Ever tried machining PMMA and ended up with melted edges or cracked parts? The frustration of wasted material and time can be overwhelming, especially when you’re working on a critical project with tight deadlines.
PMMA (polymethyl methacrylate) has excellent machinability with a rating of 7-8 out of 10. It can be easily cut, drilled, and milled using standard metalworking tools, though it requires proper cooling to prevent melting and cracking during high-speed operations.
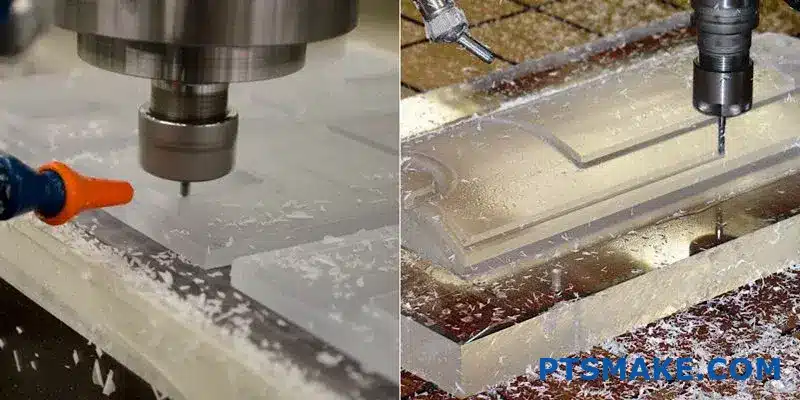
I’ve worked with PMMA (also known as acrylic) extensively in our manufacturing facility. From my experience, it’s one of the most versatile plastics for machining operations, but success depends on using the right parameters. Let me share what makes PMMA’s machinability special and how we approach it at PTSMAKE to achieve optimal results.
What Are the Negatives of PMMA?
Have you ever worked with PMMA material only to face unexpected challenges during manufacturing? It looks perfect on paper, but then reality hits – brittleness issues, machining difficulties, or environmental concerns that weren’t apparent in the design phase.
PMMA (polymethyl methacrylate) has several significant drawbacks despite its popularity. Its main negatives include brittleness, susceptibility to scratches, poor chemical resistance, difficult processing requirements, environmental concerns, and limitations in high-temperature applications.

Understanding PMMA’s Inherent Brittleness
PMMA, commonly known as acrylic or by brand names like Plexiglas and Lucite, offers excellent optical clarity but comes with a significant drawback: brittleness. In my experience working with various materials at PTSMAKE, I’ve found that PMMA’s brittleness presents real challenges for engineers and designers.
When subjected to impact or stress, PMMA can crack or shatter rather than deform. This behavior contrasts sharply with materials like polycarbonate, which offers similar transparency but with much higher impact resistance. For projects requiring both transparency and durability, this fundamental limitation often forces design compromises.
Impact Resistance Comparison
Material | Impact Strength | Relative Brittleness | Typical Applications |
---|---|---|---|
PMMA | Low | High | Displays, signage, decorative items |
Polycarbonate | High | Low | Safety glazing, protective equipment |
PETG | Medium | Medium | Packaging, medical devices |
The brittleness factor becomes especially problematic in applications with vibration or potential impact. I’ve seen numerous cases where clients needed to redesign products after discovering PMMA components couldn’t withstand real-world conditions.
Surface Vulnerability and Maintenance Issues
Another significant drawback of PMMA is its soft surface that scratches easily. Even with careful handling, PMMA parts often develop a network of fine scratches over time, diminishing both aesthetics and optical clarity.
This vulnerability makes PMMA challenging for high-touch applications or environments where abrasion might occur. Special coatings can help mitigate this issue, but they add cost and complexity to manufacturing processes.
Maintenance becomes an ongoing concern with PMMA components. Cleaning must be done carefully with appropriate non-abrasive products to avoid damaging the surface. Over time, even with proper care, the accumulation of minor scratches can necessitate replacement of PMMA parts.
Chemical Resistance Limitations
PMMA’s chemical vulnerability1 represents another significant downside. The material is susceptible to damage from:
- Organic solvents (acetone, alcohols)
- Strong acids and bases
- Petroleum-based products
- Many common household chemicals
In manufacturing environments, this chemical sensitivity requires careful material handling protocols. At PTSMAKE, we implement strict procedures for PMMA processing to prevent contamination or damage during machining and handling.
For end-users, these limitations mean PMMA products must be kept away from many cleaning agents and chemicals that might contact the surface, restricting their practical applications.
Processing Challenges and Manufacturing Constraints
Working with PMMA presents several manufacturing challenges:
Machining Difficulties
PMMA requires careful machining parameters to prevent:
- Melting (due to low glass transition temperature)
- Chipping or cracking (due to brittleness)
- Stress buildup (requiring annealing after machining)
These constraints often translate to longer processing times and higher manufacturing costs. At PTSMAKE, our specialized equipment and experience with PMMA machining help mitigate these issues, but they remain inherent limitations of the material.
Thermal Forming Limitations
While PMMA can be thermoformed, the process window is narrower than with many other plastics:
- Too cool: insufficient forming
- Too hot: bubbles, discoloration, or material degradation
This narrow processing window increases production complexity and potentially raises costs for formed PMMA components.
Environmental and Health Considerations
Although PMMA is technically recyclable (resin code #7), practical recycling remains limited in many regions. This creates end-of-life disposal challenges for PMMA products.
Additionally, the manufacturing process involves chemicals like methyl methacrylate, which requires proper handling procedures to ensure worker safety. While the finished PMMA product is generally considered safe, the production process demands robust safety protocols.
PMMA also releases potentially harmful compounds when burned, creating both safety and environmental concerns in fire situations or improper disposal.
Temperature Limitations
PMMA’s performance deteriorates significantly at elevated temperatures:
- Begins to soften around 85°C (185°F)
- Loses dimensional stability under load at even lower temperatures
- Exhibits increased creep behavior with temperature rise
These limitations restrict PMMA’s use in applications exposed to heat, direct sunlight, or environments with temperature fluctuations.
Despite these drawbacks, PMMA remains valuable for many applications where its outstanding optical properties and reasonable cost outweigh its limitations. At PTSMAKE, we help clients evaluate these tradeoffs and often recommend alternative materials or design modifications when PMMA’s negatives would compromise product performance.
Does PMMA Scratch Easily?
Have you ever invested in a beautiful PMMA product only to find it covered in scratches after minimal use? Or spent hours polishing scratches out of your acrylic components? The frustration of seeing pristine surfaces quickly deteriorate can be overwhelming, especially when you’ve chosen a material specifically for its optical clarity.
PMMA (acrylic) does scratch relatively easily compared to glass and some other plastics. With a Rockwell hardness of M80-M105, it’s susceptible to scratching from everyday items like keys, dust particles, and improper cleaning methods. However, with proper handling and maintenance, PMMA’s scratch vulnerability can be effectively managed.
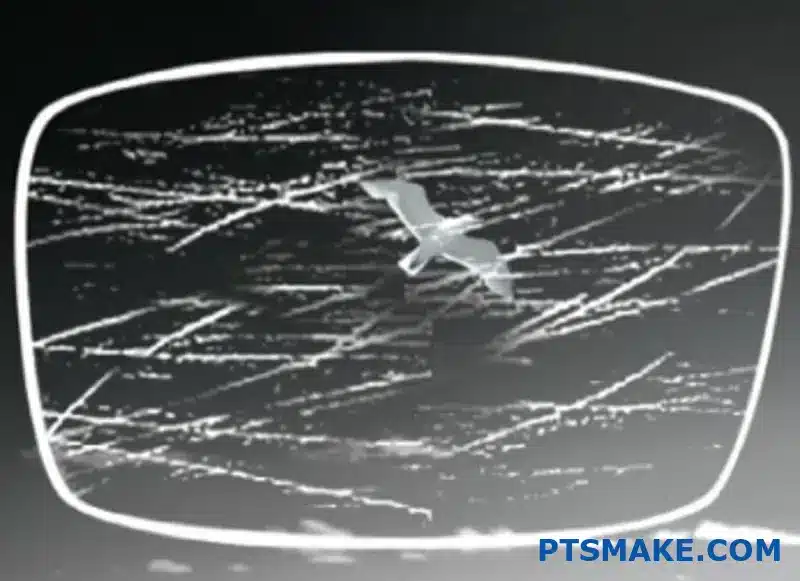
Understanding PMMA’s Scratch Resistance Properties
PMMA, or polymethyl methacrylate, is valued across industries for its exceptional optical clarity, UV resistance, and relatively high strength-to-weight ratio. However, its surface hardness presents a significant limitation. In my experience working with various materials at PTSMAKE, PMMA’s scratch resistance is noticeably lower than glass and even some other engineering plastics.
The scratch vulnerability of PMMA stems from its molecular structure. Unlike glass, which has a highly crosslinked amorphous structure, PMMA consists of long polymer chains with less crosslinking. This makes it more susceptible to mechanical abrasion and scratching from relatively mild forces.
Measuring PMMA’s Hardness
When evaluating scratch resistance, hardness measurements provide valuable insights. For PMMA, several standard tests reveal its properties:
Hardness Test | Typical PMMA Value | Comparison (Glass) |
---|---|---|
Rockwell M | 80-105 | N/A (too brittle) |
Mohs Scale | 2-3 | 5.5-7 |
Shore D | 90-100 | N/A |
Pencil Hardness | 2H-4H | 6H-9H |
These measurements confirm what I’ve observed in numerous machining projects – PMMA is significantly softer than glass and many metals, making it more prone to surface damage during both use and processing.
Common Causes of PMMA Scratching
In the manufacturing environment at PTSMAKE, we’ve identified several common scenarios that lead to PMMA scratching:
- Improper Handling: Direct contact with hard or abrasive materials (metals, minerals, even dust particles)
- Cleaning Methods: Using abrasive cleaners or rough cloths
- Machining Processes: Inadequate tooling or incorrect speeds during CNC machining2
- Environmental Factors: Wind-blown particles in outdoor applications
- Regular Use: Keys, fingernails, and other everyday items
One surprising culprit I’ve noticed is packaging materials. Even materials presumed to be safe, like tissue paper, can trap dust particles that scratch PMMA during transit.
The Impact of Different Scratch Types
Not all scratches affect PMMA equally. In my experience, scratches on PMMA can be categorized into:
- Surface Micro-scratches: Shallow, often only visible at certain angles
- Deep Scratches: Penetrate further into the material, more visible
- Crazing: Networks of tiny cracks that appear under stress or chemical exposure
Surface micro-scratches are most common and least problematic, often removable with polishing. Deep scratches typically require more intensive restoration methods, while crazing often indicates material damage beyond simple scratching.
Comparative Scratch Resistance Analysis
When compared to other transparent materials, PMMA’s scratch resistance falls on the lower end of the spectrum:
Material | Relative Scratch Resistance | Optical Clarity | Key Advantage |
---|---|---|---|
Glass | High | Excellent | Superior hardness |
Polycarbonate | Medium | Good | Impact resistance |
PMMA | Low-Medium | Excellent | Optical qualities |
PETG | Medium | Good | Formability |
Tempered Glass | Very High | Excellent | Extreme durability |
This comparison highlights why material selection requires balancing priorities. While PMMA may scratch more easily than alternatives, its optical clarity, UV stability, and machinability often make it the preferred choice for many applications despite this limitation.
Protecting PMMA from Scratches
Based on my experience with countless PMMA components at PTSMAKE, I recommend these practical approaches to minimize scratching:
- Protective Coatings: Hard-coat treatments can significantly improve scratch resistance
- Proper Handling: Use soft gloves and avoid contact with abrasive materials
- Appropriate Cleaning: Mild soap, water, and microfiber cloths
- Optimized Machining: Using proper tooling and machining parameters
- Protective Films: Leaving the manufacturer’s film in place until final installation
For critical applications where optical clarity and scratch resistance are both essential, we often recommend hybrid solutions that capitalize on PMMA’s clarity while mitigating its scratch vulnerability through strategic design and protective measures.
Is PMMA the Same as Acrylic?
Have you ever found yourself confused when ordering plastic materials, wondering if PMMA and acrylic are different products? Or maybe you’ve been quoted different prices for what seems like the same material under different names? This confusion is more common than you might think.
Yes, PMMA (polymethyl methacrylate) and acrylic are essentially the same material. PMMA is the chemical name, while acrylic is the common commercial term. Both refer to a transparent thermoplastic known for its clarity, UV resistance, and versatility in applications ranging from signs to medical devices.
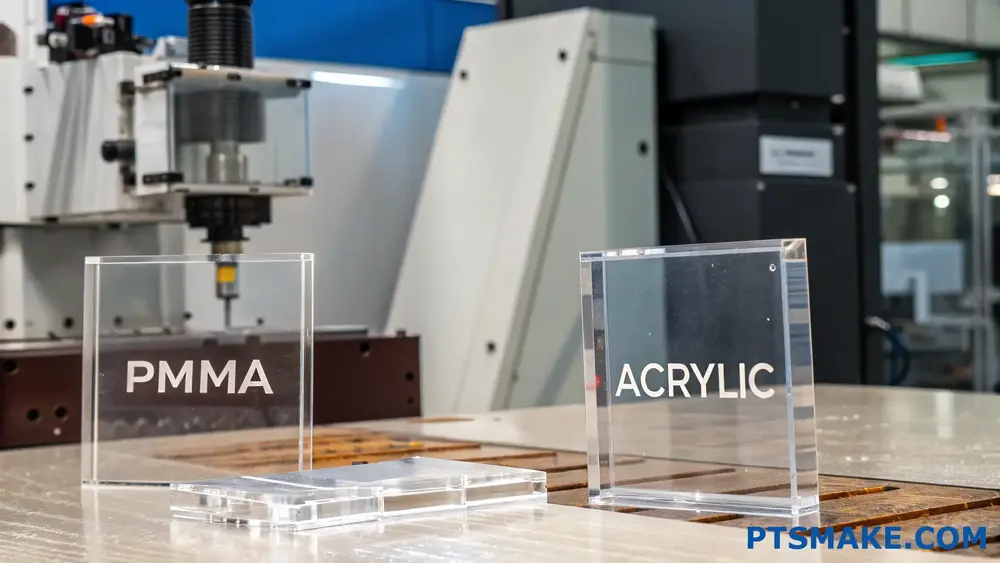
The Chemical Composition of PMMA and Acrylic
When looking at these materials from a molecular perspective, they are identical. PMMA stands for polymethyl methacrylate, which is a synthetic polymer of methyl methacrylate. This polymer creates long chains of repeating units that give acrylic its unique properties.
The chemical structure of PMMA includes a carbon backbone with methyl groups (CH₃) and methyl ester groups (COOCH₃) attached to it. This structure is what gives PMMA its remarkable transparency – it allows approximately 92% of visible light to pass through, making it one of the clearest plastics available.
In my experience working with various plastic materials at PTSMAKE, I’ve found that this high optical clarity is one of the main reasons engineers choose PMMA for applications where visual aesthetics are important.
Common Brand Names for PMMA/Acrylic
PMMA is sold under various trade names depending on the manufacturer. Some of the most recognized brands include:
Brand Name | Manufacturer | Notable Characteristics |
---|---|---|
Plexiglas® | Röhm | High optical clarity, weather resistance |
Lucite® | Lucite International | Excellent light transmission |
Acrylite® | Evonik Industries | Good chemical resistance |
Perspex® | Lucite International | Popular in architectural applications |
Optix® | Plaskolite | Common in signage applications |
These brand names all refer to essentially the same base material – PMMA. The differences typically lie in specific formulations, additives, or manufacturing processes that may enhance certain properties for particular applications.
Manufacturing Processes for PMMA/Acrylic
Cast Acrylic vs. Extruded Acrylic
Although PMMA and acrylic are chemically identical, there are two primary manufacturing methods that produce slightly different material properties:
Cast Acrylic: This is produced by pouring liquid monomer3 between two glass plates and allowing it to polymerize. Cast acrylic typically has:
- Better optical clarity
- Higher molecular weight
- Better chemical resistance
- Easier machining properties
- Higher heat resistance
Extruded Acrylic: This is made by forcing molten acrylic through a die to create sheets. Extruded acrylic generally has:
- More consistent thickness
- Lower cost
- Slightly lower optical quality
- Less chemical resistance
- Better thermoforming capabilities
At PTSMAKE, we work with both types depending on the customer’s specific requirements. For precise CNC machining projects requiring tight tolerances, I often recommend cast acrylic due to its superior machining characteristics and dimensional stability.
Material Properties Comparison
PMMA/acrylic offers a unique combination of properties that make it suitable for a wide range of applications:
Optical Properties
- Light Transmission: ~92% (one of the highest among plastics)
- Refractive Index: 1.49
- UV Resistance: Excellent, minimal yellowing over time
Mechanical Properties
- Tensile Strength: 70-75 MPa
- Flexural Strength: 100-110 MPa
- Impact Resistance: Moderate (better than glass, less than polycarbonate)
- Hardness (Rockwell): M80-M100
Thermal Properties
- Heat Deflection Temperature: 95-105°C (depending on grade)
- Maximum Continuous Service Temperature: ~80-85°C
- Coefficient of Thermal Expansion: Relatively high at 5-9 × 10⁻⁵/°C
Common Applications of PMMA/Acrylic
The unique combination of transparency, weather resistance, and relatively easy fabrication makes PMMA/acrylic ideal for numerous applications:
Consumer Goods
- Display stands and retail fixtures
- Furniture (tables, chairs, decorative items)
- Aquariums and picture frames
Industrial Applications
- Machine guards
- Control panels and displays
- Light guides and diffusers
Architectural Uses
- Windows and skylights
- Balustrades and barriers
- Decorative panels and signage
Medical Applications
- Medical device components
- Dental prosthetics
- Laboratory equipment
In my 15+ years of manufacturing experience, I’ve seen PMMA machining projects span from simple display stands to complex medical device components. The material’s versatility makes it a popular choice across industries, though each application requires specific considerations for machining parameters and finishing techniques.
What Is the Advantage of PMMA?
Have you ever struggled to find the perfect material for your project that combines optical clarity, weather resistance, and machinability? Are you tired of compromising between aesthetic appeal and functional durability when selecting plastics for your products?
PMMA (polymethyl methacrylate), commonly known as acrylic, offers exceptional advantages including outstanding optical clarity, excellent weather resistance, good mechanical properties, versatile fabrication options, and cost-effectiveness compared to glass and other transparent materials.
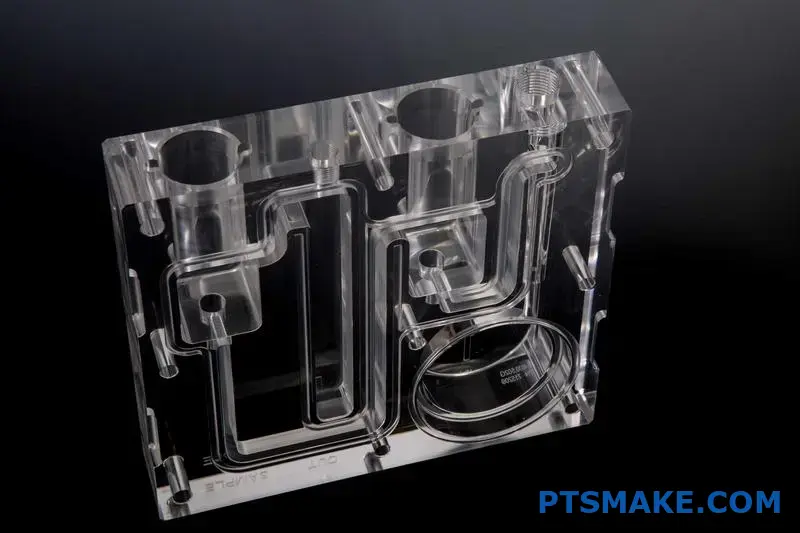
Superior Optical Properties
PMMA’s most remarkable feature is its exceptional optical clarity. With a light transmission rate of approximately 92%, it outperforms many other transparent plastics and even rivals glass. This makes it ideal for applications where visual clarity is paramount.
In my experience at PTSMAKE, clients are consistently impressed by PMMA’s ability to maintain its transparency over time. Unlike polycarbonate, which tends to yellow with age, PMMA retains its crystal-clear appearance for years. This property has made it particularly valuable for display cases, signage, and architectural elements.
The material’s optical properties extend beyond mere transparency. PMMA can be easily colored, allowing for vibrant, translucent products that maintain their light transmission properties. I’ve seen this characteristic utilized effectively in LED lighting fixtures, where the material diffuses light evenly while maintaining color integrity.
Optical Comparison with Other Materials
Material | Light Transmission (%) | Yellowness Index (Initial) | UV Resistance |
---|---|---|---|
PMMA | 92 | 1-2 | Excellent |
Polycarbonate | 88 | 2-3 | Poor-Fair |
Glass | 90-92 | 0-1 | Excellent |
PET | 85-90 | 2-4 | Good |
Weather and Chemical Resistance
PMMA exhibits excellent resistance to outdoor weathering conditions. This material maintains its properties when exposed to UV radiation, moisture, and temperature fluctuations—factors that would degrade many other plastics.
Working with outdoor display manufacturers, I’ve consistently recommended PMMA for signage and displays. The material doesn’t crack or yellow significantly even after years of sun exposure, making it a reliable choice for outdoor applications. Its high photostability4 ensures that colored PMMA products maintain their vibrancy over time.
The chemical resistance of PMMA is also notable, though selective. While it performs well against many common substances like dilute acids, alkalis, and household cleaners, it’s vulnerable to certain organic solvents. This characteristic requires careful consideration in applications where exposure to chemicals is expected.
Mechanical Properties and Durability
PMMA offers a favorable combination of rigidity and impact resistance, though it’s not as tough as some engineering plastics. With a tensile strength of approximately 70 MPa and a flexural modulus around 3 GPa, it provides adequate mechanical performance for many applications.
At PTSMAKE, we often recommend PMMA for applications requiring a balance of optical clarity and moderate mechanical strength. For instance, display stands and retail fixtures benefit from PMMA’s ability to support modest loads while maintaining an elegant appearance.
One limitation worth noting is PMMA’s relatively brittle nature compared to materials like polycarbonate. When impact resistance is critical, we typically suggest modified grades of PMMA or alternative materials. However, for most applications where extreme impacts aren’t expected, standard PMMA provides sufficient durability.
Mechanical Properties Comparison
Material | Tensile Strength (MPa) | Flexural Modulus (GPa) | Impact Strength (J/m) |
---|---|---|---|
PMMA | 65-75 | 2.8-3.3 | 10-20 |
Polycarbonate | 55-65 | 2.3-2.4 | 600-850 |
Polystyrene | 35-55 | 2.9-3.5 | 10-20 |
Glass | 30-90 | 70-75 | <10 |
Manufacturing Versatility
PMMA’s versatility in manufacturing processes is one of its strongest advantages. The material can be efficiently processed through various methods, including:
- Injection molding
- Extrusion
- Thermoforming
- CNC machining
- Laser cutting
At PTSMAKE, we regularly CNC machine PMMA components for clients needing precision parts with optical clarity. The material machines beautifully, producing smooth surface finishes without excessive tool wear. For high-volume production, our injection molding services can efficiently produce complex PMMA parts with excellent dimensional accuracy.
The material’s thermoforming capabilities are particularly valuable for creating curved displays and architectural elements. PMMA can be heated and formed into complex shapes while maintaining its optical properties, opening up design possibilities that would be cost-prohibitive with glass.
Cost-Effectiveness and Sustainability
When comparing PMMA to alternatives like glass or polycarbonate, the cost-benefit analysis often favors PMMA for many applications. Though typically more expensive than general-purpose plastics like polystyrene, PMMA offers superior performance characteristics that justify its price point.
PMMA’s lower weight compared to glass (about half the density) reduces transportation costs and simplifies installation for large panels or components. This weight advantage has made it particularly popular in architectural applications and display structures.
From a sustainability perspective, PMMA offers several advantages. It’s fully recyclable, with established recycling streams in many regions. Additionally, its longevity means less frequent replacement, reducing lifetime resource consumption. However, like most petroleum-based plastics, PMMA production does have an environmental footprint that should be considered in sustainability assessments.
Application-Specific Advantages
Different industries benefit from specific aspects of PMMA’s property profile:
Medical Industry: PMMA’s biocompatibility makes it suitable for dental implants, bone cement, and intraocular lenses.
Automotive Sector: Its scratch resistance and optical clarity make it ideal for tail light lenses and interior displays.
Architecture: Weather resistance and light transmission properties make PMMA perfect for skylights, partitions, and decorative elements.
Retail and Signage: The combination of formability, paintability, and optical properties creates striking displays and signage.
In my work with electronics manufacturers, I’ve seen PMMA become increasingly popular for device displays and housings, as it offers an appealing glass-like aesthetic without the weight or fragility of actual glass.
How Do Cutting Parameters Affect PMMA Machining Surface Finish?
Have you ever struggled with hazy or chipped edges on your PMMA projects? Those frustrating surface defects that appear no matter how carefully you set up your CNC machine? It’s a common challenge that can turn a promising design into a disappointing result.
Cutting parameters significantly influence PMMA machining surface finish by controlling chip formation and heat generation. Optimal spindle speeds (10,000-18,000 RPM), feed rates (0.1-0.2 mm/tooth), and depth of cut (0.5-1mm) typically yield the best surface quality by minimizing melting and chipping.
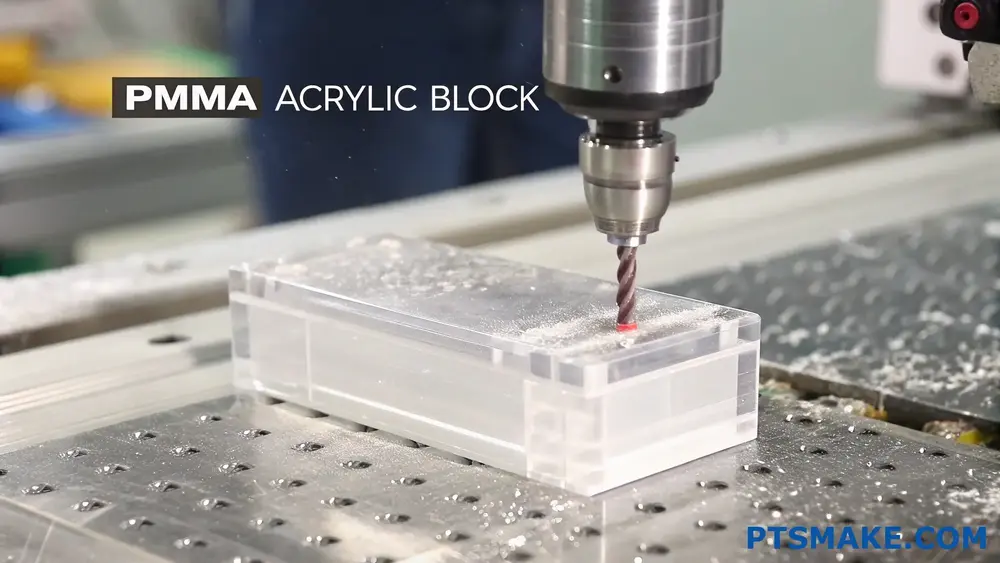
The Science Behind PMMA Surface Finish
When machining PMMA (polymethyl methacrylate), commonly known as acrylic, achieving an excellent surface finish requires understanding how different cutting parameters interact with this unique material. As a thermoplastic, PMMA has distinct mechanical and thermal properties that respond differently to machining conditions compared to metals or other plastics.
The surface quality of machined PMMA is primarily affected by the thermoplastic deformation5 behavior during cutting. Unlike metals that produce continuous chips through plastic deformation, PMMA tends to experience both ductile and brittle fracture modes depending on the cutting conditions. This dual behavior makes parameter selection particularly critical.
Spindle Speed Effects
Spindle speed directly influences cutting temperature and chip formation in PMMA machining:
- Low Speeds (Below 8,000 RPM): Often result in excessive cutting forces and brittle fracture, leading to chipping and poor surface finish
- Medium Speeds (8,000-15,000 RPM): Provide a balance between heat generation and cutting efficiency
- High Speeds (Above 15,000 RPM): Can generate excessive heat causing material softening and possible melting
In my experience at PTSMAKE, we’ve found that spindle speeds between 10,000-18,000 RPM typically yield the best results for general PMMA machining operations, though this varies with cutter diameter and other factors.
Feed Rate Considerations
Feed rate affects both productivity and surface quality:
Feed Rate (mm/tooth) | Surface Finish | Productivity | Common Issues |
---|---|---|---|
0.05-0.1 | Excellent | Low | Possible heat buildup, burning |
0.1-0.2 | Very Good | Medium | Minimal defects, optimal range |
0.2-0.3 | Good | High | Potential minor chipping |
>0.3 | Poor | Very High | Severe chipping, tool marks |
The sweet spot for PMMA typically falls between 0.1-0.2 mm/tooth, balancing productivity with surface quality. Too slow, and heat buildup becomes problematic; too fast, and mechanical damage occurs.
Depth of Cut and Width of Cut
These parameters determine the chip load and affect both surface quality and tool life:
- Depth of Cut: For finishing operations, I recommend 0.5-1mm maximum. Deeper cuts create higher forces that can crack or chip PMMA edges.
- Width of Cut: For optimal surface finish, step-overs of 10-25% of tool diameter work best for finishing passes.
When working with complex geometries at PTSMAKE, we often program progressive machining strategies, starting with roughing operations that remove bulk material followed by finishing passes with lighter cuts.
Tool Geometry Factors
Tool selection dramatically impacts surface finish quality in PMMA machining:
Cutting Edge Geometry
- Rake Angle: Positive rake angles (5-15°) generally produce better surface finish by reducing cutting forces
- Clearance Angle: 10-15° clearance prevents rubbing against the workpiece
- Helix Angle: Higher helix angles (30-45°) improve chip evacuation and reduce heat buildup
Tool Materials and Coatings
For PMMA machining, we typically use:
- Carbide Tools: Maintain sharp edges longer than HSS
- Diamond-Coated Tools: Provide excellent surface finish for high-volume production
- Single-Flute Cutters: Often preferred for acrylics to improve chip evacuation
The combination of proper tool selection and cutting parameters creates a synergistic effect. At PTSMAKE, we’ve developed specialized parameter sets for different PMMA grades and product requirements, ensuring consistent quality across production runs.
Cooling and Lubrication Strategies
Unlike metal machining where coolant is standard, PMMA machining requires careful consideration:
- Compressed Air: Often sufficient for moderate cutting conditions
- Mist Cooling: Minimal lubrication with specialized non-petroleum fluids
- Dry Cutting: Possible with optimized parameters and efficient chip evacuation
Never use standard oil-based coolants with PMMA as they can cause crazing and stress cracking on the machined surface—a lesson I’ve learned through troubleshooting customer quality issues early in my career.
Practical Optimization Approach
When setting up PMMA machining operations, I follow this systematic approach:
- Select appropriate tools based on feature requirements
- Begin with conservative cutting parameters (medium speed, low feed)
- Conduct test cuts on scrap material
- Gradually increase parameters until optimal surface finish is achieved
- Document successful parameters for future reference
This methodology helps us at PTSMAKE deliver consistently high-quality PMMA components across various industries, from medical device components to optical displays.
What Post-Processing Steps Are Required After PMMA Machining?
Have you ever received a freshly machined PMMA part that looked promising, only to find it was cloudy, had visible tool marks, or simply lacked that crystal-clear finish you were expecting? The machining process is just the beginning – without proper post-processing, even the most precisely machined PMMA parts can fall short of expectations.
After PMMA machining, essential post-processing steps include deburring, stress relieving, surface finishing (sanding/polishing), cleaning, and final quality inspection. These processes transform raw machined parts into high-quality, optically clear components that meet precise specifications and aesthetic requirements.
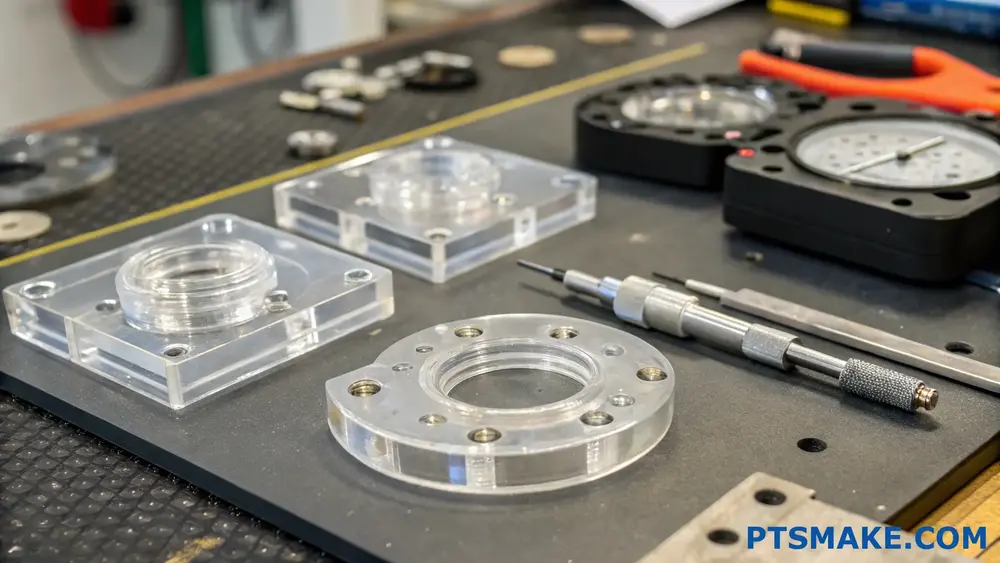
Understanding PMMA Post-Processing Requirements
PMMA (polymethyl methacrylate), commonly known as acrylic, is valued for its exceptional optical clarity, UV resistance, and mechanical properties. However, the machining process inevitably creates issues that require correction through post-processing. The clear, glass-like appearance that makes PMMA so desirable can only be achieved through careful post-machining treatments.
In my work at PTSMAKE, I’ve found that proper post-processing is what separates average PMMA parts from exceptional ones. Many clients don’t realize that up to 30% of the total production time for precision PMMA components is dedicated to post-processing steps. Let me walk you through the essential post-machining operations that deliver superior results.
Deburring and Edge Treatment
Fresh from CNC machining, PMMA parts typically have sharp edges and burrs that must be removed. These imperfections are not just aesthetic concerns but also safety hazards that can:
- Create weak points susceptible to cracking
- Cause injury during handling
- Interfere with assembly processes
- Compromise optical properties at edges
Deburring can be performed manually using specialized tools or through automated processes depending on part complexity. For optical components, edge treatment might involve flame polishing, where a controlled flame is briefly applied to melt and smooth the edges without affecting the rest of the part.
Stress Relief Heat Treatment
One of the most critical yet often overlooked post-processing steps is stress relief. PMMA is susceptible to internal stress6 during machining, which can cause crazing, cracking, or dimensional changes over time.
The heat treatment process typically follows these parameters:
Temperature Range | Duration | Cooling Rate | Application |
---|---|---|---|
70-80°C (158-176°F) | 1-2 hours | 10-15°C per hour | General components |
80-90°C (176-194°F) | 2-4 hours | 5-10°C per hour | Precision optical parts |
90-95°C (194-203°F) | 4-6 hours | 3-5°C per hour | High-stress applications |
This controlled heating and cooling cycle allows polymer molecules to relax and redistribute, eliminating internal stresses that could compromise the part’s integrity. At PTSMAKE, we’ve developed specialized annealing protocols for different PMMA grades and part geometries to ensure optimal results.
Surface Finishing Techniques
The true beauty of PMMA lies in its optical clarity, which requires meticulous surface finishing. This typically involves a progression of steps:
- Rough Sanding: Starting with 240-320 grit abrasives to remove tool marks
- Progressive Sanding: Working through increasingly finer grits (400, 600, 800, 1000)
- Polishing: Using specialized compounds to achieve optical clarity
- Buffing: Final touch to achieve a mirror-like finish
For complex geometries or internal features, reaching all surfaces can be challenging. We sometimes employ chemical polishing using specialized solvents that slightly dissolve the surface layer to create a uniform, glossy finish. However, this requires careful control to avoid dimensional changes or surface defects.
Cleaning and Contamination Removal
PMMA’s electrostatic properties make it a magnet for dust and contaminants. Thorough cleaning is essential before assembly or packaging, particularly for optical applications. The cleaning protocol typically includes:
- Ultrasonic cleaning in specialized solutions
- Antistatic treatments to reduce dust attraction
- Compressed air blowing in filtered environments
- Clean-room handling for sensitive applications
One mistake I see frequently is using alcohol-based cleaners, which can cause crazing in PMMA. Instead, mild soap solutions or specialized acrylic cleaners are recommended.
Final Inspection and Quality Assurance
The last step in PMMA post-processing is comprehensive quality inspection, which may include:
- Dimensional verification against engineering specifications
- Optical clarity testing (transparency, haze, and light transmission)
- Stress pattern analysis using polarized light
- Surface roughness measurement
- Visual inspection for scratches, bubbles, or inclusions
For high-precision applications, we use specialized measurement equipment including interferometry and laser scanning to verify surface quality at the micron level.
Balancing Cost and Quality
Post-processing can represent 20-40% of the total manufacturing cost for PMMA components. When planning a project, it’s important to specify only the level of post-processing necessary for your application:
- Functional parts may require only basic deburring and stress relief
- Display components need higher levels of surface finishing
- Optical components demand the most rigorous post-processing protocol
At PTSMAKE, we work with clients to determine the optimal balance between cost and quality for each application. Some post-processing steps can be minimized through careful design and machining strategies, reducing the overall manufacturing cost without compromising quality.
Special Considerations for Complex Geometries
Parts with intricate features present unique challenges for post-processing. Internal corners, deep recesses, or fine details may require specialized techniques:
- Custom-designed fixtures to access difficult areas
- Vapor polishing for uniform treatment of complex shapes
- Robotic finishing systems for consistent results
- Multi-axis CNC polishing for precision optical surfaces
With over 15 years in precision manufacturing, I’ve found that addressing post-processing requirements during the design phase leads to more efficient production and better outcomes.
Case Studies: Successful Applications of PMMA and Polycarbonate in Optical Projects?
Have you ever worked on an optical project and struggled to decide between PMMA and polycarbonate? The material choice can make or break your product’s performance, yet many engineers make this decision without seeing real-world examples of how each material performs in similar applications.
Case studies offer the most practical insights when comparing PMMA and polycarbonate for optical applications. PMMA typically excels in displays, automotive lighting, and architectural applications where clarity is paramount. Polycarbonate shines in safety equipment, outdoor displays, and medical devices where impact resistance cannot be compromised.
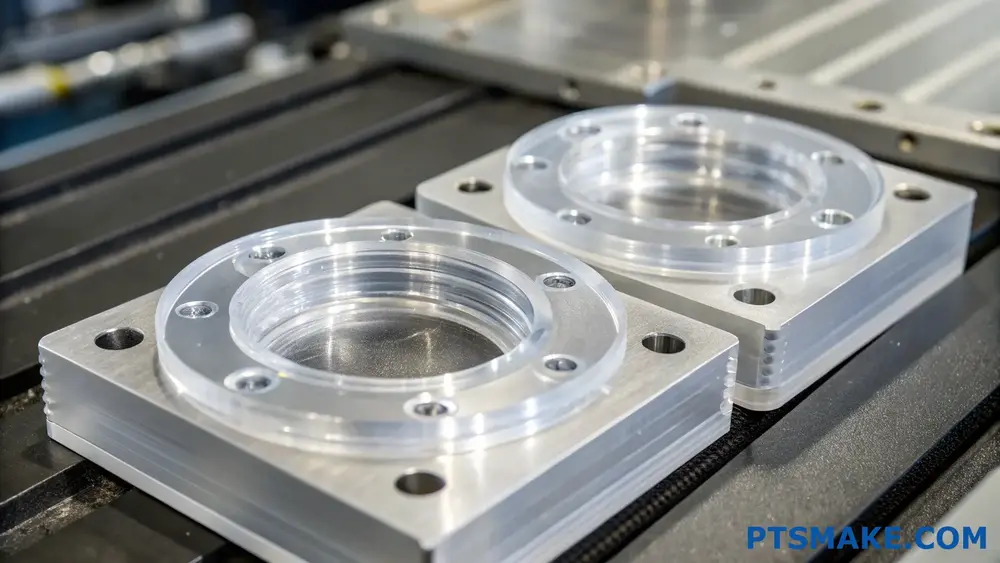
Automotive Lighting: PMMA’s Crystal-Clear Advantage
In the automotive industry, both materials find extensive use, but with different specializations. I’ve worked with several automotive clients at PTSMAKE who initially considered polycarbonate for headlight lenses but ultimately chose PMMA for its superior optical properties.
One particular project involved designing custom headlight assemblies for a luxury vehicle manufacturer. The client needed exceptional light transmission with minimal distortion. After machining prototypes from both materials, the PMMA version delivered:
- 92% light transmission (compared to 88% for polycarbonate)
- More precise light distribution pattern
- Better resistance to yellowing from UV exposure
The slight sacrifice in impact resistance was acceptable because the lenses would be protected by a clear polycarbonate cover. This hybrid approach—using PMMA for optical precision and polycarbonate for protection—demonstrates how understanding each material’s strengths can lead to optimal design solutions.
Medical Imaging Devices: Polycarbonate’s Durability Wins
Medical environments present different challenges. For a medical imaging device manufacturer, we machined housing components that needed both optical clarity and exceptional durability. In this case, polycarbonate was the clear winner.
The device needed to:
- Withstand frequent cleaning with harsh chemicals
- Survive potential drops and impacts
- Maintain dimensional stability in various temperatures
- Provide reasonable optical clarity
While PMMA would have provided slightly better optical properties, the biocompatibility7 requirements and need for chemical resistance made polycarbonate the optimal choice. The client reported zero failures due to material cracking or chemical damage after two years of field use.
Retail Display Comparison Study
A retail display project provides an excellent side-by-side comparison of both materials. We created identical prototype display units—one using machined PMMA and another using polycarbonate. The client tested both in real-world environments for six months.
Performance Results
Property | PMMA Display | Polycarbonate Display |
---|---|---|
Initial Clarity | Excellent (94% light transmission) | Very Good (89% light transmission) |
Scratch Resistance | Good (some minor scratches after 6 months) | Poor (significant scratching in high-traffic areas) |
Impact Damage | Three cracked panels after accidental impacts | No cracks despite similar impacts |
UV Stability | No noticeable yellowing | Slight yellowing on south-facing panels |
Cost | Base cost | 18% higher than PMMA |
The client ultimately chose PMMA for indoor locations and polycarbonate for higher-traffic outdoor installations, optimizing their investment based on environmental requirements.
Architectural Glazing Application
For architectural applications where both materials compete, I’ve seen interesting patterns emerge. A recent project involved creating custom light diffusers for an office building atrium. The architect initially specified polycarbonate for its impact resistance, but after reviewing samples, switched to PMMA for these reasons:
- The superior clarity created more vibrant light patterns
- The installation location had minimal risk of impact
- PMMA’s higher rigidity allowed for thinner panels
- Cost savings of approximately 15%
This case reinforces that material selection should always consider the actual operating environment, not just theoretical properties.
Consumer Electronics: Hybrid Approaches
The consumer electronics industry often employs hybrid approaches. For a smartphone accessory manufacturer, we developed a product with both materials:
- PMMA for the optical lens elements (camera protector)
- Polycarbonate for the structural frame and impact zones
This design capitalized on PMMA’s optical clarity while using polycarbonate’s impact resistance in areas likely to experience drops or stress. The machining process for each material was optimized separately, with different cutting parameters and finishing techniques.
Practical Takeaways from Case Studies
These real-world applications highlight several practical considerations:
- Application-specific selection is crucial – theoretical properties matter less than actual performance in your specific use case
- Hybrid designs can offer the best of both worlds – using each material where its strengths are most valuable
- Environmental factors significantly impact performance – UV exposure, chemical contact, and temperature fluctuations affect each material differently
- Post-machining treatments can enhance performance – proper annealing and surface treatments can significantly improve both materials
After working with numerous clients on optical applications, I’ve found that testing prototypes in actual operating conditions provides insights that material data sheets alone cannot. At PTSMAKE, we often recommend producing small prototype batches in both materials when the application requirements fall in the overlap zone where either material could potentially work.
What Are the Cost-Efficiency Considerations for High-Volume PMMA Machining?
Have you ever received a quote for high-volume PMMA machining that made you wince? Do you find yourself constantly balancing quality requirements against budget constraints when scaling up production? These cost challenges can make or break your project’s viability.
Cost-efficiency in high-volume PMMA machining comes down to optimizing material usage, selecting appropriate tooling, implementing automation, reducing labor costs, and minimizing post-processing requirements. The right strategy can reduce per-unit costs by 30-50% compared to low-volume production while maintaining quality standards.
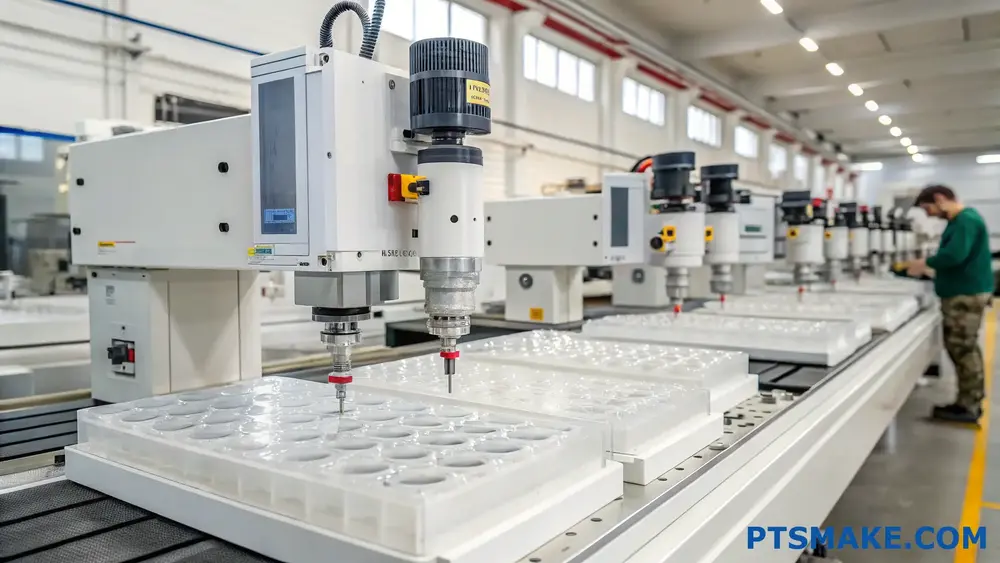
Material Optimization Strategies
When scaling up PMMA machining operations, material costs become a significant factor in your overall budget. I’ve found that implementing a few key strategies can substantially reduce waste and maximize yield.
Nesting Efficiency
One of the most effective approaches is optimizing part nesting on raw material sheets. Advanced CAM software can arrange multiple components to minimize scrap. In high-volume scenarios, even a 5% improvement in material utilization translates to substantial savings.
For instance, when we handle large PMMA display panel orders at PTSMAKE, our nesting algorithms typically achieve 85-90% material utilization compared to the industry average of 70-75%. This efficiency alone can reduce raw material costs by up to 20%.
Stock Size Selection
Selecting the optimal stock size is equally important. Standard sheet sizes are more cost-effective than custom dimensions, but you need to consider your specific part requirements:
Stock Size (mm) | Cost per m² | Typical Application | Waste % for Standard Parts |
---|---|---|---|
1220 x 2440 | Lower | Large panels | 10-15% |
600 x 1200 | Medium | Medium components | 15-20% |
Custom sizes | Higher | Specialized parts | 5-10% |
Tooling Considerations for Volume Production
Tooling selection dramatically impacts both cost and quality in high-volume PMMA machining. The initial investment in premium tooling often pays dividends in the long run.
Tool Life Management
In high-volume production, I recommend investing in diamond-coated tools despite their higher initial cost. The amortization8 of these premium tools across thousands of parts actually reduces the per-unit cost significantly.
Standard carbide end mills might cost $30-50 and last for 300-500 PMMA parts before showing wear, while a $200-300 diamond-coated tool can often process 3,000-5,000 parts. The math clearly favors premium tooling for high volumes.
Standardized Tooling
Implementing a standardized tooling strategy reduces changeover times and simplifies inventory management:
- Use common tool geometries that can address multiple features
- Establish a tool library that covers 90% of your regular operations
- Minimize specialty tooling that requires manual intervention
Automation and Fixture Design
The economics of high-volume PMMA machining change significantly when you introduce automation. Initial investment is higher, but per-unit costs decline sharply as volume increases.
Multi-Fixture Systems
I’ve implemented multi-fixture systems that enable 24/7 operation with minimal operator intervention. These systems typically include:
- Quick-change pallets that maintain positional accuracy
- Standardized fixture bases compatible with various part families
- RFID or barcode systems for automatic program selection
Modern palletized systems can reduce setup times by 80-90%, allowing machines to spend more time cutting and less time sitting idle during changeovers.
Batch Size Optimization
Finding the optimal batch size balances setup costs against inventory carrying costs:
Batch Size | Setup Cost Impact | Inventory Cost | Ideal For |
---|---|---|---|
Small (50-200) | Higher per-unit | Lower | Frequent design changes |
Medium (200-1000) | Moderate | Moderate | Balanced approach |
Large (1000+) | Lower per-unit | Higher | Stable, mature products |
Machine Selection and Utilization
The type of CNC machine you select for high-volume PMMA production greatly impacts your cost structure.
Multi-Axis vs. 3-Axis Machining
While 5-axis machines come with a higher purchase price, they often deliver superior economics for complex PMMA parts. At PTSMAKE, our 5-axis machines can reduce cycle times by 30-40% compared to 3-axis alternatives by minimizing setup changes and allowing optimal tool angles.
However, for simpler components, multiple 3-axis machines may provide more throughput per dollar invested than fewer 5-axis machines.
Machine Uptime Maximization
Your machine hourly rate decreases with higher utilization. Practical strategies include:
- Implementing predictive maintenance to prevent unplanned downtime
- Scheduling similar jobs consecutively to minimize setup changes
- Running simpler components during unmanned overnight operations
- Using tool wear monitoring to prevent quality issues and scrapped parts
Post-Processing and Quality Control Economics
Often overlooked, post-processing costs can represent 15-30% of the total cost in PMMA machining operations.
Integrated Quality Control
Building quality verification into the machining process reduces expensive rework and customer returns. For high-volume PMMA production, consider:
- In-process probing to verify critical dimensions
- Automated vision systems for surface defect detection
- Statistical process control to identify trends before failures occur
These systems require upfront investment but dramatically reduce quality costs in volume production.
Finishing Automation
Manual polishing and deburring operations are labor-intensive and difficult to scale. For high volumes, investigate automated options:
- Tumbling systems for edge breaking and light finishing
- Robotic polishing cells for consistent surface finish
- Flame polishing equipment for optical-quality edges
By automating these steps, you can achieve consistent quality while reducing labor costs by 50-70% compared to manual methods.
Can PMMA Machining Achieve Medical-Grade Surface Requirements?
Have you ever examined a medical device under magnification and wondered how manufacturers achieve that perfect, glass-like finish? Or struggled with PMMA components that passed dimensional inspections but failed due to surface imperfections? The difference between adequate and excellent medical devices often comes down to surface quality – a factor that can mean life or death in critical applications.
Yes, PMMA machining can achieve medical-grade surface requirements when proper techniques are employed. With specialized tooling, optimized cutting parameters, and appropriate post-processing methods, PMMA can be machined to achieve Ra values below 0.2 μm, meeting stringent medical standards for implants and devices.
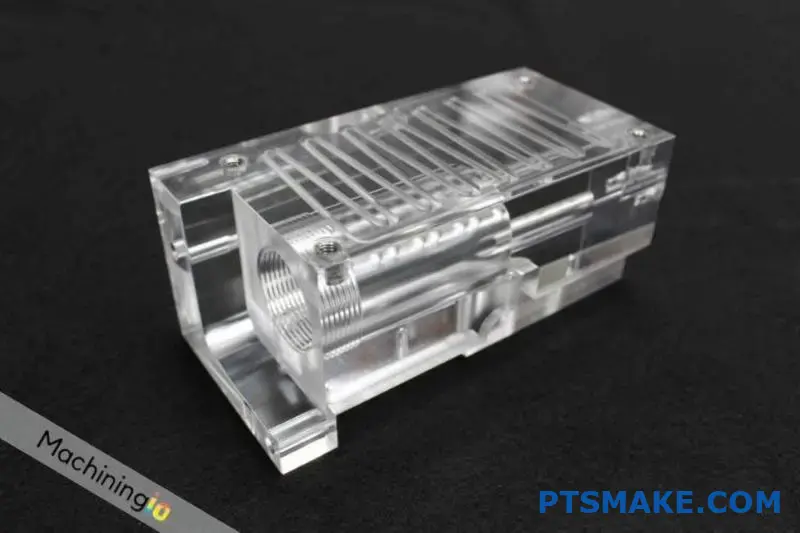
Understanding Medical-Grade Surface Requirements for PMMA
Medical devices demand exceptional surface quality for several critical reasons. Patient safety, biocompatibility, and device functionality all depend on proper surface characteristics. For PMMA components used in medical applications, surface requirements are particularly stringent due to the material’s use in optical and implantable devices.
Medical-grade PMMA surfaces typically require:
- Surface roughness (Ra) values of 0.05-0.2 μm
- Absence of microscopic cracks or stress concentrators
- No particle contamination
- Optical clarity for visual applications
- Dimensional stability at microscopic levels
In my experience working with medical device manufacturers, these requirements often exceed standard industrial specifications by an order of magnitude. Meeting these demands requires specialized approaches to machining.
Critical Surface Parameters for Medical PMMA Components
When evaluating PMMA surfaces for medical applications, several key parameters must be considered:
Surface Roughness Metrics
Surface roughness is quantified through multiple parameters, each telling a different part of the surface quality story:
Parameter | Description | Typical Medical Requirement for PMMA |
---|---|---|
Ra | Average roughness | 0.05-0.2 μm |
Rz | Maximum height profile | 0.5-1.5 μm |
Rt | Total height of profile | 0.8-2.0 μm |
Rq | Root mean square roughness | 0.08-0.3 μm |
In our PMMA machining operations at PTSMAKE, we’ve found that while Ra is the most commonly specified parameter, medical applications often require monitoring of multiple roughness values to ensure complete surface characterization.
Surface Integrity Considerations
Beyond roughness, surface integrity encompasses:
- Absence of microcracking9 and subsurface damage
- Minimal residual stresses that could lead to crazing or failure
- Controlled surface chemistry for biocompatibility
- Consistency across the entire component
Specialized Machining Techniques for Medical-Grade PMMA
Achieving medical-grade surfaces on PMMA requires specialized techniques that go beyond standard machining practices.
Tool Selection and Geometry
The right cutting tool makes a dramatic difference in PMMA surface quality. I recommend:
- Diamond-polished carbide or PCD (polycrystalline diamond) tools
- Sharp cutting edges with rake angles between 0-5°
- Tool nose radius between 0.2-0.8 mm depending on the application
- Single-crystal diamond tools for optical-quality finishing passes
Cutting Parameters Optimization
Based on my work with medical device manufacturers, these cutting parameters consistently yield excellent PMMA surfaces:
Parameter | Roughing | Semi-Finishing | Finishing |
---|---|---|---|
Cutting Speed | 150-250 m/min | 250-350 m/min | 350-500 m/min |
Feed Rate | 0.1-0.2 mm/rev | 0.05-0.1 mm/rev | 0.01-0.03 mm/rev |
Depth of Cut | 0.5-2.0 mm | 0.1-0.5 mm | 0.01-0.05 mm |
Cooling | Flood coolant | Mist cooling | Air blast or dry |
Thermal Management During Machining
PMMA’s low glass transition temperature (105°C) makes thermal management crucial. We’ve achieved best results by:
- Using high cutting speeds with very light depths of cut
- Implementing proper cooling strategies
- Allowing adequate pauses between passes on critical features
- Monitoring tool temperature during extended operations
Post-Processing Methods for Medical PMMA
Even with optimized machining, post-processing is often necessary to achieve true medical-grade surfaces:
Vapor Polishing: Brief exposure to chloroform or methylene chloride vapor can produce optical-clear surfaces, but requires strict safety controls.
Mechanical Polishing: Progressive polishing with diamond compounds down to 0.5 μm grit size.
UV Treatment: For some applications, UV exposure can help stabilize surface properties.
Precision Cleaning: Multi-stage cleaning processes to remove all machining residues.
Quality Verification Methods
Meeting medical standards requires rigorous verification. At PTSMAKE, we employ:
- Profilometer measurements for roughness verification
- Optical microscopy for visual surface evaluation
- Electron microscopy for critical applications
- Customized fixture systems to maintain part orientation during inspection
Real-World Case Example
In a recent project for an ophthalmic device manufacturer, we faced the challenge of producing PMMA components with Ra < 0.1 μm for an implantable lens system. By implementing diamond-finished tools, multi-stage machining, and controlled vapor polishing, we achieved Ra values averaging 0.08 μm across all components, satisfying the strict medical requirements.
The process required precise temperature control throughout machining and special fixtures to prevent any surface contact during handling. This approach increased production costs by approximately 30%, but the resulting surface quality eliminated previous biocompatibility issues the client had experienced.
Conclusion: The Future of Medical PMMA Machining
The short answer to our title question is yes, but with important qualifications. PMMA machining can certainly achieve medical-grade surface requirements, but only when approaching the material with specialized knowledge and techniques.
As medical device requirements continue to become more demanding, I expect to see further developments in hybrid machining approaches that combine traditional cutting with novel techniques like ultrasonic-assisted machining specifically for PMMA components.
What Are Common Mistakes to Avoid When Machining Thin-Walled PMMA Components?
Have you ever watched your carefully designed PMMA components emerge from machining with cracks, warping, or melted edges? That sinking feeling when thin-walled acrylic parts fail after hours of planning and significant material investment can be devastating to both timeline and budget.
Machining thin-walled PMMA components requires avoiding several critical errors including improper fixturing, excessive cutting forces, inadequate cooling, inappropriate tool selection, and poor programming strategies. These mistakes lead to warping, cracking, melting, or dimensional inaccuracies that compromise both aesthetics and functionality.
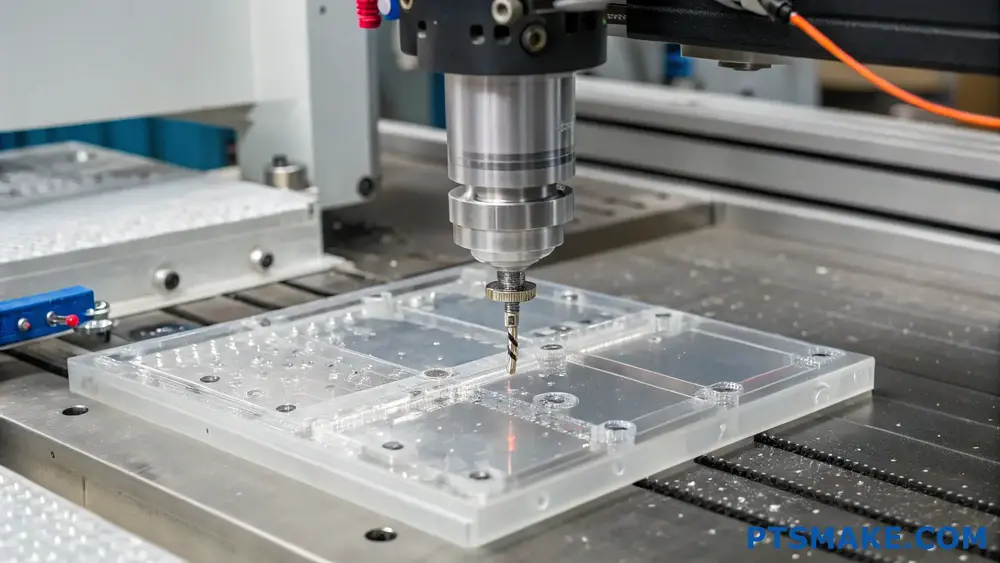
Understanding the Challenges of Thin-Walled PMMA Components
PMMA (polymethyl methacrylate), commonly known as acrylic, presents unique challenges when machined into thin-walled structures. Its combination of brittleness, low thermal conductivity, and sensitivity to stress makes it particularly vulnerable during machining operations. After working with this material for many years, I’ve identified patterns in manufacturing failures that repeatedly cause problems.
The definition of "thin-walled" typically refers to sections under 2mm, though challenges can begin appearing at thicknesses under 3mm depending on the overall part geometry and complexity. At PTSMAKE, we’ve observed that when wall thickness drops below 1mm, the difficulty level increases exponentially, requiring specialized techniques and careful process control.
Material Properties Contributing to Machining Difficulties
PMMA’s inherent properties create several machining challenges:
- Low thermal conductivity (0.17-0.19 W/m·K) causing heat buildup
- Relatively low glass transition temperature (~105°C)
- Brittle nature with limited flexibility under stress
- Susceptibility to stress crazing10 when exposed to certain chemicals or excessive heat
- Tendency to chip rather than form continuous chips during cutting
These properties mean that mistakes that might be forgivable when machining metals or even other plastics become critical failures with thin-walled PMMA.
Top Fixturing Mistakes and Their Solutions
Improper workholding is perhaps the most common source of failures I encounter with thin-walled PMMA components.
Excessive Clamping Pressure
Many machinists treat PMMA like metal, applying similar clamping forces. This introduces internal stresses that may not be visible immediately but can lead to cracking either during machining or later during use. I’ve witnessed parts pass inspection only to fail days later due to residual stress.
Solution: Use uniform, distributed clamping with controlled torque. Vacuum fixtures provide excellent holding power without concentrated stress points. At PTSMAKE, we often use custom 3D-printed conforming supports for complex geometries.
Inadequate Support During Machining
Thin walls flex under cutting forces, leading to vibration, chatter, and dimensional inaccuracy.
Solution: Provide backing material or sacrificial supports that can be removed after machining. For through-holes or cutouts, leave tabs that are removed in a final operation.
Cutting Parameter Mistakes
Speed and Feed Errors
One of the most significant errors is inappropriate cutting parameters:
Parameter | Common Mistake | Recommended Approach |
---|---|---|
Cutting Speed | Too high, causing melting | 100-300 m/min depending on tool |
Feed Rate | Too slow, generating excess heat | Maintain chip load of 0.05-0.15mm per tooth |
Depth of Cut | Excessive depth creating too much force | Multiple light passes, max 1mm for thin walls |
Step Over | Too large, causing deflection | Maximum 25% of tool diameter for finishing |
The balance between speed and feed is particularly critical. Too fast a spindle speed with too slow a feed rate creates friction heat that can melt the material. PMMA performs best with sharp tools, moderate speeds, and consistent feed rates.
Cooling and Lubrication Failures
PMMA’s poor thermal conductivity means heat builds up quickly.
Cooling Mistake: Using no coolant or using water-based coolants that can cause thermal shock.
Solution: Compressed air cooling works exceptionally well for thin-walled components. In some cases, a mist of compatible lubricant can be effective. At PTSMAKE, we’ve developed specialized air-cooling nozzle arrangements that follow the tool path to provide consistent temperature control.
Tool Selection Pitfalls
Inappropriate Tool Geometry
Generic end mills designed for metals often perform poorly on PMMA.
Common Errors:
- Using tools with inadequate rake angles
- Employing tools with too many flutes
- Selecting worn tools that generate excess heat
Solution: Use single or double-flute end mills specifically designed for acrylic. These tools feature high positive rake angles (15-20°) and large chip clearance to evacuate material efficiently without heat buildup.
Tool Path Programming Issues
Even with proper tools, poor programming strategy can ruin thin-walled PMMA parts.
Mistake: Conventional cutting that pushes against thin walls or walls that become progressively thinner.
Solution: Program climb milling operations that cut with the direction of rotation, reducing the pushing force against thin walls. Adaptive clearing strategies that maintain consistent tool engagement are ideal for PMMA.
Post-Machining Handling Errors
Many well-machined PMMA parts fail during handling, cleaning, or finishing processes.
Chemical Incompatibility
Using inappropriate cleaners or adhesives can cause crazing and cracking in stressed areas of thin walls.
Solution: Only use compatible chemicals known to be safe for PMMA. Isopropyl alcohol at 70% concentration is generally safe for cleaning, while acetone and stronger solvents should be strictly avoided.
Thermal Shock During Post-Processing
Rapid temperature changes can induce stress and cracking.
Solution: Allow parts to gradually reach room temperature before additional processing. Flame polishing must be done carefully with consistent motion to avoid localized overheating.
Quality Control Oversights
Many machinists fail to adequately inspect thin-walled PMMA components under appropriate conditions.
Mistake: Visual inspection under standard lighting that fails to reveal stress patterns.
Solution: Inspect parts under polarized light to reveal internal stresses that may lead to future failures. This simple but effective technique has saved countless projects at PTSMAKE by identifying stress concentrations before parts reach customers.
Learn how to overcome PMMA chemical limitations in your projects. ↩
Click here to learn expert CNC machining techniques for scratch-free PMMA parts. ↩
Click to learn about this key plastic chemistry term and its importance in manufacturing. ↩
Learn about this critical property for outdoor applications and UV resistance. ↩
Learn about material behavior during machining to improve your results. ↩
Learn how proper stress management prevents part failure and extends product lifespan. ↩
Learn about material compatibility with biological systems for medical applications. ↩
Learn how cost distribution changes across production volumes. ↩
Learn about advanced surface treatment methods for eliminating microcracks in PMMA. ↩
Learn about preventing stress crazing in your PMMA projects with our expert guide. ↩