Czy starasz się znaleźć odpowiedni materiał do wymagających zastosowań, w których standardowe tworzywa sztuczne zawodzą? Wielu inżynierów staje przed wyzwaniami, gdy komponenty muszą wytrzymać ekstremalne temperatury, chemikalia lub naprężenia mechaniczne. Tradycyjne tworzywa sztuczne po prostu nie wytrzymują, co prowadzi do częstych awarii części i kosztownych wymian.
Obróbka PEEK to proces cięcia, wiercenia i kształtowania materiału polieteroeteroketonu (PEEK) za pomocą maszyn CNC. To wysokowydajne tworzywo termoplastyczne oferuje wyjątkową odporność na temperaturę do 480°F, wyjątkową odporność chemiczną i wytrzymałość porównywalną z niektórymi metalami.
Współpracowałem z niezliczoną liczbą klientów, którzy przestawili się na obróbkę PEEK swoich krytycznych komponentów. Rezultaty mówią same za siebie - trwalsze części, lepsza wydajność w trudnych warunkach i krótsze cykle konserwacji. Jeśli zastanawiasz się, czy PEEK może być rozwiązaniem dla Twojej aplikacji, czytaj dalej, aby odkryć unikalne właściwości i techniki obróbki, które sprawiają, że materiał ten jest tak cenny w produkcji precyzyjnej.
Czy PEEK jest lepszy niż Delrin do obróbki skrawaniem?
Czy kiedykolwiek znalazłeś się w środku dylematu związanego z wyborem materiału, rozdarty między PEEK a Delrin dla swojego krytycznego projektu inżynieryjnego? Gdy liczy się wydajność, a awaria nie wchodzi w grę, wybór niewłaściwego tworzywa sztucznego może prowadzić do przedwczesnego zużycia, przestojów sprzętu i kosztownych przeprojektowań.
Podczas gdy PEEK oferuje doskonałą odporność na temperaturę (do 480°F), wyjątkową stabilność chemiczną i wyższą wytrzymałość, Delrin (POM) zapewnia lepszą obrabialność, stabilność wymiarową i niższy koszt. Wybór "lepszego" materiału zależy wyłącznie od konkretnych wymagań aplikacji i ograniczeń budżetowych.
Zrozumieć PEEK i Delrin: Podstawowe różnice
Porównując te dwa wysokowydajne tworzywa konstrukcyjne, ważne jest, aby zrozumieć ich podstawowy skład i właściwości. PEEK (polieteroeteroketon) jest półkrystalicznym tworzywem termoplastycznym o wyjątkowej odporności na degradację termiczną, podczas gdy Delrin (polioksymetylen lub POM) jest homopolimerem acetalu znanym z doskonałej stabilności wymiarowej.
Porównanie właściwości materiałów
Właściwości fizyczne i mechaniczne tych materiałów znacząco wpływają na ich charakterystykę obróbki i wydajność końcową.
Własność | PEEK | Delrin (POM) |
---|---|---|
Temperatura ugięcia cieplnego | 315°F (157°C) | 257°F (125°C) |
Wytrzymałość na rozciąganie | 14 500 psi | 10 000 psi |
Odporność chemiczna | Doskonały (odporny na większość kwasów i zasad) | Dobry (wrażliwy na silne kwasy) |
Odporność na zużycie | Superior | Bardzo dobry |
Współczynnik kosztów | 4-5× wyższa niż Delrin | Umiarkowany |
Gęstość | 1,32 g/cm³ | 1,41 g/cm³ |
Charakterystyka obróbki: Jak działają pod narzędziem
Z mojego doświadczenia w PTSMAKE wynika, że skrawalność jest często decydującym czynnikiem przy wyborze pomiędzy tymi materiałami. Delrin generalnie obrabia się bardziej przewidywalnie niż PEEK, zapewniając gładsze wykończenie powierzchni przy mniejszym wysiłku.
Zużycie narzędzia i parametry skrawania
PEEK jest bardziej ścierny dla narzędzi skrawających, co wymaga częstszej wymiany narzędzi. Podczas obróbki PEEK zazwyczaj zmniejszamy prędkości skrawania o około 15-20% w porównaniu do Delrin, aby zminimalizować gromadzenie się ciepła. Ma to kluczowe znaczenie, ponieważ niska przewodność cieplna PEEK powoduje koncentrację ciepła w strefie cięcia, potencjalnie powodując odkształcenie termiczne1 jeśli nie są odpowiednio zarządzane.
Z drugiej strony, Delrin oferuje doskonałą stabilność wymiarową podczas obróbki i może być cięty z wyższymi prędkościami. Powoduje mniejsze zużycie narzędzi i generalnie wymaga mniej specjalistycznych technik obróbki.
Uwagi dotyczące wykończenia powierzchni
Jedną z zalet materiału Delrin jest możliwość uzyskania doskonałego wykończenia powierzchni przy standardowych parametrach obróbki. PEEK często wymaga dodatkowych etapów polerowania, aby osiągnąć porównywalną jakość powierzchni.
Analiza kosztów i korzyści w zastosowaniach inżynieryjnych
Różnica w kosztach między tymi materiałami może być znaczna. PEEK kosztuje zwykle 4-5 razy więcej niż Delrin, co sprawia, że ważne jest, aby ocenić, czy jego doskonałe właściwości uzasadniają inwestycję.
Kiedy PEEK uzasadnia swoją cenę premium
Polecam PEEK do zastosowań obejmujących:
- Ekstremalne temperatury pracy (powyżej 250°F)
- Agresywne środowiska chemiczne
- Wysokie obciążenie mechaniczne w podwyższonych temperaturach
- Zastosowania medyczne lub lotnicze wymagające biokompatybilności lub odporności na płomienie
Kiedy Delrin jest lepszym wyborem
Delrin ma większy sens ekonomiczny, gdy:
- Temperatury robocze pozostają poniżej 180°F
- Narażenie chemiczne jest ograniczone do umiarkowanych rozpuszczalników
- Wrażliwość na koszty jest głównym czynnikiem
- Części wymagają doskonałej stabilności wymiarowej i precyzji obróbki
- Wysokie wolumeny produkcji sprawiają, że koszty materiałów są istotnym czynnikiem
Rozważania specyficzne dla branży
W różnych branżach priorytetem są różne właściwości materiału. W sektorze lotniczym, gdzie dostarczyliśmy wiele komponentów, odporność PEEK na płomienie i wyjątkowy stosunek wytrzymałości do masy często uzasadniają jego wyższy koszt. W zastosowaniach motoryzacyjnych często wygrywa połączenie rozsądnej ceny i dobrych właściwości mechanicznych materiału Delrin.
Zastosowania medyczne i w przetwórstwie żywności
W przypadku urządzeń medycznych biokompatybilność i odporność na sterylizację PEEK sprawiają, że jest on nieoceniony pomimo wyższej ceny. W przypadku sprzętu do przetwarzania żywności, zgodność Delrin z FDA i niższy koszt często sprawiają, że jest to preferowany wybór, chyba że w grę wchodzą wysokie temperatury.
Komponenty maszyn przemysłowych
W zastosowaniach przemysłowych widziałem, że decyzja często sprowadza się do warunków pracy. Koła zębate, łożyska i elementy zużywające się, które działają w umiarkowanych warunkach, doskonale sprawdzają się w Delrin, podczas gdy te narażone na ekstremalne warunki korzystają z doskonałych właściwości PEEK.
Właściwy wybór dla danego zastosowania
Decyzja między PEEK a Delrin powinna być oparta na dokładnej analizie konkretnych warunków pracy. W PTSMAKE bierzemy pod uwagę:
- Maksymalna temperatura pracy
- Profil narażenia chemicznego
- Wymagania dotyczące obciążenia mechanicznego
- Ograniczenia budżetowe
- Oczekiwania dotyczące żywotności
Dzięki dokładnej ocenie tych czynników w odniesieniu do właściwości każdego materiału, można podjąć świadomą decyzję, która równoważy wydajność i opłacalność dla konkretnego zastosowania.
Jaka jest różnica między acetalem a PEEK?
Czy kiedykolwiek zmagałeś się z wyborem między acetalem a PEEK dla krytycznych komponentów inżynieryjnych? Gdy sukces projektu zależy od wyboru materiału, niewłaściwy wybór może prowadzić do przedwczesnych awarii, nieoczekiwanych przestojów i miażdżących budżet przeprojektowań, których można było uniknąć dzięki odpowiedniej wiedzy na temat materiałów.
Acetal (POM) i PEEK różnią się przede wszystkim charakterystyką i kosztem. PEEK oferuje wyższą odporność na ciepło (480°F vs 180°F), lepszą odporność chemiczną i wyższą wytrzymałość, podczas gdy acetal zapewnia doskonałą obrabialność, stabilność wymiarową i znacznie niższe koszty, co czyni go idealnym do mniej wymagających zastosowań.
Kluczowe różnice między acetalem a PEEK
Zrozumienie podstawowych różnic między tymi dwoma tworzywami sztucznymi jest kluczowe dla podejmowania świadomych decyzji dotyczących projektów. Obydwa materiały zyskały reputację najlepszych opcji w produkcji precyzyjnej, ale służą one wyraźnie różnym celom w oparciu o ich nieodłączne właściwości.
Skład i struktura materiału
Acetal, powszechnie znany pod nazwą handlową Delrin (w postaci homopolimeru) lub pod nazwą chemiczną polioksymetylen (POM), charakteryzuje się wysoce krystaliczną strukturą z powtarzającymi się grupami -CH₂O-. Struktura ta zapewnia doskonałą stabilność wymiarową i skrawalność.
Z drugiej strony PEEK (polieteroeteroketon) należy do rodziny polieteroeteroketonów i zawiera pierścienie aromatyczne połączone wiązaniami eterowymi i ketonowymi. Taka struktura molekularna zapewnia wyjątkową stabilność termiczną i odporność chemiczną.
Porównanie charakterystyk wydajności
Różnice w wydajności między tymi materiałami sprawiają, że nadają się one do różnych zastosowań:
Własność | Acetal (POM) | PEEK | Najlepsze dla |
---|---|---|---|
Odporność na ciepło | 180°F (82°C) w trybie ciągłym | 480°F (250°C) w trybie ciągłym | PEEK |
Odporność chemiczna | Dobry (z wyjątkiem silnych kwasów) | Doskonały (odporny na większość chemikaliów) | PEEK |
Wytrzymałość na rozciąganie | 8 800-10 000 psi | 14 500-16 000 psi | PEEK |
Odporność na zużycie | Bardzo dobry | Doskonały | PEEK |
Obrabialność | Doskonały | Dobry (wymaga specjalistycznych technik) | Acetal |
Współczynnik kosztów | Referencja bazowa (1×) | 4-7× wyższa niż w przypadku acetalu | Acetal |
Absorpcja wilgoci | 0.2-0.25% | 0.1-0.15% | PEEK |
Analiza kosztów i korzyści
Podczas mojej wieloletniej pracy z klientami w PTSMAKE zauważyłem, że względy kosztowe często kierują początkowym procesem wyboru materiału. Acetal jest znacznie bardziej ekonomiczny niż PEEK, co czyni go domyślnym wyborem, gdy nie występują ekstremalne warunki.
Wysoka cena PEEK odzwierciedla jego doskonałą wydajność. Oceniając, czy dodatkowa inwestycja jest uzasadniona, należy wziąć pod uwagę następujące czynniki:
- Wymagania dotyczące temperatury pracy
- Profil narażenia chemicznego
- Poziomy naprężeń mechanicznych
- Przewidywany okres użytkowania
- Koszty przestojów związane z awarią komponentów
Rozważania dotyczące obróbki
Trwałość narzędzia i parametry cięcia
Acetal słynie z wyjątkowej skrawalności. Tnie czysto, zachowuje wąskie tolerancje i zapewnia doskonałe wykończenie powierzchni przy minimalnym wysiłku. Standardowe narzędzia z węglików spiekanych działają dobrze, a materiał nie powoduje nadmiernego zużycia narzędzi.
PEEK stawia więcej wyzwań podczas obróbki skrawaniem. Jego wysoka odporność na temperaturę oznacza, że rozpraszanie ciepła podczas obróbki jest słabe, co wymaga:
- Zmniejszone prędkości cięcia (zazwyczaj 20-30% wolniej niż acetal)
- Częstsze zmiany narzędzi
- Zwracanie szczególnej uwagi na gromadzenie się ciepła
- Specjalistyczne techniki chłodzenia
W PTSMAKE opracowaliśmy specjalne protokoły zarządzania temperaturą2 do obróbki PEEK, aby zapewnić dokładność wymiarową i zapobiec degradacji materiału podczas procesu cięcia.
Stabilność wymiarowa
Acetal oferuje doskonałą stabilność wymiarową po obróbce, przy minimalnym wypaczeniu lub relaksacji naprężeń. Sprawia to, że jest on szczególnie cenny w przypadku precyzyjnych komponentów o wąskich tolerancjach.
PEEK wykazuje również dobrą stabilność wymiarową, ale wymaga bardziej starannych procesów wyżarzania w celu zmniejszenia naprężeń wewnętrznych po obróbce. Bez odpowiedniego kondycjonowania termicznego części z PEEK mogą z czasem ulegać niewielkim zmianom wymiarowym, zwłaszcza w zastosowaniach wymagających wysokiej precyzji.
Zalecenia dotyczące konkretnych zastosowań
Motoryzacja i transport
W zastosowaniach motoryzacyjnych, gdzie temperatury pozostają umiarkowane (poniżej 180°F), acetal często zapewnia najlepszą wartość. Typowe zastosowania obejmują:
- Elementy układu paliwowego
- Mechanizmy blokujące drzwi
- Klipsy i elementy mocujące wykończenia wnętrza
- Powierzchnie łożysk w obszarach niekrytycznych
W przypadku stref o wyższej temperaturze, takich jak elementy pod maską lub części w pobliżu układów wydechowych, stabilność termiczna PEEK sprawia, że jest to lepszy wybór pomimo wyższych kosztów.
Medycyna i farmaceutyka
Przemysł medyczny przyjął PEEK ze względu na jego biokompatybilność i odporność na metody sterylizacji. Jest powszechnie stosowany w:
- Urządzenia do implantacji
- Narzędzia chirurgiczne
- Elementy obrazowania medycznego
- Sprzęt laboratoryjny
Acetal nadal znajduje zastosowanie w mniej wymagających środowiskach medycznych, takich jak
- Jednorazowe elementy instrumentów
- Laboratoryjne oprzyrządowanie testowe
- Obudowy urządzeń diagnostycznych
Urządzenia przemysłowe
W przypadku maszyn przemysłowych wybór często zależy od warunków pracy:
- Standardowe środowiska pracy: Acetal zapewnia doskonałą wartość dla kół zębatych, łożysk i powierzchni zużywających się w normalnych warunkach.
- Trudne warunki pracy: PEEK uzasadnia swoją wysoką cenę, gdy jest wystawiony na działanie wysokich temperatur, chemikaliów lub ekstremalnych naprężeń mechanicznych.
Dokonywanie optymalnego wyboru
Pomagając klientom w wyborze między acetalem a PEEK w PTSMAKE, zalecam systematyczne podejście:
- Zidentyfikuj najbardziej wymagające warunki, z jakimi część będzie musiała się zmierzyć (temperatura, chemikalia, obciążenia).
- Określenie, czy właściwości acetalu są wystarczające, aby poradzić sobie z tymi warunkami.
- Oblicz różnicę w kosztach między opcjami dla określonych wymagań dotyczących objętości
- Rozważ konsekwencje awarii i związane z nią koszty przestojów.
- Oceń, czy wysoka wydajność PEEK uzasadnia jego wyższą cenę.
Należy pamiętać, że dobór materiału rzadko jest uniwersalny. Czasami najlepiej sprawdza się podejście hybrydowe, wykorzystujące PEEK tylko do najbardziej krytycznych komponentów, a acetal do mniej wymagających części w tym samym zespole.
Jaka jest różnica między PTFE a PEEK?
Czy kiedykolwiek zagubiłeś się w morzu wysokowydajnych tworzyw sztucznych, nie mając pewności, czy wybrać PTFE czy PEEK do swojego krytycznego zastosowania? Gdy zbliżają się terminy realizacji projektu, a wybór materiału może zadecydować o jego powodzeniu lub porażce, presja dokonania właściwego wyboru może być przytłaczająca, zwłaszcza gdy oba materiały mają imponujące specyfikacje techniczne.
PTFE i PEEK są wysokowydajnymi tworzywami termoplastycznymi o wyraźnych różnicach. PTFE oferuje niezrównaną odporność chemiczną, wyjątkowo niskie tarcie (współczynnik 0,05-0,10) i działa w temperaturach od -328°F do 500°F, ale ma słabą wytrzymałość mechaniczną. PEEK zapewnia doskonałe właściwości mechaniczne, doskonałą odporność na zużycie i zachowuje integralność strukturalną do 480 ° F, a jednocześnie jest bardziej podatny na obróbkę.
Struktura molekularna i podstawowe właściwości
Podstawowe różnice między PTFE i PEEK zaczynają się na poziomie molekularnym, co wyjaśnia ich odmienne właściwości użytkowe w różnych zastosowaniach.
Skład chemiczny
PTFE (politetrafluoroetylen) posiada szkielet węglowy całkowicie otoczony atomami fluoru. Ta unikalna struktura zapewnia PTFE wyjątkową obojętność chemiczną i niskie właściwości tarcia. Wiązania węgiel-fluor należą do najsilniejszych w chemii organicznej, dzięki czemu PTFE jest niezwykle odporny na ataki chemiczne.
Tymczasem PEEK (polieteroeteroketon) ma bardziej złożoną strukturę molekularną z pierścieniami aromatycznymi połączonymi wiązaniami eterowymi i ketonowymi. Ten aromatyczny szkielet zapewnia PEEK doskonałą wytrzymałość mechaniczną i stabilność termiczną.
Analiza porównawcza nieruchomości
Własność | PTFE | PEEK | Przewaga |
---|---|---|---|
Maksymalna temperatura pracy ciągłej | 500°F (260°C) | 480°F (250°C) | PTFE (nieznacznie) |
Minimalna temperatura pracy | -328°F (-200°C) | -65°F (-54°C) | PTFE |
Współczynnik tarcia | 0,05-0,10 (najniższy ze wszystkich ciał stałych) | 0.35-0.40 | PTFE |
Wytrzymałość na rozciąganie | 3,000-5,000 psi | 14 000-16 000 psi | PEEK |
Odporność chemiczna | Superior (uniwersalny) | Doskonały (ograniczony przez silne kwasy) | PTFE |
Obrabialność | Trudne (miękkie, łatwo się odkształcają) | Dobry | PEEK |
Odporność na zużycie | Słaby do umiarkowanego | Doskonały | PEEK |
Właściwości elektryczne | Doskonały izolator | Dobry izolator | PTFE |
Współczynnik kosztów | Umiarkowany | Wysoka (3-4× więcej niż PTFE) | PTFE |
Różnice w wydajności cieplnej
Wydajność temperaturowa jest często krytycznym czynnikiem decyzyjnym przy wyborze między tymi materiałami.
Odporność na ciepło i stabilność
Podczas gdy oba materiały oferują wyjątkową odporność na ciepło, zachowują się inaczej w podwyższonych temperaturach. PTFE zachowuje swoją obojętność chemiczną i niskie tarcie do maksymalnej temperatury, ale zaczyna tracić integralność mechaniczną w znacznie niższych temperaturach (około 260°F/127°C).
Tymczasem PEEK zachowuje swoją wytrzymałość mechaniczną znacznie bliżej maksymalnej temperatury. Sprawia to, że PEEK jest znacznie bardziej wartościowy w zastosowaniach wymagających zarówno odporności na ciepło, jak i obciążeń mechanicznych.
Widziałem wiele zastosowań, w których klienci początkowo wybierali PTFE wyłącznie na podstawie wartości znamionowych temperatury, po czym odkrywali, że materiał nie jest w stanie wytrzymać naprężeń mechanicznych w tych temperaturach. Zdolność PEEK do zachowania integralności strukturalnej w wysokich temperaturach często sprawia, że jest on wart wyższej ceny.
Wydajność w niskich temperaturach
W zastosowaniach kriogenicznych PTFE ma wyraźną przewagę. Pozostaje elastyczny i funkcjonalny do -328°F (-200°C), podczas gdy PEEK staje się coraz bardziej kruchy poniżej -65°F (-54°C). To sprawia, że PTFE jest oczywistym wyborem dla przemysłu lotniczego, laboratoriów i innych środowisk o bardzo niskich temperaturach.
Porównanie wytrzymałości mechanicznej
Właściwości mechaniczne tych materiałów znacznie się różnią, co sprawia, że ich przydatność zależy od zastosowania.
Integralność strukturalna pod obciążeniem
PEEK oferuje znacznie lepsze parametry mechaniczne, z wytrzymałością na rozciąganie wynoszącą średnio 14 000-16 000 psi w porównaniu do skromnych 3 000-5 000 psi PTFE. Sprawia to, że PEEK nadaje się do zastosowań przenoszących obciążenia, w których PTFE szybko uległby deformacji lub awarii.
W PTSMAKE często zalecamy PEEK do elementów konstrukcyjnych, które podlegają stałym obciążeniom mechanicznym, zwłaszcza w podwyższonych temperaturach. Wyjątkowa odporność materiału na pełzanie pozwala mu zachować stabilność wymiarową pod ciągłym obciążeniem.
Odporność na zużycie i tarcie
Niezwykle niski współczynnik tarcia PTFE (0,05-0,10) sprawia, że jest to materiał wybierany do zastosowań wymagających minimalnego tarcia. Jednak ta sama właściwość przyczynia się do jego słabej odporności na zużycie, ponieważ materiał można łatwo zeskrobać w scenariuszach o wysokim zużyciu.
PEEK wykazuje doskonałą odporność na zużycie przy zachowaniu rozsądnego współczynnika tarcia (0,35-0,40). W zastosowaniach wymagających ciągłego ruchu względem innych powierzchni, PEEK zazwyczaj znacznie przewyższa PTFE.
Wielu naszych klientów osiąga to, co najlepsze z obu światów, stosując PEEK jako materiał konstrukcyjny z cienką powłoką PTFE lub wkładką tam, gdzie wymagana jest redukcja tarcia.
Profile odporności chemicznej
Oba materiały oferują wyjątkową odporność chemiczną, ale z ważnymi różnicami.
Odporność na agresywne środowisko
PTFE reprezentuje złoty standard odporności chemicznej, będąc praktycznie obojętnym na prawie wszystkie chemikalia (z rzadkimi wyjątkami, takimi jak stopione metale alkaliczne i pierwiastkowy fluor). Ta uniwersalna odporność chemiczna sprawia, że PTFE jest nieoceniony w przetwórstwie chemicznym, produkcji półprzewodników i środowiskach laboratoryjnych.
PEEK oferuje doskonałą odporność chemiczną na większość substancji, ale może być atakowany przez stężony kwas siarkowy i niektóre inne silne kwasy. Jednak w większości środowisk przemysłowych odporność chemiczna PEEK jest więcej niż wystarczająca.
Hydroliza i absorpcja wilgoci
PTFE jest całkowicie hydrofobowy i zasadniczo nie absorbuje wilgoci, nawet po długotrwałej ekspozycji. PEEK, choć wysoce odporny na hydrolizę, wchłania niewielką ilość wilgoci (0,1-0,3%), gdy jest wystawiony na działanie wilgotnego środowiska przez dłuższy czas.
W przypadku ultraczystej wody lub systemów, w których nawet niewielkie zanieczyszczenia są niedopuszczalne, PTFE często pozostaje preferowanym wyborem pomimo swoich ograniczeń mechanicznych.
% [Elementy obrabiane z PEEK i PTFE dla porównania strukturalnego] (
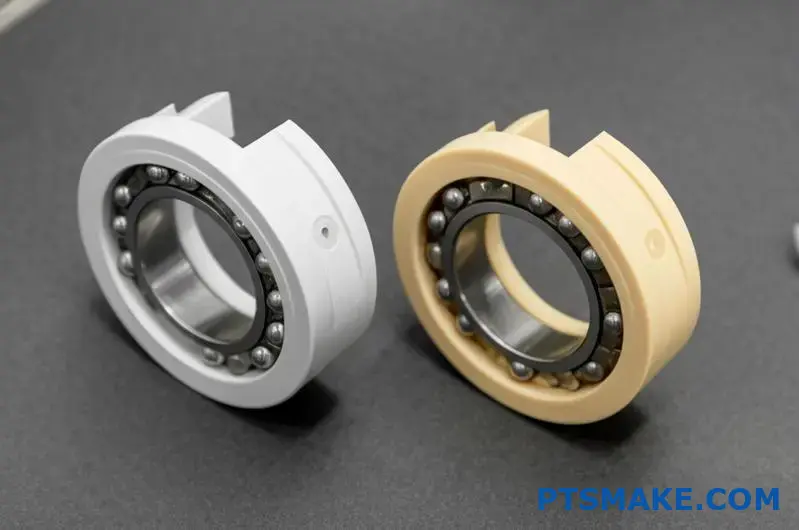
"Elementy łożysk z PEEK i PTFE")
Rozważania dotyczące obróbki i produkcji
The obrabialność3 Różnice między tymi materiałami znacząco wpływają na koszty i możliwości produkcyjne.
Wyzwania i rozwiązania związane z obróbką skrawaniem
PTFE stanowi wyjątkowe wyzwanie w obróbce skrawaniem ze względu na swoją miękkość i tendencję do płynięcia na zimno. Wymaga specjalistycznego oprzyrządowania, mniejszych prędkości skrawania i starannego mocowania, aby zapobiec deformacji podczas obróbki. Ostre narzędzia są niezbędne, aby zapobiec rozdarciu lub deformacji materiału.
PEEK obrabia się podobnie jak tradycyjne tworzywa konstrukcyjne, choć jego ścierny charakter powoduje szybsze zużycie narzędzi niż w przypadku wielu innych materiałów. Podczas obróbki PEEK zazwyczaj używamy narzędzi z węglików spiekanych i odpowiednich technik chłodzenia w celu zarządzania gromadzeniem się ciepła.
Zgodność z procesami produkcyjnymi
Wysoka lepkość stopionego PTFE uniemożliwia konwencjonalne formowanie wtryskowe. Zamiast tego musi być przetwarzany przy użyciu technik takich jak formowanie tłoczne, wytłaczanie z tłokiem lub skrawanie z kęsów. Ogranicza to złożoność projektu i zwiększa koszty produkcji złożonych kształtów.
PEEK może być przetwarzany za pomocą konwencjonalnych metod, takich jak formowanie wtryskowe i wytłaczanie, co pozwala na bardziej złożone geometrie i potencjalnie niższe koszty produkcji przy większych ilościach. Ta wszechstronność przetwarzania daje PEEK przewagę w przypadku skomplikowanych komponentów lub przy przechodzeniu od prototypowania do produkcji masowej.
Analiza kosztów i korzyści dla różnych zastosowań
Znaczna różnica w cenie między tymi materiałami wymaga starannego rozważenia ich wartości dla konkretnego zastosowania.
Porównanie propozycji wartości
Chociaż PEEK kosztuje zwykle 3-4 razy więcej niż PTFE, jego doskonałe właściwości mechaniczne i odporność na zużycie często zapewniają lepszą długoterminową wartość w zastosowaniach, w których awaria mechaniczna byłaby kosztowna lub niebezpieczna.
W przypadku zastosowań wymagających przede wszystkim odporności chemicznej, niskiego tarcia lub właściwości izolacji elektrycznej bez znacznych naprężeń mechanicznych, PTFE zwykle oferuje lepszą wartość pomimo swoich ograniczeń.
Kryteria wyboru specyficzne dla branży
W różnych branżach priorytetem są różne właściwości materiałów:
- Przetwarzanie chemiczne: Uniwersalna odporność chemiczna PTFE zazwyczaj przewyższa jego ograniczenia mechaniczne.
- Przemysł lotniczy: Oba materiały znajdują zastosowanie, przy czym PEEK jest używany do elementów konstrukcyjnych, a PTFE do uszczelek i izolacji elektrycznej.
- Medycyna: Biokompatybilność i wytrzymałość strukturalna PEEK sprawiają, że jest on popularny w przypadku implantów, podczas gdy PTFE jest preferowany do wykładzin cewników i innych zastosowań o niskim współczynniku tarcia.
- Półprzewodniki: PTFE dominuje ze względu na wyjątkową czystość i odporność na agresywne chemikalia.
- Motoryzacja: Odporność na zużycie i właściwości mechaniczne PEEK sprawiają, że jest on cenny w przypadku elementów pod maską narażonych na naprężenia mechaniczne.
Jaka jest różnica między PVDF a PEEK?
Czy kiedykolwiek stanąłeś przed dylematem wyboru między PVDF a PEEK w krytycznym projekcie, w którym wybór materiału może wpłynąć na projekt lub go zepsuć? Gdy standardowe tworzywa sztuczne nie wystarczają i potrzebna jest wyjątkowa odporność chemiczna lub stabilność termiczna, wybór między tymi dwoma wysokowydajnymi materiałami może prowadzić do kosztownych błędów lub pogorszenia wydajności.
PVDF (polifluorek winylidenu) i PEEK (polieteroeteroketon) różnią się przede wszystkim charakterystyką działania i zastosowaniami. PEEK oferuje wyższą odporność na ciepło (480°F vs 300°F), lepszą wytrzymałość mechaniczną i wyjątkową odporność na zużycie, podczas gdy PVDF zapewnia doskonałą odporność chemiczną, stabilność UV i jest znacznie tańszy.
Kluczowe różnice między PVDF a PEEK
Porównując te dwa konstrukcyjne tworzywa termoplastyczne, zrozumienie ich podstawowych właściwości pomaga określić, który materiał najlepiej nadaje się do konkretnych zastosowań. Oba materiały są uważane za opcje o wysokiej wydajności, ale wyróżniają się w różnych środowiskach i zastosowaniach.
Skład i struktura materiału
PVDF to półkrystaliczny fluoropolimer składający się z powtarzających się jednostek difluorku winylidenu. Jego struktura molekularna obejmuje wiązania węgiel-fluor, które zapewniają doskonałą odporność chemiczną, choć nie tak wszechstronną jak w przypadku w pełni fluorowanych polimerów, takich jak PTFE.
PEEK należy do rodziny poliaryloeteroketonów i charakteryzuje się złożoną strukturą molekularną z pierścieniami aromatycznymi połączonymi wiązaniami eterowymi i ketonowymi. Ta unikalna struktura zapewnia PEEK wyjątkową stabilność termiczną i wytrzymałość mechaniczną.
Porównanie charakterystyk wydajności
Poniższa tabela zawiera szczegółowe porównanie kluczowych właściwości PVDF i PEEK:
Własność | PVDF | PEEK | Doskonały materiał |
---|---|---|---|
Maksymalna temperatura pracy ciągłej | 300°F (149°C) | 480°F (250°C) | PEEK |
Wytrzymałość mechaniczna (rozciąganie) | 5,800-7,800 psi | 14 500-16 000 psi | PEEK |
Odporność chemiczna | Doskonały (większość kwasów, zasad) | Bardzo dobry (ograniczony przez silne kwasy) | PVDF |
Odporność na promieniowanie UV | Doskonały | Uczciwy do dobrego | PVDF |
Odporność na zużycie | Dobry | Doskonały | PEEK |
Współczynnik tarcia | 0.25-0.35 | 0.35-0.40 | PVDF |
Współczynnik kosztów | Umiarkowany | 2-3× wyższa niż PVDF | PVDF |
Absorpcja wilgoci | 0.03-0.04% | 0.1-0.15% | PVDF |
Gęstość | 1,75-1,78 g/cm³ | 1,30-1,32 g/cm³ | Zależne od aplikacji |
Wydajność termiczna i stabilność
Możliwości temperaturowe często wpływają na decyzje dotyczące wyboru materiału w wielu zastosowaniach inżynieryjnych.
Porównanie odporności na ciepło
PEEK wykazuje wyjątkową stabilność termiczną, zachowując swoje właściwości mechaniczne w temperaturach do 250°C (480°F) przy ciągłym użytkowaniu. Dzięki temu idealnie nadaje się do zastosowań w środowiskach o wysokiej temperaturze, w których tradycyjne tworzywa sztuczne mogłyby zawieść.
PVDF, choć nadal uważany za tworzywo wysokotemperaturowe, ma niższą maksymalną temperaturę ciągłego użytkowania wynoszącą około 149°C (300°F). Ten zakres temperatur jest wystarczający dla wielu zastosowań przemysłowych, ale nie sprawdza się w ekstremalnych środowiskach termicznych.
Z mojego doświadczenia w pracy z klientami PTSMAKE wynika, że ta różnica temperatur często staje się decydującym czynnikiem przy wyborze między tymi materiałami do zastosowań takich jak sprzęt do przetwarzania półprzewodników, gdzie temperatury procesu mogą przekraczać możliwości PVDF.
Zachowanie w cyklu termicznym
Oba materiały różnie znoszą cykle termiczne:
- PVDF wykazuje dobrą stabilność wymiarową podczas cykli termicznych, choć może doświadczać większej rozszerzalności cieplnej niż PEEK.
- PEEK zachowuje wyjątkową stabilność wymiarową nawet podczas powtarzających się cykli termicznych, dzięki czemu jest preferowany do precyzyjnych komponentów, które muszą zachować wąskie tolerancje w różnych temperaturach.
Profile odporności chemicznej
Kolejnym istotnym czynnikiem wyróżniającym te materiały jest ich odporność chemiczna.
Odporność na agresywne środowisko
PVDF oferuje doskonałą odporność na szeroki zakres chemikaliów, w tym:
- Większość kwasów (w tym stężony kwas solny i siarkowy)
- Węglowodory alifatyczne i aromatyczne
- Alkohole i rozpuszczalniki chlorowane
- Środki utleniające
PEEK wykazuje dobrą odporność chemiczną na wiele substancji, ale może być atakowany przez stężony kwas siarkowy i niektóre inne silne kwasy. Jest szczególnie odporny na hydrolizę i sterylizację parową, co czyni go cennym w zastosowaniach medycznych.
Czynniki chemiczne specyficzne dla branży
W różnych branżach priorytetem są określone właściwości odporności chemicznej:
- Przetwarzanie chemiczne: PVDF jest często preferowany ze względu na swoją wszechstronną odporność na kwasy i związki chlorowane.
- Półprzewodnik: Stosowane są oba materiały, a ich wybór zależy od konkretnych chemikaliów procesowych.
- Ropa i gaz: Połączenie właściwości mechanicznych i odporności chemicznej PEEK sprawia, że jest on cenny w zastosowaniach wiertniczych.
- Farmaceutyczny: Doskonała odporność PVDF na środki czyszczące i metody sterylizacji sprawia, że jest on popularny w urządzeniach przetwórczych.
Właściwości mechaniczne i zastosowania strukturalne
The wytrzymałość mechaniczna4 Różnice między tymi materiałami znacząco wpływają na ich przydatność do zastosowań nośnych.
Możliwości przenoszenia obciążeń
PEEK oferuje znacznie wyższą wytrzymałość mechaniczną z wartościami rozciągania wynoszącymi zazwyczaj od 14 500 do 16 000 psi, w porównaniu do bardziej skromnych 5 800-7 800 psi PVDF. Sprawia to, że PEEK doskonale nadaje się do elementów konstrukcyjnych, które muszą wytrzymywać znaczne obciążenia mechaniczne.
W przypadku zastosowań wymagających zarówno odporności chemicznej, jak i integralności strukturalnej, PEEK często zapewnia najlepszą równowagę właściwości, pomimo wyższego kosztu. Polecałem PEEK do wielu zastosowań w PTSMAKE, w których komponenty muszą być odporne zarówno na agresywne chemikalia, jak i naprężenia mechaniczne.
Odporność na zużycie i właściwości cierne
PEEK wykazuje doskonałą odporność na zużycie, dzięki czemu idealnie nadaje się do łożysk, tulei i innych elementów narażonych na ciągłe tarcie. Jego właściwości samosmarujące pomagają wydłużyć żywotność ruchomych części w wymagających środowiskach.
PVDF oferuje dobrą odporność na zużycie, choć nie na poziomie PEEK. Jego niższy współczynnik tarcia (0,25-0,35 w porównaniu do PEEK 0,35-0,40) może być korzystny w niektórych zastosowaniach ślizgowych o niskim obciążeniu, gdzie mniejsze tarcie jest ważniejsze niż maksymalna odporność na zużycie.
Właściwości izolacji elektrycznej i termicznej
Oba materiały oferują różne właściwości elektryczne, dzięki czemu nadają się do różnych zastosowań.
Właściwości dielektryczne
PVDF jest znany ze swoich właściwości piezoelektrycznych, które pozwalają mu generować ładunek elektryczny w odpowiedzi na zastosowane naprężenia mechaniczne. Ta unikalna cecha sprawia, że PVDF jest cenny w zastosowaniach czujnikowych.
PEEK zapewnia doskonałe właściwości izolacji elektrycznej w szerokim zakresie temperatur, zachowując swoją wytrzymałość dielektryczną nawet w podwyższonych temperaturach. Sprawia to, że jest on szczególnie cenny w wysokotemperaturowych zastosowaniach elektrycznych, w których standardowe tworzywa sztuczne mogłyby zawieść.
Przewodność cieplna
PVDF i PEEK mają stosunkowo niską przewodność cieplną w porównaniu do metali, co czyni je dobrymi izolatorami termicznymi:
- PVDF: 0,17-0,19 W/m-K
- PEEK: 0,25-0,29 W/m-K
Niska przewodność cieplna może być zaletą lub wadą w zależności od zastosowania. W przypadku komponentów wymagających izolacji termicznej, oba materiały sprawdzają się dobrze, choć PVDF zapewnia nieco lepszą izolację.
Rozważania dotyczące kosztów i analiza wartości
Znacząca różnica w cenie między tymi materiałami sprawia, że analiza kosztów i korzyści jest niezbędna.
Początkowy koszt materiałów
PEEK kosztuje zwykle 2-3 razy więcej niż PVDF, co stanowi znaczną premię kosztową, która musi być uzasadniona wymaganiami dotyczącymi wydajności. Ta różnica w cenie wynika z bardziej złożonego procesu produkcyjnego PEEK i wyższych kosztów surowców.
Ocena wartości w całym okresie użytkowania
Przy ocenie całkowitego kosztu posiadania należy wziąć pod uwagę kilka czynników wykraczających poza początkowy koszt materiałów:
- Przewidywany okres użytkowania w środowisku docelowym
- Częstotliwość wymiany i związane z tym koszty przestojów
- Wymagania dotyczące instalacji i konserwacji
- Kwestie bezpieczeństwa i niezawodności
W wielu zastosowaniach związanych z wysokimi temperaturami lub dużymi obciążeniami, doskonała wydajność PEEK uzasadnia jego wyższy koszt początkowy poprzez wydłużoną żywotność i lepszą niezawodność. W przypadku zastosowań mieszczących się w zakresie możliwości PVDF, tańszy materiał często zapewnia lepszą ogólną wartość.
Uwagi dotyczące przetwarzania i produkcji
Możliwości i ograniczenia produkcyjne również wpływają na wybór materiału.
Różnice w obróbce
Podczas obróbki tych materiałów przy PTSMAKE zaobserwowaliśmy znaczące różnice:
- PVDF obrabia się stosunkowo dobrze, ale wymaga ostrych narzędzi i odpowiednich prędkości, aby zapobiec stopieniu lub zatarciu.
- PEEK jest trudniejszy w obróbce ze względu na jego ścierność i słabą przewodność cieplną, co może prowadzić do gromadzenia się ciepła podczas operacji cięcia.
W przypadku elementów precyzyjnych, PEEK generalnie zachowuje węższe tolerancje podczas obróbki, ale wymaga bardziej specjalistycznych technik i narzędzi, potencjalnie zwiększając koszty produkcji.
Zgodność metod produkcji
Oba materiały mogą być przetwarzane wieloma metodami produkcyjnymi:
- PVDF: Formowanie wtryskowe, wytłaczanie, formowanie tłoczne, obróbka skrawaniem
- PEEK: formowanie wtryskowe, wytłaczanie, formowanie tłoczne, obróbka skrawaniem, drukowanie 3D (specjalistyczny sprzęt)
PVDF oferuje nieco większą elastyczność przetwarzania w niższych temperaturach, podczas gdy PEEK wymaga wyższych temperatur przetwarzania, ale zapewnia więcej opcji dla złożonych geometrii dzięki zaawansowanym technikom produkcji.
Wytyczne dotyczące wyboru aplikacji
W różnych branżach priorytetem są różne właściwości materiałów, co prowadzi do różnych preferencji materiałowych.
Przemysł półprzewodników
W produkcji półprzewodników oba materiały znajdują zastosowanie, ale w różnych obszarach:
- PVDF: Powszechnie stosowany w systemach wody ultraczystej, komponentach do dostarczania chemikaliów i urządzeniach filtrujących.
- PEEK: Preferowany do komponentów narażonych na działanie wysokich temperatur, takich jak urządzenia do obsługi płytek i komponenty komór procesowych.
Sprzęt do przetwarzania chemicznego
Do zastosowań w przetwórstwie chemicznym:
- PVDF: Doskonały do pomp, zaworów, armatury i zbiorników obsługujących żrące chemikalia w umiarkowanych temperaturach.
- PEEK: Lepiej nadaje się do komponentów wymagających zarówno odporności chemicznej, jak i odporności na wysokie temperatury lub wytrzymałości mechanicznej.
Zastosowania medyczne i farmaceutyczne
W zastosowaniach medycznych:
- PVDF: Powszechnie stosowany w membranach filtracyjnych, szwach i niektórych urządzeniach wszczepialnych.
- PEEK: Preferowany do urządzeń wszczepialnych, zwłaszcza w zastosowaniach ortopedycznych, ze względu na jego biokompatybilność, promieniotwórczość i właściwości mechaniczne podobne do kości.
Pomagając klientom w wyborze między PVDF a PEEK w PTSMAKE, zalecam systematyczne podejście, które najpierw ocenia najbardziej krytyczne czynniki środowiskowe (temperatura, chemikalia, obciążenia mechaniczne), a następnie uwzględnia czynniki drugorzędne, takie jak koszt, wymagania dotyczące przetwarzania i dostępność.
<
Czy PEEK jest polietylenem?
Czy kiedykolwiek byłeś zdezorientowany szeregiem tworzyw konstrukcyjnych o podobnie brzmiących nazwach? Podczas wybierania materiałów do krytycznych zastosowań, takie zamieszanie może prowadzić do kosztownych błędów, awarii wydajności i marnowania zasobów, jeśli omyłkowo zastąpisz jedno wysokowydajne tworzywo sztuczne innym.
Nie, PEEK (polieteroeteroketon) nie jest polietylenem. PEEK to aromatyczny polieter z grupami ketonowymi w szkielecie, tworzący półkrystaliczne tworzywo termoplastyczne o wyjątkowej odporności na ciepło (do 480°F), doskonałej odporności chemicznej i doskonałych właściwościach mechanicznych, które znacznie przewyższają właściwości materiałów polietylenowych.
Struktura chemiczna i różnice w klasyfikacji
Analizując PEEK i polietylen, fundamentalne różnice zaczynają się na poziomie molekularnym. Te różnice strukturalne wyjaśniają, dlaczego te materiały zachowują się tak różnie w praktycznych zastosowaniach.
Porównanie szkieletu molekularnego
PEEK ma złożoną aromatyczną strukturę szkieletową z eterowymi i ketonowymi wiązaniami między pierścieniami benzenowymi. Taka architektura molekularna zapewnia PEEK wyjątkową stabilność termiczną i wytrzymałość mechaniczną. Pierścienie aromatyczne zapewniają sztywność, podczas gdy wiązania eterowe zapewniają pewną elastyczność.
Z kolei polietylen ma jedną z najprostszych możliwych struktur polimerowych - tylko liniowy łańcuch atomów węgla z przyłączonymi atomami wodoru. Ta nieskomplikowana struktura występuje w różnych formach (HDPE, LDPE, UHMWPE), ale wszystkie są pozbawione składników aromatycznych i grup funkcyjnych, które nadają PEEK wyjątkowe właściwości.
Ta fundamentalna różnica strukturalna oznacza, że PEEK należy do zupełnie innej rodziny polimerów niż polietylen. Podczas gdy polietylen jest klasyfikowany jako poliolefina, PEEK należy do rodziny poliaryloeteroketonów (PAEK) wysokowydajnych tworzyw termoplastycznych.
Kluczowe różnice we właściwościach
Różnice w strukturze molekularnej przekładają się na dramatyczne różnice w wydajności:
Własność | PEEK | Polietylen (HDPE) | Współczynnik różnicy |
---|---|---|---|
Maksymalna temperatura pracy ciągłej | 480°F (250°C) | 180°F (82°C) | PEEK jest 2,7× wyższy |
Wytrzymałość na rozciąganie | 14 500 psi | 4 500 psi | PEEK jest 3,2× mocniejszy |
Odporność chemiczna | Doskonały (odporny na większość chemikaliów) | Dobry (wrażliwy na rozpuszczalniki aromatyczne) | PEEK oferuje szerszą odporność |
Koszt | Wysoki | Niski | PEEK kosztuje 15-20 razy więcej |
Gęstość | 1,32 g/cm³ | 0,95 g/cm³ | PEEK ma gęstość 39% |
Twardość (Shore D) | 85-90 | 60-70 | PEEK jest znacznie twardszy |
Różnice w procesach produkcyjnych
Metody produkcji PEEK i polietylenu odzwierciedlają ich różne struktury molekularne i właściwości użytkowe.
Proces produkcji PEEK
PEEK jest wytwarzany w złożonym procesie obejmującym nukleofilową polimeryzację z podstawieniem aromatycznym. Wymaga to precyzyjnej kontroli temperatury i specjalistycznych katalizatorów. Materiały monomerowe są znacznie droższe niż etylen, co przyczynia się do wyższych kosztów PEEK.
W PTSMAKE, gdy obrabiamy komponenty PEEK, musimy wziąć pod uwagę unikalne właściwości tego materiału - jego niższa przewodność cieplna oznacza, że zarządzanie ciepłem podczas obróbki ma kluczowe znaczenie dla zapobiegania miejscowej degradacji termicznej.
Produkcja polietylenu
Polietylen jest wytwarzany poprzez polimeryzację addycyjną etylenu przy użyciu różnych katalizatorów w zależności od pożądanej gęstości i rozgałęzienia. Ten stosunkowo prosty proces może być prowadzony w niższych temperaturach i ciśnieniach niż produkcja PEEK, zwłaszcza w przypadku odmian o niskiej gęstości.
Wydajność w ekstremalnych środowiskach
Wydajność w wysokich temperaturach
Jedną z najważniejszych różnic między tymi materiałami jest ich stabilność termiczna:
- PEEK zachowuje swoje właściwości mechaniczne do 250°C (480°F) przy ciągłym użytkowaniu i może wytrzymać krótkie ekspozycje na jeszcze wyższe temperatury.
- Polietylen zaczyna mięknąć w temperaturze około 82°C (180°F) i traci większość swojej wytrzymałości mechanicznej znacznie poniżej tej temperatury.
Widziałem wiele zastosowań, w których klienci początkowo wybierali polietylen na podstawie kosztów, a następnie doświadczali szybkiej awarii, gdy temperatury robocze przekraczały oczekiwania. W jednym z zastosowań lotniczych klient zamienił polietylen na PEEK dla komponentu w pobliżu źródła ciepła, wydłużając jego żywotność z miesięcy do lat, pomimo wyższego początkowego kosztu materiału.
Porównanie odporności chemicznej
Chociaż oba materiały oferują dobrą odporność chemiczną, PEEK zapewnia szerszą ochronę przed agresywnymi chemikaliami:
- PEEK jest odporny na większość kwasów, zasad, węglowodorów i rozpuszczalników organicznych.
- Polietylen ma dobrą odporność na kwasy i zasady, ale może być atakowany przez węglowodory aromatyczne i niektóre środki utleniające.
Różnica ta staje się krytyczna w przypadku sprzętu do przetwarzania chemicznego, produkcji półprzewodników i zastosowań medycznych, gdzie narażenie na wiele chemikaliów jest powszechne.
Przydatność aplikacji
Zastosowania lotnicze i obronne
W zastosowaniach lotniczych połączenie lekkości, odporności na płomienie i stabilności termicznej PEEK sprawia, że jest on nieoceniony w przypadku takich komponentów jak:
- Elementy wewnętrzne wymagające odporności na płomienie
- Złącza elektryczne i izolatory
- Elementy strukturalne w strefach wysokiej temperatury
- Elementy układu paliwowego wymagające odporności chemicznej
Polietylen rzadko spełnia wysokie wymagania zastosowań lotniczych ze względu na ograniczoną stabilność termiczną i właściwości mechaniczne.
Zastosowania medyczne i opieki zdrowotnej
Profile biokompatybilności tych materiałów również znacznie się różnią:
- PEEK jest biokompatybilny i stosowany w urządzeniach do implantacji, narzędziach chirurgicznych i sprzęcie medycznym wymagającym sterylizacji
- Polietylen klasy medycznej (głównie UHMWPE) jest stosowany w niektórych implantach, takich jak sztuczne stawy, ale nie jest odporny na temperaturę PEEK w przypadku wielokrotnej sterylizacji parowej.
Komponenty urządzeń przemysłowych
W przypadku maszyn przemysłowych wybór między tymi materiałami zależy zazwyczaj od warunków pracy:
- PEEK doskonale sprawdza się w środowiskach o wysokiej temperaturze, w zastosowaniach wymagających doskonałej odporności na zużycie lub narażonych na działanie agresywnych chemikaliów.
- Polietylen zapewnia odpowiednią wydajność w zastosowaniach w temperaturze otoczenia o umiarkowanych wymaganiach mechanicznych i jest często wybierany ze względu na niższy koszt i łatwość przetwarzania
Rozważania dotyczące kosztów i korzyści
Różnica w cenie między tymi materiałami jest znaczna - PEEK kosztuje zazwyczaj 15-20 razy więcej niż polietylen o wysokiej gęstości. Ta znacząca różnica w kosztach oznacza, że wybór materiału powinien opierać się na dokładnej analizie:
- Wymagany zakres temperatur pracy
- Profil narażenia chemicznego
- Wymagania dotyczące obciążenia mechanicznego
- Przewidywany okres użytkowania
- Konsekwencje niepowodzenia
W przypadku zastosowań mieszczących się w zakresie możliwości polietylenu, jego niższy koszt sprawia, że jest to ekonomiczny wybór. Jednak gdy wymagania dotyczące wydajności przekraczają ograniczenia polietylenu, doskonałe właściwości PEEK z łatwością uzasadniają jego wyższą cenę dzięki wydłużonej żywotności, zwiększonej niezawodności i niższym kosztom konserwacji.
Różnice w obróbce i przetwarzaniu
W PTSMAKE odkryliśmy znaczące różnice w obróbce tych materiałów:
- PEEK wymaga specjalnych parametrów cięcia ze względu na jego zachowanie termiczne5 podczas obróbki, ale zachowuje wąskie tolerancje i zapewnia doskonałe wykończenie powierzchni
- Polietylen jest łatwiejszy w obróbce, ale ma tendencję do odkształcania się pod wpływem sił tnących, co utrudnia zachowanie wąskich tolerancji.
Zrozumienie tych różnic w przetwarzaniu jest niezbędne przy projektowaniu komponentów pod kątem możliwości produkcji i precyzji.
Jakie są wady i zalety materiału PEEK?
Czy kiedykolwiek miałeś trudności z podjęciem decyzji, czy PEEK jest wart swojej wysokiej ceny dla krytycznego zastosowania? Gdy sukces projektu zależy od wyboru materiału, wybór między drogimi, wysokowydajnymi tworzywami sztucznymi a bardziej ekonomicznymi alternatywami może być trudny i mieć realne konsekwencje dla niezawodności i trwałości.
PEEK oferuje wyjątkowe zalety, w tym niezwykłą odporność na ciepło (do 480 ° F), wyjątkową odporność chemiczną, doskonałą wytrzymałość mechaniczną i doskonałe właściwości zużycia. Korzyści te wiążą się jednak z istotnymi wadami, w tym wysokim kosztem (5-10 razy wyższym niż w przypadku standardowych tworzyw konstrukcyjnych), trudną obróbką, ograniczonymi opcjami kolorystycznymi i słabą odpornością na promieniowanie UV.
Zrozumienie wyjątkowych właściwości PEEK
PEEK (polieteroeteroketon) wyróżnia się wśród tworzyw konstrukcyjnych dzięki unikalnemu połączeniu właściwości, które sprawiają, że nadaje się do najbardziej wymagających zastosowań. Jako ktoś, kto określał materiały dla niezliczonych precyzyjnych komponentów, widziałem na własne oczy, jak właściwości PEEK przekładają się na rzeczywiste korzyści w zakresie wydajności.
Zalety wydajności termicznej
Jedną z najbardziej imponujących cech PEEK jest jego stabilność termiczna. Materiał ten zachowuje swoje właściwości mechaniczne w temperaturach, które spowodowałyby katastrofalną awarię większości tworzyw sztucznych.
Charakterystyka temperaturowa | Wydajność PEEK | Porównanie ze standardowymi tworzywami sztucznymi |
---|---|---|
Temperatura pracy ciągłej | Do 480°F (250°C) | 2-3× wyższa niż w przypadku większości tworzyw konstrukcyjnych |
Temperatura zeszklenia | 289°F (143°C) | Utrzymuje sztywność w wyższych temperaturach |
Temperatura topnienia | 649°F (343°C) | Umożliwia sterylizację parową |
Przewodność cieplna | 0,25 W/m-K | Lepsze niż wiele tworzyw sztucznych odprowadzanie ciepła |
Ta wyjątkowa odporność termiczna pozwala na stosowanie PEEK w pobliżu źródeł ciepła, gdzie standardowe tworzywa sztuczne szybko uległyby deformacji lub degradacji. Pomogłem wielu klientom zastąpić uszkodzone komponenty wykonane z gorszych materiałów częściami z PEEK, które nadal działają bez zarzutu pomimo trudnych warunków termicznych.
Zalety odporności chemicznej
Profil odporności chemicznej PEEK jest niemal tak imponujący, jak jego właściwości termiczne. Materiał wykazuje doskonałą odporność na:
- Węglowodory i rozpuszczalniki organiczne
- Większość kwasów i zasad (z wyjątkiem stężonego kwasu siarkowego)
- Para i gorąca woda
- Płyny i paliwa samochodowe
- Procesy sterylizacji medycznej
Ta szeroka odporność chemiczna sprawia, że PEEK jest szczególnie cenny w środowiskach, w których spodziewana jest ekspozycja na wiele agresywnych substancji. Na przykład w przemyśle półprzewodnikowym komponenty z PEEK są odporne na agresywne chemikalia stosowane w przetwarzaniu płytek przy jednoczesnym zachowaniu stabilności wymiarowej.
Zalety właściwości mechanicznych
Wytrzymałość mechaniczna PEEK odróżnia go od większości innych tworzyw termoplastycznych:
- Wytrzymałość na rozciąganie 14 500 psi (porównywalna z niektórymi metalami)
- Doskonała odporność na zmęczenie
- Wyjątkowa odporność na uderzenia i wytrzymałość
- Doskonała odporność na zużycie
- Niski współczynnik tarcia
Właściwości te sprawiają, że PEEK nadaje się do zastosowań konstrukcyjnych, w których większość tworzyw sztucznych zawodzi. Stosowałem PEEK w przekładniach, łożyskach i innych komponentach o wysokim zużyciu, które działają pod znacznym obciążeniem mechanicznym, często zastępując części metalowe lżejszymi alternatywami PEEK, które zapewniają dodatkowe korzyści, takie jak odporność na korozję i redukcja hałasu.
Istotne wady materiału PEEK
Pomimo imponującej wydajności, PEEK ma kilka istotnych wad, które należy dokładnie rozważyć podczas wyboru materiału.
Ograniczenia kosztów
Najbardziej oczywistą wadą PEEK jest jego koszt. W PTSMAKE często musimy pomagać klientom zrozumieć wyższą cenę PEEK w porównaniu z innymi tworzywami konstrukcyjnymi:
- PEEK kosztuje zazwyczaj 5-10 razy więcej niż konstrukcyjne tworzywa sztuczne, takie jak nylon czy acetal.
- Koszty materiałowe części PEEK mogą być o 20-30% wyższe niż równoważnych elementów metalowych.
- Wysokie ceny surowców znacząco wpływają na ekonomikę małych części
Ten czynnik kosztowy często zmusza inżynierów do rezerwowania PEEK tylko do najbardziej krytycznych zastosowań, w których jego unikalne właściwości są absolutnie niezbędne. W wielu przypadkach zalecamy bardziej opłacalne alternatywy dla niekrytycznych komponentów w zespole.
Wyzwania związane z produkcją
PEEK wiąże się z kilkoma wyzwaniami produkcyjnymi, które mogą zwiększyć złożoność i koszty produkcji:
Trudności w obróbce: Wysoka odporność termiczna PEEK przekłada się na słabą przewodność cieplną, powodując gromadzenie się ciepła podczas operacji obróbki skrawaniem. Wymaga to wolniejszych prędkości skrawania, częstych zmian narzędzi i ostrożnych strategii chłodzenia.
Wymagania dotyczące temperatury przetwarzania: Dzięki temperaturze topnienia wynoszącej 343°C (649°F), PEEK wymaga specjalistycznego sprzętu do formowania wtryskowego i wytłaczania w wysokich temperaturach.
Ograniczone okno przetwarzania: Różnica między temperaturą topnienia PEEK a początkiem degradacji jest stosunkowo niewielka, co stwarza wyzwania podczas przetwarzania.
Kurczenie się formy: PEEK wykazuje znaczny skurcz (około 1-1,3%) podczas chłodzenia, co wymaga precyzyjnego zaprojektowania formy w celu uzyskania wąskich tolerancji.
W PTSMAKE opracowaliśmy specjalistyczne protokoły obróbki dla PEEK, aby sprostać tym wyzwaniom, ale nieuchronnie zwiększają one ogólne koszty i złożoność produkcji komponentów PEEK.
Ograniczenia aplikacji
Pomimo swoich imponujących właściwości, PEEK ma ograniczenia, które sprawiają, że nie nadaje się do niektórych zastosowań:
- Słaba odporność na promieniowanie UV: Bez dodatków PEEK ulega degradacji pod wpływem długotrwałego promieniowania UV, co ogranicza jego użycie w zastosowaniach zewnętrznych.
- Ograniczone opcje kolorów: Ze względu na swój naturalny bursztynowy/brązowy kolor i wysokie temperatury przetwarzania, PEEK jest trudny do jednolitego zabarwienia.
- Ograniczenia elektryczne: Chociaż PEEK jest dobrym izolatorem, nie jest idealny do zastosowań elektrycznych o wysokiej częstotliwości w porównaniu do specjalistycznych polimerów elektrycznych.
- Trudności z wiązaniem: Odporność chemiczna PEEK sprawia, że klejenie jest trudne i często wymaga specjalnej obróbki powierzchni.
Analiza kosztów i korzyści: Kiedy PEEK się opłaca?
Biorąc pod uwagę znaczną premię kosztową PEEK, dokładna analiza kosztów i korzyści jest niezbędna przed wyborem tego materiału. Z mojego doświadczenia wynika, że PEEK zapewnia najlepszą wartość w następujących scenariuszach:
Scenariusze, w których PEEK się sprawdza
Środowiska o wysokiej temperaturze: Gdy temperatura robocza przekracza 149°C (300°F), PEEK jest często jedyną realną opcją z tworzywa sztucznego, co sprawia, że jego wysoka cena jest uzasadniona.
Ustawienia agresywne chemicznie: W zastosowaniach narażonych na działanie wielu chemikaliów lub szczególnie trudnych substancji, szeroka odporność chemiczna PEEK zapobiega częstym wymianom wymaganym w przypadku gorszych materiałów.
Aplikacje o krytycznym zużyciu: W przypadku komponentów narażonych na ciągłe tarcie i zużycie w krytycznych systemach, wyjątkowa odporność PEEK na zużycie i niskie tarcie mogą znacznie wydłużyć okresy międzyobsługowe.
Wymagania dotyczące redukcji wagi: Zastępując elementy metalowe w zastosowaniach lotniczych lub wysokowydajnych, stosunek wytrzymałości PEEK do masy może zapewnić korzyści w zakresie wydajności, które uzasadniają jego koszt.
Zastosowania implantów medycznych: Biokompatybilność i stabilność chemiczna PEEK sprawiają, że idealnie nadaje się on do długoterminowych urządzeń do implantacji, w których awaria materiału nie wchodzi w grę.
Porównanie materiałów alternatywnych
W przypadku zastosowań, które nie wymagają ekstremalnych właściwości PEEK, kilka alternatyw może zapewnić wystarczającą wydajność przy niższych kosztach:
Materiał | Przewaga komparatywna | Koszt vs. PEEK | Kluczowe ograniczenia |
---|---|---|---|
PPS (polisiarczek fenylenu) | Dobra odporność na ciepło (400°F) | 40-60% dolny | Mniejsza odporność chemiczna |
PTFE (politetrafluoroetylen) | Doskonała odporność chemiczna | 30-50% dolny | Słaba wytrzymałość mechaniczna |
PEI (polieteroimid) | Dobra odporność na ciepło, przezroczystość | 30-40% dolny | Mniejsza odporność na zużycie |
PAI (poliamidoimid) | Wysoka wytrzymałość, dobra odporność na zużycie | 10-20% dolny | Trudniejsze do przetworzenia |
Acetal (POM) | Doskonała obrabialność, niski koszt | 80-90% dolny | Ograniczona odporność na temperaturę |
Rozważania specyficzne dla branży
Różne branże nadają priorytet różnym aspektom profilu właściwości PEEK:
Przemysł lotniczy i obronny
W zastosowaniach lotniczych połączenie lekkości, odporności na płomienie (z dodatkami) i stabilności termicznej PEEK uzasadnia jego wysoką cenę w przypadku komponentów takich jak:
- Tuleje i łożyska w układach sterowania
- Złącza elektryczne i izolatory
- Elementy strukturalne w strefach wysokiej temperatury
- Elementy układu paliwowego wymagające odporności chemicznej
Medycyna i opieka zdrowotna
Przemysł medyczny ceni PEEK za jego właściwości:
- Biokompatybilność (klasa implantu)
- Odporność na wielokrotną sterylizację
- Radiolucencja (nie zakłóca promieniowania rentgenowskiego)
- Właściwości mechaniczne podobne do kości (po wzmocnieniu)
Właściwości te sprawiają, że PEEK jest idealnym materiałem do produkcji urządzeń wszczepialnych i narzędzi chirurgicznych, pomimo jego wysokiej ceny.
Urządzenia przemysłowe
W przypadku zastosowań przemysłowych decyzja o użyciu PEEK zależy zazwyczaj od surowości warunków pracy:
- Ekstremalne warunki (wysoka temperatura, narażenie na działanie substancji chemicznych) często uzasadniają stosowanie PEEK
- Aplikacje, w których przestoje są niezwykle kosztowne, korzystają z niezawodności PEEK
- Precyzyjne komponenty korzystają ze stabilności wymiarowej PEEK
W PTSMAKE pomagamy klientom poruszać się w tych rozważaniach, aby określić, czy wysoka wydajność PEEK uzasadnia jego wysoką cenę dla ich konkretnych potrzeb.
Wygeneruję treść rozdziału 7 artykułu "Dlaczego PEEK jest tak drogi?" zgodnie z Twoimi wymaganiami.
Dlaczego PEEK jest tak drogi?
Czy kiedykolwiek doświadczyłeś szoku związanego z ceną komponentów PEEK? Kiedy inżynierowie po raz pierwszy spotykają się z ceną tego wysokowydajnego tworzywa sztucznego, wielu z nich zadaje sobie pytanie, czy jakikolwiek materiał może uzasadniać tak wysoką cenę, zwłaszcza w porównaniu z bardziej powszechnymi tworzywami konstrukcyjnymi, które wydają się oferować przyzwoitą wydajność za ułamek ceny.
Wysoki koszt PEEK wynika ze złożonego procesu produkcyjnego, drogich surowców, specjalistycznego sprzętu i stosunkowo niskiej wielkości produkcji. Skomplikowany proces polimeryzacji wymaga precyzyjnych warunków, a zastrzeżony charakter technologii produkcji i status PEEK jako materiału specjalistycznego dodatkowo podnoszą jego cenę rynkową.
Złożony proces produkcji PEEK
Zrozumienie, dlaczego PEEK ma tak wysoką cenę, zaczyna się od zbadania procesu jego produkcji. W przeciwieństwie do prostszych polimerów, produkcja PEEK wymaga zaawansowanej chemii i precyzyjnych warunków przetwarzania, które znacząco wpływają na ostateczny koszt.
Koszty surowców i ich niedobór
Monomery używane do produkcji PEEK są drogimi specjalistycznymi chemikaliami. Podstawowe składniki obejmują:
- Eter difenylowy
- 4,4′-difluorobenzofenon
- Węglan potasu
- Sulfon difenylowy (jako rozpuszczalnik)
Prekursory te wymagają wielu etapów rafinacji, aby osiągnąć czystość wymaganą do syntezy PEEK, co zwiększa koszty jeszcze przed rozpoczęciem polimeryzacji. Ponadto, niektóre z tych chemikaliów mają ograniczone zdolności produkcyjne na całym świecie, tworząc ograniczenia podaży, które podnoszą ceny.
W PTSMAKE, gdy pozyskujemy PEEK do projektów obróbki skrawaniem, płacimy nie tylko za sam polimer, ale za cały łańcuch wartości specjalistycznych chemikaliów, które zostały użyte do jego stworzenia.
Złożoność procesu polimeryzacji
Synteza PEEK obejmuje wyrafinowany proces polimeryzacji nukleofilowej substytucji aromatycznej. Reakcja ta musi zachodzić w precyzyjnie kontrolowanych warunkach:
- Temperatury pomiędzy 300-400°C (572-752°F)
- Atmosfera obojętna zapobiegająca utlenianiu
- Specjalistyczne zbiorniki ciśnieniowe
- Wydłużony czas reakcji (często 3-5 godzin)
- Staranne zarządzanie katalizatorami
Każdy z tych wymogów zwiększa złożoność i koszty produkcji. Reakcja musi być dokładnie monitorowana przez cały czas, aby zapewnić prawidłowy rozkład masy cząsteczkowej i krystaliczność, które bezpośrednio wpływają na właściwości użytkowe materiału.
Ograniczona skala produkcji i dynamika rynku
Status PEEK jako materiału specjalistycznego znacząco wpływa na jego ekonomikę produkcji i ceny rynkowe.
Zastrzeżona technologia i ochrona patentowa
Oryginalna technologia produkcji PEEK została opracowana i opatentowana przez firmę Victrex (dawniej ICI) w latach 70. ubiegłego wieku. Nawet dziś technologia produkcji pozostaje w dużej mierze zastrzeżona i chroniona różnymi patentami. Ta ograniczona konkurencja w zakresie metod produkcji pozwoliła na utrzymanie wyższych cen w porównaniu z powszechnie dostępnymi tworzywami sztucznymi.
Chociaż obecnie istnieje kilku producentów na całym świecie (w tym Victrex, Solvay i Evonik), każdy z nich wykorzystuje zastrzeżone procesy, których opracowanie wymagało ogromnych inwestycji w badania i rozwój. Te koszty rozwoju muszą zostać zwrócone poprzez ceny materiałów.
Ekonomia wielkości produkcji
W przeciwieństwie do tworzyw sztucznych produkowanych w milionach ton rocznie, PEEK jest wytwarzany w stosunkowo niewielkich ilościach:
Typ plastikowy | Globalna roczna produkcja | Względny współczynnik kosztów |
---|---|---|
Polietylen (PE) | ~100 milionów ton | 1× (linia bazowa) |
Nylon (PA) | ~8 milionów ton | 2-3× |
Poliwęglan (PC) | ~4,5 miliona ton | 3-4× |
PEEK | <10 000 ton | 30-50× |
Ograniczona wielkość produkcji oznacza, że producenci nie mogą osiągnąć korzyści skali, które obniżają koszty popularnych tworzyw sztucznych. Koszty stałe, takie jak utrzymanie obiektu, kontrola jakości i badania i rozwój, rozkładają się na mniejszą liczbę kilogramów produktu, podnosząc koszt jednostkowy.
Wymagania dotyczące sprzętu i przetwarzania
Zakłady produkcyjne PEEK wymagają specjalistycznego sprzętu, który może wytrzymać ekstremalne temperatury i ciśnienia potrzebne do polimeryzacji, mieszania i przetwarzania:
- Reaktory wysokotemperaturowe z precyzyjnymi systemami sterowania
- Specjalistyczny sprzęt do wytłaczania i granulowania
- Zaawansowane systemy filtracji i oczyszczania
- Kompleksowa kontrola jakości i zaplecze testowe
Te inwestycje kapitałowe są znaczne i znacząco wpływają na ostateczny koszt materiału. Kiedy obrabiamy części PEEK w PTSMAKE, dziedziczymy te koszty produkcji w cenie surowca.
Wyzwania związane z przetwarzaniem i obróbką
Po wyprodukowaniu PEEK wiąże się z dodatkowymi wyzwaniami w zakresie przetwarzania i obróbki, które dodatkowo przyczyniają się do jego wysokich kosztów w gotowych komponentach.
Wysokie temperatury przetwarzania
Z temperaturą topnienia około 343°C (649°F), PEEK wymaga specjalistycznego sprzętu do przetwarzania:
- Wtryskarki z możliwością pracy w wysokich temperaturach
- Formy ze specjalnymi systemami zarządzania ciepłem
- Droższe elementy grzejne i sterowniki
- Ulepszone systemy bezpieczeństwa do obsługi materiałów wysokotemperaturowych
Wymagania te oznaczają, że mniej producentów jest przygotowanych do przetwarzania PEEK, co ogranicza konkurencję i utrzymuje wyższe koszty przetwarzania.
Obróbka skrawaniem i zużycie narzędzi
Podczas obróbki PEEK w PTSMAKE napotykamy kilka czynników, które przyczyniają się do wyższych kosztów produkcji:
Zużycie narzędzia: PEEK powoduje znacznie większe zużycie narzędzi niż standardowe tworzywa sztuczne, co wymaga częstszej wymiany narzędzi lub stosowania narzędzi wysokiej jakości.
Zarządzanie ciepłem: Niska przewodność cieplna PEEK oznacza, że podczas obróbki gromadzi się ciepło, co wymaga wolniejszych prędkości skrawania i specjalnych technik chłodzenia.
Specjalistyczna wiedza: Prawidłowa obróbka PEEK wymaga doświadczenia i wiedzy, aby zapobiec degradacji materiału i osiągnąć wąskie tolerancje.
Wymagania dotyczące przetwarzania końcowego: Wiele zastosowań PEEK wymaga dodatkowych etapów przetwarzania, takich jak wyżarzanie w celu zmniejszenia naprężeń wewnętrznych i zapewnienia stabilności wymiarowej.
Każdy z tych czynników zwiększa całkowity koszt produkcji gotowych komponentów PEEK poza samą ceną surowca.
Koszty kontroli jakości i certyfikacji
Jako wysokowydajny materiał często używany w krytycznych zastosowaniach, PEEK wymaga rygorystycznej kontroli jakości podczas produkcji i przetwarzania.
Rygorystyczne wymagania testowe
Każda partia PEEK jest zazwyczaj poddawana szczegółowym testom w celu weryfikacji:
- Rozkład masy cząsteczkowej
- Procent krystaliczności
- Właściwości termiczne (temperatura zeszklenia i topnienia)
- Właściwości mechaniczne (wytrzymałość na rozciąganie, moduł, wydłużenie)
- Czystość i poziomy zanieczyszczeń
Testy te wymagają specjalistycznego sprzętu i przeszkolonego personelu, co zwiększa koszty zapewnienia jakości w stosunku do ostatecznej ceny produktu.
Certyfikaty branżowe i identyfikowalność
Wiele zastosowań PEEK w przemyśle lotniczym, medycznym i półprzewodnikowym wymaga pełnej identyfikowalności materiału i zgodności z normami branżowymi:
- Certyfikaty lotnicze (AS9100, NORSOK)
- Normy dotyczące urządzeń medycznych (ISO 13485, USP klasa VI)
- Certyfikaty przemysłu jądrowego (NQSA-1)
- Wymagania przemysłu półprzewodnikowego (wysoka czystość)
Utrzymanie tych certyfikatów wymaga obszernej dokumentacji, regularnych audytów, a czasem oddzielnych zakładów produkcyjnych lub sprzętu, co przyczynia się do wyższych kosztów.
Porównanie PEEK z materiałami alternatywnymi
Aby zrozumieć ceny PEEK w kontekście, warto porównać je z materiałami alternatywnymi zarówno pod względem kosztów, jak i wydajności.
Analiza kosztów i wydajności
PEEK kosztuje zwykle 5-10 razy więcej niż standardowe tworzywa konstrukcyjne i może być nawet droższy niż niektóre metale specjalne w ujęciu ilościowym. Jednak jego wydajność w ekstremalnych warunkach często uzasadnia tę cenę:
Własność | PEEK | Standardowe tworzywa konstrukcyjne | Metale premium |
---|---|---|---|
Temperatura pracy ciągłej | Do 250°C (480°F) | 80-170°C (176-338°F) | Zazwyczaj bez ograniczeń |
Odporność chemiczna | Doskonały | Zmienny (często ograniczony) | Często słabe (korozja) |
Specyficzna siła | Bardzo wysoka | Umiarkowany | Wysoki |
Koszt surowców | Bardzo wysoka | Niski do umiarkowanego | Umiarkowany do wysokiego |
Koszt przetwarzania | Wysoki | Niski do umiarkowanego | Wysoki |
Lifetime Value | Doskonały | Ograniczone w trudnych warunkach | Dobry, ale z problemami z korozją |
W PTSMAKE często pomagamy klientom ocenić te kompromisy, aby określić, czy wyższa cena PEEK jest uzasadniona jego zaletami w konkretnym zastosowaniu.
Czy PEEK jest wart swojej wysokiej ceny?
Kwestia, czy wysoki koszt PEEK jest uzasadniony, zależy całkowicie od wymagań aplikacji.
Zastosowania, w których PEEK zapewnia wartość pomimo kosztów
PEEK zapewnia doskonałą wartość pomimo swojej wysokiej ceny w zastosowaniach:
- Ekstremalne środowiska pracy tam, gdzie inne materiały szybko by zawiodły
- Systemy o krytycznej wadze gdzie stosunek wytrzymałości do masy PEEK oferuje korzyści
- Sprzęt wrażliwy na konserwację gdzie koszty przestojów znacznie przewyższają koszty materiałów
- Środowiska korozyjne gdzie metale uległyby szybkiej degradacji
- Implanty medyczne gdzie biokompatybilność i długoterminowa stabilność mają kluczowe znaczenie
W tych scenariuszach zalety wydajności PEEK przekładają się bezpośrednio na niższe koszty w całym okresie eksploatacji, pomimo wyższej inwestycji początkowej.
Strategie redukcji kosztów komponentów PEEK
W przypadku projektów wymagających wydajności PEEK, ale ograniczonych budżetem, należy rozważyć następujące podejścia:
- Projekty hybrydowe Używanie PEEK tylko do krytycznych komponentów
- Zoptymalizowane techniki obróbki zmniejszenie ilości odpadów materiałowych
- Przetwarzanie kształtu zbliżonego do sieci minimalizacja zużycia materiałów
- Optymalizacja projektu zmniejszenie całkowitej objętości materiału
- Niewypełnione stopnie gdy wzmocnienia nie są konieczne do osiągnięcia wydajności
W PTSMAKE pomogliśmy wielu klientom wdrożyć te strategie, aby uzyskać korzyści PEEK przy jednoczesnym efektywnym zarządzaniu kosztami.
Jak zoptymalizować obróbkę PEEK pod kątem ekonomicznej produkcji?
Czy kiedykolwiek zastanawiałeś się, czy istnieje sposób na wykorzystanie wyjątkowych właściwości PEEK bez nadwyrężania budżetu projektu? Podczas pracy z jednym z najdroższych tworzyw konstrukcyjnych na rynku, optymalizacja podejścia do obróbki skrawaniem to nie tylko kwestia wydajności - może ona oznaczać różnicę między zyskownym projektem a takim, który przynosi straty finansowe z powodu nadmiernych odpadów materiałowych i niepotrzebnego czasu obróbki skrawaniem.
Optymalizacja obróbki PEEK pod kątem opłacalnej produkcji wymaga użycia odpowiednich narzędzi skrawających (z węglików spiekanych lub powlekanych diamentem), utrzymania odpowiednich prędkości i posuwów (zazwyczaj wolniejszych niż w przypadku standardowych tworzyw sztucznych), wdrożenia skutecznych strategii chłodzenia, zminimalizowania strat materiału poprzez projektowanie kształtu zbliżonego do siatki oraz starannego planowania ścieżek narzędzi w celu skrócenia czasu cyklu.
Wybór optymalnego oprzyrządowania do obróbki PEEK
Podczas obróbki PEEK wybór narzędzi ma ogromny wpływ zarówno na jakość części, jak i na ogólne koszty obróbki. Dzięki wieloletniemu doświadczeniu nauczyłem się, że inwestowanie w odpowiednie narzędzia z wyprzedzeniem pozwala zaoszczędzić znacznie więcej w dłuższej perspektywie.
Materiały i geometrie narzędzi skrawających
Ścierny charakter PEEK, zwłaszcza gatunków wypełnionych włóknem węglowym lub szklanym, wymaga starannego doboru narzędzi:
Materiał narzędzia | Najlepsze dla | Żywotność narzędzia | Współczynnik kosztów |
---|---|---|---|
Węglik (niepowlekany) | Niewypełniony PEEK | Dobry | Umiarkowany |
Węglik powlekany diamentem | Wypełniony PEEK | Doskonały | Wysoki |
PCD (diament polikrystaliczny) | Produkcja na dużą skalę | Superior | Bardzo wysoka |
Stal szybkotnąca (HSS) | Proste operacje na niewypełnionym PEEK | Ograniczony | Niski |
Do większości zastosowań w PTSMAKE używamy narzędzi z węglików spiekanych o określonych geometriach zaprojektowanych do wysokowydajnych tworzyw sztucznych. Kluczowe cechy, na które zwracamy uwagę to
- Ostre krawędzie tnące (redukują wytwarzanie ciepła)
- Wysokie dodatnie kąty natarcia (10-15°)
- Polerowane rowki (lepsze odprowadzanie wiórów)
- Wystarczające kąty prześwitu (zapobiegają ocieraniu)
Podczas gdy narzędzia premium kosztują początkowo więcej, dłużej zachowują ostrość krawędzi i zapewniają lepsze wykończenie powierzchni, zmniejszając potrzebę dodatkowych operacji.
Uwagi dotyczące zużycia narzędzia
Zużycie narzędzi następuje znacznie szybciej podczas obróbki PEEK w porównaniu ze standardowymi tworzywami konstrukcyjnymi. Odkryliśmy, że monitorowanie i zarządzanie zużyciem narzędzi ma kluczowe znaczenie dla utrzymania zarówno jakości części, jak i kontroli kosztów.
Zalecam ustalenie harmonogramu wymiany narzędzi w oparciu o obrabianą objętość, a nie czekanie na wizualne oznaki zużycia. W naszym zakładzie narzędzia do obróbki wypełnionego PEEK są zwykle wymieniane po około 60-70% żywotności narzędzia, jakiej oczekujemy podczas obróbki aluminium. Takie proaktywne podejście zapobiega problemom jakościowym i potencjalnym złomowanym częściom, które wynikają z obróbki zużytymi narzędziami.
Optymalizacja parametrów cięcia
Znalezienie odpowiedniej równowagi między prędkością, posuwem i głębokością skrawania ma kluczowe znaczenie dla wydajnej obróbki PEEK. Celem jest maksymalizacja szybkości usuwania materiału bez generowania nadmiernego ciepła lub pogarszania jakości powierzchni.
Zalecenia dotyczące prędkości i podawania
Dzięki szeroko zakrojonym testom w PTSMAKE opracowaliśmy te ogólne wytyczne dotyczące parametrów obróbki PEEK:
Typ PEEK | Prędkość cięcia (SFM) | Prędkość podawania | Głębokość cięcia | Płyn chłodzący |
---|---|---|---|---|
Niewypełniony PEEK | 300-500 | Umiarkowany | 0.005"-0.020" | Powietrze lub mgła |
30% z wypełnieniem węglowym | 200-400 | Zmniejszona (75%) | 0.005"-0.015" | Mgła/powódź |
30% Wypełnienie szklane | 250-450 | Zmniejszona (85%) | 0.005"-0.015" | Mgła/powódź |
Parametry te należy dostosować w oparciu o konkretne oprzyrządowanie, sztywność maszyny i wymagania dotyczące części. Generalnie zalecam rozpoczęcie od konserwatywnego końca tych zakresów i stopniowe zwiększanie parametrów podczas monitorowania wyników.
Strategie zarządzania ciepłem
Słaba przewodność cieplna PEEK może prowadzić do gromadzenia się ciepła podczas obróbki, potencjalnie powodując:
- Niestabilność wymiarowa
- Zdegradowane wykończenie powierzchni
- Przyspieszone zużycie narzędzia
- Rozkład materiału w skrajnych przypadkach
Aby zwalczyć te problemy, wdrożyliśmy kilka technik zarządzania temperaturą:
Właściwy dobór płynu chłodzącego: W przypadku niewypełnionego PEEK często dobrze sprawdza się chłodzenie sprężonym powietrzem. W przypadku wypełnionych gatunków, chłodziwo w postaci mgiełki lub zalewy zapewnia lepsze rozpraszanie ciepła.
Cięcie przerywane: Okresowa przerwa podczas operacji głębokiego wciskania pozwala na rozproszenie ciepła.
Climb Milling: Zastosowanie frezowania wspinaczkowego zamiast konwencjonalnego zmniejsza tarcie i generowanie ciepła.
Wiele przejść światła: Wykonanie kilku lekkich przejść wykańczających zamiast jednego ciężkiego cięcia poprawia dokładność wymiarową i wykończenie powierzchni.
Strategie wykorzystania materiałów
Biorąc pod uwagę wysoki koszt PEEK (często $75-200 za funt w zależności od gatunku i formy), wykorzystanie materiału staje się krytycznym czynnikiem kosztowym. Każda ilość odpadów ma bezpośredni wpływ na wyniki finansowe.
Materiał wyjściowy o kształcie zbliżonym do siatki
Rozpoczęcie od materiału, który jest bliższy ostatecznym wymiarom, może znacznie zmniejszyć ilość odpadów. Rozważ następujące podejścia:
Niestandardowe wytłoczki: W przypadku części o spójnych przekrojach, rozpoczęcie produkcji od niestandardowych profili wytłaczanych może wyeliminować znaczne straty materiału. Wyższy koszt konfiguracji jest równoważony przez oszczędności materiałowe w przypadku większych serii produkcyjnych.
Wstępnie wycięte półfabrykaty: Zlecając dostawcy materiałów dostarczenie wstępnie wyciętych półfabrykatów o rozmiarach dostosowanych do konkretnych części, zmniejsza się zarówno ilość odpadów, jak i czas wstępnej obróbki.
Oprogramowanie do zagnieżdżania: W przypadku płaskich części obrabianych z blachy, użycie zaawansowanego oprogramowania do nestingu może zoptymalizować zużycie materiału o 15-30% w porównaniu do ręcznego planowania układu.
W PTSMAKE pomogliśmy klientom obniżyć koszty materiałów PEEK o ponad 40%, wdrażając te podejścia do ich wysokonakładowych komponentów.
Rozważania dotyczące recyklingu chipów
W przeciwieństwie do niektórych tworzyw termoplastycznych, PEEK nie może być łatwo poddany recyklingowi we własnym zakresie ze względu na wysoką temperaturę przetwarzania. Istnieją jednak wyspecjalizowane usługi recyklingu:
- Czyste, posortowane wióry PEEK mogą być sprzedawane firmom zajmującym się recyklingiem.
- Niektóre firmy zajmujące się recyklingiem zaliczają wartość materiałów na poczet przyszłych zakupów
- Wypełnione gatunki mają zazwyczaj niższą wartość recyklingową ze względu na obawy związane z zanieczyszczeniem.
Chociaż recykling nie zrekompensuje całkowicie kosztów materiałów, może zapewnić pewien zwrot kosztów w przypadku większych operacji obróbki skrawaniem.
Optymalizacja strategii obróbki
Poza narzędziami i parametrami, ogólne podejście do obróbki znacząco wpływa zarówno na jakość części, jak i koszty produkcji.
Projekt urządzenia dla wielu części
Dobrze zaprojektowane uchwyty, które umożliwiają obróbkę wielu części w jednym ustawieniu, oferują kilka korzyści:
- Krótszy czas konfiguracji na część
- Lepsza spójność między częściami
- Bardziej wydajne wykorzystanie maszyn
- Lepsza wydajność materiału z blachy
Dla jednego z klientów z branży lotniczej zaprojektowaliśmy mocowanie, które umożliwiło jednoczesną obróbkę 16 małych komponentów PEEK, zmniejszając koszt pojedynczej części o 62% w porównaniu z indywidualnymi konfiguracjami.
Udoskonalenie strategii CAM
Zoptymalizowane ścieżki narzędzi mogą znacznie skrócić czas obróbki i poprawić jakość części:
Wysokowydajne frezowanie: Korzystanie z zaawansowanych strategii CAM, które utrzymują stałe zaangażowanie narzędzia, skraca czas cyklu i wydłuża żywotność narzędzia.
Obróbka spoczynkowa: Prawidłowo zaplanowane operacje, które wykorzystują większe narzędzia do usuwania dużych ilości materiału i mniejsze narzędzia tylko tam, gdzie jest to konieczne, optymalizują zarówno szybkość usuwania materiału, jak i żywotność narzędzia.
Zoptymalizowane ruchy podejścia: Minimalizacja cięcia powietrzem poprzez wydajne ruchy zbliżania i wycofywania może skrócić czas cyklu o 5-15% bez wpływu na jakość części.
Kontrola jakości w celu zminimalizowania ilości odpadów
Biorąc pod uwagę wysoki koszt materiału PEEK, redukcja odpadów staje się podstawową strategią oszczędzania kosztów. Skuteczne procesy kontroli jakości, które wcześnie wychwytują problemy, zapobiegają marnowaniu drogiego materiału na części, które nie spełniają specyfikacji.
Pomiar w trakcie procesu
Wdrożyliśmy kilka etapów weryfikacji w trakcie procesu:
Inspekcja pierwszego artykułu: Dokładne pomiary pierwszej części każdej serii przed przystąpieniem do produkcji.
Inspekcje etapowe: Pomiar krytycznych cech przed przystąpieniem do kolejnych operacji, zwłaszcza podczas odwracania lub ponownego mocowania części.
Stabilizacja termiczna: Umożliwienie częściom osiągnięcia temperatury otoczenia przed ostatecznymi pomiarami, ponieważ rozszerzalność cieplna PEEK może wpływać na wymiary.
Praktyki te pomogły nam utrzymać wskaźnik złomu poniżej 2% dla komponentów PEEK, znacznie niższy niż średnie w branży.
Uwagi dotyczące obróbki końcowej
Proces nie kończy się, gdy część opuszcza maszynę. Operacje wykonywane po obróbce mogą mieć znaczący wpływ zarówno na jakość, jak i koszty.
Odciążenie i stabilność wymiarowa
Części PEEK o złożonej geometrii lub nierównomiernym usuwaniu materiału mogą korzystać z odciążenia, aby zapewnić długoterminową stabilność wymiarową:
Wyżarzanie termiczne: Kontrolowane ogrzewanie poniżej temperatury zeszklenia, a następnie powolne chłodzenie może zmniejszyć naprężenia wewnętrzne.
Strategia od zera do końca: Usunięcie większości materiału w początkowej operacji, a następnie umożliwienie ustabilizowania się części przed ostateczną obróbką poprawia dokładność wymiarową.
W przypadku krytycznych komponentów o wąskich tolerancjach, te dodatkowe kroki są warte inwestycji, aby zapobiec kosztownym awariom w terenie lub odchyleniom wymiarowym w czasie.
Wdrażając te strategie optymalizacji, pomogliśmy wielu klientom PTSMAKE osiągnąć opłacalną obróbkę PEEK bez uszczerbku dla wyjątkowych właściwości użytkowych, które sprawiają, że materiał ten jest tak cenny. Kluczem jest holistyczne podejście, które uwzględnia każdy aspekt procesu produkcyjnego, od wyboru materiału po kontrolę końcową.
Dowiedz się więcej o technikach zarządzania temperaturą w wysokowydajnej obróbce tworzyw sztucznych. ↩
Poznaj zaawansowane techniki precyzyjnej obróbki wysokowydajnych tworzyw termoplastycznych. ↩
Kliknij tutaj, aby poznać specjalistyczne techniki precyzyjnej obróbki wysokowydajnych tworzyw termoplastycznych. ↩
Dowiedz się, w jaki sposób właściwości mechaniczne wpływają na wybór materiałów do produkcji wysokowydajnych komponentów. ↩
Poznaj specjalistyczne techniki obróbki zapobiegające odkształceniom termicznym wysokowydajnych tworzyw termoplastycznych. ↩