Snažíte sa nájsť ten správny materiál pre náročné aplikácie, kde štandardné plasty zlyhávajú? Mnohí inžinieri čelia výzvam, keď musia komponenty odolávať extrémnym teplotám, chemikáliám alebo mechanickému namáhaniu. Tradičné plasty jednoducho nevydržia, čo vedie k častým poruchám dielov a nákladným výmenám.
Obrábanie PEEK je proces rezania, vŕtania a tvarovania polyéterketónu (PEEK) pomocou CNC strojov. Tento vysoko výkonný termoplast ponúka výnimočnú tepelnú odolnosť až do 480 °C, vynikajúcu chemickú odolnosť a pevnosť porovnateľnú s niektorými kovmi.
Pracoval som s nespočetným množstvom zákazníkov, ktorí prešli na obrábanie kritických komponentov z PEEK. Výsledky hovoria samy za seba - dlhšia životnosť dielov, lepší výkon v náročných podmienkach a skrátené cykly údržby. Ak uvažujete, či by PEEK mohol byť riešením pre vašu aplikáciu, čítajte ďalej a zistite, aké jedinečné vlastnosti a techniky obrábania robia tento materiál takým cenným v presnej výrobe.
Je PEEK lepší ako delrín na obrábanie?
Stali ste sa niekedy uprostred dilemy pri výbere materiálu, keď ste sa rozhodovali medzi PEEK a delrínom pre váš kritický technický projekt? Keď záleží na výkone a zlyhanie neprichádza do úvahy, výber nesprávneho plastu môže viesť k predčasnému opotrebovaniu, prestojom zariadenia a nákladným zmenám konštrukcie.
Zatiaľ čo PEEK ponúka vyššiu teplotnú odolnosť (až do 480 °C), výnimočnú chemickú stabilitu a vyššiu pevnosť, delrín (POM) poskytuje lepšiu obrobiteľnosť, rozmerovú stabilitu a nižšiu cenu. "Lepšia" voľba závisí výlučne od vašich špecifických požiadaviek na aplikáciu a rozpočtových obmedzení.
Porozumenie PEEK a delrínu: Základné rozdiely
Pri porovnávaní týchto dvoch vysoko výkonných technických plastov je dôležité pochopiť ich základné zloženie a vlastnosti. PEEK (polyéterketón) je semikryštalický termoplast s výnimočnou odolnosťou voči tepelnej degradácii, zatiaľ čo Delrin (polyoxymetylén alebo POM) je acetalový homopolymér známy svojou vynikajúcou rozmerovou stabilitou.
Porovnanie vlastností materiálov
Fyzikálne a mechanické vlastnosti týchto materiálov významne ovplyvňujú ich vlastnosti pri obrábaní a konečné použitie.
Vlastníctvo | PEEK | Delrín (POM) |
---|---|---|
Teplota vychýlenia tepla | 315°F (157°C) | 257°F (125°C) |
Pevnosť v ťahu | 14 500 psi | 10 000 psi |
Chemická odolnosť | Vynikajúci (odoláva väčšine kyselín a zásad) | Dobrý (citlivý na silné kyseliny) |
Odolnosť proti opotrebovaniu | Superior | Veľmi dobré |
Faktor nákladov | 4-5× vyššia ako delrín | Mierne |
Hustota | 1,32 g/cm³ | 1,41 g/cm³ |
Charakteristika obrábania: Ako sa prejavujú pod nástrojom
Podľa mojich skúseností v spoločnosti PTSMAKE som zistil, že pri výbere medzi týmito materiálmi je často rozhodujúcim faktorom obrobiteľnosť. Delrín sa vo všeobecnosti obrába predvídateľnejšie ako PEEK a vytvára hladšie povrchy s menšou námahou.
Opotrebovanie nástroja a rezné parametre
PEEK je abrazívnejší na rezné nástroje, čo si vyžaduje častejšie výmeny nástrojov. Pri obrábaní PEEK zvyčajne znižujeme rezné rýchlosti približne o 15-20% v porovnaní s delrínom, aby sa minimalizovalo nahromadenie tepla. Je to veľmi dôležité, pretože nízka tepelná vodivosť PEEK-u spôsobuje koncentráciu tepla v zóne rezania, čo môže spôsobiť tepelná deformácia1 ak nie je správne riadená.
Na druhej strane delrín ponúka vynikajúcu rozmerovú stabilitu počas obrábania a možno ho rezať pri vyšších rýchlostiach. Dochádza pri ňom k menšiemu opotrebovaniu nástrojov a vo všeobecnosti si vyžaduje menej špecializovaných techník obrábania.
Úvahy o povrchovej úprave
Jednou z výhod delrínu je jeho schopnosť dosiahnuť vynikajúcu povrchovú úpravu pri štandardných parametroch obrábania. PEEK často vyžaduje ďalšie kroky leštenia na dosiahnutie porovnateľnej kvality povrchu.
Analýza nákladov a prínosov pre technické aplikácie
Cenový rozdiel medzi týmito materiálmi môže byť značný. PEEK zvyčajne stojí 4 až 5-krát viac ako Delrin, preto je dôležité posúdiť, či jeho prémiové vlastnosti ospravedlňujú investíciu.
Keď PEEK ospravedlňuje svoju prémiovú cenu
Odporúčam PEEK pre aplikácie, ktoré zahŕňajú:
- Extrémne prevádzkové teploty (nad 250 °F)
- Agresívne chemické prostredie
- Vysoké mechanické zaťaženie pri zvýšených teplotách
- Lekárske alebo letecké aplikácie vyžadujúce biokompatibilitu alebo odolnosť voči plameňom
Keď je delrín lepšia voľba
Delrín má väčší ekonomický zmysel, keď:
- Prevádzkové teploty zostávajú pod 180 °F
- Expozícia chemickým látkam je obmedzená na stredne silné rozpúšťadlá
- Citlivosť na náklady je hlavným faktorom
- Diely vyžadujú vynikajúcu rozmerovú stabilitu a presnosť obrábania
- Vysoké objemy výroby spôsobujú, že náklady na materiál sú významným faktorom
Úvahy špecifické pre dané odvetvie
Rôzne priemyselné odvetvia uprednostňujú rôzne vlastnosti materiálov. V leteckom a kozmickom sektore, kam sme dodali množstvo komponentov, odolnosť PEEK voči plameňom a výnimočný pomer pevnosti k hmotnosti často ospravedlňujú jeho vyššiu cenu. V prípade automobilových aplikácií často vyhráva kombinácia primeranej ceny a dobrých mechanických vlastností Delrinu.
Lekárske a potravinárske aplikácie
Pre zdravotnícke pomôcky je PEEK vďaka svojej biokompatibilite a odolnosti voči sterilizácii neoceniteľný aj napriek vyšším nákladom. V prípade zariadení na spracovanie potravín je Delrin vďaka svojej zhode s FDA a nižším nákladom často preferovanou voľbou, pokiaľ nejde o vysoké teploty.
Komponenty priemyselných strojov
V priemyselných aplikáciách som videl, že rozhodnutie často závisí od prevádzkových podmienok. Ozubené kolesá, ložiská a súčasti podliehajúce opotrebovaniu, ktoré pracujú v miernych podmienkach, sa výborne používajú v delríne, zatiaľ čo tie, ktoré sú vystavené extrémnym podmienkam, profitujú z vynikajúcich vlastností PEEK.
Správny výber pre vašu aplikáciu
Rozhodnutie medzi PEEK a delrínom by malo byť založené na dôkladnej analýze vašich špecifických prevádzkových podmienok. V spoločnosti PTSMAKE berieme do úvahy:
- Maximálna prevádzková teplota
- Profil chemickej expozície
- Požiadavky na mechanické zaťaženie
- Rozpočtové obmedzenia
- Očakávaná životnosť
Starostlivým posúdením týchto faktorov v porovnaní s vlastnosťami jednotlivých materiálov môžete urobiť informované rozhodnutie, ktoré vyváži výkon a nákladovú efektívnosť pre vašu konkrétnu aplikáciu.
Aký je rozdiel medzi acetalom a PEEK?
Rozhodovali ste sa niekedy medzi acetalom a PEEK pre vaše kritické technické komponenty? Ak úspech projektu závisí od výberu materiálu, nesprávny výber môže viesť k predčasným poruchám, neočakávaným prestojom a prepracovaniu rozpočtu, ktorému by sa dalo predísť správnou znalosťou materiálu.
Acetal (POM) a PEEK sa líšia predovšetkým svojimi úžitkovými vlastnosťami a cenou. PEEK ponúka vyššiu tepelnú odolnosť (480 °F oproti 180 °F), lepšiu chemickú odolnosť a vyššiu pevnosť, zatiaľ čo acetal poskytuje vynikajúcu obrobiteľnosť, rozmerovú stabilitu a stojí podstatne menej, takže je ideálny pre menej náročné aplikácie.
Hlavné rozdiely medzi acetalom a PEEK
Pochopenie základných rozdielov medzi týmito dvoma technickými plastmi je kľúčové pre prijímanie informovaných rozhodnutí pre vaše projekty. Oba materiály sa presadili ako alternatívy v presnej výrobe, ale na základe ich prirodzených vlastností slúžia na výrazne odlišné účely.
Zloženie a štruktúra materiálu
Acetal, bežne známy pod obchodným názvom Delrin (vo forme homopolyméru) alebo pod chemickým názvom polyoxymetylén (POM), má vysoko kryštalickú štruktúru s opakujúcimi sa skupinami -CH₂O-. Táto štruktúra mu poskytuje vynikajúcu rozmerovú stabilitu a obrobiteľnosť.
Na druhej strane PEEK (polyéterketón) patrí do skupiny polyaryléterketónov a obsahuje aromatické kruhy spojené éterovými a ketónovými väzbami. Táto molekulová štruktúra vytvára výnimočnú tepelnú stabilitu a chemickú odolnosť.
Porovnanie výkonnostných charakteristík
Rozdiely vo výkone týchto materiálov ich robia vhodnými pre rôzne aplikácie:
Vlastníctvo | Acetal (POM) | PEEK | Najlepšie pre |
---|---|---|---|
Tepelná odolnosť | 180°F (82°C) nepretržite | 480°F (250°C) nepretržite | PEEK |
Chemická odolnosť | Dobrý (okrem silných kyselín) | Vynikajúca (odolná voči väčšine chemikálií) | PEEK |
Pevnosť v ťahu | 8 800 - 10 000 psi | 14 500-16 000 psi | PEEK |
Odolnosť proti opotrebovaniu | Veľmi dobré | Vynikajúce | PEEK |
Obrábateľnosť | Vynikajúce | Dobrý (vyžaduje špecializované techniky) | Acetal |
Faktor nákladov | Základná referencia (1×) | 4-7× vyššia ako pri acetale | Acetal |
Absorpcia vlhkosti | 0.2-0.25% | 0.1-0.15% | PEEK |
Analýza nákladov a prínosov
Počas rokov práce so zákazníkmi v spoločnosti PTSMAKE som si všimol, že pri prvotnom výbere materiálu sa často zohľadňujú náklady. Acetal je výrazne ekonomickejší ako PEEK, takže je štandardnou voľbou, keď nie sú prítomné extrémne podmienky.
Prémiová cena PEEK odráža jeho vynikajúce výkonnostné schopnosti. Pri posudzovaní, či sú dodatočné investície opodstatnené, zvážte tieto faktory:
- Požiadavky na prevádzkovú teplotu
- Profil chemickej expozície
- Úrovne mechanického namáhania
- Predpokladaná životnosť
- Náklady na prestoje spojené so zlyhaním komponentov
Úvahy o obrábaní
Životnosť nástroja a rezné parametre
Acetal je známy svojou výnimočnou obrobiteľnosťou. Reže čisto, drží prísne tolerancie a vytvára vynikajúce povrchové úpravy s minimálnym úsilím. Štandardné karbidové nástroje pracujú dobre a materiál nespôsobuje nadmerné opotrebovanie nástrojov.
PEEK predstavuje viac výziev pri obrábaní. Jeho vysoká teplotná odolnosť znamená, že odvod tepla počas obrábania je slabý, čo si vyžaduje:
- Znížené rezné rýchlosti (zvyčajne o 20-30% pomalšie ako acetal)
- Častejšie výmeny nástrojov
- Pozornosť venujte akumulácii tepla
- Špecializované techniky chladenia
V spoločnosti PTSMAKE sme vyvinuli špecifické protokoly tepelného manažmentu2 pre obrábanie PEEK, aby sa zabezpečila presnosť rozmerov a zabránilo sa degradácii materiálu počas procesu rezania.
Rozmerová stabilita
Acetal ponúka vynikajúcu rozmerovú stabilitu po obrábaní s minimálnou deformáciou alebo uvoľnením napätia. To ho robí obzvlášť cenným pre presné komponenty s prísnymi toleranciami.
PEEK tiež vykazuje dobrú rozmerovú stabilitu, ale vyžaduje si opatrnejšie procesy žíhania na uvoľnenie vnútorných napätí po obrábaní. Bez správnej tepelnej úpravy môže dôjsť v priebehu času k miernym rozmerovým zmenám dielov z PEEK, najmä pri vysoko presných aplikáciách.
Odporúčania pre konkrétne aplikácie
Automobilový priemysel a doprava
V aplikáciách v automobilovom priemysle, kde teploty zostávajú mierne (pod 180 °C), acetal často poskytuje najlepšiu hodnotu. Medzi bežné aplikácie patria:
- Komponenty palivového systému
- Mechanizmy uzamykania dverí
- Príchytky a spojovacie prvky interiérového obloženia
- Ložiskové plochy v nekritických oblastiach
Pre oblasti s vyššou teplotou, ako sú komponenty pod kapotou alebo diely v blízkosti výfukových systémov, je PEEK vďaka svojej tepelnej stabilite lepšou voľbou napriek vyšším nákladom.
Lekárenstvo a farmácia
Zdravotnícky priemysel si PEEK obľúbil pre jeho biokompatibilitu a odolnosť voči sterilizačným metódam. Bežne sa používa v:
- Implantovateľné zariadenia
- Chirurgické nástroje
- Lekárske zobrazovacie komponenty
- Laboratórne vybavenie
Acetal stále nachádza uplatnenie v menej náročných zdravotníckych zariadeniach, ako sú napr:
- Jednorazové komponenty prístrojov
- Laboratórne skúšobné prípravky
- Puzdrá diagnostických zariadení
Priemyselné zariadenia
V prípade priemyselných strojov výber často závisí od prevádzkových podmienok:
- Štandardné prevádzkové prostredie: Acetal poskytuje vynikajúcu hodnotu pre ozubené kolesá, ložiská a povrchy podliehajúce opotrebovaniu v bežných podmienkach.
- Drsné prostredie: PEEK ospravedlňuje svoju prémiovú cenu, keď je vystavený vysokým teplotám, chemikáliám alebo extrémnemu mechanickému namáhaniu.
Optimálny výber
Keď pomáham klientom pri výbere medzi acetalom a PEEK pri PTSMAKE, odporúčam systematický prístup:
- Identifikujte najnáročnejšie podmienky, ktorým bude diel vystavený (teplota, chemikálie, zaťaženie).
- Určite, či sú vlastnosti acetalu dostatočné na zvládnutie týchto podmienok
- Vypočítajte si rozdiel v nákladoch medzi možnosťami pre vaše špecifické požiadavky na objem
- Zvážte dôsledky poruchy a súvisiace náklady na prestoje.
- Vyhodnoťte, či prémiový výkon PEEK ospravedlňuje jeho vyššiu cenu
Nezabudnite, že výber materiálu je zriedkavo univerzálny. Niekedy sa najlepšie osvedčí hybridný prístup, pri ktorom sa PEEK používa len na najkritickejšie komponenty, zatiaľ čo acetal sa používa na menej náročné diely v rámci tej istej zostavy.
Aký je rozdiel medzi PTFE a PEEK?
Stalo sa vám niekedy, že ste sa stratili v mori vysokoúčinných plastov a nevedeli ste, či si pre svoju kritickú aplikáciu vybrať PTFE alebo PEEK? Keď sa blížia termíny projektu a výber materiálu môže rozhodnúť o vašom návrhu, tlak na správnu voľbu môže byť zdrvujúci, najmä keď oba materiály majú pôsobivé technické špecifikácie.
PTFE a PEEK sú vysoko výkonné termoplasty s výraznými rozdielmi. PTFE ponúka bezkonkurenčnú chemickú odolnosť, extrémne nízke trenie (koeficient 0,05-0,10) a funguje v rozsahu teplôt od -328 °C do 500 °C, ale má nízku mechanickú pevnosť. PEEK poskytuje vynikajúce mechanické vlastnosti, vynikajúcu odolnosť proti opotrebovaniu a zachováva štrukturálnu integritu až do 480 °C, pričom je lepšie opracovateľný.
Molekulová štruktúra a základné vlastnosti
Základné rozdiely medzi PTFE a PEEK začínajú na molekulárnej úrovni, čo vysvetľuje ich odlišné výkonnostné charakteristiky v rôznych aplikáciách.
Chemické zloženie
PTFE (polytetrafluóretylén) má uhlíkovú kostru úplne obklopenú atómami fluóru. Táto jedinečná štruktúra dáva PTFE výnimočnú chemickú inertnosť a nízke trenie. Väzby medzi uhlíkom a fluórom patria medzi najsilnejšie v organickej chémii, vďaka čomu je PTFE neuveriteľne odolný voči chemickým útokom.
PEEK (polyéterketón) má zložitejšiu molekulovú štruktúru s aromatickými kruhmi spojenými éterovými a ketónovými väzbami. Táto aromatická chrbtica zabezpečuje PEEK vynikajúcu mechanickú pevnosť a tepelnú stabilitu.
Porovnávacia analýza nehnuteľností
Vlastníctvo | PTFE | PEEK | Výhoda |
---|---|---|---|
Maximálna teplota nepretržitého používania | 500°F (260°C) | 480°F (250°C) | PTFE (mierne) |
Minimálna prevádzková teplota | -328°F (-200°C) | -65°F (-54°C) | PTFE |
Koeficient trenia | 0,05-0,10 (najnižšia hodnota zo všetkých pevných látok) | 0.35-0.40 | PTFE |
Pevnosť v ťahu | 3 000-5 000 psi | 14 000-16 000 psi | PEEK |
Chemická odolnosť | Superior (univerzálny) | Vynikajúca (obmedzená silnými kyselinami) | PTFE |
Obrábateľnosť | Náročný (mäkký, ľahko sa deformuje) | Dobrý | PEEK |
Odolnosť proti opotrebovaniu | Slabá až stredne silná | Vynikajúce | PEEK |
Elektrické vlastnosti | Vynikajúci izolátor | Dobrý izolátor | PTFE |
Faktor nákladov | Mierne | Vysoká (3-4× viac ako PTFE) | PTFE |
Rozdiely v tepelnom výkone
Teplotné vlastnosti sú často rozhodujúcim faktorom pri výbere medzi týmito materiálmi.
Tepelná odolnosť a stabilita
Hoci oba materiály ponúkajú výnimočnú tepelnú odolnosť, pri zvýšených teplotách sa správajú odlišne. PTFE si zachováva svoju chemickú inertnosť a nízke trenie až do maximálnej teploty, ale pri oveľa nižších teplotách (približne 260 °F/127 °C) začína strácať mechanickú integritu.
PEEK si pritom zachováva svoju mechanickú pevnosť oveľa bližšie k maximálnej teplote. Vďaka tomu je PEEK podstatne cennejší v aplikáciách, ktoré si vyžadujú tepelnú odolnosť aj mechanické zaťaženie.
Videl som mnoho aplikácií, kde si zákazníci pôvodne vybrali PTFE len na základe teplotných hodnôt, aby zistili, že materiál nezvláda mechanické namáhanie pri týchto teplotách. Schopnosť PEEK zachovať štrukturálnu integritu pri vysokých teplotách často stojí za vyššiu cenu.
Výkon pri nízkych teplotách
Pri kryogénnych aplikáciách má PTFE výraznú výhodu. Zostáva pružný a funkčný až do -328 °F (-200 °C), zatiaľ čo PEEK sa stáva čoraz krehkejším pod -65 °F (-54 °C). Preto je PTFE jasnou voľbou pre letecký priemysel, laboratóriá a iné ultranízko teplotné prostredia.
Porovnanie mechanickej pevnosti
Mechanické vlastnosti týchto materiálov sa výrazne líšia, čo spôsobuje, že ich vhodnosť závisí od aplikácie.
Integrita konštrukcie pri zaťažení
PEEK ponúka výrazne lepšie mechanické vlastnosti s pevnosťou v ťahu v priemere 14 000-16 000 psi v porovnaní so skromnými 3 000-5 000 psi PTFE. Vďaka tomu je PEEK vhodný na aplikácie prenášajúce zaťaženie, kde by sa PTFE rýchlo deformoval alebo zlyhal.
V spoločnosti PTSMAKE často odporúčame PEEK pre konštrukčné komponenty, ktoré sú vystavené trvalému mechanickému zaťaženiu, najmä pri zvýšených teplotách. Výnimočná odolnosť materiálu voči tečeniu mu umožňuje zachovať si rozmerovú stabilitu pri trvalom namáhaní.
Odolnosť proti opotrebovaniu a treniu
Pozoruhodne nízky koeficient trenia PTFE (0,05-0,10) z neho robí materiál, ktorý je vhodný pre aplikácie vyžadujúce minimálne trenie. Tá istá vlastnosť však prispieva k jeho nízkej odolnosti proti opotrebovaniu, keďže materiál sa môže ľahko ošúpať pri vysokom opotrebovaní.
PEEK vykazuje vynikajúcu odolnosť proti opotrebovaniu pri zachovaní primeraného koeficientu trenia (0,35-0,40). Pri aplikáciách, ktoré zahŕňajú nepretržitý pohyb proti iným povrchom, PEEK zvyčajne prekonáva PTFE so značnou rezervou.
Mnohí naši zákazníci dosahujú to najlepšie z oboch svetov tým, že používajú PEEK ako konštrukčný materiál s tenkou vrstvou PTFE alebo vložkou tam, kde je potrebné znížiť trenie.
Profily chemickej odolnosti
Oba materiály majú výnimočnú chemickú odolnosť, ale s dôležitými rozdielmi.
Odolnosť voči agresívnemu prostrediu
PTFE predstavuje zlatý štandard chemickej odolnosti, pretože je prakticky inertný voči takmer všetkým chemikáliám (so vzácnymi výnimkami, ako sú roztavené alkalické kovy a elementárny fluór). Vďaka tejto univerzálnej chemickej odolnosti je PTFE neoceniteľný pri chemickom spracovaní, výrobe polovodičov a v laboratórnom prostredí.
PEEK má vynikajúcu chemickú odolnosť voči väčšine látok, ale môže byť napadnutý koncentrovanou kyselinou sírovou a niektorými inými silnými kyselinami. Pre väčšinu priemyselných prostredí je však chemická odolnosť PEEK viac ako dostatočná.
Hydrolýza a absorpcia vlhkosti
PTFE je úplne hydrofóbny a v podstate neabsorbuje žiadnu vlhkosť, a to ani po dlhšom vystavení. PEEK je síce vysoko odolný voči hydrolýze, ale pri dlhodobom vystavení vlhkému prostrediu absorbuje malé množstvo vlhkosti (0,1-0,3%).
Pri aplikáciách s veľmi čistou vodou alebo v systémoch, kde je neprípustná aj nepatrná kontaminácia, je PTFE často uprednostňovanou voľbou aj napriek jeho mechanickým obmedzeniam.
%[Obrábané komponenty z PEEK a PTFE na štrukturálne porovnanie](
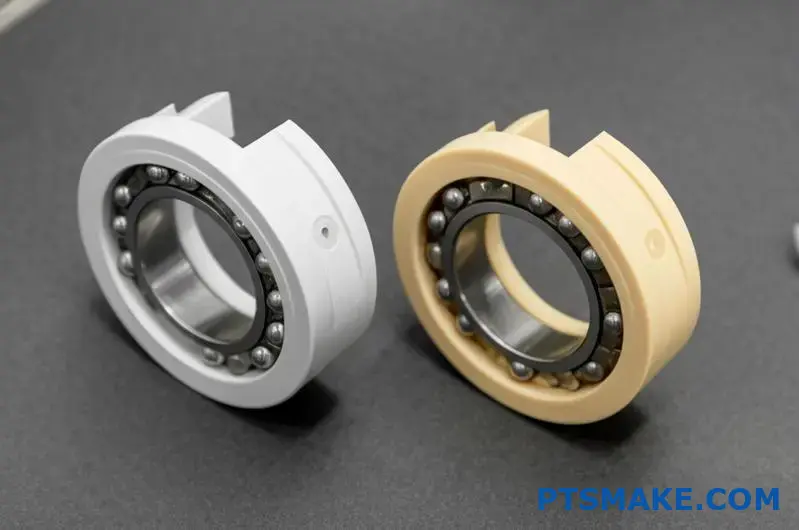
"Ložiskové komponenty z PEEK a PTFE")
Úvahy o obrábaní a výrobe
Stránka Obrábateľnosť3 rozdiely medzi týmito materiálmi významne ovplyvňujú výrobné náklady a možnosti.
Výzvy a riešenia pri obrábaní
PTFE predstavuje jedinečnú výzvu pri obrábaní vzhľadom na svoju mäkkosť a sklon k tečeniu za studena. Vyžaduje si špecializované nástroje, nižšie rezné rýchlosti a opatrné upevnenie, aby sa zabránilo deformácii počas obrábania. Ostré nástroje sú nevyhnutné, aby sa zabránilo roztrhnutiu alebo deformácii materiálu.
PEEK sa pri obrábaní podobá skôr na tradičné technické plasty, hoci jeho abrazívna povaha spôsobuje rýchlejšie opotrebovanie nástrojov ako pri mnohých iných materiáloch. Pri obrábaní PEEK zvyčajne používame karbidové nástroje a vhodné chladiace techniky na zvládnutie nárastu tepla.
Kompatibilita výrobných procesov
Vysoká viskozita taveniny PTFE znemožňuje konvenčné vstrekovanie. Namiesto toho sa musí spracovať pomocou techník, ako je lisovanie, vytláčanie pomocou rampovača alebo vyrezávanie z predvalkov. To obmedzuje zložitosť konštrukcie a zvyšuje výrobné náklady na zložité tvary.
PEEK sa dá spracovať bežnými metódami, ako je vstrekovanie a vytláčanie, čo umožňuje komplexnejšie geometrie a potenciálne nižšie výrobné náklady pri vyšších objemoch. Táto všestrannosť spracovania dáva PEEK výhodu pri výrobe zložitých komponentov alebo pri prechode od výroby prototypov k sériovej výrobe.
Analýza nákladov a prínosov pre rôzne aplikácie
Výrazný cenový rozdiel medzi týmito materiálmi si vyžaduje dôkladné zváženie ich hodnoty pre konkrétnu aplikáciu.
Porovnanie hodnotovej ponuky
Hoci PEEK zvyčajne stojí 3 až 4-krát viac ako PTFE, jeho vynikajúce mechanické vlastnosti a odolnosť proti opotrebovaniu často poskytujú lepšiu dlhodobú hodnotu v aplikáciách, kde by mechanické zlyhanie bolo nákladné alebo nebezpečné.
Pre aplikácie, ktoré vyžadujú predovšetkým chemickú odolnosť, nízke trenie alebo elektrické izolačné vlastnosti bez výrazného mechanického namáhania, PTFE zvyčajne ponúka lepšiu hodnotu napriek svojim obmedzeniam.
Výberové kritériá špecifické pre dané odvetvie
Rôzne priemyselné odvetvia uprednostňujú rôzne vlastnosti materiálov:
- Chemické spracovanie: Univerzálna chemická odolnosť PTFE zvyčajne prevažuje nad jeho mechanickými obmedzeniami.
- Letecký a kozmický priemysel: Oba materiály nachádzajú uplatnenie, pričom PEEK sa používa na konštrukčné komponenty a PTFE na tesnenia a elektrickú izoláciu.
- Zdravotná starostlivosť: Vďaka biokompatibilite a štrukturálnej pevnosti je PEEK obľúbený pre implantáty, zatiaľ čo PTFE sa uprednostňuje pre výstelky katétrov a iné aplikácie s nízkym trením.
- Polovodič: PTFE dominuje vďaka svojej výnimočnej čistote a odolnosti voči agresívnym chemikáliám.
- Automobilový priemysel: Odolnosť PEEK voči opotrebovaniu a jeho mechanické vlastnosti ho predurčujú na použitie v komponentoch pod kapotou, ktoré sú vystavené mechanickému namáhaniu.
Aký je rozdiel medzi PVDF a PEEK?
Stáli ste niekedy pred dilemou, či si vybrať medzi PVDF a PEEK pre kritický projekt, pri ktorom by výber materiálu mohol rozhodnúť o vašom návrhu? Keď vám nestačia štandardné plasty a potrebujete výnimočnú chemickú odolnosť alebo tepelnú stabilitu, zámena týchto dvoch vysoko výkonných materiálov môže viesť k nákladným chybám alebo zhoršeniu výkonu.
PVDF (polyvinylidénfluorid) a PEEK (polyéterketón) sa líšia predovšetkým svojimi výkonnostnými vlastnosťami a aplikáciami. PEEK ponúka vyššiu tepelnú odolnosť (480 °C oproti 300 °C), lepšiu mechanickú pevnosť a výnimočnú odolnosť proti opotrebovaniu, zatiaľ čo PVDF poskytuje vynikajúcu chemickú odolnosť, UV stabilitu a je výrazne lacnejší.
Hlavné rozdiely medzi PVDF a PEEK
Pri porovnávaní týchto dvoch technických termoplastov pomáha pochopenie ich základných vlastností určiť, ktorý materiál je najvhodnejší pre konkrétne aplikácie. Oba materiály sa považujú za vysoko výkonné možnosti, ale vynikajú v rôznych prostrediach a aplikáciách.
Zloženie a štruktúra materiálu
PVDF je polokryštalický fluórpolymér pozostávajúci z opakujúcich sa jednotiek vinylidéndifluoridu. Jeho molekulová štruktúra obsahuje väzby medzi uhlíkom a fluórom, ktoré zabezpečujú vynikajúcu chemickú odolnosť, hoci nie takú komplexnú ako plne fluórované polyméry, ako je PTFE.
PEEK patrí do skupiny polyaryléterketónov a má komplexnú molekulovú štruktúru s aromatickými kruhmi spojenými éterovými a ketónovými väzbami. Táto jedinečná štruktúra dáva PEEK výnimočnú tepelnú stabilitu a mechanickú pevnosť.
Porovnanie výkonnostných charakteristík
Nasledujúca tabuľka obsahuje podrobné porovnanie kľúčových vlastností PVDF a PEEK:
Vlastníctvo | PVDF | PEEK | Vynikajúci materiál |
---|---|---|---|
Maximálna teplota nepretržitého používania | 300°F (149°C) | 480°F (250°C) | PEEK |
Mechanická pevnosť (v ťahu) | 5 800-7 800 psi | 14 500-16 000 psi | PEEK |
Chemická odolnosť | Vynikajúci (väčšina kyselín, zásad) | Veľmi dobrá (obmedzená silnými kyselinami) | PVDF |
Odolnosť voči UV žiareniu | Vynikajúce | Slušný až dobrý | PVDF |
Odolnosť proti opotrebovaniu | Dobrý | Vynikajúce | PEEK |
Koeficient trenia | 0.25-0.35 | 0.35-0.40 | PVDF |
Faktor nákladov | Mierne | 2-3× vyššia ako PVDF | PVDF |
Absorpcia vlhkosti | 0.03-0.04% | 0.1-0.15% | PVDF |
Hustota | 1,75-1,78 g/cm³ | 1,30-1,32 g/cm³ | V závislosti od aplikácie |
Tepelný výkon a stabilita
Teplotné možnosti často rozhodujú o výbere materiálu v mnohých technických aplikáciách.
Porovnanie tepelnej odolnosti
PEEK vykazuje výnimočnú tepelnú stabilitu a zachováva si svoje mechanické vlastnosti pri teplotách do 250 °C (480 °F) pri nepretržitom používaní. Vďaka tomu je ideálny na použitie v prostredí s vysokými teplotami, kde by tradičné plasty zlyhali.
PVDF sa síce stále považuje za vysokoteplotný plast, ale jeho maximálna teplota pri nepretržitom používaní je nižšia, približne 149 °C (300 °F). Tento teplotný rozsah je dostatočný pre mnohé priemyselné aplikácie, ale v extrémnych tepelných prostrediach je nedostatočný.
Podľa mojich skúseností so zákazníkmi spoločnosti PTSMAKE sa tento teplotný rozdiel často stáva rozhodujúcim faktorom pri výbere medzi týmito materiálmi pre aplikácie, ako sú zariadenia na spracovanie polovodičov, kde procesné teploty môžu presahovať možnosti PVDF.
Tepelné cyklické správanie
Obidva materiály zvládajú tepelné cykly odlišne:
- PVDF vykazuje dobrú rozmerovú stabilitu počas tepelných cyklov, hoci môže mať výraznejšiu tepelnú rozťažnosť ako PEEK.
- PEEK si zachováva výnimočnú rozmerovú stabilitu aj pri opakovaných tepelných cykloch, vďaka čomu je vhodnejší pre presné komponenty, ktoré si musia zachovať prísne tolerancie pri rôznych teplotách.
Profily chemickej odolnosti
Chemická odolnosť je ďalším kľúčovým faktorom, ktorý tieto materiály odlišuje.
Odolnosť voči agresívnemu prostrediu
PVDF poskytuje vynikajúcu odolnosť voči širokému spektru chemikálií vrátane:
- Väčšina kyselín (vrátane koncentrovanej kyseliny chlorovodíkovej a kyseliny sírovej)
- Alifatické a aromatické uhľovodíky
- Alkoholy a chlórované rozpúšťadlá
- Oxidačné činidlá
PEEK vykazuje dobrú chemickú odolnosť voči mnohým látkam, ale môže byť napadnutý koncentrovanou kyselinou sírovou a niektorými inými silnými kyselinami. Je obzvlášť odolný voči hydrolýze a sterilizácii parou, čo ho robí cenným v lekárskych aplikáciách.
Úvahy o chemických látkach špecifické pre dané odvetvie
Rôzne priemyselné odvetvia uprednostňujú špecifické vlastnosti chemickej odolnosti:
- Chemické spracovanie: PVDF sa často uprednostňuje pre svoju komplexnú odolnosť voči kyselinám a chlórovaným zlúčeninám.
- Polovodič: Používajú sa oba materiály, pričom výber závisí od konkrétnych chemikálií.
- Ropa a plyn: Kombinácia mechanických vlastností a chemickej odolnosti PEEK ho predurčuje na použitie v hĺbkových vrtoch.
- Farmaceutické výrobky: PVDF je vďaka svojej vynikajúcej odolnosti voči čistiacim prostriedkom a sterilizačným metódam obľúbený pre spracovateľské zariadenia.
Mechanické vlastnosti a konštrukčné aplikácie
Stránka mechanická pevnosť4 rozdiely medzi týmito materiálmi významne ovplyvňujú ich vhodnosť pre nosné aplikácie.
Schopnosť prenášať zaťaženie
PEEK ponúka podstatne vyššiu mechanickú pevnosť s hodnotami v ťahu zvyčajne v rozmedzí 14 500 - 16 000 psi v porovnaní so skromnejšími hodnotami 5 800 - 7 800 psi PVDF. Vďaka tomu je PEEK vhodnejší pre konštrukčné komponenty, ktoré musia odolávať značnému mechanickému zaťaženiu.
Pri aplikáciách, ktoré si vyžadujú chemickú odolnosť a štrukturálnu integritu, PEEK často poskytuje najlepšiu rovnováhu vlastností, a to aj napriek vyššej cene. Odporúčal som PEEK pre mnohé aplikácie v PTSMAKE, kde komponenty musia odolávať agresívnym chemikáliám aj mechanickému namáhaniu.
Odolnosť proti opotrebovaniu a trecie vlastnosti
PEEK vykazuje vynikajúcu odolnosť proti opotrebovaniu, takže je ideálny pre ložiská, puzdrá a iné komponenty, ktoré sú vystavené trvalému treniu. Jeho samomazné vlastnosti pomáhajú predĺžiť životnosť pohyblivých častí v náročných prostrediach.
PVDF má dobrú odolnosť proti opotrebovaniu, aj keď nie na úrovni PEEK. Jeho nižší koeficient trenia (0,25 - 0,35 v porovnaní s 0,35 - 0,40 PEEK) môže byť výhodný v určitých aplikáciách s nízkym klzným zaťažením, kde je zníženie trenia dôležitejšie ako maximálna odolnosť proti opotrebovaniu.
Vlastnosti elektrickej a tepelnej izolácie
Oba materiály majú odlišné elektrické vlastnosti, vďaka ktorým sú vhodné na rôzne aplikácie.
Dielektrické vlastnosti
PVDF je známy svojimi piezoelektrickými vlastnosťami, ktoré mu umožňujú generovať elektrický náboj v reakcii na aplikované mechanické napätie. Táto jedinečná vlastnosť robí PVDF cenným v senzorových aplikáciách.
PEEK poskytuje vynikajúce elektroizolačné vlastnosti v širokom teplotnom rozsahu, pričom si zachováva svoju dielektrickú pevnosť aj pri zvýšených teplotách. Vďaka tomu je obzvlášť cenný v elektrických aplikáciách pri vysokých teplotách, kde by štandardné plasty zlyhali.
Tepelná vodivosť
PVDF a PEEK majú v porovnaní s kovmi relatívne nízku tepelnú vodivosť, takže sú dobrými tepelnými izolantmi:
- PVDF: 0,17-0,19 W/m-K
- PEEK: 0,25-0,29 W/m-K
Táto nízka tepelná vodivosť môže byť v závislosti od aplikácie výhodou alebo nevýhodou. V prípade komponentov, ktoré si vyžadujú tepelnú izoláciu, sú obidva materiály vhodné, hoci PVDF poskytuje o niečo lepšiu izoláciu.
Úvahy o nákladoch a analýza hodnoty
Vzhľadom na výrazný cenový rozdiel medzi týmito materiálmi je nevyhnutné vykonať analýzu nákladov a prínosov.
Počiatočné náklady na materiál
Cena PEEK je zvyčajne 2 až 3-krát vyššia ako cena PVDF, čo predstavuje značnú cenovú prirážku, ktorá musí byť odôvodnená požiadavkami na výkon. Tento cenový rozdiel vyplýva zo zložitejšieho výrobného procesu PEEK a vyšších nákladov na suroviny.
Hodnotenie životnosti
Pri hodnotení celkových nákladov na vlastníctvo by sa okrem počiatočných materiálových nákladov malo zohľadniť niekoľko ďalších faktorov:
- Predpokladaná životnosť v cieľovom prostredí
- Frekvencia výmeny a súvisiace náklady na prestoje
- Požiadavky na inštaláciu a údržbu
- Obavy týkajúce sa bezpečnosti a spoľahlivosti
V mnohých vysokoteplotných aplikáciách alebo aplikáciách s vysokým zaťažením ospravedlňuje vynikajúci výkon PEEK jeho vyššiu počiatočnú cenu vďaka predĺženej životnosti a zvýšenej spoľahlivosti. Pri aplikáciách v rámci možností PVDF poskytuje lacnejší materiál často lepšiu celkovú hodnotu.
Spracovanie a výroba
Výber materiálu ovplyvňujú aj výrobné možnosti a obmedzenia.
Rozdiely v obrábaní
Pri obrábaní týchto materiálov pri PTSMAKE sme zaznamenali významné rozdiely:
- PVDF sa obrába relatívne dobre, ale vyžaduje ostré nástroje a vhodné rýchlosti, aby sa zabránilo roztaveniu alebo zadretiu.
- PEEK je náročnejší na obrábanie kvôli svojej abrazívnosti a slabej tepelnej vodivosti, čo môže viesť k nahromadeniu tepla počas rezania.
V prípade presných komponentov PEEK vo všeobecnosti dodržiava prísnejšie tolerancie pri obrábaní, ale vyžaduje si špecializovanejšie techniky a nástroje, čo môže zvýšiť výrobné náklady.
Kompatibilita výrobných metód
Oba materiály sa dajú spracovať viacerými výrobnými metódami:
- PVDF: Vstrekovanie, vytláčanie, lisovanie, obrábanie
- PEEK: vstrekovanie, vytláčanie, lisovanie, obrábanie, 3D tlač (špecializované zariadenia)
PVDF ponúka o niečo väčšiu flexibilitu spracovania pri nižších teplotách, zatiaľ čo PEEK vyžaduje vyššie teploty spracovania, ale poskytuje viac možností pre komplexné geometrie vďaka pokročilým výrobným technikám.
Usmernenia pre výber špecifických aplikácií
Rôzne priemyselné odvetvia uprednostňujú rôzne vlastnosti materiálov, čo vedie k rôznym preferenciám materiálov.
Polovodičový priemysel
Pri výrobe polovodičov nachádzajú uplatnenie oba materiály, ale v rôznych oblastiach:
- PVDF: PVDF sa bežne používa v systémoch s veľmi čistou vodou, v komponentoch na dodávku chemikálií a vo filtračných zariadeniach.
- PEEK: Preferovaný pre komponenty vystavené vysokým teplotám, ako sú zariadenia na manipuláciu s plátkami a komponenty procesných komôr.
Zariadenia na chemické spracovanie
Pre aplikácie chemického spracovania:
- PVDF: Vynikajúci pre čerpadlá, ventily, armatúry a nádrže, ktoré pracujú s korozívnymi chemikáliami pri miernych teplotách.
- PEEK: Lepšie sa hodí na komponenty, ktoré vyžadujú chemickú odolnosť a odolnosť voči vysokým teplotám alebo mechanickú pevnosť.
Lekárske a farmaceutické aplikácie
V lekárskych aplikáciách:
- PVDF: PVDF sa bežne používa vo filtračných membránach, šijacích materiáloch a niektorých implantovateľných zariadeniach.
- PEEK: Preferovaný pre implantovateľné zariadenia, najmä ortopedické aplikácie, vďaka svojej biokompatibilite, rádiolucencii a mechanickým vlastnostiam podobným kosti.
Keď pomáham klientom pri výbere medzi PVDF a PEEK v PTSMAKE, odporúčam systematický prístup, ktorý najprv vyhodnotí najkritickejšie faktory prostredia (teplota, chemikálie, mechanické zaťaženie) a potom zváži sekundárne faktory, ako sú náklady, požiadavky na spracovanie a dostupnosť.
<
Je PEEK polyetylén?
Zistili ste niekedy, že ste zmätení množstvom technických plastov s podobne znejúcimi názvami? Pri výbere materiálov pre kritické aplikácie môže tento omyl viesť k nákladným chybám, zlyhaniu výkonu a plytvaniu zdrojmi, ak omylom nahradíte jeden vysoko výkonný plast iným.
Nie, PEEK (polyéterketón) nie je polyetylén. PEEK je aromatický polyéter s ketónovými skupinami v chrbtici, čím vzniká semikryštalický termoplast s výnimočnou tepelnou odolnosťou (do 480 °C), vynikajúcou chemickou odolnosťou a vynikajúcimi mechanickými vlastnosťami, ktoré ďaleko prevyšujú vlastnosti polyetylénových materiálov.
Chemická štruktúra a rozdiely v klasifikácii
Pri skúmaní PEEK v porovnaní s polyetylénom sa základné rozdiely začínajú na molekulárnej úrovni. Tieto štrukturálne rozdiely vysvetľujú, prečo sa tieto materiály v praktických aplikáciách správajú tak odlišne.
Porovnanie molekulárnej kostry
PEEK má komplexnú aromatickú štruktúru chrbtice s éterovými a ketónovými väzbami medzi benzénovými kruhmi. Táto molekulová architektúra dáva PEEK jeho výnimočnú tepelnú stabilitu a mechanickú pevnosť. Aromatické kruhy vytvárajú tuhosť, zatiaľ čo éterové väzby poskytujú určitú flexibilitu.
Polyetylén má naopak jednu z najjednoduchších možných polymérnych štruktúr - len lineárny reťazec atómov uhlíka s pripojenými atómami vodíka. Táto jednoduchá štruktúra existuje v rôznych formách (HDPE, LDPE, UHMWPE), ale všetkým chýbajú aromatické zložky a funkčné skupiny, ktoré dávajú PEEK jeho výnimočné vlastnosti.
Tento zásadný štrukturálny rozdiel znamená, že PEEK patrí do úplne inej skupiny polymérov ako polyetylén. Zatiaľ čo polyetylén je klasifikovaný ako polyolefín, PEEK patrí do skupiny polyaryléterketónu (PAEK), ktorý patrí medzi vysokoúčinné termoplasty.
Kľúčové rozdiely vo vlastnostiach
Rozdiely v molekulárnej štruktúre sa prejavujú v dramatických výkonnostných rozdieloch:
Vlastníctvo | PEEK | Polyetylén (HDPE) | Faktor rozdielu |
---|---|---|---|
Maximálna teplota nepretržitého používania | 480°F (250°C) | 180 °F (82 °C) | PEEK je 2,7× vyšší |
Pevnosť v ťahu | 14 500 psi | 4 500 psi | PEEK je 3,2× pevnejší |
Chemická odolnosť | Vynikajúci (odoláva väčšine chemikálií) | Dobrý (citlivý na aromatické rozpúšťadlá) | PEEK ponúka širšiu odolnosť |
Náklady | Vysoká | Nízka | PEEK stojí 15-20× viac |
Hustota | 1,32 g/cm³ | 0,95 g/cm³ | PEEK je 39% hustejší |
Tvrdosť (Shore D) | 85-90 | 60-70 | PEEK je výrazne tvrdší |
Rozdiely vo výrobnom procese
Metódy výroby PEEK a polyetylénu odrážajú ich rozdielne molekulové štruktúry a výkonnostné charakteristiky.
Výrobný proces PEEK
PEEK sa vyrába zložitým procesom nukleofilnej aromatickej substitučnej polymerizácie. To si vyžaduje presnú kontrolu teploty a špecializované katalyzátory. Monomérne materiály sú podstatne drahšie ako etylén, čo prispieva k vyššej cene PEEK.
V spoločnosti PTSMAKE musíme pri obrábaní komponentov z PEEK zohľadniť jedinečné vlastnosti tohto materiálu - jeho nižšia tepelná vodivosť znamená, že riadenie tepla počas obrábania je rozhodujúce, aby sa zabránilo lokálnej tepelnej degradácii.
Výroba polyetylénu
Polyetylén sa vyrába adičnou polymerizáciou etylénu pomocou rôznych katalyzátorov v závislosti od požadovanej hustoty a vetvenia. Tento relatívne jednoduchý proces sa môže vykonávať pri nižších teplotách a tlakoch ako výroba PEEK, najmä v prípade odrôd s nízkou hustotou.
Výkon v extrémnych prostrediach
Výkon pri vysokých teplotách
Jedným z najvýznamnejších rozdielov medzi týmito materiálmi je ich tepelná stabilita:
- PEEK si zachováva svoje mechanické vlastnosti až do 250 °C (480 °C) pri nepretržitom používaní a vydrží krátkodobé vystavenie ešte vyšším teplotám.
- Polyetylén začína mäknúť pri teplote 82 °C (180 °F) a väčšinu svojej mechanickej pevnosti stráca už pri teplote nižšej.
Videl som mnoho aplikácií, v ktorých si klienti pôvodne vybrali polyetylén na základe ceny, len aby došlo k rýchlemu zlyhaniu, keď prevádzkové teploty prekročili očakávania. V jednej aplikácii v leteckom priemysle klient prešiel z polyetylénu na PEEK pre komponent v blízkosti zdroja tepla, čím predĺžil jeho životnosť z mesiacov na roky napriek vyšším počiatočným nákladom na materiál.
Porovnanie chemickej odolnosti
Hoci oba materiály poskytujú dobrú chemickú odolnosť, PEEK poskytuje širšiu ochranu proti agresívnym chemikáliám:
- PEEK odoláva väčšine kyselín, zásad, uhľovodíkov a organických rozpúšťadiel
- Polyetylén má dobrú odolnosť voči kyselinám a zásadám, ale môže byť napadnutý aromatickými uhľovodíkmi a niektorými oxidačnými činidlami
Tento rozdiel je rozhodujúci v zariadeniach na spracovanie chemikálií, pri výrobe polovodičov a v lekárskych aplikáciách, kde je bežná expozícia viacerým chemikáliám.
Vhodnosť aplikácie
Aplikácie v letectve a obrane
V leteckých a kozmických aplikáciách je PEEK vďaka kombinácii nízkej hmotnosti, odolnosti voči plameňom a tepelnej stabilite neoceniteľný pre komponenty, ako sú:
- Vnútorné komponenty vyžadujúce odolnosť voči plameňom
- Elektrické konektory a izolátory
- Štrukturálne prvky v zónach s vysokou teplotou
- Komponenty palivového systému vyžadujúce chemickú odolnosť
Polyetylén len zriedkavo spĺňa náročné požiadavky leteckých aplikácií kvôli svojej obmedzenej tepelnej stabilite a mechanickým vlastnostiam.
Použitie v lekárstve a zdravotníctve
Profily biokompatibility týchto materiálov sa tiež výrazne líšia:
- PEEK je biokompatibilný a používa sa v implantovateľných zariadeniach, chirurgických nástrojoch a zdravotníckom vybavení, ktoré si vyžaduje sterilizáciu.
- Medicínsky polyetylén (predovšetkým UHMWPE) sa používa v niektorých implantátoch, ako sú umelé kĺby, ale nemá teplotnú odolnosť PEEK na opakovanú sterilizáciu parou.
Komponenty priemyselných zariadení
Pri priemyselných strojoch výber medzi týmito materiálmi zvyčajne závisí od prevádzkových podmienok:
- PEEK vyniká v prostrediach s vysokými teplotami, v aplikáciách vyžadujúcich vynikajúcu odolnosť proti opotrebovaniu alebo vystaveniu drsným chemikáliám.
- Polyetylén poskytuje primeraný výkon v aplikáciách pri teplote okolia s miernymi mechanickými požiadavkami a často sa volí pre jeho nižšiu cenu a jednoduché spracovanie.
Úvahy o nákladoch a výnosoch
Cenový rozdiel medzi týmito materiálmi je značný - PEEK stojí zvyčajne 15 - 20-krát viac ako polyetylén s vysokou hustotou. Tento výrazný cenový rozdiel znamená, že výber materiálu by mal byť založený na dôkladnej analýze:
- Požadovaný rozsah pracovných teplôt
- Profil chemickej expozície
- Požiadavky na mechanické zaťaženie
- Predpokladaná životnosť
- Dôsledky zlyhania
Pri aplikáciách v rámci možností polyetylénu je jeho nižšia cena ekonomickou voľbou. Ak však požiadavky na výkonnosť presahujú obmedzenia polyetylénu, vynikajúce vlastnosti PEEK ľahko ospravedlnia jeho vyššiu cenu vďaka predĺženej životnosti, zvýšenej spoľahlivosti a zníženým nákladom na údržbu.
Rozdiely v obrábaní a spracovaní
V spoločnosti PTSMAKE sme zistili významné rozdiely pri obrábaní týchto materiálov:
- PEEK si vyžaduje špecializované parametre rezania vzhľadom na jeho tepelné správanie5 počas obrábania, ale dodržiava prísne tolerancie a vytvára vynikajúcu povrchovú úpravu.
- Polyetylén sa ľahšie obrába, ale má tendenciu deformovať sa pri rezných silách, čo sťažuje dodržiavanie prísnych tolerancií.
Pochopenie týchto rozdielov v spracovaní je nevyhnutné pri navrhovaní komponentov pre ich vyrobiteľnosť a presnosť.
Aké sú nevýhody a výhody PEEK?
Mali ste niekedy problém rozhodnúť sa, či PEEK stojí za svoju prémiovú cenu pre vašu kritickú aplikáciu? Keď úspech projektu závisí od výberu materiálu, výber medzi drahými vysoko výkonnými plastmi a ekonomickejšími alternatívami môže byť náročným vyvažovaním s reálnymi dôsledkami na spoľahlivosť a životnosť.
PEEK ponúka výnimočné výhody vrátane pozoruhodnej tepelnej odolnosti (až do 480 °C), vynikajúcej chemickej odolnosti, vynikajúcej mechanickej pevnosti a vynikajúcich vlastností proti opotrebovaniu. Tieto výhody sú však spojené s významnými nevýhodami vrátane vysokej ceny (5 až 10-krát vyššia ako pri štandardných technických plastoch), náročnej obrobiteľnosti, obmedzených farebných možností a slabej odolnosti voči UV žiareniu.
Pochopenie výnimočných vlastností PEEK
PEEK (polyéterketón) vyniká medzi technickými plastmi jedinečnou kombináciou vlastností, vďaka ktorým je vhodný na najnáročnejšie aplikácie. Ako človek, ktorý špecifikoval materiály pre nespočetné množstvo presných súčiastok, som na vlastné oči videl, ako sa vlastnosti PEEK premietajú do skutočných výkonnostných výhod.
Výhody tepelného výkonu
Jednou z najpôsobivejších vlastností PEEK je jeho tepelná stabilita. Tento materiál si zachováva svoje mechanické vlastnosti pri teplotách, ktoré by u väčšiny plastov spôsobili katastrofálne zlyhanie.
Teplotná charakteristika | Výkonnosť PEEK | Porovnanie so štandardnými plastmi |
---|---|---|
Trvalá prevádzková teplota | Do 250 °C (480 °F) | 2-3× vyššia ako väčšina technických plastov |
Teplota prechodu skla | 289°F (143°C) | Zachováva si tuhosť pri vyšších teplotách |
Bod topenia | 343 °C (649 °F) | Umožňuje sterilizáciu parou |
Tepelná vodivosť | 0,25 W/m-K | Lepší odvod tepla ako mnohé plasty |
Táto výnimočná tepelná odolnosť umožňuje PEEK používať v aplikáciách v blízkosti zdrojov tepla, kde by sa štandardné plasty rýchlo deformovali alebo degradovali. Pomohol som mnohým klientom nahradiť zlyhané komponenty vyrobené z menej kvalitných materiálov dielmi z PEEK, ktoré aj napriek náročnému tepelnému prostrediu naďalej bezchybne fungujú.
Výhody chemickej odolnosti
Profil chemickej odolnosti PEEK je takmer rovnako pôsobivý ako jeho tepelné vlastnosti. Materiál vykazuje vynikajúcu odolnosť voči:
- Uhľovodíky a organické rozpúšťadlá
- Väčšina kyselín a zásad (okrem koncentrovanej kyseliny sírovej)
- Para a horúca voda
- Automobilové kvapaliny a palivá
- Medicínske sterilizačné procesy
Vďaka tejto širokej chemickej odolnosti je PEEK obzvlášť cenný v prostrediach, kde sa očakáva vystavenie viacerým agresívnym látkam. Napríklad v polovodičovom priemysle sú komponenty z PEEK odolné voči agresívnym chemikáliám používaným pri spracovaní doštičiek pri zachovaní rozmerovej stability.
Výhody mechanických vlastností
Mechanická pevnosť PEEK ho odlišuje od väčšiny ostatných termoplastov:
- Pevnosť v ťahu 14 500 psi (porovnateľná s niektorými kovmi)
- Vynikajúca odolnosť proti únave
- Vynikajúca odolnosť proti nárazu a húževnatosť
- Vynikajúca odolnosť proti opotrebovaniu
- Nízky koeficient trenia
Vďaka týmto vlastnostiam je PEEK vhodný na konštrukčné aplikácie, kde by väčšina plastov zlyhala. Špecifikoval som PEEK pre ozubené kolesá, ložiská a iné súčasti s vysokým opotrebovaním, ktoré pracujú pod značným mechanickým namáhaním, pričom som často nahradil kovové časti ľahšími alternatívami PEEK, ktoré poskytujú ďalšie výhody, ako je odolnosť proti korózii a zníženie hlučnosti.
Významné nevýhody PEEK
Napriek pôsobivým úžitkovým vlastnostiam má PEEK niekoľko významných nevýhod, ktoré treba pri výbere materiálu starostlivo zvážiť.
Obmedzenia nákladov
Najzjavnejšou nevýhodou PEEK je jeho cena. V spoločnosti PTSMAKE musíme často pomáhať klientom pochopiť cenovú prirážku PEEK v porovnaní s inými technickými plastmi:
- PEEK je zvyčajne 5 až 10-krát drahší ako technické plasty ako nylon alebo acetal.
- Materiálové náklady na diely z PEEK môžu byť o 20-30% vyššie ako náklady na ekvivalentné kovové komponenty
- Vysoká cena surovín výrazne ovplyvňuje ekonomiku malých dielov
Tento cenový faktor často núti konštruktérov vyhradiť PEEK len pre najkritickejšie aplikácie, kde sú jeho jedinečné vlastnosti absolútne nevyhnutné. V mnohých prípadoch odporúčame cenovo výhodnejšie alternatívy pre nekritické komponenty v zostave.
Výrobné výzvy
PEEK predstavuje niekoľko výrobných problémov, ktoré môžu zvýšiť zložitosť výroby a náklady:
Ťažkosti pri obrábaní: Vysoký tepelný odpor PEEK sa prejavuje v slabej tepelnej vodivosti, čo spôsobuje nahromadenie tepla počas obrábania. To si vyžaduje nižšie rezné rýchlosti, časté výmeny nástrojov a starostlivé stratégie chladenia.
Požiadavky na teplotu spracovania: PEEK s teplotou topenia 343 °C (649 °F) si vyžaduje špecializované vysokoteplotné zariadenia na vstrekovanie a vytláčanie.
Obmedzené okno na spracovanie: Rozdiel medzi teplotou topenia PEEK a začiatkom degradácie je relatívne malý, čo spôsobuje problémy počas spracovania.
Zmršťovanie formy: PEEK vykazuje počas chladnutia značné zmrštenie (približne 1-1,3%), čo si vyžaduje presný návrh formy na dosiahnutie prísnych tolerancií.
V spoločnosti PTSMAKE sme vyvinuli špecializované protokoly obrábania PEEK, aby sme tieto výzvy riešili, ale nevyhnutne zvyšujú celkové náklady a zložitosť výroby komponentov PEEK.
Obmedzenia aplikácie
Napriek svojim pôsobivým vlastnostiam má PEEK obmedzenia, ktoré ho robia nevhodným pre určité aplikácie:
- Slabá odolnosť voči UV žiareniu: Bez prísad PEEK degraduje pri dlhodobom vystavení UV žiareniu, čo obmedzuje jeho použitie vo vonkajších aplikáciách.
- Obmedzené možnosti farieb: Vzhľadom na jeho prirodzenú jantárovú/hnedú farbu a vysoké teploty spracovania je ťažké PEEK trvalo zafarbiť.
- Elektrické obmedzenia: Hoci je PEEK dobrý izolant, nie je ideálny pre vysokofrekvenčné elektrické aplikácie v porovnaní so špecializovanými elektrickými polymérmi.
- Ťažkosti pri vytváraní väzieb: Vďaka chemickej odolnosti PEEK je lepenie náročné a často si vyžaduje špeciálnu povrchovú úpravu.
Analýza nákladov a prínosov: Kedy sa PEEK oplatí?
Vzhľadom na značnú cenovú prirážku PEEK je pred určením tohto materiálu nevyhnutné vykonať dôkladnú analýzu nákladov a prínosov. Podľa mojich skúseností poskytuje PEEK najlepšiu hodnotu v nasledujúcich scenároch:
Scenáre, v ktorých PEEK vyniká
Prostredie s vysokou teplotou: Pri prevádzkových teplotách vyšších ako 149 °C (300 °F) je PEEK často jedinou vhodnou alternatívou plastu, takže jeho vyššia cena je opodstatnená.
Chemicky agresívne prostredie: V aplikáciách, ktoré sú vystavené viacerým chemikáliám alebo obzvlášť agresívnym látkam, široká chemická odolnosť PEEK zabraňuje častej výmene, ktorá je potrebná v prípade menej kvalitných materiálov.
Aplikácie kritického opotrebenia: V prípade komponentov, ktoré sú vystavené neustálemu treniu a opotrebovaniu v kritických systémoch, môže výnimočná odolnosť PEEK voči opotrebovaniu a nízke trenie výrazne predĺžiť servisné intervaly.
Požiadavky na zníženie hmotnosti: Pri nahrádzaní kovových komponentov v leteckom priemysle alebo pri vysoko výkonných aplikáciách môže pomer pevnosti a hmotnosti PEEK poskytnúť výkonnostné výhody, ktoré ospravedlňujú jeho cenu.
Aplikácie lekárskych implantátov: Biokompatibilita a chemická stabilita PEEK ho predurčujú na dlhodobé implantovateľné zariadenia, pri ktorých zlyhanie materiálu neprichádza do úvahy.
Porovnanie alternatívnych materiálov
V prípade aplikácií, ktoré nevyžadujú extrémne vlastnosti PEEK, môže niekoľko alternatív poskytnúť dostatočný výkon pri nižších nákladoch:
Materiál | Komparatívna výhoda | Náklady vs. PEEK | Kľúčové obmedzenie |
---|---|---|---|
PPS (polyfenylénsulfid) | Dobrá tepelná odolnosť (400 °F) | 40-60% nižšia | Menej odolné voči chemikáliám |
PTFE (polytetrafluóretylén) | Vynikajúca chemická odolnosť | 30-50% nižšia | Slabá mechanická pevnosť |
PEI (polyéterimid) | Dobrá tepelná odolnosť, priehľadnosť | 30-40% spodná | Menšia odolnosť proti opotrebovaniu |
PAI (polyamid-imid) | Vysoká pevnosť, dobrá odolnosť proti opotrebovaniu | 10-20% nižšia | Ťažšie spracovateľné |
Acetal (POM) | Vynikajúca obrobiteľnosť, nízke náklady | 80-90% nižšia | Obmedzená teplotná odolnosť |
Úvahy špecifické pre dané odvetvie
Rôzne priemyselné odvetvia uprednostňujú rôzne aspekty profilu vlastností PEEK:
Letectvo a obrana
V leteckých a kozmických aplikáciách kombinácia nízkej hmotnosti, odolnosti voči plameňom (s prísadami) a tepelnej stability PEEK odôvodňuje jeho vyššiu cenu pre komponenty, ako sú:
- Puzdrá a ložiská v riadiacich systémoch
- Elektrické konektory a izolátory
- Štrukturálne prvky v zónach s vysokou teplotou
- Komponenty palivového systému vyžadujúce chemickú odolnosť
Lekárska a zdravotnícka starostlivosť
Zdravotnícky priemysel si cení PEEK pre jeho:
- Biokompatibilita (trieda implantátu)
- Odolnosť voči opakovanej sterilizácii
- Rádiolucencia (neruší röntgenové žiarenie)
- Mechanické vlastnosti podobné kosti (ak je vystužená)
Vďaka týmto vlastnostiam je PEEK ideálny na implantovateľné zariadenia a chirurgické nástroje napriek jeho vysokej cene.
Priemyselné zariadenia
Pri priemyselných aplikáciách rozhodnutie o použití PEEK zvyčajne závisí od náročnosti prevádzkových podmienok:
- Extrémne prostredia (vysoká teplota, vystavenie chemickým látkam) často odôvodňujú použitie PEEK
- Aplikácie, kde sú prestoje veľmi nákladné, profitujú zo spoľahlivosti PEEK
- Vysoko presné komponenty profitujú z rozmerovej stability PEEK
V spoločnosti PTSMAKE pomáhame klientom zorientovať sa v týchto otázkach a určiť, či prémiový výkon PEEK ospravedlňuje jeho prémiovú cenu pre ich špecifické aplikačné potreby.
Obsah kapitoly 7 článku "Prečo je PEEK taký drahý?" vytvorím podľa vašich požiadaviek.
Prečo je PEEK taký drahý?
Zažili ste niekedy šok z cenovej ponuky na komponenty PEEK? Keď sa inžinieri prvýkrát stretnú s cenou tohto vysoko výkonného plastu, mnohí si kladú otázku, či by nejaký materiál mohol ospravedlniť takú vysokú cenu, najmä v porovnaní s bežnejšími technickými plastmi, ktoré zrejme ponúkajú slušný výkon za zlomok ceny.
Vysoké náklady na PEEK vyplývajú z jeho zložitého výrobného procesu, drahých surovín, požiadaviek na špecializované zariadenia a relatívne nízkych objemov výroby. Zložitý proces polymerizácie si vyžaduje presné podmienky, pričom patentovaná povaha výrobnej technológie a status PEEK ako špeciálneho materiálu ďalej zvyšujú jeho trhovú cenu.
Komplexný výrobný proces PEEK
Pochopenie toho, prečo je cena PEEK taká vysoká, sa začína skúmaním jeho výrobného procesu. Na rozdiel od jednoduchších polymérov výroba PEEK zahŕňa zložitú chémiu a presné podmienky spracovania, ktoré výrazne ovplyvňujú konečnú cenu.
Náklady na suroviny a ich nedostatok
Samotné monoméry používané na výrobu PEEK sú drahé špeciálne chemikálie. Medzi základné zložky patria:
- Difenyléter
- 4,4′-difluórbenzofenón
- Uhličitan draselný
- Difenylsulfón (ako rozpúšťadlo)
Tieto prekurzory si vyžadujú viacero krokov zušľachťovania, aby sa dosiahla čistota potrebná na syntézu PEEK, čo zvyšuje náklady ešte pred začiatkom polymerizácie. Okrem toho majú niektoré z týchto chemikálií celosvetovo obmedzenú výrobnú kapacitu, čo spôsobuje obmedzenia dodávok, ktoré zvyšujú ceny.
Keď v spoločnosti PTSMAKE získavame PEEK pre projekty obrábania, neplatíme len za samotný polymér, ale za celý hodnotový reťazec špecializovaných chemikálií, ktoré boli použité pri jeho výrobe.
Zložitosť polymerizačného procesu
Syntéza PEEK zahŕňa zložitý proces nukleofilnej aromatickej substitúcie polymerizácie. Táto reakcia musí prebiehať za presne kontrolovaných podmienok:
- Teploty v rozmedzí 300-400 °C (572-752 °F)
- Inertná atmosféra na zabránenie oxidácie
- Špecializované tlakové nádoby
- Predĺžený reakčný čas (často 3-5 hodín)
- Starostlivé riadenie katalyzátorov
Každá z týchto požiadaviek zvyšuje zložitosť výroby a náklady. Reakcia sa musí počas celého procesu starostlivo monitorovať, aby sa zabezpečilo správne rozloženie molekulovej hmotnosti a kryštalinita, ktoré priamo ovplyvňujú úžitkové vlastnosti materiálu.
Obmedzený rozsah výroby a dynamika trhu
Status PEEK ako špeciálneho materiálu významne ovplyvňuje ekonomiku jeho výroby a trhové ceny.
Vlastná technológia a patentová ochrana
Pôvodnú technológiu výroby PEEK vyvinula a patentovala spoločnosť Victrex (predtým ICI) v 70. rokoch 20. storočia. Aj v súčasnosti je výrobná technológia z veľkej časti patentovaná a chránená rôznymi patentmi. Táto obmedzená konkurencia v oblasti výrobných metód udržiava vyššie ceny v porovnaní s komoditnými plastmi.
Hoci v súčasnosti existuje niekoľko svetových výrobcov (vrátane spoločností Victrex, Solvay a Evonik), každý z nich používa vlastné postupy, ktorých vývoj si vyžiadal obrovské investície do výskumu a vývoja. Tieto náklady na vývoj sa musia vrátiť prostredníctvom cien materiálov.
Ekonomika objemu výroby
Na rozdiel od komoditných plastov vyrábaných v miliónoch ton ročne sa PEEK vyrába v relatívne malých objemoch:
Typ plastu | Celosvetová ročná produkcia | Faktor relatívnych nákladov |
---|---|---|
Polyetylén (PE) | ~100 miliónov ton | 1× (základná hodnota) |
Nylon (PA) | ~8 miliónov ton | 2-3× |
Polykarbonát (PC) | ~4,5 milióna ton | 3-4× |
PEEK | <10 000 ton | 30-50× |
Tento obmedzený objem výroby znamená, že výrobcovia nemôžu dosiahnuť úspory z rozsahu, ktoré znižujú náklady na bežné plasty. Fixné náklady, ako je údržba zariadenia, kontrola kvality a výskum a vývoj, sa rozložia na menej kilogramov výrobku, čo zvyšuje náklady na jednotku.
Požiadavky na vybavenie a spracovanie
Výrobné zariadenia na PEEK si vyžadujú špecializované zariadenia, ktoré zvládnu extrémne teploty a tlaky potrebné na polymerizáciu, zmiešavanie a spracovanie:
- Vysokoteplotné reaktory s presnými riadiacimi systémami
- Špecializované zariadenia na vytláčanie a peletizáciu
- Pokročilé systémy filtrácie a čistenia
- Komplexné zariadenia na kontrolu kvality a testovanie
Tieto kapitálové investície sú značné a významne prispievajú ku konečným nákladom na materiál. Keď v spoločnosti PTSMAKE obrábame diely z PEEK, tieto výrobné náklady na začiatku výrobného procesu dedíme v cene suroviny.
Výzvy pri spracovaní a obrábaní
Po výrobe predstavuje PEEK ďalšie výzvy pri spracovaní a obrábaní, ktoré ďalej prispievajú k jeho vysokej cene v hotových komponentoch.
Vysoké teploty spracovania
PEEK s teplotou topenia približne 343 °C si vyžaduje špecializované spracovateľské zariadenie:
- Vstrekovacie stroje s vysokoteplotnými funkciami
- Formy so špeciálnymi systémami riadenia tepla
- Drahšie vykurovacie telesá a regulátory
- Vylepšené bezpečnostné systémy na manipuláciu s vysokoteplotnými materiálmi
Tieto požiadavky znamenajú, že na spracovanie PEEK je vybavených menej výrobcov, čo obmedzuje hospodársku súťaž a udržiava vyššie náklady na spracovanie.
Úvahy o obrábaní a opotrebovaní nástrojov
Pri obrábaní PEEK pri PTSMAKE sa stretávame s niekoľkými faktormi, ktoré prispievajú k vyšším výrobným nákladom:
Opotrebovanie nástrojov: PEEK spôsobuje podstatne väčšie opotrebovanie nástrojov ako štandardné plasty, čo si vyžaduje častejšiu výmenu nástrojov alebo používanie prémiových nástrojov.
Riadenie tepla: Nízka tepelná vodivosť PEEK znamená, že počas obrábania sa hromadí teplo, čo si vyžaduje nižšie rezné rýchlosti a špeciálne techniky chladenia.
Špecializované odborné znalosti: Správne obrábanie PEEK si vyžaduje skúsenosti a znalosti, aby sa zabránilo degradácii materiálu a dosiahli sa prísne tolerancie.
Požiadavky na následné spracovanie: Mnohé aplikácie PEEK si vyžadujú ďalšie kroky spracovania, ako je žíhanie, aby sa zmiernili vnútorné napätia a zabezpečila rozmerová stabilita.
Každý z týchto faktorov zvyšuje celkové náklady na výrobu hotových komponentov PEEK nad rámec ceny surovín.
Náklady na kontrolu kvality a certifikáciu
PEEK ako vysoko výkonný materiál, ktorý sa často používa v kritických aplikáciách, si vyžaduje prísnu kontrolu kvality počas celej výroby a spracovania.
Prísne požiadavky na testovanie
Každá šarža PEEK sa zvyčajne podrobuje rozsiahlemu testovaniu na overenie:
- Rozdelenie molekulovej hmotnosti
- Percento kryštalinity
- Tepelné vlastnosti (teploty sklovitého prechodu a topenia)
- Mechanické vlastnosti (pevnosť v ťahu, modul pružnosti, predĺženie)
- Čistota a úrovne kontaminantov
Tieto testy si vyžadujú špecializované vybavenie a vyškolený personál, čo zvyšuje konečnú cenu výrobku o značné náklady na zabezpečenie kvality.
Priemyselné certifikáty a vysledovateľnosť
Mnohé aplikácie PEEK v leteckom, lekárskom a polovodičovom priemysle si vyžadujú úplnú sledovateľnosť materiálu a súlad s priemyselnými normami:
- Certifikácie pre letecký priemysel (AS9100, NORSOK)
- Normy pre zdravotnícke pomôcky (ISO 13485, USP Class VI)
- Certifikáty pre jadrový priemysel (NQSA-1)
- Požiadavky polovodičového priemyslu (vysoká čistota)
Udržiavanie týchto certifikátov si vyžaduje rozsiahlu dokumentáciu, pravidelné audity a niekedy aj samostatné výrobné zariadenia alebo vybavenie, čo všetko prispieva k vyšším nákladom.
Porovnanie PEEK s alternatívnymi materiálmi
Na pochopenie ceny PEEK v kontexte je užitočné porovnať ho s alternatívnymi materiálmi z hľadiska nákladov aj výkonu.
Analýza nákladov a výkonnosti
PEEK zvyčajne stojí 5 až 10-krát viac ako štandardné technické plasty a v objemovom meradle môže byť dokonca drahší ako niektoré špeciálne kovy. Jeho výkonnosť v extrémnych prostrediach však často ospravedlňuje tento príplatok:
Vlastníctvo | PEEK | Štandardné technické plasty | Prémiové kovy |
---|---|---|---|
Teplota nepretržitého používania | Do 250 °C (480 °F) | 80-170°C (176-338°F) | Zvyčajne neobmedzené |
Chemická odolnosť | Vynikajúce | Variabilné (často obmedzené) | Často zlé (korózia) |
Špecifická sila | Veľmi vysoká | Mierne | Vysoká |
Náklady na suroviny | Veľmi vysoká | Nízka až stredne vysoká | Mierne až vysoké |
Náklady na spracovanie | Vysoká | Nízka až stredne vysoká | Vysoká |
Hodnota životnosti | Vynikajúce | Obmedzené v drsných podmienkach | Dobrý, ale s problémami s koróziou |
V spoločnosti PTSMAKE často pomáhame klientom vyhodnotiť tieto kompromisy, aby sme určili, či je prémiová cena PEEK odôvodnená jeho výkonnostnými výhodami v ich konkrétnej aplikácii.
Stojí PEEK za vyššiu cenu?
Otázka, či je vysoká cena PEEK-u opodstatnená, závisí výlučne od požiadaviek na aplikáciu.
Aplikácie, v ktorých PEEK poskytuje hodnotu napriek nákladom
PEEK poskytuje vynikajúcu hodnotu napriek svojej vysokej cene v aplikáciách, ktoré obsahujú:
- Extrémne prevádzkové prostredia tam, kde by iné materiály rýchlo zlyhali.
- Systémy s kritickou hmotnosťou kde pomer pevnosti k hmotnosti PEEK ponúka výhody
- Zariadenia citlivé na údržbu kde náklady na prestoje vysoko prevyšujú náklady na materiál
- Korózne prostredia kde by kovy rýchlo degradovali
- Lekárske implantáty kde sú biokompatibilita a dlhodobá stabilita nevyhnutné.
V týchto scenároch sa výkonnostné výhody PEEK priamo premietajú do nižších nákladov počas životnosti napriek vyššej počiatočnej investícii.
Stratégie znižovania nákladov na komponenty PEEK
V prípade projektov, ktoré vyžadujú výkonnosť PEEK, ale sú obmedzené rozpočtom, zvážte tieto prístupy:
- Hybridné konštrukcie používanie PEEK len pre kritické komponenty
- Optimalizované techniky obrábania znížiť materiálový odpad
- Spracovanie takmer sieťového tvaru minimalizovať spotrebu materiálu
- Optimalizácia dizajnu na zníženie celkového objemu materiálu
- Nevyplnené triedy keď nie je potrebné posilniť výkon.
V spoločnosti PTSMAKE sme pomohli mnohým klientom implementovať tieto stratégie, aby získali výhody PEEK a zároveň efektívne riadili náklady.
Ako optimalizovať obrábanie PEEK pre nákladovo efektívnu výrobu?
Premýšľali ste niekedy, či existuje spôsob, ako využiť výnimočné vlastnosti PEEK bez toho, aby ste porušili rozpočet projektu? Pri práci s jedným z najdrahších technických plastov na trhu nie je optimalizácia obrábania len o efektivite - môže znamenať rozdiel medzi ziskovým projektom a projektom, ktorý stráca peniaze v dôsledku nadmerného plytvania materiálom a zbytočného času obrábania.
Optimalizácia obrábania PEEK pre nákladovo efektívnu výrobu si vyžaduje používanie správnych rezných nástrojov (karbidových alebo s diamantovým povlakom), udržiavanie vhodných rýchlostí a posuvov (zvyčajne pomalších ako pri štandardných plastoch), implementáciu účinných stratégií chladenia, minimalizáciu plytvania materiálom prostredníctvom konštrukcie s takmer čistým tvarom a starostlivé plánovanie dráh nástrojov na skrátenie časov cyklu.
Výber optimálneho nástroja na obrábanie PEEK
Pri obrábaní PEEK má výber nástrojov zásadný vplyv na kvalitu dielov aj na celkové náklady na obrábanie. Na základe dlhoročných skúseností som sa naučil, že investícia do správnych nástrojov vopred ušetrí z dlhodobého hľadiska podstatne viac.
Materiály a geometrie rezných nástrojov
Abrazívny charakter PEEK, najmä plnených druhov obsahujúcich uhlíkové vlákna alebo sklo, si vyžaduje starostlivý výber nástrojov:
Materiál nástroja | Najlepšie pre | Životnosť nástroja | Faktor nákladov |
---|---|---|---|
Karbid (bez povrchovej úpravy) | Nevyplnený PEEK | Dobrý | Mierne |
Karbid s diamantovým povlakom | Plnený PEEK | Vynikajúce | Vysoká |
PCD (polykryštalický diamant) | Veľkoobjemová výroba | Superior | Veľmi vysoká |
Rýchlorezná oceľ (HSS) | Jednoduché operácie s nenaplneným PEEK | Obmedzené | Nízka |
Pri väčšine aplikácií v spoločnosti PTSMAKE používame karbidové nástroje so špecifickou geometriou navrhnutou pre vysoko výkonné plasty. Medzi kľúčové vlastnosti, ktoré hľadáme, patria:
- Ostré rezné hrany (znižuje tvorbu tepla)
- Vysoké pozitívne uhly sklonu (10-15°)
- Leštené drážky (zlepšuje odvod triesok)
- Dostatočné uhly vôle (zabraňujú treniu)
Hoci prvotné náklady na prémiové nástroje sú vyššie, udržujú ostrosť hrán dlhšie a vytvárajú lepšie povrchové úpravy, čím znižujú potrebu sekundárnych operácií.
Úvahy o opotrebovaní nástrojov
Pri obrábaní PEEK dochádza k oveľa rýchlejšiemu opotrebovaniu nástrojov v porovnaní so štandardnými technickými plastmi. Zistili sme, že monitorovanie a riadenie opotrebovania nástrojov je rozhodujúce pre udržanie kvality dielov aj kontroly nákladov.
Odporúčam stanoviť plán výmeny nástrojov na základe objemu obrábania, a nie čakať na vizuálne známky opotrebenia. V našej dielni sa nástroje na obrábanie plneného PEEK zvyčajne menia približne po 60-70% životnosti nástroja, ktorú by sme očakávali pri obrábaní hliníka. Tento proaktívny prístup zabraňuje problémom s kvalitou a potenciálnym vyradeným dielom, ktoré sú výsledkom obrábania s opotrebovanými nástrojmi.
Optimalizácia rezných parametrov
Pre efektívne obrábanie PEEK je rozhodujúce nájsť správnu rovnováhu medzi rýchlosťou, posuvom a hĺbkou rezu. Cieľom je maximalizovať rýchlosť úberu materiálu bez vzniku nadmerného tepla alebo zhoršenia kvality povrchu.
Odporúčania týkajúce sa rýchlosti a kŕmenia
Na základe rozsiahleho testovania v spoločnosti PTSMAKE sme vypracovali tieto všeobecné pokyny pre parametre obrábania PEEK:
Typ PEEK | Rýchlosť rezania (SFM) | Rýchlosť podávania | Hĺbka rezu | Chladiaca kvapalina |
---|---|---|---|---|
Nevyplnený PEEK | 300-500 | Mierne | 0.005"-0.020" | Vzduch alebo hmla |
30% Plnené uhlíkom | 200-400 | Znížená (75%) | 0.005"-0.015" | Hmla/povodeň |
30% Sklenená výplň | 250-450 | Znížená (85%) | 0.005"-0.015" | Hmla/povodeň |
Tieto parametre by sa mali upraviť na základe konkrétneho nástroja, tuhosti stroja a požiadaviek na diel. Vo všeobecnosti odporúčam začať na konzervatívnom konci týchto rozsahov a postupne zvyšovať parametre pri sledovaní výsledkov.
Stratégie riadenia tepla
Slabá tepelná vodivosť PEEK môže viesť k nahromadeniu tepla počas obrábania, čo môže spôsobiť:
- Rozmerová nestabilita
- Zhoršená povrchová úprava
- Zrýchlené opotrebovanie nástrojov
- Rozklad materiálu v extrémnych prípadoch
Na boj proti týmto problémom sme implementovali niekoľko techník tepelného manažmentu:
Správny výber chladiacej kvapaliny: V prípade neplneného PEEK-u sa často osvedčuje chladenie stlačeným vzduchom. Pri plnených triedach poskytuje lepší odvod tepla hmla alebo zalievacia chladiaca kvapalina.
Prerušované rezanie: Pravidelné prestávky počas operácií hlbokého vysekávania vreciek umožňujú odvádzanie tepla.
Frézovanie stúpania: Použitie stúpavého frézovania namiesto bežného frézovania znižuje trenie a tvorbu tepla.
Viacnásobné prechody svetla: Niekoľko ľahkých dokončovacích rezov namiesto jedného ťažkého rezu zlepšuje rozmerovú presnosť a kvalitu povrchu.
Stratégie využívania materiálov
Vzhľadom na vysokú cenu PEEK (často $75-200 za libru v závislosti od triedy a formy) sa využitie materiálu stáva rozhodujúcim nákladovým faktorom. Každý kúsok odpadu má priamy vplyv na vaše hospodárske výsledky.
Východiskový materiál v tvare blízkej sieti
Ak začnete s materiálom, ktorý je bližšie k vašim konečným rozmerom, môžete výrazne znížiť množstvo odpadu. Zvážte tieto prístupy:
Vlastné výlisky: V prípade dielov s konzistentným prierezom sa môže začať s vlastnými vytlačovanými profilmi, čím sa eliminuje značné plytvanie materiálom. Vyššie zriaďovacie náklady sú kompenzované úsporou materiálu pri väčších výrobných sériách.
Predrezané polotovary: Ak vám dodávateľ materiálu poskytne predrezané polotovary s rozmermi presne pre vaše diely, zníži sa množstvo odpadu aj počiatočný čas obrábania.
Softvér pre hniezdenie: V prípade plochých dielov obrábaných z plechu môže použitie pokročilého softvéru na vytváranie hniezd optimalizovať využitie materiálu o 15-30% v porovnaní s ručným plánovaním rozloženia.
V spoločnosti PTSMAKE sme pomohli klientom znížiť náklady na materiál PEEK o viac ako 40% zavedením týchto prístupov pre ich veľkoobjemové komponenty.
Úvahy o recyklácii čipov
Na rozdiel od niektorých termoplastov sa PEEK nedá ľahko recyklovať vo vnútri podniku kvôli vysokej teplote spracovania. Existujú však špecializované recyklačné služby:
- Čisté, vytriedené čipy PEEK sa môžu predávať recyklátorom
- Niektoré recyklačné spoločnosti započítavajú hodnotu materiálu oproti budúcim nákupom
- Plnené triedy majú zvyčajne nižšiu recyklačnú hodnotu z dôvodu kontaminácie
Recyklácia síce úplne nevyrovná vaše náklady na materiál, ale môže zabezpečiť určitú návratnosť nákladov pri väčších obrábacích operáciách.
Optimalizácia stratégie obrábania
Okrem nástrojov a parametrov má celkový prístup k obrábaniu významný vplyv na kvalitu dielov aj na výrobné náklady.
Návrh prípravkov pre viacero dielov
Dobre navrhnuté upínacie prípravky, ktoré umožňujú obrábanie viacerých dielov v rámci jedného nastavenia, ponúkajú niekoľko výhod:
- Skrátenie času nastavenia na jeden diel
- Zlepšená konzistentnosť jednotlivých častí
- Efektívnejšie využívanie strojov
- Lepšia výťažnosť materiálu z plechových zásob
Pre jedného klienta z oblasti leteckej výroby sme navrhli prípravok, ktorý umožnil obrábať 16 malých komponentov PEEK súčasne, čím sa znížili náklady na jeden diel o 62% v porovnaní s jednotlivými nastaveniami.
Spresnenie stratégie CAM
Optimalizované dráhy nástrojov môžu výrazne skrátiť čas obrábania a zlepšiť kvalitu dielov:
Vysokoúčinné frézovanie: Používanie pokročilých stratégií CAM, ktoré udržujú konzistentný záber nástroja, skracuje časy cyklov a predlžuje životnosť nástroja.
Obrábanie zvyškov: Správne zoradené operácie, pri ktorých sa používajú väčšie nástroje na úber väčšieho množstva materiálu a menšie nástroje len v prípade potreby, optimalizujú rýchlosť úberu materiálu aj životnosť nástrojov.
Optimalizované prístupové pohyby: Minimalizácia rezania vzduchom prostredníctvom účinných približovacích a zasúvacích pohybov môže skrátiť čas cyklu o 5-15% bez vplyvu na kvalitu dielov.
Kontrola kvality na minimalizáciu odpadu
Vzhľadom na vysoké náklady na materiál PEEK sa hlavnou stratégiou úspory nákladov stáva zníženie množstva odpadu. Účinné procesy kontroly kvality, ktoré včas zachytia problémy, zabraňujú plytvaniu drahým materiálom na diely, ktoré nespĺňajú špecifikácie.
Meranie v procese
Zaviedli sme niekoľko krokov overovania počas procesu:
Kontrola prvého článku: Pred začatím výroby dôkladne zmerajte prvú časť každej série.
Etapové inšpekcie: Meranie kritických prvkov pred pokračovaním v ďalších operáciách, najmä pri obracaní alebo opätovnom profilovaní dielov.
Tepelná stabilizácia: Pred konečným meraním nechajte diely dosiahnuť teplotu okolia, pretože tepelná rozťažnosť PEEK môže ovplyvniť rozmery.
Tieto postupy nám pomohli udržať mieru zmetkovitosti PEEK komponentov pod 2%, čo je výrazne menej ako priemer v odvetví.
Úvahy po obrábaní
Proces sa nekončí, keď diel vyjde zo stroja. Operácie po obrábaní môžu výrazne ovplyvniť kvalitu aj náklady.
Odľahčenie napätia a rozmerová stabilita
Diely z PEEK so zložitou geometriou alebo nerovnomerným úberom materiálu môžu mať prospech z odľahčenia napätia, aby sa zabezpečila dlhodobá rozmerová stabilita:
Tepelné žíhanie: Riadené zahrievanie pod teplotu sklovitého prechodu a následné pomalé ochladzovanie môže zmierniť vnútorné napätie.
Stratégia od hrubej po konečnú fázu: Odstránenie väčšiny materiálu pri prvej operácii a následné ustálenie súčiastky pred konečným obrábaním zlepšuje rozmerovú presnosť.
V prípade kritických komponentov s prísnymi toleranciami sa oplatí investovať do týchto dodatočných krokov, aby sa predišlo nákladným poruchám v teréne alebo posunu rozmerov v priebehu času.
Implementáciou týchto optimalizačných stratégií sme pomohli mnohým klientom spoločnosti PTSMAKE dosiahnuť nákladovo efektívne obrábanie PEEK bez toho, aby sme ohrozili výnimočné výkonnostné vlastnosti, ktoré robia tento materiál takým cenným. Kľúčom je holistický prístup, ktorý zohľadňuje každý aspekt výrobného procesu, od výberu materiálu až po záverečnú kontrolu.
Zoznámte sa s technikami tepelného manažmentu pre vysokovýkonné obrábanie plastov. ↩
Naučte sa pokročilé techniky presného obrábania vysoko výkonných termoplastov. ↩
Kliknutím sem si môžete prezrieť špecializované techniky na presné obrábanie vysoko výkonných termoplastov. ↩
Zistite, ako mechanické vlastnosti ovplyvňujú výber materiálu pre vysoko výkonné komponenty. ↩
Naučte sa špecializované techniky obrábania na zabránenie deformáciám spôsobeným teplom pri vysoko výkonných termoplastoch. ↩