標準的なプラスチックでは対応できないような要求の厳しい用途で、適切な材料を見つけるのに苦労していませんか?多くのエンジニアは、部品が極端な温度、化学物質、機械的ストレスに耐える必要がある場合に課題に直面します。従来のプラスチックでは耐えられず、部品の故障が頻発し、高価な交換を余儀なくされます。
PEEK加工とは、ポリエーテルエーテルケトン(PEEK)素材をCNCマシンで切断、穴あけ、成形する加工です。この高性能熱可塑性プラスチックは、480°Fまでの優れた耐熱性、優れた耐薬品性、いくつかの金属に匹敵する強度を備えています。
私は、重要な部品をPEEK加工に切り替えた数え切れないほどのお客様と仕事をしてきました。その結果は、部品の長寿命化、過酷な環境下での性能向上、メンテナンスサイクルの短縮など、自ずと明らかです。PEEKがあなたのアプリケーションのソリューションになるかどうか疑問に思っている方は、精密製造においてこの材料を非常に価値のあるものにしているユニークな特性と加工技術を発見するために読み続けてください。
PEEKはデルリンよりも機械加工に適しているか?
重要なエンジニアリング・プロジェクトで、PEEKとデルリンの間で迷い、材料選択のジレンマに陥ったことはありませんか?性能が重要で失敗が許されない場合、間違ったプラスチックを選択すると、早期摩耗、機器のダウンタイム、コストのかかる再設計につながる可能性があります。
PEEKが優れた耐熱性(480°Fまで)、卓越した化学的安定性、高い強度を提供する一方で、デルリン(POM)はより優れた加工性、寸法安定性、低コストを提供します。より良い」選択は、特定の用途要件と予算の制約に完全に依存します。
PEEKとデルリンを理解する:基本的な違い
この2つの高性能エンジニアリングプラスチックを比較する際には、その基本的な組成と特性を理解することが重要です。PEEK(ポリエーテルエーテルケトン)は半結晶性の熱可塑性プラスチックで、熱劣化に対する卓越した耐性を備えています。一方、デルリン(ポリオキシメチレンまたはPOM)はアセタールホモポリマーで、優れた寸法安定性で知られています。
材料特性の比較
これらの材料の物理的・機械的特性は、加工特性や最終用途の性能に大きく影響する。
プロパティ | 覗き見 | デルリン(POM) |
---|---|---|
熱偏向温度 | 315°F (157°C) | 125°C |
引張強度 | 14,500 psi | 10,000 psi |
耐薬品性 | 優れている(ほとんどの酸、塩基に耐性がある) | 良好(強酸に弱い) |
耐摩耗性 | スーペリア | 非常に良い |
コスト係数 | デルリンより4-5倍高い | 中程度 |
密度 | 1.32 g/cm³ | 1.41 g/cm³ |
加工特性:工具の性能
PTSMAKEでの経験から、これらの材料のどちらかを選択する場合、加工性が決め手になることが多いことがわかりました。デルリンは一般的に、PEEKよりも加工が予測しやすく、少ない労力でより滑らかな表面仕上げができます。
工具摩耗と切削パラメータ
PEEKは切削工具に対する摩耗性が高いため、より頻繁な工具交換が必要になります。PEEKを加工する場合、熱の蓄積を最小限に抑えるため、通常、デルリンと比較して切削速度を約15-20%低下させます。PEEKは熱伝導率が低いため、切削部に熱が集中し、次のような問題を引き起こす可能性があるからです。 熱変形1 適切に管理されなければ
一方、デルリンは機械加工時の寸法安定性に優れ、高速加工が可能です。工具の摩耗が少なく、一般に特殊な加工技術を必要としない。
表面仕上げに関する考慮事項
デルリンの利点の一つは、標準的な機械加工パラメータで優れた表面仕上げを達成できることである。PEEKは、同等の表面品質を達成するために、しばしば追加の研磨工程を必要とします。
エンジニアリング用途の費用便益分析
これらの材料間のコスト差は相当なものになります。PEEKは通常デルリンより4~5倍高く、その優れた特性が投資を正当化するかどうかを評価することが重要です。
PEEKがプレミアム価格を正当化するとき
私は、PEEKを使用したアプリケーションを推奨している:
- 極端な動作温度(250°F以上)
- 過酷な化学環境
- 高温下での高い機械的負荷
- 生体適合性または難燃性を必要とする医療または航空宇宙用途
デルリンがより良い選択である場合
デルリンは経済的に理にかなっている:
- 動作温度は180°F以下を維持
- 化学物質への暴露は中程度の溶剤に限られる
- コスト感覚が大きな要因
- 優れた寸法安定性と加工精度が要求される部品
- 生産量が多いため、材料費が重要な要素となる
業界特有の考慮事項
業界によって優先される材料特性は異なります。当社が多くの部品を供給してきた航空宇宙分野では、PEEKの難燃性と卓越した強度対重量比が、しばしばその高コストを正当化します。自動車用途では、リーズナブルなコストと優れた機械的特性を併せ持つデルリンに軍配が上がることが多い。
医療および食品加工用途
医療機器では、PEEKの生体適合性と耐滅菌性が、割高なコストにもかかわらず貴重な存在となっている。食品加工機器では、高温を伴わない限り、デルリンのFDAコンプライアンスと低コストが、しばしばデルリンを好ましい選択にしている。
産業機械部品
産業用途では、使用条件によって決定されることがよくあります。中程度の条件下で使用されるギア、ベアリング、摩耗部品はデルリンで優れた性能を発揮しますが、極端な条件にさらされる部品はPEEKの優れた特性の恩恵を受けます。
用途に合わせた正しい選択
PEEKとデルリンのどちらを選択するかは、お客様の特定の使用条件を徹底的に分析して決定する必要があります。PTSMAKEでは、以下のことを考慮します:
- 最高使用温度
- 化学物質暴露プロファイル
- 機械的負荷要件
- 予算の制約
- 期待耐用年数
各素材の特性に対してこれらの要素を慎重に評価することで、特定の用途における性能と費用対効果のバランスを考慮した、十分な情報に基づいた決定を下すことができます。
アセタールとPEEKの違いは?
重要なエンジニアリング部品について、アセタールかPEEKかの選択に悩んだことはありませんか?プロジェクトの成功が材料選択に左右される場合、選択を誤ると、適切な材料知識があれば回避できたはずの早期故障や予期せぬダウンタイム、予算オーバーの再設計につながる可能性があります。
アセタール(POM)とPEEKは、主にその性能特性とコストにおいて異なる。PEEKは優れた耐熱性(480°F vs 180°F)、優れた耐薬品性、より高い強度を提供する一方、アセタールは優れた加工性、寸法安定性を提供し、コストが大幅に低いため、それほど要求の厳しくない用途に最適である。
アセタールとPEEKの主な違い
この2つのエンジニアリング・プラスチックの基本的な違いを理解することは、プロジェクトにおいて十分な情報を得た上で意思決定を行う上で非常に重要です。どちらの材料も、精密製造の現場で使用される選択肢として確立されていますが、固有の特性により、その用途は明確に異なります。
素材構成と構造
一般にデルリン(ホモポリマーの場合)という商品名で、あるいはポリオキシメチレン(POM)という化学名で知られるアセタールは、-CH₂O-基を繰り返す高度な結晶構造を特徴とする。この構造により、優れた寸法安定性と機械加工性が得られる。
一方、PEEK(ポリエーテルエーテルケトン)はポリアリールエーテルケトンに属し、エーテル結合とケトン結合でつながった芳香環を持つ。この分子構造が、卓越した熱安定性と耐薬品性を生み出している。
性能特性の比較
これらの素材の性能の違いにより、それぞれの用途に適している:
プロパティ | アセタール(POM) | 覗き見 | 最適 |
---|---|---|---|
耐熱性 | 連続180°F (82°C) | 連続 480°F (250°C) | 覗き見 |
耐薬品性 | 良好(強酸を除く) | 優れている(ほとんどの化学薬品に耐性がある) | 覗き見 |
引張強度 | 8,800-10,000 psi | 14,500~16,000 psi | 覗き見 |
耐摩耗性 | 非常に良い | 素晴らしい | 覗き見 |
加工性 | 素晴らしい | 良い(専門的な技術が必要) | アセタール |
コスト係数 | ベースリファレンス(1×) | アセタールより4~7倍高い | アセタール |
水分吸収 | 0.2-0.25% | 0.1-0.15% | 覗き見 |
コスト・ベネフィット分析
PTSMAKEで顧客と長年仕事をする中で、コストを考慮することで、最初の材料選択プロセスを進めることが多いことに気づきました。アセタールはPEEKよりもはるかに経済的であるため、極端な条件が存在しない場合は、デフォルトの選択となります。
PEEKのプレミアム価格は、その優れた性能能力を反映している。追加投資が正当化されるかどうかを評価する際には、以下の要素を考慮してください:
- 動作温度要件
- 化学物質暴露プロファイル
- 機械的ストレスレベル
- 期待耐用年数
- 部品の故障に伴うダウンタイム・コスト
機械加工の考慮事項
工具寿命と切削パラメータ
アセタールはその卓越した加工性で有名である。きれいに切断し、厳しい公差を保持し、最小限の労力で優れた表面仕上げを実現します。標準的な超硬工具はよく機能し、この材料は過度の工具摩耗を引き起こさない。
PEEKは、機械加工中にさらに多くの問題を引き起こす。耐熱性が高いため、加工中の熱放散が悪く、熱処理が必要となります:
- 切断速度の低下(通常、アセタールより20-30%遅い)
- より頻繁な工具交換
- 熱の蓄積に細心の注意を払う
- 特殊な冷却技術
PTSMAKEでは、具体的に次のようなものを開発した。 熱管理プロトコル2 寸法精度を確保し、切削加工中の材料劣化を防ぐためです。
寸法安定性
アセタールは機械加工後の寸法安定性に優れ、反りや応力緩和は最小限に抑えられる。そのため、公差の厳しい精密部品に特に適しています。
PEEKも寸法安定性に優れていますが、機械加工後の内部応力を緩和するために、より慎重なアニール工程が必要です。適切な熱処理を行わないと、PEEK部品は、特に高精度の用途では、時間の経過とともに寸法がわずかに変化することがあります。
アプリケーション固有の推奨事項
自動車・運輸
温度が中程度(180°F以下)に保たれる自動車用途では、アセタールはしばしば最高の価値を提供する。一般的な用途は以下の通り:
- 燃料系統部品
- ドアロック機構
- インテリア・トリム・クリップとファスナー
- 非重要エリアのベアリング表面
フード下の部品や排気装置付近の部品のような高温ゾーンでは、PEEKの熱安定性により、コストは高くなるものの、より良い選択となる。
医療・製薬
医療業界では、その生体適合性と滅菌方法に対する耐性からPEEKが採用されています。一般的に次のような用途で使用されている:
- インプラント機器
- 手術器具
- 医療用画像コンポーネント
- 実験設備
アセタールは現在でも、以下のような、それほど要求の厳しくない医療現場で使用されている:
- 使い捨て器具部品
- 実験室用試験治具
- 診断装置ハウジング
産業機器
産業機械の場合、その選択はしばしば運転条件によって決まる:
- 標準的な使用環境アセタールは、通常の条件下で、ギア、ベアリング、摩耗面に優れた価値を提供する。
- 過酷な環境:PEEKは、高温、化学薬品、または極度の機械的ストレスにさらされた場合、そのプレミアム価格を正当化します。
最適な選択をする
顧客がPTSMAKEでアセタールとPEEKのどちらを選ぶかをサポートするとき、私は体系的なアプローチを勧める:
- 部品が直面する最も過酷な条件(温度、化学物質、荷重)を特定する。
- アセタールの特性がこれらの条件に対処するのに十分かどうかを判断する。
- 特定の数量要件に対するオプション間のコスト差の計算
- 故障の影響とそれに伴うダウンタイム・コストを考慮する。
- PEEKの優れた性能が、その高価格を正当化できるかどうかを評価する。
材料の選択が万能であることはめったにない。最も重要な部品にのみPEEKを使用し、同じアセンブリ内の要求度の低い部品にはアセタールを使用するといった、ハイブリッドなアプローチが最適な場合もあります。
PTFEとPEEKの違いは?
高機能性プラスチックの海で迷子になり、重要な用途にPTFEとPEEKのどちらを選べばよいかわからなくなったことはありませんか?プロジェクトの締め切りが迫り、材料の選択が設計を左右する可能性がある場合、正しい選択をしなければならないというプレッシャーに圧倒されることがあります。
PTFEとPEEKはどちらも高性能の熱可塑性プラスチックで、明確な違いがあります。PTFEは耐薬品性に優れ、摩擦係数が0.05~0.10と極めて低く、-328°F~500°Fの範囲で使用できるが、機械的強度に劣る。PEEKは、優れた機械的特性、優れた耐摩耗性を備え、480°Fまで構造的完全性を維持する一方、より加工しやすい。
分子構造と基本的性質
PTFEとPEEKの基本的な違いは分子レベルから始まっており、様々な用途におけるそれぞれの性能特性を説明している。
化学組成
PTFE(ポリテトラフルオロエチレン)は、フッ素原子で完全に囲まれた炭素骨格を特徴としています。このユニークな構造により、PTFEは卓越した化学的不活性と低摩擦特性を実現している。炭素-フッ素結合は有機化学で最も強固な結合のひとつであり、PTFEを化学的攻撃に対して驚異的な耐性を持つものにしています。
一方、PEEK(ポリエーテルエーテルケトン)は、芳香環がエーテル結合やケトン結合でつながった、より複雑な分子構造を持つ。この芳香族骨格がPEEKに優れた機械的強度と熱安定性を与えている。
比較物件分析
プロパティ | PTFE | 覗き見 | メリット |
---|---|---|---|
最高連続使用温度 | 500°F (260°C) | 480°F (250°C) | PTFE(わずかに) |
最低使用温度 | -328°F (-200°C) | 華氏-65度(-54) | PTFE |
摩擦係数 | 0.05-0.10(どの固体よりも低い) | 0.35-0.40 | PTFE |
引張強度 | 3,000-5,000 psi | 14,000~16,000 psi | 覗き見 |
耐薬品性 | スーペリア(ユニバーサル) | 良好(強酸による制限あり) | PTFE |
加工性 | チャレンジング(柔らかく、変形しやすい) | グッド | 覗き見 |
耐摩耗性 | 悪い~中程度 | 素晴らしい | 覗き見 |
電気的特性 | 優れた絶縁体 | 良好な絶縁体 | PTFE |
コスト係数 | 中程度 | 高い(PTFEの3~4倍以上) | PTFE |
熱性能の違い
温度性能は、多くの場合、これらの材料の中から選択する際の重要な決定要素である。
耐熱性と安定性
どちらの素材も卓越した耐熱性を持つが、高温での挙動は異なる。PTFEは、最高温度までは化学的不活性と低摩擦を維持しますが、はるかに低い温度(約260°F/127℃)で機械的完全性を失い始めます。
一方、PEEKは最高温度に近い温度で機械的強度を維持する。このため、耐熱性と機械的負荷の両方を必要とする用途では、PEEKの価値が著しく高まります。
PEEKは、高温下でも構造的完全性を維持することができるため、高い価格設定に見合う価値があります。PEEKは高温下でも構造的完全性を維持できるため、高い価格設定に見合う価値があることがよくあります。
低温性能
極低温用途では、PTFEが明らかに有利です。PEEKが-65°F (-54°C)以下になると次第に脆くなるのに対し、PTFEは-328°F (-200°C)まで柔軟性と機能性を維持します。PEEKは-65°F(-54°C)を下回ると脆くなります。このため、航空宇宙、実験室、その他の超低温環境ではPTFEが最適です。
機械的強度の比較
これらの材料の機械的特性は劇的に異なるため、用途によって適性が異なる。
荷重下での構造的完全性
PTFEが3,000~5,000psiであるのに対し、PEEKは平均14,000~16,000psiの引張強度を持ち、圧倒的に優れた機械的性能を発揮します。このため、PTFEではすぐに変形したり破損してしまうような耐荷重用途にも適しています。
PTSMAKEでは、特に高温下で安定した機械的負荷を受ける構造部品にPEEKを頻繁に推奨しています。この材料の優れた耐クリープ性により、継続的な応力下でも寸法安定性を維持することができます。
耐摩耗性と摩擦
PTFEは摩擦係数が著しく低い(0.05~0.10)ため、最小限の摩擦を必要とする用途には最適の材料です。しかし、この特性は耐摩耗性の低さにもつながっており、摩耗の激しい場面では簡単に削り取られてしまう。
PEEKは、適度な摩擦係数(0.35~0.40)を維持しながら、優れた耐摩耗性を示します。他の表面に対する連続的な動きを伴う用途では、PEEKは通常PTFEよりもかなりの差で長持ちします。
PEEKを構造材料として使用し、摩擦低減が必要な部分には薄いPTFEコーティングまたはライナーを使用することで、多くのお客様が両方の長所を兼ね備えています。
耐薬品性プロファイル
どちらの素材も優れた耐薬品性を持つが、重要な違いがある。
過酷な環境への耐性
PTFEは耐薬品性の金字塔であり、ほとんどすべての化学物質(溶融アルカリ金属やフッ素のような稀な例外を除く)に対して事実上不活性です。この普遍的な耐薬品性により、PTFEは化学処理、半導体製造、実験環境において非常に貴重な存在となっている。
PEEKはほとんどの物質に対して優れた耐薬品性を示しますが、濃硫酸やその他の強酸には侵されることがあります。しかし、ほとんどの産業環境では、PEEKの耐薬品性は十分すぎるほどです。
加水分解と水分吸収
PTFEは完全に疎水性であり、長時間曝露しても本質的に吸湿しない。PEEKは耐加水分解性に優れていますが、湿度の高い環境に長時間さらされると、わずかな水分(0.1~0.3%)を吸収します。
超純水用途や、微細なコンタミネーションさえ許容できないシステムでは、機械的な制約があるにもかかわらず、PTFEが望ましい選択肢であり続けることが多い。
%[構造比較用PEEKおよびPTFE機械加工部品](
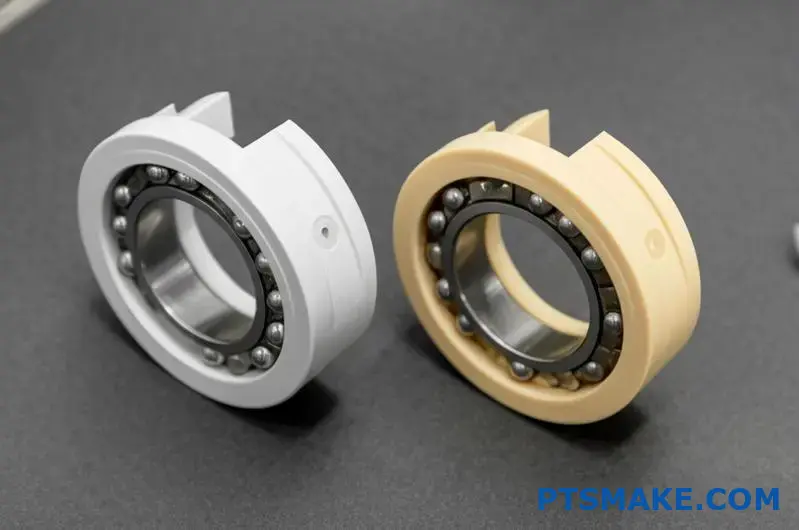
「PEEKおよびPTFEベアリング部品")
機械加工と製作に関する考慮事項
について 加工性3 これらの材料の違いは、製造コストと製造能力に大きく影響する。
機械加工の課題と解決策
PTFEは柔らかく、コールドフローを起こしやすいため、加工には独特の課題がある。加工中の変形を防ぐため、特殊な工具、遅い切削速度、慎重な固定具が必要となる。材料の破れや変形を防ぐには、鋭利な工具が不可欠です。
PEEKの機械加工は、従来のエンジニアリング・プラスチックと似ていますが、研磨性が高いため、他の多くの材料よりも工具の摩耗が早くなります。PEEKを加工する場合、一般的には超硬工具を使用し、適切な冷却技術で熱の蓄積を管理します。
製造工程の互換性
PTFEは溶融粘度が高いため、従来の射出成形は不可能である。その代わりに、圧縮成形、ラム押し出し、ビレットからのスカイビングなどの技術を用いて加工する必要があります。このため、設計の複雑さが制限され、複雑な形状の場合は製造コストが高くなる。
PEEKは射出成形や押出成形のような従来の方法で加工できるため、より複雑な形状が可能になり、大量生産時の製造コストが下がる可能性があります。このような加工の多様性により、PEEKは複雑な部品や試作品から大量生産に移行する際に優位性を発揮します。
用途別費用便益分析
これらの素材の間には大きな価格差があるため、用途に応じた価値を慎重に検討する必要がある。
バリュー・プロポジションの比較
PEEKは一般的にPTFEより3-4倍高価ですが、その優れた機械的特性と耐摩耗性は、機械的故障がコストや危険を伴うような用途において、しばしば長期的に優れた価値を提供します。
主に耐薬品性、低摩擦性、電気絶縁性を必要とする用途で、大きな機械的応力を伴わない場合、PTFEはその限界にもかかわらず、通常より優れた価値を提供する。
業界特有の選考基準
業界によって優先される材料特性は異なる:
- 化学処理:PTFEの普遍的な耐薬品性は、一般的にその機械的制限を上回る。
- 航空宇宙:PEEKは構造部品に、PTFEはシールや電気絶縁に使用されている。
- 医療用PEEKは生体適合性と構造強度からインプラント用として人気があり、PTFEはカテーテルのライニングやその他の低摩擦用途に好まれている。
- 半導体PTFEは、その卓越した純度と攻撃的な化学薬品に対する耐性により、優位を占めている。
- 自動車用PEEKの耐摩耗性と機械的特性は、機械的ストレスに直面するアンダーフード部品にとって貴重なものです。
PVDFとPEEKの違いは?
設計を左右する重要なプロジェクトで、PVDFとPEEKのどちらを選ぶかというジレンマに直面したことはありませんか?標準的なプラスチックでは十分でなく、卓越した耐薬品性や熱安定性が必要な場合、これら2つの高性能材料の間で混乱すると、コストのかかるミスや性能の低下につながる可能性があります。
PVDF(ポリフッ化ビニリデン)とPEEK(ポリエーテルエーテルケトン)は、主にその性能特性と用途が異なります。PEEKは優れた耐熱性(480°F vs 300°F)、優れた機械的強度、卓越した耐摩耗性を提供し、PVDFは優れた耐薬品性、紫外線安定性を提供し、大幅に低コストです。
PVDFとPEEKの主な違い
この2つのエンジニアリング熱可塑性プラスチックを比較する場合、その基本特性を理解することで、どちらの材料が特定の用途に最も適しているかを判断することができます。どちらの材料も高性能の選択肢と考えられていますが、それぞれ異なる環境や用途で優れた性能を発揮します。
素材構成と構造
PVDFは、二フッ化ビニリデンの繰り返し単位からなる半結晶性のフッ素樹脂である。その分子構造には炭素-フッ素結合が含まれ、PTFEのような完全フッ素化ポリマーほど包括的ではないが、優れた耐薬品性を発揮する。
PEEKはポリアリールエーテルケトンファミリーに属し、芳香環がエーテル結合とケトン結合でつながった複雑な分子構造を特徴とする。このユニークな構造により、PEEKは卓越した熱安定性と機械的強度を実現しています。
性能特性の比較
次の表は、PVDFとPEEKの主要特性の詳細な比較です:
プロパティ | PVDF | 覗き見 | 優れた素材 |
---|---|---|---|
最高連続使用温度 | 300°F (149°C) | 480°F (250°C) | 覗き見 |
機械的強度(引張) | 5,800-7,800 psi | 14,500~16,000 psi | 覗き見 |
耐薬品性 | 優れている(ほとんどの酸、塩基) | 非常に良好(強酸による制限あり) | PVDF |
耐紫外線性 | 素晴らしい | フェア~グッド | PVDF |
耐摩耗性 | グッド | 素晴らしい | 覗き見 |
摩擦係数 | 0.25-0.35 | 0.35-0.40 | PVDF |
コスト係数 | 中程度 | PVDFより2~3倍高い | PVDF |
水分吸収 | 0.03-0.04% | 0.1-0.15% | PVDF |
密度 | 1.75-1.78 g/cm³ | 1.30-1.32 g/cm³ | アプリケーション依存 |
熱性能と安定性
多くのエンジニアリング用途では、温度性能が材料選択の決め手となることが多い。
耐熱性の比較
PEEKは卓越した熱安定性を示し、連続使用において最高250°C(480°F)までの温度で機械的特性を維持します。そのため、従来のプラスチックでは破損してしまうような高温環境での用途に最適です。
PVDFは依然として高温プラスチックと見なされているが、最大連続使用温度は約300°F (149°C)と低い。この温度範囲は、多くの工業用途には十分ですが、極端な熱環境では不足します。
PTSMAKEの顧客と仕事をした経験では、プロセス温度がPVDFの能力を超える可能性のある半導体プロセス装置のような用途で、これらの材料のどちらかを選択する場合、この温度差が決め手になることがよくあります。
熱サイクル挙動
どちらの素材も熱サイクルの扱いが異なる:
- PVDFは熱サイクル中の寸法安定性は良好ですが、PEEKよりも熱膨張が大きい場合があります。
- PEEKは、熱サイクルを繰り返しても優れた寸法安定性を維持するため、さまざまな温度で厳しい公差を維持しなければならない精密部品に適しています。
耐薬品性プロファイル
耐薬品性もまた、これらの素材を区別する重要な要素である。
過酷な環境への耐性
PVDFは、以下のような広範囲の化学薬品に対して優れた耐性を発揮する:
- ほとんどの酸(濃塩酸、硫酸を含む)
- 脂肪族および芳香族炭化水素
- アルコール、塩素系溶剤
- 酸化剤
PEEKは多くの物質に対して優れた耐薬品性を示すが、濃硫酸やその他の強酸には侵されることがある。特に加水分解や蒸気滅菌に強いため、医療用途で重宝されている。
業界特有の化学物質に関する考察
業界によって優先される耐薬品性は異なる:
- 化学処理:PVDFは酸や塩素化合物に対する包括的な耐性を持つため、しばしば好まれる。
- 半導体:どちらの材料も使用されるが、特定のプロセス化学物質によって選択される。
- 石油とガスPEEKは機械的特性と耐薬品性を兼ね備えているため、ダウンホールアプリケーションに適しています。
- 医薬品:PVDFは洗浄剤や滅菌方法に対する耐性に優れているため、加工機器によく使用されています。
機械的特性と構造用途
について 機械的強度4 これらの材料の違いは、耐荷重用途への適性に大きく影響する。
耐荷重能力
PVDFが5,800~7,800psiであるのに対し、PEEKは14,500~16,000psiの引張強度を有し、機械的強度が大幅に向上しています。このため、大きな機械的負荷に耐えなければならない構造部品には、PEEKが優れています。
耐薬品性と構造的完全性の両方を必要とする用途では、PEEKはコストが高いにもかかわらず、多くの場合、特性のベストバランスを提供します。PTSMAKEでは、侵食性の化学薬品と機械的応力の両方に耐える必要がある部品にPEEKを推奨してきました。
耐摩耗性と摩擦特性
PEEKは優れた耐摩耗性を示し、ベアリング、ブッシュ、その他継続的に摩擦を受ける部品に最適です。その自己潤滑特性は、厳しい環境下で可動部品の寿命を延ばすのに役立ちます。
PVDFは、PEEKほどではありませんが、優れた耐摩耗性を発揮します。その低い摩擦係数(PEEKの0.35~0.40に対し0.25~0.35)は、耐摩耗性よりも摩擦低減が重要な低荷重摺動用途で有利に働く。
電気および熱絶縁特性
どちらの材料も、異なる用途に適する明確な電気的特性を備えている。
誘電特性
PVDFはその圧電特性で知られており、機械的応力の印加に応じて電荷を発生させることができます。このユニークな特性により、PVDFはセンサー用途で重宝されています。
PEEKは、広い温度範囲で優れた電気絶縁特性を発揮し、高温下でも絶縁耐力を維持します。このため、標準的なプラスチックでは故障してしまうような高温の電気的用途において、PEEKの価値は特に高くなります。
熱伝導率
PVDFとPEEKはどちらも金属に比べて熱伝導率が比較的低く、優れた断熱材となっている:
- PVDF: 0.17-0.19 W/m-K
- PEEK: 0.25-0.29 W/m-K
この熱伝導率の低さは、用途によって利点にも欠点にもなる。熱絶縁を必要とする部品では、どちらの素材も良好な性能を発揮しますが、PVDFの方がわずかに断熱性が優れています。
コスト検討と価値分析
これらの素材には大きな価格差があるため、費用対効果の分析が不可欠となる。
初期材料費
PEEKの価格は通常PVDFの2~3倍であり、要求性能に見合うだけの実質的なコスト・プレミアムが必要です。この価格差は、PEEKのより複雑な製造工程と高い原材料費に起因しています。
生涯価値評価
総所有コストを評価する際には、初期の材料費以外にもいくつかの要素を考慮する必要がある:
- 対象環境での期待耐用年数
- 交換頻度と関連するダウンタイム・コスト
- 設置およびメンテナンスの要件
- 安全性と信頼性への懸念
多くの高温または高負荷の用途では、PEEKの優れた性能は、耐用年数の延長と信頼性の向上により、初期コストの高さを正当化します。PVDFの性能の範囲内の用途では、低コストの材料の方が総合的な価値が高いことがよくあります。
加工と製造に関する考察
製造能力と限界も、材料の選択に影響を与える。
加工の違い
これらの材料をPTSMAKEで加工した場合、大きな違いが見られました:
- PVDFの加工は比較的良好だが、溶融やカジリを防ぐには、鋭い工具と適切な速度が必要だ。
- PEEKは研磨性が高く、熱伝導率が低いため、切削加工中に熱がこもりやすく、加工が難しい。
精密部品の場合、PEEKは一般的に機械加工時に厳しい公差を保持するが、より専門的な技術と工具を必要とするため、製造コストが上昇する可能性がある。
製造方法の互換性
どちらの素材も複数の製造方法で加工できる:
- PVDF:射出成形、押出成形、圧縮成形、機械加工
- PEEK:射出成形、押出成形、圧縮成形、機械加工、3Dプリンティング(専用設備)
PVDFは低温での加工の柔軟性がやや高いが、PEEKは加工温度が高いものの、高度な製造技術によって複雑な形状の選択肢が増える。
アプリケーション別選考ガイドライン
業界によって優先される材料特性が異なるため、材料の好みもさまざまだ。
半導体産業
半導体製造では、どちらの材料も用途があるが、分野は異なる:
- PVDF:超純水システム、薬液供給部品、ろ過装置によく使用される。
- PEEK:ウェハーハンドリング装置やプロセスチャンバー部品など、高温にさらされる部品に適している。
化学処理装置
化学処理用:
- PVDF:適度な温度で腐食性の化学物質を扱うポンプ、バルブ、継手、タンクに最適。
- PEEK:耐薬品性、高温能力、機械的強度の両方を必要とする部品により適している。
医療・医薬用途
医療用途では:
- PVDF:濾過膜、縫合糸、一部の移植器具によく使用される。
- PEEK:生体適合性、放射線透過性、および骨に類似した機械的特性により、移植器具、特に整形外科用途に好まれる。
PTSMAKEでPVDFとPEEKのどちらを選ぶかをお客様にお手伝いする際には、まず最も重要な環境要因(温度、化学薬品、機械的負荷)を評価し、次にコスト、加工要件、入手可能性などの二次的要因を考慮する体系的なアプローチをお勧めします。
<
PEEKはポリエチレン?
似たような名前のエンジニアリングプラスチックが並んでいて、混乱したことはありませんか?重要な用途に使用する材料を選択する際に、このような混乱が生じると、ある高性能プラスチックを誤って別のプラスチックに置き換えた場合、コストのかかるミスや性能の失敗、資源の浪費につながる可能性があります。
PEEK(ポリエーテルエーテルケトン)はポリエチレンではありません。PEEKは骨格にケトン基を持つ芳香族ポリエーテルであり、卓越した耐熱性(480°Fまで)、優れた耐薬品性、ポリエチレン材料をはるかに上回る優れた機械的特性を持つ半結晶性の熱可塑性プラスチックです。
化学構造と分類の違い
PEEKとポリエチレンの基本的な違いは、分子レベルから始まります。このような構造上の違いが、実用的な用途においてこれらの材料がこれほど異なる挙動を示す理由を説明しています。
分子骨格の比較
PEEKは、ベンゼン環間にエーテル結合とケトン結合を持つ複雑な芳香族骨格構造を特徴とする。この分子構造が、PEEKに優れた熱安定性と機械的強度を与えている。芳香環は剛性を、エーテル結合は柔軟性をもたらします。
対照的に、ポリエチレンは最も単純なポリマー構造のひとつで、水素原子が結合した炭素原子の直鎖だけである。この単純な構造はさまざまな形(HDPE、LDPE、UHMWPE)で存在するが、いずれもPEEKに卓越した特性を与えている芳香族成分や官能基を欠いている。
この基本的な構造の違いは、PEEKがポリエチレンとは全く異なるポリマーファミリーに属することを意味する。ポリエチレンがポリオレフィンに分類されるのに対し、PEEKは高性能熱可塑性プラスチックのポリアリールエーテルケトン(PAEK)ファミリーに属します。
プロパティの主な違い
分子構造の違いは、劇的なパフォーマンスの違いにつながる:
プロパティ | 覗き見 | ポリエチレン(HDPE) | 差異係数 |
---|---|---|---|
最高連続使用温度 | 480°F (250°C) | 180°F(82度) | PEEKは2.7倍高い |
引張強度 | 14,500 psi | 4,500 psi | PEEKは3.2倍の強度 |
耐薬品性 | 優れている(ほとんどの化学薬品に耐える) | 良好(芳香族溶剤に弱い) | PEEKはより広い耐性を提供する |
コスト | 高い | 低い | PEEKのコストは15~20倍 |
密度 | 1.32 g/cm³ | 0.95 g/cm³ | PEEKは39%密度が高い |
硬度(ショアD) | 85-90 | 60-70 | PEEKはかなり硬い |
製造工程の違い
PEEKとポリエチレンの製造方法は、それぞれの分子構造と性能特性の違いを反映している。
PEEK製造プロセス
PEEKは、求核芳香族置換重合を含む複雑な工程を経て製造される。これには精密な温度制御と特殊な触媒が必要である。モノマー材料はエチレンよりもかなり高価であり、PEEKのコスト上昇の一因となっている。
PTSMAKEでは、PEEKコンポーネントを加工する際、この素材特有の特性を考慮する必要があります。熱伝導率が低いため、局所的な熱劣化を防ぐには、加工中の熱管理が重要になります。
ポリエチレン製造
ポリエチレンは、所望の密度と枝分かれに応じ、様々な触媒を用いたエチレンの付加重合によって製造される。この比較的簡単なプロセスは、PEEKの製造よりも低い温度と圧力で実施することができ、特に低密度の品種に適しています。
極限環境における性能
高温性能
これらの素材の最も大きな違いの一つは、熱安定性である:
- PEEKは480°F(250°C)までの連続使用で機械的特性を維持し、さらに高温への短時間の暴露にも耐える。
- ポリエチレンは82°C(180°F)付近で軟化し始め、それ以下の温度では機械的強度のほとんどを失う。
当初はコスト面でポリエチレンを選択していたにもかかわらず、使用温度が想定を超えると急速に不具合が発生した事例を数多く見てきました。ある航空宇宙用途では、熱源に近い部品をポリエチレンからPEEKに切り替えたところ、初期の材料費が高くなったにもかかわらず、耐用年数が数ヶ月から数年に延びました。
耐薬品性の比較
どちらの素材も耐薬品性に優れているが、PEEKは過酷な化学薬品に対してより幅広い保護機能を備えている:
- PEEKは、ほとんどの酸、塩基、炭化水素、有機溶剤に耐性がある。
- ポリエチレンは酸や塩基に対して優れた耐性を持つが、芳香族炭化水素や一部の酸化剤に侵されることがある。
この違いは、複数の化学薬品にさらされることが多い化学処理装置、半導体製造、医療用途で重要になる。
アプリケーションの適合性
航空宇宙および防衛用途
航空宇宙用途では、軽量、難燃性、熱安定性を兼ね備えたPEEKは、次のような部品に重宝されている:
- 難燃性を必要とする内装部品
- 電気コネクターおよび絶縁体
- 高温ゾーンの構造部品
- 耐薬品性が要求される燃料系統部品
ポリエチレンは、熱安定性と機械的特性が限られているため、航空宇宙用途の厳しい要件を満たすことはほとんどない。
医療およびヘルスケア用途
これらの材料の生体適合性プロファイルも大きく異なる:
- PEEKは生体適合性があり、インプラント器具、手術器具、滅菌が必要な医療機器に使用されている。
- 医療グレードのポリエチレン(主にUHMWPE)は、人工関節などの一部のインプラントに使用されているが、繰り返し蒸気滅菌を行うためのPEEKの耐熱性が不足している。
産業機器部品
産業機械の場合、これらの材料の選択は通常、運転条件によって決まる:
- PEEKは、高温環境、優れた耐摩耗性を必要とする用途、または過酷な化学薬品にさらされる用途に優れています。
- ポリエチレンは、機械的要求が中程度の常温用途で十分な性能を発揮し、安価で加工が容易なため、しばしば選択される。
費用対効果の検討
これらの材料の価格差は大きく、PEEKは通常、高密度ポリエチレンの15~20倍もします。この大きなコスト差は、材料の選択が以下の徹底的な分析に基づいて行われるべきであることを意味します:
- 必要動作温度範囲
- 化学物質暴露プロファイル
- 機械的負荷要件
- 期待耐用年数
- 失敗の結果
ポリエチレンの能力範囲内の用途では、PEEKの方が低コストであるため、経済的な選択肢となります。しかし、ポリエチレンの限界を超える性能が要求される場合、PEEKの優れた特性は、耐用年数の延長、信頼性の向上、メンテナンスコストの削減を通じて、そのプレミアム価格を容易に正当化することができます。
加工と処理の違い
PTSMAKEでは、これらの材料の加工に大きな違いがあることを発見しました:
- PEEKはその特性上、特殊な切削パラメータを必要とする。 熱挙動5 加工中も厳しい公差を維持し、優れた表面仕上げを実現する
- ポリエチレンは加工しやすいが、切削力が加わると変形する傾向があり、厳しい公差を維持するのが難しくなる。
このような加工の違いを理解することは、製造性と精度を追求した部品を設計する際に不可欠である。
PEEKの欠点と利点は?
重要な用途において、PEEKがそのプレミアム価格に見合うかどうか判断に迷ったことはありませんか?プロジェクトの成功が材料選択に左右される場合、高価な高性能プラスチックと経済的な代替品のどちらを選ぶかは、信頼性と寿命に実際に影響を与える厳しいバランス感覚を必要とします。
PEEKは、卓越した耐熱性(480°Fまで)、卓越した耐薬品性、優れた機械的強度、優れた摩耗特性などの優れた利点を備えています。しかし、これらの利点は、高コスト(標準的なエンジニアリング・プラスチックの5~10倍)、困難な機械加工性、限られたカラー・オプション、耐紫外線性の低さなどの重大な欠点を伴います。
PEEKの優れた特性を理解する
PEEK(ポリエーテルエーテルケトン)は、最も要求の厳しい用途に適しているユニークな特性の組み合わせにより、エンジニアリングプラスチックの中でも際立っています。数え切れないほどの精密部品に材料を指定してきた者として、私はPEEKの特性が実際の性能にどのようなメリットをもたらすかを目の当たりにしてきました。
熱性能の利点
PEEKの最も印象的な特性のひとつは、その熱安定性です。この材料は、ほとんどのプラスチックが壊滅的に破損するような温度でも機械的特性を維持します。
温度特性 | PEEKの性能 | 標準プラスチックとの比較 |
---|---|---|
連続使用温度 | 最高480°F (250°C) | 一般的なエンジニアリング・プラスチックより2~3倍高い |
ガラス転移温度 | 143°C | 高温でも剛性を維持 |
融点 | 649°F (343°C) | 蒸気滅菌が可能 |
熱伝導率 | 0.25 W/m-K | 多くのプラスチックよりも優れた放熱性 |
この優れた耐熱性により、PEEKは、標準的なプラスチックではすぐに変形したり劣化してしまうような熱源付近の用途にも使用することができます。私は、多くの顧客がより劣った材料で作られた故障したコンポーネントを、厳しい熱環境にもかかわらず完璧に機能し続けるPEEK部品に置き換える手助けをしてきました。
耐薬品性の利点
PEEKの耐薬品性プロフィールは、その熱的特性とほぼ同じくらい印象的です。PEEKは、以下のような化学物質に対して優れた耐性を示します:
- 炭化水素および有機溶剤
- ほとんどの酸と塩基(濃硫酸を除く)
- スチームと温水
- 自動車用液体および燃料
- 医療用滅菌プロセス
この幅広い耐薬品性により、PEEKは複数の攻撃的な物質にさらされることが予想される環境で特に重宝されます。例えば、半導体産業では、PEEK部品は寸法安定性を維持しながら、ウェハープロセスで使用される過酷な化学薬品に耐えることができます。
機械的特性の利点
PEEKの機械的強度は、他の多くの熱可塑性プラスチックとは一線を画している:
- 14,500psiの引張強度(一部の金属に匹敵)
- 優れた耐疲労性
- 優れた耐衝撃性と靭性
- 優れた耐摩耗性
- 低摩擦係数
これらの特性により、PEEKはほとんどのプラスチックが破損するような構造用途に適しています。私はPEEKをギア、ベアリング、その他機械的ストレスの大きい磨耗の激しい部品に使用し、多くの場合、金属部品を耐食性やノイズ低減などの付加的な利点を提供する軽量のPEEK代替品に置き換えています。
PEEKの重大な欠点
PEEKはその素晴らしい性能特性にもかかわらず、いくつかの重大な欠点があり、材料選択の際には注意深く考慮する必要があります。
コスト制約
PEEKの最も明白な欠点は、そのコストです。PTSMAKEでは、他のエンジニアリングプラスチックと比較して、PEEKの価格プレミアムをお客様に理解していただく必要があります:
- PEEKは通常、ナイロンやアセタールのようなエンジニアリング・プラスチックの5~10倍の価格
- PEEK部品の材料費は、同等の金属部品よりも20-30%高くなる可能性がある。
- 原材料価格の高騰は、小型部品の経済性に大きな影響を与える。
このコスト要因から、エンジニアはPEEKをそのユニークな特性が絶対に必要な最も重要な用途にのみ使用することを余儀なくされることがよくあります。多くの場合、アセンブリ内の非重要部品には、よりコスト効果の高い代替品を推奨しています。
製造の課題
PEEKには、製造の複雑さとコストを増大させる製造上の課題がいくつかあります:
加工の難しさ:PEEKは熱抵抗が高いため熱伝導率が悪く、加工中に熱がこもりやすい。そのため、切削速度を遅くし、工具を頻繁に交換し、慎重に冷却する必要があります。
処理温度要件:融点が649°F(343°C)であるPEEKは、射出成形や押出成形に専用の高温装置を必要とする。
限られた処理枠:PEEKの溶融温度と劣化の開始温度との差は比較的狭く、加工時の課題となっている。
金型の収縮:PEEKは冷却時に大きな収縮(約1-1.3%)を示すため、厳しい公差を達成するためには精密な金型設計が必要となる。
PTSMAKEでは、このような課題に対処するため、PEEK用の特殊加工プロトコルを開発しましたが、PEEK部品製造の全体的なコストと複雑さを高めることは避けられません。
アプリケーションの制限
その素晴らしい特性にもかかわらず、PEEKには特定の用途に適さない限界がある:
- 耐紫外線性が低い:添加剤を使用しない場合、PEEKは長時間の紫外線にさらされると劣化するため、屋外での使用は制限される。
- 限定カラーオプション:PEEKは天然の琥珀色/褐色であり、加工温度が高いため、安定した着色が難しい。
- 電気的制限:PEEKは優れた絶縁体ではあるが、特殊な電気用ポリマーに比べると高周波電気用途には理想的とは言えない。
- ボンディングの難しさ:PEEKの耐薬品性は、接着剤による接合を困難にしており、しばしば特殊な表面処理が必要となる。
費用対効果分析:PEEKはいつ価値があるのか?
PEEKのコスト・プレミアムが大きいことを考えると、この材料を指定する前に徹底的なコスト・ベネフィット分析が不可欠である。私の経験では、PEEKは以下のシナリオで最高の価値を提供します:
PEEKが得意とするシナリオ
高温環境:使用温度が149℃を超える場合、PEEKが唯一の有効なプラスチック選択肢となることが多く、その割高なコストは正当化される。
化学的に攻撃的な環境:複数の化学物質や特に過酷な物質にさらされる用途では、PEEKの幅広い耐薬品性により、それ以下の材料で必要とされる頻繁な交換を防ぐことができます。
重要な摩耗用途:重要なシステムで常に摩擦や摩耗を受ける部品の場合、PEEKの優れた耐摩耗性と低摩擦性により、サービス間隔を劇的に延長することができます。
軽量化の要件:航空宇宙用途や高性能用途で金属部品を置き換える場合、PEEKの強度対重量比は、そのコストを正当化する性能上の利点を提供することができます。
医療用インプラント:PEEKの生体適合性と化学的安定性は、材料の不具合が許されない長期的な移植器具に理想的です。
代替素材の比較
PEEKの極端な特性を特に必要としない用途では、いくつかの代替品が低コストで十分な性能を発揮する可能性があります:
素材 | 比較優位 | コスト対PEEK | 主な制限 |
---|---|---|---|
PPS(ポリフェニレンサルファイド) | 優れた耐熱性(400°F) | 40-60% 下 | 耐薬品性が低い |
PTFE(四フッ化エチレン樹脂) | 優れた耐薬品性 | 30-50% 下 | 機械的強度が低い |
PEI(ポリエーテルイミド) | 良好な耐熱性、透明性 | 30-40% 下 | 耐摩耗性が低い |
PAI(ポリアミドイミド) | 高強度、優れた耐摩耗性 | 10-20% 下 | 処理がより困難 |
アセタール(POM) | 優れた加工性、低コスト | 80-90% 下 | 限られた温度耐性 |
業界特有の考慮事項
業界によって、PEEKの特性プロファイルの優先順位は異なります:
航空宇宙・防衛
航空宇宙用途では、PEEKの軽量性、難燃性(添加剤を使用した場合)、熱安定性の組み合わせは、以下のような部品に使用されるプレミアム価格を正当化する:
- 制御システムにおけるブッシュとベアリング
- 電気コネクターおよび絶縁体
- 高温ゾーンの構造部品
- 耐薬品性が要求される燃料系統部品
医療・ヘルスケア
医療業界はPEEKを高く評価している:
- 生体適合性(インプラントグレード)
- 繰り返し滅菌に対する耐性
- 放射線透過性(X線に干渉しない)
- 骨に類似した機械的特性(強化された場合)
これらの特性により、PEEKは高価であるにもかかわらず、移植可能な装置や手術器具に理想的である。
産業機器
工業用途の場合、PEEKを使用するかどうかは、通常、使用条件の厳しさによって決まります:
- 過酷な環境(高温、化学薬品への暴露)では、PEEKの使用が正当化されることが多い。
- ダウンタイムが非常にコストのかかる用途では、PEEKの信頼性が役立ちます。
- 高精度部品はPEEKの寸法安定性から恩恵を受ける
PTSMAKEでは、PEEKの優れた性能が、お客様の特定の用途のニーズに対して、その価格を正当化できるかどうかを判断するために、お客様をサポートします。
PEEKはなぜこんなに高いのか」という記事の第7章の内容を、あなたの要求に従って作成します。
PEEKはなぜ高いのか?
PEEKコンポーネントの見積もりを依頼する際、ステッカーショックを経験したことがありますか?エンジニアが初めてこの高性能プラスチックの価格に出会ったとき、多くの人は、特に、ほんのわずかな価格で適切な性能を提供しているように見えるより一般的なエンジニアリングプラスチックと比較した場合、このような割高なコストを正当化できる材料があるのか疑問に思うでしょう。
PEEKの高コストの原因は、その複雑な製造工程、高価な原材料、特殊な設備要件、比較的少ない生産量にある。複雑な重合プロセスには精密な条件が要求され、製造技術の独自性とPEEKの特殊材料としての地位が市場価格をさらに高めている。
PEEKを支える複雑な製造工程
なぜPEEKがこのようなプレミア価格をつけているのかを理解するには、その製造工程を調べることから始まります。単純なポリマーとは異なり、PEEKの製造には高度な化学と精密な加工条件が必要であり、最終的なコストに大きく影響します。
原材料コストと希少性
PEEKの製造に使用されるモノマーは、それ自体が高価な特殊化学品である。主な成分は以下の通り:
- ジフェニルエーテル
- 4,4′-ジフルオロベンゾフェノン
- 炭酸カリウム
- ジフェニルスルホン(溶剤として)
これらの前駆体は、PEEK合成に必要な純度を得るために複数の精製工程を必要とするため、重合を開始する前からコストがかさむ。さらに、これらの化学物質の中には、世界的に生産能力が限られているものもあり、供給上の制約が価格を押し上げている。
PTSMAKEでは、機械加工プロジェクト用にPEEKを調達する際、ポリマーそのものだけでなく、その製造に使われた特殊化学物質のバリューチェーン全体に対して対価を支払っています。
重合プロセスの複雑さ
PEEKの合成には、高度な求核芳香族置換重合プロセスが必要である。この反応は、精密に制御された条件下で起こる必要がある:
- 300~400°C(572~752°F)の温度
- 酸化を防ぐ不活性雰囲気
- 特殊圧力容器
- 反応時間の延長(しばしば3~5時間)
- 慎重な触媒管理
これらの要件がそれぞれ、製造の複雑さとコストに拍車をかけている。材料の性能特性に直接影響する適切な分子量分布と結晶化度を確保するためには、反応全体を注意深くモニターしなければならない。
限られた生産規模と市場力学
PEEKが特殊材料であることは、その生産経済性と市場価格に大きな影響を与える。
独自技術と特許保護
オリジナルのPEEK製造技術は、1970年代にビクトレックス社(旧ICI社)によって開発され、特許を取得した。現在でも、製造技術の大部分は独自のものであり、さまざまな特許によって保護されている。このように製造方法における競争が限られているため、コモディティ化したプラスチックに比べて高い価格設定が維持されている。
現在、ビクトレックス社、ソルベイ社、エボニック社など複数のメーカーが世界各地に存在するが、それぞれが独自のプロセスを採用しており、その開発には莫大な研究開発投資が必要である。これらの開発コストは、材料価格を通じて回収しなければならない。
生産量経済学
年間数百万トン生産される汎用プラスチックとは異なり、PEEKは比較的少量しか生産されない:
プラスチックタイプ | 世界の年間生産量 | 相対コスト係数 |
---|---|---|
ポリエチレン(PE) | ~億トン | 1×(ベースライン) |
ナイロン(PA) | ~800万トン | 2-3× |
ポリカーボネート(PC) | ~450万トン | 3-4× |
覗き見 | <万トン未満 | 30-50× |
生産量が限られているということは、一般的なプラスチックのコストを引き下げる規模の経済をメーカーが実現できないことを意味する。設備維持費、品質管理費、研究開発費などの固定費は、より少ないキログラムの製品に分散されるため、単位当たりのコストが高くなる。
設備と加工に必要な条件
PEEKの生産設備には、重合、コンパウンド、加工に必要な極端な温度と圧力に対応できる特殊な装置が必要である:
- 精密制御システムを備えた高温反応器
- 特殊押出・造粒設備
- 高度なろ過・浄化システム
- 総合的な品質管理および試験設備
これらの設備投資は多大なものであり、最終的な材料費に大きく寄与します。PTSMAKEでPEEKパーツを加工する場合、これらの上流製造コストを原材料価格に転嫁することになります。
加工と機械加工の課題
いったん製造されると、PEEKは加工や機械加工においてさらなる課題を突きつけられ、それが完成部品のコスト高にさらに拍車をかけている。
高い加工温度
融点が約343℃のPEEKは、特殊な加工装置を必要とする:
- 高温対応の射出成形機
- 特殊な熱管理システムを備えた金型
- より高価なヒーター・エレメントとコントローラー
- 高温物質を取り扱うための安全システムの強化
これらの要件は、PEEKを加工できるメーカーが少なく、競争が制限され、加工コストが高く維持されることを意味する。
加工上の注意と工具の摩耗
PTSMAKEでPEEKを加工する場合、生産コスト上昇の原因となるいくつかの要因に遭遇する:
工具の摩耗: PEEKは、標準的なプラスチックに比べて工具の摩耗が著しく、工具の交換頻度を上げるか、高級工具を使用する必要がある。
熱管理: PEEKは熱伝導率が低いため、加工中に熱がこもり、切削速度を遅くしたり、特殊な冷却技術を必要とする。
専門知識: PEEKの適切な加工には、材料の劣化を防ぎ、厳しい公差を達成するための経験と知識が必要です。
後処理の要件: 多くのPEEK用途では、内部応力を緩和し、寸法安定性を確保するために、アニールなどの追加加工工程が必要となります。
これらの要因のそれぞれが、原料価格だけでなく、完成したPEEKコンポーネントを製造するための総コストを増加させます。
品質管理と認証費用
PEEKは、重要な用途に使用されることが多い高性能材料であるため、その製造と加工には厳格な品質管理が要求されます。
厳しい試験要件
PEEKの各バッチは通常、検証のために大規模な試験を受ける:
- 分子量分布
- 結晶化率
- 熱的性質(ガラス転移点と融点)
- 機械的性質(引張強さ、弾性率、伸び)
- 純度と汚染物質レベル
これらのテストには専門的な設備と訓練を受けた人材が必要であり、最終的な製品価格に多大な品質保証コストが上乗せされる。
業界認証とトレーサビリティ
航空宇宙、医療、半導体産業における多くのPEEKアプリケーションは、完全な材料トレーサビリティと業界固有の規格への準拠を必要とします:
- 航空宇宙認証(AS9100、NORSOK)
- 医療機器規格(ISO13485、USPクラスVI)
- 原子力産業資格(NQSA-1)
- 半導体業界の要件(高純度)
これらの認証を維持するには、広範な文書化、定期的な監査、場合によっては別の生産施設や設備が必要となり、これらすべてがコスト上昇の要因となる。
PEEKと代替材料の比較
PEEKの価格設定の背景を理解するには、コストと性能の両面で代替素材と比較することが有効です。
コストパフォーマンス分析
PEEKは一般的に、標準的なエンジニアリング・プラスチックの5~10倍の価格であり、数量ベースでは一部の特殊金属よりも高価な場合があります。しかし、過酷な環境におけるその性能は、しばしばこのプレミアムを正当化します:
プロパティ | 覗き見 | 標準エンジニアリングプラスチックス | プレミアム・メタル |
---|---|---|---|
連続使用温度 | 250°C(480°F)まで | 80-170°C (176-338°F) | 通常は無制限 |
耐薬品性 | 素晴らしい | 可変(しばしば限定的) | しばしば不良(腐食) |
具体的な強さ | 非常に高い | 中程度 | 高い |
原材料費 | 非常に高い | 低~中程度 | 中~高 |
加工費 | 高い | 低~中程度 | 高い |
生涯価値 | 素晴らしい | 過酷な条件下での制限 | 良好だが腐食の問題がある |
PTSMAKEでは、お客様がこれらのトレードオフを評価し、PEEKのプレミアム価格が特定の用途における性能上の優位性によって正当化されるかどうかを判断するお手伝いをすることがよくあります。
PEEKはプレミアム価格に値するか?
PEEKの高コストが正当化されるかどうかは、アプリケーションの要件に完全に依存する。
PEEKがコストにもかかわらず価値を提供する用途
PEEKは、その高価格にもかかわらず、優れた価値を提供する:
- 過酷な使用環境 他の素材ではすぐにダメになるところ
- 重量が重要なシステム PEEKの強度対重量比が利点となる場合
- メンテナンスが必要な機器 ダウンタイムのコストが材料費をはるかに上回る場合
- 腐食性環境 金属が急速に劣化する場所
- 医療用インプラント 生体適合性と長期安定性が不可欠な場合
このようなシナリオでは、PEEKの性能上の利点は、初期投資が高いにもかかわらず、生涯コストの低減に直結します。
PEEKコンポーネントのコスト削減戦略
PEEKの性能を必要としながらも予算に制約のあるプロジェクトでは、以下のアプローチをご検討ください:
- ハイブリッド・デザイン 重要な部品にのみPEEKを使用
- 最適化された加工技術 材料の無駄を省く
- ニアネットシェイプ加工 材料消費を最小限に抑える
- デザインの最適化 材料全体の体積を減らす
- 未記入のグレード 補強がパフォーマンスに必要でない場合
PTSMAKEでは、多くのクライアントがこれらの戦略を導入し、PEEKの利点を得ながら効果的にコストを管理できるよう支援してきました。
コスト効率の高い生産のためにPEEK加工を最適化するには?
PEEKの卓越した特性を、プロジェクトの予算を圧迫することなく活用する方法はないかと考えたことはありませんか?市場で最も高価なエンジニアリングプラスチックの一つであるPEEKを使用する場合、加工方法を最適化することは単なる効率化ではありません。
PEEK加工を最適化し、コスト効率の高い生産を実現するには、適切な切削工具(超硬またはダイヤモンドコーティング)の使用、適切な速度と送り(一般的に標準的なプラスチックよりも遅い)の維持、効果的な冷却戦略の実施、ニアネットシェイプ設計による材料の無駄の最小化、サイクルタイムを短縮するための入念なツールパスの計画が必要です。
PEEK加工に最適な工具の選択
PEEKを加工する場合、工具の選択は部品の品質と全体的な加工コストの両方に劇的に影響します。私は長年の経験から、適切な工具に先行投資することで、長期的には大幅に節約できることを学びました。
切削工具の材質と形状
PEEK、特に炭素繊維やガラスを含む充填グレードは研磨性が高いため、慎重に工具を選択する必要がある:
工具材料 | 最適 | 工具寿命 | コスト係数 |
---|---|---|---|
カーバイド(非コーティング) | 未充填PEEK | グッド | 中程度 |
ダイヤモンドコート超硬合金 | 充填PEEK | 素晴らしい | 高い |
PCD(多結晶ダイヤモンド) | 大量生産 | スーペリア | 非常に高い |
高速度鋼(HSS) | 未充填PEEKの簡単な操作 | 限定 | 低い |
PTSMAKEのほとんどの用途では、高性能プラスチック用に設計された特殊形状の超硬工具を使用しています。主な特徴は以下の通りです:
- シャープな刃先(発熱を抑える)
- 高い正のすくい角(10~15°)。
- ポリッシュ仕上げのフルート(切り屑の排出性を向上)
- 十分な逃げ角(擦れを防ぐ)
高級工具は初期費用は高くつくが、切れ味を長く維持し、より良い表面仕上げができるため、二次加工の必要性を減らすことができる。
工具摩耗に関する考察
PEEKの加工では、標準的なエンジニアリングプラスチックと比較して、工具の摩耗が非常に速く発生します。工具摩耗の監視と管理は、部品の品質とコスト管理の両方を維持するために非常に重要であることがわかりました。
目視による摩耗の兆候を待つのではなく、加工量に基づいた工具交換スケジュールを確立することをお勧めします。私たちの工場では、充填されたPEEKを加工する工具は通常、アルミニウムを加工する際に想定される工具寿命の約60~70%後に交換します。この積極的なアプローチにより、磨耗した工具で加工することによる品質問題や潜在的なスクラップパーツの発生を防ぐことができます。
切削パラメータの最適化
効率的なPEEK加工には、切削速度、送り、切込み深さの適切なバランスを見つけることが重要です。目標は、過度の熱を発生させたり、表面品質を損なったりすることなく、材料除去率を最大化することです。
スピードとフィードに関する推奨事項
PTSMAKEでの広範なテストを通じて、PEEK加工パラメータの一般的なガイドラインを開発しました:
PEEKタイプ | 切削速度(SFM) | フィード・レート | 切り込み | 冷却水 |
---|---|---|---|---|
未充填PEEK | 300-500 | 中程度 | 0.005"-0.020" | 空気またはミスト |
30% カーボン充填 | 200-400 | 値下げしました (75%) | 0.005"-0.015" | 霧/洪水 |
30% ガラス充填 | 250-450 | 値下げしました (85%) | 0.005"-0.015" | 霧/洪水 |
これらのパラメーターは、特定の工具、機械の剛性、部品の要件に基づいて調整する必要があります。一般的には、これらの範囲の保守的な端から始めて、結果をモニターしながら徐々にパラメーターを増やしていくことをお勧めします。
暑さ対策
PEEKは熱伝導率が低いため、加工中に熱がこもりやすく、それが原因となる可能性がある:
- 次元の不安定さ
- 表面仕上げの劣化
- 工具摩耗の促進
- 極端な場合の材料の分解
これらの問題に対処するため、我々はいくつかの熱管理技術を導入している:
適切なクーラントの選択:未充填のPEEKの場合、圧縮空気による冷却が効果的です。充填グレードの場合、ミストまたはフラッドクーラントがより優れた放熱効果を発揮します。
断続的な切断:ディープポケット作業中に定期的に休止することで、熱を放散させることができる。
クライム・フライス:従来のフライス加工ではなく、登りフライス加工を使用することで、摩擦と発熱を減らすことができる。
マルチ・ライト・パス:1回の重切削ではなく、数回の軽い仕上げ切削を行うことで、寸法精度と表面仕上げが向上します。
素材利用戦略
PEEKは高価であるため(グレードや形状により1ポンドあたり$75~200の場合が多い)、材料の利用率が重要なコスト要因になります。廃棄物の一つひとつが収益に直接影響します。
ニアネットシェイプ・スターティング・マテリアル
最終的な寸法に近い材料から始めることで、廃棄物を大幅に減らすことができます。次のようなアプローチを考えてみよう:
カスタム押出材:一貫した断面を持つ部品の場合、カスタム押出プロファイルから開始することで、大幅な材料の無駄を省くことができます。セットアップ費用が高くなりますが、大量生産では材料の節約により相殺されます。
カット済みブランク:材料サプライヤーに、お客様の部品に特化したサイズのプレカットブランクを提供してもらうことで、廃棄物と初期加工時間の両方を削減できます。
ネスティング・ソフトウェア:板から加工された平らな部品の場合、高度なネスティングソフトウェアを使用することで、手作業によるレイアウト計画と比較して15-30%だけ材料の使用量を最適化することができます。
PTSMAKEでは、お客様の量産部品にこれらのアプローチを導入することで、PEEKの材料コストを40%以上削減するお手伝いをしてきました。
チップ・リサイクルに関する考察
一部の熱可塑性プラスチックとは異なり、PEEKは加工温度が高いため、自社でリサイクルすることは容易ではありません。しかし、専門のリサイクルサービスは存在する:
- 清浄に選別されたPEEKチップはリサイクル業者に売却可能
- リサイクル業者によっては、将来購入する商品に対して商品価値をクレジットするところもある。
- 充填グレードは通常、コンタミネーションの懸念からリサイクル価値が低い。
リサイクルによって材料費が完全に相殺されるわけではありませんが、大規模な機械加工ではある程度のコスト回収が可能です。
加工戦略の最適化
工具やパラメータだけでなく、全体的な加工アプローチは、部品の品質と生産コストの両方に大きく影響します。
複数部品の治具設計
1回のセットアップで複数のパーツを加工できるようにうまく設計された治具には、いくつかの利点があります:
- 部品あたりのセットアップ時間を短縮
- 部品間の一貫性の向上
- より効率的なマシン利用
- 板材からの歩留まり向上
ある航空宇宙産業のクライアントのために、16個の小さなPEEK部品を同時に加工できる治具を設計し、個々のセットアップと比較して部品当たりのコストを62%削減しました。
CAM戦略の洗練
最適化されたツールパスは、加工時間を大幅に短縮し、部品の品質を向上させます:
高効率粉砕:一貫した工具かみ合いを維持する高度なCAM戦略を使用することで、サイクルタイムを短縮し、工具寿命を延ばします。
レスト加工:大きな工具で材料を大量に除去し、必要な場合にのみ小さな工具を使用する、適切な順序の作業により、材料除去率と工具寿命の両方が最適化されます。
最適化されたアプローチの動き:効率的なアプローチとリトラクト動作によりエアカットを最小化することで、部品の品質に影響を与えることなく、サイクルタイムを5-15%短縮することができます。
スクラップを最小限に抑える品質管理
PEEKは材料費が高いため、スクラップの削減がコスト削減の主要な戦略となります。問題を早期に発見する効果的な品質管理プロセスは、仕様に適合しない部品で高価な材料を無駄にすることを防ぎます。
インプロセス測定
我々はいくつかの工程内検証ステップを導入している:
第一条検査:生産に取り掛かる前に、各ランの最初の部分を徹底的に測定する。
段階的検査:特に部品の反転や再固定を行う場合、後続の作業に進む前に重要な形状を測定すること。
熱安定化:PEEKの熱膨張は寸法に影響を与える可能性があるため、最終測定の前に部品を周囲温度に到達させる。
これらの実践により、当社はPEEK部品のスクラップ率を2%以下に維持し、業界平均を大幅に下回っている。
加工後の考慮事項
加工工程は、部品が機械から外れても終わりではありません。加工後の作業は、品質とコストの両方に大きな影響を与えます。
応力緩和と寸法安定性
複雑な形状や不均一な材料除去を伴うPEEK部品は、長期的な寸法安定性を確保するために応力除去が有効な場合があります:
サーマルアニーリング:ガラス転移温度以下に制御された加熱と徐冷により、内部応力を緩和することができる。
ラフ・トゥ・フィニッシュ戦略:初期加工でほとんどの材料を除去し、最終加工前に部品を安定させることで、寸法精度が向上する。
公差の厳しい重要な部品の場合、これらの余分な工程は、コストのかかる現場での不具合や経時的な寸法ドリフトを防ぐために投資する価値が十分にある。
これらの最適化戦略を実施することで、PTSMAKEでは、この材料の価値を高めている卓越した性能特性を損なうことなく、コスト効率の高いPEEK加工を実現するために、多くのお客様を支援してきました。重要なのは、材料の選択から最終検査まで、製造プロセスのあらゆる側面を考慮した全体的なアプローチです。