アルミニウム素材を選択する際、エンジニアが鋳造アルミニウムと通常のアルミニウムの選択に悩むのをよく目にします。多くのエンジニアが間違った選択で時間とお金を浪費し、プロジェクトの失敗やコストのかかる手直しにつながっています。
鋳造アルミニウムと通常のアルミニウム(展伸材)には、それぞれ異なる利点があります。鋳造アルミニウムはより複雑な形状を提供し、大量生産に適したコスト効率に優れています。一方、通常のアルミニウムは精密部品のための優れた強度と機械加工性を提供します。
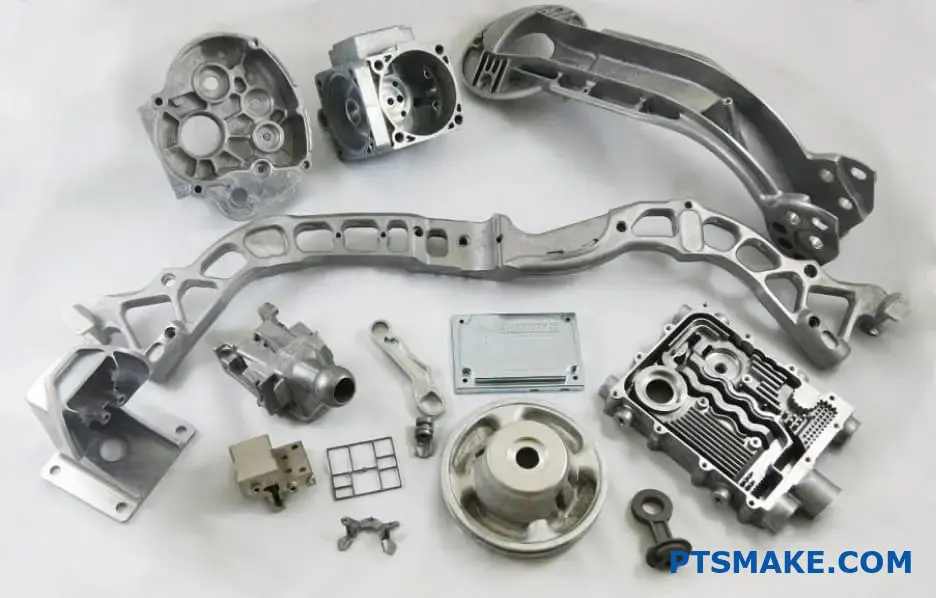
これらの材料の具体的な用途や詳細な比較について、疑問に思っていることでしょう。PTSMAKEで何千ものアルミニウム部品を製造してきた私の直接の経験をお話ししましょう。あなたのプロジェクトに適した選択ができるよう、重要な違いを探ります。
アルミ鋳造の欠点と利点は?
アルミニウム鋳造を選ぶメーカーがある一方で、避けるメーカーがあるのはなぜか、不思議に思ったことはありませんか?次のプロジェクトで材料を選択するとき、この決定は、特に複雑な部品設計や大量生産を扱う場合、成功と費用のかかる後退の違いを意味します。
アルミニウム鋳造は、優れた強度対重量比、優れた耐食性、複雑な形状のコスト効率の良い生産を提供します。しかし、鍛造アルミニウムに比べて引張強度が低い、潜在的な気孔率の問題、鋳造工程におけるサイズの制限などの制約もあります。
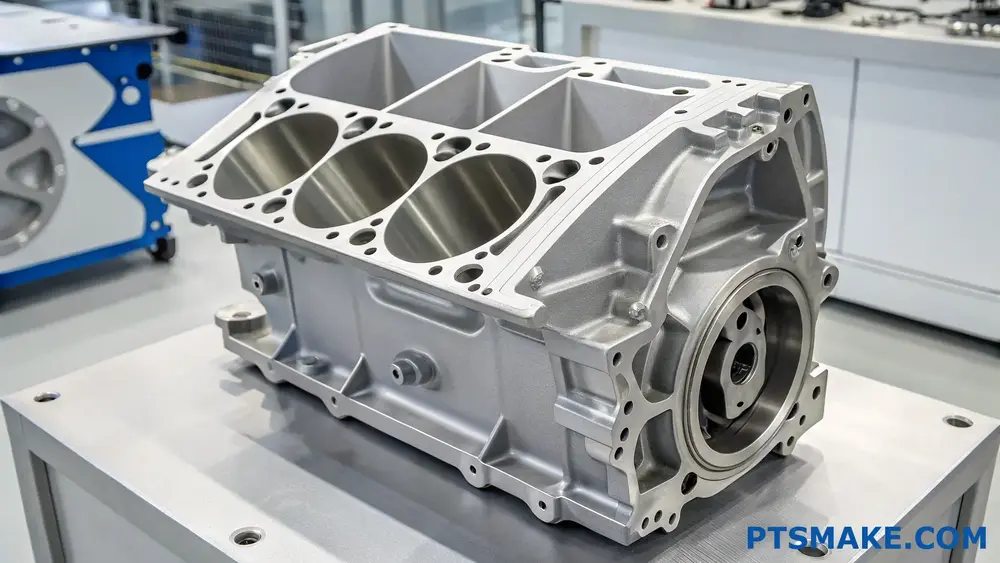
アルミニウム鋳造の特性を理解する
アルミニウム鋳物は、その汎用性の高い特性により、様々な産業でますます人気が高まっています。この素材の特性は、自動車部品から航空宇宙部品まで、数多くの用途に適しています。PTSMAKEでは、特にお客様が軽量かつ耐久性のある部品を必要とする場合、様々なプロジェクトでアルミ鋳造ソリューションを成功させてきました。
物理的性質
アルミニウム鋳造を検討する際、いくつかの重要な物理的特性が際立っている:
プロパティ | 典型的な範囲 | メリット |
---|---|---|
密度 | 2.6-2.9 g/cm³ | 軽量構造 |
融点 | 660-720°C | 良好な熱特性 |
熱伝導率 | 150-180 W/m-K | 優れた放熱性 |
電気伝導率 | 16-20 MS/m | 電気的用途に適している |
アルミ鋳造の利点
1.デザインの柔軟性
アルミニウム鋳造は、他の製造方法では困難または不可能な複雑な形状を可能にします。その 金属凝固パターン1 鋳造中に、複雑な内部通路やさまざまな肉厚を作り出すことができる。
2.費用対効果の高い生産
中量から大量生産の場合、アルミ鋳造はコスト面で大きな利点があります:
- 他の製造方法と比較して、金型費用が低い
- 材料廃棄の削減
- 生産サイクルの短縮
- 必要な二次加工は最小限
3.軽量化
自動車や航空宇宙産業の顧客と仕事をした経験では、アルミニウム鋳造の軽量特性はしばしば重要な利点をもたらします:
- スチールより軽い66%
- 構造的完全性を維持
- 自動車の燃費を向上させる
- システム全体の負荷を軽減
アルミ鋳造の欠点
1.機械的制限
鋳造工程では、機械的な制約が生じることがある:
制限 | インパクト | 緩和戦略 |
---|---|---|
多孔性 | 強度の低下 | 高度な鋳造技術 |
表面仕上げ | 後処理が必要な場合がある | 適切な金型設計 |
内部欠陥 | 品質の不一致 | 厳格な工程管理 |
2.サイズ制限
鋳造サイズの制限は、大規模なプロジェクトに影響を与える可能性がある:
- 実用的な最大サイズは鋳造方法による
- 大型鋳造品には特別な設備が必要な場合がある
- 欠陥のリスクはサイズが大きくなるほど高くなる
3.材料特性のばらつき
鋳造アルミニウムは特性にばらつきがある:
- 冷却速度の違いが強度に影響
- 機械的特性が安定しない可能性
- 追加の熱処理が必要な場合がある
アプリケーションと産業用途
アルミニウム鋳物は、さまざまな分野で幅広く使用されている:
自動車産業
- エンジンブロック
- トランスミッションハウジング
- ホイール部品
- 構造フレーム
航空宇宙用途
- エンジン部品
- 構造要素
- 住宅戸数
- 制御システム
消費者製品
- 電子ハウジング
- 家具部品
- 装飾的要素
- スポーツ用品
アルミニウム鋳造品選択のベストプラクティス
アルミ鋳造の利点を最大限に生かすには、以下の要素を考慮してください:
デザインの最適化
- 適切なドラフト角度を取り入れる
- 均一な肉厚を維持
- シュリンク引当金の計上
- 適切な半径とフィレットを含む
プロセス選択
- 適切なキャスティング方法を選択する
- 生産量を考慮する
- 表面仕上げの要件を評価する
- 寸法公差の必要性を考慮する
品質管理
- 適切なテスト手順の実施
- プロセスパラメーターの監視
- 一貫した材料特性を維持する
- 重要な寸法を確認する
PTSMAKEでは、アルミニウム鋳造部品が最も厳しい業界基準を満たすよう、包括的な品質管理プロセスを開発しました。当社のエンジニアリングチームは、お客様と緊密に連携し、特定の用途に最適な鋳造方法と設計パラメータを選択します。
鋳造に使われるアルミニウムの種類は?
鋳造プロジェクトに適切なアルミニウム合金を選ぶのに苦労したことがありますか?圧倒的な数の選択肢と様々な特性は、この決定を迷路の中をナビゲートするように感じさせ、コストのかかる間違いやプロジェクトの遅れにつながる可能性があります。
鋳造用に最も一般的に使用されるアルミニウム合金は、A356/A357(高強度)、319(良好な被削性)、713(優れた流動性)である。それぞれのタイプは、鋳造方法、部品の複雑さ、および最終用途の要件に基づいて特定の利点を提供します。
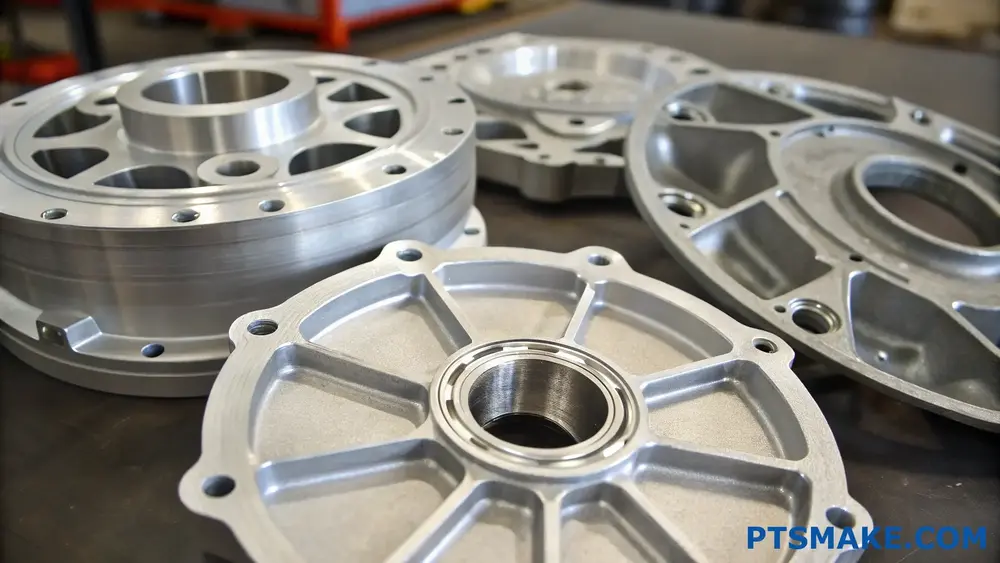
アルミニウム鋳造合金を理解する
A356/A357シリーズ業界標準
A356およびA357は、航空宇宙および自動車産業を支配する高級鋳造合金である。その優れた 樹状突起の凝集性2 は、凝固時に複雑な形状に最適です。PTSMAKEでは、高い強度対重量比を必要とする構造部品にこれらの合金を頻繁に使用しています。
組成物は典型的には以下を含む:
エレメント | A356 (%) | A357 (%) |
---|---|---|
シリコン | 6.5-7.5 | 6.5-7.5 |
マグネシウム | 0.25-0.45 | 0.45-0.7 |
鉄 | 最大0.2 | 最大0.2 |
チタン | 最大0.2 | 最大0.2 |
319 合金万能の選択
319アルミニウム合金は、優れた切削性と良好な気密性を提供します。そのバランスの取れた特性は、エンジンブロックからトランスミッションケースまで、様々な用途に適しています。自動車関連の顧客と仕事をしてきた経験から、319は薄肉部でも厚肉部でも安定した結果をもたらします。
主な特徴は以下の通り:
- 優れた流動性
- 熱割れに対する優れた耐性
- 優れた加工性
- 適度な強度特性
713 合金圧力ダイカストのチャンピオン
713合金は、その卓越した流動性とダイフィリング能力により、圧力ダイカスト用途に優れています。薄肉部品を鋳造する場合、この合金は一貫して優れた表面仕上げと寸法精度を提供します。
合金選択に影響を与える要因
応募資格
最終用途は合金の選択に大きく影響する:
アプリケーション・タイプ | 推奨合金 | キー・プロパティ |
---|---|---|
構造部品 | A356/A357 | 高強度 |
エンジン・コンポーネント | 319 | 耐熱性 |
薄肉部品 | 713 | 流動性 |
鋳造プロセス適合性
鋳造方法が異なれば、特定の合金特性が必要となる:
砂型鋳造
- 優れた流動性が必要
- 冷却速度の低下
- A356は非常によく機能する
ダイカスト
- 優れた流動特性が必要
- 急速な凝固
- 713を選択することが多い
永久鋳型鋳造
- 適度な冷却速度
- 良好な表面仕上げの要件
- 319はバランスの取れた特性を提供する
熱処理の可能性
鋳物を熱処理できるかどうかは、合金の選択に大きな影響を与える:
熱処理 | 適切な合金 | 強さの向上 |
---|---|---|
T6 | A356, A357 | 30-40% |
T5 | 713 | 15-20% |
T7 | 319 | 25-35% |
コストと利用可能性
アルミニウム鋳造合金を選択する際には、これらの経済的要因を考慮してください:
原材料費
- A356/A357プレミアム価格
- 319: ミドルレンジのコスト
- 713: 経済的なオプション
加工費
- 熱処理要件
- 加工の複雑さ
- 不合格率
生産量への影響
様々な生産量において、異なる合金の方が費用対効果が高い場合がある:
生産量 | 推奨合金 | コスト効率 |
---|---|---|
少量 | A356 | ミディアム |
中量 | 319 | 高い |
大量 | 713 | 非常に高い |
品質管理とテスト
一貫した鋳造品質を保証するために、以下の試験手順を実施してください:
化学分析
- 定期的な組成確認
- 微量元素モニタリング
- 不純物レベルコントロール
機械試験
- 引張強さ
- 降伏強度
- 伸びの測定
非破壊検査
- X線検査
- 染色浸透探傷検査
- 超音波検査
環境への影響と持続可能性
現代の鋳造作業は、環境要因を考慮しなければならない:
リサイクル性
- これらの合金はすべて100%リサイクル可能である。
- 再加工時の材料ロスを最小限に抑える
- 新素材の生産に比べ、カーボンフットプリントが低い
エネルギー効率
- 合金によって必要な加工温度は異なる
- 熱処理エネルギー消費量は様々
- 融点の違いがエネルギー使用に影響
PTSMAKEでは、アルミニウム鋳造プロセスの高品質基準を維持しながら、持続可能な製造方法を優先しています。アルミニウム鋳造における当社の専門知識は、多くのお客様が性能と持続可能性の両方のために材料選択を最適化するのに役立っています。
アルミ鋳造と複雑な部品のCNC機械加工との比較は?
複雑な部品の製造において、アルミ鋳造とCNC機械加工のどちらを選ぶかというジレンマに直面したことはありませんか?コスト、リードタイム、品質要件などの要素を考慮すると、その決定はさらに難しくなります。
アルミニウム鋳造とCNC機械加工はどちらも、複雑な部品の製造に明確な利点を提供します。鋳造は、大量生産で幾何学的に複雑な部品を低コストで製造するのに優れています。一方、CNC機械加工は、優れた精度、優れた表面仕上げ、設計の柔軟性を少量で提供します。
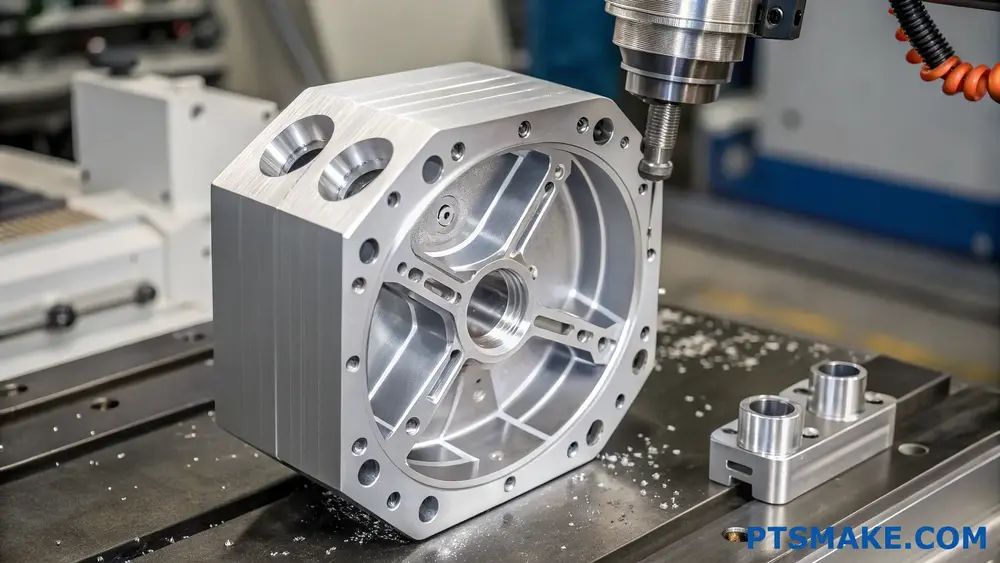
設計の複雑性に関する考察
幾何学的自由度と精度
複雑な部品に関しては、アルミ鋳造は優れた性能を発揮します。 幾何学的自由3 複雑な内部形状や複雑な形状のためです。しかし、PTSMAKEでは、CNC加工の方が公差が厳しく、重要な寸法をよりよく制御できることがわかりました。例えば、鋳造では±0.005インチの公差を達成できますが、CNC機械加工では定期的に±0.0005インチという厳しい公差を達成しています。
表面仕上げと品質
これらの工程間の表面仕上げの比較は、大きな違いを示している:
プロセス | 代表的な表面仕上げ (Ra) | 後処理の必要性 |
---|---|---|
ダイカスト | 125~300マイクロインチ | 多くの場合、二次加工が必要 |
CNC加工 | 16~125マイクロインチ | ほとんどない |
砂型鋳造 | 250~900マイクロインチ | 大規模な仕上げが必要 |
生産量とコスト分析
初期投資
ダイカスト鋳造では、金型や工具に多額の初期費用がかかりますが、CNCマシニングでは初期投資を最小限に抑えることができます。典型的なコストの内訳は以下の通り:
製造方法 | 金型費用の範囲 | 損益分岐点(部品) |
---|---|---|
ダイカスト | $10,000 - $100,000 | 3,000 - 5,000 |
CNC加工 | $0 - $1,000 | 1 - 500 |
素材利用
鋳造は通常、CNC機械加工に比べて材料利用率が優れています。私の経験では、PTSMAKEの場合、鋳造は90%までの材料効率を達成できますが、CNC機械加工では、複雑な部品の場合、原材料の30~40%しか利用できないかもしれません。
リードタイムと生産速度
生産率の比較
大量生産の場合、一般的に鋳造の方がサイクルタイムが速い:
プロセス | セットアップ時間 | 部品あたりのサイクルタイム |
---|---|---|
ダイカスト | 2~4週間 | 30~60秒 |
CNC加工 | 1~3日 | 10~60分 |
材料特性と性能
機械的特性
製造工程は最終的な部品の特性に大きく影響する:
アルミ鋳造部品には、しばしば欠陥がある:
- 低い引張強度
- より一貫性のある内部構造
- 熱サイクルに対する耐性が向上
- 空隙率が高い
CNC機械加工部品は通常、次のような特徴がある:
- より高い強度と硬度
- より優れた耐疲労性
- より予測可能な材料特性
- 内部応力の低下
品質管理への配慮
複雑な部品を製造する場合、品質管理が非常に重要になります。CNCマシニングは提供します:
- リアルタイム寸法検証
- 一貫した部品間の再現性
- 不良率の低下
- より良い文書化とトレーサビリティ
鋳造プロセスには、それが必要である:
- より徹底した品質管理
- X線またはCTスキャンによる内部欠陥の検査
- より高いサンプリングレート
- より洗練された検査プロトコル
デザイン最適化のヒント
各プロセスの利点を最大化するために、以下の設計ガイドラインを考慮すること:
キャスティングのために:
- 均一な肉厚設計
- 適切なドラフト角度を含む(通常1~3度)
- 鋭角なコーナーや急な乗り換えを避ける
- パーティングラインとゲートの位置の計画
CNC加工用:
- 深いポケットや複雑な内部構造を最小限に抑える
- ツールアクセスと固定具の要件を考慮する
- 標準的な切削工具サイズに対応した設計
- 適切なクランプ面を確保する
費用対効果の高い意思決定
鋳造とCNC加工のどちらを選ぶかは、多くの場合、次のような点に左右される:
生産量要件
- 少量生産(1-1000個):CNC機械加工
- 大量生産(1000個以上):鋳造
公差要件
- 超精密(±0.001インチ以上):CNC加工
- 標準精度(±0.005インチ以上):鋳造
表面仕上げの必要性
- 美的仕上げが必要:CNC加工
- 機能仕上げ可:鋳造
予算の制約
- 限られた先行投資:CNC加工
- 長期的なコストの最適化鋳造
PTSMAKEでは、お客様の具体的な要件に基づいた詳細な分析と提案を提供することで、このような意思決定を支援します。両工程における当社の専門知識により、複雑なアルミニウム部品の最適な製造ソリューションをお約束します。
金属鋳造アルミ部品にはどのような表面仕上げオプションがありますか?
寸法は完璧でも、表面の外観が不十分なアルミ鋳造部品を受け取ったことはありませんか?部品がすべての技術仕様を満たしているにもかかわらず、美的要件が満たされておらず、プロジェクト全体のタイムラインを遅らせる可能性がある場合、イライラさせられます。
金属鋳造アルミニウム部品の表面仕上げには、機械的、化学的、電気化学的プロセスを含む様々な方法があります。それぞれの技術は、美観の向上から耐食性や耐摩耗性などの機能特性の強化まで、独自の利点を提供します。
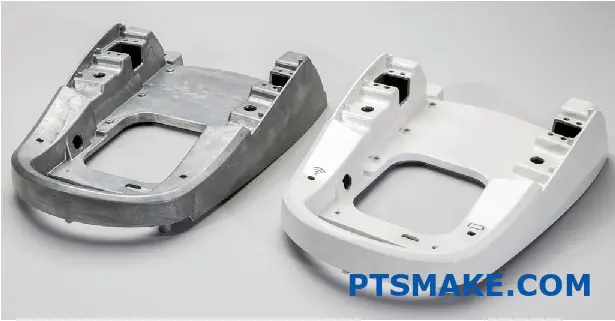
機械的仕上げ方法
ショットブラストとサンドブラスト
ショットブラストとサンドブラストは、研磨材の高圧推進力を使用する多用途の仕上げ方法です。これらの技術は、表面の欠陥を効果的に除去し、均一なテクスチャを作成します。PTSMAKEでは、ショットブラストは大型のアルミ鋳造品に特に適しており、サンドブラストは複雑な部品の制御が容易であることが分かっています。
ポリッシングとバフ研磨
研磨は、漸進的な研磨によって滑らかで反射性のある表面を作り出します。このプロセスには通常、複数の段階が含まれます:
ステージ | グリットサイズ | 目的 |
---|---|---|
ラフ | 80-120 | 大きな欠点を取り除く |
ミディアム | 240-400 | 滑らかな表面処理 |
ファイン | 800-1200 | 最初の輝きを生み出す |
決勝 | 1500+ | 鏡面仕上げを実現 |
化学的仕上げ加工
ケミカル・エッチング
ケミカルエッチングは、特殊な溶液を使用して材料の薄層を除去し、ユニークな表面テクスチャーを作り出します。このプロセスは、機械的な方法では困難な複雑な形状の均一な仕上げを実現するのに特に効果的です。
陽極酸化処理
陽極酸化処理4 は、アルミニウム鋳物の最も一般的な仕上げ方法の一つとして際立っている。このプロセスにより、耐久性と耐腐食性に優れた酸化皮膜が形成され、さまざまな色に染めることができます。
アルマイト処理には主に3つの種類がある:
タイプI(クロム酸)
- 薄いコーティング(0.00002~0.0001インチ)
- 優れた耐食性
- 航空宇宙用途で一般的
タイプII(硫酸)
- ミディアムコーティング(0.0001-0.001インチ)
- 優れた耐摩耗性
- 一般産業用規格
タイプIII(硬質アルマイト処理)
- 厚いコーティング(0.001~0.004インチ)
- 優れた耐摩耗性
- 高ストレス用途に最適
電気化学プロセス
電解研磨
電解研磨は、電気化学的プロセスによって材料を除去することにより、反射率の高い仕上げを提供します。この技法は、特に次のような場合に有効です:
- 表面粗さの低減
- 耐食性の向上
- 清掃性の向上
- 明るく装飾的な仕上げ
特殊コーティング
パウダーコーティング
パウダーコーティングは、優れた耐久性と幅広いカラーオプションを提供します。その工程は以下の通りです:
ステップ | 説明 | 目的 |
---|---|---|
準備 | 表面の洗浄と前処理 | 塗膜の密着性の確保 |
申し込み | 粉体の静電スプレー | カバー率 |
養生 | 熱処理 | 最終仕上げを行う |
コンバージョンコーティング
化成処理コーティングは、保護層を形成し、強化する:
- 塗料密着性
- 耐食性
- 電気絶縁
- 表面硬度
正しい仕上げの選択
アルミニウム鋳物の表面仕上げを選ぶ際には、以下の点を考慮する:
環境暴露
- 屋内使用と屋外使用
- 化学物質への暴露
- 紫外線暴露
機能要件
- 耐摩耗性のニーズ
- 腐食保護
- 熱への配慮
- 電気伝導度
美的要件
- 色の好み
- テクスチャーの条件
- 光沢レベル
- 視覚的一貫性
コストに関する考察
- 生産量
- 処理時間
- 材料費
- 機材要件
PTSMAKEのチームは、お客様の具体的な用途要件を考慮することで、これらの選択肢をナビゲートするお手伝いをします。部品の形状、生産量、性能仕様などの要素を評価し、最適な仕上げ方法を提案します。
品質管理対策
一貫した表面仕上げの品質を確保するために、私たちは以下を実施している:
- 定期的なプロセス監視
- 表面粗さ測定
- 膜厚試験
- 接着試験
- 目視検査プロトコル
- すべての仕上げパラメータの文書化
産業用アルミ鋳造の寸法精度を確保するには?
仕様に合わないアルミ鋳造品を受け取ったことはありませんか?寸法の不正確さに対処するフラストレーションは、特にこれらの部品が産業用途の重要な部品である場合、圧倒されることがあります。厳しい納期と品質要件が天秤にかかっています。
アルミニウム鋳造の寸法精度を確保する鍵は、適切な金型設計、精密な温度管理、高度な測定技術を組み合わせた包括的な品質管理システムの導入にあります。この体系的なアプローチにより、製造工程全体を通して一貫した部品寸法を維持することができます。
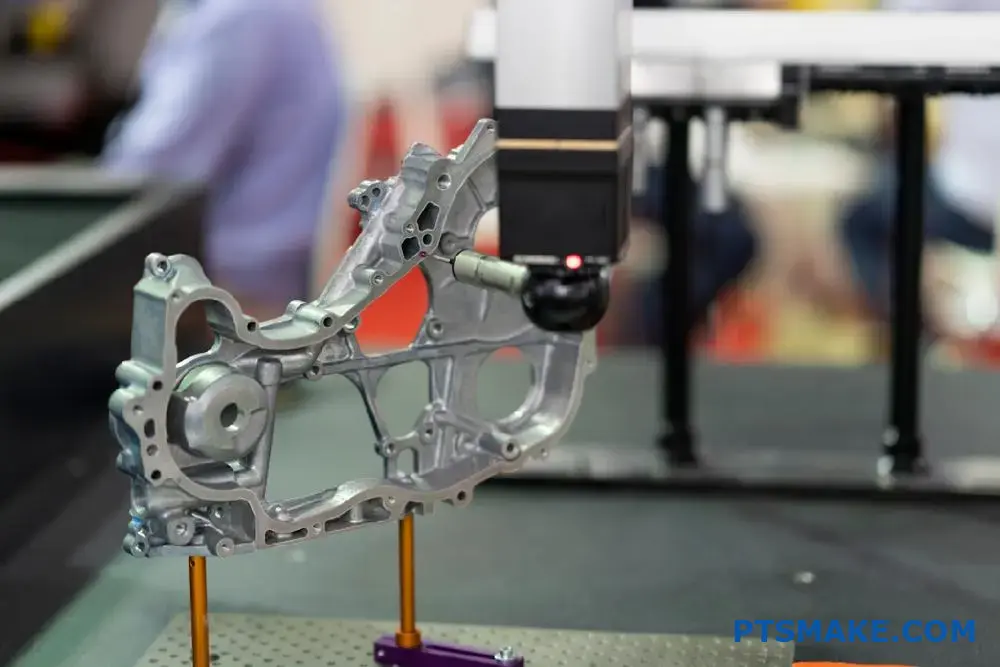
寸法管理要因を理解する
金型設計の考慮点
寸法精度の基礎は、適切な金型設計から始まります。PTSMAKEでは、いくつかの重要な側面に焦点を当てています:
- 適切なゲーティングとランナーシステム
- 適切な換気口の配置
- 戦略的なパーティングラインの位置
- 最適化された冷却チャネル設計
アルミニウム鋳造が成功するかどうかは、その鋳造方法がいかに優れているかにかかっている。 収縮率5 は設計段階で考慮されます。私たちは、使用される特定のアルミニウム合金に基づいて収縮許容量を慎重に計算します。
温度管理
温度管理は寸法精度を維持する上で重要な役割を果たす:
温度フェーズ | 最適範囲 (°C) | 寸法への影響 |
---|---|---|
注ぐ | 660-750 | フローと充填に影響 |
金型 | 200-300 | 凝固速度をコントロール |
冷却 | 25-100 | 最終寸法に影響 |
品質管理対策
鋳造前の検証
生産を開始する前に、いくつかの検証ステップを実施する:
- パターン設備検査
- 金型キャビティ測定
- コアボックスの検証
- 砂システムのテスト
インプロセス制御
鋳造の過程で、私たちは監視する:
- 分光分析による金属組成
- デジタル熱電対による注湯温度
- サーモグラフィによる冷却速度
- 金型のアライメントと型閉め圧力
高度な測定技術
三次元測定機(CMM)の統合
私たちは最先端のCMM技術を活用しています:
- 自動寸法検査の実施
- 詳細な測定レポートの作成
- 寸法トレンドの追跡
- 潜在的なプロセス・ドリフトを特定する
3Dスキャンアプリケーション
最新の3Dスキャン技術によって、私たちはこんなことができる:
- 完全な部品形状マップの作成
- 実際の部品とCADモデルを比較
- 路面の状態を記録する
- デジタル部品データのアーカイブ
プロセスの最適化
統計的工程管理
私たちはSPCの手法を導入している:
- 主要な寸法特性をモニターする
- 管理限界の設定
- プロセスのばらつきを特定する
- 積極的に是正措置を取る
継続的改善プロトコル
私たちの改善システムには以下が含まれる:
- 定期的なプロセス監査
- チーム・フィードバック・セッション
- 顧客意見の統合
- テクノロジー・アップデート
素材に関する考察
合金の選択 衝撃
アルミニウム合金によって、その特性はさまざまだ:
合金シリーズ | 標準収縮率(%) | 寸法安定性 |
---|---|---|
356 | 1.3 | 素晴らしい |
319 | 1.4 | 非常に良い |
A380 | 1.2 | グッド |
熱処理効果
鋳造後の熱処理は、寸法に影響を与える可能性がある:
- 溶液熱処理
- 焼入れ手順
- 老化プロセス
- ストレス解消法
文書化とトレーサビリティ
記録管理
我々は詳細な記録を保持している:
- 材料認証
- プロセスパラメーター
- 検査結果
- 不適合報告書
トレーサビリティ・システム
当社のトレーサビリティ・プロトコルには以下が含まれる:
- ユニークな部品識別
- バッチトラッキング
- プロセス文書
- 品質証明書
PTSMAKEでは、このような包括的な管理を実施し、高度な技術を活用することで、アルミ鋳造において常に厳しい寸法公差を達成しています。この体系的なアプローチにより、当社の産業界のお客様は、正確な仕様を満たす部品を受け取ることができ、組み立ての問題を減らし、全体的な製品品質を向上させることができます。
金属鋳造アルミニウム生産において重要な品質管理対策とは?
仕様に適合しないアルミニウム鋳物を受け取り、コストのかかるプロジェクトの遅延や手戻りにつながったことはありませんか?アルミニウム鋳造で一貫した品質を維持することの難しさは、特に複雑な形状や厳しい公差を扱う場合、圧倒されることがあります。
金属鋳造アルミニウム生産の品質管理には、材料試験、工程監視、最終検査に焦点を当てた包括的なアプローチが必要です。主な対策には、化学成分分析、温度管理、金型検査、寸法検証などがあり、一貫した製品品質を保証します。
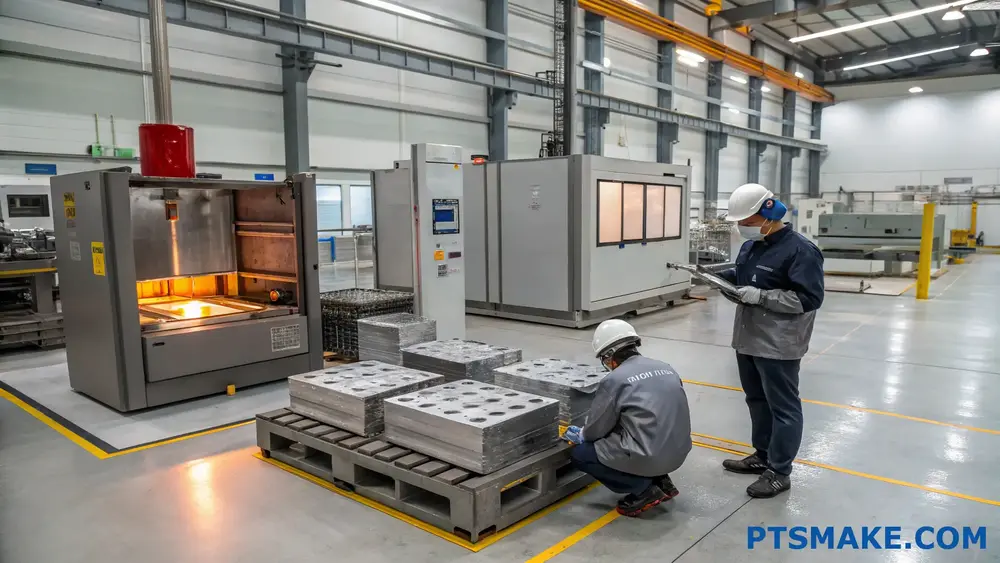
材料試験と検証
原材料分析
原材料の品質は、最終的な鋳造品質に直接影響します。PTSMAKEでは、受入材料に対して厳格な試験プロトコルを実施しています:
テスト・タイプ | 目的 | 頻度 |
---|---|---|
化学分析 | アルミニウムの組成を確認する | すべてのバッチ |
密度試験 | 材料の一貫性の確保 | 毎日 |
汚染チェック | 不純物の検出 | 1回の発送につき |
材料保管管理
適切な保管は汚染を防ぎ、材料の完全性を維持します。当社の施設では、アルミニウム合金および器具を保管するための厳格な環境管理を維持しています。 吸湿性6 吸湿を防ぐための保管条件
工程管理対策
温度モニタリング
アルミ鋳造を成功させるには、温度管理が重要です。私たちは採用しています:
- リアルタイムモニタリング用デジタル熱電対
- 自動温度記録システム
- 温度測定装置の定期校正
- 各生産工程の温度プロファイルの文書化
金型の品質検証
鋳型の完全性は鋳造品質に大きく影響する:
- 金型表面の定期検査
- 生産前の寸法検証
- 金型メンテナンス履歴の文書化
- 膜厚測定と制御
生産監視
工程内検査
生産中の継続的なモニタリングは、問題の早期発見に役立つ:
- 溶湯の流れの目視検査
- 鋳造パラメータのリアルタイムモニタリング
- 品質チェックのための定期的なサンプリング
- 工程逸脱の文書化
環境制御
鋳物の品質に影響を与える環境要因を監視しなければならない:
- 製造エリアの湿度レベル
- 周囲温度コントロール
- 大気質モニタリング
- 塵埃測定
最終製品検査
寸法検証
正確な測定により、仕様への準拠を保証します:
- CMM(三次元測定機)検査
- 複雑な形状の3Dスキャン
- ゲージの校正とメンテナンス
- 統計的工程管理の実施
表面品質評価
表面仕上げの品質は、外観と機能性の両方に影響する:
- 管理された照明下での目視検査
- 表面粗さ測定
- 気孔率試験
- 表面欠陥の記録
文書化とトレーサビリティ
品質記録
包括的な記録を維持することで、トレーサビリティを確保する:
- 材料証明書
- プロセスパラメーター
- 検査結果
- 不適合報告書
- 是正措置の文書化
統計分析
データ分析は、傾向と改善の機会を特定するのに役立つ:
- プロセス能力研究
- 欠陥率の追跡
- 根本原因分析
- 継続的改善への取り組み
高度な試験方法
非破壊検査
さまざまな方法で内部品質を保証している:
- 内部欠陥のX線検査
- 超音波探傷検査
- 磁粉探傷検査(該当する場合
- 染料浸透探傷検査による表面欠陥の検査
機械試験
物理的特性の検証は性能を保証する:
- 引張強度試験
- 硬度試験
- 耐衝撃性の検証
- 疲労試験が必要な場合
品質システムの統合
品質管理対策が成功するかどうかは、システムの統合にかかっている:
- 従業員研修プログラム
- 標準作業手順書
- 品質マネジメントシステム認証
- 定期的な監査とレビュー
- サプライヤー品質管理
- 顧客フィードバックの統合
PTSMAKEの包括的な品質管理システムにより、アルミニウム鋳物製造における一貫した品質を維持しています。当社のアプローチは、伝統的な検査方法と高度な検査技術を組み合わせることで、すべての鋳物がお客様の仕様を満たす、または上回ることを保証します。
このような対策を計画的に実施することで、アルミニウム鋳造作業における不良率が驚くほど低くなることがわかりました。検出よりも予防に重点を置くことで、一貫して信頼できる結果をもたらす強固な品質管理システムを構築することができました。
アルミニウム大量鋳造プロジェクトのコスト効率を最適化するには?
アルミニウム鋳造プロジェクトで、制御不能に陥るような高騰するコストに直面したことはありませんか?多くの製造業者は、品質とコスト効率のバランスに苦慮しています。特に、ミスや無駄が許されない大量生産に対応する場合はなおさらです。
大量のアルミ鋳造プロジェクトでコスト効率を最適化するには、戦略的な材料選択に焦点を当て、リーン生産の原則を導入し、高度なプロセス監視を活用し、予防保全に投資する。これらのアプローチにより、品質基準を維持しながら無駄を大幅に削減することができます。
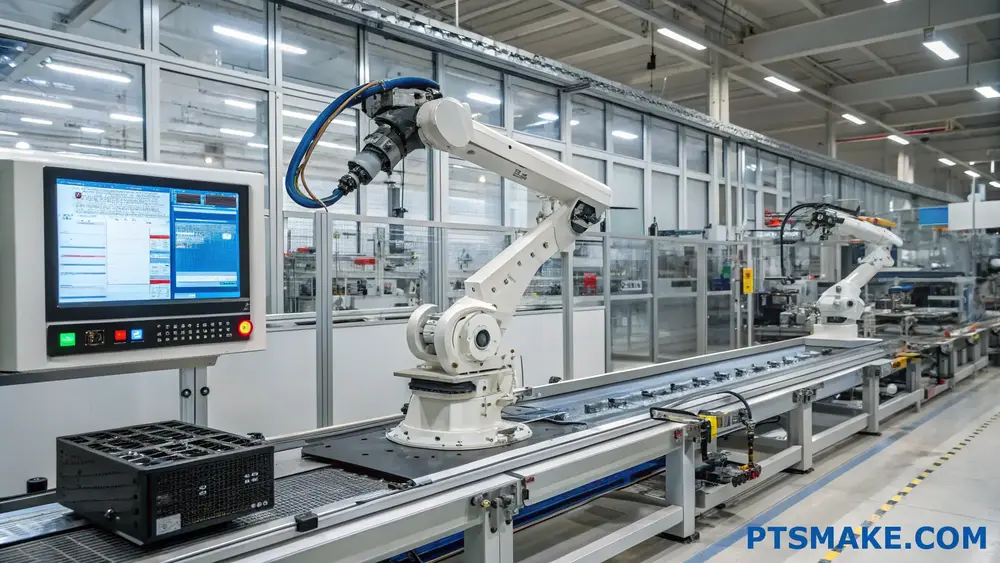
アルミニウム鋳造におけるコスト要因の理解
最適化戦略の前に、アルミ鋳造の主要なコスト要因を特定することが重要です。製造コストに影響を与える主な要因には、以下のようなものがあります:
材料費
生産効率要因
ファクター | コストへの影響 | 最適化の可能性 |
---|---|---|
サイクルタイム | 出力との直接的な相関 | 高い |
エネルギー消費 | 営業費用の20-30% | ミディアム |
労働条件 | 総費用の15-25% | ミディアム |
設備利用 | オーバーヘッド配分に影響 | 高い |
スマート・マテリアル・マネジメントの導入
PTSMAKEでは、材料費最適化のための効果的な戦略をいくつか開発してきました:
戦略的ソーシング
- 長期的なサプライヤーとの関係構築
- 大量購入プログラムの実施
- 市場動向をモニターし、最適なタイミングを探る
- 品質維持と価格交渉の両立
効率的なマテリアルハンドリング
練習 | ベネフィット | 実装の複雑さ |
---|---|---|
自動給餌システム | 廃棄物の削減 | ミディアム |
リアルタイム在庫追跡 | 在庫管理の改善 | 低い |
整理された収納システム | 損傷リスクの低減 | 低い |
適切な材料ローテーション | 陳腐化の低減 | 低い |
プロセス最適化技術
高度監視システム
- リアルタイム監視装置の設置
- 主要業績評価指標を追跡する
- 予知保全の実施
- プロセス・パラメーターの文書化
品質管理の統合
制御方法 | 品質への影響 | コスト削減 |
---|---|---|
インラインテスト | 即時フィードバック | 高い |
統計的プロセス制御 | バリエーションを減らす | ミディアム |
自動検査 | より速い検出 | 高い |
デジタル・ドキュメンテーション | トレーサビリティの向上 | ミディアム |
エネルギー効率の改善
溶解作業
- 炉への装入パターンの最適化
- 熱回収システムの導入
- オフピーク時の生産スケジュール
- 適切な断熱の維持
温度管理
エリア | 省エネの可能性 | 必要な投資 |
---|---|---|
炉の効率 | 15-25% | 高い |
熱回収 | 10-20% | ミディアム |
断熱材のアップグレード | 5-15% | 低い |
プロセスの最適化 | 10-20% | ミディアム |
労働最適化戦略
トレーニングと開発
- 定期的なスキル向上プログラム
- 柔軟性を高めるクロストレーニング
- ベストプラクティスの文書化
- パフォーマンス・モニタリング・システム
ワークフローの強化
イニシアティブ | 生産性への影響 | 実施時間 |
---|---|---|
標準作業手順書 | 高い | ミディアム |
ビジュアル管理システム | ミディアム | 低い |
チームによる問題解決 | 高い | ミディアム |
継続的改善文化 | 高い | 長期 |
機器のメンテナンスとアップグレード
予防メンテナンス
- 定期検査
- 定期校正
- 部品交換計画
- パフォーマンス・トラッキング
技術統合
テクノロジー | ROIタイムライン | 効率ゲイン |
---|---|---|
オートメーションシステム | 2~3年 | 20-30% |
デジタル制御 | 1-2年 | 15-25% |
監視装置 | 1年 | 10-20% |
データ分析 | 6ヶ月 | 5-15% |
サプライチェーンの最適化
在庫管理
- ジャスト・イン・タイム・デリバリー・システム
- 安全在庫の最適化
- サプライヤー・パフォーマンス・メトリクス
- デジタル追跡ソリューション
ロジスティクス強化
戦略 | コスト削減 | 実施努力 |
---|---|---|
ルート最適化 | 10-15% | ミディアム |
パッケージング改善 | 5-10% | 低い |
ロードコンソリデーション | 8-12% | ミディアム |
キャリアの選択 | 5-8% | 低い |
自動車用途におけるアルミニウム鋳造の主な検討事項とは?
なぜ自動車部品には、早期に故障するものもあれば、何年も長持ちするものもあるのか不思議に思ったことはありませんか?自動車業界では、間違ったアルミ鋳造プロセスを選択したり、重要なパラメータを見落としたりすると、部品の致命的な故障につながり、自動車の安全性と性能を損なう可能性があります。
自動車用途のアルミ鋳造では、合金の選択、設計の最適化、工程管理、品質検査など、いくつかの重要な要素を慎重に検討する必要があります。適切なアプローチにより、部品は厳しい自動車規格を満たしながら、費用対効果と生産効率を維持することができます。
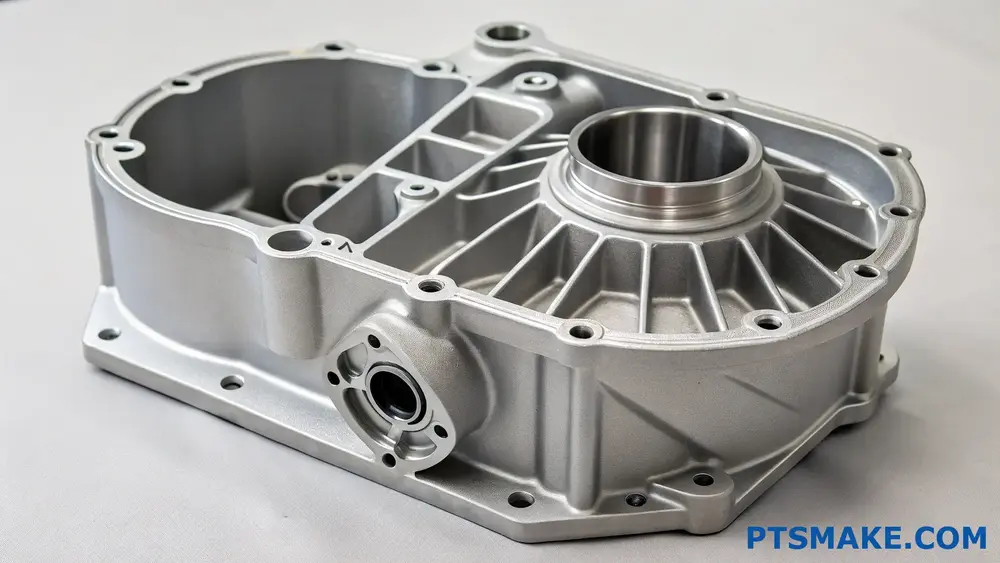
材料の選択と特性
合金組成
自動車鋳造の用途では、適切なアルミニウム合金の選択が非常に重要です。PTSMAKEでは、主にA356とA380合金を使用しています。 デンドライトアーム間隔8 と機械的特性を備えています。これらの合金は以下を提供する:
- 優れた強度対重量比
- 優れた耐食性
- 良好な熱伝導性
- 鋳造性の向上
熱処理に関する考察
熱処理はアルミニウム鋳造部品の最終特性に大きく影響します:
熱処理タイプ | メリット | 一般的なアプリケーション |
---|---|---|
T6 | 最高の強度と硬度 | エンジンブロック、シリンダーヘッド |
T4 | 優れた延性、中程度の強度 | ボディパネル、構造部品 |
T7 | より優れた寸法安定性 | トランスミッションケース |
デザインの最適化
肉厚コントロール
適切な肉厚設計は不可欠である:
- 空隙形成の防止
- 均一な固化の確保
- 材料廃棄の削減
- 軽量化の最適化
私は、ほとんどの自動車部品で肉厚を3~8mmに維持することを推奨しているが、特定の用途の要件によって変動する。
ドラフト角度とパーティングライン
重要な設計要素には以下が含まれる:
- 外面の最小抜き勾配は2°。
- 内面は3°以上
- パーティングラインを戦略的に配置し、フラッシュを最小限に抑える
- 射出要件の検討
プロセス制御パラメータ
ダイの温度管理
最適な金型温度を維持することは、高品質の鋳造品にとって極めて重要です:
温度範囲 (°C) | 効果 | アプリケーション |
---|---|---|
200-250 | より良い表面仕上げ | 装飾部品 |
250-300 | 気孔率の低下 | 構造部品 |
300-350 | 機械的特性の向上 | 高負荷部品 |
圧力制御
鋳造時の適切な圧力制御が影響する:
- 塗りつぶしパターン
- 固化率
- 表面品質
- 内部欠陥の形成
品質保証の方法
非破壊検査
様々な試験方法の実施により、部品の品質を保証します:
- 内部欠陥のX線検査
- 表面クラックの浸透探傷検査
- 超音波探傷検査
- CMMによる寸法検証
プロセス監視
主要パラメータの継続的モニタリング:
- 金属温度
- ダイ温度
- 射出圧力
- サイクルタイム
- 冷却率
コスト最適化戦略
工具に関する考察
効果的な金型設計は、全体的なコストに影響を与える:
- 量産用マルチキャビティ金型
- 柔軟性のためのモジュラーツール設計
- 適切な換気と冷却経路
- 工具を長持ちさせるための材料選択
生産効率
生産パラメータの最適化:
- サイクルタイムの最小化
- スクラップ率の低減
- 自動ハンドリングの導入
- 予防保全スケジュールの維持
環境への配慮
サステナビリティの実践
現代の自動車鋳造は、環境問題に対処しなければならない:
- 再生アルミニウムの使用
- クローズドループ冷却システムの導入
- エネルギー消費の削減
- 廃棄物発生の最小化
排ガス規制
環境影響を管理する
- 適切な換気システム
- 集塵装置
- 廃熱回収
- 水処理システム
今後の動向
先進製造技術
未来を形作る新たなテクノロジー:
- プロセス最適化のためのコンピュータ・シミュレーション
- リアルタイム監視システム
- 品質管理のための人工知能
- 自動プロセス調整
素材の革新
アルミニウム鋳造の発展:
- 新しい合金組成
- ナノ粒子補強
- ハイブリッド素材
- バイオにインスパイアされたデザイン
熱処理はアルミニウム鋳造部品の性能にどのように影響するか?
強度要件を満たさないアルミ鋳造部品を受け取ったことがありますか?あるいは、寸法仕様を満たしているにもかかわらず、早期に故障した部品を扱ったことがありますか?このような問題は、プロジェクトの大幅な遅延や予期せぬコストの原因となります。
熱処理は、アルミニウム鋳造部品の微細構造を変化させることにより、その機械的特性を向上させる重要なプロセスです。制御された加熱と冷却のサイクルにより、部品の内部応力を低減しながら、強度、硬度、耐久性を大幅に向上させることができます。
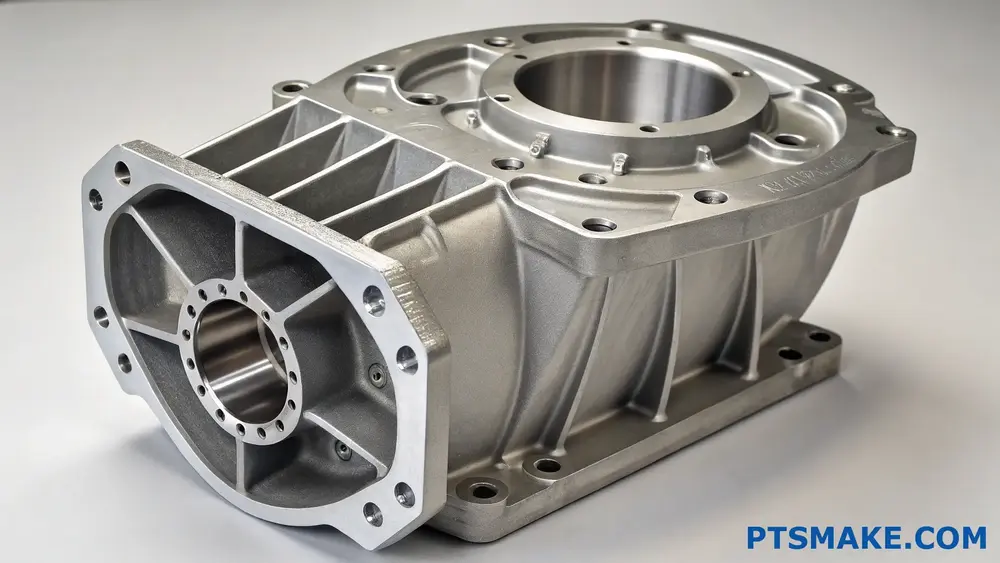
熱処理の基礎を理解する
アルミニウム鋳造の熱処理には、材料の特性を変えるいくつかの重要な工程があります。このプロセスは、最適な結果を得るために、慎重な温度制御とタイミングから始まります。この工程では 析出硬化9 はミクロのレベルで発生し、金属の特性を根本的に変える。
アルミニウム鋳物の熱処理の種類
アルミニウム鋳造部品には、いくつかの一般的な熱処理方法があります:
溶液熱処理
- 合金を融点近くまで加熱する
- 可溶性元素を溶液に溶かす
- 均質な構造を作る
焼き入れ
- 急速冷却プロセス
- 不要な降水を防ぐ
- 過飽和溶液を維持
エイジング
- 室温での自然熟成
- 高温での人工熟成
- 降水量をコントロールする
機械的特性への影響
アルミニウム鋳造部品に対する熱処理の影響は、かなり大きく、測定可能です:
プロパティ | 治療前 | 治療後 | 改善 |
---|---|---|---|
引張強度 | 180-220 MPa | 250-320 MPa | 45%まで |
降伏強度 | 90-120 MPa | 165-220 MPa | 83%まで |
伸び | 2-3% | 5-8% | 167%まで |
硬度 | 70-80 HB | 95-115 HB | 44%まで |
処理パラメータの最適化
PTSMAKEでは、熱処理パラメータの精密な制御方法を開発しました:
温度管理
- 正確なモニタリングシステム
- 均一な熱分布
- 過熱防止
時間管理
- 加熱時間の最適化
- 制御された冷却速度
- 正確なエージング期間
環境要因
- 湿度コントロール
- 大気条件
- 汚染防止
品質管理とテスト
安定した結果を得るためには、厳格なテストとモニタリングが必要である:
一般的な試験方法
機械試験
- 引張試験
- 硬度試験
- 衝撃試験
構造解析
- 顕微鏡検査
- X線分析
- 密度測定
産業別アプリケーションと考察
さまざまな産業が、特定の熱処理アプローチを必要としている:
自動車用途
- エンジン部品
- サスペンション部品
- トランスミッションハウジング
航空宇宙の要件
- 構造部品
- コントロール・サーフェス
- 着陸装置部品
よくある問題のトラブルシューティング
よくある課題とその解決策
ディストーション
- 治療中の適切な固定
- 制御された冷却速度
- ストレス解消法
一貫性のないプロパティ
- 機器の定期校正
- 標準化された手順
- 詳細資料
コスト・ベネフィット分析
熱処理の経済的影響を理解する:
ファクター | 治療なし | 治療を伴う |
---|---|---|
初期費用 | より低い | より高い |
ライフサイクルコスト | より高い | より低い |
パフォーマンス | スタンダード | 強化された |
保証請求 | より頻繁に | 削減 |
最適な結果を得るためのベストプラクティス
アルミニウム鋳造部品の熱処理で最良の結果を得るために:
設計上の考慮事項
- 均一な肉厚
- 適切なドラフト角度
- ストレス集中の緩和
プロセス制御
- 温度モニタリング
- 時間管理
- 品質検証
ドキュメンテーション
- プロセスパラメーター
- テスト結果
- トレーサビリティ記録
環境への影響と持続可能性
現代の熱処理工程は、以下の点に重点を置いている:
エネルギー効率
- 最適化された加熱サイクル
- 熱回収システム
- 最新機器の選択
廃棄物削減
- プロセスの最適化
- マテリアルリサイクル
- 排ガス規制
航空宇宙グレードのアルミニウム鋳物について、サプライヤーはどのような認証を取得すべきか?
航空宇宙アルミ鋳造プロジェクトにおいて、適切なサプライヤーを選択するという課題に直面したことはありますか?認証要件におけるわずかな見落としが、航空機部品の致命的な故障につながり、人命や数百万ドルの損害をもたらす可能性があるのです。
航空宇宙グレードのアルミニウム鋳造サプライヤーにとって不可欠な認証には、AS9100D、特殊工程用のNADCAP、ISO 9001:2015、および特定のOEM承認が含まれます。これらの認証は、品質管理システム、工程管理、厳格な航空宇宙産業規格への準拠を保証します。
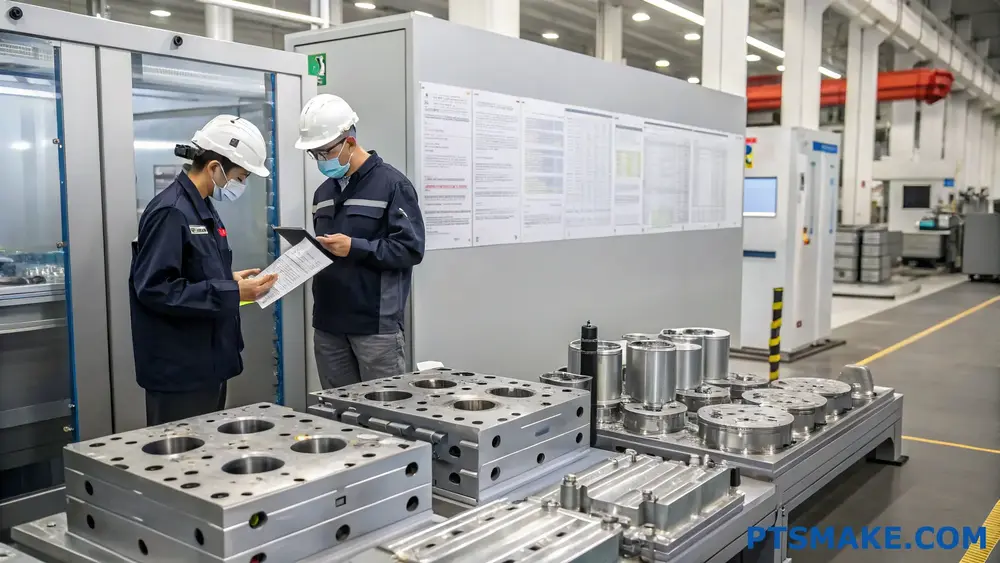
AS9100D認証を理解する
AS9100Dは航空宇宙品質管理システムのゴールドスタンダードです。PTSMAKEでは、次のことを保証するためにこの認証を取得しています。 冶金プロセス10 最高の業界基準を満たしています。この認定は以下を包括している:
AS9100Dの主な要件
- リスク管理プロトコル
- コンフィギュレーション管理
- 製品安全への配慮
- 偽造部品防止
- サプライチェーン・コントロール
航空宇宙メーカーのメリット
- 品質一貫性の強化
- 文書システムの改善
- トレーサビリティの向上
- オペレーショナル・リスクの低減
- 顧客の信頼の向上
NADCAP認定要件
NADCAP(National Aerospace and Defense Contractors Accreditation Program)認証は、航空宇宙製造における特殊工程に不可欠です。これには以下が含まれます:
プロセス・カテゴリー | 特定の要件 | 検証方法 |
---|---|---|
熱処理 | 温度の均一性 | パイロメトリック・テスト |
化学処理 | プロセス制御 | 化学分析 |
非破壊検査 | 機器校正 | パフォーマンス検証 |
材料試験 | 機械的特性 | ラボ認証 |
ISO 9001:2015 ファンデーション
AS9100DはISO 9001:2015の上に構築されたものですが、このベースライン認証を取得していることは、その証明となります:
品質管理の原則
- 顧客重視
- リーダーシップのコミットメント
- プロセス・アプローチ
- エビデンスに基づく意思決定
必要書類
- 品質マニュアル
- プロセス手順
- 作業指示
- 品質記録
OEM固有の承認
さまざまな航空宇宙メーカーには独自の要件がある:
ボーイング要件
- D1-4426 承認
- 特殊工程認証
- マテリアルハンドリング仕様
- 品質システム要求事項
エアバス規格
- AIMS仕様
- プロセス資格
- 材料認証
- 試験要件
環境・安全認証
ISO 14001:2015
環境マネジメントの認証は確実なものである:
- 廃棄物削減
- リソースの最適化
- 環境コンプライアンス
- 持続可能な実践
ohsas 18001/iso 45001
安全管理認証の対象範囲
- 労働者の安全プロトコル
- リスク評価
- 緊急時の備え
- ヘルス・モニタリング
素材別認証
アルミニウム鋳造の場合、具体的な認証には以下が含まれる:
化学組成の検証
- 分光分析
- ヒートロット検査
- 材料のトレーサビリティ
- 構成資料
機械的特性試験
- 引張強さ
- 降伏強度
- 伸び
- 硬度試験
品質管理認証
サプライヤーは維持しなければならない:
認証タイプ | フォーカス・エリア | 更新期間 |
---|---|---|
PMIテスト | 材料検証 | 年間 |
NDTレベルIII | 検査資格 | 3年 |
CQI-9 | 熱処理評価 | 年間 |
CQI-11 | めっきシステムの評価 | 年間 |
デジタル・セキュリティ資格
現代の航空宇宙製造に必要なこと
サイバーセキュリティ基準
- ISO 27001準拠
- NISTフレームワーク採用
- データ保護プロトコル
- 入退室管理システム
デジタルプロセス制御
- インダストリー4.0の統合
- デジタルツイン機能
- リアルタイム・モニタリング
- データ分析資格
継続的改善の要件
認証維持には以下が含まれる:
- 定期監査
- プロセス監視
- パフォーマンス指標
- 是正措置
- 予防措置
金属凝固パターンとそれが部品の品質にどのような影響を与えるかについて学ぶにはクリックしてください。 ↩
金属凝固時の結晶形成と鋳造品質への影響については、こちらをクリックしてください。 ↩
幾何学的自由度が部品設計と製造コストに与える影響については、こちらをクリックしてください。 ↩
アルマイト処理と、それがどのようにアルミニウム部品を強化するかについて、詳しくはこちらをクリックしてください。 ↩
アルミニウム鋳物の寸法精度を最適化するための収縮率の計算については、こちらをクリックしてください。 ↩
アルミニウム鋳物の保管における湿気対策について詳しくは、こちらをクリックしてください。 ↩
生産コストを大幅に削減できる高度な金属処理技術については、こちらをクリックしてください。 ↩
鋳物の強度と耐久性におけるデンドライトの間隔の重要な役割については、こちらをクリックしてください。 ↩
降水硬化の科学とその利点について、詳しくはこちらをご覧ください。 ↩
航空宇宙グレードのアルミニウム鋳造のための高度な冶金技術を学ぶにはクリックしてください。 ↩