Are you struggling to find the right material for demanding applications where standard plastics fail? Many engineers face challenges when components need to withstand extreme temperatures, chemicals, or mechanical stress. Traditional plastics simply can’t hold up, leading to frequent part failures and costly replacements.
PEEK machining is the process of cutting, drilling, and shaping polyetheretherketone (PEEK) material using CNC machines. This high-performance thermoplastic offers exceptional heat resistance up to 480°F, outstanding chemical resistance, and strength comparable to some metals.
I’ve worked with countless customers who switched to PEEK machining for their critical components. The results speak for themselves – longer-lasting parts, better performance in harsh environments, and reduced maintenance cycles. If you’re wondering whether PEEK might be the solution for your application, keep reading to discover the unique properties and machining techniques that make this material so valuable in precision manufacturing.
Is PEEK Better Than Delrin For Machining?
Have you ever been caught in the middle of a material selection dilemma, torn between PEEK and Delrin for your critical engineering project? When performance matters and failure isn’t an option, choosing the wrong plastic can lead to premature wear, equipment downtime, and costly redesigns.
While PEEK offers superior temperature resistance (up to 480°F), exceptional chemical stability, and higher strength, Delrin (POM) provides better machinability, dimensional stability, and lower cost. The "better" choice depends entirely on your specific application requirements and budget constraints.
Understanding PEEK and Delrin: Fundamental Differences
When comparing these two high-performance engineering plastics, it’s important to understand their basic composition and characteristics. PEEK (Polyetheretherketone) is a semi-crystalline thermoplastic with exceptional resistance to thermal degradation, while Delrin (Polyoxymethylene or POM) is an acetal homopolymer known for its excellent dimensional stability.
Material Properties Comparison
The physical and mechanical properties of these materials significantly impact their machining characteristics and end-use performance.
Property | PEEK | Delrin (POM) |
---|---|---|
Heat Deflection Temperature | 315°F (157°C) | 257°F (125°C) |
Tensile Strength | 14,500 psi | 10,000 psi |
Chemical Resistance | Excellent (resists most acids, bases) | Good (vulnerable to strong acids) |
Wear Resistance | Superior | Very Good |
Cost Factor | 4-5× higher than Delrin | Moderate |
Density | 1.32 g/cm³ | 1.41 g/cm³ |
Machining Characteristics: How They Perform Under the Tool
In my experience at PTSMAKE, I’ve found that machinability is often the deciding factor when choosing between these materials. Delrin generally machines more predictably than PEEK, producing smoother surface finishes with less effort.
Tool Wear and Cutting Parameters
PEEK is more abrasive on cutting tools, requiring more frequent tool changes. When machining PEEK, we typically reduce cutting speeds by about 15-20% compared to Delrin to minimize heat buildup. This is crucial because PEEK’s low thermal conductivity causes heat concentration at the cutting zone, potentially causing thermal deformation1 if not properly managed.
Delrin, on the other hand, offers excellent dimensional stability during machining and can be cut at higher speeds. It produces less tool wear and generally requires fewer specialized machining techniques.
Surface Finish Considerations
One advantage of Delrin is its ability to achieve excellent surface finishes with standard machining parameters. PEEK often requires additional polishing steps to achieve comparable surface quality.
Cost-Benefit Analysis for Engineering Applications
The cost difference between these materials can be substantial. PEEK typically costs 4-5 times more than Delrin, making it important to evaluate whether its premium properties justify the investment.
When PEEK Justifies Its Premium Price
I recommend PEEK for applications involving:
- Extreme operating temperatures (above 250°F)
- Aggressive chemical environments
- High mechanical loading in elevated temperatures
- Medical or aerospace applications requiring biocompatibility or flame resistance
When Delrin Is The Better Choice
Delrin makes more economic sense when:
- Operating temperatures remain below 180°F
- Chemical exposure is limited to moderate solvents
- Cost sensitivity is a major factor
- Parts require excellent dimensional stability and machined precision
- High production volumes make material cost a significant factor
Industry-Specific Considerations
Different industries prioritize different material properties. In the aerospace sector, where we’ve supplied numerous components, PEEK’s flame resistance and exceptional strength-to-weight ratio often justify its higher cost. For automotive applications, Delrin’s combination of reasonable cost and good mechanical properties often wins out.
Medical and Food Processing Applications
For medical devices, PEEK’s biocompatibility and sterilization resistance make it invaluable despite the cost premium. In food processing equipment, Delrin’s FDA compliance and lower cost often make it the preferred choice, unless high temperatures are involved.
Industrial Machinery Components
In industrial applications, I’ve seen the decision frequently come down to operating conditions. Gears, bearings, and wear components that operate in moderate conditions perform excellently in Delrin, while those exposed to extreme conditions benefit from PEEK’s superior properties.
Making The Right Choice For Your Application
The decision between PEEK and Delrin should be driven by a thorough analysis of your specific operating conditions. At PTSMAKE, we consider:
- Maximum operating temperature
- Chemical exposure profile
- Mechanical load requirements
- Budget constraints
- Service life expectations
By carefully evaluating these factors against each material’s properties, you can make an informed decision that balances performance and cost-effectiveness for your specific application.
What Is the Difference Between Acetal and PEEK?
Ever struggled to choose between acetal and PEEK for your critical engineering components? When project success hinges on material selection, the wrong choice can lead to premature failures, unexpected downtime, and budget-crushing redesigns that could have been avoided with proper material knowledge.
Acetal (POM) and PEEK differ primarily in their performance characteristics and cost. PEEK offers superior heat resistance (480°F vs 180°F), better chemical resistance, and higher strength, while acetal provides excellent machinability, dimensional stability, and costs significantly less, making it ideal for less demanding applications.
Key Differences Between Acetal and PEEK
Understanding the fundamental differences between these two engineering plastics is crucial for making informed decisions for your projects. Both materials have established themselves as go-to options in precision manufacturing, but they serve distinctly different purposes based on their inherent properties.
Material Composition and Structure
Acetal, commonly known by the brand name Delrin (when in homopolymer form) or by its chemical name polyoxymethylene (POM), features a highly crystalline structure with repeating -CH₂O- groups. This structure gives it excellent dimensional stability and machinability.
PEEK (polyetheretherketone), on the other hand, belongs to the polyaryletherketone family and contains aromatic rings connected by ether and ketone linkages. This molecular structure creates exceptional thermal stability and chemical resistance.
Performance Characteristics Comparison
The performance differences between these materials make them suitable for distinct applications:
Property | Acetal (POM) | PEEK | Best For |
---|---|---|---|
Heat Resistance | 180°F (82°C) continuous | 480°F (250°C) continuous | PEEK |
Chemical Resistance | Good (except strong acids) | Excellent (resistant to most chemicals) | PEEK |
Tensile Strength | 8,800-10,000 psi | 14,500-16,000 psi | PEEK |
Wear Resistance | Very Good | Excellent | PEEK |
Machinability | Excellent | Good (requires specialized techniques) | Acetal |
Cost Factor | Base reference (1×) | 4-7× higher than Acetal | Acetal |
Moisture Absorption | 0.2-0.25% | 0.1-0.15% | PEEK |
Cost-Benefit Analysis
In my years working with customers at PTSMAKE, I’ve noticed that cost considerations often drive the initial material selection process. Acetal is significantly more economical than PEEK, making it the default choice when extreme conditions aren’t present.
PEEK’s premium price reflects its superior performance capabilities. When evaluating whether the additional investment is justified, consider the following factors:
- Operating temperature requirements
- Chemical exposure profile
- Mechanical stress levels
- Expected service life
- Downtime costs associated with component failure
Machining Considerations
Tool Life and Cutting Parameters
Acetal is renowned for its exceptional machinability. It cuts cleanly, holds tight tolerances, and produces excellent surface finishes with minimal effort. Standard carbide tools work well, and the material doesn’t cause excessive tool wear.
PEEK presents more challenges during machining. Its high temperature resistance means heat dissipation during machining is poor, requiring:
- Reduced cutting speeds (typically 20-30% slower than acetal)
- More frequent tool changes
- Careful attention to heat buildup
- Specialized cooling techniques
At PTSMAKE, we’ve developed specific thermal management protocols2 for PEEK machining to ensure dimensional accuracy and prevent material degradation during the cutting process.
Dimensional Stability
Acetal offers excellent dimensional stability after machining, with minimal warpage or stress relaxation. This makes it particularly valuable for precision components with tight tolerances.
PEEK also exhibits good dimensional stability but requires more careful annealing processes to relieve internal stresses after machining. Without proper thermal conditioning, PEEK parts may experience slight dimensional changes over time, especially in high-precision applications.
Application-Specific Recommendations
Automotive and Transportation
In automotive applications where temperatures remain moderate (under 180°F), acetal often provides the best value. Common applications include:
- Fuel system components
- Door locking mechanisms
- Interior trim clips and fasteners
- Bearing surfaces in non-critical areas
For higher temperature zones such as under-hood components or parts near exhaust systems, PEEK’s thermal stability makes it the better choice despite the higher cost.
Medical and Pharmaceutical
The medical industry has embraced PEEK for its biocompatibility and resistance to sterilization methods. It’s commonly used in:
- Implantable devices
- Surgical instruments
- Medical imaging components
- Laboratory equipment
Acetal still finds applications in less demanding medical settings, such as:
- Disposable instrument components
- Laboratory test fixtures
- Diagnostic equipment housings
Industrial Equipment
For industrial machinery, the choice often depends on operating conditions:
- Standard operating environments: Acetal provides excellent value for gears, bearings, and wear surfaces in normal conditions.
- Harsh environments: PEEK justifies its premium price when exposed to high temperatures, chemicals, or extreme mechanical stress.
Making the Optimal Selection
When helping clients choose between acetal and PEEK at PTSMAKE, I recommend a systematic approach:
- Identify the most demanding conditions the part will face (temperature, chemicals, loads)
- Determine if acetal’s properties are sufficient to handle these conditions
- Calculate the cost difference between options for your specific volume requirements
- Consider the consequences of failure and associated downtime costs
- Evaluate whether PEEK’s premium performance justifies its higher price
Remember that material selection is rarely one-size-fits-all. Sometimes a hybrid approach works best, using PEEK only for the most critical components while utilizing acetal for less demanding parts within the same assembly.
What Is the Difference Between PTFE and PEEK?
Have you ever found yourself lost in the sea of high-performance plastics, unsure whether to choose PTFE or PEEK for your critical application? When project deadlines loom and material selection could make or break your design, the pressure to make the right choice can be overwhelming, especially when both materials come with impressive technical specifications.
PTFE and PEEK are both high-performance thermoplastics with distinct differences. PTFE offers unmatched chemical resistance, extremely low friction (0.05-0.10 coefficient), and operates from -328°F to 500°F but has poor mechanical strength. PEEK provides superior mechanical properties, excellent wear resistance, and maintains structural integrity up to 480°F while being more machinable.
Molecular Structure and Basic Properties
The fundamental differences between PTFE and PEEK begin at the molecular level, which explains their distinct performance characteristics in various applications.
Chemical Composition
PTFE (Polytetrafluoroethylene) features a carbon backbone completely surrounded by fluorine atoms. This unique structure gives PTFE its exceptional chemical inertness and low friction properties. The carbon-fluorine bonds are among the strongest in organic chemistry, making PTFE incredibly resistant to chemical attack.
PEEK (Polyetheretherketone), meanwhile, has a more complex molecular structure with aromatic rings connected by ether and ketone linkages. This aromatic backbone provides PEEK with its excellent mechanical strength and thermal stability.
Comparative Property Analysis
Property | PTFE | PEEK | Advantage |
---|---|---|---|
Maximum Continuous Use Temperature | 500°F (260°C) | 480°F (250°C) | PTFE (slightly) |
Minimum Operating Temperature | -328°F (-200°C) | -65°F (-54°C) | PTFE |
Coefficient of Friction | 0.05-0.10 (lowest of any solid) | 0.35-0.40 | PTFE |
Tensile Strength | 3,000-5,000 psi | 14,000-16,000 psi | PEEK |
Chemical Resistance | Superior (universal) | Excellent (limited by strong acids) | PTFE |
Machinability | Challenging (soft, deforms easily) | Good | PEEK |
Wear Resistance | Poor to Moderate | Excellent | PEEK |
Electrical Properties | Excellent insulator | Good insulator | PTFE |
Cost Factor | Moderate | High (3-4× more than PTFE) | PTFE |
Thermal Performance Differences
Temperature performance is often a critical decision factor when selecting between these materials.
Heat Resistance and Stability
While both materials offer exceptional heat resistance, they behave differently at elevated temperatures. PTFE maintains its chemical inertness and low friction up to its maximum temperature but begins to lose mechanical integrity at much lower temperatures (around 260°F/127°C).
PEEK, meanwhile, maintains its mechanical strength much closer to its maximum temperature. This makes PEEK significantly more valuable in applications requiring both heat resistance and mechanical loading.
I’ve seen numerous applications where customers initially selected PTFE based solely on temperature ratings, only to discover that the material couldn’t handle the mechanical stresses at those temperatures. PEEK’s ability to maintain structural integrity at high temperatures often makes it worth the higher price point.
Cold Temperature Performance
For cryogenic applications, PTFE holds a distinct advantage. It remains flexible and functional down to -328°F (-200°C), while PEEK becomes increasingly brittle below -65°F (-54°C). This makes PTFE the clear choice for aerospace, laboratory, and other ultra-low temperature environments.
Mechanical Strength Comparison
The mechanical properties of these materials differ dramatically, making their suitability application-specific.
Structural Integrity Under Load
PEEK offers vastly superior mechanical performance with tensile strength averaging 14,000-16,000 psi compared to PTFE’s modest 3,000-5,000 psi. This makes PEEK suitable for load-bearing applications where PTFE would quickly deform or fail.
At PTSMAKE, we frequently recommend PEEK for structural components that experience consistent mechanical loads, especially at elevated temperatures. The material’s exceptional creep resistance allows it to maintain dimensional stability under continuous stress.
Wear Resistance and Friction
PTFE’s remarkably low coefficient of friction (0.05-0.10) makes it the material of choice for applications requiring minimal friction. However, this same property contributes to its poor wear resistance, as the material can easily be scraped away in high-wear scenarios.
PEEK demonstrates excellent wear resistance while maintaining a reasonable coefficient of friction (0.35-0.40). For applications involving continuous movement against other surfaces, PEEK typically outlasts PTFE by a considerable margin.
Many of our customers achieve the best of both worlds by using PEEK as the structural material with a thin PTFE coating or liner where friction reduction is needed.
Chemical Resistance Profiles
Both materials offer exceptional chemical resistance, but with important distinctions.
Resistance to Aggressive Environments
PTFE represents the gold standard for chemical resistance, being virtually inert to almost all chemicals (with rare exceptions like molten alkali metals and elemental fluorine). This universal chemical resistance makes PTFE invaluable in chemical processing, semiconductor manufacturing, and laboratory environments.
PEEK offers excellent chemical resistance to most substances but can be attacked by concentrated sulfuric acid and some other strong acids. For most industrial environments, however, PEEK’s chemical resistance is more than adequate.
Hydrolysis and Moisture Absorption
PTFE is completely hydrophobic and absorbs essentially no moisture, even after prolonged exposure. PEEK, while highly resistant to hydrolysis, will absorb a small amount of moisture (0.1-0.3%) when exposed to humid environments for extended periods.
For ultra-pure water applications or systems where even minute contamination is unacceptable, PTFE often remains the preferred choice despite its mechanical limitations.
%[PEEK and PTFE machined components for structural comparison](
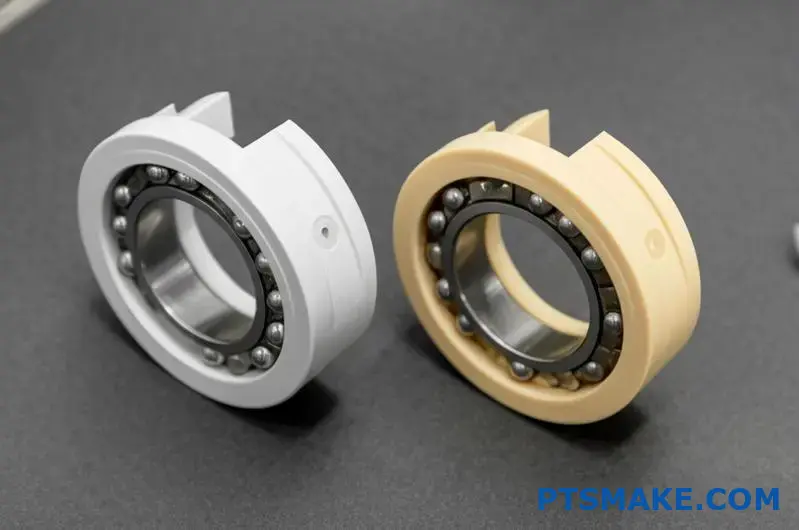
"PEEK And PTFE Bearing Components")
Machining and Fabrication Considerations
The machinability3 differences between these materials significantly impact manufacturing costs and capabilities.
Machining Challenges and Solutions
PTFE presents unique machining challenges due to its softness and tendency to cold flow. It requires specialized tooling, slower cutting speeds, and careful fixturing to prevent deformation during machining. Sharp tooling is essential to prevent tearing or deforming the material.
PEEK machines more like traditional engineering plastics, though its abrasive nature causes more rapid tool wear than many other materials. When machining PEEK, we typically use carbide tooling and appropriate cooling techniques to manage heat buildup.
Manufacturing Process Compatibility
PTFE’s high melt viscosity makes conventional injection molding impossible. Instead, it must be processed using techniques like compression molding, ram extrusion, or skiving from billets. This limits design complexity and increases manufacturing costs for complex shapes.
PEEK can be processed through conventional methods like injection molding and extrusion, allowing for more complex geometries and potentially lower production costs at higher volumes. This processing versatility gives PEEK an advantage for intricate components or when transitioning from prototyping to mass production.
Cost-Benefit Analysis for Different Applications
The significant price difference between these materials necessitates careful consideration of their application-specific value.
Value Proposition Comparison
While PEEK typically costs 3-4 times more than PTFE, its superior mechanical properties and wear resistance often provide better long-term value in applications where mechanical failure would be costly or dangerous.
For applications primarily requiring chemical resistance, low friction, or electrical insulation properties without significant mechanical stress, PTFE usually offers better value despite its limitations.
Industry-Specific Selection Criteria
Different industries prioritize different material properties:
- Chemical processing: PTFE’s universal chemical resistance typically outweighs its mechanical limitations.
- Aerospace: Both materials find applications, with PEEK used for structural components and PTFE for seals and electrical insulation.
- Medical: PEEK’s biocompatibility and structural strength make it popular for implants, while PTFE is preferred for catheter linings and other low-friction applications.
- Semiconductor: PTFE dominates due to its exceptional purity and resistance to aggressive chemicals.
- Automotive: PEEK’s wear resistance and mechanical properties make it valuable for under-hood components facing mechanical stress.
What Is the Difference Between PVDF and PEEK?
Have you ever faced the dilemma of choosing between PVDF and PEEK for a critical project where material selection could make or break your design? When standard plastics won’t suffice and you need exceptional chemical resistance or thermal stability, the confusion between these two high-performance materials can lead to costly mistakes or compromised performance.
PVDF (polyvinylidene fluoride) and PEEK (polyetheretherketone) differ primarily in their performance characteristics and applications. PEEK offers superior heat resistance (480°F vs 300°F), better mechanical strength, and exceptional wear resistance, while PVDF provides excellent chemical resistance, UV stability, and comes at a significantly lower cost.
Key Differences Between PVDF and PEEK
When comparing these two engineering thermoplastics, understanding their fundamental properties helps determine which material is best suited for specific applications. Both materials are considered high-performance options, but they excel in different environments and applications.
Material Composition and Structure
PVDF is a semi-crystalline fluoropolymer consisting of repeating units of vinylidene difluoride. Its molecular structure includes carbon-fluorine bonds that provide excellent chemical resistance, though not as comprehensive as fully-fluorinated polymers like PTFE.
PEEK belongs to the polyaryletherketone family and features a complex molecular structure with aromatic rings connected by ether and ketone linkages. This unique structure gives PEEK its exceptional thermal stability and mechanical strength.
Performance Characteristics Comparison
The following table provides a detailed comparison of key properties between PVDF and PEEK:
Property | PVDF | PEEK | Superior Material |
---|---|---|---|
Maximum Continuous Use Temperature | 300°F (149°C) | 480°F (250°C) | PEEK |
Mechanical Strength (Tensile) | 5,800-7,800 psi | 14,500-16,000 psi | PEEK |
Chemical Resistance | Excellent (most acids, bases) | Very Good (limited by strong acids) | PVDF |
UV Resistance | Excellent | Fair to Good | PVDF |
Wear Resistance | Good | Excellent | PEEK |
Coefficient of Friction | 0.25-0.35 | 0.35-0.40 | PVDF |
Cost Factor | Moderate | 2-3× higher than PVDF | PVDF |
Moisture Absorption | 0.03-0.04% | 0.1-0.15% | PVDF |
Density | 1.75-1.78 g/cm³ | 1.30-1.32 g/cm³ | Application-dependent |
Thermal Performance and Stability
Temperature capabilities often drive material selection decisions in many engineering applications.
Heat Resistance Comparison
PEEK demonstrates exceptional thermal stability, maintaining its mechanical properties at temperatures up to 480°F (250°C) for continuous use. This makes it ideal for applications in high-temperature environments where traditional plastics would fail.
PVDF, while still considered a high-temperature plastic, has a lower maximum continuous use temperature of approximately 300°F (149°C). This temperature range is sufficient for many industrial applications but falls short in extreme thermal environments.
In my experience working with customers at PTSMAKE, this temperature differential often becomes the deciding factor when selecting between these materials for applications like semiconductor processing equipment, where process temperatures can exceed PVDF’s capabilities.
Thermal Cycling Behavior
Both materials handle thermal cycling differently:
- PVDF exhibits good dimensional stability during thermal cycling, though it may experience more significant thermal expansion than PEEK.
- PEEK maintains exceptional dimensional stability even through repeated thermal cycles, making it preferable for precision components that must maintain tight tolerances across varying temperatures.
Chemical Resistance Profiles
Chemical resistance is another crucial factor that distinguishes these materials.
Resistance to Aggressive Environments
PVDF offers excellent resistance to a wide range of chemicals, including:
- Most acids (including concentrated hydrochloric and sulfuric acids)
- Aliphatic and aromatic hydrocarbons
- Alcohols and chlorinated solvents
- Oxidizing agents
PEEK demonstrates good chemical resistance to many substances but can be attacked by concentrated sulfuric acid and some other strong acids. It’s particularly resistant to hydrolysis and steam sterilization, which makes it valuable in medical applications.
Industry-Specific Chemical Considerations
Different industries prioritize specific chemical resistance properties:
- Chemical processing: PVDF is often preferred for its comprehensive resistance to acids and chlorinated compounds.
- Semiconductor: Both materials are used, with selection depending on specific process chemicals.
- Oil and gas: PEEK’s combination of mechanical properties and chemical resistance makes it valuable for downhole applications.
- Pharmaceutical: PVDF’s excellent resistance to cleaning agents and sterilization methods makes it popular for processing equipment.
Mechanical Properties and Structural Applications
The mechanical strength4 differences between these materials significantly impact their suitability for load-bearing applications.
Load-Bearing Capabilities
PEEK offers substantially higher mechanical strength with tensile values typically ranging from 14,500-16,000 psi, compared to PVDF’s more modest 5,800-7,800 psi. This makes PEEK superior for structural components that must withstand significant mechanical loads.
For applications requiring both chemical resistance and structural integrity, PEEK often provides the best balance of properties, despite its higher cost. I’ve recommended PEEK for numerous applications at PTSMAKE where components need to withstand both aggressive chemicals and mechanical stress.
Wear Resistance and Friction Properties
PEEK demonstrates excellent wear resistance, making it ideal for bearings, bushings, and other components subject to continuous friction. Its self-lubricating properties help extend the service life of moving parts in demanding environments.
PVDF offers good wear resistance, though not at the level of PEEK. Its lower coefficient of friction (0.25-0.35 compared to PEEK’s 0.35-0.40) can be advantageous in certain low-load sliding applications where reduced friction is more important than maximum wear resistance.
Electrical and Thermal Insulation Properties
Both materials offer distinct electrical characteristics that make them suitable for different applications.
Dielectric Properties
PVDF is known for its piezoelectric properties, which allow it to generate an electrical charge in response to applied mechanical stress. This unique characteristic makes PVDF valuable in sensor applications.
PEEK provides excellent electrical insulation properties across a wide temperature range, maintaining its dielectric strength even at elevated temperatures. This makes it particularly valuable in high-temperature electrical applications where standard plastics would fail.
Thermal Conductivity
PVDF and PEEK both have relatively low thermal conductivity compared to metals, making them good thermal insulators:
- PVDF: 0.17-0.19 W/m·K
- PEEK: 0.25-0.29 W/m·K
This low thermal conductivity can be either an advantage or disadvantage depending on the application. For components requiring thermal isolation, both materials perform well, though PVDF provides slightly better insulation.
Cost Considerations and Value Analysis
The significant price difference between these materials makes cost-benefit analysis essential.
Initial Material Cost
PEEK typically costs 2-3 times more than PVDF, representing a substantial cost premium that must be justified by performance requirements. This price differential stems from PEEK’s more complex manufacturing process and the higher cost of raw materials.
Lifetime Value Assessment
When evaluating total cost of ownership, several factors beyond initial material cost should be considered:
- Expected service life in the target environment
- Replacement frequency and associated downtime costs
- Installation and maintenance requirements
- Safety and reliability concerns
In many high-temperature or high-load applications, PEEK’s superior performance justifies its higher initial cost through extended service life and improved reliability. For applications within PVDF’s capabilities, the lower-cost material often provides better overall value.
Processing and Fabrication Considerations
Manufacturing capabilities and limitations also influence material selection.
Machining Differences
When machining these materials at PTSMAKE, we’ve observed significant differences:
- PVDF machines relatively well but requires sharp tooling and appropriate speeds to prevent melting or galling.
- PEEK is more challenging to machine due to its abrasiveness and poor thermal conductivity, which can lead to heat buildup during cutting operations.
For precision components, PEEK generally holds tighter tolerances during machining but requires more specialized techniques and tooling, potentially increasing manufacturing costs.
Manufacturing Methods Compatibility
Both materials can be processed through multiple manufacturing methods:
- PVDF: Injection molding, extrusion, compression molding, machining
- PEEK: Injection molding, extrusion, compression molding, machining, 3D printing (specialized equipment)
PVDF offers slightly more processing flexibility at lower temperatures, while PEEK requires higher processing temperatures but provides more options for complex geometries through advanced manufacturing techniques.
Application-Specific Selection Guidelines
Different industries prioritize different material properties, leading to varied material preferences.
Semiconductor Industry
In semiconductor manufacturing, both materials find applications, but in different areas:
- PVDF: Commonly used for ultra-pure water systems, chemical delivery components, and filtration equipment.
- PEEK: Preferred for components exposed to high temperatures, such as wafer handling equipment and process chamber components.
Chemical Processing Equipment
For chemical processing applications:
- PVDF: Excellent for pumps, valves, fittings, and tanks handling corrosive chemicals at moderate temperatures.
- PEEK: Better suited for components requiring both chemical resistance and high temperature capability or mechanical strength.
Medical and Pharmaceutical Applications
In medical applications:
- PVDF: Commonly used in filtration membranes, sutures, and some implantable devices.
- PEEK: Preferred for implantable devices, especially orthopedic applications, due to its biocompatibility, radiolucency, and mechanical properties similar to bone.
When helping clients select between PVDF and PEEK at PTSMAKE, I recommend a systematic approach that evaluates the most critical environmental factors first (temperature, chemicals, mechanical loads), then considers secondary factors like cost, processing requirements, and availability.
<
Is PEEK a Polyethylene?
Have you ever found yourself confused by the array of engineering plastics with similar-sounding names? When selecting materials for critical applications, this confusion can lead to costly mistakes, performance failures, and wasted resources if you mistakenly substitute one high-performance plastic for another.
No, PEEK (polyetheretherketone) is not a polyethylene. PEEK is an aromatic polyether with ketone groups in its backbone, creating a semi-crystalline thermoplastic with exceptional heat resistance (up to 480°F), excellent chemical resistance, and superior mechanical properties that far exceed those of polyethylene materials.
Chemical Structure and Classification Differences
When examining PEEK versus polyethylene, the fundamental differences start at the molecular level. These structural variations explain why these materials behave so differently in practical applications.
Molecular Backbone Comparison
PEEK features a complex aromatic backbone structure with ether and ketone linkages between benzene rings. This molecular architecture gives PEEK its outstanding thermal stability and mechanical strength. The aromatic rings create rigidity, while the ether linkages provide some flexibility.
Polyethylene, by contrast, has one of the simplest polymer structures possible – just a linear chain of carbon atoms with hydrogen atoms attached. This straightforward structure exists in various forms (HDPE, LDPE, UHMWPE), but all lack the aromatic components and functional groups that give PEEK its exceptional properties.
This fundamental structural difference means PEEK belongs to an entirely different polymer family than polyethylene. While polyethylene is classified as a polyolefin, PEEK belongs to the polyaryletherketone (PAEK) family of high-performance thermoplastics.
Key Property Differences
The molecular structure differences translate to dramatic performance variations:
Property | PEEK | Polyethylene (HDPE) | Difference Factor |
---|---|---|---|
Maximum Continuous Use Temperature | 480°F (250°C) | 180°F (82°C) | PEEK is 2.7× higher |
Tensile Strength | 14,500 psi | 4,500 psi | PEEK is 3.2× stronger |
Chemical Resistance | Excellent (resists most chemicals) | Good (vulnerable to aromatic solvents) | PEEK offers broader resistance |
Cost | High | Low | PEEK costs 15-20× more |
Density | 1.32 g/cm³ | 0.95 g/cm³ | PEEK is 39% denser |
Hardness (Shore D) | 85-90 | 60-70 | PEEK is significantly harder |
Manufacturing Process Differences
The production methods for PEEK and polyethylene reflect their different molecular structures and performance characteristics.
PEEK Production Process
PEEK is manufactured through a complex process involving nucleophilic aromatic substitution polymerization. This requires precise temperature control and specialized catalysts. The monomer materials are significantly more expensive than ethylene, contributing to PEEK’s higher cost.
At PTSMAKE, when we machine PEEK components, we must account for this material’s unique properties – its lower thermal conductivity means heat management during machining is critical to prevent localized thermal degradation.
Polyethylene Manufacturing
Polyethylene is produced through addition polymerization of ethylene using various catalysts depending on the desired density and branching. This relatively straightforward process can be conducted at lower temperatures and pressures than PEEK production, especially for low-density varieties.
Performance in Extreme Environments
High-Temperature Performance
One of the most significant differences between these materials is their thermal stability:
- PEEK maintains its mechanical properties up to 480°F (250°C) for continuous use and can withstand short exposures to even higher temperatures.
- Polyethylene begins to soften around 180°F (82°C) and loses most of its mechanical strength well below that temperature.
I’ve seen numerous applications where clients initially selected polyethylene based on cost, only to experience rapid failure when operating temperatures exceeded expectations. In one aerospace application, a client switched from polyethylene to PEEK for a component near a heat source, extending its service life from months to years despite the higher initial material cost.
Chemical Resistance Comparison
While both materials offer good chemical resistance, PEEK provides broader protection against harsh chemicals:
- PEEK resists most acids, bases, hydrocarbons, and organic solvents
- Polyethylene has good resistance to acids and bases but can be attacked by aromatic hydrocarbons and some oxidizing agents
This difference becomes critical in chemical processing equipment, semiconductor manufacturing, and medical applications where exposure to multiple chemicals is common.
Application Suitability
Aerospace and Defense Applications
In aerospace applications, PEEK’s combination of light weight, flame resistance, and thermal stability make it invaluable for components like:
- Interior components requiring flame resistance
- Electrical connectors and insulators
- Structural components in high-temperature zones
- Fuel system components requiring chemical resistance
Polyethylene rarely meets the demanding requirements of aerospace applications due to its limited thermal stability and mechanical properties.
Medical and Healthcare Uses
The biocompatibility profiles of these materials also differ significantly:
- PEEK is biocompatible and used in implantable devices, surgical instruments, and medical equipment requiring sterilization
- Medical-grade polyethylene (primarily UHMWPE) is used in some implants like artificial joints, but lacks PEEK’s temperature resistance for repeated steam sterilization
Industrial Equipment Components
For industrial machinery, the choice between these materials typically depends on operating conditions:
- PEEK excels in high-temperature environments, applications requiring excellent wear resistance, or exposure to harsh chemicals
- Polyethylene provides adequate performance in ambient-temperature applications with moderate mechanical requirements and is often chosen for its lower cost and ease of processing
Cost-Benefit Considerations
The price difference between these materials is substantial – PEEK typically costs 15-20 times more than high-density polyethylene. This significant cost differential means material selection should be based on a thorough analysis of:
- Required operating temperature range
- Chemical exposure profile
- Mechanical load requirements
- Expected service life
- Consequences of failure
For applications within polyethylene’s capability range, its lower cost makes it the economical choice. However, when performance requirements exceed polyethylene’s limitations, PEEK’s superior properties easily justify its premium price through extended service life, improved reliability, and reduced maintenance costs.
Machining and Processing Differences
At PTSMAKE, we’ve found significant differences in machining these materials:
- PEEK requires specialized cutting parameters due to its thermal behavior5 during machining, but holds tight tolerances and produces excellent surface finishes
- Polyethylene is easier to machine but has a tendency to deform under cutting forces, making tight tolerances more difficult to maintain
Understanding these processing differences is essential when designing components for manufacturability and precision.
What Are the Disadvantages and Advantages of PEEK?
Have you ever struggled to decide if PEEK is worth its premium price for your critical application? When project success hinges on material selection, choosing between expensive high-performance plastics and more economical alternatives can be a tough balancing act with real consequences for reliability and longevity.
PEEK offers exceptional advantages including remarkable heat resistance (up to 480°F), outstanding chemical resistance, excellent mechanical strength, and superior wear properties. However, these benefits come with significant disadvantages including high cost (5-10 times more than standard engineering plastics), challenging machinability, limited color options, and poor UV resistance.
Understanding PEEK’s Exceptional Properties
PEEK (Polyetheretherketone) stands out among engineering plastics due to its unique combination of properties that make it suitable for the most demanding applications. As someone who’s specified materials for countless precision components, I’ve seen firsthand how PEEK’s properties translate to real-world performance benefits.
Thermal Performance Advantages
One of PEEK’s most impressive characteristics is its thermal stability. This material maintains its mechanical properties at temperatures that would cause most plastics to fail catastrophically.
Temperature Characteristic | PEEK Performance | Comparison to Standard Plastics |
---|---|---|
Continuous Service Temperature | Up to 480°F (250°C) | 2-3× higher than most engineering plastics |
Glass Transition Temperature | 289°F (143°C) | Maintains rigidity at higher temperatures |
Melting Point | 649°F (343°C) | Allows for steam sterilization |
Thermal Conductivity | 0.25 W/m·K | Better than many plastics for heat dissipation |
This exceptional thermal resistance allows PEEK to be used in applications near heat sources where standard plastics would quickly deform or degrade. I’ve helped many clients replace failed components made from lesser materials with PEEK parts that continue to perform flawlessly despite challenging thermal environments.
Chemical Resistance Benefits
PEEK’s chemical resistance profile is nearly as impressive as its thermal properties. The material shows excellent resistance to:
- Hydrocarbons and organic solvents
- Most acids and bases (except concentrated sulfuric acid)
- Steam and hot water
- Automotive fluids and fuels
- Medical sterilization processes
This broad chemical resistance makes PEEK particularly valuable in environments where exposure to multiple aggressive substances is expected. In the semiconductor industry, for example, PEEK components can withstand the harsh chemicals used in wafer processing while maintaining dimensional stability.
Mechanical Property Advantages
PEEK’s mechanical strength sets it apart from most other thermoplastics:
- Tensile strength of 14,500 psi (comparable to some metals)
- Excellent fatigue resistance
- Outstanding impact resistance and toughness
- Superior wear resistance
- Low coefficient of friction
These properties make PEEK suitable for structural applications where most plastics would fail. I’ve specified PEEK for gears, bearings, and other high-wear components that operate under significant mechanical stress, often replacing metal parts with lighter-weight PEEK alternatives that provide additional benefits like corrosion resistance and noise reduction.
The Significant Disadvantages of PEEK
Despite its impressive performance characteristics, PEEK comes with several significant drawbacks that must be carefully considered during material selection.
Cost Constraints
The most obvious disadvantage of PEEK is its cost. At PTSMAKE, we often have to help clients understand the price premium of PEEK compared to other engineering plastics:
- PEEK typically costs 5-10 times more than engineering plastics like nylon or acetal
- Material costs for PEEK parts can be 20-30% higher than equivalent metal components
- The high raw material price significantly impacts small part economics
This cost factor often forces engineers to reserve PEEK for only the most critical applications where its unique properties are absolutely necessary. In many cases, we recommend more cost-effective alternatives for non-critical components in an assembly.
Manufacturing Challenges
PEEK presents several manufacturing challenges that can increase production complexity and cost:
Machining Difficulties: PEEK’s high thermal resistance translates to poor thermal conductivity, causing heat buildup during machining operations. This requires slower cutting speeds, frequent tool changes, and careful cooling strategies.
Processing Temperature Requirements: With a melting point of 649°F (343°C), PEEK requires specialized high-temperature equipment for injection molding and extrusion.
Limited Processing Window: The difference between PEEK’s melting temperature and the onset of degradation is relatively narrow, creating challenges during processing.
Mold Shrinkage: PEEK exhibits significant shrinkage (around 1-1.3%) during cooling, requiring precise mold design to achieve tight tolerances.
At PTSMAKE, we’ve developed specialized machining protocols for PEEK to address these challenges, but they inevitably add to the overall cost and complexity of manufacturing PEEK components.
Application Limitations
Despite its impressive properties, PEEK has limitations that make it unsuitable for certain applications:
- Poor UV Resistance: Without additives, PEEK degrades when exposed to prolonged UV light, limiting its use in outdoor applications.
- Limited Color Options: Due to its natural amber/brown color and high processing temperatures, PEEK is difficult to color consistently.
- Electrical Limitations: While a good insulator, PEEK isn’t ideal for high-frequency electrical applications compared to specialized electrical polymers.
- Bonding Difficulties: PEEK’s chemical resistance makes adhesive bonding challenging, often requiring special surface treatments.
Cost-Benefit Analysis: When Is PEEK Worth It?
Given PEEK’s significant cost premium, a thorough cost-benefit analysis is essential before specifying this material. In my experience, PEEK provides the best value in the following scenarios:
Scenarios Where PEEK Excels
High-Temperature Environments: When operating temperatures exceed 300°F (149°C), PEEK is often the only viable plastic option, making its premium cost justified.
Chemically Aggressive Settings: In applications exposed to multiple chemicals or particularly harsh substances, PEEK’s broad chemical resistance prevents the frequent replacements required with lesser materials.
Critical Wear Applications: For components subject to constant friction and wear in critical systems, PEEK’s exceptional wear resistance and low friction can dramatically extend service intervals.
Weight Reduction Requirements: When replacing metal components in aerospace or high-performance applications, PEEK’s strength-to-weight ratio can provide performance benefits that justify its cost.
Medical Implant Applications: PEEK’s biocompatibility and chemical stability make it ideal for long-term implantable devices where material failure is not an option.
Alternative Materials Comparison
For applications that don’t specifically require PEEK’s extreme properties, several alternatives might provide sufficient performance at lower cost:
Material | Comparative Advantage | Cost vs. PEEK | Key Limitation |
---|---|---|---|
PPS (Polyphenylene Sulfide) | Good heat resistance (400°F) | 40-60% lower | Less chemical resistant |
PTFE (Polytetrafluoroethylene) | Superior chemical resistance | 30-50% lower | Poor mechanical strength |
PEI (Polyetherimide) | Good heat resistance, transparency | 30-40% lower | Less wear resistant |
PAI (Polyamide-imide) | High strength, good wear resistance | 10-20% lower | More difficult to process |
Acetal (POM) | Excellent machinability, low cost | 80-90% lower | Limited temperature resistance |
Industry-Specific Considerations
Different industries prioritize different aspects of PEEK’s property profile:
Aerospace and Defense
In aerospace applications, PEEK’s combination of light weight, flame resistance (with additives), and thermal stability justify its premium price for components like:
- Bushings and bearings in control systems
- Electrical connectors and insulators
- Structural components in high-temperature zones
- Fuel system components requiring chemical resistance
Medical and Healthcare
The medical industry values PEEK for its:
- Biocompatibility (implant grade)
- Resistance to repeated sterilization
- Radiolucency (doesn’t interfere with X-rays)
- Mechanical properties similar to bone (when reinforced)
These properties make PEEK ideal for implantable devices and surgical instruments despite its high cost.
Industrial Equipment
For industrial applications, the decision to use PEEK typically depends on the severity of operating conditions:
- Extreme environments (high temperature, chemical exposure) often justify PEEK
- Applications where downtime is extremely costly benefit from PEEK’s reliability
- High-precision components benefit from PEEK’s dimensional stability
At PTSMAKE, we help clients navigate these considerations to determine whether PEEK’s premium performance justifies its premium price for their specific application needs.
I’ll generate the content for Chapter 7 of the article "Why Is PEEK So Expensive?" according to your requirements.
Why Is PEEK So Expensive?
Have you ever experienced sticker shock when requesting a quote for PEEK components? When engineers first encounter the price of this high-performance plastic, many question if any material could possibly justify such a premium cost, especially when compared to more common engineering plastics that seem to offer decent performance at a fraction of the price.
PEEK’s high cost stems from its complex manufacturing process, expensive raw materials, specialized equipment requirements, and relatively low production volumes. The intricate polymerization process requires precise conditions, while the proprietary nature of production technology and PEEK’s status as a specialty material further elevate its market price.
The Complex Manufacturing Process Behind PEEK
Understanding why PEEK commands such a premium price begins with examining its manufacturing process. Unlike simpler polymers, PEEK production involves sophisticated chemistry and precise processing conditions that significantly impact the final cost.
Raw Material Costs and Scarcity
The monomers used to produce PEEK are themselves expensive specialty chemicals. The primary ingredients include:
- Diphenyl ether
- 4,4′-difluorobenzophenone
- Potassium carbonate
- Diphenyl sulfone (as a solvent)
These precursors require multiple refining steps to achieve the purity needed for PEEK synthesis, adding layers of cost before polymerization even begins. Additionally, some of these chemicals have limited production capacity worldwide, creating supply constraints that drive up prices.
At PTSMAKE, when we source PEEK for machining projects, we’re paying not just for the polymer itself but for the entire value chain of specialized chemicals that went into its creation.
Polymerization Process Complexity
The synthesis of PEEK involves a sophisticated nucleophilic aromatic substitution polymerization process. This reaction must occur under precisely controlled conditions:
- Temperatures between 300-400°C (572-752°F)
- Inert atmosphere to prevent oxidation
- Specialized pressure vessels
- Extended reaction times (often 3-5 hours)
- Careful catalyst management
Each of these requirements adds to the manufacturing complexity and cost. The reaction must be carefully monitored throughout to ensure proper molecular weight distribution and crystallinity, which directly affect the material’s performance properties.
Limited Production Scale and Market Dynamics
PEEK’s status as a specialty material significantly impacts its economics of production and market pricing.
Proprietary Technology and Patent Protection
The original PEEK manufacturing technology was developed and patented by Victrex (formerly ICI) in the 1970s. Even today, production technology remains largely proprietary and protected by various patents. This limited competition in manufacturing methods has maintained higher pricing compared to commoditized plastics.
While there are now several manufacturers globally (including Victrex, Solvay, and Evonik), each uses proprietary processes that required enormous R&D investments to develop. These development costs must be recouped through material pricing.
Production Volume Economics
Unlike commodity plastics produced in millions of tons annually, PEEK is manufactured in relatively small volumes:
Plastic Type | Global Annual Production | Relative Cost Factor |
---|---|---|
Polyethylene (PE) | ~100 million tons | 1× (baseline) |
Nylon (PA) | ~8 million tons | 2-3× |
Polycarbonate (PC) | ~4.5 million tons | 3-4× |
PEEK | <10,000 tons | 30-50× |
This limited production volume means manufacturers can’t achieve the economies of scale that drive down costs for common plastics. Fixed costs like facility maintenance, quality control, and R&D are spread across fewer kilograms of product, raising the per-unit cost.
Equipment and Processing Requirements
The production facilities for PEEK require specialized equipment that can handle the extreme temperatures and pressures needed for polymerization, compounding, and processing:
- High-temperature reactors with precise control systems
- Specialized extrusion and pelletizing equipment
- Advanced filtration and purification systems
- Comprehensive quality control and testing facilities
These capital investments are substantial and contribute significantly to the final material cost. When we machine PEEK parts at PTSMAKE, we’re inheriting these upstream manufacturing costs in the raw material price.
Processing and Machining Challenges
Once produced, PEEK presents additional challenges in processing and machining that further contribute to its high cost in finished components.
High Processing Temperatures
With a melting point of approximately 343°C (649°F), PEEK requires specialized processing equipment:
- Injection molding machines with high-temperature capabilities
- Molds with special heat management systems
- More expensive heating elements and controllers
- Enhanced safety systems for handling high-temperature materials
These requirements mean that fewer manufacturers are equipped to process PEEK, limiting competition and maintaining higher processing costs.
Machining Considerations and Tool Wear
When machining PEEK at PTSMAKE, we encounter several factors that contribute to higher production costs:
Tool Wear: PEEK causes significantly more tool wear than standard plastics, requiring more frequent tool replacement or the use of premium tooling.
Heat Management: PEEK’s low thermal conductivity means heat builds up during machining, requiring slower cutting speeds and special cooling techniques.
Specialized Expertise: Proper machining of PEEK requires experience and knowledge to prevent material degradation and achieve tight tolerances.
Post-Processing Requirements: Many PEEK applications require additional processing steps like annealing to relieve internal stresses and ensure dimensional stability.
Each of these factors adds to the total cost of producing finished PEEK components beyond just the raw material price.
Quality Control and Certification Costs
As a high-performance material often used in critical applications, PEEK requires rigorous quality control throughout its production and processing.
Stringent Testing Requirements
Each batch of PEEK typically undergoes extensive testing to verify:
- Molecular weight distribution
- Crystallinity percentage
- Thermal properties (glass transition and melting points)
- Mechanical properties (tensile strength, modulus, elongation)
- Purity and contaminant levels
These tests require specialized equipment and trained personnel, adding significant quality assurance costs to the final product price.
Industry Certifications and Traceability
Many PEEK applications in aerospace, medical, and semiconductor industries require full material traceability and compliance with industry-specific standards:
- Aerospace certifications (AS9100, NORSOK)
- Medical device standards (ISO 13485, USP Class VI)
- Nuclear industry certifications (NQSA-1)
- Semiconductor industry requirements (high purity)
Maintaining these certifications requires extensive documentation, regular audits, and sometimes separate production facilities or equipment, all of which contribute to higher costs.
Comparing PEEK to Alternative Materials
To understand PEEK’s pricing in context, it’s helpful to compare it with alternative materials in terms of both cost and performance.
Cost-Performance Analysis
PEEK typically costs 5-10 times more than standard engineering plastics and may even be more expensive than some specialty metals on a volume basis. However, its performance in extreme environments often justifies this premium:
Property | PEEK | Standard Engineering Plastics | Premium Metals |
---|---|---|---|
Continuous Use Temperature | Up to 250°C (480°F) | 80-170°C (176-338°F) | Typically unlimited |
Chemical Resistance | Excellent | Variable (often limited) | Often poor (corrosion) |
Specific Strength | Very High | Moderate | High |
Raw Material Cost | Very High | Low to Moderate | Moderate to High |
Processing Cost | High | Low to Moderate | High |
Lifetime Value | Excellent | Limited in harsh conditions | Good but with corrosion issues |
At PTSMAKE, we often help clients evaluate these tradeoffs to determine if PEEK’s premium price is justified by its performance advantages in their specific application.
Is PEEK Worth the Premium Price?
The question of whether PEEK’s high cost is justified depends entirely on the application requirements.
Applications Where PEEK Provides Value Despite Cost
PEEK delivers excellent value despite its high price in applications featuring:
- Extreme operating environments where other materials would fail quickly
- Weight-critical systems where PEEK’s strength-to-weight ratio offers advantages
- Maintenance-sensitive equipment where the cost of downtime far exceeds material costs
- Corrosive environments where metals would degrade rapidly
- Medical implants where biocompatibility and long-term stability are essential
In these scenarios, PEEK’s performance advantages translate directly to lower lifetime costs despite the higher initial investment.
Cost Reduction Strategies for PEEK Components
For projects requiring PEEK’s performance but constrained by budget, consider these approaches:
- Hybrid designs using PEEK only for critical components
- Optimized machining techniques to reduce material waste
- Near-net-shape processing to minimize material consumption
- Design optimization to reduce overall material volume
- Unfilled grades when reinforcements aren’t necessary for performance
At PTSMAKE, we’ve helped many clients implement these strategies to get PEEK’s benefits while managing costs effectively.
How to Optimize PEEK Machining for Cost-Effective Production?
Ever wondered if there’s a way to harness PEEK’s exceptional properties without breaking your project budget? When working with one of the most expensive engineering plastics on the market, optimizing your machining approach isn’t just about efficiency – it could mean the difference between a profitable project and one that hemorrhages money through excessive material waste and unnecessary machining time.
Optimizing PEEK machining for cost-effective production requires using proper cutting tools (carbide or diamond-coated), maintaining appropriate speeds and feeds (typically slower than standard plastics), implementing effective cooling strategies, minimizing material waste through near-net-shape design, and carefully planning tool paths to reduce cycle times.
Selecting the Optimal Tooling for PEEK Machining
When machining PEEK, your tooling selection dramatically impacts both part quality and overall machining costs. I’ve learned through years of experience that investing in the right tools upfront saves significantly more in the long run.
Cutting Tool Materials and Geometries
The abrasive nature of PEEK, especially filled grades containing carbon fiber or glass, requires careful tool selection:
Tool Material | Best For | Tool Life | Cost Factor |
---|---|---|---|
Carbide (Uncoated) | Unfilled PEEK | Good | Moderate |
Diamond-Coated Carbide | Filled PEEK | Excellent | High |
PCD (Polycrystalline Diamond) | High-volume production | Superior | Very High |
High-Speed Steel (HSS) | Simple operations on unfilled PEEK | Limited | Low |
For most applications at PTSMAKE, we use carbide tools with specific geometries designed for high-performance plastics. The key features we look for include:
- Sharp cutting edges (reduces heat generation)
- High positive rake angles (10-15°)
- Polished flutes (improves chip evacuation)
- Sufficient clearance angles (prevents rubbing)
While premium tools cost more initially, they maintain edge sharpness longer and produce better surface finishes, reducing the need for secondary operations.
Tool Wear Considerations
Tool wear occurs much faster when machining PEEK compared to standard engineering plastics. We’ve found that monitoring and managing tool wear is critical for maintaining both part quality and cost control.
I recommend establishing a tool change schedule based on machined volume rather than waiting for visual signs of wear. In our shop, tools machining filled PEEK are typically changed after approximately 60-70% of the tool life we’d expect when machining aluminum. This proactive approach prevents the quality issues and potential scrapped parts that result from machining with worn tools.
Optimizing Cutting Parameters
Finding the right balance of speed, feed, and depth of cut is crucial for efficient PEEK machining. The goal is to maximize material removal rates without generating excessive heat or compromising surface quality.
Speed and Feed Recommendations
Through extensive testing at PTSMAKE, we’ve developed these general guidelines for PEEK machining parameters:
PEEK Type | Cutting Speed (SFM) | Feed Rate | Depth of Cut | Coolant |
---|---|---|---|---|
Unfilled PEEK | 300-500 | Moderate | 0.005"-0.020" | Air or mist |
30% Carbon Filled | 200-400 | Reduced (75%) | 0.005"-0.015" | Mist/flood |
30% Glass Filled | 250-450 | Reduced (85%) | 0.005"-0.015" | Mist/flood |
These parameters should be adjusted based on your specific tooling, machine rigidity, and part requirements. I generally recommend starting at the conservative end of these ranges and gradually increasing parameters while monitoring results.
Heat Management Strategies
PEEK’s poor thermal conductivity can lead to heat buildup during machining, potentially causing:
- Dimensional instability
- Degraded surface finish
- Accelerated tool wear
- Material decomposition in extreme cases
To combat these issues, we implement several thermal management techniques:
Proper Coolant Selection: For unfilled PEEK, compressed air cooling often works well. For filled grades, mist or flood coolant provides better heat dissipation.
Intermittent Cutting: Pausing periodically during deep pocketing operations allows heat to dissipate.
Climb Milling: Using climb milling rather than conventional milling reduces friction and heat generation.
Multiple Light Passes: Taking several light finishing passes rather than one heavy cut improves dimensional accuracy and surface finish.
Material Utilization Strategies
Given PEEK’s high cost (often $75-200 per pound depending on grade and form), material utilization becomes a critical cost factor. Every bit of waste directly impacts your bottom line.
Near-Net-Shape Starting Material
Starting with material that’s closer to your final dimensions can significantly reduce waste. Consider these approaches:
Custom Extrusions: For parts with consistent cross-sections, starting with custom-extruded profiles can eliminate significant material waste. The higher setup cost is offset by material savings for larger production runs.
Pre-Cut Blanks: Having your material supplier provide pre-cut blanks sized specifically for your parts reduces both waste and initial machining time.
Nesting Software: For flat parts machined from plate, using advanced nesting software can optimize material usage by 15-30% compared to manual layout planning.
At PTSMAKE, we’ve helped clients reduce PEEK material costs by over 40% by implementing these approaches for their high-volume components.
Chip Recycling Considerations
Unlike some thermoplastics, PEEK cannot easily be recycled in-house due to its high processing temperature. However, specialized recycling services do exist:
- Clean, sorted PEEK chips can be sold to recyclers
- Some recyclers will credit material value against future purchases
- Filled grades typically have lower recycling value due to contamination concerns
While recycling won’t completely offset your material costs, it can provide some cost recovery for larger machining operations.
Machining Strategy Optimization
Beyond tooling and parameters, your overall machining approach significantly impacts both part quality and production costs.
Fixture Design for Multiple Parts
Well-designed fixtures that allow machining multiple parts in a single setup offer several advantages:
- Reduced setup time per part
- Improved consistency across parts
- More efficient machine utilization
- Better material yield from plate stock
For one aerospace client, we designed a fixture that allowed machining 16 small PEEK components simultaneously, reducing per-part cost by 62% compared to individual setups.
CAM Strategy Refinement
Optimized tool paths can dramatically reduce machining time and improve part quality:
High-Efficiency Milling: Using advanced CAM strategies that maintain consistent tool engagement reduces cycle times and extends tool life.
Rest Machining: Properly sequenced operations that use larger tools for bulk material removal and smaller tools only where necessary optimize both material removal rates and tool life.
Optimized Approach Moves: Minimizing air cutting through efficient approach and retract moves can reduce cycle times by 5-15% with no impact on part quality.
Quality Control to Minimize Scrap
Given PEEK’s high material cost, scrap reduction becomes a primary cost-saving strategy. Effective quality control processes that catch issues early prevent wasting expensive material on parts that won’t meet specifications.
In-Process Measurement
We’ve implemented several in-process verification steps:
First Article Inspection: Thoroughly measuring the first part of each run before proceeding with production.
Staged Inspections: Measuring critical features before proceeding to subsequent operations, especially when flipping or re-fixturing parts.
Thermal Stabilization: Allowing parts to reach ambient temperature before final measurements, as PEEK’s thermal expansion can affect dimensions.
These practices have helped us maintain a scrap rate below 2% for PEEK components, significantly lower than industry averages.
Post-Machining Considerations
The process doesn’t end when the part comes off the machine. Post-machining operations can significantly impact both quality and cost.
Stress Relief and Dimensional Stability
PEEK parts with complex geometries or uneven material removal may benefit from stress relief to ensure long-term dimensional stability:
Thermal Annealing: Controlled heating below the glass transition temperature followed by slow cooling can relieve internal stresses.
Rough-to-Finish Strategy: Removing most material in an initial operation, then allowing the part to stabilize before final machining improves dimensional accuracy.
For critical components with tight tolerances, these extra steps are well worth the investment to prevent costly field failures or dimensional drift over time.
By implementing these optimization strategies, we’ve helped numerous clients at PTSMAKE achieve cost-effective PEEK machining without compromising the exceptional performance properties that make this material so valuable. The key is a holistic approach that considers every aspect of the manufacturing process, from material selection to final inspection.
Learn about thermal management techniques for high-performance plastic machining. ↩
Learn advanced techniques for precision machining high-performance thermoplastics. ↩
Click here to explore specialized techniques for machining high-performance thermoplastics with precision. ↩
Discover how mechanical properties affect material selection for high-performance components. ↩
Learn specialized machining techniques to prevent heat-related deformation in high-performance thermoplastics. ↩