Have you ever wondered how your phone case feels both rigid and soft in different areas? Or how that sleek gaming controller perfectly combines textured grips with smooth surfaces? The magic behind these innovative products lies in a manufacturing technique that’s revolutionizing product design across industries.
Two-shot injection molding is a sophisticated manufacturing process that seamlessly combines two different materials or colors into a single component within one molding cycle, eliminating assembly steps while creating complex multi-material parts that would be impossible with traditional techniques.
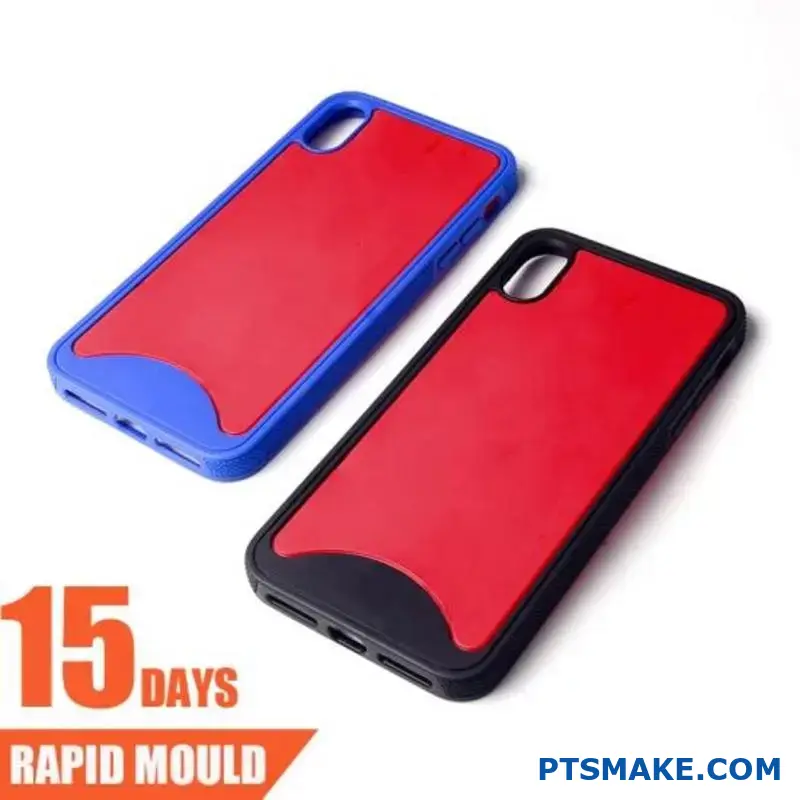
What Is Two-Shot Injection Molding?
At its core, two-shot injection molding (also called dual-shot or multi-material molding) is an advanced plastic manufacturing process that allows for the production of complex parts using two different materials or colors in a single molding operation. Unlike traditional injection molding, which creates single-material components, two-shot molding produces integrated parts with different properties in different sections.
The beauty of this technology lies in its ability to bond different materials together at the molecular level. This creates a strong, seamless connection that would be difficult or impossible to achieve through post-molding assembly processes. I’ve worked with countless clients at PTSMAKE who were initially skeptical about the bond strength, only to be amazed by the durability of the final products.
How The Two-Shot Molding Process Works
The two-shot injection molding process follows a specific sequence:
- Primeiro tiro: The primary material is injected into the mold cavity to form the base part.
- Rotação: The mold either rotates or transfers the first shot to a second cavity.
- Segundo tiro: A different material is injected over or alongside the first material.
- Arrefecimento e ejeção: The completed part cools and is ejected from the mold.
This process requires specialized equipment – either a machine with multiple injection units or a rotating platen system. The technical precision required makes this a more complex operation than standard injection molding.
Critical Parameters for Successful Two-Shot Molding
The success of any two-shot molding project depends on several critical factors:
Parâmetro | Descrição | Importância |
---|---|---|
Compatibilidade de materiais | The chemical compatibility between the two materials | Essential for proper bonding and preventing delamination |
Controlo da temperatura | Precise management of melt and mold temperatures | Critical for material flow and proper adhesion |
Timing Sequence | The exact timing between first and second shots | Affects bond quality and part integrity |
Conceção de moldes | Specialized design with proper gates and vents | Determines material flow and final part quality |
In my 15+ years in this industry, I’ve found that material compatibility is often the most challenging aspect. Not all plastics bond well together, which is why material selection requires significant expertise. At PTSMAKE, we conduct extensive compatibility testing before finalizing material choices for our clients.
Advantages of Two-Shot Injection Molding
Two-shot injection molding offers numerous benefits that make it increasingly popular across various industries:
Flexibilidade e inovação na conceção
The ability to combine materials with different properties (rigid/flexible, opaque/transparent, conductive/insulating) opens up unlimited design possibilities. Product designers can create components with haptic differentiation1 – varied tactile properties across different areas of the same part.
Eficiência de fabrico
By eliminating assembly steps, two-shot molding significantly streamlines the manufacturing process:
- Redução dos custos de mão de obra
- Fewer quality issues related to assembly
- Shorter production cycles
- Decreased inventory requirements
Desempenho melhorado do produto
Two-shot molded parts typically outperform assembled parts in several ways:
- Stronger material bonds
- Better sealing properties
- Improved chemical resistance at the interface
- Maior durabilidade
- Enhanced aesthetics
Cost Effectiveness Over Product Lifecycle
While initial tooling costs are higher than for conventional molding, the long-term economics often favor two-shot molding. At PTSMAKE, we regularly help clients conduct cost analyses that demonstrate significant savings, especially for high-volume production runs where assembly costs would otherwise be substantial.
Aplicações comuns
Two-shot injection molding has found applications across numerous industries:
- Eletrónica de consumo: Smartphone cases with hard shells and soft grips, gaming controllers, remote controls
- Automóvel: Dashboard components, steering wheel controls, gear shifters
- Dispositivos médicos: Surgical tools with ergonomic grips, equipment housings with seals
- Household Products: Kitchen utensils with comfort grips, appliance components
- Ferramentas industriais: Power tool housings, equipment handles
The versatility of this technology continues to expand its reach into new applications. I’ve witnessed a growing trend toward using two-shot molding for creating products with embedded electronics, where the second shot encapsulates and protects sensitive components.
The Two-Shot Molding Process Explained
Ever watched a master chocolatier create those perfect bonded layers in a gourmet truffle? The precision, timing, and artistry involved mirrors what happens in industrial two-shot molding—except we’re creating something far more durable than chocolate, using advanced engineering instead of culinary skills.
The two-shot molding process represents manufacturing choreography at its finest—a precisely timed sequence where two different materials are injected into specially designed tooling, creating a single component with dual properties that would be impossible to achieve through traditional assembly methods.
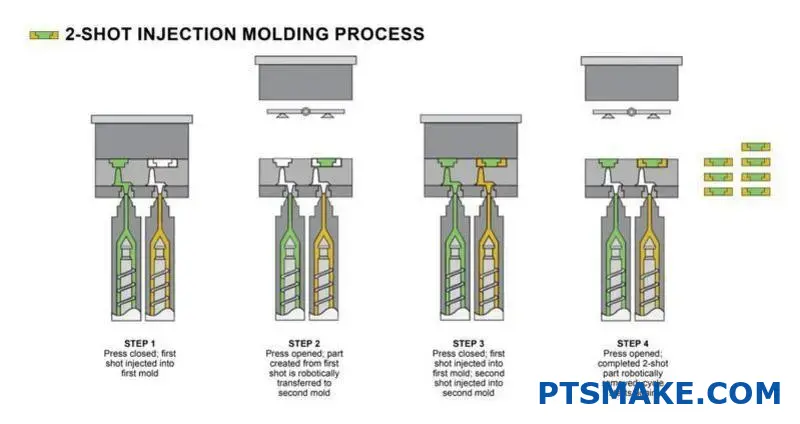
First Material Injection: Setting the Foundation
The two-shot molding journey begins with the careful preparation of both materials. Temperature control is absolutely critical at this stage—each polymer has its optimal processing temperature range that must be maintained throughout the process.
When engineering parts at PTSMAKE, we begin by injecting the first material (typically the more rigid or structural component) into the initial mold cavity. This creates what we call the “substrate” or base component. The first shot usually requires:
Material Preparation Considerations
- Pre-drying of hygroscopic materials to prevent moisture-related defects
- Precise temperature control to ensure proper flow
- Careful pressure calibration to prevent flash or short shots
- Strategic gate placement for optimal fill patterns
The first material must be selected not only for its functional properties but also for its compatibility with the second material. I’ve learned through numerous projects that this compatibility factor can make or break a two-shot application.
The Critical Transition: Mold Rotation
Once the first material has been injected and partially solidified, the mold undergoes a transformation. There are several approaches to this transition phase:
Método | Descrição | Melhores aplicações |
---|---|---|
Prato rotativo | The mold physically rotates 180° to position the first shot for the second injection | High-volume production with symmetric parts |
Core Back | The core retracts to create space for the second material | Complex geometries requiring precise material boundaries |
Transfer | The first shot is robotically moved to a second mold | Very large components or specialty applications |
Sobremoldagem | The first shot is manually or automatically placed in a second mold | Lower volume production or extremely complex geometries |
At PTSMAKE, we primarily use rotary platen technology for most applications, as it offers the fastest cycle times and most reliable performance. This transition phase must be precisely timed—too early, and the first material may not be stable enough; too late, and the bonding interface may not form properly.
Second Material Bonding: Creating the Interface
The second injection is where the true magic of two-shot molding happens. This is where we introduce the second material—often an elastomer, a different colored plastic, or a material with specific properties like conductivity or molecular adhesion2.
The second material flows into the newly created cavity space and makes contact with the first material. Several key factors influence successful bonding:
Critical Bonding Factors
- Interface temperature must be high enough to promote molecular entanglement
- Material compatibility (polar/non-polar interactions)
- Surface energy of both materials
- Flow pattern and pressure of the second injection
- Timing between first and second shots
When properly executed, the two materials form a chemical and/or mechanical bond at their interface. This bond is typically stronger than any adhesive-based connection could achieve, creating an integrated component that functions as a single unit.
Precision Tooling: The Unsung Hero
The tooling required for two-shot molding represents some of the most sophisticated mold design in the industry. These tools must:
- Accommodate multiple injection points
- Maintain precise alignment during rotation or transfer
- Control temperature differentials between different mold sections
- Incorporate specialized venting for each material
- Feature sophisticated ejection systems that can safely remove complex parts
At PTSMAKE, we invest significantly in advanced tooling capabilities because we recognize that even the best materials and machines cannot compensate for inadequate tooling design. Our mold designers work directly with our process engineers to ensure that every aspect of the tooling supports optimal material flow and bonding.
Material Compatibility: The Science Behind the Bond
Not all plastics play nicely together. Material compatibility in two-shot molding depends on several factors:
- Chemical composition of both materials
- Melting and processing temperature ranges
- Coefficient of thermal expansion
- Shrinkage rates during cooling
- Molecular structure and potential for entanglement
When consulting with clients, I often use this simplified compatibility chart to illustrate potential material pairings:
Material de base | Compatible Overmold Materials | Notas |
---|---|---|
ABS | TPE, TPU, Silicone, PC | Excellent overall compatibility |
PC | ABS, TPE, TPU | Good for high-performance applications |
Nylon | TPE, TPU, Santoprene | Strong bonding, good for functional parts |
PP | TPE (modified), TPV | Requires special grades for good adhesion |
PBT | TPE, TPU | Excellent for electrical applications |
Testing is always recommended, as specific grades of materials can behave differently than their general material family might suggest.
Controlo de processos e garantia de qualidade
The complexity of two-shot molding requires sophisticated process control and monitoring. Key quality assurance measures include:
- Real-time monitoring of injection parameters for both shots
- Vision systems to verify proper material placement
- Automated part inspection for aesthetic and functional defects
- Bond strength testing to ensure proper adhesion
- Thermal cycling tests to verify bond durability
Moldagem de dois disparos vs. sobremoldagem: Principais diferenças
Ever picked up a power tool with a perfectly grippy, soft-touch handle that seamlessly blends into a rigid body? Or noticed how some automotive controls feel pleasantly firm yet cushioned in just the right places? These tactile marvels aren’t happy accidents but the result of sophisticated manufacturing techniques that are often confused but fundamentally different.
Two-shot molding and overmolding represent distinct approaches to creating multi-material plastic parts, with two-shot molding utilizing a continuous production cycle for seamless integration, while overmolding employs separate, sequential processes that offer different advantages in material selection and production flexibility.
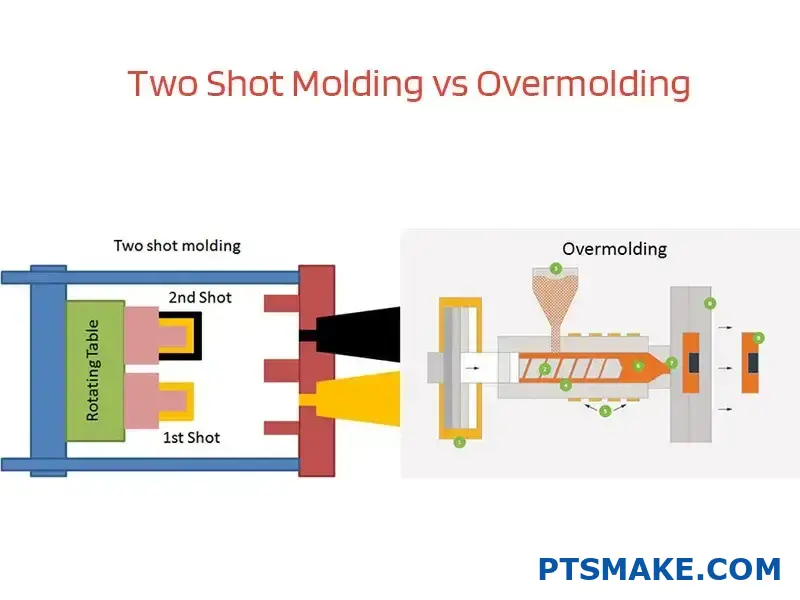
The Fundamental Distinction
When clients approach me about multi-material parts, the first question I ask is about their production volume and material requirements. This immediately helps determine whether two-shot molding or overmolding might be more appropriate for their project.
Two-Shot Molding: The Continuous Cycle Approach
Two-shot injection molding operates as a single, continuous manufacturing process. Here’s how it works:
- The first material is injected into the initial mold cavity
- The mold either rotates or indexes to a second position
- A second material is injected alongside or onto the first material
- The completed part is ejected as a single, bonded component
The key advantage here is continuity. Since everything happens in one machine during a single cycle, production is faster and more efficient for high volumes. At PTSMAKE, our two-shot molding lines can produce complex parts with cycle times that are only marginally longer than single-material molding operations.
Overmolding: The Sequential Process
In contrast, overmolding follows a more discrete approach:
- The first material is molded as a complete substrate part
- This substrate is removed from the first mold
- The substrate is placed into a second mold (either manually or by automation)
- The second material is injected around, over, or onto the substrate
- The completed assembly is ejected as the final product
This sequential process creates more flexibility but typically results in longer overall cycle times.
Considerações sobre o volume de produção
One of the most important factors when choosing between these techniques is your anticipated production volume:
Volume de produção | Processo recomendado | Justificação |
---|---|---|
High Volume (100k+ parts) | Moldagem de dois tiros | Lower per-part cost, faster cycles, reduced labor |
Medium Volume (10k-100k) | Either Method | Depends on material requirements and part complexity |
Low Volume (<10k) | Sobremoldagem | Lower tooling investment, more material flexibility |
When we work with automotive clients at PTSMAKE, they often require hundreds of thousands of identical parts, making two-shot molding the clear economic choice. For medical device manufacturers producing specialty components in lower quantities, overmolding frequently provides a better balance of cost and flexibility.
Material Compatibility Requirements
The second major consideration involves material compatibility. This represents a significant technical constraint3 that can often dictate which process makes more sense.
Two-Shot Molding Material Limitations
Two-shot molding requires materials with:
- Similar processing temperatures
- Chemical compatibility for bonding
- Comparable shrink rates
- Ability to bond without an adhesive layer
These requirements can be restrictive. When two materials don’t naturally bond well, two-shot molding may not be viable without special additives or surface treatments.
Overmolding Material Flexibility
Overmolding offers greater material flexibility because:
- The substrate can cool completely before the second shot
- Mechanical interlocks can be used when chemical bonding isn’t possible
- Surface treatments can be applied between molding steps
- Significantly different processing temperatures can be accommodated
I’ve worked with clients who needed to combine materials that simply wouldn’t bond in a two-shot process, making overmolding the only viable option despite higher production costs.
Factores de complexidade da conceção
The complexity of your part design also influences which process makes more sense:
Two-Shot Design Considerations
- Better for parts where materials meet at clearly defined boundaries
- Excellent for hard/soft combinations with substantial interface areas
- Ideal for color contrasts and decorative elements
- Limited ability to create fully encapsulated sections
Overmolding Design Advantages
- Superior for creating thin layers over complex geometries
- Better for fully encapsulating electronic components
- More suitable for drastically different material thicknesses
- Can create more complex 3D interfaces between materials
When designing multi-material components at PTSMAKE, we thoroughly evaluate geometry requirements before recommending a manufacturing approach. Sometimes what seems like a perfect two-shot application must shift to overmolding due to specific design requirements.
Economic Considerations Beyond Volume
While production volume is a primary economic factor, other financial considerations come into play:
Investimento em ferramentas
Two-shot molding typically requires more sophisticated tooling with rotating platens or transfer mechanisms, increasing initial investment. Overmolding can utilize simpler tools but requires two separate molds.
Requisitos laborais
Two-shot molding significantly reduces labor costs with its automated, continuous process. Overmolding may require manual transfers between molds for lower volumes, though this can be automated for higher quantities.
Consistência da qualidade
Two-shot molding generally provides more consistent quality with fewer opportunities for handling damage or misalignment. This can reduce scrap rates and quality control costs over the production run.
Practical Applications: Making The Choice
After working with hundreds of multi-material projects, I’ve developed a simple framework for making recommendations:
-
Choose two-shot molding when:
- High volumes justify the tooling investment
- Materials have excellent chemical compatibility
- Cycle time reduction is critical
- Labor costs are a significant concern
- Part-to-part consistency is paramount
-
Choose overmolding when:
- Production volumes are moderate to low
- Materials have significantly different processing requirements
- Complex encapsulation is needed
- Design changes may be required during product lifecycle
- Project budget constraints limit initial tooling investment
The distinctions between these processes might seem subtle on paper, but they make an enormous difference in production efficiency and part quality. Understanding these differences has saved our clients millions in unnecessary costs over the years.
Material Selection and Compatibility Considerations
Ever wonder why some multi-material products feel seamlessly integrated while others fall apart after minimal use? The secret lies not in assembly techniques but in the invisible chemistry happening when different materials meet. This critical science determines whether your two-shot molded product will be a market success or a costly failure.
Material selection for two-shot injection molding represents the single most crucial decision in your project journey, requiring careful analysis of chemical compatibility, thermal properties, and mechanical characteristics to create products with exceptional durability, functionality, and aesthetic appeal.
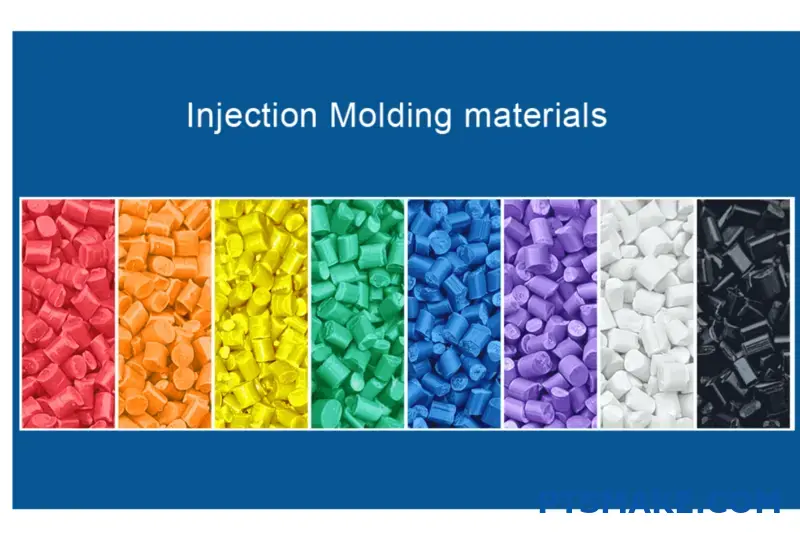
The Chemistry Behind Successful Material Bonding
In my years working with two-shot injection molding at PTSMAKE, I’ve discovered that material selection isn’t just about finding materials with the right physical properties—it’s about understanding the molecular relationship between them. The success of any two-shot molded part ultimately depends on how well your chosen materials bond at the molecular level.
Chemical Compatibility Fundamentals
Chemical compatibility between materials determines whether they’ll form strong molecular bonds during the two-shot process. This compatibility is influenced by several factors:
Polymer Polarity and Surface Energy
Materials with similar polarity typically bond better with each other. For instance, polar materials like nylon (PA) tend to bond well with other polar materials such as thermoplastic polyurethane (TPU). Non-polar materials like polypropylene (PP) often require special adhesion modifiers to bond with polar materials.
Surface energy also plays a crucial role in material bonding. Materials with high surface energy typically create stronger bonds than those with low surface energy. This explains why polypropylene, with its relatively low surface energy, tends to be more challenging to bond than materials like ABS or PC.
Molecular Entanglement Capabilities
When two compatible materials meet in their molten state during two-shot molding, their polymer chains can entangle at the interface. This molecular interdiffusion4 creates a strong physical bond that resists separation. Materials with similar chemical structures tend to allow better chain entanglement.
Here’s a simplified compatibility chart we often reference with clients:
Material de base | Highly Compatible | Moderately Compatible | Poor Compatibility |
---|---|---|---|
ABS | PC, PMMA, SAN | TPE, TPU, PVC | PE, PP, POM |
PC | ABS, PMMA, TPU | PBT, PET, PA | PE, PP, PTFE |
PA (Nylon) | TPU, TPE, PET | PC, PBT, PPS | PP, PE, PTFE |
PP (with modifiers) | TPV, TPE (olefinic) | Modified TPU | PC, PA, POM |
POM | TPU (with primer) | PBT | ABS, PC, PP |
Thermal Property Considerations
Beyond chemical compatibility, thermal properties significantly impact material selection for two-shot molding.
Compatibilidade com a temperatura de processamento
The processing temperatures of both materials must be compatible. Ideally, the second material should have a lower melting point than the first material to prevent deformation of the substrate during the second injection.
For example, when working with a PC substrate (processing temperature around 280-320°C) and TPE overmold (processing temperature around 190-230°C), the second shot’s lower temperature prevents damage to the first material while still allowing good flow and bonding.
Coefficient of Thermal Expansion (CTE)
Materials expand and contract at different rates as temperature changes. When two materials with vastly different CTEs are bonded together, thermal cycling can create stress at the interface, potentially leading to delamination over time.
Tipo de material | Typical CTE Range (10^-6/°C) | Recommended Pairing |
---|---|---|
Semi-crystalline (PP, PA, POM) | 80-150 | Best paired with flexible TPEs that can accommodate expansion |
Amorphous (ABS, PC, PMMA) | 50-90 | Compatible with most overmold materials |
Glass-filled compounds | 20-40 | Requires careful selection to avoid stress-induced separation |
Mechanical Properties Balance
A successful two-shot molded part requires thoughtful balance of mechanical properties between the chosen materials.
Rigidity and Flexibility Considerations
Many two-shot applications aim to combine rigidity in one area with flexibility in another. This creates ergonomic products that can both provide structure and comfort. The mechanical property gradient between materials should be intentional and appropriate for the application.
For instance, in a power tool handle, we might select PC or glass-filled nylon for the rigid structural component (with a flexural modulus of 2,000-10,000 MPa) paired with a TPE having a much lower flexural modulus (10-100 MPa) for the grip area.
Hardness Differential Management
The hardness differential between materials must be managed carefully, especially for parts with thin sections. A very hard material adjacent to a very soft material can create stress concentrations that lead to premature failure.
In our experience at PTSMAKE, gradual transitions work best—for example, using a 40-50 Shore D TPE against a rigid substrate rather than an extremely soft 30 Shore A material, unless design accommodations are made.
Application-Specific Material Selection Factors
Beyond the fundamental compatibility factors, application-specific requirements further constrain material selection.
Environmental Resistance Requirements
The operating environment for your two-shot molded part introduces additional selection criteria:
- Exposição a produtos químicos: Will the part contact oils, solvents, or cleaning agents?
- Exposição aos raios UV: Will the part be used outdoors or under intense lighting?
- Gama de temperaturas: What are the minimum and maximum temperatures the part will experience?
- Moisture Exposure: Will the part be subjected to high humidity or immersion?
Each of these factors may eliminate otherwise compatible material combinations. For instance, a part requiring excellent UV stability might rule out standard ABS as the substrate material, despite its excellent bonding properties with many TPEs.
Regulatory and Compliance Considerations
Regulated industries introduce additional selection requirements:
Aplicações médicas
For medical devices, biocompatibility and sterilization compatibility become paramount. Materials must often meet:
- USP Class VI or ISO 10993 biocompatibility standards
- Resistance to sterilization methods (ethylene oxide, gamma irradiation, autoclave)
- FDA compliance for food contact (if applicable)
Automotive Requirements
Automotive applications typically demand:
- Heat resistance (often 85°C continuous, with spikes to 120°C)
- Low VOC emissions to meet vehicle interior air quality standards
- Flame retardancy to UL94 standards
- Material approvals from major automotive manufacturers
Testing Protocols for Material Compatibility
At PTSMAKE, we never rely solely on material data sheets when determining compatibility. We implement rigorous testing to validate material combinations:
Adhesion Testing Methods
- Peel Testing: Measuring the force required to separate materials at their interface
- Ensaio de tração: Evaluating bond strength under tension
- Ensaios de impacto: Assessing bond integrity under sudden force
- Ciclo térmico: Subjecting the bonded materials to temperature extremes to evaluate durability
Prototype Validation Approach
For critical applications, we recommend a systematic validation approach:
- Material pair screening with small test specimens
- Adhesion testing under various conditions
- Prototype functional testing
- Accelerated aging tests to predict long-term performance
This approach minimizes risk and ensures the selected materials will perform as expected throughout the product lifecycle.
Optimizing Material Selection for Production Efficiency
Beyond compatibility and performance, material selection also impacts production efficiency.
Requisitos de secagem
Hygroscopic materials like nylon, PC, and PBT require thorough drying before processing. Pairing two highly hygroscopic materials can extend cycle times and complicate processing. Consider pairing a non-hygroscopic material with a hygroscopic one when possible to simplify processing.
Flow Characteristics Matching
Materials with vastly different flow characteristics can create processing challenges. The second material must be able to flow properly at the interface with the first material, which has already cooled somewhat. Materials with similar viscosity curves often process more consistently in two-shot applications.
Innovative Materials Expanding Two-Shot Possibilities
Recent material developments have expanded the possibilities for two-shot molding:
- Adhesion-Modified Grades: Special material formulations with enhanced bonding properties
- Thermoplastic Composites: Fiber-reinforced materials with improved strength-to-weight ratios
- Soft-Touch Materials: Specialized TPEs with enhanced tactile properties
- Antimicrobial Compounds: Materials with built-in resistance to bacteria growth
- Sustainable Bioplastics: Bio-based materials expanding eco-friendly options
These innovations continue to broaden the application range for two-shot molding across industries.
Design Guidelines for Two-Shot Molded Parts
Have you ever admired the perfect grip of your toothbrush or the sleek combination of hard and soft textures on your gaming controller? Creating these multi-material masterpieces isn’t just art—it’s precision engineering that requires careful attention to design principles most consumers never notice.
Two-shot injection molded parts demand specialized design considerations that balance aesthetic appeal with manufacturing feasibility, requiring thoughtful planning around wall thickness transitions, material interface zones, and geometric features that ensure both production efficiency and exceptional product performance.
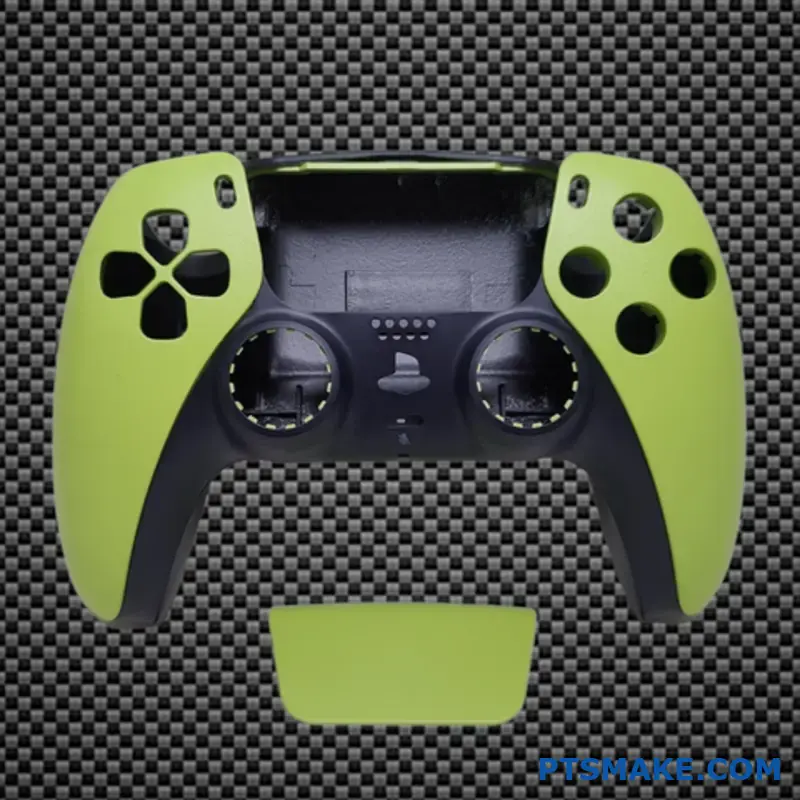
Optimizing Wall Thickness for Two-Shot Success
Wall thickness design in two-shot molding presents unique challenges that go beyond single-material parts. When designing components at PTSMAKE, I follow specific guidelines to ensure optimal performance in both materials and at their critical interface.
Maintaining Uniform Thickness Within Each Material Zone
For each material in a two-shot application, consistency is key. Uniform wall thickness prevents common defects like:
- Sink marks from thick sections cooling unevenly
- Warpage from differential shrinkage
- Flow lines where material thickness changes abruptly
- Voids from incomplete filling of thick sections
When designing rigid substrate components (first shot), I typically recommend wall thicknesses between 1.5mm and 3mm for most engineering plastics. For the second shot, especially with flexible materials like TPE or TPU, thicknesses between 1mm and 2.5mm generally provide the best balance of flexibility and moldability.
Managing Thickness Transitions Between Materials
The transition zone between materials requires special attention. Abrupt thickness changes at material interfaces often lead to:
Questão | Solução de design | Benefício |
---|---|---|
Concentração de tensões | Gradual transitions with radii | Prevents cracking and delamination |
Flow imbalance | Staged thickness reduction | Ensures complete filling of both materials |
Marcas de afundamento | Balanced cooling rates | Melhora a qualidade do acabamento da superfície |
Bond weakness | Optimized contact area | Enhances mechanical interlock |
I’ve found that limiting thickness differences between adjoining materials to no more than 25% significantly improves bond strength and overall part quality. Where greater differences are necessary, implementing a stepped transition rather than an abrupt change yields better results.
Designing Effective Material Transition Zones
The interface where materials meet represents the most critical design area in two-shot molding. This transition zone determines both aesthetic appeal and structural integrity.
Creating Strong Mechanical Bonds
While chemical compatibility between materials is essential, mechanical interlocking significantly enhances bond strength. Effective mechanical bonding features include:
Undercuts and Recesses
Incorporating strategically placed undercuts allows the second material to flow around and “lock” into the first material. This creates a physical connection that reinforces the chemical bond. The most effective undercuts have:
- Depth-to-width ratios between 0.5:1 and 1:1
- Draft angles of 1-3° for easy ejection
- Rounded internal corners to prevent stress concentration
Texturização de superfícies
Texturing the interface surface of the first shot can dramatically improve bond strength by:
- Increasing the effective surface area for bonding
- Creating microscopic mechanical interlocking features
- Promoting material interface adhesion[^5] through increased contact points
At PTSMAKE, we often apply light blast texturing (16-32 μin) to bonding surfaces of the first shot to enhance adhesion with the second material.
Color Boundary Management
For parts with contrasting colors, controlling the visible boundary between materials requires precision design:
- Define clear parting lines along natural product contours
- Use raised or recessed features to mask small alignment variations
- Implement “color break” details that create intentional visual separation
- Consider color bleed potential when selecting contrasting colors
The most successful two-shot color designs incorporate the parting line as an intentional design element rather than trying to hide it.
Implementing Effective Draft Angles
Draft angles—the slight taper applied to vertical surfaces—are crucial in all injection molding, but they require special consideration in two-shot applications.
Draft Requirements for First and Second Shots
The first shot material typically requires standard draft angles (0.5° to 3° depending on material and surface finish). However, areas that will interface with the second material often need additional draft to ensure:
- Complete filling of the second material
- Proper venting at the interface
- Prevention of trapped air pockets
- Easy ejection of the completed part
For the second shot, I typically recommend:
- Minimum 1.5° draft for smooth surfaces
- 2-5° draft for textured surfaces
- 3-7° draft for deep ribs or features with high aspect ratios
Strategic Draft Direction Planning
Draft direction planning becomes more complex in two-shot molding because the first shot becomes part of the mold for the second shot. This requires careful consideration of:
- Primary ejection direction for the completed part
- Secondary extraction directions for internal features
- Potential for undercuts in either first or second materials
- Gate location impact on flow and draft requirements
Ideally, both materials should share a common draft direction to simplify the molding process and tooling design.
Rib and Boss Design Considerations
Ribs and bosses are common structural features that require special attention in two-shot designs, particularly when they cross material boundaries.
Optimizing Rib Design for Two Materials
When ribs traverse from one material to another, consider these guidelines:
- Maintain consistent rib thickness-to-wall ratios (typically 60-80% of adjoining wall)
- Taper ribs that cross material boundaries (thicker in rigid material, thinner in flexible)
- Incorporate radius transitions at material interfaces
- Add ventilation features for ribs that might trap air during second shot
For structural ribs in the rigid component, a thickness of 40-60% of the nominal wall works well in most applications, with a minimum of 0.5mm for most engineering plastics.
Boss Design for Hardware Installation
Bosses for fasteners or inserts present unique challenges in two-shot designs:
Boss Location | Design Recommendation | Raciocínio |
---|---|---|
In rigid material only | Standard boss design with supporting ribs | Maximizes structural integrity |
At material interface | Rigid material forms inner core, flexible material creates outer layer | Provides vibration dampening while maintaining strength |
Within flexible material | Rigid material “island” surrounded by flexible material | Enables hardware attachment in otherwise soft areas |
For threaded inserts, I recommend keeping the boss entirely within the rigid material whenever possible, with a minimum wall thickness of 0.4 times the insert diameter.
Gate Location and Venting Strategies
Proper gate placement and venting are essential for successful two-shot molding, affecting both aesthetics and part quality.
Strategic Gate Placement
Gate location impacts flow patterns, weld lines, and visible marks. Consider these guidelines:
- Position first-shot gates away from second-shot contact areas when possible
- Place gates to create flow patterns that enhance rather than resist bonding
- Use multiple gates for complex geometries to ensure complete filling at interfaces
- Consider sequenced gating for controlling flow at critical transitions
For the second shot, edge gates typically provide the best balance of aesthetics and filling pressure when placed at the thickest section of the material.
Enhanced Venting Requirements
Two-shot molding requires more extensive venting than conventional molding because:
- Air can become trapped at material interfaces
- Complex geometries create multiple potential air traps
- The first shot may block traditional venting paths
Effective venting strategies include:
- Parting line vents at predicted air trap locations (0.025-0.04mm depth)
- Stepped venting at material transitions
- Strategic vent placement based on flow analysis
- Vacuum-assisted venting for highly complex parts
Inadequate venting leads to incomplete filling, burn marks, and weak bonding—issues that are particularly problematic in two-shot applications.
Shrinkage and Tolerance Management
Managing differential shrinkage between materials is among the most challenging aspects of two-shot design.
Accommodating Differential Shrinkage
Different materials shrink at different rates during cooling, which can cause warpage or stress at interfaces. To manage this:
- Select materials with compatible shrinkage rates when possible
- Design the rigid component to “control” the overall part geometry
- Allow the flexible component to accommodate more of the differential movement
- Incorporate flexibility in design to absorb shrinkage stresses
For parts combining a rigid engineering plastic with a TPE, expect shrinkage differentials of 0.5-1.5% that must be accommodated in the design.
Setting Realistic Tolerances
Tolerance capability in two-shot molding varies by:
- Material combination
- Geometria da peça
- Dimensional direction (in-flow vs. cross-flow)
- Distance from gates
- Wall thickness
As a general guideline, critical dimensions should be contained within a single material rather than crossing the interface. When dimensions must cross materials, use these guidelines:
- Standard tolerance within single material: ±0.005 in/in
- Tolerance across material boundaries: ±0.010 in/in
- Additional tolerance for thin walls: add 0.001 in for walls under 1.5mm
Optimizing for Production Efficiency
Beyond technical considerations, two-shot designs should optimize for manufacturing efficiency.
Balancing Cavity Fill Times
The volume and flow distance of both materials should be balanced to ensure:
- Similar fill times for both shots
- Consistent cooling rates
- Balanced pressure requirements
- Tempos de ciclo óptimos
I typically aim for a second shot volume between 30-70% of the first shot for the most efficient processing.
Designing for Automated Production
For high-volume production
Applications and Industries Leveraging Two-Shot Technology
Ever wondered why your sleek smartphone case feels both smooth and grippy in different areas? Or how luxury vehicles achieve those striking dashboard controls with perfect tactile feedback? Behind these seamless multi-material products lies a manufacturing revolution that’s quietly transforming the products we use every day.
Two-shot injection molding technology has become the cornerstone of innovation across numerous industries, enabling manufacturers to create complex products with multiple materials, textures, and functions in a single manufacturing process – eliminating assembly steps while enhancing both aesthetics and performance.
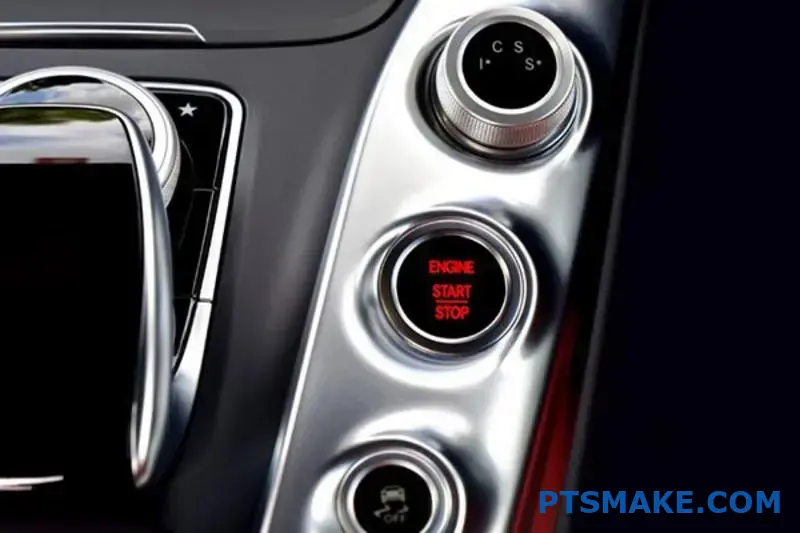
Automotive Applications: Driving Innovation Through Multi-Material Components
The automotive industry has embraced two-shot molding technology with unprecedented enthusiasm. As vehicles evolve into sophisticated machines that prioritize both functionality and passenger experience, multi-material components have become essential to meeting consumer expectations.
Interior Controls and Displays
Modern vehicle interiors showcase some of the most visible applications of two-shot molding technology:
- Controlos do painel de controlo combine rigid structural components with soft-touch overlays, creating buttons and knobs with perfect tactile feedback
- Steering wheel controls integrate hard substrates with soft, grippy surfaces for improved ergonomics and comfort during extended driving
- Center console components feature rigid housings with integrated seals and dampening elements to create premium-feeling controls that operate smoothly and quietly
These components not only look and feel better than their single-material predecessors but also offer improved durability and resistance to the constant use typical in automotive environments.
Aplicações sob o capô
Beyond the visible interior components, two-shot molding has found its way into critical functional components:
Componente | First Shot Material | Second Shot Material | Benefício chave |
---|---|---|---|
Reservatórios de fluidos | Rigid plastic (PA, PBT) | Elastomer (TPE, TPV) | Integrated seals prevent leakage |
Conectores eléctricos | Nylon com enchimento de vidro | TPE | Improved weatherproofing and vibration resistance |
Air intake components | Rigid PP/PE | Soft TPE | Enhanced vibration dampening, reduced noise |
Caixas de sensores | PC/ABS | Silicone | Waterproof seals with precise electrical properties |
The elimination of separate seals and gaskets in these applications reduces assembly complexity while improving reliability – a critical consideration in the challenging under-hood environment.
Componentes exteriores
Exterior automotive applications benefit particularly from the environmental resistance of two-shot molded parts:
- Puxadores de portas with rigid cores and soft-touch inserts provide both strength and comfort
- Peças de acabamento exteriores combine multiple colors or materials for distinctive brand styling
- Caixas de espelhos incorporate integrated seals and vibration damping elements
- Conjuntos de luzes feature rigid housings with flexible gaskets to maintain watertight seals
Working with several automotive manufacturers at PTSMAKE, I’ve observed how two-shot molding has dramatically reduced assembly time while improving the weatherability of exterior components – a critical factor in longevity and customer satisfaction.
Medical Device Applications: Precision Where It Matters Most
The medical industry demands the highest levels of precision, reliability, and safety – requirements that two-shot molding is uniquely positioned to address.
Instrumentos cirúrgicos
Modern surgical instruments leverage two-shot molding to combine functionality with ergonomics:
- Surgical handles with rigid cores and soft, non-slip grips provide surgeons with precise control
- Clamps and forceps incorporate hard structural components with soft touch points for improved grip during procedures
- Cutting guides combine rigid measurement structures with soft contact surfaces to prevent tissue damage
The ability to create these instruments as single, integrated components eliminates potential failure points while improving sterilization effectiveness.
Equipamento de diagnóstico
Diagnostic devices benefit tremendously from two-shot technology:
- Hand-held scanners feature rigid housings with integrated soft seals for fluid protection
- Equipamento de análise de sangue combines clear viewing windows with opaque structural components
- Patient monitoring devices incorporate button arrays with integrated sealing against liquids
O biocompatibilidade[^6] requirements of medical devices make material selection particularly critical in these applications.
Sistemas de administração de medicamentos
Perhaps most impressively, two-shot molding has revolutionized drug delivery systems:
- Auto-injectors combine structural components with integrated fluid paths and seals
- Insulin pens feature transparent windows with precise measurement markings bonded to structural bodies
- Inaladores incorporate rigid mechanisms with flexible sealing components in a single, reliable unit
The elimination of assembly steps is particularly valuable in these applications, where even minor manufacturing variations could affect dosing accuracy and patient safety.
Consumer Electronics: Merging Aesthetics with Function
Consumer electronics represent perhaps the most visible application area for two-shot molding, with nearly every modern device incorporating some multi-material components.
Mobile Device Accessories
The mobile accessory market has been transformed by two-shot molding:
- Capas para smartphones combine rigid protection with soft areas for shock absorption and grip
- Earbud housings feature hard structural shells with soft ear contact points for comfort
- Wearable device bands integrate rigid connection points with flexible wearing surfaces
These accessories must not only look and feel premium but also withstand thousands of interaction cycles and environmental challenges – requirements that two-shot molded parts excel at meeting.
Gaming Controllers and Input Devices
Gaming peripherals showcase some of the most sophisticated applications:
- Game controllers feature rigid structural shells with strategically placed soft-touch grips
- Keyboard components combine hard keycaps with soft dampening elements for improved feel
- VR controllers integrate multiple textures and surfaces to enhance immersion
The gaming experience is heavily influenced by how controls feel in the user’s hands, making the tactile properties of two-shot molded components critical to product success.
Small Appliances and Tools
Household electronics have widely adopted two-shot technology:
- Electric toothbrushes combine waterproof housings with soft grip sections
- Kitchen appliance controls feature hard buttons with soft overlays for water resistance
- Caixas de ferramentas eléctricas integrate rigid structures with vibration-dampening grip zones
At PTSMAKE, we’ve helped numerous consumer electronics manufacturers transition from assembled components to integrated two-shot designs, consistently achieving significant improvements in product durability while reducing warranty claims.
Industrial Equipment: Enhancing Performance in Demanding Environments
Industrial applications place extreme demands on components, making the durability advantages of two-shot molding particularly valuable.
Hand Tools and Controls
Professional-grade tools benefit significantly from two-shot technology:
- Caixas de ferramentas eléctricas combine structural rigidity with vibration-dampening grip zones
- Precision measurement tools integrate hard scales with soft gripping surfaces
- Painéis de controlo feature sealed button arrays with tactile feedback elements
For industrial users, the improved ergonomics translate directly to reduced fatigue and injury risk during extended use.
Fluid Handling Components
Industrial fluid systems leverage two-shot molding for improved reliability:
- Componentes da bomba integrate rigid structural elements with flexible seals
- Alojamentos de válvulas combine multiple materials to optimize flow characteristics while ensuring leak-proof operation
- Filter assemblies feature rigid support structures with flexible sealing surfaces
The elimination of separate gaskets and seals dramatically improves reliability in these applications, reducing maintenance requirements and downtime.
Equipamento de segurança
Worker safety equipment has been revolutionized by two-shot technology:
- Óculos de proteção combines rigid frames with soft contact points for all-day comfort
- Respirator components integrate hard structural elements with soft face-sealing surfaces
- Hard hat suspension systems feature rigid adjustment mechanisms with soft contact points
The ability to create perfect material transitions without assembly steps helps ensure consistent performance in safety-critical applications.
Sporting Goods: Enhancing Performance and Comfort
Athletic equipment manufacturers have embraced two-shot molding to create products that excel in both performance and comfort.
Performance Footwear
Modern athletic shoes leverage two-shot components in critical areas:
- Cleats and spikes combine rigid support structures with varying degrees of flexibility
- Toe guards feature hard protection with soft interfaces against the foot
- Heel counters integrate stability structures with comfort elements
These components must withstand enormous forces while maintaining comfort during extended use – a perfect application for two-shot technology.
Racquets and Bats
Striking implements benefit from the vibration-dampening capabilities of multi-material components:
- Tennis racquet handles combine rigid cores with ergonomic grip overlays
- Baseball bat grips feature hard connection points with soft handling surfaces
- Golf club components integrate multiple materials for optimal energy transfer and feel
The ability to precisely control the transition between rigid and flexible zones allows manufacturers to tune performance characteristics with unprecedented precision.
Protective Equipment
Athletic protection demonstrates the safety benefits of two-shot molding:
- Componentes do capacete combine hard impact protection with soft comfort liners
- Shin guards feature rigid shields with integrated cushioning elements
- Mouthguards utilize multiple material hardnesses for optimal protection and comfort
The perfect bonding between materials ensures these safety-critical components perform consistently under impact conditions.
The Future of Two-Shot Applications
As two-shot molding technology continues to evolve, several emerging application areas show particular promise:
Produtos sustentáveis
The ability to precisely combine different materials opens new possibilities for sustainable design:
- Recyclable products with easily separable material combinations
- Bio-based material components integrated with conventional polymers
- Water-conserving fixtures with improved sealing performance
Dispositivos inteligentes
The Internet of Things demands components that combine structural, aesthetic, and functional elements:
- Caixas de sensores with integrated environmental seals
- Wearable health monitors combining rigid electronics enclosures with comfortable body contact surfaces
- Smart home controllers featuring intuitive tactile interfaces
Medical Innovations
Next-generation medical devices will push two-shot technology to new limits:
- Dispositivos implantáveis with precisely controlled surface characteristics
- Custom prosthetics with integrated comfort features
- **Point
Cost-Benefit Analysis of Two-Shot Injection Molding
Is investing in advanced manufacturing technology always worth the price tag? When manufacturing executives face the decision to adopt two-shot injection molding, they often struggle with justifying the higher initial investment against promised long-term benefits that seem impressive on paper but uncertain in reality.
Two-shot injection molding presents a compelling economic case when evaluated comprehensively, offering significant cost advantages through eliminated assembly operations, reduced labor requirements, lower reject rates, and improved product quality—particularly for mid to high-volume production runs where the initial tooling investment can be amortized effectively.
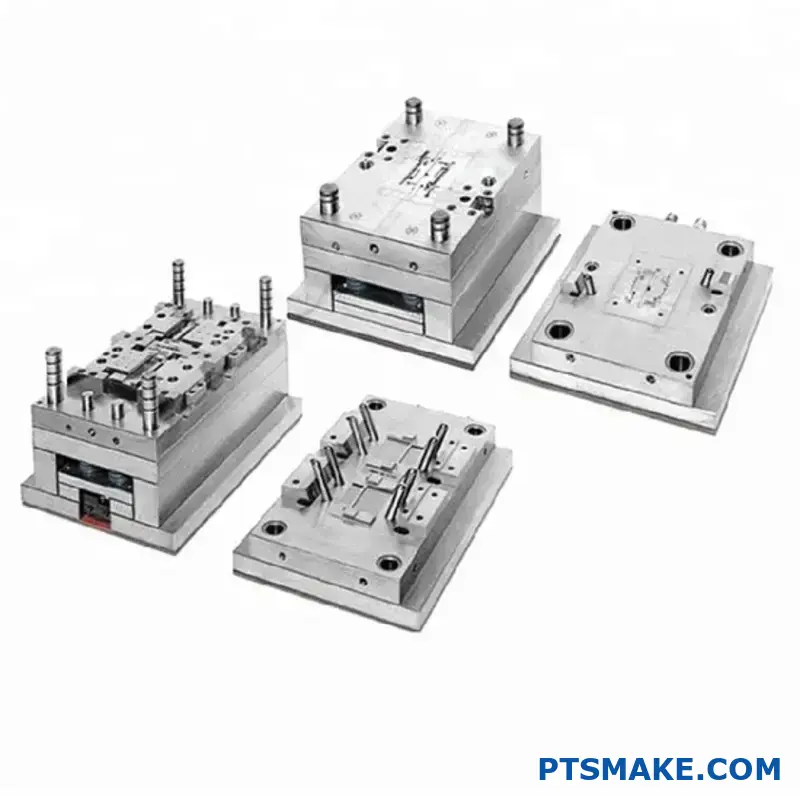
Understanding the Investment Landscape
When evaluating the financial implications of two-shot injection molding, it’s essential to consider both the upfront investments and the downstream savings. At PTSMAKE, I’ve guided numerous clients through this analysis, helping them understand when the technology makes financial sense and when alternative approaches might be more appropriate.
Initial Investment Requirements
The startup costs for two-shot injection molding typically exceed those of conventional molding processes. These investments include:
Specialized Equipment Costs
Two-shot injection molding requires dedicated machinery that significantly differs from standard injection molding equipment:
Tipo de equipamento | Gama de custos aproximados | Caraterísticas principais |
---|---|---|
Rotary Platen Machine | $300,000 – $750,000 | Built-in rotation mechanism, dual injection units |
Core-Back Machine | $250,000 – $600,000 | Specialized mold movement capability |
Transfer Automation | $150,000 – $400,000 (additional) | Robotic systems for part transfer between molds |
These specialized machines represent a substantial capital expenditure, typically 30-50% higher than conventional injection molding equipment of similar tonnage.
Advanced Tooling Investment
The tooling for two-shot molding presents another significant upfront cost:
- Two-shot molds typically cost 1.5-2.5 times more than single-shot molds
- Complex design requirements increase engineering time and costs
- Specialized features like rotating cores add mechanical complexity
- Extended development time lengthens the period before production can begin
A typical two-shot mold for a medium-complexity part might cost $50,000-$150,000, compared to $30,000-$70,000 for a comparable single-shot mold.
Process Development Expenses
Beyond equipment and tooling, companies must also invest in:
- Operator training for specialized equipment
- Process optimization and validation
- Ensaios de compatibilidade de materiais
- Quality control protocol development
These “soft costs” often add 10-15% to the total project investment but are essential for successful implementation.
Quantifying the Operational Savings
The substantial initial investment in two-shot molding technology is offset by significant operational advantages that generate ongoing savings throughout the product lifecycle.
Eliminated Assembly Operations
Perhaps the most significant economic advantage of two-shot molding comes from the elimination of secondary assembly operations:
Redução dos custos de mão de obra
When manufacturing multi-material or multi-component products using conventional methods, assembly typically requires:
- Manual or semi-automated assembly stations
- Inspeção da qualidade em várias fases
- Management of additional workforce
- Training and supervision costs
Two-shot molding eliminates these requirements by producing finished components directly from the molding machine. For products with moderate complexity, this typically reduces direct labor costs by 30-60%.
Assembly Equipment Elimination
Beyond direct labor, conventional assembly requires:
- Assembly fixtures and jigs
- Adhesive application systems or ultrasonic welding equipment
- Conveyor systems and assembly line infrastructure
- Additional factory floor space
By eliminating these needs, two-shot molding can reduce capital equipment requirements and free up valuable production space for other operations.
Reduced Inventory Management Complexity
Two-shot molding streamlines inventory management by:
- Reducing the number of unique parts that must be tracked
- Decreasing work-in-process inventory between operations
- Minimizing the risk of component shortages disrupting production
- Reducing warehouse space requirements for component storage
For manufacturers managing thousands of parts, this simplification offers both direct cost savings and operational efficiency improvements.
Quality Improvements and Scrap Reduction
Quality-related savings represent another major economic benefit:
Fator de qualidade | Conventional Assembly | Moldagem de dois tiros | Impacto económico |
---|---|---|---|
Taxa de defeitos | 2-5% typical | 0.5-1.5% typical | 60-80% reduction in quality-related losses |
Rework Costs | Significativo | Mínimo | Labor savings of 15-30% |
Pedidos de garantia | Higher risk | Lower risk | Reduced field failure costs |
Consistência | Variável | Altamente consistente | Melhoria da satisfação do cliente |
These quality improvements have compounding financial benefits that extend well beyond the manufacturing floor, affecting everything from customer satisfaction to brand reputation.
Balancing Costs and Benefits: The Volume Equation
The economic viability of two-shot molding is heavily influenced by production volume, as higher quantities allow the initial investment to be amortized across more units.
Break-Even Analysis by Production Volume
Based on data from numerous projects at PTSMAKE, I’ve observed these typical break-even points:
- Low Volume (under 10,000 units annually): Two-shot molding rarely offers cost advantages unless the assembly process is exceptionally complex or labor-intensive
- Medium Volume (10,000-100,000 units annually): Break-even typically occurs between 20,000-50,000 units, depending on part complexity
- High Volume (over 100,000 units annually): Clear economic advantages, with per-part cost savings of 15-40% compared to assembled alternatives
The exact break-even point depends on numerous factors including part geometry, material selection, assembly complexity, and labor rates in the production region.
Cost-Per-Part Comparison Across Volumes
A typical cost-per-part comparison might look like this:
Volume de produção | Conventional Assembly Cost/Part | Two-Shot Molding Cost/Part | Cost Differential |
---|---|---|---|
10,000 units | $2.15 | $2.85 | +32% (higher cost) |
50,000 units | $1.85 | $1.70 | -8% (savings) |
100,000 units | $1.75 | $1.45 | -17% (savings) |
500,000+ units | $1.65 | $1.20 | -27% (savings) |
This example illustrates how the economics shift dramatically as volume increases, transitioning from a cost penalty at low volumes to substantial savings at higher volumes.
Industry-Specific Economic Considerations
The economic case for two-shot molding varies significantly across industries due to different priorities and manufacturing environments.
Automotive Industry Economics
The automotive sector often presents the strongest economic case for two-shot molding due to:
- High production volumes (typically 50,000+ units annually)
- Stringent quality requirements that benefit from eliminated assembly
- Emphasis on weight reduction that aligns with integrated components
- Long product lifecycles that amortize tooling costs effectively
For automotive interior components like control knobs, trim pieces, and functional assemblies, two-shot molding typically reduces total production costs by 15-25% compared to conventional methods.
Medical Device Manufacturing Considerations
The medical device industry faces a different economic equation:
- Lower production volumes for many devices
- Extremely high quality requirements with zero-defect targets
- Regulatory validation costs that must be amortized
- Higher material costs for specialty medical-grade polymers
Despite these challenges, two-shot molding often remains economically viable for medical devices due to the critical importance of eliminating assembly-related contamination risks and ensuring consistent quality.
Consumer Electronics Cost Factors
Consumer electronics present unique economic considerations:
- Short product lifecycles requiring faster tooling amortization
- High cosmetic standards benefiting from seamless material transitions
- Intense pressure for cost reduction in competitive markets
- Complex geometries that are difficult to assemble conventionally
The rapid innovation cycles in consumer electronics can sometimes work against the economics of two-shot molding, making careful volume forecasting essential before committing to this technology.
Hidden Economic Benefits
Beyond the obvious production cost savings, several less apparent economic benefits should factor into the two-shot molding decision.
Product Differentiation Value
Two-shot molding enables design features that create market advantages:
- Premium tactile qualities that increase perceived product value
- Distinctive aesthetic features that strengthen brand identity
- Ergonomic improvements that enhance user experience
- Functional benefits impossible to achieve with assembled parts
These design advantages can command price premiums or increase market share, creating economic benefits beyond direct manufacturing cost savings.
Time-to-Market Acceleration
For many products, faster market introduction creates substantial economic value:
- Compressed production timelines by eliminating assembly line setup
- Reduced validation time through simplified process verification
- Faster scaling to high volumes with less workforce expansion
- Fewer supply chain complications with fewer components
In competitive markets where being first-to-market provides lasting advantages, these time savings can overshadow pure manufacturing cost considerations.
Impacto ambiental e de sustentabilidade
The environmental benefits of two-shot molding can translate into economic advantages:
- Reduced energy consumption from eliminated assembly operations
- Lower transportation costs with fewer components to ship
- Decreased packaging materials for fewer separate parts
- Potential regulatory compliance advantages in some markets
As environmental regulations and consumer expectations evolve, these sustainability benefits increasingly translate into tangible economic value.
Mitigating Investment Risks
The substantial upfront investment in two-shot molding can be managed through several strategic approaches.
Phased Implementation Strategies
Rather than an all-or-nothing approach, companies can adopt phased implementation:
- Begin with high-volume, simple parts to build expertise
- Gradually transition more complex components as experience grows
Troubleshooting Common Two-Shot Molding Challenges
Ever watched a master chef create a perfect soufflé only to see it collapse at the last moment? The disappointment is palpable. In manufacturing, we face similar high-stakes moments when seemingly perfect two-shot molded parts develop unexpected defects that can derail production schedules and impact product quality.
Two-shot injection molding challenges require systematic troubleshooting approaches that address root causes rather than symptoms, with material compatibility issues, flash formation, incomplete filling, and bonding failures representing the most common obstacles that manufacturers must overcome to achieve consistent production quality.
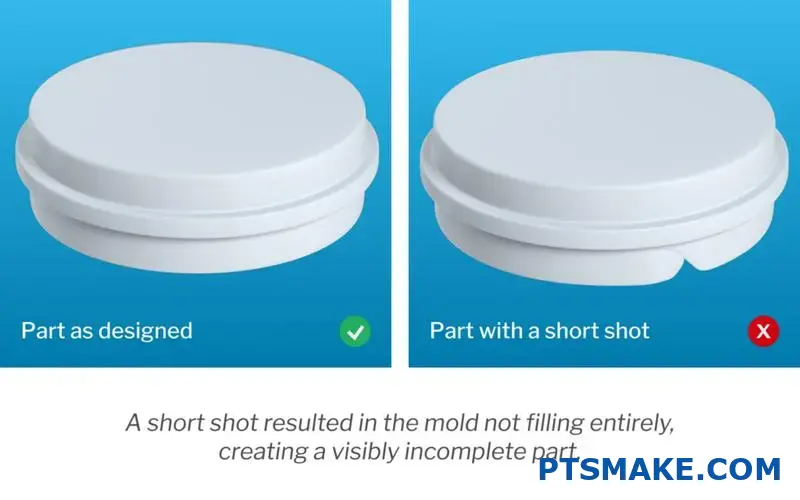
Material Incompatibility: The Foundation of Most Problems
When troubleshooting two-shot molding issues, I’ve found that material incompatibility lies at the heart of approximately 60% of persistent production problems. Understanding and addressing these compatibility challenges is essential for consistent quality.
Chemical Incompatibility Signs and Solutions
Chemical incompatibility between materials manifests in several distinct ways:
- Delamination – Materials separate at the interface after molding or during use
- Weak bonding – Parts pass visual inspection but fail under minimal stress
- Defeitos de superfície – Bubbling, discoloration, or hazing at material boundaries
- Unpredictable shrinkage – Warping or dimensional issues from incompatible shrink rates
These issues typically stem from poor material selection or insufficient processing optimization. Here’s my systematic approach to resolving chemical incompatibility:
- Verify material compatibility charts – Don’t trust generic compatibility claims; test specific material grades
- Analyze molecular compatibility – Consider polarity, surface energy, and molecular structure
- Test bond strength – Implement standardized peel or tensile tests to quantify adhesion
- Adjust material selections – Consider adhesion-modified grades specifically formulated for overmolding
- Modify process parameters – Adjust temperatures, pressures, and cooling rates to optimize bonding
In a recent project at PTSMAKE, we encountered persistent delamination between PC and TPE components. Rather than immediately changing materials, we first modified the interface temperature profile, increasing the mold temperature in the bond area by 15°C. This simple adjustment improved molecular diffusion between materials and completely resolved the delamination issue.
Thermal Incompatibility Management
Thermal incompatibility occurs when materials have significantly different processing temperature requirements or thermal expansion characteristics:
Thermal Issue | Sintomas comuns | Practical Solutions |
---|---|---|
Processing temperature mismatch | Degradation of first material during second shot | Select materials with overlapping processing windows |
Diferenças de dilatação térmica | Warping, stress cracking after cooling | Design features to accommodate differential movement |
Heat sensitivity | Discoloration, material breakdown | Use heat shields or optimize cycle times |
Cooling rate differences | Internal stress, dimensional issues | Balance cooling channels to create uniform cooling |
Most thermal compatibility issues can be resolved through proper mold temperature control. Implementing independent temperature zones for different areas of the mold allows precise thermal management at the critical interface between materials.
Flash Formation: Controlling Unwanted Material Flow
Flash—thin excess material that escapes from the mold cavity along parting lines—represents one of the most common visual defects in two-shot molding. While present in all molding processes, two-shot molding creates unique flash challenges at the interface between materials.
Identifying Flash Root Causes
Flash can stem from multiple sources in two-shot applications:
-
Mold design issues
- Insufficient clamping force at material interfaces
- Inadequate venting causing pressure buildup
- Improper parting line design at material transitions
-
Process parameter problems
- Excessive injection pressure pushing material into gaps
- Inadequate holding pressure allowing material to expand
- Incorrect material viscosity from temperature issues
-
Material-specific factors
- High-flow materials finding microscopic pathways
- Materials with extended liquid phases before solidification
- Inconsistent material preparation (moisture, contaminants)
Systematic Flash Elimination
To effectively eliminate flash in two-shot applications, I follow this methodical approach:
-
Examine flash location patterns
- Flash at parting lines indicates clamping issues
- Flash at ejector pins suggests pin fit problems
- Flash at material interfaces points to design issues
-
Verify mold condition
- Check for mold damage or wear at flash locations
- Measure actual clamping force across the mold face
- Inspect for blocked vents that increase cavity pressure
-
Optimize process parameters
- Reduce injection speed and pressure if possible
- Adjust mold temperature to control material flow
- Implement staged injection profiles to reduce pressure spikes
-
Implement design modifications if necessary
- Add overflow wells at problematic areas
- Redesign parting lines to avoid critical aesthetic areas
- Increase clamping surface area at high-pressure points
At PTSMAKE, we encountered persistent flash issues in a medical device component where TPE was overmolded onto PC. By implementing a staged injection profile that gradually reduced pressure as the cavity filled, we eliminated flash while maintaining complete filling of the complex geometry.
Incomplete Filling: Ensuring Perfect Part Formation
Incomplete filling—where material fails to reach all areas of the mold cavity—creates non-functional or aesthetically unacceptable parts. In two-shot applications, this challenge is compounded by the interaction between already-cooled first-shot material and the incoming second material.
First-Shot Filling Issues
When the first material fails to completely fill the cavity, it creates a cascade of problems:
- Missing features in the base component
- Improper substrate for the second shot
- Inconsistent cooling patterns affecting second-shot flow
- Potential short shots in both materials
To resolve first-shot filling problems:
- Optimize gate location and size – Ensure proper material flow to remote areas
- Adjust material temperature – Increase temperature to improve flow characteristics
- Modify injection speed profile – Create a dynamic speed profile matching cavity geometry
- Check for air traps – Add or enlarge vents where air may prevent complete filling
- Consider material selection – Switch to higher-flow grades if necessary
Second-Shot Specific Challenges
The second shot presents unique filling challenges because the material must flow around or alongside an already-solidified component:
- Cold substrate interference – The first shot cools the second material prematurely
- Restricted flow paths – Complex geometries create challenging flow routes
- Air entrapment – Air gets trapped between the first shot and mold surfaces
- Heat absorption – First material absorbs heat from the second material
In particularly challenging cases, we employ computer flow simulation to optimize gate locations and process conditions before cutting steel, saving substantial rework costs and accelerating development timelines.
Process Optimization for Complete Filling
For consistent filling in two-shot applications, consider these process adjustments:
Parâmetro | Ajustamento | Resultado esperado |
---|---|---|
Temperatura do molde | Increase by 10-20°C at interface areas | Prevents premature freezing of second material |
Velocidade de injeção | Increase initial speed, then moderate | Ensures material reaches extremities before cooling |
Pressão de retorno | Moderate increase (50-100 psi) | Improves material homogeneity and reduces gas content |
Pressão de retenção | Extend time by 10-20% | Compensates for cooling effects of first shot |
Material drying | Ensure complete moisture removal | Prevents viscosity issues from moisture contamination |
Addressing incomplete filling requires a holistic approach considering both design and process factors. When both are properly optimized, even the most complex two-shot geometries can be consistently filled.
Bonding Failures: Ensuring Strong Material Interfaces
The defining characteristic of successful two-shot molded parts is strong, durable bonding between materials. When this bond fails, the entire purpose of the two-shot process is compromised.
Distinguishing Bond Failure Types
Understanding the specific type of bond failure helps target appropriate solutions:
-
Adhesive failure – Complete separation at the interface with clean material surfaces
- Indicates fundamental chemical incompatibility
- Suggests improper surface energy between materials
- May result from surface contamination
-
Cohesive failure – Material tears near but not exactly at the interface
- Generally indicates good bonding but material weakness
- Can result from degraded material properties
- Sometimes caused by excessive stress concentration
-
Mixed failure – Combination of adhesive and cohesive failure
- Most common in production environments
- Suggests partial compatibility or process inconsistency
- Provides clues to both material and process improvements
Surface Preparation Optimization
The condition of the first shot’s surface dramatically impacts bond strength:
- Limpeza da superfície – Remove all mold release residues and contaminants
- Surface energy – Consider plasma or corona treatments to increase bondability
- Textura da superfície – Implement microscopic texturing to increase effective surface area
- Temperature conditioning – Optimize surface temperature before second shot
Surface preparation is particularly critical when working with challenging material combinations like polyolefins (PP/PE) with engineering thermoplastics.
Process Parameters for Enhanced Bonding
Fine-tuning process parameters can dramatically improve bonding without material changes:
-
Interface temperature management
- Increase mold temperature at interface areas
- Optimize cooling time between shots
- Consider local mold heating at critical bond areas
-
Injection parameters adjustment
- Moderate injection speed to prevent material shearing
- Optimize holding pressure to ensure intimate material contact
- Adjust back pressure to remove entrapped air
-
Timing optimization
- Minimize delay between shots when hot bonding is desired
- Allow specific cooling periods for semi-crystalline polymers
- Learn how varied surface textures can improve your product ergonomics and user experience. ↩
- Discover how proper material selection can dramatically improve product performance and durability. ↩
- Learn how material compatibility affects product durability and manufacturing costs. ↩
- Learn how proper material selection can dramatically improve bond strength and product durability. ↩