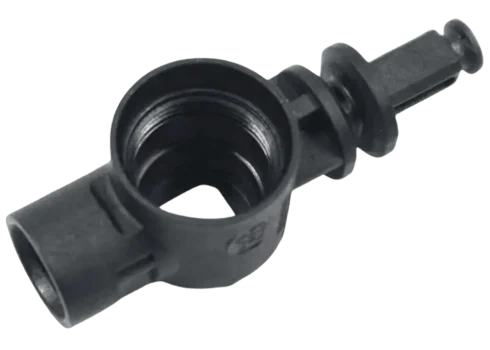
低Moq 100個
複雑部品精密成形
迅速な納期とグローバル配送
30トンから600トンまでの機械 30トンから1,600トンまで






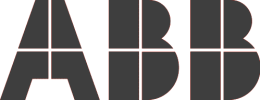

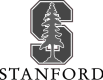
お客様の声
当社の顧客は世界中におり、そのフィードバックがすべてを物語っています。お近くのお客様から私どもの評判をお聞きになりたい場合は、ご遠慮なくお問い合わせください。
高温射出成形ソリューションに依存する8つの主要産業
精密な成形ソリューションを通じて、耐熱部品がいかに重要な分野で最高のパフォーマンスを発揮できるかをご覧ください。
高温射出成形にPTSMAKEを選ぶ理由
素材の専門知識
50種類以上の高温材料(PTFE、PEEK、PPS、PPSU、PPO、PI、PVDF、PEI、PAI、PBI、LCP)を±0.01mmの精度で加工します。
先端技術
高度な機械を駆使して寸法精度を確保し、設計を最適化することで、生産コストを30%まで削減します。
迅速なターンアラウンド
当社の50台以上の先進的な成形機は、15日の試作サイクルと30%の生産スケジュールの短縮を可能にします。
厳格な品質
3段階の品質チェックにより、不良率は0.2%以下を維持し、成形品のトレーサビリティも万全です。
PTSMAKEで高温射出成形の最高品質を保証する方法
- 高温射出成形は、厳しい業界標準を満たすために厳格な品質管理を必要とします。PTSMAKEでは、5段階の品質管理システムを用いて、すべての部品の精度と信頼性を保証しています。それでは、その方法をご紹介しましょう。
- ステージ1:材料の選択と予備テスト
まず、ASTM D638規格を用いて、ポリマー材料を300°F~500°Fで試験します。当社のエンジニアは、材料を承認する前に耐熱性、収縮率、化学的安定性を検証します。これにより、高温成形時の反りや劣化を防ぎます。
- ステージ2:精密金型設計
私たちのチームは、シーメンスNXソフトウェアを使用して±0.005mmの精度で金型を設計します。熱分布パターンをシミュレーションしてホットスポットを特定し、冷却チャネルを最適化します。98%の金型は、このデジタル検証プロセスにより、第一粒子検査(FAI)に合格しています。
- ステージ3:リアルタイム生産監視
成形中、センサーはバレル温度(最高450°F)、射出圧力(1,500~2,500psi)、サイクル時間を追跡します。逸脱があれば、自動的に警告が発せられます。当社のオペレーターは、校正されたツールを使用して毎時間チェックを行い、バッチ間で一貫した出力を保証します。
- ステージ4:ポストプロセス検証
私たちは100%の部品をテストします:
- 寸法精度(CMM測定)
- 表面欠陥(3D光学スキャナー)
- 機械的強度(ISO 527引張試験)
重要部品は250°Fで48時間以上の熱老化試験を行う。
- 第5ステージ継続的改善
すべてのプロジェクトは、当社のクラウドベースのQMSに文書化されます。不良率(常に0.3%未満)や顧客からのフィードバックなどのデータを分析し、プロセスを改善します。このシステムにより、ファーウェイのようなクライアントは、高熱ロボットアプリケーションで部品の不良を67%削減することができました。
- 20年以上の経験とISO9001認証のワークフローにより、PTSMAKEは信頼できる高温射出成形ソリューションを提供します。年中無休のエンジニアリングサポートチームが、業界平均の3倍の速さで問題を解決します。
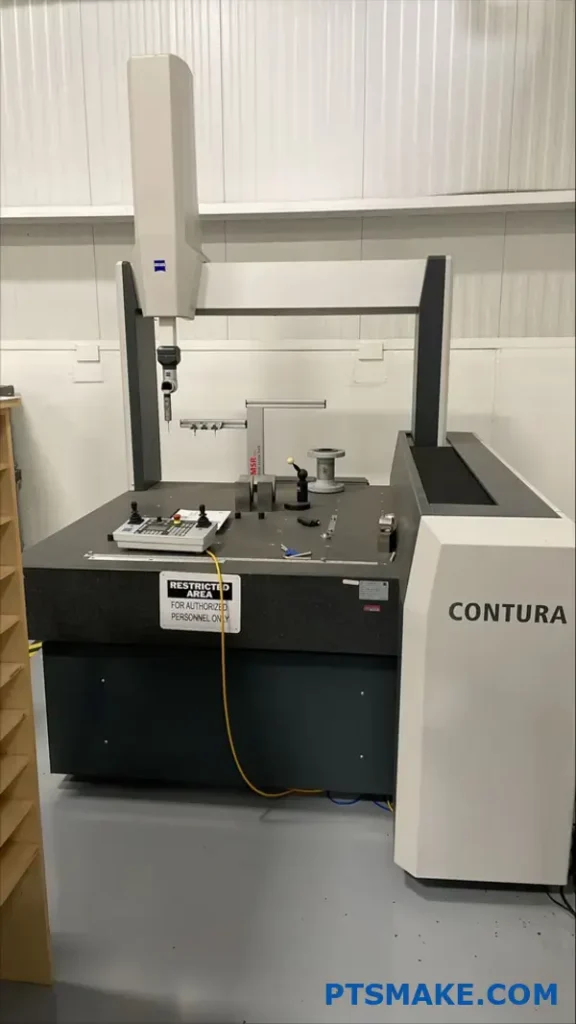
"PTSMAKEは、私たちの航空宇宙プロジェクトに耐熱ナイロンギアを納入しました。彼らの成形プロセスはMILスペック要件を満たしていました。130℃の連続使用でも反りの問題はありませんでした。以前のサプライヤーと比較して3週間短縮できました。
ライアン・カーター、製造部長、米国"
高温射出成形用トップ素材
高温射出成形の一般的なリードタイム
製造スケジュールにおけるスピードと精度のバランス
- 高温射出成形プロジェクトは、材料特有の課題により、リードタイムが長くなることがよくあります。PTSMAKEでは、カスタム金型の平均リードタイムを2~3週間、生産バッチの平均リードタイムを7~10日に短縮しました。精密製造における当社の20年以上の専門知識は、品質を損なうことなくプロセスを合理化するのに役立ちます。
- リードタイムに影響する主な要因には、材料の硬化要件(PEEK、PEIなど)、部品の複雑さ、注文量などがあります。お急ぎの場合は、納期を30~40%短縮する迅速なサービスを提供しています。弊社の専用プロジェクト管理システムにより、85%を超えるプロジェクトが当初の納期を達成、またはそれを上回っています。
- 見積もりや設計のフィードバックには、48~72時間の応答時間を維持しています。HUA WEIやBMWのようなクライアントは、深圳と東莞にある当社のISO認定施設を信頼しています。クライアントポータルを通じたリアルタイムの更新により、あらゆる段階での透明性を確保しています。
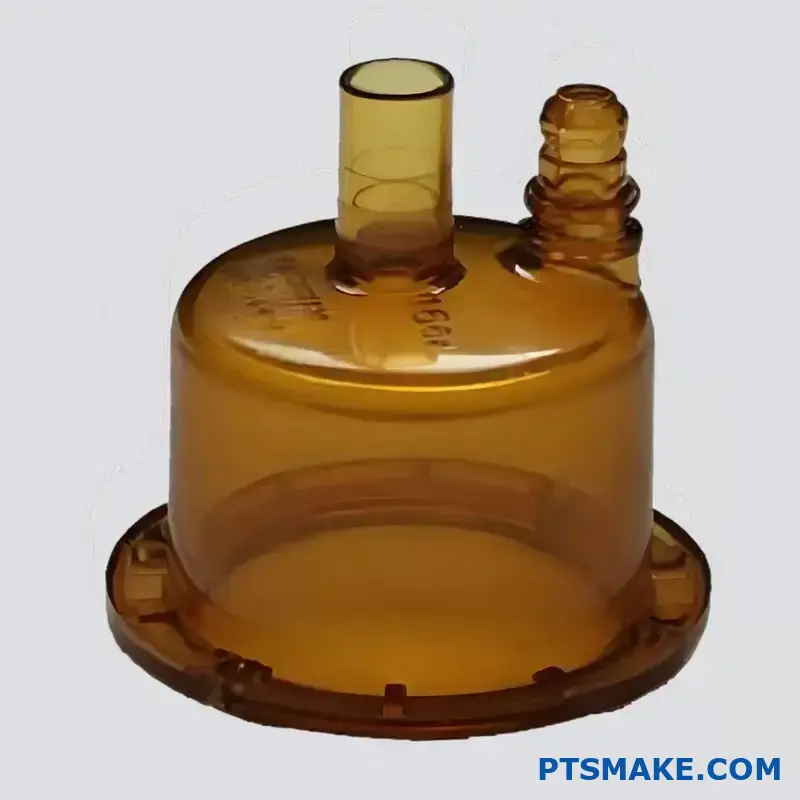
高温射出成形:8段階の製造工程
高品質な大型射出成形部品を効率的に生産するための重要なステップをご紹介します。
1.素材の選択
お客様の用途に適合した耐高温ポリマーをお選びください。PTSMAKEは、PEEK、PEI、LCPのような300~400℃に耐える先端材料を使用しています。
2.金型設計
耐熱鋼合金で精密工具を作成します。20年以上の経験により、最適なゲート配置と冷却チャンネルを確保します。
3.マシンセットアップ
精密な温度制御を備えた射出ユニットを構成します。当社では、安定した結果を得るために±3℃の安定性を持つ450トン以上のマシンを使用しています。
4.材料の乾燥
工業用乾燥機を使用して湿気を除去します。ISO認証取得のプロセスにより、吸湿性のある素材に気泡が発生するのを防ぎます。
5.射出成形
制御された圧力下で溶融材料を注入します。PTSMAKEのクローズドループシステムは、0.5%のショット重量の一貫性を維持します。
6.冷却プロセス
熱シミュレーションで冷却時間を最適化。当社のデュアルサーキットシステムは、サイクルタイムを15-20%短縮します。
7.部品の排出
カスタムリフターで自動脱型を実現薄肉部品の変形を防止します。
8.品質検査
CMMとCTスキャンを使用して寸法を検証します。当社の100%検査プロトコルは航空宇宙規格に適合しています。
高温射出成形のための費用対効果の高いソリューション
高熱用途で品質を犠牲にすることなく経費を削減する実践的戦略
1.材料の最適化
PEEKやLCPのような耐熱性ポリマーは、必要な場合にのみ選択してください。PTSMAKEは、シミュレーションツールを使用して、材料の最小厚さを特定します。
2.金型設計の効率
マルチキャビティ金型は、サイクルあたりの生産量を増加させます。当社の20年以上にわたる専門知識により、クイックチェンジインサートを備えた耐久性のある金型を提供し、ダウンタイムを削減します。
3.サイクルタイムの短縮
精密な温度制御により冷却フェーズを短縮。リアルタイムの温度モニタリングにより、18%の高速サイクルを実現しています。
4.オートメーション
ロボットによる部品取り出しで人の介入を最小限に。PTSMAKEは24時間365日の生産に対応する統合システムを導入しています。
5.一括購入
類似したプロジェクトと資材発注をプールする。連結調達により、お客様のためにボリュームディスカウントを交渉します。
6.デザインの簡素化
アンダーカットや肉厚のばらつきを減らすことで、サイクルタイムを短縮します。当社のDFM分析では、通常12-18%のコスト削減の機会を特定します。
7.二次工程の排除
PTSMAKEでのインモールドラベリング/テクスチャリングは、後加工のステップを削除します。CNC加工と成形を1社で行うシングルソースサービスです。
高温射出成形のカスタマイズオプション
高温射出成形は、厳しい産業ニーズに対応するために、特殊なカスタマイズを必要とします。PTSMAKEでは、材料、金型、工程を極端な熱条件に対応させることに重点を置いています。私たちのソリューションは、お客様の部品が高熱下でも構造的完全性と性能を維持することを保証します。
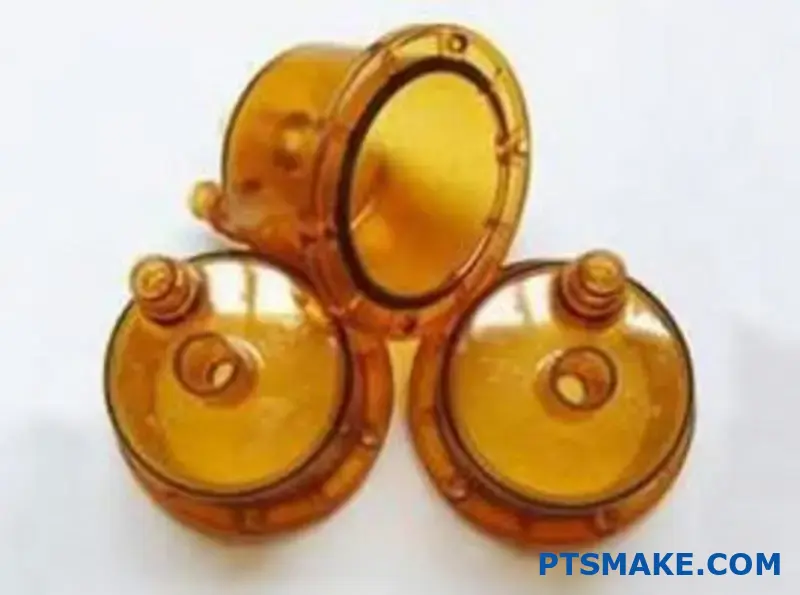
高温耐性のための材料カスタマイズ
PEEK、PEI(ウルテム)、PPS、LCPなど、20種類以上の高温プラスチックを提供しています。これらの材料は、反りや劣化に耐えながら、300°Fから500°Fの温度に耐えます。顧客は、機械的強度、耐薬品性、または電気絶縁の必要性に基づいて特定のグレードを選択します。例えば、医療機器メーカーは、オートクレーブ適合性のためにウルテムを選択することがよくあります。
金型設計の柔軟性
当社のエンジニアは、耐熱スチールコアと熱制御に最適化された冷却チャンネルを備えたカスタム金型を製作します。ホットランナーシステムを備えたマルチキャビティ金型は、大量注文にも対応可能です。高温サイクルでの焼き付きを防ぐため、ゲートの位置やベントを調整します。薄肉(0.5mm以下)やアンダーカットのような複雑な形状も、モジュラー金型設計により実現可能です。
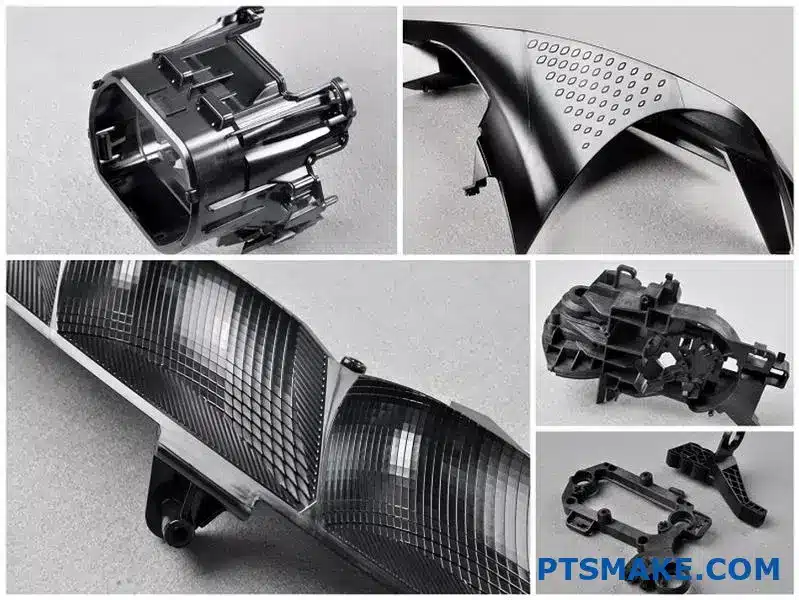
表面仕上げと後加工オプション
表面は、テクスチャー、ポリッシュ、カスタムブランドからお選びいただけます。電子機器には帯電防止コーティングを、可動部品には低摩擦処理を施します。超音波溶接スポットやEMI/RFIシールド層などの二次加工も可能です。すべての仕上げは、繰り返しの熱暴露に対する耐久性を確認するため、熱サイクル試験を受けています。
ラピッドプロトタイピングからフルプロダクションスケーリングまで
PTSMAKEは、高温材料を使用した試作品を72時間以内に提供します。当社のISO認定施設は、小ロットから50万個以上の生産まで、シームレスなスケーリングをサポートします。BMWやHuaweiのようなクライアントは、金型調整のためのCNC機械加工と自動成形プロセスを組み合わせた当社のハイブリッドアプローチを活用しています。
成功事例高温射出成形ソリューション
ドイツの医療機器メーカー
ドイツのある医療機器メーカーは、滅菌可能な機器用の耐高温ハウジングを必要としていた。既存のサプライヤーは、射出成形時に材料が反り、シール面が安定しないことに悩んでいました。
PTSMAKEは、コンフォーマル冷却チャンネルを備えた金型を再設計し、熱安定化PEEK材料に切り替えました。これにより、サイクルタイムを18%短縮し、500回以上の滅菌サイクルにわたって±0.05mmの寸法安定性を達成した。
このソリューションは、クライアントが重要なWHO認証を取得し、新興市場に進出するのに役立った。
PTSMAKEは、コンフォーマル冷却チャンネルを備えた金型を再設計し、熱安定化PEEK材料に切り替えました。これにより、サイクルタイムを18%短縮し、500回以上の滅菌サイクルにわたって±0.05mmの寸法安定性を達成した。
このソリューションは、クライアントが重要なWHO認証を取得し、新興市場に進出するのに役立った。
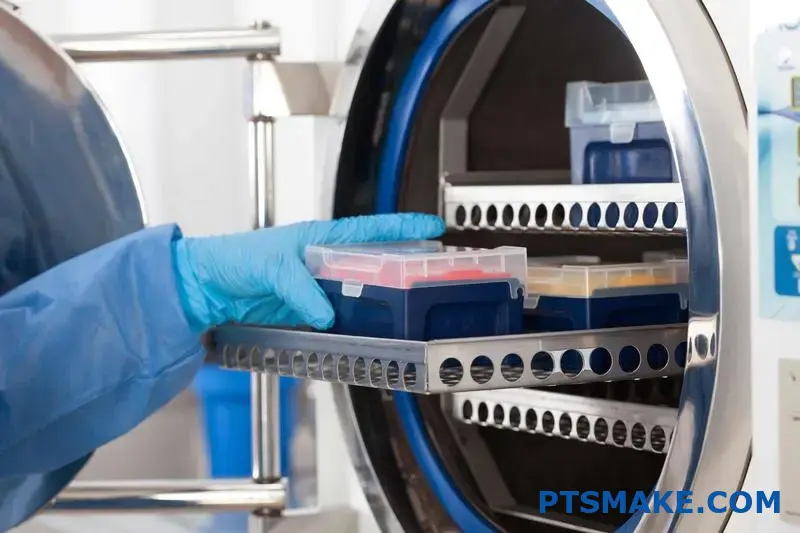
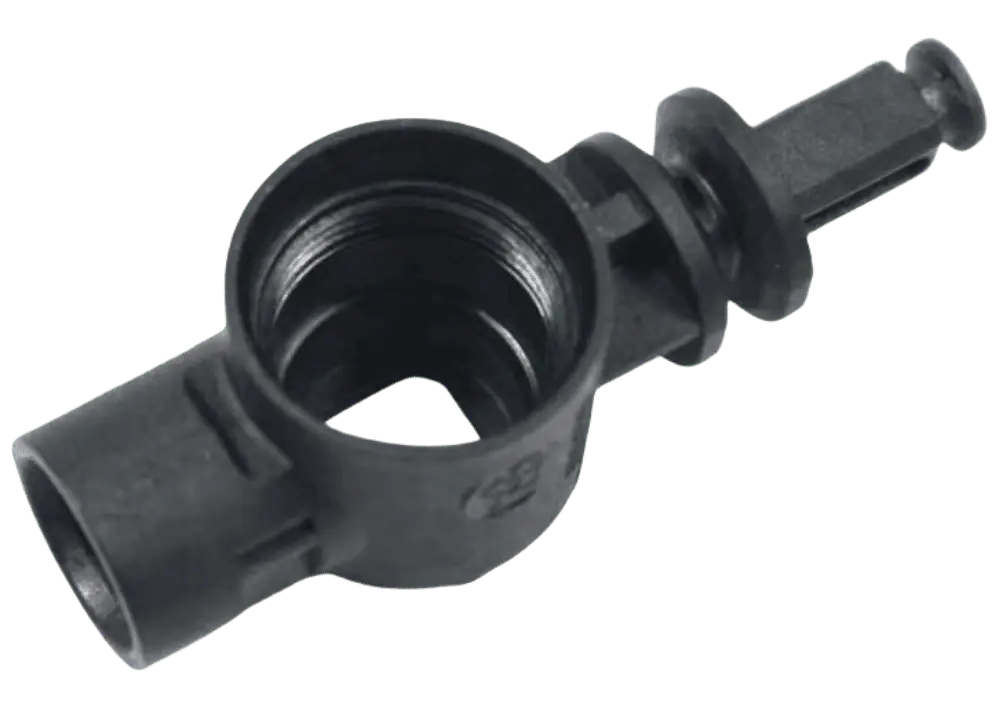
欧州産業ロボット企業
あるヨーロッパの産業用ロボット会社は、200℃の連続運転で精度を維持する複雑なギア機構を必要としていました。以前のベンダーは、10,000サイクル後に要求されるバックラッシュ公差<0.01mmを達成できませんでした。
PTSMAKEは、CNC加工された金型インサートと射出成形中の高精度温度制御を組み合わせたハイブリッドアプローチを導入しました。その結果、歯車は業界のベンチマークよりも摩耗が少ない98%を示し、クライアントはメンテナンス間隔を延長し、主要なファクトリーオートメーションプロジェクトを獲得することができました。
PTSMAKEは、CNC加工された金型インサートと射出成形中の高精度温度制御を組み合わせたハイブリッドアプローチを導入しました。その結果、歯車は業界のベンチマークよりも摩耗が少ない98%を示し、クライアントはメンテナンス間隔を延長し、主要なファクトリーオートメーションプロジェクトを獲得することができました。
高温射出成形に共通する課題の克服
高温射出成形には、独特の材料挙動や生産要件を扱うための専門知識が要求される。
課題1:素材の劣化
PEEKやPEIのような高温ポリマーは、過熱すると分解してしまいます。当社では、リアルタイムの熱モニタリングシステムと認定材料データベースを使用して、最適な溶融温度を維持しています。
課題2:工具の摩耗
金型は極端な熱の下では劣化が早くなります。セラミックコーティングを施した当社の焼入れ鋼製金型は、標準的な工具と比較して工具寿命を40%延ばします。
チャレンジ3:次元の不安定性
急冷は反りの原因に。PTSMAKEは、多段冷却チャンネルとAI駆動シミュレーションを実装し、生産前に収縮パターンを予測します。
チャレンジ4:ガストラップ
肉厚部品は空気を閉じ込めます。私たちの真空アシスト成形プロセスは、医療や航空宇宙部品に不可欠な気泡を排除します。
課題5:サイクルタイムの遅さ
高温には長い冷却時間が必要です。20年以上の成形経験から検証されたコンフォーマル冷却チャンネルを使用して、サイクルタイムを最適化します。
チャレンジ6:色の一貫性
顔料は300℃以上で劣化します。当社のプレコンパウンド・カラー・マスターバッチは、退色することなく400℃まで耐えることができます。
課題7:高いエネルギーコスト
連続加熱は電力を消耗します。当社のサーボ電気機械は、±1℃の温度制御を維持しながら、35%の消費電力を削減します。
高温射出成形に関するFAQ
Q1: 高温射出成形に最適な材料は何ですか?
A: 高温射出成形は、PEEK、PEI(Ultem)、LCPのようなエンジニアリンググレードの熱可塑性プラスチックに最適です。これらの材料は、極端な温度でも反りや劣化に耐えられます。PTSMAKEでは、航空宇宙、医療、自動車用途の寸法安定性を確保するために、高度な金型とプロセス制御を使用しています。
Q2: 高温成形は製造コストにどう影響しますか?
A: 材料費とエネルギーコストは高くなりますが、私たちの最適化されたプロセスは無駄を最小限に抑えます。自動化された品質チェックと一括購入により、コストを削減しています。ファーウェイやBMWのようなクライアントは、複雑な形状に対する当社の費用対効果の高いソリューションを信頼しています。
Q3: 高温成形で達成できる公差は?
A: 300℃以上の条件下でも±0.01mmの公差を維持しています。当社のISO認定施設では、温度制御された金型とリアルタイムのモニタリングを使用し、生産工程全体の一貫性を確保しています。
Q4: 成形中の材料の劣化をどのように防ぐのですか?
A: 当社のエンジニアは、溶融温度プロファイルと滞留時間を最適化しています。酸化を抑えるため、バレル内では窒素パージを行っています。PTSMAKEの20年以上にわたるノウハウにより、熱に敏感な樹脂の安定した処理を保証します。
Q5: 高温材料のオーバーモールドに対応できますか?
A: はい。当社のデュアルショット成形システムは、シリコーンとPEEKのような素材を剥離することなく組み合わせることができます。私たちは、耐熱性と柔軟性の両方を必要とする医療機器部品を提供してきました。
Q6: 高温射出成形を最も必要とする産業は?
A: 航空宇宙(エンジン部品)、自動車(アンダーフード部品)、エレクトロニクス(コネクター)。AS9100およびIATF16949規格に適合するEMIシールド・ハウジングや耐流体シールを製造してきました。
Q7: プロトタイプの納期はどれくらいですか?
A: ほとんどの高温プロトタイプに3~7日かかります。社内のツーリングチームと50台以上のCNCマシンが迅速な反復を可能にします。お客様は24時間以内にDFMフィードバックを受け取ります。
Q8: 高温用途に最適な金型鋼は?
A: 耐食性のために、H13のようなプリハードン鋼やステンレス鋼を使用しています。すべての金型に応力除去熱処理を施し、長時間の高熱サイクルによる変形を防止しています。
Q9: 高温成形の生産はどの程度スケーラブルですか?
A: 私たちの施設では、年間10~100万個以上の部品を扱っています。クロスコンタミネーションを防ぐため、医療用と工業用で製造ラインを分けています。
Q10:材料証明書とトレーサビリティを提供していますか?
A: はい。すべてのバッチには、完全な材料証明書(RoHS、REACH、該当する場合はFDA)が含まれています。当社のデジタル追跡システムには、各品番のプロセスパラメータが記録されています。
PTSMAKEに連絡してプロジェクトを開始
PTSMAKE - 試作から生産まで、高温射出成形の次世代パートナー。
"新製品のために高品質のカスタム射出成形部品を探していましたが、PTSMAKEはそれを実現してくれました。PTSMAKEのチームは迅速に対応してくれ、すべてのステップを案内してくれました。部品は時間通りに届き、私たちの品質基準をすべて満たしていました。今後もぜひPTSMAKEと仕事を続けていきたいと思います!
デビッド・ブラウンプロダクション・マネージャー(米国
「PTSMAKEとはもう1年以上の付き合いになります。彼らの射出成形の精度と一貫性は素晴らしいものでした。厳しい納期を守り、最高品質の部品を提供してくれました。カスタマーサービスはいつも迅速で親切です。
サラ・ミュラープロダクト・エンジニア, ドイツ
「PTSMAKEとの射出成形のパートナー契約はスムーズでした。PTSMAKEは、複雑なデザインであっても、常に高品質のパーツを納期通りに提供してくれます。PTSMAKEのおかげで、プロセス全体が簡単で信頼できるものになりました。
ジェームズ・クラークオペレーション・ディレクター(英国