tout en conservant des matériaux plus économiques dans les zones moins sollicitées.
Pour les grands services de moulage par injection de plastique, l'outillage en pont offre des avantages indéniables :
- Capacités de production étendues (typiquement 50 000-100 000 cycles)
- Stabilité dimensionnelle améliorée par rapport à l'aluminium
- Meilleure dissipation de la chaleur pour des cycles plus rapides
- Plus économique que l'outillage de production complet lorsque les volumes sont incertains
Chez PTSMAKE, nous avons utilisé avec succès l'outillage pont pour des clients qui devaient lancer des produits alors que leurs outils de production à plus grand volume étaient encore en cours de développement.
Classes 101 et 102 : Outillage de production
Lorsqu'il s'agit de grands composants en grandes quantités, l'outillage de production de classe 101 et 102 devient essentiel. Ces moules en acier trempé offrent :
- Capacité de production pratiquement illimitée (millions de cycles)
- Stabilité dimensionnelle supérieure tout au long du cycle de production
- Capacité à supporter les pressions d'injection élevées requises pour les pièces de grande taille
- Capacités de refroidissement améliorées pour l'optimisation du temps de cycle
L'investissement dans l'outillage de classe 101 pour les grands composants est substantiel, mais l'économie par pièce devient de plus en plus favorable au fur et à mesure que les volumes de production augmentent.
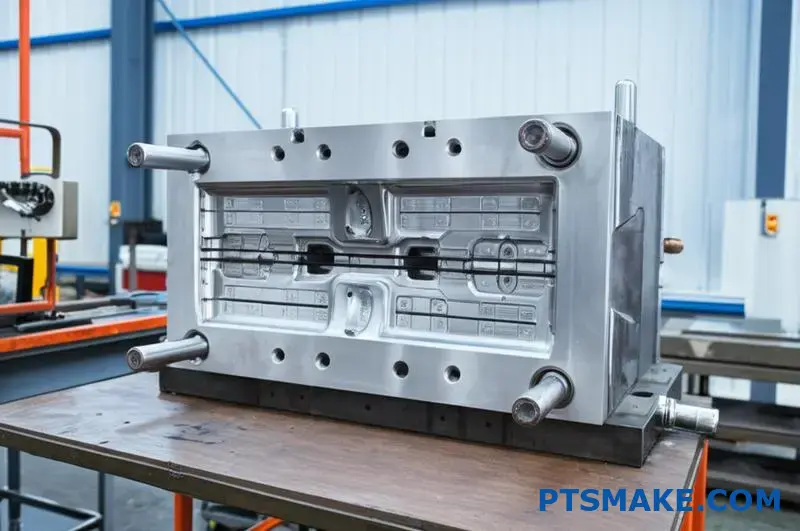
Configurations multi-empreintes pour les pièces de grande taille
L'une des avancées les plus significatives dans les services de moulage par injection de plastique de grande taille a été le développement d'un outillage multi-empreintes pour les composants surdimensionnés. Cette approche présente des défis techniques uniques, mais offre des avantages indéniables.
Options de cavité unique, de cavité familiale ou de cavité multiple
Les options de configuration de l'outillage sont les suivantes :
Type de configuration | Description | Meilleure application |
---|---|---|
Cavité unique | Une grande pièce par cycle | Géométries complexes avec des tolérances serrées |
Moule familial | Différentes pièces connexes dans un seul outil | Produits à composants multiples nécessaires en quantités égales |
Multi-empreintes | Plusieurs grandes pièces identiques par cycle | Production en grande quantité où l'efficacité est primordiale |
Pour les composants de grande taille, la complexité technique des moules à cavités multiples augmente de façon exponentielle. Les analyse du flux des moules2 nécessaire pour assurer une obturation correcte de toutes les cavités devient nettement plus sophistiquée.
Équilibrer la complexité et l'efficacité
Lors de la conception d'un outillage multi-empreintes pour des composants de grande taille, plusieurs facteurs doivent être soigneusement équilibrés :
- Répartition de la pression - Assurer que chaque cavité reçoive une pression égale malgré la distance du point d'injection
- Gestion thermique - Création d'un refroidissement uniforme dans les structures métalliques massives
- Exigences en matière de ventilation - Évacuer correctement l'air de plusieurs grandes cavités
- Systèmes d'éjection - Mise au point de méthodes robustes pour retirer des pièces importantes sans les endommager
Grâce à une ingénierie appropriée, l'outillage multi-empreintes peut améliorer considérablement les coûts de production pour les grandes pièces, réduisant souvent les coûts par pièce de 30-50% par rapport aux approches mono-empreintes.
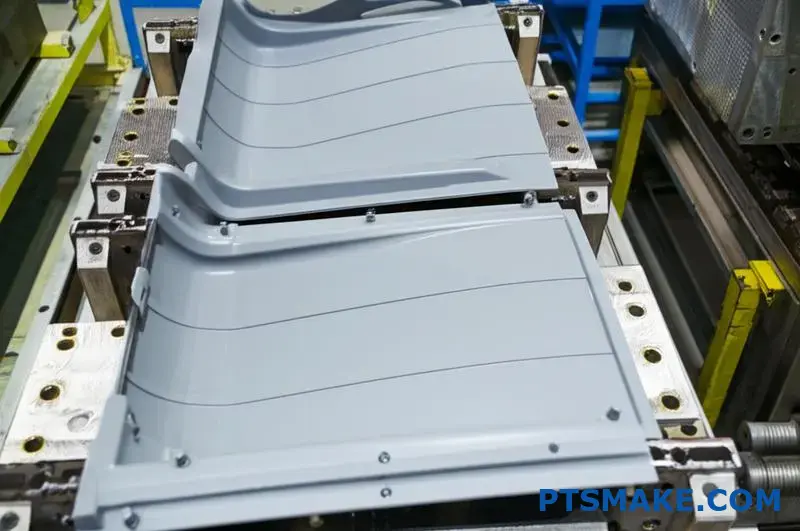
Gestion de la tolérance des caractéristiques critiques
Le maintien de tolérances serrées sur les grandes pièces moulées présente des défis uniques qui doivent être relevés par des approches d'outillage sophistiquées.
Choix de l'acier et traitement thermique
Pour les grands moules où la stabilité dimensionnelle est critique, la sélection d'aciers à outils appropriés devient encore plus importante. Nous recommandons généralement :
- Acier prétrempé P20 pour les grands moules à usage général
- H13 pour les zones exposées à une forte usure ou à des matériaux abrasifs
- S7 pour les composants présentant des exigences élevées en matière d'éjection
- Acier inoxydable 420 pour les applications résistantes à la corrosion ou les pièces médicales
Le processus de traitement thermique doit être soigneusement contrôlé pour éviter le gauchissement de ces structures en acier massif, ce qui nécessite souvent des installations de traitement thermique spécialisées.
Stratégie d'insertion pour les caractéristiques complexes
L'une des approches les plus efficaces pour maintenir des tolérances serrées sur les caractéristiques critiques est l'utilisation stratégique d'inserts dans la structure plus large du moule. Cela permet :
- Différents matériaux pour différentes parties du moule
- Programmes d'entretien distincts pour les zones à forte usure
- Possibilité de ne remplacer que les parties endommagées plutôt que des outils entiers
- Refroidissement amélioré axé sur les dimensions critiques
Chez PTSMAKE, nous avons développé des stratégies d'insertion sophistiquées qui nous permettent de maintenir des tolérances aussi étroites que ±0,001", même sur des pièces mesurant plusieurs pieds.
Conception du système de refroidissement pour la stabilité dimensionnelle
La conception du système de refroidissement dans les grands moules a un impact direct sur la stabilité dimensionnelle. Les canaux de refroidissement traditionnels à perçage droit s'avèrent souvent inadéquats pour les pièces massives. Au lieu de cela, nous mettons en œuvre :
- Canaux de refroidissement conformes à la géométrie de la pièce
- Broches thermiques pour les zones inaccessibles au refroidissement conventionnel
- Zones de refroidissement séparées avec contrôle indépendant de la température
- Surveillance thermique avancée pendant la production
Grâce à ces approches sophistiquées de la conception d'outils, les fabricants peuvent atteindre une précision remarquable, même avec les composants plastiques à grande échelle les plus difficiles.
Sélection des matériaux pour les grands composants en plastique
Vous êtes-vous déjà demandé pourquoi certains grands produits en plastique se fissurent sous la pression alors que d'autres durent des années ? Le secret ne réside pas dans les techniques de fabrication, mais dans le processus critique de sélection des matériaux qui intervient bien avant le début de la production.
La sélection du bon matériau pour les grands composants en plastique implique de trouver un équilibre entre l'intégrité structurelle, les considérations de poids et la rentabilité, tout en veillant à ce que le polymère choisi puisse résister aux contraintes propres aux applications surdimensionnées.
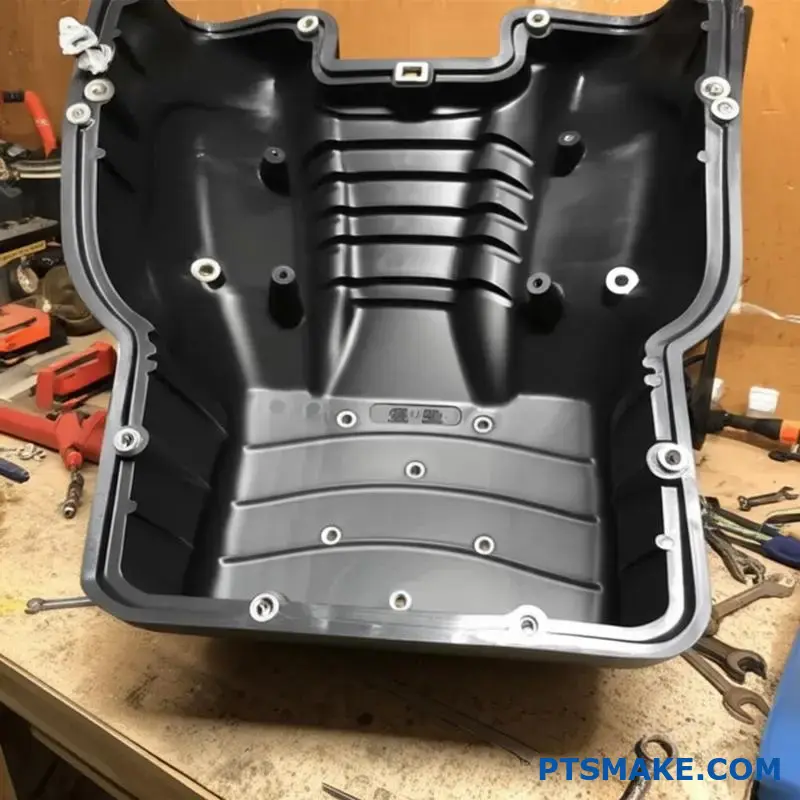
Comprendre les exigences en matière de matériaux pour les applications à grande échelle
Lorsqu'il s'agit de composants plastiques de grande taille, tous les matériaux ne sont pas créés égaux. Les exigences imposées aux pièces surdimensionnées diffèrent considérablement de celles imposées aux pièces plus petites. Chez PTSMAKE, j'ai vu de nombreux projets échouer parce que la sélection des matériaux n'avait pas reçu l'attention qu'elle méritait.
Principales considérations en matière de performances
Les grandes pièces en plastique sont confrontées à des défis uniques qui influencent directement la sélection des matériaux :
- Charges structurelles plus élevées et risque de déformation
- Susceptibilité accrue au gauchissement pendant le refroidissement
- Exposition accrue aux facteurs environnementaux
- Impact plus important du retrait des matériaux
- Exigences accrues en matière de stabilité dimensionnelle
Ces facteurs créent une matrice de décision complexe qui nécessite une connaissance approfondie des matériaux pour réussir à s'y retrouver.
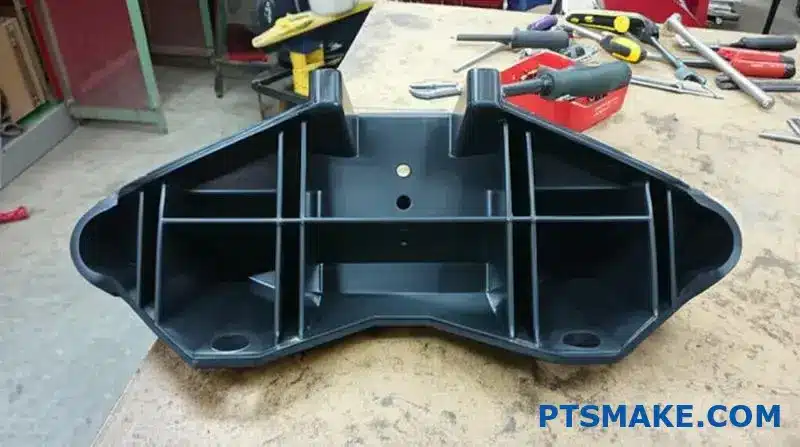
Plastiques techniques pour applications structurelles
Pour les composants dont l'intégrité structurelle est primordiale, les plastiques techniques offrent des caractéristiques de performance supérieures à celles des résines de base.
Composés de nylon chargés de verre
Le nylon chargé de fibres de verre (PA) est l'un des matériaux les plus polyvalents pour les composants de grande taille. Le renforcement par la fibre de verre améliore considérablement :
- Résistance à la traction (jusqu'à 3 fois supérieure à celle du nylon non chargé)
- Température de déviation de la chaleur
- Stabilité dimensionnelle lors de changements environnementaux
- Résistance au fluage sous charges soutenues
Ces propriétés font du nylon chargé de verre un matériau idéal pour les grands composants automobiles, les boîtiers industriels et les cadres structurels. Nous recommandons généralement la charge de verre 30-33% comme équilibre optimal entre la résistance et la facilité de traitement pour la plupart des grandes applications.
Polycarbonate et mélanges PC/ABS
Le polycarbonate (PC) et ses mélanges avec l'ABS offrent une combinaison exceptionnelle de résistance aux chocs et de stabilité dimensionnelle, essentielle pour les composants de grande taille. Les principaux avantages sont les suivants
Propriété | Polycarbonate | Mélange PC/ABS |
---|---|---|
Résistance aux chocs | Excellent | Très bon |
Résistance à la température | Jusqu'à 135°C | Jusqu'à 110°C |
Stabilité aux UV | Médiocre (nécessite des additifs) | Modéré |
Facilité de traitement | Modéré | Excellent |
Coût relatif | Plus élevé | Modéré |
Lors de la conception de grands panneaux extérieurs ou de boîtiers nécessitant à la fois une intégrité structurelle et un attrait esthétique, les mélanges PC/ABS offrent souvent l'équilibre idéal entre les propriétés et la facilité de mise en œuvre.
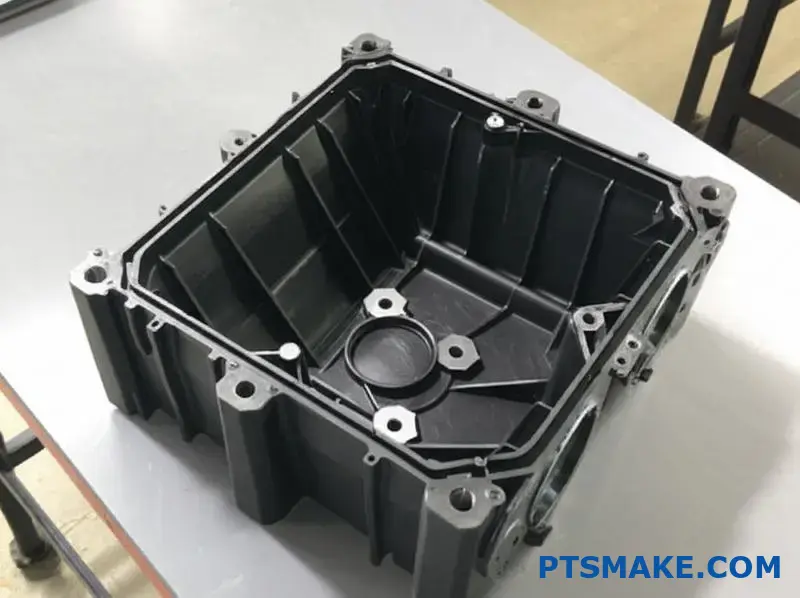
Résines haute performance pour applications exigeantes
Certains grands composants sont soumis à des conditions extrêmes qui nécessitent des matériaux spécialisés de haute performance.
PEEK et PEI pour les applications critiques
Pour les applications à grande échelle les plus exigeantes, le polyétheréthercétone (PEEK) et le polyétherimide (PEI) offrent des performances exceptionnelles :
- Températures de fonctionnement supérieures à 200°C
- Résistance chimique supérieure aux substances agressives
- Excellentes propriétés mécaniques, même à des températures élevées
- Retardateur de flamme inhérent (en particulier PEI)
Ces matériaux ont un prix élevé mais offrent des performances inégalées pour les composants de grande taille dans l'aérospatiale, la médecine et les applications industrielles spécialisées. Chez PTSMAKE, nous avons réussi à mouler des composants en PEEK d'une longueur allant jusqu'à 36 pouces tout en maintenant des tolérances serrées malgré les caractéristiques de traitement difficiles du matériau.
Formulations composites avancées
Les progrès récents dans le domaine de la science des matériaux ont permis de produire des formulations de composites spécialisées, spécialement conçues pour les composants de grande taille :
- Polymères renforcés de fibres de carbone pour un rapport poids/résistance maximal
- Thermoplastiques à fibres de verre longues (LFT) pour des propriétés d'impact améliorées
- Systèmes de renforcement hybrides3 qui combinent plusieurs types de fibres
- Additifs spéciaux pour améliorer l'écoulement des pièces massives dans les moules
Ces formulations avancées aident à surmonter de nombreuses limitations traditionnelles associées au moulage de grandes pièces, permettant des conceptions qui étaient auparavant impossibles à produire.
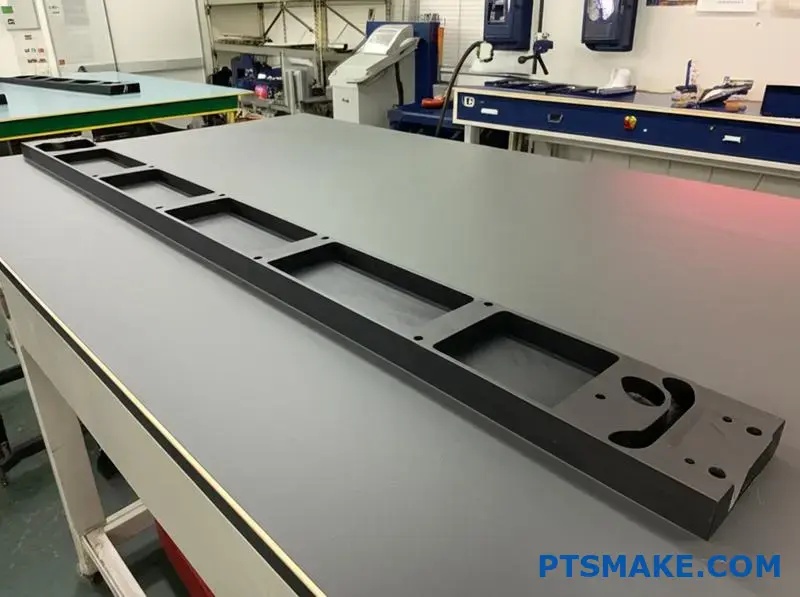
Processus de sélection des matériaux pour les composants de grande taille
La sélection du matériau optimal pour les grandes pièces en plastique nécessite une approche systématique qui tient compte à la fois des exigences techniques et des contraintes de fabrication.
Évaluation des paramètres techniques
Le processus de sélection commence par une évaluation complète des paramètres techniques :
- Exigences mécaniques: Identifier les besoins spécifiques en matière de résistance, de rigidité et de résistance aux chocs
- Exposition environnementale: Évaluer l'exposition aux UV, le contact avec les produits chimiques et les plages de température.
- Conformité réglementaire: Déterminer les normes pertinentes pour l'application (UL, FDA, ISO, etc.)
- Durée de vie prévue: Définir le délai de durabilité requis
- Besoins en matière de stabilité dimensionnelle: Évaluer les exigences de tolérance en fonction des conditions environnementales
Ces paramètres créent un profil qui réduit le nombre de matériaux potentiels avant de prendre en compte les facteurs de fabrication.
Considérations relatives à la fabrication
Pour les composants de grande taille, la sélection des matériaux doit tenir compte de la faisabilité de la fabrication :
- Caractéristiques de l'écoulement: Les matériaux doivent conserver un débit constant sur de longues distances
- Impact sur le temps de cycle: Certains matériaux nécessitent des phases de refroidissement beaucoup plus longues
- Compatibilité des équipements: Les matériaux à haute température peuvent nécessiter un équipement spécialisé.
- Stabilité après moulage: Certains matériaux continuent à se rétracter ou à se déformer plusieurs jours après le moulage.
- Opérations secondaires: Le choix des matériaux a une incidence sur les processus de peinture, de soudage et d'assemblage.
Lorsque nous développons de grands composants chez PTSMAKE, nous créons souvent des matrices de sélection des matériaux qui mettent en balance ces facteurs et les considérations de coût afin d'identifier le choix optimal des matériaux.
Analyse coûts-avantages
La sélection finale nécessite généralement de mettre en balance les exigences de performance et les facteurs économiques :
- Coût initial du matériau par kilogramme
- Impact de l'efficacité de la transformation sur le prix à la pièce
- Taux de rejet prévus pendant la production
- Considérations relatives à l'outillage (certains matériaux nécessitent un acier ou des revêtements spécialisés)
- Exigences en matière d'opérations secondaires et coûts associés
En analysant minutieusement ces facteurs, les fabricants peuvent identifier les matériaux qui offrent les performances nécessaires tout en restant économiquement viables pour une production à grande échelle.
Études de cas sur la sélection des matériaux
Mon expérience chez PTSMAKE m'a permis d'observer plusieurs modèles de sélection réussie de matériaux pour des composants de grande taille dans différents secteurs d'activité :
- Panneaux intérieurs d'automobiles: Le polypropylène chargé de verre offre un excellent équilibre entre le coût, le poids et les performances structurelles.
- Boîtiers d'équipements industriels: Les mélanges PC/ABS offrent une résistance aux chocs et une esthétique supérieures, ainsi qu'une bonne intégrité structurelle.
- Enceintes pour équipements médicaux: Le PEI offre les propriétés ignifuges, la résistance chimique et la durabilité nécessaires.
- Biens de grande consommation: L'acrylique modifié pour résister aux chocs offre une esthétique exceptionnelle et de bonnes performances structurelles.
Le point commun des mises en œuvre réussies est une compréhension approfondie des exigences de l'application et des capacités des matériaux, combinée à des essais rigoureux avant l'engagement d'une production à grande échelle.
Techniques spécialisées pour la fabrication de grandes pièces
Vous êtes-vous déjà demandé comment les fabricants créent ces énormes composants en plastique pour les véhicules, les appareils électroménagers ou les équipements industriels avec une précision aussi remarquable ? Le secret réside dans des techniques de moulage spécialisées qui transforment l'impossible en réalité grâce à des approches techniques innovantes.
Les technologies de moulage avancées ont révolutionné les services de moulage par injection de plastique de grande taille en introduisant des processus spécialisés tels que l'assistance au gaz, la mousse structurelle et les techniques de moulage par empilage qui maximisent l'efficacité tout en maintenant une intégrité structurelle et une stabilité dimensionnelle exceptionnelles.
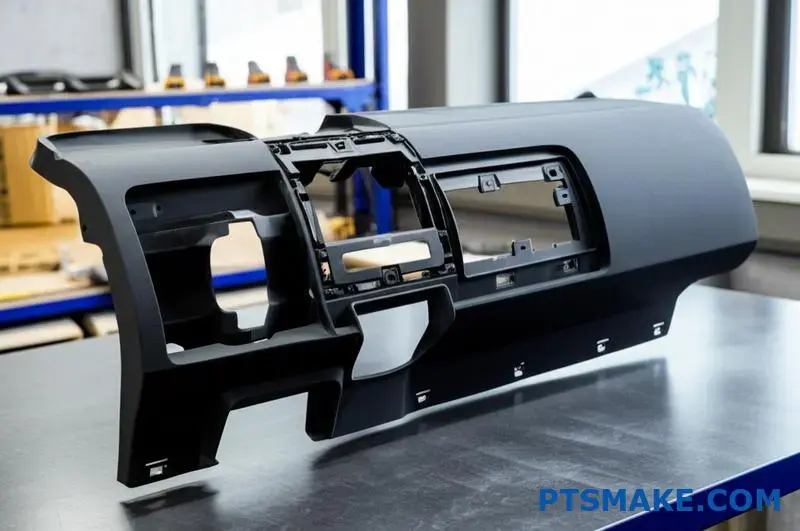
Moulage par injection avec assistance gazeuse : Création de sections creuses dans des pièces massives
Le moulage par injection assisté par gaz représente l'une des percées les plus importantes dans la fabrication de grandes pièces en plastique. Ce procédé innovant consiste à injecter de l'azote gazeux dans des cavités de moule partiellement remplies, créant ainsi des sections creuses contrôlées dans des pièces à parois épaisses.
Le processus d'assistance au gaz expliqué
Le processus d'assistance au gaz suit une séquence spécifique :
- Injection initiale de matière plastique fondue (généralement 70-80% du volume total de la cavité)
- Introduction précise d'azote gazeux sous pression contrôlée
- Le gaz suit le chemin de moindre résistance à travers des sections plus épaisses
- Formation de canaux creux tout en conservant des surfaces extérieures solides
- La pression du gaz maintient le matériau contre les parois du moule pendant le refroidissement
- Mise à l'air libre des gaz avant l'éjection de la pièce
Cette approche offre des avantages remarquables pour les composants de grande taille. En créant des sections creuses contrôlées, nous pouvons produire des pièces avec une utilisation de matériaux considérablement réduite tout en conservant une excellente rigidité structurelle. Les canaux de gaz internes fonctionnent effectivement comme des "nervures invisibles" qui soutiennent la structure de la pièce.
Avantages pour la fabrication de grands composants
Les avantages de la technologie d'assistance au gaz pour les grands services de moulage par injection de plastique sont les suivants :
Bénéfice | Impact technique | Valeur de l'entreprise |
---|---|---|
Réduction des matériaux | 20-40% moins de plastique utilisé | Réduction des coûts des matières premières |
Réduction du poids | Des composants plus légers pour une résistance équivalente | Amélioration de l'efficacité des produits |
Réduction du temps de cycle | Refroidissement plus rapide grâce à des parois plus fines | Augmentation de la capacité de production |
Marques d'évier minimisées | La pression du gaz élimine les dépressions de surface | Amélioration de la qualité esthétique |
Moins de déformation | Caractéristiques de refroidissement plus uniformes | Amélioration de la stabilité dimensionnelle |
Chez PTSMAKE, nous avons mis en œuvre avec succès la technologie d'assistance au gaz pour des composants tels que les grands tableaux de bord automobiles, où la technique crée des canaux de renforcement internes qui seraient impossibles avec les approches de moulage traditionnelles.
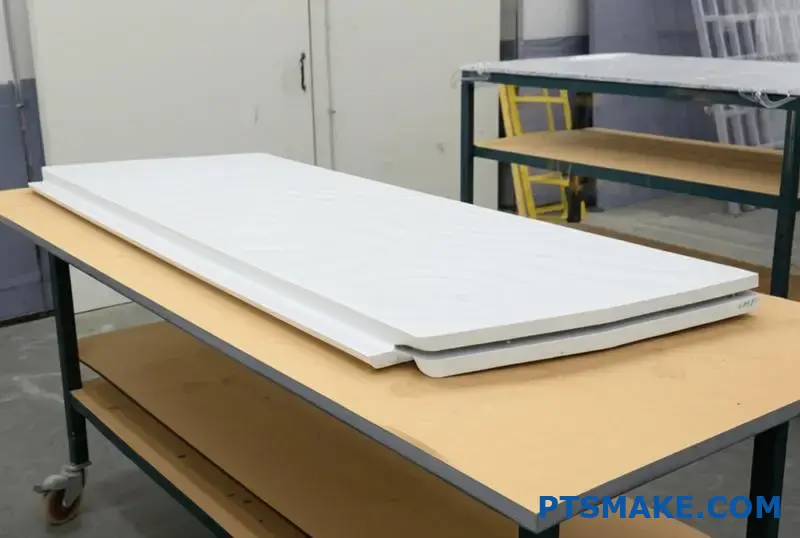
Moulage structurel de la mousse : Ingénierie de la légèreté et de la résistance
Le moulage en mousse structurelle est une autre technique spécialisée particulièrement utile pour les composants de grande taille nécessitant un rapport poids/résistance exceptionnel.
Mécanique et chimie des procédés
Le procédé de la mousse structurelle utilise un agent gonflant chimique (CBA) mélangé à la résine polymère avant l'injection. Lorsque le matériau entre dans le moule, l'agent gonflant crée une structure cellulaire centrale tout en maintenant une peau extérieure solide. Le résultat est une construction en sandwich aux propriétés structurelles remarquables.
Le noyau de mousse représente généralement 20-35% de l'épaisseur totale de la pièce, créant une structure cellulaire légère entourée d'une couche de surface dense et solide. Cette structure imite les principes d'ingénierie que l'on trouve dans la construction des poutres en I, où les matériaux sont stratégiquement placés pour maximiser l'intégrité structurelle.
Avantages techniques pour les composants surdimensionnés
Le moulage en mousse structurelle offre plusieurs avantages décisifs pour les grandes pièces en plastique :
- Rigidité accrue: La structure cellulaire du noyau permet d'obtenir un module de flexion 2 à 3 fois supérieur à celui des pièces solides de poids équivalent.
- Stabilité dimensionnelle: La densité réduite du matériau signifie moins de rétrécissement et de gauchissement.
- Diminution du stress interne: Le noyau moussé minimise les contraintes résiduelles qui provoquent des déformations dans les grandes pièces.
- Excellente isolation: La structure cellulaire offre des propriétés d'isolation thermique et acoustique
- Potentiel de remplacement du métal: Le rapport poids/résistance permet de remplacer les composants métalliques
Pour les applications industrielles telles que les grands conteneurs de manutention, les boîtiers d'équipement et les panneaux structurels, le moulage en mousse structurelle offre souvent l'équilibre idéal entre performance et efficacité de fabrication.
Considérations relatives à la conception de la mousse structurelle
Lors de la conception de grands composants pour le moulage structurel de la mousse, plusieurs facteurs doivent faire l'objet d'une attention particulière :
- Exigences en matière d'épaisseur de paroi: Epaisseur minimale de 0,125" (3,2 mm) nécessaire au bon développement de la mousse.
- Limitations de la longueur du flux: Le matériau doit atteindre toutes les zones avant qu'un refroidissement significatif ne se produise
- Attentes en matière d'état de surface: Des motifs tourbillonnaires caractéristiques peuvent apparaître sur les surfaces
- Exigences relatives à l'angle de tirant d'eau: Généralement 1 à 2° de plus que le moulage conventionnel
- Planification de l'emplacement des portes: Positionnement stratégique pour assurer le remplissage complet des pièces massives
Grâce à une optimisation adéquate de la conception, le moulage en mousse structurelle peut produire des composants de très grande taille (jusqu'à 6 pieds de long) avec des performances structurelles et un rapport coût-efficacité exceptionnels.
nul
Technologie des moules à étages : Multiplier l'efficacité de la production
La technologie des moules à étages représente une approche révolutionnaire permettant d'accroître l'efficacité de la production de composants de grande taille sans nécessiter des machines de moulage proportionnellement plus grandes.
Configuration et fonctionnement du moule à étages
Contrairement aux moules conventionnels à une seule face, les moules à étages utilisent plusieurs plans de joint et faces de moule disposés dans une configuration empilée. Un moule à étages typique peut comprendre
- Une section centrale qui se déplace avec la plaque centrale de la machine
- Deux sections extérieures fixées aux plateaux fixes et mobiles de la machine
- Systèmes de canaux chauds spécialisés pour acheminer le matériau dans toutes les cavités
- Actions mécaniques ou hydrauliques synchronisées pour assurer un fonctionnement correct
Cette configuration permet de doubler, voire de tripler la production sans nécessiter une machine de moulage par injection beaucoup plus grande. Pour les composants de grande taille, ce multiplicateur d'efficacité peut transformer l'économie de la production.
Avantages de la production de pièces de grande taille en grande quantité
La technologie des moules à étages offre plusieurs avantages distincts pour la production en grande série de composants de grande taille :
- Augmentation de la production: Production de 2 à 4 fois plus de pièces par cycle que les moules conventionnels
- Optimisation de l'utilisation des machines: Maximise le rendement de l'équipement existant
- Répartition équilibrée des forces: Permet d'obtenir une force de serrage plus uniforme sur l'ensemble du moule
- Réduit variation d'un coup à l'autre4: Paramètres de traitement cohérents dans toutes les cavités
- Efficacité énergétique: Réduction de la consommation d'énergie par pièce produite
Pour des applications telles que les grands composants automobiles, les pièces d'appareils électroménagers ou les conteneurs industriels produits en grandes quantités, les moules à étages peuvent améliorer considérablement les coûts de production tout en maintenant des normes de qualité exceptionnelles.
Défis et solutions de mise en œuvre
La mise en œuvre de la technologie des moules à étages pour les composants de grande taille présente plusieurs défis uniques :
- Gestion complexe des flux de matières: Assurer un remplissage équilibré de plusieurs cavités
- Contrôle précis de la température: Maintien de conditions thermiques uniformes dans l'ensemble de l'empilement de moules
- Synchronisation mécanique: Coordonner les mouvements de plusieurs sections de moules
- Complexité de la maintenance: Exigences de maintenance plus sophistiquées que pour les moules conventionnels
- Considérations sur l'investissement initial: Des coûts d'outillage initiaux plus élevés malgré des économies à long terme
Grâce à une ingénierie appropriée et à des techniques de simulation avancées, il est possible de relever efficacement ces défis et d'exploiter les avantages de production remarquables qu'offre la technologie des moules à étages pour la fabrication de composants de grande taille.
Approches hybrides : Combiner les technologies pour obtenir des résultats optimaux
Les services de moulage par injection de plastique de grande taille les plus sophistiqués impliquent souvent des approches hybrides qui combinent plusieurs techniques spécialisées pour répondre à des exigences complexes en matière de pièces.
Assistance au gaz combinée à la mousse structurelle
Pour les composants de taille exceptionnelle nécessitant à la fois une réduction de poids et des performances structurelles supérieures, la combinaison des technologies d'assistance au gaz et de mousse structurelle peut donner des résultats remarquables. Cette approche hybride :
- Utilise de la mousse structurelle pour la structure de la pièce principale
- Mise en place de canaux d'assistance au gaz à des endroits stratégiques pour un renforcement supplémentaire
- Répartition optimisée des matériaux pour un rapport poids/résistance maximal
- Fournit des pièces d'une excellente stabilité dimensionnelle en dépit de leur taille massive
Cette combinaison s'avère particulièrement précieuse pour les grands composants tels que les systèmes de gestion du fret automobile, pour lesquels la réduction du poids, l'intégrité structurelle et la stabilité dimensionnelle sont autant d'exigences critiques.
Solutions multi-matériaux pour grands composants
Une autre approche hybride fait appel à des techniques multi-matériaux ou de surmoulage pour les composants de grande taille :
- Combinaisons rigides/flexibles: Création de grandes pièces avec des joints intégrés ou des zones flexibles
- Couches structurelles/cosmétiques: Combinaison d'un support structurel et de couches superficielles esthétiques
- Structures hybrides métal/plastique: Insertion de renforts métalliques dans de grandes pièces en plastique
- Applications Multi-Duromètre: Dureté variable selon les différentes sections des pièces massives
Ces approches hybrides sophistiquées permettent des conceptions qui seraient impossibles avec une seule technique de moulage, élargissant ainsi les possibilités de conception et de fonction des grands composants.
Surveillance des processus et contrôle de la qualité pour les techniques avancées
Les techniques spécialisées utilisées pour la fabrication de grands composants nécessitent des systèmes de surveillance et de contrôle de la qualité tout aussi sophistiqués pour garantir des résultats constants.
Pour les processus d'assistance au gaz, un contrôle précis des profils de pression du gaz et des séquences de synchronisation est essentiel. Chez PTSMAKE, nous utilisons des capteurs de pression avancés dans les cavités des moules et des algorithmes de contrôle spécialisés pour optimiser les paramètres de gaz pour chaque pièce.
Les applications de mousse structurelle nécessitent un contrôle minutieux de la température du matériau, de la concentration en CBA et de la vitesse d'injection pour garantir un développement cohérent de la structure cellulaire. Nos systèmes de surveillance des processus suivent ces paramètres en temps réel et procèdent à des micro-ajustements pour maintenir des conditions optimales tout au long des cycles de production.
Les opérations de moulage par empilage exigent une surveillance synchronisée de plusieurs cavités simultanément, avec des paramètres de remplissage et d'emballage équilibrés sur toutes les faces du moule. Des systèmes de vision avancés et des capteurs dans le moule permettent de garantir une qualité constante pour toutes les pièces produites au cours de chaque cycle.
Grâce à ces méthodes de contrôle spécialisées, les fabricants peuvent maintenir des normes de qualité exceptionnelles, même lorsqu'ils produisent des composants massifs à l'aide des techniques de moulage les plus avancées.
Assurance qualité pour les composants moulés surdimensionnés
Vous êtes-vous déjà demandé comment les énormes composants en plastique de votre voiture, de votre machine à laver ou de votre équipement industriel conservaient une précision aussi remarquable ? Derrière chaque grande pièce réussie se cache un système d'assurance qualité aussi impressionnant que la technologie de moulage elle-même.
Garantir la précision dimensionnelle et l'intégrité structurelle des grands services de moulage par injection de plastique nécessite des systèmes de qualité sophistiqués qui combinent des technologies de mesure avancées, des contrôles de processus scientifiques et des protocoles d'inspection rigoureux tout au long du cycle de vie de la production.
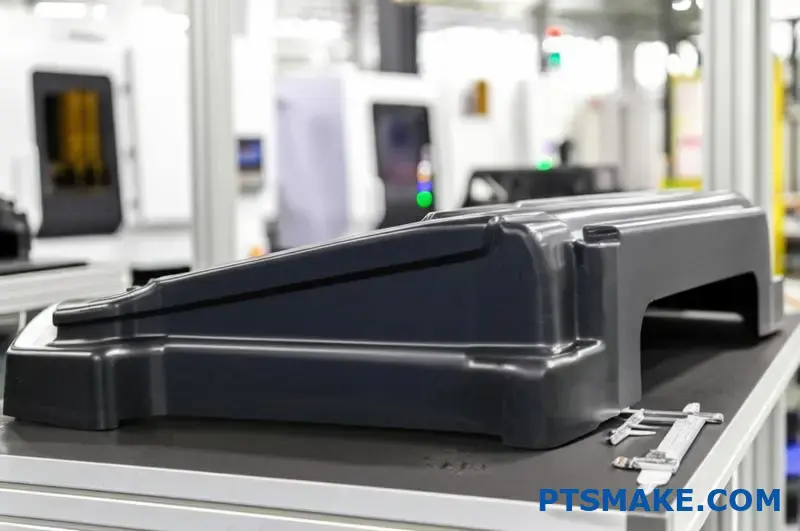
Les défis de la vérification dimensionnelle pour les composants de grande taille
L'assurance qualité des composants plastiques surdimensionnés présente des défis uniques qui vont au-delà des protocoles typiques d'inspection des petites pièces. Lorsqu'il s'agit de pièces dont les dimensions peuvent atteindre plusieurs mètres, les méthodes de mesure traditionnelles sont souvent insuffisantes.
Inspections des machines à mesurer tridimensionnelles (MMT)
La pierre angulaire de la vérification dimensionnelle des grands composants moulés est la machine à mesurer tridimensionnelle (MMT). Ces systèmes sophistiqués utilisent des palpeurs ou des capteurs optiques pour déterminer avec précision les dimensions critiques de pièces massives.
Pour les composants de grande taille, nous utilisons des équipements CMM spécialisés :
- Enveloppes de mesure étendues (jusqu'à 2000 mm x 3000 mm x 1500 mm)
- Algorithmes de mesure compensés en température
- Capacités de balayage multipoint pour les géométries complexes
- Séquencement automatisé des mesures pour une meilleure répétabilité
Le processus CMM génère des rapports d'inspection complets comparant les dimensions réelles aux modèles CAO, avec des cartes de déviation codées en couleur mettant en évidence toutes les zones se situant en dehors des limites de spécification.
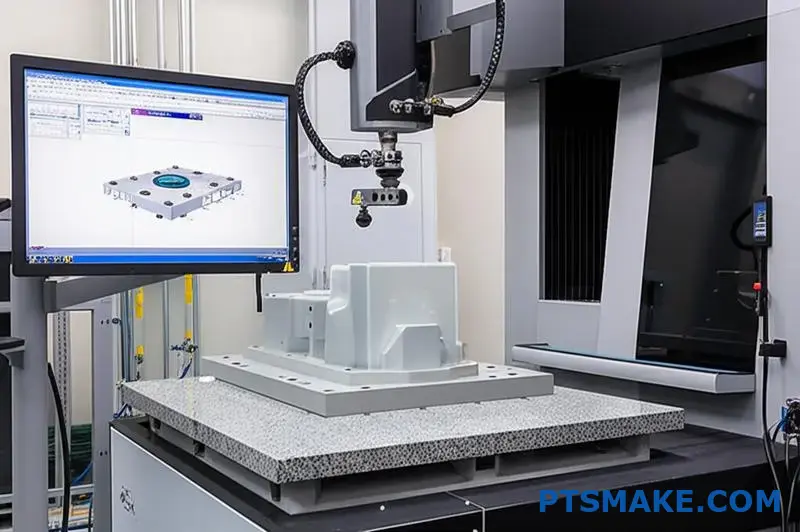
Technologies de balayage laser et de lumière structurée
Si les MMT excellent dans la mesure précise point par point, les nouvelles technologies telles que le balayage laser et les systèmes de lumière structurée offrent des capacités complémentaires particulièrement utiles pour les composants de grande taille :
Technologie | Principaux avantages | Meilleures applications |
---|---|---|
Balayage laser | Collecte rapide de millions de points de données | Surfaces à contours complexes |
Lumière structurée | Analyse plein champ avec une précision submicronique | Inspection détaillée |
Photogrammétrie | Mesure de très grands composants | Panneaux de carrosserie automobile |
Systèmes de vision | Inspection automatisée en temps réel | Production en grande quantité |
Chez PTSMAKE, nous avons découvert que l'intégration de ces technologies crée une approche de mesure complète qui capture les dimensions critiques et la géométrie globale de la pièce avec une précision exceptionnelle.
Gestion des effets thermiques sur les mesures
La gestion des effets thermiques constitue l'un des défis les plus importants de la mesure des grands composants en plastique. Les polymères ont des coefficients de dilatation thermique relativement élevés, ce qui signifie que même de petites variations de température peuvent entraîner des changements dimensionnels mesurables.
Pour vérifier la précision, nous disposons de salles de mesure spécialisées à température contrôlée, étalonnées à 20°C ±1°C (68°F ±1,8°F). En outre, les pièces sont stabilisées dans cet environnement pendant 24 à 48 heures avant l'inspection finale, ce qui garantit l'équilibre thermique.
Contrôles des processus de moulage scientifique
L'assurance qualité pour les grands composants commence bien avant l'inspection - elle commence par la mise en œuvre de principes de moulage scientifiques tout au long du processus de production.
Approche du moulage découplé
La méthodologie de moulage scientifique connue sous le nom de "moulage découplé" sépare le processus d'injection en plusieurs phases distinctes :
- Phase de remplissage: Contrôlé par la vitesse pour assurer le remplissage complet de la cavité
- Phase d'emballage: Pression contrôlée pour compenser le rétrécissement du matériau
- Phase de maintien: Maintenu jusqu'au gel de la vanne pour éviter les retours d'eau
- Phase de refroidissement: Température contrôlée pour une stabilité dimensionnelle
Pour les composants de grande taille, la mise en œuvre correcte de ces phases devient encore plus critique en raison des distances d'écoulement plus longues et du plus grand potentiel de variation sur l'ensemble de la pièce.
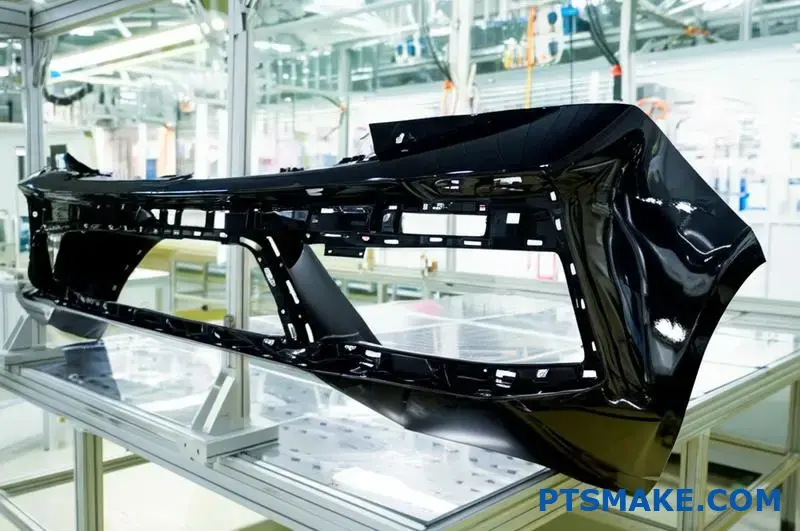
Technologies de détection dans le moule
Les technologies de détection dans le moule, qui fournissent des données en temps réel pendant le processus de moulage, sont extrêmement utiles pour les pièces de grande taille :
- Capteurs de pression de cavité: Contrôler la pression aux points critiques de la cavité
- Capteurs de température: Suivi des températures des moules et des matériaux pendant les cycles
- Jauges de contrainte: Détecter les déformations potentielles de la pièce pendant l'éjection
- Capteurs à front d'écoulement: Vérifier le remplissage complet des cavités dans les zones éloignées
Ces capteurs sont reliés à des systèmes sophistiqués de surveillance des processus qui établissent des fenêtres de fonctionnement acceptables et signalent automatiquement les cycles qui s'écartent des paramètres établis.
Études de capabilité des processus (Cpk)
Pour les grands composants de haute précision, nous menons des études complètes sur la capacité des processus afin de vérifier que nos processus répondent systématiquement aux exigences des spécifications :
- Produire des quantités d'échantillons statistiquement significatives (typiquement plus de 30 pièces)
- Mesurer les dimensions critiques sur plusieurs séries de production
- Calculer les indices de capabilité des processus (Cp et Cpk)
- Viser des valeurs Cpk de 1,33 ou plus pour les dimensions critiques
- Mettre en œuvre des ajustements de processus lorsque les capacités ne sont pas suffisantes
Grâce à ces analyses statistiques, nous pouvons démontrer de manière quantifiable la stabilité des processus et prédire les performances à long terme pour la fabrication de grands composants.
Avancé Contrôle statistique des processus5 Systèmes
Les systèmes de contrôle statistique des processus (CSP) suivent automatiquement les principaux paramètres de qualité tout au long des cycles de production, ce qui permet de détecter rapidement les dérives potentielles avant que les spécifications ne soient enfreintes. Pour les composants de grande taille, nous mettons en œuvre un SPC multi-paramètres qui surveille :
- Dimensions critiques sur les pièces échantillonnées
- Paramètres de processus de la machine de moulage par injection
- Conditions environnementales dans la zone de production
- Propriétés des matériaux des lots entrants
Cette approche globale garantit que tous les facteurs influençant la qualité des grandes pièces restent dans les limites de contrôle établies.
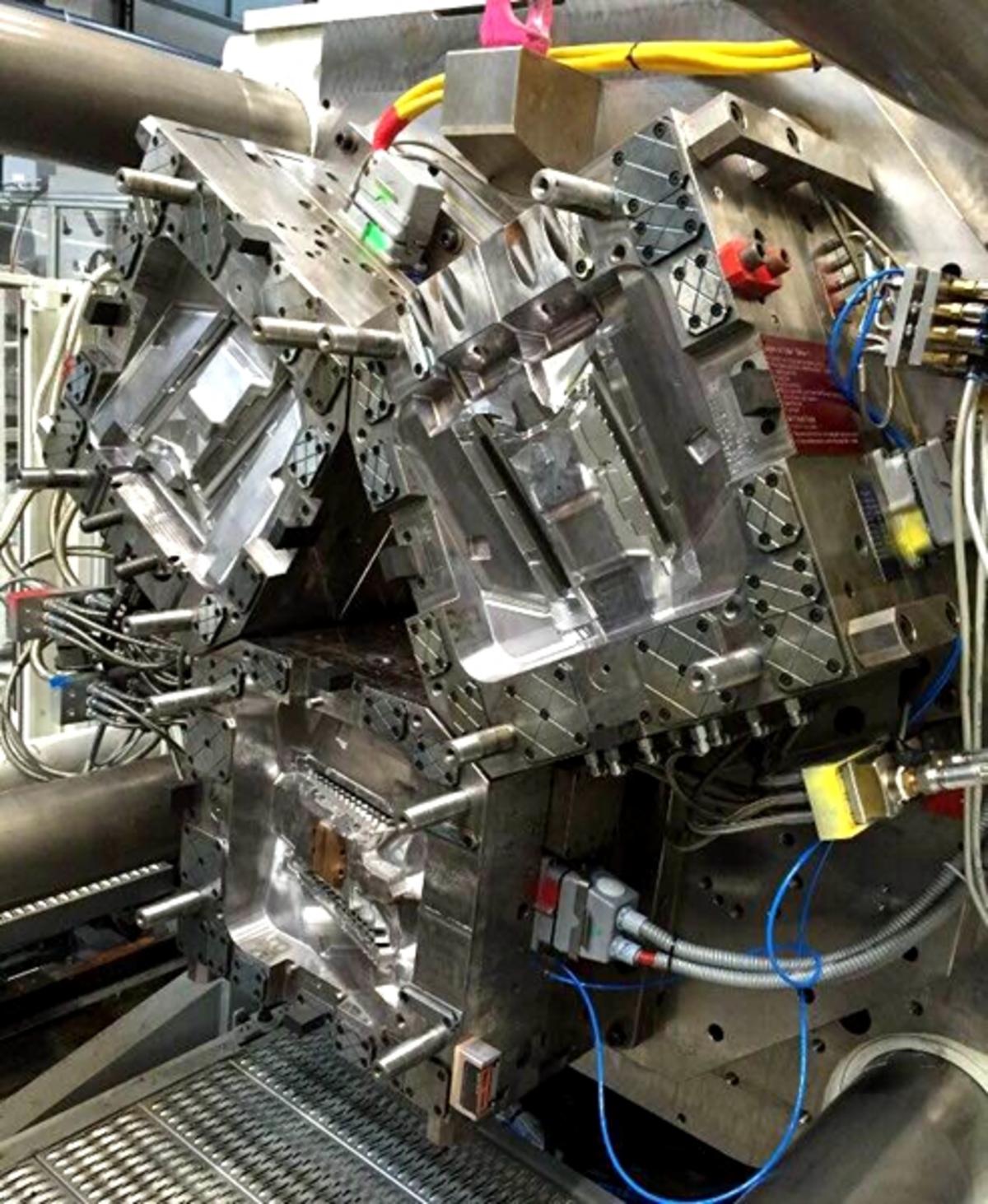
Protocoles d'inspection au titre du premier article (FAI)
L'inspection du premier article représente une étape critique dans la production de grands composants, établissant la base de la vérification ultérieure de la qualité.
Exigences en matière de documentation complète
Pour les composants de grande taille, la documentation FAI est particulièrement rigoureuse et comprend généralement les éléments suivants :
- Rapports de vérification dimensionnelle complets avec toutes les caractéristiques spécifiées
- Documentation sur la certification des matériaux
- Fiches de paramètres de processus détaillant les réglages de la machine
- Normes d'apparence avec échantillons de référence approuvés
- Résultats des essais pour les propriétés mécaniques et physiques
- Documentation sur la traçabilité des matières premières
Ces documents servent de référence de qualité par rapport à laquelle toute la production future sera mesurée.
Plans d'expériences (DOE) pour l'optimisation des processus
Avant de finaliser le processus de production des grands composants, nous réalisons souvent des plans d'expériences structurés afin d'identifier les conditions de traitement optimales :
- Identifier les variables critiques du processus qui affectent la qualité
- Créer des matrices expérimentales en faisant varier ces paramètres
- Produire des pièces d'essai pour chaque ensemble de conditions
- Mesurer les résultats par rapport aux spécifications cibles
- Analyse statistique des résultats pour identifier les paramètres optimaux
- Documenter les résultats dans le rapport FAI
Cette approche scientifique garantit que le processus de production démarre avec des paramètres optimisés plutôt que de dépendre d'ajustements par essais et erreurs.
Processus d'approbation interfonctionnel
L'approbation de la FAI pour les grands composants implique généralement une équipe interfonctionnelle comprenant
- Personnel chargé de l'ingénierie de la qualité
- Représentants de l'ingénierie de fabrication
- Personnel d'ingénierie de conception
- Représentants de la qualité auprès des clients (le cas échéant)
- Spécialistes des matériaux
Cette approche collaborative garantit que toutes les disciplines techniques contribuent au processus de vérification de la qualité avant le début de la production.
Suivi et contrôle permanents de la production
Une fois la production lancée, le maintien de la qualité des grands composants nécessite des systèmes de surveillance et des protocoles d'inspection sophistiqués.
Plans d'échantillonnage pour les grandes séries
Pour les grands composants, nous mettons en œuvre des plans d'échantillonnage personnalisés en fonction des volumes de production et de la criticité :
- La production initiale utilise souvent des niveaux d'inspection plus stricts (niveau II ou III selon ANSI/ASQ Z1.4).
- La vérification statistique permet de passer progressivement à un échantillonnage réduit au fur et à mesure que la stabilité est démontrée.
- Les caractéristiques critiques peuvent nécessiter une inspection 100%, indépendamment de l'historique de production.
- Les systèmes de mesure automatisés permettent d'augmenter les taux d'échantillonnage sans affecter le flux de production
Ces plans établissent un équilibre entre une vérification approfondie et les exigences en matière d'efficacité de la production.
Contrôle non destructif de l'intégrité des structures
Au-delà de la vérification des dimensions, les grands composants sont souvent soumis à des essais non destructifs pour vérifier l'intégrité interne :
- Essais par ultrasons pour détecter les vides ou les incohérences internes
- Inspection par rayons X des zones structurelles critiques
- Imagerie thermique pour identifier les concentrations de contraintes potentielles
- Essais d'émission acoustique pour les composants structurels
Ces techniques permettent d'identifier les problèmes de qualité potentiels qui pourraient ne pas être visibles avec les méthodes d'inspection conventionnelles.
Protocoles avancés d'essai des matériaux
Pour les grands composants, les propriétés des matériaux ont un impact direct sur les performances et la longévité. Notre assurance qualité permanente comprend des tests réguliers sur les matériaux :
- Vérification de la résistance à la traction et de l'allongement
- Essais de résistance aux chocs
- Validation de la température de déviation de la chaleur
- Résistance aux fissures dues aux contraintes environnementales
- Études sur le vieillissement accéléré
En contrôlant les propriétés des matériaux tout au long des cycles de production, nous pouvons détecter les variations subtiles susceptibles d'affecter les performances des composants avant qu'elles n'aient un impact sur les produits finis.
Systèmes de traçabilité pour la gestion de la qualité
La traçabilité complète est particulièrement importante pour les composants de grande taille, dont les volumes de production peuvent être inférieurs mais dont la valeur est nettement supérieure. Notre système de qualité assure une traçabilité complète, y compris
- Documentation sur les lots de matières premières
- Enregistrements des paramètres du processus pour chaque cycle de production
- Identification de l'opérateur et vérification de sa certification
- Registres de maintenance et d'étalonnage des équipements
- Historique complet des données d'inspection
Cette chaîne de traçabilité permet une analyse rapide des causes profondes en cas de problème, ce qui facilite l'amélioration continue des produits et des processus.
Grâce à ces approches globales d'assurance qualité, les grands services de moulage par injection de plastique peuvent fournir en permanence des composants qui répondent aux spécifications les plus exigeantes, garantissant des performances fiables tout au long de leur durée de vie.
Approches stratégiques de la production de grandes pièces
Vous êtes-vous déjà demandé pourquoi certaines grandes pièces en plastique semblent parfaitement conçues alors que d'autres se déforment, se fissurent ou ne tiennent tout simplement pas le coup ? Le secret ne réside pas dans les machines ou les matériaux, mais dans les approches stratégiques de la conception qui font ou défont le succès de la fabrication à grande échelle.
L'optimisation des services de moulage par injection de plastique de grande taille nécessite des stratégies d'ingénierie précises qui équilibrent la conception de l'épaisseur des parois, les angles de dépouille appropriés, les structures de nervures stratégiques et les emplacements d'ouverture soigneusement sélectionnés afin de garantir un remplissage cohérent, un refroidissement uniforme et une stabilité dimensionnelle pour les composants massifs.
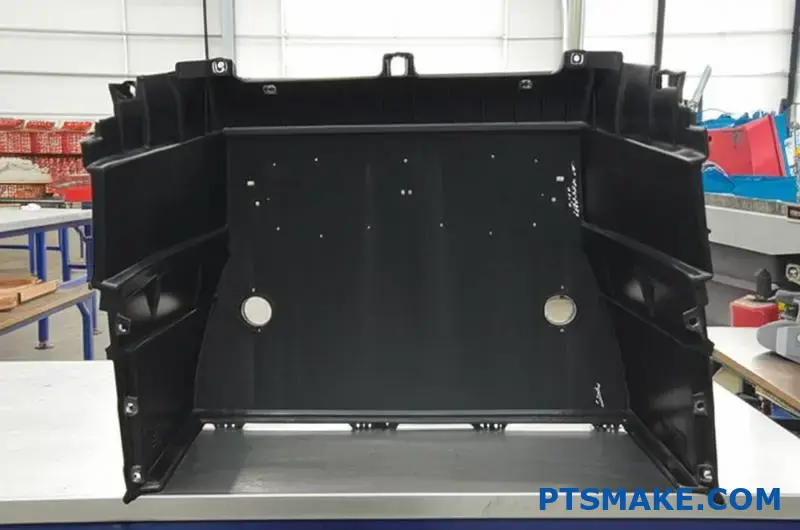
Optimisation de l'épaisseur des parois : La base de la qualité
Lors de la conception de grands composants en plastique, l'épaisseur des parois est peut-être la considération la plus critique. Contrairement aux pièces plus petites où les variations peuvent être tolérées, les grands composants amplifient chaque défaut de conception, ce qui rend l'uniformité de l'épaisseur de paroi essentielle.
Principes d'uniformité d'épaisseur
Le principe de base de la conception des grandes pièces consiste à maintenir une épaisseur de paroi uniforme sur l'ensemble du composant. Cette approche présente plusieurs avantages essentiels :
- Favorise un écoulement régulier du matériau pendant l'injection
- Garantit des taux de refroidissement cohérents sur l'ensemble de la pièce
- Minimise les contraintes internes qui causent le gauchissement
- Réduit les traces d'évier sur les surfaces visibles
- Prévient les faiblesses structurelles liées à l'épaisseur
Chez PTSMAKE, j'ai vu de nombreux projets dans lesquels les clients concevaient initialement des pièces avec des variations d'épaisseur importantes. Ces conceptions ont inévitablement entraîné des problèmes de qualité au cours de la production. En mettant en œuvre des principes d'épaisseur uniforme, nous avons toujours obtenu de meilleurs résultats.
L'épaisseur de paroi idéale pour les grandes pièces se situe généralement entre 2,5 et 3,5 mm pour la plupart des applications, bien que cela puisse varier en fonction de la sélection des matériaux et des exigences structurelles. Lorsque des sections plus épaisses sont inévitables, nous mettons en œuvre des approches stratégiques telles que le carottage, les nervures ou la technologie d'assistance au gaz pour maintenir un refroidissement efficace tout en préservant l'intégrité structurelle.
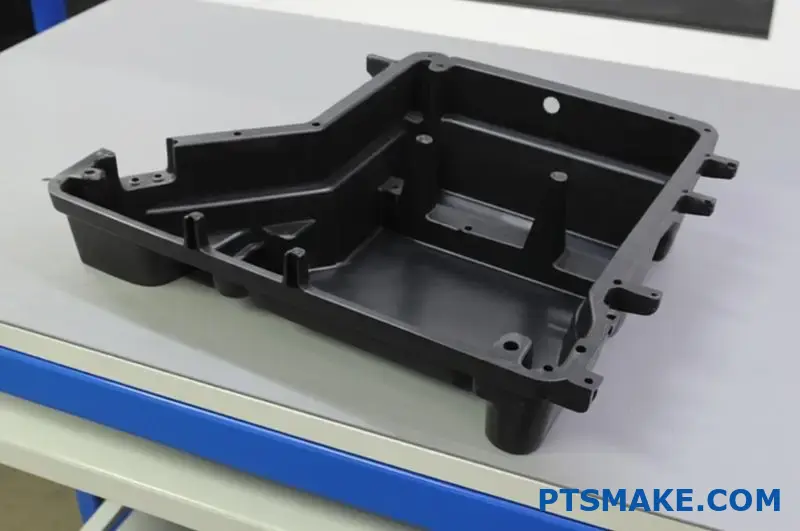
Passage d'une épaisseur à l'autre
Lorsque des transitions d'épaisseur sont inévitables dans des composants de grande taille, il est essentiel de procéder à des changements graduels. La pratique courante consiste à mettre en œuvre des transitions ne dépassant pas 40% de l'épaisseur nominale de la paroi sur une distance d'au moins trois fois l'épaisseur de la paroi.
Par exemple, le passage d'une paroi de 3 mm à une section de 4,2 mm doit se faire sur une distance minimale de 9 mm pour éviter la concentration de contraintes et un refroidissement inégal. Ces transitions progressives sont particulièrement importantes dans les grandes pièces où la différence de refroidissement entre les sections épaisses et minces peut créer des contraintes internes significatives.
Mur nominal | Étape maximale | Distance minimale de transition |
---|---|---|
2,5 mm | 1,0 mm | 7,5 mm |
3,0 mm | 1,2 mm | 9,0 mm |
3,5 mm | 1,4 mm | 10,5 mm |
4,0 mm | 1,6 mm | 12,0 mm |
Cette approche calculée des transitions d'épaisseur permet de maintenir un flux de matière et des caractéristiques de refroidissement cohérents dans les grands composants, ce qui réduit considérablement les défauts dans les pièces finies.
Mise en œuvre de l'angle de dépouille pour une éjection réussie
Les angles de dépouille représentent une autre considération critique qui devient de plus en plus importante à mesure que la taille des pièces augmente. Ces surfaces angulaires facilitent l'éjection en douceur du moule, évitant ainsi les dommages et les déformations au cours du processus de fabrication.
Déterminer les valeurs de repêchage optimales
Pour les grandes pièces en plastique, les angles de dépouille standard s'avèrent souvent insuffisants. Alors que les petites pièces peuvent fonctionner avec un angle de dépouille de 0,5°, les grandes pièces nécessitent généralement un angle de dépouille de 0,5° :
- Tirant d'eau minimum de 1,0° pour les surfaces texturées
- 0,5°-1,5° pour les zones lisses et non texturées
- 2,0°-3,0° pour les nervures et les bossages profonds
- 1,5°-2,5° pour les surfaces à texture légère
Les exigences accrues en matière de dépouille découlent de la plus grande surface de contact entre la pièce et le moule, qui crée une friction proportionnellement plus élevée lors de l'éjection. En outre, les grandes pièces sont plus susceptibles d'être déformées pendant le processus d'éjection, ce qui rend encore plus critique une bonne dépouille.
Considérations sur les projets de directives
Les angles de dépouille doivent être conçus par rapport à la direction d'éjection, ce qui devient plus complexe avec des composants de grande taille et à multiples facettes. Chez PTSMAKE, nous analysons chaque surface individuellement afin de garantir un angle de dépouille approprié par rapport à sa trajectoire d'éjection spécifique.
Pour les géométries particulièrement difficiles, nous mettons souvent en œuvre conceptions de lignes de partage6 qui permettent à des sections de la pièce de se détacher dans des directions différentes, ce qui permet d'obtenir une dépouille correcte de toutes les surfaces tout en maintenant l'intégrité dimensionnelle.
nul
Stratégies de nervures structurelles pour la solidité et la stabilité
Les nervures apportent un soutien structurel essentiel aux composants de grande taille tout en maintenant des épaisseurs de paroi raisonnables. Cependant, une mauvaise conception des nervures peut créer plus de problèmes qu'elle n'en résout, en particulier pour les pièces surdimensionnées.
Rapport entre l'épaisseur de la nervure et la paroi
La règle fondamentale pour la conception des nervures est de maintenir une épaisseur appropriée par rapport à la paroi nominale. Pour les composants de grande taille, nous recommandons généralement :
- Epaisseur de la nervure à 40-60% de l'épaisseur de la paroi adjacente
- Hauteur maximale des nervures de 3x l'épaisseur nominale de la paroi
- Rayon à la base de la nervure égal à 25-30% de l'épaisseur de la paroi
- Tirant d'air supplémentaire d'au moins 0,5° sur les flancs des nervures, au-delà de l'exigence de base
Ces proportions permettent d'équilibrer le soutien structurel par rapport aux marques d'enfoncement potentielles et aux problèmes de refroidissement. Lorsque les nervures sont trop épaisses par rapport à la paroi, elles créent des marques d'enfoncement sur les surfaces opposées ; lorsqu'elles sont trop fines, elles ne fournissent pas un soutien adéquat et peuvent se remplir de manière incomplète pendant le moulage.
Motifs de disposition des nervures pour les grandes surfaces
La disposition des nervures sur de grandes surfaces a un impact significatif sur les performances structurelles et la fabricabilité :
- Motifs de la grille: Fournit un soutien équilibré sur des surfaces planes et étendues
- Dispositions radiales: Idéal pour les sections circulaires ou courbes
- Structures triangulées: Une rigidité maximale avec un minimum de matériau
- Systèmes parallèles: Permettre un flux de matière constant pendant le moulage
Pour les très grandes surfaces planes, nous utilisons souvent une combinaison de systèmes de nervures primaires et secondaires. Les nervures primaires constituent l'ossature structurelle principale, tandis que les nervures secondaires offrent un renforcement localisé dans les zones soumises à de fortes contraintes.
Lors de la conception des nervures, il est particulièrement important de veiller à la cohérence du flux de matériau. Les nervures ne doivent jamais créer d'obstacles qui entravent le flux de matière, car cela peut entraîner des marques d'hésitation, des lignes de soudure ou un remplissage incomplet dans des zones éloignées de grandes pièces.
Conception et placement des vannes pour un flux optimal des matériaux
Aucun aspect de la conception des grandes pièces n'est peut-être plus critique que l'emplacement et la conception appropriés de l'obturateur. L'opercule représente le point d'entrée du plastique fondu dans la cavité du moule, et sa conception influence directement le flux de matière, la distribution de la pression et, en fin de compte, la qualité de la pièce.
Emplacement stratégique des portes pour les pièces massives
Pour les composants de grande taille, il est souvent nécessaire de prévoir plusieurs portes pour assurer un remplissage complet avant la solidification du matériau. L'emplacement stratégique de ces vannes doit être soigneusement étudié :
- Placer les barrières dans des sections plus épaisses lorsque c'est possible
- Maintenir des distances d'écoulement égales aux extrémités de la pièce
- Éviter de placer les barrières sur des surfaces visibles ou esthétiques
- Tenir compte de l'intégrité structurelle à l'endroit où les portes sont reliées à la pièce
- Tenir compte de la formation de lignes de soudure entre les fronts d'écoulement convergents
À l'aide d'un logiciel sophistiqué d'analyse de l'écoulement du moule, nous simulons diverses configurations de portes pour identifier la disposition optimale avant de finaliser la conception de l'outil. Cette approche permet d'éviter les ajustements coûteux par essais et erreurs au cours de la phase d'échantillonnage.
Sélection du type de vanne pour différentes applications
Diverses conceptions de portes offrent des avantages spécifiques pour différentes applications de grandes pièces :
Type de porte | Avantages | Meilleures applications |
---|---|---|
Portes de ventilateur | Large distribution des matériaux | Panneaux plats, grands couvercles |
Portes sous-marines | Suppression automatique des vestiges | Composants avec surfaces cosmétiques |
Portes de bordure | Modèle de remplissage contrôlé | Éléments structurels, cadres |
Portes Hot Tip | Vestiges minimes de la porte | Surfaces visibles nécessitant une finition propre |
Vannes | Contrôle précis de la pression d'injection | Composants critiques avec des tolérances strictes |
Pour les composants de grande taille particulièrement complexes, nous mettons souvent en œuvre un système de vannes séquentielles qui contrôle avec précision le moment de l'injection du matériau à travers plusieurs vannes. Cette approche permet d'optimiser le remplissage, ce qui serait impossible avec les systèmes d'obturation conventionnels.
Conception du système de refroidissement pour la stabilité dimensionnelle
La conception du système de refroidissement devient de plus en plus critique à mesure que la taille des pièces augmente. Les grands composants contiennent beaucoup plus d'énergie thermique et nécessitent des systèmes de refroidissement soigneusement conçus pour maintenir la stabilité dimensionnelle.
Approches de refroidissement équilibrées
Un refroidissement uniforme sur de grandes surfaces empêche le retrait différentiel qui conduit au gauchissement et à l'instabilité dimensionnelle. Les stratégies clés sont les suivantes :
- Maintien d'une distance constante entre le canal de refroidissement et la surface des pièces
- Mise en œuvre de conceptions de refroidissement conformes à la géométrie des pièces
- Création de zones de refroidissement indépendantes pour les zones présentant des profils d'épaisseur différents
- Utilisation de matériaux de moulage à haute conductivité dans les zones critiques
- Mise en place de broches thermiques pour atteindre les zones inaccessibles aux canaux de refroidissement conventionnels
Grâce à ces approches, nous créons des systèmes de gestion thermique équilibrés qui extraient uniformément la chaleur des composants massifs, garantissant ainsi la stabilité dimensionnelle et la cohérence de la production.
Optimisation du temps de refroidissement
La phase de refroidissement représente généralement la partie la plus longue du cycle de moulage, en particulier pour les grandes pièces. Optimiser le refroidissement sans compromettre la qualité nécessite des approches sophistiquées :
- Induction stratégique de turbulences dans les canaux de refroidissement
- Systèmes d'éjection à détection de pression qui détectent la solidification
- Profils de refroidissement à plusieurs niveaux qui s'adaptent tout au long du cycle
- Matériaux avancés à conductivité thermique améliorée
En mettant en œuvre ces techniques, nous avons réussi à réduire les temps de refroidissement de 15-30% pour les grands composants tout en maintenant ou en améliorant la stabilité dimensionnelle.
Grâce à la mise en œuvre stratégique de ces approches de conception, les fabricants peuvent produire avec succès de grands composants en plastique qui répondent aux exigences de qualité et de performance tout en maintenant l'efficacité de la production.
Moulage par injection à service complet : Fabrication de bout en bout
Vous êtes-vous déjà demandé comment ces énormes pièces en plastique de votre voiture, de votre réfrigérateur ou de votre équipement industriel passaient si facilement du concept au produit fini ? Derrière chaque grande pièce en plastique se cache un écosystème de fabrication sophistiqué que peu de gens peuvent voir, mais dont tout le monde profite.
Les services complets de moulage par injection de grandes quantités de plastique offrent des solutions de fabrication complètes en intégrant chaque phase, de la consultation initiale sur la conception à la distribution finale, éliminant ainsi la complexité de la chaîne d'approvisionnement tout en garantissant un contrôle de la qualité cohérent tout au long du cycle de vie de la production.
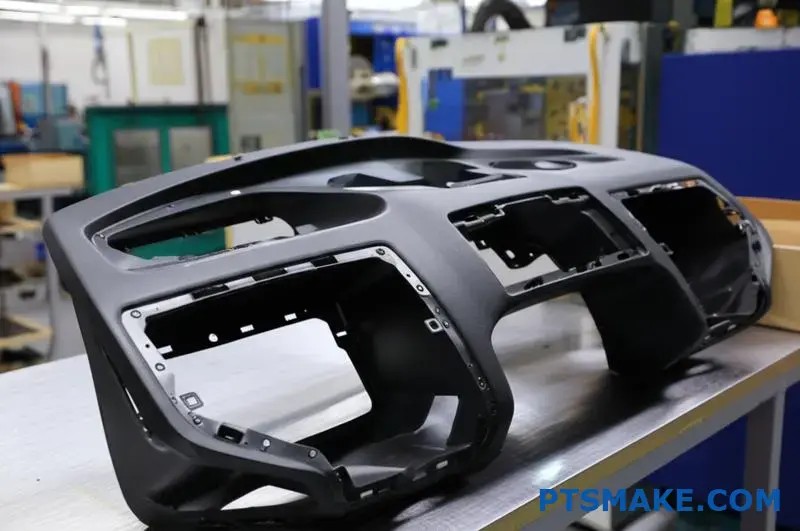
L'avantage de la fabrication intégrée
Lorsqu'il s'agit de produire de grands composants en plastique, les chaînes d'approvisionnement fragmentées posent de nombreux problèmes. Chaque transfert entre différents fournisseurs présente un risque de mauvaise communication, de variation de la qualité et d'allongement des délais. C'est pourquoi les solutions de fabrication globales sont devenues de plus en plus précieuses pour les entreprises qui cherchent à rationaliser la production de pièces plastiques surdimensionnées.
De la consultation en matière de conception à la réalité de la fabrication
Le voyage du concept au produit fini commence par une conception collaborative. Chez PTSMAKE, notre équipe d'ingénieurs travaille directement avec les clients afin d'optimiser les conceptions spécifiquement pour la fabrication de grandes pièces. Cet engagement précoce permet d'identifier et de résoudre les problèmes potentiels avant qu'ils ne deviennent coûteux.
Une véritable approche de service de bout en bout comprend
- Analyse de la conception pour la fabrication (DFM) spécifique aux grands composants
- Consultation sur la sélection des matériaux en fonction des exigences de performance
- Options de prototypage pour la validation du concept
- Optimisation de la conception des outils pour une production efficace
- Des canaux de communication clairs tout au long du processus
Cette approche intégrée élimine les clivages traditionnels entre les bureaux d'études, les outilleurs et les mouleurs - clivages qui conduisent souvent à pointer du doigt lorsque des problèmes surviennent. Au lieu de cela, une seule équipe s'approprie l'ensemble du processus, créant ainsi une responsabilité et une continuité.
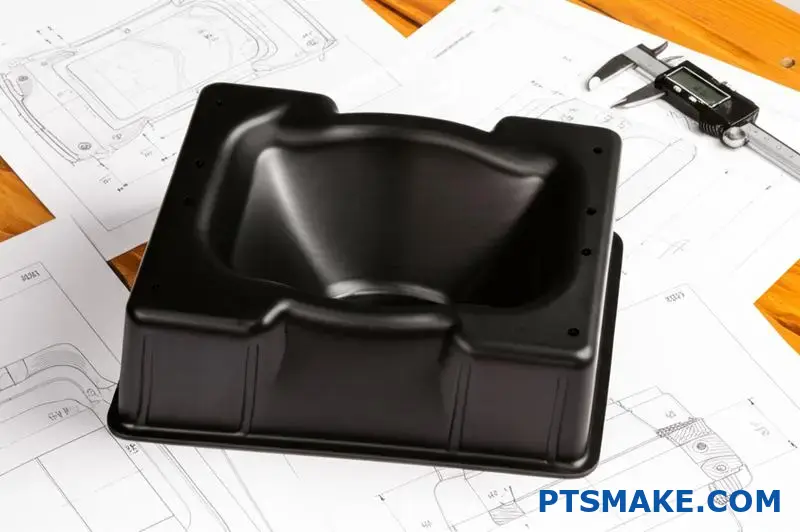
Voies de prototypage pour les composants de grande taille
La validation des conceptions avant de s'engager dans l'outillage de production devient encore plus critique pour les grands composants, pour lesquels les investissements en outillage sont substantiels. Les fournisseurs de services complets proposent plusieurs options de prototypage pour répondre aux différents besoins des projets :
- Prototypage rapide: l'impression 3D, l'usinage CNC ou le moulage sous vide pour visualiser rapidement les concepts
- Outillage de pont: Outils en aluminium ou souples pour les séries limitées
- Du prototype à la production: Approches progressives de l'outillage qui évoluent du prototype à la production finale
Ces options permettent aux fabricants de valider les conceptions, d'effectuer des tests fonctionnels et même de réaliser des essais limités sur le marché avant d'investir dans un outillage de production complet. Pour les grands composants dont les coûts d'outillage peuvent atteindre six chiffres, cette approche réduit considérablement les risques de développement.
Développement d'outils avancés
La réussite de la fabrication de grandes pièces repose sur des systèmes d'outillage sophistiqués conçus spécifiquement pour les applications surdimensionnées.
L'ingénierie à l'échelle
La création d'un outillage pour des composants plastiques de grande taille nécessite une expertise spécialisée qui va au-delà de la fabrication de moules standard. Les éléments clés à prendre en compte sont les suivants :
Défi | Solution stratégique |
---|---|
Distance entre les flux de matières | Systèmes à plusieurs portes avec couloirs équilibrés |
Refroidissement uniforme | Canaux de refroidissement conformes et gestion thermique |
Ejection de pièces | Systèmes d'éjection séquencés pour éviter les distorsions |
Stabilité des moules | Structures en acier renforcées pour éviter les déformations |
Longévité | Sélection d'acier de première qualité pour une durée de vie prolongée de l'outil |
Ces considérations techniques deviennent de plus en plus importantes à mesure que la taille des pièces augmente. Un prestataire de services complet intègre le développement de l'outillage à l'ingénierie des procédés, en veillant à ce que la conception du moule tienne compte à la fois de la géométrie de la pièce et du procédé de fabrication envisagé.
Classe 101 Outil de production
Pour la production en grande série de composants plastiques de grande taille, l'outillage de classe 101 représente la référence. Ces moules de précision sont conçus pour des millions de cycles tout en conservant des tolérances étroites. Les fournisseurs de services complets disposent de capacités d'outillage internes avec des équipements spécialisés pour manipuler des bases de moules massives pesant plusieurs tonnes.
L'intégration des opérations d'outillage et de moulage permet une amélioration continue grâce à des boucles de retour d'information sur la production. Lorsque la même équipe s'occupe à la fois de l'outillage et du processus de moulage, les ajustements peuvent être mis en œuvre rapidement, sans les retards typiques des accords multi-fournisseurs.
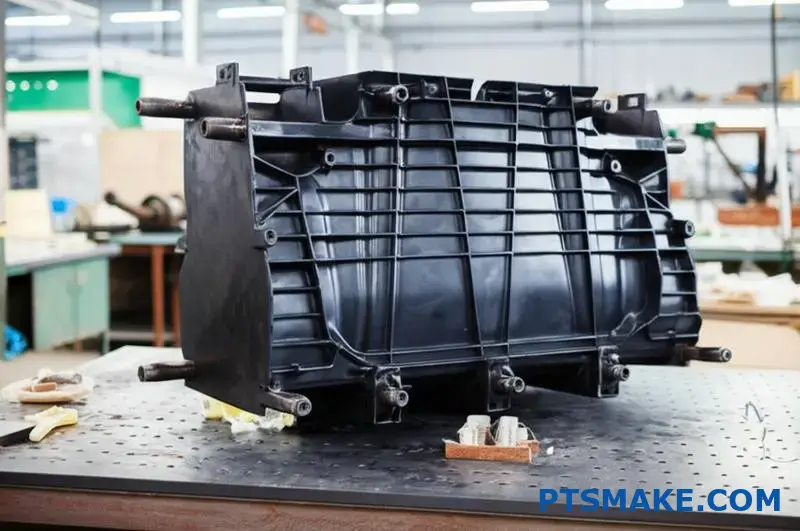
Production Excellence en matière de moulage
Le cœur de toute solution de fabrication est le processus de production lui-même. Pour les grands composants en plastique, cela nécessite un équipement et une expertise spécialisés.
Capacités de moulage par injection à grand tonnage
La production de composants plastiques surdimensionnés nécessite des machines de moulage par injection dont les forces de serrage varient de 500 à 4 000 tonnes. Ces machines massives représentent des investissements substantiels que les fournisseurs spécialisés exploitent dans le cadre de plusieurs projets.
Au-delà de la capacité de la machine brute, la réussite du moulage de grandes pièces nécessite.. :
- Configurations spécialisées des vis et des cylindres pour une préparation cohérente des matériaux
- Systèmes avancés de contrôle des processus pour l'optimisation des paramètres
- Systèmes robotisés d'enlèvement de pièces pour la manipulation de composants lourds
- Contrôle en temps réel pour l'assurance qualité
En centralisant ces ressources spécialisées au sein d'un modèle de service complet, les fabricants peuvent accéder à des capacités dont le coût de développement interne serait prohibitif.
Gestion des matériaux pour la production en série
Les grands composants consomment d'importants volumes de matériaux, ce qui rend une gestion efficace des matériaux essentielle à la maîtrise des coûts et à l'homogénéité de la qualité. Les fournisseurs de services complets mettent en œuvre des systèmes de manutention sophistiqués, notamment
- Stockage des matériaux sous contrôle climatique pour éviter l'absorption d'humidité
- Systèmes automatisés de livraison de matériel pour assurer la cohérence
- Systèmes de séchage central avec plusieurs trémies pour différents matériaux
- Additifs et colorants spécialisés pour des formulations personnalisées
Cette infrastructure permet une production régulière tout en optimisant l'utilisation des matériaux - des considérations cruciales lorsque des pièces individuelles peuvent consommer plusieurs kilogrammes de résines de qualité technique.
Intégration des opérations secondaires
Le parcours de fabrication ne s'achève pas lorsque les pièces sortent de la machine de moulage par injection. Les grands composants nécessitent souvent plusieurs opérations secondaires pour obtenir des produits finis.
Capacités d'assemblage de précision
De nombreux produits complexes nécessitent l'assemblage de plusieurs composants de grande taille. Les solutions de fabrication globales comprennent des capacités d'assemblage adaptées aux pièces surdimensionnées :
- Soudage par ultrasons ou par vibration pour l'assemblage de grandes sections
- Systèmes de fixation mécanique avec contrôle automatique du couple
- Collage d'adhésifs avec des processus de durcissement contrôlés
- Possibilités d'installation d'inserts et de surmoulage
En intégrant les opérations d'assemblage dans le processus de fabrication, les producteurs éliminent le transport entre les installations et maintiennent le contrôle de la qualité tout au long du processus.
Technologies de finition décorative
Les considérations esthétiques jouent souvent un rôle crucial dans les applications de grands composants, en particulier pour les produits de consommation visibles. Les fournisseurs de services complets proposent de multiples options de finition :
- Peinture et revêtement: Couleurs, textures et finitions protectrices personnalisées
- Tampographie: Logos, instructions et marquages réglementaires
- Marquage à chaud: Accents métalliques et identifiants de marque
- Décoration dans le moule: Films et appliques appliqués pendant le moulage
Ces capacités de finition intégrées garantissent un aspect cohérent sur l'ensemble des séries de production tout en éliminant les problèmes logistiques liés à l'expédition de composants de grande taille entre des fournisseurs distincts.
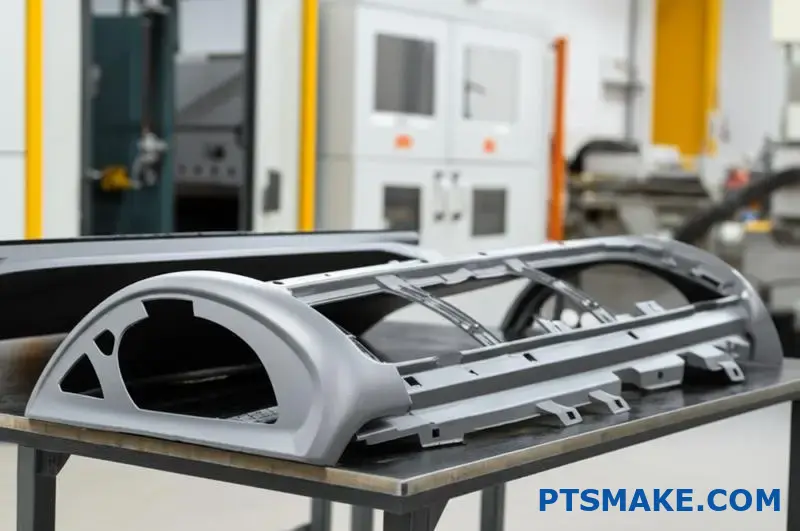
Simplification de la chaîne d'approvisionnement
L'avantage le plus important des solutions de fabrication de bout en bout est peut-être la simplification radicale de la logistique de la chaîne d'approvisionnement.
Systèmes de gestion des stocks
Les fournisseurs de services complets mettent en œuvre des systèmes complets de gestion des stocks qui permettent de suivre les composants tout au long du processus de production. Ces systèmes fournissent
- Visibilité en temps réel des stocks de produits en cours
- Déclenchement automatisé des commandes de matières premières
- Gestion des produits finis en fonction des besoins du client
- Données historiques pour l'optimisation de la planification de la production
Pour les fabricants de grandes pièces en plastique, une gestion efficace des stocks a un impact direct sur la trésorerie et la réactivité aux demandes du marché.
Distribution et soutien logistique
L'acheminement de composants plastiques massifs depuis les installations de production jusqu'aux utilisateurs finaux présente des défis uniques. Les fournisseurs de services complets proposent des solutions logistiques intégrées qui répondent aux exigences spécifiques des pièces surdimensionnées :
- Emballage sur mesure conçu pour la protection des composants
- Expédition groupée pour minimiser les coûts de transport
- Réseaux logistiques mondiaux pour la distribution internationale
- Options d'entreposage pour les programmes de livraison juste à temps
En consolidant ces fonctions au sein d'une relation de service unique, les fabricants réduisent les frais administratifs tout en améliorant la fiabilité de la chaîne d'approvisionnement.
L'assurance qualité tout au long de la chaîne de valeur
Le maintien d'une qualité constante dans des processus de fabrication complexes nécessite la gestion systématique de la qualité7 intégrée à chaque étape.
Systèmes unifiés de qualité
Les solutions de fabrication de bout en bout mettent en œuvre des systèmes de qualité unifiés qui maintiennent la cohérence depuis la conception initiale jusqu'à la livraison finale. Ces systèmes comprennent généralement
- Des processus de contrôle des documents qui garantissent l'actualisation des spécifications
- Protocoles de certification et de traçabilité des matériaux
- Contrôle en cours de fabrication avec maîtrise statistique des processus
- Vérification finale par rapport aux exigences du client
- Systèmes d'action corrective en boucle fermée
Cette approche unifiée permet d'éviter les ruptures de qualité fréquentes dans les chaînes d'approvisionnement fragmentées, où des normes ou des systèmes de qualité différents peuvent être appliqués à différents stades.
Programmes d'amélioration continue
Les partenaires industriels les plus efficaces mettent en œuvre des programmes structurés d'amélioration continue qui conduisent à une optimisation permanente. Ces programmes s'appuient sur les données collectées tout au long du processus de fabrication pour identifier les possibilités d'amélioration :
- Réduction du temps de cycle grâce à l'optimisation des processus
- Amélioration de l'utilisation des matériaux pour réduire les coûts
- Amélioration de la qualité par l'élimination des défauts
- Gains d'efficacité énergétique grâce à l'optimisation des équipements
Cet engagement en faveur de l'amélioration continue garantit que les processus de fabrication évoluent et s'améliorent tout au long du cycle de vie des produits, apportant ainsi une valeur croissante au fil du temps.
En intégrant ces capacités globales au sein d'une relation de fabrication unique, les entreprises produisant de grands composants en plastique peuvent obtenir des avantages concurrentiels significatifs grâce à des cycles de développement plus rapides, une qualité constante et un coût total de possession optimisé.
Découvrez comment les systèmes de surveillance améliorent la qualité des pièces et réduisent les coûts. ↩
Découvrez comment la simulation informatique optimise les schémas de flux de matériaux et améliore la qualité des pièces. ↩
Découvrez comment la combinaison de différents types de fibres permet d'améliorer de manière synergique les performances des grands composants. ↩
Découvrez comment la réduction des variations de processus permet d'améliorer l'homogénéité des pièces et d'augmenter les rendements. ↩
Apprenez comment les méthodes statistiques permettent d'identifier les tendances du processus avant qu'elles ne deviennent des problèmes de qualité. ↩
Explorer les techniques avancées de création de plans de joint complexes dans les conceptions de moules de grande taille. ↩
Découvrez comment les approches unifiées de la qualité réduisent les défauts et améliorent la cohérence de la production. ↩