大物射出成形サービス
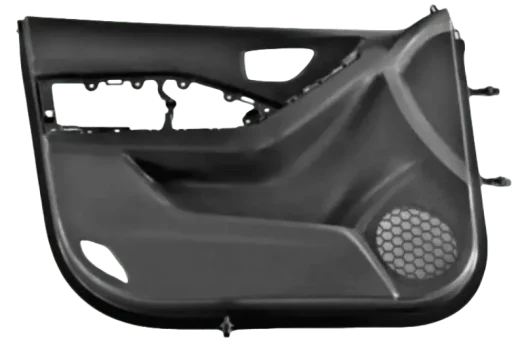
低Moq 100個
複雑部品精密成形
迅速な納期とグローバル配送
30トンから600トンまでの機械 30トンから1,600トンまで






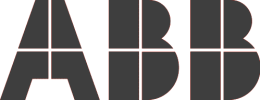

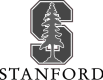
お客様の声
当社の顧客は世界中におり、そのフィードバックがすべてを物語っています。お近くのお客様から私どもの評判をお聞きになりたい場合は、ご遠慮なくお問い合わせください。
大型部品射出成形ソリューションに依存する8つの主要産業
大型部品の射出成形にPTSMAKEを選ぶ理由
PTSMAKEは20年以上の射出成形の経験があり、BMWやファーウェイなどのグローバルブランドから信頼されるソリューションを提供している。
高度な機械を駆使して寸法精度を確保し、設計を最適化することで、生産コストを30%まで削減します。
当社の50台以上の先進的な成形機は、15日の試作サイクルと30%の生産スケジュールの短縮を可能にします。
3段階の品質チェックにより、不良率は0.2%以下を維持し、成形品のトレーサビリティも万全です。
PTSMAKEの大物射出成形における品質管理について
- PTSMAKEでは、品質管理は生産開始前に始まります。私たちのチームは、潜在的な欠陥を特定するために、大規模な射出成形プロジェクトのすべての設計を検討します。高度なシミュレーションソフトウェアを使用して、材料の流れ、冷却パターン、構造的完全性を予測します。これにより、大型プラスチック部品の反りやヒケなどの欠陥を防ぐことができます。
- 私たちは射出成形用の原材料を厳しく管理しています。すべてのポリマー樹脂は、粘度、メルトフローレート、熱安定性の徹底的なテストを受けています。当社の材料トレーサビリティ・システムは、サプライヤーから完成品に至るまで、すべてのバッチを追跡します。これにより、自動車や航空宇宙用途で一般的な複雑な形状であっても、生産工程全体の一貫性が保証されます。
- 当社の射出成形機は、リアルタイム監視システムを備えています。温度、圧力、サイクルタイムは、大型部品の生産中に自動的に追跡されます。設定された基準から逸脱したパラメータがあれば、当社の技術者は即座に警告を受けます。このプロアクティブなアプローチは、生産後に品質問題を検出するのではなく、品質問題を未然に防ぎます。
- 成形された大型部品は、CMM(三次元測定機)による寸法確認が行われます。CADモデルと比較して、重要な形状を±0.01mmの精度でチェックします。ロボット部品のような高負荷がかかる用途では、さらに荷重試験と疲労解析を行います。当社の品質レポートには、詳細な測定値とプロセスデータが含まれ、完全な透明性を実現しています。
- PTSMAKEは品質手順を文書化し、ISO9001認証を維持しています。当社の品質チームは、生産工程と機器の較正について定期的な監査を実施しています。お客様には、一次検査報告書とランダムサンプリングデータを提供しています。この体系的なアプローチにより、2010年以来、重大な欠陥ゼロで99.3%の納期厳守を維持しています。
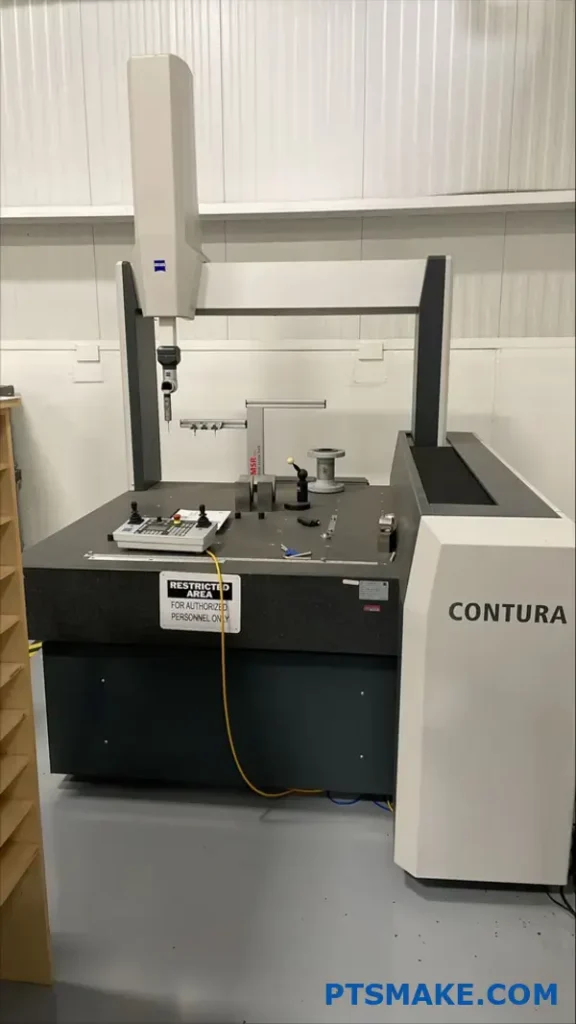
"PTSMAKEは、**0.2mmの公差**で私たちのロボットプロジェクトのための**大型プラスチックハウジング**を納入しました。彼らのチームは反りの問題を素早く修正し、18日でサンプルを出荷しました。タイトな納期に最適です。
ジェイク・ミラー(プロダクション・ディレクター、アメリカ)"
大型部品の射出成形に使用されるトップ材料
大型射出成形の標準的なリードタイム
製造スケジュールにおけるスピードと精度のバランス
- 製造業者から、"大型部品の射出成形にはどれくらいの時間がかかりますか?"という質問をよく受けます。PTSMAKEでは、プロトタイプは7-15日、生産バッチは3-5週間でお届けします。リードタイムは金型の複雑さ、材料の入手可能性、注文サイズによって異なります。社内の金型製作チームと自動化された生産システムを使ってスケジュールを最適化します。
- 大きな部品には、特別な注意が必要です。肉厚で複雑な形状の部品には、冷却と品質チェックの工程が追加されます。例えば、自動車部品は、標準的な部品よりも10%長い時間を必要とするかもしれません。当社では、材料を事前にテストし、大量注文にはマルチキャビティ金型を使用することで、遅延を短縮しています。
- タイムラインは重要です。年中無休のプロジェクト追跡ポータルにより、進捗状況をリアルタイムでご確認いただけます。すべてのご注文に専任のエンジニアを配置し、迅速なコミュニケーションをお約束します。20年以上の経験を持つ当社は、ISO認証を取得した品質を維持しながら、2010年以来、リードタイムを18%短縮してきました。
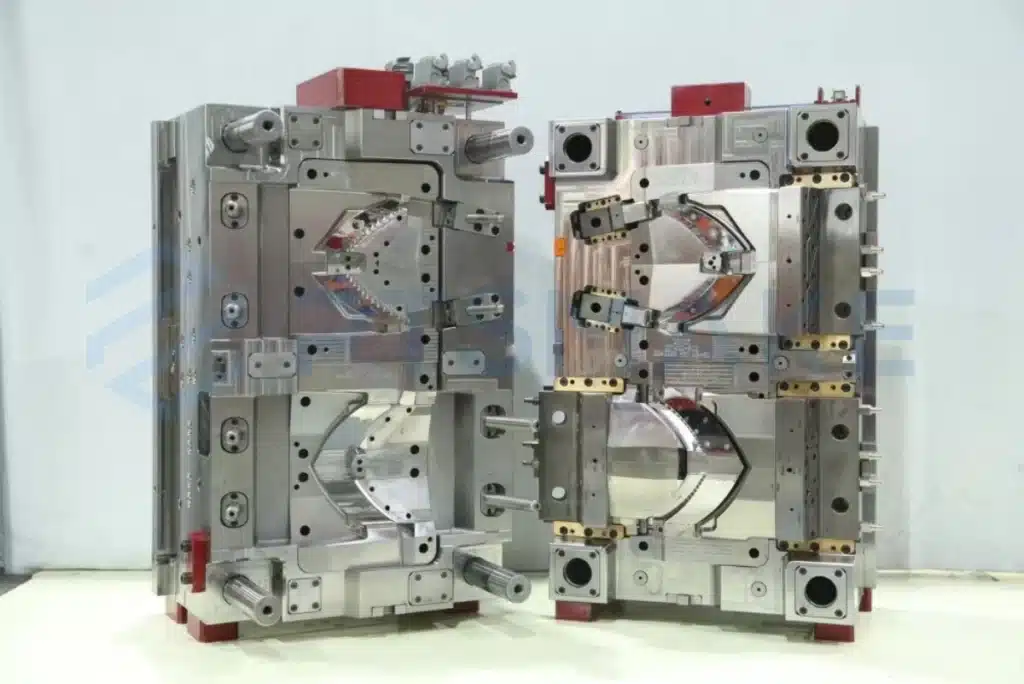
大型部品射出成形製造のステップ
1.素材の選択
2.金型設計
3.プロトタイプテスト
4.マシンセットアップ
5.プロセスの最適化
6.品質検査
7.後処理
8.梱包と配送
大物部品の射出成形における費用対効果の高いソリューション
1.材料の最適化
2.金型設計の効率
3.オートメーションの統合
4.エネルギー効率の高い機械
5.一括生産計画
6.デザインの簡素化
7.二次工程の排除
大型部品射出成形のカスタマイズオプション
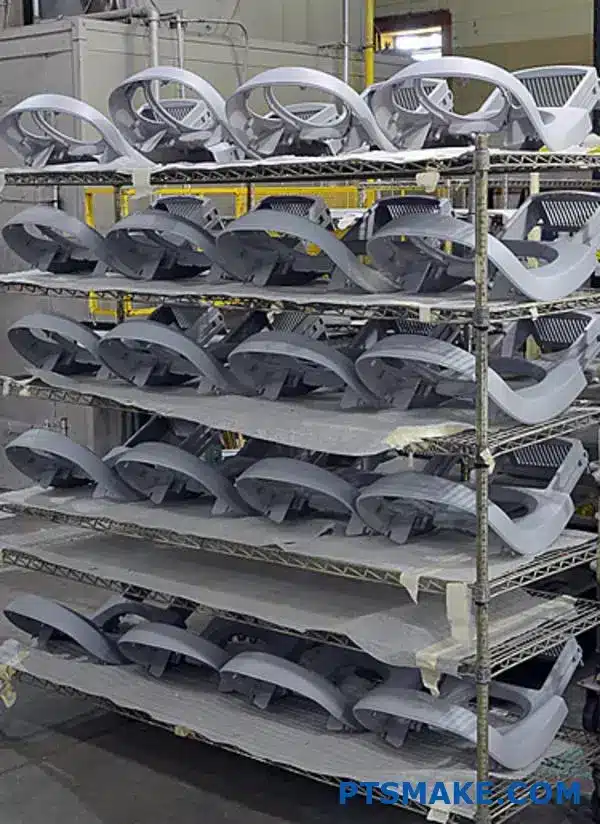
大型射出成形のためのカスタム材料選択
PTSMAKEは、大型部品の射出成形プロジェクト向けに50種類以上のエンジニアリンググレードプラスチックを提供しています。機械的強度、耐熱性、化学的適合性などの要件に基づき、お客様が材料を選択するお手伝いをいたします。私たちのチームは、ABS、ポリカーボネート、ナイロン、PEEK、および特殊用途向けのカスタムポリマーブレンドを扱っています。
医療用または食品用のプロジェクトには、USPクラスVIおよびFDA準拠の材料を提供しています。当社の材料専門家は、性能と製造コストのバランスを取るために樹脂の選択を最適化します。これにより、お客様の大型成形部品は、過剰な費用をかけることなく、機能的なニーズを正確に満たすことができます。
高度な金型設計オプション
当社のエンジニアは、シーメンスNXソフトウェアを使用してカスタム射出成形金型を作成します。大量生産用のマルチキャビティ金型やインサート金型を設計します。標準的な機械サイズを超える大型部品には、6m x 3mのプラテンを備えた型締力4,500Tの機械を利用します。
PTSMAKEは、特許取得のサイドアクション機構により、アンダーカットや薄肉設計(0.5mmまで)に対応します。すべての金型には、大型部品の反りを防止するための温度制御チャンネルが含まれています。リアルタイムの圧力監視により、安定した充填を実現します。
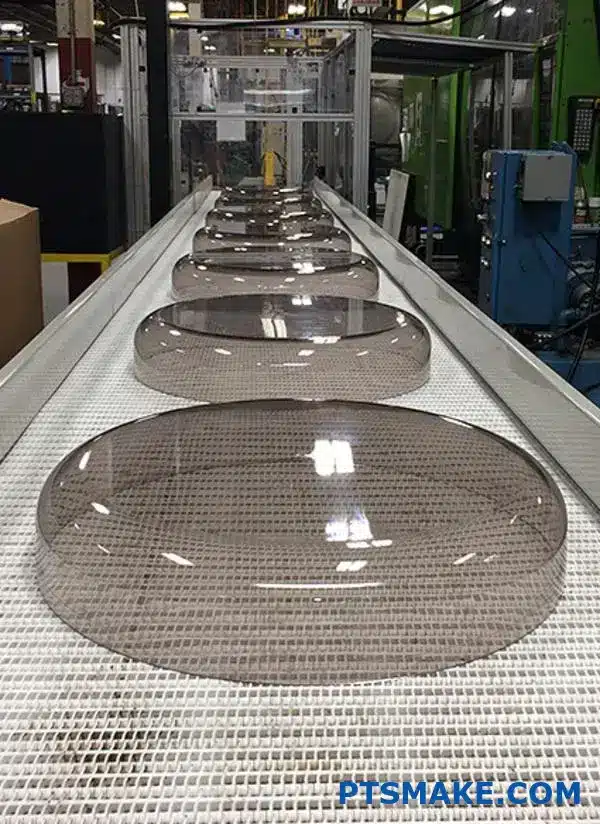
表面仕上げのカスタマイズ
12種類の標準表面仕上げからお選びいただくか、カスタムパターンをご要求ください。当社のテクスチャリング能力には、レザーシボ、マット仕上げ、高光沢研磨(Ra 0.05μm)が含まれます。技術部品には、滑り止めテクスチャーや光拡散表面を提供します。
二次加工には、塗装、パッド印刷、レーザーエッチングが含まれる。パントン・マッチング・システムを使用し、バッチ間の色の一貫性を保ちます。すべての仕上げは、耐久性を保証するために接着テストを受けます。
生産規模の柔軟性
PTSMAKEはすべての生産段階をサポートします。アルミ金型を使用して、7~10日で機能的なプロトタイプを得ることができます。当社のブリッジ金型ソリューションは、最終的なスチール金型を製作する間に500~5,000個の部品を供給します。大量生産の場合、自動化された品質チェックで24時間365日稼働します。
当社のISO9001認証工場では、最大150kgの部品を±0.15mmの公差で製造しています。コンタミネーションを防ぐため、医療用部品と工業用部品の製造ラインを分けています。
成功事例大型部品の射出成形ソリューション
自動車部品
ある大手自動車部品サプライヤーは、電気自動車用バッテリー・システム用の大型プラスチック・ハウジングを必要としていた。以前のベンダーは、反りや一貫性のない肉厚に悩まされ、組立ラインの遅れの原因となっていました。PTSMAKEは、コンフォーマル冷却チャンネルを備えた金型を再設計し、生産中にリアルタイムの圧力モニタリングを実施しました。これにより、長さ1.2mの部品全体で±0.15mmの寸法精度を維持しながら、サイクルタイムを18%短縮した。このクライアントは、当社の大型部品射出成形サービスに切り替えて以来、組立不良ゼロで毎月8,000個を生産しています。
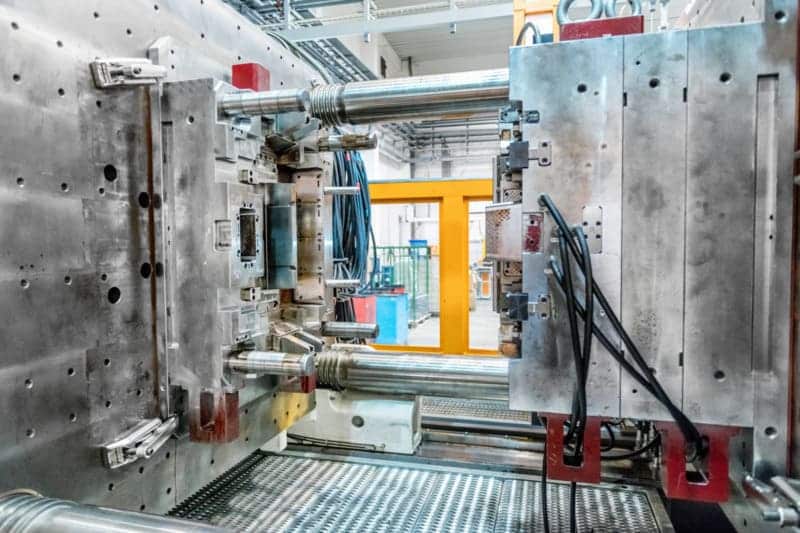
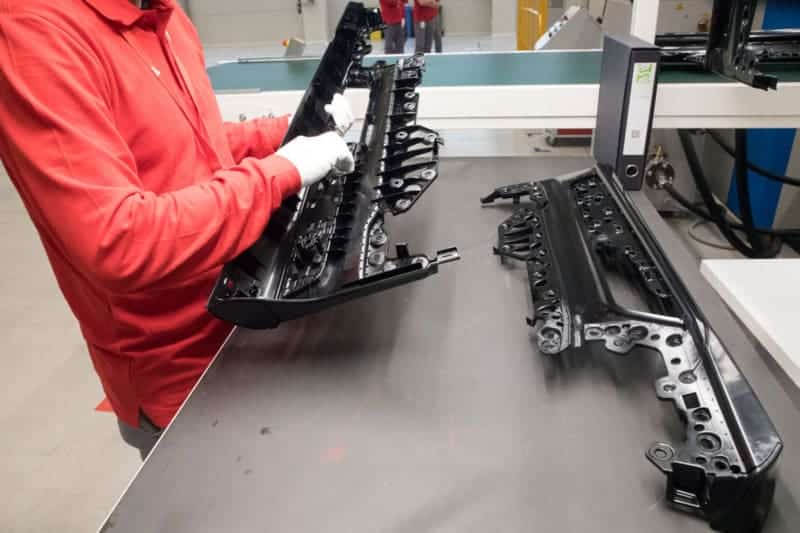
医療機器
ある医療機器メーカーは、FDA準拠の1.5m x 0.8mのMRI装置カバーを必要としていました。既存のサプライヤーでは、目に見える表面のフローラインやヒケをなくすことができませんでした。当社のチームは、医療グレードのポリカーボネートを使用した3段階のガスアシスト射出プロセスを開発しました。厳しい生体適合性基準を満たしながら、後加工なしでクラスAの表面仕上げを実現しました。このソリューションにより、従来の加工方法と比較して、ユニットあたりのコストを22%削減することができました。
産業用ロボット
ある産業用ロボット企業が、ヘビーデューティ・オートメーション・システム用に耐久性のあるナイロン製ハウジングを必要としていた。競合する提案は、予算を超えるか、耐衝撃性に妥協していました。PTSMAKEは、インサート成形と当社独自の繊維補強技術を組み合わせたハイブリッドアプローチを考案しました。こうして完成した部品は、嵌合面全体で0.05mmの位置精度を維持しながら、仕様が要求する15%の高トルク荷重に耐えることができました。
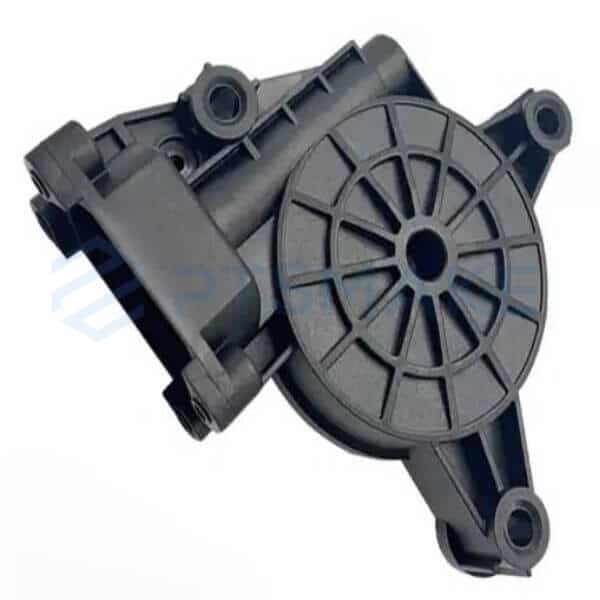