Está a ter dificuldades em encontrar o material certo para aplicações exigentes em que os plásticos normais falham? Muitos engenheiros enfrentam desafios quando os componentes têm de suportar temperaturas extremas, produtos químicos ou tensões mecânicas. Os plásticos tradicionais simplesmente não aguentam, levando a falhas frequentes nas peças e a substituições dispendiosas.
A maquinagem PEEK é o processo de corte, perfuração e moldagem de material de poliéter-éter-cetona (PEEK) utilizando máquinas CNC. Este termoplástico de elevado desempenho oferece uma resistência excecional ao calor até 480°F, uma excelente resistência química e uma força comparável à de alguns metais.
Já trabalhei com inúmeros clientes que mudaram para a maquinagem PEEK para os seus componentes críticos. Os resultados falam por si - peças mais duradouras, melhor desempenho em ambientes agressivos e ciclos de manutenção reduzidos. Se está a pensar se o PEEK poderá ser a solução para a sua aplicação, continue a ler para descobrir as propriedades únicas e as técnicas de maquinação que tornam este material tão valioso no fabrico de precisão.
O PEEK é melhor do que o Delrin para maquinagem?
Já alguma vez foi apanhado no meio de um dilema de seleção de material, dividido entre PEEK e Delrin para o seu projeto de engenharia crítico? Quando o desempenho é importante e o fracasso não é uma opção, escolher o plástico errado pode levar a um desgaste prematuro, tempo de inatividade do equipamento e redesenhos dispendiosos.
Enquanto o PEEK oferece uma resistência superior à temperatura (até 480°F), uma estabilidade química excecional e uma maior resistência, o Delrin (POM) oferece uma melhor maquinabilidade, estabilidade dimensional e um custo mais baixo. A "melhor" escolha depende inteiramente dos requisitos específicos da sua aplicação e das restrições orçamentais.
Compreender o PEEK e o Delrin: Diferenças fundamentais
Ao comparar estes dois plásticos de engenharia de elevado desempenho, é importante compreender a sua composição e caraterísticas básicas. O PEEK (poliéter-éter-cetona) é um termoplástico semi-cristalino com uma resistência excecional à degradação térmica, enquanto o Delrin (polioximetileno ou POM) é um homopolímero de acetal conhecido pela sua excelente estabilidade dimensional.
Comparação das propriedades dos materiais
As propriedades físicas e mecânicas destes materiais têm um impacto significativo nas suas caraterísticas de maquinagem e no desempenho da utilização final.
Imóveis | PEEK | Delrin (POM) |
---|---|---|
Temperatura de deflexão térmica | 315°F (157°C) | 125°C (257°F) |
Resistência à tração | 14.500 psi | 10.000 psi |
Resistência química | Excelente (resiste à maioria dos ácidos e bases) | Bom (vulnerável a ácidos fortes) |
Resistência ao desgaste | Superior | Muito bom |
Fator de custo | 4-5× superior ao Delrin | Moderado |
Densidade | 1,32 g/cm³ | 1,41 g/cm³ |
Caraterísticas de maquinagem: Como se comportam sob a ferramenta
Na minha experiência no PTSMAKE, descobri que a maquinabilidade é frequentemente o fator decisivo na escolha entre estes materiais. O Delrin é geralmente mais fácil de maquinar do que o PEEK, produzindo acabamentos de superfície mais suaves com menos esforço.
Desgaste da ferramenta e parâmetros de corte
O PEEK é mais abrasivo para as ferramentas de corte, exigindo mudanças de ferramenta mais frequentes. Ao maquinar PEEK, normalmente reduzimos as velocidades de corte em cerca de 15-20% em comparação com Delrin para minimizar a acumulação de calor. Isto é crucial porque a baixa condutividade térmica do PEEK provoca uma concentração de calor na zona de corte, causando potencialmente deformação térmica1 se não for corretamente gerido.
O Delrin, por outro lado, oferece uma excelente estabilidade dimensional durante a maquinagem e pode ser cortado a velocidades mais elevadas. Produz menos desgaste da ferramenta e geralmente requer menos técnicas de maquinação especializadas.
Considerações sobre o acabamento da superfície
Uma vantagem do Delrin é a sua capacidade de obter excelentes acabamentos de superfície com parâmetros de maquinação padrão. O PEEK requer frequentemente passos de polimento adicionais para atingir uma qualidade de superfície comparável.
Análise custo-benefício para aplicações de engenharia
A diferença de custo entre estes materiais pode ser substancial. O PEEK custa normalmente 4 a 5 vezes mais do que o Delrin, pelo que é importante avaliar se as suas propriedades premium justificam o investimento.
Quando o PEEK justifica o seu preço superior
Recomendo o PEEK para aplicações que envolvam:
- Temperaturas de funcionamento extremas (acima de 250°F)
- Ambientes químicos agressivos
- Elevada carga mecânica em temperaturas elevadas
- Aplicações médicas ou aeroespaciais que exigem biocompatibilidade ou resistência à chama
Quando o Delrin é a melhor escolha
A Delrin é mais económica quando:
- As temperaturas de funcionamento mantêm-se abaixo dos 180°F
- A exposição química é limitada a solventes moderados
- A sensibilidade aos custos é um fator importante
- As peças requerem uma excelente estabilidade dimensional e precisão de maquinação
- Os elevados volumes de produção fazem do custo dos materiais um fator significativo
Considerações específicas do sector
Diferentes indústrias dão prioridade a diferentes propriedades dos materiais. No sector aeroespacial, onde fornecemos inúmeros componentes, a resistência à chama do PEEK e a excecional relação resistência/peso justificam frequentemente o seu custo mais elevado. Para aplicações no sector automóvel, a combinação do custo razoável e das boas propriedades mecânicas do Delrin é muitas vezes a melhor opção.
Aplicações médicas e de processamento de alimentos
Para dispositivos médicos, a biocompatibilidade do PEEK e a sua resistência à esterilização tornam-no inestimável, apesar do seu custo acrescido. No equipamento de processamento de alimentos, a conformidade do Delrin com a FDA e o seu custo mais baixo tornam-no frequentemente a escolha preferida, a menos que estejam envolvidas temperaturas elevadas.
Componentes de máquinas industriais
Em aplicações industriais, tenho visto que a decisão se resume frequentemente às condições de funcionamento. As engrenagens, os rolamentos e os componentes de desgaste que funcionam em condições moderadas têm um excelente desempenho em Delrin, enquanto os que estão expostos a condições extremas beneficiam das propriedades superiores do PEEK.
Fazer a escolha certa para a sua aplicação
A decisão entre PEEK e Delrin deve ser orientada por uma análise minuciosa das suas condições de funcionamento específicas. No PTSMAKE, consideramos:
- Temperatura máxima de funcionamento
- Perfil de exposição química
- Requisitos de carga mecânica
- Restrições orçamentais
- Expectativas de vida útil
Ao avaliar cuidadosamente estes factores em relação às propriedades de cada material, pode tomar uma decisão informada que equilibre o desempenho e a relação custo-eficácia para a sua aplicação específica.
Qual é a diferença entre acetal e PEEK?
Alguma vez teve dificuldade em escolher entre acetal e PEEK para os seus componentes críticos de engenharia? Quando o sucesso de um projeto depende da seleção do material, a escolha errada pode levar a falhas prematuras, tempo de inatividade inesperado e redesenhos que esmagam o orçamento, que poderiam ter sido evitados com o conhecimento adequado do material.
O acetal (POM) e o PEEK diferem principalmente nas suas caraterísticas de desempenho e custo. O PEEK oferece uma resistência superior ao calor (480°F vs 180°F), melhor resistência química e maior resistência, enquanto o acetal oferece uma excelente maquinabilidade, estabilidade dimensional e custa significativamente menos, o que o torna ideal para aplicações menos exigentes.
Principais diferenças entre o acetal e o PEEK
Compreender as diferenças fundamentais entre estes dois plásticos de engenharia é crucial para tomar decisões informadas para os seus projectos. Ambos os materiais estabeleceram-se como opções de eleição no fabrico de precisão, mas servem propósitos distintamente diferentes com base nas suas propriedades inerentes.
Composição e estrutura do material
O acetal, vulgarmente conhecido pelo nome comercial Delrin (quando em forma de homopolímero) ou pelo seu nome químico polioximetileno (POM), apresenta uma estrutura altamente cristalina com grupos -CH₂O- repetidos. Esta estrutura confere-lhe uma excelente estabilidade dimensional e maquinabilidade.
O PEEK (poliéter-éter-cetona), por outro lado, pertence à família das poliariletercetonas e contém anéis aromáticos ligados por ligações de éter e cetona. Esta estrutura molecular cria uma estabilidade térmica e uma resistência química excepcionais.
Comparação das caraterísticas de desempenho
As diferenças de desempenho entre estes materiais tornam-nos adequados para aplicações distintas:
Imóveis | Acetal (POM) | PEEK | Melhor para |
---|---|---|---|
Resistência ao calor | 180°F (82°C) contínuo | 480°F (250°C) contínuo | PEEK |
Resistência química | Bom (exceto ácidos fortes) | Excelente (resistente à maioria dos produtos químicos) | PEEK |
Resistência à tração | 8.800-10.000 psi | 14.500-16.000 psi | PEEK |
Resistência ao desgaste | Muito bom | Excelente | PEEK |
Maquinabilidade | Excelente | Bom (requer técnicas especializadas) | Acetal |
Fator de custo | Referência de base (1×) | 4-7× superior ao acetal | Acetal |
Absorção de humidade | 0.2-0.25% | 0.1-0.15% | PEEK |
Análise custo-benefício
Ao longo dos meus anos de trabalho com clientes no PTSMAKE, reparei que as considerações de custo orientam frequentemente o processo inicial de seleção do material. O acetal é significativamente mais económico do que o PEEK, o que o torna a escolha padrão quando não estão presentes condições extremas.
O preço superior do PEEK reflecte as suas capacidades de desempenho superiores. Ao avaliar se o investimento adicional se justifica, considere os seguintes factores:
- Requisitos de temperatura de funcionamento
- Perfil de exposição química
- Níveis de tensão mecânica
- Vida útil prevista
- Custos de inatividade associados a falhas de componentes
Considerações sobre maquinagem
Vida útil da ferramenta e parâmetros de corte
O acetal é conhecido pela sua excecional maquinabilidade. Corta de forma limpa, mantém tolerâncias apertadas e produz excelentes acabamentos de superfície com um esforço mínimo. As ferramentas de metal duro padrão funcionam bem e o material não causa desgaste excessivo da ferramenta.
O PEEK apresenta mais desafios durante a maquinagem. A sua elevada resistência à temperatura significa que a dissipação de calor durante a maquinagem é fraca, exigindo..:
- Velocidades de corte reduzidas (normalmente 20-30% mais lentas do que as do acetal)
- Mudanças de ferramentas mais frequentes
- Atenção especial à acumulação de calor
- Técnicas de arrefecimento especializadas
No PTSMAKE, desenvolvemos protocolos de gestão térmica2 para a maquinagem PEEK, para garantir a precisão dimensional e evitar a degradação do material durante o processo de corte.
Estabilidade dimensional
O acetal oferece uma excelente estabilidade dimensional após a maquinagem, com um mínimo de empeno ou relaxamento de tensões. Isto torna-o particularmente valioso para componentes de precisão com tolerâncias apertadas.
O PEEK também apresenta uma boa estabilidade dimensional, mas requer processos de recozimento mais cuidadosos para aliviar as tensões internas após a maquinagem. Sem um condicionamento térmico adequado, as peças de PEEK podem sofrer ligeiras alterações dimensionais ao longo do tempo, especialmente em aplicações de alta precisão.
Recomendações específicas da aplicação
Automóvel e transportes
Nas aplicações automóveis em que as temperaturas permanecem moderadas (inferiores a 180°F), o acetal oferece frequentemente o melhor valor. As aplicações mais comuns incluem:
- Componentes do sistema de combustível
- Mecanismos de fecho de portas
- Clipes e fixadores de acabamento interior
- Superfícies de rolamento em áreas não críticas
Para zonas de temperatura mais elevada, como componentes sob o capô ou peças próximas de sistemas de escape, a estabilidade térmica do PEEK torna-o a melhor escolha, apesar do custo mais elevado.
Médico e farmacêutico
A indústria médica adoptou o PEEK pela sua biocompatibilidade e resistência aos métodos de esterilização. É normalmente utilizado em:
- Dispositivos implantáveis
- Instrumentos cirúrgicos
- Componentes de imagiologia médica
- Equipamento de laboratório
O acetal ainda encontra aplicações em ambientes médicos menos exigentes, tais como:
- Componentes de instrumentos descartáveis
- Dispositivos de teste de laboratório
- Caixas de equipamentos de diagnóstico
Equipamento industrial
Para as máquinas industriais, a escolha depende frequentemente das condições de funcionamento:
- Ambientes de funcionamento normais: O acetal oferece um excelente valor para engrenagens, rolamentos e superfícies de desgaste em condições normais.
- Ambientes agressivos: O PEEK justifica o seu preço superior quando exposto a temperaturas elevadas, produtos químicos ou tensões mecânicas extremas.
Fazer a seleção ideal
Ao ajudar os clientes a escolher entre acetal e PEEK no PTSMAKE, recomendo uma abordagem sistemática:
- Identificar as condições mais exigentes que a peça irá enfrentar (temperatura, produtos químicos, cargas)
- Determinar se as propriedades do acetal são suficientes para lidar com estas condições
- Calcular a diferença de custo entre as opções para as suas necessidades específicas de volume
- Considerar as consequências de uma falha e os custos de inatividade associados
- Avaliar se o desempenho superior do PEEK justifica o seu preço mais elevado
Lembre-se que a seleção de materiais raramente é única. Por vezes, uma abordagem híbrida funciona melhor, utilizando PEEK apenas para os componentes mais críticos e acetal para peças menos exigentes dentro do mesmo conjunto.
Qual é a diferença entre PTFE e PEEK?
Já alguma vez se viu perdido no mar de plásticos de alto desempenho, sem saber se devia escolher PTFE ou PEEK para a sua aplicação crítica? Quando os prazos do projeto se aproximam e a seleção do material pode ser decisiva para o seu projeto, a pressão para fazer a escolha certa pode ser esmagadora, especialmente quando ambos os materiais apresentam especificações técnicas impressionantes.
O PTFE e o PEEK são ambos termoplásticos de alto desempenho com diferenças distintas. O PTFE oferece uma resistência química incomparável, uma fricção extremamente baixa (coeficiente 0,05-0,10) e funciona entre -328°F e 500°F, mas tem uma fraca resistência mecânica. O PEEK oferece propriedades mecânicas superiores, excelente resistência ao desgaste e mantém a integridade estrutural até 480°F, sendo mais maquinável.
Estrutura molecular e propriedades básicas
As diferenças fundamentais entre o PTFE e o PEEK começam ao nível molecular, o que explica as suas caraterísticas de desempenho distintas em várias aplicações.
Composição química
O PTFE (politetrafluoroetileno) tem uma estrutura de carbono completamente rodeada por átomos de flúor. Esta estrutura única confere ao PTFE a sua excecional inércia química e propriedades de baixa fricção. As ligações carbono-flúor estão entre as mais fortes da química orgânica, tornando o PTFE incrivelmente resistente ao ataque químico.
O PEEK (poliéter-éter-cetona), por sua vez, tem uma estrutura molecular mais complexa com anéis aromáticos ligados por ligações de éter e cetona. Esta espinha dorsal aromática confere ao PEEK a sua excelente resistência mecânica e estabilidade térmica.
Análise comparativa de imóveis
Imóveis | PTFE | PEEK | Vantagem |
---|---|---|---|
Temperatura máxima de utilização contínua | 260°C (500°F) | 480°F (250°C) | PTFE (ligeiramente) |
Temperatura mínima de funcionamento | -328°F (-200°C) | -65°F (-54°C) | PTFE |
Coeficiente de fricção | 0,05-0,10 (o mais baixo de todos os sólidos) | 0.35-0.40 | PTFE |
Resistência à tração | 3.000-5.000 psi | 14.000-16.000 psi | PEEK |
Resistência química | Superior (universal) | Excelente (limitado por ácidos fortes) | PTFE |
Maquinabilidade | Desafiante (mole, deforma-se facilmente) | Bom | PEEK |
Resistência ao desgaste | Fraco a moderado | Excelente | PEEK |
Propriedades eléctricas | Excelente isolante | Bom isolante | PTFE |
Fator de custo | Moderado | Elevado (3-4× mais do que o PTFE) | PTFE |
Diferenças de desempenho térmico
O desempenho em termos de temperatura é frequentemente um fator de decisão crítico na seleção entre estes materiais.
Resistência ao calor e estabilidade
Embora ambos os materiais ofereçam uma resistência excecional ao calor, comportam-se de forma diferente a temperaturas elevadas. O PTFE mantém a sua inércia química e baixa fricção até à sua temperatura máxima, mas começa a perder integridade mecânica a temperaturas muito mais baixas (cerca de 260°F/127°C).
O PEEK, por sua vez, mantém a sua resistência mecânica muito mais próxima da sua temperatura máxima. Este facto torna o PEEK significativamente mais valioso em aplicações que requerem tanto resistência ao calor como carga mecânica.
Já vi inúmeras aplicações em que os clientes selecionaram inicialmente o PTFE com base apenas nas classificações de temperatura, apenas para descobrir que o material não conseguia suportar as tensões mecânicas a essas temperaturas. A capacidade do PEEK para manter a integridade estrutural a altas temperaturas faz com que, muitas vezes, valha a pena o preço mais elevado.
Desempenho em temperaturas frias
Para aplicações criogénicas, o PTFE tem uma vantagem distinta. Mantém-se flexível e funcional até -328°F (-200°C), enquanto o PEEK se torna cada vez mais frágil abaixo de -65°F (-54°C). Isto faz do PTFE a escolha óbvia para a indústria aeroespacial, laboratórios e outros ambientes de temperatura ultrabaixa.
Comparação da resistência mecânica
As propriedades mecânicas destes materiais diferem drasticamente, tornando a sua adequação específica para cada aplicação.
Integridade estrutural sob carga
O PEEK oferece um desempenho mecânico muito superior com uma resistência à tração média de 14.000-16.000 psi em comparação com os modestos 3.000-5.000 psi do PTFE. Este facto torna o PEEK adequado para aplicações de suporte de carga em que o PTFE se deformaria ou falharia rapidamente.
Na PTSMAKE, recomendamos frequentemente o PEEK para componentes estruturais que sofrem cargas mecânicas consistentes, especialmente a temperaturas elevadas. A excecional resistência à deformação do material permite-lhe manter a estabilidade dimensional sob tensão contínua.
Resistência ao desgaste e à fricção
O coeficiente de atrito extremamente baixo do PTFE (0,05-0,10) torna-o o material de eleição para aplicações que requerem um atrito mínimo. No entanto, esta mesma propriedade contribui para a sua fraca resistência ao desgaste, uma vez que o material pode ser facilmente raspado em cenários de elevado desgaste.
O PEEK apresenta uma excelente resistência ao desgaste, mantendo um coeficiente de fricção razoável (0,35-0,40). Para aplicações que envolvam movimentos contínuos contra outras superfícies, o PEEK normalmente supera o PTFE por uma margem considerável.
Muitos dos nossos clientes conseguem o melhor dos dois mundos utilizando o PEEK como material estrutural com um revestimento ou forro fino de PTFE onde é necessária uma redução da fricção.
Perfis de resistência química
Ambos os materiais oferecem uma resistência química excecional, mas com distinções importantes.
Resistência a ambientes agressivos
O PTFE representa o padrão de ouro para a resistência química, sendo praticamente inerte a quase todos os produtos químicos (com raras excepções, como metais alcalinos fundidos e flúor elementar). Esta resistência química universal torna o PTFE inestimável no processamento químico, no fabrico de semicondutores e em ambientes laboratoriais.
O PEEK oferece uma excelente resistência química à maioria das substâncias, mas pode ser atacado por ácido sulfúrico concentrado e alguns outros ácidos fortes. No entanto, para a maioria dos ambientes industriais, a resistência química do PEEK é mais do que adequada.
Hidrólise e absorção de humidade
O PTFE é completamente hidrofóbico e não absorve essencialmente qualquer humidade, mesmo após exposição prolongada. O PEEK, embora altamente resistente à hidrólise, absorve uma pequena quantidade de humidade (0,1-0,3%) quando exposto a ambientes húmidos durante longos períodos.
Para aplicações de água ultrapura ou sistemas em que mesmo uma contaminação mínima é inaceitável, o PTFE continua a ser frequentemente a escolha preferida, apesar das suas limitações mecânicas.
%[Componentes maquinados em PEEK e PTFE para comparação estrutural](
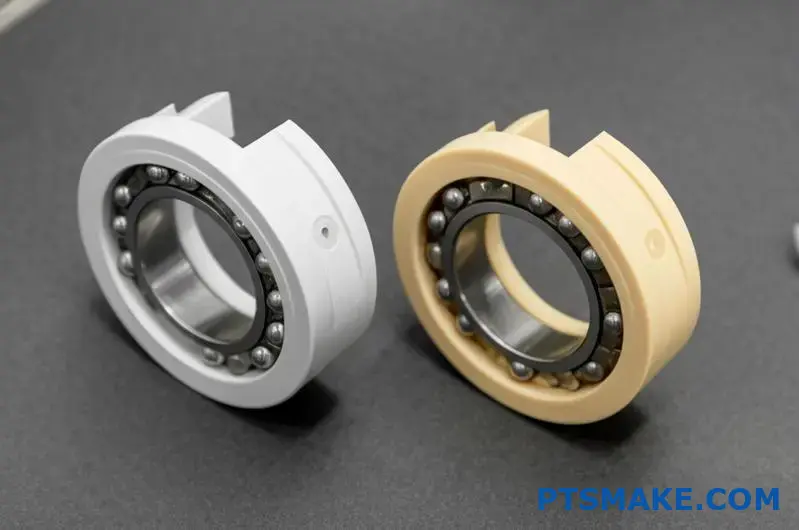
"Componentes de rolamentos PEEK e PTFE")
Considerações sobre maquinagem e fabrico
O maquinabilidade3 as diferenças entre estes materiais têm um impacto significativo nos custos e nas capacidades de fabrico.
Desafios e soluções de maquinagem
O PTFE apresenta desafios de maquinação únicos devido à sua suavidade e tendência para fluir a frio. Requer ferramentas especializadas, velocidades de corte mais lentas e uma fixação cuidadosa para evitar a deformação durante a maquinagem. As ferramentas afiadas são essenciais para evitar rasgar ou deformar o material.
O PEEK maquina mais como os plásticos de engenharia tradicionais, embora a sua natureza abrasiva cause um desgaste mais rápido da ferramenta do que muitos outros materiais. Ao maquinar PEEK, utilizamos normalmente ferramentas de metal duro e técnicas de arrefecimento adequadas para gerir a acumulação de calor.
Compatibilidade do processo de fabrico
A elevada viscosidade de fusão do PTFE impossibilita a moldagem por injeção convencional. Em vez disso, tem de ser processado através de técnicas como a moldagem por compressão, a extrusão por cilindros ou a desbaste de biletes. Isto limita a complexidade do design e aumenta os custos de fabrico de formas complexas.
O PEEK pode ser processado através de métodos convencionais como a moldagem por injeção e a extrusão, permitindo geometrias mais complexas e custos de produção potencialmente mais baixos em volumes mais elevados. Esta versatilidade de processamento confere ao PEEK uma vantagem para componentes complexos ou aquando da transição da prototipagem para a produção em massa.
Análise custo-benefício para diferentes aplicações
A diferença significativa de preço entre estes materiais exige uma análise cuidadosa do seu valor específico para a aplicação.
Comparação da proposta de valor
Embora o PEEK custe normalmente 3-4 vezes mais do que o PTFE, as suas propriedades mecânicas superiores e a sua resistência ao desgaste proporcionam frequentemente um melhor valor a longo prazo em aplicações em que uma falha mecânica seria dispendiosa ou perigosa.
Para aplicações que requerem principalmente resistência química, baixa fricção ou propriedades de isolamento elétrico sem tensão mecânica significativa, o PTFE oferece normalmente um melhor valor, apesar das suas limitações.
Critérios de seleção específicos do sector
Diferentes indústrias dão prioridade a diferentes propriedades dos materiais:
- Processamento químico: A resistência química universal do PTFE ultrapassa normalmente as suas limitações mecânicas.
- Indústria aeroespacial: Ambos os materiais têm aplicações, sendo o PEEK utilizado para componentes estruturais e o PTFE para vedantes e isolamento elétrico.
- Aplicações médicas: A biocompatibilidade e a resistência estrutural do PEEK tornam-no popular para implantes, enquanto o PTFE é preferido para revestimentos de cateteres e outras aplicações de baixa fricção.
- Semicondutores: O PTFE domina devido à sua excecional pureza e resistência a produtos químicos agressivos.
- Setor automóvel: A resistência ao desgaste e as propriedades mecânicas do PEEK tornam-no valioso para componentes sob o capô que enfrentam tensões mecânicas.
Qual é a diferença entre PVDF e PEEK?
Já alguma vez se deparou com o dilema de escolher entre PVDF e PEEK para um projeto crítico em que a seleção do material pode ser decisiva para a sua conceção? Quando os plásticos normais não são suficientes e necessita de uma resistência química ou estabilidade térmica excepcionais, a confusão entre estes dois materiais de elevado desempenho pode levar a erros dispendiosos ou a um desempenho comprometido.
O PVDF (fluoreto de polivinilideno) e o PEEK (poliéter-éter-cetona) diferem principalmente nas suas caraterísticas de desempenho e aplicações. O PEEK oferece uma resistência superior ao calor (480°F vs 300°F), uma melhor resistência mecânica e uma resistência excecional ao desgaste, enquanto o PVDF oferece uma excelente resistência química, estabilidade aos raios UV e tem um custo significativamente mais baixo.
Principais diferenças entre PVDF e PEEK
Ao comparar estes dois termoplásticos de engenharia, compreender as suas propriedades fundamentais ajuda a determinar qual o material mais adequado para aplicações específicas. Ambos os materiais são considerados opções de elevado desempenho, mas destacam-se em diferentes ambientes e aplicações.
Composição e estrutura do material
O PVDF é um fluoropolímero semi-cristalino constituído por unidades repetidas de difluoreto de vinilideno. A sua estrutura molecular inclui ligações carbono-flúor que proporcionam uma excelente resistência química, embora não tão abrangente como a dos polímeros totalmente fluorados, como o PTFE.
O PEEK pertence à família das poliariletercetonas e apresenta uma estrutura molecular complexa com anéis aromáticos ligados por ligações de éter e cetona. Esta estrutura única confere ao PEEK uma estabilidade térmica e uma resistência mecânica excepcionais.
Comparação das caraterísticas de desempenho
A tabela seguinte apresenta uma comparação pormenorizada das principais propriedades entre o PVDF e o PEEK:
Imóveis | PVDF | PEEK | Material superior |
---|---|---|---|
Temperatura máxima de utilização contínua | 300°F (149°C) | 480°F (250°C) | PEEK |
Resistência mecânica (tração) | 5.800-7.800 psi | 14.500-16.000 psi | PEEK |
Resistência química | Excelente (a maioria dos ácidos e bases) | Muito bom (limitado por ácidos fortes) | PVDF |
Resistência aos raios UV | Excelente | Razoável a bom | PVDF |
Resistência ao desgaste | Bom | Excelente | PEEK |
Coeficiente de fricção | 0.25-0.35 | 0.35-0.40 | PVDF |
Fator de custo | Moderado | 2-3× superior ao PVDF | PVDF |
Absorção de humidade | 0.03-0.04% | 0.1-0.15% | PVDF |
Densidade | 1,75-1,78 g/cm³ | 1,30-1,32 g/cm³ | Dependente da aplicação |
Desempenho térmico e estabilidade
As capacidades de temperatura determinam frequentemente as decisões de seleção de materiais em muitas aplicações de engenharia.
Comparação da resistência ao calor
O PEEK demonstra uma estabilidade térmica excecional, mantendo as suas propriedades mecânicas a temperaturas até 250°C (480°F) para utilização contínua. Isto torna-o ideal para aplicações em ambientes de alta temperatura onde os plásticos tradicionais falhariam.
O PVDF, embora ainda seja considerado um plástico de alta temperatura, tem uma temperatura máxima de utilização contínua inferior, de aproximadamente 300°F (149°C). Esta gama de temperaturas é suficiente para muitas aplicações industriais, mas é insuficiente em ambientes térmicos extremos.
Na minha experiência de trabalho com clientes do PTSMAKE, este diferencial de temperatura torna-se frequentemente o fator decisivo na seleção entre estes materiais para aplicações como equipamento de processamento de semicondutores, onde as temperaturas de processo podem exceder as capacidades do PVDF.
Comportamento de ciclo térmico
Ambos os materiais lidam com ciclos térmicos de forma diferente:
- O PVDF apresenta uma boa estabilidade dimensional durante o ciclo térmico, embora possa registar uma expansão térmica mais significativa do que o PEEK.
- O PEEK mantém uma estabilidade dimensional excecional, mesmo através de ciclos térmicos repetidos, o que o torna preferível para componentes de precisão que têm de manter tolerâncias apertadas a temperaturas variáveis.
Perfis de resistência química
A resistência química é outro fator crucial que distingue estes materiais.
Resistência a ambientes agressivos
O PVDF oferece uma excelente resistência a uma vasta gama de produtos químicos, incluindo:
- A maioria dos ácidos (incluindo os ácidos clorídrico e sulfúrico concentrados)
- Hidrocarbonetos alifáticos e aromáticos
- Álcoois e solventes clorados
- Agentes oxidantes
O PEEK demonstra boa resistência química a muitas substâncias, mas pode ser atacado por ácido sulfúrico concentrado e alguns outros ácidos fortes. É particularmente resistente à hidrólise e à esterilização a vapor, o que o torna valioso em aplicações médicas.
Considerações sobre produtos químicos específicos da indústria
As diferentes indústrias dão prioridade a propriedades específicas de resistência química:
- Processamento químico: O PVDF é frequentemente preferido devido à sua grande resistência a ácidos e compostos clorados.
- Semicondutores: São utilizados ambos os materiais, dependendo a seleção dos produtos químicos específicos do processo.
- Petróleo e gás: A combinação de propriedades mecânicas e resistência química do PEEK torna-o valioso para aplicações de fundo de poço.
- Farmacêutico: A excelente resistência do PVDF a agentes de limpeza e métodos de esterilização torna-o popular para equipamento de processamento.
Propriedades mecânicas e aplicações estruturais
O resistência mecânica4 as diferenças entre estes materiais têm um impacto significativo na sua adequação a aplicações de suporte de carga.
Capacidades de suporte de carga
O PEEK oferece uma resistência mecânica substancialmente mais elevada, com valores de tração que variam tipicamente entre 14.500 e 16.000 psi, em comparação com os mais modestos 5.800 e 7.800 psi do PVDF. Este facto torna o PEEK superior para componentes estruturais que têm de suportar cargas mecânicas significativas.
Para aplicações que requerem tanto resistência química como integridade estrutural, o PEEK fornece frequentemente o melhor equilíbrio de propriedades, apesar do seu custo mais elevado. Recomendei o PEEK para numerosas aplicações no PTSMAKE em que os componentes têm de resistir tanto a produtos químicos agressivos como a tensões mecânicas.
Resistência ao desgaste e propriedades de fricção
O PEEK demonstra uma excelente resistência ao desgaste, tornando-o ideal para rolamentos, casquilhos e outros componentes sujeitos a fricção contínua. As suas propriedades auto-lubrificantes ajudam a prolongar a vida útil das peças móveis em ambientes exigentes.
O PVDF oferece uma boa resistência ao desgaste, embora não ao nível do PEEK. O seu coeficiente de atrito mais baixo (0,25-0,35 em comparação com os 0,35-0,40 do PEEK) pode ser vantajoso em determinadas aplicações de deslizamento de baixa carga, em que o atrito reduzido é mais importante do que a resistência máxima ao desgaste.
Propriedades de isolamento elétrico e térmico
Ambos os materiais apresentam caraterísticas eléctricas distintas que os tornam adequados para diferentes aplicações.
Propriedades dieléctricas
O PVDF é conhecido pelas suas propriedades piezoeléctricas, que lhe permitem gerar uma carga eléctrica em resposta à tensão mecânica aplicada. Esta caraterística única torna o PVDF valioso em aplicações de sensores.
O PEEK proporciona excelentes propriedades de isolamento elétrico numa vasta gama de temperaturas, mantendo a sua força dieléctrica mesmo a temperaturas elevadas. Isto torna-o particularmente valioso em aplicações eléctricas de alta temperatura, onde os plásticos normais falhariam.
Condutividade térmica
O PVDF e o PEEK têm ambos uma condutividade térmica relativamente baixa em comparação com os metais, o que os torna bons isoladores térmicos:
- PVDF: 0,17-0,19 W/m-K
- PEEK: 0,25-0,29 W/m-K
Esta baixa condutividade térmica pode ser uma vantagem ou uma desvantagem, dependendo da aplicação. Para componentes que requerem isolamento térmico, ambos os materiais têm um bom desempenho, embora o PVDF proporcione um isolamento ligeiramente melhor.
Considerações sobre custos e análise de valor
A diferença significativa de preço entre estes materiais torna essencial a análise custo-benefício.
Custo inicial do material
O PEEK custa normalmente 2 a 3 vezes mais do que o PVDF, o que representa um prémio de custo substancial que tem de ser justificado pelos requisitos de desempenho. Esta diferença de preço resulta do processo de fabrico mais complexo do PEEK e do custo mais elevado das matérias-primas.
Avaliação do valor do tempo de vida
Ao avaliar o custo total de propriedade, devem ser considerados vários factores para além do custo inicial do material:
- Vida útil prevista no ambiente de destino
- Frequência de substituição e custos de inatividade associados
- Requisitos de instalação e manutenção
- Preocupações de segurança e fiabilidade
Em muitas aplicações de alta temperatura ou de carga elevada, o desempenho superior do PEEK justifica o seu custo inicial mais elevado através de uma vida útil prolongada e de uma maior fiabilidade. Para aplicações dentro das capacidades do PVDF, o material de custo mais baixo proporciona frequentemente um melhor valor global.
Considerações sobre processamento e fabrico
As capacidades e limitações de fabrico também influenciam a seleção do material.
Diferenças de maquinagem
Ao maquinar estes materiais a PTSMAKE, observámos diferenças significativas:
- O PVDF trabalha relativamente bem, mas requer ferramentas afiadas e velocidades adequadas para evitar a fusão ou a escoriação.
- O PEEK é mais difícil de maquinar devido à sua abrasividade e fraca condutividade térmica, o que pode levar à acumulação de calor durante as operações de corte.
Para componentes de precisão, o PEEK mantém geralmente tolerâncias mais apertadas durante a maquinagem, mas requer técnicas e ferramentas mais especializadas, aumentando potencialmente os custos de fabrico.
Compatibilidade dos métodos de fabrico
Ambos os materiais podem ser processados através de múltiplos métodos de fabrico:
- PVDF: Moldagem por injeção, extrusão, moldagem por compressão, maquinagem
- PEEK: Moldagem por injeção, extrusão, moldagem por compressão, maquinagem, impressão 3D (equipamento especializado)
O PVDF oferece uma flexibilidade de processamento ligeiramente superior a temperaturas mais baixas, enquanto o PEEK requer temperaturas de processamento mais elevadas, mas oferece mais opções para geometrias complexas através de técnicas de fabrico avançadas.
Diretrizes de seleção específicas da candidatura
Diferentes indústrias dão prioridade a diferentes propriedades dos materiais, o que leva a preferências de materiais variadas.
Indústria de semicondutores
No fabrico de semicondutores, ambos os materiais têm aplicações, mas em áreas diferentes:
- PVDF: Normalmente utilizado em sistemas de água ultra-pura, componentes de distribuição de produtos químicos e equipamento de filtragem.
- PEEK: Preferido para componentes expostos a temperaturas elevadas, tais como equipamento de manuseamento de bolachas e componentes de câmaras de processamento.
Equipamento de processamento químico
Para aplicações de processamento químico:
- PVDF: Excelente para bombas, válvulas, acessórios e depósitos que manuseiam produtos químicos corrosivos a temperaturas moderadas.
- PEEK: mais adequado para componentes que requerem resistência química e capacidade para altas temperaturas ou resistência mecânica.
Aplicações médicas e farmacêuticas
Em aplicações médicas:
- PVDF: Utilizado habitualmente em membranas de filtração, suturas e alguns dispositivos implantáveis.
- PEEK: Preferido para dispositivos implantáveis, especialmente aplicações ortopédicas, devido à sua biocompatibilidade, radiolucência e propriedades mecânicas semelhantes às do osso.
Ao ajudar os clientes a selecionar entre PVDF e PEEK no PTSMAKE, recomendo uma abordagem sistemática que avalie primeiro os factores ambientais mais críticos (temperatura, produtos químicos, cargas mecânicas) e, em seguida, considere factores secundários como o custo, os requisitos de processamento e a disponibilidade.
<
O PEEK é um polietileno?
Já alguma vez se sentiu confuso com a variedade de plásticos de engenharia com nomes que soam de forma semelhante? Ao selecionar materiais para aplicações críticas, esta confusão pode levar a erros dispendiosos, falhas de desempenho e desperdício de recursos se substituir por engano um plástico de elevado desempenho por outro.
Não, o PEEK (poliéter-éter-cetona) não é um polietileno. O PEEK é um poliéter aromático com grupos cetona na sua espinha dorsal, criando um termoplástico semi-cristalino com uma excecional resistência ao calor (até 480°F), excelente resistência química e propriedades mecânicas superiores que excedem em muito as dos materiais de polietileno.
Estrutura química e diferenças de classificação
Quando se examina o PEEK versus o polietileno, as diferenças fundamentais começam ao nível molecular. Estas variações estruturais explicam porque é que estes materiais se comportam de forma tão diferente em aplicações práticas.
Comparação da espinha dorsal molecular
O PEEK apresenta uma estrutura de espinha dorsal aromática complexa com ligações de éter e cetona entre anéis de benzeno. Esta arquitetura molecular confere ao PEEK a sua extraordinária estabilidade térmica e resistência mecânica. Os anéis aromáticos criam rigidez, enquanto as ligações de éter proporcionam alguma flexibilidade.
O polietileno, pelo contrário, tem uma das estruturas poliméricas mais simples possíveis - apenas uma cadeia linear de átomos de carbono com átomos de hidrogénio ligados. Esta estrutura simples existe em várias formas (HDPE, LDPE, UHMWPE), mas todas elas não possuem os componentes aromáticos e os grupos funcionais que conferem ao PEEK as suas propriedades excepcionais.
Esta diferença estrutural fundamental significa que o PEEK pertence a uma família de polímeros totalmente diferente da do polietileno. Enquanto o polietileno é classificado como uma poliolefina, o PEEK pertence à família da poliariletercetona (PAEK) de termoplásticos de alto desempenho.
Principais diferenças de propriedade
As diferenças na estrutura molecular traduzem-se em variações dramáticas de desempenho:
Imóveis | PEEK | Polietileno (HDPE) | Fator de diferença |
---|---|---|---|
Temperatura máxima de utilização contínua | 480°F (250°C) | 180°F (82°C) | PEEK é 2,7× superior |
Resistência à tração | 14.500 psi | 4.500 psi | O PEEK é 3,2 vezes mais resistente |
Resistência química | Excelente (resiste à maioria dos produtos químicos) | Bom (vulnerável a solventes aromáticos) | O PEEK oferece uma resistência mais ampla |
Custo | Elevado | Baixa | PEEK custa 15-20× mais |
Densidade | 1,32 g/cm³ | 0,95 g/cm³ | O PEEK é 39% mais denso |
Dureza (Shore D) | 85-90 | 60-70 | O PEEK é significativamente mais duro |
Diferenças no processo de fabrico
Os métodos de produção do PEEK e do polietileno reflectem as suas diferentes estruturas moleculares e caraterísticas de desempenho.
Processo de produção PEEK
O PEEK é fabricado através de um processo complexo que envolve a polimerização de substituição aromática nucleofílica. Este processo requer um controlo preciso da temperatura e catalisadores especializados. Os materiais monómeros são significativamente mais caros do que o etileno, contribuindo para o custo mais elevado do PEEK.
Na PTSMAKE, quando maquinamos componentes PEEK, temos de ter em conta as propriedades únicas deste material - a sua baixa condutividade térmica significa que a gestão do calor durante a maquinação é fundamental para evitar a degradação térmica localizada.
Fabrico de polietileno
O polietileno é produzido através da polimerização por adição de etileno, utilizando vários catalisadores, consoante a densidade e a ramificação pretendidas. Este processo relativamente simples pode ser efectuado a temperaturas e pressões mais baixas do que a produção de PEEK, especialmente para variedades de baixa densidade.
Desempenho em ambientes extremos
Desempenho a altas temperaturas
Uma das diferenças mais significativas entre estes materiais é a sua estabilidade térmica:
- O PEEK mantém as suas propriedades mecânicas até 250°C (480°F) para utilização contínua e pode suportar exposições curtas a temperaturas ainda mais elevadas.
- O polietileno começa a amolecer por volta dos 82°C (180°F) e perde a maior parte da sua resistência mecânica muito abaixo dessa temperatura.
Já vi inúmeras aplicações em que os clientes selecionaram inicialmente o polietileno com base no custo, mas acabaram por sofrer uma falha rápida quando as temperaturas de funcionamento excederam as expectativas. Numa aplicação aeroespacial, um cliente trocou o polietileno pelo PEEK para um componente próximo de uma fonte de calor, prolongando a sua vida útil de meses para anos, apesar do custo inicial mais elevado do material.
Comparação da resistência química
Embora ambos os materiais ofereçam uma boa resistência química, o PEEK oferece uma maior proteção contra produtos químicos agressivos:
- O PEEK resiste à maioria dos ácidos, bases, hidrocarbonetos e solventes orgânicos
- O polietileno tem boa resistência a ácidos e bases, mas pode ser atacado por hidrocarbonetos aromáticos e alguns agentes oxidantes
Esta diferença torna-se crítica em equipamento de processamento químico, fabrico de semicondutores e aplicações médicas em que a exposição a múltiplos produtos químicos é comum.
Adequação da aplicação
Aplicações aeroespaciais e de defesa
Em aplicações aeroespaciais, a combinação de peso leve, resistência à chama e estabilidade térmica do PEEK torna-o inestimável para componentes como:
- Componentes interiores que requerem resistência à chama
- Conectores e isoladores eléctricos
- Componentes estruturais em zonas de alta temperatura
- Componentes do sistema de combustível que requerem resistência química
O polietileno raramente satisfaz os requisitos exigentes das aplicações aeroespaciais devido à sua estabilidade térmica e propriedades mecânicas limitadas.
Utilizações médicas e de cuidados de saúde
Os perfis de biocompatibilidade destes materiais também diferem significativamente:
- O PEEK é biocompatível e é utilizado em dispositivos implantáveis, instrumentos cirúrgicos e equipamento médico que requer esterilização
- O polietileno de qualidade médica (principalmente UHMWPE) é utilizado em alguns implantes, como articulações artificiais, mas não tem a resistência à temperatura do PEEK para esterilizações repetidas a vapor
Componentes de equipamento industrial
Para as máquinas industriais, a escolha entre estes materiais depende normalmente das condições de funcionamento:
- O PEEK destaca-se em ambientes de alta temperatura, aplicações que requerem uma excelente resistência ao desgaste ou exposição a produtos químicos agressivos
- O polietileno oferece um desempenho adequado em aplicações à temperatura ambiente com requisitos mecânicos moderados e é frequentemente escolhido pelo seu baixo custo e facilidade de processamento
Considerações sobre o custo-benefício
A diferença de preço entre estes materiais é substancial - o PEEK custa normalmente 15-20 vezes mais do que o polietileno de alta densidade. Esta diferença significativa de custos significa que a seleção do material deve basear-se numa análise exaustiva de:
- Gama de temperaturas de funcionamento necessárias
- Perfil de exposição química
- Requisitos de carga mecânica
- Vida útil prevista
- Consequências do insucesso
Para aplicações dentro da gama de capacidades do polietileno, o seu custo mais baixo torna-o a escolha mais económica. No entanto, quando os requisitos de desempenho excedem as limitações do polietileno, as propriedades superiores do PEEK justificam facilmente o seu preço superior através de uma vida útil prolongada, maior fiabilidade e custos de manutenção reduzidos.
Diferenças de maquinagem e processamento
No PTSMAKE, encontrámos diferenças significativas na maquinação destes materiais:
- O PEEK requer parâmetros de corte especializados devido à sua comportamento térmico5 durante a maquinagem, mas mantém tolerâncias apertadas e produz excelentes acabamentos de superfície
- O polietileno é mais fácil de maquinar, mas tem tendência para se deformar sob as forças de corte, tornando mais difícil manter tolerâncias apertadas
Compreender estas diferenças de processamento é essencial para a conceção de componentes com vista à sua manufacturabilidade e precisão.
Quais são as desvantagens e vantagens do PEEK?
Já alguma vez teve dificuldade em decidir se o PEEK vale o seu preço superior para a sua aplicação crítica? Quando o sucesso de um projeto depende da seleção do material, a escolha entre plásticos de alto desempenho dispendiosos e alternativas mais económicas pode ser um ato de equilíbrio difícil com consequências reais para a fiabilidade e longevidade.
O PEEK oferece vantagens excepcionais, incluindo uma notável resistência ao calor (até 480°F), uma excelente resistência química, uma excelente resistência mecânica e propriedades de desgaste superiores. No entanto, estas vantagens têm desvantagens significativas, incluindo um custo elevado (5-10 vezes mais do que os plásticos de engenharia normais), maquinabilidade difícil, opções de cor limitadas e fraca resistência aos raios UV.
Compreender as propriedades excepcionais do PEEK
O PEEK (poliéter-éter-cetona) destaca-se entre os plásticos de engenharia devido à sua combinação única de propriedades que o tornam adequado para as aplicações mais exigentes. Como alguém que já especificou materiais para inúmeros componentes de precisão, vi em primeira mão como as propriedades do PEEK se traduzem em benefícios de desempenho no mundo real.
Vantagens de desempenho térmico
Uma das caraterísticas mais impressionantes do PEEK é a sua estabilidade térmica. Este material mantém as suas propriedades mecânicas a temperaturas que levariam a maioria dos plásticos a falhar catastroficamente.
Caraterística da temperatura | Desempenho PEEK | Comparação com plásticos padrão |
---|---|---|
Temperatura de serviço contínuo | Até 480°F (250°C) | 2-3× superior à maioria dos plásticos de engenharia |
Temperatura de transição vítrea | 143°C (289°F) | Mantém a rigidez a temperaturas mais elevadas |
Ponto de fusão | 649°F (343°C) | Permite a esterilização a vapor |
Condutividade térmica | 0,25 W/m-K | Melhor do que muitos plásticos para dissipação de calor |
Esta excecional resistência térmica permite que o PEEK seja utilizado em aplicações próximas de fontes de calor, onde os plásticos normais se deformariam ou degradariam rapidamente. Ajudei muitos clientes a substituir componentes avariados feitos de materiais inferiores por peças em PEEK que continuam a funcionar sem falhas apesar dos ambientes térmicos difíceis.
Benefícios da resistência química
O perfil de resistência química do PEEK é quase tão impressionante como as suas propriedades térmicas. O material apresenta uma excelente resistência a:
- Hidrocarbonetos e solventes orgânicos
- A maioria dos ácidos e bases (exceto ácido sulfúrico concentrado)
- Vapor e água quente
- Fluidos e combustíveis para automóveis
- Processos de esterilização médica
Esta ampla resistência química torna o PEEK particularmente valioso em ambientes onde é expetável a exposição a múltiplas substâncias agressivas. Na indústria de semicondutores, por exemplo, os componentes PEEK podem suportar os produtos químicos agressivos utilizados no processamento de bolachas, mantendo a estabilidade dimensional.
Vantagens das propriedades mecânicas
A resistência mecânica do PEEK distingue-o da maioria dos outros termoplásticos:
- Resistência à tração de 14.500 psi (comparável a alguns metais)
- Excelente resistência à fadiga
- Excelente resistência ao impacto e tenacidade
- Resistência superior ao desgaste
- Baixo coeficiente de atrito
Estas propriedades tornam o PEEK adequado para aplicações estruturais onde a maioria dos plásticos falharia. Especifiquei o PEEK para engrenagens, rolamentos e outros componentes de elevado desgaste que funcionam sob tensão mecânica significativa, substituindo frequentemente peças metálicas por alternativas PEEK mais leves que proporcionam benefícios adicionais como resistência à corrosão e redução do ruído.
As desvantagens significativas do PEEK
Apesar das suas impressionantes caraterísticas de desempenho, o PEEK apresenta vários inconvenientes significativos que devem ser cuidadosamente considerados durante a seleção do material.
Restrições de custos
A desvantagem mais óbvia do PEEK é o seu custo. Na PTSMAKE, temos muitas vezes de ajudar os clientes a compreender o preço mais elevado do PEEK em comparação com outros plásticos de engenharia:
- O PEEK custa normalmente 5-10 vezes mais do que os plásticos de engenharia como o nylon ou o acetal
- Os custos dos materiais para as peças PEEK podem ser 20-30% superiores aos dos componentes metálicos equivalentes
- O elevado preço das matérias-primas tem um impacto significativo na economia das peças pequenas
Este fator de custo obriga frequentemente os engenheiros a reservar o PEEK apenas para as aplicações mais críticas, em que as suas propriedades únicas são absolutamente necessárias. Em muitos casos, recomendamos alternativas mais económicas para componentes não críticos de uma montagem.
Desafios de fabrico
O PEEK apresenta vários desafios de fabrico que podem aumentar a complexidade e o custo da produção:
Dificuldades de maquinagem: A elevada resistência térmica do PEEK traduz-se numa fraca condutividade térmica, provocando a acumulação de calor durante as operações de maquinagem. Isto exige velocidades de corte mais lentas, mudanças frequentes de ferramentas e estratégias de arrefecimento cuidadosas.
Requisitos de temperatura de processamento: Com um ponto de fusão de 649°F (343°C), o PEEK requer equipamento especializado de alta temperatura para moldagem por injeção e extrusão.
Janela de processamento limitada: A diferença entre a temperatura de fusão do PEEK e o início da degradação é relativamente estreita, criando desafios durante o processamento.
Contração do molde: O PEEK apresenta uma contração significativa (cerca de 1-1,3%) durante o arrefecimento, o que exige uma conceção precisa do molde para obter tolerâncias apertadas.
Na PTSMAKE, desenvolvemos protocolos de maquinação especializados para PEEK para enfrentar estes desafios, mas estes aumentam inevitavelmente o custo global e a complexidade do fabrico de componentes PEEK.
Limitações da aplicação
Apesar das suas propriedades impressionantes, o PEEK tem limitações que o tornam inadequado para determinadas aplicações:
- Fraca resistência aos raios UV: Sem aditivos, o PEEK degrada-se quando exposto à luz UV prolongada, limitando a sua utilização em aplicações exteriores.
- Opções de cores limitadas: Devido à sua cor âmbar/castanha natural e às elevadas temperaturas de processamento, é difícil colorir o PEEK de forma consistente.
- Limitações eléctricas: Embora seja um bom isolante, o PEEK não é ideal para aplicações eléctricas de alta frequência em comparação com polímeros eléctricos especializados.
- Dificuldades de ligação: A resistência química do PEEK torna a ligação adesiva um desafio, exigindo frequentemente tratamentos de superfície especiais.
Análise custo-benefício: Quando é que a PEEK vale a pena?
Dado o significativo aumento do custo do PEEK, é essencial efetuar uma análise custo-benefício exaustiva antes de especificar este material. Na minha experiência, o PEEK oferece o melhor valor nos seguintes cenários:
Cenários em que a PEEK se destaca
Ambientes de alta temperatura: Quando as temperaturas de funcionamento excedem os 300°F (149°C), o PEEK é muitas vezes a única opção plástica viável, justificando o seu custo superior.
Ambientes quimicamente agressivos: Em aplicações expostas a vários produtos químicos ou a substâncias particularmente agressivas, a ampla resistência química do PEEK evita as substituições frequentes exigidas por materiais inferiores.
Aplicações de desgaste crítico: Para componentes sujeitos a fricção e desgaste constantes em sistemas críticos, a excecional resistência ao desgaste e a baixa fricção do PEEK podem aumentar drasticamente os intervalos de manutenção.
Requisitos de redução de peso: Ao substituir componentes metálicos em aplicações aeroespaciais ou de alto desempenho, a relação resistência/peso do PEEK pode proporcionar benefícios de desempenho que justificam o seu custo.
Aplicações de implantes médicos: A biocompatibilidade e a estabilidade química do PEEK tornam-no ideal para dispositivos implantáveis de longa duração em que a falha do material não é uma opção.
Comparação de materiais alternativos
Para aplicações que não requerem especificamente as propriedades extremas do PEEK, existem várias alternativas que podem proporcionar um desempenho suficiente a um custo inferior:
Material | Vantagem comparativa | Custo vs. PEEK | Limitação da chave |
---|---|---|---|
PPS (sulfureto de polifenileno) | Boa resistência ao calor (400°F) | 40-60% inferior | Menos resistente a produtos químicos |
PTFE (Politetrafluoroetileno) | Resistência química superior | 30-50% inferior | Fraca resistência mecânica |
PEI (Polieterimida) | Boa resistência ao calor, transparência | 30-40% inferior | Menos resistente ao desgaste |
PAI (Poliamida-imida) | Alta resistência, boa resistência ao desgaste | 10-20% inferior | Mais difícil de processar |
Acetal (POM) | Excelente maquinabilidade, baixo custo | 80-90% inferior | Resistência limitada à temperatura |
Considerações específicas do sector
Diferentes indústrias dão prioridade a diferentes aspectos do perfil de propriedades do PEEK:
Aeroespacial e Defesa
Em aplicações aeroespaciais, a combinação de peso leve, resistência à chama (com aditivos) e estabilidade térmica do PEEK justifica o seu preço premium para componentes como:
- Buchas e rolamentos em sistemas de controlo
- Conectores e isoladores eléctricos
- Componentes estruturais em zonas de alta temperatura
- Componentes do sistema de combustível que requerem resistência química
Medicina e cuidados de saúde
A indústria médica valoriza o PEEK pelo seu..:
- Biocompatibilidade (grau de implante)
- Resistência à esterilização repetida
- Radiolucência (não interfere com os raios X)
- Propriedades mecânicas semelhantes às do osso (quando reforçado)
Estas propriedades tornam o PEEK ideal para dispositivos implantáveis e instrumentos cirúrgicos, apesar do seu elevado custo.
Equipamento industrial
Para aplicações industriais, a decisão de utilizar PEEK depende normalmente da severidade das condições de funcionamento:
- Ambientes extremos (alta temperatura, exposição a produtos químicos) justificam frequentemente o PEEK
- As aplicações em que o tempo de inatividade é extremamente dispendioso beneficiam da fiabilidade do PEEK
- Os componentes de alta precisão beneficiam da estabilidade dimensional do PEEK
Na PTSMAKE, ajudamos os clientes a navegar por estas considerações para determinar se o desempenho superior do PEEK justifica o seu preço superior para as suas necessidades específicas de aplicação.
Vou gerar o conteúdo do Capítulo 7 do artigo "Porque é que a PEEK é tão cara?" de acordo com os seus requisitos.
Porque é que a PEEK é tão cara?
Já alguma vez sentiu o choque de um adesivo ao pedir um orçamento para componentes PEEK? Quando os engenheiros se deparam pela primeira vez com o preço deste plástico de alto desempenho, muitos questionam se algum material poderia justificar um custo tão elevado, especialmente quando comparado com plásticos de engenharia mais comuns que parecem oferecer um desempenho decente por uma fração do preço.
O elevado custo do PEEK resulta do seu complexo processo de fabrico, das matérias-primas dispendiosas, dos requisitos de equipamento especializado e dos volumes de produção relativamente baixos. O intrincado processo de polimerização requer condições precisas, enquanto a natureza proprietária da tecnologia de produção e o estatuto do PEEK como material de especialidade elevam ainda mais o seu preço de mercado.
O complexo processo de fabrico do PEEK
Para compreender a razão pela qual o PEEK tem um preço tão elevado, é necessário examinar o seu processo de fabrico. Ao contrário dos polímeros mais simples, a produção de PEEK envolve uma química sofisticada e condições de processamento precisas que afectam significativamente o custo final.
Custos e escassez de matérias-primas
Os monómeros utilizados para produzir PEEK são, eles próprios, produtos químicos especiais dispendiosos. Os ingredientes principais incluem:
- Éter difenílico
- 4,4′-difluorobenzofenona
- Carbonato de potássio
- Difenilsulfona (como solvente)
Estes precursores requerem vários passos de refinação para atingir a pureza necessária para a síntese de PEEK, acrescentando camadas de custos antes mesmo de se iniciar a polimerização. Além disso, alguns destes produtos químicos têm uma capacidade de produção limitada a nível mundial, criando restrições de fornecimento que fazem subir os preços.
Na PTSMAKE, quando adquirimos PEEK para projectos de maquinagem, estamos a pagar não só pelo polímero em si, mas também por toda a cadeia de valor de produtos químicos especializados que foram utilizados na sua criação.
Complexidade do processo de polimerização
A síntese do PEEK envolve um sofisticado processo de polimerização por substituição aromática nucleofílica. Esta reação tem de ocorrer em condições controladas com precisão:
- Temperaturas entre 300-400°C (572-752°F)
- Atmosfera inerte para evitar a oxidação
- Recipientes sob pressão especializados
- Tempos de reação prolongados (frequentemente 3-5 horas)
- Gestão cuidadosa do catalisador
Cada um destes requisitos aumenta a complexidade e o custo do fabrico. A reação deve ser cuidadosamente monitorizada durante todo o processo para garantir uma distribuição adequada do peso molecular e da cristalinidade, que afectam diretamente as propriedades de desempenho do material.
Escala de produção limitada e dinâmica do mercado
O estatuto do PEEK como material de especialidade tem um impacto significativo na sua economia de produção e nos preços de mercado.
Tecnologia proprietária e proteção de patentes
A tecnologia de fabrico original do PEEK foi desenvolvida e patenteada pela Victrex (antiga ICI) na década de 1970. Ainda hoje, a tecnologia de produção continua a ser largamente proprietária e protegida por várias patentes. Esta concorrência limitada nos métodos de fabrico tem mantido os preços mais elevados em comparação com os plásticos de base.
Embora existam atualmente vários fabricantes a nível mundial (incluindo a Victrex, a Solvay e a Evonik), cada um utiliza processos proprietários que exigiram enormes investimentos em I&D para serem desenvolvidos. Estes custos de desenvolvimento têm de ser recuperados através do preço dos materiais.
Economia do volume de produção
Ao contrário dos plásticos de base produzidos em milhões de toneladas por ano, o PEEK é fabricado em volumes relativamente pequenos:
Tipo de plástico | Produção anual global | Fator de custo relativo |
---|---|---|
Polietileno (PE) | ~100 milhões de toneladas | 1× (linha de base) |
Nylon (PA) | ~8 milhões de toneladas | 2-3× |
Policarbonato (PC) | ~4,5 milhões de toneladas | 3-4× |
PEEK | <10.000 toneladas | 30-50× |
Este volume de produção limitado significa que os fabricantes não conseguem obter as economias de escala que fazem baixar os custos dos plásticos comuns. Os custos fixos como a manutenção das instalações, o controlo de qualidade e a I&D são distribuídos por menos quilogramas de produto, aumentando o custo por unidade.
Requisitos de equipamento e processamento
As instalações de produção de PEEK requerem equipamento especializado que possa suportar as temperaturas e pressões extremas necessárias para a polimerização, composição e processamento:
- Reactores de alta temperatura com sistemas de controlo precisos
- Equipamento especializado de extrusão e peletização
- Sistemas avançados de filtragem e purificação
- Instalações abrangentes de controlo de qualidade e de ensaio
Estes investimentos de capital são substanciais e contribuem significativamente para o custo final do material. Quando maquinamos peças PEEK no PTSMAKE, estamos a herdar estes custos de fabrico a montante no preço da matéria-prima.
Desafios de processamento e maquinagem
Uma vez produzido, o PEEK apresenta desafios adicionais no processamento e maquinagem que contribuem ainda mais para o seu elevado custo em componentes acabados.
Temperaturas de processamento elevadas
Com um ponto de fusão de aproximadamente 343°C (649°F), o PEEK requer equipamento de processamento especializado:
- Máquinas de moldagem por injeção com capacidade para altas temperaturas
- Moldes com sistemas especiais de gestão de calor
- Elementos de aquecimento e controladores mais caros
- Sistemas de segurança melhorados para o manuseamento de materiais a alta temperatura
Estes requisitos significam que menos fabricantes estão equipados para processar PEEK, limitando a concorrência e mantendo os custos de processamento mais elevados.
Considerações sobre a maquinagem e o desgaste da ferramenta
Ao maquinar PEEK a PTSMAKE, deparamo-nos com vários factores que contribuem para o aumento dos custos de produção:
Desgaste da ferramenta: O PEEK provoca um desgaste significativamente maior da ferramenta do que os plásticos normais, exigindo uma substituição mais frequente da ferramenta ou a utilização de ferramentas de qualidade superior.
Gestão do calor: A baixa condutividade térmica do PEEK significa que o calor se acumula durante a maquinagem, exigindo velocidades de corte mais lentas e técnicas de arrefecimento especiais.
Especialização: A maquinação correta do PEEK requer experiência e conhecimento para evitar a degradação do material e alcançar tolerâncias apertadas.
Requisitos de pós-processamento: Muitas aplicações PEEK requerem etapas de processamento adicionais, como o recozimento, para aliviar as tensões internas e garantir a estabilidade dimensional.
Cada um destes factores aumenta o custo total da produção de componentes PEEK acabados para além do preço da matéria-prima.
Controlo de qualidade e custos de certificação
Sendo um material de elevado desempenho frequentemente utilizado em aplicações críticas, o PEEK requer um rigoroso controlo de qualidade ao longo da sua produção e processamento.
Requisitos de teste rigorosos
Cada lote de PEEK é normalmente submetido a testes exaustivos para verificação:
- Distribuição do peso molecular
- Percentagem de cristalinidade
- Propriedades térmicas (transição vítrea e pontos de fusão)
- Propriedades mecânicas (resistência à tração, módulo, alongamento)
- Níveis de pureza e de contaminantes
Estes testes requerem equipamento especializado e pessoal treinado, acrescentando custos significativos de garantia de qualidade ao preço final do produto.
Certificações e rastreabilidade da indústria
Muitas aplicações PEEK nas indústrias aeroespacial, médica e de semicondutores exigem total rastreabilidade do material e conformidade com normas específicas da indústria:
- Certificações aeroespaciais (AS9100, NORSOK)
- Normas para dispositivos médicos (ISO 13485, USP Classe VI)
- Certificações do sector nuclear (NQSA-1)
- Requisitos da indústria de semicondutores (elevada pureza)
A manutenção destas certificações exige uma documentação extensa, auditorias regulares e, por vezes, instalações ou equipamentos de produção separados, o que contribui para aumentar os custos.
Comparação do PEEK com materiais alternativos
Para compreender o preço do PEEK no contexto, é útil compará-lo com materiais alternativos em termos de custo e desempenho.
Análise custo-desempenho
O PEEK custa normalmente 5 a 10 vezes mais do que os plásticos de engenharia normais e pode até ser mais caro do que alguns metais especiais numa base de volume. No entanto, o seu desempenho em ambientes extremos justifica frequentemente este prémio:
Imóveis | PEEK | Plásticos de engenharia padrão | Metais Premium |
---|---|---|---|
Temperatura de utilização contínua | Até 250°C (480°F) | 80-170°C (176-338°F) | Normalmente ilimitado |
Resistência química | Excelente | Variável (frequentemente limitado) | Frequentemente deficiente (corrosão) |
Força específica | Muito elevado | Moderado | Elevado |
Custo das matérias-primas | Muito elevado | Baixo a moderado | Moderado a elevado |
Custo de processamento | Elevado | Baixo a moderado | Elevado |
Valor do tempo de vida | Excelente | Limitado em condições adversas | Bom, mas com problemas de corrosão |
Na PTSMAKE, ajudamos frequentemente os clientes a avaliar estas compensações para determinar se o preço superior do PEEK é justificado pelas suas vantagens de desempenho na sua aplicação específica.
O PEEK vale o preço elevado?
A questão de saber se o elevado custo do PEEK se justifica depende inteiramente dos requisitos da aplicação.
Aplicações em que o PEEK oferece valor apesar do custo
O PEEK oferece um excelente valor, apesar do seu elevado preço, em aplicações que incluem:
- Ambientes de funcionamento extremos onde outros materiais falhariam rapidamente
- Sistemas de peso crítico onde a relação resistência/peso do PEEK oferece vantagens
- Equipamentos sensíveis à manutenção onde o custo do tempo de inatividade excede largamente os custos de material
- Ambientes corrosivos onde os metais se degradariam rapidamente
- Implantes médicos onde a biocompatibilidade e a estabilidade a longo prazo são essenciais
Nestes cenários, as vantagens de desempenho do PEEK traduzem-se diretamente em custos de vida mais baixos, apesar do investimento inicial mais elevado.
Estratégias de redução de custos para componentes PEEK
Para projectos que exijam o desempenho da PEEK, mas com limitações orçamentais, considere estas abordagens:
- Desenhos híbridos utilizar PEEK apenas para componentes críticos
- Técnicas de maquinação optimizadas reduzir os resíduos de materiais
- Processamento de formas de quase-rede minimizar o consumo de materiais
- Otimização da conceção para reduzir o volume total de material
- Graus não preenchidos quando os reforços não são necessários para o desempenho
Na PTSMAKE, ajudámos muitos clientes a implementar estas estratégias para obter os benefícios do PEEK e gerir os custos de forma eficaz.
Como otimizar a maquinagem PEEK para uma produção rentável?
Já alguma vez se perguntou se existe uma forma de aproveitar as propriedades excepcionais do PEEK sem quebrar o orçamento do seu projeto? Quando se trabalha com um dos plásticos de engenharia mais dispendiosos do mercado, otimizar a sua abordagem de maquinação não é apenas uma questão de eficiência - pode significar a diferença entre um projeto lucrativo e um que perde dinheiro devido ao desperdício excessivo de material e ao tempo de maquinação desnecessário.
A otimização da maquinagem PEEK para uma produção rentável requer a utilização de ferramentas de corte adequadas (metal duro ou revestidas a diamante), a manutenção de velocidades e avanços apropriados (normalmente mais lentos do que os plásticos normais), a implementação de estratégias de arrefecimento eficazes, a minimização do desperdício de material através de um design de forma quase líquida e o planeamento cuidadoso dos percursos das ferramentas para reduzir os tempos de ciclo.
Seleção da ferramenta ideal para maquinagem PEEK
Ao maquinar PEEK, a seleção das ferramentas tem um impacto significativo na qualidade das peças e nos custos globais de maquinação. Aprendi, ao longo de anos de experiência, que investir nas ferramentas corretas logo à partida permite poupar muito mais a longo prazo.
Materiais e geometrias de ferramentas de corte
A natureza abrasiva do PEEK, especialmente os tipos com enchimento que contêm fibra de carbono ou vidro, exige uma seleção cuidadosa das ferramentas:
Material da ferramenta | Melhor para | Vida útil da ferramenta | Fator de custo |
---|---|---|---|
Carboneto (não revestido) | PEEK não preenchido | Bom | Moderado |
Metal duro revestido a diamante | PEEK preenchido | Excelente | Elevado |
PCD (Diamante policristalino) | Produção de grande volume | Superior | Muito elevado |
Aço de alta velocidade (HSS) | Operações simples em PEEK não preenchido | Limitada | Baixa |
Para a maioria das aplicações no PTSMAKE, utilizamos ferramentas de metal duro com geometrias específicas concebidas para plásticos de alto desempenho. As principais caraterísticas que procuramos incluem:
- Arestas de corte afiadas (reduzem a produção de calor)
- Ângulos de inclinação positivos elevados (10-15°)
- Canais polidos (melhora a evacuação das aparas)
- Ângulos de folga suficientes (evita o atrito)
Embora as ferramentas premium custem mais inicialmente, mantêm a nitidez do gume durante mais tempo e produzem melhores acabamentos de superfície, reduzindo a necessidade de operações secundárias.
Considerações sobre o desgaste da ferramenta
O desgaste da ferramenta ocorre muito mais rapidamente quando se maquina PEEK em comparação com os plásticos de engenharia padrão. Descobrimos que a monitorização e gestão do desgaste das ferramentas é fundamental para manter a qualidade das peças e o controlo dos custos.
Recomendo que se estabeleça um calendário de substituição de ferramentas com base no volume maquinado, em vez de se esperar por sinais visuais de desgaste. Na nossa oficina, as ferramentas que maquinam PEEK com enchimento são normalmente substituídas após aproximadamente 60-70% da vida útil da ferramenta que esperamos quando maquinamos alumínio. Esta abordagem pró-ativa evita os problemas de qualidade e as potenciais peças de refugo que resultam da maquinação com ferramentas gastas.
Otimização dos parâmetros de corte
Encontrar o equilíbrio correto entre velocidade, avanço e profundidade de corte é crucial para uma maquinação PEEK eficiente. O objetivo é maximizar as taxas de remoção de material sem gerar calor excessivo ou comprometer a qualidade da superfície.
Recomendações de velocidade e alimentação
Através de testes extensivos no PTSMAKE, desenvolvemos estas diretrizes gerais para os parâmetros de maquinação PEEK:
Tipo PEEK | Velocidade de corte (SFM) | Taxa de alimentação | Profundidade de corte | Líquido de refrigeração |
---|---|---|---|---|
PEEK não preenchido | 300-500 | Moderado | 0.005"-0.020" | Ar ou névoa |
30% com enchimento de carbono | 200-400 | Reduzido (75%) | 0.005"-0.015" | Névoa/inundação |
30% Enchimento de vidro | 250-450 | Reduzido (85%) | 0.005"-0.015" | Névoa/inundação |
Estes parâmetros devem ser ajustados com base nas suas ferramentas específicas, na rigidez da máquina e nos requisitos da peça. Em geral, recomendo que se comece no extremo conservador destes intervalos e que se aumentem gradualmente os parâmetros enquanto se monitorizam os resultados.
Estratégias de gestão do calor
A fraca condutividade térmica do PEEK pode levar à acumulação de calor durante a maquinagem, causando potencialmente:
- Instabilidade dimensional
- Acabamento superficial degradado
- Desgaste acelerado da ferramenta
- Decomposição do material em casos extremos
Para combater estes problemas, implementamos várias técnicas de gestão térmica:
Seleção correta do líquido de refrigeração: Para PEEK sem enchimento, o arrefecimento por ar comprimido funciona frequentemente bem. Para os tipos com enchimento, o arrefecimento por névoa ou por inundação proporciona uma melhor dissipação do calor.
Corte intermitente: As pausas periódicas durante as operações de embolsamento profundo permitem a dissipação do calor.
Fresagem de trepadeiras: A utilização da fresagem por escalada em vez da fresagem convencional reduz o atrito e a produção de calor.
Passagens múltiplas de luz: Fazer várias passagens de acabamento ligeiras em vez de um corte pesado melhora a precisão dimensional e o acabamento da superfície.
Estratégias de utilização de materiais
Dado o elevado custo do PEEK (frequentemente $75-200 por libra, dependendo do tipo e da forma), a utilização do material torna-se um fator crítico de custo. Cada pedaço de desperdício tem um impacto direto no seu resultado final.
Material de partida quase em forma de rede
Começar com material mais próximo das suas dimensões finais pode reduzir significativamente o desperdício. Considere estas abordagens:
Extrusões personalizadas: Para peças com secções transversais consistentes, começar com perfis extrudidos personalizados pode eliminar um desperdício significativo de material. O custo de instalação mais elevado é compensado pela poupança de material em grandes séries de produção.
Peças em bruto pré-cortadas: O facto de o seu fornecedor de materiais fornecer peças em bruto pré-cortadas, dimensionadas especificamente para as suas peças, reduz o desperdício e o tempo de maquinagem inicial.
Software de agrupamento: Para peças planas maquinadas a partir de chapas, a utilização de um software de colocação avançado pode otimizar a utilização de material em 15-30% em comparação com o planeamento manual da disposição.
No PTSMAKE, ajudámos os clientes a reduzir os custos do material PEEK em mais de 40%, implementando estas abordagens para os seus componentes de grande volume.
Considerações sobre a reciclagem de chips
Ao contrário de alguns termoplásticos, o PEEK não pode ser facilmente reciclado internamente devido à sua elevada temperatura de processamento. No entanto, existem serviços de reciclagem especializados:
- As aparas de PEEK limpas e selecionadas podem ser vendidas a empresas de reciclagem
- Alguns recicladores creditam o valor do material em compras futuras
- Os tipos cheios têm normalmente um valor de reciclagem mais baixo devido a preocupações com a contaminação
Embora a reciclagem não compense completamente os seus custos de material, pode proporcionar alguma recuperação de custos para operações de maquinagem maiores.
Otimização da estratégia de maquinagem
Para além das ferramentas e dos parâmetros, a sua abordagem global à maquinagem tem um impacto significativo na qualidade das peças e nos custos de produção.
Projeto de fixação para peças múltiplas
Dispositivos de fixação bem concebidos que permitem a maquinação de várias peças numa única configuração oferecem várias vantagens:
- Redução do tempo de preparação por peça
- Melhoria da coerência entre peças
- Utilização mais eficiente da máquina
- Melhor rendimento do material em chapa
Para um cliente do sector aeroespacial, concebemos um dispositivo que permitiu maquinar 16 pequenos componentes PEEK em simultâneo, reduzindo o custo por peça em 62% em comparação com as configurações individuais.
Refinamento da estratégia CAM
Os percursos de ferramenta optimizados podem reduzir drasticamente o tempo de maquinação e melhorar a qualidade das peças:
Moagem de alta eficiência: A utilização de estratégias CAM avançadas que mantêm um engate consistente da ferramenta reduz os tempos de ciclo e aumenta a vida útil da ferramenta.
Maquinação em repouso: As operações corretamente sequenciadas que utilizam ferramentas maiores para a remoção de material em massa e ferramentas mais pequenas apenas quando necessário optimizam as taxas de remoção de material e a vida útil da ferramenta.
Movimentos de aproximação optimizados: Minimizar o corte de ar através de movimentos eficientes de aproximação e retração pode reduzir os tempos de ciclo em 5-15% sem impacto na qualidade da peça.
Controlo de qualidade para minimizar a sucata
Dado o elevado custo do material PEEK, a redução de desperdícios torna-se uma estratégia de poupança de custos fundamental. Processos de controlo de qualidade eficazes que detectam problemas atempadamente evitam o desperdício de material dispendioso em peças que não cumprem as especificações.
Medição em processo
Implementámos várias etapas de verificação durante o processo:
Inspeção do primeiro artigo: Medição exaustiva da primeira parte de cada série antes de prosseguir com a produção.
Inspecções faseadas: Medição de caraterísticas críticas antes de proceder a operações subsequentes, especialmente ao virar ou refixar peças.
Estabilização térmica: Permitir que as peças atinjam a temperatura ambiente antes das medições finais, uma vez que a expansão térmica do PEEK pode afetar as dimensões.
Estas práticas ajudaram-nos a manter uma taxa de refugo inferior a 2% para os componentes PEEK, significativamente mais baixa do que as médias da indústria.
Considerações pós-acabamento
O processo não termina quando a peça sai da máquina. As operações de pós-maquinação podem ter um impacto significativo na qualidade e no custo.
Alívio de tensões e estabilidade dimensional
As peças PEEK com geometrias complexas ou remoção irregular de material podem beneficiar de um alívio de tensões para garantir a estabilidade dimensional a longo prazo:
Recozimento térmico: O aquecimento controlado abaixo da temperatura de transição vítrea, seguido de um arrefecimento lento, pode aliviar as tensões internas.
Estratégia de desbaste até ao fim: A remoção da maior parte do material numa operação inicial, permitindo depois que a peça estabilize antes da maquinação final, melhora a precisão dimensional.
Para componentes críticos com tolerâncias apertadas, estes passos extra valem bem o investimento para evitar falhas dispendiosas no terreno ou desvios dimensionais ao longo do tempo.
Ao implementar estas estratégias de otimização, ajudámos inúmeros clientes da PTSMAKE a conseguir uma maquinação PEEK rentável sem comprometer as propriedades de desempenho excepcionais que tornam este material tão valioso. A chave é uma abordagem holística que considera todos os aspectos do processo de fabrico, desde a seleção do material até à inspeção final.
Saiba mais sobre as técnicas de gestão térmica para maquinagem de plástico de elevado desempenho. ↩
Aprenda técnicas avançadas para maquinação de precisão de termoplásticos de elevado desempenho. ↩
Clique aqui para explorar técnicas especializadas para maquinar termoplásticos de elevado desempenho com precisão. ↩
Descubra como as propriedades mecânicas afectam a seleção de materiais para componentes de elevado desempenho. ↩
Aprenda técnicas de maquinagem especializadas para evitar a deformação relacionada com o calor em termoplásticos de elevado desempenho. ↩