Приходилось ли вам сталкиваться с проблемой обработки деталей из нержавеющей стали, которые постоянно не соответствуют техническим требованиям? Многие производители сталкиваются с этой проблемой ежедневно, имея дело с износом инструмента, плохим качеством обработки поверхности и неточностью размеров. Сложность работы с этим требовательным материалом может привести к дорогостоящим задержкам производства и проблемам с качеством, которые влияют на итоговый результат.
Обработка нержавеющей стали - это специализированный производственный процесс, который включает в себя резку, придание формы и формовку нержавеющей стали с помощью прецизионных инструментов и оборудования. Этот процесс требует специальных методов, инструментов и опыта для достижения точных результатов при сохранении коррозионностойких свойств материала.
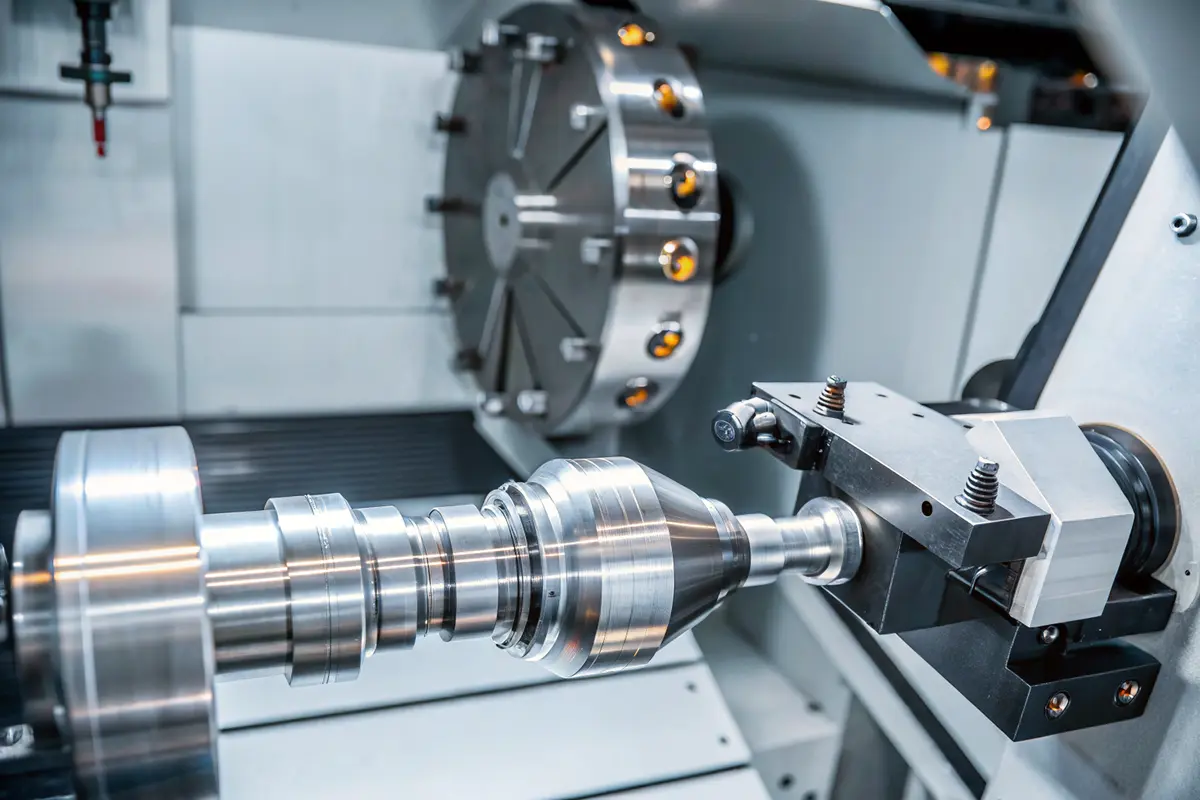
Понимание основ нержавеющей стали
Нержавеющая сталь - это замечательный материал, содержащий не менее 10,5% хрома, образующего защитный оксидный слой, который делает ее очень устойчивой к коррозии. При обработке нержавеющей стали мы должны учитывать ее уникальные свойства:
Недвижимость | Характеристика | Влияние на обработку |
---|---|---|
Твердость | Высокая степень упрочнения | Требуется определенная скорость резки |
Теплопроводность | Плохое рассеивание тепла | Требуются правильные стратегии охлаждения |
Прочность на разрыв | Высокий уровень прочности | Требуется надежная оснастка |
Отделка поверхности | Жевательная природа | Требуются острые инструменты |
Основные методы обработки
За время работы в PTSMAKE я убедился, что успешная обработка нержавеющей стали зависит от нескольких ключевых методов:
Фрезерование с ЧПУ
- Фрезерование плоских поверхностей
- Концевые фрезы для сложных геометрических форм
- Фрезерование профилей для контурных форм
Токарная обработка с ЧПУ
- Наружное точение для цилиндрических форм
- Внутреннее сверление отверстий
- Нарезание резьбы для крепежа
Отраслевые применения
Обработанные детали из нержавеющей стали играют важнейшую роль в различных отраслях:
Медицинская промышленность
- Хирургические инструменты
- Компоненты имплантатов
- Корпуса для медицинского оборудования
Аэрокосмическая промышленность
- Компоненты двигателя
- Структурные элементы
- Крепежные системы
Пищевая промышленность
- Технологическое оборудование
- Контейнеры для хранения
- Смешивание компонентов
Критические параметры успеха
Ключ к достижению точности при обработке нержавеющей стали лежит в контроле этих важнейших параметров:
Скорость резки
- Более низкие скорости по сравнению с углеродистой сталью
- Постоянная скорость подачи
- Правильная глубина реза
Выбор инструмента
- Твердосплавные инструменты для большинства применений
- Керамические инструменты для высокоскоростных операций
- Инструменты с покрытием для повышения износостойкости
Общие проблемы и решения
Работа с нержавеющей сталью сопряжена с рядом трудностей, требующих особых решений:
Управление теплом
- Решение: Внедрите правильные стратегии охлаждения
- Используйте системы охлаждения под высоким давлением
- Поддерживайте оптимальную скорость резки
Износ инструмента
- Решение: Выберите подходящие материалы для инструментов
- Регулярный контроль состояния инструмента
- Внедрение правильных графиков смены инструментов
Отделка поверхности
- Решение: Используйте острые инструменты с надлежащим покрытием
- Поддерживайте постоянные параметры резки
- Применяйте соответствующие смазочно-охлаждающие жидкости
Меры контроля качества
Чтобы обеспечить стабильное качество обработки нержавеющей стали, мы внедряем:
Контроль размеров
- Регулярные измерения на КИМ
- Измерение в процессе производства
- Протоколы окончательной проверки
Проверка качества поверхности
- Измерения шероховатости
- Визуальный осмотр
- Проверка целостности материала
Экономические соображения
Экономическая эффективность обработки нержавеющей стали зависит от:
Выбор материала
- Класс, соответствующий применению
- Оптимизация размера запасов
- Требования к сертификации материалов
Планирование производства
- Оптимизация размера партии
- Управление сроком службы инструмента
- Сокращение времени установки
Управление качеством
- Требования к осмотру
- Потребности в документации
- Расходы на сертификацию
Понимая эти фундаментальные аспекты обработки нержавеющей стали, производители могут лучше подготовиться к трудностям и возможностям, которые открывает этот процесс. В компании PTSMAKE мы разработали комплексные стратегии для преодоления этих трудностей, сохраняя при этом стандарты качества и экономическую эффективность наших операций по обработке.
Почему нержавеющая сталь трудно поддается обработке?
Каждому производителю известна головная боль, связанная с обработкой нержавеющей стали. Я видел бесчисленное количество отложенных проектов и разрушенных инструментов из-за того, что команды недооценили ее сложности. Уникальные свойства материала делают его крепостью против обычных подходов к обработке, что приводит к чрезмерному износу инструмента и задержкам производства.
Трудности обработки нержавеющей стали обусловлены ее высокой прочностью на разрыв, склонностью к упрочнению и низкой теплопроводностью. Эти свойства приводят к быстрому износу инструмента, чрезмерному нагреву и сложному образованию стружки в процессе обработки.
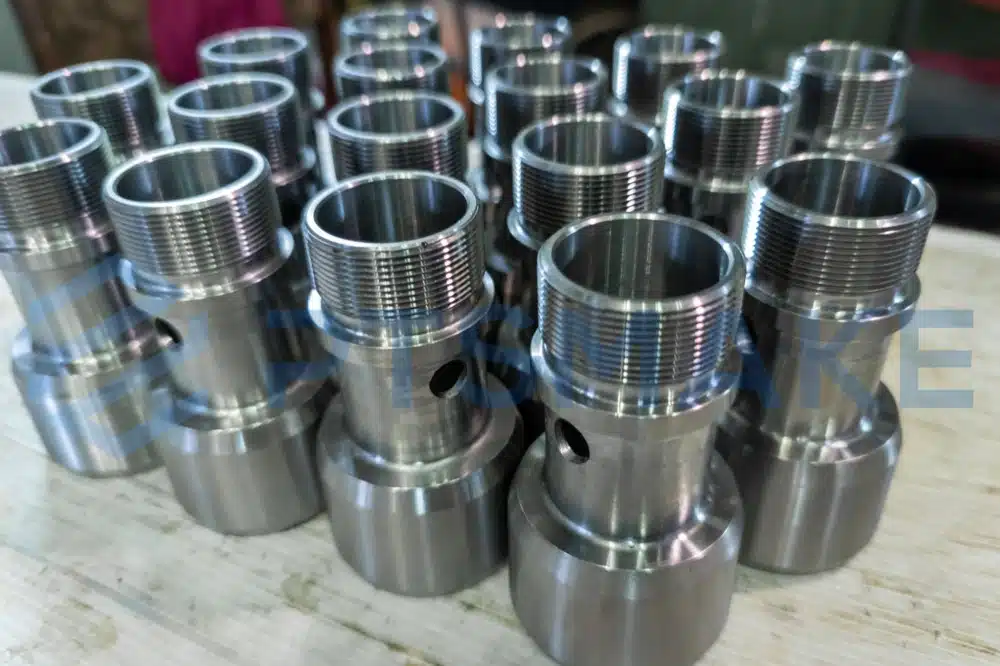
Понимание упрочнения работы
Закалка - это, пожалуй, самая серьезная проблема при обработке нержавеющей стали. Во время операций резания поверхность материала становится тверже из-за пластической деформации. Это создает порочный круг - чем тверже становится поверхность, тем большее усилие требуется для ее резки, что, в свою очередь, приводит к еще большему упрочнению.
Эффект закалки на работе | Влияние на обработку |
---|---|
Упрочнение поверхности | Повышенный износ инструмента |
Чувствительность к скорости деформации | Переменные усилия резания |
Изменения микроструктуры | Непредсказуемое поведение материала |
Выработка тепла | Сокращение срока службы инструмента |
Вопросы теплопроводности
Низкая теплопроводность нержавеющей стали создает значительные проблемы с управлением нагревом. В отличие от алюминия или обычной стали, нержавеющая сталь удерживает большую часть тепла, выделяемого в процессе обработки. Такая концентрация тепла приводит к:
- Ускоренный износ инструмента
- Формирование края при наращивании
- Проблемы с точностью размеров
- Низкое качество обработки поверхности
Требуется высокое усилие резания
Высокая прочность и вязкость нержавеющей стали требуют больших усилий резания по сравнению с другими материалами. Это требование влияет на:
Фактор | Воздействие |
---|---|
Потребляемая мощность | Более высокие затраты на электроэнергию |
Стабильность машины | Повышенный риск вибрации |
Выбор инструмента | Необходимость в более мощных инструментах |
Скорость производства | Необходимы более низкие скорости подачи |
Механизмы износа инструмента
Сочетание закалки и выделения тепла создает множество механизмов износа инструмента:
- Абразивный износ от твердых частиц
- Износ клея из-за прилипания материала
- Диффузионный износ при высоких температурах
- Износ насечек на глубине резания
Проблемы, связанные с обработкой поверхности
Для получения качественной отделки поверхности из нержавеющей стали необходимо тщательно продумать:
Параметр | Рассмотрение |
---|---|
Скорость резки | Должно быть сбалансировано производство тепла |
Скорость подачи | Влияет на шероховатость поверхности |
Геометрия инструмента | Влияет на образование стружки |
Применение охлаждающей жидкости | Критически важно для управления теплом |
Проблемы с управлением микросхемами
Нержавеющая сталь склонна к образованию длинных, нитевидных стружек, которые могут:
- Инструменты для обхвата
- Повреждение поверхностей заготовок
- Создают угрозу безопасности
- Снижение эффективности обработки
Различия в классе материала
Различные марки нержавеющей стали представляют собой разные проблемы при обработке:
Тип класса | Конкретные задачи |
---|---|
Аустенитные | Высочайшая рабочая закалка |
Мартенситная | Проблемы с износом инструмента |
Ферритные | Лучшая обрабатываемость |
Дуплекс | Чрезвычайная прочность |
Критические параметры процесса
Успех обработки нержавеющей стали зависит от контроля нескольких ключевых параметров:
- Выбор скорости резки
- Оптимизация скорости подачи
- Управление глубиной реза
- Проектирование геометрии инструмента
- Реализация стратегии использования охлаждающей жидкости
Экономические последствия
Сложность обработки нержавеющей стали напрямую влияет на стоимость производства:
- Повышенная частота замены инструмента
- Увеличение времени обработки
- Большее потребление энергии
- Более частое обслуживание оборудования
- Более высокие требования к квалифицированным операторам
Рекомендации по выбору инструмента
Правильный выбор инструмента имеет решающее значение и должен учитывать:
Фактор | Требование |
---|---|
Тип покрытия | Тепло- и износостойкость |
Материал подложки | Прочность и твердость |
Подготовка кромки | Стабильность и прочность |
Геометрия | Контроль стружки и силы резания |
По моему опыту работы в PTSMAKE, для успешной обработки нержавеющей стали требуется всестороннее понимание этих проблем и систематический подход к их решению. Ключ к успеху лежит в тщательном планировании, правильном выборе инструмента и точном контроле параметров обработки. Несмотря на то что материал представляет собой серьезную проблему, понимание этих основополагающих аспектов помогает добиться успешных результатов при обработке нержавеющей стали.
Какие распространенные марки нержавеющей стали используются для обработки?
Выбор подходящей марки нержавеющей стали для обработки может оказаться непосильной задачей. Поскольку существует множество марок, каждая из которых имеет свои свойства, многие производители пытаются определить, какая марка лучше всего подходит для конкретного применения. Неправильный выбор может привести к увеличению стоимости инструмента, увеличению времени производства и ухудшению качества деталей.
Наиболее распространенными марками нержавеющей стали, используемыми в механической обработке, являются 303, 304, 316 и 17-4 PH. Каждая марка обладает уникальными характеристиками, которые делают их подходящими для различных областей применения, при этом 303-я марка является самой обрабатываемой, а 316-я - самой коррозионностойкой.
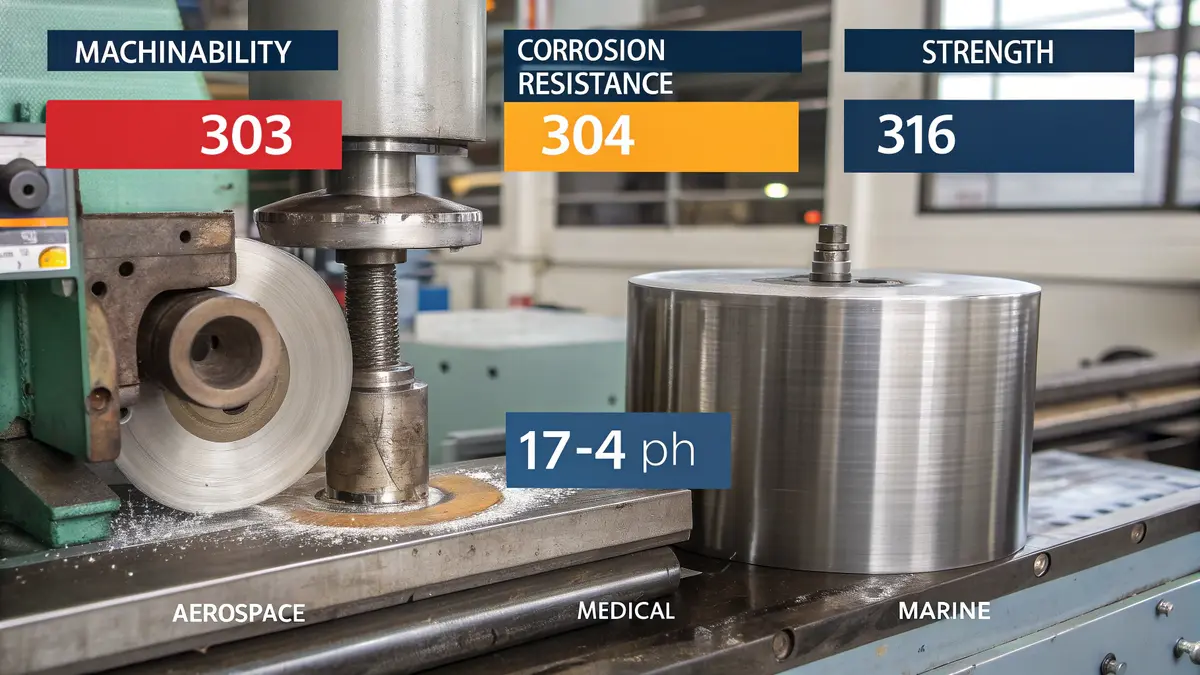
Понятие о нержавеющей стали 303
Нержавеющая сталь 303 часто считается лучшим выбором для механической обработки. Ее превосходная обрабатываемость обусловлена добавлением серы, которая способствует разрушению стружки при резке. Я обнаружил, что 303 обычно обрабатывается на 40% быстрее, чем 304, что делает ее идеальной для крупносерийного производства.
Основные характеристики 303 включают:
- Содержание серы: 0,15% минимум
- Отличная обрабатываемость
- Хорошая коррозионная стойкость
- Снижение стоимости детали за счет более быстрой обработки
Однако добавление серы несколько снижает его коррозионную стойкость по сравнению с 304. Для большинства применений этот компромисс является приемлемым, если учесть значительное улучшение обрабатываемости.
Универсальность нержавеющей стали 304
304 - наиболее широко используемая марка нержавеющей стали во всем мире, и на то есть веские причины. Она обеспечивает превосходный баланс коррозионной стойкости, прочности и умеренной обрабатываемости. Хотя ее не так легко обрабатывать, как 303, она обеспечивает превосходную коррозионную стойкость и лучшую свариваемость.
Сравнение ключевых свойств:
Недвижимость | 304 Рейтинг | Общие приложения |
---|---|---|
Устойчивость к коррозии | Превосходно | Оборудование для пищевой промышленности |
Прочность | Хорошо | Медицинские приборы |
Обрабатываемость | Умеренный | Химическая обработка |
Свариваемость | Превосходно | Кухонное оборудование |
Нержавеющая сталь 316: Борец с коррозией
Нержавеющая сталь 316 содержит молибден, который значительно повышает ее коррозионную стойкость, особенно к хлоридам. Хотя она сложнее в обработке, чем 303 или 304, ее превосходные свойства делают ее незаменимой для конкретных применений.
Важные соображения для 316:
- Более высокая стоимость материалов
- Требуется более низкая скорость резки
- Превосходная химическая стойкость
- Идеально подходит для морской среды
Сила нержавеющей стали 17-4 PH
Нержавеющая сталь 17-4 PH (закалка осадком) обладает уникальными преимуществами благодаря возможности термообработки. По моему опыту работы с клиентами из аэрокосмической отрасли, эта марка имеет решающее значение, когда требуется высокая прочность и умеренная коррозионная стойкость.
Наконечники для обработки 17-4 PH:
- Используйте острые инструменты из твердого сплава с покрытием
- Поддерживать жесткую настройку и оснастку
- Обеспечьте достаточное охлаждение
- Учитывайте состояние материала (обработанный раствором или состаренный)
Лучшие методы обработки для различных марок
Для достижения оптимальных результатов каждый сорт требует определенных параметров обработки:
Класс | Скорость резки (SFM) | Скорость подачи | Требование к охлаждающей жидкости |
---|---|---|---|
303 | 400-500 | Высокий | Умеренный |
304 | 300-400 | Средний | Heavy |
316 | 250-350 | Средний | Heavy |
17-4 PH | 200-300 | Низкий | Heavy |
Соображения по выбору материала
При выборе марок нержавеющей стали для обработки учитывайте следующие факторы:
- Среда конечного использования
- Требуемые механические свойства
- Объем производства
- Ограничения по стоимости
- Требования к чистоте поверхности
Для критически важных применений я всегда рекомендую проводить испытания материалов до начала производства. Такой подход уберег многих клиентов от дорогостоящих ошибок и обеспечивает оптимальные характеристики в конечном применении.
Анализ эффективности затрат
Общая стоимость обработки различных марок включает в себя не только цены на материалы:
Класс | Стоимость материала | Время обработки | Срок службы инструмента | Общая стоимость |
---|---|---|---|---|
303 | Умеренный | Низкий | Длинный | Самый низкий |
304 | Умеренный | Средний | Средний | Умеренный |
316 | Высокий | Высокий | Короткие | Самый высокий |
17-4 PH | Очень высокий | Средний | Средний | Высокий |
В заключение следует отметить, что выбор подходящей марки нержавеющей стали требует соблюдения баланса между обрабатываемостью, требованиями к производительности и стоимостью. Понимание этих распространенных марок и их характеристик поможет обеспечить успешную обработку и оптимальные характеристики деталей.
Каковы основные технологии обработки нержавеющей стали?
Обработка нержавеющей стали может стать настоящей проблемой для многих производителей. Я видел множество проектов, которые были отложены или сорваны из-за неправильных методов обработки, что привело к износу инструмента, плохой обработке поверхности и неточностям в размерах. Высокая прочность, склонность к закалке и низкая теплопроводность этого материала делают его особенно требовательным к правильной обработке.
Основные методы обработки нержавеющей стали включают фрезерование с ЧПУ, точение с ЧПУ, сверление и шлифование. Успех зависит от выбора правильных параметров резания, использования подходящего инструмента и поддержания оптимальных условий резания с помощью подходящих стратегий охлаждения.
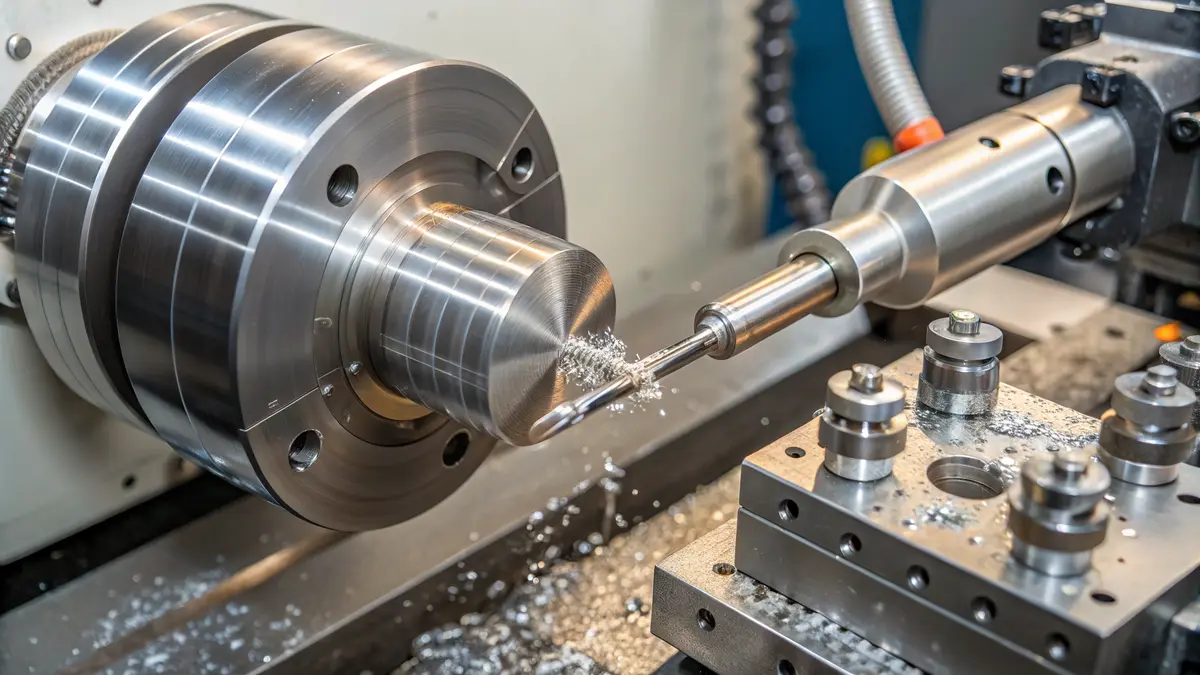
Технологии фрезерования с ЧПУ для нержавеющей стали
Когда речь идет о фрезеровании нержавеющей стали с ЧПУ, правильный подход имеет решающее значение. В компании PTSMAKE мы используем эти проверенные параметры для достижения оптимальных результатов:
- Скорость резки: 100-150 футов поверхности в минуту (SFM) для аустенитной нержавеющей стали
- Скорость подачи: 0,004-0,008 дюйма на зуб
- Глубина реза: Не более 0,125 дюйма для черновой обработки, 0,02 дюйма для чистовой обработки
Фрезерование с подъемом, а не обычное фрезерование, уменьшает закалку и продлевает срок службы инструмента. Мы всегда обеспечиваем жесткую фиксацию инструмента и минимальный выступ инструмента для предотвращения болтанки.
Токарные работы с ЧПУ
Токарная обработка нержавеющей стали требует особого внимания к этим ключевым факторам:
Параметр | Рекомендуемый диапазон | Примечания |
---|---|---|
Скорость резки | 250-350 SFM | Более высокая для отделки |
Скорость подачи | 0,005-0,015 ипр | Зависит от качества обработки поверхности |
Глубина среза | 0,040-0,200 дюймов | Зависит от материала |
Геометрия инструмента | Угол разгрузки 5-15° | Рекомендуется положительная граблина |
Техника бурения
Сверление нержавеющей стали представляет собой уникальную задачу. Мы следуем этим рекомендациям:
- По возможности используйте укороченные сверла
- Начните с пилотных отверстий для более глубоких отверстий
- Поддерживайте постоянную скорость подачи
- Обеспечьте достаточное давление смазочно-охлаждающей жидкости
Рекомендуемые параметры сверления:
- Скорость: 20-30 SFM
- Подача: 0,002-0,004 дюйма на оборот
- Циклы пекового сверления для отверстий глубиной более 3x диаметров
Особенности шлифования поверхности
Шлифование поверхности имеет решающее значение для достижения жестких допусков. Наш подход включает в себя:
Выбор колеса
- Круги из оксида алюминия для общего назначения
- Круги из КНБ для крупносерийного производства
- Зернистость 60-80 для черновой обработки
- Зернистость 120-150 для финишной обработки
Параметры измельчения
- Скорость вращения колеса: 5000-6000 футов поверхности в минуту
- Скорость перемещения стола: 50-60 футов в минуту
- Глубина резки: 0,0005-0,001 дюйма за проход
Выбор и применение смазочно-охлаждающих жидкостей
Правильно подобранная смазочно-охлаждающая жидкость необходима для обработки нержавеющей стали:
Типы смазочно-охлаждающих жидкостей
- Водорастворимые масла общего назначения
- Прямые масла для тяжелых условий эксплуатации
- Синтетические жидкости для высокоскоростных применений
Методы применения
- Заливное охлаждение для общих операций
- Сквозное охлаждение для глубоких отверстий
- Нанесение тумана для легкой стрижки
Выбор и управление инструментами
Выбор правильных инструментов существенно влияет на успех обработки:
Инструментальные материалы
- Твердые сплавы с покрытием TiAlN
- Керамические инструменты для высокоскоростных операций
- Инструменты из быстрорежущей стали для простых операций
Управление сроком службы инструмента
- Регулярный контроль износа
- Заранее установленные интервалы замены инструмента
- Правильное хранение и обращение с инструментами
Стратегии оптимизации процессов
Для достижения оптимальных результатов мы используем эти стратегии:
Оптимизация параметров
- Начните с консервативных мер и постепенно увеличивайте
- Контролируйте износ инструмента и качество обработки поверхности
- Корректировка в зависимости от фактических результатов
Контроль качества
- Регулярные проверки размеров
- Контроль качества поверхности
- Контроль износа инструмента
Эффективность производства
- Минимизация времени установки
- Оптимизация траекторий движения инструмента
- Сократите время, затрачиваемое на обработку.
Применяя эти методы и уделяя пристальное внимание деталям, мы неизменно добиваемся превосходных результатов в обработке нержавеющей стали. Ключевым моментом является понимание того, как каждый параметр влияет на результат, и внесение соответствующих корректировок на основе обратной связи в реальном времени с процессом обработки.
Помните, что успешная обработка нержавеющей стали требует сбалансированного подхода. Хотя высокая производительность важна, она не должна идти в ущерб сроку службы инструмента или качеству деталей. Регулярный контроль и регулировка параметров обработки обеспечивают оптимальные результаты и стабильное качество.
Какие инструменты и оборудование лучше всего подходят для обработки нержавеющей стали?
Обработка нержавеющей стали представляет собой серьезную проблему в наших производственных процессах. Многие мастера сталкиваются с проблемой быстрого износа инструмента, плохой обработки поверхности и несовместимых результатов при работе с этим требовательным материалом. Эти проблемы не только приводят к увеличению производственных затрат, но и вызывают досадные задержки и проблемы с качеством.
Лучшие инструменты для обработки нержавеющей стали включают твердосплавные режущие инструменты со специальными покрытиями, жесткие станки с ЧПУ с высокой мощностью шпинделя и современные режущие пластины, разработанные специально для нержавеющей стали. Правильные системы подачи СОЖ и держатели инструментов также необходимы для оптимальной работы.
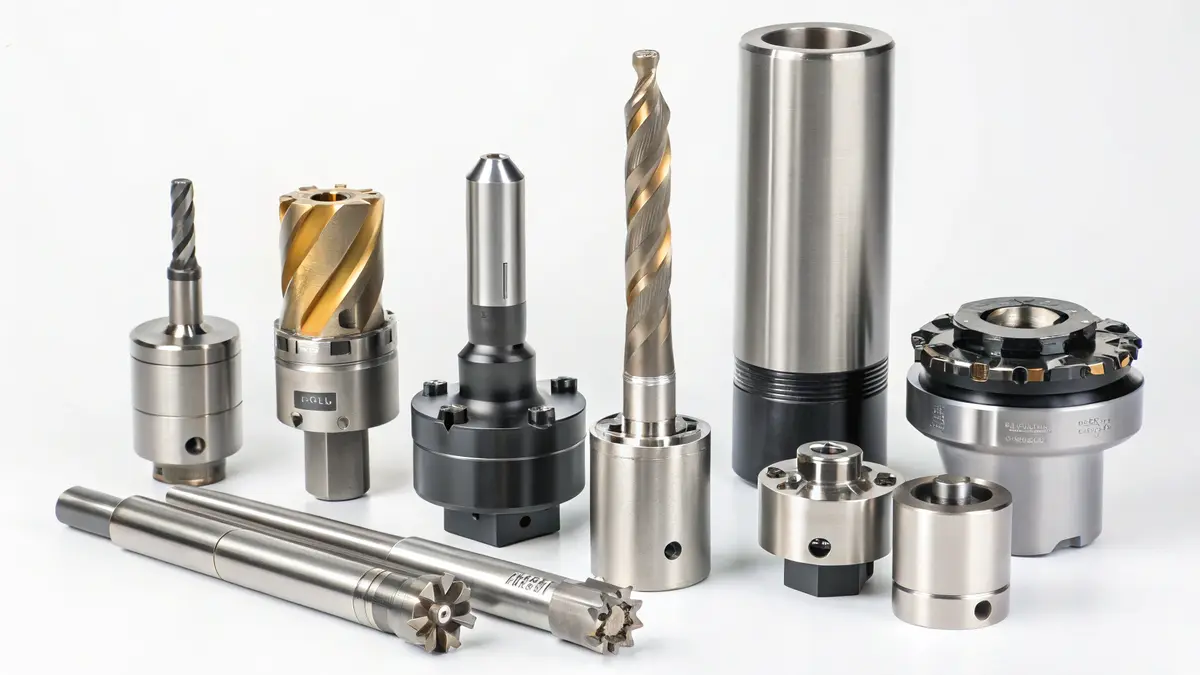
Твердосплавные режущие инструменты: Основа успеха
По моему опыту работы в компании PTSMAKE, твердосплавные инструменты оказались самым надежным выбором для обработки нержавеющей стали. В основном мы используем цельные твердосплавные концевые фрезы с такими ключевыми характеристиками:
- Микрозернистый карбидный состав для повышения износостойкости
- Переменные углы наклона спирали для уменьшения разболтанности
- Большие углы наклона для лучшего отвода стружки
- Специальная подготовка кромок для предотвращения преждевременного выхода инструмента из строя
Правильный выбор марки твердого сплава имеет решающее значение. Для работы с нержавеющей сталью мы рекомендуем марки с содержанием кобальта 10-12%, что обеспечивает оптимальный баланс между твердостью и вязкостью.
Покрытия для режущего инструмента: Элемент, меняющий игру
Современные технологии нанесения покрытий произвели революцию в обработке нержавеющей стали. Вот подробный обзор наиболее эффективных покрытий:
Тип покрытия | Преимущества | Лучшие приложения |
---|---|---|
AlTiN | Высокая термостойкость, отличная твердость | Высокоскоростная обработка |
TiCN | Хорошая износостойкость, низкое трение | Работа в средних условиях |
ZrN | Химическая стабильность, уменьшение наплывов на кромку | Отделочные работы |
TiAlN | Превосходная стойкость к окислению | Сильная черновая обработка |
Требования к станкам с ЧПУ
Успех обработки нержавеющей стали в значительной степени зависит от возможностей станка. К основным характеристикам относятся:
Высокая мощность шпинделя
- Минимум 15 л.с. для мелких и средних деталей
- 25+ л.с. для крупных компонентов
- Высокий крутящий момент на низких скоростях
Жесткая конструкция
- Прочное литье основания
- Линейные направляющие с большим преднатягом
- Надежные подшипники шпинделя
Термическая стабильность
- Шпиндель с температурным контролем
- Возможность прохода охлаждающей жидкости
- Системы термокомпенсации
Держатели для инструментов и решения для заготовок
Правильная фиксация инструмента очень важна при обработке нержавеющей стали. Мы рекомендуем:
- Гидравлические держатели инструмента для лучшего контроля биения
- Термоусадочные держатели для высокоскоростных применений
- Прочные фрезерные патроны для максимальной жесткости
Системы подачи охлаждающей жидкости
Эффективное управление охлаждающей жидкостью имеет решающее значение при обработке нержавеющей стали:
Системы охлаждения высокого давления
- 1000+ PSI для бурения глубоких скважин
- 300-500 PSI для общих фрезерных работ
- Подача охлаждающей жидкости через инструмент
Выбор охлаждающей жидкости
- Охлаждающие жидкости на масляной основе для интенсивной резки
- Водорастворимые эмульсии общего назначения
- Минимальное количество смазки (MQL) для специальных применений
Выбор вставки и геометрия
Правильный выбор геометрии пластины может существенно повлиять на срок службы инструмента и качество обработки поверхности:
- Положительные углы наклона для снижения силы резания
- Сильная подготовка кромок для прерывистых резов
- Геометрия стружколомателя для улучшения контроля стружки
- Выбор радиуса угла в зависимости от требований к чистоте поверхности
Контроль и управление сроком службы инструмента
Чтобы оптимизировать работу инструмента, мы реализуем эти стратегии:
Регулярный осмотр инструментов
- Измерьте характер износа
- Контроль силы резания
- Систематическое отслеживание срока службы инструмента
Оптимизация срока службы инструмента
- Настройка параметров резки на основе анализа износа
- Внедрение прогнозируемых графиков замены инструментов
- Документирование показателей эффективности
Оптимизация параметров процесса
Успех в обработке нержавеющей стали требует внимательного отношения к параметрам резания:
Параметр | Рекомендация | Воздействие |
---|---|---|
Скорость | 30-40% ниже, чем углеродистая сталь | Уменьшает выделение тепла |
Корм | От умеренного до тяжелого | Предотвращает закаливание при работе |
Глубина среза | Последовательное участие | Поддерживает срок службы инструмента |
Угол входа | 45°, когда это возможно | Уменьшает ударную нагрузку |
Выполняя эти рекомендации по выбору инструмента и оборудования, мы неизменно добиваемся отличных результатов в обработке нержавеющей стали. Главное - придерживаться систематического подхода к выбору инструмента, настройке станка и оптимизации процесса, всегда учитывая специфические требования вашей задачи.
Как предотвратить закалку при обработке нержавеющей стали?
Работа с нержавеющей сталью может стать настоящей головной болью при механической обработке. Я видел бесчисленное множество проектов, в которых закалка приводила к преждевременному износу инструмента, плохой обработке поверхности и даже к полному выходу из строя деталей. Эта проблема становится еще более неприятной, когда требуются жесткие допуски, так как закаленный слой может вызвать несоответствие размеров.
Чтобы предотвратить закалку при обработке нержавеющей стали, поддерживайте постоянную силу резания, используйте правильную геометрию инструмента с положительным углом наклона и применяйте эффективные стратегии охлаждения. Поддерживайте умеренную скорость резания, по возможности обеспечивайте непрерывное резание и выбирайте соответствующие покрытия инструмента для лучшего управления теплом.
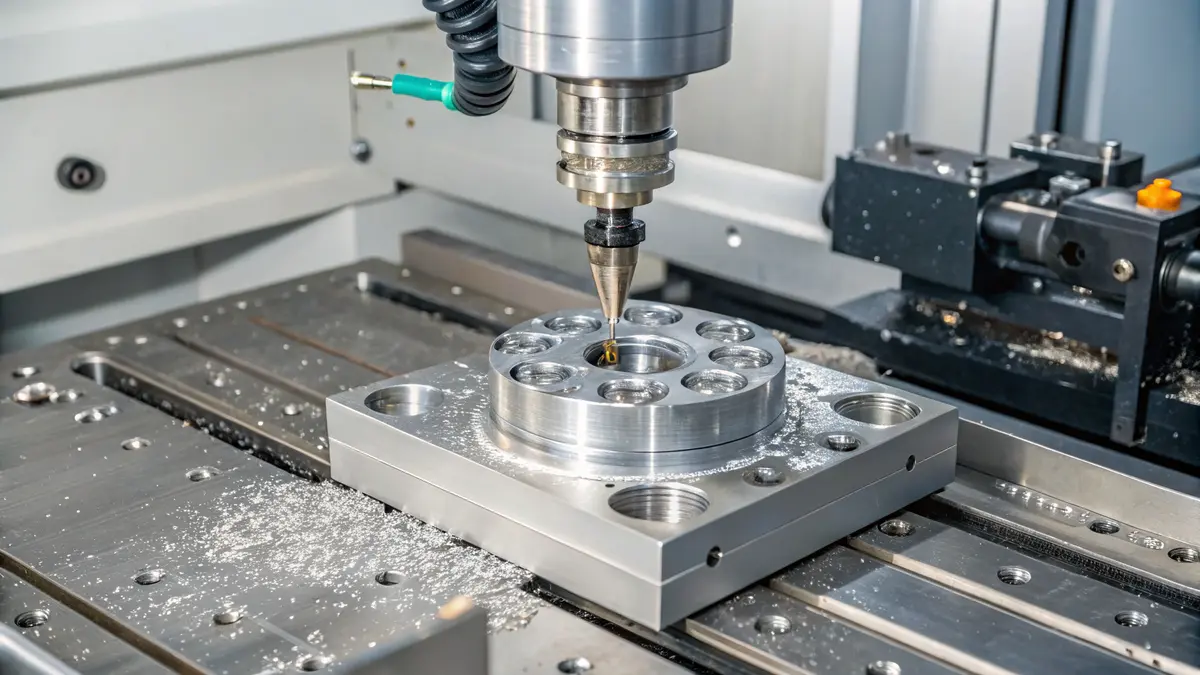
Понимание механизмов упрочнения труда
Закалка происходит, когда под действием механического напряжения кристаллическая структура материала изменяется, что приводит к повышению твердости и прочности. В нержавеющей стали это явление особенно ярко выражено из-за ее аустенитной структуры. Материал может стать до 50% тверже своего первоначального состояния, что делает последующую резку все более сложной.
Основными факторами, вызывающими закалку, являются:
- Чрезмерные усилия резания
- Повышение температуры при обработке
- Непостоянное формирование стружки
- Отклонение инструмента
- Неправильные параметры резки
Оптимизация геометрии инструмента
Правильная геометрия инструмента играет решающую роль в предотвращении закалки. Вот что я рекомендую, основываясь на результатах обширных испытаний:
Параметр инструмента | Рекомендуемое значение | Назначение |
---|---|---|
Угол наклона граблей | 10-15° положительный | Уменьшает силу резания |
Угол рельефа | 8-12° | Предотвращает натирание |
Подготовка края | Острая и легкая заточка | Чистое режущее действие |
Радиус носа инструмента | 0.015-0.032" | Баланс между прочностью и тепловыделением |
Выбор параметров резки
Правильные параметры резания необходимы для поддержания постоянной силы резания:
Параметр | Рекомендация | Обоснование |
---|---|---|
Скорость резки | 100-150 SFM | Баланс выработки тепла |
Скорость подачи | 0,004-0,008 ИПР | Поддерживает контроль за состоянием микросхем |
Глубина среза | 0.040-0.080" | Предотвращает закаливание при работе |
Шаг за шаг | 30-40% диаметр инструмента | Обеспечивает стабильную резку |
Реализация стратегии охлаждения
Эффективное охлаждение имеет решающее значение для предотвращения затвердевания. Я рекомендую применять эти стратегии:
Охлаждающая жидкость высокого давления
- Давление при использовании выше 1000 PSI
- Направляйте охлаждающую жидкость точно на режущую кромку
- Поддерживайте постоянную температуру охлаждающей жидкости
Сквозное охлаждение инструмента
- Обеспечивает лучший отвод тепла
- Улучшает эвакуацию стружки
- Уменьшает тепловой удар
Соображения по конкретным материалам
Различные марки нержавеющей стали требуют особых подходов:
Класс | Особые соображения | Рекомендуемый подход |
---|---|---|
304 | Высокая склонность к закалке | Используйте более низкую скорость, более высокую подачу |
316 | Умеренная склонность к закалке | Стандартные параметры с хорошим охлаждением |
410 | Менее склонны к закалке | Можно использовать более агрессивные резы |
Выбор покрытия для инструмента
Правильно подобранное покрытие может существенно повлиять на предотвращение закалки:
Покрытия AlTiN
- Отличная термостойкость
- Уменьшает трение
- Увеличивает срок службы инструмента
Покрытия TiCN
- Хорошо подходит для прерывистых разрезов
- Сохраняет остроту режущей кромки
- Устойчивость к образованию наросших краев
Мониторинг и корректировка процессов
Регулярный контроль помогает предотвратить застывание работы:
Индикаторы чистоты поверхности
- Увеличение шероховатости
- Обожженные участки
- Несоответствующая текстура
Знаки износа инструмента
- Ускоренный износ
- Формирование края при наращивании
- Изменение звука при резке
Потребляемая мощность
- Внезапное увеличение потребляемой мощности
- Непостоянное энергопотребление
- Более высокий, чем обычно, исходный уровень
Лучшие практики для успеха
Для обеспечения стабильных результатов:
Стратегия обработки
- По возможности используйте фрезерование с подъемом
- Поддерживайте постоянную нагрузку на чип
- Избегайте легких стрижек, которые натирают, а не режут.
Планирование траектории движения инструмента
- Минимизация колебаний зацепления инструмента
- Избегайте резких изменений направления движения
- Планируйте непрерывную резку, когда это возможно
Соображения по установке
- Обеспечение жесткой фиксации заготовок
- Минимизируйте свесы
- Используйте минимально возможную длину инструмента
Реализуя эти стратегии, мы добились стабильного успеха в предотвращении закалки в различных областях применения нержавеющей стали. Помните, что профилактика всегда лучше, чем работа с уже закаленным материалом, поскольку корректирующие меры часто приводят к увеличению затрат и задержкам производства.
Каковы наилучшие методы охлаждения и смазки?
Обрабатывать нержавеющую сталь без надлежащего охлаждения - все равно что бежать марафон в пустыне без воды. Интенсивное тепло, выделяемое в процессе резки, может быстро разрушить дорогостоящий режущий инструмент и снизить качество детали. Я видел бесчисленное множество механиков, которые боролись с преждевременным износом инструмента и плохим качеством поверхности только потому, что упускали из виду этот критический аспект.
Наиболее эффективные методы охлаждения при обработке нержавеющей стали сочетают в себе заливочное охлаждение для общих операций и туманное охлаждение для высокоскоростных задач. Не менее важен и выбор смазочно-охлаждающей жидкости - синтетические или полусинтетические СОЖ с высокими смазывающими и теплоотводящими свойствами дают наилучшие результаты.
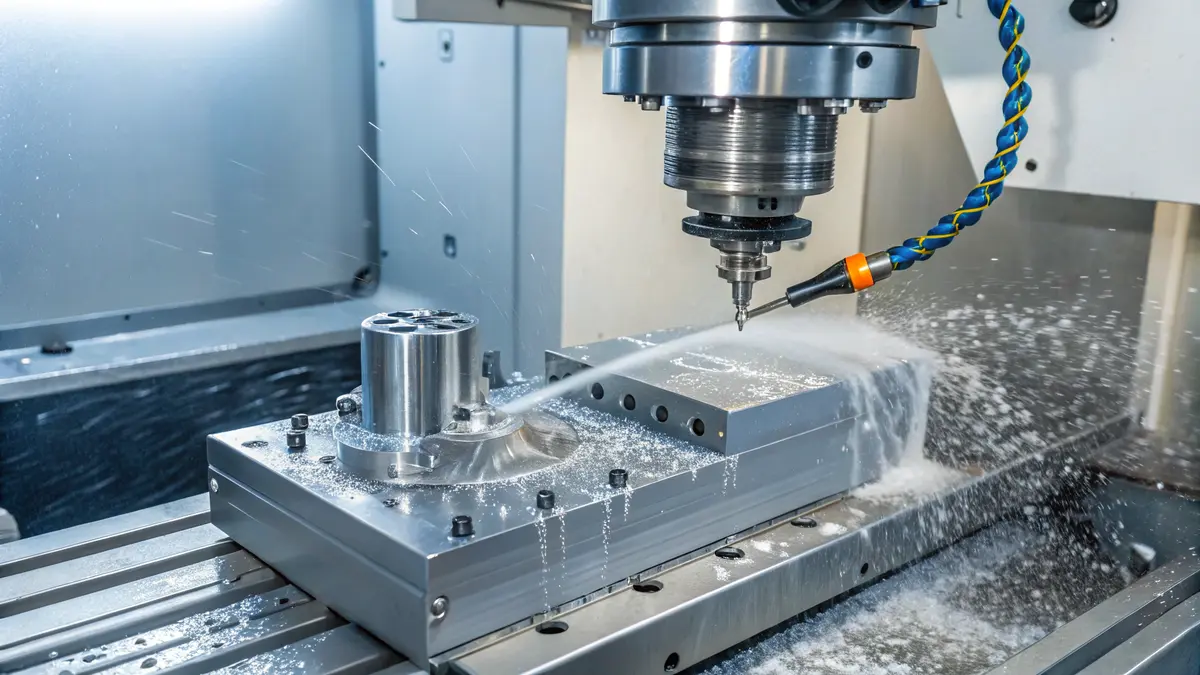
Понимание важности охлаждения при обработке нержавеющей стали
При обработке нержавеющей стали около 80% энергии, используемой при резании, превращается в тепло. Это тепло концентрируется на границе режущей кромки и заготовки. Без надлежащего охлаждения режущий инструмент может нагреться до температуры свыше 800°C, что приводит к быстрому износу инструмента и возможному повреждению заготовки.
Три основные функции систем охлаждения:
- Отвод тепла из зоны резания
- Смазка между инструментом и заготовкой
- Удаление стружки из зоны резки
Типы методов охлаждения
Охлаждение при наводнении
Этот традиционный метод остается самым распространенным способом охлаждения при обработке нержавеющей стали. Вот почему он эффективен:
- Обеспечивает постоянный контроль температуры
- Обеспечивает отличную эвакуацию стружки
- Создает защитный барьер между инструментом и заготовкой
- Обеспечивает хорошее качество обработки поверхности
Тем не менее, для поддержания эффективности работы системы охлаждения требуется надлежащее обслуживание системы охлаждения и регулярная замена жидкости.
Туманное охлаждение (MQL - минимальное количество смазки)
Современный подход предполагает использование тонкого распыления охлаждающей жидкости, смешанной со сжатым воздухом:
- Снижает расход охлаждающей жидкости до 95%
- Идеально подходит для высокоскоростной обработки
- Экологически чистый вариант
- Улучшенный обзор зоны резания
Криогенное охлаждение
Для специализированных применений охлаждение жидким азотом обладает уникальными преимуществами:
- Экстремально низкие температуры (-196°C)
- Значительно увеличивает срок службы инструмента
- Идеально подходит для труднообрабатываемых материалов
- Не оставляет следов на деталях
Выбор подходящей смазочно-охлаждающей жидкости
Выбор смазочно-охлаждающей жидкости существенно влияет на производительность обработки. Вот исчерпывающее сравнение:
Тип жидкости | Преимущества | Лучшие приложения | Диапазон концентраций |
---|---|---|---|
Синтетика | Высокая теплоотдача, чистая работа | Высокоскоростная обработка | 5-10% |
Полусинтетические | Хорошая смазка, умеренная стоимость | Общее назначение | 6-12% |
Растворимое масло | Отличная смазка, хорошее охлаждение | Сильная резка | 8-15% |
Прямое масло | Максимальная смазка | Низкоскоростные операции | 100% |
Стратегии оптимизации для систем охлаждения
Давление и скорость потока
Эффективность охлаждения во многом зависит от правильной подачи:
- Используйте охлаждение под высоким давлением (1000+ PSI) для глубоких отверстий и сложных разрезов
- Поддерживайте постоянный расход в зависимости от типа эксплуатации
- Правильно расположите сопла, чтобы направить их в зону резания
Требования к обслуживанию
Регулярное обслуживание обеспечивает оптимальную производительность системы охлаждения:
- Еженедельно контролируйте концентрацию охлаждающей жидкости
- Регулярно проверяйте уровень pH (идеальный диапазон: 8,5-9,5).
- Непрерывная фильтрация стружки и загрязнений
- Замените охлаждающую жидкость при появлении биологического роста
Передовые технологии охлаждения
Сквозное охлаждение инструмента
При этом методе охлаждающая жидкость подается непосредственно через режущий инструмент:
- Обеспечивает поступление охлаждающей жидкости в критические зоны
- Увеличивает срок службы инструмента до 50%
- Обеспечивает более высокую скорость резки
- Особенно эффективен при бурении глубоких скважин
Двухканальное охлаждение
В некоторых современных системах используются отдельные каналы для охлаждения и смазки:
- Оптимизирует функции охлаждения и смазки
- Снижает общее потребление жидкости
- Обеспечивает лучший контроль над параметрами процесса
Практические советы по внедрению
Исходя из моего опыта работы с различными методами охлаждения, вот основные соображения:
Начните с основ:
- Используйте высококачественную охлаждающую жидкость
- Поддерживайте надлежащую концентрацию
- Регулярно очищайте систему
Контролируйте эти критические параметры:
- Давление охлаждающей жидкости
- Скорость потока
- Температура
- Уровни концентрации
При выборе метода охлаждения учитывайте эти факторы:
- Характеристики материала
- Параметры резки
- Геометрия инструмента
- Объем производства
Помните, что наилучший метод охлаждения часто сочетает в себе различные технологии, основанные на специфических требованиях конкретного применения. Главное - найти правильный баланс между эффективностью охлаждения, рентабельностью и воздействием на окружающую среду.
Как достичь высокой точности при обработке нержавеющей стали?
Достижение точности при обработке нержавеющей стали - постоянная проблема, с которой сталкиваются многие производители. Я был свидетелем того, как бесчисленные проекты проваливались из-за низкого контроля точности, что приводило к браку, срыву сроков и разочарованию клиентов. Сложность свойств нержавеющей стали делает эту задачу еще более сложной, поскольку даже незначительные отклонения могут привести к существенным отклонениям.
Для достижения высокой точности обработки нержавеющей стали производители должны сосредоточиться на трех важнейших областях: поддержании стабильности станка, систематическом контроле износа инструмента и регулярном контроле качества с использованием современного метрологического оборудования.
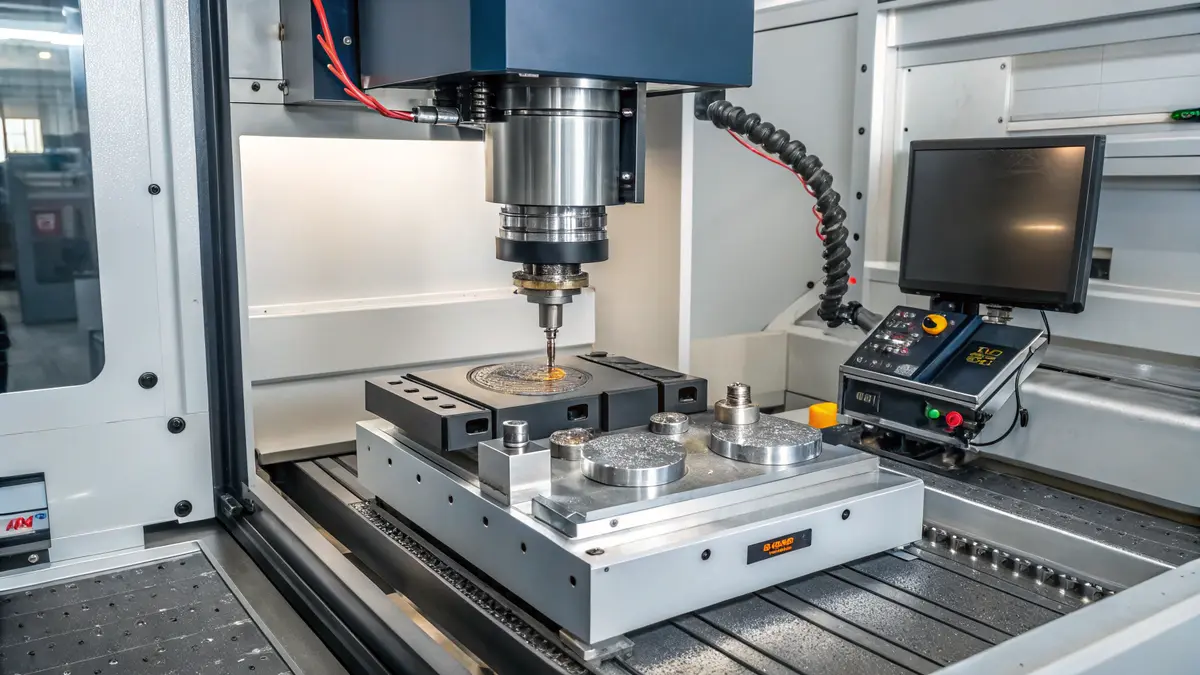
Основы устойчивости машин
Стабильность станка - основа прецизионной обработки. В компании PTSMAKE мы приняли ряд ключевых мер для обеспечения оптимальной стабильности:
Контроль температуры
- Поддерживайте температуру в мастерской на уровне 20°C ±1°C
- Установите термодатчики на критически важные компоненты машины
- Используйте системы контроля температуры охлаждающей жидкости
- Выполняйте циклы разогрева перед точными операциями
Управление вибрацией
- Установите антивибрационные крепления
- Регулярное обслуживание подшипников шпинделя
- Используйте системы контроля вибрации
- Правильная изоляция фундамента
Системы контроля износа инструмента
Износ инструмента существенно влияет на точность обработки. Наш подход включает в себя:
Методы мониторинга в реальном времени
- Датчики акустической эмиссии
- Контроль энергопотребления
- Измерение силы резания
- Системы визуального контроля
Параметр мониторинга | Метод измерения | Влияние на точность |
---|---|---|
Сила резания | Динамометр | Прямая корреляция с износом инструмента |
Потребляемая мощность | Амперметр | Указывает на состояние инструмента |
Акустическая эмиссия | Датчики | Раннее обнаружение износа |
Отделка поверхности | Визуальный/тактильный | Окончательный показатель качества |
Протокол контроля качества
Наша комплексная система контроля качества обеспечивает постоянную точность:
Измерительное оборудование
- Координатно-измерительные машины (КИМ)
- Оптические измерительные системы
- Приборы для определения шероховатости поверхности
- Цифровые микрометры
Частота проверок
Мы разработали структурированный график проверок:
Стадия производства | Тип инспекции | Частота |
---|---|---|
Настройка | Первая статья | Каждая новая установка |
Производство | В процессе | Каждые 10 деталей |
Финал | CMM | Проверка 100% |
Постобработка | Отделка поверхности | Образец основы |
Оптимизация параметров процесса
Достижение высокой точности требует тщательного подбора параметров:
Параметры резки
- Сниженная скорость резания (20-30% ниже, чем у углеродистой стали)
- Контролируемые скорости подачи
- Соответствующая глубина реза
- Жесткая фиксация заготовок
Управление охлаждающей жидкостью
- Подача охлаждающей жидкости под высоким давлением
- Регулярный контроль концентрации охлаждающей жидкости
- Фильтрованная и контролируемая по температуре охлаждающая жидкость
- Стратегическое позиционирование сопла охлаждающей жидкости
Экологический контроль
Факторы окружающей среды играют решающую роль в поддержании точности:
Окружение мастерской
- Климатическая установка
- Системы фильтрации воздуха
- Регулярные графики уборки
- Контролируемый уровень влажности
Обработка материалов
- Стабилизация температуры перед обработкой
- Правильные условия хранения
- Минимальное воздействие при обработке
- Очистите поверхности заготовок
Статистическое управление процессами
Мы внедряем комплексные методы SPC:
Сбор данных
- Автоматизированная регистрация измерений
- Анализ данных в режиме реального времени
- Мониторинг тенденций
- Исследования возможностей процессов
Тип диаграммы управления | Приложение | Пределы действия |
---|---|---|
График Х-бара | Контроль размеров | ±3σ |
R Chart | Вариации процесса | Верхний предел регулирования |
Индивидуальная диаграмма | Важнейшие особенности | ±2σ |
Непрерывное совершенствование
Наш процесс прецизионной обработки постоянно совершенствуется:
Регулярные обзоры
- Ежемесячный анализ производительности
- Интеграция отзывов клиентов
- Обновление технологий
- Программы обучения персонала
Документация
- Подробные инструкции по процессу
- Записи о контроле качества
- Журналы технического обслуживания
- Сертификаты калибровки
Такой комплексный подход к прецизионной обработке нержавеющей стали позволяет нам стабильно достигать допусков в пределах ±0,01 мм. Ключевым моментом является систематический подход ко всем аспектам процесса обработки, от контроля окружающей среды до окончательного контроля. Следуя этим рекомендациям и постоянно контролируя и совершенствуя наши процессы, мы можем обеспечить надежные и высокоточные результаты при обработке нержавеющей стали.
Каковы области применения обработанных деталей из нержавеющей стали?
Многие производители пытаются найти подходящий материал для своих критически важных компонентов, требующих одновременно долговечности и точности. Задача становится еще более сложной, когда эти детали должны противостоять коррозии, сохранять стабильность при экстремальных температурах и соответствовать строгим отраслевым нормам. Без правильного выбора материала изделия могут преждевременно выйти из строя или столкнуться с проблемами, связанными с соблюдением нормативных требований.
Обработанные детали из нержавеющей стали - это универсальные компоненты, используемые во многих отраслях промышленности, от аэрокосмической до медицинской. Эти детали обладают исключительной коррозионной стойкостью, долговечностью и точностью, что делает их идеальными для применения в сложных условиях, где надежность и производительность имеют решающее значение.
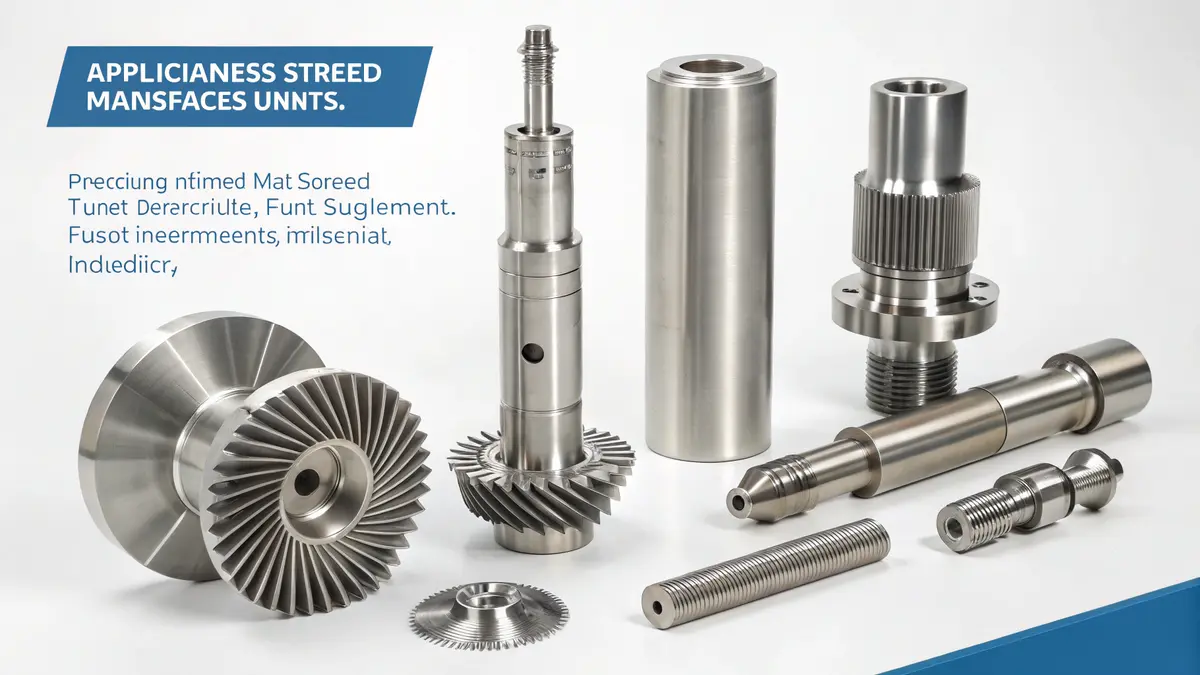
Применение в аэрокосмической промышленности
Аэрокосмический сектор в значительной степени полагается на обработанные детали из нержавеющей стали для критически важных компонентов. Я работал с многочисленными клиентами аэрокосмической отрасли в PTSMAKE, и эти детали необходимы для:
- Компоненты двигателей и лопатки турбин
- Механизмы шасси
- Конструктивные опоры и крепежные элементы
- Компоненты гидравлической системы
- Приводы поверхности управления
Высокое соотношение прочности и веса и отличная жаропрочность нержавеющей стали делают ее идеальным решением для таких сложных задач.
Производство медицинского оборудования
В медицине биосовместимость и стерилизационные возможности нержавеющей стали неоценимы. К числу распространенных областей применения относятся:
Медицинский компонент | Ключевые требования | Преимущества нержавеющей стали |
---|---|---|
Хирургические инструменты | Точность, стерилизация | Устойчивость к коррозии, долговечность |
Имплантаты | Биосовместимость, прочность | Долгий срок службы, устойчивость к жидкостям в теле |
Диагностическое оборудование | Надежность, чистота | Простота обслуживания, устойчивость |
Медицинские приспособления | Точность, долговечность | Стабильность размеров, износостойкость |
Автомобильные компоненты
Автомобильная промышленность широко использует обработанные детали из нержавеющей стали. Основные области применения включают:
- Компоненты выхлопной системы
- Системы впрыска топлива
- Компоненты клапанов двигателя
- Корпуса датчиков
- Компоненты тормозной системы
Эти детали должны выдерживать высокие температуры, давление и постоянное воздействие агрессивных веществ.
Оборудование для производства продуктов питания и напитков
Устойчивость нержавеющей стали к коррозии и легкость очистки делают ее идеальной для пищевой промышленности:
- Смесительные сосуды
- Конвейерные системы
- Режущие и обрабатывающие инструменты
- Резервуары для хранения
- Системы фильтрации
Химическая промышленность
В химической промышленности требуются материалы, способные противостоять агрессивным средам:
Приложение | Экологический вызов | Решение из нержавеющей стали |
---|---|---|
Компоненты насоса | Химическое воздействие | Превосходная коррозионная стойкость |
Корпуса клапанов | Высокое давление | Структурная целостность |
Теплообменники | Экстремальные температуры | Термическая стабильность |
Реакторные сосуды | Множественные стрессовые факторы | Общая прочность |
Морское применение
Морская среда особенно сложна из-за постоянного воздействия соленой воды:
- Валы пропеллеров
- Палубная фурнитура
- Подводные датчики
- Навигационное оборудование
- Крепеж и фитинги
Электронная промышленность
В электронной промышленности используется обработанная нержавеющая сталь:
- Корпуса для оборудования
- Теплоотводы
- Экранирующие компоненты для защиты от электромагнитных помех
- Монтажные кронштейны
- Корпуса разъемов
Нефтегазовое оборудование
Нефтегазовая промышленность требует особо прочных компонентов:
- Компоненты устья скважины
- Клапанные системы
- Сосуды под давлением
- Трубопроводная арматура
- Подводное оборудование
Учет качества в различных приложениях
При изготовлении этих компонентов решающее значение имеют несколько факторов:
Выбор материала
- Выбор класса на основании заявления
- Требования к сертификации
- Соображения, связанные с затратами
Производственный процесс
- Возможности прецизионной обработки
- Требования к чистоте поверхности
- Работа со сложной геометрией
Контроль качества
- Точность размеров
- Проверка свойств материалов
- Контроль чистоты поверхности
В компании PTSMAKE мы осуществляем строгий контроль качества, чтобы гарантировать соответствие каждого компонента отраслевым требованиям:
Промышленность | Критические требования | Показатели качества |
---|---|---|
Аэрокосмическая промышленность | Сертификация AS9100 | Проверка 100% |
Медицина | Соблюдение требований FDA | Проверенные процессы |
Автомобили | Стандарты IATF 16949 | Статистическое управление процессами |
Пищевая промышленность | Стандарты FDA/USDA | Прослеживаемость материалов |
Работая с различными отраслями промышленности, я заметил, что успех применения нержавеющей стали в значительной степени зависит от понимания специфических требований отрасли и поддержания строгого контроля качества на протяжении всего производственного процесса. Каждое применение требует тщательного рассмотрения выбора марки материала, производственных процессов и мер контроля качества для обеспечения оптимальных характеристик при использовании по назначению.
Как сократить расходы при сохранении качества?
В современном производственном ландшафте растущие затраты на обработку нержавеющей стали представляют собой серьезную проблему. Износ инструмента быстро ускоряется, цены на материалы продолжают расти, а производственные расходы, кажется, увеличиваются с каждым кварталом. Многие производители оказываются зажатыми между поддержанием стандартов качества и управлением растущими затратами, что приводит к сокращению прибыли.
Ключ к снижению затрат при сохранении качества обработки нержавеющей стали лежит в комплексном подходе, сочетающем оптимизацию параметров резания, передовые решения в области инструмента, стратегии сокращения отходов и принципы бережливого производства. Эти методы позволяют снизить затраты на 15-30% без ущерба для качества деталей.

Оптимизация параметров резки
Правильный выбор параметров резания - основа экономически эффективной обработки. Благодаря тщательному тестированию и мониторингу в компании PTSMAKE мы определили эти критические факторы:
Параметр | Влияние на стоимость | Рекомендуемая оптимизация |
---|---|---|
Скорость резки | Прямое влияние на срок службы инструмента | Используйте оптимальные диапазоны скоростей для конкретных сортов |
Скорость подачи | Влияет на качество обработки поверхности и износ инструмента | Баланс между производительностью и износом |
Глубина среза | Влияет на энергопотребление и нагрузку на инструмент | Поддерживайте постоянное взаимодействие |
Использование охлаждающей жидкости | Влияет на срок службы инструмента и качество поверхности | По возможности используйте охлаждение под высоким давлением |
Передовые инструментальные решения
Инвестиции в современные режущие инструменты поначалу могут показаться дорогими, но в долгосрочной перспективе они приносят значительную выгоду:
Твердосплавные инструменты с покрытием
- Увеличенный срок службы инструмента (на 200% дольше)
- Возможны более высокие скорости резки
- Лучшее качество обработки поверхности
Многофункциональные инструменты
- Сокращение времени установки
- Меньше смен инструмента
- Снижение затрат на инвентаризацию
Стратегии сокращения отходов
Минимизация отходов напрямую влияет на итоговый результат:
Оптимизация материалов
- Эффективная раскладка деталей
- Стратегическое использование остатков материалов
- Внедрение систем отслеживания материалов
Сокращение отходов производства
- Оптимизация программирования для минимизации брака
- Регулярное техническое обслуживание для предотвращения дефектов
- Контроль качества на источнике
Внедрение бережливого производства
Применение принципов бережливости специально для обработки нержавеющей стали включает в себя:
Производство точно в срок
- Снижение затрат на инвентаризацию
- Более эффективное управление денежными потоками
- Минимальные требования к хранению
Составление карты потока создания ценности
- Выявление неэффективности
- Устранение видов деятельности, не приносящих ценности
- Оптимизация рабочего процесса
Мониторинг и анализ затрат
Регулярный мониторинг ключевых показателей затрат помогает поддерживать контроль:
Фактор стоимости | Метод мониторинга | Улучшение целей |
---|---|---|
Расход инструмента | Отслеживание использования по каждой детали | 15-20% уменьшение |
Использование материалов | Анализ количества лома | 10-15% улучшение |
Время безотказной работы оборудования | Измерения OEE | 5-10% увеличение |
Эффективность труда | Исследования времени | Усиление 10-15% |
Интеграция технологий
Современные технологии играют решающую роль в снижении затрат:
Оптимизация программного обеспечения CAM
- Улучшенные стратегии траектории инструмента
- Сокращение времени цикла
- Улучшенная обработка поверхности
Системы мониторинга оборудования
- Отслеживание производительности в режиме реального времени
- Предиктивное обслуживание
- Оптимизация энергопотребления
Интеграция обеспечения качества
Для поддержания качества при снижении затрат требуется:
Мониторинг в процессе производства
- Раннее обнаружение проблем
- Снижение количества брака
- Постоянное качество продукции
Статистическое управление процессами
- Принятие решений на основе данных
- Анализ тенденций
- Непрерывное совершенствование
В компании PTSMAKE мы успешно внедрили эти стратегии на нашем производстве. Например, оптимизировав параметры резания и внедрив передовые инструментальные решения, мы добились снижения затрат на обработку сложного медицинского компонента из нержавеющей стали на 25% при соблюдении жестких допусков ±0,01 мм.
Главное - рассматривать снижение затрат не как единовременное мероприятие, а как непрерывный процесс постоянного совершенствования. Систематическое рассмотрение каждого аспекта процесса обработки, от выбора инструмента до сокращения отходов, позволяет добиться значительного снижения затрат без ущерба для стандартов качества, которых ожидают и заслуживают наши клиенты.
Помните, что успешное снижение затрат при обработке нержавеющей стали требует сбалансированного подхода. Хотя очень соблазнительно сосредоточиться исключительно на немедленных мерах по сокращению расходов, в долгосрочной перспективе приоритетом всегда должно быть поддержание стандартов качества. Это обеспечит устойчивое снижение затрат, которое не поставит под угрозу вашу репутацию и не приведет к дорогостоящим проблемам с качеством в будущем.