State lottando per trovare il materiale giusto per applicazioni impegnative in cui le materie plastiche standard falliscono? Molti ingegneri devono affrontare sfide quando i componenti devono resistere a temperature estreme, sostanze chimiche o sollecitazioni meccaniche. I materiali plastici tradizionali non sono in grado di resistere, causando frequenti guasti ai componenti e costose sostituzioni.
La lavorazione del PEEK è il processo di taglio, foratura e sagomatura del materiale polietereterchetone (PEEK) mediante macchine CNC. Questo materiale termoplastico ad alte prestazioni offre un'eccezionale resistenza al calore fino a 480°F, una straordinaria resistenza chimica e una forza paragonabile a quella di alcuni metalli.
Ho lavorato con innumerevoli clienti che sono passati alla lavorazione del PEEK per i loro componenti critici. I risultati parlano da soli: pezzi più duraturi, migliori prestazioni in ambienti difficili e cicli di manutenzione ridotti. Se vi state chiedendo se il PEEK possa essere la soluzione per la vostra applicazione, continuate a leggere per scoprire le proprietà uniche e le tecniche di lavorazione che rendono questo materiale così prezioso nella produzione di precisione.
Il PEEK è migliore del Delrin per la lavorazione?
Vi è mai capitato di trovarvi nel bel mezzo di un dilemma sulla scelta del materiale, indecisi tra PEEK e Delrin per un progetto di ingegneria critico? Quando le prestazioni sono importanti e il fallimento non è un'opzione, la scelta del materiale plastico sbagliato può portare a un'usura prematura, a tempi di fermo delle apparecchiature e a costose riprogettazioni.
Mentre il PEEK offre una resistenza superiore alla temperatura (fino a 480°F), un'eccezionale stabilità chimica e una maggiore forza, il Delrin (POM) offre una migliore lavorabilità, stabilità dimensionale e costi inferiori. La scelta "migliore" dipende esclusivamente dai requisiti applicativi specifici e dai vincoli di budget.
Conoscere il PEEK e il Delrin: Differenze fondamentali
Quando si confrontano questi due tecnopolimeri ad alte prestazioni, è importante comprenderne la composizione e le caratteristiche di base. Il PEEK (Polietereterchetone) è un termoplastico semicristallino con un'eccezionale resistenza alla degradazione termica, mentre il Delrin (Poliossimetilene o POM) è un omopolimero acetalico noto per la sua eccellente stabilità dimensionale.
Confronto tra le proprietà dei materiali
Le proprietà fisiche e meccaniche di questi materiali influenzano in modo significativo le loro caratteristiche di lavorazione e le prestazioni nell'uso finale.
Proprietà | SETTIMANA | Delrin (POM) |
---|---|---|
Temperatura di deflessione del calore | 315°F (157°C) | 257°F (125°C) |
Resistenza alla trazione | 14.500 psi | 10.000 psi |
Resistenza chimica | Eccellente (resiste alla maggior parte degli acidi e delle basi) | Buono (vulnerabile agli acidi forti) |
Resistenza all'usura | Superiore | Molto buono |
Fattore di costo | 4-5 volte superiore a quello del Delrin | Moderato |
Densità | 1,32 g/cm³ | 1,41 g/cm³ |
Caratteristiche di lavorazione: Come si comportano sotto l'utensile
Nella mia esperienza all'PTSMAKE, ho scoperto che la lavorabilità è spesso il fattore decisivo nella scelta tra questi materiali. Il Delrin in genere si lavora in modo più prevedibile rispetto al PEEK, producendo finiture superficiali più lisce con meno sforzo.
Usura dell'utensile e parametri di taglio
Il PEEK è più abrasivo sugli utensili da taglio e richiede cambi di utensili più frequenti. Quando lavoriamo il PEEK, in genere riduciamo le velocità di taglio di circa 15-20% rispetto al Delrin per minimizzare l'accumulo di calore. Questo aspetto è fondamentale perché la bassa conducibilità termica del PEEK provoca una concentrazione di calore nella zona di taglio, causando potenzialmente deformazione termica1 se non gestita correttamente.
Il Delrin, invece, offre un'eccellente stabilità dimensionale durante la lavorazione e può essere tagliato a velocità più elevate. Inoltre, produce una minore usura degli utensili e in genere richiede un minor numero di tecniche di lavorazione specializzate.
Considerazioni sulla finitura della superficie
Un vantaggio del Delrin è la capacità di ottenere eccellenti finiture superficiali con parametri di lavorazione standard. Il PEEK spesso richiede ulteriori fasi di lucidatura per ottenere una qualità superficiale paragonabile.
Analisi costi-benefici per applicazioni ingegneristiche
La differenza di costo tra questi materiali può essere sostanziale. Il PEEK costa in genere 4-5 volte di più del Delrin, per cui è importante valutare se le sue proprietà superiori giustificano l'investimento.
Quando il PEEK giustifica il suo prezzo premium
Raccomando il PEEK per le applicazioni che prevedono:
- Temperature di esercizio estreme (oltre 250°F)
- Ambienti chimici aggressivi
- Elevato carico meccanico a temperature elevate
- Applicazioni mediche o aerospaziali che richiedono biocompatibilità o resistenza alla fiamma
Quando il Delrin è la scelta migliore
Il Delrin ha più senso dal punto di vista economico quando:
- Le temperature di esercizio rimangono inferiori a 180°F
- L'esposizione chimica è limitata a solventi moderati
- La sensibilità ai costi è un fattore importante
- I pezzi richiedono un'eccellente stabilità dimensionale e precisione di lavorazione.
- Gli elevati volumi di produzione rendono il costo dei materiali un fattore significativo
Considerazioni specifiche per il settore
I diversi settori industriali danno priorità alle diverse proprietà dei materiali. Nel settore aerospaziale, dove abbiamo fornito numerosi componenti, la resistenza alla fiamma e l'eccezionale rapporto forza-peso del PEEK spesso giustificano il suo costo più elevato. Per le applicazioni automobilistiche, la combinazione di costo ragionevole e buone proprietà meccaniche del Delrin è spesso vincente.
Applicazioni mediche e alimentari
Per i dispositivi medici, la biocompatibilità e la resistenza alla sterilizzazione del PEEK lo rendono prezioso, nonostante il sovrapprezzo. Nelle apparecchiature per la lavorazione degli alimenti, la conformità alla FDA e il costo inferiore del Delrin ne fanno spesso la scelta preferita, a meno che non si tratti di temperature elevate.
Componenti per macchinari industriali
Nelle applicazioni industriali, ho visto che la decisione si riduce spesso alle condizioni operative. Gli ingranaggi, i cuscinetti e i componenti soggetti a usura che operano in condizioni moderate si comportano in modo eccellente con il Delrin, mentre quelli esposti a condizioni estreme beneficiano delle proprietà superiori del PEEK.
La scelta giusta per la vostra applicazione
La scelta tra PEEK e Delrin deve essere guidata da un'analisi approfondita delle condizioni operative specifiche. Noi di PTSMAKE consideriamo:
- Temperatura massima di esercizio
- Profilo di esposizione chimica
- Requisiti di carico meccanico
- Vincoli di bilancio
- Aspettative di vita utile
Valutando attentamente questi fattori rispetto alle proprietà di ciascun materiale, è possibile prendere una decisione informata che bilanci le prestazioni e il rapporto costo-efficacia per la vostra specifica applicazione.
Qual è la differenza tra acetale e PEEK?
Avete mai lottato per scegliere tra acetale e PEEK per i vostri componenti tecnici critici? Quando il successo di un progetto dipende dalla scelta del materiale, la scelta sbagliata può portare a guasti prematuri, tempi di inattività imprevisti e riprogettazioni che avrebbero potuto essere evitate con una conoscenza adeguata del materiale.
L'acetale (POM) e il PEEK si differenziano principalmente per le caratteristiche prestazionali e il costo. Il PEEK offre una resistenza termica superiore (480°F contro 180°F), una migliore resistenza chimica e una maggiore forza, mentre l'acetale offre un'eccellente lavorabilità, stabilità dimensionale e un costo decisamente inferiore, che lo rende ideale per le applicazioni meno impegnative.
Differenze chiave tra acetale e PEEK
Comprendere le differenze fondamentali tra questi due tecnopolimeri è fondamentale per prendere decisioni informate per i vostri progetti. Entrambi i materiali si sono affermati come opzioni di punta nella produzione di precisione, ma servono a scopi nettamente diversi in base alle loro proprietà intrinseche.
Composizione e struttura del materiale
L'acetale, comunemente noto con il nome commerciale di Delrin (quando è in forma di omopolimero) o con il nome chimico di poliossimetilene (POM), presenta una struttura altamente cristallina con gruppi -CH₂O- ripetuti. Questa struttura gli conferisce un'eccellente stabilità dimensionale e lavorabilità.
Il PEEK (polietereterchetone), invece, appartiene alla famiglia dei poliarileterchetoni e contiene anelli aromatici collegati da legami eterei e chetonici. Questa struttura molecolare crea un'eccezionale stabilità termica e resistenza chimica.
Confronto tra le caratteristiche delle prestazioni
Le differenze di prestazioni tra questi materiali li rendono adatti ad applicazioni diverse:
Proprietà | Acetale (POM) | SETTIMANA | Il migliore per |
---|---|---|---|
Resistenza al calore | 180°F (82°C) continuo | 480°F (250°C) continuo | SETTIMANA |
Resistenza chimica | Buono (eccetto acidi forti) | Eccellente (resistente alla maggior parte dei prodotti chimici) | SETTIMANA |
Resistenza alla trazione | 8.800-10.000 psi | 14.500-16.000 psi | SETTIMANA |
Resistenza all'usura | Molto buono | Eccellente | SETTIMANA |
Lavorabilità | Eccellente | Buono (richiede tecniche specializzate) | Acetale |
Fattore di costo | Riferimento di base (1×) | 4-7 volte superiore all'acetale | Acetale |
Assorbimento dell'umidità | 0.2-0.25% | 0.1-0.15% | SETTIMANA |
Analisi costi-benefici
Negli anni in cui ho lavorato con i clienti di PTSMAKE, ho notato che le considerazioni sui costi spesso guidano il processo iniziale di selezione dei materiali. L'acetale è significativamente più economico del PEEK, il che lo rende la scelta predefinita quando non sono presenti condizioni estreme.
Il prezzo superiore del PEEK riflette le sue capacità prestazionali superiori. Per valutare se l'investimento aggiuntivo è giustificato, considerare i seguenti fattori:
- Requisiti di temperatura di esercizio
- Profilo di esposizione chimica
- Livelli di stress meccanico
- Vita utile prevista
- Costi dei tempi di inattività associati a guasti dei componenti
Considerazioni sulla lavorazione
Durata dell'utensile e parametri di taglio
L'acetale è rinomato per la sua eccezionale lavorabilità. Taglia in modo netto, mantiene tolleranze strette e produce eccellenti finiture superficiali con uno sforzo minimo. Gli utensili in carburo standard funzionano bene e il materiale non provoca un'usura eccessiva.
Il PEEK presenta maggiori difficoltà durante la lavorazione. La sua resistenza alle alte temperature comporta una scarsa dissipazione del calore durante la lavorazione, che richiede un'elevata resistenza:
- Velocità di taglio ridotte (in genere 20-30% più lente dell'acetale)
- Cambio degli utensili più frequente
- Attenzione all'accumulo di calore
- Tecniche di raffreddamento specializzate
Noi di PTSMAKE abbiamo sviluppato specifiche protocolli di gestione termica2 per la lavorazione del PEEK per garantire la precisione dimensionale e prevenire la degradazione del materiale durante il processo di taglio.
Stabilità dimensionale
L'acetale offre un'eccellente stabilità dimensionale dopo la lavorazione, con deformazioni o rilassamenti minimi. Ciò lo rende particolarmente prezioso per i componenti di precisione con tolleranze ristrette.
Anche il PEEK presenta una buona stabilità dimensionale, ma richiede processi di ricottura più accurati per alleviare le tensioni interne dopo la lavorazione. Senza un adeguato condizionamento termico, i pezzi in PEEK possono subire lievi variazioni dimensionali nel tempo, soprattutto nelle applicazioni di alta precisione.
Raccomandazioni specifiche per le applicazioni
Automotive e trasporti
Nelle applicazioni automobilistiche in cui le temperature rimangono moderate (sotto i 180°F), l'acetale offre spesso il miglior valore. Le applicazioni più comuni includono:
- Componenti del sistema di alimentazione
- Meccanismi di chiusura delle porte
- Clip e fissaggi per finiture interne
- Superfici di supporto in aree non critiche
Per le zone a temperatura più elevata, come i componenti sotto il cofano o le parti vicine ai sistemi di scarico, la stabilità termica del PEEK lo rende la scelta migliore, nonostante il costo più elevato.
Medico e farmaceutico
L'industria medica ha adottato il PEEK per la sua biocompatibilità e resistenza ai metodi di sterilizzazione. È comunemente usato in:
- Dispositivi impiantabili
- Strumenti chirurgici
- Componenti per imaging medicale
- Attrezzature di laboratorio
L'acetale trova ancora applicazioni in contesti medici meno impegnativi, come ad esempio:
- Componenti per strumenti monouso
- Apparecchiature per test di laboratorio
- Alloggiamenti per apparecchiature diagnostiche
Apparecchiature industriali
Per i macchinari industriali, la scelta dipende spesso dalle condizioni operative:
- Ambienti operativi standard: L'acetale offre un valore eccellente per ingranaggi, cuscinetti e superfici di usura in condizioni normali.
- Ambienti difficili: Il PEEK giustifica il suo prezzo elevato quando è esposto a temperature elevate, sostanze chimiche o sollecitazioni meccaniche estreme.
Fare una selezione ottimale
Quando aiuto i clienti a scegliere tra acetale e PEEK a PTSMAKE, raccomando un approccio sistematico:
- Identificare le condizioni più impegnative che il pezzo dovrà affrontare (temperatura, sostanze chimiche, carichi).
- Determinare se le proprietà dell'acetale sono sufficienti per gestire queste condizioni
- Calcolate la differenza di costo tra le opzioni per le vostre specifiche esigenze di volume
- Considerare le conseguenze di un guasto e i costi di inattività associati.
- Valutare se le prestazioni superiori del PEEK giustificano il suo prezzo più elevato.
Ricordate che la scelta del materiale è raramente univoca. A volte è meglio adottare un approccio ibrido, utilizzando il PEEK solo per i componenti più critici e l'acetale per le parti meno impegnative dello stesso gruppo.
Qual è la differenza tra PTFE e PEEK?
Vi siete mai persi nel mare delle materie plastiche ad alte prestazioni, incerti se scegliere il PTFE o il PEEK per la vostra applicazione critica? Quando le scadenze del progetto incombono e la scelta del materiale può essere decisiva per il vostro progetto, la pressione di fare la scelta giusta può essere schiacciante, soprattutto quando entrambi i materiali hanno caratteristiche tecniche impressionanti.
Il PTFE e il PEEK sono entrambi materiali termoplastici ad alte prestazioni, ma con differenze distinte. Il PTFE offre un'impareggiabile resistenza chimica, un attrito estremamente ridotto (coefficiente 0,05-0,10) e funziona da -328°F a 500°F, ma ha una scarsa resistenza meccanica. Il PEEK offre proprietà meccaniche superiori, un'eccellente resistenza all'usura e mantiene l'integrità strutturale fino a 480°F, pur essendo più lavorabile.
Struttura molecolare e proprietà di base
Le differenze fondamentali tra PTFE e PEEK iniziano a livello molecolare, il che spiega le loro diverse caratteristiche prestazionali nelle varie applicazioni.
Composizione chimica
Il PTFE (politetrafluoroetilene) presenta una spina dorsale di carbonio completamente circondata da atomi di fluoro. Questa struttura unica conferisce al PTFE un'eccezionale inerzia chimica e proprietà di basso attrito. I legami carbonio-fluoro sono tra i più forti della chimica organica e rendono il PTFE incredibilmente resistente agli attacchi chimici.
Il PEEK (Polietereterchetone), invece, ha una struttura molecolare più complessa con anelli aromatici collegati da legami eterei e chetonici. Questa spina dorsale aromatica conferisce al PEEK un'eccellente resistenza meccanica e stabilità termica.
Analisi comparativa della proprietà
Proprietà | PTFE | SETTIMANA | Vantaggio |
---|---|---|---|
Temperatura massima di utilizzo continuo | 500°F (260°C) | 480°F (250°C) | PTFE (leggermente) |
Temperatura minima di esercizio | -328°F (-200°C) | -65°F (-54°C) | PTFE |
Coefficiente di attrito | 0,05-0,10 (il più basso di tutti i solidi) | 0.35-0.40 | PTFE |
Resistenza alla trazione | 3.000-5.000 psi | 14.000-16.000 psi | SETTIMANA |
Resistenza chimica | Superiore (universale) | Eccellente (limitato dagli acidi forti) | PTFE |
Lavorabilità | Impegnativo (morbido, si deforma facilmente) | Buono | SETTIMANA |
Resistenza all'usura | Da scarso a moderato | Eccellente | SETTIMANA |
Proprietà elettriche | Eccellente isolante | Buon isolante | PTFE |
Fattore di costo | Moderato | Elevato (3-4 volte più del PTFE) | PTFE |
Differenze di prestazione termica
Le prestazioni in termini di temperatura sono spesso un fattore critico nella scelta di questi materiali.
Resistenza al calore e stabilità
Pur offrendo un'eccezionale resistenza al calore, entrambi i materiali si comportano in modo diverso a temperature elevate. Il PTFE mantiene la sua inerzia chimica e il suo basso attrito fino alla temperatura massima, ma inizia a perdere l'integrità meccanica a temperature molto più basse (circa 260°F/127°C).
Il PEEK, invece, mantiene la sua resistenza meccanica molto più vicino alla temperatura massima. Ciò rende il PEEK molto più prezioso nelle applicazioni che richiedono sia resistenza al calore che carico meccanico.
Ho visto numerose applicazioni in cui i clienti hanno scelto inizialmente il PTFE solo in base alle temperature nominali, per poi scoprire che il materiale non era in grado di gestire le sollecitazioni meccaniche a quelle temperature. La capacità del PEEK di mantenere l'integrità strutturale alle alte temperature spesso vale il prezzo più alto.
Prestazioni a basse temperature
Per le applicazioni criogeniche, il PTFE presenta un netto vantaggio. Rimane flessibile e funzionale fino a -328°F (-200°C), mentre il PEEK diventa sempre più fragile sotto i -65°F (-54°C). Per questo motivo, il PTFE è la scelta ideale per il settore aerospaziale, i laboratori e altri ambienti a bassissima temperatura.
Confronto della resistenza meccanica
Le proprietà meccaniche di questi materiali differiscono notevolmente, rendendo la loro idoneità specifica all'applicazione.
Integrità strutturale sotto carico
Il PEEK offre prestazioni meccaniche nettamente superiori, con una resistenza alla trazione media di 14.000-16.000 psi rispetto ai modesti 3.000-5.000 psi del PTFE. Ciò rende il PEEK adatto ad applicazioni portanti in cui il PTFE si deformerebbe o cederebbe rapidamente.
Noi di PTSMAKE consigliamo spesso il PEEK per i componenti strutturali sottoposti a carichi meccanici consistenti, soprattutto a temperature elevate. L'eccezionale resistenza allo scorrimento del materiale gli consente di mantenere la stabilità dimensionale in presenza di sollecitazioni continue.
Resistenza all'usura e attrito
Il coefficiente di attrito notevolmente basso del PTFE (0,05-0,10) lo rende il materiale preferito per le applicazioni che richiedono un attrito minimo. Tuttavia, questa stessa proprietà contribuisce alla sua scarsa resistenza all'usura, in quanto il materiale può essere facilmente raschiato via in situazioni di elevata usura.
Il PEEK dimostra un'eccellente resistenza all'usura, mantenendo un coefficiente di attrito ragionevole (0,35-0,40). Per le applicazioni che prevedono un movimento continuo contro altre superfici, il PEEK di solito supera il PTFE con un margine considerevole.
Molti dei nostri clienti ottengono il meglio dei due mondi utilizzando il PEEK come materiale strutturale con un sottile rivestimento o liner in PTFE dove è necessaria una riduzione dell'attrito.
Profili di resistenza chimica
Entrambi i materiali offrono un'eccezionale resistenza chimica, ma con importanti distinzioni.
Resistenza agli ambienti aggressivi
Il PTFE rappresenta il gold standard per la resistenza chimica, essendo praticamente inerte a quasi tutte le sostanze chimiche (con rare eccezioni come i metalli alcalini fusi e il fluoro elementare). Questa resistenza chimica universale rende il PTFE prezioso nei processi chimici, nella produzione di semiconduttori e negli ambienti di laboratorio.
Il PEEK offre un'eccellente resistenza chimica alla maggior parte delle sostanze, ma può essere attaccato dall'acido solforico concentrato e da alcuni altri acidi forti. Per la maggior parte degli ambienti industriali, tuttavia, la resistenza chimica del PEEK è più che sufficiente.
Idrolisi e assorbimento dell'umidità
Il PTFE è completamente idrofobo e non assorbe sostanzialmente umidità, anche dopo un'esposizione prolungata. Il PEEK, pur essendo altamente resistente all'idrolisi, assorbe una piccola quantità di umidità (0,1-0,3%) se esposto ad ambienti umidi per periodi prolungati.
Per le applicazioni con acqua ultrapura o per i sistemi in cui anche una minima contaminazione è inaccettabile, il PTFE rimane spesso la scelta preferita nonostante le sue limitazioni meccaniche.
%[Componenti lavorati in PEEK e PTFE per un confronto strutturale](
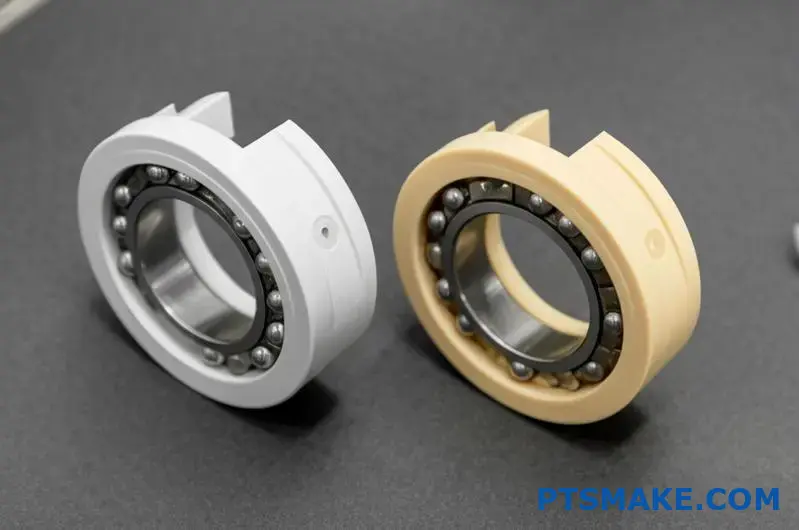
"Componenti per cuscinetti in PEEK e PTFE")
Considerazioni sulla lavorazione e sulla fabbricazione
Il lavorabilità3 Le differenze tra questi materiali hanno un impatto significativo sui costi e sulle capacità di produzione.
Sfide e soluzioni di lavorazione
Il PTFE presenta sfide di lavorazione uniche a causa della sua morbidezza e della sua tendenza alla fluidità a freddo. Richiede utensili speciali, velocità di taglio ridotte e un accurato fissaggio per evitare deformazioni durante la lavorazione. Gli utensili affilati sono essenziali per evitare di strappare o deformare il materiale.
Il PEEK si lavora come i tradizionali tecnopolimeri, anche se la sua natura abrasiva causa un'usura più rapida degli utensili rispetto a molti altri materiali. Quando lavoriamo il PEEK, in genere utilizziamo utensili in metallo duro e tecniche di raffreddamento adeguate per gestire l'accumulo di calore.
Compatibilità del processo di produzione
L'elevata viscosità del PTFE rende impossibile lo stampaggio a iniezione tradizionale. È invece necessario lavorarlo con tecniche come lo stampaggio a compressione, l'estrusione a ram o la scrematura da billette. Questo limita la complessità del progetto e aumenta i costi di produzione per le forme complesse.
Il PEEK può essere lavorato con metodi convenzionali come lo stampaggio a iniezione e l'estrusione, consentendo geometrie più complesse e costi di produzione potenzialmente inferiori a volumi più elevati. Questa versatilità di lavorazione offre al PEEK un vantaggio per i componenti più complessi o per la transizione dalla prototipazione alla produzione di massa.
Analisi costi-benefici per diverse applicazioni
La notevole differenza di prezzo tra questi materiali richiede un'attenta considerazione del loro valore specifico per l'applicazione.
Confronto tra le proposte di valore
Sebbene il PEEK costi in genere 3-4 volte di più del PTFE, le sue proprietà meccaniche superiori e la sua resistenza all'usura offrono spesso un valore migliore a lungo termine in applicazioni in cui un guasto meccanico sarebbe costoso o pericoloso.
Per le applicazioni che richiedono principalmente resistenza chimica, basso attrito o proprietà di isolamento elettrico senza significative sollecitazioni meccaniche, il PTFE offre solitamente un valore migliore, nonostante i suoi limiti.
Criteri di selezione specifici per il settore
I diversi settori industriali danno priorità alle diverse proprietà dei materiali:
- Trattamento chimico: La resistenza chimica universale del PTFE supera in genere le sue limitazioni meccaniche.
- Aerospaziale: Entrambi i materiali trovano applicazione, con il PEEK utilizzato per i componenti strutturali e il PTFE per le guarnizioni e l'isolamento elettrico.
- Medicale: La biocompatibilità e la resistenza strutturale del PEEK lo rendono popolare per gli impianti, mentre il PTFE è preferito per i rivestimenti dei cateteri e altre applicazioni a basso attrito.
- Semiconduttori: Il PTFE domina grazie alla sua eccezionale purezza e resistenza agli agenti chimici aggressivi.
- Automotive: La resistenza all'usura e le proprietà meccaniche del PEEK lo rendono prezioso per i componenti sotto il cofano sottoposti a sollecitazioni meccaniche.
Qual è la differenza tra PVDF e PEEK?
Vi siete mai trovati di fronte al dilemma di dover scegliere tra PVDF e PEEK per un progetto critico in cui la selezione del materiale potrebbe fare la differenza? Quando le plastiche standard non sono sufficienti e avete bisogno di un'eccezionale resistenza chimica o stabilità termica, la confusione tra questi due materiali ad alte prestazioni può portare a costosi errori o a prestazioni compromesse.
Il PVDF (fluoruro di polivinilidene) e il PEEK (polietereterchetone) si differenziano principalmente per le caratteristiche prestazionali e le applicazioni. Il PEEK offre una resistenza termica superiore (480°F contro 300°F), una migliore forza meccanica e un'eccezionale resistenza all'usura, mentre il PVDF offre un'eccellente resistenza chimica, stabilità ai raggi UV e un costo significativamente inferiore.
Principali differenze tra PVDF e PEEK
Quando si confrontano questi due tecnopolimeri, la comprensione delle loro proprietà fondamentali aiuta a determinare quale materiale sia più adatto per applicazioni specifiche. Entrambi i materiali sono considerati opzioni ad alte prestazioni, ma eccellono in ambienti e applicazioni diverse.
Composizione e struttura del materiale
Il PVDF è un fluoropolimero semicristallino costituito da unità ripetute di difluoruro di vinilidene. La sua struttura molecolare comprende legami carbonio-fluoro che garantiscono un'eccellente resistenza chimica, anche se non così completa come quella dei polimeri completamente fluorurati come il PTFE.
Il PEEK appartiene alla famiglia dei poliarileterchetoni e presenta una struttura molecolare complessa con anelli aromatici collegati da legami eterei e chetonici. Questa struttura unica conferisce al PEEK un'eccezionale stabilità termica e resistenza meccanica.
Confronto tra le caratteristiche delle prestazioni
La tabella seguente fornisce un confronto dettagliato delle principali proprietà del PVDF e del PEEK:
Proprietà | PVDF | SETTIMANA | Materiale superiore |
---|---|---|---|
Temperatura massima di utilizzo continuo | 300°F (149°C) | 480°F (250°C) | SETTIMANA |
Resistenza meccanica (trazione) | 5.800-7.800 psi | 14.500-16.000 psi | SETTIMANA |
Resistenza chimica | Eccellente (maggior parte degli acidi e delle basi) | Molto buono (limitato da acidi forti) | PVDF |
Resistenza ai raggi UV | Eccellente | Da discreto a buono | PVDF |
Resistenza all'usura | Buono | Eccellente | SETTIMANA |
Coefficiente di attrito | 0.25-0.35 | 0.35-0.40 | PVDF |
Fattore di costo | Moderato | 2-3 volte superiore al PVDF | PVDF |
Assorbimento dell'umidità | 0.03-0.04% | 0.1-0.15% | PVDF |
Densità | 1,75-1,78 g/cm³ | 1,30-1,32 g/cm³ | Dipendente dall'applicazione |
Prestazioni termiche e stabilità
Le capacità di temperatura spesso guidano le decisioni di selezione dei materiali in molte applicazioni ingegneristiche.
Confronto della resistenza al calore
Il PEEK dimostra un'eccezionale stabilità termica, mantenendo le sue proprietà meccaniche a temperature fino a 250°C (480°F) per un uso continuo. Questo lo rende ideale per le applicazioni in ambienti ad alta temperatura, dove le plastiche tradizionali si guasterebbero.
Il PVDF, pur essendo considerato una plastica per alte temperature, ha una temperatura massima di utilizzo continuo inferiore, pari a circa 300°F (149°C). Questo intervallo di temperatura è sufficiente per molte applicazioni industriali, ma è insufficiente in ambienti termici estremi.
Nella mia esperienza di collaborazione con i clienti di PTSMAKE, questo differenziale di temperatura diventa spesso il fattore decisivo nella scelta tra questi materiali per applicazioni come le apparecchiature di lavorazione dei semiconduttori, dove le temperature di processo possono superare le capacità del PVDF.
Comportamento al ciclo termico
Entrambi i materiali gestiscono in modo diverso i cicli termici:
- Il PVDF presenta una buona stabilità dimensionale durante i cicli termici, anche se può subire un'espansione termica più significativa rispetto al PEEK.
- Il PEEK mantiene un'eccezionale stabilità dimensionale anche attraverso ripetuti cicli termici, rendendolo preferibile per i componenti di precisione che devono mantenere tolleranze ristrette a temperature variabili.
Profili di resistenza chimica
La resistenza chimica è un altro fattore cruciale che contraddistingue questi materiali.
Resistenza agli ambienti aggressivi
Il PVDF offre un'eccellente resistenza a un'ampia gamma di sostanze chimiche, tra cui:
- La maggior parte degli acidi (compresi gli acidi cloridrico e solforico concentrati)
- Idrocarburi alifatici e aromatici
- Alcoli e solventi clorurati
- Agenti ossidanti
Il PEEK dimostra una buona resistenza chimica a molte sostanze, ma può essere attaccato dall'acido solforico concentrato e da alcuni altri acidi forti. È particolarmente resistente all'idrolisi e alla sterilizzazione a vapore, il che lo rende prezioso nelle applicazioni mediche.
Considerazioni chimiche specifiche del settore
I diversi settori industriali danno priorità a specifiche proprietà di resistenza chimica:
- Trattamento chimico: Il PVDF è spesso preferito per la sua ampia resistenza agli acidi e ai composti clorurati.
- Semiconduttori: Vengono utilizzati entrambi i materiali, la cui scelta dipende dalle specifiche sostanze chimiche di processo.
- Petrolio e gas: La combinazione di proprietà meccaniche e resistenza chimica del PEEK lo rende prezioso per le applicazioni downhole.
- Farmaceutico: L'eccellente resistenza del PVDF ai detergenti e ai metodi di sterilizzazione lo rende popolare per le apparecchiature di lavorazione.
Proprietà meccaniche e applicazioni strutturali
Il resistenza meccanica4 Le differenze tra questi materiali influiscono in modo significativo sulla loro idoneità alle applicazioni portanti.
Capacità di carico
La SBIRCIATA offre una resistenza meccanica nettamente superiore, con valori di trazione che vanno tipicamente da 14.500 a 16.000 psi, rispetto ai più modesti 5.800-7.800 psi del PVDF. Ciò rende il PEEK superiore per i componenti strutturali che devono sopportare carichi meccanici significativi.
Per le applicazioni che richiedono sia la resistenza chimica che l'integrità strutturale, il PEEK offre spesso il miglior equilibrio di proprietà, nonostante il suo costo più elevato. All'PTSMAKE ho consigliato il PEEK per numerose applicazioni in cui i componenti devono resistere sia a sostanze chimiche aggressive che a sollecitazioni meccaniche.
Resistenza all'usura e proprietà di attrito
Il PEEK dimostra un'eccellente resistenza all'usura, che lo rende ideale per cuscinetti, boccole e altri componenti soggetti ad attrito continuo. Le sue proprietà autolubrificanti contribuiscono a prolungare la durata delle parti in movimento in ambienti difficili.
Il PVDF offre una buona resistenza all'usura, anche se non al livello del PEEK. Il suo coefficiente di attrito inferiore (0,25-0,35 rispetto a 0,35-0,40 del PEEK) può essere vantaggioso in alcune applicazioni di scorrimento a basso carico, dove la riduzione dell'attrito è più importante della massima resistenza all'usura.
Proprietà di isolamento elettrico e termico
Entrambi i materiali offrono caratteristiche elettriche distinte che li rendono adatti a diverse applicazioni.
Proprietà dielettriche
Il PVDF è noto per le sue proprietà piezoelettriche, che gli consentono di generare una carica elettrica in risposta alle sollecitazioni meccaniche applicate. Questa caratteristica unica rende il PVDF prezioso nelle applicazioni dei sensori.
Il PEEK offre eccellenti proprietà di isolamento elettrico in un'ampia gamma di temperature, mantenendo la sua rigidità dielettrica anche a temperature elevate. Ciò lo rende particolarmente prezioso nelle applicazioni elettriche ad alta temperatura, dove i materiali plastici standard non sarebbero in grado di funzionare.
Conduttività termica
PVDF e PEEK hanno entrambi una conducibilità termica relativamente bassa rispetto ai metalli, il che li rende buoni isolanti termici:
- PVDF: 0,17-0,19 W/m-K
- PEEK: 0,25-0,29 W/m-K
Questa bassa conduttività termica può essere un vantaggio o uno svantaggio a seconda dell'applicazione. Per i componenti che richiedono l'isolamento termico, entrambi i materiali offrono buone prestazioni, anche se il PVDF offre un isolamento leggermente migliore.
Considerazioni sui costi e analisi del valore
La notevole differenza di prezzo tra questi materiali rende essenziale l'analisi costi-benefici.
Costo iniziale del materiale
Il PEEK costa in genere 2-3 volte di più del PVDF, il che rappresenta un sostanziale sovrapprezzo che deve essere giustificato dai requisiti di prestazione. Questa differenza di prezzo deriva dal processo di produzione più complesso del PEEK e dal costo più elevato delle materie prime.
Valutazione del valore di vita
Quando si valuta il costo totale di proprietà, si devono considerare diversi fattori oltre al costo iniziale del materiale:
- Vita utile prevista nell'ambiente di destinazione
- Frequenza di sostituzione e costi di fermo macchina associati
- Requisiti di installazione e manutenzione
- Problemi di sicurezza e affidabilità
In molte applicazioni ad alta temperatura o ad alto carico, le prestazioni superiori del PEEK giustificano il suo costo iniziale più elevato grazie alla maggiore durata e affidabilità. Per le applicazioni che rientrano nelle capacità del PVDF, il materiale più economico offre spesso un valore complessivo migliore.
Considerazioni sulla lavorazione e sulla fabbricazione
Anche le capacità e le limitazioni di produzione influenzano la scelta del materiale.
Differenze di lavorazione
Lavorando questi materiali a PTSMAKE, abbiamo osservato differenze significative:
- Il PVDF si lavora relativamente bene, ma richiede utensili affilati e velocità adeguate per evitare la fusione o la formazione di gocce.
- Il PEEK è più difficile da lavorare a causa della sua abrasività e della scarsa conducibilità termica, che può portare all'accumulo di calore durante le operazioni di taglio.
Per i componenti di precisione, il PEEK mantiene generalmente tolleranze più strette durante la lavorazione, ma richiede tecniche e utensili più specializzati, con un potenziale aumento dei costi di produzione.
Compatibilità dei metodi di produzione
Entrambi i materiali possono essere lavorati con diversi metodi di produzione:
- PVDF: Stampaggio a iniezione, estrusione, stampaggio a compressione, lavorazione
- PEEK: stampaggio a iniezione, estrusione, stampaggio a compressione, lavorazione, stampa 3D (attrezzature specializzate)
Il PVDF offre una flessibilità di lavorazione leggermente superiore a temperature più basse, mentre il PEEK richiede temperature di lavorazione più elevate ma offre maggiori opzioni per geometrie complesse grazie a tecniche di produzione avanzate.
Linee guida di selezione specifiche per le applicazioni
I diversi settori industriali danno priorità alle diverse proprietà dei materiali, con conseguenti preferenze diverse.
Industria dei semiconduttori
Nella produzione di semiconduttori, entrambi i materiali trovano applicazione, ma in aree diverse:
- PVDF: Comunemente utilizzato per sistemi di acqua ultrapura, componenti di erogazione di sostanze chimiche e apparecchiature di filtrazione.
- PEEK: Preferito per i componenti esposti a temperature elevate, come le apparecchiature di manipolazione dei wafer e i componenti delle camere di processo.
Apparecchiature per il trattamento chimico
Per applicazioni di lavorazione chimica:
- PVDF: Eccellente per pompe, valvole, raccordi e serbatoi che trattano sostanze chimiche corrosive a temperature moderate.
- PEEK: più adatto per i componenti che richiedono resistenza chimica e capacità di resistere alle alte temperature o alla forza meccanica.
Applicazioni mediche e farmaceutiche
Nelle applicazioni mediche:
- PVDF: Comunemente utilizzato in membrane di filtrazione, suture e alcuni dispositivi impiantabili.
- PEEK: Preferito per i dispositivi impiantabili, soprattutto per le applicazioni ortopediche, grazie alla sua biocompatibilità, alla radiotrasparenza e alle proprietà meccaniche simili all'osso.
Quando aiuto i clienti a scegliere tra PVDF e PEEK all'PTSMAKE, raccomando un approccio sistematico che valuta innanzitutto i fattori ambientali più critici (temperatura, sostanze chimiche, carichi meccanici), quindi considera fattori secondari come il costo, i requisiti di lavorazione e la disponibilità.
<
Il PEEK è un polietilene?
Vi siete mai trovati confusi di fronte a una serie di tecnopolimeri con nomi simili? Quando si scelgono materiali per applicazioni critiche, questa confusione può portare a errori costosi, a prestazioni insufficienti e a uno spreco di risorse se si sostituisce erroneamente una plastica ad alte prestazioni con un'altra.
Il PEEK (polietereterchetone) non è un polietilene. Il PEEK è un polietere aromatico con gruppi chetonici nella spina dorsale, che crea un materiale termoplastico semicristallino con un'eccezionale resistenza al calore (fino a 480°F), un'eccellente resistenza chimica e proprietà meccaniche superiori a quelle dei materiali in polietilene.
Struttura chimica e differenze di classificazione
Quando si esamina il PEEK rispetto al polietilene, le differenze fondamentali iniziano a livello molecolare. Queste variazioni strutturali spiegano perché questi materiali si comportano in modo così diverso nelle applicazioni pratiche.
Confronto tra le dorsali molecolari
Il PEEK presenta una complessa struttura a dorsale aromatica con legami eterei e chetonici tra gli anelli benzenici. Questa architettura molecolare conferisce al PEEK un'eccezionale stabilità termica e resistenza meccanica. Gli anelli aromatici creano rigidità, mentre i legami eterei forniscono una certa flessibilità.
Il polietilene, invece, ha una delle strutture polimeriche più semplici possibili: una semplice catena lineare di atomi di carbonio con atomi di idrogeno collegati. Questa struttura semplice esiste in varie forme (HDPE, LDPE, UHMWPE), ma tutte mancano dei componenti aromatici e dei gruppi funzionali che conferiscono al PEEK le sue eccezionali proprietà.
Questa fondamentale differenza strutturale fa sì che il PEEK appartenga a una famiglia di polimeri completamente diversa da quella del polietilene. Mentre il polietilene è classificato come poliolefina, il PEEK appartiene alla famiglia dei materiali termoplastici ad alte prestazioni del poliarileterchetone (PAEK).
Principali differenze di proprietà
Le differenze di struttura molecolare si traducono in drastiche variazioni di prestazioni:
Proprietà | SETTIMANA | Polietilene (HDPE) | Fattore di differenza |
---|---|---|---|
Temperatura massima di utilizzo continuo | 480°F (250°C) | 180°F (82°C) | Il PEEK è 2,7 volte superiore |
Resistenza alla trazione | 14.500 psi | 4.500 psi | Il PEEK è 3,2 volte più resistente |
Resistenza chimica | Eccellente (resiste alla maggior parte dei prodotti chimici) | Buono (vulnerabile ai solventi aromatici) | Il PEEK offre una resistenza più ampia |
Costo | Alto | Basso | Il PEEK costa 15-20 volte di più |
Densità | 1,32 g/cm³ | 0,95 g/cm³ | Il PEEK è 39% più denso |
Durezza (Shore D) | 85-90 | 60-70 | Il PEEK è significativamente più duro |
Differenze nel processo di produzione
I metodi di produzione del PEEK e del polietilene riflettono le loro diverse strutture molecolari e caratteristiche di prestazione.
Processo di produzione del PEEK
Il PEEK viene prodotto attraverso un complesso processo di polimerizzazione per sostituzione nucleofila aromatica. Questo processo richiede un controllo preciso della temperatura e catalizzatori specializzati. I materiali monomerici sono significativamente più costosi dell'etilene e contribuiscono al costo più elevato del PEEK.
Alla PTSMAKE, quando lavoriamo componenti in PEEK, dobbiamo tenere conto delle proprietà uniche di questo materiale: la sua minore conduttività termica significa che la gestione del calore durante la lavorazione è fondamentale per evitare il degrado termico localizzato.
Produzione di polietilene
Il polietilene viene prodotto attraverso la polimerizzazione per addizione dell'etilene, utilizzando diversi catalizzatori a seconda della densità e della ramificazione desiderata. Questo processo relativamente semplice può essere condotto a temperature e pressioni inferiori rispetto alla produzione di PEEK, soprattutto per le varietà a bassa densità.
Prestazioni in ambienti estremi
Prestazioni ad alta temperatura
Una delle differenze più significative tra questi materiali è la loro stabilità termica:
- Il PEEK mantiene le sue proprietà meccaniche fino a 480°F (250°C) per un uso continuo e può sopportare brevi esposizioni a temperature ancora più elevate.
- Il polietilene inizia ad ammorbidirsi intorno ai 180°F (82°C) e perde la maggior parte della sua resistenza meccanica ben al di sotto di tale temperatura.
Ho visto numerose applicazioni in cui i clienti hanno scelto inizialmente il polietilene in base al costo, per poi sperimentare un rapido guasto quando le temperature di esercizio superavano le aspettative. In un'applicazione aerospaziale, un cliente è passato dal polietilene al PEEK per un componente vicino a una fonte di calore, prolungandone la durata da mesi ad anni nonostante il costo iniziale più elevato del materiale.
Confronto della resistenza chimica
Sebbene entrambi i materiali offrano una buona resistenza chimica, il PEEK offre una protezione più ampia contro le sostanze chimiche aggressive:
- Il PEEK resiste alla maggior parte degli acidi, delle basi, degli idrocarburi e dei solventi organici.
- Il polietilene ha una buona resistenza agli acidi e alle basi, ma può essere attaccato dagli idrocarburi aromatici e da alcuni agenti ossidanti.
Questa differenza diventa fondamentale nelle apparecchiature per il trattamento chimico, nella produzione di semiconduttori e nelle applicazioni mediche, dove l'esposizione a più sostanze chimiche è comune.
Idoneità all'applicazione
Applicazioni aerospaziali e di difesa
Nelle applicazioni aerospaziali, la combinazione di leggerezza, resistenza alla fiamma e stabilità termica del PEEK lo rende prezioso per componenti quali:
- Componenti interni che richiedono resistenza alla fiamma
- Connettori e isolatori elettrici
- Componenti strutturali in zone ad alta temperatura
- Componenti del sistema di alimentazione che richiedono resistenza chimica
Il polietilene raramente soddisfa gli esigenti requisiti delle applicazioni aerospaziali a causa della sua limitata stabilità termica e delle sue proprietà meccaniche.
Usi medici e sanitari
Anche i profili di biocompatibilità di questi materiali differiscono in modo significativo:
- Il PEEK è biocompatibile e viene utilizzato in dispositivi impiantabili, strumenti chirurgici e apparecchiature mediche che richiedono la sterilizzazione.
- Il polietilene di grado medico (principalmente UHMWPE) è utilizzato in alcuni impianti come le articolazioni artificiali, ma non ha la resistenza alle temperature del PEEK per la sterilizzazione a vapore ripetuta.
Componenti di apparecchiature industriali
Per i macchinari industriali, la scelta tra questi materiali dipende tipicamente dalle condizioni operative:
- Il PEEK eccelle in ambienti ad alta temperatura, in applicazioni che richiedono un'eccellente resistenza all'usura o all'esposizione a sostanze chimiche aggressive.
- Il polietilene offre prestazioni adeguate in applicazioni a temperatura ambiente con requisiti meccanici moderati e viene spesso scelto per il suo costo inferiore e la facilità di lavorazione.
Considerazioni sul rapporto costi-benefici
La differenza di prezzo tra questi materiali è sostanziale: il PEEK costa in genere 15-20 volte di più del polietilene ad alta densità. Questa significativa differenza di costo significa che la scelta del materiale deve basarsi su un'analisi approfondita di:
- Intervallo di temperatura di esercizio richiesto
- Profilo di esposizione chimica
- Requisiti di carico meccanico
- Vita utile prevista
- Conseguenze del fallimento
Per le applicazioni che rientrano nella gamma di capacità del polietilene, il suo costo inferiore lo rende la scelta più economica. Tuttavia, quando le prestazioni richieste superano i limiti del polietilene, le proprietà superiori del PEEK giustificano facilmente il suo prezzo superiore grazie alla maggiore durata, alla migliore affidabilità e alla riduzione dei costi di manutenzione.
Differenze di lavorazione e trasformazione
Noi di PTSMAKE abbiamo riscontrato differenze significative nella lavorazione di questi materiali:
- Il PEEK richiede parametri di taglio specifici a causa della sua comportamento termico5 durante la lavorazione, ma mantiene tolleranze strette e produce eccellenti finiture superficiali.
- Il polietilene è più facile da lavorare, ma ha la tendenza a deformarsi sotto le forze di taglio, rendendo più difficile il mantenimento di tolleranze strette.
La comprensione di queste differenze di lavorazione è essenziale quando si progettano componenti per la producibilità e la precisione.
Quali sono gli svantaggi e i vantaggi del PEEK?
Avete mai lottato per decidere se il PEEK vale il suo prezzo premium per la vostra applicazione critica? Quando il successo di un progetto dipende dalla selezione del materiale, la scelta tra le costose materie plastiche ad alte prestazioni e le alternative più economiche può essere un difficile esercizio di bilanciamento con conseguenze reali per l'affidabilità e la durata.
Il PEEK offre vantaggi eccezionali, tra cui una notevole resistenza al calore (fino a 480°F), un'eccezionale resistenza chimica, un'eccellente resistenza meccanica e proprietà antiusura superiori. Tuttavia, questi vantaggi sono accompagnati da svantaggi significativi, tra cui il costo elevato (5-10 volte superiore a quello dei tecnopolimeri standard), la difficile lavorabilità, le opzioni di colore limitate e la scarsa resistenza ai raggi UV.
Capire le eccezionali proprietà del PEEK
Il PEEK (Polietereterchetone) si distingue tra i tecnopolimeri per la sua combinazione unica di proprietà che lo rendono adatto alle applicazioni più impegnative. Avendo specificato materiali per innumerevoli componenti di precisione, ho potuto constatare di persona come le proprietà del PEEK si traducano in vantaggi reali in termini di prestazioni.
Vantaggi in termini di prestazioni termiche
Una delle caratteristiche più impressionanti del PEEK è la sua stabilità termica. Questo materiale mantiene le sue proprietà meccaniche a temperature che causerebbero il cedimento catastrofico della maggior parte delle materie plastiche.
Caratteristica di temperatura | Prestazioni del PEEK | Confronto con le plastiche standard |
---|---|---|
Temperatura di servizio continua | Fino a 250°C (480°F) | 2-3 volte superiore alla maggior parte dei tecnopolimeri |
Temperatura di transizione del vetro | 289°F (143°C) | Mantiene la rigidità a temperature più elevate |
Punto di fusione | 649°F (343°C) | Consente la sterilizzazione a vapore |
Conduttività termica | 0,25 W/m-K | Migliore di molte plastiche per la dissipazione del calore |
Questa eccezionale resistenza termica consente di utilizzare il PEEK in applicazioni vicine a fonti di calore, dove le plastiche standard si deformerebbero o degraderebbero rapidamente. Ho aiutato molti clienti a sostituire componenti guasti realizzati con materiali meno pregiati con componenti in PEEK che continuano a funzionare perfettamente nonostante gli ambienti termici difficili.
Vantaggi della resistenza chimica
Il profilo di resistenza chimica del PEEK è impressionante quasi quanto le sue proprietà termiche. Il materiale mostra un'eccellente resistenza a:
- Idrocarburi e solventi organici
- La maggior parte degli acidi e delle basi (tranne l'acido solforico concentrato)
- Vapore e acqua calda
- Fluidi e carburanti per autoveicoli
- Processi di sterilizzazione medica
Questa ampia resistenza chimica rende il PEEK particolarmente prezioso negli ambienti in cui è prevista l'esposizione a più sostanze aggressive. Nell'industria dei semiconduttori, ad esempio, i componenti in PEEK sono in grado di resistere alle sostanze chimiche aggressive utilizzate nella lavorazione dei wafer, mantenendo la stabilità dimensionale.
Vantaggi delle proprietà meccaniche
La resistenza meccanica del PEEK lo distingue dalla maggior parte degli altri materiali termoplastici:
- Resistenza alla trazione di 14.500 psi (paragonabile a quella di alcuni metalli)
- Eccellente resistenza alla fatica
- Eccezionale resistenza agli urti e tenacità
- Resistenza all'usura superiore
- Basso coefficiente di attrito
Queste proprietà rendono il PEEK adatto ad applicazioni strutturali in cui la maggior parte delle materie plastiche fallirebbe. Ho specificato il PEEK per ingranaggi, cuscinetti e altri componenti ad alta usura che operano in condizioni di notevole stress meccanico, spesso sostituendo le parti metalliche con alternative in PEEK più leggere che offrono ulteriori vantaggi come la resistenza alla corrosione e la riduzione del rumore.
Gli svantaggi significativi del PEEK
Nonostante le sue impressionanti caratteristiche prestazionali, il PEEK presenta diversi svantaggi significativi che devono essere attentamente considerati durante la selezione del materiale.
Vincoli di costo
Lo svantaggio più evidente del PEEK è il suo costo. Noi di PTSMAKE dobbiamo spesso aiutare i clienti a comprendere il sovrapprezzo del PEEK rispetto ad altri tecnopolimeri:
- Il PEEK costa in genere 5-10 volte di più rispetto ai tecnopolimeri come il nylon o l'acetale.
- I costi dei materiali per le parti in PEEK possono essere 20-30% più alti rispetto ai componenti metallici equivalenti.
- L'elevato prezzo delle materie prime incide in modo significativo sull'economia dei piccoli componenti.
Questo fattore di costo spesso costringe gli ingegneri a riservare il PEEK solo alle applicazioni più critiche, dove le sue proprietà uniche sono assolutamente necessarie. In molti casi, consigliamo alternative più economiche per i componenti non critici di un gruppo.
Sfide di produzione
Il PEEK presenta diverse sfide produttive che possono aumentare la complessità e i costi di produzione:
Difficoltà di lavorazione: L'elevata resistenza termica del PEEK si traduce in una scarsa conducibilità termica, che provoca un accumulo di calore durante le operazioni di lavorazione. Ciò richiede velocità di taglio più basse, frequenti cambi di utensile e attente strategie di raffreddamento.
Requisiti di temperatura di lavorazione: Con un punto di fusione di 343°C (649°F), il PEEK richiede attrezzature specializzate ad alta temperatura per lo stampaggio a iniezione e l'estrusione.
Finestra di elaborazione limitata: La differenza tra la temperatura di fusione del PEEK e l'inizio della degradazione è relativamente bassa, il che crea problemi durante la lavorazione.
Ritiro dello stampo: Il PEEK presenta un ritiro significativo (circa 1-1,3%) durante il raffreddamento, che richiede una progettazione precisa dello stampo per ottenere tolleranze ristrette.
Noi di PTSMAKE abbiamo sviluppato protocolli di lavorazione specializzati per il PEEK per affrontare queste sfide, che però inevitabilmente aumentano il costo complessivo e la complessità della produzione di componenti in PEEK.
Limitazioni dell'applicazione
Nonostante le sue straordinarie proprietà, il PEEK presenta dei limiti che lo rendono inadatto a determinate applicazioni:
- Scarsa resistenza ai raggi UV: Senza additivi, il PEEK si degrada in caso di esposizione prolungata ai raggi UV, limitandone l'uso in applicazioni esterne.
- Opzioni di colore limitate: A causa del suo colore naturale ambrato/marrone e delle elevate temperature di lavorazione, il PEEK è difficile da colorare in modo uniforme.
- Limitazioni elettriche: Pur essendo un buon isolante, il PEEK non è ideale per le applicazioni elettriche ad alta frequenza rispetto ai polimeri elettrici specializzati.
- Difficoltà di legame: La resistenza chimica del PEEK rende difficile l'incollaggio, che spesso richiede trattamenti superficiali speciali.
Analisi costi-benefici: Quando conviene il PEEK?
Dato il notevole sovrapprezzo del PEEK, prima di scegliere questo materiale è necessario effettuare un'analisi approfondita dei costi e dei benefici. Secondo la mia esperienza, il PEEK offre il miglior valore nei seguenti scenari:
Scenari in cui PEEK eccelle
Ambienti ad alta temperatura: Quando le temperature di esercizio superano i 300°F (149°C), il PEEK è spesso l'unica opzione plastica praticabile, rendendo giustificato il suo costo superiore.
Ambienti chimicamente aggressivi: Nelle applicazioni esposte a più sostanze chimiche o a sostanze particolarmente aggressive, l'ampia resistenza chimica del PEEK evita le frequenti sostituzioni richieste da materiali meno pregiati.
Applicazioni critiche per l'usura: Per i componenti soggetti a costante attrito e usura nei sistemi critici, l'eccezionale resistenza all'usura e il basso attrito del PEEK possono prolungare notevolmente gli intervalli di manutenzione.
Requisiti per la riduzione del peso: Quando si sostituiscono componenti metallici in applicazioni aerospaziali o ad alte prestazioni, il rapporto forza-peso del PEEK può fornire vantaggi prestazionali che ne giustificano il costo.
Applicazioni di impianti medici: La biocompatibilità e la stabilità chimica del PEEK lo rendono ideale per i dispositivi impiantabili a lungo termine, dove la rottura del materiale non è un'opzione.
Confronto tra materiali alternativi
Per le applicazioni che non richiedono specificamente le proprietà estreme del PEEK, diverse alternative possono fornire prestazioni sufficienti a costi inferiori:
Materiale | Vantaggio comparato | Costo rispetto al PEEK | Limitazione dei tasti |
---|---|---|---|
PPS (solfuro di polifenilene) | Buona resistenza al calore (400°F) | 40-60% inferiore | Meno resistente agli agenti chimici |
PTFE (politetrafluoroetilene) | Resistenza chimica superiore | 30-50% inferiore | Scarsa resistenza meccanica |
PEI (polieterimmide) | Buona resistenza al calore, trasparenza | 30-40% inferiore | Meno resistente all'usura |
PAI (poliammide-immide) | Alta resistenza, buona resistenza all'usura | 10-20% inferiore | Più difficile da elaborare |
Acetale (POM) | Eccellente lavorabilità, basso costo | 80-90% inferiore | Resistenza limitata alla temperatura |
Considerazioni specifiche per il settore
I diversi settori industriali danno priorità a diversi aspetti del profilo delle proprietà del PEEK:
Aerospaziale e difesa
Nelle applicazioni aerospaziali, la combinazione di leggerezza, resistenza alla fiamma (con gli additivi) e stabilità termica del PEEK giustifica il suo prezzo elevato per componenti quali:
- Boccole e cuscinetti nei sistemi di controllo
- Connettori e isolatori elettrici
- Componenti strutturali in zone ad alta temperatura
- Componenti del sistema di alimentazione che richiedono resistenza chimica
Settore medico e sanitario
L'industria medica apprezza il PEEK per le sue caratteristiche:
- Biocompatibilità (grado di impianto)
- Resistenza alla sterilizzazione ripetuta
- Radiolucenza (non interferisce con i raggi X)
- Proprietà meccaniche simili all'osso (se rinforzato)
Queste proprietà rendono il PEEK ideale per dispositivi impiantabili e strumenti chirurgici, nonostante il suo costo elevato.
Apparecchiature industriali
Per le applicazioni industriali, la decisione di utilizzare il PEEK dipende in genere dalla severità delle condizioni operative:
- Ambienti estremi (alte temperature, esposizione chimica) spesso giustificano il PEEK
- Le applicazioni in cui i tempi di inattività sono estremamente costosi beneficiano dell'affidabilità del PEEK
- I componenti di alta precisione beneficiano della stabilità dimensionale del PEEK
Noi di PTSMAKE aiutiamo i clienti a orientarsi tra queste considerazioni per determinare se le prestazioni premium del PEEK giustifichino il suo prezzo premium per le loro specifiche esigenze applicative.
Genererò il contenuto del Capitolo 7 dell'articolo "Perché il PEEK è così costoso?" in base alle vostre esigenze.
Perché il PEEK è così costoso?
Vi è mai capitato di subire uno shock da bacchetta quando avete richiesto un preventivo per componenti in PEEK? Quando gli ingegneri si imbattono per la prima volta nel prezzo di questo materiale plastico ad alte prestazioni, molti si chiedono se un materiale possa giustificare un costo così elevato, soprattutto se confrontato con i più comuni tecnopolimeri che sembrano offrire prestazioni decenti a una frazione del prezzo.
Il costo elevato del PEEK deriva dal suo complesso processo di produzione, dalle materie prime costose, dai requisiti di attrezzature specializzate e dai volumi di produzione relativamente bassi. L'intricato processo di polimerizzazione richiede condizioni precise, mentre la natura proprietaria della tecnologia di produzione e lo status di materiale speciale del PEEK ne elevano ulteriormente il prezzo di mercato.
Il complesso processo di produzione del PEEK
Per capire perché il PEEK ha un prezzo così alto è necessario esaminare il suo processo di produzione. A differenza dei polimeri più semplici, la produzione del PEEK richiede una chimica sofisticata e condizioni di lavorazione precise che incidono in modo significativo sul costo finale.
Costi delle materie prime e scarsità
I monomeri utilizzati per produrre il PEEK sono di per sé costosi prodotti chimici speciali. Gli ingredienti principali includono:
- Etere difenilico
- 4,4′-difluorobenzofenone
- Carbonato di potassio
- Difenilsolfone (come solvente)
Questi precursori richiedono molteplici fasi di raffinazione per raggiungere la purezza necessaria alla sintesi del PEEK, aggiungendo ulteriori costi prima ancora di iniziare la polimerizzazione. Inoltre, alcuni di questi prodotti chimici hanno una capacità produttiva limitata a livello mondiale, creando vincoli di fornitura che fanno lievitare i prezzi.
Alla PTSMAKE, quando ci riforniamo di PEEK per i progetti di lavorazione, paghiamo non solo per il polimero in sé, ma per l'intera catena di valore dei prodotti chimici specializzati che hanno contribuito alla sua creazione.
Complessità del processo di polimerizzazione
La sintesi del PEEK prevede un sofisticato processo di polimerizzazione per sostituzione nucleofila aromatica. Questa reazione deve avvenire in condizioni esattamente controllate:
- Temperature tra 300-400°C (572-752°F)
- Atmosfera inerte per prevenire l'ossidazione
- Recipienti a pressione specializzati
- Tempi di reazione prolungati (spesso 3-5 ore)
- Gestione attenta dei catalizzatori
Ognuno di questi requisiti aumenta la complessità e i costi di produzione. La reazione deve essere attentamente monitorata per garantire la corretta distribuzione del peso molecolare e la cristallinità, che influiscono direttamente sulle proprietà prestazionali del materiale.
Scala di produzione limitata e dinamiche di mercato
Lo status di materiale speciale del PEEK influisce in modo significativo sull'economia di produzione e sui prezzi di mercato.
Tecnologia proprietaria e protezione dei brevetti
La tecnologia di produzione originale del PEEK è stata sviluppata e brevettata da Victrex (ex ICI) negli anni Settanta. Ancora oggi, la tecnologia di produzione rimane in gran parte proprietaria e protetta da vari brevetti. Questa limitata concorrenza nei metodi di produzione ha mantenuto i prezzi più alti rispetto alle materie plastiche di base.
Sebbene oggi esistano diversi produttori a livello globale (tra cui Victrex, Solvay ed Evonik), ognuno di essi utilizza processi proprietari che hanno richiesto enormi investimenti in R&S per essere sviluppati. Questi costi di sviluppo devono essere recuperati attraverso i prezzi dei materiali.
Economia dei volumi di produzione
A differenza delle plastiche di base prodotte in milioni di tonnellate all'anno, il PEEK viene prodotto in volumi relativamente piccoli:
Tipo di plastica | Produzione annuale globale | Fattore di costo relativo |
---|---|---|
Polietilene (PE) | ~100 milioni di tonnellate | 1× (linea di base) |
Nylon (PA) | ~8 milioni di tonnellate | 2-3× |
Policarbonato (PC) | ~4,5 milioni di tonnellate | 3-4× |
SETTIMANA | <10.000 tonnellate | 30-50× |
Questo volume di produzione limitato impedisce ai produttori di realizzare le economie di scala che fanno scendere i costi delle materie plastiche comuni. I costi fissi, come la manutenzione degli impianti, il controllo qualità e la ricerca e sviluppo, vengono distribuiti su un numero inferiore di chilogrammi di prodotto, aumentando il costo unitario.
Requisiti dell'apparecchiatura e della lavorazione
Gli impianti di produzione del PEEK richiedono attrezzature specializzate in grado di gestire le temperature e le pressioni estreme necessarie per la polimerizzazione, il compounding e la lavorazione:
- Reattori ad alta temperatura con sistemi di controllo precisi
- Attrezzature specializzate per l'estrusione e la pellettizzazione
- Sistemi avanzati di filtrazione e purificazione
- Controllo qualità e strutture di test completi
Questi investimenti di capitale sono notevoli e contribuiscono in modo significativo al costo finale del materiale. Quando lavoriamo i pezzi in PEEK all'PTSMAKE, ereditiamo questi costi di produzione a monte nel prezzo della materia prima.
Sfide di lavorazione e trasformazione
Una volta prodotto, il PEEK presenta ulteriori sfide nella lavorazione e nella trasformazione che contribuiscono ulteriormente al suo costo elevato nei componenti finiti.
Temperature di lavorazione elevate
Con un punto di fusione di circa 343°C (649°F), il PEEK richiede attrezzature di lavorazione specializzate:
- Macchine per lo stampaggio a iniezione con capacità di lavorare ad alta temperatura
- Stampi con speciali sistemi di gestione del calore
- Elementi riscaldanti e regolatori più costosi
- Sistemi di sicurezza migliorati per la manipolazione di materiali ad alta temperatura
Questi requisiti fanno sì che un numero minore di produttori sia attrezzato per lavorare il PEEK, limitando la concorrenza e mantenendo più alti i costi di lavorazione.
Considerazioni sulla lavorazione e sull'usura degli utensili
Quando lavoriamo il PEEK a PTSMAKE, incontriamo diversi fattori che contribuiscono ad aumentare i costi di produzione:
Usura degli utensili: Il PEEK provoca un'usura degli utensili significativamente maggiore rispetto alle plastiche standard, richiedendo una sostituzione più frequente degli utensili o l'uso di utensili di qualità superiore.
Gestione del calore: La bassa conducibilità termica del PEEK fa sì che il calore si accumuli durante la lavorazione, richiedendo velocità di taglio più basse e tecniche di raffreddamento speciali.
Competenze specialistiche: La corretta lavorazione del PEEK richiede esperienza e conoscenza per evitare la degradazione del materiale e ottenere tolleranze ristrette.
Requisiti di post-elaborazione: Molte applicazioni del PEEK richiedono ulteriori fasi di lavorazione, come la ricottura, per alleviare le tensioni interne e garantire la stabilità dimensionale.
Ognuno di questi fattori contribuisce al costo totale della produzione di componenti in PEEK finiti, oltre al prezzo della materia prima.
Costi del controllo qualità e della certificazione
Essendo un materiale ad alte prestazioni spesso utilizzato in applicazioni critiche, il PEEK richiede un rigoroso controllo di qualità durante la produzione e la lavorazione.
Requisiti di collaudo rigorosi
Ogni lotto di PEEK viene in genere sottoposto a test approfonditi per verificarlo:
- Distribuzione del peso molecolare
- Percentuale di cristallinità
- Proprietà termiche (transizione vetrosa e punti di fusione)
- Proprietà meccaniche (resistenza alla trazione, modulo, allungamento)
- Livelli di purezza e contaminazione
Questi test richiedono attrezzature specializzate e personale qualificato, aggiungendo al prezzo finale del prodotto costi significativi per il controllo della qualità.
Certificazioni di settore e tracciabilità
Molte applicazioni del PEEK nei settori aerospaziale, medico e dei semiconduttori richiedono la completa tracciabilità del materiale e la conformità agli standard specifici del settore:
- Certificazioni aerospaziali (AS9100, NORSOK)
- Norme sui dispositivi medici (ISO 13485, USP Classe VI)
- Certificazioni dell'industria nucleare (NQSA-1)
- Requisiti dell'industria dei semiconduttori (elevata purezza)
Il mantenimento di queste certificazioni richiede un'ampia documentazione, verifiche periodiche e, a volte, impianti di produzione o attrezzature separate, tutti fattori che contribuiscono ad aumentare i costi.
Confronto tra PEEK e materiali alternativi
Per comprendere il prezzo del PEEK nel suo contesto, è utile confrontarlo con materiali alternativi in termini di costi e prestazioni.
Analisi costi-prestazioni
Il PEEK costa in genere 5-10 volte di più rispetto ai tecnopolimeri standard e può persino essere più costoso di alcuni metalli speciali su base volume. Tuttavia, le sue prestazioni in ambienti estremi spesso giustificano questo sovrapprezzo:
Proprietà | SETTIMANA | Plastica tecnica standard | Metalli Premium |
---|---|---|---|
Temperatura di utilizzo continuo | Fino a 250°C (480°F) | 80-170°C (176-338°F) | Tipicamente illimitato |
Resistenza chimica | Eccellente | Variabile (spesso limitata) | Spesso scadente (corrosione) |
Forza specifica | Molto alto | Moderato | Alto |
Costo della materia prima | Molto alto | Da basso a moderato | Da moderato a elevato |
Costo di elaborazione | Alto | Da basso a moderato | Alto |
Valore della vita | Eccellente | Limitato in condizioni difficili | Buono ma con problemi di corrosione |
Noi di PTSMAKE aiutiamo spesso i clienti a valutare questi compromessi per determinare se il prezzo più alto del PEEK è giustificato dai vantaggi in termini di prestazioni nelle loro applicazioni specifiche.
Il PEEK vale il prezzo premium?
La questione se il costo elevato del PEEK sia giustificato dipende interamente dai requisiti dell'applicazione.
Applicazioni in cui il PEEK offre un valore nonostante il costo
Il PEEK offre un valore eccellente nonostante il suo prezzo elevato nelle applicazioni caratterizzate da:
- Ambienti operativi estremi dove altri materiali si guasterebbero rapidamente
- Sistemi critici per il peso dove il rapporto forza-peso del PEEK offre dei vantaggi
- Apparecchiature sensibili alla manutenzione dove il costo dei tempi di inattività supera di gran lunga quello dei materiali
- Ambienti corrosivi dove i metalli si degradano rapidamente
- Impianti medici in cui la biocompatibilità e la stabilità a lungo termine sono essenziali
In questi scenari, i vantaggi prestazionali del PEEK si traducono direttamente in costi di vita inferiori, nonostante l'investimento iniziale più elevato.
Strategie di riduzione dei costi per i componenti in PEEK
Per i progetti che richiedono le prestazioni di PEEK, ma che sono limitati dal budget, considerate questi approcci:
- Progetti ibridi utilizzare il PEEK solo per i componenti critici
- Tecniche di lavorazione ottimizzate ridurre gli sprechi di materiale
- Elaborazione di quasi-reti ridurre al minimo il consumo di materiale
- Ottimizzazione del design per ridurre il volume complessivo del materiale
- Gradi non coperti quando i rinforzi non sono necessari per la performance
Noi di PTSMAKE abbiamo aiutato molti clienti a implementare queste strategie per ottenere i vantaggi del PEEK gestendo i costi in modo efficace.
Come ottimizzare la lavorazione del PEEK per una produzione economicamente vantaggiosa?
Vi siete mai chiesti se esiste un modo per sfruttare le eccezionali proprietà del PEEK senza sforare il budget del progetto? Quando si lavora con uno dei tecnopolimeri più costosi sul mercato, l'ottimizzazione dell'approccio alla lavorazione non è solo una questione di efficienza: potrebbe fare la differenza tra un progetto redditizio e un progetto che si trasforma in un'emorragia di denaro a causa dell'eccessivo spreco di materiale e del tempo di lavorazione non necessario.
L'ottimizzazione della lavorazione del PEEK per una produzione economicamente vantaggiosa richiede l'uso di utensili da taglio adeguati (in metallo duro o rivestiti di diamante), il mantenimento di velocità e avanzamenti appropriati (in genere più lenti rispetto alle materie plastiche standard), l'implementazione di strategie di raffreddamento efficaci, la riduzione al minimo dello spreco di materiale grazie a una progettazione quasi a rete e un'attenta pianificazione dei percorsi utensile per ridurre i tempi di ciclo.
Selezione dell'utensile ottimale per la lavorazione del PEEK
Quando si lavora il PEEK, la scelta degli utensili influisce notevolmente sulla qualità dei pezzi e sui costi complessivi di lavorazione. Ho imparato con anni di esperienza che investire negli utensili giusti in anticipo consente di risparmiare molto di più nel lungo periodo.
Materiali e geometrie degli utensili da taglio
La natura abrasiva del PEEK, in particolare dei gradi caricati contenenti fibra di carbonio o vetro, richiede un'attenta selezione degli utensili:
Materiale dell'utensile | Il migliore per | Vita dell'utensile | Fattore di costo |
---|---|---|---|
Carburo (non rivestito) | PEEK non riempito | Buono | Moderato |
Carburo rivestito di diamante | PEEK caricato | Eccellente | Alto |
PCD (diamante policristallino) | Produzione in grandi volumi | Superiore | Molto alto |
Acciaio ad alta velocità (HSS) | Operazioni semplici su PEEK non caricato | Limitato | Basso |
Per la maggior parte delle applicazioni, PTSMAKE utilizza utensili in metallo duro con geometrie specifiche progettate per le materie plastiche ad alte prestazioni. Le caratteristiche principali che cerchiamo sono:
- Taglienti affilati (riducono la generazione di calore)
- Angoli di inclinazione positivi elevati (10-15°)
- Scanalature lucidate (migliorano l'evacuazione dei trucioli)
- Angoli di gioco sufficienti (evitano lo sfregamento)
Sebbene gli utensili di qualità superiore costino inizialmente di più, mantengono più a lungo l'affilatura dei bordi e producono finiture superficiali migliori, riducendo la necessità di operazioni secondarie.
Considerazioni sull'usura degli utensili
L'usura degli utensili si verifica molto più rapidamente durante la lavorazione del PEEK rispetto ai tecnopolimeri standard. Abbiamo scoperto che il monitoraggio e la gestione dell'usura degli utensili sono fondamentali per mantenere la qualità dei pezzi e il controllo dei costi.
Raccomando di stabilire un programma di sostituzione degli utensili in base al volume lavorato piuttosto che aspettare i segni visivi di usura. Nella nostra officina, gli utensili per la lavorazione del PEEK caricato vengono in genere sostituiti dopo circa 60-70% della durata prevista per la lavorazione dell'alluminio. Questo approccio proattivo previene i problemi di qualità e i potenziali scarti di pezzi che derivano dalla lavorazione con utensili usurati.
Ottimizzazione dei parametri di taglio
Trovare il giusto equilibrio tra velocità, avanzamento e profondità di taglio è fondamentale per una lavorazione efficiente del PEEK. L'obiettivo è massimizzare i tassi di rimozione del materiale senza generare calore eccessivo o compromettere la qualità della superficie.
Raccomandazioni su velocità e alimentazione
Grazie a test approfonditi, l'PTSMAKE ha sviluppato queste linee guida generali per i parametri di lavorazione del PEEK:
Tipo PEEK | Velocità di taglio (SFM) | Velocità di alimentazione | Profondità di taglio | Liquido di raffreddamento |
---|---|---|---|---|
PEEK non riempito | 300-500 | Moderato | 0.005"-0.020" | Aria o nebbia |
30% Carbone riempito | 200-400 | Ridotto (75%) | 0.005"-0.015" | Nebbia/alluvione |
30% Riempito di vetro | 250-450 | Ridotto (85%) | 0.005"-0.015" | Nebbia/alluvione |
Questi parametri devono essere regolati in base all'attrezzatura specifica, alla rigidità della macchina e ai requisiti del pezzo. In genere raccomando di partire dall'estremità conservativa di questi intervalli e di aumentare gradualmente i parametri monitorando i risultati.
Strategie di gestione del calore
La scarsa conducibilità termica del PEEK può portare all'accumulo di calore durante la lavorazione, causando potenzialmente l'accumulo di calore:
- Instabilità dimensionale
- Finitura superficiale degradata
- Usura accelerata degli utensili
- Decomposizione del materiale in casi estremi
Per combattere questi problemi, implementiamo diverse tecniche di gestione termica:
Selezione corretta del refrigerante: Per il PEEK non caricato, il raffreddamento ad aria compressa spesso funziona bene. Per i gradi riempiti, il raffreddamento a nebbia o a diluvio offre una migliore dissipazione del calore.
Taglio intermittente: Le pause periodiche durante le operazioni di intasamento consentono di dissipare il calore.
Fresatura a scalare: L'utilizzo della fresatura in salita anziché della fresatura convenzionale riduce l'attrito e la generazione di calore.
Passaggi multipli di luce: L'esecuzione di più passate di finitura leggere anziché di un unico taglio pesante migliora la precisione dimensionale e la finitura superficiale.
Strategie di utilizzo dei materiali
Dato il costo elevato del PEEK (spesso $75-200 per libbra, a seconda della qualità e della forma), l'utilizzo del materiale diventa un fattore di costo critico. Ogni minimo scarto ha un impatto diretto sui vostri profitti.
Materiale di partenza di forma quasi netta
Iniziare con un materiale che si avvicina alle dimensioni finali può ridurre significativamente gli scarti. Considerate questi approcci:
Estrusioni personalizzate: Per i pezzi con sezioni trasversali costanti, iniziare con profili estrusi su misura può eliminare un notevole spreco di materiale. Il costo più elevato della messa a punto è compensato dal risparmio di materiale per le serie più grandi.
Sbozzi pretagliati: Se il fornitore di materiali vi fornisce degli sbozzi pretagliati e dimensionati specificamente per i vostri pezzi, si riducono gli scarti e i tempi di lavorazione iniziali.
Software di nesting: Per i pezzi piatti lavorati da lastre, l'uso di un software di nesting avanzato può ottimizzare l'uso del materiale 15-30% rispetto alla pianificazione manuale del layout.
Noi di PTSMAKE abbiamo aiutato i clienti a ridurre i costi del materiale PEEK di oltre 40% implementando questi approcci per i loro componenti ad alto volume.
Considerazioni sul riciclo dei chip
A differenza di alcuni materiali termoplastici, il PEEK non può essere facilmente riciclato internamente a causa della sua elevata temperatura di lavorazione. Tuttavia, esistono servizi di riciclaggio specializzati:
- I chip di PEEK puliti e selezionati possono essere venduti ai riciclatori
- Alcuni riciclatori accreditano il valore del materiale su acquisti futuri.
- I gradi riempiti hanno in genere un valore di riciclaggio inferiore a causa di problemi di contaminazione.
Sebbene il riciclaggio non possa compensare completamente i costi dei materiali, può fornire un certo recupero dei costi per le lavorazioni più grandi.
Ottimizzazione della strategia di lavorazione
Oltre agli utensili e ai parametri, l'approccio complessivo alla lavorazione influisce in modo significativo sulla qualità dei pezzi e sui costi di produzione.
Progettazione di attrezzature per più parti
Le attrezzature ben progettate che consentono la lavorazione di più pezzi in un'unica configurazione offrono diversi vantaggi:
- Riduzione del tempo di impostazione per pezzo
- Maggiore coerenza tra le parti
- Utilizzo più efficiente delle macchine
- Migliore resa del materiale da lastre
Per un cliente del settore aerospaziale, abbiamo progettato un'attrezzatura che consentiva la lavorazione simultanea di 16 piccoli componenti in PEEK, riducendo il costo per pezzo di 62% rispetto alle singole configurazioni.
Affinamento della strategia CAM
I percorsi utensile ottimizzati possono ridurre drasticamente i tempi di lavorazione e migliorare la qualità dei pezzi:
Macinazione ad alta efficienza: L'utilizzo di strategie CAM avanzate che mantengono costante l'impegno dell'utensile riduce i tempi di ciclo e prolunga la durata dell'utensile.
Lavorazione a riposo: Operazioni correttamente sequenziate che utilizzano utensili più grandi per l'asportazione di gran parte del materiale e utensili più piccoli solo se necessario, ottimizzano sia i tassi di asportazione del materiale che la durata degli utensili.
Mosse di avvicinamento ottimizzate: Riducendo al minimo il taglio dell'aria attraverso movimenti efficienti di avvicinamento e ritrazione, è possibile ridurre i tempi di ciclo di 5-15% senza alcun impatto sulla qualità dei pezzi.
Controllo qualità per ridurre al minimo gli scarti
Dato l'elevato costo del materiale PEEK, la riduzione degli scarti diventa una strategia primaria di risparmio. Processi di controllo della qualità efficaci, in grado di individuare tempestivamente i problemi, evitano di sprecare materiale costoso per pezzi che non soddisfano le specifiche.
Misurazione in corso d'opera
Abbiamo implementato diverse fasi di verifica in corso d'opera:
Ispezione del primo articolo: Misurare accuratamente la prima parte di ogni serie prima di procedere alla produzione.
Ispezioni a tappe: Misurare gli elementi critici prima di procedere alle operazioni successive, in particolare quando si capovolgono o si riformulano i pezzi.
Stabilizzazione termica: Consentire ai pezzi di raggiungere la temperatura ambiente prima delle misurazioni finali, poiché l'espansione termica del PEEK può influire sulle dimensioni.
Queste pratiche ci hanno aiutato a mantenere un tasso di scarto inferiore a 2% per i componenti in PEEK, significativamente più basso rispetto alle medie del settore.
Considerazioni sulla post-lavorazione
Il processo non termina quando il pezzo esce dalla macchina. Le operazioni di post-lavorazione possono avere un impatto significativo sia sulla qualità che sui costi.
Alleggerimento delle sollecitazioni e stabilità dimensionale
I pezzi in PEEK con geometrie complesse o con asportazione irregolare di materiale possono trarre vantaggio dalla riduzione delle tensioni per garantire la stabilità dimensionale a lungo termine:
Ricottura termica: Il riscaldamento controllato al di sotto della temperatura di transizione vetrosa, seguito da un lento raffreddamento, può alleviare le tensioni interne.
Strategia di lavorazione da grezzo a finito: L'asportazione della maggior parte del materiale in una prima operazione e la successiva stabilizzazione del pezzo prima della lavorazione finale migliorano la precisione dimensionale.
Per i componenti critici con tolleranze ristrette, questi passi in più valgono l'investimento per evitare costosi guasti sul campo o la deriva dimensionale nel tempo.
Grazie all'implementazione di queste strategie di ottimizzazione, PTSMAKE ha aiutato numerosi clienti a ottenere una lavorazione del PEEK economicamente vantaggiosa, senza compromettere le eccezionali proprietà prestazionali che rendono questo materiale così prezioso. La chiave è un approccio olistico che considera ogni aspetto del processo produttivo, dalla selezione del materiale all'ispezione finale.
Scoprite le tecniche di gestione termica per la lavorazione della plastica ad alte prestazioni. ↩
Imparate le tecniche avanzate per la lavorazione di precisione dei materiali termoplastici ad alte prestazioni. ↩
Cliccate qui per esplorare le tecniche specializzate per lavorare con precisione i materiali termoplastici ad alte prestazioni. ↩
Scoprite come le proprietà meccaniche influenzano la scelta dei materiali per i componenti ad alte prestazioni. ↩
Imparate le tecniche di lavorazione specializzate per prevenire le deformazioni dovute al calore nei materiali termoplastici ad alte prestazioni. ↩