Large Part Injection Molding Service
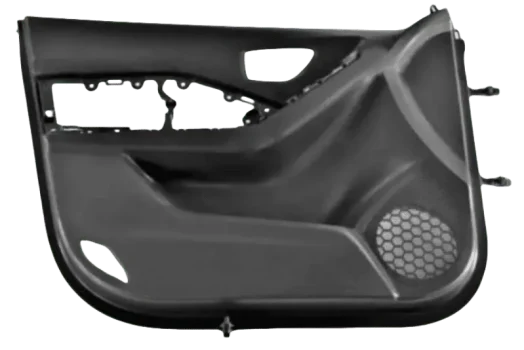
LOW MOQ 100 PCS
Complex Part Precision Molding
Fast Turnaround & Global Shipping
Machines Ranging From 30 Tons to 1,600 Tons








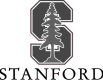
What Our Clients Say
Our clients are located worldwide, and their feedback speaks for itself. If you’d like to verify our reputation with customers in your area, don’t hesitate to contact us—we’d be happy to connect you with them and share relevant case studies.
8 Key Industries Relying on Large Part Injection Molding Solutions
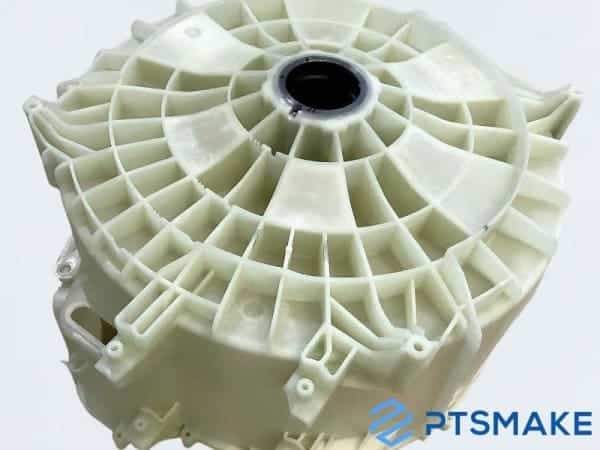
Home Appliances
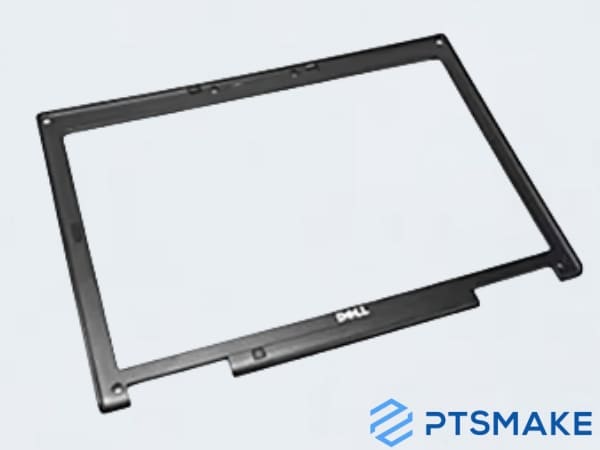
Consumer Electronics
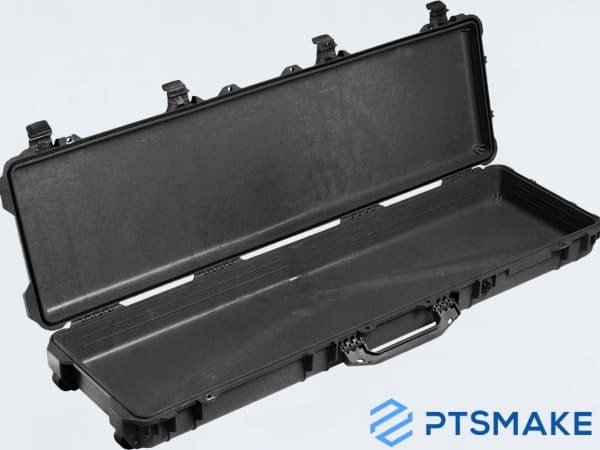
Industrial Machinery
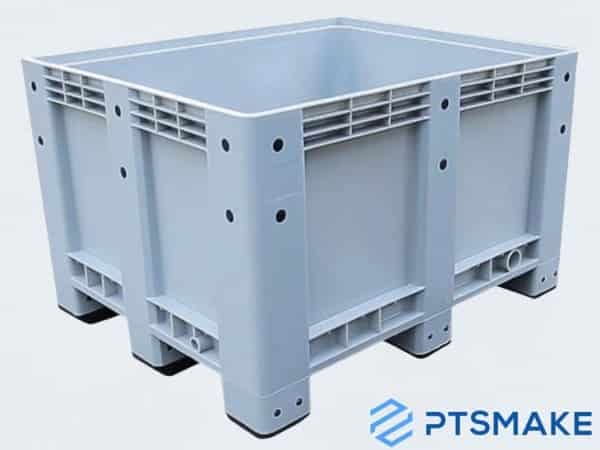
Logistics & Storage
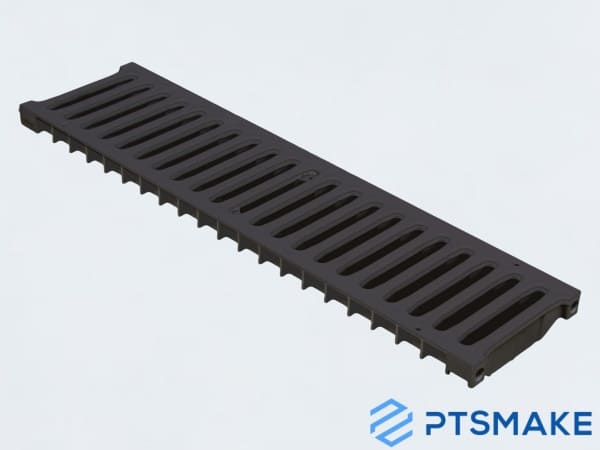
Construction & Building Materials
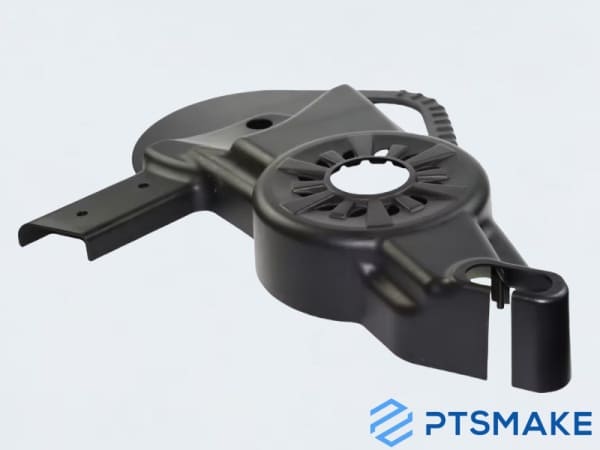
Sports & Fitness Equipment
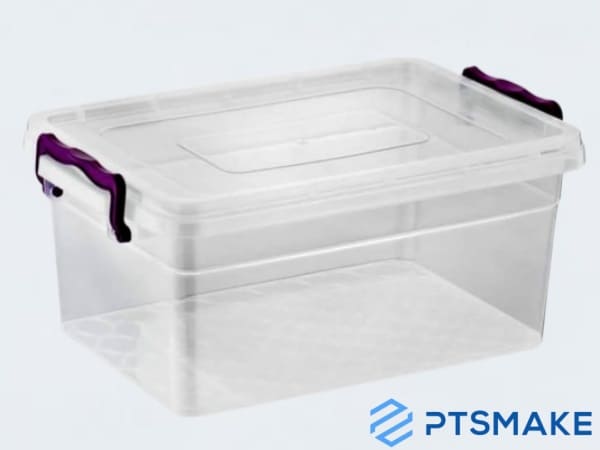
Medical Equipment
Why Choose PTSMAKE for Large Part Injection Molding?
PTSMAKE has over 20 years of injection molding experience, providing solutions trusted by global brands like BMW and Huawei.
Utilizing advancedmachines, we ensure dimensional accuracy and optimize designs, reducing production costs by up to 30%.
Our 50+ advanced molding machines enable 15-day prototype cycles and 30% faster production timelines.
Our 3-stage quality checks maintain a defect rate below 0.2% with full traceability for every molded parts.
How We Ensure Quality Control in Large Part Injection Molding at PTSMAKE
- At PTSMAKE, quality control starts before production begins. Our team reviews every design for large part injection molding projects to identify potential flaws. We use advanced simulation software to predict material flow, cooling patterns, and structural integrity. This helps us prevent defects like warping or sink marks in your large plastic components.
- We maintain strict control over raw materials for injection molding. All polymer resins undergo thorough testing for viscosity, melt flow rate, and thermal stability. Our material traceability system tracks every batch from supplier to finished part. This ensures consistency across production runs, even for complex geometries common in automotive and aerospace applications.
- Our injection molding machines feature real-time monitoring systems. Temperature, pressure, and cycle times get tracked automatically during large part production. If any parameter deviates from set standards, our technicians receive immediate alerts. This proactive approach prevents quality issues rather than detecting them after production.
- Every molded large part undergoes dimensional verification using CMM (Coordinate Measuring Machines). We check critical features against CAD models with ±0.01mm accuracy. For high-stress applications like robotics components, we perform additional load testing and fatigue analysis. Our quality reports include detailed measurements and process data for complete transparency.
- PTSMAKE maintains ISO 9001 certification with documented quality procedures. Our quality team conducts regular audits of production processes and equipment calibration. We provide customers with first-article inspection reports and random sampling data. This systematic approach has helped us maintain 99.3% on-time delivery with zero critical defects since 2010.
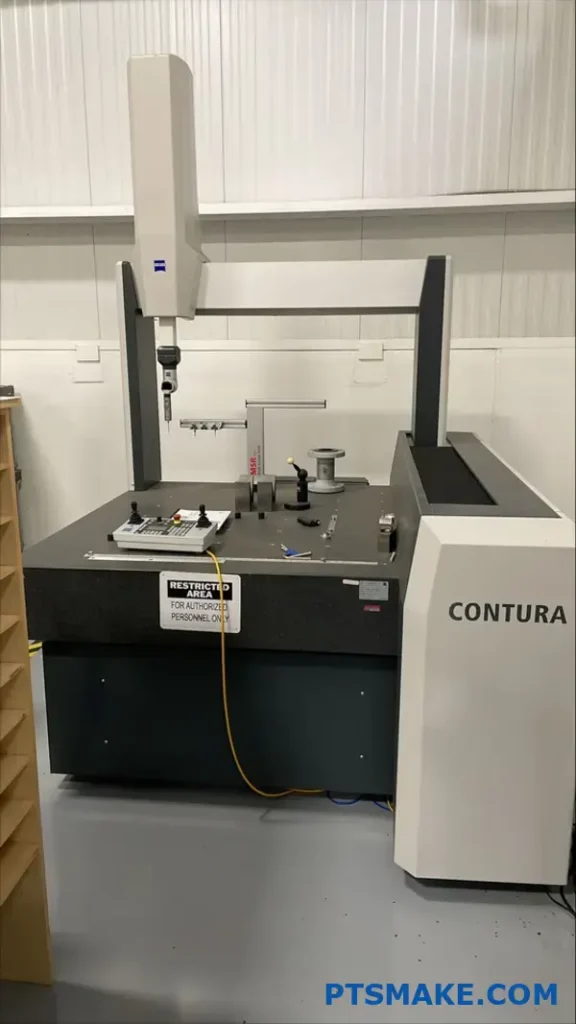
"PTSMAKE delivered **large plastic housings** for our robotics project with **0.2mm tolerance**. Their team fixed a warping issue fast and shipped samples in 18 days. Perfect for tight deadlines
Jake Miller, Production Director, USA"
Top Materials Used in Large Part Injection Molding
Polypropylene (PP)
ABS
Polyethylene (PE)
Polycarbonate (PC)
Nylon (PA)
POM
PET
TPE
Typical Lead Times for Large Part Injection Molding
Balancing speed and precision in manufacturing timelines
- Manufacturers often ask, “How long does large part injection molding take?” At PTSMAKE, we deliver prototypes in 7-15 days and production batches in 3-5 weeks. Lead times depend on mold complexity, material availability, and order size. We optimize schedules using our in-house mold-making team and automated production systems.
- Large parts require extra care. Thicker walls and complex geometries add cooling and quality-check steps. For example, automotive components may need 10% more time than standard parts. We reduce delays by pre-testing materials and using multi-cavity molds for high-volume orders.
- Your timeline matters. Our 24/7 project tracking portal lets you monitor progress in real-time. We assign a dedicated engineer to every order, ensuring fast communication. With 20+ years of experience, we’ve shortened lead times by 18% since 2010 while maintaining ISO-certified quality.
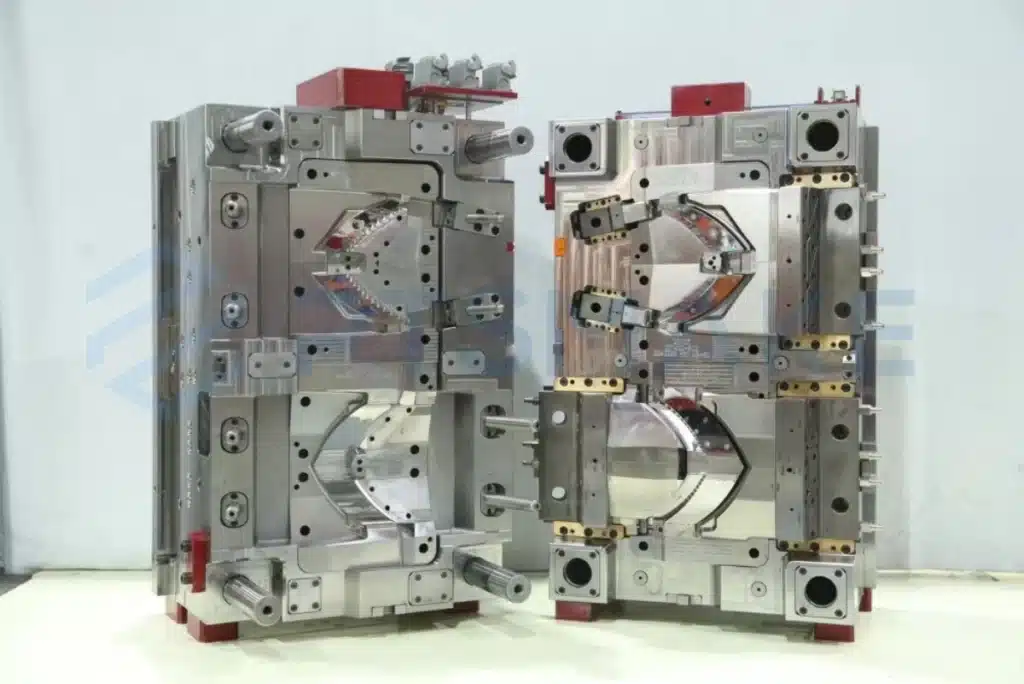
Steps for Large Part Injection Molding Manufacturing
1. Material Selection
2. Mold Design
3. Prototype Testing
4. Machine Setup
5. Process Optimization
6. Quality Inspection
7. Post-Processing
8. Packaging & Delivery
Request a Custom Quote Today
Get an accurate estimate for your project today. Let us help you meet your exact specifications.
Cost-Effective Solutions for Large Part Injection Molding
1. Material Optimization
2. Mold Design Efficiency
3. Automation Integration
4. Energy-Efficient Machinery
5. Bulk Production Planning
6. Design Simplification
7. Secondary Process Elimination
Customization Options for Large Part Injection Molding
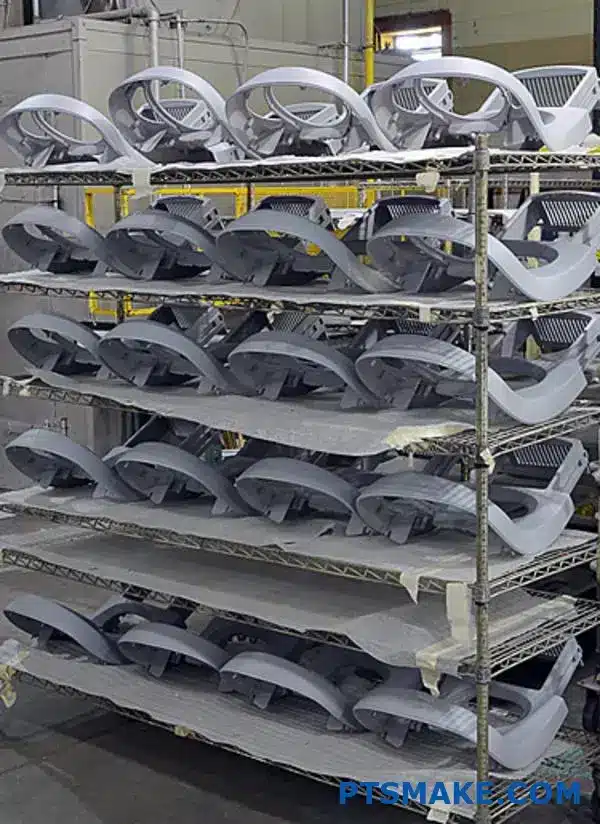
Custom Material Selection for Large Part Injection Molding
PTSMAKE offers 50+ engineering-grade plastics for large part injection molding projects. We help clients choose materials based on mechanical strength, temperature resistance, and chemical compatibility requirements. Our team works with ABS, Polycarbonate, Nylon, PEEK, and custom polymer blends for specialized applications.
For medical or food-grade projects, we provide USP Class VI and FDA-compliant materials. Our material experts optimize resin selection to balance performance with production costs. This ensures your large molded parts meet exact functional needs without overspending.
Advanced Tooling Design Options
Our engineers create custom injection molds using Siemens NX software. We design multi-cavity tools and insert molds for high-volume production. For large parts exceeding standard machine sizes, we utilize 4,500T clamping force machines with 6m x 3m platens.
PTSMAKE handles undercuts and thin-wall designs (as low as 0.5mm) through our patented side-action mechanisms. All molds include temperature control channels to prevent warping in large components. We implement real-time pressure monitoring to ensure consistent filling.
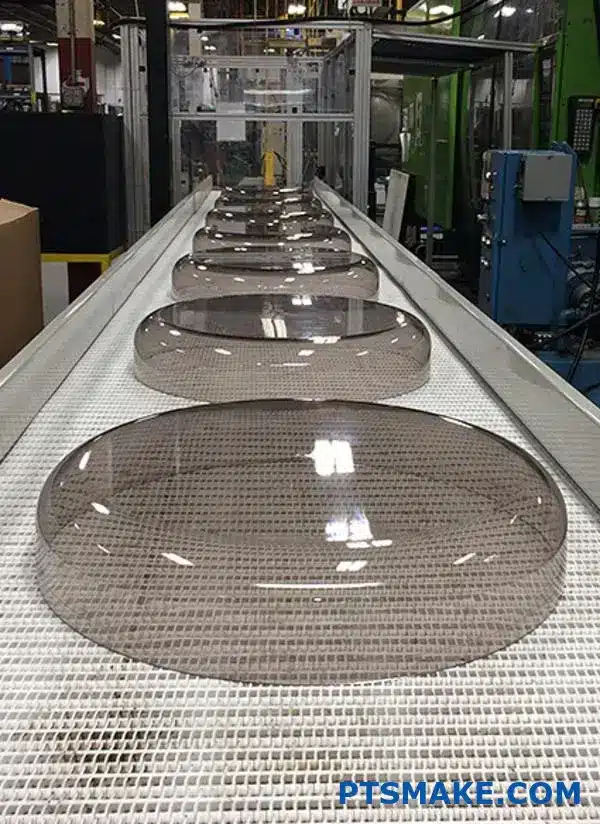
Surface Finish Customization
Choose from 12 standard surface finishes or request custom patterns. Our texturing capabilities include leather grains, matte finishes, and high-gloss polishing (Ra 0.05μm). For technical parts, we offer anti-slip textures or light-diffusing surfaces.
Secondary operations include painting, pad printing, and laser etching. We maintain color consistency across batches using Pantone-matching systems. All finishes undergo adhesion testing to guarantee durability.
Production Scale Flexibility
PTSMAKE supports all production stages. Get functional prototypes in 7-10 days using aluminum molds. Our bridge tooling solution delivers 500-5,000 parts while final steel molds are being made. For mass production, we operate 24/7 with automated quality checks.
Our ISO 9001-certified facility handles parts up to 150kg with ±0.15mm tolerance. We maintain separate production lines for medical-grade and industrial components to prevent contamination.
Success Stories: Large Part Injection Molding Solutions
Automotive Parts
A leading automotive parts supplier needed large plastic housings for electric vehicle battery systems. Their previous vendor struggled with warping and inconsistent wall thickness, causing assembly line delays. PTSMAKE redesigned the mold with conformal cooling channels and implemented real-time pressure monitoring during production. This reduced cycle time by 18% while maintaining ±0.15mm dimensional accuracy across 1.2-meter-long components. The client now produces 8,000 units monthly with zero assembly rejections since switching to our large part injection molding services.
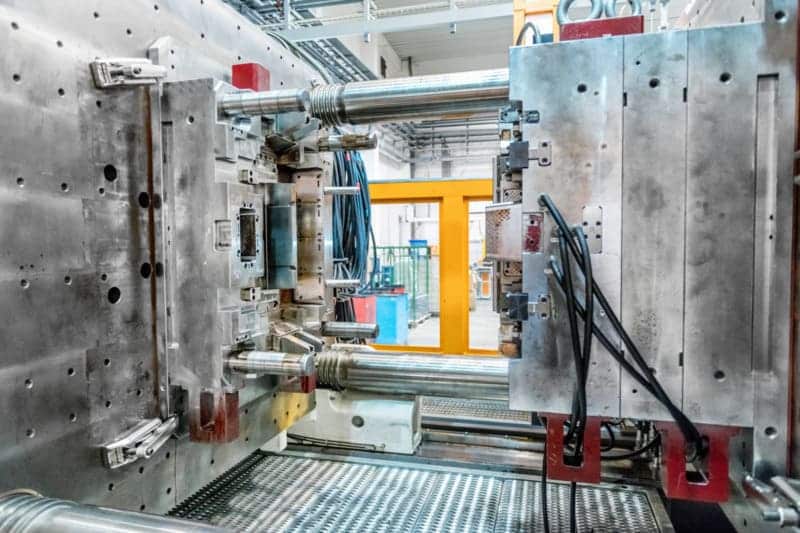
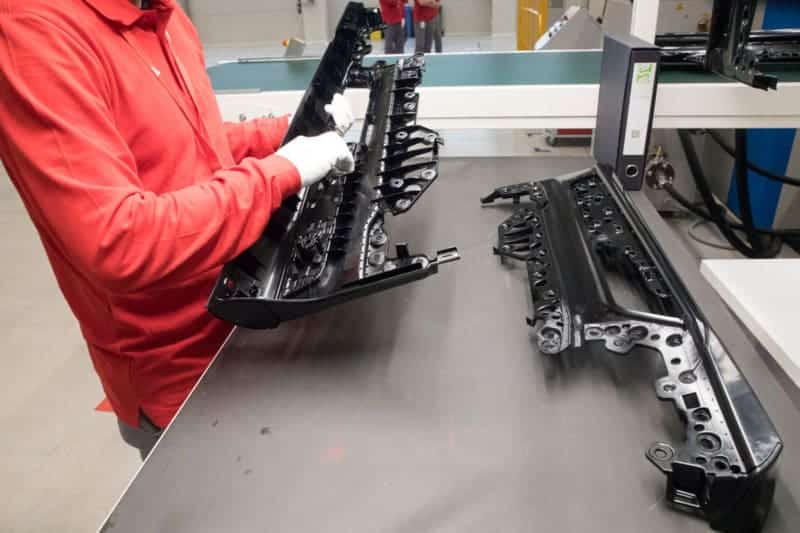
Medical Equipment
A medical equipment manufacturer required FDA-compliant MRI machine covers measuring 1.5m x 0.8m. Their existing supplier couldn’t eliminate flow lines and sink marks on the visible surfaces. Our team developed a three-stage gas-assisted injection process using medical-grade polycarbonate. We achieved Class A surface finish without post-processing while meeting strict biocompatibility standards. The solution cut their per-unit costs by 22% compared to traditional machining methods.
Industrial Robotics
An industrial robotics company needed durable nylon housing for heavy-duty automation systems. Competing proposals either exceeded budget or compromised on impact resistance. PTSMAKE created a hybrid approach combining insert molding and our proprietary fiber-reinforcement technique. The resulting components withstand 15% higher torque loads than specifications required while maintaining 0.05mm positional accuracy across mating surfaces.
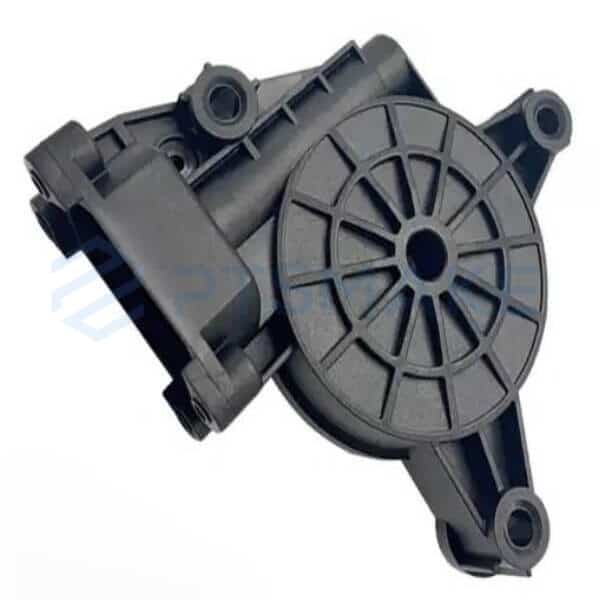
Contact Custom Large Part Injection Molding Expert Today!
We look forward to the opportunity to work with you and contribute to your project’s success.