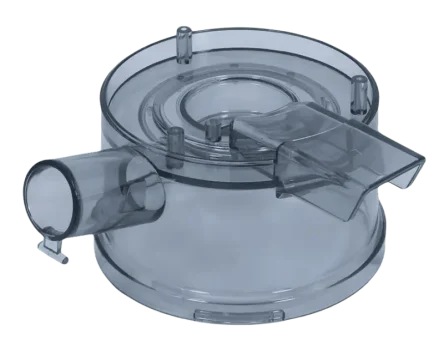
低Moq 100個
50% コスト削減 vs US/EU
迅速な納期とグローバル配送
30トンから600トンまでの機械 30トンから1,600トンまで






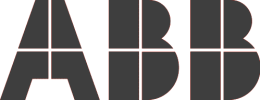

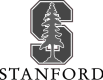
お客様の声
当社の顧客は世界中におり、そのフィードバックがすべてを物語っています。お近くのお客様から私どもの評判をお聞きになりたい場合は、ご遠慮なくお問い合わせください。
HDPE射出成形を使用するトップ8産業
HDPE射出成形にPTSMAKEを選ぶ理由
ISO 9001認証を取得し、0.01mm未満の精度と、すべての製造工程における99.8%の一次検査合格率を誇ります。
高度な機械を駆使して寸法精度を確保し、設計を最適化することで、生産コストを30%まで削減します。
8つの主要産業にわたる複雑なプロジェクトを扱う30人以上の専門家を擁するエンジニアリング・チームでの22年以上の専門経験。
戦略的な中国拠点は、グローバルな品質基準を維持しながら、30-40%のコストを削減し、数量ベースの割引を提供しています。
HDPE射出成形の品質管理
厳格な材料試験 が品質管理プロセスを開始します。当社では、HDPEの適正密度(0.941~0.960g/cm³)と引張強度(20~37MPa)をバッチごとにテストし、反りを防止して安定した部品品質を保証しています。
温度精度 は欠陥を防ぐために非常に重要です。当社のシステムは、溶融温度を246~280℃、金型温度を45~65℃に維持し、±5℃の許容差で、HDPEでは4%に達することもある収縮の問題を排除します。
多段階検査 問題を早期に発見します。当社では、100%の目視検査、精密ノギス(精度±0.02mm)を使用した10%の寸法確認、HDPEの高い熱膨張係数(143μm/℃)に対応するための高度な反り検出システムを活用しています。
工程内検査と最終検査: 品質チェックは生産全体を通して行われます。初品検査(FAI)、ノギスやゲージを使用した毎時の工程内寸法検査、最終部品の100%目視検査を実施しています。CMM測定により、お客様の図面に対する重要な寸法を検証します。
包括的な文書 はトレーサビリティを保証します。各バッチには、完全な処理パラメータ、検査結果、材料証明書を含む固有のIDが付与され、生産工程間の不整合に関する懸念に対処する。
- PTSMAKEは、20年以上の経験とISO9001認証取得のワークフローにより、信頼できる高品質のオーバーモールディングとインサート成形ソリューションを提供します。年中無休のエンジニアリングサポートチームが、業界平均の3倍の速さで問題を解決します。
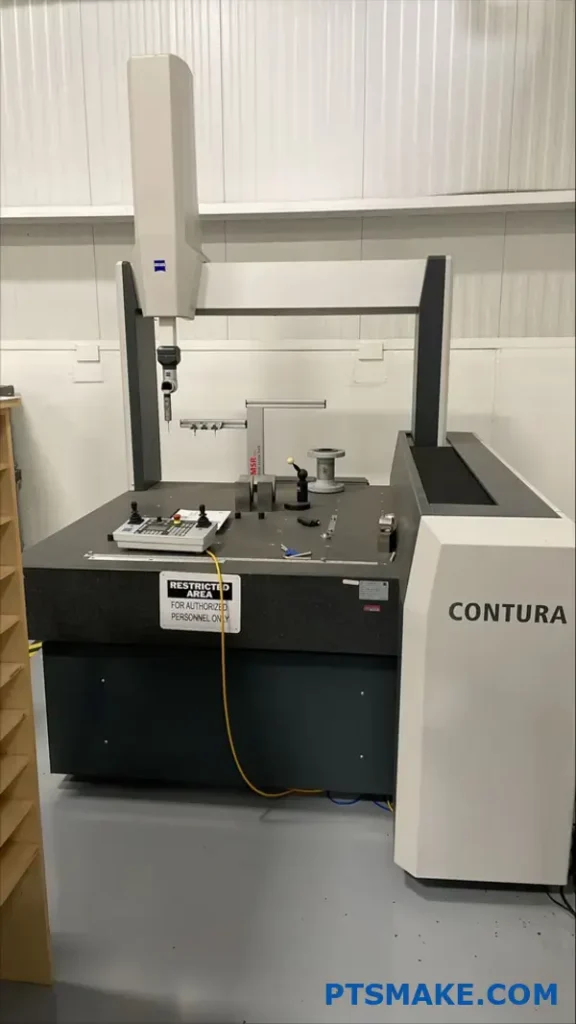
「我々の新しいコンシューマーガジェットのケーシングの耐久性と仕上げは素晴らしい。PTSMAKEは私たちのデザインニーズを理解し、イメージ通りのものを提供してくれました。彼らのサービスを強くお勧めします。
アントワーヌ、プロダクトデザイナー、フランス"
HDPE射出成形の最も一般的な材料
一般HDPE
ハイインパクトHDPE
食品グレードHDPE
高剛性HDPE
耐紫外線HDPE
耐薬品性HDPE
医療グレードHDPE
ハイフローHDPE
ABS射出成形の一般的なリードタイムを理解する
- HDPE射出成形プロジェクトの一般的なリードタイムは、大きく異なる場合があります。最初の射出成形金型の作成に最も時間がかかることが多く、通常4~8週間、非常に複雑な設計の場合はそれ以上かかることもあります。
- HDPE部品の設計の複雑さは、金型製作時間に直接影響します。単純な形状であれば、金型製作は短時間で済みます。複雑なディテールや厳しい公差は、より精密な機械加工を必要とし、この段階を延長します。
- カスタム射出成形金型の準備が整い、承認されると、実際のHDPE部品の生産が始まります。ここでのリードタイムは注文数量に大きく依存します。少量の試作品であれば数日、大量生産であれば数週間かかります。
- 特定のHDPEグレードの材料入手可能性も、スケジュールに影響する可能性がある。HDPEは一般的ですが、特殊なグレードは調達に時間がかかる場合があります。PTSMAKEは、お客様のプロジェクトのために効率的に材料を調達できるよう、真摯に取り組みます。
- 最後に、必要な品質管理チェックと、組み立てや特殊仕上げのような後処理工程が全体のリードタイムに追加されます。PTSMAKEは、最初のデザインレビューから最終出荷までのすべての段階を考慮した、明確なタイムラインを提供します。
- 2002年以来、お客様のパートナーとして、PTSMAKEは精密射出成形サービスのリードタイムに関する透明性の高いコミュニケーションに重点を置き、試作品からフル生産まで効果的に計画できるようにしています。
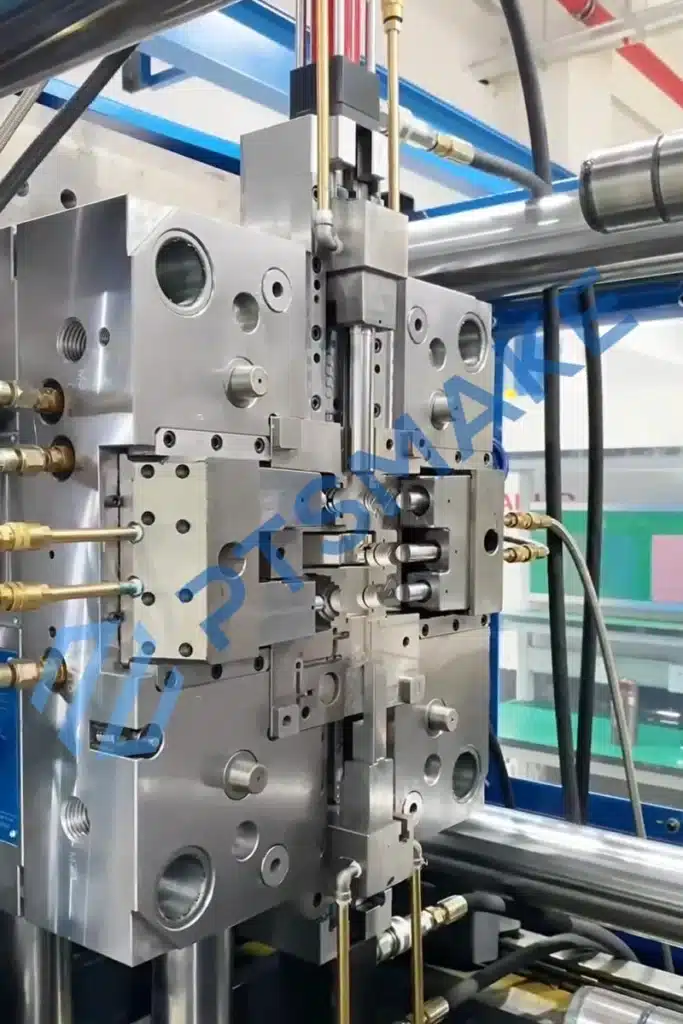
ABS射出成形に欠かせない8つのステップ
1.素材の選択
2.金型設計
3.材料の準備
4.マシンセットアップ
5.射出工程
6.冷却フェーズ
7.部品の排出
8.品質検査
HDPE射出成形の費用対効果に優れたソリューション
1.部品設計の最適化(DFM)
2.複雑な機能の簡素化
3.均一な壁の確保
4.現実的な公差を指定する
5.適切なドラフトを組み込む
6.アンダーカットの最小化
7.マルチキャビティ金型の活用
8.家族の型を考える
9.製造ノウハウのパートナー
HDPE射出成形のカスタマイズオプション
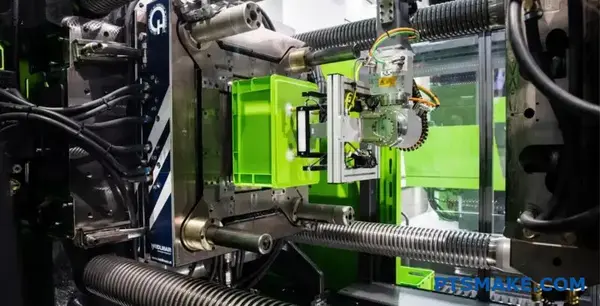
素材のカスタマイズ
カラーカスタマイズ
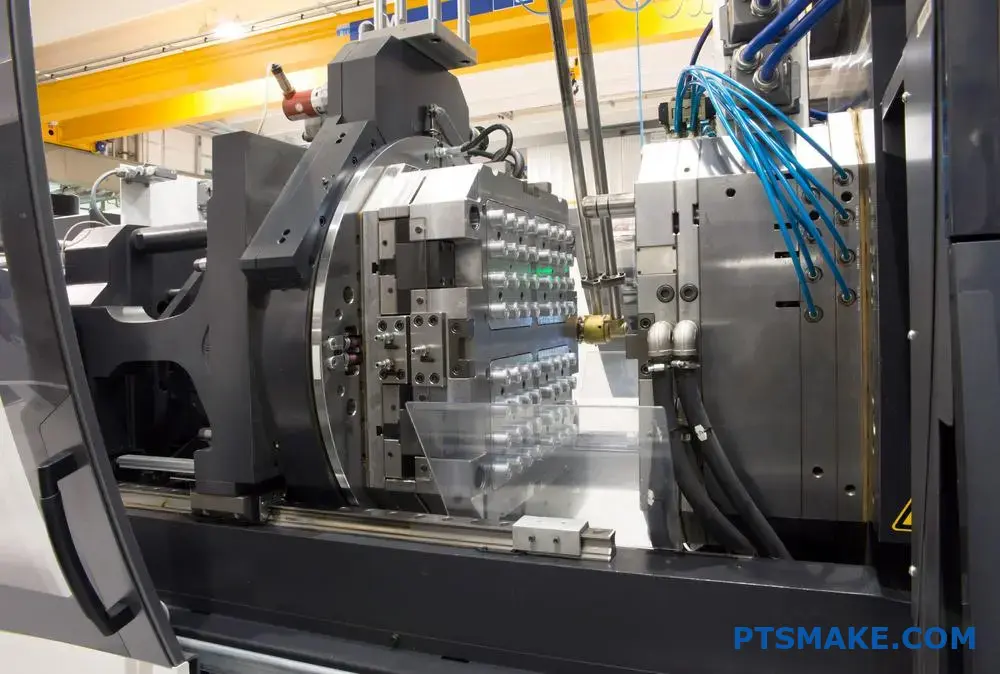
表面仕上げのカスタマイズ
ジオメトリー制限なし
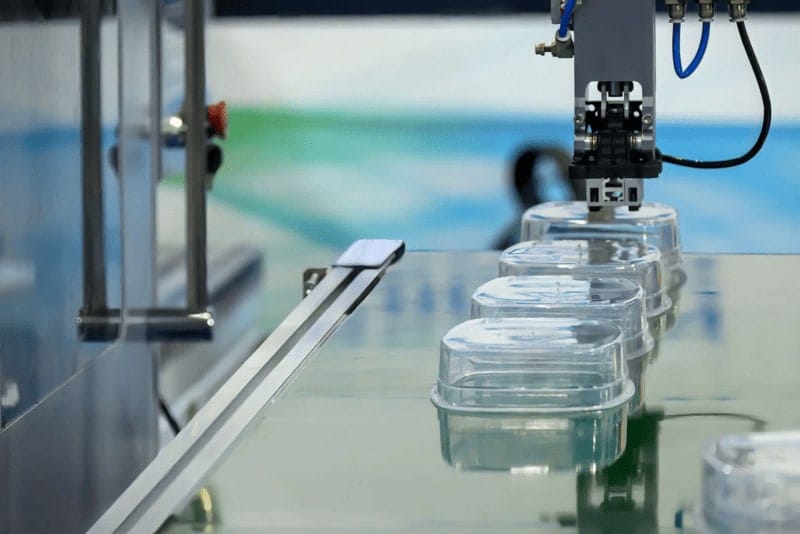
ボリュームの柔軟性
統合の挿入
HDPE射出成形の成功事例
米国におけるヘビーデューティ・ストレージ・ソリューション
クライアントのタイプ 頑丈なストレージ・ソリューションのメーカー
クライアントの国 米国
クライアントの問題 この米国の大企業は、産業用および小売市場向けに、耐久性に優れ、積み重ね可能なHDPE木枠を毎年数百万個必要としていました。既存のサプライヤーは、木箱の肉厚を常に均一に保つことができませんでした。その結果、木枠を積み込む際にゆがみが生じたり、積み重ねが不安定になったりして、倉庫や小売店の棚で問題を引き起こしていました。バッチ間の色の一貫性も悪かった。さらに、サプライヤーからの頻繁な納品遅延により、小売パートナーとの約束が乱れていた。同社は、大量かつ高品質な生産が可能な、信頼できる*HDPE射出成形*のスペシャリストを必要としていました。
私たちのソリューション PTSMAKEは、この大量生産の課題に戦略的に取り組みました。私たちは、高速サイクルタイムと完全に均一な溶融分布のために特別に最適化された堅牢なマルチキャビティ*プラスチック射出成形金型*を設計・製作しました。ホットランナーシステムを金型設計に組み込み、流量制御を改善し、材料の無駄を減らし、サイクルタイムをさらに短縮しました。肉厚の問題に対処するため、成形中にセンサーを使用した自動インプロセスモニタリングを導入しました。色の一貫性については、*射出成形*中の正確なプロセス・パラメーター制御とともに、入荷するHDPE材料とカラー・マスターバッチの厳格な品質管理チェックを確立しました。当社の生産計画チームは、クライアントの予測と緊密に連携し、スムーズな納期遵守を実現しました。
結果 PTSMAKEは一貫して、強度、寸法、積み重ね可能性のすべての仕様を満たすHDPEクレートを納品しました。色はすべてのバッチで均一でした。当社の生産効率により、クライアントのコスト目標内に収まりながら、厳しい数量要件を満たすことができました。信頼性の高いサプライチェーンにより、小売店での在庫切れの問題も解消されました。顧客は特に、PTSMAKEの積極的なコミュニケーション、品質重視、そして*大量生産*のシームレスな対応を高く評価し、その結果、調達チームは他の戦略的タスクに集中できるようになりました。
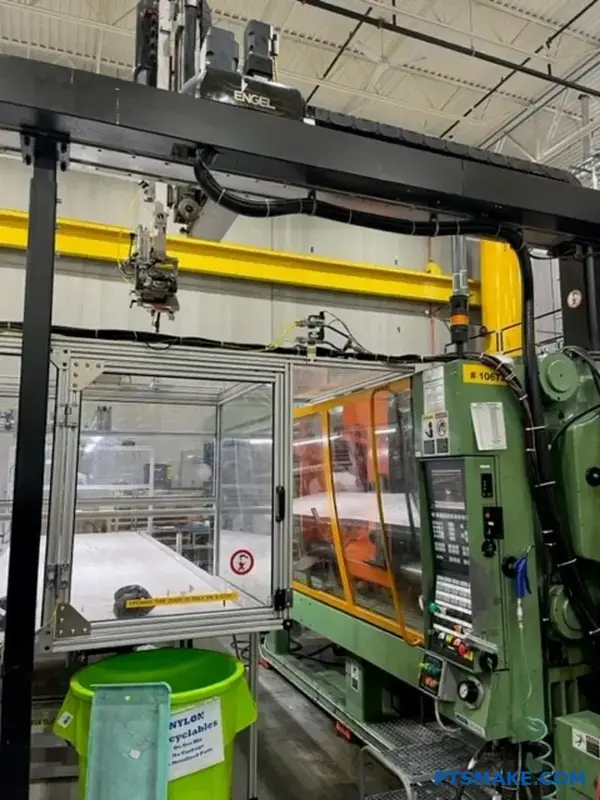