PTSMAKEに15年以上勤務する中で、オーバーモールドと2K射出成形に戸惑うお客様を多く見てきました。それは、サンドイッチとハンバーガーを選ぶようなもので、見た目は似ていても、それぞれ異なるニーズがあります。
オーバーモールドは、2つの別々の工程で既存の部品の上に材料を射出するのに対し、2K(ツーショット)射出成形は、1回の機械サイクルで複数の材料を使用した製品を作る。両者は、工程、コスト、最終用途が異なります。
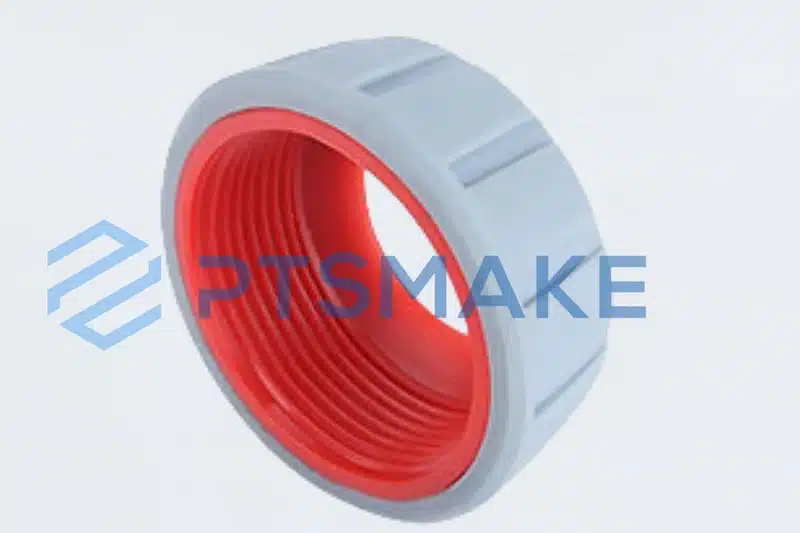
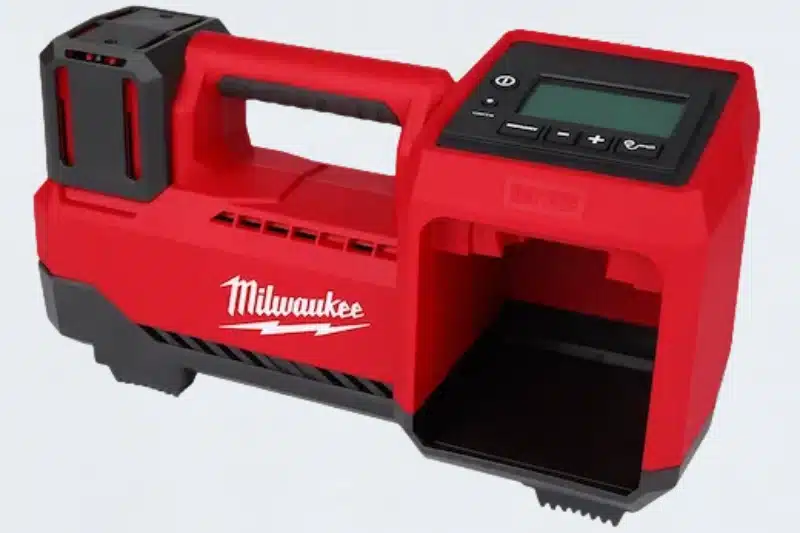
PTSMAKEで何百人ものクライアントと仕事をしてきた中で学んだことをお話ししましょう。これらのプロセスはどちらも素晴らしいマルチマテリアル製品を作ることができますが、正しい方を選ぶことで時間とコストを節約することができます。主な違いを説明し、実際の例をお見せしながら、あなたのプロジェクトに最適なプロセスを決めるお手伝いをします。
オーバーモールディングとは?
携帯電話のケースが、硬いプラスチックと柔らかくグリップ性のある表面をどのように組み合わせているのか不思議に思ったことはないだろうか。あるいは、最新の医療器具が頑丈さと快適さを兼ね備えているのはなぜだろう?その秘密はオーバーモールディング技術にあります。
オーバーモールドとは、既存の第一の材料の上に第二の材料を注入し、単一のマルチマテリアル部品を作成する製造プロセスです。この技術は、製品の機能性、耐久性、ユーザーエクスペリエンスを向上させるために、異なる材料の特性を組み合わせるものです。
オーバーモールドの基本を理解する
PTSMAKEでの15年以上、私はオーバーモールドが様々な業界の製品デザインに革命を起こすのを目の当たりにしてきました。このプロセスには通常2つの主要コンポーネントが含まれます:硬い基材(通常は熱可塑性プラスチック)とオーバーモールドされた材料(多くの場合、TPEやゴムのような柔らかく、より柔軟な材料)です。
このプロセスは2段階に分かれている:
- まず、伝統的な射出成形でベースとなる部品を作ります。
- 次に、第二の材料をベース部品の特定の部分に注入する。
オーバーモールドの主な利点
さまざまな業界のクライアントとの豊富な経験に基づき、私はいくつかの重要な利点を特定した:
ベネフィット | 説明 | 実例 |
---|---|---|
人間工学の向上 | ソフトタッチの表面により、グリップと使い心地を向上 | 電動工具のハンドル |
耐久性の向上 | 衝撃吸収と振動減衰 | 電子機器ケース |
デザインの柔軟性 | 複数の色と素材の組み合わせ | 消費者製品の筐体 |
コスト効率 | 組立工程を省き、部品を削減 | 医療機器部品 |
環境シーリング | 防水・防塵バリア | アウトドア用品 |
素材の組み合わせと互換性
私がオーバーモールドで学んだ最も重要な点のひとつは、材料の選択です。ここでは、PTSMAKEで最もよく使う組み合わせを紹介します:
硬い基板材料:
- ABS(アクリロニトリル・ブタジエン・スチレン)
- PC(ポリカーボネート)
- ナイロン
- PP(ポリプロピレン)
オーバーモールド材料:
- TPE(熱可塑性エラストマー)
- TPU(熱可塑性ポリウレタン)
- シリコーン
- ソフトPVC
産業用途
私はこれまでのキャリアの中で、オーバーモールドがさまざまな産業を変えるのを見てきた:
医療機器
- グリップ力が向上した手術器具
- 剛性ハウジングと快適な皮膚接触面を組み合わせたウェアラブル機器
- 抗菌性を備えた医療機器ハンドル
コンシューマー・エレクトロニクス
- スマートフォン&タブレットケース
- ゲーミング・コントローラー用グリップ
- 防水電子筐体
自動車部品
- ダッシュボード・コントロール
- インテリア・トリム
- ギアシフトノブ
設計上の考慮事項
オーバーモールドの設計をする際、私はいつもクライアントにこうアドバイスしている:
素材適合性
- 化学結合特性
- 熱膨張率
- 加工温度要件
幾何学的特徴
- 肉厚のばらつき
- アンダーカットとドラフトアングル
- ゲート位置
生産要件
- 出来高予想
- コスト制約
- 品質基準
共通の課題と解決策
これまでの経験を通じて、私はオーバーモールドでいくつかの難題に遭遇してきた:
チャレンジ | ソリューション | インパクト |
---|---|---|
接着不良 | 材料適合性試験 | 製品耐久性の向上 |
フラッシュ・フォーメーション | 最適化された工具設計 | より良い美的品質 |
寸法安定性 | 適切な冷却時間の計算 | 精度の向上 |
コスト管理 | 戦略的な素材選択 | 収益性の改善 |
オーバーモールドの品質管理
PTSMAKEでは、厳格な品質管理対策を実施しています:
プリプロダクション・テスト
- 材料適合性の検証
- 金型流動解析
- プロトタイプ評価
インプロセス制御
- 温度モニタリング
- 圧力検証
- サイクルタイムの最適化
ポストプロダクション検査
- 目視検査
- 接着試験
- 寸法検証
私はこの業界での長年の経験を通じて、オーバーモールドがニッチなプロセスから主流の製造ソリューションへと進化するのを見てきました。組み立てコストを削減し、製品の性能を向上させながら、異なる素材をひとつの部品に組み合わせることができるオーバーモールドは、現代の製造業において非常に貴重なツールとなっている。
2K射出成形とは?
ソフトグリップのついたスマートフォンのケースは、どうやって一体成型されているのだろうと不思議に思ったことはないだろうか。あるいは、車のダッシュボードはどうやって硬いプラスチックとソフトタッチの素材をシームレスに組み合わせているのだろう?
2K射出成形は、1つの金型に2つの異なる材料または色を順次射出する高度な製造プロセスで、1回の製造サイクルで複数の特性を持つ複雑な部品を作り、組み立ての必要性をなくします。
2K成形の基本メカニズム
PTSMAKEでの15年以上、私は数え切れないほどの2K射出成形プロジェクトを監督してきた。この工程は、金型のキャビティに最初の材料(通常は硬質プラスチック)を射出することから始まります。次に、金型を回転させるかロボットを使って、2つ目の材料を別のキャビティに注入します。2つの材料は冷却過程で化学的または機械的に結合します。
2K射出成形の主要部品
コンポーネント | 機能 | 重要性 |
---|---|---|
一次射出ユニット | 最初の材料を加工する | フォームの基本構造 |
セカンダリー・インジェクション・ユニット | 第二の素材を加工する | 機能的/審美的特徴の追加 |
回転金型システム | 材料の移送が可能 | 正確なアライメントを保証 |
制御システム | タイミングと順序を管理する | 品質の一貫性を維持 |
素材の適合性と選択
私がいつもお客様に強調している重要な点は、素材の相性です。すべての素材がうまく結合するわけではありません。私たちはこれまでの経験から、包括的な素材の組み合わせガイドを開発しました:
主要素材 | 適合副資材 | 一般的なアプリケーション |
---|---|---|
PC | TPE、TPU、シリコーン | 電子機器ハウジング |
ABS | TPE、TPU、SEBS | 自動車部品 |
PA | TPE、TPU | ツールハンドル |
PP | TPE、TPU、SEBS | 消費財 |
伝統的な成形を超える利点
グローバル・メーカーと仕事をした経験から言うと、2K射出成形にはいくつかの明確な利点がある:
生産効率
- 組み立てステップを排除
- 人件費の削減
- 生産サイクルを25-40%短縮
品質向上
- より良い材料接着
- 不良率の低減
- 安定した部品品質
デザインの柔軟性
- 複雑な形状も可能
- 複数の色の組み合わせ
- 1つの部品で異なる材料特性
産業用途
PTSMAKEでの仕事から、2K射出成形がさまざまな分野で優れているのを見てきました:
自動車産業
- ダッシュボード・コンポーネント
- ギアシフター
- インテリア・トリム
- ライトハウジング
コンシューマー・エレクトロニクス
- スマートフォンケース
- リモコン
- ゲーミングコントローラー
- ウェアラブル機器
医療機器
- 手術器具
- 薬物送達デバイス
- 診断機器
- 医療機器ハウジング
技術的考察
2K射出成形を実施する際には、いくつかの要素に注意を払う必要がある:
プロセス・パラメーター
- 射出圧力制御
- 材料の温度管理
- サイクルタイムの最適化
- 冷却時間の調整
デザイン・ガイドライン
- 肉厚比
- ゲート位置
- 材料流路
- 接着表面積
品質管理対策
- 目視検査プロトコル
- 接着強度試験
- 寸法精度チェック
- 表面仕上げ評価
コストへの影響
長年の経験を通じて、2K成形の初期金型費用は高くつくが、長期的な利益は投資を正当化することが多いということを私は見てきた:
コスト係数 | インパクト | ROIタイムライン |
---|---|---|
工具 | 従来の30-50%より高い | 6-12ヶ月 |
労働 | 40-60% 下 | 即時 |
廃棄物 | 20-30% リダクション | 3-6ヶ月 |
品質管理 | 25-35%より低い不合格率 | 3-6ヶ月 |
プロセスの限界と解決策
その利点があっても、2K射出成形には一定の限界があり、私たちはそれに対処する方法を学んできました:
素材の制約
- 限られた素材の組み合わせ
- 温度互換性の問題
- 接着強度のばらつき
設計上の制限
- 最小肉厚要件
- ゲート位置の制限
- 部品サイズの制約
コストに関する考察
- 高い初期投資
- 複雑な金型設計
- 特殊機器のニーズ
入念な計画と材料の選択によって、これらの制限を効果的に管理し、最適な結果を得ることができる。
オーバーモールドは2K射出成形とどう違うのか?
プラスチック射出成形に15年以上携わってきた私は、オーバーモールド成形と2K射出成形を混同するクライアントを数え切れないほど見てきた。
オーバーモールドと2K射出成形は異なる製造工程である。オーバーモールドは2つの別々の成形工程を順番に行うのに対し、2K射出成形は特殊な設備を使って両方の工程を1つのサイクルにまとめる。
プロセス・ワークフローの違い
PTSMAKEでの日々の業務の中で、ワークフローを理解することが非常に重要であることを実感している。主な違いを説明しよう:
オーバーモールド工程
- 最初のステップベース・コンポーネント(基板)の作成
- 第二段階:別の金型または機械に移す
- 最終段階:基材の上に第2の材料を成形する
- 合計時間通常、全サイクルで20~45分
2K射出成形プロセス
- 単一機械操作
- ショット間の自動回転
- 連続成形サイクル
- 合計時間通常30~60秒/パーツ
機材要件
両プロセスを管理した私の経験に基づき、以下に詳細な比較を示す:
特徴 | オーバーモールディング | 2K射出成形 |
---|---|---|
マシンタイプ | 標準射出成形機 | マルチコンポーネント専用機 |
ツールの複雑さ | シンプルなセパレート型 | 複雑で統合された金型システム |
セットアップ時間 | 長時間の複数セットアップ | より短く、シングルセットアップ |
投資コスト | 初期投資の低減 | 機械・工具コストの上昇 |
材料適合性の考慮
私はこれまで数多くのクライアントがプロジェクトに適した素材を選ぶお手伝いをしてきました。ここで知っておくべきことがあります:
オーバーモールディング材料オプション
- より柔軟な素材の組み合わせ
- 非相溶性材料に最適
- 適切な結合のための時間を確保する
- 接着促進剤の使用が可能
2K成形材料の要件
- 材料は化学的に適合していなければならない
- 同様の処理温度が必要
- 限られた素材の組み合わせオプション
- より迅速なボンディング要件
設計上の考慮事項
長年のプロジェクト・マネジメントを通じて、私はこれらの重要な設計要素を特定した:
オーバーモールディング・デザインの利点
- より複雑な形状も可能
- 界面の厚みをより良くコントロール
- 設計変更が容易
- より寛容な公差要件
2K成形設計の限界
- 工具の移動による制限
- 正確なゲート位置の必要性
- 限定的なアンダーカットが可能
- より厳しい公差要件
コストへの影響
私たちの価格設定の議論から得た洞察をいくつか紹介しよう:
オーバーモールド・コスト
- 金型投資の削減
- 人件費の上昇
- ハンドリング・コストの増加
- 少量生産に適している
2K成形コスト
- 高い初期投資
- 人件費の削減
- ハンドリング・コストの削減
- 大量生産でより経済的
品質への配慮
私の品質管理の経験では:
オーバーモールドの品質
- 各レイヤーをより良くコントロール
- ステップ間の検査が容易
- より安定したボンディング
- 複雑な部品の不合格率を低減
2K成形の品質要因
- サイクルタイムの短縮は接着に影響する
- インターフェイスの検査がより困難に
- シンプルな部品における高い一貫性
- 大量の一貫性を保つのに適している
アプリケーション選択ガイド
私が監督してきた何千ものプロジェクトに基づいている:
オーバーモールドに最適
- 認証材料を必要とする医療機器
- 複雑な電子筐体
- ソフトタッチのハンドルとグリップ
- 低~中程度の生産量
2K成形に最適
- 自動車部品
- 大量消費財
- シンプルな2色のアプリケーション
- 速い生産サイクルを必要とする部品
PTSMAKEでの豊富な経験を通じて、オーバーモールドと2K射出成形のどちらを選ぶかは、技術的な能力だけでなく、具体的なプロジェクトのニーズ、生産量、品質要件を理解することだと学びました。各プロセスにはそれぞれ独自の利点があり、成功の鍵は、お客様の特定の用途に基づき、十分な情報を得た上で選択することにあります。
オーバーモールドの利点と限界とは?
PTSMAKEに15年以上勤務する製造の専門家として、私は、オーバーモールディングが書類上完璧に見えても、現実には予期せぬ課題をもたらすプロジェクトを数え切れないほど見てきました。
オーバーモールドは、複数の材料を1つの部品に組み合わせる製造工程であり、グリップ力の向上や組み立ての必要性の低減といった利点があるが、製造サイクルの長期化や材料の接着の問題といった課題もある。
オーバーモールドの主な利点
製品機能の強化
大手エレクトロニクス・メーカーと仕事をした経験では、オーバーモールドは製品のグリップと感触を向上させる上で非常に貴重であることが証明されている。以下は、私が観察した結果である:
- 電動工具のソフトタッチ・グリップ
- 医療機器の滑り止め
- 消費者製品の人間工学的ハンドル
組み立ての手間を軽減
私が目にした最も大きな利点のひとつは、複数の組み立て工程が不要になることだ:
- メカニカルファスナー不要
- 部品点数の削減
- 人件費の削減
- 組み立てミスのリスクを低減
製品保護の向上
オーバーモールドの密閉性は注目に値する:
- 耐水性バリア
- 塵や埃からの保護
- 振動減衰
- 過酷な環境下での耐久性が向上
保護タイプ | ベネフィット | 一般的なアプリケーション |
---|---|---|
モイスチャーシール | 水の浸入を防ぐ | アウトドア・エレクトロニクス |
衝撃保護 | 衝撃を吸収 | モバイル機器 |
耐薬品性 | 腐食を防ぐ | 産業機器 |
断熱 | 温度管理 | ハンドツール |
限界と課題
生産サイクルの延長
私の製造現場での経験から:
- セットアップ時間が長くなる
- 追加の品質チェックが必要
- 複数のマテリアルハンドリング要件
- ショット間の冷却時間
コストに関する考察
財務上の影響には以下が含まれる:
- 高い初期金型投資
- 二次操業コスト
- 材料適合性試験
- 品質管理の強化
技術的課題
マテリアル・ボンディングの問題
私はこのような一般的な問題に遭遇したことがある:
- 素材間の接着不良
- 熱膨張のミスマッチ
- 化学的適合性に関する懸念
- 表面処理の要件
設計上の制限
主な制限事項は以下の通り:
- 材料の厚さの制約
- ゲート位置の制限
- 複雑な形状の課題
- 工具設計の考慮点
チャレンジ | インパクト | 緩和戦略 |
---|---|---|
素材適合性 | 層間剥離のリスク | 広範な材料試験 |
ツールデザイン | より高い複雑性 | 高度なCADシミュレーション |
品質管理 | 検査ニーズの増加 | 自動ビジョンシステム |
生産スピード | 長いサイクルタイム | プロセスの最適化 |
実際のアプリケーションとケーススタディ
コンシューマー・エレクトロニクス
大手電機メーカーとの仕事では
- リモコンのソフトタッチボタン
- 屋外機器用防水シール
- 携帯電話用耐衝撃ケース
医療機器
私たちの医療機器プロジェクトが実証している:
- 人間工学に基づいた手術器具ハンドル
- 耐薬品性機器ハウジング
- 滅菌適合部品
自動車用途
一般的な自動車用途には以下のようなものがある:
- 内装トリム部品
- 耐候性電気コネクタ
- 防振マウント
オーバーモールドを成功させるためのベストプラクティス
何千ものプロジェクトを管理した経験に基づいている:
素材の選択
- 徹底した互換性テスト
- 温度抵抗の検証
- 耐薬品性評価
デザインの最適化
- 適切なゲート位置計画
- 肉厚の考慮
- ドラフトアングルの実装
プロセス制御
- 温度モニタリング
- 圧力の最適化
- サイクルタイム管理
品質保証
- 目視検査プロトコル
- 接着強度試験
- 寸法検証
PTSMAKEでの数年間を通して、オーバーモールドを成功させるには、これらの利点と限界の間で注意深くバランスを取る必要があることを学びました。メリットは大きいのですが、最適な結果を得るためには慎重な計画と専門知識が不可欠です。私は常に、オーバーモールディング・ソリューションにコミットする前に、これらの要素に照らして具体的な要求を徹底的に評価するよう、クライアントにアドバイスしています。
2K射出成形の利点と限界は?
2K射出成形があなたのプロジェクトに適しているかどうか、判断に迷っていませんか?業界で15年以上働いてきた私は、この技術の驚くべき利点と困難な限界の両方を見てきました。
2K射出成形は、速い生産サイクルと強力な材料接着を提供しますが、高い初期設備費用がかかり、大量生産に最適です。これらのトレードオフを理解することは、十分な情報に基づいた製造上の決定を行う上で非常に重要です。
2K射出成形の主な利点
PTSMAKEでの経験から、私は2K射出成形を際立たせるいくつかの重要な利点を特定した:
効率的な生産サイクル
1回の成形サイクルで2つの素材を統合することで、生産時間を大幅に短縮することができます。私たちの施設では
伝統的なプロセス | 2K成形プロセス | 時間の節約 |
---|---|---|
45~60秒/パート | 25~35秒/パート | 40%まで |
優れた材料接着
従来の組み立て方法とは異なり、2K成形は材料間に分子結合を形成します。その結果
- より高い構造的完全性
- 環境要因に対する耐性が向上
- 部品分離のリスクを低減
- 製品寿命の向上
強化された設計の柔軟性
異なる素材を組み合わせることで、新たなデザインの可能性が広がる:
- マルチカラーの組み合わせ
- ソフトタッチのオーバーレイ
- 一体型シールとガスケット
- 複雑な形状
限界と課題
高額な初期投資
生産ラインを管理した経験から言うと、初期コストは相当なものになる:
投資カテゴリー | おおよそのコスト範囲 |
---|---|
2K成形機 | $150,000 - $500,000 |
カスタム金型 | $25,000 - $100,000 |
セットアップとトレーニング | $10,000 - $30,000 |
ボリューム要件
2K成形は、主に大量生産において費用対効果が高くなる:
- 最低推奨年間販売台数:100,000台以上
- 最適生産範囲:25万台以上
- 損益分岐点には通常、かなりの生産量が必要
技術的な複雑さ
PTSMAKEに15年以上在籍し、いくつかの技術的な課題を見てきた:
- 材料適合性要件
- 複雑な工具設計のニーズ
- 精密なプロセス制御の要求
- 特別なオペレーター・トレーニングの要件
実世界での応用
自動車産業
私たちは2K成形の導入に成功している:
- ソフトタッチのダッシュボード・コンポーネント
- マルチカラー表示灯
- 電気コネクタの一体型シール
- 耐候性エクステリア・トリム
コンシューマー・エレクトロニクス
私たちの経験には以下が含まれる:
- ラバーグリップ付きスマートフォンケース
- ゲーミング・コントローラー・コンポーネント
- 防水ハウジング
- マルチカラー表示灯
医療機器
重要な用途には以下が含まれる:
- エルゴノミック・グリップ付き手術器具
- シール一体型医療機器ハウジング
- 複数の素材を用いた薬物送達デバイス
- 実験装置部品
プロセス最適化戦略
我々の製造経験に基づき、私は推薦する:
素材の選択
- 徹底した材料適合性試験の実施
- 両素材の収縮率を考慮する
- 材料の組み合わせによる費用対効果の評価
ツールデザイン
- 適切な換気と冷却経路の確保
- 最適なゲート位置を設計
- マテリアルフローパターンを考慮する
品質管理
- 自動検査システムの導入
- 明確な品質パラメータの設定
- 厳格なプロセス文書の管理
コスト管理
- サイクルタイムの最適化
- 材料の無駄を最小限に抑える
- 予知保全の実施
- 効果的なオペレーターの育成
PTSMAKEで様々なクライアントと長年仕事をする中で、2K射出成形を成功させるには、これらの要素を慎重に検討する必要があることを学びました。この技術は、生産効率と製品品質の面で顕著な利点を提供しますが、その利点が、お客様の特定の用途のための初期投資と継続的な運用要件を正当化するかどうかを慎重に評価することが不可欠です。
重要なのは、2K射出成形に踏み切る前に、生産要件、材料仕様、長期的な製造戦略を徹底的に分析することです。多くの場合、この技術の利点は大きな競争力をもたらしますが、それは製造目標や生産量と適切に整合している場合に限られます。
オーバーモールドが最も恩恵を受ける産業は?
どの業界がオーバーモールドの可能性を本当に最大化できるのか、疑問に思っていませんか?製造業に15年以上携わってきた私は、さまざまな分野で目覚ましい変革を見てきました。
オーバーモールディング技術は、主に医療機器、家電製品、自動車、携帯工具の4つの主要産業に恩恵をもたらしています。これらの分野では、オーバーモールディングを活用することで、製品の機能性を高め、使い勝手を向上させ、費用対効果を維持しながら耐久性を高めています。
医療産業への応用
医療機器メーカーと仕事をした経験から言うと、オーバーモールドは医療機器の設計に革命をもたらしました。医療機器には、正確なグリップ力、快適性、滅菌機能が求められます。主な用途をいくつかご紹介しましょう:
- 人間工学に基づいたハンドルの手術器具
- グリップが強化された医療用注射器
- 快適なグリップの歯科器具
- 密閉性を備えた医療機器用エンクロージャー
医療業界では、シームレスで細菌が繁殖しにくく、洗浄や滅菌が容易なオーバーモールド成形が特に評価されている。
家電製品への影響
コンシューマー・エレクトロニクスの分野では、保護と美観の両方の目的でオーバーモールドが採用されている。私は、この技術が製品の耐久性とユーザー体験を向上させた例を数え切れないほど見てきました:
製品カテゴリー | オーバーモールドの利点 |
---|---|
スマートフォンケース | 耐衝撃性、グリップ強化 |
イヤホン | 快適性、防水性 |
リモコン | 耐久性、衝撃吸収性 |
ゲームコントローラー | 人間工学に基づいたグリップ、耐汗性 |
自動車産業統合
自動車産業は、オーバーモールディングの最大市場のひとつです。大手自動車メーカーとの協力関係から、私はこれらの重要な用途を観察してきました:
内装部品
- ダッシュボード・コントロール
- ドアハンドル
- センターコンソール・エレメント
- ステアリング・グリップ
外部部品
- ウェザーシール
- ガスケット
- ケーブルコネクター
- トリム部品
ハンディツール革命
工具メーカーと仕事をしていると、オーバーモールドが電動工具やハンドツール業界をどのように変えたかがよくわかる:
電動工具
- 防振機能付きドリルハンドル
- 安全機能を強化したノコギリグリップ
- 耐久性を向上させたインパクトドライバハウジング
- コントロールしやすい電動ドライバーハンドル
ハンドツール
- エルゴノミックデザインのドライバーハンドル
- 快適機能付きプライヤーグリップ
- 滑り止め付きレンチハンドル
- 衝撃吸収機能付きハンマーグリップ
業界を超えたメリット
PTSMAKEでの経験を通じて、私はオーバーモールドがこれらの産業にもたらすいくつかの普遍的な利点を特定しました:
機能強化
- より良いグリップとコントロール
- シール性の向上
- 振動減衰
- 耐衝撃性
美観の向上
- カスタム・カラー・オプション
- テクスチャーのバリエーション
- ブランドの差別化
- プレミアム・ルック&フィール
コスト効率
- 組み立てステップの削減
- 人件費の削減
- 生産時間の短縮
- 最小限の廃棄物
ユーザー・エクスペリエンス
- 人間工学の改善
- より良い触覚フィードバック
- 強化された安全機能
- より快適
製造に関する考慮事項
さまざまなクライアントとの豊富な経験に基づき、私は、オーバーモールドの導入を成功させるためには、次のような重要な要素が不可欠であることを発見しました:
考察 | インパクト |
---|---|
素材の選択 | 接着強度と性能を判定 |
デザインの最適化 | 製造効率に影響 |
品質管理 | 一貫した結果を保証 |
コスト管理 | 市場競争力に影響 |
様々な業界と仕事をする中で、オーバーモールディングを成功させるためには、次のようなことを注意深く考慮する必要があることを学んだ:
- 素材適合性
- 設計要件
- 生産量
- 環境条件
- 規制遵守
これらの産業におけるオーバーモールドの成功は、その汎用性と有効性を証明しています。数え切れないほどのプロジェクトを監督してきた経験から、オーバーモールドが適切に導入されれば、製品の品質、ユーザーの満足度、製造効率の面で大きな競争力を発揮すると自信を持って言えます。
2K射出成形から最も恩恵を受ける産業は?
どの業界が2K射出成形革命をリードしているのか気になりませんか?製造業に15年以上携わってきた私は、さまざまな分野で目覚ましい変革を見てきました。
2K射出成形は、自動車、家電、医療業界において、画期的な技術となっている。これらの分野では、この先進的な製造プロセスを通じて、組み立てコストの削減、製品の機能性の向上、生産効率の改善などの恩恵を受けています。
自動車産業への応用
大手自動車メーカーと仕事をした経験から言うと、2K射出成形は内装部品の生産に革命をもたらしました。自動車産業は次のようなメリットを享受している:
- マルチマテリアル・ダッシュボード・コンポーネント
- ソフトタッチのステアリング・ホイール・コントロール
- 照光式ボタンアセンブリ
- 耐候性エクステリア・トリム
硬質材料と軟質材料を単一工程で統合することにより、組立時間が大幅に短縮され、部品の品質が向上しました。例えば、ソフトグリップ素材が一体化されたドアハンドルは、従来の製造方法と比べ、40%短縮されました。
コンシューマー・エレクトロニクスの進化
エレクトロニクス業界は2K成形を採用している:
コンポーネント・タイプ | メリット | 一般的なアプリケーション |
---|---|---|
ボタンアセンブリ | 多色展開、触感の向上 | 携帯電話、リモコン |
デバイス・ハウジング | 防水シーリング、美観 | スマートデバイス、ウェアラブル |
コントロールパネル | 強化された耐久性、一体型ディスプレイ | 家電製品、ゲーム機 |
医療機器製造
医療分野では特に、2K成形の造形能力の恩恵を受けている:
- ソフトグリップハンドルの人間工学に基づいた手術器具
- マルチコンポーネント診断装置
- ガスケット一体型密閉医療用ハウジング
滅菌対応素材と快適なグリップ面を組み合わせ、製品の安全性を高めながら製造工程を減らしているのを見たことがある。
家電製品の革新
最新の家電製品には2Kモールディングが使われている:
- コントロール・パネル・インターフェース
- 密封された防水部品
- 人間工学に基づいたハンドルとグリップ
- 機能性を備えた装飾要素
パーソナルケア製品
パーソナルケア業界は、2K成形を活用している:
- グリップゾーン付き歯ブラシハンドル
- 剛性とソフトタッチを兼ね備えたカミソリハンドル
- 複数の材料特性を持つ化粧品パッケージ
業界を超えた費用対効果
私は製造業の経験から、次のような主な利点を感じている:
組み立てコストの削減
- 二次オペレーションの排除
- より少ない労働力
- 在庫管理の必要性が減少
生産効率
- サイクルタイムの短縮
- スクラップ率の低減
- 品質の一貫性の向上
デザインの自由
- 複数の機能の統合
- 美的オプションの充実
- より良い人間工学的ソリューション
品質とパフォーマンスの向上
2K成形の導入がもたらしたもの:
アスペクト | 伝統的な成形 | 2K成形 |
---|---|---|
組み立てステップ | 3-4ステップ | 1ステップ |
サイクルタイム | 45~60秒 | 25~35秒 |
不良率 | 2-3% | <1% |
材料の接着強度 | 中程度 | 高い |
環境への影響
2K射出成形は、以下のような環境上のメリットをもたらします:
- 組み立て工程を省くことで廃棄物を削減
- 生産におけるエネルギー消費の低減
- 部品の輸送ニーズの減少
- 製品寿命の向上
これらの業界のクライアントと仕事をすると、従来の製造方法と比較して15-20%のコスト削減を常に目にします。単一工程で材料を組み合わせる能力は、効率を向上させるだけでなく、以前は不可能だった革新的な設計ソリューションを可能にします。
PTSMAKEでの数年間を通して、私はこれらのセクターにおける製造プロセスの変革を目の当たりにしてきました。2K射出成形の採用は、コスト削減、品質向上、革新的な設計ソリューションの実現という利点がより多くの業界で認識されるにつれて、拡大し続けています。
2K射出成形を検討している企業にとって、成功するかどうかは適切な材料選択、金型設計、工程管理にかかっていることを理解することは極めて重要である。2K技術への初期投資は、多くの場合、長期的な生産コストの節約と製品品質の改善によって相殺されます。
オーバーモールドではどのような材料の組み合わせが可能か?
歯ブラシの柄は柔らかいのに、なぜヘッドは硬いままなのか不思議に思ったことはありませんか?あるいは、電動工具のグリップ面が完璧なのはなぜだろう?それは、オーバーモールドのマジックなのです。
オーバーモールドでは、主に熱可塑性プラスチックとエラストマーの組み合わせ、金属とプラスチックの組み合わせ、複数の熱可塑性プラスチックの組み合わせなど、さまざまな材料の組み合わせが可能です。成功するかどうかは、材料の適合性、表面処理、適切な接着技術にかかっている。
一般的な素材の組み合わせ
PTSMAKEでの15年以上の経験に基づき、私は数多くの素材の組み合わせを扱ってきました。ここでは最も一般的なものを紹介します:
熱可塑性プラスチックとエラストマーの組み合わせ
私たちが最もよく使う組み合わせは、熱可塑性基材と熱可塑性エラストマー(TPE)の組み合わせです。これらの組み合わせは、優れた接着特性と汎用性を提供します。以下は、私たちが使用している典型的な適合表です:
基板材料 | 適合TPE | 一般的なアプリケーション |
---|---|---|
PP | TPE-S、TPV | 消費者製品、自動車部品 |
ABS | TPE-S、TPU | 電子ハウジング、ハンドル |
PC | TPE-U、TPE-E | 医療機器、工具 |
PA | TPE-E、TPU | 産業用部品 |
PBT | TPE-E、TPU | 電気コネクタ |
金属とプラスチックの組み合わせ
金属とプラスチックを組み合わせる場合、表面処理が非常に重要になります。私は、表面処理が不十分なために多くのプロジェクトが失敗するのを見てきました。私たちがよく使う主な材料は以下の通りです:
- アルミニウムとエンジニアリング熱可塑性プラスチック
- 高性能ポリマーを使用したステンレス鋼
- 真鍮と特殊グレードのナイロン
マルチ熱可塑性樹脂システム
ここからが面白くなる。異なる熱可塑性プラスチックを組み合わせることで、特定の特性を得ることができる:
- 耐衝撃性を向上させるPC/ABSの組み合わせ
- 耐薬品性を高めるPBT/PETブレンド
- コストパフォーマンスの高いPA/PPシステム
ボンディングを成功させるための重要な要素
素材適合性
私の経験では、化学的適合性がオーバーモールドを成功させる基礎となります。私たちが考慮することは以下の通りです:
- 化学構造の類似性
- 溶融温度範囲
- 分子鎖相互作用ポテンシャル
- 表面エネルギー特性
表面処理技術
私は、適切な表面処理がオーバーモールディング・プロジェクトを左右することを学んだ:
準備方法 | 最適 | 効果 |
---|---|---|
プラズマ治療 | 金属、高機能プラスチック | 素晴らしい |
コロナ・トリートメント | ほとんどの熱可塑性プラスチック | 非常に良い |
ケミカル・エッチング | 金属、難接着性プラスチック | グッド |
機械的摩耗 | 金属基板 | 中程度 |
アドバンスド・ボンディング・ソリューション
PTSMAKEでの私の仕事では、ボンディングを強化するためのいくつかのアプローチを開発してきた:
プライマーの用途
- 非相溶性材料用の特殊プライマーの使用
- カスタムプライマー処方の開発
- 表面処理剤の塗布
メカニカル・インターロック
- アンダーカットとチャンネルの設計
- マイクロテクスチャー・パターンの作成
- ダブテール機能の実装
プロセス・パラメーター
当社の製造データに基づいている:- 5℃以内の金型温度制御
- 射出圧力の最適化
- 材料の組み合わせによるサイクルタイムの調整
よくある問題のトラブルシューティング
この業界に身を置いて何年か、私はさまざまな困難に遭遇してきた:
デラミネーション防止
層間の剥離を防ぐ:
材料選択の考慮点
- 互換性チャートをチェック
- 耐熱性の確認
- 耐薬品性試験
プロセス制御
- 射出速度をモニターする
- 冷却速度のコントロール
- 圧力を一定に保つ
品質管理対策
私たちは厳格な品質管理を行っています:
試験方法 | 測定パラメータ | 頻度 |
---|---|---|
プル・テスト | 接着強度 | すべてのバッチ |
断面分析 | インターフェース品質 | ウィークリー |
環境試験 | 長期耐久性 | 毎月 |
耐薬品性 | 素材の完全性 | プロジェクトごと |
私の経験を通して、オーバーモールドを成功させるには、材料特性と加工パラメータを深く理解する必要があることがわかりました。PTSMAKEでは、お客様に最適な結果を提供するために、材料の組み合わせデータベースと加工パラメータを継続的に更新しています。
材料の選択と加工に対するこの包括的なアプローチは、私たちのオーバーモールディング・プロジェクトにおいて、接合不良や品質問題を最小限に抑えながら、98%の成功率を達成するのに役立っています。重要なのは、単に適合する材料を選択するだけでなく、それらを正しく加工する方法を理解することです。
2K射出成形ではどのような材料の組み合わせが可能か?
射出成形に15年以上携わってきて、私は数え切れないほどの顧客が2Kプロジェクトで正しい材料の組み合わせを選ぶのに苦労しているのを見てきました。実際に何が効果的なのかをお話ししましょう。
2成分(2K)射出成形は、硬質プラスチックと軟質プラスチックのような特定の材料の組み合わせや、多色の硬質材料の組み合わせを可能にします。一般的な組み合わせとしては、ABSとTPE、PCとABS、その他様々な相性の良い熱可塑性プラスチックがあり、これらは強い化学結合を形成します。
一般的な適合材料の組み合わせ
PTSMAKEでの日々の仕事の中で、私はこうした実績のある素材の組み合わせをクライアントに頻繁に勧めている:
ベース素材 | 適合オーバーモールド素材 | 一般的なアプリケーション |
---|---|---|
ABS | TPE/TPU | 電動工具グリップ、家電製品 |
PC | ABS | 自動車部品、電子機器ハウジング |
PA | TPE/TPU | 機械部品、スポーツ用品 |
PP | TPE/TPU | 消費者製品、医療機器 |
PBT | TPE/TPU | 電気コネクター、自動車部品 |
硬い素材と硬い素材の組み合わせ
ハードなコンビネーションを扱うとき、私はこれらの組み合わせが特に効果的だと感じている:
PC/ABSコンビネーション
- 優れた機械的特性
- 高い耐衝撃性
- 良好な耐薬品性
- 自動車およびエレクトロニクス産業で一般的
PA/PBTコンビネーション
- 優れた強度特性
- 優れた寸法安定性
- 耐熱性の向上
- 機械部品に広く使用
ソフトとハードの組み合わせ
何百ものプロジェクトに携わってきた経験から、これらの組み合わせは最高の結果をもたらす:
ABS/TPE 構成
- 強力な接着強度
- 優れた表面仕上げ
- ソフト・コンポーネントの優れた柔軟性
- 人間工学に基づいた用途に最適
PC/TPUセットアップ
- 高い耐久性
- 優れた耐衝撃性
- 優れた摩耗特性
- 屋外での使用に最適
化学結合に関する考察
長年の経験から、2K成形の成功は適切な化学結合に大きく依存していることを学んだ:
素材適合性
- 分子構造アライメント
- 似たような融解温度
- 適合する化学的性質
処理パラメーター
- 溶融温度制御
- 射出圧力の最適化
- 冷却時間管理
デザイン最適化戦略
私がこれまでのキャリアで培ってきた主な戦略を紹介しよう:
インターフェース・デザイン
- 接触面積の最大化
- メカニカル・インターロックを作る
- 適切なマテリアルフローの確保
部品形状
- 収縮率を考慮する
- 熱膨張差を考慮した計画
- 適切な肉厚の遷移を設計する
品質管理対策
PTSMAKEでは、これらの重要な品質チェックを実施しています:
フィジカル・テスト
- 接着強度の評価
- 耐衝撃試験
- 環境ストレステスト
目視検査
- 表面仕上げの品質
- 色の一貫性
- 部品寸法の検証
産業別アプリケーション
さまざまな分野で、特定の材料の組み合わせが必要とされる:
自動車産業
- 内装部品用PC/ABS
- 外装トリム用PA/TPE
- 機能部品用PBT/TPU
コンシューマー・エレクトロニクス
- ハンドヘルド機器用ABS/TPE
- ハウジング用PC/ABS
- 保護部品用PA/TPE
医療機器
- 人間工学に基づいたハンドル用PP/TPE
- 機器ハウジング用PC/TPU
- デバイス部品用PBT/TPE
私は2K射出成形の豊富な経験を通じて、材料の組み合わせをうまく選択するには、以下のことを慎重に考慮する必要があることを学んだ:
- 最終用途の要件
- 環境条件
- 製造上の制約
- コスト
- 規制遵守
2K射出成形を成功させる鍵は、材料特性だけでなく、これらの材料が成形プロセスでどのように相互作用するかを理解することにあります。PTSMAKEでは、このような材料の組み合わせを最適化することで、お客様の特定の用途に最適な結果を得るための幅広い専門知識を培ってきました。
オーバーモールドの設計上の重要な考慮点とは?
PTSMAKEに15年以上勤務する中で、私は設計上の配慮不足が原因で失敗したオーバーモールディング・プロジェクトを数え切れないほど見てきました。最近のあるプロジェクトは、成功は最初の設計計画の細部にあることを教えてくれました。
オーバーモールドの設計を成功させるには、抜き勾配の角度、材料の厚さの均一性、収縮率に注意を払う必要があります。重要なのは、基材とオーバーモールド部品の材料適合性を確保しながら、適切な機械的インターロックを作り出すことです。
必須ドラフト角度と肉厚
何千ものオーバーモールド・プロジェクトに携わり、私は適切な抜き勾配が非常に重要であることを学びました。私は、ほとんどの用途で最低1~2°の抜き勾配を推奨していますが、複雑な形状では5°まで必要な場合もあります。適切な抜き勾配は、次のことを保証します:
- 金型からの部品取り出しが容易
- 工具の摩耗を低減
- 安定した部品品質
- 生産コストの低減
肉厚の均一性も同様に重要です。私は常に、基材とオーバーモールド材の肉厚比を一定に保つようクライアントにアドバイスしていますが、通常は1:1から1:3の間です。
材料の選択と収縮率管理
一般的な素材の組み合わせと収縮率の内訳は以下の通り:
基板材料 | オーバーモールド素材 | 標準的な収縮率 | 互換性評価 |
---|---|---|---|
ABS | ティーピーイー | 0.004-0.006 in/in | 素晴らしい |
PC | TPU | 0.005-0.007 in/in | 非常に良い |
PP | ティーピーイー | 0.015-0.025 in/in | グッド |
ナイロン | ティーピーブイ | 0.008-0.012 in/in | 中程度 |
PBT | LSR | 0.002-0.004 in/in | 素晴らしい |
機械的インターロック戦略
私の経験によれば、機械式インターロックを成功させるには、3つの重要な要素が必要である:
- アンダーカット - 通常は0.5~1.0mmの深さで設計します。
- 表面テクスチャリング - 深さ0.1~0.3mmのパターンを使用
- ダブテール機能 - 15~30°の角度で最適なグリップを実現
化学結合の最適化
素材の接着は耐久性にとって非常に重要です。私は最適な接着のためにこのプロセスを開発しました:
表面処理
- プラズマ治療
- 必要に応じてケミカル・プライマー
- 汚染のない清潔な表面
加工パラメーター
- 5℃以内の温度制御
- 適切な圧力設定
- 最適なサイクル時間
幾何学的デザインの制約
オーバーモールド部品を設計するとき、私は常にこのような幾何学的な制限を考慮する:
- コーナー半径 - 内側コーナーは最小0.5mm
- ゲートの位置 - 重要な特徴から少なくとも1.5倍の材料厚さ
- パーティングラインの位置 - 表面から離す
- ベントの必要条件 - 適切に空気を逃がすための深さ0.02~0.03mm
処理ウィンドウに関する考察
私の長年の経験から、これらの処理パラメーターは非常に重要だとわかった:
温度制御
- 基板材料温度
- オーバーモールド材温度
- 金型温度
圧力設定
- 射出圧力
- 圧力を保持する
- 背圧
品質管理対策
一貫した品質を保証するために、私はこれらのチェックを実施している:
目視検査
- 完全取材
- 空洞や隙間がない
- 表面仕上げの品質
身体検査
- 接着強度
- 耐衝撃性
- 環境ストレステスト
デザイン最適化のヒント
最適なデザインを実現するための、私の実績ある戦略を紹介しよう:
マテリアルフロー分析
- シミュレーション・ソフトウェアの使用
- 潜在的な問題を特定する
- ゲート位置の最適化
プロトタイプテスト
- デザインコンセプトの検証
- 機械的特性試験
- アセンブリの適合性を確認する
生産に関する考慮事項
- 工具メンテナンスアクセス
- サイクルタイムの最適化
- 費用対効果の高い製造
オーバーモールド設計の成功は、これらの重要な考慮事項を理解し、実行することにかかっています。PTSMAKEでの経験を通じて、設計の初期段階でこれらの細部に注意を払うことで、生産時にコストのかかる問題を防ぎ、顧客の期待以上の高品質で耐久性のある部品を確保できることを学びました。
オーバーモールド成形を成功させるには、単に設計ルールに従うだけでなく、これらの要素がどのように組み合わさって優れた製品を生み出すのかを理解する必要があることを忘れないでください。私が説明した各側面を注意深く考慮することで、機能性と価値の両方を提供するオーバーモールド部品を設計するための十分な準備が整います。
2K射出成形における設計上の留意点とは?
ある2K成形品が失敗する一方で、ある2K成形品が成功するのはなぜか、不思議に思ったことはありませんか?射出成形に15年以上携わってきた私は、適切な設計がいかにプロジェクトを左右するかを見てきました。
2液(2K)射出成形では、材料適合性、部品形状、ゲート位置、金型設計を慎重に検討する必要があります。成功するかどうかは、これらの重要な要素を理解し、最初から適切な設計戦略を実行するかどうかにかかっています。
材料適合性の考慮
PTSMAKEで数え切れないほどの2Kプロジェクトに携わってきた経験から、2K成形を成功させる基本は材料の選択です。2つの材料が持っていなければなりません:
- 適合融解温度
- 同様の収縮率
- 良好な接着性
- 化学的適合性
以下は、私が長年のテストを通じて作成した詳細な互換性表である:
素材1 | 素材2 | 互換性レベル | 一般的なアプリケーション |
---|---|---|---|
PC | ティーピーイー | 素晴らしい | 家電製品 |
ABS | ティーピーイー | 非常に良い | 自動車部品 |
PA | ティーピーイー | グッド | ツールハンドル |
PP | ティーピーイー | フェア | 消費財 |
POM | ティーピーイー | 貧しい | 推奨しない |
インターロッキングの設計ガイドライン
インターロッキングをデザインする際、私はいつもこれらの重要なポイントをクライアントに強調する:
- 材料間の最小肉厚比は1:1.5とする。
- インターフェイス部分の鋭角を避ける
- 適切な機械的インターロックの設計
- 素材間に十分な重なりを持たせる
ゲートの位置と流れの分析
私の豊富な経験から、2K成形を成功させるには、適切なゲートの位置が重要です。お勧めは
一次材料ゲートの位置:
- ゲートを厚く配置する
- バランスの取れた流路を維持する
- 溶接線の位置を考慮する
副次的な素材への配慮:
- 窩洞への完全な充填
- 圧力損失の最小化
- 材料の粘度の違いを考慮する
部品排出戦略
PTSMAKEでは、部品の排出を成功させるための具体的なガイドラインを開発しました:
ドラフトの角度
- 主材料:最低1.5度
- 副資材:最低2度
表面の質感を考慮する:
- 平滑面:ドラフト角度を1°上げる
- テクスチャー表面:ドラフト角度を2°増加
サイクルタイムの最適化
効率的なサイクルタイムを実現するために、私は常に次のことに重点を置いている:
温度調節:
- 冷却チャンネルレイアウトの最適化
- 素材間の冷却バランス
- インターフェース温度の監視
プロセスパラメーター:
- 射出速度の調整
- 保持圧力のコントロール
- 冷却時間の最適化
コスト削減戦略
何百もの2Kプロジェクトを管理してきた私の経験に基づき、コストを削減する効果的な方法をご紹介します:
デザインの最適化:
- 材料使用量の最小化
- 部品形状の簡素化
- サイクルタイムの短縮
素材の選択:
- 費用対効果の高い素材を選ぶ
- リグラインドの使用を検討する
- 材料特性の最適化
製造に関する考慮事項
2K射出成形のために設計するとき、私は常にこれらの製造面を考慮する:
金型設計:
- 適切な換気
- 効率的なランナーシステム
- バランスの取れた充填
プロセス制御:
- 温度モニタリング
- 圧力の最適化
- 品質管理対策
PTSMAKEに15年以上勤務する中で、2K射出成形を成功させるには全体的なアプローチが必要であることがわかりました。材料の選択から製造上の考慮事項まで、各側面が高品質の部品を実現するために重要な役割を果たしています。重要なのは、開発プロセスの早い段階で、これらの設計上の考慮事項に対処することです。
シミュレーションとプロトタイピングによる設計の検証は不可欠です。私たちは常に、本生産前に流動解析を行い、さまざまな材料の組み合わせをテストすることをお勧めしています。このアプローチにより、お客様のコストを最小限に抑えながら、安定した品質を実現することができました。
2K射出成形は、専門知識と細部への注意を必要とする複雑な工程であることを忘れないでください。このような設計上の注意点を守り、経験豊富なメーカーと協力することで、プロジェクト成功の可能性を最大限に高め、最適な結果を得ることができます。
あなたのプロジェクトにはどのプロセスが良いか?
次のプロジェクトで、オーバーモールド成形と2K射出成形のどちらを選ぶか悩んでいませんか?製造業に15年以上携わってきた私は、数え切れないほどのお客様がこの重要な決断をするのを助けてきました。
オーバーモールド成形と2K射出成形のどちらにも独自の利点がありますが、生産量、部品の複雑さ、材料の適合性、予算などの具体的な要因によって選択する必要があります。正しい決断をするためのガイドをさせてください。
生産量に関する考察
PTSMAKEで様々なクライアントと仕事をした経験から、生産量はしばしば考慮すべき最初の要素です。両プロセスの比較は以下の通りです:
生産量 | オーバーモールディング | 2K射出成形 |
---|---|---|
少量生産(10,000台未満) | より費用対効果の高い | 高いイニシャルコスト |
中量(10,000~100,000枚) | 中程度の効率 | 優れた効率性 |
大量(10万枚以上) | 労働集約的 | 最も費用対効果が高い |
部品複合性解析
パーツの複雑さに関して言えば、これらのプロセスには明確な違いがある:
複雑さ要因 | オーバーモールディング | 2K射出成形 |
---|---|---|
幾何学的複雑性 | 手作業による制限 | 非常に複雑な可能性 |
素材の組み合わせ | ワイドレンジが可能 | 互換性のある素材に限定 |
表面詳細 | 素晴らしい | 非常に良い |
内部機能 | 限定 | 高度な機能 |
材料要件と互換性
私の15年以上の製造経験によれば、材料の選択は極めて重要な役割を果たす:
素材の側面 | オーバーモールディング | 2K射出成形 |
---|---|---|
素材範囲 | 幅広いセレクション | 互換性のあるペアに限る |
ボンド強度 | 可変 | 素晴らしい |
耐薬品性 | 素材による | おおむね良好 |
耐熱温度 | グッド | 素晴らしい |
コスト構造の内訳
両プロセスの財務的側面について私が学んだことを紹介しよう:
コスト係数 | オーバーモールディング | 2K射出成形 |
---|---|---|
初期工具 | より低い | より高い |
部品単価 | より高い | より低い |
人件費 | より高い | より低い |
廃棄物 | 中程度 | 最小限 |
生産時間と効率
PTSMAKEにいる間に、生産効率に大きな違いがあることに気づいた:
タイムファクター | オーバーモールディング | 2K射出成形 |
---|---|---|
サイクルタイム | 長い | より短い |
セットアップ時間 | より短い | 長い |
交代時間 | 中程度 | 長い |
総合効率 | 中程度 | 高い |
品質と一貫性
品質管理は非常に重要であり、私が観察したところでは以下のようなことがあった:
品質係数 | オーバーモールディング | 2K射出成形 |
---|---|---|
パーツの一貫性 | グッド | 素晴らしい |
不良率 | より高い | より低い |
ボンド強度 | 可変 | 一貫性 |
表面仕上げ | 素晴らしい | 非常に良い |
デザインの柔軟性
様々なプロジェクトに携わってきた経験から言うと:
設計係数 | オーバーモールディング | 2K射出成形 |
---|---|---|
デザインの変更 | よりフレキシブルに | 柔軟性が低い |
素材の組み合わせ | その他のオプション | 限られたオプション |
ジオメトリーの自由 | 中程度 | 高い |
プロトタイプ・オプション | より良い | 限定 |
環境への影響
持続可能性はますます重要になっている:
環境要因 | オーバーモールディング | 2K射出成形 |
---|---|---|
廃棄物 | もっと見る | より少ない |
エネルギー消費 | より高い | より低い |
リサイクル性 | 可変 | より良い |
プロセス・エミッション | より高い | より低い |
決断を下す
私の豊富な経験に基づき、簡略化した意思決定の枠組みを紹介しよう:
オーバーモールドはこんなときに選ぶ
- 素材の組み合わせに最大限の柔軟性が必要
- 生産量が少ない
- 頻繁なデザイン変更が必要
- 初期金型の予算は限られている
2K射出成形を選択する場合
- 生産量が多い
- 部品の一貫性が重要
- サイクルタイムの短縮が必要
- 長期的なコスト効率を優先
私は最近、あるクライアントの医療機器部品について、これらのプロセスのどちらかを選択する手助けをした。彼らは当初、初期コストの低さからオーバーモールドに傾いた。しかし、年間50万個の生産量を分析した結果、2K射出成形の方が部品単価を40%削減でき、一貫性も向上するため、初期金型費用は高くなるものの、より良い選択であると判断しました。
万能のソリューションは存在しないことを忘れないでください。PTSMAKEでは、各プロジェクトを個別に評価し、すべての要素を考慮して、お客様の特定のニーズに最適なプロセスを提案します。
オーバーモールドと2K射出成形の将来動向?
射出成形に15年以上携わってきた製造の専門家として、私は劇的な変化を見てきました。しかし、次に来るものは、オーバーモールドと2K成形工程についての考え方を一変させるだろう。
オーバーモールディングと2K射出成形の未来は、統合センサー、持続可能な材料、AIによるプロセスの最適化など、スマート製造へと向かっている。これらの進歩は、環境への影響を低減しながら、より速い生産時間とより複雑な設計を可能にします。
持続可能な素材革新
PTSMAKEでの経験では、素材の革新は急速に変化している。ほんの数年前には想像もできなかったような新たな発展が見られます:
- 再生可能資源からのバイオベースポリマー
- 特性を向上させたリサイクル素材
- 自己修復性ポリマーによる製品寿命の延長
- 環境変化に対応するスマート素材
私たちのチームは、いくつかの持続可能な新素材のテストに成功し、性能と環境影響の両方で有望な結果を示しています。
スマート・マニュファクチャリングの統合
スマート・テクノロジーの統合は、従来の成形工程に変革をもたらしつつある:
テクノロジー | 現在のアプリケーション | 将来の可能性 |
---|---|---|
IoTセンサー | プロセス監視 | 予知保全 |
AIシステム | 品質管理 | 自律走行 |
デジタル・ツインズ | デザインの最適化 | リアルタイム調整 |
クラウド・コンピューティング | データ収集 | プロセスの完全自動化 |
金型設計の進化
現代の金型設計はより洗練されてきている:
- コンフォーマル・クーリング・チャンネル
- トポロジー最適化構造
- 3Dプリント金型インサート
- ダイナミックベントシステム
私は個人的に、これらの進歩が部品の品質を向上させながら、サイクルタイムを35%短縮したプロジェクトを監督してきました。
インダストリー4.0の導入
インダストリー4.0の原則の統合は、私たちのアプローチを再構築している:
- リアルタイムプロセス監視
- 自動品質管理システム
- デジタル・ワークフロー管理
- 予知保全スケジュール
ハイブリッド製造ソリューション
PTSMAKEでは、伝統的な技術と新しい技術の組み合わせを模索している:
- 添加剤+射出成形
- インモールド・アセンブリ・ソリューション
- 複数の素材の組み合わせ
- ポスト処理の自動化
強化された設計能力
新しいデザインの可能性が生まれている:
- 複雑な形状
- 統合エレクトロニクス
- 可変材料特性
- マイクロフィーチャー成形
環境に優しいプロセス革新
持続可能性は、成形事業の中心になりつつある:
- エネルギー効率の高いシステム
- クローズド・ループのマテリアルリサイクル
- 節水方法
- 廃棄物削減戦略
昨年、私たちの施設では、こうした工夫によってエネルギー消費量を25%削減しました。
生産速度の最適化
いくつかの要因が、より速い生産を促している:
ファクター | インパクト | 実施スケジュール |
---|---|---|
AIによるサイクルの最適化 | 30%高速化 | 1-2年 |
高度な冷却システム | 40%リダクション | 6-12ヶ月 |
自動部品ハンドリング | 50%の効率向上 | 3-6ヶ月 |
スマートなマテリアルフローコントロール | 20%改良 | 1年 |
品質管理の向上
現代の品質管理は進化している:
- インモールドセンサー
- コンピュータ・ビジョン・システム
- AIによる欠陥検出
- リアルタイムプロセス調整
コスト効率の改善
新しい技術によって、生産コストはより効率的になっている:
- 材料廃棄の削減
- エネルギー消費の低減
- 人件費の削減
- 最低限の品質問題
これらの改善により、ROIの期間が24ヶ月からわずか12ヶ月に短縮された。
業界特有の適応
さまざまなセクターが独自のイノベーションを推進している:
- メディカルクリーンルーム統合
- 自動車軽量化ソリューション
- エレクトロニクスEMIシールド
- 航空宇宙高性能材料
様々な業界と仕事をしてきて、私は各分野が異なる方向にテクノロジーを押し進め、イノベーションの豊かなエコシステムを作り出していることに気づいた。
これらのトレンドは、この業界で15年以上働いてきた私の見解と、PTSMAKEでの継続的な取り組みを表しています。オーバーモールドと2K射出成形の未来は、効率、持続可能性、能力の継続的な改善により、明るいものとなるでしょう。成功の鍵は、品質と顧客のニーズに焦点を当てながら、適応性を維持し、これらの新技術を受け入れることでしょう。
次の10年は、さらに劇的な変化をもたらすと私は信じています。そして、今準備をする企業は、これらの進歩から利益を得るのに最も有利な立場になるでしょう。PTSMAKEでは、すでにこれらのイノベーションの多くを導入しており、製造技術の最前線にいることを確実にしています。