Kämpar du med att hitta rätt material för krävande applikationer där standardplaster inte räcker till? Många ingenjörer ställs inför utmaningar när komponenterna måste klara extrema temperaturer, kemikalier eller mekanisk påfrestning. Traditionella plaster håller helt enkelt inte måttet, vilket leder till frekventa fel på delar och kostsamma utbyten.
PEEK-bearbetning är en process där man skär, borrar och formar polyetereterketonmaterial (PEEK) med hjälp av CNC-maskiner. Denna högpresterande termoplast erbjuder exceptionell värmebeständighet upp till 480 °F, enastående kemisk beständighet och styrka som kan jämföras med vissa metaller.
Jag har arbetat med otaliga kunder som har gått över till PEEK-bearbetning för sina kritiska komponenter. Resultaten talar för sig själva - delar med längre livslängd, bättre prestanda i tuffa miljöer och kortare underhållscykler. Om du undrar om PEEK kan vara lösningen för din applikation, fortsätt läsa för att upptäcka de unika egenskaper och bearbetningstekniker som gör detta material så värdefullt inom precisionstillverkning.
Är PEEK bättre än Delrin för maskinbearbetning?
Har du någonsin hamnat mitt i ett materialvalsdilemma, sliten mellan PEEK och Delrin för ditt kritiska ingenjörsprojekt? När prestanda är viktigt och fel inte är ett alternativ kan valet av fel plast leda till för tidigt slitage, driftstopp och kostsamma omkonstruktioner.
Medan PEEK erbjuder överlägsen temperaturbeständighet (upp till 480 °F), exceptionell kemisk stabilitet och högre hållfasthet, ger Delrin (POM) bättre bearbetbarhet, dimensionsstabilitet och lägre kostnad. Vilket som är det "bättre" valet beror helt på dina specifika applikationskrav och budgetbegränsningar.
Förstå PEEK och Delrin: Grundläggande skillnader
När man jämför dessa två högpresterande tekniska plaster är det viktigt att förstå deras grundläggande sammansättning och egenskaper. PEEK (polyetereterketon) är en halvkristallin termoplast med exceptionell motståndskraft mot termisk nedbrytning, medan Delrin (polyoximetylen eller POM) är en acetalhomopolymer som är känd för sin utmärkta dimensionsstabilitet.
Jämförelse av materialegenskaper
De fysiska och mekaniska egenskaperna hos dessa material påverkar i hög grad deras bearbetningsegenskaper och prestanda vid slutanvändningen.
Fastighet | PEEK | Delrin (POM) |
---|---|---|
Värme Avböjningstemperatur | 157°C (315°F) | 125°C (257°F) |
Draghållfasthet | 14.500 psi | 10.000 psi |
Kemisk beständighet | Utmärkt (motstår de flesta syror och baser) | Bra (känslig för starka syror) |
Motståndskraft mot slitage | Överlägsen | Mycket bra |
Kostnadsfaktor | 4-5× högre än Delrin | Måttlig |
Täthet | 1,32 g/cm³ | 1,41 g/cm³ |
Bearbetningsegenskaper: Hur de presterar under verktyget
Min erfarenhet på PTSMAKE är att bearbetbarheten ofta är den avgörande faktorn när man väljer mellan dessa material. Delrin bearbetas i allmänhet mer förutsägbart än PEEK och ger jämnare ytfinish med mindre ansträngning.
Verktygsslitage och skärparametrar
PEEK sliter hårdare på skärverktygen och kräver oftare verktygsbyten. Vid bearbetning av PEEK minskar vi vanligtvis skärhastigheten med ca 15-20% jämfört med Delrin för att minimera värmeutvecklingen. Detta är avgörande eftersom PEEK:s låga värmeledningsförmåga orsakar värmekoncentration i skärzonen, vilket kan leda till termisk deformation1 om den inte hanteras på rätt sätt.
Delrin, å andra sidan, erbjuder utmärkt dimensionsstabilitet under bearbetning och kan skäras i högre hastigheter. Det ger mindre verktygsslitage och kräver i allmänhet färre specialiserade bearbetningstekniker.
Överväganden om ytfinish
En fördel med Delrin är dess förmåga att uppnå utmärkt ytfinish med standardbearbetningsparametrar. PEEK kräver ofta ytterligare poleringssteg för att uppnå jämförbar ytkvalitet.
Kostnads- och nyttoanalys för tekniska tillämpningar
Kostnadsskillnaden mellan dessa material kan vara betydande. PEEK kostar vanligtvis 4-5 gånger mer än Delrin, vilket gör det viktigt att utvärdera om dess premiumegenskaper motiverar investeringen.
När PEEK rättfärdigar sitt premiumpris
Jag rekommenderar PEEK för applikationer som involverar:
- Extrema driftstemperaturer (över 250°F)
- Aggressiva kemiska miljöer
- Hög mekanisk belastning vid förhöjda temperaturer
- Medicinska tillämpningar eller tillämpningar inom flyg- och rymdindustrin som kräver biokompatibilitet eller flamskydd
När Delrin är det bättre valet
Delrin är mer ekonomiskt vettigt när:
- Driftstemperaturen förblir under 180°F
- Kemisk exponering är begränsad till måttliga lösningsmedel
- Kostnadskänslighet är en viktig faktor
- Delar som kräver utmärkt dimensionsstabilitet och maskinbearbetad precision
- Höga produktionsvolymer gör materialkostnaden till en betydande faktor
Branschspecifika överväganden
Olika branscher prioriterar olika materialegenskaper. Inom flygindustrin, där vi har levererat många komponenter, motiverar PEEK:s flamskydd och exceptionella förhållande mellan styrka och vikt ofta den högre kostnaden. För fordonstillämpningar är det ofta Delrins kombination av rimlig kostnad och goda mekaniska egenskaper som vinner.
Tillämpningar inom medicin och livsmedelsbearbetning
För medicintekniska produkter är PEEK ovärderligt tack vare sin biokompatibilitet och steriliseringsbeständighet, trots den högre kostnaden. När det gäller utrustning för livsmedelsbearbetning är Delrin ofta det bästa valet eftersom det uppfyller FDA:s krav och är billigare, såvida det inte handlar om höga temperaturer.
Komponenter till industrimaskiner
I industriella tillämpningar har jag sett att beslutet ofta handlar om driftsförhållanden. Kugghjul, lager och slitdelar som arbetar under måttliga förhållanden fungerar utmärkt i Delrin, medan de som utsätts för extrema förhållanden drar nytta av PEEK:s överlägsna egenskaper.
Gör rätt val för din applikation
Valet mellan PEEK och Delrin bör grundas på en noggrann analys av dina specifika driftsförhållanden. På PTSMAKE överväger vi:
- Maximal driftstemperatur
- Kemisk exponeringsprofil
- Krav på mekanisk belastning
- Budgetrestriktioner
- Förväntad livslängd
Genom att noggrant utvärdera dessa faktorer mot varje materials egenskaper kan du fatta ett välgrundat beslut som balanserar prestanda och kostnadseffektivitet för din specifika applikation.
Vad är skillnaden mellan Acetal och PEEK?
Har du någonsin haft svårt att välja mellan acetal och PEEK för dina kritiska tekniska komponenter? När projektframgången hänger på materialvalet kan fel val leda till för tidiga fel, oväntade driftstopp och budgetöverskridande omkonstruktioner som hade kunnat undvikas med rätt materialkunskap.
Acetal (POM) och PEEK skiljer sig främst åt när det gäller prestanda och kostnad. PEEK erbjuder överlägsen värmebeständighet (480 °F jämfört med 180 °F), bättre kemisk beständighet och högre hållfasthet, medan acetal ger utmärkt bearbetbarhet, dimensionsstabilitet och kostar betydligt mindre, vilket gör den idealisk för mindre krävande applikationer.
De viktigaste skillnaderna mellan Acetal och PEEK
Att förstå de grundläggande skillnaderna mellan dessa två tekniska plaster är avgörande för att kunna fatta välgrundade beslut för dina projekt. Båda materialen har etablerat sig som förstahandsalternativ inom precisionstillverkning, men de tjänar distinkt olika syften baserat på deras inneboende egenskaper.
Materialets sammansättning och struktur
Acetal, allmänt känt under varumärket Delrin (när det är i homopolymerform) eller under det kemiska namnet polyoximetylen (POM), har en högkristallin struktur med repetitiva -CH₂O-grupper. Denna struktur ger en utmärkt dimensionsstabilitet och maskinbearbetbarhet.
PEEK (polyeteretereterketon), å andra sidan, tillhör familjen polyaryleterketoner och innehåller aromatiska ringar som är förbundna med eter- och ketonbindningar. Denna molekylära struktur skapar exceptionell termisk stabilitet och kemisk resistens.
Jämförelse av prestandaegenskaper
Skillnaderna i prestanda mellan dessa material gör att de lämpar sig för olika tillämpningar:
Fastighet | Acetal (POM) | PEEK | Bäst för |
---|---|---|---|
Värmebeständighet | 82°C (180°F) kontinuerligt | 250°C (480°F) kontinuerligt | PEEK |
Kemisk beständighet | Bra (utom starka syror) | Utmärkt (motståndskraftig mot de flesta kemikalier) | PEEK |
Draghållfasthet | 8.800-10.000 psi | 14.500-16.000 psi | PEEK |
Motståndskraft mot slitage | Mycket bra | Utmärkt | PEEK |
Bearbetbarhet | Utmärkt | Bra (kräver specialiserad teknik) | Acetal |
Kostnadsfaktor | Basreferens (1×) | 4-7× högre än Acetal | Acetal |
Fuktabsorption | 0.2-0.25% | 0.1-0.15% | PEEK |
Kostnads- och nyttoanalys
Under de år som jag har arbetat med kunder på PTSMAKE har jag märkt att det ofta är kostnadsaspekten som styr det första materialvalet. Acetal är betydligt mer ekonomiskt än PEEK, vilket gör det till standardvalet när det inte råder extrema förhållanden.
PEEK:s premiumpris återspeglar dess överlägsna prestanda. När du utvärderar om den extra investeringen är motiverad bör du ta hänsyn till följande faktorer:
- Krav på driftstemperatur
- Kemisk exponeringsprofil
- Mekaniska påfrestningsnivåer
- Förväntad livslängd
- Kostnader för stilleståndstid i samband med komponentfel
Överväganden om maskinbearbetning
Verktygslivslängd och skärparametrar
Acetal är känt för sin exceptionella bearbetbarhet. Det skär rent, håller snäva toleranser och ger utmärkt ytfinish med minimal ansträngning. Standardverktyg i hårdmetall fungerar bra och materialet orsakar inte överdrivet verktygsslitage.
PEEK innebär fler utmaningar vid maskinbearbetning. Dess höga temperaturbeständighet innebär att värmeavledningen under bearbetningen är dålig, vilket kräver:
- Lägre skärhastigheter (typiskt 20-30% långsammare än acetal)
- Mer frekventa verktygsbyten
- Noggrann uppmärksamhet på värmeutveckling
- Specialiserad kylteknik
På PTSMAKE har vi utvecklat specifika protokoll för termisk hantering2 för PEEK-bearbetning för att säkerställa måttnoggrannhet och förhindra materialnedbrytning under skärprocessen.
Dimensionell stabilitet
Acetal ger utmärkt dimensionsstabilitet efter bearbetning, med minimal skevhet eller spänningsavlastning. Detta gör det särskilt värdefullt för precisionskomponenter med snäva toleranser.
PEEK uppvisar också god dimensionsstabilitet men kräver mer noggranna glödgningsprocesser för att minska inre spänningar efter bearbetning. Utan korrekt termisk konditionering kan PEEK-delar uppleva små dimensionsförändringar över tid, särskilt i högprecisionsapplikationer.
Applikationsspecifika rekommendationer
Fordon och transport
I fordonstillämpningar där temperaturen är måttlig (under 180°F) ger acetal ofta det bästa värdet. Vanliga applikationer inkluderar:
- Bränslesystemets komponenter
- Låsmekanismer för dörrar
- Clips och fästanordningar för invändiga lister
- Lagerytor i icke-kritiska områden
För områden med högre temperaturer, t.ex. komponenter under huven eller delar nära avgassystem, gör PEEK:s termiska stabilitet det till ett bättre val trots den högre kostnaden.
Medicinska och farmaceutiska produkter
Den medicinska industrin har anammat PEEK för dess biokompatibilitet och motståndskraft mot steriliseringsmetoder. Det används ofta i:
- Implanterbara enheter
- Kirurgiska instrument
- Komponenter för medicinsk bildbehandling
- Laboratorieutrustning
Acetal används fortfarande i mindre krävande medicinska miljöer, t.ex:
- Instrumentkomponenter för engångsbruk
- Testfixturer för laboratorier
- Höljen för diagnostisk utrustning
Industriell utrustning
För industrimaskiner beror valet ofta på driftsförhållandena:
- Standard driftsmiljöer: Acetal ger utmärkt värde för kugghjul, lager och slitytor under normala förhållanden.
- Tuffa miljöer: PEEK motiverar sitt premiumpris när det utsätts för höga temperaturer, kemikalier eller extrema mekaniska påfrestningar.
Gör det optimala urvalet
När jag hjälper kunder att välja mellan acetal och PEEK vid PTSMAKE rekommenderar jag ett systematiskt tillvägagångssätt:
- Identifiera de mest krävande förhållanden som detaljen kommer att utsättas för (temperatur, kemikalier, belastningar)
- Fastställ om acetals egenskaper är tillräckliga för att hantera dessa förhållanden
- Beräkna kostnadsskillnaden mellan alternativen för dina specifika volymkrav
- Beakta konsekvenserna av ett fel och kostnaderna för stilleståndstid
- Utvärdera om PEEK:s förstklassiga prestanda motiverar dess högre pris
Kom ihåg att materialval sällan är en lösning som passar alla. Ibland fungerar en hybridmetod bäst, där PEEK endast används för de mest kritiska komponenterna medan acetal används för mindre krävande delar inom samma enhet.
Vad är skillnaden mellan PTFE och PEEK?
Har du någonsin gått vilse i mängden av högpresterande plaster och varit osäker på om du ska välja PTFE eller PEEK för din kritiska applikation? När tidsfristerna för projektet närmar sig och materialvalet kan vara avgörande för din design kan pressen att göra rätt val vara överväldigande, särskilt när båda materialen har imponerande tekniska specifikationer.
PTFE och PEEK är båda högpresterande termoplaster med tydliga skillnader. PTFE har oöverträffad kemisk beständighet, extremt låg friktion (koefficient 0,05-0,10) och kan användas från -328°F till 500°F, men har dålig mekanisk styrka. PEEK ger överlägsna mekaniska egenskaper, utmärkt slitstyrka och bibehåller strukturell integritet upp till 480 °F samtidigt som det är mer bearbetningsbart.
Molekylstruktur och grundläggande egenskaper
De grundläggande skillnaderna mellan PTFE och PEEK börjar på molekylär nivå, vilket förklarar deras olika prestandaegenskaper i olika applikationer.
Kemisk sammansättning
PTFE (polytetrafluoretylen) har en kolstomme som är helt omgiven av fluoratomer. Denna unika struktur ger PTFE dess exceptionella kemiska inerthet och låga friktionsegenskaper. Kol-fluorbindningarna är bland de starkaste inom den organiska kemin, vilket gör PTFE otroligt motståndskraftigt mot kemiska angrepp.
PEEK (polyetereterketon) har däremot en mer komplex molekylstruktur med aromatiska ringar som är sammankopplade med eter- och ketonbindningar. Denna aromatiska ryggrad ger PEEK dess utmärkta mekaniska styrka och termiska stabilitet.
Jämförande fastighetsanalys
Fastighet | PTFE | PEEK | Fördel |
---|---|---|---|
Maximal temperatur vid kontinuerlig användning | 260°C (500°F) | 250°C (480°F) | PTFE (något) |
Minsta driftstemperatur | -328°F (-200°C) | -65°F (-54°C) | PTFE |
Friktionskoefficient | 0,05-0,10 (lägst av alla fasta ämnen) | 0.35-0.40 | PTFE |
Draghållfasthet | 3.000-5.000 psi | 14.000-16.000 psi | PEEK |
Kemisk beständighet | Överlägsen (universell) | Utmärkt (begränsas av starka syror) | PTFE |
Bearbetbarhet | Utmanande (mjuk, deformeras lätt) | Bra | PEEK |
Motståndskraft mot slitage | Dålig till måttlig | Utmärkt | PEEK |
Elektriska egenskaper | Utmärkt isolator | Bra isolator | PTFE |
Kostnadsfaktor | Måttlig | Hög (3-4× mer än PTFE) | PTFE |
Skillnader i termisk prestanda
Temperaturprestanda är ofta en kritisk faktor när man ska välja mellan dessa material.
Värmebeständighet och stabilitet
Båda materialen är mycket värmetåliga, men de beter sig olika vid förhöjda temperaturer. PTFE bibehåller sin kemiska inertitet och låga friktion upp till sin maximala temperatur, men börjar förlora sin mekaniska integritet vid mycket lägre temperaturer (ca 260 °F/127 °C).
PEEK bibehåller däremot sin mekaniska styrka mycket närmare sin maximala temperatur. Detta gör PEEK betydligt mer värdefullt i applikationer som kräver både värmebeständighet och mekanisk belastning.
Jag har sett många tillämpningar där kunderna först valde PTFE enbart på grund av temperaturklassningen, för att sedan upptäcka att materialet inte klarade de mekaniska påfrestningarna vid dessa temperaturer. PEEK:s förmåga att bibehålla strukturell integritet vid höga temperaturer gör att det ofta är värt det högre priset.
Prestanda vid kalla temperaturer
För kryogena tillämpningar har PTFE en klar fördel. Det förblir flexibelt och funktionellt ned till -200°C (-328°F), medan PEEK blir allt sprödare under -54°C (-65°F). Detta gör PTFE till det självklara valet för flyg- och rymdindustrin, laboratorier och andra miljöer med extremt låga temperaturer.
Jämförelse av mekanisk styrka
De mekaniska egenskaperna hos dessa material skiljer sig dramatiskt åt, vilket gör deras lämplighet applikationsspecifik.
Strukturell integritet under belastning
PEEK har en helt överlägsen mekanisk prestanda med en draghållfasthet på i genomsnitt 14.000-16.000 psi jämfört med PTFE:s blygsamma 3.000-5.000 psi. Detta gör PEEK lämpligt för lastbärande applikationer där PTFE snabbt skulle deformeras eller gå sönder.
På PTSMAKE rekommenderar vi ofta PEEK för strukturella komponenter som utsätts för konstant mekanisk belastning, särskilt vid förhöjda temperaturer. Materialets exceptionella krypmotstånd gör att det kan bibehålla dimensionsstabiliteten under kontinuerlig belastning.
Slitstyrka och friktion
PTFE:s anmärkningsvärt låga friktionskoefficient (0,05-0,10) gör det till det bästa materialet för applikationer som kräver minimal friktion. Samma egenskap bidrar dock till dess dåliga slitstyrka, eftersom materialet lätt kan skrapas bort i situationer med hög slitstyrka.
PEEK uppvisar utmärkt slitstyrka samtidigt som den har en rimlig friktionskoefficient (0,35-0,40). För applikationer som innebär kontinuerlig rörelse mot andra ytor är PEEK vanligtvis betydligt mer hållbart än PTFE.
Många av våra kunder uppnår det bästa av två världar genom att använda PEEK som konstruktionsmaterial med en tunn PTFE-beläggning eller liner där friktionsreducering behövs.
Profiler för kemisk resistens
Båda materialen erbjuder exceptionell kemisk beständighet, men med viktiga skillnader.
Motståndskraft mot aggressiva miljöer
PTFE representerar guldstandarden för kemisk resistens och är praktiskt taget inert mot nästan alla kemikalier (med sällsynta undantag som smälta alkalimetaller och elementärt fluor). Denna universella kemikaliebeständighet gör PTFE ovärderlig i kemisk bearbetning, halvledartillverkning och laboratoriemiljöer.
PEEK har utmärkt kemisk beständighet mot de flesta ämnen, men kan angripas av koncentrerad svavelsyra och vissa andra starka syror. För de flesta industriella miljöer är PEEK:s kemiska beständighet dock mer än tillräcklig.
Hydrolys och fuktabsorption
PTFE är helt hydrofobiskt och absorberar i stort sett ingen fukt, inte ens efter långvarig exponering. PEEK, som är mycket hydrolysresistent, absorberar en liten mängd fukt (0,1-0,3%) när det utsätts för fuktiga miljöer under längre perioder.
För applikationer med ultrarent vatten eller system där även små föroreningar är oacceptabla, är PTFE ofta det bästa valet trots sina mekaniska begränsningar.
%[Maskinbearbetade komponenter av PEEK och PTFE för strukturell jämförelse](
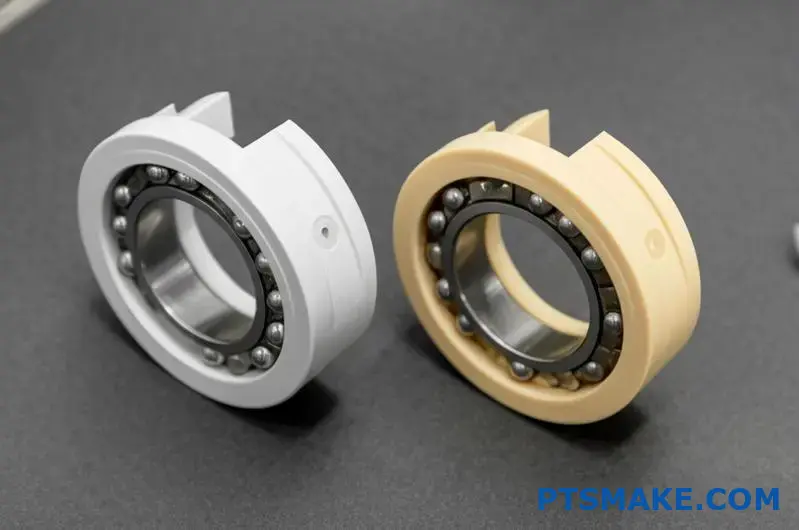
"PEEK- och PTFE-lagerkomponenter")
Bearbetning och tillverkning - överväganden
Den maskinbearbetbarhet3 Skillnaderna mellan dessa material påverkar tillverkningskostnaderna och -möjligheterna avsevärt.
Utmaningar och lösningar inom maskinbearbetning
PTFE innebär unika bearbetningsutmaningar på grund av sin mjukhet och tendens till kallflytning. Det kräver specialverktyg, långsammare skärhastigheter och noggrann fixturering för att förhindra deformation under bearbetningen. Vassa verktyg är avgörande för att förhindra att materialet rivs eller deformeras.
PEEK bearbetas mer som traditionell konstruktionsplast, även om dess abrasiva egenskaper orsakar snabbare verktygsslitage än många andra material. Vid bearbetning av PEEK använder vi vanligtvis hårdmetallverktyg och lämpliga kyltekniker för att hantera värmeutvecklingen.
Kompatibilitet med tillverkningsprocessen
PTFE:s höga smältviskositet gör konventionell formsprutning omöjlig. Istället måste det bearbetas med tekniker som kompressionsgjutning, ramsträngsprutning eller skiving från billets. Detta begränsar designkomplexiteten och ökar tillverkningskostnaderna för komplexa former.
PEEK kan bearbetas med konventionella metoder som formsprutning och extrudering, vilket möjliggör mer komplexa geometrier och potentiellt lägre produktionskostnader vid högre volymer. Denna mångsidiga bearbetningsmöjlighet ger PEEK en fördel för komplicerade komponenter eller vid övergång från prototyp- till massproduktion.
Kostnads-nyttoanalys för olika tillämpningar
Den betydande prisskillnaden mellan dessa material gör det nödvändigt att noga överväga deras applikationsspecifika värde.
Jämförelse av värdeerbjudande
Även om PEEK normalt kostar 3-4 gånger mer än PTFE, ger dess överlägsna mekaniska egenskaper och slitstyrka ofta ett bättre långsiktigt värde i applikationer där mekaniska fel skulle vara kostsamma eller farliga.
För applikationer som främst kräver kemisk beständighet, låg friktion eller elektriska isoleringsegenskaper utan betydande mekanisk påfrestning, erbjuder PTFE vanligtvis ett bättre värde trots sina begränsningar.
Branschspecifika urvalskriterier
Olika branscher prioriterar olika materialegenskaper:
- Kemisk bearbetning: PTFE:s universella kemiska beständighet uppväger vanligtvis dess mekaniska begränsningar.
- Flyg- och rymdindustrin: Båda materialen har användningsområden, där PEEK används för strukturella komponenter och PTFE för tätningar och elektrisk isolering.
- Medicinska tillämpningar: PEEK:s biokompatibilitet och strukturella styrka gör den populär för implantat, medan PTFE föredras för kateterfoder och andra applikationer med låg friktion.
- Halvledare: PTFE dominerar på grund av sin exceptionella renhet och motståndskraft mot aggressiva kemikalier.
- Fordon: PEEK:s slitstyrka och mekaniska egenskaper gör det värdefullt för komponenter under huven som utsätts för mekanisk belastning.
Vad är skillnaden mellan PVDF och PEEK?
Har du någonsin ställts inför dilemmat att välja mellan PVDF och PEEK för ett kritiskt projekt där materialvalet kan vara avgörande för din design? När standardplaster inte räcker till och du behöver exceptionell kemisk beständighet eller termisk stabilitet, kan förvirringen mellan dessa två högpresterande material leda till kostsamma misstag eller försämrad prestanda.
PVDF (polyvinylidenfluorid) och PEEK (polyetereterketon) skiljer sig främst åt när det gäller prestanda och användningsområden. PEEK erbjuder överlägsen värmebeständighet (480 °F jämfört med 300 °F), bättre mekanisk hållfasthet och exceptionell slitstyrka, medan PVDF ger utmärkt kemisk beständighet, UV-stabilitet och kommer till en betydligt lägre kostnad.
De viktigaste skillnaderna mellan PVDF och PEEK
När man jämför dessa två tekniska termoplaster är det viktigt att förstå deras grundläggande egenskaper för att kunna avgöra vilket material som är bäst lämpat för specifika tillämpningar. Båda materialen anses vara högpresterande alternativ, men de utmärker sig i olika miljöer och applikationer.
Materialets sammansättning och struktur
PVDF är en halvkristallin fluorpolymer som består av upprepade enheter av vinylidendifluorid. Dess molekylära struktur innehåller kol-fluorbindningar som ger utmärkt kemisk beständighet, men inte lika omfattande som helfluorerade polymerer som PTFE.
PEEK tillhör familjen polyaryleterketoner och har en komplex molekylstruktur med aromatiska ringar som är sammankopplade med eter- och ketonbindningar. Denna unika struktur ger PEEK dess exceptionella termiska stabilitet och mekaniska styrka.
Jämförelse av prestandaegenskaper
I följande tabell finns en detaljerad jämförelse av viktiga egenskaper mellan PVDF och PEEK:
Fastighet | PVDF | PEEK | Överlägset material |
---|---|---|---|
Maximal temperatur vid kontinuerlig användning | 149°C (300°F) | 250°C (480°F) | PEEK |
Mekanisk hållfasthet (draghållfasthet) | 5.800-7.800 psi | 14.500-16.000 psi | PEEK |
Kemisk beständighet | Utmärkt (de flesta syror och baser) | Mycket bra (begränsas av starka syror) | PVDF |
UV-beständighet | Utmärkt | Medelgod till god | PVDF |
Motståndskraft mot slitage | Bra | Utmärkt | PEEK |
Friktionskoefficient | 0.25-0.35 | 0.35-0.40 | PVDF |
Kostnadsfaktor | Måttlig | 2-3× högre än PVDF | PVDF |
Fuktabsorption | 0.03-0.04% | 0.1-0.15% | PVDF |
Täthet | 1,75-1,78 g/cm³ | 1,30-1,32 g/cm³ | Beroende på tillämpning |
Termisk prestanda och stabilitet
I många tekniska tillämpningar är det ofta temperaturegenskaperna som styr materialvalet.
Jämförelse av värmemotstånd
PEEK uppvisar exceptionell termisk stabilitet och bibehåller sina mekaniska egenskaper vid temperaturer upp till 250°C (480°F) vid kontinuerlig användning. Detta gör den idealisk för applikationer i högtemperaturmiljöer där traditionella plaster inte skulle fungera.
PVDF anses fortfarande vara en högtemperaturplast, men har en lägre maximal kontinuerlig användningstemperatur på ca 149°C (300°F). Detta temperaturområde är tillräckligt för många industriella tillämpningar, men räcker inte till i extrema termiska miljöer.
Enligt min erfarenhet av att arbeta med kunder på PTSMAKE blir denna temperaturskillnad ofta den avgörande faktorn när man väljer mellan dessa material för applikationer som utrustning för halvledarbearbetning, där processtemperaturerna kan överstiga PVDF:s kapacitet.
Beteende vid termisk cykling
Båda materialen hanterar termisk cykling på olika sätt:
- PVDF uppvisar god dimensionsstabilitet under termisk cykling, även om den kan uppleva mer betydande termisk expansion än PEEK.
- PEEK bibehåller en exceptionell dimensionsstabilitet även under upprepade termiska cykler, vilket gör den lämplig för precisionskomponenter som måste hålla snäva toleranser under varierande temperaturer.
Profiler för kemisk resistens
Kemikalieresistens är en annan avgörande faktor som skiljer dessa material åt.
Motståndskraft mot aggressiva miljöer
PVDF har utmärkt beständighet mot ett brett spektrum av kemikalier, t.ex:
- De flesta syror (inklusive koncentrerad saltsyra och svavelsyra)
- Alifatiska och aromatiska kolväten
- Alkoholer och klorerade lösningsmedel
- Oxiderande medel
PEEK uppvisar god kemisk beständighet mot många ämnen, men kan angripas av koncentrerad svavelsyra och vissa andra starka syror. Det är särskilt motståndskraftigt mot hydrolys och ångsterilisering, vilket gör det värdefullt i medicinska tillämpningar.
Branschspecifika kemiska överväganden
Olika branscher prioriterar specifika egenskaper för kemisk beständighet:
- Kemisk bearbetning: PVDF föredras ofta för sin omfattande beständighet mot syror och klorerade föreningar.
- Halvledare: Båda materialen används, och valet beror på specifika processkemikalier.
- Olja och gas: PEEK:s kombination av mekaniska egenskaper och kemisk resistens gör den värdefull för applikationer i borrhål.
- Farmaceutisk: PVDF:s utmärkta motståndskraft mot rengöringsmedel och steriliseringsmetoder gör den populär för processutrustning.
Mekaniska egenskaper och strukturella tillämpningar
Den mekanisk styrka4 Skillnaderna mellan dessa material påverkar i hög grad deras lämplighet för lastbärande applikationer.
Lastbärande förmåga
PEEK erbjuder betydligt högre mekanisk hållfasthet med draghållfasthetsvärden på 14.500-16.000 psi, jämfört med PVDF:s mer blygsamma 5.800-7.800 psi. Detta gör PEEK överlägset för strukturella komponenter som måste motstå betydande mekaniska belastningar.
För applikationer som kräver både kemikalieresistens och strukturell integritet ger PEEK ofta den bästa balansen mellan egenskaperna, trots sin högre kostnad. Jag har rekommenderat PEEK för många applikationer på PTSMAKE där komponenterna måste tåla både aggressiva kemikalier och mekanisk påfrestning.
Slitstyrka och friktionsegenskaper
PEEK har utmärkt slitstyrka, vilket gör det idealiskt för lager, bussningar och andra komponenter som utsätts för kontinuerlig friktion. Dess självsmörjande egenskaper bidrar till att förlänga livslängden på rörliga delar i krävande miljöer.
PVDF har god slitstyrka, dock inte i nivå med PEEK. Dess lägre friktionskoefficient (0,25-0,35 jämfört med PEEK:s 0,35-0,40) kan vara fördelaktig i vissa glidande applikationer med låg belastning där minskad friktion är viktigare än maximal slitstyrka.
Elektriska och termiska isoleringsegenskaper
Båda materialen har olika elektriska egenskaper som gör dem lämpliga för olika tillämpningar.
Dielektriska egenskaper
PVDF är känt för sina piezoelektriska egenskaper, som gör att det kan generera en elektrisk laddning som svar på applicerad mekanisk spänning. Denna unika egenskap gör PVDF värdefull i sensortillämpningar.
PEEK har utmärkta elektriska isoleringsegenskaper över ett brett temperaturområde och bibehåller sin dielektriska styrka även vid förhöjda temperaturer. Detta gör den särskilt värdefull i elektriska applikationer med höga temperaturer där standardplaster inte skulle fungera.
Termisk konduktivitet
PVDF och PEEK har båda relativt låg värmeledningsförmåga jämfört med metaller, vilket gör dem till bra värmeisolatorer:
- PVDF: 0,17-0,19 W/m-K
- PEEK: 0,25-0,29 W/m-K
Den låga värmeledningsförmågan kan vara både en fördel och en nackdel beroende på användningsområde. För komponenter som kräver termisk isolering fungerar båda materialen bra, även om PVDF ger något bättre isolering.
Kostnadsöverväganden och värdeanalys
Den betydande prisskillnaden mellan dessa material gör att en kostnads- och intäktsanalys är nödvändig.
Initial materialkostnad
PEEK kostar normalt 2-3 gånger mer än PVDF, vilket innebär en avsevärd kostnadspremie som måste motiveras av prestandakraven. Denna prisskillnad beror på PEEK:s mer komplexa tillverkningsprocess och den högre kostnaden för råmaterial.
Bedömning av livstidsvärde
Vid utvärdering av den totala ägandekostnaden bör flera faktorer utöver den initiala materialkostnaden beaktas:
- Förväntad livslängd i målmiljön
- Utbytesfrekvens och därmed sammanhängande stilleståndskostnader
- Krav på installation och underhåll
- Säkerhets- och tillförlitlighetsproblem
I många applikationer med höga temperaturer eller hög belastning motiverar PEEK:s överlägsna prestanda den högre initialkostnaden genom förlängd livslängd och förbättrad tillförlitlighet. För tillämpningar som ligger inom PVDF:s kapacitet ger det billigare materialet ofta ett bättre totalvärde.
Överväganden om bearbetning och tillverkning
Tillverkningsmöjligheter och -begränsningar påverkar också materialvalet.
Skillnader i maskinbearbetning
När vi bearbetar dessa material vid PTSMAKE har vi observerat betydande skillnader:
- PVDF bearbetas relativt bra men kräver skarpa verktyg och lämpliga hastigheter för att förhindra smältning eller fastfrysning.
- PEEK är mer utmanande att bearbeta på grund av dess abrasivitet och dåliga värmeledningsförmåga, vilket kan leda till värmeutveckling under skärning.
För precisionskomponenter håller PEEK i allmänhet snävare toleranser vid maskinbearbetning, men kräver mer specialiserade tekniker och verktyg, vilket kan öka tillverkningskostnaderna.
Kompatibilitet mellan tillverkningsmetoder
Båda materialen kan bearbetas genom flera olika tillverkningsmetoder:
- PVDF: Formsprutning, extrudering, kompressionsgjutning, maskinbearbetning
- PEEK: Formsprutning, extrudering, formpressning, maskinbearbetning, 3D-printing (specialutrustning)
PVDF ger något större flexibilitet vid bearbetning vid lägre temperaturer, medan PEEK kräver högre bearbetningstemperaturer men ger fler möjligheter till komplexa geometrier med hjälp av avancerade tillverkningstekniker.
Ansökningsspecifika riktlinjer för urval
Olika branscher prioriterar olika materialegenskaper, vilket leder till varierande materialpreferenser.
Halvledarindustrin
Inom halvledartillverkningen används båda materialen, men inom olika områden:
- PVDF: Används ofta för system med ultrarent vatten, komponenter för kemikalietillförsel och filtreringsutrustning.
- PEEK: Föredras för komponenter som utsätts för höga temperaturer, t.ex. waferhanteringsutrustning och komponenter i processkammare.
Utrustning för kemisk bearbetning
För applikationer inom kemisk bearbetning:
- PVDF: Utmärkt för pumpar, ventiler, armaturer och tankar som hanterar frätande kemikalier vid måttliga temperaturer.
- PEEK: Bättre lämpad för komponenter som kräver både kemisk beständighet och hög temperaturkapacitet eller mekanisk styrka.
Medicinska och farmaceutiska tillämpningar
I medicinska tillämpningar:
- PVDF: Används ofta i filtreringsmembran, suturer och vissa implanterbara enheter.
- PEEK: Företrädesvis för implantat, särskilt ortopediska tillämpningar, på grund av dess biokompatibilitet, genomskinlighet och mekaniska egenskaper som liknar ben.
När jag hjälper kunder att välja mellan PVDF och PEEK på PTSMAKE rekommenderar jag ett systematiskt tillvägagångssätt där man först utvärderar de mest kritiska miljöfaktorerna (temperatur, kemikalier, mekaniska belastningar) och sedan tar hänsyn till sekundära faktorer som kostnad, bearbetningskrav och tillgänglighet.
<
Är PEEK en polyeten?
Har du någonsin blivit förvirrad av alla tekniska plaster med namn som låter lika? När du väljer material för kritiska applikationer kan denna förvirring leda till kostsamma misstag, bristande prestanda och bortkastade resurser om du felaktigt byter ut en högpresterande plast mot en annan.
Nej, PEEK (polyeteretereterketon) är inte en polyeten. PEEK är en aromatisk polyeter med ketongrupper i ryggraden, vilket skapar en halvkristallin termoplast med exceptionell värmebeständighet (upp till 480°F), utmärkt kemisk beständighet och överlägsna mekaniska egenskaper som vida överstiger polyetenmaterialens.
Kemisk struktur och klassificeringsskillnader
När man undersöker PEEK kontra polyeten börjar de grundläggande skillnaderna på molekylär nivå. Dessa strukturella variationer förklarar varför dessa material beter sig så olika i praktiska tillämpningar.
Jämförelse av molekylär ryggrad
PEEK har en komplex aromatisk ryggradsstruktur med eter- och ketonbindningar mellan bensenringar. Denna molekylära arkitektur ger PEEK dess enastående termiska stabilitet och mekaniska styrka. De aromatiska ringarna skapar styvhet, medan eterbindningarna ger viss flexibilitet.
Polyeten har däremot en av de enklaste polymerstrukturerna som finns - bara en linjär kedja av kolatomer med väteatomer kopplade till sig. Denna enkla struktur finns i olika former (HDPE, LDPE, UHMWPE), men alla saknar de aromatiska komponenter och funktionella grupper som ger PEEK dess exceptionella egenskaper.
Denna grundläggande strukturella skillnad innebär att PEEK tillhör en helt annan polymerfamilj än polyeten. Medan polyeten klassificeras som en polyolefin, tillhör PEEK familjen polyaryleterketon (PAEK) av högpresterande termoplaster.
Viktiga skillnader mellan olika fastigheter
Skillnaderna i molekylstruktur leder till dramatiska prestandaförändringar:
Fastighet | PEEK | Polyeten (HDPE) | Skillnadsfaktor |
---|---|---|---|
Maximal temperatur vid kontinuerlig användning | 250°C (480°F) | 82°C (180°F) | PEEK är 2,7× högre |
Draghållfasthet | 14.500 psi | 4.500 psi | PEEK är 3,2× starkare |
Kemisk beständighet | Utmärkt (motstår de flesta kemikalier) | Bra (känslig för aromatiska lösningsmedel) | PEEK erbjuder bredare motståndskraft |
Kostnad | Hög | Låg | PEEK kostar 15-20× mer |
Täthet | 1,32 g/cm³ | 0,95 g/cm³ | PEEK är 39% tätare |
Hårdhet (Shore D) | 85-90 | 60-70 | PEEK är betydligt hårdare |
Skillnader i tillverkningsprocessen
Produktionsmetoderna för PEEK och polyeten återspeglar deras olika molekylstrukturer och prestandaegenskaper.
Produktionsprocess för PEEK
PEEK tillverkas genom en komplex process som omfattar nukleofil aromatisk substitutionspolymerisation. Detta kräver exakt temperaturkontroll och specialiserade katalysatorer. Monomermaterialen är betydligt dyrare än etylen, vilket bidrar till PEEK:s högre kostnad.
När vi på PTSMAKE bearbetar PEEK-komponenter måste vi ta hänsyn till materialets unika egenskaper - dess lägre värmeledningsförmåga innebär att värmehanteringen under bearbetningen är avgörande för att förhindra lokal termisk nedbrytning.
Tillverkning av polyeten
Polyeten framställs genom additionspolymerisation av eten med hjälp av olika katalysatorer beroende på önskad densitet och förgrening. Denna relativt enkla process kan utföras vid lägre temperaturer och tryck än PEEK-produktion, särskilt för varianter med låg densitet.
Prestanda i extrema miljöer
Prestanda vid höga temperaturer
En av de viktigaste skillnaderna mellan dessa material är deras termiska stabilitet:
- PEEK bibehåller sina mekaniska egenskaper upp till 250°C (480°F) vid kontinuerlig användning och klarar korta exponeringar för ännu högre temperaturer.
- Polyeten börjar mjukna vid ca 82°C (180°F) och förlorar det mesta av sin mekaniska styrka långt under denna temperatur.
Jag har sett många tillämpningar där kunderna först valde polyeten på grund av kostnaden, men sedan upplevde snabba fel när drifttemperaturerna översteg förväntningarna. I en rymdtillämpning bytte en kund från polyeten till PEEK för en komponent nära en värmekälla, vilket förlängde dess livslängd från månader till år trots den högre initiala materialkostnaden.
Jämförelse av kemisk resistens
Båda materialen har god kemisk beständighet, men PEEK ger ett bredare skydd mot starka kemikalier:
- PEEK står emot de flesta syror, baser, kolväten och organiska lösningsmedel
- Polyeten har god beständighet mot syror och baser men kan angripas av aromatiska kolväten och vissa oxidationsmedel
Denna skillnad blir kritisk i utrustning för kemisk bearbetning, halvledartillverkning och medicinska tillämpningar där exponering för flera kemikalier är vanligt förekommande.
Applikationens lämplighet
Tillämpningar inom flyg- och försvarsindustrin
I flyg- och rymdtillämpningar gör PEEK:s kombination av låg vikt, flamskydd och termisk stabilitet det ovärderligt för komponenter som t.ex:
- Invändiga komponenter som kräver flamskydd
- Elektriska kontaktdon och isolatorer
- Strukturella komponenter i högtemperaturzoner
- Bränslesystemkomponenter som kräver kemisk resistens
Polyeten uppfyller sällan de krävande kraven för flyg- och rymdtillämpningar på grund av dess begränsade termiska stabilitet och mekaniska egenskaper.
Medicinska och hälsovårdsmässiga användningsområden
Biokompatibilitetsprofilerna för dessa material skiljer sig också avsevärt:
- PEEK är biokompatibelt och används i implanterbara enheter, kirurgiska instrument och medicinsk utrustning som kräver sterilisering
- Polyeten av medicinsk kvalitet (främst UHMWPE) används i vissa implantat, t.ex. konstgjorda leder, men saknar PEEK:s temperaturbeständighet för upprepad ångsterilisering
Komponenter för industriell utrustning
För industrimaskiner beror valet mellan dessa material vanligtvis på driftsförhållandena:
- PEEK utmärker sig i miljöer med höga temperaturer, applikationer som kräver utmärkt slitstyrka eller exponering för starka kemikalier
- Polyeten ger adekvat prestanda i tillämpningar vid omgivande temperatur med måttliga mekaniska krav och väljs ofta för sin lägre kostnad och enkla bearbetning
Överväganden om kostnad och nytta
Prisskillnaden mellan dessa material är betydande - PEEK kostar normalt 15-20 gånger mer än polyeten med hög densitet. Denna betydande kostnadsskillnad innebär att materialvalet bör baseras på en noggrann analys av:
- Nödvändigt driftstemperaturområde
- Kemisk exponeringsprofil
- Krav på mekanisk belastning
- Förväntad livslängd
- Konsekvenser av misslyckande
För tillämpningar inom polyetenens kapacitetsområde är den lägre kostnaden det ekonomiska valet. Men när prestandakraven överstiger polyetenens begränsningar motiverar PEEK:s överlägsna egenskaper lätt premiumpriset genom förlängd livslängd, förbättrad tillförlitlighet och minskade underhållskostnader.
Skillnader i maskinbearbetning och bearbetning
På PTSMAKE har vi funnit betydande skillnader i bearbetningen av dessa material:
- PEEK kräver specialiserade skärparametrar på grund av dess termiskt beteende5 under bearbetningen, men håller snäva toleranser och ger utmärkt ytfinish
- Polyeten är lättare att bearbeta men har en tendens att deformeras under skärkrafterna, vilket gör det svårare att hålla snäva toleranser
Att förstå dessa skillnader i bearbetning är viktigt när man konstruerar komponenter för tillverkningsbarhet och precision.
Vilka är nackdelarna och fördelarna med PEEK?
Har du någonsin haft svårt att avgöra om PEEK är värt sitt höga pris för din kritiska applikation? När ett projekts framgång hänger på materialvalet kan valet mellan dyra högpresterande plaster och mer ekonomiska alternativ vara en svår balansgång med verkliga konsekvenser för tillförlitlighet och livslängd.
PEEK erbjuder enastående fördelar, t.ex. anmärkningsvärd värmebeständighet (upp till 480 °F), enastående kemisk beständighet, utmärkt mekanisk styrka och överlägsna slitageegenskaper. Dessa fördelar har dock betydande nackdelar, t.ex. hög kostnad (5-10 gånger högre än för vanliga tekniska plaster), svår bearbetbarhet, begränsade färgalternativ och dålig UV-beständighet.
Förstå PEEK:s exceptionella egenskaper
PEEK (polyetereterketon) sticker ut bland konstruktionsplasterna tack vare sin unika kombination av egenskaper som gör den lämplig för de mest krävande tillämpningarna. Jag har specificerat material för otaliga precisionskomponenter och har själv sett hur PEEK:s egenskaper leder till verkliga prestandafördelar.
Fördelar med termisk prestanda
En av PEEK:s mest imponerande egenskaper är dess termiska stabilitet. Materialet behåller sina mekaniska egenskaper även vid temperaturer som skulle få de flesta plaster att gå sönder katastrofalt.
Temperaturkarakteristik | PEEK Prestanda | Jämförelse med standardplaster |
---|---|---|
Kontinuerlig driftstemperatur | Upp till 250°C (480°F) | 2-3× högre än de flesta konstruktionsplaster |
Glasövergångstemperatur | 143°C (289°F) | Bibehåller styvheten vid högre temperaturer |
Smältpunkt | 343°C (649°F) | Möjliggör ångsterilisering |
Termisk konduktivitet | 0,25 W/m-K | Bättre värmeavledning än många plastmaterial |
Denna exceptionella värmebeständighet gör att PEEK kan användas i applikationer nära värmekällor där standardplaster snabbt skulle deformeras eller brytas ned. Jag har hjälpt många kunder att ersätta trasiga komponenter tillverkade av sämre material med PEEK-delar som fortsätter att fungera felfritt trots utmanande termiska miljöer.
Fördelar med kemisk resistens
PEEK:s kemiska beständighetsprofil är nästan lika imponerande som dess termiska egenskaper. Materialet visar utmärkt motståndskraft mot:
- Kolväten och organiska lösningsmedel
- De flesta syror och baser (utom koncentrerad svavelsyra)
- Ånga och varmvatten
- Vätskor och bränslen för fordon
- Medicinska steriliseringsprocesser
Denna breda kemiska resistens gör PEEK särskilt värdefullt i miljöer där exponering för flera aggressiva ämnen förväntas. Inom t.ex. halvledarindustrin kan PEEK-komponenter stå emot de tuffa kemikalier som används vid waferbearbetning och samtidigt bibehålla dimensionsstabiliteten.
Fördelar med mekaniska egenskaper
PEEK:s mekaniska styrka skiljer den från de flesta andra termoplaster:
- Draghållfasthet på 14.500 psi (jämförbar med vissa metaller)
- Utmärkt utmattningshållfasthet
- Enastående slagtålighet och seghet
- Överlägsen slitstyrka
- Låg friktionskoefficient
Dessa egenskaper gör PEEK lämpligt för strukturella tillämpningar där de flesta plaster skulle gå sönder. Jag har specificerat PEEK för kugghjul, lager och andra slitstarka komponenter som utsätts för betydande mekaniska påfrestningar, och ofta ersatt metalldelar med lättare PEEK-alternativ som ger ytterligare fördelar som korrosionsbeständighet och brusreducering.
De betydande nackdelarna med PEEK
Trots sina imponerande prestandaegenskaper har PEEK flera betydande nackdelar som måste beaktas noga vid materialvalet.
Kostnadsbegränsningar
Den mest uppenbara nackdelen med PEEK är dess kostnad. På PTSMAKE måste vi ofta hjälpa våra kunder att förstå prispremien för PEEK jämfört med andra tekniska plaster:
- PEEK kostar vanligtvis 5-10 gånger mer än tekniska plaster som nylon eller acetal
- Materialkostnaderna för PEEK-komponenter kan vara 20-30% högre än för motsvarande metallkomponenter
- Det höga råvarupriset har en betydande inverkan på ekonomin för små detaljer
Denna kostnadsfaktor tvingar ofta ingenjörer att reservera PEEK för endast de mest kritiska applikationerna där dess unika egenskaper är absolut nödvändiga. I många fall rekommenderar vi mer kostnadseffektiva alternativ för icke-kritiska komponenter i en montering.
Utmaningar för tillverkningen
PEEK innebär flera tillverkningsutmaningar som kan öka produktionskomplexiteten och kostnaderna:
Svårigheter vid maskinbearbetning: PEEK:s höga värmemotstånd innebär dålig värmeledningsförmåga, vilket orsakar värmeutveckling under bearbetningen. Detta kräver lägre skärhastigheter, frekventa verktygsbyten och noggranna kylningsstrategier.
Krav på bearbetningstemperatur: Med en smältpunkt på 343°C (649°F) kräver PEEK specialutrustning för höga temperaturer för formsprutning och extrudering.
Begränsat bearbetningsfönster: Skillnaden mellan PEEK:s smälttemperatur och den begynnande nedbrytningen är relativt liten, vilket skapar utmaningar under bearbetningen.
Formkrympning: PEEK uppvisar betydande krympning (cirka 1-1,3%) under kylning, vilket kräver exakt formkonstruktion för att uppnå snäva toleranser.
På PTSMAKE har vi utvecklat specialiserade bearbetningsprotokoll för PEEK för att hantera dessa utmaningar, men de ökar oundvikligen den totala kostnaden och komplexiteten vid tillverkning av PEEK-komponenter.
Begränsningar i tillämpningen
Trots sina imponerande egenskaper har PEEK begränsningar som gör den olämplig för vissa tillämpningar:
- Dålig UV-resistens: Utan tillsatser bryts PEEK ned när det utsätts för långvarigt UV-ljus, vilket begränsar dess användning i utomhusapplikationer.
- Begränsade färgalternativ: På grund av sin naturliga bärnstensfärgade/bruna färg och höga bearbetningstemperaturer är PEEK svårt att färga konsekvent.
- Elektriska begränsningar: PEEK är visserligen en bra isolator, men är inte idealisk för elektriska högfrekvenstillämpningar jämfört med specialiserade elektriska polymerer.
- Svårigheter att binda: PEEK:s kemiska beständighet gör limning till en utmaning och kräver ofta speciella ytbehandlingar.
Kostnads-nyttoanalys: När är PEEK värt det?
Med tanke på PEEK:s betydande kostnadspremie är det viktigt att göra en noggrann kostnads- och nyttoanalys innan man specificerar detta material. Enligt min erfarenhet ger PEEK det bästa värdet i följande scenarier:
Scenarier där PEEK utmärker sig
Miljöer med hög temperatur: När drifttemperaturen överstiger 149°C (300°F) är PEEK ofta det enda hållbara plastalternativet, vilket gör att premiumkostnaden är motiverad.
Kemiskt aggressiva miljöer: I applikationer som utsätts för flera kemikalier eller särskilt starka ämnen förhindrar PEEK:s breda kemiska beständighet de frekventa byten som krävs med mindre material.
Kritiska slitagetillämpningar: För komponenter som utsätts för konstant friktion och slitage i kritiska system kan PEEK:s exceptionella slitstyrka och låga friktion dramatiskt förlänga serviceintervallerna.
Krav på viktreduktion: När PEEK ersätter metallkomponenter i flyg- och rymdapplikationer eller högpresterande applikationer kan PEEK:s styrka/vikt-förhållande ge prestandafördelar som motiverar kostnaden.
Tillämpningar för medicinska implantat: PEEK:s biokompatibilitet och kemiska stabilitet gör den idealisk för långtidsimplanterbara enheter där materialfel inte är ett alternativ.
Jämförelse av alternativa material
För applikationer som inte specifikt kräver PEEK:s extrema egenskaper finns det flera alternativ som kan ge tillräcklig prestanda till lägre kostnad:
Material | Komparativ fördel | Kostnad jämfört med PEEK | Begränsning av nycklar |
---|---|---|---|
PPS (polyfenylensulfid) | God värmebeständighet (400°F) | 40-60% lägre | Mindre kemikaliebeständig |
PTFE (polytetrafluoretylen) | Överlägsen kemisk beständighet | 30-50% lägre | Dålig mekanisk hållfasthet |
PEI (polyeterimid) | Bra värmebeständighet, transparens | 30-40% lägre | Mindre slitstark |
PAI (polyamid-imid) | Hög hållfasthet, bra slitstyrka | 10-20% lägre | Svårare att bearbeta |
Acetal (POM) | Utmärkt bearbetbarhet, låg kostnad | 80-90% lägre | Begränsad temperaturtålighet |
Branschspecifika överväganden
Olika branscher prioriterar olika aspekter av PEEK:s egenskapsprofil:
Flyg- och rymdindustrin samt försvar
I flyg- och rymdtillämpningar motiverar PEEK:s kombination av låg vikt, flamskydd (med tillsatser) och termisk stabilitet dess höga pris för komponenter som t.ex:
- Bussningar och lager i styrsystem
- Elektriska kontaktdon och isolatorer
- Strukturella komponenter i högtemperaturzoner
- Bränslesystemkomponenter som kräver kemisk resistens
Medicin och hälsovård
Den medicinska industrin värdesätter PEEK för dess
- Biokompatibilitet (implantatkvalitet)
- Motståndskraft mot upprepad sterilisering
- Radiolucens (stör inte röntgenstrålning)
- Mekaniska egenskaper som liknar ben (när det är förstärkt)
Dessa egenskaper gör PEEK idealisk för implantat och kirurgiska instrument, trots dess höga kostnad.
Industriell utrustning
För industriella tillämpningar beror beslutet att använda PEEK vanligtvis på hur svåra driftförhållandena är:
- Extrema miljöer (hög temperatur, kemisk exponering) motiverar ofta att PEEK
- Applikationer där driftstopp är extremt kostsamma drar nytta av PEEK:s tillförlitlighet
- Högprecisionskomponenter drar nytta av PEEK:s dimensionsstabilitet
På PTSMAKE hjälper vi våra kunder att navigera i dessa överväganden för att avgöra om PEEK:s premiumprestanda motiverar premiumpriset för deras specifika applikationsbehov.
Jag genererar innehållet för kapitel 7 av artikeln "Varför är PEEK så dyrt?" enligt dina önskemål.
Varför är PEEK så dyrt?
Har du någonsin upplevt en chock när du begärt en offert på PEEK-komponenter? När ingenjörer för första gången stöter på priset för denna högpresterande plast frågar sig många om något material verkligen kan motivera en sådan hög kostnad, särskilt jämfört med mer vanliga konstruktionsplaster som verkar erbjuda hyfsad prestanda till en bråkdel av priset.
PEEK:s höga kostnad beror på dess komplexa tillverkningsprocess, dyra råmaterial, krav på specialutrustning och relativt låga produktionsvolymer. Den komplicerade polymerisationsprocessen kräver exakta förhållanden, medan produktionsteknologin är patentskyddad och PEEK:s status som specialmaterial höjer marknadspriset ytterligare.
Den komplexa tillverkningsprocessen bakom PEEK
För att förstå varför PEEK betingar ett så högt pris måste man först undersöka tillverkningsprocessen. Till skillnad från enklare polymerer innebär PEEK-produktion sofistikerad kemi och exakta bearbetningsförhållanden som påverkar den slutliga kostnaden avsevärt.
Råvarukostnader och brist på råvaror
De monomerer som används för att producera PEEK är i sig dyra specialkemikalier. De primära ingredienserna inkluderar:
- Difenyleter
- 4,4′-difluorbensofenon
- Kaliumkarbonat
- Difenylsulfon (som lösningsmedel)
Dessa prekursorer kräver flera raffineringssteg för att uppnå den renhet som krävs för PEEK-syntesen, vilket innebär att kostnaderna ökar innan polymeriseringen ens har börjat. Dessutom har vissa av dessa kemikalier begränsad produktionskapacitet i världen, vilket skapar utbudsbegränsningar som driver upp priserna.
När vi på PTSMAKE köper in PEEK för maskinbearbetningsprojekt betalar vi inte bara för själva polymeren utan för hela värdekedjan av specialkemikalier som ingick i dess framställning.
Polymeriseringsprocessens komplexitet
Syntesen av PEEK involverar en sofistikerad nukleofil aromatisk substitutionspolymerisationsprocess. Denna reaktion måste ske under exakt kontrollerade förhållanden:
- Temperaturer mellan 300-400°C (572-752°F)
- Inert atmosfär för att förhindra oxidation
- Specialiserade tryckkärl
- Förlängda reaktionstider (ofta 3-5 timmar)
- Noggrann hantering av katalysatorn
Vart och ett av dessa krav gör tillverkningen mer komplicerad och dyrare. Reaktionen måste övervakas noggrant under hela processen för att säkerställa korrekt molekylviktsfördelning och kristallinitet, vilket direkt påverkar materialets prestandaegenskaper.
Begränsad produktionsskala och marknadsdynamik
PEEK:s status som specialmaterial har en betydande inverkan på produktionsekonomin och marknadspriserna.
Äganderättsligt skyddad teknik och patentskydd
Den ursprungliga tillverkningstekniken för PEEK utvecklades och patenterades av Victrex (tidigare ICI) på 1970-talet. Än idag är produktionstekniken till stor del egenutvecklad och skyddas av olika patent. Denna begränsade konkurrens inom tillverkningsmetoderna har lett till högre priser jämfört med vanliga plastprodukter.
Även om det nu finns flera tillverkare globalt (bl.a. Victrex, Solvay och Evonik), använder var och en proprietära processer som krävde enorma investeringar i FoU för att utvecklas. Dessa utvecklingskostnader måste återvinnas genom materialprissättningen.
Produktionsvolym Ekonomi
Till skillnad från plastråvaror som produceras i miljontals ton årligen, tillverkas PEEK i relativt små volymer:
Plasttyp | Global årlig produktion | Relativ kostnadsfaktor |
---|---|---|
Polyeten (PE) | ~100 miljoner ton | 1× (baslinje) |
Nylon (PA) | ~8 miljoner ton | 2-3× |
Polykarbonat (PC) | ~4,5 miljoner ton | 3-4× |
PEEK | <10.000 ton | 30-50× |
Den begränsade produktionsvolymen innebär att tillverkarna inte kan uppnå de stordriftsfördelar som driver ned kostnaderna för vanliga plaster. Fasta kostnader som anläggningsunderhåll, kvalitetskontroll och FoU fördelas på färre kilo produkt, vilket höjer kostnaden per enhet.
Krav på utrustning och bearbetning
Produktionsanläggningarna för PEEK kräver specialutrustning som kan hantera de extrema temperaturer och tryck som krävs för polymerisering, sammansättning och bearbetning:
- Högtemperaturreaktorer med exakta styrsystem
- Specialiserad extruderings- och pelleteringsutrustning
- Avancerade filtrerings- och reningssystem
- Omfattande kvalitetskontroll och testanläggningar
Dessa kapitalinvesteringar är betydande och bidrar i hög grad till den slutliga materialkostnaden. När vi bearbetar PEEK-delar på PTSMAKE ärver vi dessa uppströms tillverkningskostnader i råmaterialpriset.
Utmaningar vid bearbetning och maskinbearbetning
När PEEK väl har producerats innebär det ytterligare utmaningar vid bearbetning och maskinbearbetning, vilket bidrar till den höga kostnaden för färdiga komponenter.
Höga bearbetningstemperaturer
PEEK har en smältpunkt på ca 343°C (649°F) och kräver därför specialiserad bearbetningsutrustning:
- Formsprutningsmaskiner med kapacitet för höga temperaturer
- Gjutformar med speciella värmehanteringssystem
- Dyrare värmeelement och regulatorer
- Förbättrade säkerhetssystem för hantering av material med hög temperatur
Dessa krav innebär att färre tillverkare är utrustade för att bearbeta PEEK, vilket begränsar konkurrensen och upprätthåller högre bearbetningskostnader.
Bearbetningsöverväganden och verktygsslitage
När vi bearbetar PEEK vid PTSMAKE stöter vi på flera faktorer som bidrar till högre produktionskostnader:
Verktygsslitage: PEEK orsakar betydligt mer verktygsslitage än standardplaster, vilket kräver mer frekventa verktygsbyten eller användning av premiumverktyg.
Värmehantering: PEEK:s låga värmeledningsförmåga innebär att värme byggs upp under bearbetningen, vilket kräver långsammare skärhastigheter och speciella kylningstekniker.
Specialiserad expertis: Korrekt bearbetning av PEEK kräver erfarenhet och kunskap för att förhindra materialförstöring och uppnå snäva toleranser.
Krav på efterbearbetning: Många PEEK-tillämpningar kräver ytterligare bearbetningssteg som glödgning för att minska inre spänningar och säkerställa dimensionsstabilitet.
Var och en av dessa faktorer bidrar till den totala kostnaden för att producera färdiga PEEK-komponenter utöver bara råvarupriset.
Kostnader för kvalitetskontroll och certifiering
PEEK är ett högpresterande material som ofta används i kritiska applikationer och kräver därför rigorös kvalitetskontroll under hela produktions- och bearbetningsprocessen.
Stränga testkrav
Varje parti av PEEK genomgår vanligtvis omfattande tester för att verifiera:
- Molekylviktsfördelning
- Kristallinitetsprocent
- Termiska egenskaper (glasövergång och smältpunkter)
- Mekaniska egenskaper (draghållfasthet, modul, töjning)
- Renhets- och föroreningsnivåer
Dessa tester kräver specialutrustning och utbildad personal, vilket innebär att betydande kvalitetssäkringskostnader läggs till slutproduktens pris.
Branschcertifieringar och spårbarhet
Många PEEK-applikationer inom flyg-, medicin- och halvledarindustrin kräver fullständig spårbarhet av materialet och överensstämmelse med branschspecifika standarder:
- Certifieringar inom flyg- och rymdindustrin (AS9100, NORSOK)
- Standarder för medicintekniska produkter (ISO 13485, USP Class VI)
- Certifieringar inom kärnkraftsindustrin (NQSA-1)
- Krav från halvledarindustrin (hög renhet)
För att upprätthålla dessa certifieringar krävs omfattande dokumentation, regelbundna revisioner och ibland separata produktionsanläggningar eller utrustning, vilket bidrar till högre kostnader.
Jämförelse mellan PEEK och alternativa material
För att förstå PEEK:s prissättning i sitt sammanhang är det bra att jämföra det med alternativa material när det gäller både kostnad och prestanda.
Analys av kostnad och prestanda
PEEK kostar vanligtvis 5-10 gånger mer än vanliga tekniska plaster och kan till och med vara dyrare än vissa specialmetaller på volymbasis. Dess prestanda i extrema miljöer motiverar dock ofta denna premie:
Fastighet | PEEK | Standard Engineering Plastics | Premium Metals |
---|---|---|---|
Temperatur vid kontinuerlig användning | Upp till 250°C (480°F) | 80-170°C (176-338°F) | Vanligtvis obegränsat |
Kemisk beständighet | Utmärkt | Variabel (ofta begränsad) | Ofta dålig (korrosion) |
Specifik styrka | Mycket hög | Måttlig | Hög |
Kostnad för råmaterial | Mycket hög | Låg till måttlig | Måttlig till hög |
Bearbetningskostnad | Hög | Låg till måttlig | Hög |
Livstidsvärde | Utmärkt | Begränsad i tuffa förhållanden | Bra men med korrosionsproblem |
Vi på PTSMAKE hjälper ofta våra kunder att utvärdera dessa avvägningar för att avgöra om PEEK:s höga pris är motiverat av dess prestandafördelar i deras specifika applikation.
Är PEEK värt det höga priset?
Frågan om PEEK:s höga kostnad är motiverad beror helt och hållet på applikationskraven.
Applikationer där PEEK ger värde trots kostnad
PEEK ger ett utmärkt värde trots sitt höga pris i applikationer med:
- Extrema driftsmiljöer där andra material snabbt skulle ge vika
- Viktkritiska system där PEEK:s förhållande mellan styrka och vikt ger fördelar
- Underhållskänslig utrustning där kostnaden för stillestånd vida överstiger materialkostnaderna
- Korrosiva miljöer där metaller skulle brytas ned snabbt
- Medicinska implantat där biokompatibilitet och långsiktig stabilitet är avgörande
I dessa scenarier leder PEEK:s prestandafördelar direkt till lägre livstidskostnader, trots den högre initiala investeringen.
Strategier för kostnadsreducering för PEEK-komponenter
För projekt som kräver PEEK:s prestanda men begränsas av budgeten kan du överväga dessa metoder:
- Hybridkonstruktioner PEEK används endast för kritiska komponenter
- Optimerade bearbetningstekniker för att minska materialspill
- Bearbetning av nära-nät-former för att minimera materialförbrukningen
- Optimering av design för att minska den totala materialvolymen
- Ej fyllda betyg när förstärkningar inte är nödvändiga för prestationen
På PTSMAKE har vi hjälpt många kunder att implementera dessa strategier för att få PEEK:s fördelar samtidigt som kostnaderna hanteras effektivt.
Hur optimerar man PEEK-bearbetning för kostnadseffektiv produktion?
Har du någonsin undrat om det finns ett sätt att utnyttja PEEK:s exceptionella egenskaper utan att spräcka din projektbudget? När du arbetar med en av de dyraste konstruktionsplasterna på marknaden handlar optimering av bearbetningen inte bara om effektivitet - det kan innebära skillnaden mellan ett lönsamt projekt och ett som förlorar pengar på grund av onödigt materialspill och onödig bearbetningstid.
För att optimera bearbetningen av PEEK för kostnadseffektiv produktion krävs att man använder rätt skärverktyg (hårdmetall eller diamantbelagda), håller lämpliga hastigheter och matningar (vanligtvis långsammare än för standardplaster), implementerar effektiva kylstrategier, minimerar materialspillet genom att konstruera nära nätform och noggrant planerar verktygsbanorna för att minska cykeltiderna.
Val av optimala verktyg för bearbetning av PEEK
Vid bearbetning av PEEK har valet av verktyg en dramatisk inverkan på både detaljkvaliteten och de totala bearbetningskostnaderna. Min mångåriga erfarenhet har lärt mig att man sparar betydligt mer i det långa loppet om man investerar i rätt verktyg på förhand.
Material och geometrier för skärverktyg
PEEK:s abrasiva egenskaper, särskilt fyllda kvaliteter som innehåller kolfiber eller glas, kräver noggrant val av verktyg:
Verktygsmaterial | Bäst för | Verktygets livslängd | Kostnadsfaktor |
---|---|---|---|
Hårdmetall (obelagd) | Ofylld PEEK | Bra | Måttlig |
Diamantbelagd hårdmetall | Fylld PEEK | Utmärkt | Hög |
PCD (polykristallin diamant) | Produktion av stora volymer | Överlägsen | Mycket hög |
Höghastighetsstål (HSS) | Enkla operationer på ofylld PEEK | Begränsad | Låg |
För de flesta tillämpningar på PTSMAKE använder vi hårdmetallverktyg med specifika geometrier som är utformade för högpresterande plast. De viktigaste egenskaperna vi letar efter inkluderar:
- Vassa skäreggar (minskar värmeutvecklingen)
- Höga positiva rake-vinklar (10-15°)
- Polerade skär (förbättrar spånevakuering)
- Tillräckliga frigångsvinklar (förhindrar gnidning)
Premiumverktyg kostar visserligen mer i början, men de behåller skärpan längre och ger bättre ytfinhet, vilket minskar behovet av sekundära bearbetningar.
Hänsyn till verktygsslitage
Verktygsslitaget sker mycket snabbare vid bearbetning av PEEK än vid bearbetning av vanliga tekniska plaster. Vi har kommit fram till att övervakning och hantering av verktygsslitage är avgörande för att upprätthålla både detaljkvalitet och kostnadskontroll.
Jag rekommenderar att man upprättar ett schema för verktygsbyte baserat på bearbetad volym i stället för att vänta på visuella tecken på slitage. I vår verkstad byts verktyg som bearbetar fylld PEEK vanligtvis efter ungefär 60-70% av den verktygslivslängd som vi förväntar oss vid bearbetning av aluminium. Detta proaktiva tillvägagångssätt förhindrar kvalitetsproblem och potentiellt skrotade detaljer som uppstår vid bearbetning med slitna verktyg.
Optimera skärparametrar
Att hitta rätt balans mellan hastighet, matning och skärdjup är avgörande för effektiv PEEK-bearbetning. Målet är att maximera materialavverkningshastigheten utan att generera överdriven värme eller försämra ytkvaliteten.
Rekommendationer för hastighet och matning
Genom omfattande tester på PTSMAKE har vi tagit fram dessa allmänna riktlinjer för bearbetningsparametrar för PEEK:
PEEK Typ | Skärhastighet (SFM) | Matningshastighet | Skärdjup | Kylvätska |
---|---|---|---|---|
Ofylld PEEK | 300-500 | Måttlig | 0.005"-0.020" | Luft eller dimma |
30% Kolfiber fylld | 200-400 | Reducerad (75%) | 0.005"-0.015" | Mist/översvämning |
30% Glasfylld | 250-450 | Reducerad (85%) | 0.005"-0.015" | Mist/översvämning |
Dessa parametrar bör justeras utifrån dina specifika verktyg, maskinens styvhet och detaljens krav. Jag rekommenderar generellt att man börjar i den konservativa änden av dessa intervall och gradvis ökar parametrarna samtidigt som man övervakar resultaten.
Strategier för värmehantering
PEEK:s dåliga värmeledningsförmåga kan leda till värmeuppbyggnad under bearbetning, vilket kan orsaka..:
- Dimensionell instabilitet
- Försämrad ytfinish
- Påskyndat verktygsslitage
- Materialnedbrytning i extrema fall
För att motverka dessa problem implementerar vi flera tekniker för värmehantering:
Korrekt val av kylvätska: För ofylld PEEK fungerar kylning med tryckluft ofta bra. För fyllda kvaliteter ger kylvätska i form av dimma eller översvämning bättre värmeavledning.
Intermittent kapning: Genom att pausa regelbundet under djupa fickoperationer kan värmen avledas.
Klättringsfräsning: Genom att använda klättringsfräsning i stället för konventionell fräsning minskar friktionen och värmeutvecklingen.
Flera ljuspassager: Genom att göra flera lätta finbearbetningar i stället för en tung bearbetning förbättras måttnoggrannheten och ytfinheten.
Strategier för materialutnyttjande
Med tanke på PEEK:s höga kostnad (ofta $75-200 per pund beroende på kvalitet och form) blir materialutnyttjandet en kritisk kostnadsfaktor. Varje bit av avfallet har en direkt inverkan på slutresultatet.
Utgångsmaterial med nära-nät-form
Genom att börja med material som ligger närmare dina slutliga mått kan du minska avfallet avsevärt. Överväg dessa tillvägagångssätt:
Anpassade extruderingar: För detaljer med konsekventa tvärsnitt kan man genom att börja med specialextruderade profiler eliminera betydande materialspill. Den högre installationskostnaden kompenseras av materialbesparingar vid större produktionskörningar.
Förskurna ämnen: Genom att låta din materialleverantör tillhandahålla förskurna ämnen som är dimensionerade specifikt för dina detaljer minskar både spill och den initiala bearbetningstiden.
Nesting-programvara: För platta detaljer som bearbetas från plåt kan avancerad nesting-programvara optimera materialanvändningen med 15-30% jämfört med manuell layoutplanering.
På PTSMAKE har vi hjälpt kunder att minska materialkostnaderna för PEEK med över 40% genom att implementera dessa metoder för deras högvolymkomponenter.
Överväganden om återvinning av chip
Till skillnad från vissa termoplaster kan PEEK inte enkelt återvinnas internt på grund av den höga bearbetningstemperaturen. Det finns dock specialiserade återvinningstjänster:
- Rena, sorterade PEEK-chips kan säljas till återvinningsföretag
- Vissa återvinningsföretag krediterar materialvärdet mot framtida inköp
- Fyllda kvaliteter har vanligtvis lägre återvinningsvärde på grund av kontamineringsproblem
Även om återvinning inte helt kompenserar dina materialkostnader kan det ge viss kostnadstäckning för större bearbetningsoperationer.
Optimering av bearbetningsstrategi
Utöver verktyg och parametrar har din övergripande bearbetningsmetod en betydande inverkan på både detaljkvalitet och produktionskostnader.
Fixturkonstruktion för flera delar
Välkonstruerade fixturer som gör det möjligt att bearbeta flera detaljer i en och samma uppställning har flera fördelar:
- Minskad ställtid per detalj
- Förbättrad enhetlighet mellan olika delar
- Mer effektivt maskinutnyttjande
- Bättre materialutbyte från plåtlager
För en kund inom flyg- och rymdindustrin konstruerade vi en fixtur som gjorde det möjligt att bearbeta 16 små PEEK-komponenter samtidigt, vilket minskade kostnaden per detalj med 62% jämfört med individuella inställningar.
Förfining av CAM-strategi
Optimerade verktygsbanor kan dramatiskt minska bearbetningstiden och förbättra detaljkvaliteten:
Högeffektiv fräsning: Genom att använda avancerade CAM-strategier som upprätthåller en konsekvent verktygsingrepp minskas cykeltiderna och verktygens livslängd förlängs.
Maskinbearbetning i vila: Korrekt sekvenserade operationer som använder större verktyg för större materialavverkning och mindre verktyg endast där det är nödvändigt optimerar både materialavverkningen och verktygens livslängd.
Optimerade inflygningsrörelser: Minimering av luftskärning genom effektiva till- och frånkörningar kan minska cykeltiderna med 5-15% utan att påverka detaljkvaliteten.
Kvalitetskontroll för att minimera skrot
Med tanke på PEEK:s höga materialkostnad blir minskad kassation en primär kostnadsbesparingsstrategi. Effektiva kvalitetskontrollprocesser som fångar upp problem tidigt förhindrar att dyrt material slösas bort på delar som inte uppfyller specifikationerna.
Mätning under pågående process
Vi har implementerat flera verifieringssteg under processens gång:
Första artikeln Inspektion: Mät noggrant den första delen av varje körning innan du fortsätter med produktionen.
Inspektioner i olika steg: Mätning av kritiska egenskaper innan man fortsätter med efterföljande operationer, särskilt vid vändning eller omfixering av detaljer.
Termisk stabilisering: Låt delarna nå omgivande temperatur före slutmätning, eftersom PEEK:s värmeutvidgning kan påverka måtten.
Dessa metoder har hjälpt oss att hålla en skrotningsgrad på under 2% för PEEK-komponenter, vilket är betydligt lägre än branschgenomsnittet.
Överväganden om efterbearbetning
Processen är inte slut när detaljen kommer ut ur maskinen. Efterbearbetningen kan ha en betydande inverkan på både kvalitet och kostnad.
Avlastning och dimensionsstabilitet
PEEK-detaljer med komplexa geometrier eller ojämn materialavverkning kan ha nytta av spänningsavlastning för att säkerställa långsiktig dimensionsstabilitet:
Termisk glödgning: Kontrollerad uppvärmning under glasövergångstemperaturen följt av långsam kylning kan lindra inre spänningar.
Strategi för grovbearbetning till slutbearbetning: Genom att ta bort det mesta materialet i en första operation och sedan låta detaljen stabiliseras före slutbearbetningen förbättras måttnoggrannheten.
För kritiska komponenter med snäva toleranser är dessa extra steg väl värda investeringen för att förhindra kostsamma fel på plats eller dimensionsavvikelser över tid.
Genom att implementera dessa optimeringsstrategier har vi hjälpt många kunder på PTSMAKE att uppnå kostnadseffektiv PEEK-bearbetning utan att kompromissa med de exceptionella prestandaegenskaper som gör detta material så värdefullt. Nyckeln är ett holistiskt synsätt som tar hänsyn till alla aspekter av tillverkningsprocessen, från materialval till slutkontroll.
Lär dig mer om tekniker för termisk hantering vid högpresterande plastbearbetning. ↩
Lär dig avancerad teknik för precisionsbearbetning av högpresterande termoplaster. ↩
Klicka här för att utforska specialiserade tekniker för precisionsbearbetning av högpresterande termoplaster. ↩
Upptäck hur mekaniska egenskaper påverkar materialvalet för högpresterande komponenter. ↩
Lär dig specialiserade bearbetningstekniker för att förhindra värmerelaterad deformation i högpresterande termoplaster. ↩