Завод литья под давлением PEEK
Являясь ведущим производителем PEEK для литья под давлением в Китае, мы поставляем высокопроизводительные полимерные решения для аэрокосмической, медицинской и промышленной отраслей. Опыт работы более 20 лет, сертификат ISO 9001.
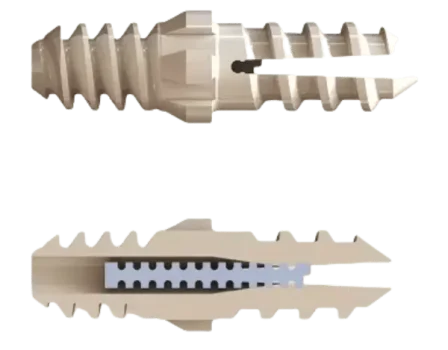
Высокопроизводительные материалы PEEK
Прецизионное литье сложных деталей
Быстрый оборот и глобальная доставка
Машины от от 30 тонн до 1 600 тонн






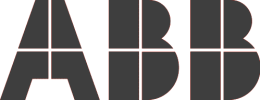

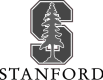
Что говорят наши клиенты
Если вы хотите проверить нашу репутацию среди клиентов в вашем регионе, обращайтесь к нам - мы с удовольствием свяжем вас с ними и поделимся соответствующими примерами из практики.
8 Основные промышленные применения решений для литья под давлением из ПЭЭК
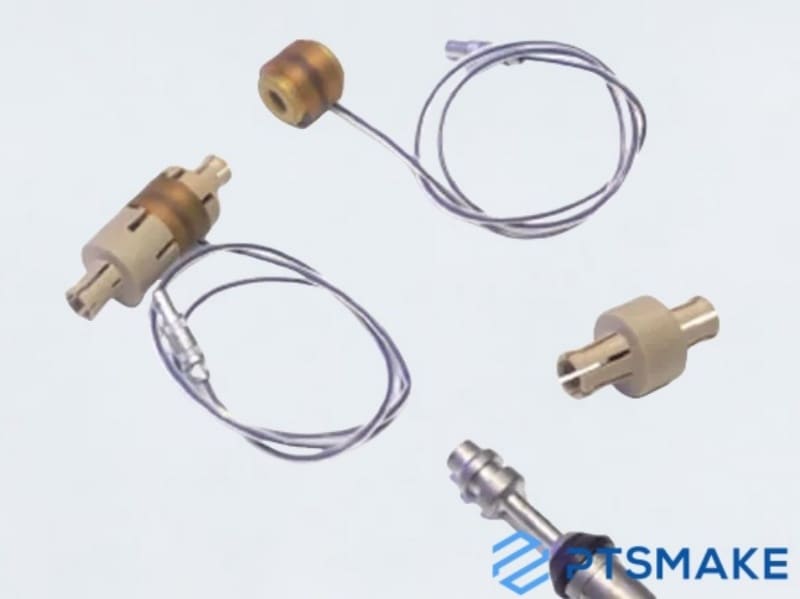
Аэрокосмические компоненты
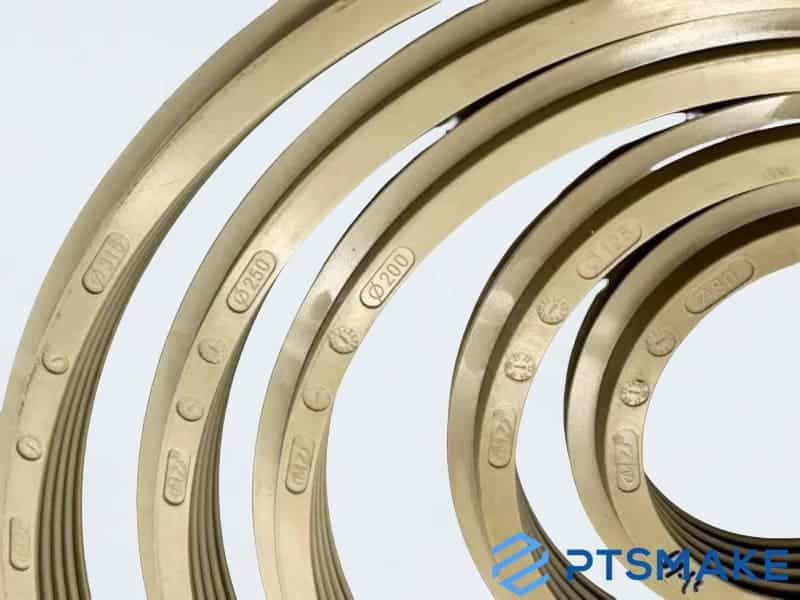
Автомобильные уплотнения
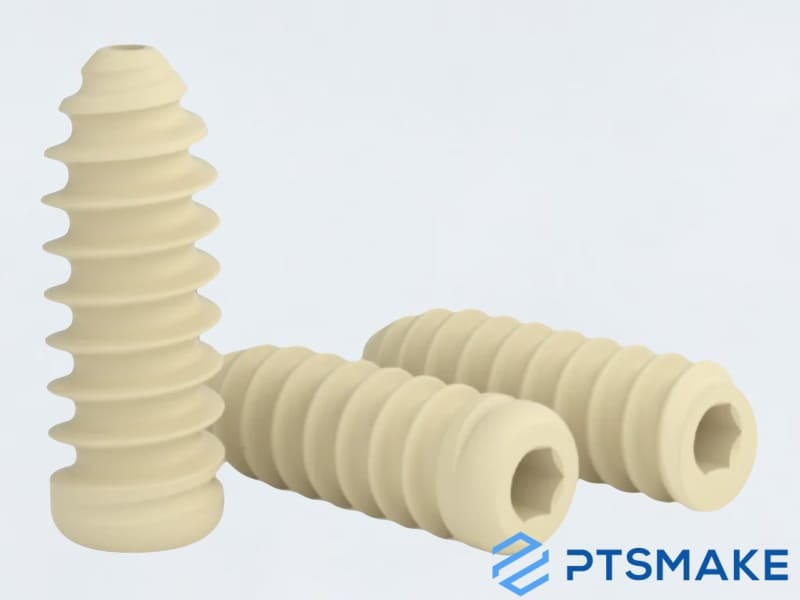
Медицинские винты
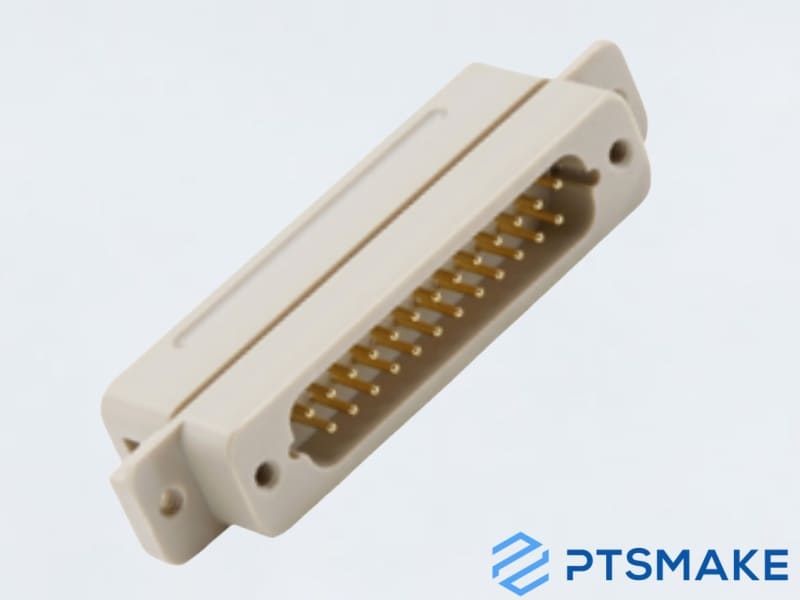
Разъемы для электроники
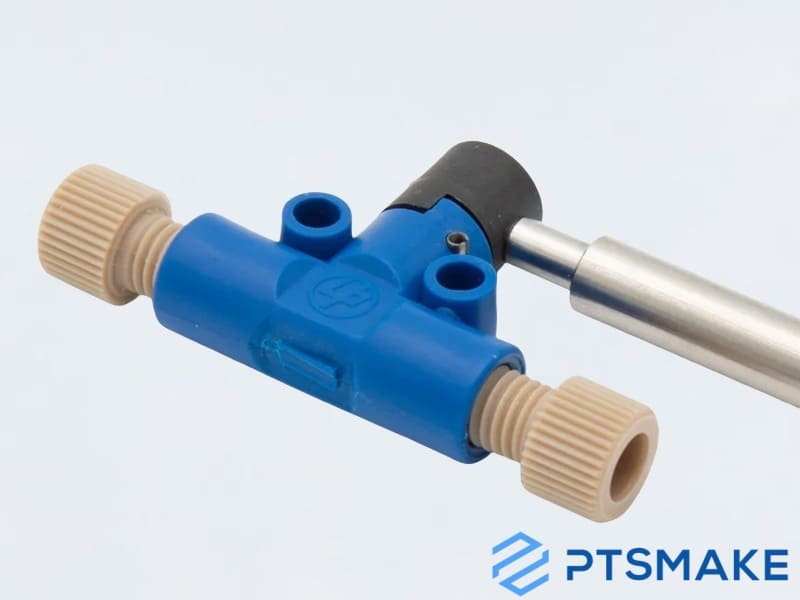
Нефтяные и газовые клапаны
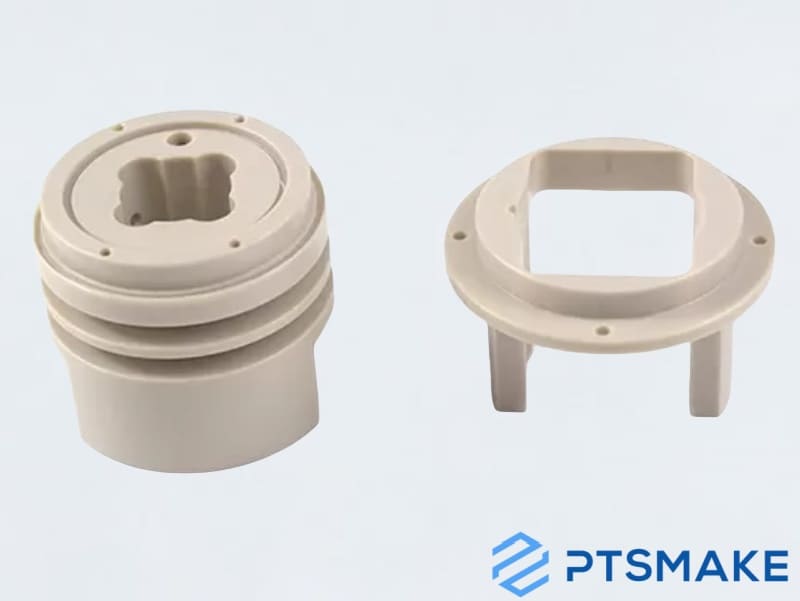
Запчасти для робототехники
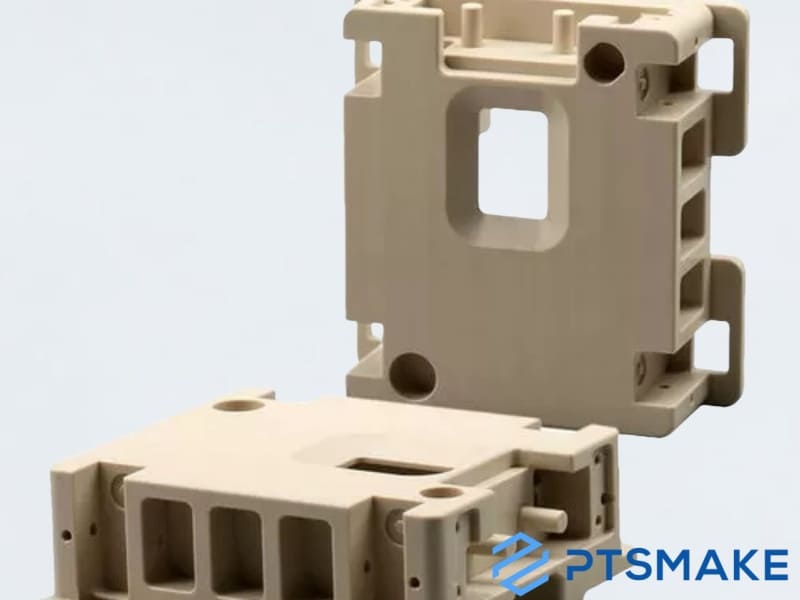
Промышленные корпуса
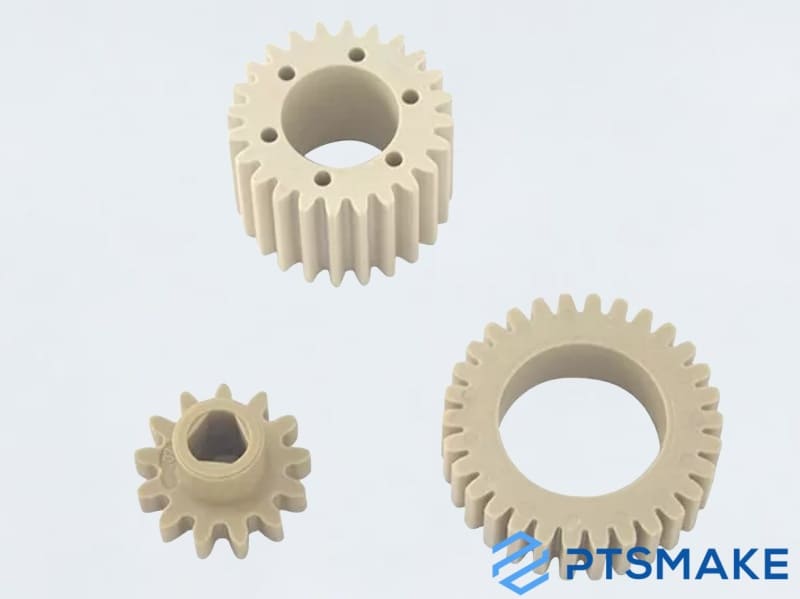
Промышленные шестерни
Почему стоит выбрать PTSMAKE для литья под давлением PEEK?
Компания PTSMAKE имеет более чем 20-летний опыт литья под давлением и предлагает решения, которым доверяют такие мировые бренды, как BMW и Huawei.
Используя передовые станки, мы обеспечиваем точность размеров и оптимизируем конструкции, снижая производственные затраты до 30%.
Наши 50 с лишним современных формовочных машин обеспечивают 15-дневные циклы создания прототипов и ускоренные сроки производства 30%.
Наши трехступенчатые проверки качества поддерживают уровень брака ниже 0,2% с полной прослеживаемостью каждой формованной детали.
Контроль качества при литье под давлением PEEK: Как мы обеспечиваем точность и надежность
- В компании PTSMAKE контроль качества является основой наших услуг по литью под давлением PEEK. С 2002 года мы создали свою репутацию благодаря превышению строгих отраслевых стандартов для клиентов из аэрокосмической, медицинской и автомобильной промышленности. Для таких высокопроизводительных материалов, как PEEK, даже незначительные дефекты могут привести к поломке детали. Именно поэтому мы применяем 6-ступенчатый процесс контроля качества, чтобы исключить риски на каждом этапе.
- Шаг 1: Сертификация материалов и предварительная обработка
Мы поставляем гранулы PEEK только от поставщиков, прошедших сертификацию ISO. Каждая партия проходит FTIR-тестирование для проверки химического состава и содержания влаги. Перед формовкой мы предварительно высушиваем материалы, чтобы предотвратить образование пузырей или коробление, что очень важно для сохранения механической стабильности PEEK.
- Шаг 2: Разработка и проверка прецизионных пресс-форм
Наши инженеры используют моделирование Moldflow для прогнозирования поведения потока и напряжений при охлаждении. Все пресс-формы обрабатываются на собственном производстве с ЧПУ, с допусками ±0,005 мм. Перед началом серийного производства мы проводим 50+ пробных испытаний каждой пресс-формы, измеряя размеры и шероховатость поверхности в соответствии с вашими спецификациями CAD.
- Шаг 3: Мониторинг процессов в режиме реального времени
Во время формовки датчики отслеживают температуру (±5°C), давление (разрешение 0,7 МПа) и время цикла. Если параметры смещаются, наша система автоматически приостанавливает производство и предупреждает технический персонал. Это позволяет предотвратить такие дефекты, как раковины или неполное заполнение - распространенные болевые точки в проектах PEEK.
- Шаг 4: Проверка после формовки
Первый контроль деталей включает в себя измерения на КИМ и испытания на растяжение. Мы проверяем 100% деталей на наличие визуальных дефектов под 10-кратным увеличением. Для заказов медицинского класса мы проводим испытания на биосовместимость в соответствии с протоколами ISO 10993.
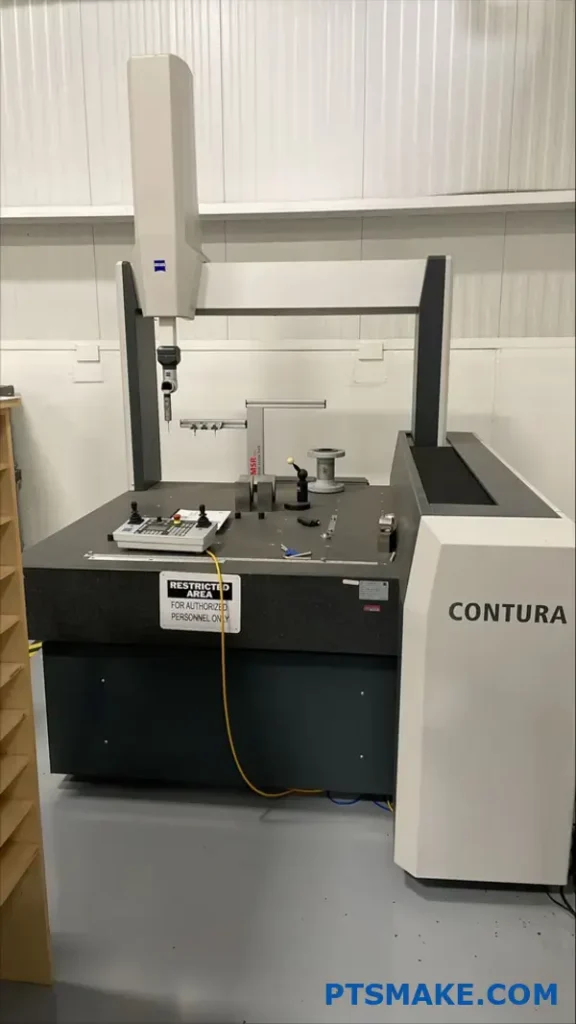
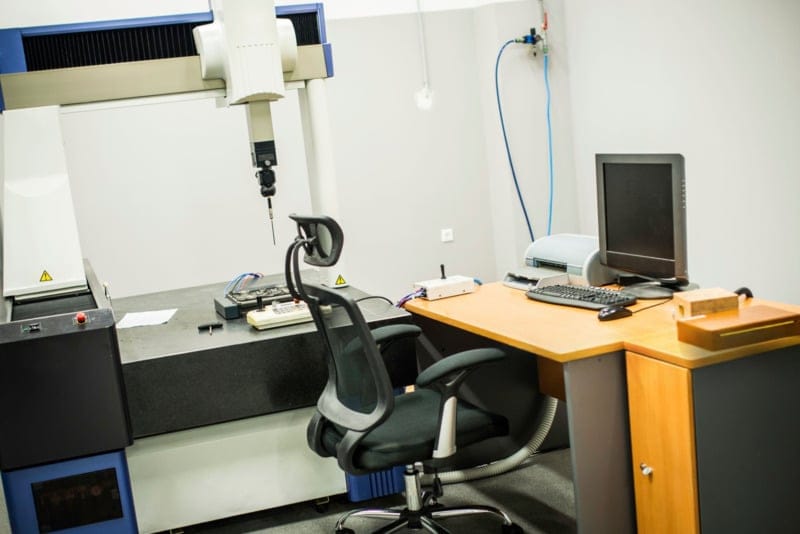
- Шаг 5: Прослеживаемость и документация
Каждая партия поставляется с досье качества: сертификатами на материалы, отчетами о проверках и журналами технологических процессов. Наша облачная платформа позволяет отслеживать состояние производства 24 часа в сутки 7 дней в неделю и заранее решать проблемы, связанные с задержками поставок.
- Шаг 6: Непрерывное совершенствование
После поставки мы анализируем ваши отзывы, чтобы усовершенствовать процессы. Более 80% клиентов сообщают о сокращении количества правок на 30% после перехода на PTSMAKE - доказательство нашей приверженности долгосрочным партнерским отношениям.
- Имея 4 дочерних предприятия и таких клиентов, как Huawei и BMW, мы упрощаем сложные цепочки поставок. Наши менеджеры проектов, расположенные в США, отвечают на запросы в течение 2 часов, обеспечивая согласованность между дизайном, производством и логистикой.
Нам требовались детали из ПЭЭК с ультратонкими стенками для медицинского устройства. Компания PTSMAKE не только обеспечила допуски 0,2 мм, но и выполнила поставку за 12 дней. Их инженеры даже предложили лучшую конструкцию охлаждения, что позволило нам сэкономить время цикла 20%. Ноль дефектов после более 10 тысяч выстрелов!
Марк Салливан, инженер по медицинскому оборудованию, США".
Лучшие материалы, используемые при литье под давлением из полиэфирэфиркетона
Дева PEEK
PEEK, армированный стекловолокном
Износостойкий PEEK
PEEK, армированный углеродным волокном
ESD PEEK (электростатический разряд PEEK)
Минералонаполненный полиэфирэфиркетон
Типичные сроки выполнения работ по литью под давлением из ПЭЭК
Что ожидать от сроков литья под давлением PEEK
- Сроки изготовления изделий из полиэфирэфиркетона под давлением зависят от сложности проекта, объема заказа и требований к конструкции. Для простых геометрических деталей со стандартной оснасткой может потребоваться 4-6 недель. Сложные детали, требующие индивидуальных форм или жестких допусков, часто занимают 6-8 недель. В компании PTSMAKE мы оптимизируем процессы для соблюдения сроков без ущерба для точности.
- На сроки влияют такие факторы, как доступность материалов, пересмотр конструкции пресс-формы и проверка качества. Наш более чем 20-летний опыт в области точного производства помогает нам предвидеть задержки. Мы поддерживаем складские запасы смол PEEK и используем передовую обработку с ЧПУ для ускорения создания пресс-форм. Это сокращает время изготовления на 15-20% по сравнению со средними показателями по отрасли.
- Мы уделяем первостепенное внимание прозрачности. Клиенты получают еженедельные обновления и доступ к панелям управления проектом в режиме реального времени. В случае срочных потребностей наша служба быстрого прототипирования предоставляет образцы за 7-10 дней. Такая гибкость помогает таким отраслям, как аэрокосмическая промышленность и медицинское оборудование, где скорость и точность имеют решающее значение.
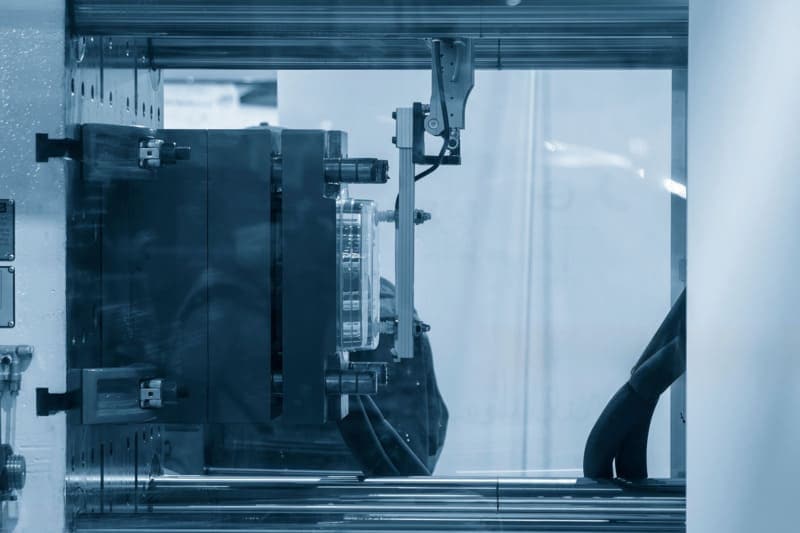
8 ключевых этапов производства литья под давлением из полиэфирэфиркетона
Откройте для себя точный процесс, лежащий в основе высококачественных деталей из PEEK для литья под давлением в аэрокосмической, медицинской и робототехнической промышленности.
1. Подготовка материалов
2. Предварительная сушка
3. Установка пресс-формы
4. Параметры машины
5. Процесс впрыска
6. Фаза охлаждения
7. Постобработка
8. Проверка качества
Запросите индивидуальное предложение сегодня
Получите точную оценку вашего проекта уже сегодня. Позвольте нам помочь вам удовлетворить ваши точные требования.
Экономически эффективные решения для литья под давлением PEEK: 7 проверенных стратегий снижения затрат
1. Оптимизация материалов
2. Эффективность конструкции пресс-формы
3. Автоматизация процессов
4. Закупка сыпучих материалов
5. Вторичные операции
6. Упрощение конструкции
7. Масштабируемое производство
Варианты персонализации для литья под давлением из полиэфирэфиркетона
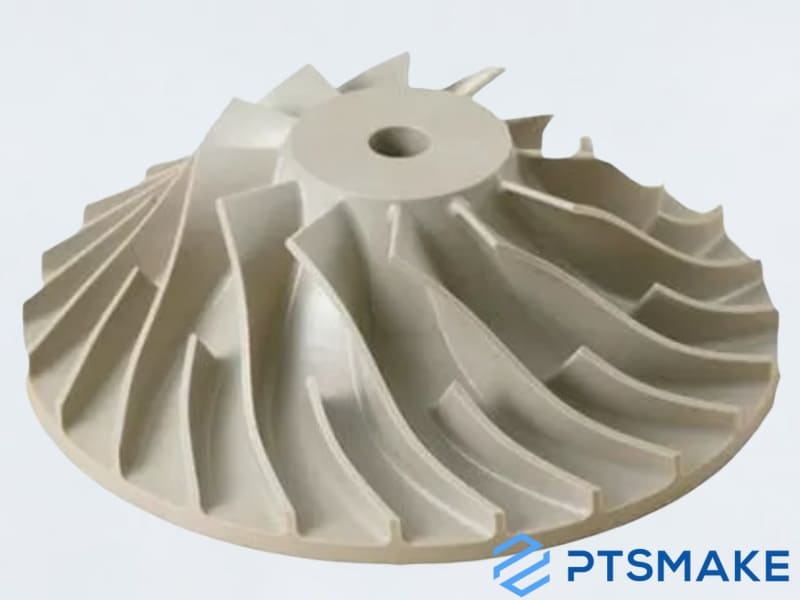
Истории успеха литья под давлением PEEK в производстве B2B
Высокопроизводительные компоненты медицинского оборудования
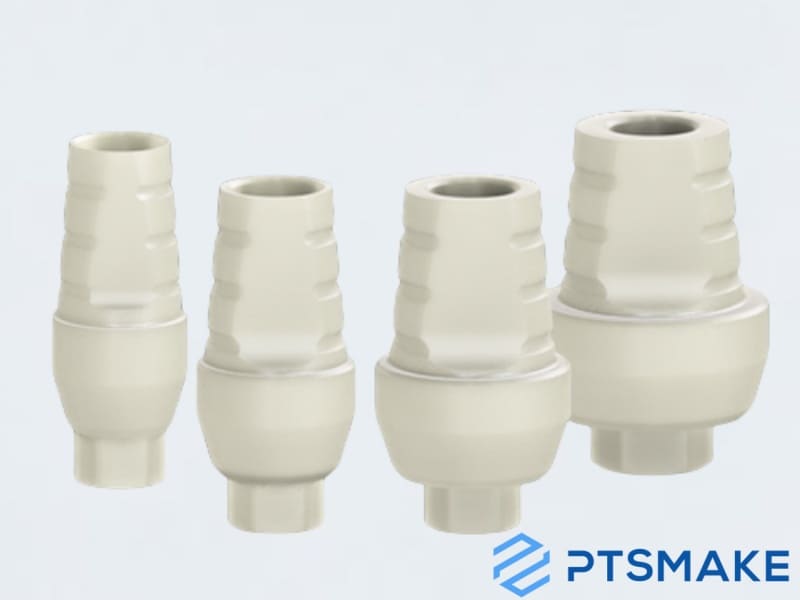
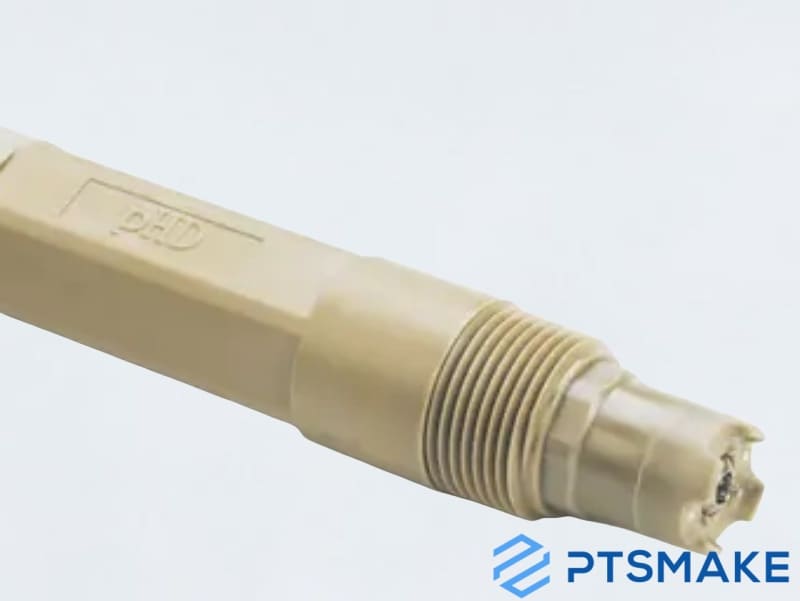
Корпус автомобильного датчика для экстремальных условий
Изоляция разъемов для аэрокосмической техники
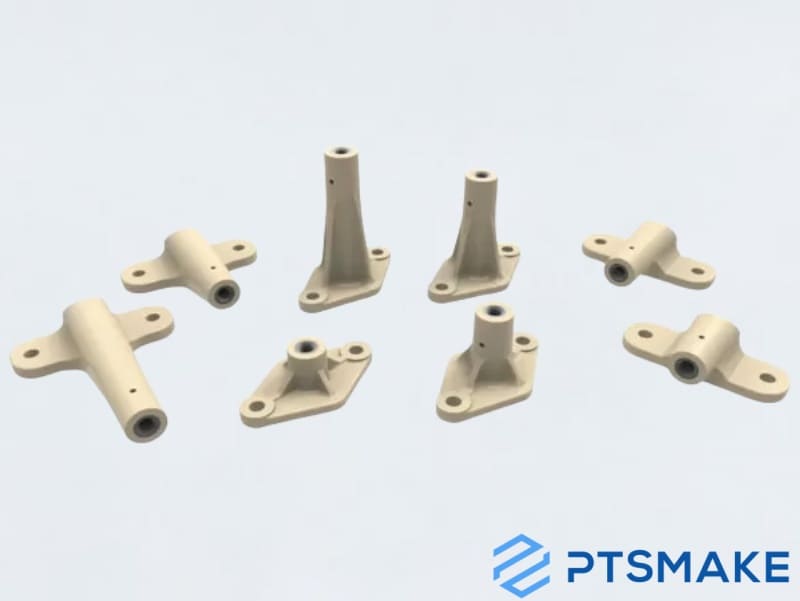
Свяжитесь с экспертом по литью под давлением Peek сегодня!
Мы с нетерпением ждем возможности работать с вами и внести свой вклад в успех вашего проекта.