Worstelt u met het vinden van het juiste materiaal voor veeleisende toepassingen waar standaard kunststoffen het laten afweten? Veel ingenieurs worden geconfronteerd met uitdagingen wanneer onderdelen bestand moeten zijn tegen extreme temperaturen, chemicaliën of mechanische spanning. Traditionele kunststoffen houden het gewoon niet vol, wat leidt tot veelvuldige defecten en dure vervangingen.
PEEK verspanen is het proces van snijden, boren en vormen van polyetheretherketone (PEEK) materiaal met behulp van CNC machines. Deze hoogwaardige thermoplast biedt een uitzonderlijke hittebestendigheid tot 480°F, een uitstekende chemische weerstand en een sterkte die vergelijkbaar is met die van sommige metalen.
Ik heb met talloze klanten gewerkt die voor hun kritieke onderdelen zijn overgestapt op machinale bewerking met PEEK. De resultaten spreken voor zich: onderdelen die langer meegaan, betere prestaties onder zware omstandigheden en kortere onderhoudscycli. Als je je afvraagt of PEEK de oplossing is voor jouw toepassing, lees dan verder om de unieke eigenschappen en bewerkingstechnieken te ontdekken die dit materiaal zo waardevol maken voor precisiefabricage.
Is PEEK beter dan Delrin voor machinale bewerking?
Hebt u ooit midden in een dilemma bij de materiaalselectie gestaan, verscheurd tussen PEEK en Delrin voor uw kritieke engineeringproject? Wanneer prestaties van belang zijn en falen geen optie is, kan het kiezen van de verkeerde kunststof leiden tot voortijdige slijtage, stilstand van apparatuur en kostbare herontwerpen.
Terwijl PEEK superieure temperatuurbestendigheid (tot 480°F), uitzonderlijke chemische stabiliteit en hogere sterkte biedt, zorgt Delrin (POM) voor betere bewerkbaarheid, maatvastheid en lagere kosten. De "betere" keuze hangt volledig af van uw specifieke toepassingseisen en budgetbeperkingen.
Begrijpen van PEEK en Delrin: Fundamentele verschillen
Bij het vergelijken van deze twee hoogwaardige technische kunststoffen is het belangrijk om hun basissamenstelling en eigenschappen te begrijpen. PEEK (Polyetheretherketone) is een semikristallijne thermoplast met een uitzonderlijke weerstand tegen thermische degradatie, terwijl Delrin (Polyoxymethylene of POM) een acetal homopolymeer is dat bekend staat om zijn uitstekende dimensionale stabiliteit.
Vergelijking van materiaaleigenschappen
De fysische en mechanische eigenschappen van deze materialen hebben een grote invloed op hun bewerkingseigenschappen en prestaties bij het eindgebruik.
Eigendom | PEEK | Delrin (POM) |
---|---|---|
Temperatuur warmteafbuiging | 157°C (315°F) | 257°F (125°C) |
Treksterkte | 14.500 psi | 10.000 psi |
Chemische weerstand | Uitstekend (weerstaat de meeste zuren en basen) | Goed (kwetsbaar voor sterke zuren) |
Slijtvastheid | Superieur | Zeer goed |
Kostenfactor | 4-5× hoger dan Delrin | Matig |
Dichtheid | 1,32 g/cm³ | 1,41 g/cm³ |
Bewerkingseigenschappen: Hoe ze presteren onder het gereedschap
Mijn ervaring bij PTSMAKE is dat bewerkbaarheid vaak de doorslaggevende factor is bij de keuze tussen deze materialen. Delrin machinaal bewerkt over het algemeen voorspelbaarder dan PEEK en produceert gladdere oppervlakteafwerkingen met minder moeite.
Gereedschapsslijtage en snijparameters
PEEK is abrasiever voor snijgereedschappen, waardoor vaker van gereedschap gewisseld moet worden. Bij het bewerken van PEEK verlagen we de snijsnelheden meestal met ongeveer 15-20% ten opzichte van Delrin om de warmteontwikkeling te minimaliseren. Dit is cruciaal omdat de lage warmtegeleiding van PEEK warmteconcentratie veroorzaakt in de snijzone, waardoor mogelijk thermische vervorming1 als er niet goed mee wordt omgegaan.
Delrin daarentegen biedt een uitstekende maatvastheid tijdens het bewerken en kan op hogere snelheden worden gesneden. Het veroorzaakt minder gereedschapsslijtage en vereist over het algemeen minder gespecialiseerde bewerkingstechnieken.
Overwegingen voor oppervlakteafwerking
Een voordeel van Delrin is dat het een uitstekende oppervlakteafwerking kan bereiken met standaard bewerkingsparameters. PEEK vereist vaak extra polijststappen om een vergelijkbare oppervlaktekwaliteit te bereiken.
Kosten-batenanalyse voor technische toepassingen
Het kostenverschil tussen deze materialen kan aanzienlijk zijn. PEEK kost doorgaans 4 tot 5 keer meer dan Delrin, waardoor het belangrijk is om te evalueren of de premium eigenschappen de investering rechtvaardigen.
Wanneer PEEK zijn hogere prijs rechtvaardigt
Ik raad PEEK aan voor toepassingen waarbij:
- Extreme bedrijfstemperaturen (boven 250°F)
- Agressieve chemische omgevingen
- Hoge mechanische belasting bij hoge temperaturen
- Medische of ruimtevaarttoepassingen waarbij biocompatibiliteit of vlambestendigheid vereist is
Wanneer Delrin de betere keuze is
Delrin is economisch zinvoller als:
- Bedrijfstemperaturen blijven onder 180°F
- Chemische blootstelling is beperkt tot matige oplosmiddelen
- Kostengevoeligheid is een belangrijke factor
- Onderdelen vereisen uitstekende maatvastheid en machinale precisie
- Hoge productievolumes maken materiaalkosten tot een belangrijke factor
Industriespecifieke overwegingen
Verschillende industrieën geven de voorkeur aan verschillende materiaaleigenschappen. In de lucht- en ruimtevaart, waar we tal van onderdelen hebben geleverd, rechtvaardigen de vlambestendigheid en uitzonderlijke sterkte-gewichtsverhouding van PEEK vaak de hogere kostprijs. Voor toepassingen in de auto-industrie wint Delrin het vaak van de combinatie van redelijke kosten en goede mechanische eigenschappen.
Medische en voedselverwerkingstoepassingen
Voor medische apparatuur zijn de biocompatibiliteit en sterilisatiebestendigheid van PEEK van onschatbare waarde, ondanks de hogere kosten. Voor voedselverwerkende apparatuur wordt vaak de voorkeur gegeven aan Delrin vanwege de FDA-conformiteit en de lagere kosten, tenzij het om hoge temperaturen gaat.
Industriële machineonderdelen
In industriële toepassingen heb ik de beslissing vaak zien afhangen van de bedrijfsomstandigheden. Tandwielen, lagers en slijtageonderdelen die onder gematigde omstandigheden werken, presteren uitstekend in Delrin, terwijl onderdelen die worden blootgesteld aan extreme omstandigheden profiteren van de superieure eigenschappen van PEEK.
De juiste keuze maken voor uw toepassing
De keuze tussen PEEK en Delrin moet worden gemaakt op basis van een grondige analyse van uw specifieke bedrijfsomstandigheden. Bij PTSMAKE houden we rekening met:
- Maximale bedrijfstemperatuur
- Chemisch blootstellingsprofiel
- Mechanische belastingseisen
- Budgettaire beperkingen
- Verwachte levensduur
Door deze factoren zorgvuldig te evalueren aan de hand van de eigenschappen van elk materiaal, kunt u een weloverwogen beslissing nemen waarbij prestaties en kosteneffectiviteit in balans zijn voor uw specifieke toepassing.
Wat is het verschil tussen acetaal en PEEK?
Ooit geworsteld met de keuze tussen acetaal en PEEK voor uw kritische technische componenten? Als het succes van een project afhangt van de materiaalkeuze, kan de verkeerde keuze leiden tot voortijdige defecten, onverwachte stilstand en budgetverpletterende herontwerpen die vermeden hadden kunnen worden met de juiste materiaalkennis.
Acetal (POM) en PEEK verschillen vooral in prestatiekenmerken en kosten. PEEK biedt een superieure hittebestendigheid (480°F vs 180°F), een betere chemische weerstand en een hogere sterkte, terwijl acetal een uitstekende bewerkbaarheid en maatvastheid biedt en aanzienlijk minder kost, waardoor het ideaal is voor minder veeleisende toepassingen.
Belangrijkste verschillen tussen Acetal en PEEK
Inzicht in de fundamentele verschillen tussen deze twee technische kunststoffen is cruciaal om weloverwogen beslissingen te kunnen nemen voor uw projecten. Beide materialen hebben zichzelf gevestigd als de beste opties voor precisiefabricage, maar ze dienen duidelijk verschillende doelen op basis van hun inherente eigenschappen.
Materiaalsamenstelling en structuur
Acetaal, algemeen bekend onder de merknaam Delrin (in homopolymeervorm) of onder de chemische naam polyoxymethyleen (POM), heeft een zeer kristallijne structuur met zich herhalende -CH₂O-groepen. Deze structuur geeft het een uitstekende dimensionale stabiliteit en bewerkbaarheid.
PEEK (polyetheretherketone) daarentegen behoort tot de polyaryletherketone familie en bevat aromatische ringen verbonden door ether- en ketonverbindingen. Deze moleculaire structuur zorgt voor een uitzonderlijke thermische stabiliteit en chemische weerstand.
Vergelijking van prestatiekenmerken
De prestatieverschillen tussen deze materialen maken ze geschikt voor verschillende toepassingen:
Eigendom | Acetaal (POM) | PEEK | Beste voor |
---|---|---|---|
Hittebestendigheid | 180°F (82°C) continu | 480°F (250°C) continu | PEEK |
Chemische weerstand | Goed (behalve sterke zuren) | Uitstekend (bestand tegen de meeste chemicaliën) | PEEK |
Treksterkte | 8.800-10.000 psi | 14.500-16.000 psi | PEEK |
Slijtvastheid | Zeer goed | Uitstekend | PEEK |
Bewerkbaarheid | Uitstekend | Goed (vereist gespecialiseerde technieken) | Acetaal |
Kostenfactor | Basisreferentie (1×) | 4-7× hoger dan acetaal | Acetaal |
Vochtabsorptie | 0.2-0.25% | 0.1-0.15% | PEEK |
Kosten-batenanalyse
In de jaren dat ik bij PTSMAKE met klanten werk, heb ik gemerkt dat kostenoverwegingen vaak de eerste materiaalkeuze bepalen. Acetal is aanzienlijk zuiniger dan PEEK, waardoor het de standaardkeuze is als er geen extreme omstandigheden zijn.
De hogere prijs van PEEK weerspiegelt de superieure prestaties. Om te beoordelen of de extra investering gerechtvaardigd is, moet u de volgende factoren in overweging nemen:
- Vereisten voor bedrijfstemperatuur
- Chemisch blootstellingsprofiel
- Mechanische belastingsniveaus
- Verwachte levensduur
- Stilstandkosten in verband met defecte onderdelen
Overwegingen bij machinale bewerking
Standtijd en snijparameters
Acetal staat bekend om zijn uitzonderlijke bewerkbaarheid. Het snijdt zuiver, houdt strakke toleranties en produceert uitstekende oppervlakteafwerkingen met minimale inspanning. Standaard hardmetalen gereedschap werkt goed en het materiaal veroorzaakt geen overmatige slijtage van het gereedschap.
PEEK biedt meer uitdagingen tijdens het bewerken. De hoge temperatuurbestendigheid betekent dat de warmteafvoer tijdens het bewerken slecht is, waardoor:
- Lagere snijsnelheden (meestal 20-30% langzamer dan acetal)
- Vaker wisselen van gereedschap
- Zorgvuldige aandacht voor warmteontwikkeling
- Gespecialiseerde koeltechnieken
Bij PTSMAKE hebben we specifieke protocollen voor thermisch beheer2 voor PEEK-bewerking om de maatnauwkeurigheid te garanderen en materiaaldegradatie tijdens het snijden te voorkomen.
Dimensionale stabiliteit
Acetal biedt een uitstekende maatvastheid na machinale bewerking, met minimale vervorming of spanningsontspanning. Dit maakt het bijzonder waardevol voor precisiecomponenten met nauwe toleranties.
PEEK heeft ook een goede maatvastheid, maar vereist voorzichtiger gloeiprocessen om de interne spanningen na machinale bewerking te verlichten. Zonder de juiste thermische conditionering kunnen PEEK onderdelen na verloop van tijd lichte dimensionale veranderingen ondergaan, vooral bij toepassingen met hoge precisie.
Toepassingsspecifieke aanbevelingen
Auto's en transport
In toepassingen voor de auto-industrie waar de temperaturen gematigd blijven (onder 180°F), biedt acetal vaak de beste waarde. Veel voorkomende toepassingen zijn:
- Onderdelen brandstofsysteem
- Deursluitmechanismen
- Interieurclips en bevestigingsmiddelen
- Lageroppervlakken in niet-kritieke gebieden
Voor zones met hogere temperaturen, zoals onderdelen onder de motorkap of onderdelen in de buurt van uitlaatsystemen, maakt de thermische stabiliteit van PEEK het ondanks de hogere kosten de betere keuze.
Medisch en farmaceutisch
De medische industrie heeft PEEK omarmd vanwege zijn biocompatibiliteit en bestendigheid tegen sterilisatiemethoden. Het wordt vaak gebruikt in:
- Implanteerbare apparaten
- Chirurgische instrumenten
- Componenten voor medische beeldvorming
- Laboratoriumapparatuur
Acetal vindt nog steeds toepassingen in minder veeleisende medische omgevingen, zoals:
- Componenten voor wegwerpinstrumenten
- Laboratorium testopstellingen
- Behuizingen voor diagnoseapparatuur
Industriële apparatuur
Voor industriële machines hangt de keuze vaak af van de bedrijfsomstandigheden:
- Standaard bedrijfsomgevingen: Acetal biedt uitstekende waarde voor tandwielen, lagers en slijtageoppervlakken in normale omstandigheden.
- Ruwe omgevingen: PEEK rechtvaardigt zijn hogere prijs wanneer het wordt blootgesteld aan hoge temperaturen, chemicaliën of extreme mechanische spanning.
De optimale selectie maken
Als ik klanten help bij hun keuze tussen acetaal en PEEK bij PTSMAKE, raad ik een systematische aanpak aan:
- De meest veeleisende omstandigheden identificeren waaraan het onderdeel zal worden blootgesteld (temperatuur, chemicaliën, belasting)
- Bepaal of de eigenschappen van acetal voldoende zijn om met deze omstandigheden om te gaan
- Bereken het kostenverschil tussen opties voor je specifieke volumevereisten
- Houd rekening met de gevolgen van een storing en de bijbehorende kosten van stilstand
- Evalueren of de hoogwaardige prestaties van PEEK de hogere prijs rechtvaardigen
Onthoud dat materiaalselectie zelden one-size-fits-all is. Soms werkt een hybride aanpak het beste, waarbij PEEK alleen wordt gebruikt voor de meest kritische onderdelen en acetaal voor minder veeleisende onderdelen binnen dezelfde assemblage.
Wat is het verschil tussen PTFE en PEEK?
Bent u wel eens verdwaald in de zee van hoogwaardige kunststoffen en weet u niet zeker of u PTFE of PEEK moet kiezen voor uw cruciale toepassing? Wanneer de deadlines van een project naderen en de materiaalkeuze uw ontwerp kan maken of breken, kan de druk om de juiste keuze te maken overweldigend zijn, vooral wanneer beide materialen indrukwekkende technische specificaties hebben.
PTFE en PEEK zijn beide hoogwaardige thermoplasten met duidelijke verschillen. PTFE biedt een ongeëvenaarde chemische weerstand, extreem lage wrijving (coëfficiënt 0,05-0,10) en werkt van -328°F tot 500°F, maar heeft een slechte mechanische sterkte. PEEK biedt superieure mechanische eigenschappen, uitstekende slijtvastheid en handhaaft structurele integriteit tot 480°F terwijl het bewerkbaarder is.
Moleculaire structuur en basiseigenschappen
De fundamentele verschillen tussen PTFE en PEEK beginnen op moleculair niveau, wat hun verschillende prestatiekenmerken in verschillende toepassingen verklaart.
Chemische samenstelling
PTFE (Polytetrafluoroethyleen) heeft een koolstofruggengraat die volledig is omgeven door fluoratomen. Deze unieke structuur geeft PTFE zijn uitzonderlijke chemische inertie en lage wrijvingseigenschappen. De koolstof-fluorverbindingen behoren tot de sterkste in de organische chemie, waardoor PTFE ongelooflijk bestand is tegen chemische aanvallen.
PEEK (Polyetheretherketone) heeft daarentegen een complexere moleculaire structuur met aromatische ringen die verbonden zijn door ether- en ketonverbindingen. Deze aromatische ruggengraat geeft PEEK zijn uitstekende mechanische sterkte en thermische stabiliteit.
Vergelijkende analyse van onroerend goed
Eigendom | PTFE | PEEK | Voordeel |
---|---|---|---|
Temperatuur voor maximaal continu gebruik | 260°C (500°F) | 480°F (250°C) | PTFE (licht) |
Minimale bedrijfstemperatuur | -328°F (-200°C) | -65°F (-54°C) | PTFE |
Wrijvingscoëfficiënt | 0,05-0,10 (laagste van alle vaste stoffen) | 0.35-0.40 | PTFE |
Treksterkte | 3.000-5.000 psi | 14.000-16.000 psi | PEEK |
Chemische weerstand | Superieur (universeel) | Uitstekend (beperkt door sterke zuren) | PTFE |
Bewerkbaarheid | Uitdagend (zacht, vervormt gemakkelijk) | Goed | PEEK |
Slijtvastheid | Slecht tot matig | Uitstekend | PEEK |
Elektrische eigenschappen | Uitstekende isolator | Goede isolator | PTFE |
Kostenfactor | Matig | Hoog (3-4× meer dan PTFE) | PTFE |
Thermische prestatieverschillen
De temperatuurprestaties zijn vaak een kritieke beslissingsfactor bij de keuze tussen deze materialen.
Hittebestendigheid en stabiliteit
Hoewel beide materialen uitzonderlijke hittebestendigheid bieden, gedragen ze zich anders bij hogere temperaturen. PTFE behoudt zijn chemische inertie en lage wrijving tot de maximumtemperatuur, maar begint mechanische integriteit te verliezen bij veel lagere temperaturen (rond 260 °F/127 ° C).
PEEK daarentegen behoudt zijn mechanische sterkte veel dichter bij de maximale temperatuur. Dit maakt PEEK aanzienlijk waardevoller in toepassingen die zowel hittebestendigheid als mechanische belasting vereisen.
Ik heb talloze toepassingen gezien waarbij klanten aanvankelijk PTFE selecteerden op basis van uitsluitend temperatuurwaarderingen, om er vervolgens achter te komen dat het materiaal de mechanische spanningen bij die temperaturen niet aankon. Het vermogen van PEEK om de structurele integriteit bij hoge temperaturen te behouden, maakt het vaak de hogere prijs waard.
Prestaties bij koude temperaturen
Voor cryogene toepassingen heeft PTFE een duidelijk voordeel. Het blijft flexibel en functioneel tot -328°F (-200°C), terwijl PEEK steeds brosser wordt onder -65°F (-54°C). Dit maakt PTFE de duidelijke keus voor ruimte, laboratorium, en andere ultra-lage temperatuurmilieu's.
Vergelijking mechanische sterkte
De mechanische eigenschappen van deze materialen verschillen enorm, waardoor hun geschiktheid toepassingsspecifiek is.
Structurele integriteit onder belasting
PEEK biedt enorm superieure mechanische prestaties met een treksterkte van gemiddeld 14.000-16.000 psi in vergelijking met de bescheiden 3.000-5.000 psi van PTFE. Dit maakt PEEK geschikt voor lastdragende toepassingen waar PTFE snel zou vervormen of falen.
Bij PTSMAKE, adviseren wij vaak PEEK voor structurele componenten die consistente mechanische ladingen, vooral bij opgeheven temperaturen ervaren. De uitzonderlijke kruipweerstand van het materiaal staat het toe om dimensionale stabiliteit onder ononderbroken spanning te handhaven.
Slijtvastheid en wrijving
De opmerkelijk lage wrijvingscoëfficiënt van PTFE (0,05-0,10) maakt het het materiaal bij uitstek voor toepassingen die minimale wrijving vereisen. Deze zelfde eigenschap draagt echter bij aan de slechte slijtvastheid, omdat het materiaal gemakkelijk kan worden weggeschraapt in scenario's met veel slijtage.
PEEK vertoont een uitstekende slijtvastheid met behoud van een redelijke wrijvingscoëfficiënt (0,35-0,40). Voor toepassingen waarbij continu tegen andere oppervlakken wordt bewogen, gaat PEEK doorgaans veel langer mee dan PTFE.
Veel van onze klanten bereiken het beste van beide werelden door PEEK te gebruiken als constructiemateriaal met een dunne PTFE-coating of -voering waar wrijvingsvermindering nodig is.
Profielen chemische weerstand
Beide materialen bieden een uitzonderlijke chemische weerstand, maar met belangrijke verschillen.
Weerstand tegen agressieve omgevingen
PTFE is de gouden standaard voor chemische weerstand en is vrijwel inert voor bijna alle chemicaliën (met zeldzame uitzonderingen zoals gesmolten alkalimetalen en elementair fluor). Deze universele chemische weerstand maakt PTFE van onschatbare waarde in chemische verwerking, halfgeleiderproductie en laboratoriumomgevingen.
PEEK biedt een uitstekende chemische weerstand tegen de meeste stoffen, maar kan worden aangetast door geconcentreerd zwavelzuur en sommige andere sterke zuren. Voor de meeste industriële omgevingen is de chemische weerstand van PEEK echter meer dan voldoende.
Hydrolyse en vochtabsorptie
PTFE is volledig hydrofoob en absorbeert vrijwel geen vocht, zelfs niet na langdurige blootstelling. PEEK, dat zeer goed bestand is tegen hydrolyse, absorbeert een kleine hoeveelheid vocht (0,1-0,3%) wanneer het langdurig wordt blootgesteld aan vochtige omgevingen.
Voor ultrazuivere watertoepassingen of systemen waar zelfs minieme verontreiniging onaanvaardbaar is, blijft PTFE vaak de voorkeurskeuze, ondanks de mechanische beperkingen.
%[Bewerkte componenten van PEEK en PTFE voor structurele vergelijking](
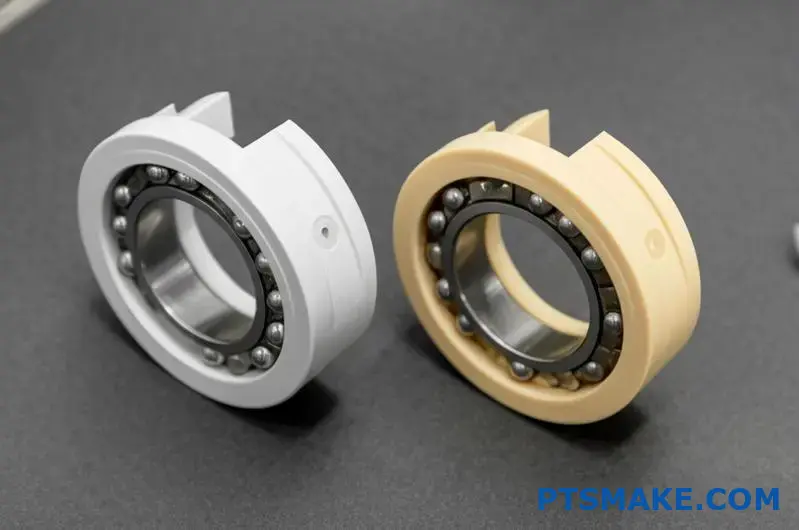
"PEEK- en PTFE-lageringcomponenten")
Overwegingen bij machinale bewerking en fabricage
De bewerkbaarheid3 De verschillen tussen deze materialen hebben een aanzienlijke invloed op de productiekosten en -mogelijkheden.
Uitdagingen en oplossingen voor verspaning
PTFE biedt unieke bewerkingsuitdagingen vanwege de zachtheid en neiging tot koudvloeien. Het vereist speciaal gereedschap, lagere snijsnelheden en zorgvuldige opspanning om vervorming tijdens het bewerken te voorkomen. Scherp gereedschap is essentieel om te voorkomen dat het materiaal scheurt of vervormt.
PEEK verspant zich meer als traditionele technische kunststoffen, hoewel de abrasieve aard van PEEK sneller slijtage aan het gereedschap veroorzaakt dan veel andere materialen. Bij het bewerken van PEEK gebruiken we meestal hardmetalen gereedschappen en de juiste koeltechnieken om de warmteontwikkeling onder controle te houden.
Compatibiliteit productieproces
De hoge smeltviscositeit van PTFE maakt conventioneel spuitgieten onmogelijk. In plaats daarvan moet het worden verwerkt met technieken als persgieten, ram-extrusie of snijden uit knuppels. Dit beperkt de ontwerpcomplexiteit en verhoogt de productiekosten voor complexe vormen.
PEEK kan worden verwerkt via conventionele methoden als spuitgieten en extrusie, waardoor complexere geometrieën mogelijk worden en de productiekosten bij grotere volumes mogelijk lager uitvallen. Deze veelzijdigheid in verwerking geeft PEEK een voordeel voor ingewikkelde onderdelen of bij de overgang van prototyping naar massaproductie.
Kosten-batenanalyse voor verschillende toepassingen
Het aanzienlijke prijsverschil tussen deze materialen maakt een zorgvuldige afweging van hun toepassingsspecifieke waarde noodzakelijk.
Vergelijking van waardeproposities
Hoewel PEEK doorgaans 3-4 keer meer kost dan PTFE, bieden de superieure mechanische eigenschappen en slijtvastheid vaak een betere langetermijnwaarde in toepassingen waar mechanische storingen duur of gevaarlijk zouden zijn.
Voor toepassingen die voornamelijk chemische weerstand, lage wrijving of elektrische isolatie-eigenschappen vereisen zonder significante mechanische spanning, biedt PTFE meestal een betere waarde ondanks de beperkingen.
Branche-specifieke selectiecriteria
Verschillende industrieën geven de voorkeur aan verschillende materiaaleigenschappen:
- Chemische verwerking: De universele chemische weerstand van PTFE weegt meestal zwaarder dan de mechanische beperkingen.
- Ruimtevaart: Beide materialen vinden toepassingen, waarbij PEEK wordt gebruikt voor structurele onderdelen en PTFE voor afdichtingen en elektrische isolatie.
- Medisch: De biocompatibiliteit en structurele sterkte van PEEK maken het populair voor implantaten, terwijl PTFE de voorkeur geniet voor kathetervoeringen en andere wrijvingsarme toepassingen.
- Halfgeleider: PTFE domineert vanwege de uitzonderlijke zuiverheid en bestendigheid tegen agressieve chemicaliën.
- Automobiel: De slijtvastheid en mechanische eigenschappen van PEEK maken het waardevol voor onderdelen onder de motorkap die onderhevig zijn aan mechanische belasting.
Wat is het verschil tussen PVDF en PEEK?
Hebt u ooit voor het dilemma gestaan te moeten kiezen tussen PVDF en PEEK voor een kritisch project waarbij de materiaalkeuze uw ontwerp kan maken of breken? Wanneer standaard kunststoffen niet voldoen en u uitzonderlijke chemische weerstand of thermische stabiliteit nodig hebt, kan de verwarring tussen deze twee hoogwaardige materialen leiden tot kostbare fouten of verminderde prestaties.
PVDF (polyvinylideenfluoride) en PEEK (polyetheretherketone) verschillen vooral in hun prestatiekenmerken en toepassingen. PEEK biedt een superieure hittebestendigheid (480°F vs 300°F), een betere mechanische sterkte en een uitzonderlijke slijtvastheid, terwijl PVDF een uitstekende chemische weerstand en UV-stabiliteit biedt en aanzienlijk goedkoper is.
Belangrijkste verschillen tussen PVDF en PEEK
Als je deze twee thermoplasten met elkaar vergelijkt, kun je aan de hand van hun fundamentele eigenschappen bepalen welk materiaal het meest geschikt is voor specifieke toepassingen. Beide materialen worden beschouwd als hoogwaardige opties, maar ze blinken uit in verschillende omgevingen en toepassingen.
Materiaalsamenstelling en structuur
PVDF is een semikristallijn fluorpolymeer dat bestaat uit zich herhalende eenheden vinylideendifluoride. De moleculaire structuur bevat koolstof-fluorverbindingen die zorgen voor een uitstekende chemische weerstand, hoewel niet zo uitgebreid als volledig gefluoreerde polymeren zoals PTFE.
PEEK behoort tot de polyaryletherketon familie en heeft een complexe moleculaire structuur met aromatische ringen verbonden door ether- en ketonverbindingen. Deze unieke structuur geeft PEEK zijn uitzonderlijke thermische stabiliteit en mechanische sterkte.
Vergelijking van prestatiekenmerken
De volgende tabel geeft een gedetailleerde vergelijking van de belangrijkste eigenschappen van PVDF en PEEK:
Eigendom | PVDF | PEEK | Superieur materiaal |
---|---|---|---|
Temperatuur voor maximaal continu gebruik | 149°C (300°F) | 480°F (250°C) | PEEK |
Mechanische sterkte (trek) | 5.800-7.800 psi | 14.500-16.000 psi | PEEK |
Chemische weerstand | Uitstekend (de meeste zuren, basen) | Zeer goed (beperkt door sterke zuren) | PVDF |
UV-bestendigheid | Uitstekend | Redelijk tot goed | PVDF |
Slijtvastheid | Goed | Uitstekend | PEEK |
Wrijvingscoëfficiënt | 0.25-0.35 | 0.35-0.40 | PVDF |
Kostenfactor | Matig | 2-3× hoger dan PVDF | PVDF |
Vochtabsorptie | 0.03-0.04% | 0.1-0.15% | PVDF |
Dichtheid | 1,75-1,78 g/cm³ | 1,30-1,32 g/cm³ | Toepassingsafhankelijk |
Thermische prestaties en stabiliteit
De temperatuur bepaalt vaak de materiaalkeuze in veel technische toepassingen.
Hittebestendigheid Vergelijking
PEEK heeft een uitzonderlijke thermische stabiliteit en behoudt zijn mechanische eigenschappen bij temperaturen tot 250°C (480°F) bij continu gebruik. Dit maakt het ideaal voor toepassingen in omgevingen met hoge temperaturen waar traditionele kunststoffen het zouden laten afweten.
PVDF wordt nog steeds beschouwd als een kunststof voor hoge temperaturen, maar heeft een lagere maximale continue gebruikstemperatuur van ongeveer 149°C (300°F). Dit temperatuurbereik is voldoende voor veel industriële toepassingen, maar schiet tekort in extreme thermische omgevingen.
Uit mijn ervaring met klanten van PTSMAKE blijkt dat dit temperatuurverschil vaak de doorslag geeft bij de keuze tussen deze materialen voor toepassingen zoals halfgeleiderverwerkingsapparatuur, waar de procestemperaturen de mogelijkheden van PVDF kunnen overschrijden.
Thermisch cyclisch gedrag
Beide materialen gaan anders om met thermische cycli:
- PVDF vertoont een goede maatvastheid tijdens thermische cycli, hoewel het een grotere thermische uitzetting kan ondergaan dan PEEK.
- PEEK handhaaft een uitzonderlijke dimensionale stabiliteit, zelfs bij herhaalde thermische cycli, waardoor het de voorkeur verdient voor precisiecomponenten die nauwe toleranties moeten handhaven bij verschillende temperaturen.
Profielen chemische weerstand
Chemische weerstand is een andere cruciale factor die deze materialen onderscheidt.
Weerstand tegen agressieve omgevingen
PVDF is uitstekend bestand tegen een breed scala aan chemicaliën, waaronder:
- De meeste zuren (inclusief geconcentreerd zoutzuur en zwavelzuur)
- Alifatische en aromatische koolwaterstoffen
- Alcoholen en gechloreerde oplosmiddelen
- Oxiderende middelen
PEEK heeft een goede chemische bestendigheid tegen veel stoffen, maar kan worden aangetast door geconcentreerd zwavelzuur en sommige andere sterke zuren. Het is bijzonder goed bestand tegen hydrolyse en stoomsterilisatie, waardoor het waardevol is in medische toepassingen.
Industriespecifieke chemische overwegingen
Verschillende industrieën geven de voorkeur aan specifieke chemische weerstandseigenschappen:
- Chemische verwerking: PVDF heeft vaak de voorkeur vanwege de uitgebreide bestendigheid tegen zuren en chloorverbindingen.
- Halfgeleider: Beide materialen worden gebruikt, waarbij de selectie afhangt van specifieke proceschemicaliën.
- Olie en gas: De combinatie van mechanische eigenschappen en chemische weerstand van PEEK maakt het waardevol voor toepassingen in boorgaten.
- Farmaceutisch: De uitstekende weerstand van PVDF tegen reinigingsmiddelen en sterilisatiemethoden maakt het populair voor verwerkingsapparatuur.
Mechanische eigenschappen en structurele toepassingen
De mechanische sterkte4 De verschillen tussen deze materialen hebben een aanzienlijke invloed op hun geschiktheid voor dragende toepassingen.
Draagvermogen
GLUUR biedt een aanzienlijk hogere mechanische sterkte met trekwaarden die doorgaans variëren van 14.500-16.000 psi, vergeleken met de meer bescheiden 5.800-7.800 psi van PVDF. Dit maakt PEEK superieur voor structurele componenten die bestand moeten zijn tegen aanzienlijke mechanische belastingen.
Voor toepassingen die zowel chemische weerstand als structurele integriteit vereisen, biedt PEEK vaak de beste balans van eigenschappen, ondanks de hogere kosten. Ik heb PEEK aanbevolen voor talloze toepassingen bij PTSMAKE waar componenten zowel agressieve chemicaliën als mechanische spanning moeten kunnen weerstaan.
Slijtvastheid en wrijvingseigenschappen
PEEK vertoont een uitstekende slijtvastheid, waardoor het ideaal is voor lagers, bussen en andere onderdelen die onderhevig zijn aan voortdurende wrijving. Zijn zelfsmerende eigenschappen helpen de levensduur van bewegende delen in veeleisende omgevingen uitbreiden.
PVDF biedt een goede slijtvastheid, maar niet op het niveau van PEEK. Zijn lagere wrijvingscoëfficiënt (0,25-0,35 in vergelijking met 0,35-0,40 bij PEEK) kan voordelig zijn bij bepaalde glijdende toepassingen met lage belasting waarbij minder wrijving belangrijker is dan maximale slijtvastheid.
Elektrische en thermische isolatie-eigenschappen
Beide materialen hebben verschillende elektrische eigenschappen die ze geschikt maken voor verschillende toepassingen.
Diëlektrische eigenschappen
PVDF staat bekend om zijn piëzo-elektrische eigenschappen, waardoor het een elektrische lading kan genereren als reactie op toegepaste mechanische spanning. Deze unieke eigenschap maakt PVDF waardevol in sensortoepassingen.
PEEK biedt uitstekende elektrische isolatie-eigenschappen over een breed temperatuurbereik en behoudt zijn diëlektrische sterkte zelfs bij verhoogde temperaturen. Dit maakt het bijzonder waardevol in elektrische toepassingen op hoge temperatuur waar standaardkunststoffen het zouden laten afweten.
Thermische geleidbaarheid
PVDF en PEEK hebben beide een relatief lage thermische geleidbaarheid in vergelijking met metalen, waardoor ze goede thermische isolatoren zijn:
- PVDF: 0,17-0,19 W/m-K
- PEEK: 0,25-0,29 W/m-K
Deze lage thermische geleidbaarheid kan zowel een voordeel als een nadeel zijn, afhankelijk van de toepassing. Voor onderdelen die thermische isolatie vereisen, presteren beide materialen goed, hoewel PVDF iets betere isolatie biedt.
Kostenoverwegingen en waardeanalyse
Het aanzienlijke prijsverschil tussen deze materialen maakt een kosten-batenanalyse essentieel.
Initiële materiaalkosten
PEEK kost doorgaans 2 tot 3 keer meer dan PVDF, wat neerkomt op een aanzienlijke meerkost die moet worden gerechtvaardigd door de prestatievereisten. Dit prijsverschil is het gevolg van het complexere productieproces van PEEK en de hogere grondstofkosten.
Beoordeling van de levensduur
Bij het evalueren van de totale eigendomskosten moet rekening worden gehouden met verschillende factoren naast de initiële materiaalkosten:
- Verwachte levensduur in de doelomgeving
- Vervangingsfrequentie en bijbehorende stilstandkosten
- Installatie- en onderhoudsvereisten
- Zorgen over veiligheid en betrouwbaarheid
In veel toepassingen met hoge temperaturen of hoge belasting rechtvaardigen de superieure prestaties van PEEK de hogere initiële kosten dankzij de langere levensduur en de verbeterde betrouwbaarheid. Voor toepassingen die binnen de mogelijkheden van PVDF liggen, biedt het goedkopere materiaal vaak een betere algemene waarde.
Verwerkings- en fabricageoverwegingen
Productiemogelijkheden en -beperkingen beïnvloeden ook de materiaalkeuze.
Bewerkingsverschillen
Bij het bewerken van deze materialen op PTSMAKE hebben we significante verschillen waargenomen:
- PVDF werkt relatief goed, maar vereist scherp gereedschap en de juiste snelheden om smelten of vreten te voorkomen.
- PEEK is moeilijker te bewerken vanwege zijn abrasiviteit en slechte thermische geleidbaarheid, wat kan leiden tot warmteontwikkeling tijdens het snijden.
Voor precisiecomponenten houdt PEEK over het algemeen nauwere toleranties tijdens de bewerking, maar zijn meer gespecialiseerde technieken en gereedschappen nodig, waardoor de productiekosten mogelijk hoger uitvallen.
Compatibiliteit productiemethoden
Beide materialen kunnen worden verwerkt via meerdere productiemethoden:
- PVDF: Spuitgieten, extrusie, persgieten, machinale bewerking
- PEEK: Spuitgieten, extrusie, persgieten, machinale bewerking, 3D-printen (gespecialiseerde apparatuur)
PVDF biedt iets meer verwerkingsflexibiliteit bij lagere temperaturen, terwijl PEEK hogere verwerkingstemperaturen vereist maar door geavanceerde productietechnieken meer opties biedt voor complexe geometrieën.
Toepassingsspecifieke selectierichtlijnen
Verschillende industrieën geven de voorkeur aan verschillende materiaaleigenschappen, wat leidt tot verschillende materiaalvoorkeuren.
Halfgeleiderindustrie
In de halfgeleiderproductie vinden beide materialen toepassingen, maar op verschillende gebieden:
- PVDF: Vaak gebruikt voor ultrazuivere watersystemen, onderdelen voor de levering van chemicaliën en filtratieapparatuur.
- PEEK: Bij voorkeur voor onderdelen die worden blootgesteld aan hoge temperaturen, zoals waferbehandelingsapparatuur en onderdelen van proceskamers.
Apparatuur voor chemische verwerking
Voor chemische verwerkingstoepassingen:
- PVDF: Uitstekend voor pompen, kleppen, fittingen en tanks die corrosieve chemicaliën verwerken bij gematigde temperaturen.
- PEEK: Beter geschikt voor componenten die zowel chemisch resistent moeten zijn als bestand tegen hoge temperaturen of mechanische sterkte.
Medische en farmaceutische toepassingen
In medische toepassingen:
- PVDF: Vaak gebruikt in filtratiemembranen, hechtingen en sommige implanteerbare apparaten.
- PEEK: Heeft de voorkeur voor implanteerbare hulpmiddelen, vooral orthopedische toepassingen, vanwege de biocompatibiliteit, radiolucentie en mechanische eigenschappen die lijken op die van bot.
Wanneer ik klanten help bij het maken van een keuze tussen PVDF en PEEK bij PTSMAKE, adviseer ik een systematische aanpak waarbij eerst de meest kritische omgevingsfactoren worden geëvalueerd (temperatuur, chemicaliën, mechanische belasting) en vervolgens secundaire factoren zoals kosten, verwerkingsvereisten en beschikbaarheid.
<
Is PEEK een polyethyleen?
Bent u wel eens in de war geraakt door de vele technische kunststoffen met gelijkluidende namen? Bij het selecteren van materialen voor kritieke toepassingen kan deze verwarring leiden tot kostbare fouten, mislukte prestaties en verspilling van middelen als u per ongeluk de ene hoogwaardige kunststof vervangt door een andere.
Nee, PEEK (polyetheretherketone) is geen polyethyleen. PEEK is een aromatische polyether met ketongroepen in de ruggengraat, waardoor een semi-kristallijne thermoplast ontstaat met een uitzonderlijke hittebestendigheid (tot 480°F), een uitstekende chemische bestendigheid en superieure mechanische eigenschappen die die van polyethyleenmaterialen ver overtreffen.
Chemische structuur en classificatieverschillen
Bij het onderzoek naar PEEK versus polyethyleen beginnen de fundamentele verschillen op moleculair niveau. Deze structurele verschillen verklaren waarom deze materialen zich in praktische toepassingen zo verschillend gedragen.
Moleculaire ruggengraat vergelijking
PEEK heeft een complexe aromatische ruggengraatstructuur met ether- en ketonverbindingen tussen benzeenringen. Deze moleculaire architectuur geeft PEEK zijn uitstekende thermische stabiliteit en mechanische sterkte. De aromatische ringen zorgen voor stijfheid, terwijl de etherverbindingen voor enige flexibiliteit zorgen.
Polyethyleen daarentegen heeft een van de eenvoudigst mogelijke polymeerstructuren: slechts een lineaire keten van koolstofatomen met daaraan waterstofatomen. Deze eenvoudige structuur bestaat in verschillende vormen (HDPE, LDPE, UHMWPE), maar ze missen allemaal de aromatische bestanddelen en functionele groepen die PEEK zijn uitzonderlijke eigenschappen geven.
Dit fundamentele structurele verschil betekent dat PEEK tot een heel andere polymeerfamilie behoort dan polyethyleen. Terwijl polyethyleen wordt geclassificeerd als een polyolefine, behoort PEEK tot de polyaryletherketone (PAEK) familie van hoogwaardige thermoplasten.
Belangrijkste verschillen tussen eigenschappen
De verschillen in moleculaire structuur leiden tot dramatische prestatieverschillen:
Eigendom | PEEK | Polyethyleen (HDPE) | Verschil Factor |
---|---|---|---|
Temperatuur voor maximaal continu gebruik | 480°F (250°C) | 180°F (82°C) | PEEK is 2,7× hoger |
Treksterkte | 14.500 psi | 4.500 psi | PEEK is 3,2× sterker |
Chemische weerstand | Uitstekend (weerstaat de meeste chemicaliën) | Goed (gevoelig voor aromatische oplosmiddelen) | PEEK biedt bredere weerstand |
Kosten | Hoog | Laag | PEEK kost 15-20× meer |
Dichtheid | 1,32 g/cm³ | 0,95 g/cm³ | PEEK is 39% dichter |
Hardheid (Shore D) | 85-90 | 60-70 | PEEK is aanzienlijk harder |
Verschillen in productieproces
De productiemethoden voor PEEK en polyethyleen weerspiegelen hun verschillende moleculaire structuren en prestatiekenmerken.
PEEK Productieproces
PEEK wordt vervaardigd via een complex proces van nucleofiele aromatische substitutiepolymerisatie. Dit vereist een nauwkeurige temperatuurregeling en gespecialiseerde katalysatoren. De monomeren zijn aanzienlijk duurder dan ethyleen, wat bijdraagt aan de hogere kosten van PEEK.
Wanneer we bij PTSMAKE PEEK componenten bewerken, moeten we rekening houden met de unieke eigenschappen van dit materiaal. De lagere warmtegeleiding betekent dat warmtebeheer tijdens het bewerken van cruciaal belang is om lokale thermische degradatie te voorkomen.
Productie van polyethyleen
Polyethyleen wordt geproduceerd door polymerisatie van ethyleen met behulp van verschillende katalysatoren, afhankelijk van de gewenste dichtheid en vertakking. Dit relatief eenvoudige proces kan bij lagere temperaturen en drukken worden uitgevoerd dan de productie van PEEK, vooral voor varianten met een lage dichtheid.
Prestaties in extreme omgevingen
Prestaties bij hoge temperaturen
Een van de belangrijkste verschillen tussen deze materialen is hun thermische stabiliteit:
- PEEK behoudt zijn mechanische eigenschappen tot 250°C (480°F) voor continu gebruik en is bestand tegen korte blootstelling aan nog hogere temperaturen.
- Polyethyleen begint zacht te worden rond 180°F (82°C) en verliest ruim onder die temperatuur het grootste deel van zijn mechanische sterkte.
Ik heb talloze toepassingen gezien waarbij klanten aanvankelijk voor polyethyleen kozen op basis van de kosten, om vervolgens snel defect te raken als de bedrijfstemperaturen de verwachtingen overtroffen. In één luchtvaarttoepassing stapte een klant over van polyethyleen op PEEK voor een onderdeel in de buurt van een warmtebron, waardoor de levensduur ondanks de hogere initiële materiaalkosten van maanden op jaren werd gebracht.
Vergelijking chemische weerstand
Hoewel beide materialen goed bestand zijn tegen chemicaliën, biedt PEEK een bredere bescherming tegen agressieve chemicaliën:
- PEEK is bestand tegen de meeste zuren, basen, koolwaterstoffen en organische oplosmiddelen
- Polyethyleen is goed bestand tegen zuren en basen, maar kan worden aangetast door aromatische koolwaterstoffen en sommige oxidatiemiddelen.
Dit verschil wordt cruciaal in chemische verwerkingsapparatuur, halfgeleiderfabricage en medische toepassingen waar blootstelling aan meerdere chemicaliën gebruikelijk is.
Geschiktheid voor toepassingen
Ruimtevaart en defensietoepassingen
In luchtvaarttoepassingen is PEEK dankzij zijn combinatie van licht gewicht, vlambestendigheid en thermische stabiliteit van onschatbare waarde voor onderdelen zoals:
- Interieuronderdelen die vlambestendig moeten zijn
- Elektrische connectoren en isolatoren
- Structurele componenten in zones met hoge temperaturen
- Onderdelen van brandstofsystemen die bestand moeten zijn tegen chemicaliën
Polyethyleen voldoet zelden aan de hoge eisen van luchtvaarttoepassingen vanwege de beperkte thermische stabiliteit en mechanische eigenschappen.
Medisch en gezondheidszorggebruik
De biocompatibiliteitsprofielen van deze materialen verschillen ook aanzienlijk:
- PEEK is biocompatibel en wordt gebruikt in implanteerbare apparaten, chirurgische instrumenten en medische apparatuur die gesteriliseerd moet worden.
- Polyethyleen van medische kwaliteit (voornamelijk UHMWPE) wordt gebruikt in sommige implantaten zoals kunstgewrichten, maar heeft niet de temperatuurbestendigheid van PEEK voor herhaalde stoomsterilisatie.
Industriële onderdelen
Voor industriële machines hangt de keuze tussen deze materialen meestal af van de bedrijfsomstandigheden:
- PEEK blinkt uit in omgevingen met hoge temperaturen, toepassingen die een uitstekende slijtvastheid vereisen of blootstelling aan agressieve chemicaliën.
- Polyethyleen levert toereikende prestaties in toepassingen bij omgevingstemperatuur met gematigde mechanische vereisten en wordt vaak gekozen vanwege de lagere kosten en het verwerkingsgemak.
Kosten-batenoverwegingen
Het prijsverschil tussen deze materialen is aanzienlijk - PEEK kost doorgaans 15-20 keer meer dan hogedichtheidspolyethyleen. Dit aanzienlijke kostenverschil betekent dat de materiaalkeuze gebaseerd moet zijn op een grondige analyse van:
- Vereist bedrijfstemperatuurbereik
- Chemisch blootstellingsprofiel
- Mechanische belastingseisen
- Verwachte levensduur
- Gevolgen van falen
Voor toepassingen binnen het capaciteitsbereik van polyethyleen is het dankzij de lagere kosten de meest economische keuze. Maar wanneer de prestatievereisten de beperkingen van polyethyleen overschrijden, rechtvaardigen de superieure eigenschappen van PEEK gemakkelijk de hogere prijs door een langere levensduur, verbeterde betrouwbaarheid en lagere onderhoudskosten.
Verschillen in bewerking en verwerking
Bij PTSMAKE hebben we aanzienlijke verschillen ontdekt bij het bewerken van deze materialen:
- PEEK vereist speciale snijparameters vanwege de thermisch gedrag5 tijdens de bewerking, maar houdt strakke toleranties en produceert uitstekende oppervlakteafwerkingen
- Polyethyleen is gemakkelijker te bewerken, maar heeft de neiging om te vervormen onder de snijkrachten, waardoor strakke toleranties moeilijker te handhaven zijn.
Inzicht in deze verschillen in verwerking is essentieel bij het ontwerpen van componenten voor maakbaarheid en precisie.
Wat zijn de nadelen en voordelen van PEEK?
Hebt u wel eens geworsteld met de vraag of PEEK zijn hoge prijs waard is voor uw kritische toepassing? Als het succes van een project afhangt van de materiaalkeuze, kan de keuze tussen dure hoogwaardige kunststoffen en goedkopere alternatieven een lastige evenwichtsoefening zijn met reële gevolgen voor betrouwbaarheid en levensduur.
PEEK biedt uitzonderlijke voordelen zoals opmerkelijke hittebestendigheid (tot 480°F), uitstekende chemische weerstand, uitstekende mechanische sterkte en superieure slijtage-eigenschappen. Echter, deze voordelen komen met belangrijke nadelen, waaronder hoge kosten (5-10 keer meer dan standaard engineering plastics), uitdagende bewerkbaarheid, beperkte kleuropties en slechte UV-bestendigheid.
De uitzonderlijke eigenschappen van PEEK begrijpen
PEEK (Polyetheretherketone) onderscheidt zich onder de technische kunststoffen door zijn unieke combinatie van eigenschappen die het geschikt maken voor de meest veeleisende toepassingen. Als iemand die materialen heeft gespecificeerd voor talloze precisiecomponenten, heb ik met eigen ogen gezien hoe de eigenschappen van PEEK zich vertalen in prestatievoordelen in de praktijk.
Thermische prestatie Voordelen
Een van de meest indrukwekkende eigenschappen van PEEK is zijn thermische stabiliteit. Dit materiaal behoudt zijn mechanische eigenschappen bij temperaturen die de meeste kunststoffen catastrofaal zouden doen falen.
Temperatuurkenmerk | PEEK prestaties | Vergelijking met Standaard Kunststoffen |
---|---|---|
Continue bedrijfstemperatuur | Tot 250°C (480°F) | 2-3× hoger dan de meeste technische kunststoffen |
Glasovergangstemperatuur | 143°C (289°F) | Behoudt stijfheid bij hogere temperaturen |
Smeltpunt | 343°C (649°F) | Maakt stoomsterilisatie mogelijk |
Thermische geleidbaarheid | 0,25 W/m-K | Beter dan veel kunststoffen voor warmteafvoer |
Dankzij deze uitzonderlijke thermische weerstand kan PEEK worden gebruikt in toepassingen in de buurt van warmtebronnen waar standaardkunststoffen snel zouden vervormen of degraderen. Ik heb veel klanten geholpen om defecte onderdelen van mindere materialen te vervangen door PEEK onderdelen die ondanks de uitdagende thermische omgevingen probleemloos blijven presteren.
Voordelen van chemische weerstand
Het chemische weerstandsprofiel van PEEK is bijna even indrukwekkend als zijn thermische eigenschappen. Het materiaal is uitstekend bestand tegen:
- Koolwaterstoffen en organische oplosmiddelen
- De meeste zuren en basen (behalve geconcentreerd zwavelzuur)
- Stoom en heet water
- Vloeistoffen en brandstoffen voor auto's
- Medische sterilisatieprocessen
Deze brede chemische resistentie maakt PEEK bijzonder waardevol in omgevingen waar blootstelling aan meerdere agressieve stoffen wordt verwacht. In de halfgeleiderindustrie bijvoorbeeld zijn PEEK onderdelen bestand tegen de agressieve chemicaliën die worden gebruikt bij de verwerking van wafers, terwijl de maatvastheid behouden blijft.
Mechanische eigenschappen Voordelen
De mechanische sterkte van PEEK onderscheidt het van de meeste andere thermoplasten:
- Treksterkte van 14.500 psi (vergelijkbaar met sommige metalen)
- Uitstekende weerstand tegen vermoeiing
- Uitstekende slagvastheid en taaiheid
- Superieure slijtvastheid
- Lage wrijvingscoëfficiënt
Deze eigenschappen maken PEEK geschikt voor structurele toepassingen waar de meeste kunststoffen het zouden laten afweten. Ik heb PEEK gespecificeerd voor tandwielen, lagers en andere slijtagegevoelige onderdelen die onder grote mechanische spanning werken, waarbij ik metalen onderdelen vaak heb vervangen door lichtere PEEK alternatieven die extra voordelen bieden zoals corrosiebestendigheid en geluidsreductie.
De belangrijke nadelen van PEEK
Ondanks de indrukwekkende prestatiekenmerken heeft PEEK een aantal belangrijke nadelen die zorgvuldig overwogen moeten worden tijdens de materiaalselectie.
Kostenbeperkingen
Het meest voor de hand liggende nadeel van PEEK zijn de kosten. Bij PTSMAKE moeten we klanten vaak helpen om de prijspremie van PEEK ten opzichte van andere engineering plastics te begrijpen:
- PEEK kost doorgaans 5-10 keer meer dan technische kunststoffen zoals nylon of acetal
- De materiaalkosten voor PEEK onderdelen kunnen 20-30% hoger liggen dan gelijkwaardige metalen onderdelen.
- De hoge grondstofprijs heeft een grote invloed op de rendabiliteit van kleine onderdelen
Deze kostenfactor dwingt ingenieurs vaak om PEEK alleen te gebruiken voor de meest kritische toepassingen waar de unieke eigenschappen absoluut noodzakelijk zijn. In veel gevallen raden we kosteneffectievere alternatieven aan voor niet-kritische onderdelen in een assemblage.
Uitdagingen voor productie
PEEK kent verschillende productie-uitdagingen die de productie complexer en duurder kunnen maken:
Moeilijkheden bij machinale bewerking: De hoge thermische weerstand van PEEK vertaalt zich in een slechte thermische geleiding, wat warmteontwikkeling veroorzaakt tijdens bewerkingen. Dit vereist lagere snijsnelheden, regelmatige gereedschapswissels en zorgvuldige koelstrategieën.
Vereisten voor verwerkingstemperatuur: Met een smeltpunt van 343°C (649°F) vereist PEEK speciale hogetemperatuurapparatuur voor spuitgieten en extrusie.
Beperkt Verwerkingsvenster: Het verschil tussen de smelttemperatuur van PEEK en het begin van degradatie is relatief klein, wat een uitdaging vormt tijdens de verwerking.
Vormkrimp: PEEK vertoont een aanzienlijke krimp (ongeveer 1-1,3%) tijdens het koelen, wat een nauwkeurig matrijsontwerp vereist om strakke toleranties te bereiken.
Bij PTSMAKE hebben we speciale bewerkingsprotocollen voor PEEK ontwikkeld om deze uitdagingen het hoofd te bieden, maar ze verhogen onvermijdelijk de totale kosten en complexiteit van de productie van PEEK-componenten.
Toepassingsbeperkingen
Ondanks de indrukwekkende eigenschappen heeft PEEK beperkingen die het ongeschikt maken voor bepaalde toepassingen:
- Slechte UV-bestendigheid: Zonder additieven degradeert PEEK bij langdurige blootstelling aan UV-licht, wat het gebruik in buitentoepassingen beperkt.
- Beperkte kleuropties: Door zijn natuurlijke amber/bruine kleur en hoge verwerkingstemperaturen is PEEK moeilijk consistent te kleuren.
- Elektrische beperkingen: Hoewel PEEK een goede isolator is, is het in vergelijking met gespecialiseerde elektrische polymeren niet ideaal voor hoogfrequente elektrische toepassingen.
- Moeilijkheden met verbinden: De chemische bestendigheid van PEEK maakt hechting moeilijk en vereist vaak speciale oppervlaktebehandelingen.
Kosten-batenanalyse: Wanneer is PEEK de moeite waard?
Gezien de aanzienlijke kostenstijging van PEEK is een grondige kosten-batenanalyse essentieel voordat dit materiaal wordt gespecificeerd. Mijn ervaring is dat PEEK in de volgende scenario's de beste waarde biedt:
Scenario's waarin PEEK uitblinkt
Omgevingen met hoge temperaturen: Wanneer de bedrijfstemperaturen hoger zijn dan 149°C (300°F), is PEEK vaak de enige haalbare kunststofoptie, waardoor de hogere kosten gerechtvaardigd zijn.
Chemisch agressieve instellingen: In toepassingen die worden blootgesteld aan meerdere chemicaliën of bijzonder agressieve stoffen, voorkomt de brede chemische bestendigheid van PEEK de veelvuldige vervangingen die nodig zijn bij mindere materialen.
Kritische slijtagetoepassingen: Voor onderdelen in kritische systemen die onderhevig zijn aan constante wrijving en slijtage, kunnen de uitzonderlijke slijtvastheid en lage wrijving van PEEK de onderhoudsintervallen aanzienlijk verlengen.
Vereisten voor gewichtsvermindering: Bij het vervangen van metalen onderdelen in ruimtevaarttoepassingen of toepassingen met hoge prestaties kan de verhouding sterkte/gewicht van PEEK prestatievoordelen opleveren die de kosten rechtvaardigen.
Medische implantaattoepassingen: De biocompatibiliteit en chemische stabiliteit van PEEK maken het ideaal voor implanteerbare hulpmiddelen op lange termijn waarbij materiaaldefecten geen optie zijn.
Vergelijking van alternatieve materialen
Voor toepassingen die niet specifiek de extreme eigenschappen van PEEK vereisen, kunnen verschillende alternatieven voldoende prestaties leveren tegen lagere kosten:
Materiaal | Comparatief voordeel | Kosten vs. PEEK | Belangrijkste beperking |
---|---|---|---|
PPS (polyfenyleensulfide) | Goede hittebestendigheid (400°F) | 40-60% lager | Minder bestand tegen chemicaliën |
PTFE (polytetrafluorethyleen) | Superieure chemische weerstand | 30-50% lager | Slechte mechanische sterkte |
PEI (polyetherimide) | Goede hittebestendigheid, transparantie | 30-40% lager | Minder slijtvast |
PAI (polyamide-imide) | Hoge sterkte, goede slijtvastheid | 10-20% lager | Moeilijker te verwerken |
Acetaal (POM) | Uitstekende bewerkbaarheid, lage kosten | 80-90% lager | Beperkte temperatuurbestendigheid |
Industriespecifieke overwegingen
Verschillende industrieën geven prioriteit aan verschillende aspecten van het eigenschappenprofiel van PEEK:
Ruimtevaart en defensie
In luchtvaarttoepassingen rechtvaardigt de combinatie van licht gewicht, vlambestendigheid (met additieven) en thermische stabiliteit van PEEK de hogere prijs voor componenten zoals:
- Bussen en lagers in besturingssystemen
- Elektrische connectoren en isolatoren
- Structurele componenten in zones met hoge temperaturen
- Onderdelen van brandstofsystemen die bestand moeten zijn tegen chemicaliën
Medisch en gezondheidszorg
De medische industrie waardeert PEEK om zijn:
- Biocompatibiliteit (implantaatkwaliteit)
- Weerstand tegen herhaalde sterilisatie
- Radiolucentie (verstoort röntgenstralen niet)
- Mechanische eigenschappen vergelijkbaar met bot (indien versterkt)
Deze eigenschappen maken PEEK ideaal voor implanteerbare hulpmiddelen en chirurgische instrumenten, ondanks de hoge kosten.
Industriële apparatuur
Voor industriële toepassingen hangt de beslissing om PEEK te gebruiken meestal af van de zwaarte van de bedrijfsomstandigheden:
- Extreme omgevingen (hoge temperatuur, chemische blootstelling) rechtvaardigen vaak PEEK
- Toepassingen waar de onderbreking uiterst duur voordeel van PEEK betrouwbaarheid is
- Nauwkeurige componenten profiteren van de maatvastheid van PEEK
Bij PTSMAKE, helpen wij cliënten door deze overwegingen navigeren om te bepalen of de premieprestaties van PEEK zijn premieprijs voor hun specifieke toepassingsbehoeften rechtvaardigen.
Ik genereer de inhoud voor hoofdstuk 7 van het artikel "Waarom is PEEK zo duur?" volgens jouw vereisten.
Waarom is PEEK zo duur?
Heeft u wel eens een sticker shock ervaren toen u een offerte aanvroeg voor PEEK onderdelen? Als ingenieurs voor het eerst geconfronteerd worden met de prijs van deze hoogwaardige kunststof, vragen velen zich af of een materiaal wel zo'n hoge prijs kan rechtvaardigen, vooral in vergelijking met meer gangbare technische kunststoffen die behoorlijke prestaties lijken te leveren voor een fractie van de prijs.
De hoge kosten van PEEK zijn te wijten aan het complexe productieproces, de dure grondstoffen, de gespecialiseerde apparatuur en de relatief lage productievolumes. Het ingewikkelde polymerisatieproces vereist precieze omstandigheden, terwijl de gepatenteerde aard van de productietechnologie en de status van PEEK als gespecialiseerd materiaal de marktprijs nog verder opdrijven.
Het complexe productieproces achter PEEK
Om te begrijpen waarom PEEK zo'n hoge prijs heeft, moet eerst worden gekeken naar het productieproces. In tegenstelling tot eenvoudigere polymeren vereist de productie van PEEK een geavanceerde chemie en precieze verwerkingsomstandigheden die een aanzienlijke invloed hebben op de uiteindelijke kosten.
Grondstofkosten en schaarste
De monomeren die worden gebruikt voor de productie van PEEK zijn zelf dure speciale chemicaliën. De belangrijkste ingrediënten zijn:
- Difenylether
- 4,4′-difluorbenzofenon
- Kaliumcarbonaat
- Difenylsulfon (als oplosmiddel)
Deze precursoren vereisen meerdere raffinagestappen om de zuiverheid te bereiken die nodig is voor de synthese van PEEK, waardoor de kosten nog hoger worden voordat de polymerisatie begint. Bovendien is de productiecapaciteit van sommige van deze chemicaliën wereldwijd beperkt, wat leidt tot aanbodbeperkingen die de prijzen opdrijven.
Als we bij PTSMAKE PEEK inkopen voor machinale bewerkingsprojecten, betalen we niet alleen voor het polymeer zelf, maar voor de hele waardeketen van gespecialiseerde chemicaliën die aan de creatie ervan ten grondslag liggen.
Complexiteit polymerisatieproces
Voor de synthese van PEEK is een geavanceerd nucleofiel aromatisch substitutiepolymerisatieproces nodig. Deze reactie moet plaatsvinden onder nauwkeurig gecontroleerde omstandigheden:
- Temperaturen tussen 300-400°C (572-752°F)
- Inerte atmosfeer om oxidatie te voorkomen
- Gespecialiseerde drukvaten
- Langere reactietijden (vaak 3-5 uur)
- Zorgvuldig katalysatorbeheer
Elk van deze vereisten maakt de productie complexer en duurder. De reactie moet gedurende het hele proces zorgvuldig worden gecontroleerd om een juiste verdeling van het moleculaire gewicht en kristalliniteit te garanderen, die de prestatie-eigenschappen van het materiaal direct beïnvloeden.
Beperkte productieschaal en marktdynamiek
De status van PEEK als gespecialiseerd materiaal is van grote invloed op de rendabiliteit van de productie en de marktprijzen.
Bedrijfseigen technologie en octrooibescherming
De oorspronkelijke PEEK productietechnologie werd in de jaren 1970 ontwikkeld en gepatenteerd door Victrex (voorheen ICI). Tot op de dag van vandaag is de productietechnologie grotendeels gepatenteerd en beschermd door diverse patenten. Deze beperkte concurrentie op het gebied van productiemethoden heeft ervoor gezorgd dat de prijzen hoger zijn gebleven in vergelijking met gangbare kunststoffen.
Hoewel er nu wereldwijd verschillende fabrikanten zijn (waaronder Victrex, Solvay en Evonik), gebruikt elk van hen eigen processen waarvoor enorme R&D-investeringen nodig waren om ze te ontwikkelen. Deze ontwikkelingskosten moeten worden terugverdiend via de materiaalprijzen.
Productie Volume Economie
In tegenstelling tot basiskunststoffen die jaarlijks in miljoenen tonnen worden geproduceerd, wordt PEEK in relatief kleine volumes vervaardigd:
Plastic Type | Wereldwijde jaarlijkse productie | Relatieve kostenfactor |
---|---|---|
Polyethyleen (PE) | ~100 miljoen ton | 1× (basislijn) |
Nylon (PA) | ~8 miljoen ton | 2-3× |
Polycarbonaat (PC) | ~4,5 miljoen ton | 3-4× |
PEEK | <10.000 ton | 30-50× |
Dit beperkte productievolume betekent dat fabrikanten niet de schaalvoordelen kunnen behalen die de kosten voor gewone kunststoffen drukken. Vaste kosten zoals onderhoud van faciliteiten, kwaliteitscontrole en R&D worden uitgesmeerd over minder kilo's product, waardoor de kosten per eenheid stijgen.
Apparatuur en verwerkingsvereisten
De productiefaciliteiten voor PEEK vereisen gespecialiseerde apparatuur die bestand is tegen de extreme temperaturen en drukken die nodig zijn voor polymerisatie, compounding en verwerking:
- Hoge-temperatuurreactoren met nauwkeurige regelsystemen
- Gespecialiseerde extrusie- en pelletiseerapparatuur
- Geavanceerde filtratie- en zuiveringssystemen
- Uitgebreide faciliteiten voor kwaliteitscontrole en testen
Deze kapitaalinvesteringen zijn aanzienlijk en dragen aanzienlijk bij aan de uiteindelijke materiaalkosten. Wanneer we PEEK-onderdelen bij PTSMAKE bewerken, nemen we deze upstream productiekosten mee in de grondstofprijs.
Uitdagingen op het gebied van verwerking en bewerking
Na de productie brengt PEEK extra uitdagingen met zich mee op het gebied van bewerking en verwerking, die nog eens extra bijdragen aan de hoge kosten van afgewerkte onderdelen.
Hoge verwerkingstemperaturen
Met een smeltpunt van ongeveer 343 °C (649 °F) vereist PEEK gespecialiseerde verwerkingsapparatuur:
- Spuitgietmachines met mogelijkheden voor hoge temperaturen
- Mallen met speciale warmtebeheersystemen
- Duurdere verwarmingselementen en regelaars
- Verbeterde veiligheidssystemen voor het hanteren van materialen met hoge temperaturen
Door deze eisen zijn er minder fabrikanten die PEEK kunnen verwerken, waardoor de concurrentie wordt beperkt en de verwerkingskosten hoger blijven.
Bewerkingsoverwegingen en gereedschapsslijtage
Bij het bewerken van PEEK bij PTSMAKE komen we verschillende factoren tegen die bijdragen aan hogere productiekosten:
Slijtage van gereedschap: PEEK veroorzaakt aanzienlijk meer gereedschapsslijtage dan standaard kunststoffen, waardoor gereedschap vaker moet worden vervangen of premium gereedschap moet worden gebruikt.
Warmtebeheer: De lage thermische geleidbaarheid van PEEK betekent dat er warmte wordt opgebouwd tijdens het bewerken, waardoor lagere snijsnelheden en speciale koeltechnieken nodig zijn.
Gespecialiseerde expertise: Een juiste bewerking van PEEK vereist ervaring en kennis om materiaaldegradatie te voorkomen en nauwe toleranties te bereiken.
Vereisten voor nabewerking: Veel toepassingen van PEEK vereisen extra verwerkingsstappen zoals gloeien om interne spanningen te verlichten en dimensiestabiliteit te garanderen.
Elk van deze factoren draagt bij aan de totale kosten van de productie van afgewerkte PEEK-componenten die verder gaan dan alleen de grondstofprijs.
Kosten voor kwaliteitscontrole en certificering
Als hoogwaardig materiaal dat vaak in kritische toepassingen wordt gebruikt, vereist PEEK een strenge kwaliteitscontrole tijdens de productie en verwerking.
Strenge testvereisten
Elke batch PEEK wordt uitgebreid getest om dit te verifiëren:
- Molecuulgewichtverdeling
- Kristalliniteitspercentage
- Thermische eigenschappen (glasovergang en smeltpunten)
- Mechanische eigenschappen (treksterkte, modulus, rek)
- Zuiverheid en verontreinigingsniveaus
Deze tests vereisen gespecialiseerde apparatuur en opgeleid personeel, waardoor de kosten voor kwaliteitsborging aanzienlijk hoger zijn dan de prijs van het eindproduct.
Industriecertificeringen en traceerbaarheid
Veel PEEK-toepassingen in de ruimtevaart, de medische sector en de halfgeleiderindustrie vereisen volledige traceerbaarheid van het materiaal en naleving van industriespecifieke normen:
- Luchtvaartcertificeringen (AS9100, NORSOK)
- Normen voor medische hulpmiddelen (ISO 13485, USP klasse VI)
- Nucleaire industrie certificeringen (NQSA-1)
- Vereisten voor de halfgeleiderindustrie (hoge zuiverheid)
Het onderhouden van deze certificeringen vereist uitgebreide documentatie, regelmatige audits en soms aparte productiefaciliteiten of apparatuur, wat allemaal bijdraagt aan hogere kosten.
Vergelijken van GLUURT met alternatieve materialen
Om de prijsstelling van PEEK in zijn context te begrijpen, is het nuttig om het te vergelijken met alternatieve materialen, zowel wat de kosten als de prestaties betreft.
Kosten-prestatieanalyse
PEEK kost doorgaans 5-10 keer meer dan standaard technische kunststoffen en kan op volumebasis zelfs duurder zijn dan sommige speciale metalen. De prestaties in extreme omgevingen rechtvaardigen deze meerprijs echter vaak wel:
Eigendom | PEEK | Standaard Techniekplastieken | Hoogwaardige metalen |
---|---|---|---|
Temperatuur voor continu gebruik | Tot 250°C (480°F) | 80-170°C (176-338°F) | Gewoonlijk onbeperkt |
Chemische weerstand | Uitstekend | Variabel (vaak beperkt) | Vaak slecht (corrosie) |
Specifieke sterkte | Zeer hoog | Matig | Hoog |
Kosten grondstoffen | Zeer hoog | Laag tot gemiddeld | Matig tot hoog |
Verwerkingskosten | Hoog | Laag tot gemiddeld | Hoog |
Levensduur | Uitstekend | Beperkt in zware omstandigheden | Goed maar met corrosieproblemen |
Op PTSMAKE, helpen we vaak klanten evalueren deze afwegingen om te bepalen of PEEK de premie prijs wordt gerechtvaardigd door de prestatievoordelen in hun specifieke toepassing.
Is PEEK de hoofdprijs waard?
De vraag of de hoge kosten van PEEK gerechtvaardigd zijn, hangt volledig af van de toepassingseisen.
Toepassingen waar PEEK waarde biedt ondanks de kosten
PEEK biedt ondanks zijn hoge prijs een uitstekende waarde in toepassingen met:
- Extreme gebruiksomgevingen waar andere materialen het snel zouden begeven
- Gewichtskritieke systemen waar de sterkte-gewichtverhouding van PEEK voordelen biedt
- Onderhoudsgevoelige apparatuur waar de kosten van stilstand veel hoger zijn dan de materiaalkosten
- Corrosieve omgevingen waar metalen snel zouden degraderen
- Medische implantaten waar biocompatibiliteit en stabiliteit op lange termijn essentieel zijn
In deze scenario's vertalen de prestatievoordelen van PEEK zich direct in lagere levensduurkosten, ondanks de hogere initiële investering.
Strategieën voor kostenbesparing voor PEEK-componenten
Voor projecten die de prestaties van PEEK vereisen maar een beperkt budget hebben, kunt u deze benaderingen overwegen:
- Hybride ontwerpen PEEK alleen gebruiken voor kritieke onderdelen
- Geoptimaliseerde bewerkingstechnieken materiaalafval verminderen
- Bijna-netvorm verwerking materiaalverbruik minimaliseren
- Ontwerpoptimalisatie om het totale materiaalvolume te verminderen
- Ongevulde rangen wanneer versterkingen niet nodig zijn voor prestaties
Bij PTSMAKE hebben we veel klanten geholpen bij het implementeren van deze strategieën om de voordelen van PEEK te benutten en tegelijkertijd de kosten effectief te beheren.
Hoe PEEK bewerken optimaliseren voor kosteneffectieve productie?
Hebt u zich ooit afgevraagd of er een manier is om de uitzonderlijke eigenschappen van PEEK te benutten zonder uw projectbudget te overschrijden? Wanneer u werkt met een van de duurste technische kunststoffen op de markt, is het optimaliseren van uw bewerkingsaanpak niet alleen een kwestie van efficiëntie - het kan het verschil betekenen tussen een winstgevend project en een project dat geld verliest door overmatig materiaalafval en onnodige bewerkingstijd.
Het optimaliseren van de bewerking van PEEK voor kosteneffectieve productie vereist het gebruik van de juiste snijgereedschappen (hardmetaal of met diamant bekleed), het aanhouden van de juiste snelheden en voedingen (meestal langzamer dan bij standaard kunststoffen), het toepassen van effectieve koelstrategieën, het minimaliseren van materiaalverspilling door een bijna-netvormig ontwerp en het zorgvuldig plannen van de gereedschapsbanen om de cyclustijden te verkorten.
Optimale gereedschappen selecteren voor PEEK-bewerking
Bij het bewerken van PEEK is de keuze van het gereedschap van grote invloed op zowel de productkwaliteit als de totale bewerkingskosten. Jarenlange ervaring heeft me geleerd dat investeren in de juiste gereedschappen op de lange termijn aanzienlijk meer bespaart.
Materialen en geometrieën voor snijgereedschappen
De abrasieve aard van PEEK, vooral gevulde kwaliteiten die koolstofvezels of glas bevatten, vereist een zorgvuldige gereedschapsselectie:
Gereedschapsmateriaal | Beste voor | Levensduur gereedschap | Kostenfactor |
---|---|---|---|
Hardmetaal (ongecoat) | Ongevuld PEEK | Goed | Matig |
Met diamant bekleed carbide | Gevuld PEEK | Uitstekend | Hoog |
PCD (polykristallijn diamant) | Productie van grote volumes | Superieur | Zeer hoog |
Staal met hoge snelheid (HSS) | Eenvoudige bewerkingen op ongevuld PEEK | Beperkt | Laag |
Voor de meeste toepassingen bij PTSMAKE gebruiken we hardmetalen gereedschappen met specifieke geometrieën die ontworpen zijn voor hoogwaardige kunststoffen. De belangrijkste eigenschappen waar we naar kijken zijn onder andere:
- Scherpe snijranden (vermindert warmteontwikkeling)
- Grote positieve hellingshoeken (10-15°)
- Gepolijste groeven (verbetert spaanafvoer)
- Voldoende vrijloophoeken (voorkomt wrijving)
Hoewel premium gereedschappen in eerste instantie meer kosten, behouden ze langer hun scherpte en produceren ze betere oppervlaktekwaliteiten, waardoor er minder secundaire bewerkingen nodig zijn.
Overwegingen met betrekking tot gereedschapsslijtage
Gereedschapsslijtage treedt veel sneller op bij het bewerken van PEEK in vergelijking met standaard technische kunststoffen. We hebben gemerkt dat het controleren en beheersen van gereedschapsslijtage essentieel is voor het behoud van zowel de productkwaliteit als de kostenbeheersing.
Ik raad aan om een vervangingsschema op te stellen op basis van het bewerkte volume in plaats van te wachten op visuele tekenen van slijtage. In onze werkplaats worden gereedschappen voor het bewerken van PEEK doorgaans vervangen na ongeveer 60-70% van de levensduur die we verwachten bij het bewerken van aluminium. Deze proactieve aanpak voorkomt kwaliteitsproblemen en mogelijk afgedankte onderdelen als gevolg van het bewerken met versleten gereedschap.
Snijparameters optimaliseren
De juiste balans vinden tussen snelheid, voeding en snedediepte is cruciaal voor efficiënt PEEK bewerken. Het doel is om de materiaalafnamesnelheid te maximaliseren zonder overmatige hitte te genereren of de oppervlaktekwaliteit in gevaar te brengen.
Snelheid en voedingsaanbevelingen
Na uitvoerig testen bij PTSMAKE hebben we deze algemene richtlijnen voor PEEK-bewerkingsparameters ontwikkeld:
PEEK Type | Snijsnelheid (SFM) | Toevoersnelheid | Zaagdiepte | Koelvloeistof |
---|---|---|---|---|
Ongevuld PEEK | 300-500 | Matig | 0.005"-0.020" | Lucht of nevel |
30% Koolstofgevuld | 200-400 | Verlaagd (75%) | 0.005"-0.015" | Nevel/overstroming |
30% Glas Gevuld | 250-450 | Verlaagd (85%) | 0.005"-0.015" | Nevel/overstroming |
Deze parameters moeten worden aangepast op basis van uw specifieke gereedschap, machinestijfheid en productvereisten. Ik raad over het algemeen aan om aan de conservatieve kant van deze bereiken te beginnen en de parameters geleidelijk te verhogen terwijl ik de resultaten controleer.
Hittebeheerstrategieën
De slechte thermische geleidbaarheid van PEEK kan leiden tot warmteontwikkeling tijdens de bewerking, wat mogelijk de oorzaak is:
- Dimensionale instabiliteit
- Degradatie van de oppervlakteafwerking
- Versnelde gereedschapsslijtage
- Materiaaldecompositie in extreme gevallen
Om deze problemen te bestrijden, implementeren we verschillende technieken voor thermisch beheer:
Juiste keuze van koelvloeistof: Voor ongevuld PEEK werkt persluchtkoeling vaak goed. Voor gevulde kwaliteiten zorgt nevel- of vloedkoeling voor een betere warmteafvoer.
Intermitterend snijden: Door regelmatig te pauzeren tijdens het diepliggen kan de warmte worden afgevoerd.
Klimfrezen: Het gebruik van klimfrezen in plaats van conventioneel frezen vermindert wrijving en warmteontwikkeling.
Meerdere lichtpassages: Meerdere lichte nabewerkingen in plaats van één zware snede verbetert de maatnauwkeurigheid en oppervlakteafwerking.
Strategieën voor materiaalgebruik
Gezien de hoge kosten van PEEK (vaak $75-200 per pond, afhankelijk van de soort en vorm) wordt materiaalgebruik een kritieke kostenfactor. Elk beetje afval heeft een directe impact op uw bedrijfsresultaten.
Startmateriaal met bijna-netvorm
Beginnen met materiaal dat dichter bij de uiteindelijke afmetingen ligt, kan de hoeveelheid afval aanzienlijk verminderen. Overweeg deze benaderingen:
Aangepaste extrusies: Voor onderdelen met een consistente doorsnede kan het beginnen met op maat geëxtrudeerde profielen aanzienlijke materiaalverspilling elimineren. De hogere instelkosten worden gecompenseerd door materiaalbesparingen bij grotere productieruns.
Voorgesneden blanks: Als uw materiaalleverancier voorgesneden vormstukken levert met specifieke afmetingen voor uw onderdelen, vermindert dat zowel het afval als de eerste bewerkingstijd.
Nestsoftware: Voor vlakke producten die bewerkt worden uit plaat kan geavanceerde nestingsoftware het materiaalgebruik 15-30% optimaliseren in vergelijking met handmatige lay-outplanning.
Bij PTSMAKE hebben we klanten geholpen om de materiaalkosten voor PEEK met meer dan 40% te verlagen door deze benaderingen toe te passen voor hun hoogvolume componenten.
Overwegingen bij chiprecycling
In tegenstelling tot sommige thermoplasten kan PEEK niet gemakkelijk zelf worden gerecycled vanwege de hoge verwerkingstemperatuur. Er bestaan echter gespecialiseerde recyclingdiensten:
- Schone, gesorteerde PEEK-chips kunnen worden verkocht aan recyclingbedrijven
- Sommige recyclers verrekenen de waarde van het materiaal met toekomstige aankopen
- Gevulde kwaliteiten hebben doorgaans een lagere recyclewaarde vanwege vervuiling
Hoewel recycling uw materiaalkosten niet volledig zal compenseren, kan het voor grotere machinale bewerkingen wel voor enige terugwinning van kosten zorgen.
Optimalisatie bewerkingsstrategie
Naast de gereedschappen en parameters heeft uw algehele bewerkingsaanpak een grote invloed op zowel de productkwaliteit als de productiekosten.
Opspansystemen voor meerdere onderdelen
Goed ontworpen opspanmiddelen die het mogelijk maken om meerdere onderdelen in een enkele opstelling te bewerken, bieden verschillende voordelen:
- Kortere insteltijd per onderdeel
- Verbeterde consistentie tussen onderdelen
- Efficiënter machinegebruik
- Betere materiaalopbrengst uit plaatvoorraad
Voor een klant uit de lucht- en ruimtevaartsector hebben we een opspanning ontworpen waarmee 16 kleine PEEK-componenten tegelijk bewerkt konden worden, waardoor de kosten per onderdeel met 62% daalden ten opzichte van afzonderlijke opstellingen.
CAM-strategie verfijnen
Geoptimaliseerde gereedschapspaden kunnen de bewerkingstijd drastisch verkorten en de productkwaliteit verbeteren:
Zeer efficiënt frezen: Door gebruik te maken van geavanceerde CAM-strategieën die een consistente aanzet van het gereedschap garanderen, worden cyclustijden verkort en standtijden verlengd.
Bewerking: Goed opeenvolgende bewerkingen waarbij grotere gereedschappen worden gebruikt voor bulk materiaalverwijdering en kleinere alleen waar nodig, optimaliseren zowel de materiaalverwijderingssnelheid als de standtijd.
Geoptimaliseerde benaderingsbewegingen: Het minimaliseren van luchtsnijden door efficiënte naderings- en intrekbewegingen kan de cyclustijden met 5-15% verkorten zonder gevolgen voor de productkwaliteit.
Kwaliteitscontrole om uitval te minimaliseren
Gezien de hoge materiaalkosten van PEEK is het terugdringen van uitval een primaire kostenbesparingsstrategie. Effectieve kwaliteitscontroleprocessen die problemen vroegtijdig opsporen, voorkomen verspilling van duur materiaal aan onderdelen die niet aan de specificaties voldoen.
Meting tijdens proces
We hebben verschillende procesverificatiestappen geïmplementeerd:
Inspectie eerste artikel: Meet het eerste deel van elke run grondig voordat je verder gaat met de productie.
Gefaseerde inspecties: Cruciale kenmerken meten voordat er volgende bewerkingen worden uitgevoerd, vooral bij het omdraaien of opnieuw stansen van onderdelen.
Thermische stabilisatie: Onderdelen op omgevingstemperatuur laten komen voor de uiteindelijke metingen, omdat de thermische uitzetting van PEEK de afmetingen kan beïnvloeden.
Dankzij deze praktijken hebben we een uitvalpercentage van minder dan 2% voor PEEK-componenten, aanzienlijk lager dan de gemiddelden in de sector.
Overwegingen na het machinaal bewerken
Het proces eindigt niet wanneer het onderdeel van de machine komt. Bewerkingen na het bewerken kunnen zowel de kwaliteit als de kosten aanzienlijk beïnvloeden.
Ontlasting en dimensionale stabiliteit
PEEK onderdelen met complexe geometrieën of ongelijkmatige materiaalverwijdering kunnen baat hebben bij spanningsontlasting om dimensionale stabiliteit op lange termijn te garanderen:
Thermisch ontharden: Gecontroleerde verwarming onder de glasovergangstemperatuur gevolgd door langzame afkoeling kan interne spanningen wegnemen.
Ruw-tot-finish strategie: De maatnauwkeurigheid wordt verbeterd door het meeste materiaal in een eerste bewerking te verwijderen en het werkstuk vervolgens te laten stabiliseren voor de uiteindelijke bewerking.
Voor kritieke onderdelen met krappe toleranties zijn deze extra stappen de investering meer dan waard om kostbare defecten in de praktijk of dimensionale afwijkingen na verloop van tijd te voorkomen.
Door deze optimalisatiestrategieën toe te passen, hebben we bij PTSMAKE tal van klanten geholpen om PEEK kosteneffectief te bewerken zonder afbreuk te doen aan de uitzonderlijke prestatie-eigenschappen die dit materiaal zo waardevol maken. De sleutel is een holistische benadering die elk aspect van het productieproces in ogenschouw neemt, van materiaalkeuze tot eindinspectie.
Leer meer over technieken voor thermisch beheer bij hoogwaardige kunststofbewerking. ↩
Leer geavanceerde technieken voor precisiebewerking van hoogwaardige thermoplasten. ↩
Klik hier om gespecialiseerde technieken te ontdekken voor het nauwkeurig bewerken van hoogwaardige thermoplasten. ↩
Ontdek hoe mechanische eigenschappen de materiaalselectie beïnvloeden voor hoogwaardige componenten. ↩
Leer gespecialiseerde bewerkingstechnieken om warmtegerelateerde vervorming in hoogwaardige thermoplasten te voorkomen. ↩