PTSMAKEに15年以上勤務する中で、多くのエンジニアがピストン加工で苦労しているのを見てきました。加工不良はエンジンの故障、性能低下、高額な修理費につながります。これらの問題を回避しましょう。
ピストン加工は、材料の選択、表面仕上げの要件、正確な寸法公差、熱的考慮、適切な工具の選択という5つの重要な側面に重点を置いています。これらの要素は、ピストンの性能とエンジンの信頼性に直接影響します。
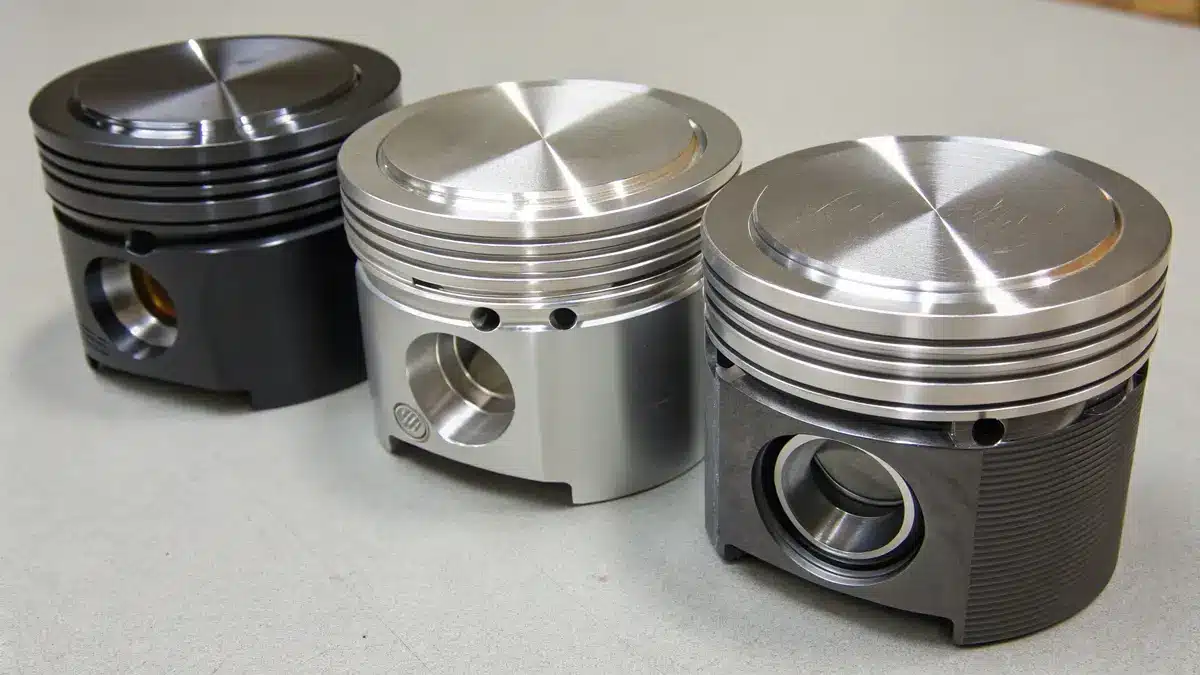
大手自動車メーカーと仕事をした経験を共有したいと思います。私はキャリアを通じて、さまざまな用途の何千ものピストンの機械加工を手伝ってきました。重要な仕様や一般的な課題について私が得た知識は、完璧に加工されたピストンを作るには何が必要かを理解するのに役立ちます。あなたのプロジェクトにとって最も重要な細部に飛び込んでみましょう。
ピストン加工とは?
何十年も長持ちするエンジンがある一方で、早々に故障してしまうエンジンもあることを不思議に思ったことはないだろうか。その秘密は多くの場合、ピストン加工の精度にある。
ピストン加工は、CNC技術を駆使して金属ピストンを成形する高精度な製造プロセスであり、極度の圧力と温度に耐え、燃焼エネルギーを効率的にエンジンの機械的動力に変換する部品を作る。
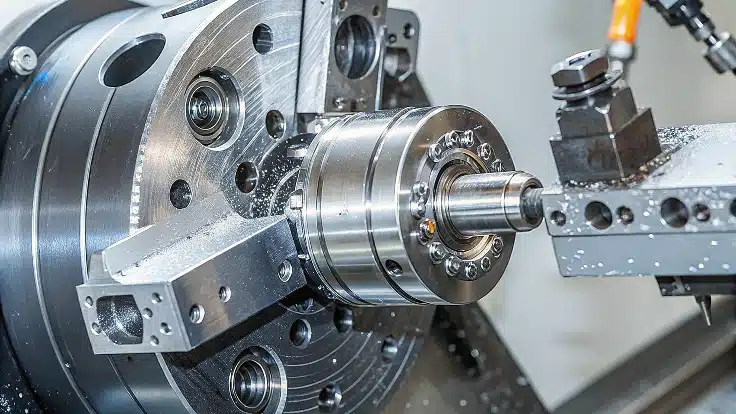
ピストン加工の基礎
PTSMAKEで数え切れないほどの自動車や航空宇宙のお客様と仕事をしてきて、適切なピストン加工がいかに重要であるかを身をもって感じてきました。このプロセスでは、金属ブランク(通常はアルミニウム合金)から材料を除去し、正確な仕様を満たすピストンを作成します。これがなぜ重要なのかを説明します:
- 精密公差制御(通常±0.001インチ)
- 最適なパフォーマンスを実現する表面仕上げの品質
- 加工中の材料の完全性維持
- 特定のエンジン設計のための複雑な形状作成
ピストン設計における重要部品
現代のピストンは、精密な機械加工を必要とするいくつかの重要な特徴で構成されている:
特徴 | 機能 | 加工要件 |
---|---|---|
クラウン | 燃焼室表面 | 複雑なプロファイル切断 |
リングの溝 | 封じ込め | 精密円形加工 |
スカート | シリンダーウォールガイド | 正確な直径制御 |
ピンボス | リストピン接続 | 正確なホールアライメント |
事業環境の課題
私の経験では、ピストンはあらゆる機械システムの中で最も過酷な条件に直面している:
- 温度変動(室温から600°F以上まで)
- 過酷な圧力サイクル(1,000 psiまで)
- 連続往復運動
- 常に金属と金属が接触
産業用途
さまざまな部門と仕事をしてきた経験から、ピストン加工は独自の要件を持つさまざまな業界に貢献している:
自動車産業
- 高性能レーシング・エンジン
- 商用車用モーター
- 舶用推進システム
航空宇宙用途
- 航空機エンジン
- 補助電源ユニット
- 推進システムの研究
産業機械
- 建設機械
- 発電ユニット
- 製造機械
高度加工技術
PTSMAKEでの仕事を通じて、私はピストン加工技術の進化を目の当たりにしてきました:
5軸CNC加工
- 複雑な形状の作成が可能
- セットアップ時間の短縮
- 精度の向上
品質管理システム
- インプロセス測定
- 自動検査
- リアルタイム調整
素材の革新
- 先進アルミニウム合金
- コーティング技術
- 熱処理工程
精度のインパクト
ピストン加工の精度がエンジン性能に直接影響するケースを数多く見てきた:
パフォーマンスのメリット
- 出力向上
- 燃費の向上
- 排出量の削減
- エンジン寿命の延長
コストへの影響
- 保証クレームの減少
- メンテナンスの必要性を低減
- 信頼性の向上
- より良いリセールバリュー
製造に関する考慮事項
生産ラインを管理した経験から言うと、ピストン加工を成功させるには、以下のことが必要だ:
素材の選択
- 適切な合金の選択
- 品質管理チェック
- 材料認証
プロセス制御
- 温度モニタリング
- 工具摩耗管理
- 切削パラメータの最適化
品質保証
- 寸法検査
- 表面仕上げの検証
- 冶金テスト
今後の動向
製造業のイノベーションに深く関わる者として、私はいくつかの新たなトレンドがあると見ている:
スマート・マニュファクチャリング
- IoT統合
- リアルタイム・モニタリング
- 予知保全
持続可能な実践
- 廃棄物の削減
- エネルギー効率
- リサイクル可能な素材
先端材料
- 新合金の開発
- コンポジット・インテグレーション
- 表面処理
ピストン加工に求められる精度は、エンジン技術の進歩とともに進化し続けています。私はPTSMAKEでの15年以上を通じて、この製造工程が、さまざまな産業において信頼性が高く効率的なエンジンを生み出すためにいかに重要であるかを目の当たりにしてきました。これらの基本を理解することは、エンジンの製造やメンテナンスに携わる人にとって不可欠です。
ピストン加工に使用される材料は?
CNC機械加工業界で15年以上の経験を持つ製造のエキスパートとして、私は材料の選択がピストンの性能を左右することを身をもって体験してきました。この重要な決断を私にお任せください。
ピストン加工で最も一般的に使用される材料は、アルミニウム合金(2618や4032など)、スチール合金、チタンです。アルミニウムは軽量性能と放熱性を提供し、スチールは耐久性を提供し、チタンは強度と軽量化を兼ね備えています。
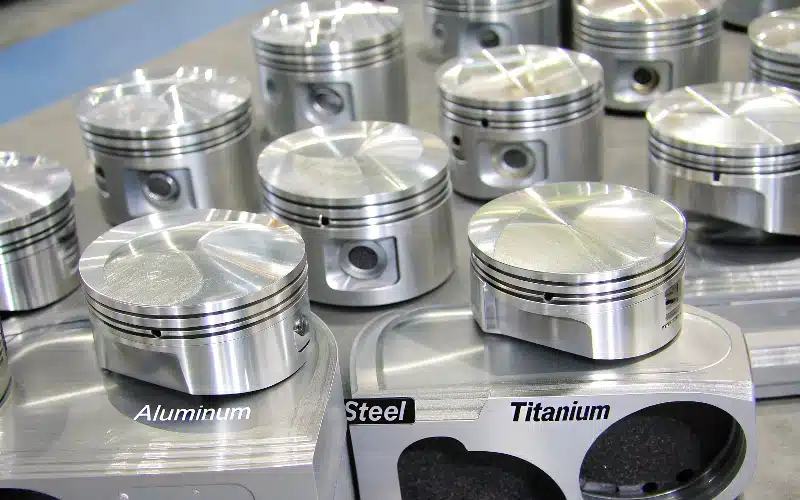
ピストン製造におけるアルミニウム合金の理解
PTSMAKEでの経験では、アルミニウム合金がピストン製造の主流を占めています。私たちが扱う最も人気のある2つのグレードは以下の通りです:
2618アルミニウム:高性能アプリケーションに最適
- 高温での高い強度
- より優れた耐疲労性
- レース用エンジンによく使われる
4032アルミニウム:標準的な自動車用途に最適
- 低熱膨張
- より優れた耐摩耗性
- より費用対効果の高いソリューション
合金鋼耐久性のチャンピオン
卓越した耐久性が必要な場合は、スチール合金を勧めることが多い。主な選択肢の内訳は以下の通りです:
スチールタイプ | 主なメリット | ベストアプリケーション |
---|---|---|
4140 | 高強度、優れた耐疲労性 | 大型ディーゼルエンジン |
4340 | 優れた靭性、優れた耐摩耗性 | レーシングエンジン |
8620 | 良好なケース硬化、適度なコスト | 商用車 |
チタンプレミアムな選択
チタンピストンはピストン技術の最先端を代表するものです。私の長年の製造経験において、特にチタンの需要が伸びているのを目の当たりにしてきました:
- 航空宇宙用途
- 高級レーシング・エンジン
- 軍用車両
素材選択基準
クライアントの素材選びをサポートする際、私はこれらの重要な要素を考慮する:
エンジンの種類と用途
- 乗用車アルミニウム合金 (4032)
- レーシングエンジン2618アルミニウムまたはチタン
- 大型ディーゼル:スチール合金
パフォーマンス要件:
- 最高使用温度
- 期待される出力
- 耐久性のニーズ
- 体重制限
コストを考慮する:
- 材料単価
- 加工時間と複雑さ
- 予想生産量
- ライフサイクル要件
材料特性が加工に与える影響
PTSMAKEでの仕事を通じて、材料の特性が加工プロセスに大きく影響することを学びました:
アルミニウム合金:
- 加工速度の高速化が可能
- 慎重な温度管理が必要
- 適切なチップ排出の必要性
- 工具摩耗の低減
スチール:
- より遅い切断速度が必要
- 高い工具摩耗率
- より強固な冷却が必要
- より大きな消費電力
チタン:
- 専用の切削工具が必要
- 非常に特殊な速度と送り速度
- 冷却戦略の強化が必要
- 加工コストの上昇
材料整合性要件
私がいつもお客様に強調していることのひとつは、素材の一貫性です。なぜ重要なのか、その理由を説明しよう:
品質管理:
- 一貫した材料特性により、信頼性の高い性能を実現
- 生産工程での不合格率を低減
- 予測可能な加工パラメータ
生産効率:
- 標準化された加工プロセス
- バッチ間のセットアップ時間の短縮
- より正確なコスト見積もり
パフォーマンスの予測可能性:
- 一貫した熱特性
- 信頼性の高い摩耗特性
- バッチ全体で均一な強度
PTSMAKEでの15年以上の経験を通じて、ピストン加工を成功させるには、適切な材料を選択するだけでなく、その材料が製造工程全体を通してどのように作用するかを理解することが重要であることを学びました。それぞれの材料が最適な結果を得るためには、特定の専門知識、適切な工具、加工パラメータの正確な制御が必要です。
ピストン加工の主なステップとは?
単純な金属の塊が、どのようにして精密に設計されたピストンに変わるのか、不思議に思ったことはありませんか?CNC機械加工に15年以上携わってきた私が、それを可能にする重要なステップを明らかにします。
ピストン加工には、粗加工、CNC加工、精密穴あけ加工、仕上げ加工という体系的な工程が含まれます。各工程では、エンジン性能を最適化するために不可欠な厳しい公差を達成するために、厳格な品質管理と高度な機械が要求されます。
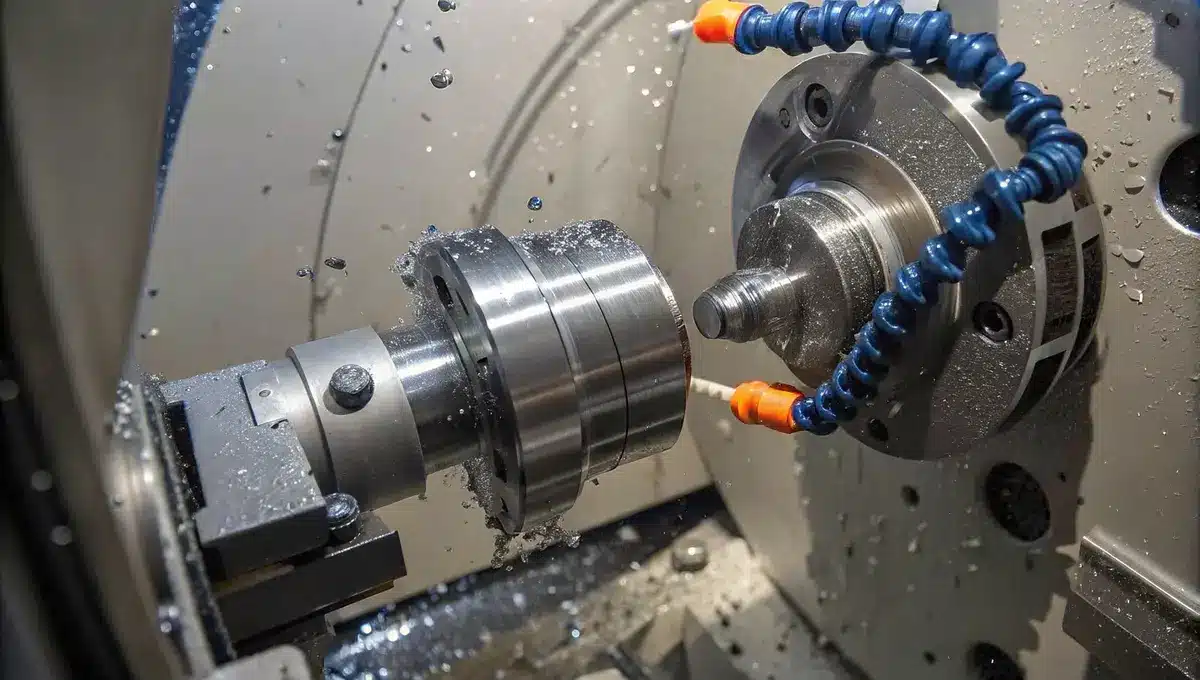
初期準備と粗加工
PTSMAKEでの経験では、ピストン製造の旅は常に慎重な材料選択と準備から始まります。私たちは通常、優れた強度対重量比と熱特性を持つ高級アルミニウム合金を使用します。粗加工の段階では、以下のことが行われます:
- 材料の欠陥検査
- おおよその寸法への初期カット
- 従来の機械加工による基本形状の形成
CNCフライス加工
CNCフライス加工の段階は、ピストンが実際に形になり始める場所です。当社の高度な5軸CNCマシンを使用して、いくつかの重要な作業を行います:
オペレーション | 目的 | 標準公差 |
---|---|---|
クラウンプロファイリング | 燃焼室の表面を作る | ±0.02mm |
スカート加工 | 円筒状のガイド面を定義 | ±0.01mm |
ピンボスのボーリング | リストピンの取り付け準備 | ±0.005mm |
リング溝切削 | ピストンリング用の精密な溝を形成 | ±0.008mm |
精密旋盤加工
フライス加工の後は、旋盤加工に移ります。これは、完璧な円筒形を実現するために特に重要です。15年以上の経験の中で、この段階には細部への並外れた注意が必要であることを学びました:
- 外径ターニング
- 表面仕上げ
- 溝精密旋盤加工
- 同心度検証
石油通路掘削
ピストン加工の最も重要な側面の1つは、オイル通路の作成です。PTSMAKEでは、適切な潤滑を確保するために特殊な穴あけ技術を使用しています:
- 主要油路の深穴掘削
- 石油分配のためのクロスホール掘削
- すべての通路の面取りとバリ取り
- ボアスコープ技術による品質検査
表面処理と仕上げ
仕上げの段階が、良いピストンと優れたピストンを分けるのです。私たちのプロセスには以下が含まれます:
- 重要面の精密研削
- 表面粗さの最適化
- 遮熱コーティング
- 最終寸法確認
品質管理と検査
全工程を通じて、私たちは厳格な品質管理措置を維持しています:
検査ポイント | 方法 | 受け入れ基準 |
---|---|---|
寸法精度 | CMM測定 | ±0.01mm |
表面仕上げ | プロフィロメーター | Ra 0.4 μm |
丸み | 真円度試験機 | 0.005mm以下 |
素材の完全性 | 超音波検査 | 欠陥ゼロ |
CAD/CAMの統合
現代のピストン加工は、高度なソフトウェアソリューションに大きく依存しています。PTSMAKEでは、これを活用しています:
- 設計最適化のための3Dモデリング
- プロセス検証用シミュレーション・ソフトウェア
- ツールパス最適化プログラム
- リアルタイム監視システム
数え切れないほどのピストン製造プロジェクトを監督してきた経験から、これらのステップの適切な順序付けが非常に重要であると自信を持って言えます。私たちは詳細な工程を文書化し、性能に関するフィードバックや技術の進歩に基づいて、常に手順を更新しています。
特殊な要件
エンジンの用途が異なれば、基本的なプロセスに特別な変更を加える必要がある:
- レース用ピストンは、さらに強度を考慮する必要がある
- 大型ディーゼル・ピストンは熱管理の強化が必要
- 高性能ピストンは、しばしばカスタムコーティングを必要とする
PTSMAKEでの経験を通じて、私たちはアプリケーションの種類ごとに独自の技術を開発し、最適なパフォーマンスと長寿命を保証してきました。
プロセスの最適化
競争力を維持するために、私たちは常に以下の方法でプロセスを最適化しています:
- リーン生産方式の導入
- 標準化によるセットアップ時間の短縮
- 工具寿命管理システムの活用
- 予防保全スケジュールの維持
ピストン加工の成功は、最終的には、全工程を通じて一貫した品質を維持しながら、各工程を正確に実行できるかどうかにかかっています。PTSMAKEでは、長年の経験からこれらの手順を洗練させ、OEMの仕様を常に満たす、または上回るピストンを生み出しています。
なぜピストン加工で精度が重要なのか?
なぜピストンの小さな傷がエンジンの完全な故障につながるのか、不思議に思ったことはありませんか?私はPTSMAKEに15年以上勤務する中で、微細な欠陥がいかに大きな問題を引き起こすかを目の当たりにしてきた。
0.001インチのズレでもエンジン性能、燃費、寿命に大きく影響するため、ピストン加工の精度は極めて重要です。完璧な精度は、最適な圧縮を保証し、摩耗を減らし、エンジンの致命的な故障を防ぎます。
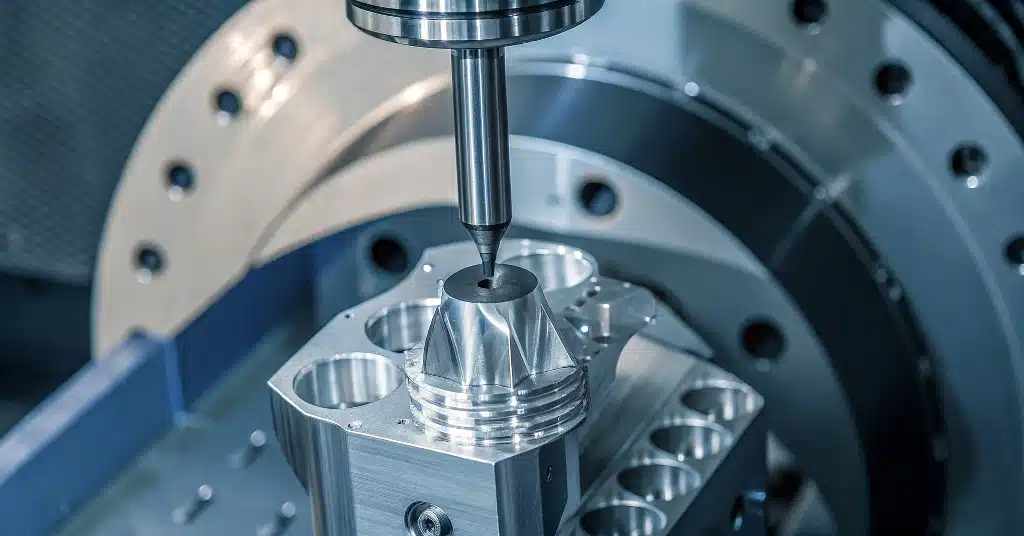
寸法精度の重要な影響
自動車メーカーと仕事をした経験から、私はピストンの精度が3つの重要な分野に直接影響することを学んだ:
- エンジン性能
- 燃費
- コンポーネントの寿命
ピストン製造において、なぜ各ミクロンが重要なのかを説明しよう:
許容レベルを理解する
PTSMAKEで維持している重要なピストン公差の詳細な内訳は以下の通りです:
コンポーネント・エリア | 標準公差 | コンプライアンス違反の影響 |
---|---|---|
ピストン径 | ±0.0005インチ | 圧縮損失、ブローバイ |
リング溝 | ±0.0003インチ | オイル消費、パワーロス |
ピンボア | ±0.0002インチ | 過度の摩耗、騒音 |
スカートのプロフィール | ±0.0004インチ | 擦り傷、発作のリスク |
表面仕上げの要件
表面仕上げの品質は、寸法精度と同様に重要です。当社の製造工程では、以下のことを保証しています:
- シリンダー壁の仕上げ:10-20マイクロインチRa
- リングランド面15-25マイクロインチRa
- スカートの面積8~15マイクロインチ Ra
温度と材料の挙動
見落とされがちなのが熱膨張だ。現代のピストンはそうでなければならない:
- 動作温度(最高600°F)でクリアランスを維持する
- 素材によって異なる膨張率を考慮する
- 熱サイクル下でも表面仕上げを保持
最新の加工技術
PTSMAKEでは、いくつかの最先端技術を採用しています:
5軸CNCマシニングセンタ
- 複雑な形状の作成が可能
- 一貫した精度を保証
- セットアップ時間とヒューマンエラーを削減
先進計測システム
- 三次元測定機(CMM)
- レーザースキャニング技術
- リアルタイム品質管理
熱管理
- 温度管理された製造環境
- 材料の安定化プロセス
- 熱補償システム
品質管理プロトコル
当社の品質保証プロセスには以下が含まれる:
加工前材料分析
- 化学組成の検証
- 硬度試験
- 微細構造検査
工程内検査
- リアルタイム寸法監視
- 表面仕上げの検証
- 温度トラッキング
最終検証
- 寸法検査
- 表面仕上げ測定
- 真円度と円筒度のチェック
精密関連のよくある失敗
私の経験では、これらは精度が不十分なために起こる最も頻繁な問題である:
圧縮ロス
- 不適切なリング溝寸法の結果
- 電力削減につながる
- 燃料消費量の増加
過剰なオイル消費
- 不適切なリングランドの仕上げが原因
- 青い排気煙を出す
- 頻繁なオイル補充が必要
ピストンスラップ
- 誤ったクリアランスの結果
- 騒音と振動を発生させる
- 摩耗を促進する
実社会への影響
PTSMAKEに15年以上在籍し、精度が実際のエンジンにどのような影響を与えるかを見てきた:
- 0.001インチのオーバーサイズは、エンジン寿命を50%短くする可能性がある
- 不適切な表面仕上げはオイル消費を倍増させる
- クリアランスを誤ると、即座に発作を引き起こす可能性がある
精密な製造工程と品質管理を通じて、私たちはお客様をサポートしてきました:
- エンジン寿命を最大30%延長
- 保証クレームを45%削減
- 5-8%の燃費向上
精度の代償
高精度を実現すれば製造コストは上昇するが、そのメリットは投資をはるかに上回る:
- 保証クレームの減少
- コンポーネント寿命の延長
- 顧客満足度の向上
- 総所有コストの低減
私たちは、製造時の精度に投資することで、長期的なメンテナンスや交換費用を約3~4倍節約できることを発見しました。
先端技術はピストン加工をどのように強化するか?
想像してみてほしい:たったひとつのピストンの欠陥が、エンジンの致命的な故障につながる可能性があるのです。PTSMAKEでの15年以上の勤務で、私は先端技術がピストン製造を芸術から精密な科学に変えたことを目の当たりにしてきました。
最新のピストン加工は、5軸CNCマシン、レーザー技術、スマート計測システムとインダストリー4.0の統合を組み合わせています。これらの技術革新は、前例のない精度、一貫性、効率を実現すると同時に、ヒューマンエラーと製造コストを削減します。
5軸CNC加工の革命
グローバルな自動車メーカーと仕事をしてきた経験から、5軸CNCマシンはピストン生産に革命をもたらしました。これらのシステムは、1回のセットアップで複雑な形状を加工することができ、生産時間を大幅に短縮し、精度を向上させます。5軸CNCマシンの特徴は以下の通りです:
特徴 | ベネフィット |
---|---|
同時5軸動作 | 複雑なサーフェスを再位置決めなしで加工 |
高度なツールパスの最適化 | サイクルタイムの短縮と表面仕上げの向上 |
統合プローブシステム | リアルタイム寸法検証 |
自動工具交換 | 運転休止時間の最小化 |
レーザー加工:光速の精度
レーザー加工は、現代のピストン製造に欠かせないものとなっています。PTSMAKEでは、この技術を使用しています:
- オイル保持溝の微細加工
- 潤滑性向上のための表面テクスチャリング
- リング溝の高精度切削
- 品質管理マーキングとトレーサビリティ
スマート計測と品質管理
品質管理は、高度な計測機器によって劇的に進化しました。私たちの施設では
- 三次元座標測定機(CMM)
- 光学測定システム
- 表面粗さ計
- 非接触レーザースキャナー
これらのシステムはリアルタイムのフィードバックを提供し、すべてのピストンが正確な仕様を満たしていることを保証します。
インダストリー4.0の統合と自動化
インダストリー4.0の原則の導入により、私たちの生産現場は一変しました。主なコンポーネントは以下の通りです:
システム | 機能 |
---|---|
IoTセンサー | リアルタイムプロセス監視 |
機械学習 | 予知保全 |
デジタルプロセス制御 | 自動化された品質チェック |
データ分析 | 生産最適化 |
ダイヤモンドライクカーボン(DLC)コーティングの革新
DLCコーティングは、ピストン技術における大きな進歩です。我々のテストに基づくと
- 摩擦を最大40%低減
- 耐摩耗性が200%向上
- 燃費の向上
- ピストンの寿命を大幅に延長
デジタル・ツインとプロセス・シミュレーション
デジタルツイン技術は、ピストン加工へのアプローチに革命をもたらしました。私たちはこれを次のような用途に使用しています:
- 仮想プロセス最適化
- 工具摩耗の予測
- 生産前に潜在的な問題を特定
- オペレーターの安全なトレーニング
高度工具管理システム
近代的な工具管理は、効率的なオペレーションに欠かせないものとなっている:
- 自動工具寿命モニタリング
- スマートな工具選択アルゴリズム
- 統合された工具在庫管理
- リアルタイム摩耗検知
環境と効率のメリット
これらの技術は環境面で大きなメリットをもたらす:
- カッティングパスの最適化により、材料の無駄を削減
- スマートな電源管理でエネルギー消費を低減
- 最適化されたデリバリーシステムにより、クーラント使用量を最小化
- 生産量当たりの二酸化炭素排出量を削減
PTSMAKEでの15年以上の勤務の中で、私はこれらの技術がピストン加工を、手作業でミスの起こりやすい工程から、高度に自動化された精密な作業へと変えてきたことを目の当たりにしてきました。5軸CNCマシン、レーザー技術、スマートシステムの組み合わせにより、品質が向上しただけでなく、生産コストも大幅に削減されました。インダストリー4.0の原則を統合することで、自動車業界のお客様からますます厳しくなる仕様に対応しながら、競争力を維持することができます。
将来はさらにエキサイティングな展開が約束されています。私たちは現在、AIを活用した最適化システムと、ピストン製造にさらなる革命をもたらす可能性のある先端材料を探求しています。このような技術進化を目の当たりにしてきた者として、これらの進歩により、精密ピストン製造はかつてないほど身近で信頼できるものになったと自信を持って言えます。
高精度ピストン製造が求められる産業とは?
PTSMAKEに15年以上勤務する中で、精密ピストンがいかに重要な機械を左右するかを目の当たりにしてきました。ほんの小さな欠陥が致命的な故障につながり、何百万ドルもの損害とダウンタイムをもたらすのです。
高精度のピストン製造は、自動車、航空宇宙、船舶、産業機械の4つの主要産業にとって極めて重要です。各分野では、レーシングエンジン用の軽量素材や船舶用途の耐腐食性など、特定のピストン特性が要求されます。
自動車業界の要件
大手自動車メーカーと仕事をしてきた者として、彼らの厳しい要求を理解しています。自動車部門では、性能と信頼性の両方を実現するピストンが求められています。
主な要件は以下の通り:
- 燃費を向上させる軽量素材
- 燃焼室の高温耐性
- 最適な圧縮比のための精密な公差
- 長寿命を実現する耐久性
あるレーシング・チームが、高度なピストン設計と素材の選択によって、エンジンの重量を15%削減するのを支援したプロジェクトを覚えています。その結果は、加速の向上と燃費の改善という素晴らしいものでした。
航空宇宙用途
航空宇宙産業では、失敗は許されません。私の経験では、航空宇宙産業のクライアントの要求は最も厳しいものです:
必要条件 | 仕様 | 目的 |
---|---|---|
素材グレード | 航空宇宙認定合金 | 安全コンプライアンス |
表面仕上げ | Ra 0.4μm以上 | 摩擦の低減 |
寸法公差 | ±0.005mm | パーフェクトフィット |
体重の変化 | 最大±0.1g | バランス要件 |
マリンエンジン仕様
海洋環境には独特の課題があります。海水、絶え間ない振動、高荷重の組み合わせは、特殊なソリューションを必要とします:
- 耐食性素材(通常は船舶用ステンレス鋼)
- シーリング性能の向上
- ヘビーデューティ仕様
- 塩水保護のための特殊コーティング
産業機械需要
産業機械の分野では、カスタマイズの傾向が強まっている。それぞれの用途に特有の配慮が必要です:
重機
- 耐久性の向上
- 高負荷容量
- 費用対効果の高いメンテナンス
製造設備
- 精密な動き
- 連続運転能力
- 迅速な交換オプション
発電
- 最大効率
- サービス間隔の延長
- 環境コンプライアンス
精密加工によるカスタムソリューション
PTSMAKEでは、このような多様な要件を満たすために、専門的なプロセスを開発しました。私たちのアプローチには以下が含まれます:
高度な素材選択
- 航空宇宙用チタン合金
- 自動車用高強度アルミニウム
- 船舶用特殊合金鋼
- ユニークなアプリケーションのためのカスタム素材
精密製造技術
- 複雑形状の5軸CNC加工
- 高度な表面仕上げ
- 総合的な品質管理
- 工程内検査
品質保証プロトコル
- 100% 重要寸法検査
- 材料認証
- パフォーマンステスト
- 文書化とトレーサビリティ
私はこれまでのキャリアを通じて、適切なピストン製造がいかに機器の性能に大きな影響を与えるかを目の当たりにしてきました。例えば、ある船舶用エンジンメーカーでは、革新的な材料選定と表面処理により、メンテナンス間隔を40%延長することができました。
業界別ソリューション
各業界は独自のソリューションを必要としている:
自動車レース
- 超軽量設計
- 高強度素材
- パフォーマンスのために最適化されたジオメトリー
民間航空
- 認証された素材とプロセス
- 完全な文書化
- 定期的な監査への対応
マリンアプリケーション
- 耐腐食設計
- 強化されたシーリングシステム
- 堅牢な構造
産業システム
- アプリケーション固有のカスタマイズ
- 費用対効果の高いソリューション
- メンテナンスに配慮した設計
高精度ピストン製造の成功の鍵は、これらの特定の要件を理解し、一貫して満たす能力を持つことです。PTSMAKEでは、このような要求の厳しい業界に効果的に対応するため、技術と専門知識の両方に投資してきました。
多様なアプリケーションの経験を通じて、当社は最高水準の品質と精度を維持しながら、業界固有の要件を満たすための包括的なアプローチを開発しました。この専門知識により、それぞれ独自の課題と仕様を持つ複数のセクターにおいて、信頼できるパートナーとしての役割を果たすことができます。
ピストン加工で直面する課題とは?
ピストン加工に関しては、わずかな狂いが致命的なエンジンの故障につながる可能性があります。精密製造に15年以上携わってきた私は、プロジェクトの成否を左右する数え切れないほどの課題を見てきました。
ピストン加工における主な課題には、厳しい公差(多くの場合、±0.005mm以内)の維持、材料のばらつきへの対応、熱処理問題の管理、複雑な形状を加工する際の工具摩耗の制御などがあります。これらの課題には、高度なソリューションと専門知識が必要です。
素材関連の課題
PTSMAKEでの数年間、私は材料の不一致が最も頻繁に起こる課題の一つであることを観察してきました。同じ材料でもロットが異なれば特性も異なり、加工パラメーターや最終結果に影響を与えます。
素材問題 | インパクト | ソリューション |
---|---|---|
硬度の変化 | 一貫性のない工具摩耗 | 定期的な材料試験 |
内部ストレス | 寸法変更 | 適切なストレス解消 |
多孔性 | 表面仕上げの問題 | 材料認証 |
化学組成 | 工具寿命の短縮 | サプライヤー資格 |
耐性コントロールの課題
厳しい公差を維持することは、ピストンの性能にとって極めて重要です。自動車業界のお客様との経験に基づき、0.01mmの誤差でもエンジン効率に影響を与えます。
特徴 | 標準公差 | 重要な要素 |
---|---|---|
直径 | ±0.005mm | 温度制御 |
丸み | ±0.003mm | 固定安定性 |
表面仕上げ | Ra 0.4 | 切削パラメータ |
溝幅 | ±0.008mm | ツール選択 |
熱処理による合併症
私が遭遇した最も困難な側面のひとつは、機械加工中の熱関連の問題を管理することだ:
- 切断時の熱膨張
- 熱処理後の歪み
- 冷却速度制御
- 温度の均一性
工具摩耗管理
PTSMAKEでは、工具の磨耗に対処するためにいくつかの戦略を導入している:
- 高度なコーティング技術
- 最適化された切削パラメータ
- 定期的な工具の状態監視
- 戦略的ツールパス計画
複雑な形状の課題
現代のピストンの複雑な設計は、ユニークな課題を提示している:
- 深溝加工
- 薄肉部
- アンダーカットの特徴
- ポート形状精度
プロセス・モニタリングの要件
継続的なモニタリングが不可欠であることがわかった:
- インプロセス測定
- リアルタイム工具摩耗検知
- サーマルモニタリング
- 振動解析
オペレーター・スキル要件
CNCオペレーションを管理した経験から言うと、オペレーターの専門知識は非常に重要だ:
- 材料の挙動を理解する
- プログラミングの専門知識
- セットアップの最適化
- 品質管理の知識
ソリューションの導入
PTSMAKEのアプローチには以下が含まれる:
- 高度なCAMソフトウェアの使用法
- カスタム治具開発
- 専用切削工具
- 定期的なオペレーター・トレーニング
- 品質管理の自動化
コスト管理の課題
品質とコスト効率を両立させるためには
コスト係数 | 経営戦略 |
---|---|
工具寿命 | 最適化された切削パラメータ |
サイクルタイム | 効率的なプログラミング |
セットアップ時間 | 標準化された手順 |
品質管理 | 自動検査 |
PTSMAKEでは、高度な技術、熟練したオペレーター、厳格な工程管理の組み合わせにより、これらの課題を克服することに成功しています。これにより、ピストン加工において99.7%のファーストパス歩留まり率を維持することができました。
これらの課題を理解し、対処することは、ピストン生産に携わるメーカーにとって極めて重要です。当社は、継続的な改善と技術への投資を通じて、生産効率を維持しながら一貫した品質を確保する強固なソリューションを開発してきました。
ピストン加工の将来動向は?
ピストン加工業界は劇的な変貌を遂げている。精密製造に15年以上携わる者として、私は伝統的な方法が革命的な技術に取って代わられるのを見てきました。
ピストン加工の未来は、積層造形、AI駆動プロセス、環境に優しい材料、進化するエンジン要件という4つの大きなトレンドによって形作られるでしょう。これらの技術革新は、ピストンの設計、製造、最適化の方法を変えつつあります。
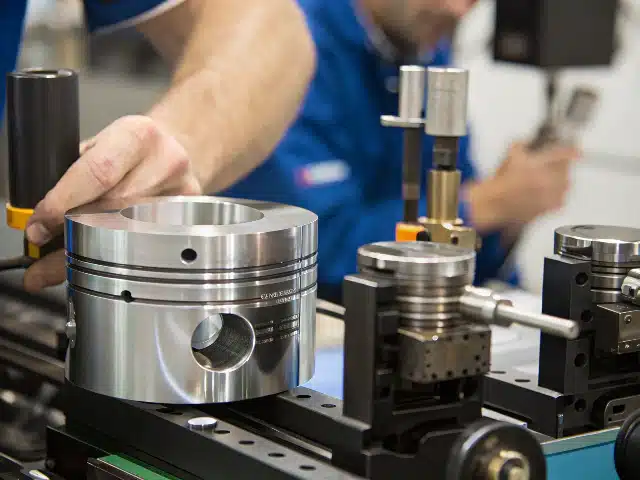
積層造形革命
PTSMAKEでの私の経験では、3Dプリンティングはピストンのプロトタイピングを大きく変えるものになりました。この技術により、以下のことが可能になりました:
- 従来の機械加工では不可能だった複雑な形状の作成
- プロトタイプ開発時間を60%短縮
- 複数の設計を迅速かつコスト効率よくテスト
- 内部構造を最適化した軽量ピストンを製造
AIと機械学習の統合
ピストン加工におけるAIの統合は、私たちの生産工程を大きく変えました。その活用方法をご紹介します:
AIアプリケーション | メリット | 生産への影響 |
---|---|---|
リアルタイム品質管理 | 99.9%欠陥検出 | 40%廃棄物の削減 |
予知保全 | 85%の故障予測精度 | 30%ダウンタイムの減少 |
プロセスの最適化 | 自動パラメータ調整 | 25%の効率改善 |
工具摩耗モニタリング | リアルタイムの工具状態トラッキング | 50%による工具不良の減少 |
環境に優しい素材と持続可能性
業界は持続可能な製造へとシフトしています。PTSMAKEでは、それを実践しています:
- 特性を向上させたリサイクル・アルミニウム合金
- 機械加工用バイオベース潤滑剤
- エネルギー効率の高い加工戦略
- 材料の最適利用による廃棄物の削減
電気およびハイブリッド・エンジンの要件
電気自動車やハイブリッド車の台頭は、ピストン設計に対する新たな要求を生み出した:
- 軽量素材による効率の向上
- 強化された熱管理能力
- より高い耐久性
- 摩擦低減のための特殊コーティング
スマート製造システム
私たちの工場はインダストリー4.0のコンセプトを取り入れています:
- 接続されたマシニングセンターがリアルタイムデータを共有
- プロセスシミュレーションのためのデジタルツイン技術
- 継続的モニタリングのためのIoTセンサー
- クラウドベースの生産管理
高度な表面処理
現代のピストンは、高度な表面仕上げを必要とする:
- 耐摩耗性プラズマコーティング
- ダイヤモンドライクカーボン(DLC)処理
- レーザー表面テクスチャリング
- ナノスケールの表面改質
品質管理の進化
新しい検査方法を導入した:
テクノロジー | 申し込み | 精度レベル |
---|---|---|
3Dスキャン | 寸法検証 | ±0.001mm |
X線分析 | 内部構造検査 | 99.8%検出率 |
サーマルイメージング | 熱分布分析 | 分解能±0.1 |
表面粗さ試験 | 仕上げの品質管理 | Ra 0.1μm精度 |
コスト最適化戦略
現代のピストン製造では、技術革新とコストのバランスを取ることが求められる:
- 自動マテリアルハンドリングシステム
- 最適化された切削パラメータ
- セットアップ時間の短縮
- 工具寿命管理の強化
今後の課題と解決策
私の経験によれば、この業界はいくつかの課題に直面している:
- ますます厳しくなる公差への対応
- 新素材への対応
- 生産コストの管理
- 新技術に対応した労働力の育成
このような課題に対処するために、私たちPTSMAKEは次のようなことを行っている:
- 高度なトレーニングプログラムへの投資
- ハイブリッド製造ソリューションの開発
- 柔軟な生産システムの導入
- 研究機関との協力
環境コンプライアンス
将来のピストン加工は、環境問題に対応しなければならない:
- 製造における二酸化炭素排出量の削減
- 廃棄物の発生を最小限に抑える
- エネルギー効率の高いプロセス
- 持続可能な素材調達
この業界に15年以上身を置く中で、私はピストン加工における目覚ましい変化を見てきました。今後は、特にAI統合、持続可能な製造、先端材料などの分野で、さらに大きなイノベーションが求められるでしょう。PTSMAKEでは、このようなトレンドを先取りし、新しい技術や持続可能な手法を取り入れながら、最高品質のピストンを確実にお届けできるよう、常にプロセスを適応させています。
ピストン加工はどのように性能と信頼性を高めるのか?
なぜ、あるエンジンは長持ちするのに、あるエンジンは早く故障してしまうのか不思議に思ったことはありませんか?私は15年以上精密機械加工に携わり、ピストンの品質がいかに大きな違いを生むかを見てきました。
精密ピストン加工は、最適な圧縮を確保し、摩擦を低減し、一貫した熱特性を維持することで、エンジンの性能と信頼性に直接影響します。高品質の機械加工ピストンは、燃費を最大15%向上させ、エンジン寿命を大幅に延ばすことができます。
エンジン性能への影響
私は大手自動車メーカーと仕事をしてきた経験から、精密機械加工されたピストンは3つの主要な性能上の利点をもたらすと見てきた:
圧縮率の向上
- より厳しい公差が最適な圧縮を維持
- ピストンとシリンダーウォール間のシール性向上
- 出力と効率の向上
摩擦の低減
- より滑らかな表面仕上げ
- 機械損失の低減
- 燃費の向上
優れた熱管理
- 均一な熱膨張
- より優れた放熱性
- 熱ストレスのリスクを低減
燃費改善
PTSMAKEでのテストデータから、適切に加工されたピストンは燃費を向上させることができる:
改善要因 | 燃料節減の可能性 |
---|---|
摩擦の低減 | 3-5% |
より良い圧縮 | 5-7% |
最適重量 | 2-3% |
インパクト | 10-15% |
排出削減効果
最新の排気ガス規制では、正確なピストン仕様が要求されます。高品質の機械加工がどのように役立つかをご紹介します:
より良い燃焼制御
- 精密なクラウン形状
- 最適な火炎伝播
- 未燃焼燃料の低減
オイル消費量の低減
- 正確なリング溝寸法
- 適切なリングの取り付け
- オイル焼けを最小限に抑える
エンジン寿命の延長
長年の製造業の経験を通じて、私はいくつかの長寿の要因を特定した:
素材の完全性
- 適切な応力分布
- 摩耗パターンの低減
- 耐久性の向上
寸法安定性
- 一貫したクリアランス
- バランス運転
- 振動の低減
製造精度要件
PTSMAKEでは、厳格な公差を維持しています:
コンポーネント | 許容範囲 |
---|---|
スカート直径 | ±0.005mm |
ピンボア | ±0.002mm |
リング溝 | ±0.008mm |
クラウンの高さ | ±0.010mm |
品質管理対策
当社の品質保証プロセスには以下が含まれる:
高度な測定
- 3次元座標測定
- 表面粗さ試験
- 真円度の検証
パフォーマンス・テスト
- 応力シミュレーション
- サーマルサイクリング
- 耐摩耗性評価
先進製造技術の役割
現代のピストン製造には、それが必要だ:
5軸CNC加工
- 複雑な形状に対応
- シングルセットアップ完了
- 精度の向上
先端材料加工
- 熱処理の最適化
- 表面強化
- コーティング
経験豊富なメーカーとの提携
適切な製造パートナーを選ぶことは非常に重要です。主な検討事項は以下の通り:
技術力
- 最新設備
- プロセス制御
- 品質システム
業界経験
- 実績
- 業界資格
- エンジニアリング・サポート
生産の柔軟性
- プロトタイプの能力
- ボリュームのスケーラビリティ
- 迅速な対応
私はこれまでのキャリアの中で、適切なピストン加工がエンジンの故障と卓越した性能の違いを生んだ例を数え切れないほど見てきました。精密な製造とエンジンの信頼性の関係は、直接的で測定可能です。これらの重要な関係を理解している経験豊富なメーカーと協力することは、最適な結果を得るために不可欠です。
PTSMAKEの私の見解では、高品質のピストン加工に投資することは、単に仕様を満たすことではなく、長期的な性能、信頼性、顧客満足を確保することです。精密製造への初期投資は、効率の向上、排出ガスの削減、エンジン寿命の延長という形で配当されます。
ピストン加工に関しては、精度は単なる目標ではなく、最新のエンジン性能と信頼性の要件であることを忘れないでください。