China HDPE Injection Molding Factory Direct Services
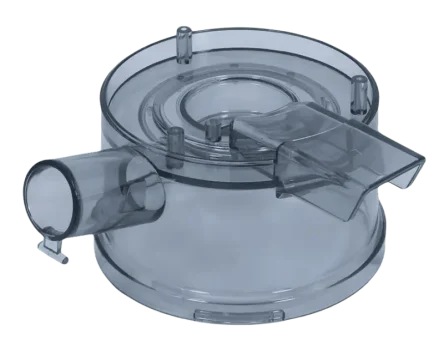
LOW MOQ 100 PCS
50% Cost Savings vs US/EU
Fast Turnaround & Global Shipping
Machines Ranging From 30 Tons to 1,600 Tons






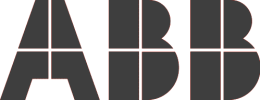

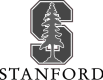
What Our Clients Say
Our clients are located worldwide, and their feedback speaks for itself. If you’d like to verify our reputation with customers in your area, don’t hesitate to contact us—we’d be happy to connect you with them and share relevant case studies.
Top 8 Industries Using HDPE Injection Molding
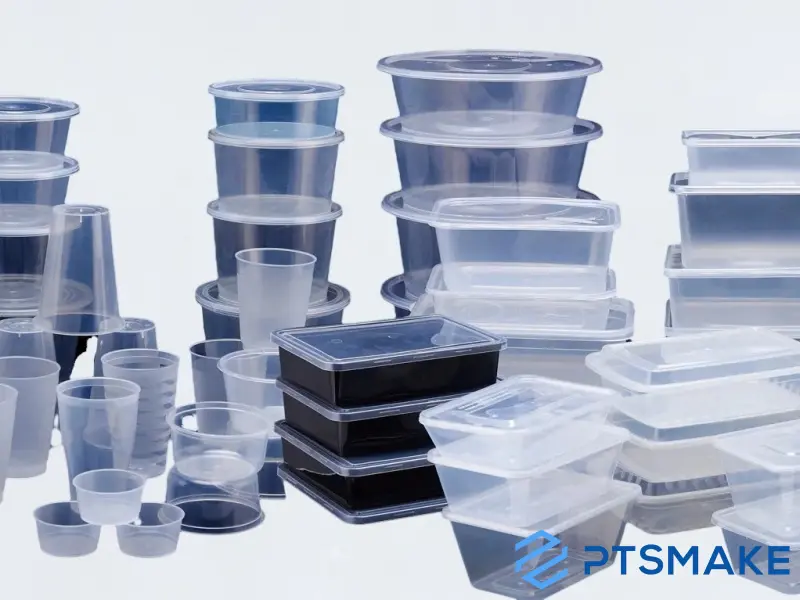
Packaging Industry
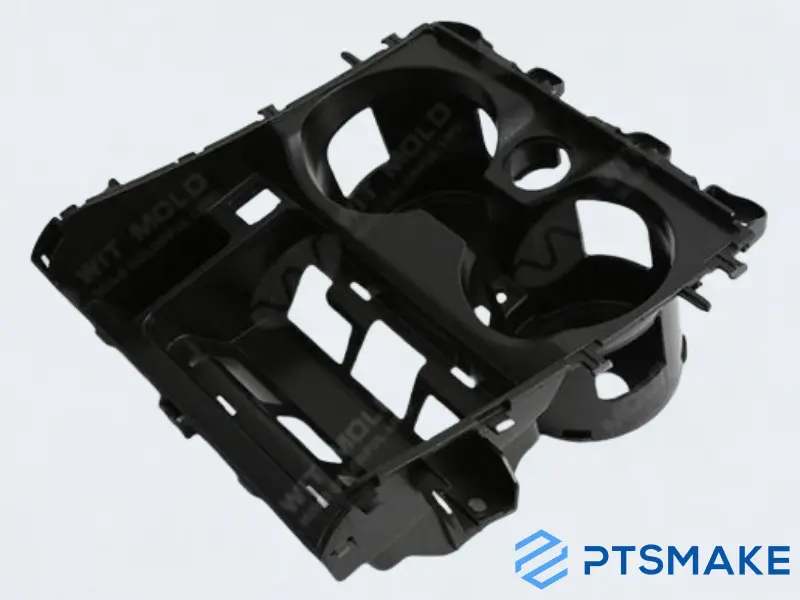
Automotive
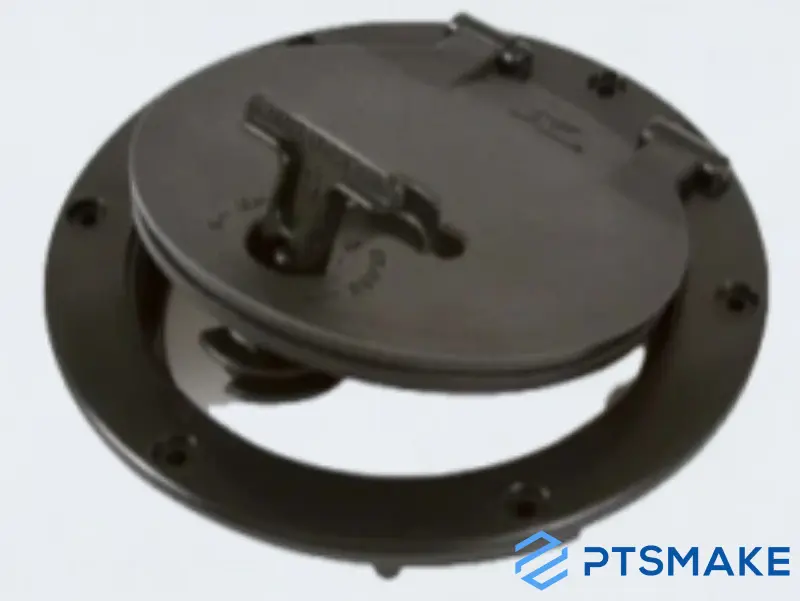
Medical
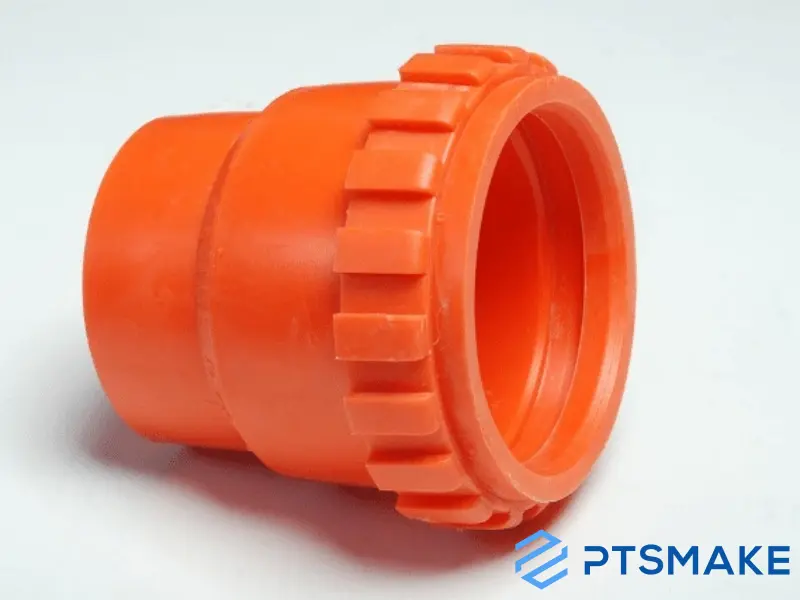
Construction
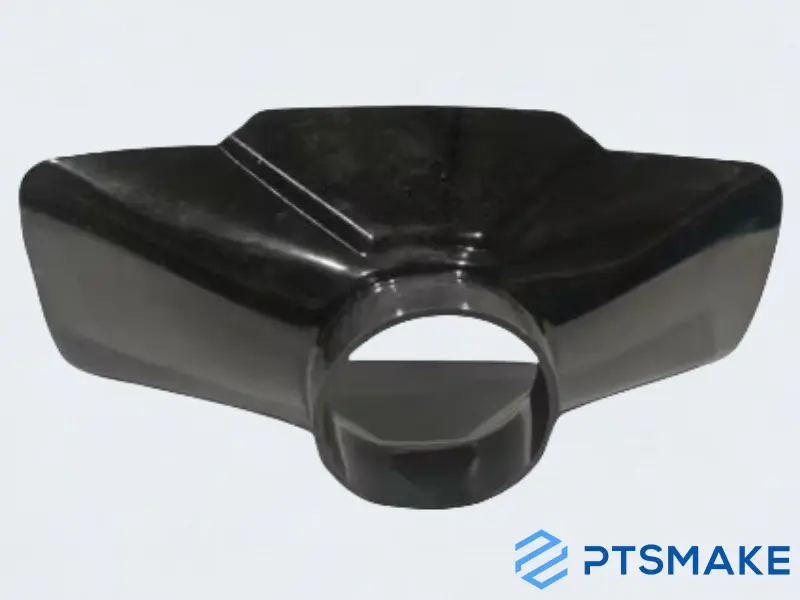
Consumer Goods
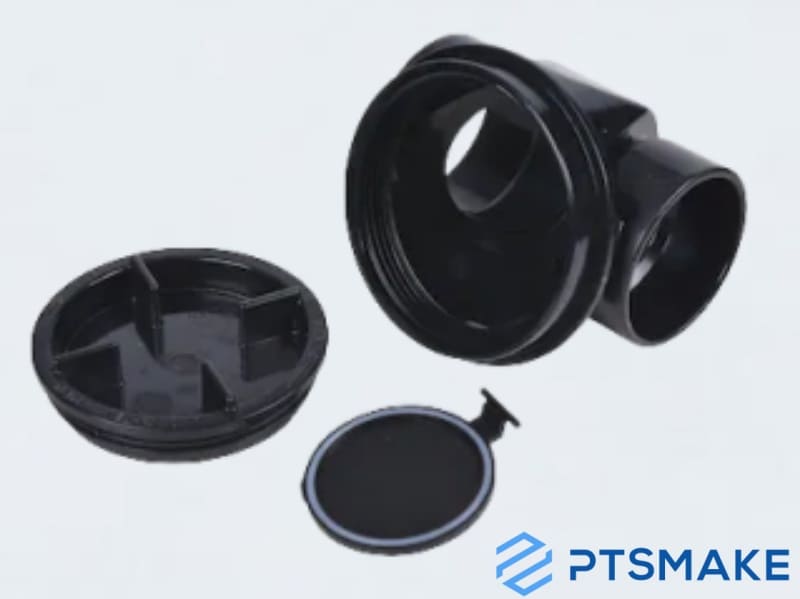
Agricultural
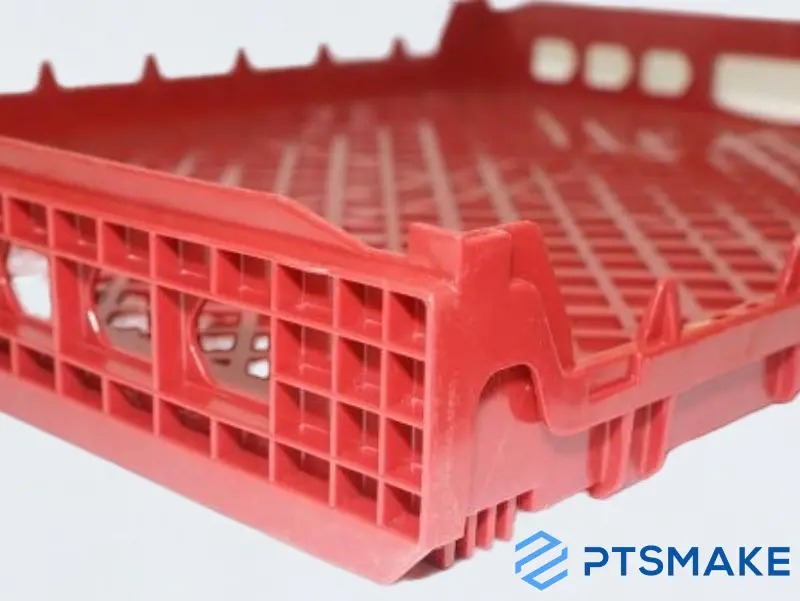
Industrial
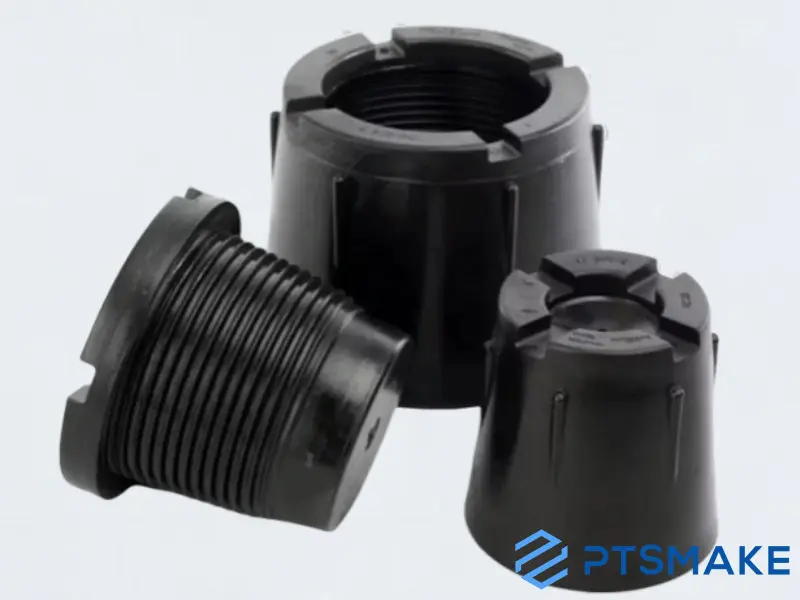
Sporting
Why Choose PTSMAKE for HDPE Injection Molding?
ISO 9001 certified with <0.01mm precision and 99.8% pass rate on first inspection across all manufacturing processes.
Utilizing advancedmachines, we ensure dimensional accuracy and optimize designs, reducing production costs by up to 30%.
22+ years specialized experience with engineering team of 30+ professionals handling complex projects across 8 major industries.
Strategic China location reduces costs by 30-40% while maintaining global quality standards and offering volume-based discounts .
Quality Control for HDPE Injection Molding
Rigorous material testing starts our quality control process. We test every batch of HDPE for proper density (0.941-0.960 g/cm³) and tensile strength (20-37 MPa) to prevent warping and ensure consistent part quality.
Temperature precision is critical for preventing defects. Our systems maintain melt temperatures between 246-280°C and mold temperatures at 45-65°C, with ±5°C tolerance to eliminate shrinkage issues that can reach up to 4% with HDPE.
Multi-stage inspections catch problems early. We perform 100% visual inspection, conduct dimensional verification on 10% of production using precision calipers (±0.02mm accuracy), and utilize advanced warpage detection systems to address HDPE’s high thermal expansion coefficient (143 μm/°C).
In-Process & Final Inspections: Quality checks occur throughout production. We conduct First Article Inspection (FAI), hourly in-process dimensional checks using calipers and gauges, and a 100% visual inspection on final parts. CMM measurements verify critical dimensions against your drawings.
Comprehensive documentation ensures traceability. Every batch receives a unique ID with complete processing parameters, inspection results, and material certification, addressing concerns about inconsistency across production runs.
- With 20+ years of experience and ISO 9001-certified workflows, PTSMAKE delivers high quality overmolding and insert molding solutions you can trust. Our 24/7 engineering support team resolves issues 3x faster than industry averages.
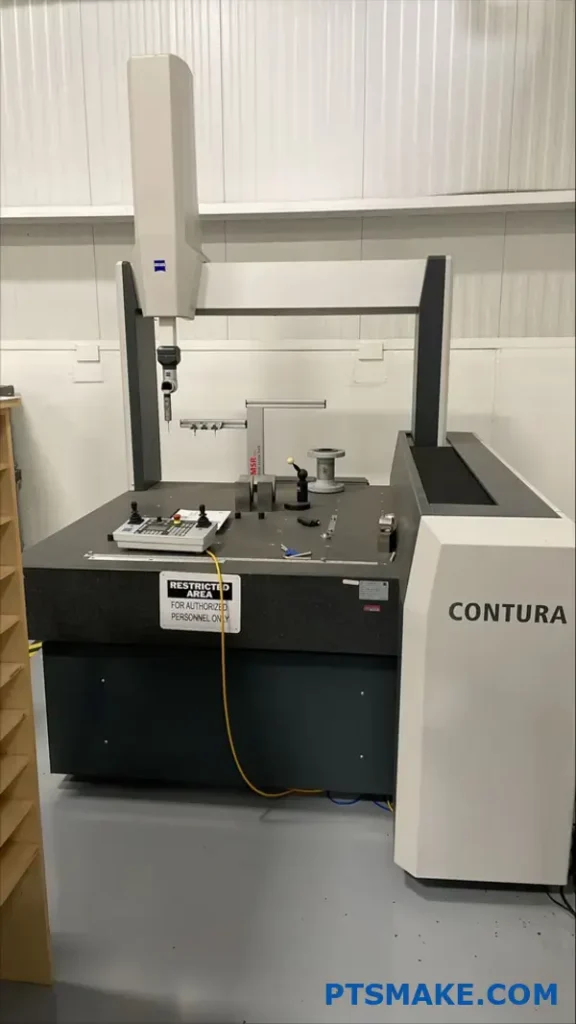
"The durability and finish on the casings for our new consumer gadget are fantastic. PTSMAKE understood our design needs and delivered exactly what we envisioned. We highly recommend their service.
Antoine, Product Designer, France"
Most Common Materials for HDPE Injection Molding
General HDPE
High Impact HDPE
Food Grade HDPE
High Stiffness HDPE
UV Resistant HDPE
Chemical Resistant HDPE
Medical Grade HDPE
High Flow HDPE
Understanding Typical Lead Times for ABS Injection Molding
- General lead times for HDPE injection molding projects can vary significantly. Creating the initial injection mold often takes the most time, typically ranging from 4 to 8 weeks, sometimes longer for highly complex designs.
- The complexity of your HDPE part design directly impacts mold manufacturing time. Simple geometries allow for faster mold creation. Intricate details or tight tolerances require more precise machining, extending this phase.
- Once your custom injection mold is ready and approved, actual HDPE part production begins. Lead time here depends heavily on the order quantity. Small prototype runs might take days, while large-scale production runs require several weeks.
- Material availability for specific HDPE grades can also influence the schedule. While HDPE is common, specialized grades might have longer procurement times. PTSMAKE works diligently to source materials efficiently for your project.
- Finally, required quality control checks and any post-processing steps like assembly or special finishing add to the overall lead time. PTSMAKE provides clear timelines, factoring in all stages from initial design review to final shipment.
- As your partner since 2002, PTSMAKE focuses on transparent communication regarding lead times for all our precision injection molding services, ensuring you can plan effectively from prototype to full production.
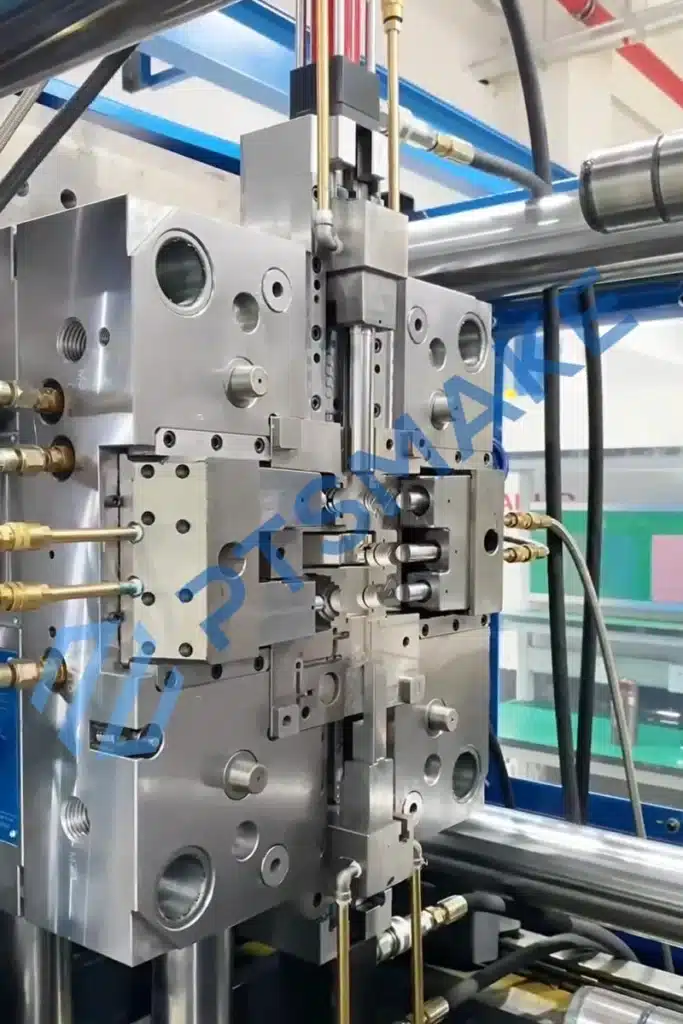
8 Essential Steps for ABS Injection Molding
1. Material Selection
2. Mold Design
3. Material Preparation
4. Machine Setup
5. Injection Process
6. Cooling Phase
7. Part Ejection
8. Quality Inspection
Request a Custom Quote Today
Get an accurate estimate for your project today. Let us help you meet your exact specifications.
Cost-Effective Solutions for HDPE Injection Molding
1. Optimize Part Design (DFM)
2. Simplify Complex Features
3. Ensure Uniform Walls
4. Specify Realistic Tolerances
5. Incorporate Proper Draft
6. Minimize Undercuts
7. Utilize Multi-Cavity Molds
8. Consider Family Molds
9. Partner for Manufacturing Expertise
Customization Options for HDPE Injection Molding
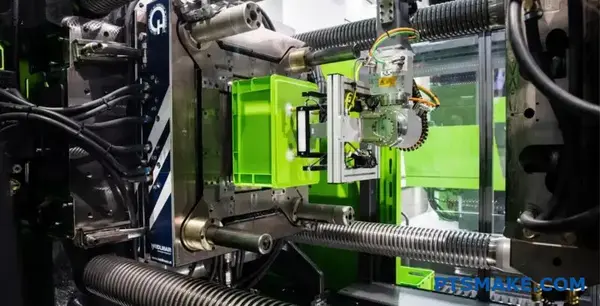
Material Customization
Color Customization
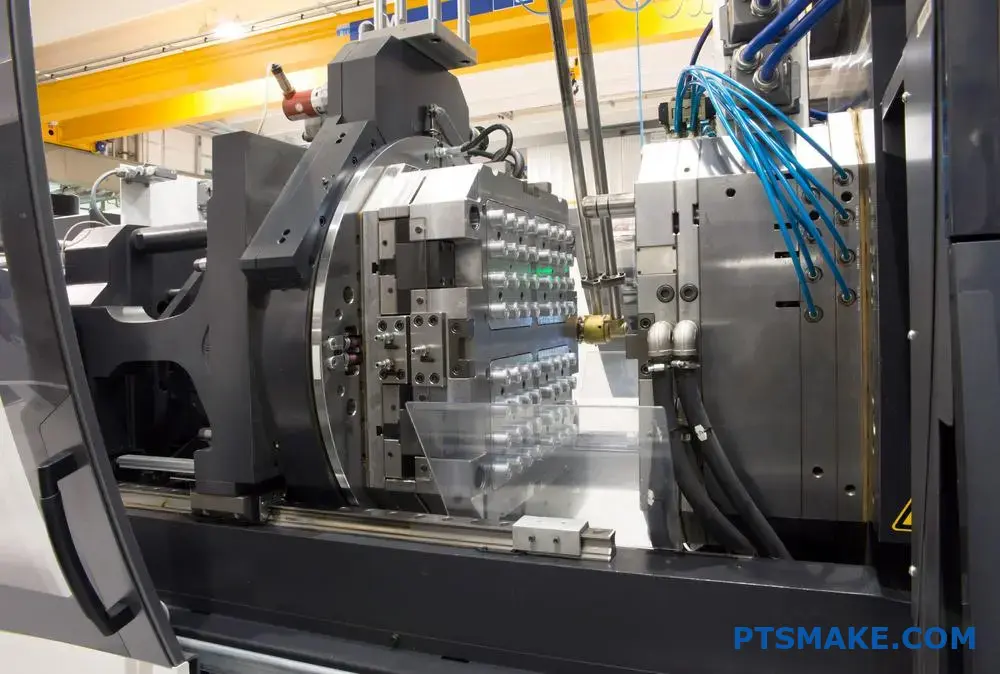
Surface Finish Customization
No Geometry Limits
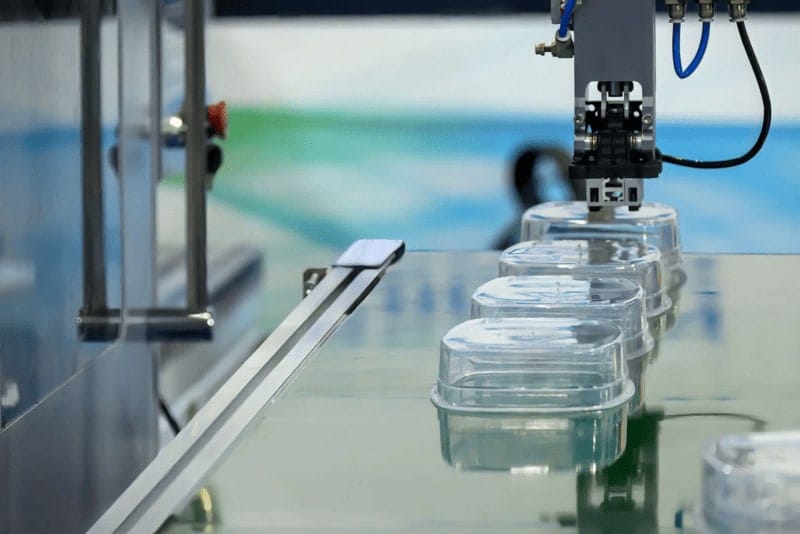
Volume Flexibility
Insert Integration
HDPE Injection Molding Success Stories
Heavy-Duty Storage Solutions in USA
Client Type: Producer of Heavy-Duty Storage Solutions
Client Country: United States
Client’s Problem: This large US company required millions of very durable, stackable HDPE crates each year for industrial and retail markets. Their existing supplier consistently failed to maintain uniform wall thickness in the crates. This resulted in warping when the crates were loaded and unstable stacking, causing problems in warehouses and on retail shelves. Batch-to-batch color consistency was also poor. Furthermore, frequent delivery delays from the supplier were disrupting their commitments to retail partners. They needed a dependable *HDPE injection molding* specialist capable of high-volume, high-quality production.
Our Solution: PTSMAKE approached this high-volume challenge strategically. We designed and built robust, multi-cavity *plastic injection molds* specifically optimized for fast cycle times and perfectly uniform melt distribution. We incorporated a hot runner system into the mold design to improve flow control, reduce material waste, and shorten cycle times further. To address the wall thickness issue, we implemented automated in-process monitoring using sensors during molding. For color consistency, we established strict quality control checks for incoming HDPE material and color masterbatch, along with precise process parameter control during *injection molding*. Our production planning team worked closely with the client’s forecast to ensure smooth, on-time deliveries.
The Result: PTSMAKE consistently delivered HDPE crates that met all strength, dimensional, and stackability specifications. The color was uniform across all batches. Our production efficiencies allowed us to meet the demanding volume requirements while staying within the client’s cost targets. The reliable supply chain eliminated the previous stock-out issues at retail locations. The client specifically praised PTSMAKE’s proactive communication, quality focus, and seamless handling of *large-volume production*, allowing their procurement team to focus on other strategic tasks.
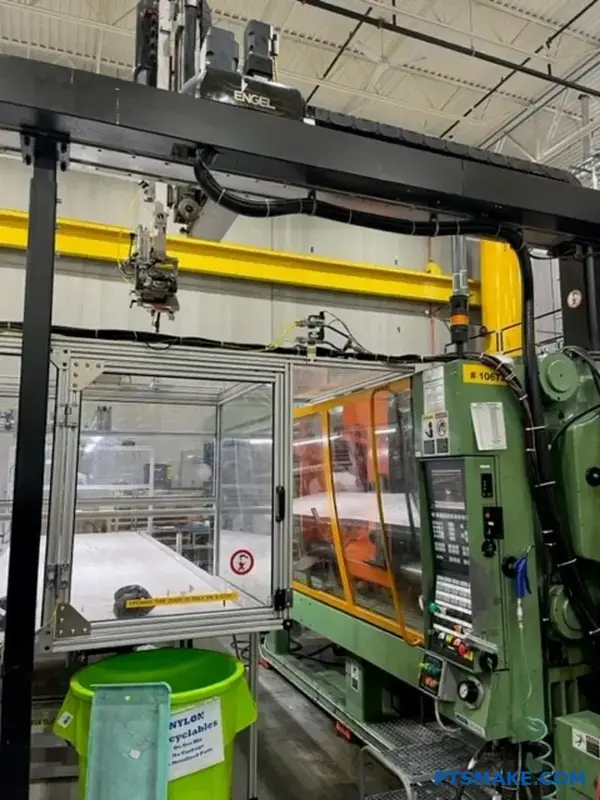
Contact Custom HDPE Injection Molding Expert Today!
We look forward to the opportunity to work with you and contribute to your project’s success.