Struggling with inconsistent surface finishes in your plastic parts? I’ve seen many clients face this challenge during my 15+ years in injection molding. 3K injection molding might be the solution you’re looking for.
3K injection molding is a specialized manufacturing process that uses three different materials or colors in a single molding cycle. This advanced technique creates parts with unique aesthetic combinations or functional properties through a single injection molding operation.
In my experience working with PTSMAKE, I’ve seen 3K injection molding transform complex multi-material projects into streamlined, cost-effective solutions. This technology not only reduces assembly steps but also creates stunning visual effects that can set your products apart. Let me share more about how this process can benefit your specific manufacturing needs.
What Does 3K Injection Molding Mean?
Ever wondered how modern smartphones combine rigid frames, soft-touch grips, and transparent displays in a single piece? The secret lies in an advanced manufacturing process that’s revolutionizing product design.
3K injection molding is a sophisticated manufacturing technique that enables the combination of three different materials or colors in a single molded part through a multi-shot process using specialized machinery with rotating platens.
Understanding the Basics of 3K Molding
In my 15+ years at PTSMAKE, I’ve witnessed the evolution of injection molding technology. 3K injection molding, where ‘K’ stands for ‘component’ or ‘material’, represents one of the most significant advances in this field. This process allows manufacturers to create complex parts using three different materials or colors in a single production cycle.
The key difference between traditional injection molding and 3K molding lies in its ability to handle multiple materials. While standard injection molding works with just one material, and 2K handles two, 3K takes it to the next level with three distinct materials or colors.
The Technical Framework
Machine Configuration
The heart of 3K injection molding is its specialized machinery. A typical 3K setup includes:
Component | Function |
---|---|
Rotary Platen | Enables mold rotation between shots |
Multiple Injection Units | Handles different materials |
Advanced Control System | Coordinates timing and material flow |
Special Mold Design | Features multiple cavities for each material |
Process Sequence
First Material Injection
- The first material creates the base structure
- The mold rotates to the next position
Second Material Addition
- The second material bonds with the first
- Another rotation occurs
Third Material Completion
- The final material completes the part
- The finished product is ejected
Applications and Advantages
Based on my experience working with various industries, 3K injection molding offers several unique benefits:
Industry Applications
- Automotive: Multi-color dashboard components
- Consumer Electronics: Soft-touch buttons with clear displays
- Medical Devices: Ergonomic handles with grip zones
- Sporting Goods: Multi-density equipment parts
Key Benefits
Design Flexibility
- Combine different material properties
- Create complex color combinations
- Achieve varying surface textures
Production Efficiency
- Eliminate assembly steps
- Reduce production time
- Lower labor costs
Quality Improvements
- Better material bonds
- Consistent part quality
- Reduced reject rates
Common Challenges and Solutions
During my years at PTSMAKE, I’ve encountered several challenges with 3K molding:
Material Compatibility
Not all materials work well together. We maintain a comprehensive material compatibility database to ensure successful bonding between different materials.
Process Control
3K molding requires precise timing and temperature control. Our advanced monitoring systems help maintain optimal conditions throughout the production cycle.
Cost Considerations
The initial investment in 3K equipment is significant. However, I’ve helped many clients analyze their long-term ROI, often finding that the reduced assembly costs and improved part quality justify the investment.
Future Trends
The 3K injection molding industry continues to evolve. Current trends include:
Integration with Smart Manufacturing
- Real-time process monitoring
- AI-powered quality control
- Predictive maintenance systems
Sustainable Solutions
- Bio-based materials compatibility
- Reduced waste through precise material control
- Energy-efficient processing
Advanced Applications
- Micro-molding capabilities
- Enhanced material combinations
- Complex geometric possibilities
At PTSMAKE, we’re continuously investing in these emerging technologies to stay ahead of industry demands. From my experience, companies that embrace 3K molding technology often gain a significant competitive advantage in their respective markets.
This advanced manufacturing process may seem complex, but understanding its fundamentals is crucial for modern product development. As manufacturing continues to evolve, 3K injection molding stands as a testament to how far we’ve come from traditional single-material molding processes.
How Does the 3K Injection Molding Process Work?
Have you ever wondered how complex plastic parts with multiple materials and colors are made in a single mold? After 15+ years in injection molding, I’m excited to share the secrets behind 3K technology.
3K injection molding is an advanced manufacturing process that injects three different materials or colors into a single mold through synchronized nozzle switching. This creates complex parts with multiple properties in one production cycle.
Material Selection and Preparation
In my experience at PTSMAKE, material selection is crucial for 3K molding success. We carefully evaluate material compatibility, processing temperatures, and shrinkage rates. Here’s what we consider:
Material Compatibility
- Chemical bonding potential
- Thermal expansion rates
- Adhesion properties
Processing Requirements
- Melt temperatures
- Injection pressures
- Cooling times
Machine Configuration
The 3K injection molding machine is more complex than standard equipment. It requires:
Multiple Injection Units
- Primary injection unit
- Secondary injection unit
- Tertiary injection unit
Each unit needs independent control for:
Parameter | Control Range | Typical Accuracy |
---|---|---|
Temperature | 150-400°C | ±1°C |
Pressure | 0-2000 bar | ±5 bar |
Speed | 0-200 mm/s | ±0.1 mm/s |
The Multi-Shot Process
The 3K process follows a precise sequence:
First Shot
- First material injection
- Partial cooling
- Mold rotation/movement
Second Shot
- Second material injection
- Additional cooling
- Position adjustment
Third Shot
- Final material injection
- Complete cooling
- Part ejection
Tooling Design Considerations
At PTSMAKE, we’ve developed specialized tooling approaches:
Core Requirements
- Multiple gates
- Cooling channel optimization
- Material flow path design
Special Features
Feature | Purpose | Benefit |
---|---|---|
Sequential gates | Control flow | Better quality |
Hot runners | Temperature maintenance | Less waste |
Rotating plates | Position control | Precise alignment |
Process Control and Optimization
Temperature Management
From my 15+ years of experience, temperature control is critical:
- Material-specific heating zones
- Mold temperature regulation
- Cooling system efficiency
Pressure Control
We maintain precise pressure control through:
- Injection pressure monitoring
- Hold pressure adjustment
- Back pressure regulation
Timing Synchronization
The success of 3K molding depends on perfect timing:
- Material injection sequence
- Mold movement coordination
- Cooling time optimization
Quality Control Measures
Process Monitoring
We implement:
- Real-time parameter tracking
- Statistical process control
- Quality verification systems
Common Challenges
In my time at PTSMAKE, I’ve encountered and solved various issues:
- Material interface bonding
- Warpage control
- Flash prevention
Production Considerations
Cycle Time Optimization
We focus on:
- Material preparation efficiency
- Movement synchronization
- Cooling time reduction
Cost Management
Key factors include:
- Material waste reduction
- Energy efficiency
- Maintenance scheduling
Through my years of experience with 3K injection molding, I’ve learned that success depends on careful attention to each of these aspects. The process requires precise control, advanced equipment, and experienced operators. At PTSMAKE, we’ve developed comprehensive systems to ensure consistent quality in our 3K molding operations.
The sophistication of 3K injection molding makes it an ideal choice for complex parts that require multiple materials or colors. While it demands more sophisticated equipment and expertise than traditional injection molding, the ability to produce complex parts in a single cycle offers significant advantages for the right applications.
I’ve seen this technology evolve significantly over my 15+ years in the industry, and it continues to advance with new developments in control systems and automation. Understanding these technical aspects is crucial for anyone considering 3K injection molding for their manufacturing needs.
What Are the Applications of 3K Injection Molding?
As someone who has spent 15+ years in injection molding, I’ve seen 3K injection molding revolutionize product design across industries, offering unprecedented possibilities for complex, multi-material components.
3K injection molding finds its primary applications in automotive, medical devices, consumer electronics, and aerospace industries, where it enables the production of complex parts combining different materials or colors in a single manufacturing process.
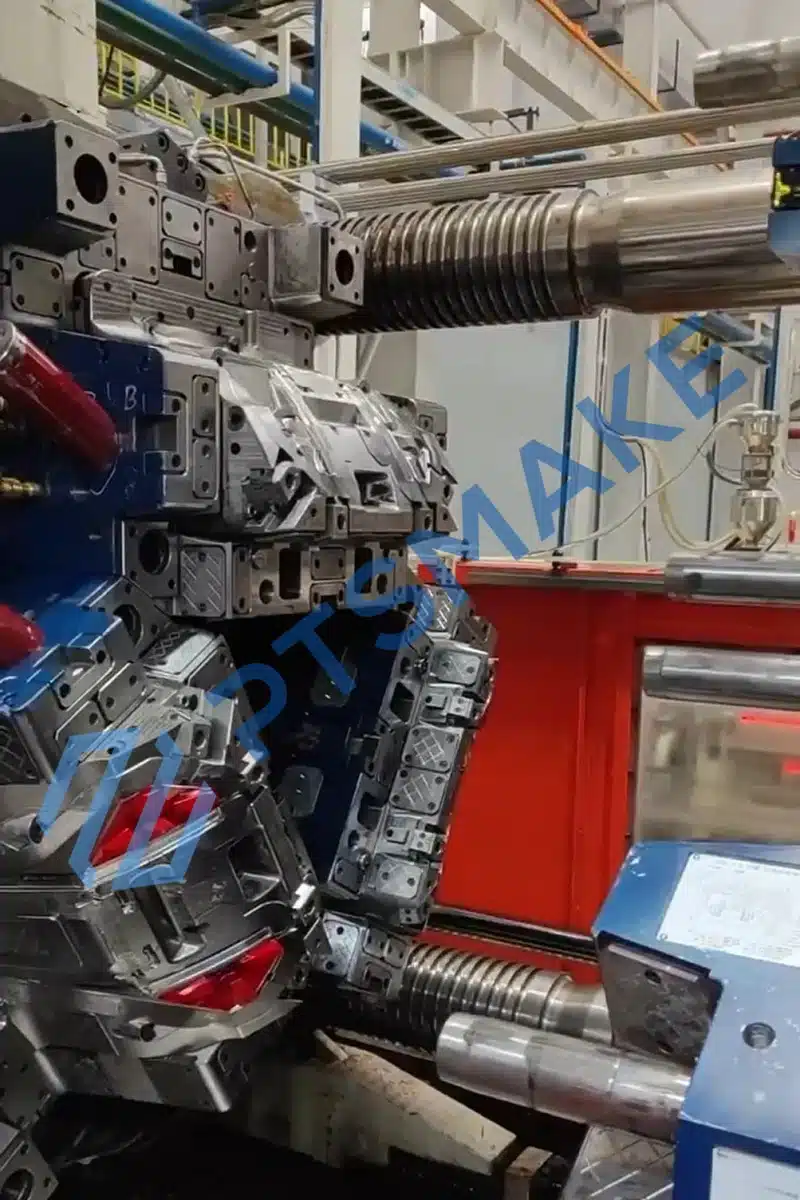
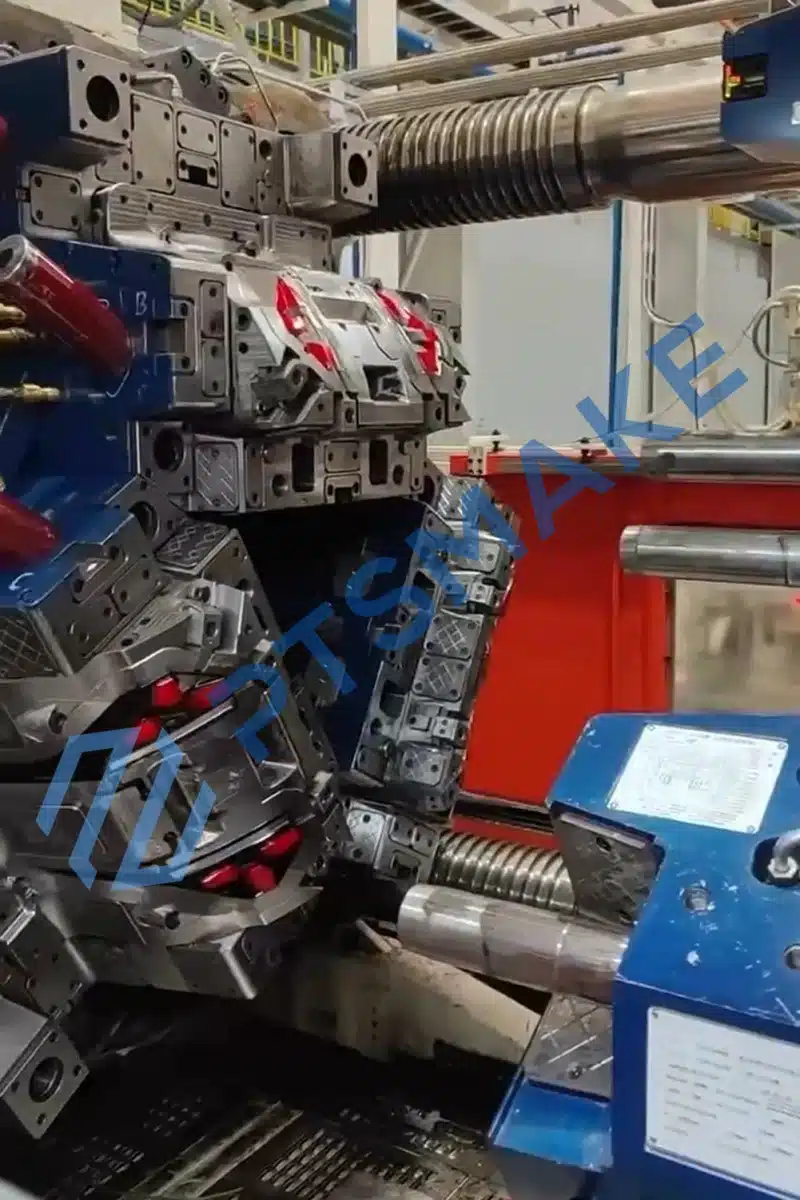
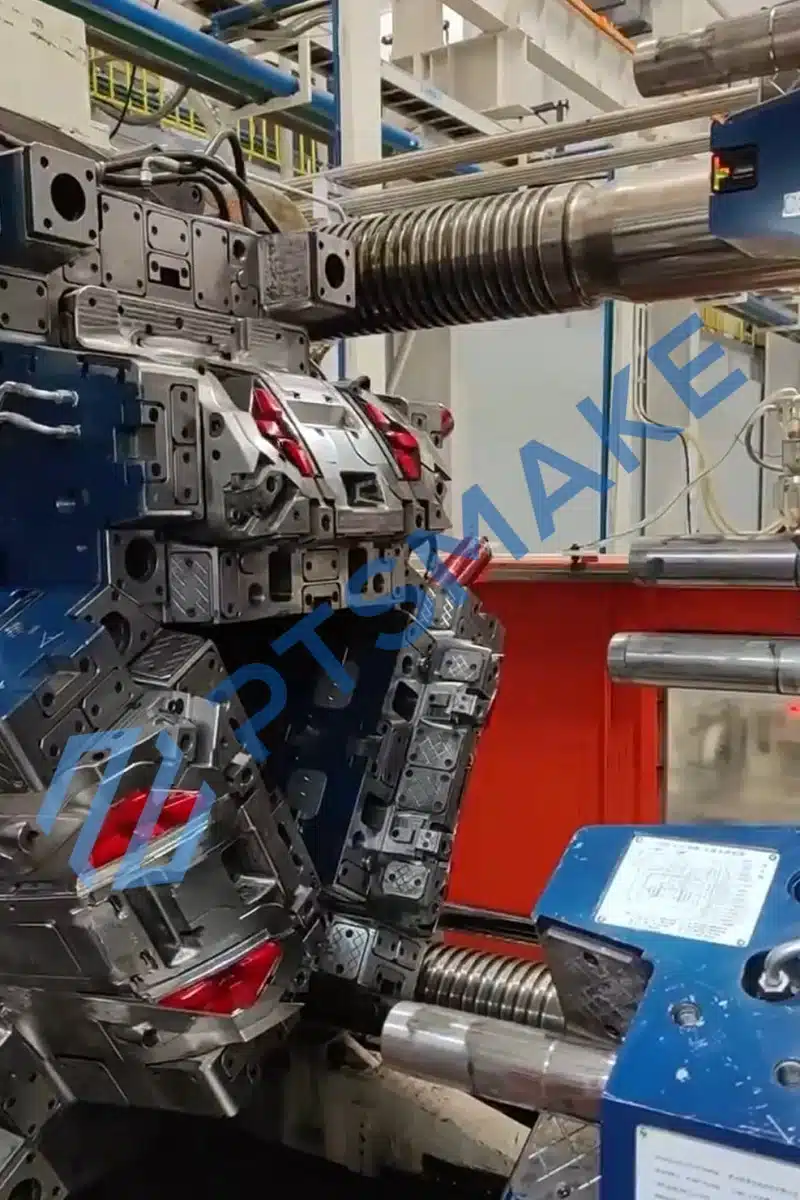
Automotive Industry Applications
In my experience working with major automotive manufacturers, 3K injection molding has become indispensable in creating sophisticated interior components. Here are some key applications:
- Dashboard components with soft-touch surfaces
- Multi-color indicator lights and controls
- Ergonomic gear shifters with different material combinations
- Door trim panels with integrated soft-touch areas
The automotive sector particularly benefits from this technology because it allows for:
- Weight reduction through material optimization
- Enhanced aesthetic appeal with multiple colors
- Improved tactile comfort through selective material use
- Cost-effective integration of multiple functions
Consumer Electronics Applications
The consumer electronics industry has embraced 3K injection molding for several compelling reasons:
Component Type | Materials Used | Benefits |
---|---|---|
Smartphone cases | PC + TPE + ABS | Durability, grip, aesthetics |
Laptop housings | PC + ABS + TPU | Impact resistance, texture variation |
Gaming controllers | ABS + TPE + PC | Ergonomics, durability, comfort |
Wearable devices | TPU + PC + LSR | Water resistance, comfort, durability |
Medical Device Applications
Having worked with numerous medical device manufacturers, I’ve observed how 3K injection molding has transformed the industry:
Surgical Instruments
- Ergonomic handles with different hardness levels
- Color-coded components for easy identification
- Anti-slip grips integrated with rigid bodies
Diagnostic Equipment
- Complex housings with sealed interfaces
- Multi-material components for improved functionality
- Integrated soft-touch control panels
Aerospace Industry Implementation
The aerospace sector utilizes 3K injection molding for:
- Interior cabin components
- Complex duct systems
- Lightweight structural elements
- Multi-functional control panels
Product Design Innovation
From my extensive experience, 3K injection molding enables several design innovations:
Material Combination Benefits
- Enhanced product functionality
- Improved durability
- Better aesthetic appeal
- Reduced assembly costs
Design Freedom
- Complex geometries
- Integrated functions
- Reduced part count
- Streamlined assembly processes
Industrial Equipment Applications
The industrial sector leverages 3K injection molding for:
Application | Key Features | Advantages |
---|---|---|
Control panels | Multi-material interfaces | Improved durability |
Safety equipment | Integrated soft components | Enhanced ergonomics |
Tool handles | Variable hardness zones | Better grip comfort |
Machine guards | Clear + solid sections | Improved visibility |
Sports and Recreation Equipment
Based on my work with sports equipment manufacturers, 3K injection molding offers unique advantages:
- Grip components with varying durometer
- Impact-resistant protective gear
- Water-resistant seals and interfaces
- Customizable aesthetic elements
Future Applications and Trends
From my industry perspective, emerging applications include:
Sustainable Products
- Bio-based material combinations
- Recyclable multi-material components
- Reduced environmental impact designs
Smart Devices
- Integrated sensor housings
- Electronic component encapsulation
- Multi-functional interfaces
Advanced Manufacturing
- Industry 4.0 integration
- Automated quality control
- Enhanced process control
Through my 15+ years of experience at PTSMAKE, I’ve witnessed 3K injection molding evolve into a cornerstone technology for modern manufacturing. Its versatility in combining materials, colors, and properties makes it invaluable across industries. The technology continues to push the boundaries of what’s possible in product design and manufacturing efficiency.
Each application area demonstrates how 3K injection molding solves specific challenges while offering new opportunities for innovation. As materials science advances and design requirements become more complex, this technology will play an increasingly important role in shaping the future of manufacturing.
What Are the Benefits of 3K Injection Molding?
Are you struggling with complex assembly processes and high production costs? 3K injection molding might be the game-changing solution you’ve been looking for.
3K injection molding offers significant benefits including reduced assembly costs, enhanced durability, improved aesthetics through multi-material layering, and greater design flexibility. This advanced process allows combining three different materials in a single mold, revolutionizing product manufacturing.
Cost Efficiency Through Simplified Assembly
In my 15+ years at PTSMAKE, I’ve seen how 3K injection molding consistently reduces production costs. Traditional manufacturing often requires multiple parts to be produced separately and then assembled, which increases labor costs and production time. With 3K injection molding, we can:
- Combine multiple components into a single part
- Eliminate secondary assembly operations
- Reduce labor costs by up to 40%
- Minimize inventory management needs
- Lower quality control expenses
Enhanced Product Durability
The ability to combine different materials in a single mold significantly improves product durability. Here’s what I’ve observed in our manufacturing processes:
Material Layer | Function | Benefit |
---|---|---|
Core Material | Structural integrity | Provides strength and stability |
Middle Layer | Bonding agent | Ensures secure material adhesion |
Outer Layer | Protection/Aesthetics | Offers wear resistance and visual appeal |
Aesthetic Advantages
3K injection molding opens up new possibilities for product aesthetics:
- Multi-color combinations without painting
- Varied surface textures in a single part
- Seamless material transitions
- Custom visual effects through material layering
Design Flexibility and Innovation
Through my experience working with various industries, I’ve seen 3K injection molding enable remarkable design innovations:
- Complex geometries previously impossible with traditional molding
- Integration of soft-touch surfaces with rigid structures
- Customizable material combinations for specific applications
- Reduced design constraints compared to conventional methods
Functional Benefits
Material Property Integration
The ability to combine different materials creates unique functional advantages:
- Rigid support structures with flexible outer layers
- Heat-resistant cores with insulating surfaces
- Electrically conductive components with non-conductive housings
- Chemical-resistant exteriors with structural interiors
Performance Optimization
Our clients have achieved significant performance improvements through:
- Better impact resistance through strategic material layering
- Enhanced thermal management capabilities
- Improved chemical resistance
- Superior electrical insulation properties
Manufacturing Efficiency
Process Integration
3K injection molding streamlines production by:
- Reducing the number of manufacturing steps
- Minimizing material waste
- Shortening production cycles
- Improving quality consistency
Quality Control Benefits
Based on our manufacturing data at PTSMAKE:
- 30% fewer quality issues compared to traditional assembly
- Reduced risk of human error in assembly
- Better part-to-part consistency
- Improved structural integrity
Environmental Impact
The process offers several environmental advantages:
- Reduced material waste
- Lower energy consumption compared to multiple molding operations
- Fewer transportation requirements for components
- Decreased packaging needs
Industry Applications
In my years of experience, I’ve seen 3K injection molding excel in various sectors:
- Automotive: Interior trim components with soft-touch surfaces
- Consumer Electronics: Device housings with multiple functionalities
- Medical Devices: Ergonomic handles with antimicrobial properties
- Industrial Equipment: Complex functional components with integrated seals
Through our work at PTSMAKE, we’ve consistently seen how 3K injection molding provides substantial benefits across manufacturing processes. The technology continues to evolve, offering new possibilities for product design and functionality while maintaining cost-effectiveness and production efficiency.
What Challenges Are Associated with 3K Injection Molding?
Having spent over 15 years in injection molding, I’ve seen many manufacturers struggle with 3K technology despite its amazing capabilities. The challenges are real, but understanding them is the first step to success.
3K injection molding faces several key challenges including high initial investment costs, complex tooling requirements, and the need for skilled operators. Additionally, manufacturers must deal with color contamination risks, extended cycle times, and material flow inconsistencies.
High Initial Investment Considerations
The financial aspect of implementing 3K injection molding is often the first hurdle companies face. In my experience working with various clients at PTSMAKE, I’ve observed that the initial investment can be 2-3 times higher than traditional single-component molding systems. Here’s a breakdown of the major cost factors:
Investment Category | Approximate Cost Range (USD) | Notes |
---|---|---|
Machine Equipment | $300,000 – $800,000 | Varies by size and capabilities |
Tooling | $50,000 – $150,000 | Depends on part complexity |
Auxiliary Equipment | $30,000 – $80,000 | Including material handling systems |
Training | $10,000 – $25,000 | Initial operator training |
Complex Tooling Requirements
The tooling complexity in 3K injection molding presents unique challenges that I’ve helped numerous clients navigate. The main considerations include:
- Multiple injection points requiring precise positioning
- Complex runner systems for material flow control
- Advanced cooling channel designs
- Special venting requirements
- Precise gate location planning
Operator Skill Requirements
From my 15+ years of experience, I can confidently say that skilled operators are crucial for successful 3K molding operations. The key competencies needed include:
- Understanding of material properties and behavior
- Knowledge of process parameter optimization
- Ability to troubleshoot multiple material flows
- Experience with advanced control systems
- Expertise in quality control methods
Color Contamination Issues
Color contamination is a persistent challenge that requires careful attention. At PTSMAKE, we’ve developed several strategies to minimize this issue:
- Proper purging procedures between color changes
- Dedicated material handling systems for each component
- Regular maintenance schedules for nozzles and runners
- Color sequence optimization in production planning
Cycle Time Management
Longer cycle times are inherent to 3K molding due to:
- Multiple injection stages
- Sequential filling requirements
- Additional cooling time needed
- Complex part ejection sequences
- Quality inspection requirements
Material Flow Inconsistencies
Managing material flow in 3K injection molding requires careful consideration of:
- Viscosity matching between materials
- Temperature control for each material
- Flow rate optimization
- Gate location and sizing
- Runner system design
Quality Control Challenges
Based on my experience working with precision parts, quality control in 3K molding requires:
Quality Aspect | Control Method | Frequency |
---|---|---|
Material Interface | Visual Inspection | Every Part |
Color Consistency | Spectrophotometer | Hourly |
Dimensional Accuracy | CMM Measurement | Per Batch |
Bond Strength | Destructive Testing | Daily |
Process Optimization Difficulties
Optimizing a 3K injection molding process involves balancing multiple variables:
- Material temperature control for each component
- Injection speed and pressure settings
- Cooling time optimization
- Shot size accuracy
- Changeover efficiency
Maintenance Requirements
Proper maintenance is critical for successful 3K molding operations:
- Regular cleaning of multiple injection units
- Frequent nozzle and check ring inspection
- Cooling system maintenance
- Preventive maintenance scheduling
- Wear component monitoring
Future Challenges
Looking ahead, the industry faces several emerging challenges:
- Integration with Industry 4.0 systems
- Environmental sustainability requirements
- Energy efficiency demands
- Material compatibility with new compounds
- Increasing quality standards
Through my years at PTSMAKE, I’ve learned that success in 3K injection molding requires a systematic approach to addressing these challenges. While the obstacles are significant, proper planning, investment in training, and maintaining robust quality control systems can help manufacturers overcome these hurdles and achieve successful production outcomes.
What Are the Critical Factors for Success in 3K Injection Molding?
Have you ever wondered why some 3K injection molding projects fail while others succeed? After 15+ years in the industry, I’ve seen both spectacular successes and costly failures.
Success in 3K injection molding depends on five critical factors: material compatibility, precise machine calibration, optimized mold design, advanced simulation software usage, and comprehensive prototyping. Each factor plays a crucial role in preventing production issues.
Material Compatibility
In my experience at PTSMAKE, material selection is the foundation of successful 3K injection molding. The key is ensuring all three materials work together harmoniously. Here’s what I’ve learned:
Chemical Compatibility
- Materials must have similar processing temperatures
- Chemical bonds between materials should be stable
- Thermal expansion rates should be within acceptable ranges
Processing Windows
Each material needs specific conditions for optimal molding. I use this table as a quick reference:
Property | Material 1 | Material 2 | Material 3 |
---|---|---|---|
Melt Temperature (°C) | 190-230 | 200-240 | 180-220 |
Mold Temperature (°C) | 40-60 | 50-70 | 35-55 |
Injection Pressure (MPa) | 80-120 | 90-130 | 70-110 |
Machine Calibration and Control
Precise machine calibration is crucial. I’ve seen many projects fail due to poor calibration. Here’s my approach:
Temperature Control
- Monitor and maintain consistent temperatures across all injection units
- Use independent temperature control for each material
- Regular calibration of temperature sensors
Pressure Management
- Balance injection pressure between all three materials
- Monitor and adjust holding pressure for each material
- Implement pressure sensors for real-time monitoring
Mold Design Optimization
After working on countless 3K projects, I’ve developed these mold design principles:
Gate Design
- Strategic gate placement for each material
- Proper sizing to prevent shear heating
- Balance runner systems for consistent flow
Cooling System
- Independent cooling circuits for each material zone
- Optimized cooling channel layout
- Temperature monitoring points at critical locations
Simulation Software Integration
Modern simulation tools have revolutionized 3K molding. At PTSMAKE, we use advanced software for:
Flow Analysis
- Predict material behavior during injection
- Identify potential weld lines and air traps
- Optimize injection sequence
Cooling Analysis
- Evaluate cooling efficiency
- Identify hot spots
- Optimize cooling channel design
Prototyping Strategy
I always emphasize the importance of proper prototyping. Here’s my proven approach:
Initial Testing
- Single-shot trials for each material
- Progressive integration of materials
- Documentation of process parameters
Quality Verification
- Dimensional accuracy checks
- Bond strength testing
- Visual inspection for defects
Process Control and Monitoring
Based on my experience, continuous monitoring is essential:
Real-time Parameters
- Injection speed
- Pressure profiles
- Temperature stability
- Cycle time consistency
Quality Checks
- Regular part measurements
- Visual inspection protocols
- Bond strength testing
Troubleshooting Common Issues
Here are solutions to problems I frequently encounter:
Warpage Prevention
- Balanced cooling design
- Proper material selection
- Optimized process parameters
Flash Prevention
- Correct clamping force calculation
- Proper venting design
- Regular mold maintenance
Through my years at PTSMAKE, I’ve learned that successful 3K injection molding requires a systematic approach. It’s not just about having the right equipment – it’s about understanding how all these factors work together. I always tell my clients that investing time in proper planning and setup will save significant costs in the long run.
Regular maintenance and documentation of successful parameters are also crucial. I maintain detailed records of every successful project, which helps in quickly setting up similar projects in the future. This approach has helped us achieve a 98% success rate in our 3K molding projects.
Remember, 3K injection molding is complex, but with careful attention to these critical factors, consistent success is achievable. The key is staying methodical and never taking shortcuts in any of these crucial areas.
How to Choose the Right Manufacturer for 3K Injection Molding?
Finding a reliable 3K injection molding manufacturer can feel like searching for a needle in a haystack. After 15+ years in this industry, I’ve seen many companies struggle with this decision.
The key to choosing the right 3K injection molding manufacturer lies in evaluating their technical expertise, equipment capabilities, quality control systems, and production flexibility. You need a partner who can handle multi-material molding while maintaining consistent quality.
Technical Expertise Assessment
Having worked with hundreds of clients at PTSMAKE, I’ve learned that technical expertise is the foundation of successful 3K injection molding projects. Here’s what you should evaluate:
Experience in Multi-material Molding
- Years of experience with 3K molding
- Types of materials they commonly work with
- Previous similar projects
- Technical team qualifications
Design Optimization Capabilities
- DFM (Design for Manufacturing) knowledge
- Material compatibility understanding
- Gate location optimization expertise
- Cooling system design experience
Equipment and Facility Evaluation
Equipment Factor | What to Look For | Why It Matters |
---|---|---|
Machine Types | Modern 3K injection molding machines | Ensures precise material control |
Machine Size Range | Various tonnage capabilities | Flexibility for different part sizes |
Automation Level | Robots and handling systems | Consistent quality and efficiency |
Maintenance Records | Regular maintenance schedule | Reliable production output |
Quality Control Systems
After 15+ years in the industry, I can’t stress enough how crucial quality control is. Here’s what I recommend checking:
Quality Certifications
- ISO 9001:2015 certification
- Industry-specific certifications
- Quality management system documentation
- Regular audit records
Inspection Equipment
- CMM (Coordinate Measuring Machine)
- Visual inspection systems
- Material testing capabilities
- Documentation processes
Production Capacity Assessment
From my experience managing large-scale projects at PTSMAKE, I’ve developed this production evaluation framework:
Short-run Capabilities
- Minimum order quantities
- Setup time efficiency
- Quick changeover procedures
- Prototype development process
Long-run Production
- Maximum monthly capacity
- Production planning systems
- Resource allocation methods
- Inventory management
Communication and Support
Aspect | Important Factors | Red Flags |
---|---|---|
Response Time | Within 24 hours | Delayed responses |
Technical Support | Engineering team availability | Limited technical knowledge |
Language Skills | Clear communication | Miscommunication issues |
Project Management | Dedicated project manager | No single point of contact |
Cost Structure Analysis
Pricing Transparency
- Detailed quotation breakdown
- Tool cost explanation
- Material cost structure
- Production cost factors
Value-Added Services
- Design optimization suggestions
- Material selection assistance
- Assembly services
- Packaging solutions
Essential Checklist for Manufacturer Evaluation
Technical Capabilities
- Multi-material molding experience
- Design optimization expertise
- Material compatibility knowledge
- Advanced equipment availability
Quality Assurance
- Relevant certifications
- inspection equipment
- Quality control procedures
- Defect rate statistics
Production Management
- Capacity utilization rate
- Lead time reliability
- Production planning system
- Inventory management
Business Stability
- Years in business
- Financial stability
- Customer references
- Industry reputation
Risk Assessment
Based on my 15+ years of experience, here are critical risk factors to consider:
Technical Risks
- Material compatibility issues
- Tool design problems
- Process stability concerns
- Quality consistency challenges
Business Risks
- Financial stability
- Intellectual property protection
- Supply chain reliability
- Geographic location impacts
From my years managing complex 3K injection molding projects at PTSMAKE, I’ve learned that successful manufacturer selection requires a systematic approach. Consider this comprehensive evaluation process as your roadmap to finding the right manufacturing partner. Remember, the goal isn’t just to find a supplier; it’s to establish a long-term partnership that can support your product development and production needs.
Don’t rush this decision – take time to thoroughly evaluate each aspect mentioned above. A well-chosen manufacturer will become a valuable asset to your supply chain, while a poor choice can lead to costly delays and quality issues. If you need more specific guidance about any of these aspects, feel free to reach out to me directly.